电阻加热炉度控制
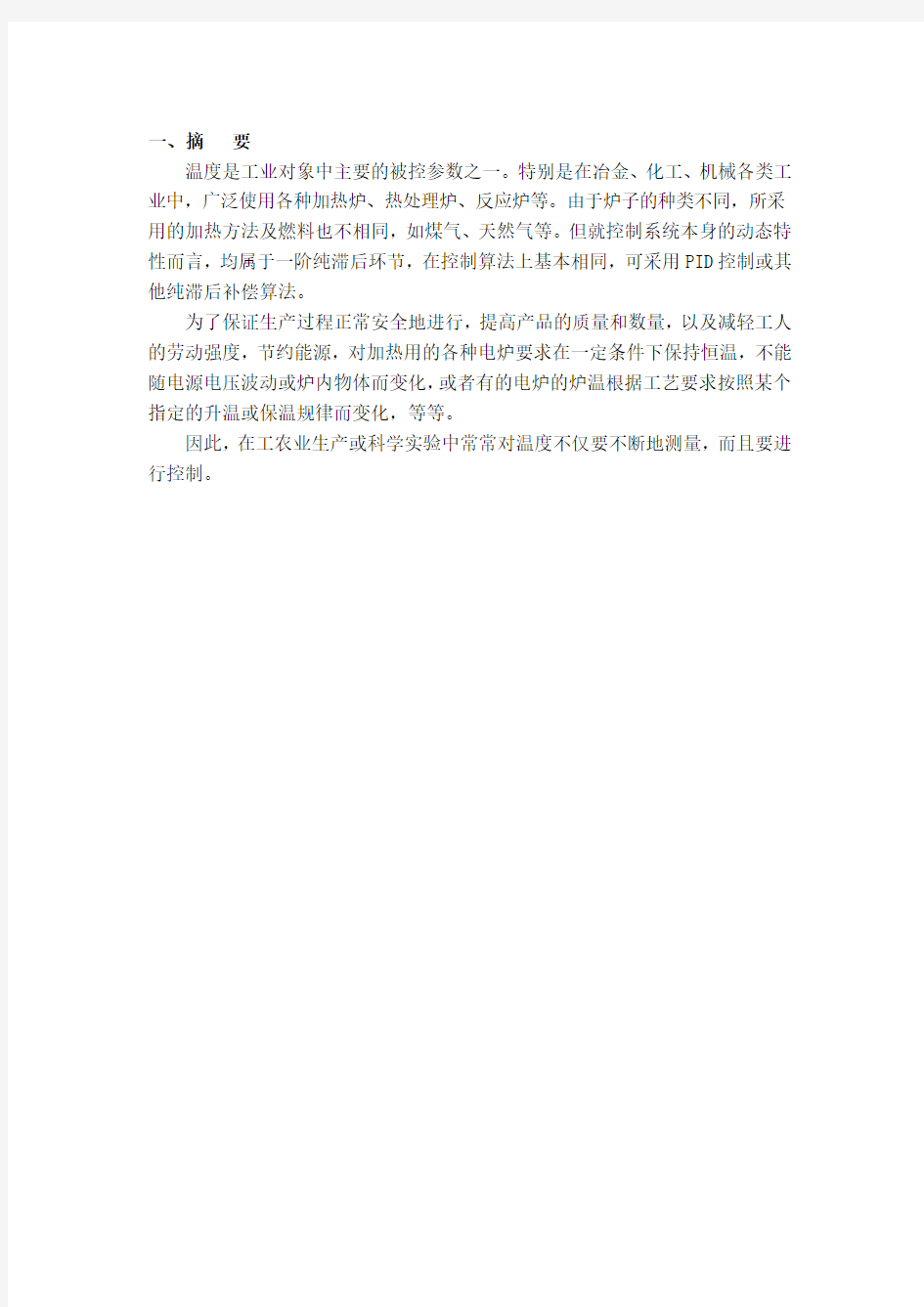
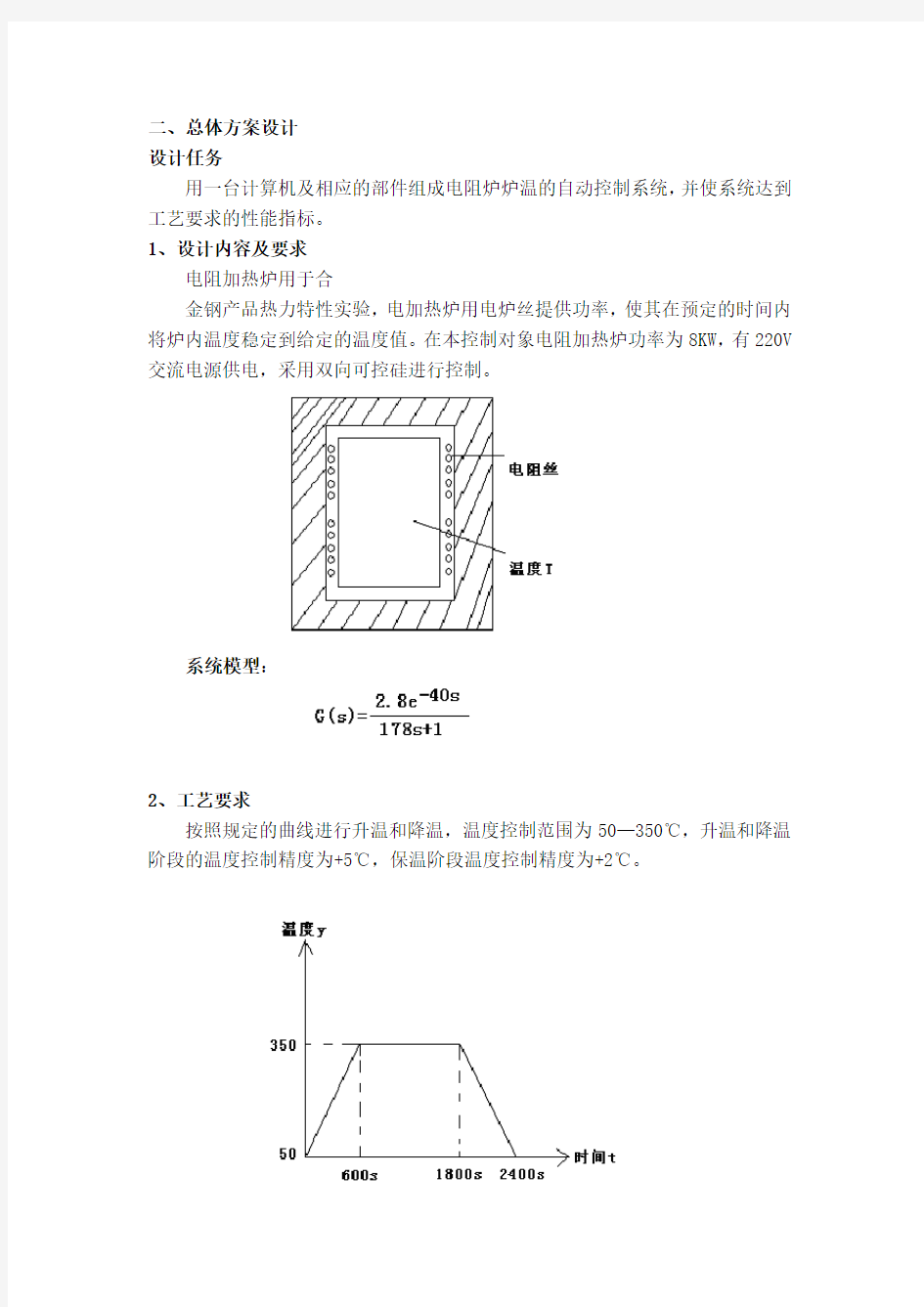
一、摘要
温度是工业对象中主要的被控参数之一。特别是在冶金、化工、机械各类工业中,广泛使用各种加热炉、热处理炉、反应炉等。由于炉子的种类不同,所采用的加热方法及燃料也不相同,如煤气、天然气等。但就控制系统本身的动态特性而言,均属于一阶纯滞后环节,在控制算法上基本相同,可采用PID控制或其他纯滞后补偿算法。
为了保证生产过程正常安全地进行,提高产品的质量和数量,以及减轻工人的劳动强度,节约能源,对加热用的各种电炉要求在一定条件下保持恒温,不能随电源电压波动或炉内物体而变化,或者有的电炉的炉温根据工艺要求按照某个指定的升温或保温规律而变化,等等。
因此,在工农业生产或科学实验中常常对温度不仅要不断地测量,而且要进行控制。
二、总体方案设计
设计任务
用一台计算机及相应的部件组成电阻炉炉温的自动控制系统,并使系统达到工艺要求的性能指标。
1、设计内容及要求
电阻加热炉用于合
金钢产品热力特性实验,电加热炉用电炉丝提供功率,使其在预定的时间内将炉内温度稳定到给定的温度值。在本控制对象电阻加热炉功率为8KW,有220V 交流电源供电,采用双向可控硅进行控制。
系统模型:
2、工艺要求
按照规定的曲线进行升温和降温,温度控制范围为50—350℃,升温和降温阶段的温度控制精度为+5℃,保温阶段温度控制精度为+2℃。
3、要求实现的系统基本功能
微机自动调节:正常工况下,系统投入自动。
模拟手动操作:当系统发生异常,投入手动控制。
微机监控功能:显示当前被控量的设定值、实际值,控制量的输出值,参数报警时有灯光报警。
4、对象分析
在本设计中,要求电阻炉炉内的温度,按照上图所示的规律变化,从室温开始到50℃为自由升温阶段,当温度一旦到达50℃,就进入系统调节,当温度到达350℃时进入保温段,要始终在系统控制下,一保证所需的炉内温度的精度。加工结束,要进行降温控制。保温段的时间为600—1800s。过渡过程时间:即从开始控制到进入保温阶段的时间要小于600s。在保温段当温度高于352℃或低于348℃时要报警,在升温和降温阶段也要进行控制,使炉内温度按照曲线的斜率升或降。
采用MCS—51单片机作为控制器,ADC0809模数转换芯片为模拟量输入,DAC0832数模转换芯片为模拟量输出,铂电阻为温度检测元件,运算放大器和可控硅作为功率放大,电阻炉为被控对象,组成电阻炉炉温控制系统,另外,系统还配有数字显示,以便显示和记录生产过程中的温度和输出值。
5、系统功能设计
计算机定时对炉温进行测量和控制一次,炉内温度是由一铂电阻温度计来进行测量,其信号经放大送到模数转换芯片,换算成相应的数字量后,再送入计算机中进行判别和运算,得到应有的电功率数,经过数模转换芯片转换成模拟量信号,供给可控硅功率调节器进行调节,使其达到炉温变化曲线的要求。
三、硬件的设计和实现
1、计算机机型:MCS—51 8031(不包含ROM、EPROM)
系统总线:PC总线
2、设计输入输出通道
输入通道:因为所控的实际温度在50 ~ 350℃左右,即(350-50)=300所以选用8位A/D转换器,其分辨率约为1.5℃/字,再加放大器偏置措施实现。(通过调整放大器的零点来实现偏置)这里采用一般中速芯片ADC0809。ADC0809是带有8位A/D转换器,8路多路开关以及微型计算机兼容的控制逻辑的CMOS 组件,其转换方法为逐次逼近型。8路的模拟开关由地址锁存器和译码器控制,可以在8个通道中任意访问一个通道的模拟信号。
输出通道:据其实际情况,D/A转换器的位数可低于A/D转换器的位数,因为一般控制系统对输出通道分辨率的要求比输入通道的低,所以这里采用常用的DAC0832芯片
DAC0832是8位D/A转换器,与微处理器完全兼容。期间采用先进的CMOS工艺,因此功耗低,输出漏电流误差较小。因DAC0832电流输出型D/A转换芯片,为了取得电压输出,需在电流输出端接运算放大器,Rf为为运算放大器的反馈电阻端。
3、设计支持计算机工作的外围电路
矩阵键盘技术:
温度输出显示技术:
LED静态显示接口技术,所谓静态显示,即CPU输出显示值后,由硬件保存输出值,保持显示结果.
特点:占用机时少,显示可靠.但元件多,线路复杂、成本高,功耗大。
报警电路设计:正常运行时绿灯亮,在保温阶段炉内温度超出系统允差范围,就要进行报警。报警时报警灯亮,电笛响,同时发送中断信号至CPU进行处理。
4、元器件的选择
传感器的选择:铂铑10—铂热电偶,S型,正极性,量程0—1300C,使用温度小于等于600C,允差+1.5C。
执行元件的选择:电阻加热炉采用晶闸管(SCR)来做规律控制,结合电阻炉的具体要求,为了减少炉温的纹波,对输出通道采用较高的分辨率的方案,因此采用移相触发方式,并且由模拟触发器实现移相触发。
变送器的选择:因为系统要求有偏置,又需要对热电偶进行冷端补偿,所以采用常规的DDZ系列温度变送器。
控制元件:采用双向可控硅进行控制,其功能相当于两个单向可控硅反向连接,具有双向导通功能,其通断状态有控制极G决定。在控制极加上脉冲可使其正向或反向导通。
第4章数字控制系统设计
4.1 系统控制参数确定
4.1.1 被控参数选择
单回路控制系统选择被控参数时要遵循以下原则:在条件许可的情况下,首先应尽量选择能直接反应控制目的的参数为被控参数;其次要选择与控制目的有某种单值对应关系的间接单数作为被控参数;所选的被控参数必须有足够的变化灵敏度。
综合以上原则,在本系统中选择物料的出口温度θ作为被控参数。该参数可直接反应控制目的。
4.1.2 控制参数选择
工业过程的输入变量有两类:控制变量和扰动变量。其中,干扰时客观存在的,它是影响系统平稳操作的因素,而操纵变量是克服干扰的影响,使控制系统重新稳定运行的因素。而控制参数选择的基本原则为:
①选择对所选定的被控变量影响较大的输入变量作为控制参数;
②在以上前提下,选择变化范围较大的输入变量作为控制参数,以便易于控制;
③在①的基础上选择对被控变量作用效应较快的输入变量作为控制参数,使控制系统响应较快;
综合以上原则,选择燃料的流量Qg量作为控制参数。
4.2 PID调节器设计
对温度的控制算法, 采用技术成熟的PID 算法, 对于时间常数比较大的系
统来说, 其近似于连续变化, 因此用数字PID 完全可以得到比较好的控制效果。简单的比例调节器能够反应很快, 但不能完全消除静差, 控制不精确, 为了消除比例调节器中残存的静差, 在比例调节器的基础上加入积分调节器, 积分器的输出值大小取决于对误差的累积结果, 在差不变的情况下, 积分器还在输出
直到误差为零, 因此加入积分调节器相当于能自动调节控制常量, 消除静差, 使系统趋于稳定。积分器虽然能消除静差, 但使系统响应速度变慢。 进一步改进调节器的方法是通过检测信号的变化率来预报误差, 并对误差的变化作出响应, 于是在PI 调节器的基础上再加上微分调节器, 组成比例、积分、微分( PID)调节器, 微分调节器的加入将有助于减小超调, 克服振荡, 使系统趋于稳定, 同时加快了系统的稳定速度,缩短调整时间, 从而改善了系统的动态性能, 其控制规律的微分方程为:
)1(Y P dt
dX
T Xdt T X K D I ++
=? 传递函数为:
