设计工艺性检查
简述TPR塑料注塑成型加工前材料和工艺性能检测

简述TPR塑料注塑成型加工前材料和工艺性能检测TPR(热塑性橡胶)是一种具有橡胶弹性和塑料可加工性的材料,常用于注塑成型加工。
在进行TPR塑料注塑成型加工前,需要进行材料和工艺性能检测,以确保产品质量和生产效率。
本文将简述TPR塑料注塑成型加工前的材料和工艺性能检测。
一、TPR塑料的材料检测:1.外观检测:通过目视检查TPR塑料的颜色、表面光洁度、气泡、杂质等外观问题,确保材料质量。
2.密度检测:使用密度计对TPR塑料样品进行密度测量,了解其物理特性和杂质含量。
3.熔流率检测:通过熔流指数测试仪测量TPR塑料的熔流指数,评估其流动性和加工性能。
4.硬度检测:使用硬度计对TPR塑料进行硬度测量,了解其弹性和硬度特性。
5.拉伸强度和断裂伸长率检测:通过拉伸试验仪测量TPR塑料的拉伸强度和断裂伸长率,评估其机械性能和韧性。
6.热稳定性检测:通过热膨胀系数测试仪对TPR塑料进行热稳定性检测,了解其热性能和稳定性。
二、TPR塑料的工艺性能检测:1.熔融指数检测:通过熔融指数仪测试TPR塑料在不同温度和压力条件下的熔融指数,评估其熔融流动性。
2.热稳定性检测:使用热膨胀系数测试仪对TPR塑料进行热稳定性检测,了解其在高温下的热膨胀性。
3.压缩回弹率检测:通过压缩试验仪测量TPR塑料的压缩回弹率,评估其弹性恢复性能。
4.硬度检测:使用硬度计对TPR塑料的硬度进行测量,了解其硬度特性及变化。
5.热导率检测:使用热导率仪对TPR塑料的热导率进行测量,评估其热传导性能。
6.耐候性检测:通过模拟环境测试,如光老化试验、盐雾试验等评估TPR塑料的耐候性能。
综上所述,TPR塑料注塑成型加工前的材料和工艺性能检测对于确保产品质量和生产效率至关重要。
通过对TPR塑料的外观、密度、熔流率、硬度、拉伸强度、断裂伸长率、热稳定性等方面进行检测,可以评估其材料特性。
通过熔融指数、热稳定性、压缩回弹率、硬度、热导率、耐候性等方面的检测,可以评估其工艺性能。
结构设计规范检查表
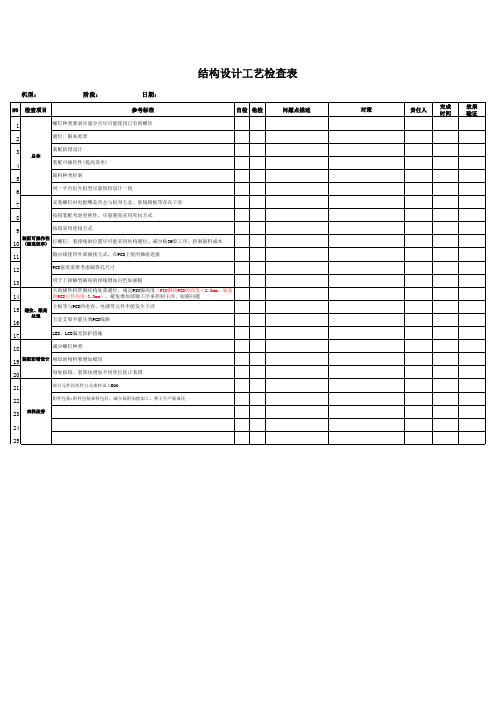
机型:
阶段:
日期:
NO 检查项目
参考标准
自检 他检
1
螺钉种类要求尽量少且尽可能使用已有的螺丝
2
பைடு நூலகம்避位、限高处理
3
总体
装配防错设计
4
装配可操作性(提高效率)
5
辅料种类控制
6
同一平台衍生机型尽量保持设计一致
7
安装螺钉时电批嘴是否会与机身五金、软线路板等存在干涉
8
按钮装配考虑更换性,尽量避免采用死扣方式
14
距PCB元件高度>3.0mm),避免增加剪脚工序来控制干涉、短路问题
15 避位、限高 主板等与PCB的电容、电感等元件不能发生干涉
处理
16
五金支架不能压到PCB线路
17
LED、LCD漏光防护措施
18
减少螺钉种类
19 装配防错设计 相似的物料要增加模印
20
每处按钮、装饰块增加不同骨位防止装错
21
部分元件以组件方式来料录入BOM
22
附件包装:附件包装来料包好,减少低附加值加工,利于生产集成化
23 来料改善
24
25
问题点描述
对策
责任人
完成 时间
效果 验证
9
