A08M-6.1-02汽车零件渗碳淬火技术条件-有效硬化层深度.tds
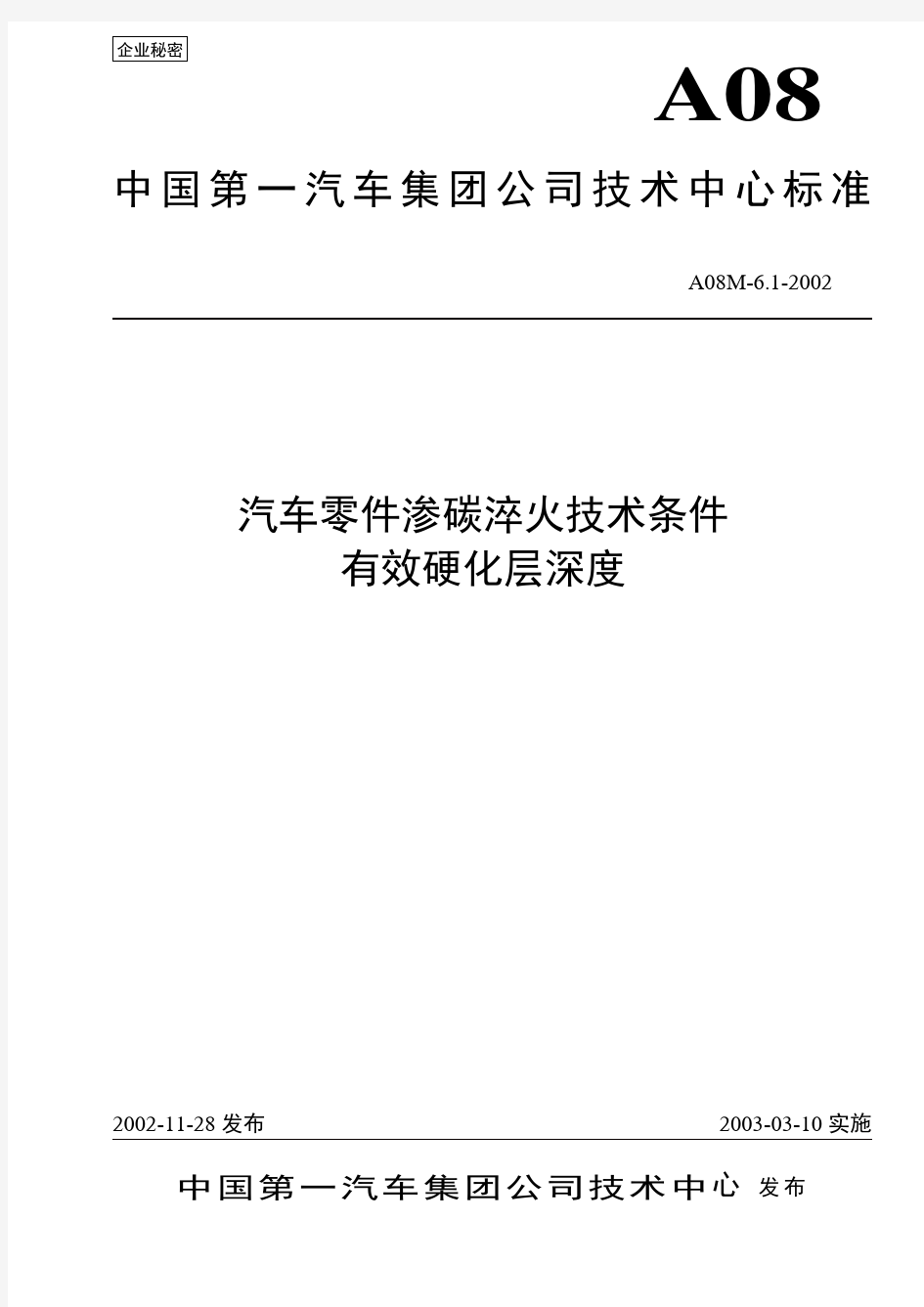

浅谈齿轮渗碳淬火有效硬化层及硬度梯度
浅谈齿轮渗碳淬火有效硬化层及硬度梯度 随着机械工业的发展,对齿轮的质量要求日益提高,而齿轮的强度寿命和制造精度与热处理质量有很大关系。为了检验齿轮材料热处理质量,在1987年以前,我国的齿轮渗碳淬火内在质量检验标准多为终态金相检验标准。由于检测仪器的精度、分辨率等因素以及检验人员的经验参差不齐,造成检验结果有很大差异和争议。为了解决金相法内在检验存在的弊端,机械部在1987年借鉴了DIN.ISO等标准中有关内容,修订了我国现行齿轮渗碳淬火内在质量检验标准。此检验标准中,其金相组织检验标准基本与原标准相似,主要是对渗碳层深度及碳浓度梯度的测定作了较大的修改。下面就渗碳层深度和碳浓度梯度分别采用金相法与硬度法测定进行简述。 一、渗碳层深度的检测 1.1、金相法 1.1.1、取本体或与零件材料成分相同,预先热处理状态基本 相似的圆试样或齿形试样进行检测。 1.1.2、送检试样热处理状态为平衡状态,即退火状态。 1.1.3、低碳钢渗层深度为:过共析层+共析层+1/2亚共析层。 1.1.4、低碳合金钢渗层深度为:过共析层+共析层+亚共析层。 1.2、硬度法 1.2.1、取样方法同金相法取样方法一致。 1.2.2、送检试样状态为淬火+回火状态。 1.2.3、渗碳深度用有效硬化层来表示,其极限硬度根据不同要
求进行选择。 1.2.4、有效硬化层深度(DCp):从试样表面测至极限硬度(如 HV550)之间垂直距离。 1.3、两种关于渗碳深度检测的方法存在着一定的对应关系,下面 用图形来描述。 从图中可看出:DCp(芯部)>DCp(HV500)>DCp(HV550) DCp(HV550)对应渗碳层中碳含量约为0.35~0.38%,此界限处即为金相法中1/2亚共析层处。 DCp(HV500)对应渗碳层中碳含量约为0.31~0.33%,此界限处为金相法中1/2亚共析层处。 DCp(芯部)对应渗碳层中碳含量为基体碳含量,一般为0.17~0.23%,此界限处为金相法中基体组织。
渗碳层深度
渗碳层深度 渗碳层深度(Carburized case depth)就是由渗碳工件表面向内至碳含量为规定值处(一般为0。4%C)得垂直距离。渗碳层(Carburized case)就是指渗碳工件含碳量高于原材料得表层。某渗碳层深度得测量有维氏硬度法、断口法与金相法、维氏硬度法直接反映了零件得力学性能(硬度),就是国家标准指定得唯一仲裁方法,但因操作复杂效率低而较少被采用,生产中一般用断口法与金相法。断口法常用于零件炉前检查,便于控制零件出炉时间;金相法则就是渗碳后对零件进行相应热处理,通过分析热处理后得组织来判定渗碳层得深度,就是生产中常用得测试零件渗碳层深度得方法。 中文名 渗碳层深度 外文名 Carburizedcase depth 学科 冶金工程 领域 冶炼 释义 渗碳工件表面向内至碳含量得距离 应用 18Cr2Ni4WA钢 目录
2. ?维氏硬度测定法简介 3. 4总结 简介 编辑 低碳钢与合金钢渗碳时得主要区别在于低碳钢比合金钢渗层中得碳浓度要低,其组织与硬度略有不同,但对渗碳层深度测量无影响、由于渗碳层具有变化得碳浓度,其由表及里逐渐减小,退火状态得渗碳层由表及里由以下三个区域组成: ①过共析层组织为珠光体+二次渗碳体; ②共析层组织为珠光体; ③亚共析渗碳层过渡层,组织为珠光体+铁素体。珠光体逐渐减少,铁素体逐渐增加,直 到心部原始组织(珠光体+铁素体),渗碳缓冷试样渗碳层界限为出现铁素体组织,较容易区分。 飞机防扭臂销棒材料为18Cr2Ni4WA钢,要求在外径φ38、5mm得两端各40mm内渗碳,渗碳层深度为1.0~1、4mm、采用气体渗碳法对该零件进行渗碳,对渗碳后过程试样水淬打断,测定渗碳深度为1。2mm,深度符合要求,零件及随炉试样出炉。 随炉试样经正火后测定渗碳层深度为0.9mm,渗碳层深度不符合要求,零件判定为不合格。为此,针对炉前测定合格、随炉试样正火后检测为不合格,且两者测定深度相差0、3mm得情况,开展了渗碳后热处理工艺、组织与深度测试得分析与探讨[1]。 渗碳后热处理工艺与组织 编辑 渗碳后淬火及组织 渗碳过程试样φ8mm×100mm随零件经920±10℃渗碳约615min后出炉水淬打断,表面渗碳层组织为粗针状马氏体加较多得残余奥氏体与少量碳化物,而心部组织为低碳马氏体(板条状马氏体),由于淬火温度高,心部几乎没有析出铁素体。 在10~40倍得读数显微镜下直接观察断面,外层(渗碳层)就是银亮且带闪光点得一圈,内层(心部组织)为均匀得浅灰色,两者界限分明、但此法易将亚共析过渡层与心部组织交接处混为一体,造成对渗碳深度过深得误判。 渗碳后退火及组织 随炉金相试样Φ38mm×40mm经850±10℃加热并保温50~55min,随炉冷却到400℃后出炉,从表面到心部均可得到马氏体,在高碳区与基体交界处经常有针状贝氏体析出,但在金相显微镜下观察其界限往往不甚清晰。 渗碳后正火及组织 18Cr2Ni4WA钢试样渗碳后出炉空冷得淬透直径达Φ75mm,从表面到心部均为马氏体。其表层为高碳马氏体,心部为低碳马氏体,在高碳区与基体交界处经常有针状贝氏体
齿轮表面渗碳及渗碳深度
