钢包全程加盖设备与工艺研究现状
工业和信息化部、全国总工会关于表扬“我为节能减排献一策”活动优秀集体和个人的通报

工业和信息化部、全国总工会关于表扬“我为节能减排献一策”活动优秀集体和个人的通报
文章属性
•【制定机关】工业和信息化部,中华全国总工会
•【公布日期】2012.05.03
•【文号】工信部联节函[2012]190号
•【施行日期】2012.05.03
•【效力等级】部门规范性文件
•【时效性】现行有效
•【主题分类】机关工作,节能管理
正文
工业和信息化部、全国总工会关于表扬“我为节能减排献一
策”活动优秀集体和个人的通报
(工信部联节函[2012]190号)
为贯彻落实国务院节能减排工作布署和相关文件要求,充分调动工业和通信业系统干部职工参与节能减排的积极性,2010年6月工业和信息化部、中华全国总工会联合开展了“我为节能减排献一策”活动。
广大职工积极参与,提出了百万条优秀合理化建议,涌现了一批先进集体和个人。
经各地工业和信息化主管部门、省总工会审核推荐,工业和信息化部、中华全国总工会组织专家评审,最终评选出优秀合理化建议245条、优秀征文77篇、优秀个人146名、优秀企业120家和优秀组织单位17个。
为表彰先进,宣传典型,进一步推进工业和通信业“十二五”节能工作,现将“我为节能减排献一策”活动优秀名单(名单见附件)予以通报。
希望受表扬的单位和个人不断创新,再接再厉,为节能减排再立新功。
各地主管部门和企业以先进集体和先进个人为榜样,深入实践科学发展观,认真贯彻落实
中央关于节能减排的工作部署,坚定信心,全力以赴做好各项工作,确保完成“十二五”工业节能减排目标任务。
工业和信息化部
中华全国总工会
二〇一二年五月三日附件:
附件2、
“我为节能减排献一策”活动优秀征文名单
附件3、。
钢铁行业智能制造技术发展现状
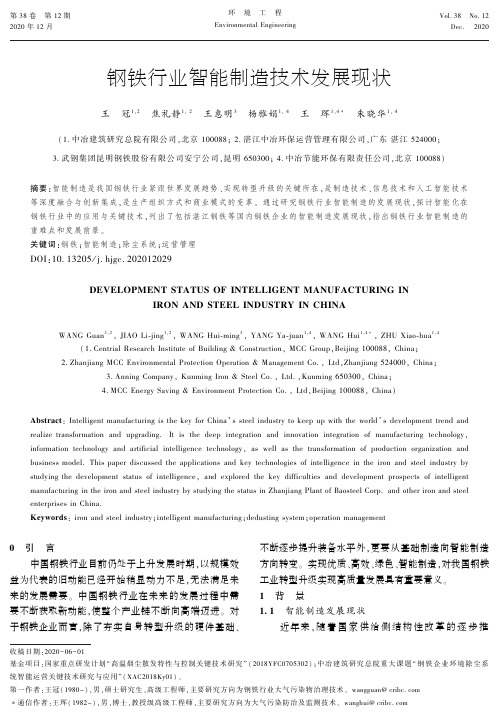
第38卷㊀第12期2020年12月环㊀境㊀工㊀程Environmental EngineeringVol.38㊀No.12Dec.㊀2020钢铁行业智能制造技术发展现状王㊀冠1,2㊀焦礼静1,2㊀王惠明3㊀杨雅娟1,4㊀王㊀珲1,4∗㊀朱晓华1,4(1.中冶建筑研究总院有限公司,北京100088;2.湛江中冶环保运营管理有限公司,广东湛江524000;3.武钢集团昆明钢铁股份有限公司安宁公司,昆明650300;4.中冶节能环保有限责任公司,北京100088)摘要:智能制造是我国钢铁行业紧跟世界发展趋势㊁实现转型升级的关键所在,是制造技术㊁信息技术和人工智能技术等深度融合与创新集成,是生产组织方式和商业模式的变革㊂通过研究钢铁行业智能制造的发展现状,探讨智能化在钢铁行业中的应用与关键技术,列出了包括湛江钢铁等国内钢铁企业的智能制造发展现状,指出钢铁行业智能制造的重难点和发展前景㊂关键词:钢铁;智能制造;除尘系统;运营管理DOI:10.13205/j.hjgc.202012029DEVELOPMENT STATUS OF INTELLIGENT MANUFACTURING INIRON AND STEEL INDUSTRY IN CHINAWANG Guan 1,2,JIAO Li-jing 1,2,WANG Hui-ming 3,YANG Ya-juan 1,4,WANG Hui 1,4∗,ZHU Xiao-hua 1,4(1.Centrial Research Institute of Building &Construction,MCC Group,Beijing 100088,China;2.Zhanjiang MCC Environmental Protection Operation &Management Co.,Ltd,Zhanjiang 524000,China;3.Anning Company,Kunming Iron &Steel Co.,Ltd.,Kunming 650300,China;4.MCC Energy Saving &Environment Protection Co.,Ltd,Beijing 100088,China)Abstract :Intelligent manufacturing is the key for China s steel industry to keep up with the world s development trend andrealize transformation and upgrading.It is the deep integration and innovation integration of manufacturing technology,information technology and artificial intelligence technology,as well as the transformation of production organization andbusiness model.This paper discussed the applications and key technologies of intelligence in the iron and steel industry bystudying the development status