顶吹转炉

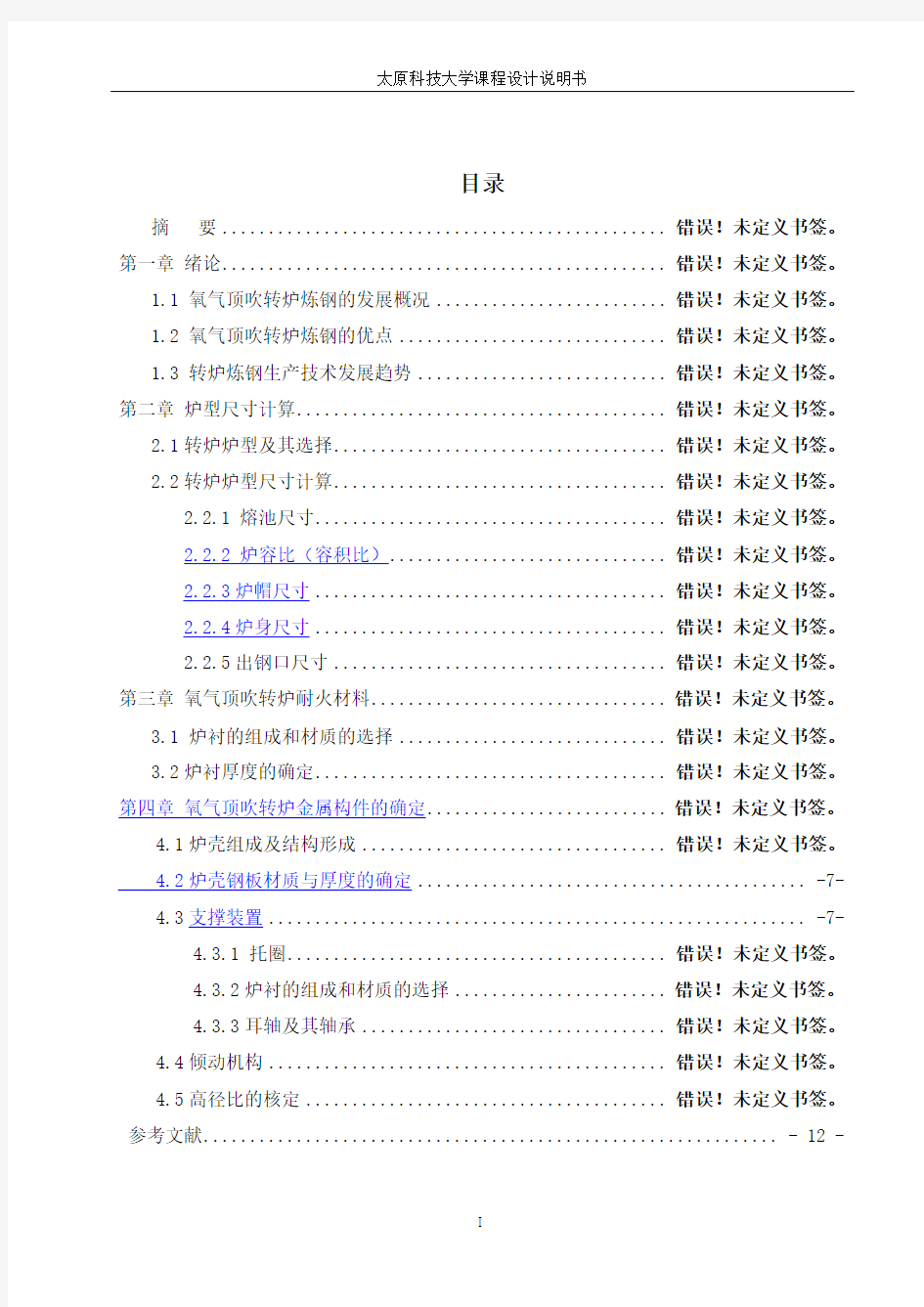
太原科技大学
课程设计说明书
设计题目: 50t 氧气顶吹转炉设计
设计人:郭晓琴
指导老师:杨晓蓉
专业:冶金工程
班级:冶金工程081401 学号: 200814070105
材料科学与工程学院
2011年12月30 日
目录
摘要................................................ 错误!未定义书签。第一章绪论................................................ 错误!未定义书签。
1.1 氧气顶吹转炉炼钢的发展概况......................... 错误!未定义书签。
1.2 氧气顶吹转炉炼钢的优点............................. 错误!未定义书签。
1.3 转炉炼钢生产技术发展趋势........................... 错误!未定义书签。第二章炉型尺寸计算........................................ 错误!未定义书签。
2.1转炉炉型及其选择.................................... 错误!未定义书签。
2.2转炉炉型尺寸计算.................................... 错误!未定义书签。
2.2.1 熔池尺寸...................................... 错误!未定义书签。
2.2.2 炉容比(容积比).............................. 错误!未定义书签。
2.2.3炉帽尺寸...................................... 错误!未定义书签。
2.2.4炉身尺寸...................................... 错误!未定义书签。
2.2.5出钢口尺寸.................................... 错误!未定义书签。第三章氧气顶吹转炉耐火材料................................ 错误!未定义书签。
3.1 炉衬的组成和材质的选择............................. 错误!未定义书签。
3.2炉衬厚度的确定...................................... 错误!未定义书签。第四章氧气顶吹转炉金属构件的确定.......................... 错误!未定义书签。
4.1炉壳组成及结构形成................................. 错误!未定义书签。
4.2炉壳钢板材质与厚度的确定 (7)
4.3支撑装置 (7)
4.3.1 托圈......................................... 错误!未定义书签。
4.3.2炉衬的组成和材质的选择....................... 错误!未定义书签。
4.3.3耳轴及其轴承................................. 错误!未定义书签。
4.4倾动机构........................................... 错误!未定义书签。
4.5高径比的核定....................................... 错误!未定义书签。参考文献.............................................................. - 12 -
50t氧气顶吹转炉设计
摘要
本文主要介绍了50T氧气顶吹转炉设计。炼钢过程就是铁水向钢水转变的过程,这对加入料及产物的成分、数量都有严格要求。氧气转炉炼钢在大型的钢铁企业中处于整个钢铁生产流程的中间环节,起到承上启下的作用,炼钢是决定钢材产量、质量的关键所在。氧气转炉炼钢环节的任何延误或产量、质量变化都会影响前后生产工序的协调运转。这都与转炉炼钢的设备、工艺、组织管理等因素有关。所以在设计氧气顶吹转炉时,应当处理好各种设计问题,为正常生产,保持良好的生产秩序打下基础。
关键词:氧气顶吹转炉;
第1章绪论
1.1 氧气顶吹转炉炼钢的发展概况
氧气顶吹转炉炼钢法是20世纪50年代产生和发展起来的炼钢技术,但从起初至今已有100多年历史。早在1856年英国人亨利·贝塞麦就研究开发了酸性底吹转炉炼钢法铁水为原料,从转炉底部通入空气氧化去除杂质冶炼成钢。第一次实现了液态钢冶炼的规模生产,从此进入了现代钢铁工业生产阶段。1878年德国尼·托马斯研究发明的碱性地吹转炉炼钢法,以碱性耐火材料砌筑炉衬,吹炼过程中加入石灰造渣,能够脱除铁水中的P、S,解决了高磷铁水冶炼技术问题。由于转炉炼钢法有生产率高,成本低,设备简单等优点,在欧洲得到迅速的发展,并成为当时主要的炼钢方法【1】
第二次世界大战之后,从空气中分离氧气技术的成功,提供了大量廉价的工业纯氧,使贝塞麦的氧气炼钢设想得以实现。由于氧气顶吹转炉炼钢首先在林茨和多那维茨两城投入生产,所以去这两个城市名称的第一个字母LD作为氧气顶吹转炉炼钢法的代称【10】。
LD炼钢法具有反应速度快,热效率高,又可使用约30%的废钢为原料:并克服了底吹转炉钢质量差,品种少的缺点;因而一经问世就显示出巨大的优越性和生命力。进入20世纪70年代以后,顶吹转炉炼钢技术趋于完善。转炉的最大公称吨位达380t;单位生产能力达到400~500万t/a;能够冶炼全部平炉钢种,若与有关精炼技术相匹配,还可以冶炼部分电炉钢种;大型转炉炉龄在1999年达到10000炉次/炉役以上;并实现了计算机控制终点碳与出钢温度。
1951年碱性空气侧吹转炉炼钢法首先在我国唐山钢厂实验成功,并于1952年投入工业生产。1954年开始了小型氧气顶吹转炉炼钢的实验研究工作,1962将首钢实验厂空气侧吹转炉改建成3t氧气顶吹转炉,开始了工业性实验[3]。在捡取得成功的基础上,我国第一个氧气顶吹转炉炼钢车间(2×30t)在首钢建成,于1964年12月26日投入生产。以后,又在唐山,上海,杭州等地改建了一批3.5~5t小型氧气顶吹转炉。1966年上钢一厂将原有的一个空气侧吹转炉炼钢车间,改建成3座30t的氧气顶吹转炉炼钢车间,并首次采用了先进的烟气净化回收系统,于当年8月投入生产,还建设弧形连铸机与之相配套,试验和扩大了氧气顶吹转炉炼钢的品种。这些都为我国日后氧气顶吹转炉炼钢技术的发展提供了宝贵经验。此后,我国原有的一些空气侧吹转炉车间逐渐改建成中小型氧气顶吹转炉车间,并建了一批中、大型氧气顶吹转炉车间。20世纪80年代宝钢从日本引进建成并
具有70年代末技术水平的300t大型转炉3座、首钢购入二手设备建成210t转炉车间;90年代宝钢又建成250t转炉车间,武钢引进250t转炉,唐钢建成150t转炉车间,重钢和首钢又建成80t转炉炼钢车间,许多平炉车间改建成氧气顶吹车间等。到1998年,我国氧气顶吹转炉共有221座,其中100t以下的转炉有188座,(50~90t的转炉有25座),100~200t的转炉有23座,200t以上的转炉有10座,最大公称吨位有300t。顶吹转炉钢占年总纲产量的82.67%。
1.2氧气顶吹转炉的优点[4]
LD法具有如下优点:
(1)吹炼速度快,生产率高;
(2)品种多,质量好;
(3)原材料消耗少,热效率高、成本低;