仪器在400倍以上的放大倍数下测量压痕。 测定应在各方约定的位置上,在制备好的试样表面上的两条或更多条硬化线上进行,并绘制出每一条线的硬度分布曲线 二.齿轮固体渗碳工艺 (一)渗碳剂的成份及其作用: 固体渗碳剂主要是由木炭粒和碳酸盐(BaCO3或Na2CO3等组成。木炭粒是主渗剂,碳酸盐是催渗剂。 木炭颗粒均匀,并要求3—6mm左右的占80%,1—3mm左右占20%左右,1mm以下的不大于1%,如果是大零件渗碳,大颗粒木炭应多些,小零件,小颗粒应多些。常用的渗碳剂成份如表1所示。 常用渗碳剂的成份 渗碳加热时,炭与其间隙中的氧作用(不完全燃烧),生成一氧化碳。 2C+O2—→2CO 一氧化碳在渗碳条件下,是不稳定的。活性碳原子被钢件表面吸收,并向内部扩散。整个反反应过程可用下式示意表示:C+CO2—→2CO—→CO2+[C]单独用木炭进行渗碳,周期长,效果差,为了增加渗碳剂的活性,增加活性碳原子数量,一般加入一定数量的碳酸盐作为催渗剂。催渗剂在高温下与木碳产生如下反应:BaCO3+C—→BaO2+CO Na2CO3 + C(木炭) —→ Na2O + 2CO 2CO —→ CO2 + [C]渗碳过程中,木炭受到了烧损,但催渗剂分解氧化物,在开箱冷却时与空气接触,如按下方程式进行还原,这使催渗剂消耗大为减少。BaO+CO2—→BaCO3,Na2O+CO2—→Na2CO3 为了提高催渗剂再生效果,在此介绍一种有效的方法,即将高温下倒出来的渗碳剂,立刻用水喷洒(水的重量是渗碳剂重量的4—5%)。通过这样的处理,碳酸盐可得较完全的再生,其原因是:BaO+CO2—→BaCO3这个过程随温度下降而缓慢,如果在高温下喷水,就能使BaO变成氢氧化钡,而氢氧化钡向碳酸钡转变
渗碳层深度
渗碳层深度 渗碳层深度(Carburized casedepth)就是由渗碳工件表面向内至碳含量为规定值处(一般为0、4%C)得垂直距离。渗碳层(Carburizedcase)就是指渗碳工件含碳量高于原材料得表层。某渗碳层深度得测量有维氏硬度法、断口法与金相法.维氏硬度法直接反映了零件得力学性能(硬度),就是国家标准指定得唯一仲裁方法,但因操作复杂效率低而较少被采用,生产中一般用断口法与金相法。断口法常用于零件炉前检查,便于控制零件出炉时间;金相法则就是渗碳后对零件进行相应热处理,通过分析热处理后得组织来判定渗碳层得深度,就是生产中常用得测试零件渗碳层深度得方法。 中文名 渗碳层深度 外文名 Carburized case depth 学科 冶金工程 领域 冶炼 释义 渗碳工件表面向内至碳含量得距离 应用 18Cr2Ni4WA钢 目录
2. ?维氏硬度测定法简介 3. 4总结 简介 编辑 低碳钢与合金钢渗碳时得主要区别在于低碳钢比合金钢渗层中得碳浓度要低,其组织与硬度略有不同,但对渗碳层深度测量无影响。由于渗碳层具有变化得碳浓度,其由表及里逐渐减小,退火状态得渗碳层由表及里由以下三个区域组成: ①过共析层组织为珠光体+二次渗碳体; ②共析层组织为珠光体; ③亚共析渗碳层过渡层,组织为珠光体+铁素体。珠光体逐渐减少,铁素体逐渐增加,直 到心部原始组织(珠光体+铁素体),渗碳缓冷试样渗碳层界限为出现铁素体组织,较容易区分. 飞机防扭臂销棒材料为18Cr2Ni4WA钢,要求在外径φ38、5mm得两端各40mm内渗碳,渗碳层深度为1、0~1、4mm。采用气体渗碳法对该零件进行渗碳,对渗碳后过程试样水淬打断,测定渗碳深度为1、2mm,深度符合要求,零件及随炉试样出炉。 随炉试样经正火后测定渗碳层深度为0、9mm,渗碳层深度不符合要求,零件判定为不合格。为此,针对炉前测定合格、随炉试样正火后检测为不合格,且两者测定深度相差0、3mm得情况,开展了渗碳后热处理工艺、组织与深度测试得分析与探讨[1]。 渗碳后热处理工艺与组织 编辑 渗碳后淬火及组织 渗碳过程试样φ8mm×100mm随零件经920±10℃渗碳约615min后出炉水淬打断,表面渗碳层组织为粗针状马氏体加较多得残余奥氏体与少量碳化物,而心部组织为低碳马氏体(板条状马氏体),由于淬火温度高,心部几乎没有析出铁素体。 在10~40倍得读数显微镜下直接观察断面,外层(渗碳层)就是银亮且带闪光点得一圈,内层(心部组织)为均匀得浅灰色,两者界限分明。但此法易将亚共析过渡层与心部组织交接处混为一体,造成对渗碳深度过深得误判。 渗碳后退火及组织 随炉金相试样Φ38mm×40mm经850±10℃加热并保温50~55min,随炉冷却到400℃后出炉,从表面到心部均可得到马氏体,在高碳区与基体交界处经常有针状贝氏体析出,但在金相显微镜下观察其界限往往不甚清晰. 渗碳后正火及组织 18Cr2Ni4WA钢试样渗碳后出炉空冷得淬透直径达Φ75mm,从表面到心部均为马氏体。其表层为高碳马氏体,心部为低碳马氏体,在高碳区与基体交界处经常有针状贝氏体析出,故渗碳深度得测定一般就是从表面直到贝氏体结束处,但在金相显微镜下其界限仍然模糊。
齿轮热处理
1 齿轮热处理概述众所周知,齿轮是机械设备中关键的零部件,它广泛的 用于汽车、飞机、坦克、齿轮传动是近代机它具有传动准确、结构紧凑使用寿命长等优点。轮船等工业领域。是机械产品重要器中最常见的一种机械振动是传递机械动力和运动的一种重要形式、基础零件。它与带、链、摩擦、液压等机械相比具有功率范围大,传动效率高、圆周速度高、传动比准确、使用寿命长、尺寸结构小等一系列优点。因此它已成为许多机由于齿轮在工业械产品不可缺少的传 动部件,也是机器中所占比例最大的传动形式。得益于近年来汽车、风电、. 发 展中的突出地位,使齿轮被公认为工业化的一种象征据大规格齿轮加工机床的需求增长十分耀眼。核电行业的拉动,汽车齿轮加工机床、近年来涉及齿轮加工机床制造的企业也日益增随着齿轮加工机床需求的增加,了解,多。无论是传统的汽车、船舶、航空航天、军工等行业,还是近年来新兴的高铁、铁对齿轮加工机床制都对机床工具行业的快速发展提出了紧迫需求,路、电子等行业,万吨。但 我国齿轮的质量年将达到200 2012 造商提出了新的要求。据权威部门预测主要 表现在齿轮的平均使用寿与其他发达国家的同类产品相较还是具有一定的差距,本设计是在课堂学习热处理知识后的探索和单位产品能耗、生产率这几方面上。