供应商质量能力审核评估要素检查表
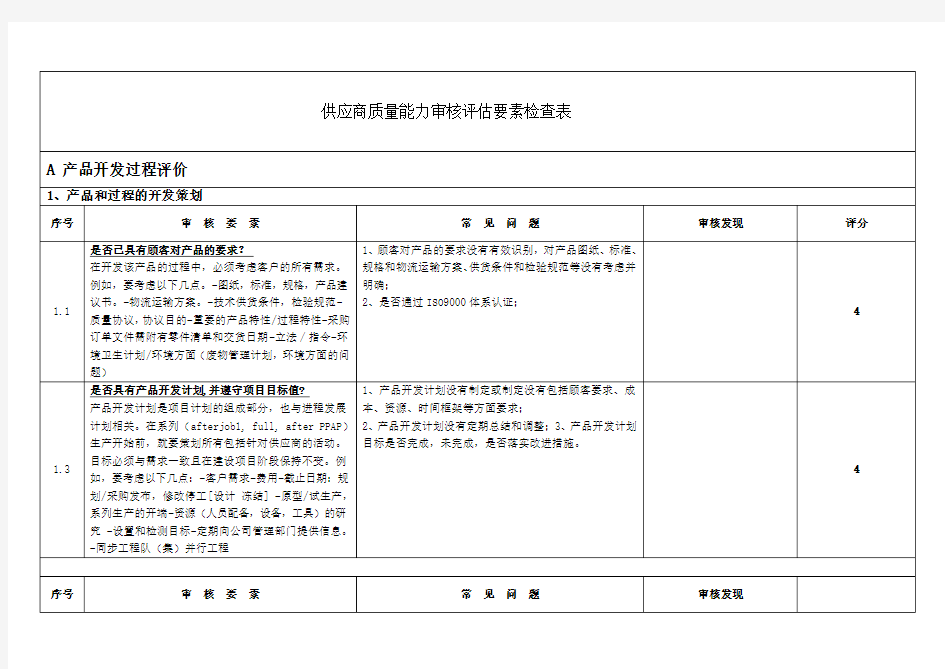

供应商质量能力审核评估要素检查表
A 产品开发过程评价
1、产品和过程的开发策划
序号审核要素常见问题审核发现评分
1.1 是否已具有顾客对产品的要求?
在开发该产品的过程中,必须考虑客户的所有需求。
例如,要考虑以下几点。-图纸,标准,规格,产品建
议书。-物流运输方案。-技术供货条件,检验规范-
质量协议,协议目的-重要的产品特性/过程特性-采购
订单文件需附有零件清单和交货日期-立法∕指令-环
境卫生计划/环境方面(废物管理计划,环境方面的问
题)
1、顾客对产品的要求没有有效识别,对产品图纸、标准、
规格和物流运输方案、供货条件和检验规范等没有考虑并
明确;
2、是否通过ISO9000体系认证;
4
1.3 是否具有产品开发计划,并遵守项目目标值?
产品开发计划是项目计划的组成部分,也与进程发展
计划相关。在系列(afterjob1, full, after PPAP)
生产开始前,就要策划所有包括针对供应商的活动。
目标必须与需求一致且在建设项目阶段保持不变。例
如,要考虑以下几点:-客户需求-费用-截止日期:规
划/采购发布,修改停工[设计冻结] -原型/试生产,
系列生产的开端-资源(人员配备,设备,工具)的研
究 -设置和检测目标-定期向公司管理部门提供信息。
-同步工程队(集)并行工程
1、产品开发计划没有制定或制定没有包括顾客要求、成
本、资源、时间框架等方面要求;
2、产品开发计划没有定期总结和调整;
3、产品开发计划
目标是否完成,未完成,是否落实改进措施。
4
序号审核要素常见问题审核发现
2.2 是否已获得各阶段所要求的认可/合格证明?
要证明所有个别零件,部件和购买部分的版本或者资
格记录。例如,要考虑以下几点:产品实验(如装修视
察(零部件装配∕应用)功能测试,耐用性检查,环
境模拟)原型零件的状态试点序列模型生产/检验,在
试验安装中测量和试验设备。
1、对产品的合格认可不合格,无改进措施或措施未落实
到位;
2、产品开发各阶段无推进计划或未实施进度和有效性监
控。
4
2.4 生产和检查文件完整可用吗?
工艺参数/检查的特点是始终有公差,工作站检查站必
须有生产和检验文件。不合格将被记录在案,有详细
资料,例如:工艺参数(如压力,温度,时间,速度)机
械/工具/辅助手段数据检验要求(重要特征,检验,
测量和测试设备,方法,检验频率)工艺控制图(控
制限制)中的干预限制机械和加工能力的记录操作说
明工作指示检查指导记录不合格部分。(记录和跟踪不
合格材料)
1、生产和检查文件不完整,检验员不能方便得到检验作
业指导书,现场的检验设备操作说明和试验规范不完整,
工艺文件不完
整;;
2、生产或检验不合格没有记录和有效处理。 4
2.5 批量生产的能力和要求是否已具备?
所需资源取自报价计算和预案。他们必须可用,或者
在规定的时间(适时)分别规划和提供。对此的必要
手段必须包括在该项目中。例如,要考虑以下几点。
客户需求人才由于旷工浪费[时间可控和不可控]通过
处理时间建筑,房地试验装置原型建设工具/设备测试
/检查/实验室设备。
1、产品开发的量产能力未确认即开始量产;
2、量产确认不规范,产品尺寸、性能、工装模具和检验
检测设备、人力配置等都有评审得到确认后进入量产阶
段。 4
序号审核要素常见问题审核发现
3.1 是否仅允许已认可并具备质量能力的分供应商供货是
否对分供方的质量绩效进行了评价?当出现偏差时是
否采取了措施??
在确定分供方前必须存在质量体系审核结果(认证 /
审核)。投入批量生产前,应确保仅从适宜的分供方
处采购。应考虑其以往的质量绩效的评估情况。
需考虑的要点,例如:
- 与分供方会谈 / 定期跟踪
- 质量能力评价,例如审核结果、过程审核 / 产品审
核、质量管理体系认证
- 根据质量绩效(质量 / 成本 / 服务)的高低级别
进行选择
- 关键控制特性供应商的特别认可
常见问题:
- 对批量和潜在供应商没有有效的管理和评价方法;
- 没有严格实施公司对于分供方的管理方法,过于关注成
本,未淘汰不合格分供方;
- 合格分供方清单信息不完整,未及时更新;供应商分类
不合理;
- 新供应商“先供货,后审核”,未进行潜在评价;
- 工序外包时未纳入分供方管理;
- 缺少对分供方(包括关键的n级分供方)质量能力的掌
握;
- 没有审核计划,未按计划对分供方实施过程审核;审核
计划未涵盖全体分供方;
- 审核报告的质量,审核改进工作未进行跟踪;有没有合
理的供方质量绩效评价系统?- 评价涵盖的范围:前期、
批量、售后、顾客、市场、质量能力等;- 评价数据的来
源是否可靠?评价结果是否符合实际情况?- 如何有效
的利用评价结果?和目标有偏差时的分析和整改措施;-
评价结果持续恶化,没有相应的措施(如降级和计划外的
过程审核等);- 未对评价结果不佳的分供方进行问题分
析、改进计划和跟踪工作;TOP5最差供应商;- 质量绩
效评价结果应和新项目定点挂钩
4
3.2 是否可以保证采购件符合约定的质量要求?
应能在本企业内(自身核心技术、出现问题时快速反
应)进行基本、必要的检验(实验室和测量设备)。
需考虑的要点,例如:
- 足够的检验可能性(实验室和测量设备)
- 内部的 / 外部的检验
- 所提供的量具 / 工装器具
- 图纸 / 订货要求 / 规范
- 质量保证协议
- 对检验方法、检验流程、检验频次的约定
- 对主要缺陷的分析
- 能力验证(尤其针对产品和过程的关键特性)
常见问题:
- 没有有效的入库检验工作,如缺乏测量和检验设备、进
口零件免检、没有针对零件的入库检验计划等;
- 没有认真进行入库检验工作,审核复检时数据和记录有
明显差异,检验记录无批次信息;
- 不确定的检验计划,包括检验方法、检验流程和抽样标
准等;没有考虑近期的质量问题;
- 不合理的零件特性重要度分级,关注关键特性;
- 分供方自检报告未确认;自检结果和入库检验结果不做
对比,有重大差异情况下的处理规范;检验记录未进行统
计分析和关键特性的定期Cpk计算等;
- 让步接收的管理要求过于简单;缺少详细的不合格品/
让步接收处理记录;
- 出现不合格后的处理流程和整改有效性跟踪,入库检验
应加严;
- 免检制度,“永远免检”,没有退出机制;
4
3.4 是否与分供方就产品和过程的持续改进目标达成了协
议并落实?
