缠绕管式换热器的简捷计算
螺旋缠绕管式换热器的设计要点

工艺与设备化 工 设 计 通 讯Technology and EquipmentChemical Engineering Design Communications·87·第44卷第7期2018年7月1 螺旋缠绕管式换热器应用分析从装置应用实际情况来说,在煤化工和其他领域中,以不同的结构形式,被广泛的应用。
以LNG 系列螺旋缠绕管式换热器为例,其类型主要如下:①一级制冷四股流缠绕管式换热器;②二级制冷三股流缠绕管式换热器;③三级制冷两股流缠绕管式换热器等。
此类换热器的应用涉及到多个过程,比如低温混合制冷剂、多股流回热换热过程等,设计计算复杂,缺少通用技术标准以及换热工艺设计计算法等,受到工艺流程或者物性参数等因素的影响,因此难以标准化。
2 螺旋缠绕管式换热器的基本结构常规的单股流螺旋缠绕管的基本结构如图1所示,它主要由1-管程壳体;2-管板;3-壳程筒体;4-螺旋管束组成。
它的螺旋管束是由数根外径φ8mm~φ12mm 的换热管根据一定角度正向反向缠绕而成。
1234图1 螺旋缠绕管换热器的基本结构3 螺旋缠绕管式换热器设计要点3.1 做好力学分析在机械设计中,为保证其使用性能,必须要做好力学分析,包括刚性力学分析和弹性力学分析,进而优化设计。
在进行分析的过程中,主要采用的计算方法包括雷诺数计算法以及普朗特数计算等。
基于力学原理,采用对数平均值法以及体积分率法等进行力学分析。
采用单元模型流场数值模拟分析法可确定其在物理参数,简化计算过程获得管束模型以及结构参数。
采用迭代计算法,结合运用数值模拟计算结果,利用计算机进行设计结果优化,进而保证计算的准确性。
3.2 立足于实际在进行螺旋缠绕管式换热器设计时,要考虑到后期加工制作和使用需求。
多数螺旋缠绕管式换热器的换热管和管板的连接采用强度焊的方法。
因为焊接的质量直接影响着换热器使用性能和寿命,所以在设计和制造环节,需要做好壳程部分的优化设计,通过压力试验或者渗漏试验等,检查接头的致密性以及强度。
换热管规格计算公式

换热管规格计算公式换热管是一种用于传递热量的装置,通常由金属或其他导热材料制成。
在工业生产中,换热管被广泛应用于各种设备和系统中,如锅炉、冷却塔、空调系统等。
为了确保换热管的性能和效率,需要对其规格进行合理的计算和设计。
本文将介绍换热管规格计算的基本原理和公式,并通过实例进行详细说明。
换热管规格计算的基本原理是根据热量传递的需求和工作环境的条件,确定换热管的尺寸、材料和结构。
换热管的规格通常由管道的直径、壁厚、长度等参数来描述。
在进行规格计算时,需要考虑以下几个方面的因素:1. 热量传递需求,根据具体的工艺流程和设备要求,确定换热管需要传递的热量大小和传热系数。
2. 工作环境条件,包括换热管所处的介质类型、温度、压力等条件,以及换热管的安装位置和使用环境。
3. 材料选择,根据工作环境条件和热量传递需求,选择合适的换热管材料,如不锈钢、铜、铝等。
基于以上的考虑因素,换热管规格计算的公式可以通过以下步骤进行:1. 确定换热管的热量传递需求,包括传热系数、传热面积等参数。
2. 根据工作环境条件,计算换热管的传热温度差,确定换热管的传热面积。
3. 根据传热面积和传热系数,计算出换热管的传热能力。
4. 根据传热能力和工作条件,确定换热管的尺寸和材料。
在实际的换热管规格计算中,可以采用以下公式来进行计算:1. 换热管的传热面积计算公式:A = Q / (U ×ΔT)。