命、并按重点是制定合理的热处理规程,尝试,其内容讨论如何设计齿轮的热处理工艺,此设计齿轮的热处理方法。齿轮是机械工业中应用最广泛的重要零件之一。其主要作用是传递动力,改变运 动速度和方向。是主要零件。其服役条件如下:齿轮工作时,通过齿面的接触来传递动力。两齿轮在相对运动过程中,既有滚动,(1)在齿根部位受因此,齿轮 表面受到很大的接触疲劳应力和摩擦力的作用。又有滑动。到很大的弯曲应力作用;word 编辑版. ⑵高速齿轮在运转过程中的过载产生振动,承受一定的冲击力或过载;⑶在一些特殊环境下,受介质环境的影响而承受其它特殊的力的作用。因此,齿轮的表面有高的硬度和耐磨性,高接触疲劳强度,有较高的齿根抗弯强度,高的心部 抗冲击能力。齿轮常用材料有。20Cr ,20CrMnTi, 18Cr2Ni4WA①20Cr降温直接淬火对渗碳时有晶粒长大倾向,有较高的强度及淬透性,但韧性较差。可切削性良好,冲击韧性影响较大,因而渗碳后进行二次淬火提高零件心部韧性;20Cr 为珠光体,焊接性较好,焊后一般不需热处理。但退火后较差;②20CrMnTi 20CrMnTi是性能良好的渗碳钢,淬透性较高,经渗碳淬火后具有高的强度和 韧性,特别是具有较高的低温冲击韧性,切削加工性良好,加工变形小,抗疲劳性能好。 ③18Cr2Ni4WA
钢的渗碳硬化深度的检测方法
钢的渗碳硬化深度的检测方法 1.适用范围此规格规定了钢的渗碳淬火或碳氮共渗淬火时的硬化层深度(以下,称硬化 层)的检测方法。 备注:1 此规格出自以下规格 JIS B 0601 表面粗糙度—定义及表示 JIS G 0201 钢铁用语(热处理) JIS G 0202 钢铁用语(试验) JIS Z 2244 维氏硬度检测方法 JIS Z 2244 洛氏硬度检测方法 2 与此规格相对应的国际规格如下所示。 ISO 2639: 1982 Steel-Determination and verification of the effective depth of carburized and hardness case 3 附表是有效硬化层深度的辅助检测方法。 2.用语的定义此规格使用的主要用语的定义,除出自JIS G 0201 及JIS G 0202 之外,还出 自以下几项 (1)有效硬化层深度淬火后,或用不超过200℃的温度进行挥霍的硬化层的表面开始,到 表1所示的界限硬度的位置的距离。但是,关于非硬化区域的硬度超 出维氏硬度450时,根据双方协议,也可以使用超出维氏硬度550(维 氏硬度25刻度的)界限硬度。 (2)全硬化层深度从硬化层的表面开始,到硬化层与素材的物理性质或是化学性质几乎没有 差异时的位置的距离。 备注:这里所说的物理性质用硬度,化学性质用宏观组织来判定。 (3)硬度推移曲线从硬化层表面开始的,表示垂直距离和硬度之间关系的曲线。 3.测定方法的种类 3.1硬度试验测定方法对试验块的断面通过硬度检测来测定硬化层深度的方法。 3.2宏观组织试验测定方法吧试验块的断面腐蚀后,在低倍率的放大镜下进行观察,测定 硬化层深度的检测方法。 备注:硬化层深度的检测方法,一般使用硬度试验的测定方法,要是简单一点的话,就 用宏观组织试验测定方法。 4.试验品试验品原则上使用产品本身。但是,不得已时也可以使用与产品同种条件下的同 一钢种的钢材。 5.硬度试验检测方法 5.1 把试验品沿与硬化层垂直的方向切开,把切开面研磨后作为被检测面。切割或是研磨时, 注意不要对被检测面的硬度造成影响,同时,不要使边部变圆。 5.2 关于被检测面,根据JIS Z 2244 的维氏硬度试验或由双方协定进行洛氏试验力 硬度试验,制作硬度推移曲线,根据此曲线测定有效硬化层或是全硬层 深度。这时,维氏硬度试验的试验荷重,原则上使用2.9N.但是,如 有必要,也可使用0.98~98.1N的荷重。 5.3 硬度推移曲线的制作,如下所示。 (1)在需要做测定的被检测面,沿与表面相垂直的直线,依次检测硬度,制作硬度推移曲
渗碳层深度
渗碳层深度 令狐采学 渗碳层深度(Carburized case depth)是由渗碳工件表面向内至碳含量为规定值处(一般为0.4%C)的垂直距离。渗碳层(Carburized case)是指渗碳工件含碳量高于原材料的表层。某渗碳层深度的测量有维氏硬度法、断口法和金相法。维氏硬度法直接反映了零件的力学性能(硬度),是国家标准指定的唯一仲裁方法,但因操作复杂效率低而较少被采用,生产中一般用断口法和金相法。断口法常用于零件炉前检查,便于控制零件出炉时间;金相法则是渗碳后对零件进行相应热处理,通过分析热处理后的组织来判定渗碳层的深度,是生产中常用的测试零件渗碳层深度的方法。 中文名 渗碳层深度 外文名 Carburized case depth 学科 冶金工程 领域 冶炼 释义 渗碳工件表面向内至碳含量的距离
应用 18Cr2Ni4WA钢 目录 1. 1 简介 2. 2 渗碳后热处理工艺与组织 3. ?渗碳后淬火及组织 4. ?渗碳后退火及组织 5. ?渗碳后正火及组织 简介 编辑
低碳钢与合金钢渗碳时的主要区别在于低碳钢比合金钢渗层中的碳浓度要低,其组织和硬度略有不同,但对渗碳层深度测量无影响。由于渗碳层具有变化的碳浓度,其由表及里逐渐减小,退火状态的渗碳层由表及里由以下三个区域组成: ①过共析层组织为珠光体+二次渗碳体; ②共析层组织为珠光体; ③亚共析渗碳层过渡层,组织为珠光体+铁素体。珠光体逐渐减少,铁素体逐渐增加,直到心部原始组织(珠光体+铁素体),渗碳缓冷试样渗碳层界限为出现铁素体组织,较容易区分。 飞机防扭臂销棒材料为18Cr2Ni4WA钢,要求在外径φ38.5mm 的两端各40mm内渗碳,渗碳层深度为1.0~1.4mm。采用气体渗碳法对该零件进行渗碳,对渗碳后过程试样水淬打断,测定渗碳深度为1.2mm,深度符合要求,零件及随炉试样出炉。 随炉试样经正火后测定渗碳层深度为0.9mm,渗碳层深度不符合要求,零件判定为不合格。为此,针对炉前测定合格、随炉试样正火后检测为不合格,且两者测定深度相差0.3mm的情况,开展了渗碳后热处理工艺、组织与深度测试的分析与探讨[1] 。渗碳后热处理工艺与组织 编辑 渗碳后淬火及组织 渗碳过程试样φ8mm×100m m随零件经920±10℃渗碳约615min后出炉水淬打断,表面渗碳层组织为粗针状马氏体加较多