)1
1()(G s T s
T K s D I P ++
= 用PID 控制算法实现加热炉温度控制是这样一个反馈过程: 比较实际物料出口温度和设定温度得到偏差, 通过对偏差的处理获得控制信号, 再去调节加热炉的燃料流量, 从而实现对炉温的控制, 由于加热炉一般都是下一阶段对象和带纯滞后的一阶对象, 所以式中Kp 、K d 和K i 的选择取决于加热炉的响应特性和实际经验。
4.3 控制算法
电阻加热炉温度控制系统框图:
整个闭环系统可用一个带纯滞后的一阶惯性环节来近似,所以其控制算法采
用大林算法。电阻加热炉温度控制系统模型为
其广义的传递函数为:
大林算法的设计目标是设计一个合适的数字控制器,使整个闭环系统的传递函数相当于一个带有纯滞后的一阶惯性环节,即:
通常认为对象与一个零阶保持器相串联, 相对应的整个闭环系统的脉冲传递函
数是:
11788.2)(40+=
-s e s G s
4.4 计算过程:
连同零阶保持器在内的系统广义被控对象的传递函数
]
11788.21[)(40+-=--s e s e Z z G s
Ts
]
)1178(1
[
)1(8.2401
+-=-
-s s Z z
z T
]11781781[)1(8.2401
+--=-
-s s Z z
z T
]1111
[)1(8.21178
11
41---------=z e
z z z
15945.01154.0---=
z z
系统闭环传递函数
]
11[)()()(+-==Φ--s e s e Z z R z C z NTs
Ts τ
1
11)
1(---
----=
z e
e z T
T
N τ
τ
数字控制器:
)](1)[()
()(z z G z z D Φ-Φ=
)(])1(1[)
1(11
1
z G z e
z e
e
z
N T
T
T
N ---
--
-
------=τ
τ
τ
5
1510
1
10
10
5154.0945.01]
)1(1[)
1(------
-
------=z z z e
z e
e
z τ
τ
τ
511933.0007.01)945.01(448.6------=
z z z
]933.0933.0933.0933.01)[1()
945.01(448.6)(432111------++++--=
z z z z z z z D
消除振铃现象后的数字控制器:
111)
945.01(448.6)(----=
z z z D
1
1
1945.0297.1297.1)()()(---?-=
=z z z E z U z D
将上式离散化:U (Z )—U (Z )Z —1=1.279E (Z )—1.226E (Z )Z —1
U (K )—U (K —1)=1.279E (K )—1.226E (K —1) 最终得:U (K )=U (K —1)+1.279E (K )—1.226E (K —1)
第5章控制仪表的选型和配置
5.1 检测元件
温度的测量方式有接触式测温和非接触式测温两大类。本系统选择接触式测温元件。其中较为常用的有热电偶、热电阻和集成温度传感器三种,本系统选择热电偶作为测温元件,其电路原理图如下图所示:
图5-1 热电偶电路原理图
5.2 变送器
5.2.1 变送器选型
本系统中的变送器用于温度信号变送,故选择温度变送器。其中较为常用的有模拟式温度变送器、一体化温度变送器和智能式温度变送器三种,本系统采用典型模拟式温度变送器中的DDZ-III型热电偶温度变送器,属安全火花型防暴仪表,还可以与作为检测元件的热电偶相配合,将温度信号线性的转换成统一标准信号。变送器构成方框图如图5-2所示。
图5-2 电动III型热电偶典型模拟温度变送器构成方框图
5.2.2 变送器配置
本设计选用放入是KBW—1131型热电偶温度变送器。
1.主要技术参数:
表5.1 热电偶温度变送器参数表
2.工作原理:
KBW —1131型热电偶温度变送器是由WS 热电偶温度转换模块和GF750信号隔离模块组成,见图5-3所示。
V + 输出I/V
-
24VDC
图5-3 热电偶温度变送器原理框图
3.端子图:
图5-4 热电偶变送器接线端子图
5.3 调节器
5.3.1 调节器选型
实现PID算法的控制仪表的主要类型大致分为电动或气动,电动I型、II 型、III型,单元组合仪表或是基地是仪表等。常用的控制仪表有电动II型、III型。在串级控制系统中,选用的仪表不同,具体的实施方案也不同。电动III 型和电动II型仪表就其功能来说基本相同,但是其控制信号不相同,控制II
型典型信号为mADC
10
4,此外。
20
~
~
0,而电动III型仪表的典型信号为mADC
III型仪表较II型仪表操作、维护更为方便、简捷,同时III型仪表还具有完善的跟踪、保持电路,使得手动切换非常方便,随时都可以进行切换,且保证无扰动。所以在本设计中选用电动III型仪表。调节器的构成方框图如图5-4所示。
图5-5 电动III型调节器构成方框图
作用方式选择:对于单回路控制系统,调节器正、反作用的选择要根据控制系统所包括的各个环节的情况来确定,这样只要根据被控参数与变送器放大倍数的符号及整个控制回路开环放大倍数的符号为“负”的要求,就可以确定调节器的正、反作用。在本系统中,被控参数的放大倍数为的符号为“正”,所以调节器应选“负”作用即反作用。
5.3.2 调节器配置
1.本系统采用的DDZ-III型PID调节器TDM-400性能指标如下表所示:
表5.2 DDZ-III型PID调节器性能指标
2.DDZ-III型调节器接线端子如下图所示:
名称性能
输入信号1~5V直流电压
外给定信号4~20mA直流电流(输入电阻250?)
输出信号4~20mA直流电流
负载电阻250?~750?
输入与给定指示0~100%,指示误差为±1.0%
输出信号指示0~100%,指示误差为±2.5%
图5-6 DDZ-III型调节器调节器接线端子
5.4 执行器
5.4.1 执行器选型
本系统中,执行器是系统的执行机构,是按照调节器所给定的信号大小和方向,改变阀的开度,以实现调节燃料流量的装置。
1.执行器的结构形式:
执行器在结构上分为执行机构和调节机构。其中执行机构包括气动、电动和液动三大类,而液动执行机构使用甚少,同时气动执行机构中使用最广泛的是气动薄膜执行机构,因此执行机构的选择主要是指对气动薄膜执行机构和电动执行机构的选择,由于气动执行机构的工作温度范围较大,防爆性能较好,故本系统选择气动薄膜执行机构并配上电/气阀门定位器。
调节阀的开、关形式需要考虑到以下几种因素:
①生产安全角度:当气源供气中断,或调节阀出故障而无输出等情况下,
应该确保生产工艺设备的安全,不至发生事故;
②保证产品质量:当发生控制阀处于无源状态而恢复到初始位置时,产品的质量不应降低;
③尽可能的降低原料、产品、动力损耗;
④从介质的特点考虑。
综合以上各种因素,在加热炉温度控制系统中,执行器的调节阀选择气开阀:执行机构采用正作用方式,调节机构正装以实现气开的气动薄膜调节蝶阀。执行器由电/气阀门定位器和气动调节阀配合使用组成,其方框图如图5-7所示。
图5-7 电/气阀门定位器和气动调节阀组成的系统框图
1.调节阀的流量特性:
调节阀的流量特性的选择,在实际生产中常用的调节阀有线性特性、对数特性、抛物线特性和快开特性四种,在本系统中执行器的调节阀的流量特性选择等百分比特性。