这一任务对模块供货具有重要的意义。供应商对分供
方的持续改进负有全部责任。
需考虑的要点,例如:
- 工作小组(由各相关部门组成)
- 确定质量、价格及服务的量化目标,例如:
- 在提高过程可靠性的同时降低检验成本
- 减少废品(内部 / 外部)
- 减少在制品量
- 提高顾客满意度
常见问题:;
- 没有基于数据分析的合理目标;针对外购件关键特性制
定的质量目标;
- 分供方质量问题分析,8D报告的水平,5Why,鱼刺图,,,
避免问题的再次/重复发生;
- 8D报告的有效性,问题分析的深入性;
- 过程改进,能力提升目标;
- 缺少针对质量、成本和服务等方面与分供方不断改进的
目标/协议,并监控其完成;
4
3.5 已批量供货的产品是否已获得所要求的认可?要求的
改进措施是否已落实?在新的 / 更改的产品 / 过程
批量投产前,必须对分供方的所有产品进行放行。若
采用模块供货,供应商对所有的单个零部件的质量监
控负有全部的责任。需考虑的要点,例如:- 顾客信
息(其中如技术规范 / 标准 / 检验规范)- 工程样
件的认可、试制样件的认可- 符合要求的首批样品检
验报告- 重要特性的能力证明- 可靠性分析评估- 定
期的对产品全部特性的检验报告- 材料和重量的文件
常见问题:A)新产品的认可:- 新产品/产品更改后认可
流程、认可内容的规定(可以参考VDA或TS手册)- 新
产品尚未完成认可即批量供货;认可中发现的问题没有得
到有效整改,并重新送样;- 分供方报告中的材料、尺寸、
性能等内容未做复检,以分供方的报告数据作为认可报告
数据存在很大的风险;- 认可报告存档内容不统一,没有
规范要求;B)批量产品的监控:- 综合产品风险判断,
制定合理的监控方法:简单的以分供方提交的产品型式试
验报告作为年度监控是不够的;- 没有年度的产品型式试
验要求:每年完成一次完整的产品型式试验;- 产品型式
试验中出现问题时的处理流程和记录;
4
3.7 原材料的库存量是否适合生产要求?在过程策划时就
必须已调查并考虑到了所要求的库存量。在要求已发
生变更的情况下,应酌情重新进行需求分析。需考虑
的要点,例如:- 顾客要求- 看板 / 准时交付- 仓储
成本- 原材料 / 外购件供货出现瓶颈时的应急计划
(应急战略)- FIFO(先进先出)
常见问题:- 没有建立先进的计算机管理系统:人工管理
存在不足;- 管理系统数据问题:帐、卡、物及其库位实
际情况和记录不符;- 库存量预警机制;库存量管理(成
本和供货风险);- 库存量管理条件没有根据实际的生产
变化而进行更新;- 应急计划;- 仓库条件;- 特殊时期
(如节假日、让电期间等)对分供方生产的影响,和原材
料的储备工作;
4
3.8 原材料 / 内部剩余材料是否按要求发送 / 仓储?
按放行状态仓储发放的原材料和从生产部门退回的剩
余材料,防止损坏和混放。有疑问的 / 隔离的产品必
须仓储在隔离库中。
需考虑的要点,例如:
- 包装
- 仓库管理系统
- FIFO(先进先出)/ 按批次投入使用
- 有序和清洁
- 气候条件
- 防损 / 防污 / 防锈
- 标识(可追溯性 / 检验状态 / 工作流程 / 使用状
态)
- 防混料
- 隔离仓库(设置和使用)
常见问题:
- 仓库条件:面积、、库位明显;
- 仓库布局:隔离区、试制品区、辅料区、化学品和危险
品区等;
- 帐、卡、物的统一;
- 批次管理:按原材料生产批次管理(而不是入库批次)、
FIFO、有效期管理(按生产日期而不是入库日期);颜色
管理(颜色区分批次)
- 状态管理:明显的标识(待检、合格、可疑、待确认、
呆滞物资、加工工序、使用状态等)
- 包装和料箱:零件防护、清洁、防磕碰伤、生锈、灰尘
等;兼顾物流过程简洁;
- 抽检、发运零件后的包装需要恢复原样,开箱后必须关
闭;
- 来料包装损伤的管理要求;
- 生产退回多余零件的管理:临时储存而不入帐、不防护、
无标识、随意放置等;
4
3.9 是否根据员工所承担的任务对其进行了培训?需考虑
要点如负责下列工作的人员:- 分供方的选择、评价、
培训- 产品检验- 仓储/运输- 物流必须具备有关知
识,例如:- 产品 / 技术规范 / 顾客特殊要求- 模
块供货中每个零部件的产品特性和生产流程的专业知
识- 标准/法规- 包装- 生产- 评价方法(例如:审
核,统计)- 质量技术(例如 8 D 方法、因果图)
常见问题:- 条款1~8审核发现的问题,是否为人员素
质不足造成?- 员工素质不能满足岗位要求,需培训;-
分供方审核人员的资质;- 物流人员的培训和岗位要求:
化学品的有效期识别、重要零件的运输、零件包装/料箱
上的警示和储存要求等;-入库检验人员能否熟练操作测
量设备; 4
4。生产过程管理
4.1 人员/素质
序号审核要素常见问题审核发现
4.1.1 员工是否负有监控产品质量 / 过程质量的职责?
需考虑的要点,例如:
- 提出改进计划
- 操作工自检
- 过程认可(设备点检 / 首件检验 / 末件检验)
- 过程控制(理解控制图)
- 终止生产的权利
常见问题:
-员工不了解产品特性、质量要求、检验和评价方法;
-没有识别并指出生产设备、检测设备和操作指导文件中
的缺陷;
-没有识别不同文件之间对于产品要求和设备参数的偏
差;
-检验记录不能识别或一成不变,记录和实际测量有偏
差;
-未按照控制计划严格执行过程认可和零件自检;
-不能理解控制图,不能对控制图做出判定和反应;
-没有主动标识和隔离可疑产品;问题重复情况下未停止
生产和汇报;
-没有执行公司对于“落地零件”的处理要求;
4
4.1.3 员工是否适于完成所交付的任务,并保持其素质?
需考虑的要点,例如:
- 过程上岗指导 / 培训 / 资格的证明
- 关于产品和可能 / 已出现缺陷的专业知识
- 对安全生产 / 环境意识的指导
- 对存档责任件的零部件的处置的指导说明
- 能力证明(例如焊工证书、视力检查、厂内机动车
驾驶证)
常见问题:
-没有有效的新员工培训和考核制度:应知应会,注重岗
位技能;
-班组长的特别培训;
-注重实际上岗培训:包括各种动作、防错、检验等,通
过“做”和复述记住岗位要求;
-培训记录和考核:上岗证的获得、必要的实习期、独自
上岗初期的特别关照;
-培训/考核记录和员工技能矩阵表结果不符合;
-特殊工种的要求和管理:国家资历证明、视力/听力的
定期检查、工间休息(疲劳);
-换岗未培训;新产品生产未培训;员工长时间停工后复
工前未培训;
-没有持续的培训,培训内容不全面;未调查员工的培训
需求;
4
4.2 生产设备设施
序号审核要素常见问题审核发现
4.2.1 生产设施 / 工装模具是否能确保产品特定的质量要
求?
对于选定的重要产品特征 / 过程特性,要测算其过程
能力并不断进行验证。对于短期过程能力(MFU)和临
时过程能力(PFU),Cmk / PpK 必须≥ 1.67。长期
过程能力Cpk 必须至少达到最低要求 Cpk ≥ 1.33,
并得到持续改进。
需考虑的要点,例如:
- 对重要特性 / 过程特定的参数进行机器能力调查
/ 过程能力调查
- 重要参数的强制 / 调整
- 在偏离极限值时报警(例如:声光报警,喇叭、自
动断闸)
- 上料 / 下料装置
- 工装、模具 / 设备 / 机器的保养、维护状态(包
括计划内的维护)。
常见问题:
-没有定期计算重要特性相关的Cpk值;
-Cpk值不满足要求时的措施;
-重要过程参数的强制性控制/调整;人员权限;
-防错的应用不足;
-设备性能的定期验证工作;
-设备/工装模具履历表管理和使用寿命统计;
-生产过程中对产品的防护,特别如上下料位置、有表面
质量的零件;
-进口设备/关键设备的know-how不够(特别是外资企
业);
4
4.2.2 批量生产中使用的测量和检验设备能否有效地监控质
量要求?
需考虑的要点,例如:
- 可靠性试验、功能试验和耐腐蚀试验
- 测量精度 / 检测工具能力调查
- 数据采集和可评价性
- 检测工具校准的证明
常见问题:
-测量设备的状态、能力、精度符合要求;
-可操作性,如使用夹具取代三坐标;
-检具的保养状态,有无标样检验检具;测量前未置零位;
-校准和标定,班前标定后,班中/班后是否有差异;
-极限样件;
-MSA测量系统分析;
4
4.2.4 是否在生产文件和检验文件中列举了全部的相关规定
并切实遵守?
原则上必须为过程参数、检验和实验特性标明公差。
在生产工位和检验工位必须有相应的生产文件和检验
文件。必须记录存档偏差与采取的措施。
需考虑的要点,例如:
- 过程参数(例如压力、温度、速度、时间)
- 机器 / 工装、模具 / 辅助工具的数据
- 检测要求(重要特性、检验器具、方法、检验频次)
- 过程控制图的控制极限
- 设备能力证明和过程能力证明
- 操作指导书
- 作业指导书
- 检验指导书
- 缺陷事件的最新信息
- 过程参数的调整应能防止未经准许的干预
常见问题:
-工艺/检验文件:有没有、是否全面、是否有效、是否
执行?