按钮采用连钮方式
10
装配可操作性 (提高效率)
打螺钉、装排线的位置尽可能采用结构避位,减少贴3M胶工序,控制辅料成本
11
输出线使用外部插接方式,在PCB上使用插座连接
12
PCB宽度需要考虑邮票孔尺寸
13
用于上接触型插座的排线增加白色加强板
大的插件料管脚结构处需避位,规定PIN脚高度(PIN脚距PCB的高度<2.0mm,底盖
工艺验证的一般原则和方法
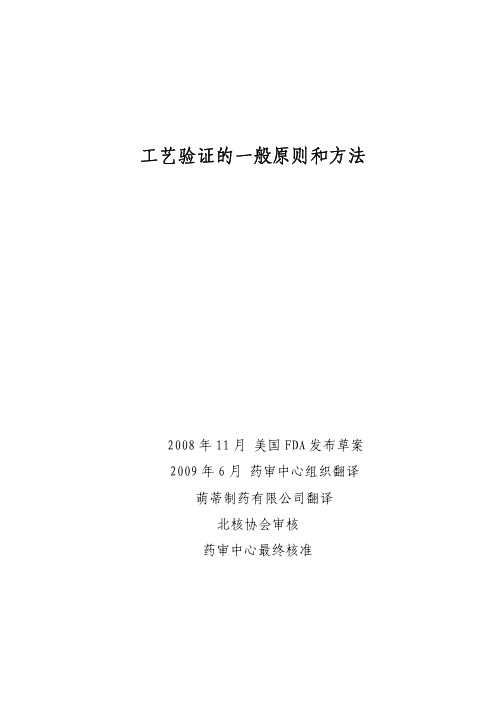
工艺验证的一般原则和方法2008年11月 美国FDA发布草案 2009年6月 药审中心组织翻译 萌蒂制药有限公司翻译北核协会审核药审中心最终核准目录I. 前言 (1)II. 背景 (2)III. 工艺验证的法规要求 (3)IV. 对企业的建议 (5)A. 工艺验证的一般考虑 (5)B. 药品生命周期中工艺验证的具体阶段与内容 (5)1. 第1阶段——工艺设计 (5)2.第2阶段——工艺评价 (8)3. 第3阶段——持续工艺确证 (11)V. 性能确认批次的同步放行 (12)VI.文件整理 (13)VII.分析方法 (13)工艺验证的一般原则和方法I.前言本指南概述了工艺验证的一般原则与方法,这些原则与方法是FDA认为对生产化学药品以及生物制品,包括活性药物成分(活性药用成份(API)或原料药)的工艺进行验证的适用要素,所生产的对象在本指南中统称为药物或产品。
本指南综合了一般的原则和方法,所有的生产企业都可以将这些原则和方法应用于生产工艺的验证。
本指南将工艺验证与产品生命周期概念以及现有FDA指南1进行了整合。
生命周期这一概念将产品与工艺开发、规模化生产工艺的确认以及保持工艺在日常规模化生产中的可控状态连结在一起。
本指南提倡现代化的生产原则,工艺改进和创新,以及合理的科学。
以下类别的药品涵盖于本指南所讨论的范围内:•人用药品•生物制品和生物技术产品•制剂产品与活性药用成分(API或原料药)2•复方产品(药物和医疗设备)中的药物成分本指南不适用于以下类别的产品:•A类添加药物的产品与添加药物的饲料•医疗设备•膳食补充剂•公共卫生服务法361节下的移植用人体组织3本指南没有具体说明哪些信息应包括在注册提交文件中,有兴趣的人士可以参照适当的指南或与相应的中心联系,以确定哪些信息应包括在内。
本指南也没有专门讨论自动化工艺控制系统的验证(例如计算机硬件和软件1参见FDA/ICH行业指南:Q8药品研发,Q9质量风险管理以及完成后的Q10药品质量体系(2007年5月的ICH-Q10草案可以在2007年7月13日发布的联邦公报(72 FR 38604)中获得)。
五金模具设计图纸检查项目
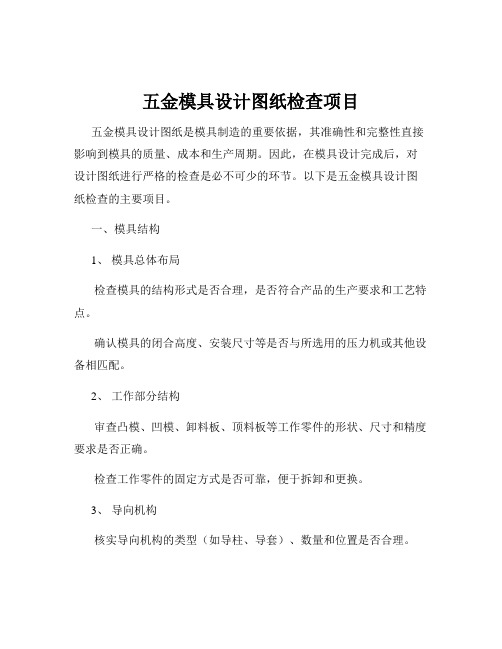
五金模具设计图纸检查项目五金模具设计图纸是模具制造的重要依据,其准确性和完整性直接影响到模具的质量、成本和生产周期。
因此,在模具设计完成后,对设计图纸进行严格的检查是必不可少的环节。
以下是五金模具设计图纸检查的主要项目。
一、模具结构1、模具总体布局检查模具的结构形式是否合理,是否符合产品的生产要求和工艺特点。
确认模具的闭合高度、安装尺寸等是否与所选用的压力机或其他设备相匹配。
