基体对流动锌酸钾碱液中锌电沉积的影响
溶液中锌与铁沉积电位的比较
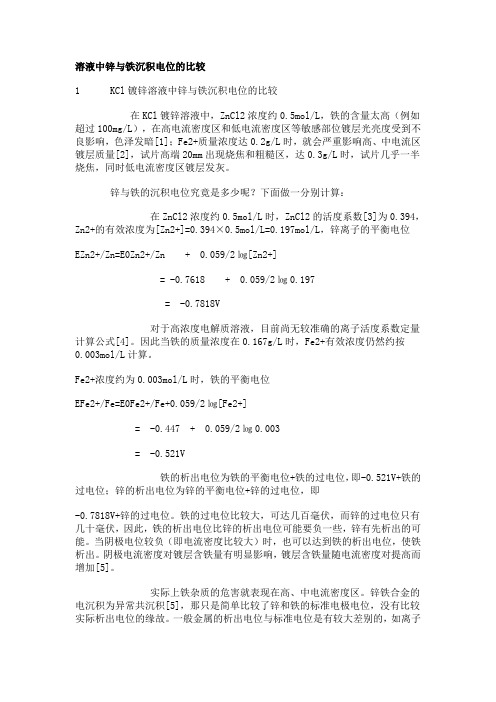
溶液中锌与铁沉积电位的比较1 KCl镀锌溶液中锌与铁沉积电位的比较在KCl镀锌溶液中,ZnCl2浓度约0.5mol/L,铁的含量太高(例如超过100mg/L),在高电流密度区和低电流密度区等敏感部位镀层光亮度受到不良影响,色泽发暗[1];Fe2+质量浓度达0.2g/L时,就会严重影响高、中电流区镀层质量[2],试片高端20mm出现烧焦和粗糙区,达0.3g/L时,试片几乎一半烧焦,同时低电流密度区镀层发灰。
锌与铁的沉积电位究竟是多少呢?下面做一分别计算:在ZnCl2浓度约0.5mol/L时,ZnCl2的活度系数[3]为0.394,Zn2+的有效浓度为[Zn2+]=0.394×0.5mol/L=0.197mol/L,锌离子的平衡电位EZn2+/Zn=E0Zn2+/Zn + 0.059/2㏒[Zn2+]= -0.7618 + 0.059/2㏒0.197= -0.7818V对于高浓度电解质溶液,目前尚无较准确的离子活度系数定量计算公式[4]。
因此当铁的质量浓度在0.167g/L时,Fe2+有效浓度仍然约按0.003mol/L 计算。
Fe2+浓度约为0.003mol/L时,铁的平衡电位EFe2+/Fe=E0Fe2+/Fe+0.059/2㏒[Fe2+]= -0.447 + 0.059/2㏒0.003= -0.521V铁的析出电位为铁的平衡电位+铁的过电位,即-0.521V+铁的过电位;锌的析出电位为锌的平衡电位+锌的过电位,即-0.7818V+锌的过电位。
铁的过电位比较大,可达几百毫伏,而锌的过电位只有几十毫伏,因此,铁的析出电位比锌的析出电位可能要负一些,锌有先析出的可能。
当阴极电位较负(即电流密度比较大)时,也可以达到铁的析出电位,使铁析出。
阴极电流密度对镀层含铁量有明显影响,镀层含铁量随电流密度对提高而增加[5]。
实际上铁杂质的危害就表现在高、中电流密度区。
锌铁合金的电沉积为异常共沉积[5],那只是简单比较了锌和铁的标准电极电位,没有比较实际析出电位的缘故。
锌电解沉积过程电解槽建模与优化控制技术研究
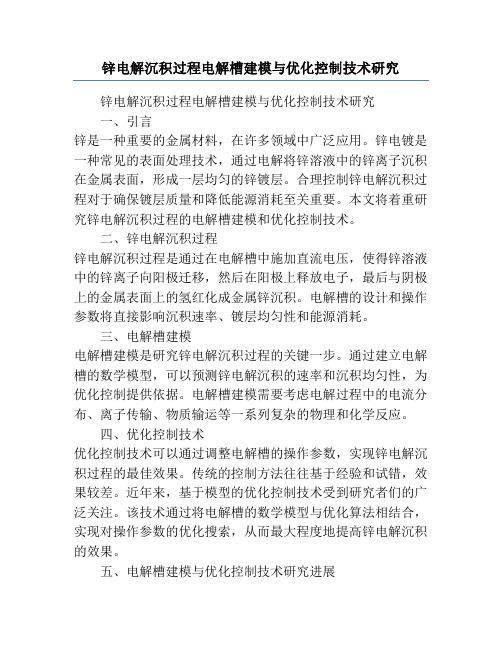
锌电解沉积过程电解槽建模与优化控制技术研究锌电解沉积过程电解槽建模与优化控制技术研究一、引言锌是一种重要的金属材料,在许多领域中广泛应用。
锌电镀是一种常见的表面处理技术,通过电解将锌溶液中的锌离子沉积在金属表面,形成一层均匀的锌镀层。
合理控制锌电解沉积过程对于确保镀层质量和降低能源消耗至关重要。
本文将着重研究锌电解沉积过程的电解槽建模和优化控制技术。
