影响管线钢X60屈强比的基础参数研究
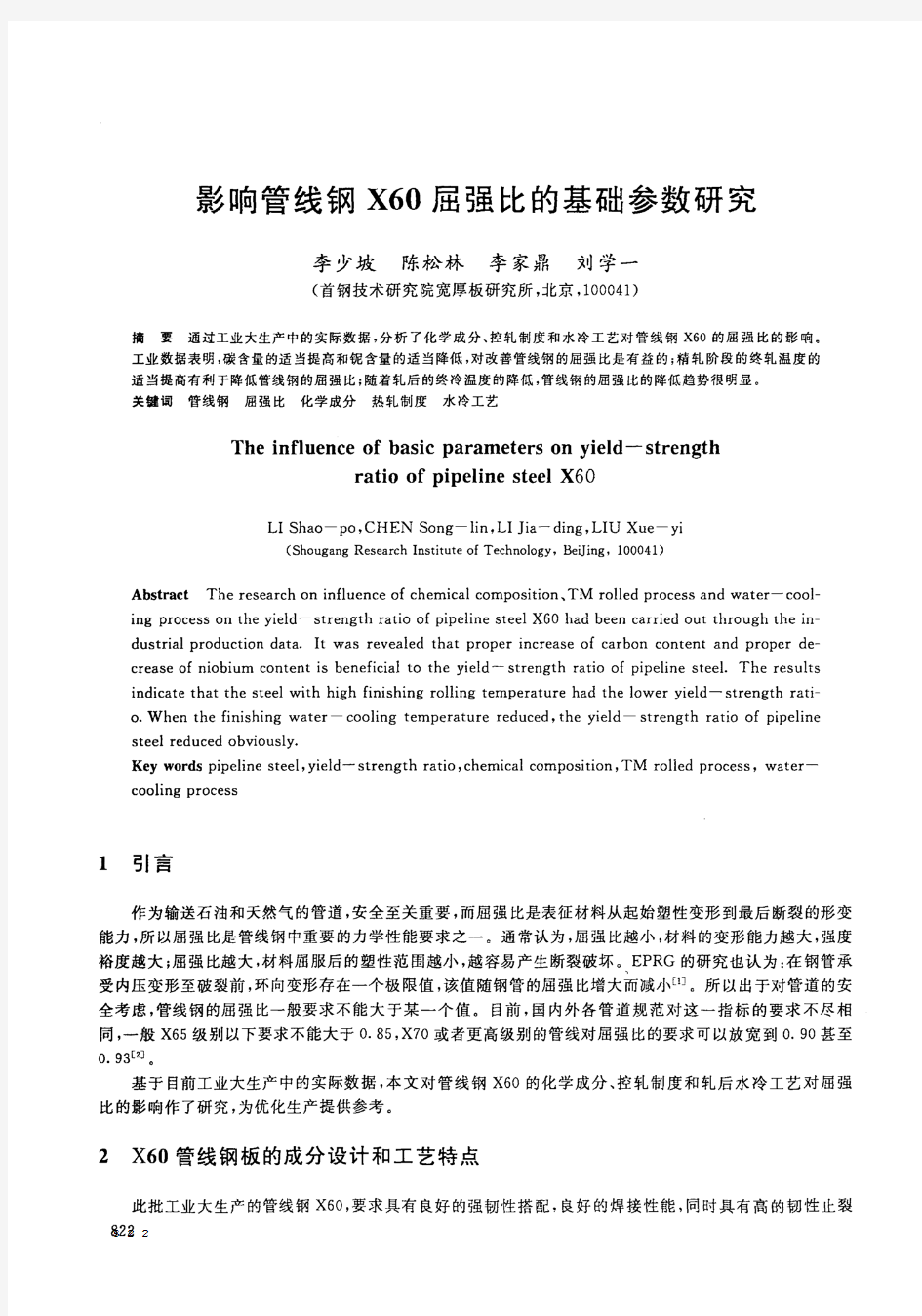
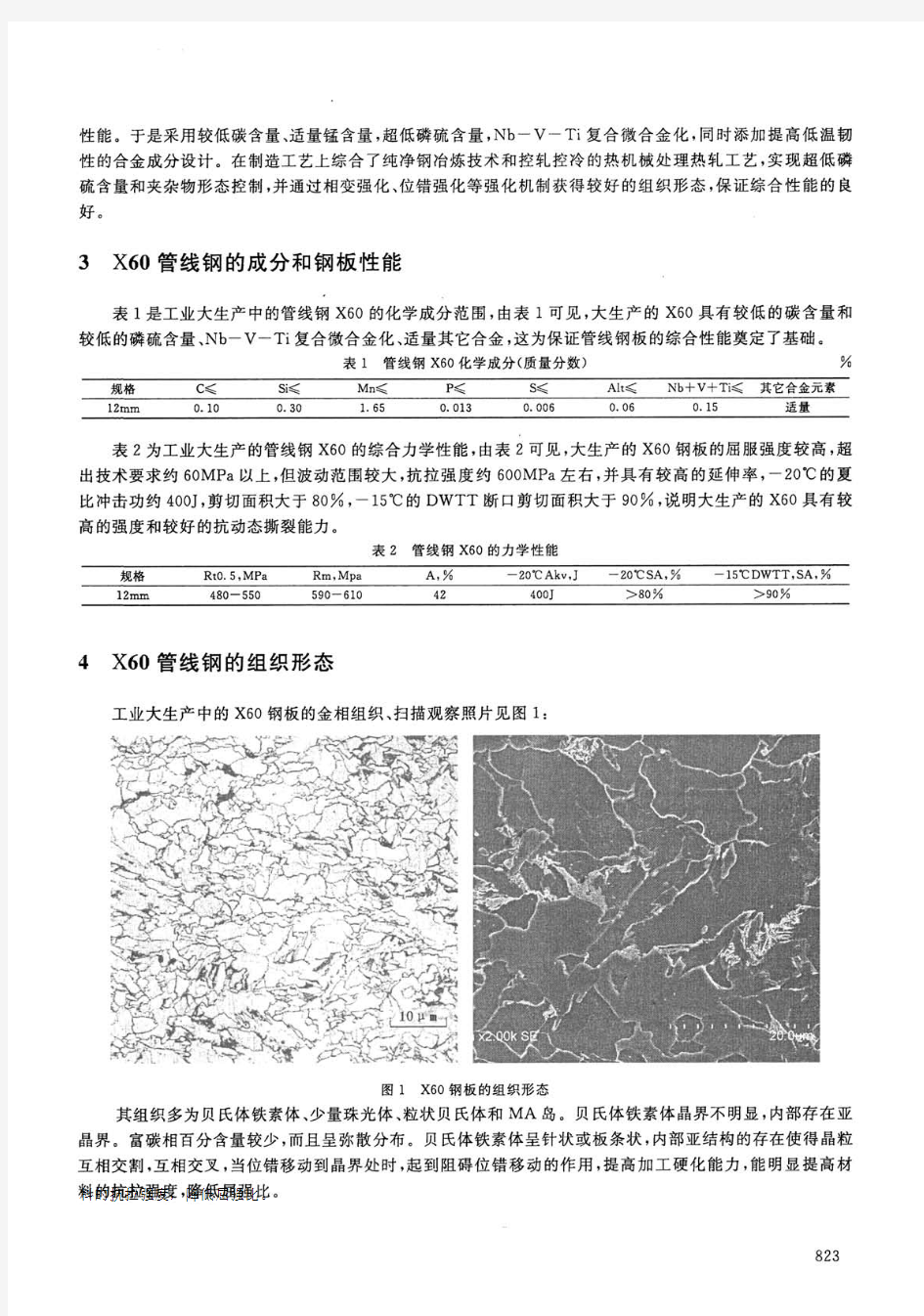
天然气管道管壁穿孔失效分析
摘要:co2腐蚀是油气田开发和油气集输过程中最常见的腐蚀形式之一,在天然气集输过程中,co2引起的管线内腐蚀问题普遍存在,往往导致管体发生严重局部减薄,甚至穿孔、断裂.一旦发生,会给生产实际造成重大经济损失和灾难性后果。因此,研究co2腐蚀的机理、分析co2腐蚀的影响因素,对预防由此引发的安全事故以及提高天然气输送效率具有重要的现实意义。文章以本文以某天然气管道管壁穿孔失效分析为例,对试样从co2致天然气管线腐蚀的产物形貌及成分进行了微观分析,并对co2腐蚀机理、影响因素等方面做了较为详尽的阐述。 关键词:co2腐蚀;穿孔;失效分析;腐蚀产物形貌;腐蚀机理; 1 前言 在石油和天然气勘探开发过程中,co2作为开采伴生气同时产出。由于co2的广泛存在,使得石油和天然气开采和集输的整个过程面临着严重的co2腐蚀威胁[1]。 co2容易溶于水,形成h2co3,降低环境的ph,对石油和天然气开采与集输系统中的油套管钢、管线钢等造成严重的腐蚀,并且h2co3可以直接在钢铁表面还原,因此在相同ph 条件下,co2水溶液的腐蚀性要比hcl溶液还要强[2]。co2腐蚀穿孔造成的原油和天然气泄漏事故,不仅直接造成了资源的浪费,还污染了水和大气资源,破坏了环境。在能源需求日益增大,油气工业大发展的今天,co2腐蚀成为困扰油气工业发展的一个极为突出并急需解决的问题。 2 腐蚀分析 2.1化学成分分析 取样对泄漏管道进行化学成分分析,结果见表1。分析结果表明,管道的化学成分符合gb/t 9711.2-1999[3]的对规定。 2.2. 扫描电镜分析 对管道内部泄漏孔处进行扫描电镜检测,发现其内壁被腐蚀产物覆盖,腐蚀产物上可见龟裂裂纹,未见裸露金属表面。 2.3 xrd物相分析 为确定腐蚀产物的结构,对管道内壁泄漏孔处的腐蚀产物进行了xrd物相分析。检测结果表明,腐蚀产物的主要物相为fe3o4、α- fe2o3和feo。 2.4 水质分析 取泄漏管道沿线的7组水样进行氯离子含量测定,结果显示氯离子含量最高达到6522mg/l,最低也到了250mg/l。