2、工作部分结构审查凸模、凹模、卸料板、顶料板等工作零件的形状、尺寸和精度要求是否正确。
检查工作零件的固定方式是否可靠,便于拆卸和更换。
3、导向机构核实导向机构的类型(如导柱、导套)、数量和位置是否合理。
确保导向精度能够满足模具的工作要求,防止模具在工作过程中出现偏移或卡死现象。
4、卸料与顶出机构检验卸料装置和顶出机构的结构是否能够顺利卸料和顶出制件,且动作灵活、无干涉。
确定卸料力和顶出力的大小是否足够,弹簧、橡胶等弹性元件的选型是否合理。
二、尺寸精度1、零件尺寸仔细核对模具中各个零件的尺寸标注是否清晰、准确,有无遗漏或错误。
检查配合尺寸的公差配合是否合理,满足装配和工作要求。
2、模具型腔尺寸根据产品的尺寸要求和公差,验证模具型腔的尺寸计算是否正确。
考虑模具的磨损、收缩等因素,对型腔尺寸进行适当的修正。
3、冲裁间隙对于冲裁模具,检查冲裁间隙的取值是否符合材料的厚度和性能要求。
确保冲裁间隙均匀分布,以保证冲裁件的质量和模具的寿命。
三、材料与热处理1、零件材料确认模具零件所选材料的牌号、性能是否满足工作条件和使用寿命的要求。
检查材料的成本是否合理,在满足性能的前提下尽量降低成本。
2、热处理要求核实需要进行热处理的零件,其热处理工艺(如淬火、回火、氮化等)是否正确。
明确热处理后的硬度要求和硬度检测部位,以保证零件的强度和耐磨性。
四、加工工艺性1、结构工艺性评估模具结构是否便于机械加工、装配和调试。
避免出现尖角、薄壁、深孔等难以加工的结构。
新版GMP对工艺验证要求及思路

新版GMP对工艺验证要求及思路内容工艺验证的新思路工艺验证的新思路工艺验证应当证明一个生产工艺按照规定的工艺参数能够持续生产出符合预定用途和注册要求的产品。
中国2010版收集并评估从工艺设计阶段一直到商业化生产的数据用这些数据确立科学证据证明该工艺能够始终如一地生产出优质产品。
FDA2011书面化的证据证明工艺在所建立的参数范围内能有效和重复生产出符合预期标准和质量属性的医药产品。
EU2001规定的工艺能始终如一地生产出符合预期标准和质量属性的产品。
PIC/S2001确认的定义证明厂房、设施、设备能正确运行并可达到预期结果的一系列活动。
验证的定义证明任何操作规程或方法、生产工艺或系统能够达到预期结果的一系列活动。
第一百三十八条企业应当确定需要进行的确认或验证工作以证明有关操作的关键要素能够得到有效控制。
确认或验证的范围和程度应当经过风险评估来确定。
第一百三十九条企业的厂房、设施、设备和检验仪器应当经过确认应当采用经过验证的生产工艺、操作规程和检验方法进行生产、操作和检验并保持持续的验证状态。
第一百四十条应当建立确认与验证的文件和记录并能以文件和记录证明达到以下预定的目标一设计确认应当证明厂房、设施、设备的设计符合预定用途和本规范要求二安装确认应当证明厂房、设施、设备的建造和安装符合设计标准三运行确认应当证明厂房、设施、设备的运行符合设计标准四性能确认应当证明厂房、设施、设备在正常操作方法和工艺条件下能够持续符合标准五工艺验证应当证明一个生产工艺按照规定的工艺参数能够持续生产出符合预定用途和注册要求的产品。
第一百四十一条采用新的生产处方或生产工艺前应当验证其常规生产的适用性。