2.调节阀的口径:
调节阀的口径的大小,直接决定着控制介质流过它的能力。为了保证系统有较好的流通能力,需要使控制阀两端的压降在整个管线的总压降中占有较大的比例。
5.4.2 执行器配置
1.电/气阀门定位器ZPD-01
表5.3 ZPD-01参数表
名称性能
输入信号4-20mA·DC
输出信号0-0.14MPa
图5-8 ZPD-01端子图
3.薄膜气动调节阀ZMBS-16K
表5.4 ZMBS-16K参数表
名称性能
输入信号0.02-0.1MPa
输出信号开度(%)
图5-9 执行器接线端子图
五、软件设计
1、系统程序流程图
a、系统主程序框图
b、A/D转换子程序流程图
C、数字控制算法子程序流程图
d、LED显示流程图
电加热炉温度控制系统设计
湖南理工学院南湖学院 课程设计 题目:电加热炉温度控制系统设计专业:机械电子工程 组名:第三组 班级:机电班 组成员:彭江林、谢超、薛文熙
目录 1 意义与要求 (2) 1.1 实际意义 (2) 1.2 技术要求 (2) 2 设计内容及步骤 (2) 2.1 方案设计 (2) 2.2 详细设计 (3) 2.2.1 主要硬件介绍 (3) 2.2.2 电路设计方法 (4) 2.2.3 绘制流程图 (7) 2.2.4 程序设计 (8) 2.3 调试和仿真 (8) 3 结果分析 (9) 4 课程设计心得体会 (10) 参考文献 (10) 附录............................................................ 10-27
1 意义与要求 1.1 实际意义 在现实生活当中,很多场合需要对温度进行智能控制,日常生活中最常见的要算空调和冰箱了,他们都能根据环境实时情况,结合人为的设定,对温度进行智能控制。工业生产中的电加热炉温度监控系统和培养基的温度监控系统都是计算机控制系统的典型应用。通过这次课程设计,我们将自己动手设计一个小型的计算机控制系统,目的在于将理论结合实践以加深我们对课本知识的理解。 1.2 技术要求 要求利用所学过的知识设计一个温度控制系统,并用软件仿真。功能要求如下: (1)能够利用温度传感器检测环境中的实时温度; (2)能对所要求的温度进行设定; (3)将传感器检测到得实时温度与设定值相比较,当环境中的温度高于或低于所设定的温度时,系统会自动做出相应的动作来改变这一状况,使系统温度始终保持在设定的温度值。 2 设计内容及步骤 2.1 方案设计 要想达到技术要求的内容,少不了以下几种器件:单片机、温度传感器、LCD显示屏、直流电动机等。其中单片机用作主控制器,控制其他器件的工作和处理数据;温度传感器用来检测环境中的实时温度,并将检测值送到单片机中进行数值对比;LCD显示屏用来显示温度、时间的数字值;直流电动机用来表示电加热炉的工作情况,转动表示电加热炉通电加热,停止转动表示电加热炉断
电阻加热炉温度控制
电阻加热炉温度控制精 选文档 TTMS system office room 【TTMS16H-TTMS2A-TTMS8Q8-
微型计算机控制技术 课程设计 ----电阻加热炉温度控制 学院:信息工程学院 专业班级:自动化0703班 姓名:唐凯 学号:07001139
目录 一、摘要 二、总体方案设计 1、设计内容及要求 2、工艺要求 3、要求实现的系统基本功能 4、对象分析 5、系统功能设计 三、硬件的设计和实现 四、数字控制器的设计) 五、软件设计) 1、系统程序流程图 2、程序清单 六、完整的系统电路图 七、系统调试 八、设计总结 九、参考文献
一、摘要 温度是工业对象中主要的被控参数之一。特别是在冶金、化工、机械各类工业中,广泛使用各种加热炉、热处理炉、反应炉等。由于炉子的种类不同,所采用的加热方法及燃料也不相同,如煤气、天然气等。但就控制系统本身的动态特性而言,均属于一阶纯滞后环节,在控制算法上基本相同,可采用PID 控制或其他纯滞后补偿算法。 为了保证生产过程正常安全地进行,提高产品的质量和数量,以及减轻工人的劳动强度,节约能源,对加热用的各种电炉要求在一定条件下保持恒温,不能随电源电压波动或炉内物体而变化,或者有的电炉的炉温根据工艺要求按照某个指定的升温或保温规律而变化,等等。 因此,在工农业生产或科学实验中常常对温度不仅要不断地测量,而且要进行控制。 二、总体方案设计 设计任务 用一台计算机及相应的部件组成电阻炉炉温的自动控制系统,并使系统达到工艺要求的性能指标。 1、设计内容及要求 电阻加热炉用于合金钢产品热力特性实验,电加热炉用电炉丝提供功率,使其在预定的时间内将炉内温度稳定到给定的温度值。在本控制对象电阻加热炉功率为8KW,有220V交流电源供电,采用双向可控硅进行控制。
电阻加热炉温度控制
微型计算机控制技术 课程设计 ----电阻加热炉温度控制 学院:信息工程学院 专业班级:自动化0703班 姓名:唐凯 学号:
目录 一、摘要 二、总体方案设计 1、设计内容及要求 2、工艺要求 3、要求实现的系统基本功能 4、对象分析 5、系统功能设计 三、硬件的设计和实现 四、数字控制器的设计) 五、软件设计) 1、系统程序流程图 2、程序清单 六、完整的系统电路图 七、系统调试 八、设计总结 九、参考文献
一、摘要 温度是工业对象中主要的被控参数之一。特别是在冶金、化工、机械各类工业中,广泛使用各种加热炉、热处理炉、反应炉等。由于炉子的种类不同,所采用的加热方法及燃料也不相同,如煤气、天然气等。但就控制系统本身的动态特性而言,均属于一阶纯滞后环节,在控制算法上基本相同,可采用PID控制或其他纯滞后补偿算法。 为了保证生产过程正常安全地进行,提高产品的质量和数量,以及减轻工人的劳动强度,节约能源,对加热用的各种电炉要求在一定条件下保持恒温,不能随电源电压波动或炉内物体而变化,或者有的电炉的炉温根据工艺要求按照某个指定的升温或保温规律而变化,等等。 因此,在工农业生产或科学实验中常常对温度不仅要不断地测量,而且要进行控制。 二、总体方案设计 设计任务 用一台计算机及相应的部件组成电阻炉炉温的自动控制系统,并使系统达到工艺要求的性能指标。 1、设计内容及要求 电阻加热炉用于合金钢产品热力特性实验,电加热炉用电炉丝提供功率,使其在预定的时间内将炉内温度稳定到给定的温度值。在本控制对象电阻加热炉功率为8KW,有220V交流电源供电,采用双向可控硅进行控制。
电阻炉温度控制实习报告
北华大学 过程控制实习 实习题目:电阻炉温度控制系统 班级学号:_________________________ 姓名:_________________________ 专业名称:_________________________ 指导教师:_________________________ 2014年3月24日
前言 在大二的课程里我们学习了自动控制系统、过程控制工程及工业自动化仪表等课程。我们学习到了许多关于自动控制方面的理论知识,但实践是检验一切真理的标准,只有真真正正的将理论与实践相结合。用理论来指导实践,用实践来检验并完善理论。为了使提高我们的动手能力及理论相结合的能力,学校组织了为期三周的关于电阻炉温度控制系统的生产实习。 生产实习为期三周,分为两阶段。第一阶段为第一周,在这一周里,我们要了解温度控制系统所用到的仪器仪表及理论知识,学习使用组态王这一生产模拟软件并用它将温度控制系统的整个控制过程做成动态模拟动画。第二阶段为第二、第三两周,在这段时间里,我们需要学会PID自整定控制仪、无纸记录仪及可控硅三相调功器的功能、使用方法以及校准。画出整个系统的电气原理图及仪器仪表的电路接线图。利用4:1衰减曲线法来调节PID的控制参数,以实现无偏差控制的控制目标。经过三周的生产实习能够更好的做到学以致用,将理论实际相结合,用理论来指导实践,用实践来完善理论。
