连杆的机械加工工艺及工装设计
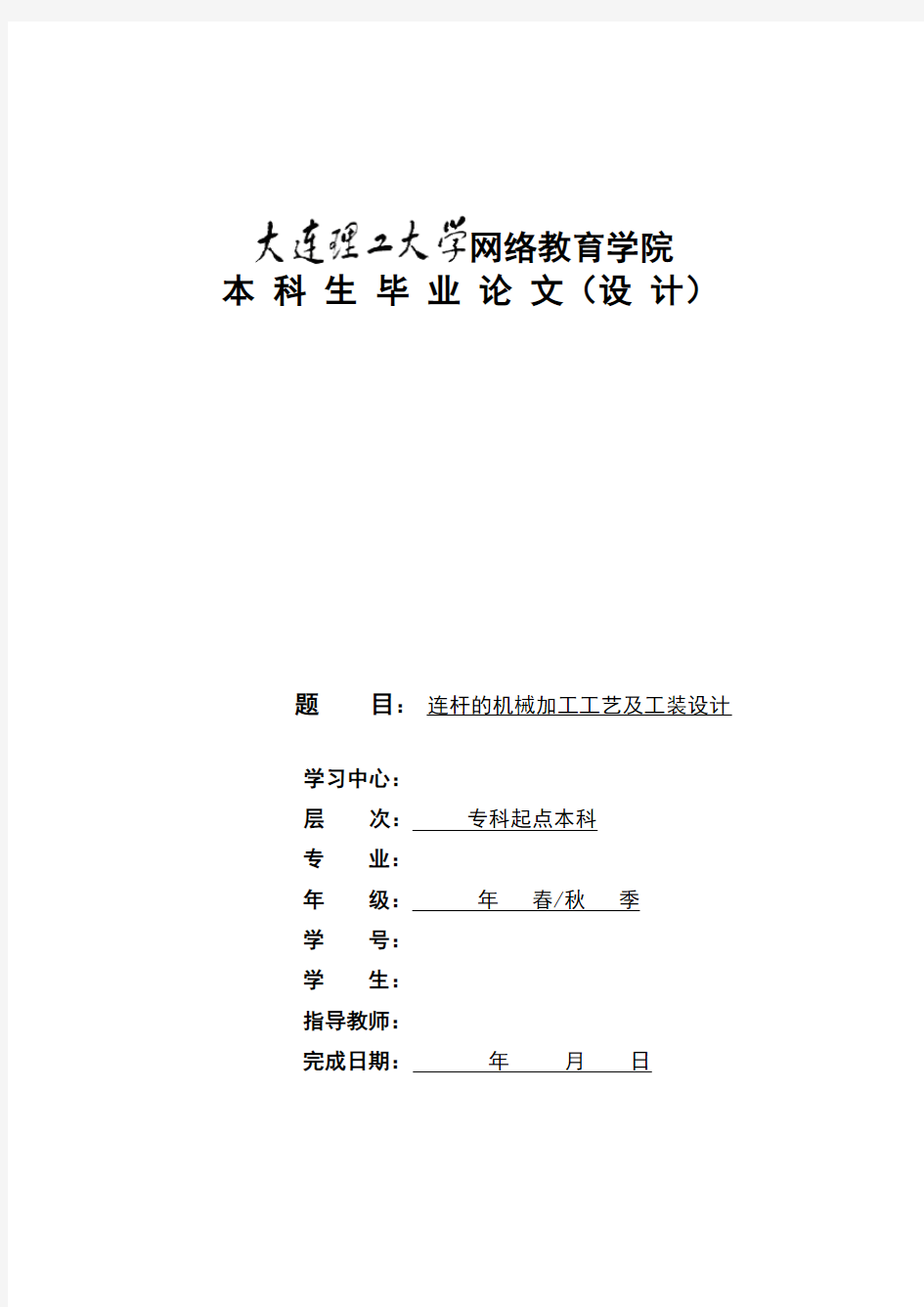
- 1、下载文档前请自行甄别文档内容的完整性,平台不提供额外的编辑、内容补充、找答案等附加服务。
- 2、"仅部分预览"的文档,不可在线预览部分如存在完整性等问题,可反馈申请退款(可完整预览的文档不适用该条件!)。
- 3、如文档侵犯您的权益,请联系客服反馈,我们会尽快为您处理(人工客服工作时间:9:00-18:30)。
网络教育学院
本科生毕业论文(设计)
题目:连杆的机械加工工艺及工装设计
学习中心:
层次:专科起点本科
专业:
年级:年春/秋季
学号:
学生:
指导教师:
完成日期:年月日
内容摘要
在机械制造批量生产中根据加工零件的工艺要求,就需要使用不同的加工方式。本文所要讲的连杆,其在柴油机的传动系统中颇为重要,由于连杆在柴油机中所占的重要地位,其加工的要求也较为精细,就例如在连杆加工中的形状精度以及尺寸精度的要求就很高。连杆在加工过程中,由于其自身的刚度条件较差,故而就可能在加工中产生变形,使零件作废,所以就需要在连杆的加工中将表面的粗加工及精加工分步而行,减小零件变形的可能性。零件加工技术要求的达成不仅仅需要在零件的加工中避免边形,还需要在加工中逐步的去达成加工要求,从而制造出精细标准的连杆零件。
连杆作为汽车发动机中的主要零件,其在柴油机中的作用就是将作用于柴油机活塞头部的力传递给柴油机的曲轴,再通过曲轴所作用的力带动活塞挤压活塞腔内的柴油气,从而不断的重复运动,带来源源不断的动力。而发动机所带来的动力是人们所不可缺少的,所以说,连杆零件在机械制造行业中占有十分重要的地位。
关键词:连杆;加工工艺;工装设计
目录
内容摘要........................................................................................................ I 引言 (1)
1 绪论 (2)
2 工艺规程设计 (3)
2.1年生产量和批量的确定 (3)
2.2零件分析 (3)
2.3 定位基准的分析与选择 (4)
2.3.1 基准的概念 (4)
2.3.2 基准选择原则 (4)
2.3.3 定位基准的选择 (4)
2.4 工艺路线的制定 (4)
2.5 工艺卡的填写 .................................................................. 错误!未定义书签。