生产工艺在使用规定的原辅料和设备条件下应当能够始终生产出符合预定用途和注册要求的产品。
第一百四十二条当影响产品质量的主要因素如原辅料、与药品直接接触的包装材料、生产设备、生产环境或厂房、生产工艺、检验方法等发生变更时应当进行确认或验证。
工艺及设备检查表(1)

三
安全附件
1
安全阀必须由有检验资格的部门每年进行一次校验。
《压力容器安全技术监察规程》第154条
安全阀已检测,见附件
符合
2
安全阀应垂直安装并应设在压力容器液面上的气相空间部分或装在压力容器气相空间相连的管道上。
《压力容器安全技术监察规程》第152条
垂直安装,安装在压力容器液面以上气相空间部分
符合
成品罐区接地设施已设断接卡。
符合
11
液化烃储罐成组布置时,罐组内的储罐不应超过2排。
《石油化工企业设计防火规范》GB50160-2008第6.3.2
现场为2排设置
符合
12
液化烃储罐的安全阀出口管应接至火炬系统
《石油化工企业设计防火规范》GB50160-2008第6.3.13
安全阀出口管接至火炬系统
符合
GB50160-2008第8.3.8
设有又动力源;柴油机的油料储备量能满足机组连续运转6h
符合
5
可燃液体的储罐区、可燃气体储罐区、装卸区及化学危险品仓库区应设环形消防车道,当受地形条件限制时,也可设有回车场的尽头式消防车道。消防车道的路面宽度不应小于6m,路面内缘转弯半径不宜小于12m,路面上净空高度不应低于5m。
符合
2
消防水泵房宜与生活或生产水泵房合建,其耐火等级不应低于二级。
GB50160-2008第8.3.3
消防水泵房与循环水泵房合建,耐火等级为二级。
符合
3
消防水泵的出水管应设防止超压的安全设施。
GB50160-2008第8.3.5
出口设有电接点压力表,压力高时自动停泵
符合
4
消防水泵应设双动力源;当采用柴油机作为动力源时,柴油机的油料储备量应能满足机组连续运转6h的要求
公路工程施工工艺检查报告

公路工程施工工艺检查报告一、项目简介本次工程为某A省S市境内的一条市政公路的改扩建工程,总长约10公里,设计标准为城市次干道。
工程涉及路基、路面、排水、交通标志标线等方面。
二、施工工艺检查1.路基工程在现场检查中发现,路基填土质量符合设计要求,压实度满足规范要求。
但存在填土坡度施工不够均匀的情况,需要及时调整,并配合检测单位进行检测。
2.路面工程路面材料应符合设计要求,厚度应符合标准。
现场检查发现,路面的平整度、均匀性和厚度均满足设计要求,但在铺设沥青时存在漏铺、漏铺、破损等情况,需要及时整改。
3.排水工程排水工程是公路建设中至关重要的一环。
现场检查发现,排水设施安装位置合理、施工质量符合规范要求。
但部分排水口堵塞,需要及时疏通。
4.交通标志和标线交通标志和标线的设置应符合设计规范,位置合理,清晰可辨。
现场检查发现,标线和标志设置不够清晰,需要及时重新设置,以确保交通安全。
三、存在的问题和建议1.路基填土均匀性需要加强,确保路基稳定性。
2.路面施工过程要严格控制,防止漏铺、漏铺导致的质量问题。
3.排水设施要及时清理,确保排水畅通。
4.交通标志和标线设置需要重新调整,保证交通安全。