(4)基建投资省,建设速度快;
(5)容易与连续铸钢相匹配。
鉴于以上优点,氧气顶吹转炉炼钢现已成为主要炼钢方法。大型转炉有如下优点:(1)产量高、质量稳定(2)热损失小;(3)吨钢原材料消耗少;(4)易于实现自动控制;(5)生产率高、成本低。所以,国际、国内新建转炉向大型化发展。
1.3转炉炼钢生产技术发展趋势
(1)合理优化工艺流程,形成了紧凑的连续化专业生产线[5]
其目标是以产品为核心,将铁水预处理→炼钢→精炼→连铸和轧钢有机地
结合起来,形成紧凑式连续化生产的专业生产线。从铁水到成品钢材的生产周期将缩短到2.5~3h。铁水预处理对改进转炉操作指标及提高钢的质量又着十分重要的作用。美国及西欧各国铁水预处理只限于脱硫,而日本铁水预处理则包括脱硫、脱硅及脱磷的三脱处理。例如1989年日本经预处理的铁水比例为:NKK公司京滨厂为55%,新日铁君津厂为74%,神户厂为85%,川崎千叶厂为90%。
(2)转炉高速吹炼工艺技术[6]
目标是建立一座转炉吹炼制,使一座转炉的产量达到传统两座转炉的生产能力。冶炼周期20~25min,年产炉数≥15000炉,转炉炉龄≥15000炉。
(3)建立大规模、廉价生产洁净钢的生产体系[7]
提高钢水洁净度,即大大降低吹炼终点时的各种夹杂物含量,要求S含量低于0.005%;
P含量低于0.005%, N含量低于0.002%。提高化学成分及温度给定范围的命中精度,为此采用复合吹炼、对熔池进行高水平搅拌并采用现代检测手段及控制模型是十分必要的。另外要减少补吹炉次比例,降低吨钢耐材消耗。
(4)节能与环境保护[8]
其目的是转炉炼钢工序实现“负能”炼钢;炼钢渣量减少50%;全部粉尘回收利用。
第3章 50吨氧气顶吹转炉设计
3.1 转炉炉型及各部分尺寸
3.1.1 转炉炉型及其选择
转炉由炉帽、炉身、炉底三部分组成。转炉炉型是指由上述三部分组成的炉衬内部空间的几何形状。由于炉帽和炉身的形状没有变化,所以通常按熔池形状将转炉分为筒球型、锥球型和截锥型等三种。炉型的选择往往与转炉的容量
【4】
有关。
锥球型炉型的形状更符合钢渣环流的要求,炉衬蚀损后,其形状变化较小,对操作较为有利。在装入量和熔池深度均相同的情况下,增加了熔池反应界 面。而且我国过去已建成的30~80t 转炉多用锥球型,在中小型转炉的设计上应用较普遍,所以本次50t 氧气顶吹转炉采用锥球型炉型。 3.1.2转炉炉型各部分尺寸的确定
转炉炉型各部分尺寸,主要是通过总结现有转炉的实际情况,结合一些经验公式并通过模型试验来确定。 3.2.1 熔池尺寸
(1)熔池直径D 。熔池直径指转炉熔池在平静状态时金属液面的直径。 计算公式:t
G k D
式中:D ---熔池直径,m ; K ---系数,参见表3-1;
G ---新炉金属装入量,t ,可取公称容量;
t ---平均每炉钢纯吹氧时间,min ,参见表3-2.
表3-1 系数k 的推荐值 转炉容量/t
<30 30~100 >100 备注 k
1.85~
2.10
1.75~1.85
1.50~1.75
大容量取下限,小容量取上限。
表3-2平均每炉钢冶炼时间推荐表
转炉容量/t <30 30~100 >100 备注 冶炼时间/min
28~32 (12~16)
32~38 (14~18)
38~45 (16~20)
综合供养强度,铁水成分和所炼钢种等具体条件确定。
注:括号内系数系吹氧时间参考值。
确定吹氧时间t 和比例系数k :由表2-1和2-2知,t 取15min,k 取1.75 mm m D 320020.315
5075.1==?
=
(2)熔池深度h 。熔池深度指转炉熔池在平静状态时,从金属液面到炉底 的深度。对于一定容量的转炉,炉型和熔池直径确定之后,可利用几何公式计算熔池深度h 。锥球型熔池体积V 池和熔池直径D 及熔池深度h 有如下关系: V 池=0.62
-0.033D 3
因而 2
D
665.0033.0V h 3
D +=
池
确定熔池体积 V 3
3
m
37.6m
t 85.7t 50G ==
=
ρ
(钢液的密度取7.85t/m 3)
所以 00.1)
2.3(665.0)
2.3(03
3.037.6D
665.0D 033.0V h 2
3
2
3
≈??+=
+=
池m
(3)熔池其他尺寸的确定
①球缺体高度h 1:h 1=0.09D=0.09×3200=288mm; ②球缺底半径R : R=1.1D=1.1×3200=3520mm 。 3.2.2 炉容比(容积比)
炉容比指转炉有效容积Vt 与公称容量G 的比值Vt/G (m 3/t )。本次设计,炉容比为
t /m 90.0G
Vt 3
=得3
455090.090.0m
G V t =?=?=
3.2.3 炉帽尺寸
顶吹转炉一般是正口炉帽,其主要尺寸有炉帽倾角,炉口直径和炉帽高度。
(1)炉帽倾角θ。倾角过小,炉帽内衬不稳定,容易坍塌;过大则出钢时容易钢渣混出和从炉口大量流渣。倾角一般为60o ~80o ,小炉子取上限,大炉子取下限,这是因为大炉子的炉口直径相对要小些。
(2)炉口直径d 。在满足顺利兑铁水和加废钢的前提下,应适当减小炉口直径,以减少热损失。一般炉口直径为熔池直径的43%~53%较为适宜。小炉子取上限,大炉子取下限。 (3)炉帽高度H 帽。为了维护炉口的正常形状,防止因砖衬蚀损二使其进速扩大,在炉口上部设有高度为H 口=300~400㎜的直线段。因此炉帽高度为: 口帽)(H tan d -D 21
H +=θ
确定炉帽倾角θ,θ=65o
炉口直径d ,d=50%D=50%×3.2=1.6m H 口=400㎜=0.4m
H 帽=口)(H tan d -D 21
+θ=1/2×(3.20-1.60)×tan65o
+0.4=2.11m=2110mm
炉帽总容积V 帽为:
m
77.84.06.14
6.16.12.32.34.0-11.212H d 4
d Dd D H -H 12V 2
222
2
2=??+
+?+=+++=
πππ
π
))(())((口
口帽帽
3.2.4 炉身尺寸
转炉炉帽以下,熔池面以上的圆柱体部分称为炉身。其直径与熔池直 径是一致的,故需确定的尺寸是炉身高度H 身。 2
2
D
-V -V Vt 4D
V 4H ππ)
(池帽身
身=
=
式中 V 帽,V 身,V 池----分别为炉帽,炉身和熔池的容积。Vt---转炉的有效容积,为V 帽,V 身,V 池三者之和,取决于炉容量和炉容比。
所以 H 身mm 3710m 71.32
.314.337.6-77.8-454D V -V -Vt 42
2==?==)()(池帽π。
则有效高度:H 壳内=h+H 帽+H 身=1000+2110+3710=6820mm 。
3.2.5 出钢口尺寸
出钢口内口一般都设在炉帽和炉身交界处,以使转炉出钢时其位置最便于钢水全部出净。出钢口的主要尺寸是中心线的水平倾角和直径。
(1)出钢口中心线水平倾角θ1。为了缩短出钢口长度,以利于维修和减少钢液二次氧化及热损失,大型转炉的θ1趋于减小。国外不少转炉采用一般为15o~20o。本设计取20o。
(2)出钢口直径d出。出钢口直径决定着出钢时间,因此随炉子容量而异。出钢时间通常为2~8min。时间过短,难以控制下渣,且钢包内钢液静和吸气,散压力增长过快,脱氧产物不易上浮。时间过长,钢液容热也大。通常d出(cm)按下面经验公式确定:
d+
63
=
G
75
.1
出
式中 G---转炉公称容量,t。
。(取13cm)
63
?