说明氯离子的含量已经达到了很高的程度。 3. 腐蚀机理分析 根据上述的分析,管道在泄漏前处于非常恶劣的环境。首先,管道底部可能残留cl-含量很高的液态水;其次管道在安装完成后,长期接触富含co2和o2的空气。在上述因素的影响下,在管道内壁发生了复杂的电化学腐蚀过程,最终导致管道内壁的点蚀和全面腐蚀的发生。 相关研究表明,在潮湿的环境中,c02的存在既可造成全面腐蚀,也可能造成局部腐蚀。其中cl-和温度是影响c02腐蚀形态最重要的两个因素。排除其他因素的影响,根据温度的不同可将co2腐蚀分为三类:低温区(150℃),形成钝化膜抑制腐蚀的发生。 在本案例中,显然管道内部是处于低温区,因此加入只存在co2腐蚀的话,管道会发生全面腐蚀,不会导致管道在短时间内穿孔泄漏。 cl-在金属材料的腐蚀过程中是一个非常特殊、非常重要的例子,它是诱发点蚀和促进点蚀的重要因素。首先,当腐蚀产物膜的保护性较差时,溶液中的cl-会降低材料表面钝化膜形成的可能性或加速钝化膜的破坏,租金局部腐蚀损伤;其次,cl-能优先吸附于金属缺陷的
管线钢综述
管线钢综述 欧阳高凤 摘要:本文对管线钢的大概发展历程、成分冶金、显微组织、力学性能、轧制工艺、焊接性及焊接工艺进行了论述,从而能够了解管线钢的发展,为课题研究打下基础。 关键词:管线钢成分显微组织力学性能生产工艺焊接工艺发展 1 管线钢的大概发展历程 半个多世纪以来,随着石油和天然气的开发和需求量的增加,从而带动了管线钢的发展。由于管道运输具有经济、方便、安全等特点,进入二十一世纪以来,管线钢呈现蓬勃发展的趋势。我国管线钢的应用和起步较晚,过去已铺设的油、气管线大部分采用Q235和16Mn钢。我国开始按照API标准研制X60、X65管线钢,并成功地与进口钢管一起用于管线铺设。90年代初宝钢、武钢又相继开发了高强高韧性的X70管线钢,随后成功研制了X80管线钢,X70和X80管线钢已大量应用于油气管道运输中。近几年开发的高强韧的X100和X120管线钢还处在试验阶段,应用方面还比较少。 在我国,石油、天然气的运输基本上已经实现了管道运输。但是与世界上工业发达国家相比,国内的管道运输在质量上和数量上都存在很大差距。中国虽然为世界的主要石油出产国之一,但输油输气的管道不足世界管线总长度的百分之一,而且普遍存在输送压力低、管径小的缺点。