毕业论文外文文献翻译We-need-strategic-cost-management我们需要战略成本管理
工程造价毕业论文外文文献
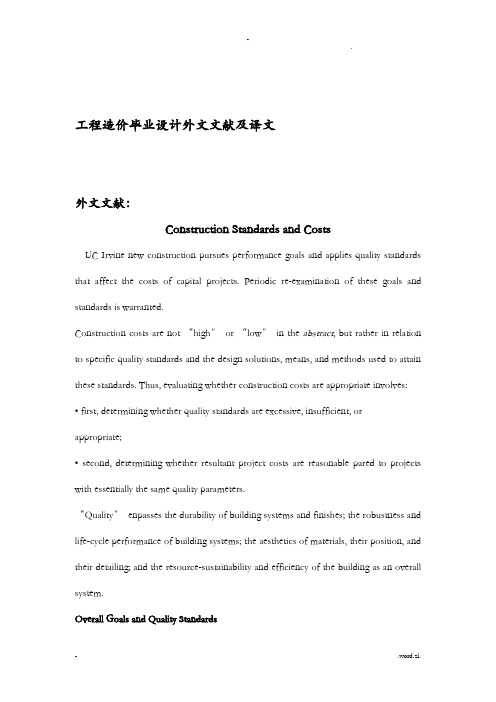
工程造价毕业设计外文文献及译文外文文献:Construction Standards and CostsUC Irvine new construction pursues performance goals and applies quality standards that affect the costs of capital projects. Periodic re-examination of these goals and standards is warranted.Co nstruction costs are not “high〞or “low〞in the abstract, but rather in relation to specific quality standards and the design solutions, means, and methods used to attain these standards. Thus, evaluating whether construction costs are appropriate involves: • first, determining whether quality standards are excessive, insufficient, or appropriate;• second, determining whether resultant project costs are reasonable pared to projects with essentially the same quality parameters.“Quality〞enpasses the durability of building systems and finishes; the robustness and life-cycle performance of building systems; the aesthetics of materials, their position, and their detailing; and the resource-sustainability and efficiency of the building as an overall system.Overall Goals and Quality StandardsUC Irvine, in order to support distinguished research and academic programs, builds facilities of high quality. As such, UC Irvine’s facilities aim to convey the “look and feel,〞as well as embody the inherent construction quality, of the best facilities of other UC campuses, leading public universities, and other research institutions with whom we pete for faculty, students, sponsored research, and general reputation.Since 1992, new buildings have been designed to achieve these five broad goals:1. New bu ildings must “create a place,〞rather than constitute stand-alone structures, forming social, aesthetic, contextually-sensitive relationships with neighboring buildings and the larger campus.2. New buildings reinforce a consistent design framework of classical contextual architecture, applied in ways that convey a feeling of permanence and quality and interpreted in ways that meet the contemporary and changing needs of a modern research university.3. New buildings employ materials, systems, and design features that will avoid the expense of major maintenance (defined as >1 percent of value)for twenty years.4. New buildings apply “sustainability〞principles -- notably, outperforming Title 24 (California’s energy code) by at least 20 percent.5. Capital construction projects are designed and delivered within theapproved project budget, scope, and schedule.UC Irvine’s goals for sustainable materials and energy performance were adopted partly for environmental reasons, and partly to reverse substantial operating budget deficits. The latter problems included a multi-million dollar utilities deficit that was growingrapidly in the early ‘90s, and millions of dollars of unfunded major maintenance that was emerging prematurely in buildings only 10-20 years old. Without the quality and performance standards adopted in 1992, utilities deficits and unfunded major maintenance costs would have exceeded $20 million during the past decade, and these costs would still be rising out-of-control.UC Irvine’s materials standards, building systems standards, sustainability and energy efficiency criteria, and site improvements all add cost increments that can only be afforded through aggressive cost management. Institutions that cannot manage capital costs tend to build projects that consume excessive energy, that cost a lot to maintain, that suffer premature major maintenance costs, and that require high costs to modify. Such problems tend to pound and spiral downward into increasingly costly consequences.Every administrator with facilities experience understands this dynamic. Without effective construction cost management, quality would suffer and UC Irvine would experience all of these problems.The balance of this document outlines in greater detail the building performance criteria and quality standards generally stated above, organized according to building systems ponent classes. Each section discusses key cost-drivers, cost-control strategies, and important cost trade-offs. Design practices cited are consistently applied (although some fall short of hard and fast “rules〞).Building Organization and MassingConstruction cost management starts with the fundamentals of building organization andmassing. UC Irvine’s new structures’ floor plates tend to have length-to-width ratios<1.5, to avoid triggering disproportionate costs of external cladding, circulation, and horizontal mechanical distribution. Our new buildings tend to be at least three floors high -- taller if floor plate areas do not dip below a cost-effective threshold, and generally taller in the case of non-laboratory buildings (but not so tall that a high-rise cost penalty is incurred). Other design ratios are observed, such as exterior cladding area/floor area <0.5, and roof+foundation area/floor area <0.4.Architectural articulation is generally achieved through textured or enriched materials,integral material detailing (such as concrete reveal patterning), and applied detailing (e.g.,2window frames and sills), particularly at the building base. Large-scale articulation is concentrated at the roofline (e.g., shaped roof forms) and at the pedestrian level (e.g.,arcades), where it will “create the biggest bang for the buck,〞rather than through modulating the building form, itself. This is more than a subtle design philosophy, as the cost impact is substantial.Lab buildings pleted in the past decade separate laboratory and non-laboratory functions into distinct, adjoined structures (although such a building may look like one structure). Consolidated non-laboratory functions include faculty, departmental, staff,post-doc, and graduate student offices; restrooms; circulation (elevators, lobbies, primary stairways); classrooms, seminar rooms, conference rooms, and social areas designed tofoster interaction and to provide a safe area for eating and drinking; dry labs and dry lab support functions; and general administrative support.Consolidating these functions into a separate structure provides considerable cost savings:lower-cost HVAC (heating/ventilation/air-conditioning) system, wider column spacing, lower floor stiffness (less stringent vibration criterion), lower floor-loading,fewer fire-control features and other code requirements, steel-framed or steel/concrete hybrid structural system with concrete flat-slab flooring system, smaller footings, and(typically) curtain wall fenestration. This approach usually enables offices to have operable windows.This two-building approach can be seen clearly at Gillespie Neurosciences Building, the Sprague Building, Hewitt Hall, and the UCI Medical Center Health Sciences Laboratory,where consolidating and separating non-laboratory functions saved 7-10 percent in overall construction costs and 15 percent/year in energy expense. (The non-laboratory building incurs a small fraction of the energy expense of the laboratory block.)A set of design strategies, applied in bination, has proven effective in controlling the cost of laboratories:• Utilizing a consistent lab module• Utilizing a reasonable vibration criterion and locating ultra-sensitive conditions at-grade or employing benchtop vibration isolation• Using 22 ft. X 22 ft. column-spacing• Concentrating fume hoods and utility risers into a central “wet zone,〞thus limiting horizontal mechanical distribution• Concentrating laboratory support areas into the central core of a laboratory structure, where utilities are available but daylight is not needed, thus enablinglab structures to be 110-132 feet wide• Utilizing dual-usage circulation/equipment cross-corridors through this central lab support zone, with sufficient width (typically 11 feet) to line the corridors with shared equipment while providing cross-circulation through the lab support zone• Utilizing open laboratory layout with one or more “ghost〞corridors for intra lab circulation• And, most importantly, concentrating non-laboratory functions into an adjoining, lower-cost structure (as discussed in detail above).To further control laboratory construction costs, non-standard fume hood sizes are minimized, “generic〞lab casework is specified, laboratory-grade movable tables substitute for fixed casework in some lab bays, building DI systems provide intermediate water quality (with localized water purity polishing in the lab, rather than building-wide),facility-wide piped services do not include gases that can be cost-effectively provided locally via canisters, and glass-wash facilities are consolidated -- typically, one glass wash facility for an entire laboratory building.Finally, our design philosophy leans toward generic, modular laboratories supported by a robust building infrastructure, rather than highly customized spaces with limited capacity to make later changes. This is an important trade off. Although some post-occupancy expenses may be necessary to “fine-tune〞a laboratory to a PI’s requirements, building infrastructure elements – typically over sized twenty percent, including HVAC supply ducts, exhaust system capacity, emergency generator capacity, and electric risers and service capacity – seldom limit the ability to modify labs to meet researcher needs.Structural and Foundation SystemsFor both cost-benefit reasons and past seismic performance, UC Irvine favors concrete shear wall or steel braced-frame structural systems. The correlating foundation systems depend on site-specific soil conditions. Past problems with undiscovered substrates and uncharacterized soil conditions are minimized through extensive, pre-design soil-testing. This minimizes risk to both the University and the design/build contractor.When feasible, design/build contractors are allowed flexibility to propose alternate structural or seismic-force systems. All structural system designs must pass a peer review, according to Regents’ policy. This process results in conservative structural design, and an associated cost premium. However, the seismic performance of University of California buildings constructed since this policy went into effect in 1975 appears to substantiate the value of the Regents’ Seismic Revi ew Policy.Structural vibration is carefully specified in research buildings where vibration-sensitive protocols and conditions must be maintained on above-grade floors. The most cost effective tools to control vibration are generally employed: first, to program vibration sensitive procedures at on-grade locations or to isolate them at the bench; second, to space columns at a distance that does not entail excessive structural costs. In laboratory 4buildings we typically utilize 22 ft. X 22 ft. column-spacing. Conversely, where vibration is not problematic a beam/column system can be cost-optimized and lighter floor loading can be tolerated. Design/build contractors are, accordingly, allowed more flexibility under such conditions.To control costs, UC Irvine avoids use of moment-resisting structures; unconventionalseismic systems; non-standard structural dimensions; inconsistent, unconventional, or non-stacking structural modules; and non-standard means and methods.Roofs and FlashingsUC Irvine specifies 20 year roofing systems and stainless steel or copper flashings whenever possible. At minimum, we specify hot-dip galvanized flashings.Why this emphasis on flashings? Our roof replacement projects typically double in cost when the old roofing is torn off and it is determined that the flashings have deteriorated. Moreover, many roof leaks of recent years have been due to faulty flashings, rather than roofing membranes or coatings, per se. Saving money on flashings is false economy. Another special roofing expe nse we may have to incur in order to attain the Regents’ Green Building Policy is that of reflective roofing. It is too early to understand the potential cost impact.中文翻译:建立标准和本钱加州大学欧文分校新建筑追求性能目标和适用的质量标准,影响资本本钱的工程。
毕业论文(设计)外文文献翻译及原文
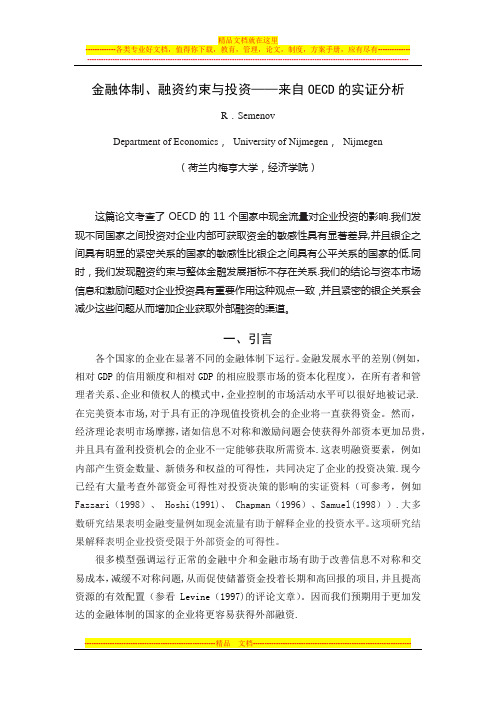