其中,A为传热面积,Q为传热量,U为传热系数,ΔT为传热温度差。
2. 换热管的传热能力计算公式:Q = U × A ×ΔT。
其中,Q为传热量,U为传热系数,A为传热面积,ΔT为传热温度差。
3. 换热管的尺寸计算公式:d = (4 × Q / (π× U ×ΔT))^(1/2)。
其中,d为换热管的直径,Q为传热量,U为传热系数,ΔT为传热温度差。
通过以上的公式计算,可以得到换热管的合理尺寸和材料选择,从而确保其在工作中能够满足热量传递的需求,并具有良好的传热效率和稳定性。
管壳式换热器的设计及计算
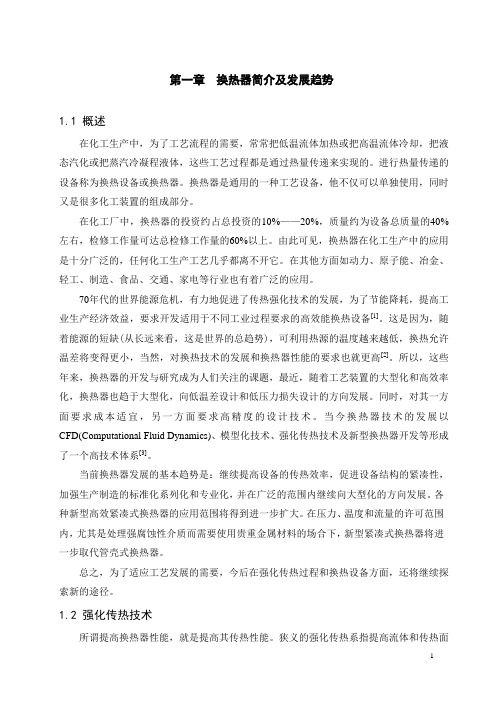
第一章换热器简介及发展趋势1.1 概述在化工生产中,为了工艺流程的需要,常常把低温流体加热或把高温流体冷却,把液态汽化或把蒸汽冷凝程液体,这些工艺过程都是通过热量传递来实现的。
进行热量传递的设备称为换热设备或换热器。
换热器是通用的一种工艺设备,他不仅可以单独使用,同时又是很多化工装置的组成部分。
在化工厂中,换热器的投资约占总投资的10%——20%,质量约为设备总质量的40%左右,检修工作量可达总检修工作量的60%以上。
由此可见,换热器在化工生产中的应用是十分广泛的,任何化工生产工艺几乎都离不开它。
在其他方面如动力、原子能、冶金、轻工、制造、食品、交通、家电等行业也有着广泛的应用。
70年代的世界能源危机,有力地促进了传热强化技术的发展,为了节能降耗,提高工业生产经济效益,要求开发适用于不同工业过程要求的高效能换热设备[1]。
这是因为,随着能源的短缺(从长远来看,这是世界的总趋势),可利用热源的温度越来越低,换热允许温差将变得更小,当然,对换热技术的发展和换热器性能的要求也就更高[2]。
所以,这些年来,换热器的开发与研究成为人们关注的课题,最近,随着工艺装置的大型化和高效率化,换热器也趋于大型化,向低温差设计和低压力损失设计的方向发展。
同时,对其一方面要求成本适宜,另一方面要求高精度的设计技术。
当今换热器技术的发展以CFD(Computational Fluid Dynamics)、模型化技术、强化传热技术及新型换热器开发等形成了一个高技术体系[3]。
当前换热器发展的基本趋势是:继续提高设备的传热效率,促进设备结构的紧凑性,加强生产制造的标准化系列化和专业化,并在广泛的范围内继续向大型化的方向发展。
各种新型高效紧凑式换热器的应用范围将得到进一步扩大。
在压力、温度和流量的许可范围内,尤其是处理强腐蚀性介质而需要使用贵重金属材料的场合下,新型紧凑式换热器将进一步取代管壳式换热器。
总之,为了适应工艺发展的需要,今后在强化传热过程和换热设备方面,还将继续探索新的途径。
换热器管计算
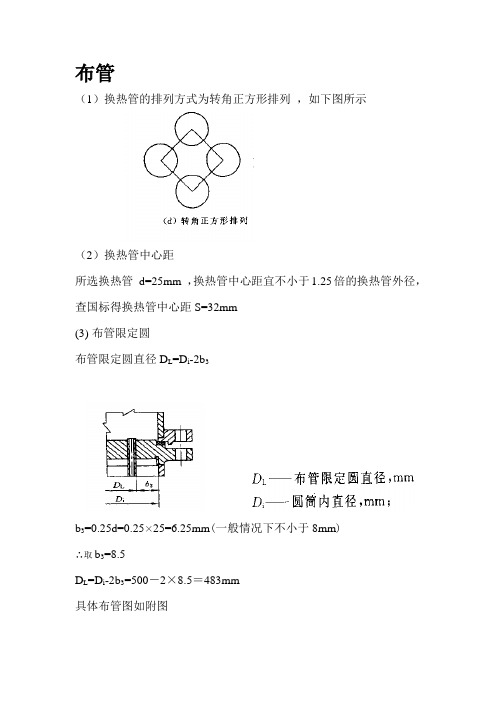
布管(1)换热管的排列方式为转角正方形排列,如下图所示(2)换热管中心距所选换热管d=25mm ,换热管中心距宜不小于1.25倍的换热管外径,查国标得换热管中心距S=32mm(3)布管限定圆布管限定圆直径D L=D i-2b3b3=0.25d=0.25×25=6.25mm(一般情况下不小于8mm)∴取b3=8.5D L=D i-2b3=500-2×8.5=483mm具体布管图如附图U型管换热器的设计与校核1由工艺设计给定壳体公称直径为500mm,壳程的最高工作压力为1.2MPa,管程最高工作压力为1.5MPa,壳程液体进口温度为70℃,出口温度为110℃;管程液体进口温度180℃,出口温度125℃;管长为6000mm,4管程单壳程的换热器。