of intelligence,and explored the key difficulties and development prospects of intelligent manufacturing in the iron and steel industry by studying the status in Zhanjiang Plant of Baosteel Corp.and other iron and steel enterprises in China.Keywords :iron and steel industry;intelligent manufacturing;dedusting system;operation management㊀㊀㊀㊀㊀㊀㊀㊀收稿日期:2020-06-01基金项目:国家重点研发计划 高温烟尘散发特性与控制关键技术研究 (2018YFC0705302);中冶建筑研究总院重大课题 钢铁企业环境除尘系统智能运营关键技术研究与应用 (XAC2018Ky01)㊂第一作者:王冠(1980-),男,硕士研究生,高级工程师,主要研究方向为钢铁行业大气污染物治理技术㊂wangguan@ ∗通信作者:王珲(1982-),男,博士,教授级高级工程师,主要研究方向为大气污染防治及监测技术㊂wanghui@0㊀引㊀言中国钢铁行业目前仍处于上升发展时期,以规模效益为代表的旧动能已经开始稍显动力不足,无法满足未来的发展需要㊂中国钢铁行业在未来的发展过程中需要不断获取新动能,使整个产业链不断向高端迈进㊂对于钢铁企业而言,除了夯实自身转型升级的硬件基础㊁不断逐步提升装备水平外,更要从基础制造向智能制造方向转变㊂实现优质㊁高效㊁绿色㊁智能制造,对我国钢铁工业转型升级实现高质量发展具有重要意义㊂1㊀背㊀景1.1㊀智能制造发展现状近年来,随着国家供给侧结构性改革的逐步推环㊀境㊀工㊀程第38卷进,我国钢铁行业生产经营情况得到显著改善,自身竞争力得到显著提高[1]㊂ 十三五 期间,国家积极推进信息化发展,中共中央办公厅㊁国务院办公厅印发了‘国家信息化发展战略纲要“,落实国家大数据战略㊁ 互联网+ 行动等相关要求,贯彻创新㊁协调㊁绿色㊁开放㊁共享发展理念,以提升国家经济社会智能化水平[2]㊂‘工业绿色发展规划(2016 2020年)“中提到,近五年是落实制造强国战略的关键时期,是实现工业绿色发展的攻坚阶段[3]㊂‘智能制造发展规划(2016 2020年)“指出:到2020年制造业重点领域企业数字化研发设计工具普及率超过70%,关键工序数控化率超过50%,数字化车间/智能工厂普及率超过20%[4]㊂所以,进一步落实‘中国制造2025“,推进信息化和工业化深度融合,抓住全球制造业分工调整和我国智能制造快速发展的战略机遇期,以智能制造为突破口,加快信息技术与制造技术㊁产品㊁装备融合创新,全面提升企业研发㊁生产㊁管理和服务的智能化水平,实现信息化智能化发展,是我国钢铁行业未来发展的重要方向㊂1.2㊀钢铁行业智能制造技术需求德国提出的 工业4.0 概念是以智能制造为主导的第四次工业革命,将制造业向智能化转型,作为制造业的重要组成部分,中国钢铁行业应当与新一代信息技术深度融合形成新的经济增长点㊂但是,我国国内钢铁行业智能化建设中,智能化基础比较薄弱,整体行业水平相对较低㊂尽管钢铁行业智能化在国内的发展已经取得很大进步,但智能化发展速度相对缓慢,缺乏信息共享㊁大数据集成等相关核心技术㊂此外,行业智能化资金支持上相对薄弱;管理机制㊁运作机制和人才机制尚未完善,缺乏专业性强的高素质人才[5]㊂同时, 十九大 在报告 贯彻新发展理念,建设现代化经济体系 部分明确指出,要加快建设制造强国,加快发展先进制造业,推动互联网㊁大数据㊁人工智能和实体经济深度融合㊂由此可见,智能制造已然成为钢铁行业转型升级的现实需要和必然选择㊂2㊀技术体系钢铁行业积极布局智能制造项目,参与了工信部实施的智能制造试点示范专项行动㊂工信部网站发布的‘工业和信息化部办公厅关于开展2018年智能制造试点示范项目推荐的通知“中提到:钢铁行业现已设置了包含宝钢㊁鞍钢㊁河钢㊁南钢㊁太钢等7家企业共9个项目智能制造试点,涵盖智能车间㊁智慧矿山㊁大规模定制等试点示范项目㊂目前,钢铁行业智能制造水平提升明显,各企业正逐步由点到面地推进智能制造进程,成果初步显现㊂1)数字化㊂2018年,我国大型钢铁行业数字化基础水平(以基础建设得分水平反映)和应用水平(以单项应用得分水平反映)分别达到64.9㊁59.4,较2015年增长2.5%㊁2.8%[6]㊂生产数字化:2018年大型钢铁行业关键工序数控化率达到78.1%,高于全国制造业水平(48.4%) 