二、锌电解沉积过程锌电解沉积过程是通过在电解槽中施加直流电压,使得锌溶液中的锌离子向阳极迁移,然后在阳极上释放电子,最后与阴极上的金属表面上的氢红化成金属锌沉积。
电解槽的设计和操作参数将直接影响沉积速率、镀层均匀性和能源消耗。
三、电解槽建模电解槽建模是研究锌电解沉积过程的关键一步。
通过建立电解槽的数学模型,可以预测锌电解沉积的速率和沉积均匀性,为优化控制提供依据。
电解槽建模需要考虑电解过程中的电流分布、离子传输、物质输运等一系列复杂的物理和化学反应。
四、优化控制技术优化控制技术可以通过调整电解槽的操作参数,实现锌电解沉积过程的最佳效果。
传统的控制方法往往基于经验和试错,效果较差。
近年来,基于模型的优化控制技术受到研究者们的广泛关注。
该技术通过将电解槽的数学模型与优化算法相结合,实现对操作参数的优化搜索,从而最大程度地提高锌电解沉积的效果。
五、电解槽建模与优化控制技术研究进展在电解槽建模方面,研究者们通过建立质量守恒、动量守恒和电荷守恒方程,考虑电解槽中的电流分布和离子传输过程,成功地建立了锌电解沉积过程的数学模型,并对模型进行了验证和修正。
在模型优化控制方面,研究者们采用了各种各样的优化算法,包括遗传算法、粒子群算法和模拟退火算法等,以实现对锌电解沉积过程的优化控制。
六、研究展望锌电解沉积过程的电解槽建模与优化控制技术研究在工业应用中具有重要意义。
通过建立准确的数学模型,可以预测电解槽的操作参数对沉积速率和镀层均匀性的影响,为优化控制提供依据。
通过优化控制技术,可以实现锌电解沉积过程的能源消耗最小化和镀层质量的最优化。
锌液中各元素对热镀锌的影响
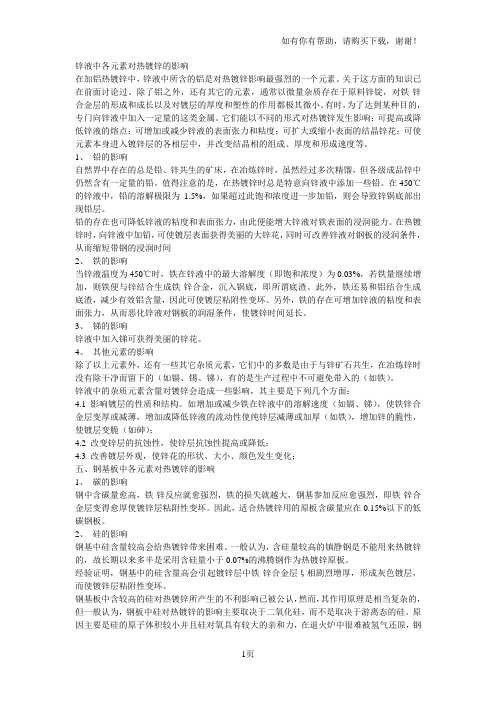
锌液中各元素对热镀锌的影响在加铝热镀锌中,锌液中所含的铝是对热镀锌影响最强烈的一个元素。
关于这方面的知识已在前面讨论过。
除了铝之外,还有其它的元素,通常以微量杂质存在于原料锌锭,对铁-锌合金层的形成和成长以及对镀层的厚度和塑性的作用都极其微小。
有时,为了达到某种目的,专门向锌液中加入一定量的这类金属。
它们能以不同的形式对热镀锌发生影响:可提高或降低锌液的熔点;可增加或减少锌液的表面张力和粘度;可扩大或缩小表面的结晶锌花;可使元素本身进入镀锌层的各相层中,并改变结晶相的组成、厚度和形成速度等。
1、铅的影响自然界中存在的总是铅、锌共生的矿床,在冶炼锌时,虽然经过多次精馏,但各级成品锌中仍然含有一定量的铅。
值得注意的是,在热镀锌时总是特意向锌液中添加一些铅。
在450℃的锌液中,铅的溶解极限为1.5%,如果超过此饱和浓度进一步加铅,则会导致锌锅底部出现铅层。
铅的存在也可降低锌液的粘度和表面张力,由此便能增大锌液对铁表面的浸润能力。
在热镀锌时,向锌液中加铅,可使镀层表面获得美丽的大锌花,同时可改善锌液对钢板的浸润条件,从而缩短带钢的浸润时间2、铁的影响当锌液温度为450℃时,铁在锌液中的最大溶解度(即饱和浓度)为0.03%,若铁量继续增加,则铁便与锌结合生成铁-锌合金,沉入锅底,即所谓底渣。