金融体制、融资约束与投资——来自OECD的实证分析R.SemenovDepartment of Economics,University of Nijmegen,Nijmegen(荷兰内梅亨大学,经济学院)这篇论文考查了OECD的11个国家中现金流量对企业投资的影响.我们发现不同国家之间投资对企业内部可获取资金的敏感性具有显著差异,并且银企之间具有明显的紧密关系的国家的敏感性比银企之间具有公平关系的国家的低.同时,我们发现融资约束与整体金融发展指标不存在关系.我们的结论与资本市场信息和激励问题对企业投资具有重要作用这种观点一致,并且紧密的银企关系会减少这些问题从而增加企业获取外部融资的渠道。
一、引言各个国家的企业在显著不同的金融体制下运行。
金融发展水平的差别(例如,相对GDP的信用额度和相对GDP的相应股票市场的资本化程度),在所有者和管理者关系、企业和债权人的模式中,企业控制的市场活动水平可以很好地被记录.在完美资本市场,对于具有正的净现值投资机会的企业将一直获得资金。
然而,经济理论表明市场摩擦,诸如信息不对称和激励问题会使获得外部资本更加昂贵,并且具有盈利投资机会的企业不一定能够获取所需资本.这表明融资要素,例如内部产生资金数量、新债务和权益的可得性,共同决定了企业的投资决策.现今已经有大量考查外部资金可得性对投资决策的影响的实证资料(可参考,例如Fazzari(1998)、 Hoshi(1991)、 Chapman(1996)、Samuel(1998)).大多数研究结果表明金融变量例如现金流量有助于解释企业的投资水平。
这项研究结果解释表明企业投资受限于外部资金的可得性。
很多模型强调运行正常的金融中介和金融市场有助于改善信息不对称和交易成本,减缓不对称问题,从而促使储蓄资金投着长期和高回报的项目,并且提高资源的有效配置(参看Levine(1997)的评论文章)。
因而我们预期用于更加发达的金融体制的国家的企业将更容易获得外部融资.几位学者已经指出建立企业和金融中介机构可进一步缓解金融市场摩擦。
毕业论文外文翻译-施工质量控制、安全和成本控制

工程管理专业毕业外文翻译(房地产)Quality Control 、Safety During Construction andCost ControlQuality and Safety Concerns in ConstructionQuality control and safety represent increasingly important concerns for project managers. Defects or failures in constructed facilities can result in very large costs. Even with minor defects, re-construction may be required and facility operations impaired. Increased costs and delays are the result. In the worse case, failures may cause personal injuries or fatalities. Accidents during the construction process can similarly result in personal injuries and large costs. Indirect costs of insurance, inspection and regulation are increasing rapidly due to these increased direct costs. Good project managers try to ensure that the job is done right the first time and that no major accidents occurs on the project.As with cost control, the most important decisions regarding the quality of a completed facility are made during the design and planning stages rather than during construction. It is during these preliminary stages that component configurations, material specifications and functional performance are decided. Quality control during construction consists largely of insuring conformance to these original design and planning decisions.While conformance to existing design decisions is the primary focus of quality control, these are exceptions to this rule. First, unforeseen circumstances, incorrect design decisions or changes desired by an owner in the facility function may require re-evaluation of design decisions during the course of construction. While these changes may be motivated by the concern for quality, they represent occasions for re-design with all the attendant objectives and constraints. As a second case, some designs rely upon informed and appropriate decision making during the construction process itself. For example, some tunneling methods make decisions about the amount of shoring required at different locations based upon observation of soil conditions during the tunneling process. Since such decisions are based on better information concerning actual site conditions, the facility design may be more cost effective as a result. Any special case of re-design during construction requires the various considerations discussed.With the attention to conformance as the measure of quality during the construction process, the specification of quality requirements in the design and contract documentation becomes extremely important. Quality requirements should be clear and verifiable, so that all parties in the project can understand the requirements for conformance.Safety during the construction project is also influenced in large part by decisions made during the planning and design process. Some designs or construction plans are inherently difficult and dangerous to implement, whereas other, comparable plans may considerably reduce the possibility of accidents. For example, clear separation oftraffic from construction zones during roadway rehabilitation can greatly reduce the possibility of accidental collisions. Beyond these design decisions, safety largely depends upon education, vigilance and cooperation during the construction process. Workers should be constantly alert to the possibilities of accidents and avoid taken unnecessary risks.Total Quality ControlQuality control in construction typically involves insuring compliance with minimum standards of material and workmanship in order to insure the performance of the facility according to the design. These minimum standards are contained in the specifications. For the purpose of insuring compliance, random samples and statistical methods are commonly used as the basis for accepting or rejecting work completed and batches of materials. Rejection of a batch is based on non-conformance or violation of the relevant design specifications.An implicit assumption in these traditional quality control practices is the notion of an acceptable quality level which is a allowable fraction of defective items. Materials obtained from suppliers or work performed by an organization is inspected and passed as acceptable if the estimated defective percentage is within the acceptable quality level. Problems with materials or goods are corrected after delivery of the product.In contrast to this traditional approach of quality control is the goal of total quality control. In this system, no defective items are allowed anywhere in the construction process. While the zero defects goal can never be permanently obtained, it provides a goal so that an organization is never satisfied with its quality control program even if defects are reduced by substantial amounts year after year. This concept and approach to quality control was first developed in manufacturing firms in Japan and Europe , but has since spread to many construction companies.Total quality control is a commitment to quality expressed in all parts of an organization and typically involves many elements. Design reviews to insure safe and effective construction procedures are a major element. Other elements include extensive training for personnel, shifting the responsibility for detecting defects from quality control inspectors to workers, and continually maintaining equipment. Workers involvement in improved quality control is often formalized in quality circles in which groups of workers meet regularly to make suggestions for quality improvement. Material suppliers are also required to insure zero defects in delivered goods. Initially, all materials from a supplier are inspected and batches of goods with any defective items are returned. Suppliers with good records can be certified and not subject to complete inspection subsequently.The traditional microeconomic view of quality control is that there is an “optimum” proportion o f defective items. Trying to achieve greater quality than this optimum would substantially increase costs of inspection and reduce worker productivity. However, many companies have found that commitment to total quality control has substantial economic benefits that had been unappreciated in traditional approaches. Expenses associated with inventory, rework, scrap and warranties were reduced. Worker enthusiasm and commitment improved. Customers often appreciatedhigher quality work and would pay a premium for good quality. As a result, improved quality control became a competitive advantages.Of course, total quality control is difficult to apply, particular in construction. The unique nature of each facility, the variability in the workforce, the multitude of subcontractors and the cost of marking necessary investments in education and procedures make programs of total quality control in construction difficult. Nevertheless, a commitment to improved quality even without endorsing the goal of zero defects can pay real dividends to organizations.SafetyConstruction is a relatively hazardous undertaking. These are significantly more injuries and lost workdays due to injuries or illnesses in construction than in virtually any other industry. These work related injuries and illnesses are exceedingly costly. The Construction Industry Cost Effectiveness Project estimated that accidents cost $8.9 billion or nearly seven percent of the $ 137 billion (in 1979 dollars) spent annually for industrial, utility and commercial construction in the United States. Included in this total are direct costs (medical costs, premiums for workers’ compensation benefits, liability and property losses) as well as indirect costs (reduced worker productivity, delays in projects, administrative time, and damage to equipment and the facility). In contrast to most industrial accidents, innocent bystanders may also be injured by construction have resulted in fatalities to passerby’s. Prudent project managers and owners would like to reduce accidents, injuries and illnesses as much as possible.As with all the other costs of construction, it is a mistake for owners to ignore a significant category of costs such as injury and illness. While contractors may pay insurance premiums directly, these costs are reflected in bid prices or contract amounts. Delays caused by injuries and illnesses can present significant opportunity costs to owners. In the long run, the owners of constructed facilities must pay all the costs of construction. For the case of injuries and illnesses, this general principle might be slightly qualified since significant costs are borne by workers themselves or society at large. However, court judgments and insurance payments compensate for individual losses and ultimately borne by the owners.Various measures are available to improve jobsite safety in construction. Several of the most important occur before construction is undertaken. These include design, choice of technology and education. By altering facility designs, particular structures can be safer or more hazardous to construct. For example, parapets can be designed to appropriate heights for construction worker safety, rather than the minimum height required by building codes.Choice of technology can also be critical in determining the safety of a jobsite. Safeguards built into machinery can notify operators of problems or prevent injuries. For example, simple switches can prevent equipment from being operating when protective shields are not in place. With the availability of on-board electronics (including computer chips) and sensors, the possibilities for sophisticated machine controllers and monitors has greatly expanded for construction equipment and tools. Material and work process choices also influence the safety of construction. Forexample, substitution of alternative material for asbestos can reduce or eliminate the prospects of long term illnesses such as asbestosis.Educating workers and managers in proper procedures and hazards can have a direct impact on jobsite safety. The realization of the large costs involved in construction injuries and illnesses provides a considerable motivation for awareness and education. Regular safety inspections and safety meetings have become standard practices on most job sites.Pre-qualification of contractors and sub-contractors with regard to safety is another important avenue for safety improvement. If contractors are only invited to bid or enter negotiations if they have an acceptable record of safety (as well as quality performance), then a direct incentive is provided to insure adequate safety on the part of contractors.During the construction process itself, the most important safety related measures are to insure vigilance and cooperation on the part of managers, inspectors and workers. Vigilance involves considering the risks of different working practices. In also involves maintaining temporary physical safeguards such as barricaders, braces, guiltiness, railings, toe boards and the like. Sets of standard practices are also important, such as:• requiring hard hats on site.• requiring eye protection on site.• requiring hearing protection near loud equipment.• insuring safety shoes for workers.