28.7百分点,较2015年增长4.5百分点,生产流程关键工序装备基本实现较为全面的数字化控制㊂能源管理数字化:2018年已有58.5%的大型钢铁企业应用数字化手段实现能源在线实时监控管理,但部分企业在能源平衡㊁调度㊁计划,尤其是预测方面,尚存在一定的提升空间㊂质量管理数字化:2018年,55.4%的大型钢铁企业应用数字化手段实现覆盖产成品㊁产成品制造过程和原材料入场等环节的质量管理,较2015年增长8.7百分点㊂2)网络化㊂底层装备网络化基础:2018年全国数字化生产设备联网率仅为39.4%,其中大型钢铁行业为54.8%,较2015年仅增长1百分点[6],故钢铁企业亟须大幅提升工业设备设施网络化水平,突破发展瓶颈㊂纵向集成:目前我国大型钢铁行业实现纵向管控集成的企业比例仅为29.5%㊂钢铁企业应进一步提升生产管控水平,实现自动化㊁过程控制㊁生产控制㊁质量管理的数据自下而上贯通,由此实现管控衔接和工序衔接,以及行程制造过程的整体协调,突破个性化高端产品制造的瓶颈㊂横向集成:2018年我国大型钢铁行业实现产供销横向集成的企业比例仅为37.1%,钢铁企业应着力突破供应链集成关键环节,形成产供销相结合的整体供应链体系,加快供应链能力和绩效的有效增长㊂3)智能化㊂2018年大型钢铁行业智能制造就绪率达到19.9%,较全国平均水平(7.0%)高出12.9百分点[8],这些企业底层装备数控化程度较高,在管理信息化与底层自动化之间及内部供应链上主要业务环节实现集成,并不断向智能工厂㊁智慧企业迈进㊂471第12期王㊀冠,等:钢铁行业智能制造技术发展现状从智能生产新体系的构建上看:目前大数据技术在大型钢铁企业中得到了广泛应用,主要包括工业污染与环保监测㊁预警,产品质量管理与分析,生产计划与排程,销售预测与需求管理,供应链分析和优化,生产流程优化,产品设计与开发等方面,其中我国42.6%的大型钢铁企业已经针对工业大数据采集分析体系开展产品质量管理与分析㊂3㊀重点应用案例3.1㊀韶钢智慧中心钢铁一体化智能管控平台韶钢打造的智慧中心整合了铁区和能介全部单元的控制与决策,实现了距离5km以上跨工序㊁跨区域㊁远距离的大规模集控和无边界协同㊂一体化管控后,高炉㊁烧结㊁焦化㊁料场㊁能介等环节各生产终端与智慧中心连接起来,通过采取 厂直管作业区 模式,现场42个中控室全部撤并,取消9个分厂(车间),作业区从64个减少到25个,操作屏从原来的454块减少到193块,人员效率提升31%,实现35万点数据的全覆盖,报表自动生成,并由手机APP自动推送,分层级按时发布给相关人员㊂智慧中心将现场生产与管控平台无缝对接,完善了现场监控手段,实现了跨厂㊁跨工序的远距离沟通,使得管理层得以专注于精细化管理㊂3.2㊀宝钢股份1580热轧智能车间改造2016年9月,宝钢正式启动1580智能车间改造项目,搭建一个自动化㊁无人化㊁智慧化的平台,实现产品的生产管理㊂宝钢股份1580智能车间改造项目,是我国钢铁业唯一正式入围国家工信部‘2015年智能制造试点示范专项行动实施方案“试点示范的项目㊂目前,宝钢产线自动化㊁信息化建设基础较好,但产线自动化率低㊁产品质量和关键消耗指标等仍有提升空间㊂宝钢将1580智能车间改造项目划分为3个阶段推进实施:智能化车间㊁模块优化㊁平台搭建㊂通过使用无人行车解决方案和全套产品㊁优化吊装及物流系统算法㊁应用互联互通系统和专家工程服务等,将生产工序能耗降低6.5%,内部质量损失降低30.6%,废次降低10%,全自动投入率提升10.5%,指标实绩优于设定目标㊂完工后的1580热轧智能车间将成为中国钢厂热轧车间中第1个真正意义上的无人行车车间,为我国钢铁工业的智能化转型提供经验㊂3.3㊀宝钢节能绿色智慧钢渣处理技术上海宝钢节能环保技术有限公司针对钢渣处理技术的智能化,以设备三维非标设计为核心,将产品设计信息㊁制造要求共同定义到该数字化模型中,实现更高层次的设计㊁制造一体化㊂同时,钢渣处理车间无人化生产以渣罐流转为中心,实现起重机无人化运行及实时动态优化调整,提高滚筒系统的定位精度和远程扒渣技术;并通过对滚筒系统的状态数据进行梳理,筛选与设计㊁生产㊁运维密切相关的数据,利用网络手段采集滚筒法渣处理系统的关键数据,实现滚筒渣处理生产线的实时监测㊁管理及设备状态预测诊断㊂从基于滚筒法的钢渣一次处理技术,到针对性的钢渣二次分选处理,最终到因地制宜的钢渣三次资源化利用,各个环节创新协同,旨在构建绿色㊁智慧相融合的钢渣全流程处理技术㊂3.4㊀武钢推进智能制造项目2017 2020年,武钢公司共投资60多亿元用于节能环保领域,全力推进 智能制造与绿色发展 ,一改传统钢铁制造业的发展模式,自动化㊁智能化的智能制造从最初的探索逐步走向成熟,生产清洁化㊁工厂园林化让企业与城市不断亲近㊁融合㊂仅2019年,武钢建成验收了67个智能制造项目,企业智能化率已接近70%,居国内行业前列㊂通过智能制造建设,武钢公司推进 四个一律 (操作室一律集中㊁操作岗位一律机器人㊁运维一律远程㊁服务环节一律上线),以无人化㊁集控化㊁一键化㊁可视化为目标,实现 千米之外 操纵, 千里之外 决策㊂以1个管控中心对多个操控中心构建智慧工厂,实现了所有操作在1个中心,所有操作一键化㊂如今,武钢公司已建成公司级管控中心和铁区㊁炼钢㊁热轧㊁CSP 共4个操控中心,生产工序实现了深度整合, AI+ 5G 的技术在4个操控中心普及,使得工程师们运用移动设备就可以监控机器运行状况并发出指令㊂3.5㊀湛江钢铁环境除尘系统智能化运营管理平台湛江钢铁生产流程涉及码头㊁原料㊁烧结㊁焦化㊁炼铁㊁炼钢㊁连铸㊁热轧㊁厚板㊁冷轧及其他配套建设的公辅等单元㊂湛江钢铁信息化建设是企业全面管理变革的过程,包括生产㊁经营㊁财务㊁质量㊁设备㊁物资㊁运输㊁消防㊁安全环保等管理业务再造,即营销方式㊁生产组织㊁人员管理㊁业务流程和信息化的重新整合[9],实现对生产的集中管理㊁统一指挥㊂湛江钢铁在国内首创将生产管制中心㊁能源管控中心㊁物流管制中心㊁设备管理中心㊁安保消防中心合并的 五部571环㊀境㊀工㊀程第38卷合一 