四、施工进度和质量检查工程进度符合计划,施工质量整体满足规范要求。
但需要加强对施工过程的监督和管理,确保施工质量和安全。
五、结论通过本次工艺检查,发现了一些存在的问题,并提出了相应的整改建议。
下一步,施工方应按照要求进行整改,并加强对施工过程的监督和管理,确保工程质量和安全。
同时,施工方应严格按照设计标准和规范要求进行施工,确保工程如期竣工。
工艺纪律检查管理办法[优秀范文五篇]
![工艺纪律检查管理办法[优秀范文五篇]](https://img.taocdn.com/s3/m/3cad016ce55c3b3567ec102de2bd960590c6d9b8.png)
工艺纪律检查管理办法[优秀范文五篇]第一篇:工艺纪律检查管理办法工艺纪律检查管理办法目的为了健全和巩固公司(厂)正常生产秩序,提高产品质量和经济效益,必须加强工艺管理,严肃工艺纪律。
对生产工人加强工艺纪律教育,提高按图样及工艺文件要求生产的自觉性。
2 适用范围适用于公司(厂)工艺纪律检查和考核。
3职责生产厂总工程师负责组织生产技术科、安全质量科、工资科及车间等有关部门和人员进行检查。
4 管理要求4.1 严肃工艺纪律,严格按设计图样、工艺文件等技术文件的规定加工制作。
4.2 产品图样、工艺文件是企业的技术法规,是组织生产和判断质量的依据。
经逐级会签、审批、归档后,任何人不得任意更改。
如必须更改时应按《产品图样及工艺文件管理办法》进行。
4.3 如车间由于特殊原因需临时改变工艺者,需由施工人员编制《临时施工工艺卡》,并通知有关部门及工艺人员,并由技术部门根据实际情况下发《技术业务联系书》发可实施。
4.4 生产工人要认真做好操作前准备工作,按要求借全图样、工艺文件、工装,严格按规定进行操作。
必须保存好首件检验记录,并签名。
对完工的零件做好自分,养成轻放、涂油防锈的良好习惯。
选用合适的工位器具,防止零件磕碰划伤、锈蚀。
4.5 所有设备及工装的精度必须满足质量要求,其工作技术状态良好,工装必须按照有关制度规定进行复检和周期鉴定,以保证精度合格。
关键设备做好点检工作,保证设备完好。
4.6 对主要零件在加工前应做好三定(定人、定机、定工种)工作,以保证制作质量。
4.7 在积极开展群众性质量管理活动,大力推广QC小组活动中,对QC成果、合理化建议和技改成果,必须经过生产验证、并纳入有关设计、工艺文件,方可投入生产。
4.8原材料坯料种类必须符合工艺规定,如金属材料代用,应按有关规定办理。
4.9生产技术部门应指导车间加强工序质量管理,检验部门严格把好质量关,生产工人必须爱护图样、工艺卡,并保持清洁。
4.10对进厂的新工人,有关部门在组织新工人教育的同时,应加强质量意识和严格执行工艺纪律的教育,使新职工了解严格执行工艺纪律的重要性。
- 1、下载文档前请自行甄别文档内容的完整性,平台不提供额外的编辑、内容补充、找答案等附加服务。
- 2、"仅部分预览"的文档,不可在线预览部分如存在完整性等问题,可反馈申请退款(可完整预览的文档不适用该条件!)。
- 3、如文档侵犯您的权益,请联系客服反馈,我们会尽快为您处理(人工客服工作时间:9:00-18:30)。
