PFI汽油机的进气道和燃烧室优化
基于机内净化通用小型汽油机燃烧与排放性能优化

通用小型汽油机近年来在产销应用和出口方面均取得了良好的成绩。
目前来讲,国内通用小型汽油机主要通过机内净化技术来降低排放,但在批量生产时,其排放合格率不尽如人意。
本文通过分析当前基于机内净化通用小型汽油机燃烧与排放性能存在的问题,提出了相应的优化措施。
1 通用小型汽油机机内净化存在的主要问题降低通用小型汽油机的排放污染是汽油机发展的主要问题和难点。
净化方式可分为机内净化和机外净化。
机外净化的成本比较高,国内的技术水平、产品质量尚未达到要求。
因而机内净化是目前国内主要采用的净化手段。
机内净化以汽油机产生主要污染物的形成机理为核心,运用新技术、工艺等对发动机的结构进行改进。
最终达到提高发动机的燃烧效率,降低排放的目的。
目前来讲通用小型汽油机的机内净化主要存在以下问题:(1)通用小型汽油机的进排气系统存在缺陷。
主要是空气滤清器的气体流通性低,对进气形成不良阻力,进而影响整机的燃烧排放性能。
(2)发动机工作的混合气浓度大,过量空气系数有待优化。
传统的化油器式燃油供给方式仍是国内市场的主流。
这种供给方式为了使发动机能够有稳定的、持续的动力输出,方便启动,在混合气浓度通常较浓且在控制方面往往不理想。
(3)点火提前角的选择不当。
点火提前角对汽油机的动力性、经济性以及节能减排都会产生影响。
点火提前角过大,汽油机难以维持稳定运转,产生恶性爆震。
提前角过小会使燃烧不充分,增加HC、co的排放。
因此需要有效合理的调节点火提前角。
2 基于机内净化通用小型汽油机燃烧与排放性能优化措施2.1进排气系统优化改进进排气过程组织对汽油机的燃烧效率有显著影响。
其中最为关键的因素就是气道流通能力。
影响气道流通能力主要存在两方面的阻力,即气道内沿程阻力和局部阻力。
为了减小两种阻力对气道流通性的影响,笔者认为应从以下三个方面进行改进。
第一,改善空气滤清器的结构。
空气流通距离大,会产生较大的沿程阻力,因此可以在不改变进气口数量及口径的情况下,调节进气管的长度进而有效的减少沿程损失。
燃气轮机燃烧室设计与优化技术研究

燃气轮机燃烧室设计与优化技术研究燃气轮机作为一种高效能的发电机组,广泛应用于能源行业。
而燃气轮机的核心部件就是燃烧室,它直接影响轮机的性能和经济效益。
因此,如何设计和优化燃气轮机燃烧室的结构、形状和燃烧过程已成为燃气轮机技术研究的重要方向。
一、燃气轮机燃烧室的基本原理燃气轮机通过将空气进行压缩后喷入燃烧室,再加入燃料进行燃烧,产生高温高压气体,推动涡轮旋转,从而带动发电机发电。
其中,燃烧室作为燃气轮机的关键部件,需要具备以下性能:1.高效能:燃烧室应该尽可能地提高燃料的利用率,使燃烧过程充分进行,同时在燃烧的同时也能够提供足够的热量;2.低排放:燃气轮机的燃烧应该尽可能地减少有害氧化物等排放物的产生,保持环境的卫生和健康;3.高可靠性:燃烧室应该具有抗高温、抗冲击和耐久性等性能,以确保其长期运行的稳定性和安全性。
二、燃气轮机燃烧室设计的基本原则在燃气轮机燃烧室的设计中,需要遵循以下原则:1.保证工作稳定性:燃气轮机燃烧室的设计应考虑到燃料的配比、氧气的供应、排气阻力等,以保证稳定地燃烧,避免反复振荡或失控的情况出现;2.保证安全性:由于燃烧室与其他设备都有着密不可分的联系,其设计中还需考虑到能否预防火灾、爆炸等意外事件的发生;3.保证排放标准:随着环保要求的提高,燃气轮机燃烧室设计还需考虑到排放质量标准,尽量减少对环境的污染。