原油的黏度大,因此壳程走原油,管程走被冷却的柴油。
2筒体壁厚设计由工艺设计给定设计温度为150℃,选用低合金钢Q345R。
查GB 150一2011可知:150℃时Q345R的许用应力[]150δ=189MPa,厚度暂取3~16mm,焊接采用双面对接焊局部无损探伤检测,焊接系数φ=0.85,钢板的厚度负偏差按GB/T 709一2006 查3B类钢板得钢板负偏差为C1=0.3,腐蚀裕量C2=3mm,设计压力为最大工作压力的1.05~1.1倍,由工艺设计给定壳程的最高工作压力为1.2MPa(绝);表压=绝压—当地大气压=1.2Mpa-101.3kpa=1.1Mpa∴P c=(1.05~1.1)×1.1=1.2Mpa计算壁厚t=﹙P c D i/2[δ]tφ﹣P c﹚+C1+C2=5.175mm由于管壳式换热器在工作过程中除承受内压外还受到温差应力、支座反力和自重等载荷的作用,因此壳体壁厚应比计算值大,对碳素钢和低合金钢应满足GB 151一1999的最小厚度要求,查得U型管式换热器的壁厚应不小于8mm,圆整后取钢板名义厚度t n=8mm。
缠绕管式换热器

2绕管式换热器
优点
结构紧凑,单位体 积换热面积大。 100-170 m2/m3 同时处理多股流体 换热
冷热端温差小,传 热效率高
自行补偿热膨胀效 应
绕管式 换热器
缺点
传热计算复杂
流动阻力大
壳程流体分布 均匀性差
对介质清洁度 高 制造成本高, 难度大
2绕管式换热器
管内传热与流动研究
特点:弯曲换热管的曲率使得管内流体惯性力和离心力不平衡,在横截面发生 二次流,从而传热效果会得到强化,其性能将远远优于直管式换热管。
在传热模型建立上,考虑弯曲率和扭转率对管内流 动的影响。
结果表明,与弯曲率相比,扭转率对管内的流动影 响极小。弯曲率使流动截面出现两个旋转方向不同 的漩涡,而扭转率只是使一个漩涡的中心角度发生 扭转,失去对称性。
管内流动几何模型
2绕管式换热器
壳侧传热与流动研究
特点:两相制冷剂在壳侧的流动属于降膜流 动,即在换热管表面和换热管中间形成液膜。 由于制冷剂的干度逐渐增加,液膜越来越不 完整,形态发生变化,如右图所示。
按照传热方式分类 1)直接接触式
热流体Leabharlann 冷流体2)间壁式管壁
3)蓄热式
蓄热室
冷热流体直接相容 传热效率高
冷热流体通过管壁传热 冷热流体不接触
冷热流体间接传热 传热不同时
2绕管式换热器
绕管式换热器:
在芯筒与外筒之间的空间 内将传热管按螺旋线形状交 替缠绕而成,相邻两层螺旋 状传热管的螺旋方向相反, 并采用一定形状的定距件使 之保持一定的间距。
绕管式优于板翅式
管路复杂度
大型LNG绕管式换热器: 常温的天然气从换热器的底部进入管程,从
过冷的LNG从顶部流出,壳侧内的流体为制冷剂,且从顶 部进入。
管壳式换热器热力计算(最全版)PTT文档
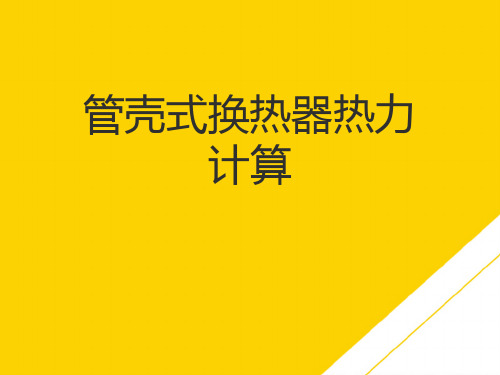
传热系数和导热系数的区别
1.传热系数以往称总传热系数。国家现行标准规范统一定 名为传热系数。传热系数K值,是指在稳定传热条件下, 围护结构两侧空气温差为1度(K,℃),1小时内通过1 平方米面积传递的热量,单位是瓦/平方米·度(W/㎡·K, 对于低粘度流体(μi<2μa, μa为常温下水的粘度),可用
(1)算术平均温度差
Δtm1= (Δt1+ Δt2)/2 (2)对数平均温度差
Δtm2= (Δt2- Δt1)/ln (Δt2 / Δt1) 式中 Δtm2——较大的温度差;