• providing first-aid supplies and trained personnel on site.While eliminating accidents and work related illnesses is a worthwhile goal, it will never be attained. Construction has a number of characteristics making it inherently hazardous. Large forces are involved in many operations. The jobsite is continually changing as construction proceeds. Workers do not have fixed worksites and must move around a structure under construction. The tenure of a worker on a site is short, so the worker’s familiarity and the employer-employees relationship are less settled than in manufacturing settings. Despite these peculiarities and as a result of exactly these special problems, improving worksite safety is a very important project management concern.A cost control procedure for construction worksIntroductionThe construction industry, unlike many manufacturing situations, is concerned mostly with one-off projects. This naturally creates difficulties for effective management control, because each new contract is often characterized by the following features:• A fresh management team• Labor is transient and recruited on an ad hoc basis•Sites are dispersed through the county, which tends to cause problems in effective communications with other parts of the company•Subcontractors and ‘lump’ labor are common• Added to all this are the ever-changing weather conditionsNevertheless, irrespective of the scale of operation from small sub-contractor to the multifaceted project, production costs need to be monitored and controlled if the anticipated level of profit is to be received.FundamentalsTo control costs is an obvious objective of most managers, but it should be reconciled that no amount of paperwork achieves this control. Ultimately the decision of the manager that something should be done differently, and the translation of that decision into practice, are the actions that achieve control. The paperwork can provide guidance on what control actions should be taken and, while we shall continue to call it ‘the cost control system’. It should more properly be called ‘the cost information system’.The elements of any control system are:• Observation• Comparison of observation with some desired standard• Corrective action to take if necessaryThe domestic thermostat is a good example of a controller. This instrument measures temperature, compares it with the desired range, and then switches the temperature heating system ‘on’or ‘off’depending on how the current temperature compares with the desired range.A cost control system should enable a manager to observe current cost levels, compare them with a standard plan or norm, and institute corrective action to keep cost within acceptable bounds. The system should help to identify where corrective action is necessary and provide pointers as to what that action should be.Unlike the humble thermostat, most cost control systems have an inordinately long response time. Even the best current system provides information on what was happening last week or last month. As the work is typically part of a one-off project it is quite likely that the information is only partly relevant to the work going on now. So the scope for corrective action is limited. For example, the system might indicate on 1 May that the from-work operation in March cost too much. If from-work operations are still continuing the manager will give this work particular attention, but if form-work is complete nothing can be done to correct the situation.In the conventional systems described below two fundamental points are important. First, all costs must be allocated, even if this is on a very ‘coarse grained’coding arrangement. If only the major items are monitored you can be sure that the wasted time will be booked against the items which are not being monitored. Thus the manager will be deluded by the reports on the ‘important items’into thinking the whole site is satisfactory; in fact it might be incurring disastrous hidden losses. Second, there must always be a standard against which to compare recorded costs. In simple projects this might be the bill of quantities; generally, however, a properly prepared and appropriately updated contract budget forms a better basis.Systems in Current UseThe following systems and variants of them are in use in the construction industry. The selection of a system depends in part on the size and complexity of the contract, but more on the attitude and level of sophistication of top management.By overall profit or lossThe contractor waits until the contract is complete and then compares the sums of money that have been paid with the monies incurred in purchasing materials, payments for labor, subcontractors, plant and overheads. The figures are normally extracted from the financial accounts compulsorily kept by all companies. Such a system is useful only on minor contracts of short duration involving a small workforce and little construction equipment. It sacredly qualified as a control system as the information it produces can only be used to avoid the recurrence of gross errors in later contracts.Profit or loss on each contract at valuation datesThe total costs to date are compared with valuations gross of retentions. Care has to be taken to include the cost of materials delivered but not yet invoiced and to exclude materials on site not yet built into the permanent work. If the certificate is not a time reflection of the value of work done, a further adjustment is necessary. This system suffers from the disadvantage that there is no breakdown of the profit figure between types of work; it therefore provides guidance only which contract requires management attention. It is not suitable for contracts, which involve significant set-up costs, which are distributed over the unit rates.Unit costingIn this system costs of various tapes of work, such as mixing and placing concrete, are recorded separately. The costs, both cumulatively and on a period basis, are divided by the quantity of work of each type that has been done. This provides unit costs, which can be compared with those in the tender. Considerable care must be taken to ensure that all costs are accounted for, as indicated above under ‘Fundamentals’. Any miscellaneous costs must be recorded and allowed for in some way, e.g. by proportional distribution over the defined work-types. It is usually best to record site costs only and to compare with bill rates net of contribution for profit and head office overheads.Systems based on the principles of standard costingStandard costing has been used successfully in manufacturing industries, particularly in companies producing a limited range of products or at least a limited range of basic components. Standard minute values are associated with the production of each component and assembly and converted to money values by reference to the hourly rates of the appropriate grades of operatives. Variances are calculated, basically by comparing the value of the output with the cost of producing it. A variance is the amount by which the achieved profit differs from the budgeted profit. With appropriate records it is possible to analyze the total variance into sub-variances, e.g.: • Material price• Material usage• Labor rate• Labor efficiency• Fixed and variable overhead expenditure• V olume of production• SalesStandard costing is seldom directly applicable in construction owing to the variety of the product. This makes the use of standard minute values difficult if not impossible. However, as an alternative, the value of work done can be assessed in relation to the contract budget, which, in turn must reflect the amount that the contractor can expect to be paid.One of the important features is the calculation of a sales variance. This encourages the company to define sales (marketing, public relations, negotiations, estimating and bid strategy) as the responsibility of one department. An adverse variance indicates immediately that the level of acquiring new contracts is inadequate.Altogether, quite substantial departures from the manufacturing system are necessary and this accounts for the fact that standard costing is not in common use in construction. However, the system is basically very sound and provides comprehensive control of the company from boardroom down to workforce.PERT/costThis system requires each contract to be networked with PERT (performance evaluation and review technique). The values of work packages, which in essence are groups of activities, are assessed in advance. The time update of the network provides the value of work done as a ‘by-product’ of the calculation. The value can be divided by cost code, provided that the work package information is similarly divided. Thus, when incurred costs are recorded against the same codes, variances can be calculated for management information.施工质量控制、安全和成本控制施工中的质量和安全问题对项目经理来说,质量控制和安全越来越成为受关注的重要问题。
外文参考文献译文及原文【范本模板】
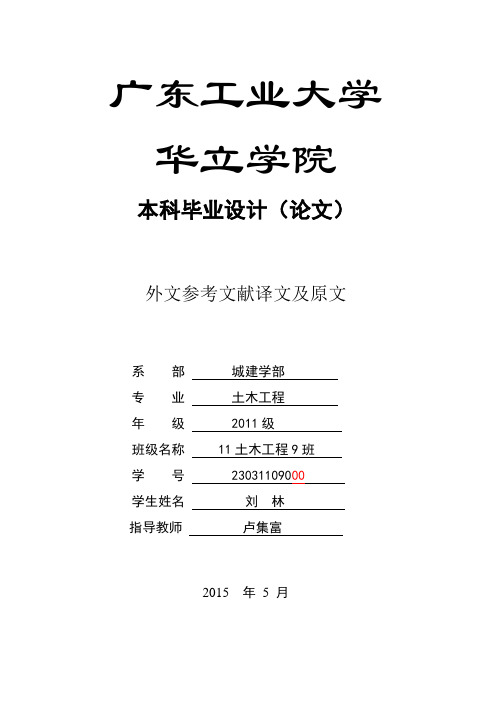
广东工业大学华立学院本科毕业设计(论文)外文参考文献译文及原文系部城建学部专业土木工程年级 2011级班级名称 11土木工程9班学号 23031109000学生姓名刘林指导教师卢集富2015 年5 月目录一、项目成本管理与控制 0二、Project Budget Monitor and Control (1)三、施工阶段承包商在控制施工成本方面所扮演的作用 (2)四、The Contractor’s Role in Building Cost Reduction After Design (4)一、外文文献译文(1)项目成本管理与控制随着市场竞争的激烈性越来越大,在每一个项目中,进行成本控制越发重要。
本文论述了在施工阶段,项目经理如何成功地控制项目预算成本。
本文讨论了很多方法。
它表明,要取得成功,项目经理必须关注这些成功的方法.1。
简介调查显示,大多数项目会碰到超出预算的问……功控制预算成本.2.项目控制和监测的概念和目的Erel and Raz (2000)指出项目控制周期包括测量成……原因以及决定纠偏措施并采取行动。
监控的目的就是纠偏措施的。
.。
标范围内。
3.建立一个有效的控制体系为了实现预算成本的目标,项目管理者需要建立一……被监测和控制是非常有帮助的。
项目成功与良好的沟通密。
决( Diallo and Thuillier, 2005).4.成本费用的检测和控制4.1对检测的优先顺序进行排序在施工阶段,很多施工活动是基于原来的计……用完了。
第四,项目管理者应该检测高风险活动,高风险活动最有。
..重要(Cotterell and Hughes, 1995)。
4.2成本控制的方法一个项目的主要费用包括员工成本、材料成本以及工期延误的成本。
为了控制这些成本费用,项目管理者首先应该建立一个成本控制系统:a)为财务数据的管理和分析工作落实责任人员b)确保按照项目的结构来合理分配所有的……它的变化-—在成本控制线上准确地记录所有恰..。
本科毕业论文内部控制外文文献翻译完整版中英对照

A Clear Look at Internal Controls: Theory and ConceptsHammed Arad (Philae)Department of accounting, Islamic Azad University, Hamadan, IranBarak Jamshedy-NavidFaculty Member of Islamic Azad University, Kerman-shah, IranAbstract: internal control is an accounting procedure or system designed to promote efficiency or assure the implementation of a policy or safeguard assets or avoid fraud and error. Internal Control is a major part of managing an organization. It comprises the plans, methods, and procedures used to meet missions, goals, and objectives and, in doing so, support performance-based management. Internal Control which is equal with management control helps managers achieve desired results through effective stewardship of resources. Internal controls should reduce the risks associated with undetected errors or irregularities, but designing and establishing effective internal controls is not a simple task and cannot be accomplished through a short set of quick fixes. In this paper the concepts of internal controls and different aspects of internal controls are discussed. Keywords: Internal Control, management controls, Control Environment, Control Activities, Monitoring1. IntroductionThe necessity of control in new variable business environment is not latent for any person and management as a response factor for stockholders and another should implement a great control over his/her organization. Control is the activity of managing or exerting control over something. he emergence and development of systematic thoughts in recent decade required a new attention to business resource and control over this wealth. One of the hot topic a bout controls over business resource is analyzing the cost-benefit of each control.Internal Controls serve as the first line of defense in safeguarding assets and preventing and detecting errors and fraud. We can say Internal control is a whole system of controls financial and otherwise, established by the management for the smooth running of business; it includes internal cheek, internal audit and other forms of controls.COSO describe Internal Control as follow. Internal controls are the methods employed to help ensure the achievement of an objective. In accounting and organizational theory, Internal control is defined as a process effected by an organization's structure, work and authority flows, people and management information systems, designed to help the organization accomplish specific goals or objectives. It is a means by which an organization's resources are directed, monitored, and measured. It plays an important role in preventing and detecting fraud and protecting the organization's resources, both physical (e.g., machinery and property) and intangible (e.g., reputation or intellectual property such as trademarks). At the organizational level, internal control objectives relate to the reliability of financial reporting, timely feedback on the achievement of operational or strategic goals, and compliance with laws and regulations. At the specific transaction level, internal control refers to the actions taken to achieve a specific objective (e.g., how to ensure the organization's payments to third parties are for valid services rendered.) Internal controlprocedures reduce process variation, leading to more predictable outcomes. Internal controls within business entities are called also business controls. They are tools used by manager's everyday.