此外,铁还易和铝结合生成底渣,减少有效铝含量,因此可使镀层粘附性变坏。
另外,铁的存在可增加锌液的粘度和表面张力,从而恶化锌液对钢板的润湿条件,使镀锌时间延长。
3、锑的影响锌液中加入锑可获得美丽的锌花。
4、其他元素的影响除了以上元素外,还有一些其它杂质元素,它们中的多数是由于与锌矿石共生,在冶炼锌时没有除干净而留下的(如镉、锡、锑),有的是生产过程中不可避免带入的(如铁)。
锌液中的杂质元素含量对镀锌会造成一些影响,其主要是下列几个方面:4.1 影响镀层的性质和结构。
如增加或减少铁在锌液中的溶解速度(如镉、锑),使铁锌合金层变厚或减薄,增加或降低锌液的流动性使纯锌层减薄或加厚(如铁),增加锌的脆性,使镀层变脆(如砷);4.2 改变锌层的抗蚀性,使锌层抗蚀性提高或降低;4.3 改善镀层外观,使锌花的形状、大小、颜色发生变化;五、钢基板中各元素对热镀锌的影响1、碳的影响钢中含碳量愈高,铁-锌反应就愈强烈,铁的损失就越大,钢基参加反应愈强烈,即铁-锌合金层变得愈厚使镀锌层粘附性变坏。
溶液浓度及温度对电沉积效果的影响

溶液浓度及温度对电沉积效果的影响1孙达,储洪强,赵明,张洪智,苗成祥,蒋林华河海大学材料科学与工程系(210098)E-mail(sunda0315@)摘要:就电沉积方法修复混凝土裂缝中溶液浓度及温度对电沉积效果的影响进行了试验研究,测定了电沉积过程中的试件质量增加率、表面覆盖率、裂缝愈合率及20d后裂缝填充深度,比较了不同温度下砂浆试件距沉积面5mm处的总孔体积,结果表明:表面覆盖率、裂缝愈合率随电沉积溶液浓度的增大而降低,而20d后裂缝填充深度随浓度的增大而升高,质量增加率随浓度的变化无明显的规律;表面覆盖率随温度的升高而降低,裂缝愈合率随温度升高而升高,质量增加率随温度的变化无明显的规律,温度对20d后裂缝填充深度影响不大,30℃时总孔体积最大。
关键词:电沉积溶液浓度温度电沉积效果1. 引言电沉积方法是修复钢筋混凝土结构裂缝的一项新技术,日本自80年代后期开始电沉积技术修复海工混凝土结构裂缝的研究,以带裂缝的海工混凝土结构中的钢筋为阴极,同时在海水中放置难溶性阳极,两者之间施加弱电流,在电位差的作用下正负离子分别向两极移动,并发生一系列的反应,最后在海工混凝土结构的表面和裂缝里生成沉积物,覆盖混凝土表面,愈合混凝土裂缝。
这些沉积物不仅为混凝土提供了物理保护层,而且也在一定程度上阻止各种有害物质侵蚀混凝土。
根据这一原理日本、美国近年来对电沉积方法修复陆上混凝土裂缝的可行性及经电沉积方法修复后具有干缩裂缝混凝土性能的影响进行了初步研究[1-3],国内对该项技术的研究才刚刚起步。