-各类文件在现场不能方便的获取,现场文件不是最新状
态;
-没有根据具体零件制定文件,特别是检具指导书;
-没有标明重要事项和关键要求,包括近期质量缺陷;
-大量的文字描述,难以掌握;重视图示的作用;
-返修、返工的管理;
-SPC控制图的控制限没有定期计算;
-人员权限管理;控制柜关闭;
4
4.2.6 是否在生产开始时进行了认可,并记录设置的数据和
偏差情况?“批量生产认可”是按订单对生产起始的
认可(首次认可 / 重新认可)。应对产品和过程进行
认可,应由被授权的人员按验收标准进行书面认可。
此时应已消除了在产品策划 / 过程策划和 / 或以前
批量生产中识别的问题。应按明确的检验指导书进行
认可检查,以确保可重复性。在此应采用检查表。若
在抽取检验零部件后继续进行生产,则在被检验零部
件的认可前生产的产品应被隔离,直至认可。返修 /
返工也应被纳入认可过程中。需考虑的要点,例如:-
新产品、产品更改- 停机 / 过程中断- 修理、更换模
具- 更换材料(例如:更换批次)- 生产参数更改- 首
件检验及记录存档- 参数的现时性- 工作岗位的有序
和清洁- 包装- 工装、模具和检测设备的认可 / 更改
状态-变更的管理
常见问题:-生产起始的认可:设备点检、参数确认、来
料确认、首末件检验;-过程认可检查表的内容是否全面;
-过程认可:仅有开班时的认可,没有考虑过程中断后恢
复生产时的认可;-更换模具、参数更改、批次变化等,
无过程认可和记录;-记录不完善、难识别、和实际复检
有偏差等;-若在抽取检验零部件后继续进行生产,则在
被检验零部件的认可前生产的产品应被隔离,直至认可。
应有相应标识,防止流入下工序!-是否有变更管理-是
否存在变更 4
4.3 运输/搬运/仓储/包装
序号审核要素常见问题审核发现
4.3.1 生产数量 / 批次大小是否按需求而定,并有目的地运
往下一道工序?工序的外包是否会在物流链中造成额
外的产品风险?需考虑的要点,例如:- 外包的工序
(零部件搬运、增加的运输等在物流链中造成额外的
产品风险)- 合适的运输工具- 定置存放- 最小库存
/ 无中间库存- 看板管理- 准时交货- 先进先出- 仓
库管理- 更改状态- 只向下道工序提供合格件- 记录
/ 统计零部件数量- 信息流
常见问题:-生产计划管理;-中间库存;-无法实现
FIFO;-工序跟单卡的记录;-集中生产造成的大量中间
品,中间品批次管理不足;-合理的生产流程和流水线布
置;-有没有识别工序外包造成的对物流链的风险?如何
降低风险?
4
4.3.4 材料流和零部件流是否保证了不混批 / 不错料,并确
保了可追溯性?鉴于产品风险,必须确保从分供方至
顾客整个供应链的可追溯性。需考虑的要点,例如:-
零部件标识- 工作状态、检验状态和使用状态的标识-
批次标识- 失效日期- 去除无效标识- 附有零部件数
据 / 生产数据的工作文件
常见问题:-没有确保从分供方至顾客整个供应链的可追
溯性;-批次管理不到位,中间品没有实施FIFO;-不
混批、不混料;-明确的零件状态:加工、检验、使用等;
-有效期的管理;-无效标识未及时去除;
4
4.4 缺陷分析/纠正/持续改进
序号审核要素常见问题审核发现
4.4.1 质量数据 / 过程数据是否被完整地记录并具有可评
价性?
应出示完整的质量数据和过程数据,以证明是否满足
要求。必须确保可分析性。应记录异常情况(工作日
志)。
需考虑的要点,例如:
- 原始数据记录卡
- 缺陷收集卡
- 控制图
- 数据采集
- 过程参数(例如温度、时间、压力)的记录装置
- 设备停机
- 参数更改
- 停电
常见问题:
- 未搞清楚顾客是谁及其他们的期望;
- 不能有效识别关键过程;
- 质量信息没有可评价性;
4
4.4.2 是否通过统计技术对质量数据 / 过程数据进行了分
析,并由此得出改进计划?应确定发现和处理问题的
责任部门,由责任部门负责制订改进措施并落实。需
考虑的要点,例如:- 过程能力- 缺陷种类/缺陷频
次- 缺陷成本(不符合性)- 过程参数- 报废 / 返工、
返修- 隔离通知 / 分选行动- 生产节拍 / 单件全过
程生产时间- - 可靠性 / 失效方式- 功能可使用的
方法有,例如:- SPC- 排列图- 因果图
常见问题:-未定期统计关键特性的过程能力;-未统计
一次合格率;-未对缺陷种类进行分析和改进;-未对返
修/返工率进行持续改进;-收集了相关数据之后没有进
行有效的统计分析,质量和过程未得到持续改进;
4
5。顾客关怀/顾客满意度
序号审核要素常见问题审核发现评分
5.2 是否保证顾客关怀,并且收集和分析了顾客投诉?必
须确保针对不同的顾客职能部门,安排有能力的对口
人员。顾客关怀也是衡量积极合作的一个尺度。供应
商有义务对其产品从产生到使用的各个阶段进行关注
并在必要时进行改进。需考虑的要点,例如:- 顾客
访问的纪要,必要时制订出措施- 产品使用的知识-
产品故障的知识、运输方面的投诉- 落实新的要求-
通报改进措施- 通报产品和过程更改 / 易地生产(也
包括分供方)- 首批样品送检 / 重新送检(试制样品
/ 批产样品)- 重复认证检验- 出现与要求偏差时的
信息(也包括包装和运输)- 供应商物流数据的质量
(例如:关于周转箱库存的明细摘要)
常见问题:-缺乏合作的态度,合作才能共赢;-不进行
主动的顾客信息收集,如售后质量信息、Audit、各类试
验结果等;-没有定期的、涵盖各职能部门的顾客访问/
满意度调查;-现场服务人员不进行信息收集和问题汇
总;-没有问题收集和处理跟踪系统,不汇总各类抱怨;
-收集的顾客抱怨仅仅为正式抱怨,不包括口头、邮件等
其他途径信息;-作为发动机公司定点的非直接供应商,
对其供货的直接供应商的管理要求接受度较差;-产品/
过程更改、易地生产(包括分供方)必须通知顾客!
4
5.3 对顾客投诉是否能快速做出反应并确保零部件供应?
在过程策划时就要针对意外事件制定方案,以保障零
部件供货。在批量生产时要确
保方案的现时有效性。
需考虑的要点,例如:
- 应急计划(例如:其他可选择的制造、分供方、包
装、运输)
- 分选行动的能力和反应时间
- 对设备、特种生产设备和工模具的更改可能性
- 利用外部资源
常见问题:
-没有应急计划(特别如水、电、物流、信息传递、设备
突发故障等);
-分析内部过程,了解出现偏差的可能性;关键/瓶颈设
备的管理;
-未考虑产能预留量;通过零件储备来缓冲;
-返修、返工需进行质量证明;获得开发和质量部门认可
后才能特殊放行;
4
5.6 是否定期对关键特性或法规特性要求进行内部审核,
和其他法律要求进行的评价?