d=
+
=
.1
+
=
50
.
27
cm
75
12
75
63
.1
G
出
出钢口砖衬外径:d出=6×130=780mm。
出钢口长度:L出=8×130=1040mm。
第三章氧气顶吹转炉耐火材料的选用
3.1炉衬的组成和材质的选择[11]
氧气转炉的炉衬一般由永久层,填充层和工作层组成。
(1)永久层。永久层紧贴炉壳(无绝热层时),修炉时一般不予拆除。其主要作用是保护壳,该层常用镁砖砌筑。
(2)填充层。填充层介于永久层与工作层之间,一般用焦油镁砂捣打而成,厚度约80~100mm。其主要功能是减轻炉衬受热膨胀时对炉壳产生挤压和便于拆除工作层。
(3)工作层。工作层系指与金属,熔渣和炉气接触的内层炉衬,工作条件极其苛刻。目前,该层多用镁碳砖和焦油白云石砖综合砌筑。
表3转炉炉衬厚度设计参考值
转炉容量/t
炉衬各部位名称
<100 100~200 >200
永久层厚度/mm 60~115 115~150 115~150
炉帽
工作层厚度/mm 40~600 500~600 550~650
永久层厚度/mm 115~150 115~200 115~200 炉身(加料侧)
工作层厚度/mm 550~700 700~800 750~850
永久层厚度/mm 115~150 115~-200 115~200 炉身(出钢侧)
工作层厚度/mm 500~650 600~700 650~750
永久层厚度/mm 300~450 350~450 350~450 炉底
工作层厚度/mm 550~600 600~650 600~750
3.2炉衬厚度的确定
根据上述表3得:
(1)炉身加料侧工作层选700mm,永久层115+115100=915mm
(2)炉身出钢侧工作层选650mm,永久层115mm,填充层100mm,总厚度650+115+100=865mm 故炉壳内径
D内壳=3200+915+865=4900mm
(3)炉帽工作层厚度600mm,永久层厚度60mm,填充层厚度100mm。
(4)炉衬工作层厚度600mm,永久层厚度300mm,则炉衬砖衬总厚度为600+300=900mm。工作层材质全部采用镁碳砖,永久层全部采用标准镁砖,填充层选用焦油镁砂填料。
第四章氧气顶吹转炉金属构件的确定
转炉金属构件是指炉壳,支撑装置(托圈与耳轴)和倾动机构。
4.1炉壳组成及结构形成[12]
炉壳通常有炉帽,炉身和炉底三部分组成。炉帽制成截圆形。由于炉帽,特别是炉口受高温作用易变形,所以普遍炉身制成圆柱形,它是整个炉子的承载部分,受力最大。炉底本设计采用球冠型。
4.2炉壳钢板材质与厚度的确定
转炉吹炼过程中,炉壳承受多种负荷,有炉壳,炉衬自重和炉料重引起的静负荷,兑铁水,加废钢时的冲击以及炉体旋转时产生的动负荷,还有炉衬热膨胀和炉壳本身温度分布不均匀引起的热负荷。这些负荷必然,使炉壳承受相应的应力,以致引起不同程度的变形。研究表明,其中热应力起主导作用,所以设计时力求选用抗蠕变强度高,焊接性能好的材料。大中型转炉全用耐高温,高压的锅炉钢板制作炉壳,也有用金刚板的。国内用于制作炉壳的低合金高强度钢有16Mn,14MnNb,20g等。本次设计的转炉炉壳采用16Mn低合金钢[13]。
由于炉壳各部分受力不均匀,炉帽和炉底应选用不同厚度的钢板根据经值,炉身部分选取55mm厚的钢板,炉帽和炉底部分选取45mm厚的钢板则 H总=H壳内+45mm=7720+45=7765mm D壳=D内壳+55×2=4900+55×2=5000mm
4.3支撑装置
支承装置承载转炉炉体的全部重量,有托圈,炉壳与托圈的连铸接装置,耳轴及轴承构成。
4.3.1 托圈
托圈是转炉的承载和传动部件,通常是用钢板焊厂的呈箱形断面的环形结构,两侧焊
有铸钢的耳轴座,供装耳轴用。 4.3.2 炉壳与托圈的连接装置[14]
炉壳与托圈连接装置的基本形式有两种。本设计采用第一种即支承托架夹持器。其结构是沿炉壳圆周固接若干组上,下托架,它们夹住托圈的顶底面,支架数目通常为3~6组,表在同一水平面上。
4.3.3耳轴及其轴承
倾动力矩又通过耳轴传给托圈,再传给炉体。可见耳轴要受多种负荷的作用,因此应有足够的强度和刚度。耳轴材质一般为合金钢。
表5不同容量转炉的耳轴直径[15]
本设计选耳轴直径为800mm 。
4.4倾动机构
选耳轴中心到炉底距离为3510mm 。选用半悬挂式。
4.5高经比的核定
高经比是指转炉壳总高H 总与转炉外径D 壳之比值。增大高经比有利于减少溅和溢渣,提高金属收的率。但是高经比过大,在炉膛体积一定时,反而面转炉倾动力矩大,耗电大。转炉高经比推荐值为1.35~1.65。
总
总D H =
5000
7765=1.55
符合转炉高宽比推荐值(1.35~1.65)。因此,认为设计的炉子尺寸基本上 是合适的,能够保证正常冶炼。
转炉容量/t 30 50 130 200 300 耳轴直径/mm
630~650
800~820
850~900
1000~1050
1100~1200
参考文献
[1] 冯聚和.氧气顶吹转炉炼钢[M].北京:冶金工业出版社,1995.
[2] 李传薪.炼钢厂设计原理[M].北京:北京科技大学,1993.
[3] 万真雅,薛立基.钢铁冶金原理[M].重庆:重庆大学出版社,1992.
[4] A.M.雅库谢夫,姜永林等.钢铁厂设计[M].沈阳:东北工学院出版社,1992.
[5] 炼钢设计参考资料,工艺设计部分[M].北京:冶金工业出版社,1972.
[6] 徐文派.转炉炼钢学[M].北京:冶金工业出版社,1988.
[7] 陈家祥.连续铸钢手册[M].北京:冶金工业出版社,1991.
[8] 袁章福,潘贻芳.炼钢氧枪技术[M].北京:冶金工业出版社,1992.
[9] 蔡开科.连续铸钢[M].北京:科学出版社,1990.
[10] 罗振才.炼钢机械(修订版)[M].北京:冶金工业出版社,1989.
[11] 北京钢铁设计研究总院.小方坯连铸[M].北京:冶金工业出版社,1985.
[12] 吴勉华.转炉炼钢500问[M].北京:中国计量出版社,1992.
[13] 袁熙志.冶金工艺工程设计[M].北京:冶金工业出版社,2003.
