冷轧企业乳化液分析操作规程
乳化液各参数的控制方法

( 1 )用 P H仪测定 ,必须在环境 温度 下校准后使用 ,并等读盘 稳定后读 数。由于乳化剂要在一定的 P H 范围才 能发挥最佳作用 , 所 以要控制 好乳化 液的 P H值 。 ( 2 )P H值的控制范围 :5 . 5 ~6 . 5 。如果超出正常范 围,通过 适当加 N a 0 H或 H a P 0 来调节。 3电导率 ( 1 ) 用 电导率仪测定 , 电导率 是乳化液水相 中导 电物质 的总反 应 ,电导率过高会对乳化液的稳定性造成不 良影响 ,增加灰分值 , 且板面与导电物质会在 局部发 生化学反应 ,增加钢板生锈 的机会 。 ( 2 )电导率大于 4 0 0 u s / c m时 ,根据所测值 ,加入新轧制油和 脱盐水,直到电导率小于 4 0 0 u s / c m 。 4皂化值 ( 1 ) 用氢氧化钾 乙醇溶液加入到所提取的油品和空白样 中, 冷 凝 回流 3 5 分钟,再 用盐酸标准溶液滴定 的方法测定
在实际轧机的生产中液压油齿轮油等矿物油与轧制油都是有机连结构的有机物在乳化液中经过循环后会与轧制油相融合杂油的粘度大而离水展着性差粘附在带钢表面难以去除且矿物油的润滑性比酯类差很多这些杂油会造成皂化值的降低
T e c h பைடு நூலகம் o l o g y F O r u m
乳化液各参数的控制方法
郭 静 孙 宁涛 贾英英 苏东磊
公 式 : 皂 化 值= ( A — B )* C . 5 6 . 1 1 / D m g K O H / g
冷轧钢板中轧制乳化油的选用

冷轧钢板中轧制乳化油的选用1.乳化液的分类通常,乳化液可根据乳化后的稳定性分为稳态乳化液、半稳态乳化液和非稳态乳化液三类。
乳化 液的稳定性是一个极其重要的指标,其测定方法是将油品配制成一定浓度的乳化液,在一个分料漏斗 中静置8分钟,然后将最底下和最上面的四分之一溶液分离出来。
用离心分离法测定两部分的浓度, 然后以最底下部分的油含量对最上面部分的油含量比例构成乳化液的稳定指数,用ESI表示。
1.1 稳态乳化液稳态乳化液,以精炼轻、中质矿物油和合成酯为主要成分,再加入多种添加剂,如脂肪酸、脂肪 油、阴离子和非离子型等表面活性剂,极压添加剂,防锈剂,抗氧剂,抗泡剂等。
此类乳化液可在室 温下将浓缩油直接加入水中形成稳定的乳化液,稳定指数ESI在0.6以上,皂化值小于50,使 用浓度为5%至10%。
配制后的乳化液颗粒大小在1至1.5微米之间,少数可达5微米。
稳态乳 化液具有良好的退火清洁性,可以不经清洗而直接退火。
1.2 半稳态乳化液半稳态乳化液,以精炼脂肪油、合成酯和矿物油的混合油为基油,另加入分散剂,极压添加剂, 防锈剂,抗氧剂等添加剂组成。
此类乳化液需在50至60℃温度下,将油在水中调配成乳化液。
配 制好的乳化液颗粒大部分为1至10微米,比稳态乳化液,因此半稳态乳化液在使用过程中需不断搅 拌并保持一定的温度,防止部分基油从乳化液中析出。
半稳步态乳化液的使用浓度为2%至7%,皂 化值在50至130之间。