研究表明[4-5]:辅助电极、电极距离、混凝土参数等因素均对电沉积效果均有影响,而溶液浓度及温度对电沉积效果的影响尚不清楚,所以本文就电沉积方法修复混凝土裂缝中溶液浓度与温度对电沉积效果的影响进行了试验研究。
2. 试验装置及工作原理将带有裂缝的水泥砂浆试件放入电解槽中,试件中预先埋入钢筋并引出导线,该导线与电源的负极相连作为阴极,同时将片状钛网板放入电解槽底部,并与电源的正极相连作为阳极,然后注入电沉积溶液。
锌电积过程中添加剂对阴极的影响
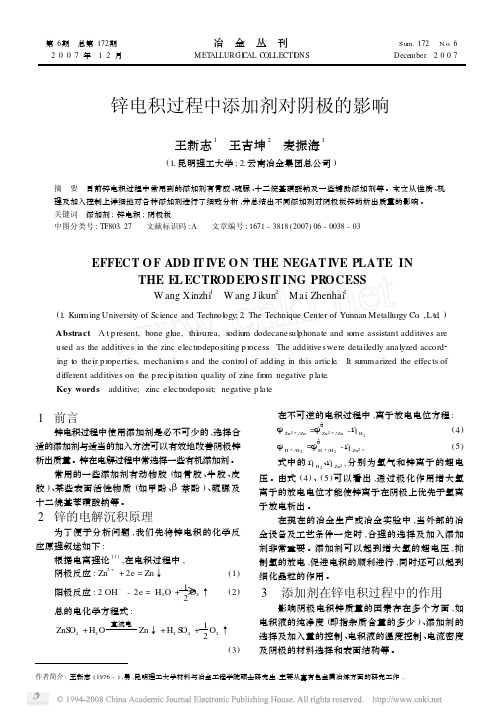
第6期总第172期冶 金 丛 刊Sum.172 N o .6 2007年12月M ET ALLURGI C AL C OLLECTI O NSDece mber 2007 作者简介:王新志(1976-),男,昆明理工大学材料与冶金工程学院硕士研究生,主要从事有色金属冶炼方面的研究工作1锌电积过程中添加剂对阴极的影响王新志1 王吉坤2 麦振海1(1.昆明理工大学;2.云南冶金集团总公司)摘 要 目前锌电积过程中常用到的添加剂有骨胶、硫脲、十二烷基磺酸钠及一些辅助添加剂等。
本文从性质、机理及加入控制上详细地对各种添加剂进行了细致分析,并总结出不同添加剂对阴极板锌的析出质量的影响。
关键词 添加剂;锌电积;阴极板中图分类号:TF803.27 文献标识码:A 文章编号:1671-3818(2007)06-0038-03EFFECT O F ADD I T I VE O N THE NEGAT I VE PLATE INTHE EL ECTROD EPO S I T ING PR OCESSW ang Xinzhi 1 W ang J ikun 2 Mai Zhenhai1(1.Kun m ing University of Science and Technol ogy;2.The Technique Center of Yunnan Metallurgy Co .,Ltd .)Abstract A t p resent,bone glue,thi ourea,s odiu m dodecanesul phonate and s ome assistant additives are used as the additives in the zinc electr odepositing p r ocess .The additives were detailedly analyzed accord 2ing t o their p r operties,mechanis m s and the contr ol of adding in this article .It su mmarized the effects of different additives on the p reci p itati on quality of zine fr om negative p late .Key words additive;zinc electr odeposit;negative p late1 前言锌电积过程中使用添加剂是必不可少的,选择合适的添加剂与适当的加入方法可以有效地改善阴极锌析出质量。