目录 第一部分系统简介及工艺流程 (1) 1.1系统简介 (1) 1.2双向可控硅 (2) 1.3三相电阻炉 (3) 1.4K型热电偶 (5) 1.5温度变送器 (9) 1.6无纸记录仪 (10) 1.7工艺流程图 (13) 第二部分零点调整及量程调整 (14) 2.1零点调整 (14) 2.2量程调整 (18) 第三部分静态特性及动态特性 (18) 3.1静态特性及动态特性的定义 (18) 3.2实验步骤 (19) 3.3PID的参数整定口诀 (20) 3.4积分饱和问题 (20) 第四部分参数整定及投运 (22) 4.1在纯比例作用的参数整定 (22) 4.2在比例积分作用下的参数整定 (24) 4.3比例积分微分的参数整定 (25) 4.4系统的投运 (26) 第五部分组态王软件的应用 (27) 5.1组态王软件的简介 (27) 心得体会 (28) 参考文献 (30) 附录一 (31) 附录二 (32) 附录三 (33) 附录四 (34)
管式加热炉温度控制系统设计
过程控制系统课程设计报告书管式加热炉温度控制系统设计 学院:自动化 班级:15级自动化4班 指导老师:陈刚 组员: 重庆大学自动化学院 2019年1月
任务分配 过程控制系统课程设计——管式加热炉温度控制系统的设计
目录 任务分配 (2) 过程控制系统课程设计——管式加热炉温度控制系统的设计 (2) 1摘要 (4) 2模型简介 (4) 2.1背景 (4) 2.2模型假设 (4) 2.3系统扰动因素 (5) 3控制方案 (5) 3.1传统PID控制方法 (5) 3.2串级控制系统 (6) 3.3 方案选择 (7) 4串级控制器的设计 (7) 4.1主副控制器设计 (7) 4.1.1主、副回路的设计原则 (7) 4.1.2主、副调节器的选型 (7) 4.1.3主、副调节器调节规律的选择作用 (8) 4.2串级控制器的参数整定 (8) 5系统的仿真和改进 (9) 5.1串级控制系统仿真 (9) 5.2基于Smith预估计补偿器的串级控制系统 (11) 六.总结 (14) 七.参考文献 (15)
1摘要 当今世界,随着市场竞争的日益激烈,产品的质量和功能也向更高的档次发展,制造产品的工艺过程变得越来越复杂,为满足优质、高产、低消耗,作为工业自动化重要分支的过程控制的任务也愈来愈重,无论是在大规模的工业生产过程中,还是在传统工业过程改造中,过程控制技术对于提高产品质量以及节省能源等均起十分重要的作用。为了能将课程所学理论知识初步尝试应用于实践。 本设计针对管式加热炉系统的控制问题展开了研究。通过将实际加热炉模型化,通过实验法建立锅炉的数学模型。针对物料温度控制问题,在对比了简单的单回路PID控制方法、串级控制两种方法的优劣性后,选择了串级控制的方法控制物料温度。综合应用过程控制理论以及MATLAB仿真技术,通过经验模型及参数整定,得到系统响应曲线。通过反复实验,调整参数,使控制效果比较理想。 关键词:管式加热炉系统、串级控制、MATLAB仿真 2模型简介 2.1背景 管式加热炉是石油工业中重要装置之一,加热炉控制的主要任务就是保证工艺介质最终温度达到并维持在工艺要求范围内,由于其具有强耦合、大滞后等特性,控制起来非常复杂。同时,近年来能源的节约、回收和合理利用日益受到关注。加热炉是冶金、炼油等生产部门的典型热工设备,能耗很大。因此,在设计加热炉控制系统时,在满足工艺要求的前提下,节能也是一个重要质量指标,要保证加热炉的热效率最高,经济效益最大。另外,为了更好地保护环境,在设计加热炉控制系统时,还要保证燃料充分燃烧,使燃烧产生的有害气体最少,达到减排的目的。 2.2模型假设 管式加热炉的主要任务是把原质油或重油加热到一定的温度,保证下一道工序正常进行。假设有一个加热炉系统,系统参数设定为: 1.物料以恒定速度进入管道,流速为10L/s,管道直径为10cm,不考虑物料浓度变化、压力变化等其他条件。 2.物料在加热炉内的长度为L=5m,假定物料受热均匀,并在t=10s后上升至指定温度。 3.假定燃气混合浓度不变,物料温度上升只受燃料流量影响。 4.不考虑环境温度、燃料值等影响,主要考虑燃料流量的扰动。
电阻炉的工作原理和操作步骤
电阻炉的工作原理和操作步骤 一、工作原理 电阻炉是以电流通过导体所产生的焦耳热为热源的电炉。 电阻炉以电为热源,通过电热元件将电能转化为热能,在炉内对金属进行加热。电阻炉和火焰比,热效率高,可达50-80℅,热工制度容易控制,劳动条件好,炉体寿命长,适用于要求较严的工件的加热,但耗电费用高。 按传热方式,电阻炉分为辐射式电阻炉和对流式电阻炉。辐射式电阻炉以辐射传热为主,对流传热作用较小;对流式电阻炉以对流传热为主,通常称为空气循环电阻炉,靠热空气进行加热,炉温多低于650℃。 按电热产生方式,电阻炉分为直接加热和间接加热两种。 在直接加热电阻炉中,电流直接通过物料,因电热功率集中在物料本身,所以物料加热很快,适用于要求快速加热的工艺,例如锻造坯料的加热。这种电阻炉可以把物料加热到很高的温度,例如碳素材料石墨化电炉,能把物料加热到超过2500□。直接加热电阻炉可作成真空电阻加热炉或通保护气体电阻加热炉,在粉末冶金中,常用于烧结钨、钽、铌等制品。 采用这种炉子加热时应注意:①为使物料加热均匀,要求物料各部位的导电截面和电导率一致;②由于物料自身电阻相当小,为达到所需的电热功率,工作电流相当大,因此送电电极和物料接触要好,以免起电弧烧损物料,而且送电母线的电阻要小,以减少电路损失; ③在供交流电时,要合理配置短网,以免感抗过大而使功率因数过低。 大部分电阻炉是间接加热电阻炉,其中装有专门用来实现电-热转变的电阻体,称为电热体,由它把热能传给炉中物料。这种电炉炉壳用钢板制成,炉膛砌衬耐火材料,内放物料。最常用的电热体是铁铬铝电热体、镍铬电热体、碳化硅棒和二硅化钼棒。根据需要,炉内气氛可以是普通气氛、保护气氛或真空。一般电源电压220伏或380伏,必要时配置可调节电压的中间变压器。小型炉(<10千瓦)单相供电,大型炉三相供电。对于品种单一、批料量大的物料,宜采用连续式炉加热。炉温低于700□的电阻炉,多数装置鼓风机,以强化炉内传热,保证均匀加热。用于熔化易熔金属(铅、铅铋合金、铝和镁及其合金等)的电阻炉,可做成坩埚炉;或做成有熔池的反射炉,在炉顶上装设电热体。 电阻炉- 电阻炉操作流程 二、工作前的流程 1、检查炉内是否干净,清理杂物,确保炉内干净。 2、检查炉壁,炉底板是否有破裂等损坏。 3、电阻丝和热电偶引出棒的安装紧固情况,检查仪表是否正常。 4、检查电阻炉炉门开关是否灵活。 5、确保各项正常以后,开始放工件。 三、工作中的流程 1、放工件时确保电源关闭。 2、轻拿轻放以免砸坏电热元件、炉底板等; 3、严禁投放潮湿的工件,炉内加热的工件和电热元件应保持50—70mm的距离; 4、工作中检查各种仪表仪器,如有异常,及时维修。 5、炉温在700℃以上时,不准打开炉门降温或出炉,以免因骤冷而减短炉子寿命。 四、工作后的流程。 1、切断电源 2、轻拿轻放工件,确保不要损坏炉体和工件。 3、重新装炉,按以上程序重复进行。