三、燃气轮机燃烧室设计和优化技术燃气轮机燃烧室设计和优化技术主要针对燃烧室的结构和形状等方面进行优化,以提高燃料的利用率和减少废气排放,同时也需考虑燃烧室的耐久性和可靠性。
1.燃烧室结构优化燃烧室的结构主要涉及到燃料喷嘴、压缩空气喷出口、气体混合器等,针对这些核心部件可以通过增加氧和燃料喷口数量、改变燃料供应的方式和喷出口方向等措施,优化燃烧室结构,提高其燃烧效率和环保性能。
2.燃烧室形状优化通过改变燃烧室形状,如加宽或加深燃烧室,改变燃料喷嘴对燃烧室内部的配比,优化燃烧过程。
PFI汽油机混合气形成的三维数值模拟
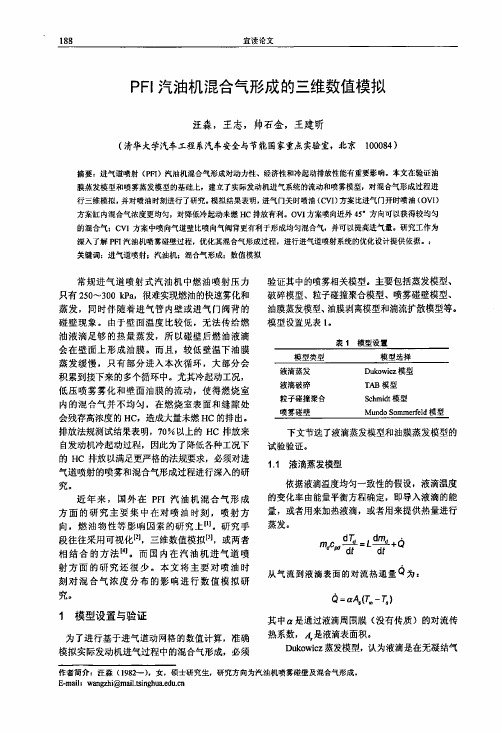
表1模型设置 模型选择
Dukowicz模型 TAB模型 Schmidt模型 Mundo Sommerfeld模型
下文节选了液滴蒸发模型和油膜蒸发模型的 试验验证。
1.1液滴蒸发模型
依据液滴温度均匀一致性的假设.液滴温度 的变化率由能量平衡方程确定,即导入液滴的能 量,或者用来加热液滴,或者用来提供热量进行 蒸发。
计算整个循环,0"CA到720"CA。在计算的 初始20"CA和气门间隙较小的进气上止点处前后 15"CA采用0.1"CA的时间步长,其他时刻则选 择0.5"CA的时间步长。计算机(CPU 3.6 Onz) 求解一个工况约耗时72小时。
3喷油时刻的影响
为了研究喷油时刻的影响,分别模拟进气门 关时喷油(CVI)和进气门开时喷油(OVI)两种 不同的喷油时刻条件。其中,CVI时设置在压缩 上止点时喷油,OVI设置在进气上止点喷油,如 图5所示。喷射方向均是指向气阀背面中心 处。
燃空当量比分布
从图8可以看出: 1)N向、c向和F向的对比代表了喷射方向 远近的影响。从进气门结束时的气阀平面和中间 平面来看,N向时缸内整体较为均匀,在活塞顶 面稍浓;C向时缸内当量比分布不均匀,浓区主 要集中在气缸中下部,另外排气阀下的壁面上还 会形成局部极浓的区域;而F向时更加不均匀, 浓区收缩在气缸的底部中间,浓区核心依然在底 部壁面,比N向时左移,面积进一步扩大。综合 上面的分析可以看出,浓区都会分布在底部壁面, 燃油喷射得越远,在气流的运动下,当量比分布 越不均匀,浓区位置越偏左,浓区面积也会越大。 比较这三种喷射方向,N向时由于当量比分布相 对均匀,较为理想。 2)I向、C向和O向的对比代表了喷射方向 里外的影响。分析进气门结束时气阀平面和中间 平面的当量比分布,可以看出,I向时整体缸内偏 稀,在底面和右侧壁面形成小面积的较浓区域, 摄浓的位置出现在靠近排气阀的壁面上,这对控 制排放不利。O向时前面已有分析,在底部中间 和排气阀下侧形成当量比大于2的浓区。而O向 时整体相对均匀,没有形成当量比大于1的浓区, 是比较理想的喷射方向。无论是I向,还是O向, 在喷雾达到气阀时,气阀已经开启,喷雾主要通 过气阀开启缝隙进入缸内,二次破碎对其混合气 形成起了有利的作用,使得两者的当量比分布都 比C向直接射向气阀要好。
航空发动机的燃烧室流动与燃烧特性优化

航空发动机的燃烧室流动与燃烧特性优化航空发动机作为一种重要的动力装置,在航空航天领域起着至关重要的作用。