* Writing procedures to encourage compliance, locking your office to discourage theft, and reviewing your monthly statement of account to verify transactions are common internal controls employed to achieve specific objectives.All managers use internal controls to help assure that their units operate according to plan, and the methods they use--policies, procedures, organizational design, and physical barriers-constitute. Internal control is a combination of the following:1. Financial controls, and2. Other controlsAccording to the institute of chartered accountants of India internal control is the plan of organization and all the methods and procedures adopted by the management of an entity to assist in achieving management objective of ensuring as far as possible the orderly and efficient conduct of its business including adherence to management policies, the safe guarding of assets prevention and detection of frauds and error the accuracy and completeness of the accounting records and timely preparation of reliable financial information, the system of internal control extends beyond those matters which relate to the function of accounting system. In other words internal control system of controls lay down by the management for the smooth running of the business for the accomplishment of its objects. These controls can be divided in two parts i.e. financial control and other controls.Financial controls:- Controls for recording accounting transactions properly.- Controls for proper safe guarding company assets like cash stock bank debtor etc- Early detection and prevention of errors and frauds.- Properly and timely preparation of financial records I e balance sheet and profit and loss account.- To maximize profit and minimize cost.Other controls: Other controls include the following:Quality controls.Control over raw materials.Control over finished products.Marketing control, etc6. Parties responsible for and affected by internal controlWhile all of an organization's people are an integral part of internal control, certain parties merit special mention. These include management, the board of directors (including the audit commit tee), internal auditors, and external auditors.The primary responsibility for the development and maintenance of internal control rests with an organization's management. With increased significance placed on the control environment, the focus of internal control has changed from policies and procedures to an overriding philosophy and operating style within the organization. Emphasis on these intangible aspects highlights the importance of top management's involvement in the internal control system. If internal control is not a priority for management, then it will not be one for people within the organization either.As an indication of management's responsibility, top management at a publicly owned organization will include in the organization's annual financial report to the shareholders a statement indicating that management has established a system of internal control that management believes is effective. The statement may also provide specific details about the organization's internal control system.Internal control must be evaluated in order to provide management with some assurance regarding its effectiveness. Internal control evaluation involves everything management does to control the organization in the effort to achieve its objectives. Internal control would be judged as effective if its components are present and function effectively for operations, financial reporting, and compliance. he boards of directors and its audit committee have responsibility for making sure the internal control system within the organization is adequate. This responsibility includes determining the extent to which internal controls are evaluated. Two parties involved in the evaluation of internal control are the organization's internal auditors and their external auditors.Internal auditors' responsibilities typically include ensuring the adequacy of the system of internal control, the reliability of data, and the efficient use of the organization's resources. Internal auditors identify control problems and develop solutions for improving and strengthening internal controls. Internal auditors are concerned with the entire range of an organization's internal controls, including operational, financial, and compliance controls.Internal control will also be evaluated by the external auditors. External auditors assess the effectiveness of internal control within an organization to plan the financial statement audit. In contrast to internal auditors, external auditors focus primarily on controls that affect financial reporting. External auditors have a responsibility to report internal control weaknesses (as well as reportable conditions about internal control) to the audit committee of the board of directors.8. Limitations of an Entity's Internal ControlInternal control, no matter how well designed and operated, can provide only reasonable assurance of achieving an entity's control objectives. The likelihood of achievement is affected by limitations inherent to internal control. These include the realities that human judgment in decision-making can be faulty and that breakdowns in internal control can occur because of human failures such as simple errors or mistakes. For example, errors may occur in designing,Maintaining, or monitoring automated controls. If an entity’s IT personnel do not completely understand how an order entry system processes sales transactions, they may erroneously design changes to the system to process sales for a new line of products. On the other hand, such changes may be correctly designed but misunderstood by individuals who translate the design into program code. Errors also may occur in the use of information produced by IT. For example, automated controls may be designed to report transactions over a specified dollar limit for management review, but individuals responsible for conducting the review may not understand the purpose of such reports and, accordingly, may fail to review them or investigate unusual items.Additionally, controls, whether manual or automated, can be circumvented by the collusion of two or more people or inappropriate management override of internal control. For example, management may enter into side agreements with customers that alter the terms and conditions of the entity’s standard sales con tract in ways that would preclude revenuerecognition. Also, edit routines in a software program that are designed to identify and report transactions that exceed specified credit limits may be overridden or disabled.Internal control is influenced by the quantitative and qualitative estimates and judgments made by management in evaluating the cost-benefit relationship of an entity’s internal control. The cost of an entity's internal control should not exceed the benefits that are expected to be derived. Although the cost-benefit relationship is a primary criterion that should be considered in designing internal control, the precise measurement of costs and benefits usually is not possible.Custom, culture, and the corporate governance system may inhibit fraud, but they are not absolute deterrents. An effective control environment, too, may help reduce the risk of fraud. For example, an effective board of directors, audit committee, and internal audit function may constrain improper conduct by management. Alternatively, the control environment may reduce the effectiveness of other components. For example, when the nature of management incentives increases the risk of material misstatement of financial statements, the effectiveness of control activities may be reduced.9. Balancing Risk and ControlRisk is the probability that an event or action will adversely affect the organization. The primary categories of risk are errors, omissions, delay and fraud In order to achieve goals and objectives, management needs to effectively balance risks and controls. Therefore, control procedures need to be developed so that they decrease risk to a level where management can accept the exposure to that risk. By performing this balancing act "reasonable assurance” can be attained. As it relates to financial and compliance goals, being out of balance can causebe proactive, value-added, and cost-effective and address exposure to risk.11. ConclusionThe concept of internal control and its aspects in any organization is so important, therefore understanding the components and standards of internal controls should be attend by management. Internal Control is a major part of managing an organization. Internal control is an accounting procedure or system designed to promote efficiency or assure the implementation of a policy or safeguard assets or avoid fraud and error. According to custom definition, Internal Control is a process affected by an entity's board of directors, management and other personnel designed to provide reasonable assurance regarding the achievement of objectives in the following categories namely. The major factors of internal control are Control environment, Risk assessment, Control activities, Information and communication, Monitoring. This article reviews the main standards and principles of internal control and described the relevant concepts of internal control for all type of company.内部控制透视:理论与概念哈米德阿拉德(Philae)会计系,伊斯兰阿扎德大学,哈马丹,伊朗巴克Joshed -纳维德哈尼学院会员伊斯兰阿扎德大学,克尔曼伊朗国王,伊朗摘要:内部控制是会计程序或控制系统,旨在促进效率或保证一个执行政策或保护资产或避免欺诈和错误。
成本管理国内外文献综述
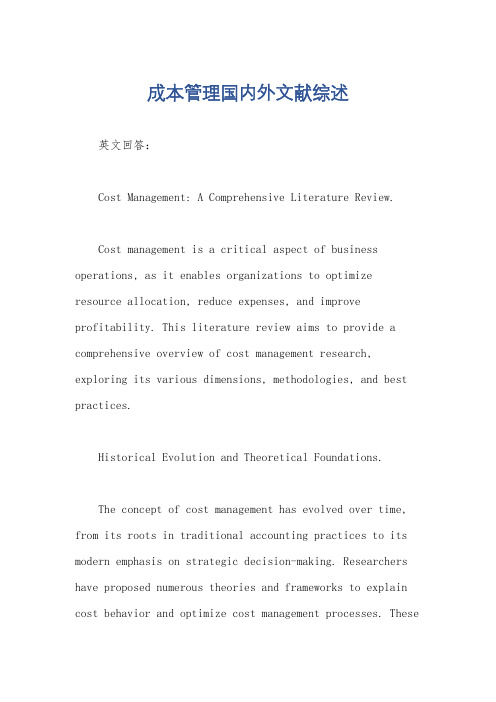
成本管理国内外文献综述英文回答:Cost Management: A Comprehensive Literature Review.Cost management is a critical aspect of business operations, as it enables organizations to optimize resource allocation, reduce expenses, and improve profitability. This literature review aims to provide a comprehensive overview of cost management research, exploring its various dimensions, methodologies, and best practices.Historical Evolution and Theoretical Foundations.The concept of cost management has evolved over time, from its roots in traditional accounting practices to its modern emphasis on strategic decision-making. Researchers have proposed numerous theories and frameworks to explain cost behavior and optimize cost management processes. Theseinclude activity-based costing (ABC), target costing, and value-based costing (VBC).Cost Classification and Estimation Techniques.Cost management requires a comprehensive understanding of cost classification systems and estimation techniques. Direct costs are directly attributable to specific products or services, while indirect costs are shared acrossmultiple activities. Estimation methods, such as time and motion studies, parametric modeling, and simulation, provide reliable estimates for various cost elements.Cost Reduction and Optimization Strategies.Organizations employ various strategies to reduce costs and optimize their operations. Value analysis, process mapping, and lean manufacturing principles help identify and eliminate waste and improve efficiency. Cost-benefit analysis and risk management techniques assess thepotential outcomes of cost-saving initiatives.Technology and Cost Management.Technological advancements have significantly influenced cost management practices. Enterprise resource planning (ERP) systems provide real-time data and analytics for better cost monitoring and decision-making. Cloud computing and machine learning algorithms automate cost analysis and forecasting tasks.International Perspectives on Cost Management.Cost management practices vary across countries due to differences in economic, regulatory, and cultural factors. International organizations face challenges in applying uniform cost management standards and achieving cost synergies across their global operations.Emerging Trends and Future Directions.Current trends in cost management include a focus on sustainability, digital transformation, and data-driven decision-making. Researchers are exploring the use ofartificial intelligence (AI) and blockchain technology to enhance cost management capabilities.中文回答:成本管理综述。