硫酸锌溶液的电积过程
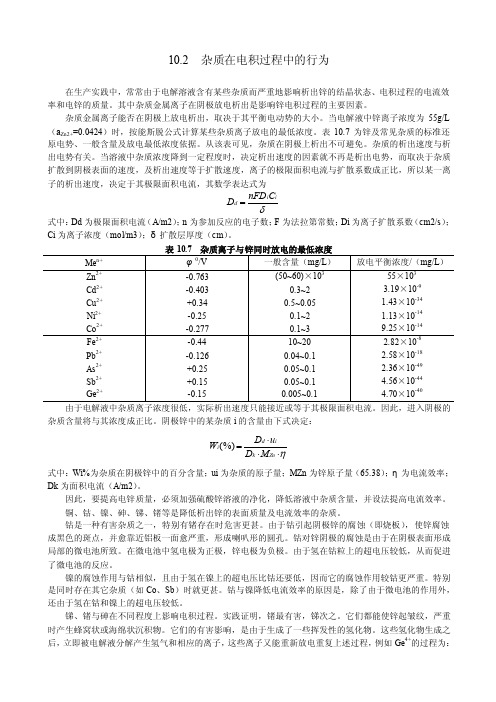
10.2 杂质在电积过程中的行为在生产实践中,常常由于电解溶液含有某些杂质而严重地影响析出锌的结晶状态、电积过程的电流效率和电锌的质量。
其中杂质金属离子在阴极放电析出是影响锌电积过程的主要因素。
杂质金属离子能否在阴极上放电析出,取决于其平衡电动势的大小。
当电解液中锌离子浓度为55g/L (a Zn2+=0.0424)时,按能斯脱公式计算某些杂质离子放电的最低浓度。
表10.7为锌及常见杂质的标准还原电势、一般含量及放电最低浓度依据。
从该表可见,杂质在阴极上析出不可避免。
杂质的析出速度与析出电势有关。
当溶液中杂质浓度降到一定程度时,决定析出速度的因素就不再是析出电势,而取决于杂质扩散到阴极表面的速度,及析出速度等于扩散速度,离子的极限面积电流与扩散系数成正比,所以某一离子的析出速度,决定于其极限面积电流,其数学表达式为δii d C nFD D =式中:Dd 为极限面积电流(A/m2);n 为参加反应的电子数;F 为法拉第常数;Di 为离子扩散系数(cm2/s );Ci 为离子浓度(mol/m3);δ扩散层厚度(cm )。
杂质含量将与其浓度成正比。
阴极锌中的某杂质i 的含量由下式决定:η⋅⋅⋅=Zn k id i M D u D W (%)式中:Wi%为杂质在阴极锌中的百分含量;ui 为杂质的原子量;MZn 为锌原子量(65.38);η为电流效率;Dk 为面积电流(A/m2)。
因此,要提高电锌质量,必须加强硫酸锌溶液的净化,降低溶液中杂质含量,并设法提高电流效率。
铜、钴、镍、砷、锑、锗等是降低析出锌的表面质量及电流效率的杂质。
钴是一种有害杂质之一,特别有锗存在时危害更甚。
由于钴引起阴极锌的腐蚀(即烧板),使锌腐蚀成黑色的斑点,并愈靠近铝板一面愈严重,形成喇叭形的圆孔。
钴对锌阴极的腐蚀是由于在阴极表面形成局部的微电池所致。
在微电池中氢电极为正极,锌电极为负极。
由于氢在钴粒上的超电压较低,从而促进了微电池的反应。
锌酸盐镀锌常见故障现象分析:锌酸盐镀锌液成分及工艺参数的影响

(1)氧化锌。
氧化锌是碱性镀锌液的主盐,它与氢氧化钠作用后生成Zn(OH)44-络离子,其含量对镀液的性能影响很大,镀液中氧化锌含量一般控制在89/L~129/L为宜。
当锌含量过高时,镀层结晶粗糙,镀液的分散能力和深镀能力降低;当锌含量过低时,电流密度范围缩小,高电流密度区易烧焦,阴极电流效率下降,镀层沉积速率慢。