需考虑的要点,例如:
-审核计划
-完整地实施要求
-制定并跟踪改进计划
-分供方参与
-符合法律的零部件、总成等的书面确认
常见问题:
-安全件管理工作不到位;
-未定期进行特殊特性或安全件自审,并将报告提交相关
审核员;
-关键特性未识别,或仅仅局限于供方要求;
-记录不能识别;
-存档工作不完善,历史资料查阅困难;
-未考虑对分供方的要求;
4
供应商质量体系审核检查表.docx
供应商质量体系审核检查表 序号问题检查记录得分 一、质量管理及职责 1.1是否明确公司的质量管理机构和职责? A组织机构明确,部门的职能得到有效履 行; B有专职质量管理部门及质量检验人员; C质量管理负责人等职责分工明确; 1.2是否建立了质量分析会制度? A 定期召开公司内的质量会议,确认质量目 标值的达成情况; B领导把握质量状况,提出改善指示; C保存质量会议记录,确定需改进项目,且 他们的改进进度情况得到控制; D 改进效果得到验证,有彻底的反馈,其结 果令人满意 二、质量管理体系建设 2.1是否按计划进行有效的管理评审和内部审 核? A 应有完整的管理评审输入资料,支持状态 评审; B管理评审的输出应关注涉今世缘公司或 体系的重大改进,并有计划和措施支持; C内部审核覆盖所有部门和车间,并按重要 性安排,内外部审核发现的问题应采取措施 并跟踪验证。 2.2是否有质量方针? A有明确的方针且这些方针得到了积极的 实施; B主要的措施根据这些方针得以实施; C活动结果的进度情况根据这些方针得到 了控制。 2.3是否制定了质量目标?是否分解到各单位 及岗位? 有明确的目标,并且将目标按照管理层级进 行了分解; 2.4目标是否得到有效监控? A应对目标完成情况进行统计并分析; B应定期召开绩效评审会,针对适宜的绩效 指标所实施的持续改进活动计划应进行评 审。 三、文件和资料控制 3.1是否有文件化的控制体系? A有文件及各项必要的管理规定; B起草、审核、批准部门明确; C文件描述完备; D制定了员工培训文件的内容 3.2文件现场的使用状态? A根据需要,及时更新现场版本;
供应商质量体系审核检查表
供应商质量体系审核检查表
序号问题检查记录 得 分 一、质量管理及职责 1. 1 是否明确公司的质量管理机构和职责? A 组织机构明确,部门的职能得到有效履行; B 有专职质量管理部门及质量检验人员; C 质量管理负责人等职责分工明确; 1. 2 是否建立了质量分析会制度? A 定期召开公司内的质量会议,确认质量目标值的达成情况; B 领导把握质量状况,提出改善指示; C保存质量会议记录,确定需改进项目,且他们的改进进度情况得到控制; D 改进效果得到验证,有彻底的反馈,其结果令人满意 二、质量管理体系建设
序号问题检查记录 得 分 2. 1 是否按计划进行有效的管理评审和内部审核? A 应有完整的管理评审输入资料,支持状态评审; B管理评审的输出应关注涉今世缘公司或体系的重大改进,并有计划和措施支持; C 内部审核覆盖所有部门和车间,并按重要性安排,内外部审核发现的问题应采取措施并跟踪验证。 2. 2 是否有质量方针? A有明确的方针且这些方针得到了积极的实施; B 主要的措施根据这些方针得以实施; C活动结果的进度情况根据这些方针得到了控制。
序号问题检查记录 得 分 2. 3 是否制定了质量目标?是否分解到各单位及岗位? 有明确的目标,并且将目标按照管理层级进行了分解; 2. 4 目标是否得到有效监控? A 应对目标完成情况进行统计并分析; B 应定期召开绩效评审会,针对适宜的绩效指标所实施的持续改进活动计划应进行评审。 三、文件和资料控制 3. 1 是否有文件化的控制体系? A 有文件及各项必要的管理规定; B 起草、审核、批准部门明确; C 文件描述完备; D 制定了员工培训文
提升供应商质量管理方案
提升供应商质量管理方案 1.目的 确保供应商提供的物料满足XXXX建设对物料质量的要求,推动供应商持续改进,促使供应商过程能力不断提高,从而达到双赢。 2.范围 限于2015年入围并提供物料的供应商,不涵盖服务和施工供应商,不涵盖XXXXXXXXX供应商。 3.职责 3.1 管理组职责 供应商质量管理的策略规划和方向指引,提供必要的资源,指导和支持工作组的工作;组织工作组开展活动并对工作组的活动计划或总结等重要事项进行决策;协调或帮助工作组解决在开展活动时遇到的内部或外部障碍。3.2工作组职责 审查供应商产品的型式试验和产品认证情况、设计(图纸和技术协议的转化)和工艺(设备能力、工艺流程、作业方法等)能力及变更控制的管理情况;(技术人员) 审查供应商资信情况、财务三表和融资等财务运作能力;(财务人员)
审查供应商的生产能力、生产周期、成本控制和服务政策;(采购人员) 审查供应商的质量管理体系建立和执行情况;(体系人员) 审查供应商的重点过程质量控制情况,如:来料、过程、成品质量控制;人员培训和资格;设备点检、维护和保养;检测仪器或设备的检定校准;现场作业文件;半成品或成品的贮存和防护、标识和追溯;不合格品或异常处理等。(质量人员) 对供应商的审查结果做出评定或总结,必要时对部分供应商进行有针对性的辅导。 4.管理方案 4.1启动 4.1.1编写质量提升管理方案 由安全质量部编制供应商质量管理提升方案,报送部门主管审核确认无误后,由相关部门进行会签,确认无误后,报送公司领导签字发布。 《供应商质量提升管理方案流程图》见附件。 4.1.2成立管理组和工作组 经公司授权成立供应商质量管理组,由公司领导担任管理组组长,主管质量工作的副总任副组长,成员由质量
供应商质量能力
VOLKSWAGEN AG 德国大众汽车集团 供应商质量能力评定准则 质量管理体系-要求 潜在供应商评价 过程审核,产品审核验证(D/TLD-零件)
经全面修订的第四版德国大众汽车集团 2000年4月 4.vollstaendig ueberarbeitete Auflage Volkswagen AG, April 2000
第一版-1991年 第二版-1994年 1月 经全面修订的第三版-1997年 1月 经全面修订的第四版-2000年 4月 本中文版源自德文版的翻译。如有疑义,以德文版为准。 同时提供英文译本、西班牙文译本、葡萄牙文译本,捷克文译本。 我们将保留所有的权利,尤其是复制、传播以及翻译的权利。 出版者:德国大众汽车集团 集团供应商质量审核部 信箱:1467/0 D-38436 狼堡(Wolfsburg) 电话: (0049) 5361-973185 传真: (0049) 5361-972237
前言 此第四次全面修订版重视了德国汽车工业联合会(VDA)范围内的整车厂和供应商之间达成的新的质量战略,就是说,汽车工业的供应商必须证实其质量管理体系符合VDA 6.1或ISO/TS 16949的要求。 对于质量管理体系的具体要求,在VDA 6.1以及ISO/TS 16949中有详尽 的描述,本手册将不再把质量管理体系作为内容的组成部分。 针对新的质量战略,过程审核和产品审核是汽车制造厂和供应商们的重点,因此也就是本手册重点。对这两种审核的各种要求在实践经验的基础上进行了更准确的描述并部分地进行了补充。潜在供应商评价,作为对不了解的供应商在建立供货关系之前进行的先期检查,新被收录在本手册中。 “Formel Q-质量能力”手册是对“Formel Q-Konkret”
供应商质量能力审核评估要素检查表
供应商质量能力审核评估要素检查表 A 产品开发过程评价 1、产品和过程的开发策划 序号审核要素常见问题审核发现评分 1.1 是否已具有顾客对产品的要求? 在开发该产品的过程中,必须考虑客户的所有需求。 例如,要考虑以下几点。-图纸,标准,规格,产品建 议书。-物流运输方案。-技术供货条件,检验规范- 质量协议,协议目的-重要的产品特性/过程特性-采购 订单文件需附有零件清单和交货日期-立法∕指令-环 境卫生计划/环境方面(废物管理计划,环境方面的问 题) 1、顾客对产品的要求没有有效识别,对产品图纸、标准、 规格和物流运输方案、供货条件和检验规范等没有考虑并 明确; 2、是否通过ISO9000体系认证; 4 1.3 是否具有产品开发计划,并遵守项目目标值? 产品开发计划是项目计划的组成部分,也与进程发展 计划相关。在系列(afterjob1, full, after PPAP) 生产开始前,就要策划所有包括针对供应商的活动。 目标必须与需求一致且在建设项目阶段保持不变。例 如,要考虑以下几点:-客户需求-费用-截止日期:规 划/采购发布,修改停工[设计冻结] -原型/试生产, 系列生产的开端-资源(人员配备,设备,工具)的研 究 -设置和检测目标-定期向公司管理部门提供信息。 -同步工程队(集)并行工程 1、产品开发计划没有制定或制定没有包括顾客要求、成 本、资源、时间框架等方面要求; 2、产品开发计划没有定期总结和调整; 3、产品开发计划 目标是否完成,未完成,是否落实改进措施。 4 序号审核要素常见问题审核发现