的管控模式,实现了钢铁基地制造流程的多维物流控制,为大型钢铁企业结构优化和发展模式创新提供了技术手段㊂应环保设施运营管理的实际需要,中冶建筑研究总院有限公司作为BOO单位,率先建成1套环境除尘系统智能化运营管理平台[10]㊂该平台集生产运行监控㊁能源管理㊁环保数据中心等功能为一体,以自动化㊁工业网络㊁工业电视㊁计算机软件为基础,实现对各种信号的集中处理,以及与主体㊁点检㊁能环部㊁物流部的信号联络(图1)㊂集中监控平台由生产运行监控系统㊁能耗统计系统㊁排放监测系统㊁视频监控系统㊁电气室监测系统㊁数据中心等子系统组成,通过数据接口与主体厂部通信㊂该平台结合信息化网络技术,集成SCADA系统㊀㊀图1㊀环境除尘集中监控平台信号联络结构Figure1㊀Signal contact diagram of the centralized monitoring platform forenvironmental dust removal实现实时集中监控,并支持制作报表及对实时数据进行应用分析,利用大数据技术,通过算法模型对设备故障进行诊断,对能源用量进行实时监控㊂其开发的关键技术包括数据采集㊁远程传输㊁存储与集中显示技术等,工作平台主界面如图2所示㊂图2㊀环境除尘集中监控平台主界面Figure2㊀Main screen of the environment dedusting centralized monitoring platform1)数据采集㊂非工艺除尘的数据采集对象主要包括除尘系统㊁能源介质㊁在线监测系统㊂除尘系统主要是由PLC完成设备状态监测与控制㊁仪表数据监测㊂主要设备包括风机㊁风机电动机㊁除尘器㊁输灰卸灰阀㊁输灰刮板机㊁斗提机㊁储灰仓卸灰阀等设备,PLC采集设备的运行㊁故障㊁远程㊁电流等状态信息,实现对设备控制和连锁保护㊂能源介质包括电能㊁压缩空气㊁水㊁氧气,其计量数据作为湛江中冶环保与湛江钢铁结算的依据㊂能源数据进入PLC系统进行累计,通过在电气室内安装通信管理机,进行能耗数据采集㊂在线监测系统包括粉尘浓度仪和CEMS系统, CEMS通过数据采集仪进行无线数据传输,用于采集国控源及重点监控的除尘系统㊂2)远程传输㊂非工艺除尘的运营范围包括原料㊁烧结㊁焦化㊁高炉㊁炼钢5个单元,共计90套除尘系统㊂各单元控制室分散布置,独立控制㊂湛江钢铁由于占地面积大,各单元分散,距离远,采用光缆进行网络连接,将各单元的控制网络接入集中监控中心㊂生产运行监控系统通过画面展现生产运行情况,实现对现场设备的实时监控㊁远程操作㊁报警等功能;视频监控系统通过大屏幕展示现场的生产情况,在一些主要工位㊁吸尘点㊁区域设置摄像机,帮助操作人员及时掌握现场情况㊂3)设备运行监控与故障预警技术㊂自动化数据传输到集中监控中心后,读取并存入数据库㊂其中,自主开发的SCADA系统,完成对设备的监视与控制,历史数据查询,数据曲线,能源数据显示等功能㊂同时,平台可以对风机㊁除尘器等关键设备的运行状态进行实时监控,并首次实现设备故障诊断及预报预警功能,为除尘系统的稳定高效运营提供了技术支撑㊂4㊀结㊀语我国制造业目前尚存在各行业机械化㊁电气化㊁自动化㊁信息化参差不齐,不同地区㊁行业㊁企业间发展不平衡,发展智能制造面临关键技术装备受制于人,智能制造标准㊁软件㊁网络㊁信息安全基础薄弱,智能制造新模式推广尚未起步,智能化集成应用缓慢等㊀㊀(下转第137页)671。
炼钢工艺简介及能源介质消耗

参数 300吨 13% 4个 1.4-1.7Nm3·t-1·min-1 8个 0.04-0.3Nm3·t-1·min-1 8-10min
产品一流 管理一流 环境一流 效益一流
三、工艺设备简介及能源消耗
2、炼钢作业区-转炉脱磷
加3废钢
兑铁
降枪开氧 点火
吹炼
加辅料造 渣
倒渣
溅渣护炉
合金化
出钢
提枪闭氧
过程能源消耗: 1)转炉倾动耗电,氧枪、副枪升降耗电; 2)氧枪吹氧、吹氮,底吹吹氮、吹氩,氧枪孔、副枪孔
三、工艺设备简介及能源消耗
5、精炼作业区-钢包
主要参数
项目
参数
钢包
39个
烤包器
8个
倾翻
4个
钢包烘烤时间
8-44h
渣罐烘烤时间
2h
产品一流 管理一流 环境一流 效益一流
精炼作业区能源介质情况(CAS+RH+LF+钢包):
项目 耗电 氧气 氮气 氩气 煤气消耗 煤气回收 蒸汽消耗 蒸汽回收
单位 kwh/t m3/t m3/t m3/t m3/t m3/t kg/t kg/t
提升能力
30吨
பைடு நூலகம்
提升行程
7000mm
提升速度
7.0m/min
停止精度
±30mm
正常100~120rpm,新搅拌头
搅拌头的转速
时最大150rpm
类型
绞盘式提升和搅拌设备
炼铁—炼钢界面采用了铁水罐一罐到底 技术。铁水脱后硫≤0.002%比例达到98% ,采用一键式脱硫。
产品一流 管理一流 环境一流 效益一流
消耗的主要能源:电
拥有两座泵站,主要设备 有: 2座旋流井,6台中速罐、 20台高速罐、4台稀土磁盘、2 套高效澄清器、2套压滤机设 备及冷却塔、空冷器、供水泵 等,包括14个循环水系统,主 要为全厂各工序提冷却水和循 环水质处理。
炼钢经济铁耗效益分析及控制措施

炼钢经济铁耗效益分析及控制措施摘要:铁水消耗指炼钢生产单位合格钢坯所消耗铁水量,近年来实施的经济铁耗指的是,在炼钢工艺允许的前提下,通过控制铁耗,实现公司效益最大化。
近年来,各钢铁企业都致力于通过经济铁耗控制实现尽可能大的产量规模和效益最大化,近些年以来,废钢铁价格在大多时段也低于铁水成本,经济铁耗在该企业的重要性更为凸显。