设计工艺性检查 随着科学技术的飞速发展,现代产品的构造和功能越来越复杂,在保证产品性能、质量要求的前提下,如何降低制造成本和缩短产品的研制生产周期,是市场竞争取胜的关键。另外,在产品全寿命周期中,设计对产品的性能、质量和成本控制起着关键作用。一般情况下,设计费用约占产品总成本的5%,但却决定了产品总成本的约70%,而约80%的设计差错要到制造、使用过程才能发现。制造业公认的”十倍定律”表明,如果在概念设计阶段发现并改正一个错误所需费用为1,那么改正同一错误,在详细设计阶段所需费用为10,在生产制造阶段所需费用为100,并且直接造成制造周期的延长。 设计工艺性是产品设计工作中的一项重要因素,也是产品的固有属性之一,它直接决定了产品的可制造性,是采用经济、合理和可靠的方法制造产品的基础。因此,产品设计中选用合理的结构、合适的材料及工艺,在制造源头提高产品的设计工艺性,对保证产品的质量和可靠性、提高快速研制水平、增强产品批生产能力和有效控制成本有着重要的现实意义。 1、设计工艺性的内涵 设计工艺性与可制造性或可生产性在很大程度上表示的意义是一致的。美国军用标准MIL—STDl528《生产管理》中给出的定义是:”设计工艺性是多种特性的综合,即通过产品设计和生产策划,形成最有效的和经济的方法,进行产品的制造、装配、检查、试验、安装、检验和验收”;美国军用手册MIL—HDBK—727《可制造性设计导则》给出的定义是:”可制造性是设计要素、特性和生产策划的综合,通过折中权衡,在满足质量和性能要求前提下,使设计描述的产品,在最小可能成本和最短时间的优化方案下进行生产和检验”;美国国防部指令50000.34《生产管理》给出的定义是:”可制造性就是相对容易地生产出受设计特性和要求规定的产品或系统,即采用可利用的生产技术经济地制造、装配、检验和试验产品或系统”;原苏联航空工艺与生产组织科学研究院编写出版的《飞机构造工艺性指南》对设计工艺性的定义为:”构造工艺性是指在保证产品使用质量的条件下,在产品制造过程中,可以达到高生产指标的那些构造特性”;对工艺性的定义是:”在一定的产量和生产条件下,经综合权衡后,能以尽可能低的成本和短的周期制造出来,并能符合必须的使用性能和质量要求”的那些结构特性。 归纳上述定义可以看到:在从产品设计、材料、加工、装配、检验、试验到使用、维护的全寿命周期中均体现了产品的设计工艺性。因此,具有良好工艺性的设计应该是:具有适当技能的操作者,通过合理、经济的方法,采用经济和易获得的材料,在较短时间内,制造出满足技术要求的产品。 设计工艺性的内涵,可以归结为以下三点: 1)设计工艺性是产品的固有属性,产品结构设计的各种要素都对设计工艺性产生影响。 2)设计工艺性是对产品性能、生产周期、全寿命成本、可靠性、安全性和可维护性等的综合平衡优化的结果,其目标是在满足产品性能和可靠性要求的前提下,满足经济高效生产的要求。 3)设计工艺性不但与产品结构的要素相关,而且与工艺布局、设备条件等生产要素密切相关,同时与产品的生产批量密切相关。 2、设计工艺性工作的目标 设计工艺性是设计人员进行产品设计时必须考虑的重要因素之一。设计人员在产品设计伊始,不但要考虑产品性能和可靠性等方面的要求,还要考虑产品生产时的可制造性问题。