而燃烧室作为航空发动机的核心部件,其流动和燃烧特性的优化对于提高发动机的性能和效率具有重要意义。
本文将探讨航空发动机的燃烧室流动与燃烧特性的优化方法和技术。
一、航空发动机燃烧室流动特性的研究与分析燃烧室内气体的流动特性对于燃烧效率和发动机性能的影响不可忽视。
燃烧室内流动的不稳定性和不均匀性会导致燃烧的不完全和功率损失。
因此,研究和分析燃烧室的流动特性对于优化燃烧室设计具有重要意义。
在流动特性的研究中,可以采用数值模拟方法,如计算流体力学(CFD)模拟,来模拟和预测燃烧室内的流动情况。
通过建立准确的数学模型,可以分析燃烧室内的湍流和速度分布等参数,以及分析燃烧室内的湍流能量传递和燃料混合情况。
这有助于了解燃烧室内的流动特性,并根据分析结果对燃烧室进行优化设计。
另外,通过实验手段,如高速摄影和颗粒图像测速(PIV)等技术,也可以对燃烧室的流动特性进行直接观测和测量。
通过实验数据的分析和处理,可以获取燃烧室内的流场信息,揭示流动特性的规律,指导优化燃烧室结构。
二、航空发动机燃烧特性的研究与优化航空发动机的燃烧特性对于其性能和效率具有直接影响。
燃烧效率的提高和污染物的减排是航空发动机燃烧特性优化的主要目标。
在燃烧特性的研究中,首先需要研究燃料在燃烧室内的混合过程。
合理的燃料混合可以提高燃烧效率和燃烧稳定性。
通过数值模拟和实验手段,可以研究燃料在燃烧室内的分布和混合情况,以及燃烧室内的温度和压力分布等参数。
这有助于找出燃料混合的不足之处,并提出相应的优化措施。
其次,燃烧室内的燃烧过程也需要研究和优化。
燃料的燃烧速度、燃烧温度和燃烧稳定性等参数对于燃烧效率和污染物排放有重要影响。
通过数值模拟和实验手段,可以研究燃料的燃烧机理和燃烧过程中的各种化学反应,以及燃烧产物的生成和分布情况。
这有助于优化燃烧室的设计和调整燃烧参数,提高燃烧效率和减少污染物排放。
车辆发动机燃烧优化技术研究

车辆发动机燃烧优化技术研究随着人们对环保和节能的重视,车辆发动机燃烧优化技术逐渐成为汽车工业的热门研究领域。
发动机燃烧优化技术的研究,旨在降低油耗和排放,提高发动机的性能和使用寿命。
一、发动机燃烧原理了解发动机燃烧原理对于研究发动机燃烧优化技术非常重要。
发动机的燃烧是通过燃油和空气的混合来完成的,混合后的燃料被点燃,从而产生气体热能,并推动车辆前进。
在燃烧过程中,燃料和空气的比例以及点火时机等因素会直接影响燃烧效率和排放。
二、发动机燃烧优化技术1. 直喷技术直喷技术是一种在汽车燃油系统中较新的技术,其将燃油直接喷入发动机的燃烧室中,从而降低油耗和减少污染物的排放。
与传统的多点喷射系统相比,直喷技术具有更高的喷射压力和更精准的油气控制,从而提高了燃烧效率和动力性能。
2. 涡轮增压技术涡轮增压技术是一种通过在发动机进气系统中增加压力,从而提高发动机输出功率和燃油经济性的技术。
涡轮增压器通过将排气气流转换成压缩空气,将其送入到发动机的燃烧室中。
这种技术可以提高发动机的效率和动力输出,同时减少燃料的消耗和污染物的排放。
3. 缸内直喷技术缸内直喷技术是一种比较先进的燃烧优化技术,其是在缸内喷射燃油,并结合滚动进气的原理来实现出色的燃烧效果。
与传统的多点喷射技术相比,缸内直喷技术可以减少燃油的喷射量和喷射次数,从而降低了油耗和污染物的排放,同时提高了动力性能和车辆的驾驶舒适度。