基于PID的电阻炉温度控制系统
基于PID的炉温控制系统 摘要:在科学实验中,温度是极为普遍又极为重要的热工参数之一。为了保证科学实验正常安全的进行,提高实验的精确性,介绍了用AT89S51单片机为主要元件组成的 控制系统,并给出了部分硬件图、控制算法和软件流程图。 关键词:PID;炉温控制 1引言 电阻炉是一种利用电流通过电热元件产生的热量加热工件的热处理设备具有结构简单操作简便价格低廉等特点广泛用于工业中,而温度是工业对象中主要的被控参数之一。在冶金、化工、机械、火工、食品等各类工业中,广泛使用各种加热炉、烘箱、恒温箱等,它们均需对温度进行精确的控制。 采用单片机进行炉温控制,具有电路设计简单、精度高、控制效果好等优点,对提高生产效率、促进科技进步等方面具有重要的现实意义。本文以加热炉为具体对象介绍温度控制系统的设计方法。该系统是以AT89S51为核心建立起来的一个温度测量控制系统,加热炉的被控温度为0~500℃,精度:±0.5°C,显示分辨率0.2°C。通过单片机显示温度值。显示:000.0。 本文介绍炉温控制系统的设计。 图1 温控系统组成 1 硬件系统 本系统的硬件电路包括:过零触发电路、温度检测电路、双向可控硅触发电路。电炉一般采用电阻丝作为加热元件,系统中温度传感器采用PT100。炉体的加热通过加热电热丝的方法来实现。工频220V电压被电阻分压后,经过运放输出得到幅值为10V的正弦电压,此电压的频率与工频电压频率相同,为50HZ。经过芯片MC14528,正弦波整形为脉宽为2~3ms、周期为10ms的方波。方波信号触发双向晶闸管导通,从而实现加热丝加热回路的导通,使加热丝正常工作加热炉体,电路如图2。 由图2可以看到LM311电压比较器将50HZ的正弦交流电压变成方波,得到的电压为10V。方波的正跳沿和负跳沿作为单稳态触发器的输入信号,从单稳态触发器输出220v过零同步脉冲。MC14528在Q1、Q2脚输出同步脉冲,脉冲的宽度为2~3ms ,Q1、Q2输出脉冲通过或门后,输出的方波信号变成可以触发双向可控硅的窄脉冲信号。此信号进过光电隔离器MOC3061/3021,便可以触发双向可控硅。此信号经单片机控制信号控制后,可以任意控制可控硅的导通关断,从而控制加热炉的开断。
加热炉出口温度与炉膛温度串级控制系统设计
第一章系统分析与控制方案的确立 1.系统分析 图1.1所示为某工业生产中的加热炉,其任务是将被加热物料加热到一定温度,然后送到下道工序进行加工。加热炉工艺过程为:被加热物料流过排列炉膛四周的管道后,加热到炉出口工艺所要求的温度。在加热用的燃料油管道上装有一个调节阀,用以控制燃料油流量,以达到控制出口温度的目的。 T1出口 支路1 炉膛 支路2 燃料 被加热物料 图1.1加热炉出口温度系统 由于加热炉时间常数大,而且扰动的因素多,比如原料侧的扰动及负荷扰动;燃烧侧的扰动等,单回路反馈控制系统不能满足工艺对加热炉出口温度的要求。为了提高控制质量,采用串级控制系统,运用副回路的快速作用,有效地提高控制质量,满足生产要求。 2.串级控制系统的设计 加热炉工艺过程为:被加热物料流过排列炉膛四周的管道后,加热到炉出口工艺所要求的温度。在加热用的燃料油管道上装有一个调节阀,用以控制燃料油流量,以达到控制出口温度的目的。由于加热炉时间常数大,而且扰动的因素多,比如原料侧的扰动及负荷扰动;燃烧侧的扰动等,单回路反馈控制系统不能满足工艺对加热炉出口温度的要求。为了提高控制质量,采用串级控制系统,运用副回路的快速作用,以加热炉出口温度为主变量,选择滞后较小的炉膛温度为副变量,构成炉出口温度与炉膛温度的串级控制系统有效地提高控制质量,以满足工业生产的要求,系统的串级控制结构图如图1.2所示。
图 1.2 加热炉出口温度串级控制系统结构图 串级控制系统的工作过程,就是指在扰动作用下,引起主、副变量偏离设 定值,由主、副调节器通过控制作用克服扰动,使系统恢复到新的稳定状态的 过渡过程。由加热炉出口温度串级控制系统结构图可绘制出其结构方框图,如 图 1.3 所示。 图 1.3 加热炉出口温度串级控制系统结构方框图 (1) 主被控参数的选择 应选择被控过程中能直接反映生产过程中的产品产量和质量,又易于测量 的参数。在加热炉出口温度与炉膛温度的串级控制系统中加热炉出口温度为系 统的主被控参数,因为加热炉出口温度是整个控制作用的关键,要求出口物料 温度维持在某给定值上下。如果其调节欠妥当,会造成整个系统控制设计的失 败。 (2) 副被控制参数的选择 从整个系统来看,加热炉的炉膛温度虽然不是我们要控制的直接目标,但 是炉膛温度会很大程度上影响出口物料的温度,因此我们选择炉膛温度为副被 控参数。 (3) 控制器的选择 主控制器的选择:主被控变量是工艺操作的主要指标(温度),允许波动的 度 副控制器 调节阀 主控制器 主检测、变送仪表 副检测、变送仪表 炉膛 出口温度
电阻炉和感应炉
电阻炉以电流通过导体所产生的焦耳热为热源的电炉。按电热产生方式,电阻炉分为直接加热和间接加热两种。在直接加热电阻炉中,电流直接通过物料,因电热功率集中在物料本身,所以物料加热很快,适用于要求快速加热的工艺,例如锻造坯料的加热。这种电阻炉可以把物料加热到很高的温度,例如碳素材料石墨化电炉,能把物料加热到超过2500□。直接加热电阻炉可作成真空电阻加热炉或通保护气体电阻加热炉,在粉末冶金中,常用于烧结钨、钽、铌等制品。采用这种炉子加热时应注意:①为使物料加热均匀,要求物料各部位的导电截面和电导率一致;②由于物料自身电阻相当小,为达到所需的电热功率,工作电流相当大,因此送电电极和物料接触要好,以免起电弧烧损物料,而且送电母线的电阻要小,以减少电路损失;③在供交流电时,要合理配置短网,以免感抗过大而使功率因数过低。 大部分电阻炉是间接加热电阻炉,其中装有专门用来实现电-热转变的电阻体,称为电热体,由它把热能传给炉中物料(图1 间接加热电阻炉)。这种电炉炉壳用钢板制成,炉膛砌衬耐火材料,内放物料。最常用的电热体是铁铬铝电热体、镍铬电热体、碳化硅棒和二硅化钼棒。根据需要,炉内气氛可以是普通气氛、保护气氛或真空。一般电源电压220伏或380伏,必要时配置可调节电压的中间变压器。小型炉(<10千瓦)单相供电,大型炉三相供电。对于品种单一、批料量大的物料,宜采用连续式炉加热。炉温低于700□的电阻炉,多数装置鼓风机,以强化炉内传热,保证均匀加热。用于熔化易熔金属(铅、铅铋合金、铝和镁及其合金等)的电阻炉,可做成坩埚炉;或做成有熔池的反射炉,在炉顶上装设电热体。电渣炉是由溶渣实现电热转变的电阻炉(见电渣重熔)。 感应炉利用物料的感应电热效应而使物料加热或熔化的电炉。感应炉的基本部件是用紫铜管绕制的感应圈。感应圈两端加交流电压,产生交变的电磁场,导电的物料放在感应圈中,因电磁感应在物料中产生涡流,受电阻作用而使电 能转变成热能来加热物料;所以,也可认为感应电热是一种直接加热式电阻电热。 感应电热的特点是在被加热物料中转变的电热功率(电流分布)很不均匀,表面最大,中心最小,称为趋肤效应。为了提高感应加热的电热效率,供电频率要合宜,小型熔炼炉或对物料的表面加热采用高频电,大型熔炼炉或对物料深透加热采用中频或工频电。感应圈是电感量相当大的负载,其功率因数一般很低。为了提高功率因数,感应圈一般并联电容器,称为补偿电容。感应圈和物料之间的间隙要小,感应圈宜用方形紫铜管制作,管内通水冷却,