半稳态乳化液的润滑性能较稳态乳化液好,但其清洁性较差,故退火前需 经脱脂清洗。
1.3 非稳态乳化液非稳态乳化液的主要成分是动、植物油如牛油、菜仔油等,加入极压添加剂,抗氧剂,防锈剂, 乳化剂等。
这类乳化液对钢板和轧辊的附着性好,可大幅降低摩擦系数,润滑性能特别好。
但残炭多, 退火前必须经过电解脱脂。
非稳态乳化液的皂化值在150至230之间,使用浓度5%至10%。
以上三类乳化液的皂化值,润滑性,冷却性及清净性之间的关系如图1所示。
冷钢气动乳化脱硫操作规程2014.7.6

冷水江钢铁有限责任公司2×1352烧结机烟气脱硫项目操作规程广州舒创有限公司编制一、前言气动乳化脱硫法是一种以工业废渣、电石泥、工业废碱液等为脱硫剂,本发明特别适用于高硫烟气,以废治废,资源化利用工业废渣和废气,产出大宗工业原料,生产过程无污染,涉及环保和资源利用技术领域。
其特征在于气动乳化脱硫塔和电石泥等脱硫剂结合使用,气动乳化的过滤单元为单级或多级垂直串联,烟气旋切吸收液,形成一个或多个稳定的乳化液层,在乳化液层内,吸收液和含二氧化硫烟气进行以脱硫为目的的强传质,强传质的乳化液层由烟气旋切吸收液产生,实现各种炉窑的烟气SO2排放达到国家环保标准,保护了生态环境。
二、原理利用石灰石、石灰、电石泥、纯碱、烧碱、软锰矿、氨水、工业废碱液等在水溶液状态下与烟气中的SO2等酸性气体进行化学反应,生成稳定的盐类,从而减少或去除烟气中的SO2等酸性气体排放。
在脱硫塔的过滤元件中,经加速的待处理烟气以一定角度从下进入脱硫塔,形成旋转上升的紊流气流,与脱硫塔上端流下不稳定溶液相碰,烟气高速旋切流下溶液,溶液被切碎,气液相互持续碰撞旋切。
液粒被粉碎得愈来愈细,气液充分混合,形成一层稳定的乳化液。
在乳化过程中,乳化液层逐渐增厚,上流的气动托力与乳化液的重力达到平衡,乳化液层继续增厚,最早形成的乳化液将被新形成的乳化液取代。
带着被捕集的杂质落回脱硫塔的底部,在过滤单元内,只要有足够的处理气流量,总将保持一相对稳定的乳化液层。
由于在乳化液中,液粒比表面积比水膜除尘、喷淋除尘等方法大数倍至数十部,因此,单位液量捕集和吸收有害物质的效率显著增大。
三、吸收机理脱硫塔是系统的核心,气流在塔内过塔高度15m,在塔内停留时间7秒。
湿法烟气脱硫效率由塔的传质能力决定,与液气二相在塔内接触程度相关。
在塔内,SO 2被水吸收,成为亚硫酸(氧化后为硫酸),再与碱性物(或二性物)反应生成亚硫酸盐及硫酸盐。
石灰石脱硫主要产物是石膏。
冷轧机操作规程范文

冷轧机操作规程范文一、总则1.1本操作规程适用于冷轧机的操作人员,确保操作人员的生命安全和设备的正常运行。
1.2操作人员必须熟悉冷轧机的结构和工作原理,严格按照操作规程进行操作。
1.3操作人员必须穿戴防护装备,严禁穿戴松散的衣物和长发,以防被冷轧机捕捞。
二、操作准备2.1操作人员必须在进行操作前检查冷轧机及相关设备是否正常运行,消除隐患。
2.2操作人员必须佩戴防护手套、防护面具、耳塞等个人防护装备。
2.3确保操作环境干燥、通风良好,不得有易燃、易爆物品存在。
三、操作流程3.1操作人员必须先向领导报备,获得操作许可后方可进行操作。