4. 智能化控制技术智能化控制技术是将计算机等高科技设备整合到车辆发动机控制系统中,通过实时监测和优化燃烧过程,从而提高发动机燃烧效率和稳定性。
智能化控制技术可以根据行驶环境、驾驶习惯和车辆状态等参数来优化发动机控制参数,从而实现更加优化的燃烧效果。
三、发动机燃烧优化技术前景随着环保和节能的要求越来越高,发动机燃烧优化技术将会得到越来越广泛的应用。
特别是在新能源汽车领域,燃烧优化技术更是不可或缺的一部分。
未来,随着技术的不断升级和成熟,发动机燃烧优化技术将进一步发展,为人们的出行提供更加舒适、节能和环保的选择。
内燃机进气道的优化设计

关于内燃机进气道的优化设计分析热工101班周维顺1001100135摘要:发动机进气道系统的气体流动特性复杂,影响发动机的充气效率和换气损失,对发动机的动力性和经济性有重要的影响。
以A VL—FIRE软件为平台,进而利用CFD技术进行三维稳态CFD分析和优化,研究发动机内的进气道内的气体流动状况是目前的研究热点。
采用合适的湍流模型和计算方法对发动机气道内的三维流场进行数值模拟,得到了不同气门升程下详细的流场信息。
通过流场分析,找到了进气道不合理的部位,提出了进气道改进优化措施,并再次进行了数值模拟计算,并进行优化前后的对比,达到内燃机的优化效果。
关键词:内燃机进气道A VL—FIRE CFD 优化措施仿真(1)我们为什么要对内燃机的气道进行优化这是一个值得深思熟虑的问题。
进气道作为发动机进气系统的重要组成部分,其结构直接影响进入气缸的空气量、气体的速度分布及其湍流状况等,这些因素都直接关系到发动机的燃烧过程,从而影响发动机的经济性、动力性和排放性。
因此,对发动机进气道内气体的流动特性进行分析对了解和研究发动机的工作性能是至关重要的。
传统进气道研发采用经验设计和稳流实验相结合的方法,研制周期长且较难得到理想方案,已不能适应现代高性能发动机研制工作的需要。
在现代发动机的研发中,进气道的设计和进气道一气门一燃烧室的匹配变得十分重要。
为获得良好的混合物质量和高燃烧率,新鲜充量的运动需要合适的宏观和微观结构:宏观结构包括缸内大尺度充气运动,如涡流和滚流;微观结构通常用湍流强度、湍流积分尺度和湍流时间尺度来度量,它们决定了火焰的传播速度。
因此由进气过程产生、在进气门关闭时刻建立的缸内流场结构对着火燃烧前燃烧室内的流场结构具有重要影响,并影响后续的燃烧过程。
在发动机产品的开发阶段,应用CFD 能准确找出气道结构不合理的部位,进行改进优化。
能够有效缩短设计周期,降低设计成本。
所以对内燃机的进气道进行优化是很重要的。
汽油机进气道造型仿真浅析

汽油机进气道造型仿真浅析汽油机进气道的造型设计对发动机性能、燃油经济性等方面有着重要影响,因此对进气道的优化设计十分关键。
传统的进气道设计通常依靠经验和试验方式,但这种方式效率低下、成本高昂。
与此相比,利用计算机辅助仿真技术对进气道进行形状优化设计可以加速设计流程、减少成本、提高设计质量。
本文将针对汽油机进气道造型仿真相关内容进行浅析。
一、进气道的主要作用进气道是发动机吸入空气的通道,其作用主要有以下几个方面:1.削弱气流的涡旋等不稳定性,保持气流稳定。
2.塑造气流,使其更接近理想流体,提高进气量和进气效率。