2.2 是否已获得各阶段所要求的认可/合格证明? 要证明所有个别零件,部件和购买部分的版本或者资 格记录。例如,要考虑以下几点:产品实验(如装修视 察(零部件装配∕应用)功能测试,耐用性检查,环 境模拟)原型零件的状态试点序列模型生产/检验,在 试验安装中测量和试验设备。 1、对产品的合格认可不合格,无改进措施或措施未落实 到位; 2、产品开发各阶段无推进计划或未实施进度和有效性监 控。 4 2.4 生产和检查文件完整可用吗? 工艺参数/检查的特点是始终有公差,工作站检查站必 须有生产和检验文件。不合格将被记录在案,有详细 资料,例如:工艺参数(如压力,温度,时间,速度)机 械/工具/辅助手段数据检验要求(重要特征,检验, 测量和测试设备,方法,检验频率)工艺控制图(控 制限制)中的干预限制机械和加工能力的记录操作说 明工作指示检查指导记录不合格部分。(记录和跟踪不 合格材料) 1、生产和检查文件不完整,检验员不能方便得到检验作 业指导书,现场的检验设备操作说明和试验规范不完整, 工艺文件不完 整;; 2、生产或检验不合格没有记录和有效处理。 4 2.5 批量生产的能力和要求是否已具备? 所需资源取自报价计算和预案。他们必须可用,或者 在规定的时间(适时)分别规划和提供。对此的必要 手段必须包括在该项目中。例如,要考虑以下几点。 客户需求人才由于旷工浪费[时间可控和不可控]通过 处理时间建筑,房地试验装置原型建设工具/设备测试 /检查/实验室设备。 1、产品开发的量产能力未确认即开始量产; 2、量产确认不规范,产品尺寸、性能、工装模具和检验 检测设备、人力配置等都有评审得到确认后进入量产阶 段。 4 序号审核要素常见问题审核发现
供应商质量保证书范文
供应商质量保证书范文 1.名词定义: 原材料——指我司为了生产产品而购买的所有直接和间接材料,包括电子材料、五金塑料件、包装材料、辅助材料、外协加工产品等的统称。 需方——专指徐州市精英电器技术有限公司。 供方——指为我司提供所有原材料的厂商。 2.适用范围: 供方提供给需方的所有原材料出现质量问题时,均依本协议负责赔偿。 3.质量责任: 需方应承担对质量问题的事实和实际损失情况负有举证责任。供方承担证明该产品合格的举证责任。 需方对于原材料的品质控制采用委托供方检验的方式,即使不做任何检验和测试也能直接投入生产。 供方应承担的责任: 供方应对自己原材料进行严格的进货检验,建立和保存进货检验的原始记录,对供应商的材料质量进行跟踪考核,建立质量档案。 供方应健全完善生产过程的控制管理,必须制定生产过程控制文件和作业指导书等,在对最终产品质量有影响的关键生产工序上建立必要的质控点,所有质控点供方应设专人负责,严格做好原始记录和数据统计,监控工序质量和产品质量,及时发现和纠正生产过程的异常状况,确保产品质量的一致性,稳定性。 供方应使生产完全受控,如有失控,应及时查明原因采取纠正措施,并通知需方采取相应的措施,否则一切后果由供方承担。对以上,需方有权对供方进行不定期的监督考察,并进行符合性考核,对供方执行有效性不符合者,需方指出后,供方须及时进行有效整改,对未整改或整改情况不符合需方要求的,需方有权终止供货关系,视为供方违约。 供方提供的原材料应完全符合需方采购订单中明确规定的质量要求,及相应的国际、国家、部委颁发的有关质量标准(包括隐含的质量需要),超出国际、国家质量要求标准的,以需方要求为准。 供方提供的环保材料应完全不含有对地球环境和人体存在显著影响的物质,并符合相关的法律法规,包括rohs指令(2002/95/eec)、欧盟镉指令(91/338/eec)、包装材指令(94/62/ec)、elv废弃汽车指令、废弃电子电器产品指令(weee,2002/96/ec)、pvc禁用指令等。针对每种材料签订环保质量保证书,并每年提供一次有效期不超过一年的有害物质检测报告(如sgs). 供方交货时间超出订单合约交期(交期延误)造成需方生产线停线。 供方需保障原材料从出厂至需方收料之前的包装、运输品质。 供方原材料在需方入厂检验时因品质问题供方不能及时处理而造成需方停线。 供方原材料在需方生产过程中发生品质异常造成需方生产线停线或已生产的产品返工、返修。
供应商质量能力评定准则
VOLKSWAGEN AG 德国××汽车集团 供应商质量能力评定准则 质量管理体系-要求 潜在供应商评价 过程审核,产品审核验证(D/TLD-零件)
经全面修订的第四版德国××汽车集团 2000年4月 4.vollstaendig ueberarbeitete Auflage Volkswagen AG, April 2000
第一版-1991年 第二版-1994年 1月 经全面修订的第三版-1997年 1月 经全面修订的第四版-2000年 4月 本中文版源自德文版的翻译。如有疑义,以德文版为准。 同时提供英文译本、西班牙文译本、葡萄牙文译本,捷克文译本。我们将保留所有的权利,尤其是复制、传播以及翻译的权利。 出版者:德国××汽车集团 集团供应商质量审核部 信箱:1467/0 D-38436 狼堡(Wolfsburg) 电话: (0049) 5361-973185 传真: (0049) 5361-972237
前言 此第四次全面修订版重视了德国汽车工业联合会(VDA)范围内的整车厂和供应商之间达成的新的质量战略,就是说,汽车工业的供应商必须证实其质量管理体系符合VDA 6.1或ISO/TS 16949的要求。 对于质量管理体系的具体要求,在VDA 6.1以及ISO/TS 16949中有详尽 的描述,本手册将不再把质量管理体系作为内容的组成部分。 针对新的质量战略,过程审核和产品审核是汽车制造厂和供应商们的重点,因此也就是本手册重点。对这两种审核的各种要求在实践经验的基础上进行了更准确的描述并部分地进行了补充。潜在供应商评价,作为对不了解的供应商在建立供货关系之前进行的先期检查,新被收录在本手册中。 “Formel Q-质量能力”手册是对“Formel Q-Konkret” 一书的补充,描述和介绍了有关评价大众集团供货厂质量能力的程序。它对大众集团的所有品牌的生产资料供应商以及大众集团全球范围的合资公司具有约束力。 本手册的内容依然与适用的VDA准则和VDA丛书相关。当然,它也描述了大众集团针对过程,产品,持续改进(KVP)以及为开展新项目与供货商进行合作提出的特殊要求。 本手册的目的是,向供货商阐明质量能力要求,并能使供货商通过自审使质量管理体系、过程和产品不失时宜地向国际上通常的要求和大众汽车集团的特殊要求靠拢并能有效地保持。 本手册是准则框架,是大众汽车集团对供货商提出的具有约束性的要求,本手册是对供货商的生产场所进行审核的依据。 F.J.Garcia Sanz H.Kreiner 大众品牌采购部董事大众集团质保部经理 狼堡(Wolfsburg) 2000年4月
供方质量保证能力评价要点(范本)
供方质量保证能力及产品实物质量检查办法 一、技术文件管理 企业应建立完善的技术文件管理制度,确保文件的有效性。 1、企业应建立技术文件的管理制度,技术文件的管理符合管理制度的要求。 2、图纸管理 ①、图纸的来源是否符合规定要求。 ②、图纸的转换、更改、批准是否符合要求。 ③、图纸的更改依据是否充分。 ④、现场使用的图纸是否为有效版本。 ⑤、文件资料是否完整、齐全(包括设计文件的图样目录、零部件明细表、总装图、部件图、零件图、标准、技术要求等和工艺文件的工艺过程卡、工序卡、作业指导书、检验规程等)。 ⑥、设计变更、材料代用是否符合相关规定,是否覆盖了产品生产全过程。 3、工艺文件 ①、工艺规程、操作规程、试验规程、试验标准、检验标准等工艺文件是否齐全,产品要求是否得到全部覆盖,是否可以指导生产。 ②、文件的转换、更改、批准是否符合要求。 ③、引用文件、标准是否齐全、有效。 ④、现场使用文件是否为有效版本。 二、生产设备管理 企业必须建立工装设备管理制度,对所验产品的生产工装设备建立定期维护、验证制度,并按要求定期进行维护和验证。 1、企业必须建立工装设备管理制度。 2、对所验产品的生产设备、工装(包括模具)必须规定定期(量)维护和验证的要求。 3、设备、工装的性能、精度是否满足产品生产及质量的要求。
4、按产品形成工艺流程,对场地和工装、设备进行核对并记录,确认设备状态符合标识要求。 三、检测试验设备 企业必须建立检测试验设备和检测量具及样板的管理规范,强化对监视测量设备的有效性管理。 1、企业必须建立检测试验设备和检测量具管理制度。 2、对检测试验设备和检测量具,必须制定定期检定制度,并须符合有关标准的规定。 3、必须具有满足对产品质量特性进行监视测量的检测量具和试验设备。 4、检测试验设备核检测量具须经国家认可的计量单位检定合格后,方可使用。 5、对允许委外检测和试验的项目,应对受委托方按有关要求进行能力和资质的确认。 6、建立完善的测量设备管理、维护保养制度及台帐、技术资料等,制定设备操作规程,并在检定或校准有效期内使用。 7、对用于出厂检验的设备除应进行日常操作检查外,还应进行运行检查。当发现运行检查结果不能满足规定要求时,应能追溯至已检测过的产品。必要时,对产品重新进行检测。应规定操作人员在发现设备功能失效时需采取的措施。 8、发现检验、测量或试验设备偏离校准状态时,应评定已检验和试验结果的有效性,并形成文件。 9、用计算机软件进行监视和测量时,是否在初次使用前进行了确认并在必要时再确认。 四、采购控制 1、是否有分供方的评定和控制程序。 2、企业对供方的评价是否充分,是否符合文件规定的要求。 3、对关键供方是否进行现场审核,对供方质量保证能力的评价是否有效。 4、企业是否建立对采购产品进行验证的程序。 5、企业是否编制产品接收准则,明确不合格原材料的处理。