毕设外文文献+翻译1
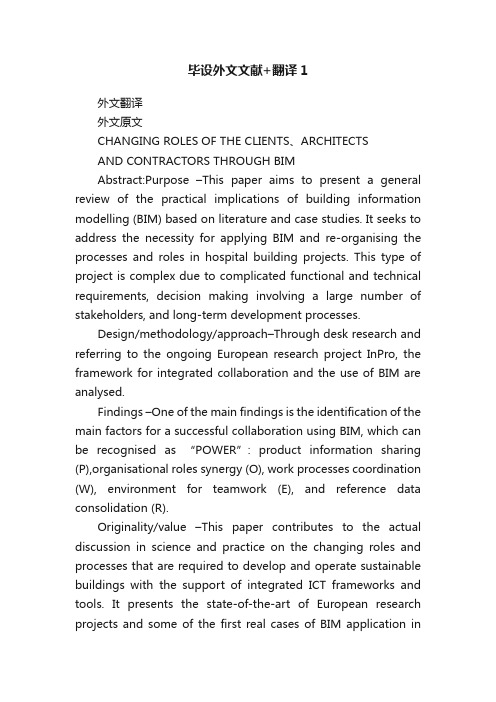
毕设外文文献+翻译1外文翻译外文原文CHANGING ROLES OF THE CLIENTS、ARCHITECTSAND CONTRACTORS THROUGH BIMAbstract:Purpose –This paper aims to present a general review of the practical implications of building information modelling (BIM) based on literature and case studies. It seeks to address the necessity for applying BIM and re-organising the processes and roles in hospital building projects. This type of project is complex due to complicated functional and technical requirements, decision making involving a large number of stakeholders, and long-term development processes.Design/methodology/approach–Through desk research and referring to the ongoing European research project InPro, the framework for integrated collaboration and the use of BIM are analysed.Findings –One of the main findings is the identification of the main factors for a successful collaboration using BIM, which can be recognised as “POWER”: product information sharing (P),organisational roles synergy (O), work processes coordination (W), environment for teamwork (E), and reference data consolidation (R).Originality/value –This paper contributes to the actual discussion in science and practice on the changing roles and processes that are required to develop and operate sustainable buildings with the support of integrated ICT frameworks and tools. It presents the state-of-the-art of European research projects and some of the first real cases of BIM application inhospital building projects.Keywords:Europe, Hospitals, The Netherlands, Construction works, Response flexibility, Project planningPaper type :General review1. IntroductionHospital building projects, are of key importance, and involve significant investment, and usually take a long-term development period. Hospital building projects are also very complex due to the complicated requirements regarding hygiene, safety, special equipments, and handling of a large amount of data. The building process is very dynamic and comprises iterative phases and intermediate changes. Many actors with shifting agendas, roles and responsibilities are actively involved, such as: the healthcare institutions, national and local governments, project developers, financial institutions, architects, contractors, advisors, facility managers, and equipment manufacturers and suppliers. Such building projects are very much influenced, by the healthcare policy, which changes rapidly in response to the medical, societal and technological developments, and varies greatly between countries (World Health Organization, 2000). In The Netherlands, for example, the way a building project in the healthcare sector is organised is undergoing a major reform due to a fundamental change in the Dutch health policy that was introduced in 2008.The rapidly changing context posts a need for a building with flexibility over its lifecycle. In order to incorporate life-cycle considerations in the building design, construction technique, and facility management strategy, a multidisciplinary collaboration is required. Despite the attempt for establishing integrated collaboration, healthcare building projects still facesserious problems in practice, such as: budget overrun, delay, and sub-optimal quality in terms of flexibility, end-user?s dissatisfaction, and energy inefficiency. It is evident that the lack of communication and coordination between the actors involved in the different phases of a building project is among the most important reasons behind these problems. The communication between different stakeholders becomes critical, as each stakeholder possesses different setof skills. As a result, the processes for extraction, interpretation, and communication of complex design information from drawings and documents are often time-consuming and difficult. Advanced visualisation technologies, like 4D planning have tremendous potential to increase the communication efficiency and interpretation ability of the project team members. However, their use as an effective communication tool is still limited and not fully explored. There are also other barriers in the information transfer and integration, for instance: many existing ICT systems do not support the openness of the data and structure that is prerequisite for an effective collaboration between different building actors or disciplines.Building information modelling (BIM) offers an integrated solution to the previously mentioned problems. Therefore, BIM is increasingly used as an ICT support in complex building projects. An effective multidisciplinary collaboration supported by an optimal use of BIM require changing roles of the clients, architects, and contractors; new contractual relationships; and re-organised collaborative processes. Unfortunately, there are still gaps in the practical knowledge on how to manage the building actors to collaborate effectively in their changing roles, and todevelop and utilise BIM as an optimal ICT support of the collaboration.This paper presents a general review of the practical implications of building information modelling (BIM) based on literature review and case studies. In the next sections, based on literature and recent findings from European research project InPro, the framework for integrated collaboration and the use of BIM are analysed. Subsequently, through the observation of two ongoing pilot projects in The Netherlands, the changing roles of clients, architects, and contractors through BIM application are investigated. In conclusion, the critical success factors as well as the main barriers of a successful integrated collaboration using BIM are identified.2. Changing roles through integrated collaboration and life-cycle design approachesA hospital building project involves various actors, roles, and knowledge domains. In The Netherlands, the changing roles of clients, architects, and contractors in hospital building projects are inevitable due the new healthcare policy. Previously under the Healthcare Institutions Act (WTZi), healthcare institutions were required to obtain both a license and a building permit for new construction projects and major renovations. The permit was issued by the Dutch Ministry of Health. The healthcare institutions were then eligible to receive financial support from the government. Since 2008, new legislation on the management of hospital building projects and real estate has come into force. In this new legislation, a permit for hospital building project under the WTZi is no longer obligatory, nor obtainable (Dutch Ministry of Health, Welfare and Sport, 2008). This change allows more freedom from the state-directed policy, and respectively,allocates more responsibilities to the healthcare organisations to deal with the financing and management of their real estate. The new policy implies that the healthcare institutions are fully responsible to man age and finance their building projects and real estate. The government?s support for the costs of healthcare facilities will no longer be given separately, but will be included in the fee for healthcare services. This means that healthcare institutions must earn back their investment on real estate through their services. This new policy intends to stimulate sustainable innovations in the design, procurement and management of healthcare buildings, which will contribute to effective and efficient primary healthcare services.The new strategy for building projects and real estate management endorses an integrated collaboration approach. In order to assure the sustainability during construction, use, and maintenance, the end-users, facility managers, contractors and specialist contractors need to be involved in the planning and design processes. The implications of the new strategy are reflected in the changing roles of the building actors and in the new procurement method.In the traditional procurement method, the design, and its details, are developed by the architect, and design engineers. Then, the client (the healthcare institution) sends an application to the Ministry of Healthto obtain an approval on the building permit and the financial support from the government. Following this, a contractor is selected through a tender process that emphasises the search for the lowest-price bidder. During the construction period, changes often take place due to constructability problems of the design and new requirements from the client.Because of the high level of technical complexity, and moreover, decision-making complexities, the whole process from initiation until delivery of a hospital building project can take up to ten years time. After the delivery, the healthcare institution is fully in charge of the operation of the facilities. Redesigns and changes also take place in the use phase to cope with new functions and developments in the medical world.The integrated procurement pictures a new contractual relationship between the parties involved in a building project. Instead of a relationship between the client and architect for design, and the client and contractor for construction, in an integrated procurement the client only holds a contractual relationship with the main party that is responsible for both design and construction. The traditional borders between tasks and occupational groups become blurred since architects, consulting firms, contractors, subcontractors, and suppliers all stand on the supply side in the building process while the client on the demand side. Such configuration puts the architect, engineer and contractor in a very different position that influences not only their roles, but also their responsibilities, tasks and communication with the client, the users, the team and other stakeholders.The transition from traditional to integrated procurement method requires a shift of mindset of the parties on both the demand and supply sides. It is essential for the client and contractor to have a fair and open collaboration in which both can optimally use their competencies. The effectiveness of integrated collaboration is also determined by the client?s capacity and strategy to organize innovative tendering procedures.A new challenge emerges in case of positioning an architect in a partnership with the contractor instead of with the client. In case of the architect enters a partnership with the contractor, an important issues is how to ensure the realisation of the architectural values as well as innovative engineering through an efficient construction process. In another case, the architect can stand at the client?s side in a strategic advisory role instead of being the designer. In this case, the architect?s responsibility is translating client?s requirements and wishes into the architectural values to be included in the design specification, and evaluating the contractor?s proposal against this. In any of this new role, the architect holds the responsibilities as stakeholder interest facilitator, custodian of customer value and custodian of design models.The transition from traditional to integrated procurement method also brings consequences in the payment schemes. In the traditional building process, the honorarium for the architect is usually based on a percentage of the project costs; this may simply mean that the more expensive the building is, the higher the honorarium will be. The engineer receives the honorarium based on the complexity of the design and the