电阻炉温度控制系统的设计说明
电炉温度控制系统设计
摘要 热处理是提高金属材料及其制品质量的重要技术手段。近年来随工业的发展, 对金属材料的性能提出了更多更高的要求,因而热处理技术也向着优质、高效、节能、无公害方向发展。电阻炉是热处理生产中应用最广泛的加热设备,加热时恒温过程的测量与控制成为了关键技术,促使人们更加积极地研制热加工工业过程的温度控制器。 此设计针对处理电阻炉炉温控制系统,设计了温度检测和恒温控制系统,实现了基本控制、数据采样、实时显示温度控制器运行状态。控制器采用51 单片机作为处理器,该温度控制器具有自动检测、数据实时采集处理及控制结果显示等功能,控制的稳定性和精度上均能达到要求。满足了本次设计的技术要求。 关键词:电阻炉,温度测量与控制,单片机
目录 一、绪论 ....................................................................................................... - 1 - 1.1 选题背景........................................................................................ - 1 - 1.2 电阻炉国发展动态........................................................................... - 1 - 1.3 设计主要容 .................................................................................... - 2 - 二、温度测量系统的设计要求........................................................................... - 3 - 2.1 设计任务......................................................................................... - 3 - 2.2 系统的技术参数................................................................................ - 3 - 2.3 操作功能设计................................................................................... - 4 - 三、系统硬件设计........................................................................................... - 5 - 3.1 CPU选型........................................................................................ - 5 - 3.2 温度检测电路设计.............................................................................. - 6 - 3.2.1 温度传感器的选择..................................................................... - 6 - 3.2.1.1热电偶的测温原理 ......................................................... - 7 - 3.2.1.2 热电偶的温度补偿......................................................... - 7 - 3.2.2 炉温数据采集电路的设计.......................................................... - 8 - 3.2.2.1 MAX6675芯片.......................................................... - 8 - 3.2.2.2 MAX6675的测温原理................................................. - 9 - 3.2.2.3 MAX6675 与单片机的连接.......................................... - 10 - 3.3 输入/输出接口设计......................................................................... - 10 - 3.4 保温定时电路设计 .......................................................................... - 13 - 3.4.1 DS1302 与单片机的连接....................................................... - 13 - 3.5 温度控制电路设计............................................................................ - 14 - 系统硬件电路图...................................................................................... - 17 - 四、系统软件设计......................................................................................... - 19 - 4.1 软件总体设计 .................................................................................. - 19 - 4.2 主程序设计 ..................................................................................... - 19 - 4.3 温度检测及处理程序设计................................................................... - 20 - 4.4 按键检测程序设计............................................................................ - 23 - 4.5 显示程序设计 .................................................................................. - 25 - 4.6 输出程序设计 .................................................................................. - 27 - 4.7中值滤波 ......................................................................................... - 28 - 五、结论 ..................................................................................................... - 30 - 参考文献 ..................................................................................................... - 31 -