供应商二方审核检查表
二方审核检查表(1.0版) 项目过程要求记录得分1 原材料/供方 1.1 是否由已认可的且有质量能力的分供方供货? 确定供方之前,应已具有质量管理体系的评价结果(认证/ 审核)。投入批量生产前,应确保仅从适宜的供方处采购。应考 虑其以往的质量绩效的评估情况。 需考虑的要点,例如: - 供方的基本情况、资质调查 - 质量能力评价,例如:审核结果 过程审核/ 产品审核、质量管理体系认证 - 根据质量绩效(质量 / 成本 / 服务)的高低级别进行选择 - 合格供方目录的建立并使用 - 供方清单获得顾客的批准/变更的再批准 1.2 是否可以保证采购件符合约定的质量要求? 应能在组织内(自身核心技术、出现问题时快速反应)进行 基本、必要的检验(实验室和测量设备)。组织自己的实验室应 进行系统管理。委外实验室符合ISO / IEC 17025 (或具有可比 性的国家标准)。 需考虑的要点,例如: - 足够的检验可能性(实验室和测量设备) - 图纸/ 订货要求/ 规格的充分和明确 - 质量保证协议的签订 - 基于主要缺陷的分析及特性重要程度,制订进货产品控制计划 并执行/或委托外部检验 - 与供方对检验方法、检验流程、检验频次的约定并执行 - 测量能力证明(MSA,尤其针对产品和过程的关键特性)
项目过程要求记录得分1.3 已批量供货的产品是否已获得所要求的认可?要求的改进措 施是否已落实? 要求/ 说明 在新的/ 更改的产品/ 过程批量投产前,必须对供方的所 有产品进行认可。若采用模块供货,组织对所有的单个部件负有 质量监督的完全责任。 需考虑的要点,例如: - 顾客信息(其中包括技术规范/ 标准/ 检验规定) - 工程样件的认可、试制样件的认可 - 首批样品检验报告及生产件批准(PPAP) - 重要特性的能力证明(CPK,PPK) - 可靠性分析评估 - 定期的对产品全部特性的检验报告(年度全尺寸检验和型式试 验) 1.4 是否对供方的质量绩效进行了评价?当出现偏差时是否采取 了措施? 要求/ 说明 应定期检查供方的能力和绩效,按零件分类记录在一个表(供 应商清单)中并作评价。若评定的结果不佳则要制订质量能力提 高计划,并对实施情况进行验证。若采用模块供货,供应商对所 有的单个部件的质量监控负有全部的责任。 需考虑的要点,例如: - 对质量绩效进行连续监控和评价(质量/ 成本/交付/ 服务等) - 整改计划的商定与跟踪 - 改进后零部件的检验记录和测量记录 - 对主要缺陷/ 有问题的供方进行分析
供应商审核检查表.pdf
供应商审核检查表供应商名称审核日期公司地址报告编号审核员供应商代表不符合项的回复日期 评审项目项目总分供应商自我评 实际得分百分制得分估分数 1. 质量体系10 2. 文件、记录控制10 3.合同评审8 4. 采购和进料检验控制9 5.仓库、标识和可追溯性 6 6. 检查测量和测试设备 6 7. 设备保养 4 8.制程控制、加工能力25 9. 最终成品检验控制7 10.内部审核 4 11. 培训、环境与安全11 总分数100 判断标准百分制总得分% 分数判断 ≧ 75.0% 合格 75.0% - 60.0% 有条件合格等级 最终判定结果< 60.0% 不合格 ┈┈┈┈┈┈┈┈┈┈┈┈┈┈┈┈┈┈┈┈┈┈┈┈┈┈┈┈┈┈┈┈┈┈┈┈┈┈┈┈┈┈┈┈ 编制:审核:核准:
NO 检查项目分数得分备注1 质量体系 1.1 有文件化的质量方针吗?手册中有无描述HSF过程控制计 2 划、目标和HSF程序文件的指引? 1.2 是否对公司ROHS活动进行了管理?如何证明? 2 1.3 品管人员在组织图中有无指明的权责和责任范围? 1 1.4 品管是否是一个独立的职能部门?品质部经理是否受最高 1 管理层直接领导? 1.5 管理层定期评审质量目标的实施状态和充分性吗? 1 1.6 为建立品质管理目标,是否使用柏拉图分析内部或外部的 2 品质问题? 1.7 相对于客户期望和目标,供应商的品质是否有持续改善? 1 2 文件,记录控制 2.1 系统文件的发放和更改的控制,是否有文件化程序? 1 2.1 现行文件/规范是否易于取得且存放在受控文件夹中? 1 2.3 是否有程序保证所用的都是最新版本的规范? 1 2.4 是否有程序规范作废文件的处理? 1 2.5 文件变更及其特征有否标识? 1 2.6 是否定义有外来文件的鉴定和控制程序? 1 2.7 是否有一个记录管理一览表? 1 2.8 表单的发行有无经过批准? 2 2.9 工程文件控制方面是否使用计算机辅助设计系统? 1 3 合同评审 3.1 是否满足了客户HSF的要求?抽查三份. 2 3.2 是否有正式的合同评审管理程序?相关记录保存完整? 1 3.3 供应商是否确认:当产品要求被改变,组织应确保相关文 1 件已经被修订,且将变更的要求知会相关人员? 3.4 对客户提供的图纸有无经评审并转为自己的图纸? 1 3.5 客户的资料和新项目的资料是否保存在安全的地点? 1
上海通用供应商审核检查表 中文版
供应商名字: 邓白氏码:供应商所在地:全球采购/供应商品质潜在供应商评估检查 审查人名字: 审查主管的电话和邮箱: 审查日期: Page 1 of 23
审查主管的电话和邮箱: 电话号码 工作时间 供应商全称:=Title!$F$3邓白氏码:=Title!F4审查人名字: =Title!F7=Title!F8 人员 供应商所在地:=Title!F5审查日期:=Title!F6名字 在职时间 邮箱地址 潜在供应商评估检查 1负责设备质量的工程师总数?2负责设备生产的工程师总数?3 负责设备研究与发展的工程师总数? 总数 管理人员 生产部经理产品控制总裁质量部经理其他计时薪员工 生产线人员 工艺部经理产品工程部经理销售4 设备员工总数?
8车间工作正常有多少次轮班? 8a 车间正常工作多少天? 11目前车间利用的百分比? % 6 员工工作完成量的百分比轮班天 5 每年平均有多少资深员工 12 只增加劳动力能扩大百分之多少的利用点?% 13难处理的业务占工厂效用的百分比? % 14对于增加的生产量有补充计划吗? 如果有,解释: 15未来5 年的利用能力: 第一年第二年 第三年第四年 第五年 16产品的标准领先时期t: PPAP 的领先时期产品配送的领先时期 17供应商/设备当前的百万分率是多少(每一百万所占比例)? 百万分率 注: 百万分率 = [(盈利+剩余+种类+再造)*1000,000]/总量18仓库的防火安全符合通用的标准吗?19供应商/设备建造他们自己的工具吗?如果是,百分比是:% 20供应商/设备回收仓库里的工具吗?21 供应商/设备有能力制造吗? Yes Yes Yes
外协供应商质量保证能力基本要求
外协供应商质量保证能力基本要求 1目的和范围为保证我公司主机产品的符合性质量,有序的生产出可靠的我设备,不断提升我品牌形象,提高用户满意度,外协供应商的质量保证能力应满足本基本要求。适用于本公司对外协供应商的质量管理。 2职责和资源 2.1职责 2.1.1外协供应商应规定与质量活动有关的各类人员职责及相互关系。 2.1.2外协供应商的最高管理者应指定一名质量负责人,就质量事宜直接与我公司联络。质量负责人应具有能力履行以下职责和权限: a)负责建立满足本文件要求的质量管理体系,并确保其实施和保持。 b)确保协作产品或项目符合我公司要求,当不能保证满足要求时,有权停止生产。 c)建立文件化的程序,确保产品或协作项目的实施过程得到有效控制。 d)建立文件化的程序,确保产品不合格或变更后未经我公司认可,不得放行和交付。 2.2资源 2.2.1人力资源应确保具备满足要求的能力,建立协作产品/项目有关过程人员的培训和能力评价的记录。 2.2.2基础设施应满足实现产品符合性的要求,建立协作产品/项目有关过程的设施设备明细(包括:生产设备、工艺装备、工作场所、建筑物等),并进行有效管理。 2.2.3工作环境条件适宜产品生产、检验、储存要求。 3文件和记录 3.1应建立并保持协作产品或协作项目质量管理所需要的文件。这些文件包括: a)质量保证手册(供应商质量管理体系的描述); b)质量管理文件汇编(职责、程序、制度、规定、办法等); c)产品过程作业文件(工艺流程、加工工艺、指导书、图纸、计划等); d 检验文件(进货/ 过程/ 成品检验规范、相关标准等); e)其它(技术协议、质量/服务保证书等)。 3.2应建立并保持文件化的程序,对文件和资料进行有效控制,确保: a)文件发布和更改应由授权人批准,以确保其适宜性; b)文件的更改和修订状态得到识别,防止作废文件的非预期使用; c)在使用处可获得相应文件的有效版本。 3.3应建立并保持协作产品或协作项目所需要的记录。这些记录包括: a)文件批准、接收、发放、更改有关的记录; b)产品出厂检验、过程检验、进货检验、不合格品处置有关的记录; c)质量管理、人员管理、设备管理、量具管理有关的记录; b)产品交付、计划、订单、合同有关的记录; e)其它有关协作产品或协作项目的质量活动的记录。 应建立并保持质量记录的文件化程序,对记录的标识、保管和处理、保存期限作出规