3.通过变道、弯道、收缩等方式,将气流引导到进气歧管的正确位置。
二、进气道的优化设计汽油机的进气道设计需要从机械结构、气动特性、燃烧特性等方面进行综合考虑。
进气道设计中的主要考虑因素包括以下几个方面:1.形状参数:进气道的形状参数主要包括进气道的长度、收缩比、弯曲角度和弯曲半径等。
2.气体运动特性:气体在进气道内的流动状态包括速度、压力和流向等特性,如进气道内的气体流速分布、流向变化、激波波形等。
3.振动和噪音:进气道中的气流对管壁的作用力会产生振动和噪音,需要进行优化控制。
4.燃烧特性:进气道对涡轮增压系统的效率、燃烧室的燃烧效率都会有影响,需要进行优化设计。
三、进气道的仿真分析进气道的仿真分析一般包括以下几个步骤:1.建立进气道的三维几何模型:通过CAD等软件绘制进气道的三维几何模型。
2.输入边界条件:根据实际情况设置进气道的入口流速、出口压力等边界条件,并选择材料属性和气体状态参数。
3.流体求解:使用CFD软件对进气道中的气体流动进行数值求解,获得速度场、压力场、温度场等结果。
4.结果分析:对流场特性进行结果分析,包括进气量、进气效率、流速分布、压力损失等。
5.优化设计:结合流场分析结果,完成进气道的形状优化设计。
1.减少试错:利用计算机辅助仿真技术可以在短时间内模拟多种设计方案,减少试错环节,提高优化效率。
进气道燃油喷射汽油机稀燃优化技术

f r r o e ne t n mo en me s”n p r wief e n e t n .So x e i n e e u t a n d o wa dan v lijc i d a d a i — o tt c u l jci ” o i o me e p r me td r s lsg ie i - v le e g n r v h tt i e ii ci n mo e c n r d c u lc n u t n b na5 av n ie p o et a h sn w n t d a e u ef e o s mp i y 1 t a h to e o o 7 h n t a f
关 键词 : 油 喷射 方式 ; 部 充 量 分层 ; 混合 气 燃 烧 ; 燃 局 稀 汽油 机
Ke o d F e n to o e Lo a ag taic t n; a r Ga oie yW r s: u 1IjcinM d ; c1 e Ch r eS rt iai Le nBu n; s l f o n
En n gi e
中 图分 类 号 : TK4 3 8 1 . 文献标识码 : A
I 概 述
为满 足更 严 格 的排放 法 规 , 国外 的研 究 重 点定 位 在稀 燃 汽 油 机 , 且 与 汽 油 机 稀 燃 相 匹 配 , 而 已研 制 成 富 氧 型 催 化 器 , 决 了 稀 燃 汽 油 机 的后 顾 之 解
- 1、下载文档前请自行甄别文档内容的完整性,平台不提供额外的编辑、内容补充、找答案等附加服务。
- 2、"仅部分预览"的文档,不可在线预览部分如存在完整性等问题,可反馈申请退款(可完整预览的文档不适用该条件!)。
- 3、如文档侵犯您的权益,请联系客服反馈,我们会尽快为您处理(人工客服工作时间:9:00-18:30)。