[14] 戴云阁,李文秀,龙腾春.现代转炉炼钢[M].沈阳,东北工业大学出版社,1998.
[15] 蒋仲乐.炼钢工艺及设备[M].北京:冶金工业出版社,1981.
太钢第二炼钢厂顶底复吹转炉工艺生产实践解读
太钢第二炼钢厂顶底复吹转炉工艺生产实践 发表日期:2007-3-14 阅读次数:328 摘要:太钢第二炼钢厂通过引进钢铁研究总院的“长寿复吹转炉炼钢工艺技术”,将2号、3号顶吹氧气转炉改造为顶底复吹转炉。总结阐述了改造后复吹转炉终点碳氧积、脱磷、脱碳、造渣和吹炼等各项工艺的研究。 关键词:顶底复吹转炉工艺研究 太原钢铁(集团)有限公司(以下简称太钢)第二炼钢厂有3座转炉,其中2号、3号转炉冶炼碳钢,原设计公称容量为50t顶吹氧气转炉,是1970年从奥地利引进投产的,2000年将其出钢量扩容为80t。2004年,引进钢铁研究总院的“长寿复吹转炉炼钢工艺技术”,将顶吹氧气转炉改造为顶底复吹转炉。 1 顶底复合吹炼转炉主要工艺技术指标 1.1 复吹转炉终点碳氧积 2005年对Q235-A、HP345、T5IOL、45钢等钢种进行了68炉碳氧积的测定,表明:在终点w(C)为0.07%,温度为1669℃的条件下,碳氧浓度积为0.00277。顶底复吹转炉终点碳氧关系见图1。 从图1中看出,随着转炉终点C含量的降低,终点溶解氧含量升高,特别是w(C)低于0.05%,溶解氧升高明显,因此在生产高碳钢时应控制终点C含量。使C含量控制在规格上限,降低溶解氧含量,提高钢液纯净度。 1.2 复吹转炉脱磷研究 1.2.1 复吹转炉吹炼终点渣中,FeO含量、碱度同磷分配比的关系 由于复吹终点渣中FeO含量明显降低,熔池相对平稳,致使脱磷困难,磷分配比低,仅为46.75。2005年,通过工艺摸索,提高转炉造渣工艺,转炉成品P含量降低,磷分配比明显提高,达到了76.44。取样分析渣中FeO含量、碱度同磷分配比的关系,结果见图2、图3。
世界氧气顶吹转炉炼钢技术发展史
世界氧气顶吹转炉炼钢技术发展史 氧气顶吹转炉炼钢(oxygen top blown converter steelmaking)由转炉顶部垂直插入的氧枪将工业纯氧吹入熔池,以氧化铁水中的碳、硅、锰、磷等元素,并发热提高熔池温度而冶炼成为钢水的转炉炼钢方法。它所用的原料是铁水加部分废钢,为了脱除磷和硫,要加入石灰和萤石等造渣材料。炉衬用镁砂或白云石等碱性耐火材料制作。所用氧气纯度在99%以上,压力为0.81~1.22MPa(即8~12atm)。 简史 空气底吹转炉和平炉是氧气转炉出现以前的主要炼钢设备。炼钢是氧化熔炼过程,空气是自然界氧的主要来源。然而空气中4/5的气体是氮气,空气吹炼时,这样多的氮气在炉内穿行而过,白白带走大量的热且有部分氮溶解在铁液中,成为恶化低碳钢品质的重要原因。平炉中,氧在用于燃烧燃料之后,过剩的氧要通过渣层传入钢水,所以反应速率极慢,这也就增加了热损失。因此,直接把氧气吹入熔池炼钢,成为许多冶金学家向往的目标。早在19世纪,现代炼钢法的创始人贝塞麦(H.Bessemer)就有了纯氧炼钢的设想,但因没有大量氧气而未进行试验。20世纪20年代后期,以空气液化和分馏为基础的林德一弗兰克(Linde—Frankel)制氧技术开发成功,能够生产可供工业使用的廉价氧气,氧气炼钢又为冶金界所注意。从1929年开始,柏林工业大学的丢勒尔教授(R.Durrer)在实验室中研究吹氧炼钢,第二
次世界大战开始后转到瑞士的冯?罗尔(V.Roll)公司继续进行研究。1936~1939年勒莱普(O.Lellep)在奥伯豪森(Oberhausen)进行了底吹氧炼钢的试验,由于喷嘴常损坏未能成功。1938年亚琛(Aachen)工业大学的施瓦茨(C.V.Schwarz)提出用超音速射流向下吹氧炼钢,并在实验室进行了试验,将托马斯生铁吹炼成低氮钢,但因熔池浅而损坏了炉底。1948年丢勒尔(R.Durrer)等在冯?罗尔(VonRoll)公司建成2.5t的焦油白云石衬的试验转炉,以450的斜度将水冷喷嘴插入铁水吹氧炼钢,无论贝塞麦生铁或托马斯生铁都能成功炼成优质钢水,而且认识到喷嘴垂直向下时,最有利于喷嘴和炉衬的寿命。这样就最后完成了转炉吹氧炼钢的实验室试验。从实验室研究向工业化试验的进一步发展是由奥地利的沃埃施特(VOEST)公司完成的。第二次世界大战后奥地利面临重建钢铁工业的需要,该国缺少废钢使得平炉或电炉炼钢法缺乏竞争力。沃埃施特公司注意到丢勒尔的试验,决心开发一个具有竞争力的新的炼钢方法。1949年5月在奥地利累欧本(Leoben)开了一次氧气炼钢的讨论会,决定冯?罗尔、曼内斯曼(Mannesmann)、阿尔派(ALPINE)和沃埃施特4个公司协作,在沃埃施特的林茨(Linz)钢厂作进一步的试验。1949年6月在林茨建成2t顶吹氧试验转炉,由苏埃斯(T.Suess)和豪特曼(H.Hauttmann)负责,在丢勒尔参与下,成功地解决了合适的氧气压力、流量和喷嘴与熔池面距离等工艺操作问题。之后迅速建立15t试验转炉,广泛研究新方法所冶炼钢的品质。由于钢的质量很好而且炼钢工艺的
100t顶底复吹转炉炉型设计说明书
目录 前言 (1) 一、转炉炉型及其选择 (1) 二、炉容比的确定 (3) 三、熔池尺寸的确定 (3) 四、炉帽尺寸的确定 (5) 五、炉身尺寸的确定 (6) 六、出钢口尺寸的确定 (6) 七、炉底喷嘴数量及布置 (7) 八、高径比 (9) 九、炉衬材质选择 (9) 十、炉衬组成及厚度确定 (9) 十一、砖型选择 (12) 十二、炉壳钢板材质与厚度的确定 (14) 十三、校核 (15) 参考文献 (16)
专业班级学号姓名成绩 前言: 转炉是转炉炼钢车间的核心设备。转炉炉型及其主要参数对转炉炼钢的生产率、金属收的率、炉龄等经济指标都有直接的影响,其设计是否合理也关系到冶炼工艺能否顺利进行,车间主厂房高度和与转炉配套的其他相关设备的选型。所以,设计一座炉型结构合理,满足工艺要求的转炉是保证车间正常生产的前提,而炉型设计又是整个转炉车间设计的关键。 设计内容:100吨顶底复吹转炉炉型的选择与计算;耐火材料的选择;相关参数的选择与计算。 一、转炉炉型及其选择 转炉有炉帽、炉身、炉底三部分组成。转炉炉型是指由上述三部分组成的炉衬内部空间的几何形状。由于炉帽和炉身的形状没有变化,所以通常按熔池形状将转炉炉型分为筒球形、锥球型和截锥形等三种。炉型的选择往往与转炉的容量有关。
(1)筒球形。熔池由球缺体和圆柱体两部分组成。炉型形状简单,砌砖方便,炉壳容易制造,被国内外大、中型转炉普遍采用。 (2)锥球型。熔池由球缺体和倒截锥体两部分组成。与相同容量的筒球型比较,锥球型熔池较深,有利于保护炉底。在同样熔池深度的情况下,熔池直径可以比筒球型大,增加了熔池反应面积,有利于去磷、硫。我国中小型转炉普遍采用这种炉型,也用于大型炉。 (3)截锥形。熔池为一个倒截锥体。炉型构造较为简单,平的熔池底较球型底容易砌筑。在装入量和熔池直径相同的情况下,其熔池最深,因此一般不适用于大容量炉,我国30t以下的转炉采用较多。不过由于炉底是平的,便于安装底吹系统,往往被顶底复吹转炉所采用。 顶底复吹转炉炉型图 顶底复吹转炉炉型的基本特征如下: (1)吹炼的平稳和喷溅程度优于顶吹转炉,而不及底吹转炉,故炉子的高宽比略小于顶吹转炉,却大于底吹转炉,即略呈矮胖型。 (2)炉底一般为平底,以便设置喷口,所以熔池常为截锥型。 (3)熔池深度主要取决于底部喷口直径和供气压力,同时兼顾顶吹氧流的穿透
转 炉 长 寿 复 吹 冶 炼 工 艺 技 术
转炉长寿复吹冶炼工艺技术 转炉长寿复吹冶炼工艺技术 钢铁研究总院工艺所是我国最早开发、推广复吹转炉炼钢工艺技术的企业。在70-80年代,钢铁研究总院工艺所就率先在国内首钢、唐钢等钢厂推广了复吹转炉炼钢工艺技术。 上世纪末90年代,转炉溅渣护炉技术在我国大面积推广应用,转炉炉龄大幅度 提高。在我国出现了复吹转炉底吹供气元件寿命低,不能与转炉炉龄同步、复吹效益不能得到充分发挥的问题。钢铁研究总院工艺所针对这一问题,作了大量开发研究工作。目前已成功地开发出“长寿复吹转炉冶炼工艺技术”,形成了多项专利技术。现已在包钢、本钢、首钢、莱钢、武钢二炼钢和济钢等数十家大、中、小型钢铁企业得到应用,并取得了显著的效果。采用“长寿复吹转炉冶炼技术”后,底吹供气元件寿命做到了与转炉高炉龄基本同步,使复吹的冶金效果在全炉役得到发挥。“长寿复吹转炉冶炼技术”的开发成功,使我国复吹转炉炼钢工艺技术一举走在了世界的前列。该项技术现已在国内多次获得了国家、行业的科学技术进步奖。 1 复吹转吹炼工艺技术基本原理 复吹转炉炼钢工艺技术是氧气转炉诞生五十年来,所出现的两次重大的技术进步之一,基本原理是在顶吹氧气炼钢同时底吹辅助性搅拌气体: l 钢水终点氧含量降低:0.01-0.03% l 低碳钢水终点氧含量降低:100PPm; l 吨钢效益为2-6元/t; l 金属收得率提高:0.5~1.5%; l 石灰消耗降低:3~10kg/t; l 复吹工艺具有成渣速度快和吹炼平稳的双重优点; l 复吹工艺具有降低消耗,具有广泛的钢种冶炼适应性; l 氧气消耗减少:4~6Nm3/t; l 是否采用复吹炼钢工艺,已成为现代转炉的标志之一。
顶吹转炉