Δtm1——较小的温度差。 当Δtm1/ Δtm2<2时,采用算术平均温度差,否则采用对数 平均温度差。在计算平均温度差时,对无相变的对流传热, 逆流的平均温度差大于并流的平均温度差,因而在工业设 计中在工业设计中,在满足工艺条件的情况下,通常选用 逆流。
若考虑换热器对外界环境的散热损失Qc,则热流体放 出的热量Q1将大于冷流体所吸收的热量Q2 : Q1=Q2+Qc
Q2=ηcQ1 热损失系数ηc通常取; 不管师傅考虑热损失,在管壳式换热器的设计计算中, 热负荷Q一般取管内流体放出或吸收的热量。
总传热系数K
1/K=1/αo+1/αi(Ao/ Ai)+ro+ ri( Ao/ Ai)+ δAo/ λw Am 式中 αo——管外流体传热膜系数,W/(m2 · ℃);
雷诺数Re
Re=ρvd/μ ,其中v、ρ、μ分别为流体的流速、密度与黏 度,d为一特征长度。例如流体流过圆形管道,则d为管 道直径。利用雷诺数可区分流体的流动是层流或湍流,也 可用来确定物体在流体中流动所受到的阻力。
热管换热器计算书

热管换热器设计计算1 确定换热器工作参数1.1 确定烟气进出口温度t 1,t 2,烟气流量V ,空气出口温度t 2c,饱和蒸汽压力p c .对于热管式换热器,t 1范围一般在250C ~600C 之间,对于普通水-碳钢热管的工作温度应控制在300C 以下.t 2的选定要避免烟气结露形成灰堵及低温腐蚀,一般不低于180C .空气入口温度t 1c.所选取的各参数值如下:2 确定换热器结构参数2.1 确定所选用的热管类型 烟气定性温度: t f =t 1+t 22=420°C+200°C2=310°C在工程上计算时,热管的工作温度一般由烟气温度与4倍冷却介质温度的和的平均值所得出:烟气入口处: t i =t 1+t 2c ×45=420°C+152°C×45=180°C 烟气出口处:t o =t 2+t 1c ×45=200°C+20°C×45=56°C选取钢-水重力热管,其工作介质为水,工作温度为30C ~250C ,满足要求,其相容壳体材料:铜、碳钢(内壁经化学处理)。
2.2 确定热管尺寸对于管径的选择,由音速极限确定所需的管径d v =1.64√Q cr(ρv p v )12根据参考文献《热管技能技术》,音速限功率参考范围,取C Q 4kW =,在t o =56°C 启动时ρv =0.1113kg/m 3p v =0.165×105pa r =2367.4kJ/kg因此 d v =1.64√Q cr(ρv p v )12=10.3mm由携带极限确定所要求的管径d v =√1.78×Q entπ∙r(ρL −14⁄+ρv −14⁄)−2[gδ(ρL−ρv ]14⁄ 根据参考文献《热管技能技术》,携带限功率参考范围,取4Q ent =kw 管内工作温度 t i =180℃时ρL =886.9kg/m 3 ρv =5.160kg/m 3r =2013kJ/kg4431.010/N m δ-=⨯因此 d v =√1.78×4π×2013×(886.9−14⁄+5.16−14⁄)−2[g×431.0×10−4(886.9−5.160)]14⁄=13.6mm考虑到安全因素,最后选定热管的内径为m m 22d i =管壳厚度计算由式][200d P S iV σ=式中,V P 按水钢热管的许用压力228.5/kg mm 选取,由对应的许用230C 来选取管壳最大应力2MAX 14kg/mm σ=,而2MAX 1[] 3.5/4kg mm σσ==故 0.896mm 3.52000.02228.5S =⨯⨯=考虑安全因素,取 1.5S mm =,管壳外径:m m 25.51222S 2d d i f =⨯+=+=. 