本文基于通用解析流体软件 star-cd 对一四缸汽油机进气道和燃烧室进行优化,分析了 不同进气道和燃烧室方案的缸内气流运动,研究了气道和燃烧室的匹配。
1 研究对象
本文的研究对象是一四缸四冲程进气道喷射汽油机,为了满足新一代油耗和排放法规,
对原机进行性能优化。图 1 为该发动机原机的 CAD 模型,发动机参数如表 1 所示。
(3)三个燃烧室方案,滚流比以无挤气方案表现最优;湍流在进气阶段主要受进气道 结构影响,三个方案一样,压缩阶段无挤气方案的湍流最强而且湍流场中心更靠近火花塞。 因此,三个方案中无挤气燃烧室方案与低滚流气道匹配最合理。
参考文献
[1] 周龙保, 刘忠长, 高忠英, 等. 内燃机学[M].机械工业出版社. 2010. 8 [2] John B Heywood. Internal Combustion Engine Fundamental [M]. New York: McGraw-Hill Company. 1988
表 2 计算边界温度(单位:K)
参数名称
参数值
图 2 计算网格模型
进气道壁面温度
303
排气道壁面温度
700
气缸内壁温度
450
汽缸盖表面温度
560
活塞表面温度
560
1.2 边界条件和初始条件 进出口的边界条件由 GT-power 一维循环数值模拟给出,进口为动态流量边界,出口为
STAR 2013 中国用户大会论文集
在汽油机开发过程中,通过气道与燃烧室的合理匹配来组织合适的缸内气体流动,可以 提高发动机的性能,从而满足开发目标。因此由于进气道结构改变,需要重新评估进气道与 燃烧室的匹配,并根据气道结构给出新的燃烧室方案,寻找与低滚流气道匹配的燃烧室方案。
分析原机燃烧室结构发现,原机是四面挤气缸盖,挤区面积较大。挤气面可以在压缩冲 程后期形成挤流运动,以增强燃烧室内的湍流强度,促进混合燃烧。但如果挤气面积过大或 与气道匹配不合理,则会影响进气,减少进气量和降低滚流比。为此在低滚流气道大气门方 案(方案二)的四面挤气缸盖基础上设计了两面挤气和无挤气两种缸盖方案。
STAR 2013 中国用户大会论文集
6000rpm
4400rpm 图 10 平均湍流动能曲线
1200rpm
对于汽油机来说,点火时刻的缸内气体流动状况对发动机点火以及着火后的火焰传播速 度有很大影响,火花塞附近必须有足够的湍动能,才能保证顺利点火。保证缸内有一个合理 的湍动能分布,可以使缸内燃烧更加合理,从而满足发动机性能的需求。图 11 是最大扭矩 点(4400rpm WOT)压缩上止点前 20°CA 时刻的缸内湍动能分布云图。该时刻无挤气燃烧 室方案(方案四)的湍动能最强,其次是四面挤气燃烧室方案(方案二),两面挤气燃烧室 方案(方案三)的湍动能最小。无挤气方案的湍流场中心更靠近火花塞,这有利于保证顺利 点火以及火焰的传播,而另两个方案的湍流场中心偏向进气门侧。
STAR 2013 中国用户大会论文集
4 结论
(1)不管是气门直径、气道结构或是燃烧室结构对高速工况的气流运动影响较小,尤 其是对压缩冲程气流运动的影响不大,对高速工况压缩行程的气流运动占主要作用的是活塞 的高速运动,因此,本文中多个方案高速工况在上止点附近的滚流和湍流都差不多。
(2)低滚流大气门方案相比原机方案,气道流通能力提升,同时由于喉口处结构的变 化,弥补了低滚流气道的滚流削弱,缸内滚流运动与原机方案持平。