因此,必须严格控制锌含量在工艺范围内。
(2)氢氧化钠。
镀液中氢氧化钠含量一般控制在909/L~1509/L。
氢氧化钠除了络合锌外,还起到促进锌阳极溶解和提高镀液导电性的作用。
因此,当镀液中氢氧化钠含量过低时,镀液导电能力降低,将引起阳极钝化,阴极电流效率下降,沉积速率慢,镀层无光;当含量过高时,则阳极溶解快,镀液中锌离子浓度增大,易导致镀层结晶粗糙、毛刺及光亮不均匀,镀液分散能力差。
(3)添加剂。
氧化锌和氢氧化钠是锌酸盐镀锌的主要成分,如果镀液不加入添加剂,只能得到黑色的海绵状镀层。
锌酸盐镀锌添加剂的种类很多,其作用大都是提高阴极极化,获得光亮细致的镀锌层。
添加剂的管理非常重要,首先是选择优良的添加剂,其次是控制其添加量。
第一次配槽时要按所需添加剂量加入,日常维护应根据生产班次及数量酌情补加,即少加、勤加。
如采用DPE-Ⅲ型添加剂的镀液,最好按每升溶液通电约10A·h消耗lmL量进行补加。
如果镀液中添加剂不足,就不能获得质量良好的镀层;如果添加量过多,将会造成镀层夹杂严重,使镀层发脆,阴极极化增大,引起初始状态渗氢过多,容易产生镀层起泡等故障。
(4)有机杂质。
无论是采用哪种方法补加添加剂,镀液中总是存在一些有机物杂质。
这是因为锌酸盐镀锌添加剂由有机胺和环氧氯丙烷等成分在一定温度条件下反应得到的,其反应产物并不是都在电镀过程中起到良好作用,而有相当一部分是有机分解物。
因此,必须对镀液定期进行净化处理(活性炭59/L吸附、过滤).(5)金属杂质。
锌酸盐镀锌液中的金属杂质主要有铜、铅、铁等,这些金属离子参与电极反应,对镀锌层的结晶有显著影响。
锌002择优沉积

锌002择优沉积
锌的002择优沉积是指锌在沉积过程中,其(002)晶面具有优先生长的趋势。
这种择优沉积现象对于锌金属的应用,特别是在水性锌离子电池中,具有重要意义。
锌的(002)晶面具有最低的表面能和最高的析氢能垒,这有助于抑制电极界面副反应,提升锌负极的可逆性和使用寿命。
同时,(002)晶面的择优沉积也有助于缓解锌枝晶的生长,从而避免电池短路的问题。
为了实现锌的002择优沉积,研究者们采用了多种策略。
其中,调控电沉积电流密度是一种有效的方法。
通过将电沉积电流密度从较低的值提升至较高的值,锌的沉积形态可以从随机的(101)晶面取向逐渐转变为(002)晶面取向。
这种电流调控策略无需使用特定的导电基底和特定电解液,因此在工业化应用中具有较大的潜力。
此外,添加电解质添加剂也是控制锌沉积形态的一种手段。
例如,使用1-丁基-3-甲基咪唑鎓阳离子(BMIm+离子)作为电解质添加剂,可以稳定地诱导Zn(002)面的优先生长并抑制枝晶的形成。
另外,通过六方密排(hcp)Zn(002)晶面和面心立方(fcc)Cu(100)晶面表面晶格的原子尺度匹配,以及欠电位沉积(UPD)亲锌作用,也可以实现平面锌层的定向择优生长,而不是随机生长锌枝晶。