通常热管外径为25~38mm 时,翅片高度选10~17mm (一般为热管外径的一半),厚度选在0.3~1.2mm 为宜,应保证翅片效率在0.8以上为好.翅片间距对干净气流取2.5~4mm ;积灰严重时取6~12mm ,并配装吹灰装置.综上所述,热管参数如下:翅片节距:'415f f f S S mm δ=+=+= 每米热管长的翅片数:'10001000200/5f f n m S === 肋化系数的计算:每米长翅片热管翅片表面积22[2()]14f f o f f f A d d d n ππδ=⨯⨯-+⋅⋅⋅⋅每米长翅片热管翅片之间光管面积(1)r o f f A d n πδ=⋅⋅-⋅每米长翅片热管光管外表面积o o A d π=⋅ 肋化系数:22[2()]1(1)4f o f f f o f f f rood d d n d n A A A d ππδπδβπ⨯⨯-+⋅⋅⋅⋅+⋅⋅-⋅+==⋅22[0.5(0.050.025)0.050.001]2000.025(10.2)8.70.025⨯-+⨯⨯+⨯-==2.3 确定换热器结构将热管按正三角形错列的方式排列,管子中心距S ′=(1.2~1.5)d f 取S ′=70mm 。
列管式换热器的计算

列管式换热器的计算列管式换热器是一种常见的热交换设备,用于将热量从一个流体传递给另一个流体。
它由一组管子和外壳组成,热量通过管壁传递。
在设计或计算列管式换热器时,需要考虑各种参数和因素。
下面将详细介绍列管式换热器的计算方法。
首先,需要确定列管式换热器的传热面积。
传热面积影响热量传递的效率,可以通过以下公式计算:A=n×π×D×L其中:A表示传热面积(m2)n表示管子数量D表示管子外径(m)L表示管子长度(m)然后,需要计算每个管子的传热系数。
传热系数表示单位面积上的传热量,可以通过以下公式计算:U=(1/(1/h_i+δ_i/k_i+1/h_o))其中:U表示总传热系数(W/(m2·K))h_i表示内壁对流传热系数(W/(m2·K))δ_i表示管壁导热系数(W/(m·K))k_i表示管壁导热系数(W/(m·K))h_o表示外壁对流传热系数(W/(m2·K))对流传热系数可以通过经验公式、实验或计算获得。
管壁导热系数可以根据管材的材料及厚度获得。
接下来,需要计算传热器的热负荷。
热负荷表示单位时间内流体传递的热量,可以通过以下公式计算:Q=m×Cp×ΔT其中:Q表示热负荷(W)m 表示流体的质量流量(kg/s)Cp 表示流体的定压比热容(J / (kg·K))ΔT表示流体进出口温度的温差(K)最后,需要计算传热器的温度差。
温度差表示流体进出口温度之间的差距,可以通过以下公式计算:ΔT = (T_i - T_o) / ln(T_i / T_o)其中:ΔT表示温度差(K)T_i表示进口温度(K)T_o表示出口温度(K)根据以上公式,可以计算出列管式换热器的传热面积、传热系数、热负荷和温度差。
这些参数和结果对于合理设计和选择列管式换热器非常重要。
- 1、下载文档前请自行甄别文档内容的完整性,平台不提供额外的编辑、内容补充、找答案等附加服务。
- 2、"仅部分预览"的文档,不可在线预览部分如存在完整性等问题,可反馈申请退款(可完整预览的文档不适用该条件!)。