2 进气道结构优化
对于汽油机来说,发动机的进气过程很重要,进气过程进入气缸的空气量和气体的速度 分布及其涡流(或滚流)和湍流状况等可以影气体在缸内的流动状况、燃油雾化分布状况及燃 烧状况,从而对发动机的经济性、动力性、排放指标、燃烧噪音和怠速稳定性等产生重要的 影响。一般要求进气道能提供尽可能多的适合强度涡流(或滚流)的新鲜空气。
动态压力边界。气门的开启和关闭由气门升程文件控制,整个模拟过程与发动机的实际工作 状态相同。计算开始时刻的缸内和进排气道内的初始状态数据也由 GT-power 一维循环数值 模拟给出。给定进排气道壁面、气缸内壁面、气缸盖表面温度和活塞表面温度,具体参数值 如表 2 所示,作为缸内工作过程计算的换热边界条件,采用恒温边界,不考虑活塞运动和缸 内燃烧对温度的影响。
图 7 是缸内平均湍动能随曲轴转角的变化曲线。两个方案在不同工况的缸内平均湍动能 差异很小
6000rpm
4400rpm 图 7 不同气道方案平均湍动能对比
1200rpm
总体来说,低滚流大气门方案在提高气道流量系数的前提下,还保证了缸内较高的滚流。
STAR 2013 中国用户大会论文集
3 燃烧室结构优化
1200rpm
图 6 是最大扭矩点几个进气时刻的速度切图,虽然低滚流气道有削弱滚流的作用,但是 喉口处截面积增大导致沿气门前沿进入气缸的气体增加,沿气门后沿进入气缸的气体减少, 从而使得缸内的滚流运动加强。
方 案 一
方 案 二
-270°CA
-210°CA
-150°CA
图 6 不同气道方案 4400rpm 工况的速度切图
表 1 发动机参数表
参数名称/单位 缸径/mm 行程/mm 压缩比 余隙/mm
参数值 73 80 10.5 -0.7
图 1 原机 CAD 模型
1.1 计算网格
计算网格由 star-cd 内燃机专家系统 es-ice 生成,采用 mapping 方法生成高质量、易收 敛计算网格。单元格大小 1.5mm,总网格数 55 万,如图 2 所示。
由于在评价过程中主要评价流动状态的参数,不涉及到燃烧排放,所以计算区间仅包括 进气压缩冲程。计算起始点为进气门开启前 2°CA,由于此发动机有进气 VVT,所以各工况 计算起始时刻不尽相同,计算终止点统一为 40°CA,其中 0°CA 为计算压缩上止点。计算 工况为最大功率点(6000rpm WOT)、最大扭矩点(4400rpm WOT)和冷启动(1200rpm 1barBMEP)。
0 前言
汽油机的缸内气流运动对汽油机的燃烧至关重要,组织合理的缸内气流运动以保证燃烧
的充分有效进行是燃烧室优化的目标。传统的设计方法,即基于宏观概念的经验外推、在台
架上反复调试、对比以及各种参数的半试验分析、试凑等方法,花费大、周期长、适用性小、
效果不明显等问题越来越显著。CFD(Computational Fluid Dynamics)模拟计算辅助发动机设 计能够给设计提供大量的信息,设计开发周期短、花费小、效果显著。
STAR 2013 中国用户大会论文集
PFI 汽油机的进气道和燃烧室优化
武珊,李红洲,段加全,李伟
(中国第一汽车股份有限公司技术中心,长春 130011) (Tel: 0431-85788836, Email: wushan@)