3.2操作人员在操作冷轧机前,必须按照操作手册上的要求检查设备的运行状态,确保无异常。
3.3操作人员必须按照操作手册上的要求对设备进行润滑,确保设备正常工作。
3.4操作人员在操作冷轧机时,必须确保设备处于停止状态,严禁在运行状态下进行操作。
3.5操作人员必须按照设备的使用要求正确调节和安装工作模具,确保冷轧板坯的质量。
四、安全操作4.1操作人员必须保持清醒的状态,严禁酒后操作冷轧机。
4.2操作人员必须按照操作手册上的要求正确使用冷轧机各个控制按钮,严禁擅自修改设备的操作参数。
4.3操作人员操作冷轧机时,应保持稳定的姿势,确保不会滑倒或意外摔倒。
4.4操作人员在操作冷轧机时,必须时刻保持注意力集中,严禁分心做其他事情。
4.5操作人员在冷轧机运行过程中,需随时注意设备的运行情况,如发现异常应立即停止操作并向上级汇报。
五、设备保养5.1操作人员需定期检查和保养冷轧机的润滑系统、电气系统等设备部件,确保正常运行。
5.2操作人员需定期清洁和检查冷轧机各个部件,防止灰尘、油渍等杂物对设备造成损坏或隐患。
5.3在设备保养期间,操作人员需按照设备保养要求,对设备进行必要的维修和保养工作。
六、事故应急处理6.1在发生事故或异常操作时,操作人员必须立即停止设备运行,并向上级汇报。
6.2操作人员在事故应急处理中,应按照操作手册上的要求采取必要的应急措施,保证人员的生命安全,并减少事故对设备的损伤。
关于冷轧中乳化液的技术指标
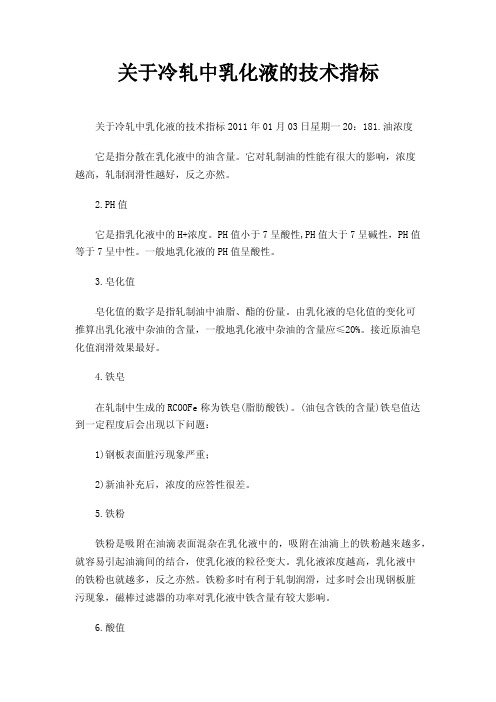
关于冷轧中乳化液的技术指标关于冷轧中乳化液的技术指标2011年01月03日星期一20:181.油浓度它是指分散在乳化液中的油含量。
它对轧制油的性能有很大的影响,浓度越高,轧制润滑性越好,反之亦然。
2.PH值它是指乳化液中的H+浓度。
PH值小于7呈酸性,PH值大于7呈碱性,PH值等于7呈中性。
一般地乳化液的PH值呈酸性。
3.皂化值皂化值的数字是指轧制油中油脂、酯的份量。
由乳化液的皂化值的变化可推算出乳化液中杂油的含量,一般地乳化液中杂油的含量应≤20%。
接近原油皂化值润滑效果最好。
4.铁皂在轧制中生成的RCOOFe称为铁皂(脂肪酸铁)。
(油包含铁的含量)铁皂值达到一定程度后会出现以下问题:1)钢板表面脏污现象严重;2)新油补充后,浓度的应答性很差。
5.铁粉铁粉是吸附在油滴表面混杂在乳化液中的,吸附在油滴上的铁粉越来越多,就容易引起油滴间的结合,使乳化液的粒径变大。
乳化液浓度越高,乳化液中的铁粉也就越多,反之亦然。
铁粉多时有利于轧制润滑,过多时会出现钢板脏污现象,磁棒过滤器的功率对乳化液中铁含量有较大影响。
6.酸值酸值的数值表示轧制油中脂肪酸的量。
1)脂肪酸的优点:酸基对钢板表面有较强的附着力,因此它对润滑性和防锈性都很好。
2)脂肪酸的缺点:脂肪酸过多,将会促进油箱以及管道的腐蚀,此外还将生成大量铁油泥,使钢板表面及轧机机组的脏污急剧增加。
7.电导率一般指乳化液的导电能力,是电阻的倒数。
(离子高则容易油水分离!)8.温度温度是个管理项目,它对性能有很大的影响。