- 3、如文档侵犯您的权益,请联系客服反馈,我们会尽快为您处理(人工客服工作时间:9:00-18:30)。
缠绕管式换热器的简捷计算曲 平 王长英 俞裕国(大连理工大学化工学院,辽宁大连,116012)摘要 建立了缠绕管式换热器简捷计算的数学模型。
并对某厂各缠绕管式换热器进行了核算与扩产110%工况的计算。
计算结果表明所建数学模型基本合理、可靠。
关键词 缠绕管式换热器 数学模型 简捷计算 缠绕管式换热器(CTH E )的发展与深冷技术的发展密切相关,最早是由德国的林德公司于1898年制造。
我国一些化肥厂引进了该公司生产的这种类型的换热器。
缠绕管式换热器的结构紧凑,传热效率高。
其单位体积的换热面积大,适合深冷系统的换热。
但其制造工艺要复杂一些,对材质的要求相对较高;此外,设备的清洗也比较困难。
文中建立了缠绕管式换热器简捷计算的数学模型。
并对某厂的缠绕管式换热器进行了换热面积与压力损失的核算,计算结果表明了所建数学模型的可靠性,在此基础上,对扩产110%的情况进行了缠绕管式换热器的计算。
本工作能够为装置扩产改造的核算提供参考依据。
1 缠绕管式换热器模型的建立111 几何结构模型[1]图1 缠绕管式换热器的几何结构示意图图2 错流流动示意图 假设在壳侧流体流动方向上相邻两绕管间距为一常数,且相反缠绕方向的相邻两绕管的相对位置为x ,则有两个特征位置: 收稿日期:1998-01-13。
S m ax ={[(c +d )2]2+(a +d )2}1 2-d ,当x =(c +d )2时(1)S m in =a ,当x =0时(2)相邻两绕管的间隙S m 将处于S m ax 与S m in 之间,其计算公式:S m =[2(c +d )]∫(c +d ) 2S d x(3)积分结果:S m =a +d2[1+(c +d 2a +2d )]1 2+(a +d )2c +d·ln {c +d 2a +2d +[1+(c +d 2a +2d)2]12}-d (4)壳侧流道截面积:S 0=D m ΠkS m -(S 1+S 2)(5)其中:S 1=Πa 2110107·k 4(6)S 2=Πc 2(n -k )l(410l c )(7)D m =D i +(k -1)a +kd +S m(8)由壳侧流道截面积可求得壳侧流道的当量直径:D e =410S 0 L(9)浸润周边L =210(ΠD m +kS m )(10)传热管的缠绕角为Α与缠绕管换热器的轴向管束1998年 大 氮 肥L arge Scale N itrogenous Fertilizer Industry 第21卷 第3期长度l c 、缠绕圈数W j 的关系分别为:l c =l sin Α(11)W j =l co s Α (ΠD j )(12)各缠绕管层j 的中心圆平均直径D j 为:D j =D i +(j -1)a +jd +2e(13)式中,e 是第1层绕管与芯筒之间的隔板厚度,m 。
对于多流股(共m 个)缠绕管换热器,设第i 流股的管长为l i ,管子根数为z i ,则总的壳侧换热面积为:A 0=2m i =1A i =Πd 2m i =1z i l i (14)112 壳侧传热膜系数模型[2]缠绕管式热换器中,传热管在缠绕芯筒周围介于隔板中间呈螺旋状依次缠绕多层,形成圆筒状盘管而构成流道。
传热管的缠绕方向逐层相反,缠绕角与纵向间距通常是均匀的,且管长相同。
因此,随着传热管缠绕直径的增加,各层传热管数目也随之成比例增加。