太原科技大学 课程设计说明书 设计题目: 50t 氧气顶吹转炉设计 设计人:郭晓琴 指导老师:杨晓蓉 专业:冶金工程 班级:冶金工程081401 学号: 200814070105 材料科学与工程学院 2011年12月30 日
目录 摘要................................................ 错误!未定义书签。第一章绪论................................................ 错误!未定义书签。 1.1 氧气顶吹转炉炼钢的发展概况......................... 错误!未定义书签。 1.2 氧气顶吹转炉炼钢的优点............................. 错误!未定义书签。 1.3 转炉炼钢生产技术发展趋势........................... 错误!未定义书签。第二章炉型尺寸计算........................................ 错误!未定义书签。 2.1转炉炉型及其选择.................................... 错误!未定义书签。 2.2转炉炉型尺寸计算.................................... 错误!未定义书签。 2.2.1 熔池尺寸...................................... 错误!未定义书签。 2.2.2 炉容比(容积比).............................. 错误!未定义书签。 2.2.3炉帽尺寸...................................... 错误!未定义书签。 2.2.4炉身尺寸...................................... 错误!未定义书签。 2.2.5出钢口尺寸.................................... 错误!未定义书签。第三章氧气顶吹转炉耐火材料................................ 错误!未定义书签。 3.1 炉衬的组成和材质的选择............................. 错误!未定义书签。 3.2炉衬厚度的确定...................................... 错误!未定义书签。第四章氧气顶吹转炉金属构件的确定.......................... 错误!未定义书签。 4.1炉壳组成及结构形成................................. 错误!未定义书签。 4.2炉壳钢板材质与厚度的确定 (7) 4.3支撑装置 (7) 4.3.1 托圈......................................... 错误!未定义书签。 4.3.2炉衬的组成和材质的选择....................... 错误!未定义书签。 4.3.3耳轴及其轴承................................. 错误!未定义书签。 4.4倾动机构........................................... 错误!未定义书签。 4.5高径比的核定....................................... 错误!未定义书签。参考文献.............................................................. - 12 -
转炉炼钢工艺标准经过流程
转炉炼钢工艺流程 这种炼钢法使用的氧化剂是氧气。把空气鼓入熔融的生铁里,使杂质硅、锰等氧化。在氧化的过程中放出大量的热量(含1%的硅可使生铁的温度升高200摄氏度),可使炉内达到足够高的温度。因此转炉炼钢不需要另外使用燃料。 转炉炼钢是在转炉里进行。转炉的外形就像个梨,内壁有耐火砖,炉侧有许多小孔(风口),压缩空气从这些小孔里吹炉内,又叫做侧吹转炉。开始时,转炉处于水平,向内注入1300摄氏度的液态生铁,并加入一定量的生石灰,然后鼓入空气并转动转炉使它直立起来。这时液态生铁表面剧烈的反应,使铁、硅、锰氧化 (FeO,SiO2 , MnO,) 生成炉渣,利用熔化的钢铁和炉渣的对流作用,使反应遍及整个炉内。几分钟后,当钢液中只剩下少量的硅与锰时,碳开始氧化,生成一氧化碳(放热)使钢液剧烈沸腾。炉口由于溢出的一氧化炭的燃烧而出现巨大的火焰。最后,磷也发生氧化并进一步生成磷酸亚铁。磷酸亚铁再跟生石灰反应生成稳定的磷酸钙和硫化钙,一起成为炉渣。 当磷与硫逐渐减少,火焰退落,炉口出现四氧化三铁的褐色蒸汽时,表明钢已炼成。这时应立即停止鼓风,并把转炉转到水平位置,把钢水倾至钢水包里,再加脱氧剂进行脱氧。整个过程只需15分钟左右。如果空气是从炉低吹入,那就是低吹转炉。 随着制氧技术的发展,现在已普遍使用氧气顶吹转炉(也有侧吹转炉)。这种
转炉吹如的是高压工业纯氧,反应更为剧烈,能进一步提高生产效率和钢的质量。 转炉一炉钢的基本冶炼过程。顶吹转炉冶炼一炉钢的操作过程主要由以下六步组成: (1)上炉出钢、倒渣,检查炉衬和倾动设备等并进行必要的修补和修理;(2)倾炉,加废钢、兑铁水,摇正炉体(至垂直位置); (3)降枪开吹,同时加入第一批渣料(起初炉内噪声较大,从炉口冒出赤色烟雾,随后喷出暗红的火焰;3~5min后硅锰氧接近结束,碳氧反应逐渐激烈,炉口的火焰变大,亮度随之提高;同时渣料熔化,噪声减弱); (4)3~5min后加入第二批渣料继续吹炼(随吹炼进行钢中碳逐渐降低,约12min 后火焰微弱,停吹); (5)倒炉,测温、取样,并确定补吹时间或出钢; (6)出钢,同时(将计算好的合金加入钢包中)进行脱氧合金化。 上炉钢出完钢后,倒净炉渣,堵出钢口,兑铁水和加废钢,降枪供氧,开始吹炼。在送氧开吹的同时,加入第一批渣料,加入量相当于全炉总渣量的三分之二,开吹3-5分钟后,第一批渣料化好,再加入第二批渣料。如果炉内化渣不好,则许加入第三批萤石渣料。 吹炼过程中的供氧强度:
氧气顶吹转炉炼钢终点碳控制的方法
氧气顶吹转炉炼钢终点碳控制的方法 终点碳控制的方法有三种,即一次拉碳法、增碳法和高拉补吹法。 一次拉碳法 按出钢要求的终点碳和终点温度进行吹炼,当达到要求时提枪。 这种方法要求终点碳和温度同时到达目标,否则需补吹或增碳。一次拉碳法要求操作技术水平高,其优点颇多,归纳如下: (1) 终点渣TFe含量低,钢水收得率高,对炉衬侵蚀量小。 (2) 钢水中有害气体少,不加增碳剂,钢水洁净。 (3) 余锰高,合金消耗少。 (4) 氧耗量小,节约增碳剂。 增碳法 是指吹炼平均含碳量≥0.08%的钢种,均吹炼到ω[C]=0.05%~0.06%提枪,按钢种规范要求加入增碳剂。增碳法所用碳粉要求纯度高,硫和灰分要很低,否则会玷污钢水。 采用这种方法的优点如下: (1)终点容易命中,比“拉碳法”省去中途倒渣、取样、校正成分及温度的补吹时间,因而生产率较高; (2)吹炼结束时炉渣Σ(FeO)含量高,化渣好,去磷率高,吹炼过程的造渣操作可以简化,有利于减少喷溅、提高供氧强度和稳定吹炼工艺; (3)热量收入较多,可以增加废钢用量。 采用“增碳法”时应严格保证增碳剂质量,推荐采用C>95%、粒度≤10毫米的沥青焦。增碳量超过0.05%时,应经过吹Ar等处理。 高拉补吹法 当冶炼中、高碳钢钢种时,终点按钢种规格稍高一些进行拉碳,待测温、取样后按分析结果与规格的差值决定补吹时间。 由于在中、高碳(ω[c]>0.40%)钢种的碳含量范围内,脱碳速度较快,火焰没有明显变化,从火花上也不易判断,终点人工一次拉碳很难准确判断,所以采用高拉补吹的办法。用高拉补吹法冶炼中、高碳钢时,根据火焰和火花的特征,参考供氧时间及氧耗量,按所炼钢种碳规格要求稍高一些来拉碳,使用结晶定碳和钢样化学分析,再按这一碳含量范围内的脱碳速度补吹一段时间,以达到要求。高拉补吹方法只适用于中、高碳钢的吹炼。根据某厂30 t 转炉吹炼的经验数据,补吹时的脱碳速度一般为0.005%/s。当生产条件变化时,其数据也有变化。
氧气顶吹转炉设计