课程设计(论文)-基于PLC的电加热炉温度控制系统设计
第一章绪论 1.1选题背景及意义 加热炉是利用电能来产生蒸汽或热水的装置。因为其效率高、无污染、自动化程度高,稳定性好的优点,冶金、机械、化工等各类工业生产过程中广泛使用电加热炉对温度进行控制。而传统的加热炉普遍采用继电器控制。由于继电器控制系统中,线路庞杂,故障查找和排除都相对困难,而且花费大量时间,影响工业生产。随着计算机技术的发展,传统继电器控制系统势必被PLC所取代。二十世纪七十年代后期,伴随着微电子技术和计算机技术的快速发展,也使得PLC 具有了计算机的功能,成为了一种以电子计算机为核心的工业控制装置,在温度控制领域可以让控制系统变得更高效,稳定且维护方便。 在过去的几十年里至今,PID控制已在工业控制中得到了广泛的应用。在工业自动化的三大支柱(PLC、工业机器人、CAD/CAM)中位居第一。由于其原理简单、使用方便、适应能力强,在工业过程控制中95%甚至以上的控制回路都采用了PID结构。虽然后来也出现了很多不同新的算法,但PID仍旧是最普遍的规律。 1.2国内外研究现状及发展趋势 一些先进国家在二十世纪七十年代后期到八十年代初期就开始研发电热锅炉,中国到八十年代中期才开始起步,对电加热炉的生产过程进行计算机控制的研究。直到九十年代中期,不少企业才开始应用计算机控制的连续加热炉,可以说发展缓慢,而且对于国内的温度控制器,总体发展水平仍不高,不少企业还相当落后。与欧美、日本,德国等先进国家相比,其差距较大。目前我国的产品主要以“点位”控制和常规PID为主,只能处理一些简单的温度控制。对于一些过程复杂的,时变温度系统的场合往往束手无策。而相对于一些技术领先的国家,他们生产出了一批能够适应于大惯性、大滞后、过程复杂,参数时变的温度控制系统。并且普遍采用自适应控制、模糊控制及计算机技术。 近年来,伴随着科学技术的不断快速发展,计算机技术的进步和检测设备及
电阻炉的工作原理和常见操作注意事项
一、电阻炉的工作原理 电阻炉是以电流通过导体所产生的焦耳热为热源的电炉。 电阻炉以电为热源,通过电热元件将电能转化为热能,在炉内对金属进行加热。电阻炉和火焰比,热效率高,可达50-80℅,热工制度容易控制,劳动条件好,炉体寿命长,适用于要求较严的工件的加热,但耗电费用高。 按传热方式,电阻炉分为辐射式电阻炉和对流式电阻炉。辐射式电阻炉以辐射传热为主,对流传热作用较小;对流式电阻炉以对流传热为主,通常称为空气循环电阻炉,靠热空气进行加热,炉温多低于650℃。 按电热产生方式,电阻炉分为直接加热和间接加热两种。 在直接加热电阻炉中,电流直接通过物料,因电热功率集中在物料本身,所以物料加热很快,适用于要求快速加热的工艺,例如锻造坯料的加热。这种电阻炉可以把物料加热到很高的温度,例如碳素材料石墨化电炉,能把物料加热到超过2500□。直接加热电阻炉可作成真空电阻加热炉或通保护气体电阻加热炉,在粉末冶金中,常用于烧结钨、钽、铌等制品。 采用这种炉子加热时应注意:①为使物料加热均匀,要求物料各部位的导电截面和电导率一致;②由于物料自身电阻相当小,为达到所需的电热功率,工作电流相当大,因此送电电极和物料接触要好,以免起电弧烧损物料,而且送电母线的电阻要小,以减少电路损失; ③在供交流电时,要合理配置短网,以免感抗过大而使功率因数过低。 大部分电阻炉是间接加热电阻炉,其中装有专门用来实现电-热转变的电阻体,称为电热体,由它把热能传给炉中物料。这种电炉炉壳用钢板制成,炉膛砌衬耐火材料,内放物料。最常用的电热体是铁铬铝电热体、镍铬电热体、碳化硅棒和二硅化钼棒。根据需要,炉内气氛可以是普通气氛、保护气氛或真空。一般电源电压220伏或380伏,必要时配置可调节电压的中间变压器。小型炉(<10千瓦)单相供电,大型炉三相供电。对于品种单一、批料量大的物料,宜采用连续式炉加热。炉温低于700□的电阻炉,多数装置鼓风机,以强化炉内传热,保证均匀加热。用于熔化易熔金属(铅、铅铋合金、铝和镁及其合金等)的电阻炉,可做成坩埚炉;或做成有熔池的反射炉,在炉顶上装设电热体。 二、安全操作规程 装炉 1.开车前检查轨道有无障碍物,钢丝绳、卷扬机、托轮、小托车必须完好,并按规定加油润滑。 2.开车人员必须听从装炉操作人员指挥,密切配合。放置炉底乏料,要用钢尺插量三点(两端及中间),按规定尺寸检查,炉头四角的乏料要装足踩实,防止流盐烧墙。 3.炉芯位置确定要准确,反应箱必须垂直吊放,高度适中,放置端正,两排箱体之间保持等距,定保炉芯宽度尺寸精确无误。反应箱四角与端墙缝隙处,用纸填实。 4.吊反应箱时,应指挥吊车摆正位置,垂直提升。须待箱体全部拨出后,才能开动大车吊走。严禁炉车在运行中吊反应箱。放反应箱时,按顺序摆放。装炉工应将去掉的四链钩放于箱体之内,以免起钩时挂住外沿使箱体移动位置或箱体碰伤操作人员。 5.每放完一部炉料后,料斗闭合器要关严密。炉料装完后,洒在端墙拉杆上的乏料或石墨要清理干净,卷扬机小车停放在安全位置,压起顶轴,用盖盖好,并将所装炉号及装炉异常情况填入工艺卡片,随炉传送托车组。 扒炉 1.冶炼炉停炉24小时之后,方可进行扒炉操作。 2.根据当天风向,确定扒墙顺序。炉墙和支柱上吊环完整好用时,操作人员不应上墙挂钩。如果吊环断裂脱落或无吊环,上炉挂钩人员注意力必须高度集中,采取安全措施,在炉墙上小心稳步行走,挂好钩后立即返回安全位置,指挥起吊。
计算机控制技术课程设计-电阻炉温度控制系统设计
合肥工业大学 《计算机控制技术》课程设计 ——电阻炉温度控制系统设计 学院专业 姓名 学号_______ ________ _ 完成时间