表面淬火材料的硬度及淬火深度检测方法
上海中研仪器制造厂 https://www.360docs.net/doc/1f7714203.html,/ 钢铁零件表面淬火硬度及淬火深度检测方法 A、首先熟悉以下两个名词: 1、有效硬化层深度(DS):是指从零件表面到维氏硬度等于极限硬度那一层之间的距离。 2、极限硬度:是指零件表面所要求的最低硬度乘以系数,通常HV1试验力系数可以选用 0.8,也可以选用0.9或者更高(如零件表面硬度320HV,那么极限硬度 =320X0.8=256HV)。 B、试验力的选择 通常选用显微维氏硬度计,试验力通常选用HV1(9.807N),也可选用4.9N-49N范围内。 C、检测 1、检测应在规定试样表面的一个或者多个区域内进行,并在图纸上注明。 2、检测试样的制备: 应在垂直淬硬面切取试样,切断面作为检测面。检测面应做好磨抛处理,使其达到光洁如镜。在切割、磨抛过程中要注意避免工件过热、变形、出现倒角等。详见上海中研仪器制造厂技术文章栏目内的《金相试样制备流程》,这里不做过多阐述。 3、硬度检测: 硬度压痕应当打在垂直于表面的一条或多条平行线上,而且宽度为1.5mm区域内,最靠近表面的压痕中心与表面的距离为0.15mm,从表面到各逐次压痕中心的距离应每次增加0.1mm。当表面硬化层深度大时,各压痕中心的距离可以大一些,但在接近极限硬度区域附近,仍应保持压痕中心之间的距离为0.1mm。 4、测量结果: 用垂直表面横截面上的硬度变化曲线来确定有效硬化层深度。由绘制的硬度变化曲线,确定从零件表面到硬度值等于极限硬度的距离,这个距离就是感应淬火或火焰淬火后有效硬化层深度。 备注:一个区域内有多条硬度变化曲线时,应取各曲线测得的硬化层深度平均值,作为有效硬化层深度。有效硬化层深度用字母DS表示,深度单位为mm,例如硬化层深度0.5mm 可以写成DS0.5。 技术支持邮箱:zhongyanyiqi@https://www.360docs.net/doc/1f7714203.html,
渗碳层有效层标准修订事项说明2013.3.23
关于《拖拉机渗碳齿轮金相检验》标准修订的说明 一、有关渗碳齿轮金相检验标准 1.意大利菲亚特公司标准: 经过表面渗碳硬化热处理的齿轮零件的机械性能和组织特征检验方法(Q.NL/0025) A.表面硬度HRC58~60 心部硬度HRC33.5~43.5 (检测部位齿根圆) B.层深有效硬化层深(硬度法),测至525HV5处。齿根有效硬化层深应 不小于节圆所示深度的70%。 C.表面非马氏体层深≤0.01mm。 D.金相组织检测6项:碳化物、残余奥氏体、心部铁素体、氧化层、贝氏 体、显微裂纹。 2 . 汽车行业渗碳齿轮检验标准: 1)汽车渗碳齿轮金相标准BR5-74 (参照50-60年代前苏联标准) A.硬度按产品图心部硬度检测部位2/3齿高处 B. 层深渗碳层深法(金相法) C. 表面非马氏体层深无规定。 D.金相组织检测4项:碳化物、残余奥氏体、马氏体、心部铁素体。 2)汽车渗碳齿轮金相检验ZB T04 001-88 A.硬度按产品图心部硬度检测部位齿根圆 B.层深有效硬化层深法测至515HV5或550HV1处。 C. 表面非马氏体层深≤0.02mm。 D. 金相组织检测3项:碳化物、残余奥氏体、马氏体。 3)汽车渗碳齿轮金相检验QC/T262-1999
A.硬度按产品图心部硬度检测部位齿根圆 B.层深有效硬化层深法测至515HV5或550HV1处。 C.表面非马氏体层深按“齿轮材料及热处理质量检验的一般规定”GB 8539 D. 金相组织检测3项:碳化物、残余奥氏体、马氏体。 3.重载渗碳齿轮标准: 重载齿轮渗碳质量检验JB/T6141.2-1992 重载齿轮渗碳金相检验JB/T6141.3-1992 A.表面硬度HRC58~62 心部硬度HRC30~46(检测部位齿根圆) B.层深有效硬化层深法测至550HV1(或HRC 52)处。允许齿根部位的 有效硬化层深度比节圆处小15%。 C.金相组织检测4项:碳化物、残余奥氏体、马氏体、心部铁素体。 4 .拖拉机渗碳齿轮检验标准: 1)拖拉机渗碳齿轮金相检验标准:YTQ310.5-90 A. 硬度按产品图心部硬度检测部位2/3齿高处 B. 层深渗碳层深法(金相法) C. 表面非马氏体层深无规定。 D.金相组织检测3项:碳化物、残余奥氏体、心部铁素体。 2)新修订的拖拉机渗碳齿轮检验标准:Q/YT 310.5-2008 A. 硬度按产品图心部硬度检测部位齿根圆 B. 层深有效硬化层深法,测至515HV5或550HV1处。 C. 表面非马氏体层深≤0.04mm。 D.金相组织检测3项:碳化物、残余奥氏体、心部铁素体。
渗层厚度的测定