这些盘管层所组成的管束,其壳侧流道形式因圆周方向位置的不同而变化,由于相邻两个盘管呈直列、错列的变化,则流道构成就变成管子布置为直列、错列组合排列时的管外流动的流道构成。
传热膜系数:a 0=01338F tF iF n R e 01610P r 013330(Κ0 D e )(15)其中,F t ——管子排列(流道结构)修正系数;F i ——管子倾斜修正系数;F n ——管排数修正系数。
F i =[co s Β]-0161{(1-<90)co s <+<100sin <}< 235(16)Β如图2所示,表示实际流动方向偏离盘管中心线方向的角度:Β=Α(1-Α90)(1-k 0125)(17)<=Α+Β(18)k —盘管的特性数,盘管层左右缠绕交替时,值取1;仅一个方向缠绕时,值取0。
F n =1-01558n +01316n 2-01112n3(19)其中,n 是流动方向一条直线上的管排数。
当n >10时,可近似认为F n =1。
F t =(F in-line +F staggerd2)(20)直列布置时的修正系数F in-line 与规则错列布置时的修正系数F staggerd 可由文献[2]查得。
113 管侧传热膜系数模型[2]从层流到紊流过渡的临界雷诺数:(R e )c =2300[1+816(d i D m )0145](21)①当10010<R e <(R e )c 时Αi ={3165+0108[1+018(d i D m )019]R e i i·P r i 01333}(Κi d i )(22)i =015+012903(d i D m )01194(23)②当(R e )c <R e <2200010时Αi ={01023[1+1418(1+d i D m )·(d i D m )01333]R e i i P r i 01333}(Κi d i )(24)i =018-0122(d i D m )011(25)③当2200010<R e <150000时Αi ={01023[1+316(1-d i D m )(d i D m )018]·R e 018i P r i 01333}(Κi d i )(26)114 总传热系数与总传热面积的计算总传热系数K =11 Α0+R 0+(bd ) (Κd m )+d (Αi d i )+R i dd i (27)总传热面积A =Q∗Εm ∃t m(28)平均温差∃t m =∃T 1-∃T 2ln (∃T 1∃T 2)(29)其中:∃T 1=T 1-t 2,∃T 2=T 2-t 1Εm 为平均温差校正系数。
115 压力损失的计算[2]11511 壳程压力损失∃P 0=01334C t C i C nnG 22g c Θ0(30)传热管倾斜修正系数C i =(co s Β)-118(co s <)11355(31)管排数修正系数Cn =019524(1+01375n)(32)管子布置修正系数C t =C in-line+C staggerd2(33)直列布置时的修正系数C in-line 与规则错列布置时的修正系数C staggerd 可由文献[2]查得。
11512 管程压力损失∃P i =f i G 2i 2g c Θi (ld i)(34)摩擦系数f i =[1+28800R e i (d i D m)0162]013164(R e i )0125(35)2 缠绕管式换热器的计算用所建立的缠绕管式换热器的模型,对某厂的几台缠绕管式换热器进行了核算,以验证其模型的准确度。