随着我国油气资源的进一步开发利用,西气东输的工程实施,油气管线向长距离、大口径发展是必然趋势。下面从管线钢的冶金成分、显微组织、力学性能、生产工艺及焊接工艺等方面,进一步较详细的介绍管线钢的发展。 2 管线钢的冶金成分的发展 管线钢和其他的微合金钢一样,都是在传统的C-Mn钢的基础上加上合金元素。合金元素主要以Nb、Ti、V或少量的Mo、Cu、Ni、Cr及B为主,以这些合金元素来对管线钢进行合金设计,以达到不同的强度等级及性能要求。 管线钢的冶金成分的发展大致经历三个阶段。第一阶段为1950年以前,是以C-Mn和C-Mn-Si钢为主的普通碳钢,强度级别在X52以下。第二阶段为1950-1972年,在C-Mn钢的基础上引入微量的Nb、Ti、V,通过相应的热轧和轧后处理工艺,提高了钢的综合性能,生产出X60及X65级别的钢。第三阶段为1972年至今,这一阶段合金化的发展特点为微合金的多元化,相继又加入少量的Mo、Cu、Ni、Cr及B,结合控轧控冷的新工艺,生产出综合性能优异的管线钢,主要以X70和X80管线钢为主,X100和X120管线钢在试验研究阶段。 下面具体论述以下管线钢中这些合金元素或微合金元素的作用及添加量。2.1 碳 碳是最传统的合金元素、强化元素,而且也是最经济的元素,但它对钢的可焊性影响很大。碳是影响焊接性能最敏感的一个元素,所以20多年来管线钢的碳含量是逐步趋向于低碳或超低碳方向发展。而且随着含碳量的增加,韧性下降,偏析加剧,抗HIC和SSC的能力下降。因此,随着管线钢级别的提高,碳含量应逐渐降低。管线钢的含碳量从开始的1.0%左右逐步降低,最低可达到0.01%。
石油管线钢市场分析
石油管线钢市场分析 一、概况 1、简介 石油管线钢主要指用于制造输送石油的大口径焊接钢管用热轧卷板或宽厚板。国际多采用美国石油协会规范(API5L),通用为X系列,级别越高表示其强度及抗压性越大,如X42、X46为低强度管线钢,X52、X56为中强度管线钢,X60、X65、X70为高强度管线钢,X80、X100、X110为超高强度管线钢。不过管线钢强度级别的提高不是依靠C、Mn的提高来实现的,而是依靠轧制时的控轧控冷来实现的,通过控轧控冷得到超细晶粒的钢,强度级别高的钢种,需要添加微量元素,如Nb、V、B、Ti、Mo等,目前管线钢已成为低合金高强度和微合金钢领域内富有活力的一个重要分支。 