intensity of the assignment. A highly complex building, which takes a number of redesigns, is usually favourable for the engineers in terms of honorarium. A traditional contractor usually receives the commission based on the tender to construct the building at the lowest price by meeting the minimum specifications given by the client. Extra work due to modifications is charged separately to the client. After the delivery, the contractor is no longer responsible for the long-term use of the building. In the traditional procurement method, all risks are placed with theclient.In integrated procurement method, the payment is based on the achieved building performance; thus, the payment is non-adversarial. Since the architect, engineer and contractor have a wider responsibility on the quality of the design and the building, the payment is linked to a measurement system of the functional and technical performance of the building over a certain period of time. The honorarium becomes an incentive to achieve the optimal quality. If the building actors succeed to deliver a higher added-value thatexceed the minimum client?s requirements, they will receive a bonus in accordance to the client?s extra gain. The level of transparency is also improved. Open book accounting is an excellent instrument provided that the stakeholders agree on the information to be shared and to its level of detail (InPro, 2009).Next to the adoption of integrated procurement method, the new real estate strategy for hospital building projects addresses an innovative product development and life-cycle design approaches. A sustainable business case for the investment and exploitation of hospital buildings relies on dynamic life-cycle management that includes considerations and analysis of the market development over time next to the building life-cycle costs (investment/initial cost, operational cost, and logistic cost). Compared to the conventional life-cycle costing method, the dynamic life-cycle management encompasses a shift from focusing only on minimizing the costs to focusing on maximizing the total benefit that can be gained. One of the determining factors for a successful implementation of dynamic life-cycle management is the sustainable design of the building and building components, which means that the design carriessufficient flexibility to accommodate possible changes in the long term (Prins, 1992).Designing based on the principles of life-cycle management affects the role of the architect, as he needs to be well informed about the usage scenarios and related financial arrangements, the changing social and physical environments, and new technologies. Design needs to integrate people activities and business strategies over time. In this context, the architect is required to align the design strategies with the organisational, local and global policies on finance, business operations, health and safety, environment, etc.The combination of process and product innovation, and the changing roles of the building actors can be accommodated by integrated project delivery or IPD (AIA California Council, 2007). IPD is an approach that integrates people, systems, business structures and practices into a process that collaboratively harnesses the talents and insights of all participants to reduce waste and optimize efficiency through all phases of design, fabrication and construction. IPD principles can be applied to a variety of contractual arrangements. IPD teams will usually include members well beyond the basic triad of client, architect, and contractor. At a minimum, though, an Integrated Project should include a tight collaboration between the client, the architect, and the main contractor ultimately responsible for construction of the project, from the early design until the project handover. The key to a successful IPD is assembling a team that is committed to collaborative processes and is capable of working together effectively. IPD is built on collaboration. As a result, it can only be successful if the participants share and apply common values and goals.3. Changing roles through BIM applicationBuilding information model (BIM) comprises ICT frameworks and tools that can support the integrated collaboration based on life-cycle design approach. BIM is a digital representation of physical and functional characteristics of a facility. As such it serves as a shared knowledge resource for information about a facility forming a reliable basis for decisions during its lifecycle from inception onward (National Institute of Building Sciences NIBS, 2007). BIM facilitates time and place independent collaborative working. A basic premise of BIM is collaboration by different stakeholders at different phases of the life cycle of a facility to insert, extract, update or modify information in the BIM to support and reflect the roles of that stakeholder. BIM in its ultimate form, as a shared digital representation founded on open standards for interoperability, can become a virtual information model to be handed from the design team to the contractor and subcontractors and then to the client.BIM is not the same as the earlier known computer aided design (CAD). BIM goes further than an application to generate digital (2D or 3D) drawings. BIM is an integrated model in which all process and product information is combined, stored, elaborated, and interactively distributed to all relevant building actors. As a central model for all involved actors throughout the project lifecycle, BIM develops andevolves as the project progresses. Using BIM, the proposed design and engineering solutions can be measured against the client?s requirements and expected building performance. The functionalities of BIM to support the design process extend to multidimensional (nD), including: three-dimensional visualisation and detailing, clash detection, material schedule, planning, costestimate, production and logistic information, and as-built documents. During the construction process, BIM can support the communication between the building site, the factory and the design office– which is crucial for an effective and efficient prefabrication and assembly processes as well as to prevent or solve problems related to unforeseen errors or modifications. When the building is in use, BIM can be used in combination with the intelligent building systems to provide and maintain up-to-date information of the building performance, including the life-cycle cost.To unleash the full potential of more efficient information exchange in the AEC/FM industry in collaborative working using BIM, both high quality open international standards and high quality implementations of these standards must be in place. The IFC open standard is generally agreed to be of high quality and is widely implemented in software. Unfortunately, the certification process allows poor quality implementations to be certified and essentially renders the certified software useless for any practical usage with IFC. IFC compliant BIM is actually used less than manual drafting for architects and contractors, and show about the same usage for engineers. A recent survey shows that CAD (as a closed-system) is still the major form of technique used in design work (over 60 per cent) while BIM is used in around 20 percent of projects for architects and in around 10 per cent of projects for engineers and contractors.The application of BIM to support an optimal cross-disciplinary and cross-phase collaboration opens a new dimension in the roles and relationships between the building actors. Several most relevant issues are: the new role of a model manager; the agreement on the access right and IntellectualProperty Right (IPR); the liability and payment arrangement according to the type of contract and in relation to the integrated procurement; and the use of open international standards.Collaborative working using BIM demands a new expert role of a model manager who possesses ICT as well as construction process know-how (InPro, 2009). The model manager deals with the system as well as with the actors. He provides and maintains technological solutions required for BIM functionalities, manages the information flow, and improves the ICT skills of the stakeholders. The model manager does not take decisions on design and engineering solutions, nor the organisational processes, but his roles in the chain of decision making are focused on:the development of BIM, the definition of the structure and detail level of the model, and the deployment of relevant BIM tools, such as for models checking, merging, and clash detections;the contribution to collaboration methods, especially decision making and communication protocols, task planning, and risk management;and the management of information, in terms of data flow and storage, identification of communication errors, and decision or process (re-)tracking.Regarding the legal and organisational issues, one of the actual questions is: “In what way does the intellectual property right (IPR) in collaborative working using BIM differ from the IPR in a traditional teamwork?”. In terms of combine d work, the IPR of each element is at tached to its creator. Although it seems to be a fully integrated design, BIM actually resulted from a combination of works/elements; for instance: the outline of the building design, is created by the architect, the design for theelectrical system, is created by the electrical contractor, etc. Thus, in case of BIM as a combined work, the IPR is similar to traditional teamwork. Working with BIM with authorship registration functionalities may actually make it easier to keep track of the IPR.How does collaborative working, using BIM, effect the contractual relationship? On the one hand,collaborative working using BIM does not necessarily change the liability position in the contract nor does it obligate an alliance contract. The General Principles of BIM A ddendum confirms: …This does not effectuate or require a restructuring of contractual relationships or shifting of risks between or among the Project Participants other than as specifically required per the Protocol Addendum and its Attachments? (ConsensusDOCS, 2008). On the other hand, changes in terms of payment schemes can be anticipated. Collaborative processes using BIM will lead to the shifting of activities from to the early design phase. Much, if not all, activities in the detailed engineering and specification phase will be done in the earlier phases. It means that significant payment for the engineering phase, which may count up to 40 per cent of the design cost, can no longer be expected. As engineering work is done concurrently with the design, a new proportion of the payment in the early design phase is necessary.4. Review of ongoing hospital building projects using BIMIn The Netherlands, the changing roles in hospital building projects are part of the strategy, which aims at achieving a sustainable real estate in response to the changing healthcare policy. Referring to literature and previous research, the main factors that influence the success of the changing roles can be concluded as: the implementation of an integrated procurementmethod and a life-cycle design approach for a sustainable collaborative process; the agreement on the BIM structure and the intellectual rights; and the integration of the role of a model manager. The preceding sections have discussed the conceptual thinking on how to deal with these factors effectively. This current section observes two actual projects and compares the actual practice with the conceptual view respectively.The main issues, which are observed in the case studies, are: the selected procurement method and the roles of the involved parties within this method;the implementation of the life-cycle design approach;the type, structure, and functionalities of BIM used in the project;the openness in data sharing and transfer of the model, and the intended use of BIM in the future; and the roles and tasks of the model manager.The pilot experience of hospital building projects using BIM in the Netherlands can be observed at University Medical Centre