1)温度较低时容易出现的问题:①润滑不良,轧制力升高,振动现象多发;②容易产生轧后钢板表面脏污现象;③钢板表面水分蒸发困难,钢板容易生锈。
2)温度较高时容易出现的问题:①乳化不安定,附着量增加,容易产生打滑现象;②蒸汽大量产生,污染工作环境。
乳化液在轧制过程中的润滑和冷却乳化液在冷轧中的主要作用是润滑和冷却。
在轧制过程中,轧制变形区产生的高温使乳化液产生油水分离,油吸附在轧辊与钢板表面形成油膜,起到润滑作用。
乳化液的使用

乳化液的合理使用近几年来,我国切削液生产发展较快,新产品不断推出,但归纳起来,它们的基本成分都是由油、水和各种化学添加剂配制而成。
生产中常用的切削液有切削油、乳化液和水溶液三大类。
切削油润滑和防锈性好,但冷却和清洗性较差,切削时在切削区会形成油雾,造成环境污染,同时油资源消耗多,生产成本高。
水基切削液的冷却和清洗性较好,但防锈性较差。
乳化液具有一定的润滑性、冷却性、清洗性和防锈性,是目前生产中使用最广泛的一种切削液。
但它的使用寿命短,废液多,排放时水质污染较严重,因此必须进行净化和废液回收处理。
现就乳化液的组成及其净化方法,废液的回收处理,以及如何延长乳化液使用寿命等问题,介绍如下。
乳化液的组成及其净化方法乳化液的组成乳化液是用矿物油、乳化剂(如石油磺酸钠、磺化蓖麻油等)及添加剂预先配制好的乳化油,加水稀释而成。
因为油不溶于水,为了使两者混合,所以必须加入乳化剂。
乳化剂是一种表面活性剂,它的分子是由极性基团和非极性基团两部分组成。
前者亲水,可溶于水;后者亲油,可溶于油。
把油在水中搅拌成细粒时,乳化剂分子能定向地排列吸附在油水两界面上,把油和水连接起来,使分离的细粒不再因凝聚而浮游在水中,成为浮浊液。
乳化液中含乳化油少,即浓度低的(如浓度为3%~5%),冷却和清洗作用较好,适于粗加工和磨削;浓度高的(如浓度为10%~20%),润滑作用较好,适于精加工(如拉削和铰孔等)。
为了进一步提高乳化液的润滑性能,还可加入一定量的氯、硫、磷等极压添加剂,配制成极压乳化液。
乳化液的净化方法近几年来研究表明,如将切削液中的杂质(如碎屑、砂轮粉末等)从40μm降低到10μm,刀具耐用度可延长1~3倍。
由于人们的肉眼看不见小于40μm的微粒,所以当切削液中的杂质,尺寸小于20μm,常被人们所忽视,然而这些不可见的杂质对金属切削加工有着不可低估的影响。
在切削加工时,它们将进入到刀具前刀面与切屑以及刀具后刀面与工件接触区的界面上,产生强烈摩擦,使切削温度增加,并使刀具耐用度大大降低,同时使加工表面质量变差。
冷轧机的乳化液控制与回收系统
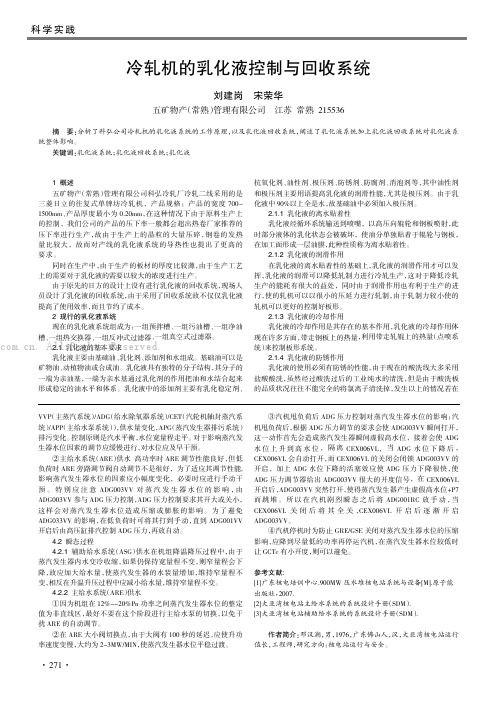
VVP(主蒸汽系统)/ADG(给水除氧器系统)/CET(汽轮机轴封蒸汽系统)/APP(主给水泵系统)),供水量变化,APG(蒸汽发生器排污系统)排污变化。
控制原则是汽水平衡,水位宽量程走平。
对于影响蒸汽发生器水位因素的调节应缓慢进行,对水位应及早干预。