摘要:内燃机缸内气流运动对混合气的形成和燃烧过程有决定性影响,在汽油机开发过程中,通过气道与 燃烧室的合理匹配来组织合适的缸内气体流动,可以提高发动机的性能,从而满足开发目标。在设计阶段, 通过 CFD 的方法,建立缸内流动的三维模型,可以精确的模拟出发动机的进气过程和缸内气体的流动状况, 通过分析缸内速度分布状况以及涡流、滚流和湍动能的分布状况选择出适合的气道和燃烧室。 关键词:CFD, 汽油机,滚流,湍流
进气道性能主要通过进气道流通能力(流量系数)及气体旋流能力(涡流或滚流)来评价。 而滚流比的提高往往是以牺牲流量系数为代价的,在不改变发动机布置方式的情况下很难做 到两者都提升,在工程实践中,如何平衡滚流比和流量系数是气道优化选型的关键。修改气 道喉口处角度(如图 3 所示)得到低滚流气道,牺牲部分气流运动来提升进气道流通能力; 同时增大气道喉口处直径也就是增大气门直径,气门直径由原来的 27mm 增大为 27.5mm。
图 3 气道修改方案
图 4 是所研究的三个工况的缸内充气量对比,原方案命名为方案一,低滚流大气门方案 命名为方案二。可以看出,两个全负荷工况低滚流气道大气门方案(方案二)的充气量比原 机方案有一定提高,有利于保证全负荷工况的功率输出;冷启动工况,两个方案的功率一样, 缸内充气量也就一样。
图 4 不同气道方案充气量对比
6000rpm
4400rpm 图 8 三个燃烧室方案的滚流比曲线
1200rpm
四面挤气-方案二
STAR 2013 中国用户大会论文集
两面挤气-方案三
无挤气-方案四
-240°CA
-120°CA
-20°CA 图 9 6000rpm 的速度切面图
图 9 是最大功率点(6000rpm WOT)几个曲轴转角下通过气门轴线的速度切图,三个方 案的气流运动趋势一致,发展过程也类似;但在压缩上止点附近,无挤气燃烧室的缸内滚流 下降的很快,这说明燃烧室结构对上止点附近时刻的缸内流动还是有比较大的影响。
图 5 是缸内滚流比随曲轴转角的变化曲线。最大功率点两个方案的滚流比在进气阶段略
STAR 2013 中国用户大会论文集
有差异,低滚流大气门方案滚流比更高,压缩阶段两个方案一样;最大扭矩点低滚流大气门 方案的滚流高于原机气道方案;冷启动工况两个方案的滚流比差异很小。
6000rpm
4400rpm 图 5 不同气道方案滚流比对比
低滚流气道+大气门+两面挤气命名为方案三,低滚流气道+大气门+无挤气命名为方案 四。本章节主要讨论进气道与燃烧室的匹配,通过计算分析,选择出适合低滚流气道的燃烧 室方案,因此分析内容主要围绕方案二、方案三和方案四进行。
图 8 是三个燃烧室方案的滚流比对比图,两面挤气方案(方案三)的滚流比最低,四面 挤气方案(方案二)和无挤气方案(方案四)在最大功率和冷启动工况相差不大,最大扭矩 点无挤气方案(方案四)的滚流比有大幅提升。无挤气方案滚流在进气阶段和压缩阶段前期 均高于其它两个方案,但是上止点附近滚流强度下降很快。这是因为相同排量和相同压缩比 条件下,各方案上止点时的容积是相同的。无挤气燃烧室缸盖容积最大,因此活塞凹坑容积 最小,棚顶夹角和活塞顶凹坑直径不变的情况下,缸盖到活塞的距离也最小。随着压缩冲程 活塞的上行,滚流的发展空间越来越小,宏观滚流涡团开始破碎。无挤气燃烧室由于缸盖活 塞距离最小,滚流破碎程度最大,导致压缩后期无挤气方案(方案四)滚流比下降最快。