3.1 转炉炉型设计3.1.1 转炉炉型设计概述(1)公称容量及其表示方法 公称容量(T),对转炉容量大小的称谓,即平时所说的转炉的吨位。它是转炉生产能力的主要标志和炉型设计的重要依据。目前国内外对公称容量的含义的解释还很不统一,归纳起来,大体上有以下三种表示方法: 1)以平均金属装入量(t)表示; 2)以平均出钢量(t)表示; 3)以平均炉产良坯量(t)表示。 在一个炉役期内,炉役前期和后期的装入量或出钢量不同,随着吹炼的进行,炉衬不断地受到侵蚀,熔池不断扩大,装入量增大,所以三种表示方法都是以其平均容量来表示。 这三种表示方法各有其优缺点,以平均金属装入量表示公称容量,便于进行物料平衡和热平衡计算,换算成新炉装入量时也比较方便。 以平均炉产良坯量表示公称容量,便于车间生产规模和技术经济指标的比较,但是在进行炉型设计时需做较复杂的换算。 以平均出钢量表示公称容量则介于两者之间,其产量不受操作方法和浇铸方法的影响,便于炼钢后步工序的设计,也比教容易换算成平均金属装入量和平均炉产良坯量。设计的公称容量与实际生产的炉产量基本一致。所以在进行炉型设计时采用以平均出钢量表示公称容量比较合理。 (2)炉型的定义: 转炉炉型是指转炉炉膛的几何形状,亦即指由耐火材料砌成的炉衬内形。 (3)炉型设计的意义 转炉是转炉炼钢车间的核心设备,炉型及其主要参数对转炉炼钢的生产率、金属收得率、炉龄等技术经济指标都有着直接的影响,炉型设计的是否合理关系到冶炼工艺能否顺利进行的问题,如喷溅问题,除与操作因素有关外,炉型设计是否合理也是个重要因素,并且车间的主厂房高度以及主要设备,像除尘设备,倾动机构设备等都与炉型尺寸密切相关。而且转炉一旦投产使用,炉型尺寸就很难再作改动,因为不论变动直径还是高度都牵涉到耳轴位置,它是与转炉基础联系在一起的,一般不能随意变动。 所以说,设计一座炉型结构合理,满足工艺要求的转炉是保证车间正常生产的前提。而炉型设计又是整个转炉设计的关键。 设计内容:炉型种类的选择; 炉型主要参数的确定; 炉型尺寸设计计算; 炉衬和炉壳厚度的确定; 顶底复吹转炉设计。 3.1.2炉型种类及其选择 吹炼过程中炉膛内进行着极其复杂而又激烈地物理化学反应和机械运动,因此,转炉的炉型必须适应这些反应特点和运动规律,否则就不能保证冶炼过程的正常进行。那么,什么样的炉型才是比较理想的炉型呢?也就是说,炉型具备什么特点才能适应转炉炼钢反应激烈,吹炼速度快的特点呢? (1)炉型种类的选择原则 选择炉型时应考虑以下几条基本原则: ①炉型应能适应炉内钢液、炉渣和炉气的循环运动规律,使熔池得到激烈而又均匀的搅拌,从而加快炼钢过程的物理化学反应; ②有利于提高供氧强度(B),缩短冶炼时间,减少喷溅,降低金属损耗; ③新砌好的炉子的炉型要尽量接近于停炉以后残余炉衬的轮廓,减少吹炼过程中钢液、炉渣和炉气对炉衬的冲刷侵蚀及局部侵蚀,提高炉龄,降低耐火材料的消耗; ④炉壳应容易制造,炉衬砖的砌筑和维护要方便,从而改善工人的劳动条件,缩短修炉时间,提高转炉作业率。 总之应能使转炉炼钢获得较好的经济效益,优质、高产、低耗。 (2)炉型种类及其选择
转炉工作原理及结构设计要点
攀枝花学院本科课程设计 转炉工作原理及结构设计 学生姓名: 学生学号: 院(系): 年级专业: 指导教师: 二〇一三年十二月
转炉工作原理及结构设计 1.1 前言 1964年,我国第一座30t氧气顶吹转炉炼钢车间在首钢建成投产。其后,上钢一厂三转炉车间、上钢三厂二转炉车间等相继将原侧吹转炉改为氧气顶吹转炉。20世纪60年代中后期,我国又自行设计、建设了攀枝花120t大型氧气顶吹转炉炼钢厂,并于1971年建成投产。进入20世纪80年代后,在改革开放方针策的指引下,我国氧气转炉炼钢进入大发展时期,由于氧气转炉炼钢和连铸的迅速发展,至1996年我国钢产量首次突破1亿t,成为世界第一产钢大国。 1.2 转炉概述 转炉(converter)炉体可转动,用于吹炼钢或吹炼锍的冶金炉。转炉炉体用钢板制成,呈圆筒形,内衬耐火材料,吹炼时靠化学反应热加热,不需外加热源,是最重要的炼钢设备,也可用于铜、镍冶炼。转炉按炉衬的耐火材料性质分为碱性(用镁砂或白云石为内衬)和酸性(用硅质材料为内衬)转炉;按气体吹入炉内的部位分为底吹、顶吹和侧吹转炉;按吹炼采用的气体,分为空气转炉和氧气转炉。转炉炼钢主要是以液态生铁为原料的炼钢方法。其主要特点是:靠转炉内液态生铁的物理热和生铁内各组分(如碳、锰、硅、磷等)与送入炉内的氧进行化学反应所产生的热量,使金属达到出钢要求的成分和温度。炉料主要为铁水和造渣料(如石灰、石英、萤石等),为调整温度,可加入废钢及少量的冷生铁块和矿石等。 1.2.1 转炉分类 1.2.1.1 炼钢转炉 早期的贝塞麦转炉炼钢法和托马斯转炉炼钢法都用空气通过底部风嘴鼓入钢水进行吹炼。侧吹转炉容量一般较小,从炉墙侧面吹入空气。炼钢转炉按不同需要用酸性或碱性耐火材料作炉衬。直立式圆筒形的炉体,通过托圈、耳轴架置于支座轴承上,操作时用机械倾动装置使炉体围绕横轴转动。 50年代发展起来的氧气转炉仍保持直立式圆筒形,随着技术改进,发展成顶吹喷氧枪供氧,因而得名氧气顶吹转炉,即L-D转炉(见氧气顶吹转炉炼钢);用带吹冷却剂的炉底喷嘴的,称为氧气底吹转炉(见氧气底吹转炉炼钢)。
设计作业 300t顶底复吹转炉炉型计算
转炉炉型设计计算 1.1原始数据 (1)、转炉的公称容量为300t 。 (2)、采用顶底复吹冶炼工艺 1.2 转炉的炉型选择 图为常见转炉炉型 (a)筒球型; (b)锥球型; (c)截锥型 根据原始条件及采用顶底复吹工艺的要求,为便于安装底部供气元件,要求转炉底部为平的,所以本设计将采用截锥型炉型作为设计炉型。 1.3炉容比 炉容比系指转炉有效容积与公称容量之比值。转炉炉容比主要与供氧强度有关,与炉容量关系不大。从目前实际情况来看,顶底复吹转炉炉容比一般取0.85~0.95m 3/t 。 本设计为300t ,取V/T=0.92 1.4熔池尺寸的计算 熔池直径的计算公式 t G k D 式中 D ——熔池直径,m ; G ——新炉金属装入量,t ,可取公称容量; K ——系数,参见表1-1;
t ——平均每炉钢纯吹氧时间,min 表1-1 系数K 的推荐值 b.确定吹氧时间 表1.2 推荐的转炉纯吹氧时间 本设计的转炉公称容量为300t , 又根据国家关于新建转炉的要求,吹氧时间在16min , 所以选择的吹氧时间为16min 。 取K=1.50 则)(495.616 30050.1m t G K D =?=? = ② 截锥型熔池深度的计算公式为: )(822.1495.6574.0119 .44574.0574.02 22m D V D V h =?=?== ) (金池 V 池=G/Y=44.119m 3 其中Y=6.8t/ m 3 ③熔池其他尺寸确定. )(546.4495.67.07.01m D D =?== 1.5炉帽尺寸的确定 ①炉口直径d 0.取 )(2475.3495.65.00m d =?= ②炉帽倾角: 取?60 ③炉帽高度H 帽: 取H 口=400mm , )(76.260tan )2475.3495.6(2 1 tan )(2100m d D H =?-=?-= θ锥 则整个炉帽高度为:
50吨氧气顶吹转炉炉体设计
50吨氧气顶吹转炉炉体设计 1 氧气顶吹转炉炼钢的发展概况 氧气顶吹转炉炼钢法是20世纪50年代产生和发展起来的炼钢技术,但从起出现至今已有100多年的历史。早在1856年英国人亨利·贝塞麦就研究开发了酸性底吹转炉炼钢法,以铁水为原料,从转炉底部通入空气氧化去除杂质冶炼成钢。第一次实现了液态钢冶炼的规模生产,从此进入了现代钢铁工业生产阶段。1878年德国尼·托马斯研究发明的碱性底吹转炉炼钢法,以碱性耐火材料砌筑炉衬,吹炼过程中可加入石灰造渣,能够脱除铁水中的P、S,解决了高磷铁水冶炼技术问题。由于转炉炼钢法有生产率高、成本低、设备简单等优点,在欧洲得到迅速的发展,并成为当时主要的炼钢方法。 第二次世界大战之后,从空气中分离氧气技术的成功,提供了大量廉价的工业纯氧,使贝塞麦的氧气炼钢设想得以实现。由于氧气顶吹转炉炼钢首先在林茨和多那维茨两城投入生产,所以取这两个城市名称的第一个字母L-D(LD)作为氧气顶吹转炉炼钢法的代称。 LD炼钢法具有反应速度快,热效率高,又可使用约30%的废钢为原料;并克服了底吹转炉钢质量差,品种少的缺点;因而一经问世就显示出巨大的优越性和生命力。进入20世纪70年代以后,顶吹转炉炼钢技术趋于完善。转炉的最大公称吨位达380t;单炉生产能力达到400~500万t/a;能够冶炼全部平炉钢种,若与有关精炼技术相匹配,还可以冶炼部分电炉钢种;大型转炉炉龄在1999年达到10000炉次/炉役以上;并实现了计算机控制终点碳与出钢温度。 1951年碱性空气侧吹转炉炼钢法首先在我国唐山钢厂试验成功,并于1952年投入工业生产。1954年开始了小型氧气顶吹转炉炼钢的试验研究工作,1962年将首钢试验厂空气侧吹转炉改建成3t氧气顶吹转炉,开始了工业性试验。在试验取得成功的基础上,我国第一个氧气顶吹转炉炼钢车间(2×30t)在首钢建成,于1964年12月26日投入生产。以后,又在唐山、上海、杭州等地改建了一批3.5~5t的小型氧气顶吹转炉。1966年上钢一厂将原有的一个空气侧吹转炉炼钢车间,改建成3座30t的氧气顶吹转炉炼钢车间,并首次采用了先进的烟气净化回收系统,于当年8月投入生产,还建设了弧形连铸机与之相配套,试验和扩大了氧气顶吹转炉炼钢的品种。这些都为我国日后氧气顶吹转炉炼钢技术的发展提供了宝贵经验。此后,我国原有的一些空气侧吹转炉车间逐渐改建成中小型氧气顶吹转炉车间,并新建了一批中、大型氧气顶吹转炉车间。20世纪80年代宝钢从日本引进建成具有70年代末技术水平的300t大型转炉3座、首钢购入二手设备建成210t转炉车间;90年代宝钢又建成250t转炉车间,武钢引进250t 转炉,唐钢建成150t转炉车间,重钢和首钢又建成80t转炉炼钢车间;许多平炉车间改建成氧气顶吹转炉车间等。到1998年,我国氧气顶吹转炉共有221座,其中100t以下的转炉有188座,(50-90t的转炉有25座),100-200t的转炉有23
150吨转炉设计