供应商质量评估调查作业办法
供应商质量评估调查作业办法 一.目的 规范供应商质量评估调查的作业流程,确保评估作业得到有效、顺利开展。 二.适用范围 适用於本公司对供应商质量评估调查作业。 三.工作职权 1.采购单位 1.1负责制定《年度供应商现场评估计划》﹔ 1.2提出临时评估调查申请﹔ 1.3不符合的追踪确认﹔ 2.品保单位 2.1按要求准备评估资料,并主导完成供应商调查评估﹔ 2.2调查评估完成后出具《质量评估调查报告》﹔ 2.3提出临时评估调查申请﹔ 2.4不符合的追踪确认﹔ 四. 作业内容 1. 采购每年12月份针对年度对供应商的采购及供应商质量状况,制定《年度供应商 现场评估计划》﹔ 2.供应商调查评估时机:
2.1依《年度供应商现场评估计划》要求,需执行时﹔ 2.2供应商产品质量出现重大品质异常,且经主管批准时﹔ 2.3新增或更换供应商时﹔ 3.调查评估的通知: 3.1采购依以上时机的要求提前3个工作日,开立《供应商评估调查通知单》并附 上《供应商基本资料表》知会品保单位。 3.2品保於接到通知的1个小时内,依通知及《供应商基本资料表》内容确定调查 评估的内容,并提供《供应商质量评估调查表》内容於采购﹔ 3.3采购接到品保提供的资料后,可视情况将《供应商质量评估调查表》传供应商, 要求供应商先进行自评,并签回至我司品保。供应商依要求进行针对性改善﹔ 3.4采购至少应提前2个工作日前以联络单的形式知会供应商,内容包括:随行人 员,到达时间,评估依据,评估重点,各稽查人员安排及供应商需配合事项等。 3.5以上内容实施应得到供应商的确认。 4.厂内准备: 4.1品保依确定的调查评估内容准备相关评估资料或工具。 4.2品保应根据供应商提供产品的信息收集产品质量记录,以备待查。 4.3必要时,采购与品保进行评估前会议,会议内容:评估目的,评估重点,人员 安排及评估的相关注意事项说明等。 4.4外出时,应对携带物品进行确认,确认依《外出点检验记录表》进行,以防产 生遗漏。 5.调查评估:
质量内部审核检查表
内部审核检查表 审核部门: 1.请管理者代表介绍本组织 的业务情况,主要产品或服 务,面对的客户群体和组织 的发展方向等。 2.请管理者代表介绍公司的 体系建立依据的标准形成了 哪些文件?评价体系文件实 施的的效果? 3. 请最高管理介绍体系建立 的时间是什么时候?什么时 候开始试运行?任命的管理 者代表是谁?有无任命证据 和分配其职责? 4. 请管理者代表说说建立时 识别了哪些过程?如何进行 控制? 5. 请总经理谈谈公司是否存 在外包的过程?有,如何进 行控制? 标准条款 审核(调查)内容 审核(调查)记录 评价 4.1总要求
审核部门: 标准条款审核(调查)内容审核(调查)记录评价 421总则1是否建立质量方针、质量 目标并形成文件? 2是否编制质量手册? 3标准要求的六个必须的程序 文件是否形成?(六个必须 的是文件、记录、内审、不 合格、纠正措施、预防措施 控制程序)。 4除形成上述文件外,在体系 中还建立了哪些文件? 5形成的记录有哪些?是否达 到标准的要求? 6文件保存的方式有哪些? 是用纸张还是电子?是如何 管理的?
审核部门: 标准条款 审核(调查)内容 审核(调查)记录 评价 4.2.2 质量手册 2请管理者代表说说手册内 容是否对各部门和过程进行 描述?是否包涵或引用程序 文件?(验证质量手册内容) 3检查质量手册是否进行受 控管理? 1请管理者代表说说手册内 容是否覆盖了标准所有要 求?若有删减,请说明理 由?
审核部门: 标准条款 审核(调查)内容 审核(调查)记录 评价 4.2.3 文件控制 2文件发布前是否得到相关 人员的批准(抽查质量手册/ 程序文件/作业文件等)? 6文件是否定期进行整理和 处理作废文件? 3文件是否有修改?文件的 修改如何进行? 5公司有哪些外来文件(法 律法规及标准)?如何进行 保管? 1形成的文件有哪些(请提 供文件总目录)? 4文件的标识(编码)是如 何规定的(如质量手册、程 序文件等)?
电梯内部质量审核检查表
XXXXXXX电梯工程有限公司修订号O/A 批准日 期 2011年9月7日 编号QP-26标题内部质量审核检查表 内审(质量)检查表 第1页共2页编号:审核组长审核员受审部门审核类型受审部门确认审核日期 质量管理部 序号审核内容依据条款验证方法、验证记录审核结果 1 抽查质量方针内容及含义? 5.3 2 部门的质量目标是否量化?是否适合并可实现? 5.4.1 3 抽查是否明确质检员职责? 5.5.1 4 对外来标准、文件是否按要求进行控制? 4.2.3 5 是否明确测量和试验装置要求?有无清单?7.6 6 测量和试验装置是否进行周期校验?有无校验记录?7.6
7 抽查测量和试验装置有无标识?使用或维护是否恰当?7.6 8 有无明确原材料检验标准?标准是否可行并充分?8.2.4 9 是否按规定对原材料检验?有无记录?8.2.4 10 有无明确过程工序检验和监视要求?检验方法和标准是否 明确? 8.2.4 11 是否对成品检验并标识状态?有无记录报告?8.2.4 12 抽查8份相关的检验记录,是否符合检验文件或标准要求?8.2.4 13 现场抽查1名检验人员,对照检验文件考核检验方法和记 录? 8.2.4
内审(质量)检查表 第2页共2页编号:审核组长审核员受审部门审核类型受审部门确认审核日期 质量管理部 序号审核内容依据条款验证方法、验证记录审核结果 14 是否有文件化的不合格品处理程序?8.3 15 是否对不合格品进行类别处理?有无不合格处理记录?8.3 16 是否进行数据分析?8.4 17 数据分析是否可提供顾客满意/产品符合性/过程和产品特 性/供方等信息? 8.4 18 是否有文件化纠正和预防措施控制?8.5 19 是否对严重不合格或退货做分析处理?是否发出纠正预防 措施报告? 8.5 20 抽查1份纠正措施记录,是否确定原因并有效纠正和预防?8.5.2 21 检查产品的标识记录是否可实现追溯?7.5.3 22 说明:审核结果:合格打“√”;严重不合格打“╳”;一般不合格打“○”
供应商能力评定办法.doc
供应商能力评定办法1 供应商评审及分级办法 1 目的 为了提高产品质量,稳定供应商队伍,建立长期互惠供求关系,特制定本办法。 2 范围 本办法适用于向公司供应原辅材料,零部件及提供配套服务的厂商和供应商。 3 定义 供应商评审:对供应商的生产能力,检测能力,服务能力等进行的考评,以判断其是否满足公司的要求。 分级制度:技术质量部结合供应商实力和供货情况对供应商进行的等级划分。 追溯索赔:因供应商原因用户要求本公司赔偿的,本公司有权通过制造部采购室向供应商追溯责任及相关赔付。 4 职责 采购室负责收集供应商资料,同供应商签署协议。 技术质量部负责组织相关部门对供应商进行资质调查和评审。
总经理负责合格供应商的审批。 5 程序 5.1 采购物资的分类 一类物资为对产品质量、性能有直接重大影响的主要材料和重要的外购件。如:(视各公司情况而定) 二类物资为对产品质量、性能有较大影响的主要材料和重要的外购件。如:(视各公司情况而定) 三类物资为除一、二类物资以外的用于产品生产的辅助用料、一般外购件和生产维修用料等其他物资。如:(视各公司情况而定) 单笔采购金额在5000(含)元人民币以上的为A类物资;单笔采购金额在1000(含)~4999元人民币的为B类物资;单笔采购金额在999元人民币以下的为C类物资。 5.1.3 原则上,A、B、C类的管理控制方法对应等同于一、二、三类物资。以下如遇物资类别,一、二、三类均对应包含A、B、C类。 5.2 供应商评审流程 5.2.1 采购室根据生产需要选择合适的供应商作为候选,并要求其填写《供应商调查表》。,由技术质量部对供应商的情况进行核实并判断是否需对其进一步的评审,评审结果通知采购室。 5.2.3 一、二类物资供应商在获得技术质量部的批准后由采购室通知其送样或小批量试用。
ISO9001内部质量审核检查表范例完整版