金相法渗层厚度的测定 一、实验目的 1)了解渗碳、渗氮工艺及渗碳后热处理的组织特征。 2)掌握金相法测定渗层深度的方法。 二、原理概述 渗碳是将钢件置于渗碳介质中,加热到单相奥氏体区,保温一定时间使碳原子渗入钢件表面层的热处理工艺。渗碳的目的是使钢件获得硬而耐磨的表面,同时又使心部保持一定的韧性和强度。对于进行渗碳的钢材是碳的质量分数一般都小于0.3%的低碳钢和低碳合金钢,渗碳后的工件主要用于受严重磨损和较大冲击载荷的零件,如齿轮、曲轴、凸轮轴等。渗碳温度一般取860~930℃,不仅使钢处于奥氏体状态,而又不使奥氏体晶粒显著长大。近年来,为了提高渗碳速度,也有将渗碳温度提高到1000℃左右的,渗碳层的深度根据钢件的性能要求决定,一般为l mm左右。按照渗碳介质的状态,可分为固体渗碳、液体渗碳和气体渗碳三种,常用固体和气体渗碳。 渗氮又称氮化,是指向钢的表面层渗入氮原子的过程。其目的是提高表面层的硬度与耐磨性以及提高疲劳强度、抗腐蚀性等。传统的气体渗氮是把工件放入密封容器中,通以流动的氨气并加热,保温较长时间后,氨气热分解产生活性氮原子,不断吸附到工件表面,并扩散渗入工件表层内, 渗入钢中的氮一方面由表及里与铁形成不同含氮量的氮化铁,一方面与钢中的合金元素结合形成各种合金氮化物,特别是氮化铝、氮化铬。这些氮化物具有很高的硬度、热稳定性和很高的弥散度,因而可使渗氮后的钢件得到高的表面硬度、耐磨性、疲劳强度、抗咬合性、抗大气和过热蒸汽腐蚀能力、抗回火软化能力,并降低缺口敏感性。与渗碳工艺相比,渗氮温度比较低,因而畸变小,但由于心部硬度较低,渗层也较浅,一般只能满足承受轻、中等载荷的耐磨、耐疲劳要求,或有一定耐热、耐腐蚀要求的机器零件,以及各种切削刀具、冷作和热作模具等。渗氮有多种方法,常用的是气体渗氮和离子渗氮。目前生产中多采用气体渗氮法。 1.渗碳工艺 将渗碳件置入具有活性碳气氛中加热到860~930℃,保温一定时间,再将渗碳后的钢件按照性能要求不同,进行不同的热处理工艺有直接淬火、一次淬火和二次淬火三种。2.渗碳及渗碳淬火后的金相组织 钢在渗碳后因冷却方式不同,可得到平衡状态的组织或非平衡状态的组织。 (1)平衡状态的渗碳组织、 钢渗碳缓冷后的显微组织符合铁一碳平衡相图,表面到中心依次是过共析区、共析区、亚共析区和原始组织(图1是20钢渗碳后的平衡组织)。渗碳的过程是碳原子在γ-Fe中 的扩散过程。
齿轮渗碳淬火工艺培训讲义(1)
齿轮渗碳淬火工艺培训讲义 一、齿轮受力状态及失效形式: 1、受力状态:齿面摩擦力、齿面接触应力和齿根弯曲应力。 2、失效形式: 齿面剥落:表面网状碳化物和渗碳过渡区拉应力是造成齿面剥落的原因。 麻点:齿面金属的塑性变形和齿面的摩擦力导到齿面产生疲劳裂纹,润滑油挤入加速裂纹扩展,由此而产生麻点。 断裂:表现为断齿或断轴,原因为齿轮基体强度不夠。 二、齿轮渗碳淬火通用技术要求: 1、对原材料的要求要: 根据不同使用要求对材料疏松、成份偏析、非金属夹物、带状组织、原始晶粒度和材料淬透性等均有不同级别要求。 2、对预备热处理组织状态和热处理硬度的要求: 包括组织状态、基体硬度、晶粒度等。 3、对最终热处理质量的要求: 包括渗碳淬火表面硬度、渗碳层深度和渗层金相组织、工件基体组织及硬度、强度等。 三、齿轮渗碳淬火工艺规程: 1、渗碳淬火齿轮(低速重载和高速齿轮) 选材: 2、渗碳齿轮工艺流程:锻造---正火---机加工---渗碳淬火---精加工---强力喷丸。
3、齿轮渗碳淬火技术要求: 4、正火热处理:
5、齿轮渗碳工艺: 渗碳淬火工艺曲线 温度 时间 6、使用设备: 可控气氛多用炉。 7、装炉工装及装料方式:详见附图。 (1)使用工装: 工装料架应为抗渗碳、抗热疲劳、高温具有高强度的高Ni-Cr 含量材质的工装。工装结构视工件大小、结构特征而定。工装的结构应保证工件加热、冷却均匀,有利于减小工件淬火变形。 (2)、装料方式: 一般齿轮类工件垂直挂装,套类齿轮多层碼放。工件间应留有一定间隙,以保证不同工件和相同工件不同部位加热和冷却均匀。 滚动件均匀、薄层应平摊于料筛底部,采用多层料筛叠放装料的形式较好。 8、淬火介质及淬火冷却方式: (1)、淬火介质采用德润宝或好富顿淬火油较好。因为这类淬火油蒸气膜持续时间短,蒸气薄且厚度均匀,奥氏体不稳定区冷速较高,有利于避免其产生非马转变;马氏体转变温度下的冷却速度较慢,有利于减小工件淬火应力和淬火变形。 (2)、淬火介质的搅拌强度和循环方向: 选择强力向下搅拌为宜,但最终应根据工件淬火效果确定。
自攻螺钉渗碳层深度的金相法测定
自攻螺钉渗碳层深度的金相法测定 浏览次数:发布时间:2007-11-5 在我国的行业标准中,金相法对渗碳层的测定要求必须在退火状态下。这样,渗碳层与基体色泽界限明显,能比较直观、准备地测出渗碳层深度。但是,在实际情况下,有哪种渗碳零件是在退火状态下使用呢?这样测得的渗碳层在零件在工作状态下的渗碳层吗?能满足零件在工作状态时对渗层的要求吗?我 们能不能用金相法对工作状态的渗碳零件直接测定其渗碳层呢? 渗碳层深度测量有断口法——主要适用于较深层渗碳的炉前测定;显微硬度法——主要用于渗碳层深度的仲裁测定,能直接反映零件渗碳层深度;金相法——普遍用于对渗碳零件生产控制过程中。在 GB/T3098.5——2000自攻螺钉机械性能中,推荐用金相法测自攻螺钉的渗碳层深度,而显微维氏硬度法仅做仲裁。可见,用金相法测自攻螺钉的渗碳层是可行的,也是必要的。 我公司生产的自攻螺钉,普遍采用材质为SWRCH18A、SWRCH22A钢,冷加工成型后,采用在网带炉里渗碳、直接淬火+低温回火工艺。由于自攻螺钉渗层比较浅,渗层深度容易控制,炉前检查一般由热处理技术员用火花鉴别法初步判定渗碳浓度及深度,做一定的定性分析,然后再送理化室做定量检测。下面,我们就以自攻螺钉ST6.3X22为例来谈谈用金相法直接测定自攻螺钉的渗碳层深度。 一、取样 按GB/T3098.5——2000自攻螺钉机械性能中的推荐规定,用金相法检测自攻螺钉渗碳层深度应在螺纹侧面上进行,测点应该在牙顶与牙底的距离之半处,对规格小于或等于ST3.9的自攻螺钉,应在牙底上进行试验。但是有的金相工作者在实际的工作中,喜欢在头部或头部支承面处取样,因为在头部或头部支承面渗碳层相对比较均匀,而且该处也比较光滑,能比较直观地测出渗层。