St Radboud (further referred as UMC) and Maxima Medical Centre (further referred as MMC). At UMC, the new building project for the Faculty of Dentistry in the city of Nijmegen has been dedicated as a BIM pilot project. At MMC, BIM is used in designing new buildings for Medical Simulation and Mother-and-Child Centre in the city of Veldhoven.The first case is a project at the University Medical Centre (UMC) St Radboud. UMC is more than just a hospital. UMC combines medical services, education and research. More than 8500 staff and 3000 students work at UMC. As a part of the innovative real estate strategy, UMC has considered to use BIM for its building projects. The new development of the Faculty ofDentistry and the surrounding buildings on the Kapittelweg in Nijmegen has been chosen as a pilot project to gather practical knowledge and experience on collaborative processes with BIM support.The main ambition to be achieved through the use of BIM in the building projects at UMC can be summarised as follows: using 3D visualisation to enhance the coordination and communication among the building actors, and the user participation in design;integrating the architectural design with structural analysis, energy analysis, cost estimation, and planning;interactively evaluating the design solutions against the programme of requirements and specifications;reducing redesign/remake costs through clash detection during the design process; andoptimising the management of the facility through the registration of medical installations andequipments, fixed and flexible furniture, product and output specifications, and operational data.The second case is a project at the Maxima Medical Centre (MMC). MMC is a large hospital resulted from a merger between the Diaconessenhuis in Eindhoven and St Joseph Hospital in Veldhoven. Annually the 3,400 staff of MMC provides medical services to more than 450,000 visitors and patients. A large-scaled extension project of the hospital in Veldhoven is a part of its real estate strategy. A medical simulation centre and a women-and-children medical centre are among the most important new facilities within this extension project. The design has been developed using 3D modelling with several functionalities of BIM.The findings from both cases and the analysis are as follows.Both UMC and MMC opted for a traditional procurement method in which the client directly contracted an architect, a structural engineer, and a mechanical, electrical and plumbing (MEP) consultant in the design team. Once the design and detailed specifications are finished, a tender procedure will follow to select a contractor. Despite the choice for this traditional method, many attempts have been made for a closer and more effective multidisciplinary collaboration. UMC dedicated a relatively long preparation phase with the architect, structural engineer and MEP consultant before the design commenced. This preparation phase was aimed at creating a common vision on the optimal way for collaboration using BIM as an ICT support. Some results of this preparation phase are: a document that defines the common ambition for the project and the collaborative working process and a semi-formal agreement that states the commitment of the building actors for collaboration. Other than UMC, MMC selected an architecture firm with an in-house engineering department. Thus, the collaboration between the architect and structural engineer can take place within the same firm using the same software application.Regarding the life-cycle design approach, the main attention is given on life-cycle costs, maintenance needs, and facility management. Using BIM, both hospitals intend to get a much better insight in these aspects over the life-cycle period. The life-cycle sustainability criteria are included in the assignments for the design teams. Multidisciplinary designers and engineers are asked to collaborate more closely and to interact with the end-users to address life-cycle requirements. However, ensuring the building actors to engage in an integrated collaboration to generate sustainable design solutions that meet the life-cycle。
工程造价成本管理外文文献

Evaluation of the influence of the organizational environment on projectcost management based on the Grey Relational AnalysisZhi Dou,Wenjun YangCollege of Civil Engineering ,Chang'an University ,Xi'an 710061,ChinaKeywords :the Organizational Environment, Engineering Project, Cost Management, ImpactEvaluation, Grey Relational AnalysisAbstract. From the organizational environment perspective, to explore the influence factors ofproject cost management, and to determine a evaluation system about the influence of theorganizational environment on project cost management. Using gray system theory to build a modelof the gray relational analysis between organizational environment and project cost management.The examples show that this method has a certain theoretical significance and practical value tosolve the project cost management.IntroductionAccompanied by the rapid development of China's construction industry and the further openingup of construction markets, the uncertainty of the external environment which constructionenterprises face increased, the underpricing bid between enterprises for contending projects, thedrastic fluctuation in raw material prices, the entering barriers are down while the exit cost are stillhigh, the ferocious entering momentum of foreign builders, these make China constructionenterprises stand in a competitive industry, and its profit margins are severely squeezed. The way toeffectively control the project cost has already become a focus of attention of constructionenterprises. Survey shows that the extensive management approach of China's constructionenterprises currently has not been fundamentally changed, the corporate structure, operationalprocesses and infrastructure management is weak, the level of project management is low, and theexisting project cost should be improved in aspects about management concepts, objectives, meansand so on [1].The effective implementation of advanced cost management methods must considerenterprises' particular organizational environment, Kaplan and Norton believes, the advanced costmanagement and evaluation methods break away from its corresponding organizationalenvironment, the possibility to success almost not exists [2].Therefore, the objective understandingof the organizational environment the construction enterprises face, and the comprehensive analysisabout the mechanism of the organizational environment to the project cost management for theconstruction cost management is essential.The determination of the affecting factor system of the project cost management byorganizational environmentOrganizational environment is a sum of forces and conditions which exist in the internal andexternal organization and affect the organizational performance. There are many environmentalfactors in internal and external organization, but not all of these factors constitute the organization'senvironment, the factors who has no impact on organizational performance do not belong to theenvironmental factors of organization, and elements of the organizational environment is often influx, the dynamics of environment perform clearly in a background of fierce competition both indomestic and foreign markets [3].According to the organization's controllable degree to its faced environment, the organizationalenvironment can be divided into two categories: the internal organizational environment and theexternal organizational environment. The external environment that construction enterprises face isthe sum of various factors which exist around the construction organization and affect the businessactivities and development of enterprises. The external environmental uncertainty of constructionInternational Conference on Education Technology, Management and Humanities Science (ETMHS 2015) © 2015. The authors - Published by Atlantis Press 985enterprises include the general environmental uncertainty and the task environmental uncertainty,the general environmental uncertainty include the uncertainties which brought for constructionenterprises from the political environment, economic environment, legal environment and technicalenvironment, and the task environmental uncertainty include the uncertainties which brought forconstruction enterprises from new entrants, owners, suppliers and existing competitors.Through the above analysis, the several affecting factors of the project cost management by theorganizational environment were researched; this paper considers the factors are: organizationstructure, control system and social relations. And the table 1, the affecting factor system of theproject cost management by organizational environment, is built by these factors.Tab.1. the Affecting Factor System of the Project Cost Management by Organizational EnvironmentFirst class index Second class indexThird class indexProject CostManagementA Organization Structure 1B Organization Framework 1C Internal Coordination 2C Internal Restriction 3CControl System 2B Budget Mechanism 4CAccounting Mechanism 5CMonitoring Mechanism 6C Analyzing Mechanism 7CChecking Mechanism 8CMaterial Cost Management 9CProject Manager Management 10CSocialRelations 3B Major Stakeholder 11C External Communication andCoordination 12CEvaluation of the influence of the organizational environment on project cost managementbased on the Grey Relational AnalysisTo determine the weighing values of all levelsBecause of the important degree of the influence of the above indexes on project cost are notidentical, it is required to determine the weights.We can choose to invited several experts whoadopted the ratio scale method to compare two factors, and to determine the ratio scale betweenvarious factors, as shown in table 2, then in turn collect the statistics of frequency mij of each indexratio scale Cj.()jij C i j m U U c n= (2.1) In the formula, mij is the number of times of Ui ∈ci; n is the number of experts to participate inthe evaluation; Uci(Ui) is the ratio scale of Ui belong to the cj, we can get the ratio scale()j n i C i j i R U U ==∑ (2.2)986Tab.2. The meaning of the scaledivision meaning1 Have the same importance3 The former is a bit more important than the latter5 The former is obviously more important than thelatter7 The former is particularly more important than thelatter9 The former is extremely more important than thelatter2,4,6,8 The median value of the above-mentioned adjacentvaluereciprocal The degree that the latter is more important than the formerCalculate the feature vector W of matrix H, inspect whether have stochastic consistencybetween matrix H and the feature vector W, and compute consistency index CI=(λmax-n)/(n-1),when CR=CI/RI<0.10, the consistency of judgment matrix is satisfied, or need to adjust thejudgment matrix. Among them, the elements Wi(i=1,2,...n) of W represents the lower the weight ofeach index relative to its upper part index.Quantitative treatment of indicatorsEvaluation index can be divided into two types: quantitative index and qualitative index.Qualitative indicators are unquantitative fuzzy evaluation index, thus the comprehensive fuzzyevaluation method of quantitative index can be used. By experts fuzzy scoring in the first place,reoccupy the average value to quantify according to the fuzzy membership degree just as is shownin table 3.Tab.3. The fuzzy membership listfuzzy language best bette r goo d general ly ba d wors e wor stmembership 0.8 0.7 0.6 0.5 0.40.3 0.2 To determine the reference data sequence and compared sequenceIn order to evaluate the eligible object data sequence, the first thing is to determine theevaluation reference data sequence, usually write to uik=(ui1,ui2,...uin),k=1,2,...s.A comparison with reference data sequence uik have n data index sequences, and each datasequence (scheme) have s factors (indicators), then these comparative data column can be written asU0=(u10,u20,...un0)T.To determine the reference sequence, according to the comparison reference sequence types ofindicators selected, index of different types, different values