这种方法具有出色的可逆性,并可以实现超高的库仑效率。
这些研究为锌金属在水性锌离子电池中的应用提供了新的思路,有助于推动锌金属负极的稳定性和性能提升。
- 1、下载文档前请自行甄别文档内容的完整性,平台不提供额外的编辑、内容补充、找答案等附加服务。
- 2、"仅部分预览"的文档,不可在线预览部分如存在完整性等问题,可反馈申请退款(可完整预览的文档不适用该条件!)。
- 3、如文档侵犯您的权益,请联系客服反馈,我们会尽快为您处理(人工客服工作时间:9:00-18:30)。
添加甘露醇和山梨醇 , 研究 了锌在不锈钢基体上的电沉积.本课题组¨ 提出 z .i nN 单液流 电池新体 系, 该体系中, 由于离子传质速度加快 , 极大地 降低了这种流动 电解液中锌沉积 的浓差极化 , 避免了
程 杰, 文越 华 , 北京 10 9 0 1 1)
摘要 在 流动的高浓度锌酸钾碱液 中研究 了镍 箔和镀镍 冲孔钢 带基体 电极 对锌沉 积/ 溶解 电化学行 为 的影
响.结果表明 , 在流动 电解液 中电极表面浓度梯度变化不大 , 同基体上均未 出现锌沉积 的阴极 峰 ; 不 扫描 速 度超 过 1 / , 0mV s 循环伏安 曲线基本不随扫速变化 , 明锌 的沉积/ 说 溶解 峰 电流不 仅与扫 描速度有关 , 取 还
决于锌沉积的时间.采用镀镍冲孔钢带基体兼有析氢 过 电位 大和稳定性 好 的特点 , 由于其特殊 的 冲孔 结 又
构, 改变 了传质方式 , 锌沉积 的极化 降低 ,孔的周围形成 紧密堆积 的沉 积锌 , 锌沉 积的 电流和 电量 大 , 积 沉 效率高 , 4次充放电循环后 , 经 库仑效率 即达 9 % 以上 , 5 是性能较佳 的基体电极. 关键词 流动电解液 ; 电沉积 ; 锌 基体 ; 电化学行为
锌枝 晶和 电极变 形 .通过 这种 电极反 应形 式 的改变 , 电极 的使 用 寿命 得 到 显 著提 高 .但 由于析 氢 副 锌
反应及极化等因素的影响 , 易形成海绵状沉积锌 , 导致沉积锌与集流体的结合力较差 , 从而使电池性 能下降.基体是锌镍单电池负极沉积锌的载体 , 直接影响其沉积形貌 、电极反应动力学和结合力 . 因此需充分考虑基体上锌沉积特性和基体在溶液中的稳定性. hn 等 研究 了 c Z ag 钊 u上镀 c d或 P b的 基体 , 明锌在镉基体上沉积的电化学行为简单 , 表 具有较高的沉积效率. c 和 P 镀层在锌 电极多 但 d b 次充放电后易脱落. 在此基础上 , 本文采用循环伏安以及单电极充放 电等电化学方法 , 并结合扫描 电 镜测试技术 , 研究了镍箔和镀镍冲孔钢带基体对流动的锌酸钾碱液 中锌沉积/ 溶解电化学行为的影响.