但是,我个人认为这是不足取的,因为自攻螺钉在工作中,其渗碳层性能的直接体现应该是螺纹,因此我们应该在牙顶与牙底距离之半处取样。 二、渗碳层分析 我们都知道渗碳零件的渗碳层都具有变化的碳浓度,由表及里逐渐减少,它由特别典型的三个区域组成:过共析层、共析层、过渡层。对于浅层渗碳件自攻螺钉来说,过共析层在正常情况下是没有的,只存在共析层和过渡层。 该自攻螺钉采用的热处理参数为:渗碳(温度约880℃)→预冷淬火(温度约840℃)→回火(温度约200℃)。其表面碳浓度为:共析层含碳量0.5%—0.8%,组织为隐针回火马氏体+少量极细针回火马氏体;过渡层(亚共析层)含碳量0.18%—0.5%,组织为极细针状回火马氏体+针状回火马氏体+板条回火马氏体+少量铁素体。 三、渗碳层深度的确定 对于渗碳自攻螺钉来说,要确定其渗碳层深度必找出共析层及过渡层界限。现在,我们就沿该螺钉轴向剖开,做成金相试样(腐蚀剂为4%硝酸酒精溶液)测定其渗碳层深度。 金相法测定渗碳层的深度是建立在渗碳层组织的变化基础上。含碳量在0.18%左右的自攻螺钉经预冷至
淬回火零件渗碳层深度的金相法测定
淬回火零件渗碳层深度的金相法测定 陈静,易琨 (东风汽车电气公司,襄樊441021) 摘要:金相法测定渗碳层深度要求试件必须为退火状态。采用金相法对淬火+低温回火状态渗碳试件进行了渗层深度的测定,并对其误差作了对比分析。实验说明,直接用金相法测定淬火+低温回火状态的化学热处理试件渗层深度是可行性的。 关键词:淬火和回火;渗层深度;金相法测定 1 引言 渗层深度的测量有断口法、显微硬度法和金相法。断口法仅适用于热处理炉前检查;显微硬度法能直接反映零件的力学性能,为渗层深度的仲裁方法,并有相应的国家标准[1]及行业标准[2];金相法采用渗碳后缓冷试样测定渗层,由于检测效率较高且界限明显而得到广泛使用[3]。目前渗碳层深度的测定若是仲裁和校核则采用显微硬度法[4],一般生产控制普遍采用金相法。 我公司生产的汽车渗碳齿轮材质为20CrMo钢,采用气体渗碳,渗碳后采用预冷直接淬火+低温回火工艺,炉前检测渗碳层深度采用断口法,最终检验采用试件缓冷后的金相法。由于试件状态与实际生产零件的不同,退火金相法测定的结果不能代表零件的最终使用状态,因此需要对预冷直接淬火+低温回火零件直接进行渗层深度测量,但是目前对淬火+低温回火零件渗碳层深度的测定尚无明确的方法与界限阐述。 2 淬回火件渗层深度金相法测量的可行性 目前国内常用的渗碳钢有20钢、20Mn钢、20Cr钢、20CrMo钢和20CrMnTi钢等,其含碳量均在低碳钢(或低碳合金钢)范围。低碳钢与合金钢渗碳时的主要区别在于低碳钢比合金钢渗层中的碳浓度要低,其组织和硬度略有不同,但对渗碳层深度测量无影响。由于渗碳层具有变化的碳浓度,其由表及里逐渐减小,退火状态的渗碳层由表及里由以下三个区域组成[5]:①过共析层组织为珠光体+二次渗碳体;②共析层组织为珠光体;③亚共析渗碳层过渡层,组织为珠光体+铁素体。珠光体逐渐减少,铁素体逐渐增加,直到心部原始组织(珠光体+铁素体),渗碳缓冷试样渗碳层界限为出现铁素体组织,较容易区分。 渗碳零件采用渗碳预冷直接淬、回火工艺的一般工艺曲线如下[6]。
表面热处理零件有效硬化层、渗层等的有关说明
表面热处理零件有效硬化层、渗层等的有关说明 一、常用热处理零件硬化层深度、渗层深度有关术语、定义、代号和适用范围及检测方法
附注:①特殊情况下,经有关方协议,也可采用 4.903N~49.03N(0.5kgf~5kgf)内的某一试验力和其他值的极限硬度值,在特殊情况下要注明,如Dc49.03/515=0.6表示采用试验力49.03N(5kgf),极限硬度值为515HV时的有效硬化层深度等于0.6mm; ②特殊情况下,经有关方协议,也可采用4.903N~49.03N(0.5kgf~5kgf)内的某一试验力和其他值的极限硬度值,在特殊情况 下要注明,如Ds4.903/0.9=0.6表示采用试验力4.903N(0.5kgf),极限硬度值等于零件表面所要求的最低硬度的0.9倍时的有效硬化层深度等于0.6mm; ③测量方法有显微组织测量法和显微硬度测量法,选择的测量方法和它的精度取决于硬化层的性质和估计的深度。由于测量方 法也影响到测量结果,因此选择哪种方法测量及何种试样形式,必须在图纸和工艺上预先规定; ④当工艺/图纸没有规定测量方法时,优先采用显微硬度法。用显微硬度测量法检测时,一般试验力用1.96N(0.2kgf)的界线显 微硬度为基体硬度加30HV,除非工艺/图纸另有规定; ⑤试验力为0.9807N(0.1kgf)(HV0.1),极限硬度值HG一般规定为基体硬度加30HV。特殊情况下,经有关方协议,也可采用
其他试验力的显微硬度和极限硬度值; ⑥试验力为0.9807(0.1kgf)(HV0.1),特殊情况下,经有关方协议,也可采用其他试验力的显微硬度和极限硬度值; ⑦测量方法有硬度法和金相法两种,采用哪种测量方法应预先规定。硬度法规定采用试验力为2.94N(0.3kgf)的维氏硬度,从试 样表面测至比基体硬度高50HV处的垂直距离为渗氮层深度,对于渗氮层硬度变化很平缓的钢件(如碳钢、低碳低合金钢制件)可从试样表面沿垂直方向测至比基体维氏硬度值高30HV处。特殊情况下,可由有关方协议,也可采用其他试验力和其他维氏极限硬度值,但应在工艺/图纸文件中注明。 二、对实际应用中的几点说明 1、本文是为了统一理解,使其规范化和标准化而编制的,要求各部门有关人员认真执行; 2、从前面表中所列术语可知,凡是有效硬化层深度都有一个极限硬度(或称界线硬度)的要求,对不同零件、不同的热处理方法、 不同的材料、不同的热处理要求的零件其定义的有效硬化层深度的极限硬度可能是不同的,因此,在设计图纸和编制工艺时应同时确定合理的极限硬度,只有可采用标准中规定了的极限硬度,工艺/产品图纸才可不作规定。 3、从2004年5月1日起,设计、工艺人员新设计编制的产品图、工艺文件应统一采用本文的相关术语,对于有同义的术语,只选择 带※的术语。 4、对于2004年5月1日以前设计、编制的产品图纸和工艺文件有相关热处理深度的术语,统一按照本文相应的术语来理解或解释, 对有明显不符本文的术语的个别零件,由技术开发部填写更改单经批准后进行更改。上述时间以前的产品图纸有的有渗层深度要求又有有效硬化层深度要求的零件,在验收产品时,只检测有效硬化层深度,允许不检渗层深度,其图纸工艺再版时再作更改。 编制:审核:审定: 技术开发部 2004年4月12日