②主给水系统(ARE)供水高功率时ARE调节性能良好,但低负荷时ARE旁路调节阀自动调节不是很好,为了适应其调节性能,影响蒸汽发生器水位的因素应小幅度变化,必要时应进行手动干预。
特别应注意ADG003VV对蒸汽发生器水位的影响,由ADG003VV参与ADG压力控制,ADG压力控制要求其开大或关小,这样会对蒸汽发生器水位造成压缩或膨胀的影响。
为了避免ADG033VV的影响,在低负荷时可将其打到手动,直到ADG001VV 开启后由高压缸排汽控制ADG压力,再放自动。
4.2瞬态过程4.2.1辅助给水系统(ASG)供水在机组降温降压过程中,由于蒸汽发生器内水变冷收缩,如果仍保持宽量程不变,则窄量程会下降,故应加大给水量,使蒸汽发生器的水装量增加,维持窄量程不变,相反在升温升压过程中应减小给水量,维持窄量程不变。
4.2.2主给水系统(ARE)供水①因为机组在12%--20%Pn功率之间蒸汽发生器水位的整定值为非直线区,最好不要在这个阶段进行主给水泵的切换,以免干扰ARE的自动调节。
②在ARE大小阀切换点,由于大阀有100秒的延迟,应使升功率速度变慢,大约为2-3MW/MIN,使蒸汽发生器水位平稳过渡。
③汽机甩负荷后ADG压力控制对蒸汽发生器水位的影响:汽机甩负荷后,根据ADG压力调节的要求会使ADG003VV瞬间打开,这一动作首先会造成蒸汽发生器瞬间虚假高水位,接着会使ADG 水位上升到高水位,隔离CEX006VL,当ADG水位下降后,CEX006VL会自动打开,而CEX006VL的关闭会闭锁ADG003VV的开启,加上ADG水位下降的活塞效应使ADG压力下降很快,使ADG压力调节器给出ADG003VV很大的开度信号,在CEX006VL 开启后,ADG003VV突然打开,使得蒸汽发生器产生虚假高水位+P7而跳堆。
乳化沥青生产操作规程(3篇)

第1篇一、目的为规范乳化沥青生产过程,确保产品质量,保障生产安全,特制定本规程。
二、适用范围本规程适用于乳化沥青生产过程中的原料准备、设备操作、生产过程控制及成品检验等环节。
三、生产准备1. 原料准备:根据生产计划,提前准备好所需原料,包括沥青、乳化剂、水、矿粉等。
2. 设备准备:检查设备是否正常运行,确保搅拌器、加热器、过滤装置等设备完好。
3. 工具准备:准备好计量工具、搅拌工具、取样工具等。
四、生产过程1. 搅拌:将沥青加热至预定温度,同时将乳化剂、水、矿粉等原料按比例加入搅拌器中,搅拌均匀。
2. 加热:将搅拌好的原料加热至乳化温度,确保沥青与乳化剂充分混合。
3. 乳化:在加热过程中,使用搅拌器不断搅拌,使沥青与乳化剂充分乳化。
4. 过滤:将乳化后的沥青通过过滤装置进行过滤,去除杂质。
5. 冷却:将过滤后的乳化沥青冷却至预定温度,确保产品品质。
6. 包装:将冷却后的乳化沥青装入专用容器,进行封口。
五、生产过程控制1. 温度控制:严格控制加热、乳化、冷却等环节的温度,确保产品质量。
2. 时间控制:按照生产计划,严格控制各环节的时间,确保生产进度。
3. 搅拌控制:确保搅拌均匀,避免沥青与乳化剂分离。
4. 过滤控制:确保过滤效果,避免杂质进入产品。
六、成品检验1. 外观检查:检查产品外观,确保无杂质、无沉淀。