转炉炉型设计 转炉是转炉炼钢车间的核心设备。转炉炉型及其主要参数对转炉炼钢的生产率、金属收得率、炉龄等经济指标都有直接的影响,其设计是否合理也关系到冶炼工艺能否顺利进行,车间主厂房高度和转炉配套的其他相关设备的选型。2.1 炉型的选择 本设计为150t的中型转炉,选用筒球型转炉。 2.2 炉容比与高宽比 2.2.1 炉容比(V/T , m3/t) 炉容比是转炉有效容积与公容量的比值,主要与供氧强度有关,本设计选取炉容比为0.93 2.2.2 高宽比 高宽比是指转炉炉壳总高度与炉壳外径的比值,是作为炉型设计的校核数据。在 1.25-1.45之间。 2.3 转炉主要尺寸的确定 2.3.1 熔池尺寸 (1)熔池直径D 熔池直径是指转炉熔池在平静状态时金属液面的直径。可根据公 式 D?K G ——新炉金属装入量,t;(取公称容量) t ——吹氧时间,min,取16min K——比例系数,取1.70 则熔池直径D?K 1.7×√(150÷16)=5.21m 熔池深度是指转炉熔池在平静状态时,从金属液面到炉底的深度。对于筒球 型熔池,取球缺体半径R = 1.1D = 5726mm,此时熔池体积VC与熔池直径存在如下关系:VC?0.790hD?0.046D,即h0? 2 3 VC?0.046D 0.79D 2 3 。 熔池体积VC = 装入量/比重 =150/5.0 = 30m3 则熔池深度h0? VC?0.046D 0.79D 2 3 =(30+0.046×5.21)/(0.790×5.21)=1.70m 32
2.3.2 炉帽尺寸 (1)炉帽倾角? 倾角过小,炉帽内衬不稳定,容易倒塌;过大则出钢时容易钢渣混出和从炉口大量流渣。在本设计中取? = 60°. (2)炉口直径d0 本设计中取炉口直径为熔池直径的48%,即d0 = 5.21×48% = 2.5m =2500mm (3) 炉帽高度H 帽 口 = 350 mm,则炉帽高度为: 取炉口上部直线段高度H H帽 = ? (D?d)tan??H= 1/2(5.21 — 2.5)tan60°+ 0.35 = 2.70m 002 2.3.3 炉身尺寸 (1)炉身直径 转炉炉帽以下,熔池面以上的圆柱体部分称为炉身。其直径与熔池直径一致,即为D。(2)炉身高度H 身 2 2 H身 = 4V 式中 V 身 身 /(?D)?4(Vb?V帽?VC)/(?D) 、V帽、VC——分别为炉身、炉帽、熔池的容积。其中: V帽??/24(D3?d口3)tan???/4d口2H口 =0.262(H帽?H口)(D+Dd口+d口)+0.785d口H口 2 2 2 Vb ——转炉有效容积,为V身、V帽、VC三者之和,取决于容量和炉容 比。Vb = 炉容比×G。 根据已得的数据,则有: 3 Vb = 炉容比×G = 0.93×150 =140 m V帽?0.262(H帽?H口)(D+Dd口+d口)+0.785d口H口 222 =0.262(2.70-0.35)(5.21+5.21×2.5+2.5)+0.785×2.5×0.35 = 30.30 m3 2 22 由此,则有炉身高度为: H身 = 4V 身 /(?D)?4(Vb?V帽?VC)/(?D) 22
氧气顶吹转炉炼钢
R.D.佩尔克等著,邵象华、楼盛赫等译校:《氧气顶吹转炉炼钢》,冶金工业出版社,北京,(上册)1980,(下册)1982。(R.D.Pehlke,ed., BOF Steelmaking,AIME,1974~1977.) 氧气顶吹转炉炼钢 责任编辑:苏方来源:成都钢铁网2008年06月20日 氧气顶吹转炉炼钢(oxygen top blown converter steelmaking) 由转炉顶部垂直插入的氧枪将工业纯氧吹入熔池,以氧化铁水中的碳、硅、锰、磷等元素,并发热提高熔池温度而冶炼成为钢水的转炉炼钢方法。它所用的原料是铁水加部分废钢,为了脱除磷和硫,要加入石灰和萤石等造渣材料。炉衬用镁砂或白云石等碱性耐火材料制作。所用氧气纯度在99%以上,压力为0.81~1.22MPa(即8~12atm)。 简史空气底吹转炉和平炉是氧气转炉出现以前的主要炼钢设备。炼钢是氧化熔炼过程,空气是自然界氧的主要来源。然而空气中4/5的气体是氮气,空气吹炼时,这样多的氮气在炉内穿行而过,白白带走大量的热且有部分氮溶解在铁液中,成为恶化低碳钢品质的重要原因。平炉中,氧在用于燃烧燃料之后,过剩的氧要通过渣层传入钢水,所以反应速率极慢,这也就增加了热损失。因此,直接把氧气吹入熔池炼钢,成为许多冶金学家向往的目标。早在19世纪,现代炼钢法的创始人贝塞麦(H.Bessemer)就有了纯氧炼钢的设想,但因没有大量氧气而未进行试验。20世纪20年代后期,以空气液化和分馏为基础的林德一弗兰克(Linde —Frankel)制氧技术开发成功,能够生产可供工业使用的廉价氧气,氧气炼钢又为冶金界所注意。从1929年开始,柏林工业大学的丢勒尔教授(R.Durrer)在实验室中研究吹氧炼钢,第二次世界大战开始后转到瑞士的冯?罗尔(V.Roll)公司继续进行研究。1936~1939年勒莱普(O.Lellep)在奥伯豪森(Oberhausen)进行了底吹氧炼钢的试验,由于喷嘴常损坏未能成功。1938年亚琛(Aachen)工业大学的施瓦茨(C.V.Schwarz)提出用超音速射流向下吹氧炼钢,并在实验室进行了试验,将托马斯生铁吹炼成低氮钢,但因熔池浅而损坏了炉底。1948年丢勒尔(R.Durrer)等在冯?罗尔(V onRoll)公司建成2.5t的焦油白云石衬的试验转炉,以450的斜度将水冷喷嘴插入铁水吹氧炼钢,无论贝塞麦生铁或托马斯生铁都能成功炼成优质钢水,而且认识到喷嘴垂直向下时,最有利于喷嘴和炉衬的寿命。这样就最后完成了转炉吹氧炼钢的实验室试验。从实验室研究向工业化试验的进一步发展是由奥地利的沃埃施特(VOEST)公司完成的。第二次世界大战后奥地利面临重建钢铁工业的需要,该国缺少废钢使得平炉或电炉炼钢法缺乏竞争力。沃埃施特公司注意到丢勒尔的试验,决心开发一个具有竞争力的新的炼钢方法。1949年5月在奥地利累欧本(Leoben)开了一次氧气炼钢的讨论会,决定冯?罗尔、曼内斯曼(Mannesmann)、阿尔派(ALPINE)和沃埃施特4个公司协作,在沃埃施特的林茨(Linz)钢厂作进一步的试验。1949年6月在林茨建成2t顶吹氧试验转炉,由苏埃斯(T.Suess)和豪特曼(H.Hauttmann)负责,在丢勒尔参与下,成功地解决了合适的氧气压力、流量和喷嘴与熔池面距离等工艺操作问题。之后迅速建立15t试验转炉,广泛研究新方法所冶炼钢的品质。由于钢的质量很好而且炼钢工艺的效率很高,1949年末该公司决定在林茨投资建设世界第一个氧气顶吹转炉工厂。并命名该炼钢法为LD法。林茨的30tLD转炉工厂于1952年11月投产。翌年春季第2个30tLD转炉工厂在奥地利多纳维兹([)onawitz)建成投产。1950年由苏埃斯申请得到专利权。推动炼钢工业再次大变革的氧气顶吹转炉炼钢法登上了历史舞台。该法问世后,数十年内迅速取代了平炉炼钢而成为世界上最主要的炼钢方法。在北美,美国是平炉炼钢大国,有平炉熔池吹氧的经验。美国又是第二次世界大战的最大战胜国,工业基础雄厚。在得知转炉氧气炼钢的信息后,美国麦克劳斯(McLouth)公司和加拿大多法斯柯(DOFASCO)公司于1954年各迅速建成一个35t氧气顶吹转炉车间并投产。随后
氧气顶吹转炉炉体设计
氧气顶吹转炉炉体设计
目录 一转炉系统设备.............................................................................................................- 1 - 1.1 炉型.....................................................................................................................- 1 - 1.1.1 转炉炉型概念.............................................................................................- 1 - 1.1.2 合理的炉型要求.........................................................................................- 1 - 1.1.3 转炉的基本炉型.........................................................................................- 2 - 1.1.3.1 筒球型.................................................................................................- 2 - 1.1.3.2 锥球型.................................................................................................