表1有效硬化层的界限硬度
1.适用范围 本标准规定钢的火焰淬火和高频淬火硬化层深度(以下称硬化层深度)的测定方法。 2.术语的意义 本标准所用主要术语的意义如下: (1)有效硬化成深度 从淬火状态或淬火回火状态的硬化层表面到表1中所规定的界限硬度位置的距离。 另外,根据用途也可以规定表1以外的界限硬度。 表1 有效硬化层的界限硬度 钢的含碳量% (1)维氏硬度HV洛氏硬度HR C ≥0.23—<0.3335036 ≥0.33—<0.4340041 ≥0.43—<0.5345045 ≥0.5350049 注:钢的含碳量为被测定钢的标准规定含碳量标准的中间值。 (2)全硬化深度 从硬化层表面到硬化层与基体在物理或化学性能的差异几乎无法区别的位置的距离。 注:这里所指的物理性能是以硬度来衡定,而化学性能则是用宏观组织来判断。 (3)硬度变化曲线 是指硬度与距硬化层表面的垂直距离之间的关系曲线。 3.测定方法的种类 (1) 硬度测定法 是在试样的切断面上用硬度测定其硬化侧深度的方法。 (2)宏观组织测定法 是将试样切断面进行腐蚀而用低倍放大镜观察、测定硬化层深度的方法。 注:测定硬化层深度通常采用硬度测定法:宏观组织测定方法是作为一种简便方法而采用。 4.试样 试样原则上应用制品本身,但是在不得已的情况下,可以用与零件的淬硬部位有相同形状、相同尺寸,同一钢种并与零件在同样条件处理的试样 5.硬度测定方法 5.1 将试样沿与淬硬表面垂直的方向切断,切断面经抛磨成检验面。在切断和抛光过程中,必须充分注意不要影响检验面的硬度,同时边缘不要磨成圆角。
5.2在被检验面进行维氏硬度或洛氏硬度HRc测量,然后绘制成硬度变化曲线,从这些曲线测定有效硬化层深度或全硬化层深度。维氏硬度测量的负荷使用0.1—10Kgf(0.98—98.1牛顿)。 注:()内单位和数值是国际单位制(SI),供参考。 5.3 硬度变化曲线依下列方法绘制; (1)在被检面需要测定的位置,沿着与其表面相垂直的直线上顺次测定硬度,根据测定数据绘成硬度变化曲线;但有时也在被检面的1.5mm范围内取2—5点,分别从各点沿与表面相垂直的直线上测定硬度,然后绘成一条硬度变化曲线(参照下图) (2)采用维氏硬度测量绘制硬度变化曲线时,测定点的间隔原则上应不大于0.1mm;另外,若要洛氏硬度测量绘制硬度变化曲线则应有各方协商决定。 (3)维氏硬度试验时的相邻压痕的中心间隔应大于压痕对角线长度的2.5倍。 5.4除上述规定,按JIS Z 2244(维氏硬度试验方法)或JIS Z 2245(洛氏硬度试验方法)。 6 宏观组织测定法 6.1 沿淬硬面处置切断,切断面经抛磨即为检验面。在切断和研磨过程中,必须充分注意不要影响检验面的组织。检验面的光洁度应为6.3S。 检验面用5%左右的硝酸酒精溶液或5%的硝酸水溶液腐蚀适当的时间,直到腐蚀出清晰的硬化层为止,然后用水和酒精冲洗干净,吹干后在20倍以下的放大镜下观察。 6.2 圈硬化层深度是从表面测到与基本具有不同腐蚀颜色的地方的深度。 7 标记 7.1 硬化层深度以毫米表示,精确小数点以下一位。 7.2 硬化层深度的标记代号如表2所示: 表2 硬化层深度标记代号 测定方法硬化层硬度测量法宏观组织测定法 用维氏硬度时用洛氏硬度时 高频淬火有效硬化深度火焰淬火有效硬化深度高频淬火全硬化深度火焰淬火全硬化深度HD—HΔ—E ( ) FD—HΔ—E ( ) HD—HC—E( ) FD—HC—E( ) HD—HC—T FD—HC—T — — HD—M—T FD—M—T
钢铁零件表面淬火后的硬度及淬火深度检测方法
钢铁零件表面淬火后的硬度及淬火深度检测方法有效硬化层深度(DS):是指从零件表面到维氏硬度等于极限硬度那一层之间的距离。 极限硬度(HVHL):是指零件表面所要求的最低硬度(HVMS)乘以系数,通常HV1试验力系数可以选用0.8,也可以选用0.9或者更高(如零件表面硬度320HV,那么极限硬度=320X0.8=256HV)。 1、试验力的选择 ---通常选用显微维氏硬度计,试验力通常选用HV1(9.807N),也可选用4.9N-49N范围内。 2、检测 a、检测应在规定试样表面的一个或者多个区域内进行,并在图纸上注明。 b、检测试样的制备: --- 应在垂直淬硬面切取试样,切断面作为检测面。检测面应做好磨抛处理,使其达到光洁如镜。在切割、磨抛过程中要注意避免工件过热、变形、出现倒角等。详见技术文章栏目内的《金相试样制备流程》,这里不做过多阐述。 c、硬度检测: ---硬度压痕应当打在垂直于表面的一条或多条平行线上,而且宽度为 1.5mm区域内,最靠近表面的压痕中心与表面的距离为0.15mm,从表面到各逐次压痕中心的距离应每次增加0.1mm。当表面硬化层深度大时,各压痕中心的距离可以大一些,但在接近极限硬度