摘要:电阻炉的类型根据其热量产生的方式不同,可分为间接加热式和直接加热式两大类。间接加热式电阻炉,就是在炉子内部有专用的电阻材料制作的加热元件,电流通过加热元件时产生热量,再通过热的传导、对流、辐射而使放置在炉中的炉料被加热。直接加热式电阻炉,是将电源直接接在所需加热的材料上,让强大的电流直接流过所需加热的材料,使材料本身发热从而达到加热的效果。工业电阻炉,大部分采用间接加热式,只有一小部分采用直接加热式。由于电阻炉具有热效率高、热量损失小、加热方式简单、温度场分布均匀、环保等优点,应用十分广泛。 关键词:炉温控制;高效率;加热 一、总体方案设计 本次课程设计主要就是使用计算机以及相应的部件组成电阻炉炉温的自动控制系统,从而使系统达到工艺要求的性能指标。 1、设计内容及要求 电阻加热炉用于合金钢产品热力特性实验,电加热炉用电炉丝提供功率,使其在预定的时间内将炉内温度稳定到给定的温度值。在本控制对象电阻加热炉功率为8KW,有220V交流电源供电,采用双向可控硅进行控制。 2、工艺要求及要求实现的基本功能 本系统中所选用的加热炉为间接加热式电阻炉,控制要求为采用一台主机控制8个同样规格的电阻炉温度;电炉额定功率为20 kW;)恒温正常工作温度为1000℃,控温精度为±1%;电阻炉温度按预定的规律变化,超调量应尽可能小,且具有良好的稳定性;具有温度、曲线自动显示和打印功能,显示精度为±1℃;具有报警、参数设定、温度曲线修改设置等功能。 3、控制系统整体设计 电阻炉温度计算机控制系统主要由主机、温度检测装置、A/D转换器、执行机构及辅助电路组成。系统中主机可以选用工业控制计算机、单片微型计算机或可编程序控制器中的一种作为控制器,再根据系统控制要求,选择一种合理的控制算法对电阻炉温度进行控制。控制系统组成框图如图11-1所示。采用热电偶
电加热炉温度控制
基于单片机的电加热炉温度控制系统设计 王丽华1郑树展2 (1、天津职业大学,天津300402;2、天津航空机电有限公司,天津300123) 摘要:温度控制是工业对象中主要的控制参数之一,其控制系统本身的动态特性属于一阶纯滞后环节。以8051单片机为核心,采用温度变送器桥路和固态继电器控温电路,实现对电炉温度的自动控制。该控制系统具有硬件成本低、控温精度较高、可靠性好、抗干扰能力强等特点。 关键词:电加热炉控温固态继电器飞升曲线 0引言 传统的以普通双向晶闸管(SCR)控制的高温电加热炉采用移相触发电路改变晶闸管导通角的大小来调节输出功率,达到自动控制电加热炉温度的目的。这种移相方式输出一种非正弦波,实践表明这种控制方式产生相当大的中频干扰,并通过电网传输,给电力系统造成“公害”。采用固态继电器控温电路,通过单片机控制固态继电器,其波形为完整的正弦波,是一种稳定、可靠、较先进的控制方法。为了降低成本和保证较高的控温精度,采用普通的ADC0809芯片和具有零点迁移、冷端补偿功能的温度变送器桥路,使实际测温范围缩小。 1电加热炉温度控制系统的硬件设计 电加热炉温度控制系统的硬件由图1所示各部件组成,它以8051单片机为核心,外扩键盘输入和LED显示温度。电加热炉炉内的实际温度由热电偶测量并转换成毫伏级的电压信号,通过温度变送器桥路实现零点迁移和冷端补偿,经运算放大器7650放大到0~5V,再经过有源低通滤波器滤波后,由A/D转换成数字量。此数字量经数字滤波、标度转换后,一方面通过LED将炉温显示出来;另一方面,将该温度值与被控温度值进行比较,根据其偏差值的大小,采用PID控制,通过PWM脉冲调宽功率放大器控制SSR固态继电器来控制电加热炉炉丝的导通时间,就可以控制电炉丝的加热功率大小,从而控制电炉的温度及升温速度,使其逐渐趋于给定值且达到平衡。 1.1 热电偶的选取 热电偶是温度测量传感器,对它的选择将直接影响检测误差的大小。目前多选K型或S 型(镍铬-镍硅)热电偶。两者相比,K型有较好的温度—热电势的线性度,但它不适宜于长时间在高温区适用;S型有高的精度,但温度—热电势的线性度较差。 A/D转换器 图1中A/D转换芯片采用ADC0809,其转换精度是1/256。若电加热炉工作温度是256℃,这样在(0~256)℃范围A/D的转换精度为256℃/256=1℃/bit,即一个数字量表示1℃,这显然不能满足控制精度为±0.5℃要求。为了提高控制精度,可以选用更高位的A/D转换器,如10位、12位、16位A/D转换器,其控值精度均能满足要求。然而根据实际需要温度控制情况,也可以通过具有零点迁移和冷端补偿功能的温度变送桥路,缩小测温的范围,如
单片(加热炉温度控制器)机
本科生课程设计(论文)辽宁工业大学 单片机原理及接口技术课程设计(论文)题目:加热炉温度控制器设计 院(系):电气工程学院 专业班级:电气092 学号: 090303040 学生姓名: 指导教师:(签字) 起止时间:2012.06.24-2012.07.06
课程设计(论文)任务及评语 院(系):电气工程学院 教研室: 电气工程及其自动化 注:成绩:平时20% 论文质量60% 答辩20% 以百分制计算 学 号 学生姓名 专业班级 电气092 课程设计(论文)题目 加热炉温度控制器设计 课程设计(论文)任务 高温加热炉利用煤气加热,通过传感器测量温度,四相5V 、1A 步进电机调节阀门来调节进气量。温度控制范围0~1800℃。 设计任务: 1. CPU 最小系统设计(包括CPU 选择,晶振电路,复位电路) 2. 温度传感器及接口电路设计 3. 步进电机驱动电路设计 4. 程序流程图设计及程序清单编写 技术参数: 1.温度控制范围:0-1800℃ 2.工作电源220V 设计要求: 1、分析系统功能,尽可能降低成本,选择合适的单片机、AD 转换器、输出电路等; 2、应用专业绘图软件绘制硬件电路图和软件流程图; 3、按规定格式,撰写、打印设计说明书一份,其中程序开发要有详细的软件设计说明,详细阐述系统的工作过程,字数应在4000字以上。 进度计划 第1天 查阅收集资料 第2天 总体设计方案的确定 第3-4天 CPU 最小系统设计 第5天 温度传感器及接口电路设计 第6天 步进电机驱动电路设计 第7天 程序流程图设计 第8天 软件编写与调试 第9天 设计说明书完成 第10天 答辩 指导教师评语及成绩 平时: 论文质量: 答辩: 总成绩: 指导教师签字: 年 月 日
电阻炉温度控制.
项目九电阻炉温度控制 项目内容: 在现代化的工业生产中,电流、电压、温度、压力、流量、流速和开关量都是常用的主要被控参数。例如:在冶金工业、化工生产、电力工程、造纸行业、机械制造和食品加工等诸多领域中,人们都需要对各类加热炉、热处理炉、反应炉和锅炉中的温度进行检测和控制。采用MCS-51单片机来对温度进行控制,不仅具有控制方便、组态简单和灵活性大等优点,而且可以大幅度提高被控温度的技术指标,从而能够大大提高产品的质量和数量。因此,单片机对温度的控制问题是一个工业生产中经常会遇到的问题。 温度采集采用热电偶,经过变送器后转换为电信号。经过A/D转换器ADC0809转变为数字量。 8031对温度的控制是通过D/A转换实现的。双向可控硅管和加热丝串接在交流220V、50Hz市电回路。在给定周期T内,8031只要改变可控硅管的接通时间即可改变加热丝的功率,以达到调节温度的目的。 通常,电阻炉炉温控制都采用偏差控制法。偏差控制的原理是先求出实测炉温对所需炉温的偏差值,然后对偏差值处理获得控制信号去调节电阻炉的加热功率,以实现对炉温的控制。在工业上,偏差控制又称PID控制,这是工业控制过程中应用最广泛的一种控制形式,一般都能收到令人满意的效果。
能力目标: 课题1 A-D转换接口技术 课题2 ADC0809的应用技术 课题3 D-A转换接口技术 课题4 TLC5615的应用技术 实践演练: 1.亲手设计调试电阻炉的温度,对炉温的采集,与预设值相比较,对偏差值处理获得控制信号去调节电阻炉的加热功率,以实现对炉温的控制。 2.动手设计采集A/D转换温度对电炉丝进行控制,从而实现温度的调节。 3.通过该项目的训练,提高学生的实际动手操作能力,养成学生的工程道德观念,建立工程敬业精神和团队合作精神。