3 夹具设计 (6)
3.1 定位基准的选择 (7)
3.2定位元件选择 (7)
3.3 夹紧元件的选择 (8)
3.4夹紧力的计算 (8)
结语 (10)
参考文献 (11)
引言
连杆的组成有连杆体、连杆盖、螺栓以及螺母等零件,作为柴油机的重要零件之一,其形状参数以及尺寸参数都对柴油机的重量及形状尺寸结构等存在着很大的影响。故而,在连杆设计定型后的加工中需要去选择适合的加工工艺及工装设计,从而保证连杆零件的生产质量及效果。连杆在诸多发达国家的生产质量都很高,相对于国内的诸多产品来说非常的领先,除了设备问题及设计问题外大都是由于加工工艺及工装设计间的差距所造成的。本课题就通过对连杆这个零件的研究与了解,对其工艺规程进行了设计,并对夹具也进行了配套设计,从而使得所制造的连杆质量能够更上一层楼。
1 绪论
本次设计主要研究的是连杆工艺以及钻孔夹具。在组合机床的设计中,夹具的设计是其中最为主要的一个部分,而夹具的设计是否合理,是被加工零件精度参数的最直接影响因素。此次设计中,主要针对以往手夹具动夹紧时的夹紧力不同、精度系数低、劳动强度大、误差大等不足进行改进,设计了气动夹紧的夹具,整体思路就是以加工端面作为工件的定位基准,以夹具的大断面孔和凸台作为定位面,以空气作为运行的动力源,具有环保、清洁、干净等优点。
具体设计思路:第一先确定已加工端面的定位方法,然后通过夹具的内孔、凸台,使用设计的气动夹具夹紧,这样可以使六个连杆的活动全部受到限制,从而夹紧零件,然后就可以确定零件的夹紧方法。
2 工艺规程设计
2.1年生产量和批量的确定
1)已知生产纲领:2000件/年,
年生产量=生产纲领⨯每台件数⨯(1+1%储备量)⨯(1+1%废品率)=2000⨯1(单缸柴油机)⨯1.01⨯1.01
=2040件
月产量=年产量/12=170件
日产量=月产量/25.5=6.667 =7件
2)生产类型的确定:
查工艺人员手册,年产量2000件的属于中批生产。
3)批量的确定及生产间隔期
在一个零件总的加工时间及最长工序时间确定的情况下,批量和生产间隔期相互制约,批量越大,生产间隔期越长,生产率高,但资金周转慢,批量越小,生产间隔期短,资金周转快,但生产率低,所以要同时兼顾二者。
批量的确定:
除了要考虑生产间隔期外,还要考虑车间毛坯仓库的面积,如批量大,则占用车间面积过大,资金投入大,周转慢,反之,如批量小,则毛坯的供给满足不了加工需要,则出现停工,以至于设备的闲置,工人的浪费。