好好学习社区 ISO9001:2015内部质量审核检查表 受审核部门审核日期审核员 审核准则ISO9001、体系文件、适用法律法规 符合说明○”符合;“?”观察项;“△”一般不符合;“×”重大不符合※不符时记入证据、事实。 涉及条款审核内容、证据及方法审核记录审核发现范围 1.组织QMS覆盖范围和过程是否有缺失?无缺失、覆盖全面√ 2.组织QMS对标准条款是否删减?如有,所删减条款中过程确 凿没有? 无删减√ 4.1 理解组织及其环1.组织是否确定与其目标和战略方向相关并影响其实现质量管 理体系预期结果的各种外部和内部因素?是否对这些相关信息 进行监视和评审? 最高管理者应确定与本公司质量目标和战略方向相关并影响实现质量管理体系预期结果 的各种内部因素(公司的价值观、文化、知识、绩效等相关因素)和外部因素(国际、 国家、地区和当地的各种法律法规、技术、竞争、文化和社会因素等)。这些因素可以包 括需要考虑的正面和负面因素或条件。 本公司定期对这些内部和外部因素的相关信息进行监视和评审,以确保其充分和适宜。 √ 4.2 理解相关方的需求和期望1.组织是否确定了与质量管理体系有关的所有相关方?是否对 这些相关方制定相关要求并进行了监视和评审? 公司应确定: a)与质量管理体系有关的相关方; b)这些相关方的要求; 公司应对这些相关方及其要求的相关信息进行监视和评审,以便于理解和持续满足相关 方的需求和期望。 组织应考虑以下相关方: --顾客; --最终用户或受益人; --法人,股东; --银行; --外部供应商; --雇员及其他为组织工作者; √
--法律法规及监管机关; --地方社区团体; --非政府组织;。 理解相关方的需求和期望可以帮助本公司更好的建立清晰的方针和目标,做到目的明确。满足相关方的要求并争取做到更高的期望值。 表1 外部相关方及要求与期望 相关方要求与期望 法律法规及监管机关符合法律法规要求 顾客、最终用户或受益人提供的技术方案或研发的产品符合最初提出的要求 银行有能力支付银行的款项 外部供应商价格合理,结算及时,有规范的流程或手续 第三方认证服务机构满足ISO9001体系要求,持续改进质量管理体系 第三方监测机构配合监测 表2 内部相关方及要求与期望 相关方要求与期望 法人,股东合法,客户满意,成本低 雇员及其他为组织工作者清洁卫生,工作时间合理,工作强度不大、薪酬合理 4.3 确定质量管理体系的范围1.组织是否确定了质量管理体系的范围?是否对这些信息形成 了相关文件? 组织应明确质量管理体系的边界和适用性,以确定其范围。 在确定质量管理体系范围时,组织应考虑: a)各种内部和外部因素,见4.1; b)相关方的要求,见4.2; c) 组织的产品和服务。 根据本组织产品和服务特点,标准的所有条款均适用于本组织并决定全部予以实施。 本公司质量管理体系的范围为:杭州市滨江区滨康路568号物理边界区域范围内的医药 健康产品的技术开发。 √
供应商质量管理SQE职责
供应商质量管理 SQE“Supplier Quality Engineer” 一、供应商质量管理业务流程 1.1、衡量供应商的质量 品质结果的衡量--产品质量的测定 品质过程能力指数Ca、Cp、Cpk、Ppk、Cmk及其应用 品质测量的方法和程序 抽样计划 测量系统分析(MSA)介绍 品质过程的衡量--质量保证体系的评审 基于流程的ISO9000、ISO/TS16949质量体系 产品质量先期策划APQP的概念及方法 评审的流程 1.2、分析供应商的质量 过程能力指数分析 基于供应链的流程分析
运用SPC识别质量变异 运用FMEA识别质量变异 1.3、提升供应商的质量 解决质量问题 建立组织架构和机制 质量问题改进小组—团队、任务、计划和授权因果关系图 差错防止 实验设计法DOE 预防质量问题 从营运体系的角度帮助供应商建立: ¨供应链上下游的技术和标准的一体化 ¨共享的信息通道和作业流程 ¨基于标准化的流程管理 从产品和工艺的角度帮助供应商建立: ¨产品的鲁棒设计 ¨工艺的鲁棒设计 从组织和团队的角度帮助供应商建立: ¨以品质为核心的企业文化和激励制度 ¨完善的绩效管理 ¨有效的培训和员工发展 1.4 先期产品质量策划(APQP)
1.5 批量生产控制 二、SQE供应商质量管理工程师 新的环境下供应商管理角色越来越多地由专门化的职能人员来承担,一个标志性的职能就是供应商质量管理工程师-SQE。SQE的应运而生已经有数年了,目前企业对这一职位的需求在不断增加。但是对于这一个职位,往往是只有要求,没有规范,靠SQE 的自主经验以及和采购人员、产品品质人员的共同协调,很多SQE的上岗是由以往的工作转行,没有接受过系统培训。SQE管理需要有很强的专业知识和管理工具基础,学习
内部质量审核检查表(已填).doc
审核主题 标准要求4.1 总要求 4.2.1 总则总要求总则管理承诺以顾客为中心 审核要点 ☆本厂建立质量体系识别了哪些过 程?是否在本厂中得到应用?☆识 别出的过程之间的顺序和相互作 用如何? ☆是否对识别出的过程制定了运行和 控制的准则? ☆是否获得了必要的资源和信息? ☆是否对过程实施了监视、测量和分 析? ☆是否实施了必要的措施,以实现对这 些过程的策划结果和对这些过程的持续 改进? ☆是否识别了本厂的外包过程?是否 对外包过程进行了控制?☆本厂 建立的质量管理体系文件包括 哪些 ? 标准要求的文件是否都得到 了满足 ? 质量方针审核部门 /人员 审核结果 审核方法 无此项不符合符合 ☆通过与最高管理者座谈,了解最高√管理者是否知道建立质量 管理体系的 总要求,做了哪些工作? ☆查核文件清单及要求出示具体的文√ 件,以了解本厂已制定了哪些文件。 最高管理者 /叶奇 审核记录 建立质量体系初期识别本公 司的所有过程:主要是管理智 能、资源、产品实现、监视和 测量四大过程 对识别出来的过程进行了策 划,策划结果形成了文件 质量管理体系文件有:质量方 针、目标、程序文件、作业指 导书、记录 5.1 管理承诺☆最高管理者对其建立和改进质量管 理体系的承诺和改进质量管理体系 的承诺能够提供那些证据? ☆最高管理者如何认识满足顾客的要 求和法律、法规要求的重要性?☆最 高管理者采取了那些相应措施将满足 顾客要求和法律要求的重要性 传达给组织的成员? ☆组织的成员如何认识这种重要性?☆通过与最高管理者座谈,了解最高√ 管理者是否知道满足顾客要求和法 律、法规要求的重要性。在质量管 理体系中是如何体现的?如对顾客 要求的识别、产品要求的评审、顾 客满意的监视和测量、数据分析以 及持续改进等方面的要求。 总经理提供以下承诺:传达满 足顾客和法律法规要求重要 性,制定方针、目标、进行挂 历评审、确保资源获得
供应商现场评审检查表
供应商现场评审检查表 客户满意 1、是否有文件化过程来测定客户满意度,包括:测定频率、交付产品的质量、客户中断应 急管理、现场退货,交付业绩以及通知客户吗? 2、量化监控于供应商制造的客户满意度,并被理解和跟踪。 3、有适当的计划和程序去提高客户满意,基于纠正措施处理,以及闭环评审制度的实施。 4、为大客户设立了多功能服务团队 质量体系 1、你们有质量体系标准认证,如IS09000 / TS16949吗? 2、有季度管理评审来验证质量体系运行的有效性吗? 3、每个部门都有明确定义和可测量的目标,着重关注质量方针,目标、审核结果、数据分析、 纠正措施和预防措施。 4、管理人员定期按计划评审项目管理的完成情况。管理人员应评审纠正措施计划以确保任 何过期项目制定计划,并形成在目前的项目管理计划中。 5、内部审核频率应该基于不合格的趋势进行修正。 6、内部审核可以用来验证质量体系被跟踪。 7、正式的商务/业务/制造系统在应用(如:产能计划,工作场所控制,ERP,等等). 8、主动告知可能影响交货或质量问题,记录在案,并执行。 9、供应商是否有一个最终产品的标识流程,包括条形码识别(如果需要)。 10、当产品/过程不同于已批准的加工工艺或工艺过程时,在进一步加工处理之前,供应 商是否获得客户批准或让步接收?当这种情况发生的时候,是否在包装上适当地进行标识? 商务系统 1、是否有开发和开展以客户为中心(以顾客为关注焦点、顾客导向)的战略,以确保业务组 合的多样性? 2、是否有证据和使用工具,如电子数据接口(EDI),RFQ(询价单),先期策划与调度按排(APS)? 3、是否为一旦发生紧急情况的时候准备了充分的应急反应计划以满足顾客的需求,如:公用 事业设施中断,劳动力短缺的危机、关键设备的故障,以及现场退货? 4、是否有制定明确的产品责任/召回问题处理程序流程? 5、供应商是否有一个长期的持续改进计划,包括系统可持续发展地方识别关键的商业运作 和产品的风险与机会吗? 6、是否对采购订单进行评审,包括:对数量,价格,交货日期,交货方式,任何额外的特别的要 求或指示的承诺?如果出现任何差异,在接受签署订单之前这些差异是否得到解决? 7、执行特定任务或作业的人员应具备资格认定,是基于实适当的教育、培训、和/或经验。环境、健康和安全及风险管理 1、有效的EHS流程被正式定义,文件化,并了解对所有EHS的缺陷进行系统化的根本原 因调查及追踪纠正措施。 2、在现场有一套明文规定且被理解的有效的风险评估流程方法,要求正式的风险评估是基 于变化或初期的设备设置。 3、认识到每一滴废水,最终定位,废物处理场所的监督管理许可证,数量有关的。 4、公司是否符合职业安全与卫生管理局或其他有关安全卫生规程,特别是在使用个人防护 设备吗? 5、有适当的程序以保证有害物质控制