另外,随着新材料、新工艺技术不断涌现,先进的制造方法不断发展,在材料、工艺、质量和可靠性等方面人员的合作和支持下,在产品研制和生产过程中不断对结构和工艺方法等进行各种权衡和优化,以持续改善产品的可制造性。 产品设计工艺性的目标概括来说,就是在满足产品性能、进度、质量、可靠性等要求的同时,依据现有生产条件,以最合理、最经济和最可靠的方式将其快捷地生产出来。 提高产品设计工艺性的目的主要是在以较低的成本、较短的生产周期得到产品的同时,对使用性能、可靠性和可维护性等设计要求不产生负面影响。 3、设计工艺性相关要素 设计工艺性虽不是一个独立的学科,但它涵盖了从产品设计、材料科学、工艺技术、制造工程、工业经济等到质量、可靠性、有效性和可维护性等诸多学科和领域。因此,与设计工艺性相关的影响要素很多。下面重点从设计和生产两个方面,对影响设计工艺性的要素进行分析。 3.1. 设计相关要素 3.1.1.简化设计、实现产品可生产 满足产品技术要求是设计产品的最基本要求,对产品技术要求的全面、正确理解对实现工艺性良好的产品至关重要。由于对产品技术要求理解不全面,往往导致对所设计产品的某一特性提出过高要求,可能对产品的工艺性产生严重损害。例如,对产品表面粗糙度提出过高的要求,有时会导致产品合格率下降、制造周期和成本大幅提高。另外,采用复杂的方法满足设计要求将导致制造成本增加,也会影响生产周期,同时增加可靠性、有效性和可维护性的成本。如图3-1;图3-2所示。 图3-1 图3-2 DFA的实质是:使所设计的产品结构:减少产品结构中的零件数,减少所需装配工序与装配方法。 DFM的实质是:使所设计的产品结构:能便于制造,成本最少,能符合企业现有的生产能力。 3.1.2. 元器件、原材料选择 对于选择材料满足产品设计目标要求,材料的力学、物理和化学性能构成了基本的设计准则,这些性能将影响制造工艺的选择。因为在可成形性、可加工性、连接、热处理及表面处理等方面存在相互影响。设计应规定尽可能多的材料选择,以拓宽潜在制造工艺的种类,并且允许用非稀缺材料和非战略材料进行替代,仅指定一种材料的设计将限制其与制造过程的兼容性。如图3-3所示。 图3-3 3.1.3. 工艺选择 仅有一种材料或制造工艺才能满足产品设计目标要求的情况很少,多数情况下,多种材料和工艺中的任何一种都可以制造出满足要求的产品。通过预计由于材料短缺或可应用工艺不足形成的”瓶颈”而确定替代材料和工艺,会极大提高产品的可制造性。 3.1.4. 容错及公差要求 不必要的严格公差和表面粗糙度要求对可制造性是极为不利的,有时需要采用更专用、特殊的工艺过程或依赖操作者的特殊技能才能保证达到严格的公差和粗糙度要求。因此,应规定满足产品要求的最低的质量等级。 3.1.5 产品技术基线状态确定 技术状态确定原则 1)在设计和研制中,选择满足用户需求和技术指标要求的成熟资源平台作为技术状态基线,产品的方案、技术和产品尽量继承资源平台系列产品以及成熟的产品或设计技术; 2)产品的型谱内产品为基础,最大程度的利用成熟技术和成熟产品,提高研制质量,确保研制进度; 3)充分利用和完善已有的预研成果; 4)汲取在研制过程中的经验和教训,注意和跟踪其它产品研制过程中出现的问题和解决措施,落实在方案设计和产品研制之中。 