通过建立经济铁耗模型、按月测算经济铁耗平衡点,企业实现了效益最大化。
关键词:炼钢;经济铁耗;边际效益引言近年来,国内有的钢铁企业经济型铁料资源短缺,企业建设之初没有科学评估周围条件,炼钢设计生产能力大于炼铁生产能力过多,炼钢生产节奏难以提升。
以上问题都使得铁水的供应成为瓶颈环节,能耗物耗浪费巨大,需要企业控制较低的铁耗,以克服以上资源或设计上的问题。
同时,因为市场具有调节作用,会出现废钢铁价格阶段性明显低于铁水价格的情况,此时在钢铁料结构控制时,采用较低的铁耗能显著降低钢铁料结构成本。
以上问题就引出一个“经济铁耗”的概念。
本文对经济铁耗的测算,对效益进行对比,并提出经济铁耗控制措施,尤其建议钢铁企业有必要进行低铁耗和高废钢比的实战积累经验以及技术储备以应对金属料市场变化,同时给出常用的低铁耗高废钢比措施。
旨在结合业界情况,提出一些想法,以期助力钢铁企业降本增效工作,同时为专业技术人员和成本控制人员提供思路与参考。
1经济铁耗测算基准及边际条件1.1出钢温度从表1可以看出,通过调整入炉金属料结构及过程辅料的加入,该炼钢工序4季度普碳钢转炉出钢温度基本在1640~1650℃范围内,受铁耗因素影响较小。
以下核算过程出钢温度按照1645℃计算,同时忽略铁耗变化对精炼成本影响。
表1 某公司炼钢工序4季度不同铁耗下转炉出钢温度统计1.2普碳钢铁耗控制下限1.2.1物料平衡计算以目前正常控制下限铁耗880kg/t为例,以100kg金属料为单位进行计算(只用废钢与铁块作冷却剂)。
⑴炉渣量及成分计算炼钢余锰含量约占金属原料中锰含量的30%;脱硫效率为20%,其中气化脱S 比例1/3;脱磷效率为90%。
探讨如何做好炼钢厂的节能降耗工作
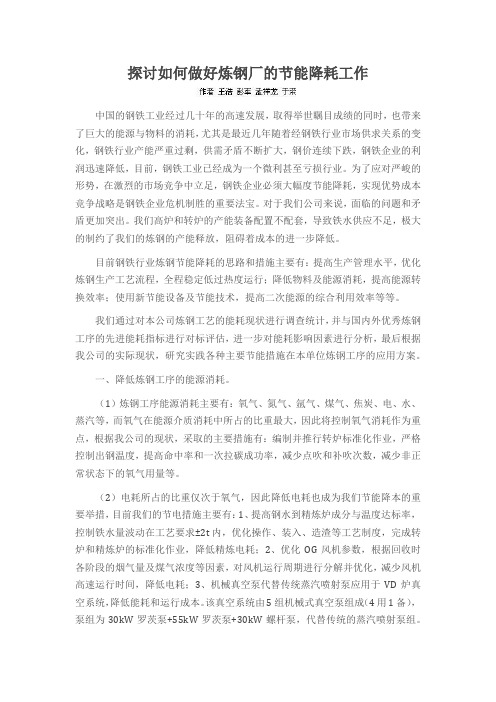
探讨如何做好炼钢厂的节能降耗工作中国的钢铁工业经过几十年的高速发展,取得举世瞩目成绩的同时,也带来了巨大的能源与物料的消耗,尤其是最近几年随着经钢铁行业市场供求关系的变化,钢铁行业产能严重过剩,供需矛盾不断扩大,钢价连续下跌,钢铁企业的利润迅速降低,目前,钢铁工业已经成为一个微利甚至亏损行业。
为了应对严峻的形势,在激烈的市场竞争中立足,钢铁企业必须大幅度节能降耗,实现优势成本竞争战略是钢铁企业危机制胜的重要法宝。
对于我们公司来说,面临的问题和矛盾更加突出。
我们高炉和转炉的产能装备配置不配套,导致铁水供应不足,极大的制约了我们的炼钢的产能释放,阻碍着成本的进一步降低。
目前钢铁行业炼钢节能降耗的思路和措施主要有:提高生产管理水平,优化炼钢生产工艺流程,全程稳定低过热度运行;降低物料及能源消耗,提高能源转换效率;使用新节能设备及节能技术,提高二次能源的综合利用效率等等。
我们通过对本公司炼钢工艺的能耗现状进行调查统计,并与国内外优秀炼钢工序的先进能耗指标进行对标评估,进一步对能耗影响因素进行分析,最后根据我公司的实际现状,研究实践各种主要节能措施在本单位炼钢工序的应用方案。
一、降低炼钢工序的能源消耗。
(1)炼钢工序能源消耗主要有:氧气、氮气、氩气、煤气、焦炭、电、水、蒸汽等,而氧气在能源介质消耗中所占的比重最大,因此将控制氧气消耗作为重点,根据我公司的现状,采取的主要措施有:编制并推行转炉标准化作业,严格控制出钢温度,提高命中率和一次拉碳成功率,减少点吹和补吹次数,减少非正常状态下的氧气用量等。
(2)电耗所占的比重仅次于氧气,因此降低电耗也成为我们节能降本的重要举措,目前我们的节电措施主要有:1、提高钢水到精炼炉成分与温度达标率,控制铁水量波动在工艺要求±2t内,优化操作、装入、造渣等工艺制度,完成转炉和精炼炉的标准化作业,降低精炼电耗;2、优化OG风机参数,根据回收时各阶段的烟气量及煤气浓度等因素,对风机运行周期进行分解并优化,减少风机高速运行时间,降低电耗;3、机械真空泵代替传统蒸汽喷射泵应用于VD炉真空系统,降低能耗和运行成本。
RH-LF和 LF-VD 工艺生产管线钢洁净度的比较

RH-LF和LF-VD工艺生产管线钢洁净度的比较一、电弧炉炼钢的时代特点1、变为初炼炉进入20 世纪80年代后,随着炉外精炼技术、工艺、装备的快速发展,原冶炼工艺中在电弧炉内完成的合金钢、特殊钢的脱氧、合金化、除气、去夹杂的电炉“重头戏”移到炉外精炼炉去进行了。
电弧炉及转炉皆变为只须向炉外精炼炉提供含碳、硫、磷、温度、合金化合格或基本合格的钢水就算完成任务的炼钢初炼炉。
改变和结束了原电弧炉的熔时长(三个多小时)、老三期操作(熔化期、氧化期、还原期)以及产量低、渣量大、炉容小、成本高的状况。
2、炉容大型化随着电炉—炉外精炼—连铸—直接轧材工艺的发展,这种短流程(相对于焦化、烧结—高炉—转炉—炉外精炼炉—连铸—)轧材工艺而言的轧机产量要求电炉与之相匹配,例如长材年产50-80 万t、板材100-200 万t 、热轧卷年产200万t以上,因此单一匹配电炉的炉容量和生产率,生产速率必须与轧机相衔接.目前, 较多采用公称炉容量80-120万t 左右的电弧炉,从趋势看炉容量仍在提高。
变压器向超高功率发展(1000KV A/t)。
3 、电炉转炉化氧气顶吹转炉依靠铁水为原料,吹氧冶炼故冶炼周期短(20min左右),产量高,即获得了比电炉高的多的生产率和生产速率( 科技工作者在20 世纪50年代在电弧炉上吹氧(炉门和炉顶)兑入约30%~50%的铁水(EOF 炉),把转炉的工艺优势移植过来,电炉的冶炼周期大大缩短,目前均在45min 左右( 故电炉顶吹氧、热装铁水、电炉双炉壳很快得到推广。