- 2 - 1.1.3.3 截锥型.................................................................................................- 2 - 1.2 转炉炉型主要参数确定.....................................................................................- 3 - 1.2.1 转炉的公称容量.........................................................................................- 3 - 1.2.2 炉容比.........................................................................................................- 3 - 1.2.2.1 铁水比、铁水成分.............................................................................- 3 - 1.2.2.2 供氧强度.............................................................................................- 3 - 1.2.2.3 冷却剂的种类.....................................................................................- 4 - 1.2.3 高径比.........................................................................................................- 4 - 1.3 炉型主要尺寸的确定.........................................................................................- 4 - 1.3.1 筒球型氧气顶吹转炉的主要尺寸.............................................................- 4 - 1.3.1.1 熔池直径D..........................................................................................- 5 - 1.4 炉壳.....................................................................................................................- 6 - 1.4.1 炉壳的作用.................................................................................................- 6 - 1.4.2 炉壳的组成.................................................................................................- 6 - 1.4. 2.1 炉帽.....................................................................................................- 6 - 1.4. 2.2 炉身.....................................................................................................- 8 - 1.4. 2.3 炉底.....................................................................................................- 8 - 1.4. 2.4 制作及要求.........................................................................................- 8 - 1.5 炉体支撑系统.....................................................................................................- 9 - 1.5.1 托圈与耳轴.................................................................................................- 9 - 1.5.1.1 托圈与耳轴的作用、结构.................................................................- 9 - 1.5.1.2 托圈与耳轴的连接...........................................................................- 10 - 1.5.2 炉体与托圈...............................................................................................- 10 - 1.5.3 耳轴轴承座...............................................................................................- 13 - 1.6 转炉倾动机构...................................................................................................- 14 - 1.6.1 工作特点...................................................................................................- 14 - 1.6.1.1 减速比大...........................................................................................- 14 - 1.6.1.2 倾动力矩大.......................................................................................- 14 - 1.6.1.3 启动制动频繁,承受的动载荷大...................................................- 14 - 1.6.1.4 工作条件恶劣...................................................................................- 15 - 1.6.2 结构要求...................................................................................................- 15 - 1.6. 2.1 满足工艺需要...................................................................................- 15 - 1.6. 2.2 具有两种以上倾动速度...................................................................- 15 - 1.6. 2.3 安全可靠运转...................................................................................- 15 - 1.6. 2.4 良好的适应性...................................................................................- 15 - 1.6. 2.5 结构紧凑效率高...............................................................................- 15 -