2. 粘度检查:使用粘度计测定产品粘度,确保符合标准要求。
3. 酸值检查:使用酸值测定仪测定产品酸值,确保符合标准要求。
4. 粒度检查:使用粒度分析仪测定产品粒度,确保符合标准要求。
七、生产安全1. 操作人员必须穿戴好个人防护用品,如防尘口罩、防护眼镜、手套等。
2. 严禁在生产过程中吸烟、饮食。
3. 严禁在设备附近进行敲击、打磨等操作。
4. 严禁在设备运行时进行维修、保养。
八、记录与档案1. 记录生产过程中的关键参数,如原料配比、温度、时间等。
2. 建立生产档案,包括原料采购、生产过程、检验结果等。
- 1、下载文档前请自行甄别文档内容的完整性,平台不提供额外的编辑、内容补充、找答案等附加服务。
- 2、"仅部分预览"的文档,不可在线预览部分如存在完整性等问题,可反馈申请退款(可完整预览的文档不适用该条件!)。
- 3、如文档侵犯您的权益,请联系客服反馈,我们会尽快为您处理(人工客服工作时间:9:00-18:30)。
1、油浓度分析
1.1、适用于冷轧用稳定性乳化液和半稳定性他化液中总油浓度的测定。
1.2、试剂与仪器
a、 H2SO4 (ρ=1.84g/ml)
b、刻度容量瓶(115ml,长颈部上刻有0-15ml的刻度值,分度值为0.1ml)
1.3、分析步骤
a、将乳化液试样摇匀后,移取90ml 试样倒入一半于刻度瓶中,加入10ml H2SO4,
摇匀,加入剩余的另一半乳化液。
b、试样置于恒温水浴锅中,保持在90℃,直至明显的油层形成。
c、记录油含量,精确到0.1ml,并报告重量百分数的油浓度
2、总铁含量分析
2.1、适用于冷轧用稳定性乳化液和半稳定生乳化液中总铁含量测定
2.2、试剂
a、盐酸(ρ=1.19g/ml)
b、过氧化氢(30%)
c、氢氧化钠(30%)
d、磺基水杨酸(5%)
e、乙二胺四乙钠标液 C(EDTA)=0.1mol/l
2.3、分析步骤
移取乳化液试样50ml 置于200ml 带有沸石的三角瓶中,加入5ml Hcl 、1ml H2O2 ,于电热板上煮沸10-15min 后取下,加入100ml 热水,用NaOH调节溶液PH 2-2.5,滴加8-10滴磺基水杨酸,用EDTA滴至乳白色消失为终点。
Fe(mg/l)=CV*55.85*1000/V0
式中: C-EDTA标准物质的量浓度,mol/l
V-滴定试样所消耗EDTA标液体积,ml
V0-试样的体积,ml
2.4、记录并报告乳化液总铁量
3、乳化液皂化值的分析
3.1、适用于冷轧用稳定性乳化液和半稳定生乳化液中皂化值的测定。
3.2、试剂
a、氯化钠
b、无水亚硫酸钠
c、丁酮
d、酚酞乙醇溶液
e、氢氧化钠-乙醇溶液(1%)C(KOH)=0.5mol/L
f、盐酸溶液C(HCL)=0.5mol/L
3.3、仪器
A、恒温水浴锅(温度37~100℃,水温波动1℃)
B、空气冷凝管
C、分液漏斗(1000ml)
3.4、分析步骤
3.4.1、制备试油:取800-1000ml乳化液倒入1L烧杯中,加入50g Nacl,加热至75℃,