4、电弧炉钢产量大幅增长在上述三项电炉自身工艺变化的同时,随着社会发电技术,能力的增长(核电站、水力发电等)及社会废钢量的增加,直接还原铁DRI、HBI、Fe3C 技术工艺的发展,都为电弧炉快速发展提供了条件. 因此,世界各国电弧炉钢产量由1950 年占世界总产钢量的6.5%增至1990 年的27.5% , 2003 年的36%.5、提质、降耗、防污染使电弧炉获得新的活力电弧炉使用废钢为原料与使用高炉铁水的转炉相比,总能耗是高炉-转炉工艺的1/2~1/3。
合金烘烤装置在转炉炼钢中的应用

EXCHANGE OF EXPERIENCE 经验交流摘要:通过介绍合金烘烤装置的原理和构成,提出了一种新型高性能燃气燃烧器的合金烘烤装置,其烘烤系统燃烧成效显著,提高热效率的同时也降低了能源消耗。
关键词:合金烘烤;节能降耗;控制系统一、前言当前企业增加市场竞争力及降本增效必须要在炼钢的能耗降低和产品附加值的提升端两方面做好出路。
因此各钢企针对转炉出钢温度的降低及出钢期间温降都做了大量的研究和实践,例如:降低钢包周转频率,钢包烤包预热,出钢后全程加盖,合金烘烤等,都取得不错的效果。
其中,合金烘烤装置是烘烤铁合金的专用设备,通过对硅铁、锰铁、铬铁、钼铁、钛铁、钒铁等合金炉料进行脱水份烘烤,使合金达到要求温度,能满足炼钢工艺要求,实现缩短冶炼时间,提高钢材质量的目的。
本文介绍的唐山中厚板公司3座120吨转炉所采用新型高性能燃气燃烧器的合金烘烤装置,相对于其他类型的合金烘烤采用了设计独特的环形扁缝式燃气射流方式,热效率得到显著提高。
同时转炉煤气的使用相比于燃烧其他介质燃料也降低了能源消耗。
二、合金烘烤的工作原理(一) 合金烘烤装置简介。
烘烤装置主要的系统构成有:热风发生装置、烘烤料仓、排烟系统、热风管路系统、控制系统。
主要采用转炉煤气为燃烧介质,其LGB低速燃气燃烧器是一种新型的高性能燃气燃烧器。
与以往的套管式和多管式燃气喷嘴均不相同,LGB燃烧器采用了设计独特的环形扁缝式燃气射流方式,在每一层环形燃气射流的两侧则均为环形的空气射流。
因而,在燃烧器的出口处燃气和空气能迅速产生强烈而均匀的掺混,造成特别适合燃烧的燃气——空气混合气流从而保证整个燃烧器能完全、稳定、高效地燃烧。
其中自动控制系统为图1所示。
图1 合金烘烤炉自动控制系统(二)合金烘烤装置的性能及其技术参数。
(1) 该合金烘烤装置采用转炉煤气作为燃料,热值为1500kCal/Nm3。
(2)转炉煤气压力处于7-15kPa范围内能燃烧稳定。
(3) 压缩空气压力范围:0.4-0.6Mpa ;氮气压力范围:0.4-0.6Mpa。
钢包底吹氩工艺开发

钢包底吹氩工艺开发摘要:钢包底吹氩工艺是一种有效的钢水处理方法,通过向钢包底部吹入氩气,使钢水中的杂质和气体充分上浮,达到净化钢水的目的。
本文主要介绍了钢包底吹氩工艺的原理、开发过程及应用效果,阐述了该工艺对提高钢水质量和连铸效率的影响。
一、钢包底吹氩工艺原理钢包底吹氩工艺的原理是在钢包底部通过特制的喷嘴向钢水中吹入氩气。
氩气在钢水中形成气泡,气泡在上升过程中会吸附钢水中的杂质,并携带杂质上浮,从而达到净化钢水的目的。
同时,氩气的搅拌作用还可以使钢水成分和温度更加均匀,提高钢水的质量。
二、钢包底吹氩工艺开发钢包底吹氩工艺的开发主要包括工艺流程设计、设备选型和控制系统优化三个环节。
首先,需要确定合适的氩气流量、压力和喷嘴结构,保证氩气能够充分搅拌钢水。
其次,需要根据钢包容量、钢水处理量和现场实际情况选择合适的设备型号和数量。
最后,需要对控制系统进行优化,确保工艺过程的稳定性和可靠性。
三、钢包底吹氩工艺应用效果钢包底吹氩工艺在多个钢铁企业得到了广泛应用,并取得了良好的应用效果。
首先,该工艺可以显著提高钢水质量,降低钢水中杂质含量,提高钢材的力学性能和耐腐蚀性能。
其次,该工艺可以显著提高连铸效率,降低铸造成本,提高钢铁企业的经济效益。
此外,该工艺还可以减少铸坯裂纹、提高铸坯质量,延长铸坯使用寿命。
四、结论钢包底吹氩工艺是一种有效的钢水处理方法,通过向钢包底部吹入氩气,可以显著提高钢水质量和连铸效率。
该工艺的开发和应用对于提高钢铁企业的产品质量和经济效益具有重要意义。
未来,还需要进一步研究和优化钢包底吹氩工艺,以推动钢铁工业的持续发展。
在铜冶金工业中,新型双侧吹熔池熔炼工艺设备的应用已经成为了一种趋势。
这种工艺设备可以提高铜金属的产量和质量,同时降低能耗和污染物排放,为铜冶金工业的可持续发展做出了巨大的贡献。
铜冶金工业是一个重要的基础工业,对于国民经济和科学技术的发展具有重要意义。
然而,传统的铜冶金工艺存在一些问题,如能耗高、污染物排放量大、产量低等。
- 1、下载文档前请自行甄别文档内容的完整性,平台不提供额外的编辑、内容补充、找答案等附加服务。
- 2、"仅部分预览"的文档,不可在线预览部分如存在完整性等问题,可反馈申请退款(可完整预览的文档不适用该条件!)。
- 3、如文档侵犯您的权益,请联系客服反馈,我们会尽快为您处理(人工客服工作时间:9:00-18:30)。
第 - 1 - 页 共 4 页 钢包全程加盖设备与工艺研究现状 刘晓峰 (重庆钢铁股份有限公司炼钢厂 重庆 400081) 摘 要:通过大量文献调研,介绍了炼钢生产中钢包全程加盖设备与工艺研究现状,为重