区域附近,仍应保持压痕中心之间的距离为0.1mm。 d、测量结果: ---用垂直表面横截面上的硬度变化曲线来确定有效硬化层深度。由绘制的硬度变化曲线,确定从零件表面到硬度值等于极限硬度的距离,这个距离就是感应淬火或火焰淬火后有效硬化层深度。 备注: --- 一个区域内有多条硬度变化曲线时,应取各曲线测得的硬化层深度平均值,作为有效硬化层深度。有效硬化层深度用字母DS表示,深度单位为mm,例如硬化层深度0.5mm可以写成DS0.5。
齿轮热处理
1 齿轮热处理概述 众所周知,齿轮是机械设备中关键的零部件,它广泛的用于汽车、飞机、坦克、轮船等工业领域。它具有传动准确、结构紧凑使用寿命长等优点。齿轮传动是近代机器中最常见的一种机械振动是传递机械动力和运动的一种重要形式、是机械产品重要基础零件。它与带、链、摩擦、液压等机械相比具有功率范围大,传动效率高、圆周速度高、传动比准确、使用寿命长、尺寸结构小等一系列优点。因此它已成为许多机械产品不可缺少的传动部件,也是机器中所占比例最大的传动形式。由于齿轮在工业发展中的突出地位,使齿轮被公认为工业化的一种象征. 得益于近年来汽车、风电、核电行业的拉动,汽车齿轮加工机床、大规格齿轮加工机床的需求增长十分耀眼。据了解,随着齿轮加工机床需求的增加,近年来涉及齿轮加工机床制造的企业也日益增多。无论是传统的汽车、船舶、航空航天、军工等行业,还是近年来新兴的高铁、铁路、电子等行业,都对机床工具行业的快速发展提出了紧迫需求,对齿轮加工机床制造商提出了新的要求。据权威部门预测2012 年将达到200 万吨。但我国齿轮的质量与其他发达国家的同类产品相较还是具有一定的差距,主要表现在齿轮的平均使用寿命、单位产品能耗、生产率这几方面上。本设计是在课堂学习热处理知识后的探索和尝试,其内容讨论如何设计齿轮的热处理工艺,重点是制定合理的热处理规程,并按此设计齿轮的热处理方法。 齿轮是机械工业中应用最广泛的重要零件之一。其主要作用是传递动力,改变运动速度和方向。是主要零件。其服役条件如下: (1)齿轮工作时,通过齿面的接触来传递动力。两齿轮在相对运动过程中,既有滚动,又有滑动。因此,齿轮表面受到很大的接触疲劳应力和摩擦力的作用。在齿根部位受到很大的弯曲应力作用; ⑵高速齿轮在运转过程中的过载产生振动,承受一定的冲击力或过载; ⑶在一些特殊环境下,受介质环境的影响而承受其它特殊的力的作用。 因此,齿轮的表面有高的硬度和耐磨性,高接触疲劳强度,有较高的齿根抗弯强度,高的心部抗冲击能力。 齿轮常用材料有20Cr ,20CrMnTi, 18Cr2Ni4WA。 ①20Cr 有较高的强度及淬透性,但韧性较差。渗碳时有晶粒长大倾向,降温直接淬火对
如何解决渗碳或碳氮共渗零件有效硬化深度的测试
如何解决渗碳或碳氮共渗零件有效硬化深度的测试 目前,在我国航空、航天、汽车、兵器等众多单位的零件加工和热处理工艺都涉及渗碳或碳氮共渗的问题,针对客户的需求,我司开发出半自动显微硬度测试系统,快速解决有效硬化层深度测量。 针对半自动显微硬度计测试系统FEM-7000的特点,介绍一下此系统在工厂中常用的功能,齿轮热处理方法使用碳氮共渗工艺的最多,,作到俗说的“表硬心软”,需要对渗碳的有效深度作检测。现在的标准采用硬度梯度法,大多数都采用1Kgf 载荷,看HV550时的深度值。具体做法如图示:以齿顶为基准,从表面向心部连续打多个点,分别测出各点之硬度,绘制硬度曲线 齿轮剖面示意图 硬度曲线示意图
以往通过此方法作测试时,大家普遍困难的是此工作较繁杂。一是要打多个点测硬度,二是要不断移动和记录载物台移动量,三是手工绘制曲线图。这几个环节易出的问题分别是:一测量时人为误差,二移动物台的精度,三绘图的准确性。往往做一个样品用很长时间,一天若需大量做此工作,人会很疲劳影响测试精度。而现在利用半自动测试系统(FEM-7000) 可以大大提高效率与精度。首先硬度计主机具有自动打压痕功能,第二由于采用自动载物台,可以在测试前将要测点的坐标值一次输入,仪器会自动找到设置点,位移回复精度在2 m以内,第三仪器测试后,由打印机打印一份标准报告,包括数据与曲线图,也可以利用Windows 中的Word软件自己编辑,在报告中任意插入文字、数字及图片,另外打印机还可以打印金相组织的图谱。 重点介绍半自动显微硬度测试系统的功能:FEM-7000半自动显微硬度测试系统是一台以日本F-T公司(FUTURE-TECH CORP.)生产的FM-700型显微硬度计为主机,由电脑控制的自动载物台及高分辨率的CCD图象采集游标测量装置组成的显微硬度测量系统。 该系统由三部分组成: 1. FM-700显微硬度计 2. 自动载物台及PC电脑控制器 3. 高分辨CCD图象采集装置及电脑游标测量装置和数据处理激光打印系统。 其特点分别为: 1.FM-700显微硬度计特点 FM-700显微硬度计是2000年由日本F-T公司推出的最新型显微硬度计。它是当前世界上最完善的显微硬度计,它是在原日本松泽公司MXT-α7的基础上作了重要改进的显微镜型显微硬度计。具有以下特点: 1) AUTO TURRET 物镜压头物镜自动转换。在目镜的视域里选好所要测 试的点后,按START,压头会自动旋至已选好点的位置, 自动打压痕后, 物镜再自 动旋回到原位,这时在目镜中便可观察到清晰的压痕, 再进行测量。 2) 触摸式照明LCD菜单式显示屏取代原有繁多的操作按键,操作十分方便并有HV对其 它12种标尺的自动对照转换值, 如 (HK.HRA.HRB.HRC.HB.HS) 3)有内装微处理器存贮多达999个测量数据,并具有对测量数据的数理统计(最大 值、最小值、均方差、平均值、偏差)等。 4) 配接打印机可将测量结果全部打印输出。 5) 配接电脑控制的自动载物台及高分辨CCD图像采集游标测量装置可组成半自动测量 系统(参阅FEM-7000)。 6) FM-700显微硬度计可在原有2个物镜(10倍、40倍)外,另任选配装一个物镜 (5 倍、20倍、50倍、100倍)。这样FM-700同时也成为一台高品质的明场显微 镜。