of the methods. Seen in the literatureindex types have six kinds, including efficiency, cost, fixed type, range, deviation and deviationinterval[4].Index correlation calculation of index layerIn order to ensure the quality of modeling and get the right system analysis, the data must becarried out on the original data standardization transformation and data processing, so that thedimension can be eliminated and the data can be comparable. in correlation analysis, the mostcommon methods were used in data transformation are initial value transformation method, themean transformation method, full transformation method, unitary transformation method, multiplechanges, poor maximum transformation method, standardized method and interval valuetransformation method[4-5]. In this paper, using the standardized method for data processing, namely:,1,2,,k k i i i u x k s u == (2.3) 987In the formula, 0 means the reference solution.Corresponds to a sequence of reference data, there are a number of comparative data sequence,the ith comparative data with reference data sequences in the first k corresponding indicators of relative difference is the correlation coefficient, can be expressed as()0000min min max max max max 1,2,;1,2,k k i i i i k i k i ki k k i i i i i k X X X X X X X X i n k s ηξη-+-=-+-== (2.4)Type: η is distinguish coefficient, 0<η<1, typically take η=0.5.The weighted average correlation coefficient under various factors11(1,2,;1,2,)n k k k i k n i n k s γωξ====∑ (2.5)Type: ωk is the weight, 0≤ωk≤1.According to the comparison and analysis of correlation, multi-level comprehensive evaluationof the construction project cost management is adopted. Generally speaking, the bigger thecorrelation of engineering project cost management level was, the engineering project costmanagement situation greater. In this way, we can made a more objective comprehensiveevaluation for the construction enterprise project cost management situation, and use this asreference data for the management of engineering project cost.ExampleNow with the influence of A, B, C three construction enterprise environment present situation onthe engineering project cost management as an example to illustrate the specific application ofevaluation model of gray association analysis.The index classification, the classification and the weight of each index of A, B, C threeconstruction enterprise organizational environment , are shown in table4 the comprehensiveevaluation of engineering project cost management.Tab.4. The project cost management comprehensive evaluationLevel indicator s The weigh t The second Level indicators The weig ht the index sequence of Project cost management evaluation A B C 0i uB 10.3 C 1 0.4 0.4 0.6 0.5 0.6C 2 0.3 0.5 0.7 0.6 0.7 C 3 0.3 0.6 0.7 0.5 0.7B 20.4 C 4 0.2 0.7 0.6 0.4 0.7C 5 0.15 0.7 0.6 0.5 0.7C 60.1 0.6 0.5 0.5 0.6 C 7 0.2 0.5 0.5 0.6 0.6 C 8 0.1 0.6 0.5 0.5 0.6C 9 0.12 0.6 0.6 0.7 0.7C 10 0.13 0.6 0.5 0.5 0.6B 3 0.3C 11 0.56 0.7 0.6 0.6 0.7 C 12 0.44 0.5 0.5 0.6 0.6Weight is index to describe the affection of properties and various indicators of project costmanagement evaluation , scored by the expert , calculated the weight according to the type 2.1, 2.2 ,through the consistency check, in view of the length, not do detailed calculation here.Determine the optimal index (reference sequence)According to the principle of determining the optimal index, we can determine the referencesequence 0(0.6,0.7,0.7,0.7,0.7,0.6,0.6,0.6,0.7,0.6,0.7,0.6)i u =988Data standardization processBy the evaluation index system of project cost management, the evaluation index points belongto three classes. Processed the index sequence standardized according to the type (2.3) , threeclassification subset sequence are obtained. Calculate the absolute difference between the evaluation and the reference sequences sequencematrix, the calculation results are as follows:1max 0.33B ∆=,1min 0B ∆=;2max 0.17B ∆=,2min 0B ∆=;3max 0.43B ∆=,3min 0B∆=. Evaluation of the primary engineering project cost managementTake the resolution 0.5η=, the correlation coefficient of each subset can be calculated accordingto the type (2.4) , and correlation coefficient matrix is established. The table 4 shows that for Ⅰindexes, the weights 12(0.4,0.3,0.3)B ω=. According to the type (2.5) , he correlation of this indicator canbe calculated. [][]11120.330.370.541110.40.30.30.4110.470.50.540.37T B B B γωξ⎡⎤⎢⎥=⋅=⋅=⎢⎥⎢⎥⎣⎦On the basis of above, the primary evaluation can be conducted. For the class index, the sort ofthree construction enterprise correlation is C > B > A, which the index of engineering project costmanagement of construction enterprises B is optimal, C construction enterprise take the second, Abusiness is the worst.Similarly for II indexes, []20.790.350.5B γ=, we can judge that the optimal is A enterprise and Benterprise is the worst. For III indexes, []30.810.580.58B γ=, we can judge the optimal is A enterprise, B and C enterprise is the same.According to the corresponding evaluation results, management of construction enterprise projectcost management is optimized.The secondary comprehensive evaluation of the gray correlation analysisFrom the primary evaluation,we can be see that in the category of different indicators of thesame construction enterprise, both the optimal and the worst index category of engineering projectcost management can be appeared. Obviously , it is difficult to reflect the overall condition of theengineering project cost management. Therefore, all categories should be considered to thesecondary comprehensive evaluation on engineering project cost management. Primary indexweights ω1=(0.3,0.4,0.3), according to the type (2.5) ,we can get comprehensive correlation degree [][]10.410.790.8110.350.580.30.40.30.680.610.520.470.500.58T A γωξ⎡⎤⎢⎥=⋅=⋅=⎢⎥⎢⎥⎣⎦ Order By the correlation size:A B C γγγ>>. As you can see, the construction enterprise project costmanagement situation of quality for A is the best, B enterprise second, C enterprise is the worst.ConclusionBased on actual engineering project cost management, this paper considers the organizationalenvironment factors and builds the organization environment factors to the engineering project costmanagement. With gray correlation analysis method to engineering project cost managementconducts a multi-level evaluation, obtains different levels of management evaluation results, theresult is consistent with the actual situation of construction enterprise.shows that this method hascertain theoretical significance and practical value. But in this study, the main factors affecting theproject cost management may have failed to be included in some factors, such as enterprise culture,national macro policy and other factors. In future study, we can further complete factors through thedesign organization environment impact on the engineering project cost of questionnaire.989References[1] XuTang.Based on the strategy of target cost management method in the application of international engineering contracting project .Chong qing.Southwestern university of finance and economics , 2003:6-7.[2] Kaplan,Norton.Strategic center type organization. Beijing:Ren min university of China publishing house,2001.[3] Yan Haifeng,Wang Ruixu.The modern organization theory and organizationinnovation.Beijing:People's posts and telecommunications publishing house,2003:61-81.[4] Wu Weidong , Jing Guoxun,Wei Jianping. Grey correlation analysis in six coal mine ventilation system scheme (recent) the application of the optimization . Journal of coal , 2001, 34(3): 290-293.[5] Xiao Xinping, Song Zhongmin,Li Feng.Gray technology base and application.Beijing: Science press.2005.990。
- 1、下载文档前请自行甄别文档内容的完整性,平台不提供额外的编辑、内容补充、找答案等附加服务。
- 2、"仅部分预览"的文档,不可在线预览部分如存在完整性等问题,可反馈申请退款(可完整预览的文档不适用该条件!)。
- 3、如文档侵犯您的权益,请联系客服反馈,我们会尽快为您处理(人工客服工作时间:9:00-18:30)。
毕业设计(论文)外文文献翻译文献、资料中文题目:我们需要战略成本管理文献、资料英文题目:We need strategic cost management 文献、资料来源:文献、资料发表(出版)日期:院(部):专业:班级:姓名:学号:指导教师:翻译日期: 2017.02.14本科毕业论文(设计)外文翻译原文:We need strategic cost managementWe need strategic cost management? As noted earlier, the global financial crisis continues to wantonly slightly, off-season already unsolicited, but also to a year was bad, but even worse this year, Xi. Improve efficiency, reduce costs, many companies have become one of the ultimate weapon. Consequently, from Europe to the Americas, from global to domestic, sounded a dismissal, caused many large and small vibration. Various enterprises began Wujin their own property, to control expenditure, lowering of standards, so these are all related to the cost of this topic.In fact, the companies cut costs, all costs should not be without identification, "indiscriminate white uniform." If a business manager to every expenditure appears to cut off the excess, it is likely this weakened the competitiveness of enterprises and thus affects the business, results of more harm than good. Therefore, managers should be the perspective of corporate strategy to control costs and avoid damage to the value of those core elements of the decision. Consequently, cost-plus strategy, it leads to strategic cost management topics.He suggested approach for dedicating resources to supplier cost management may seem cost prohibitive. However, the organizations studied unanimously agree that they receive extremely high returns on their investments in supplier cost management efforts. The money spent on supplier cost management efforts. The money spent on supplier should-cost analysis, supplier development, and other tools and approaches pays for itself many times over in terms of reducing costs and bottom-line prices paid to suppliers. for large fortune 500 companies, successful strategic cost management may mean the addition of dedicated personnel to focus on supplier cost management. for smaller organizations which might not have as great an on-going need, or as great an asset base.So, what is strategic cost management? Strategy can be defined as the establishment of their fundamental long-term goals and to achieve the goals to take the necessary action planning and resource allocation, is to guide the overall plans and strategies. The so-called strategic cost management from a strategic perspective to study the formation and control costs. In established under the principle of corporate strategy, in terms of cost management for the strategic choice and design, it will lead to the final delivery of business products and services to lower costs, not every part of Shang Du Zhuiqiu lowest cost. Includes two levels of content: one from a cost perspective, the selection and optimization of business strategy; Second, the implementation of cost control strategies. Strategic cost management thinking on strategic cost management theoretical framework of the general and summary, which determines the strategic cost management theory and methodology to start the basic ideas.In the background of the crisis under the cost-cutting, more Xuyao follow strategic cost management thinking, to have a choice cut, not important link in the conduct of large Ke Yi drastic cuts; and the related core competitive Li's Guanjianyaosu, but not rule out the possibility of expanding into so targeted, there are tight with loose, smart, cost-cutting, a square is not only lower costs, but also without prejudice to the company health and even enhance the core competitiveness of the ideal choice.The basic tools of strategic cost management cost management strategy has three elements: value chain analysis, strategic positioning analysis and cost driver analysis. They also analyzed in the framework of strategic management and cost factors closely related to the three basic analysis tools.(A) of the value chain analysis of each end product from initial raw materials into the hands until it reaches the final consumer, intermediate to go through numerous interrelated operating procedures, these operating procedures is both a product of the production process, but it is also a value formation and value-added process to form the value chain (Value-chain). Value chain analysis can be divided into industry specific value chain analysis, value chain analysis and value chain。