极所 存 在 的问题依 然没 有得 到很 好解 决 .早 期 C u等 I 曾考察 过 静 止 碱溶 液 中锌 在 P , u d和 h 9 b A ,C
c 等金属基体上的伏安特性及其沉积形态 , u 但未与 电极充放电性能相结合. edi 等 _。 H nr x 1用多晶银 k 。 作基体 , 在碱性溶液中研究了锌电沉积形成锌银合金的过程. as B s等 在固体和涂浆式石墨基体上研
1 2 实验过 程 .
采用 Sl t n18z o ro 0 电化学工作站 , ar 2 用循环伏安法( V 和阴极极化法研究 了基体对锌沉 溶解 C)
收稿 日期 : 0 01—6 2 1 —21 .
基金项 目:国家“ 九七三” 计划项 目( 批准号 : 0 0 B 2 2 1 和国家 自 21C 270) 然科学基金 ( 准号 : 0 00 0 资助 批 5 84 5 )
0 4 .4 T 1 6 6 5 ; M9 1 文献标识码 A 文章编号 0 5 -70 2 1 ) 1 60 5 2 1 9 (0 1 1- 4 - 0 2 0 中图分类号
锌电极具有资源丰富、 平衡电位低 、 可逆性好、 能量密度高和无环境污染等优异性能 , 在化学电 源 尤其是 碱性 锌 系列 电池 中被 广 泛应 用 ,如锌 银 电池 ¨ 、锌 空气 电池 _ 和锌 镍 电池 .等.但 锌 电极 J 2 4 在充放电过程 中易形成枝晶、 钝化 、 腐蚀和电极形变等 , 使电池容量衰减 , 循环性能下降. 通常 , 人们 通过加入电极添加剂以及改变 电解液组分等形式来改善锌 电极的电化学性能 J 然而 , . 碱液 中锌电
Vo . 2 13
21 0 1年 1 1月
高 等 学 校 化 学 学 报
C HEMI CAL J OURNAL OF CHI S NE E UNI VERSTI I ES
No 1 .1
24 6 0—2 4 64
基 体对 流 动锌 酸 钾 碱 液 中锌 电沉 积 的影 响
1 实 验 部 分
1 1 试 剂与 电极 .
K H, n O Z O和 LO 为分 析纯 ( iH 北京化 工 厂 ) 溶 液用 去离 子水 配制 . ;
工作 电极为沉积锌基体 , 分别为 0 1m . m厚 的镍箔、 .5m 00 m厚的镀镍冲孔钢带( 基体结构示意见 图1 , ) 具体特征 : 孔径 15 m, 间隔 10m 孔均匀六方排布 , . m 孔 . m, 镀镍层厚度 1 m, 孔隙率约 3%. 4
联 系人简介 :文越华 , , 士,副研究员 ,主要从事化学电源与材料研究.Ema : e_ uha 2 . o 女 博 — i w n ye u@16 cn l
程
杰等 : 基体对流动锌酸钾碱液 中锌 电沉积 的影响
24 61
过程的影响, 三电极体系中, 大面积烧结镍 电极 为辅助 电极 , H / g 以 gH O为参 比电极 , 沉积锌的基体为工作 电
极 ( 极 尺 寸 :1c c ;电解 质 溶 液 为 1m lL 电 m X1 m) o /
Z O+1 lLK H+ 0g LLO n 0mo O / 2 / i H.所 有测 试均 在磁 力
(吕 善 _ 《 鲁
i a in o c lp a e p r o a e Fg1 Co fgur to fnike- l td e f r t d i n . se lsr p s b t a e t e ti u sr t s