石油输送管线管多由石油管线钢经过深加工(压力加工、焊接、热处理、机加工、表面处理、无损检测等)而成,一般板卷用于生产直缝电阻焊管(ERW)或埋弧螺旋焊管(SSAW),中厚板制成厚壁直缝焊管(LSAW)。用无缝钢管作为输送油管的数量相对较少。 图 1 输油管线用(钢)管 目前我国石油输送管线钢屈服强度多为306—450MPa(约相当于X52~X65),但随着石油需求量的不断增加,管道的输送压力和管径也不断地增大以增加其输送效率,考虑到管道的结构稳定性和安全性,还需增加管壁厚度和进步管材的强度,因此用作石油输送管的管线钢都向着厚规格和高强度方向发展。
2、使用标准 目前在我国使用的油气输送管线(钢)管的主要技术标准有API SPEC 5L、GB/T 9711、ISO 3183。除对管线钢化学成分、冶金质量、力学性能、残余应力、可焊性等有严格的要求外,对成品的几何形状和尺寸例如外径、内径、壁厚、圆度、直度等结构完整性也都有要求。 表 1 输油管线(钢)管使用标准 上大多数石油公司都习惯采用API SPEC 5L规范作为管线钢管采购的基础规范,国内1985年才开始按API标准生产。不过API SPEC 5L是一个通用标准,技术要求显得比较松,而世界各地地理、气候等自然条件差别很大,输送介质的性质也不尽相同,因此,很多石油公司将API SPEC 5L视为一个基础标准,在该标准基础上,根据当地实际情况或管线的具体要求,制订质量技术补充技术规范(技术条件)。 (2)ISO 3183—l(—2、—3)(石油天然气工业输送钢管交货技术条件第一部分:A级钢管/第二部分:B级钢管/第三部分:C级钢管)是国际标准化组织制定的关于油气输送钢管交货条件的标准,根据钢管不同的服役条件,分成A、B、C三个级别。 (3)GB/T 9711.1(一2)是中国标准化委员会管材专标委等同采用IS03183—l(—2)标准制定的石油工业用输送钢管交货技术条件。对钢管的化学成分、力学性能、止裂韧性、焊接性能等提出要求。 (4)DNV OS—F101(海底管线系统)是挪威船级社专门针对海底管线而制定的规范。涉及内容很广泛,包括管线设计、材料、制造、安装、检测、运行、维护等各方面。单就对钢管的技术要求,通常比API 5L要严格。
常用耐热钢的焊接工艺