破乳后移入分液漏斗中,缓慢加入200-300ml 丁酮,充分振荡后静置分层,将其中的水相及铁皂弃去,将分液漏斗中的有机相滤于400ml 烧杯中,把有机相滤液低温蒸发除去要丁酮,取得试油。
3.4.2、测定
将试油置于200ml 锥形瓶中,准确加入25ml KoH-乙醇标液,连接空气冷凝管,置于恒温水浴中,在90℃时皂化1h 以下。
取下空气冷凝管,用50ml 无水乙醇冲洗冷凝管壁及瓶口,加入2滴酚酞指示液,用Hcl标液滴至无色为终点。
同时做空白试验皂化值(mgKoH/g)=C*(V1-v2)*56.10/m
式中c-Hcl标液的物质量浓度,mol/l
V1-滴定空白所耗HCL标液体积,ml
V2-滴定式样所耗标液体积,ml
m-KOH摩尔质量,g/mol
3.4.3计算记录并出具报告
4、酸值分析
4.1 本标准适用于冷轧用稳定性和非稳定性乳化液中酸值分析
4.2 试剂
中性乙醇
酚酞溶液(1%)
KOH-乙醇标液C(KOH)=0.1mol/l
4.3 分析步骤
在测定皂化值萃取蒸发后的油样中称取试油3~5g,称准至0.01g,置于300ml锥形瓶中,加入50ml 中性乙醇,回流5min,取下试液,加2滴酚酞溶液,趁热用KOH-乙醇溶液滴至微红色为终点。
4.4 结果计算
酸值=CV×56.11/m mgKOH/g
式中C—KOH-乙醇物质的量浓度,mol/l
V-滴定试样所耗KOH-乙醇标液体积,ml
m-试油量,g
56.10—KOH的(摩尔质量)g/mol
4.5 计算并出具相应报告
5、电导率的测定
5.1 适用于冷轧用稳定性乳化液和非稳定性乳化液中电导率测定。
5.2 仪器
电导率仪
5.3 分析步骤
打开仪器开关,预热数分钟,将仪器旋至“校正”位置,调节“调正”旋钮使至校正值。
将乳化液试样倒入100ml烧杯中,把电极浸入该试液中,将测量开关扳至“测量”
档,测出试液的电导率值。
5.4 记录并报告乳化液的电导率值。
6 PH值
6.1 在操作台上放好PH计
6.2 用水彻底清洗电极擦至近干
6.3 将电极浸入PH等于6.864的缓冲溶液并校准PH至6.864
6.4 用水冲洗电极并用滤纸擦至几手干燥
6.5 将电极浸入PH=4.003的缓冲溶液并校准至PH至4.003
6.6 用水冲洗电极并擦到将近干燥
6.7 将电极浸入待测样品中,等读数稳定后作以纪录
6.8 报告PH值,精确至0.01单位
7、氯含量测定
7.1 本标准适用于冷轧用稳定性乳化液和非稳定性乳化液中氯含量测定,但不适用于
油浓度大于10%的试样。
7.2试剂
a、硝酸
b、苯肼羰基偶氮苯(0.5%)
c、硝酸汞标液 C(1/2Hg(NO3)2)=0.0141mol/l
7.3 分析步骤
移取乳化液试样20ml,置于250ml锥形瓶中,加入80~100ml水及8~10滴苯肼羰基偶氮苯溶液,用HNO3调至溶液PH2.5~3.0,用硝酸汞标液滴至紫红色为终点。
7、4分析结果计算
氯含量(mg/l)=CV×35.45×1000/L.
式中C-Hg(NO3)2标液体积,ml
V0-试样体积,ml
35.45-氯摩尔质量g/mol
编制:审核:批准:
发布日期:实施日期:。