3.1.6.部件选择 应尽可能选择标准的、摸块化的部件来完成规定的功能。进行新产品设计时,尤其应注意在继承与创新之间做好平衡。新部件过多,则产品的研制周期和生产成本会大幅增加。 3.1.7 试验、检验和维护 产品的试验、检验,是产品生产、组装、交付等质量保证的必要过程,在产品设计时必须考虑这些过程对产品分离面设置、工艺选择、流程设置等的影响。另外,产品设计时必须考虑产品使用的维护性。 3.1.8 设计文件与产品定型 设计成套技术文件传递的信息准确可靠,对设计目标的成功生产至关重要。不清晰的模糊的或不完整的设计信息对可制造性是有害的。产品的成套技术文件直接影响工艺选择,工艺师应在设计文件会签过程中仔细审查和把关。设计工艺性审查《设计阶段》如图3-4所示;设计工艺性审查《工艺方面》如图3-5所示;设计工艺性审查《生产方面》如图3-6所示。
图3-4 图3-5 图3-6 4: 下面的三个基本过程(目标评估、分析改进、文件编制)分别加以说明。 4.1 复审所有设计明确性是十分必要的。 4.2 设计工艺性工作流程 在产品设计过程中,设计工艺性问题是一个最基本,也是非常重要的设计要素。围绕产品设计中目标评估 正确的定义问题是解决问题的关键,因此,评价这一环节的重要性不容忽视。系统的技术条件应该包括性能指标、设计约束和可制造性目标。然而,性能指标和可制造性目标经常出现矛盾,可制造性目标往往被忽略。只要企业拥有必需的基本设备和技术以及比较熟练的操作人员,就必须能够生产出设计者所设计的最终产品。鉴于这种原因,设计要求的完整性以及在性能指标、设计约束和可制造性目标之间的权衡十分重要。要求的完整性和分析改进 可行的方法很多,因此对于选取最有效方法的分析是必需的。特殊的问题可能促进一些相关方法、手段的发展,但需要选择设计方法的步骤是相同的。即使是一个很小的问题,分析的内容同样包括四项:设计选择中的风险、功能与成本、进度与成本、部件构成与生产能力。进度是设计工艺性的一个重要因素用1年内才能完成产品生产的制造工艺。 设计方案最终要转化成零件的制造和装配,从概念变得具体。产品尺寸、质量、单元结构可能性、可靠性和目标可维护性都将被审差、应力和配合的精确分析也将同时进行。 4.3 文件编制三维网技术论坛# F$ y5 {1 f2 L) E 文件编制是连接设计和生产的桥梁。它对无数的分析、调查、替代和改进结果进行详细说明。它是设计师、操作员、绘图员以及很料、人力和制造成本初步预算的工作手册。 另外,在设计工艺性工作流程阶段工作完成后,应由专门的设计工艺性评审专家组对产品设计工艺性工作进行审查、咨询,这对提高产品的可制造性是非常必要的。设计工艺性评审专家组的成员来自涉及产品的多个领域(如设计、制造、可靠性、材料以及物资保障等),组长一般由单位总工程师担任。专家组遵循一个基本原则来讨论和分根据可制造性因素,对新设计方案的设计工艺性提出审查意见和建议。一个要求在6个月出产品的项目,就不能采查。另外,载荷、压降、流量、加热率、偏
多其他人员之间的信息传达手段,是提供材
析产品的工艺性。。
(2):电子产品设计工艺性审查工作的主要流程如图4-2所示。 (1):结构件设计工艺性审查工作的一般流程如图4-1所示。