钢环保搬迁改造,落实国家节能减排政策,建设低成本洁净钢平台,实现绿色、环保、高效生产提供有益借鉴。 关键词:钢包,全程加盖,设备与工艺,重钢,借鉴
The whole equipment and craft affixed to the ladle research status Liu Xiaofeng (Chongqing Iron and Steel Co., Steel Plant Chongqing 400081,China) Abstract : Through the literature available, introduced in the steelmaking ladle stamped with
equipment and technologies for environmental research situation, for chongqing iron and steel company, to carry out the national environmental move transformation energy saving and emission reduction policy, construction low cost clean steel platform to realize green, environmental protection, high efficiency production provides useful reference. Key words :ladle,stamped with the whole,equipment and technology,Chongqing Iron and
Steel,reference
1 前 言 钢包作为炼钢工序与连铸工序之间的盛钢容器,其在生产周转过程的热状态,直接影响出钢和盛钢过程中钢水温度的变化。针对炼钢生产过程钢水温度波动较大,影响过程温度控制,一般采取强化钢包烘烤、提高钢包热周转、优化包衬结构、钢水运转过程加保温剂和浇注过程钢包加盖等手段来减少钢水温降[1]。虽采取以上手段,但效果炼钢过程钢水温度控制精确能力非常有限。研究表明,一台150t钢包空包开始后,前20min内由包衬向空气的辐射热损失将导致下一炉钢水温度损失达15℃。而这种热损失的40%发生在空包开始后的前5min。 通过在钢包上加盖,辐射热损失可显著减少。由于钢包加盖显而易见的节能效果,成为钢铁企业节能降耗的一个重要手段。比如连铸机上广泛采用了钢包加盖装置[2]。然而,即使是连铸机上加盖,也是属于局部的非全程式保温措施。现有钢包加盖操作必须由天车辅助完成,使得这项技术在实际应用中的可操作性受到了极大限制,无法做到在整个使用循环过程中都使钢包盖盖在钢包上。据文献[3-11]介绍,国内外部分设计单位联合钢厂经过技术引进、消化、转化创新,设计研发出适合我国炼钢厂实际生产需要的钢包全程加盖设备和工艺技术,取得了很好的生产实践效果。本文介绍炼钢生产中钢包全程加盖设备与工艺研究现状,为重钢环保搬迁改造,落实国家节能减排政策,建设低成本洁净钢平台,实现绿色、环保、高效生产提供有益借鉴。 2 设备状况 钢包全程加盖主要设备包括: 1)加揭盖机。有插齿式、移动插齿式、液压升降/伸缩-式、回转式、悬挂移动式等(见图1、图2)。根据不同炼钢厂工艺布置的差异采用不同的设备组合。 第 - 2 - 页 共 4 页
图 1 回转式钢包加盖机加盖 图 2 插齿式钢包加盖机揭盖 2)钢包盖。盖体有整体浇注式和耐火纤维式。据文献[3]介绍,钢包盖通过联接爪与钢包联接,这种联接方式在钢包直立时便于包盖的摘取,而在钢包因排渣、更换滑动水口等作业而必须倾倒时,包盖与钢包靠联接爪自行锁紧。由于在钢包盖上留有靠自重而自动开闭的排渣门和测温取样孔,所以在钢包接完钢水后的全程作业中,实现包盖一直盖在钢包上的目的。连在包盖上的上联接爪和固定在钢包上部的下联接爪等组成,其特征在于上联接爪呈倒“U”状,并在“U”口处安设一销杆,下联接爪呈“U”形并在外侧“U”板上开设一带凹沟的销槽,在销槽的平直侧加一靠自重而转动的栓销,在盖体盖在钢包上时上、下联接爪相吻合,销杆下入销槽内。 3)辅助设备:铰链座、包盖存放台、包盖烘烤设备、专用吊具、专用工装等。 3 操作工艺
3.1 出钢前准备 在完成炉次之间对钢包的准备服务后,钢包不是象通常那样被放到预热器上进行预热,而是被放回到等候在电炉或转炉旁边的钢包车上,并且有钢包盖盖在上面,直到下一炉开始出钢,所以在使用钢包全程加盖设备与工艺进行生产时,正常周转钢包将不再需要在线预热。只有在遇到长达几个小时的超时工序延迟时,钢包预热才需加以考虑。
图 3 钢包倒渣加盖设备自动开启 图 4 钢包带盖热修 钢包倒掉铸余渣,清洗水口滑板后,可直接在钢包带盖或炼钢炉出钢前完成加入引流砂填入。完成填砂后,钢包经过出钢线,采用揭盖装置完成揭盖,包盖存放专用存放台,进入炼钢炉下出钢(见图5)。 第 - 3 - 页 共 4 页
图 5 炼钢炉出钢线自动加盖 图 6 炼钢炉出钢线自动揭盖 3.2 出钢后加盖 炼钢炉出钢完成后,当钢包经过包盖专用存放台,自动完成加盖操作,不需要人为干预(见图6)。 3.3 精炼揭盖 钢包进入精炼工位(LF或RH)可完成喂丝脱氧处理,包盖设置测温取样和喂丝孔。钢包经过精炼平台钢车线,采用揭盖装置完成揭盖,包盖存放专用存放台,进入精炼炉完成处理位钢水精炼(见图7)。