在此基础上进行了扩产110%工况·971·第3期曲 平等1缠绕管式换热器的简捷计算下各缠绕管式换热器所需的管长、传热面积及壳、管程压力损失的计算。
对多流股(管侧)换热器,采取分别计算单一流股换热器的处理策略,壳侧流股分别与管侧流股换热,其流率按各管侧流股所需的换热负荷大小成比例分配,总传热面积为各流股所需换热面积之和。
211 缠绕管式换热器的核算核算结果见表1。
由表1中数据可知所建立的模型基本符合设计要求。
在此基础上进行了扩产110%工况中缠绕管式换热器的模拟计算。
212 扩产110%工况下缠绕管式换热器的计算针对扩产110%工况(由于温度的变化,其换热负荷并不一定增加10%),进行了各缠绕管式换热器的计算,其结果见表2。
由表2中数据可知,E 6、E 7和E 8的热负荷均减少,而总传热系数却增大了,使得所需换热面积减小。
同时E 9与E 10的所需面积增大很多,其原因:热负荷虽相应增大,但平均传热温差却变小了,所以,总传热系数的增大也不能使这两台换热器满足换热要求。
表1 缠绕管式换热器核算结果E 1E 6E 7E 8E 9E 10管长 m 设计值计算值传热面设计值积 m 2计算值壳程压力设计值损失 kPa 计算值管程压力设计值损失 kPa 计算值换热负荷 k W总传热系数 W ·K -1·m -2平均温差 K 面积裕度,%19101,8183,818315180,6118,419010351287041559106518929162,58139,3910213156,20145,11114328211765210,24119,169159130,15198,231304619432185,3218526141,221681949112144715180102814727122,2516319143,15155458213031519,3571511123,8145341653218721166230192152114100107714415110761181137016396419916851178281312412124312520810229134231581501451091269691128371251771619415811012814520191051640135917261072441161651597320178620127146231098412865110157110212131644189312419111944182653416167615911729145表2 扩产110%工况缠绕管式换热器计算结果E 1E 6E 7E 8E 9E 10管长 m 传热面积 m2壳程压力损失 kPa 管程压力损失 kPa 换热负荷 k W总传热系数 W ·K -1·m -2平均温差 K 面积裕度,%16157,6194,4137720194612316172,30108,9120356414668213,25119,181169130,15198,231304316013167,15167874182291108168,8189444310051713,480169180,1111712218016103112161801835114813341001040191113910510620106172135241609711382610088313516341113233111297619461402761368102100641164140-3211811115120781764110851627215100640175162-241433 结论(1)建立了缠绕管式换热器简捷计算的数学模型。