考虑到以上的种种因素,定的批量时间为2天。
2.2零件分析
1.零件作用:本零件作为柴油机活塞连杆用。
2.零件材料:本零件材料为HT200。
3.零件热处理要求:由于本零件为铸件,需要进行时效处理。
4.零件技术要求:
本零件需加工的表面为:两端面、大头凸块两侧面、体与盖的结合面、螺栓定位孔面,其中两端面及结合面本身尺寸精度、表面粗糙度有较高要求,而且位置精度也有一定要求。(详细见工件零件图)
5.零件结构特点:由连杆大头、小头及连杆组成。
6.加工出该工件所用的加工方法主要有:平面加工及孔加工。
7.零件设计基准:分析得知,其设计基准是大头孔。
2.3 定位基准的分析与选择
8.在制定零件加工工艺规程时,正确选择定位基准对保证加工表面的尺寸精度和相互位置精度的要求以及合理安排加工顺序都有重要的影响。
2.3.1 基准的概念
基准是机械制造中应用十分广泛的一个概念,机械产品从设计时零件尺寸的标注,制造时工件的定位,校验时尺寸的测量,一直到装配时零部件的的装配位置确定等,都要用到基准的概念。基准就是用来确定生产对象上几何关系所依据的点,线或面。
2.3.2 基准选择原则
在加工起始工序中。只能用毛坯上未曾加工过的表面作为定位基准,则该表面称为粗基准。利用已加工过的表面作为定位基准,则称为精基准。
2.3.3 定位基准的选择
在连杆的加工中,主要定位基准的选择是在小孔进行精铣之后选择小孔以及一个基面作为主要的定位基准,并用大头处指定一侧外表面为另一定位基面。
2.4 工艺路线的制定
(1)两端面的加工
(2)身盖分开面加工
(3)小头孔加工
(4)大头孔加工
其中工艺过程设计大致采用:锻造→调制→粗加工→检验→入库
在生产纲领已经确定为大量生产的条件下,可以考虑采用通用机床配以专用夹具,并尽量使工序集中来提高生产率。除此以外,还应当考虑经济效果,以便使生产成本尽量下降。
2.5 切削用量的确定
正确的对切削用量进行选择,不仅仅能够提高切削效率,还能够保证必要的刀具耐用度和经济性,同时保证加工质量,具有相当重要的作用。
(1)切削深度的选择,在进行加工时的切削深度应根据加工的粗精留下的余量确定。通常希望加工余量不要留得太大,否则,当吃刀深度较大时,切削力增加较为显著,从而就影响加工质量。
(2)进给量的选择,在进行加工时限制进给量提高的主要因素就是表面粗糙度。在进给量增大时,虽有利于断屑,但残留面积的高度会增大,从而导致切削