图 7 精炼揭盖装置 图 8 精炼加盖装置 3.4 精炼加盖 处理位钢水完成精炼任务,当钢包经过包盖专用存放台,自动完成加盖操作(见图8)。加盖钢包可进行钙处理或微合金化。钢水成分、温度、洁净度等合格后,直接用天车吊上连铸回转台。连铸工序可不设置钢包加盖装置。 4 效果评价 钢包全程加盖系统使炼钢厂显著降低钢包内的热量损失,减少钢包内钢水温降。这些能量损失的减小转化成重要的生产经济效益。最主要的效益表现在操作成本的降低、产品质量的提高和生产效率的提高。
使用钢包全程加盖节能系统使钢包盖在近乎整个钢包使用循环周期内都始终盖在钢包上,由此带来的直接效益有: 1)可免除周转钢包在线预热,在线烘烤主要用于非正常情况下的抢救性升温。钢包加盖浇注完1h后包衬温度在1000℃以上,能够实现红包出钢。马钢第四钢轧总厂炼钢分厂300t钢包下线10h不用,也不需再进行烘烤[4]。刑钢炼钢厂停用8h后的加盖钢包包壁温度在550~600℃之间,比未加盖钢包的温度提高400℃以上,与大火烘烤4h的钢包相比温度基本相同(烘烤4h后钢包内壁温度一般在550~650℃之间),停用8h之内的钢包直接进行加盖操作能够保证钢包内壁温度[5]。 2)钢水出炉温度可以被降低20-30℃。唐钢二钢轧厂转炉出钢温度比未加盖前降低15-20℃[11-12]。邢钢炼钢厂转炉出钢过程 第 - 4 - 页 共 4 页
温度损失减少4℃,运输过程温度损失约减少19℃,全程温度损失减少23℃,铝镇静钢和硅铝镇静钢系列的出钢温度在原基础上下调20℃[10]。 3)减少包内钢水的冷却。减少钢水在钢包、中间包及结晶器内的温度波动,可实现低过热度浇注,免除连铸过程中对中间包的辅助预热。刑钢炼钢厂加盖钢包连铸中包温度合格率提高8%[5]。合金收得率更加稳定,减少钢包内的废钢产生,节约保温剂的使用量。 4)减少对钢包边沿及渣线的清理需求,从而减少对包衬耐火的机械损伤。马钢第四钢轧总厂炼钢分厂300t钢包带盖翻铸余,翻得干净,包底残钢、残渣明显减少[4]。 5)节能减排[7-8]。转炉出钢吹氧升温按5Nm3℃吨钢计算,温度提高10℃,年产500万吨钢厂节约氧气用量25000万Nm3。在线烘烤焦炉煤气升温按400Nm3/h烘烤20min,年产500万吨钢厂节约烘烤煤气量4000万Nm3。转炉出钢降温10℃减少烟气排放25000万Nm3/h。钢包烘烤减少烟气排放6000万Nm3/h。 6)可实现的吨钢费用节约一般在20-25元之间,每100万吨钢可节支800万至1300万元[7-8]。唐钢二钢轧厂吨钢成本降低5元,预计年创效2000万元[11-12]。 7)炼钢炉及钢包上的耐火侵蚀被减小,因此炉龄/包龄被延长。邢钢炼钢厂转炉出钢口寿命提高30炉以上,钢包寿命有加盖前的75.4炉提高至77.9炉[10]。 8)减少LF升温时间,减少RH、CAS 的OB频率及时间。产品质量得以提高。 9)职工劳动力需求减少。钢包服务区的操作空间可以缩小,提高车间人员的安全保护。整个厂区环境温度改善,污染减少。 5 结 语 通过国内钢铁企业的实践应用,已经充分的证明钢包全程加盖技术是一项节能、环保、降耗的新技术。此项技术,可以为重钢环保搬迁改造,落实国家节能减排政策,建设低成本洁净钢平台,实现绿色、环保、高效生产提供有益的借鉴。
参考文献 [1] 张威,刘晓峰,朱光俊,杨治立.炼钢厂钢水温降研究现状[J].重庆科技学院学报(自然科学版),2005(4):34-36. [2] 王英哲,冯志太,李开强,江志庚.连铸钢包全过程加盖保温试验[J].炼钢,1994(2):11-15. [3] 李开强,王英哲,徐成锁,冯志太等.钢包全程加盖封闭保温装置[P].中国专利:ZL93228802.2,1994-06-22. [4] 中国矿冶设备网.中钢设备公司引进“钢包全程自动加盖”节能技术[EB/OL].http://www.yjzhan.com.2007-08-02. [5] 李拥军,郝江敏,王洪波,丁继忠.加盖工艺在刑钢80t钢包上的应用[J].河北冶金,2011(2):46-48. [6] 袁方明,杜洋,牛博.高温熔体容器全程自动加盖装置[P].中国专利:ZL200720000491.5, 2008-06-25. [7] 上海国冶工程技术有限公司.钢包加盖[EB/OL].http://www.meccsh.com. 2010-12-01. [8] foxtaillzm.炼钢全程加盖节能系统[EB/OL].http://www.youku.com.2011-01-14 [9] 宝钢工程技术集团有限公司.宝钢工程技术集团研发成功首套钢包加盖系统[EB/OL].http://bsee.baosteel.com.2010-11-12. [10] 中国矿业网.邢钢炼钢大包加盖技术助推精品钢生产[EB/OL].http://www.chinamining.com.cn.2009-10-01. [11] 兰格钢铁.唐钢二钢轧厂钢包周转全程加盖系统正式投入使用[EB/OL].http://www.lgmi.com.2010-7-14 . [12] 杨媛媛.河北钢铁唐钢二钢轧自主研发钢包周转全程加盖装置[EB/OL]. http://www.csteelnews.com. 2010-07-13