常用耐热钢的焊接工艺 耐热钢是指钢再高温条件下既具有热稳定性,又具有热强性的 钢材。热稳定性是指钢材在高温条件下能保持化学稳定性(耐腐蚀、 不氧化)。热强性是指钢材在高温条件下具有足够的强度。其中耐热 性能主要通过铬、钼、钒、钛、铌等合金元素来保证,因此在焊接材 料的选择上应根据母材的合金元素含量来确定。耐热钢在石油石化工业装置施工中应用较为广泛,我们能够经常接触到的多为合金含量较 低的珠光体耐热钢,如15CrMo,1Cr5Mo等。 1铬钼耐热钢的焊接性 铬和钼是珠光体耐热钢的主要合金元素,显著提高金属的高温强度和高温抗氧化性,但它们使金属的焊接性能变差,在焊缝和热影响区具有淬应倾向,焊后在空气中冷却易产生硬而脆的马氏体组织,不仅影响焊接接头的机械性能,而且产生很大的内应力,从而产生冷裂倾向。 因此耐热钢焊接时的主要问题是裂纹,而形成裂纹的三要素是: 组织、应力和焊缝中的含氢量,因此制定合理的焊接工艺尤为重 要。 2珠光体耐热钢焊接工艺 2.1坡口 坡口的加工通常用火焰或者等离子切割工艺,必要时切割也要预热,打磨干净后做PT检验,去除坡口上的裂纹。通常选用V型坡口, 坡口角度为60°,从防止裂纹的角度考虑,坡口角度大些有利,但
是增加了焊接量,同时将坡口及内处两侧打磨干净,去除油污、铁锈及水份等污物(去氢、防止气孔)。 2.2组对 要求不能强制组对,防止产生内应力,由于铬钼耐热钢裂纹倾 向较大,故在焊接时焊缝的拘束度不能过大,以免造成过大的刚度,特别在厚板焊接时,妨碍焊缝自由收缩的拉筋、夹具和卡具等应尽量避免使用。 2.3焊接方法的选用 目前,我们石油石化安装单位管线焊接常用的焊接方法是钨极氩弧焊打底,焊条电弧焊填充盖面,其它焊接方法还有熔化极惰性气体保护焊(MIG焊)、CO2气体保护焊、电渣焊和埋弧自动焊等。 2.4焊接材料的选择 选配焊接材料的原则,焊缝金属的合金成分与强度性能基本上要与母材相应指标一致或者应达到产品技术条件提出的最低性能指标。而且为了降低氢含量应先用低氢型碱性焊条,焊条或者焊剂应按规定工艺烘干,随用随取,要装在焊条保温桶中随用随取,焊条再保温桶内不得超过4个小时,否则应重新烘干,烘干次数不得超过三次,这在具体施工过程中都有详细的规定。铬钼耐热钢手弧焊时,也可选用奥氏体不锈钢焊条,如A307焊条,但焊前仍需要预热,这种方法适用于焊件焊后不能热处理的情况。 耐热钢焊材选用表如下所示:
国内管线钢标准应用现状分析
收稿日期:2005-11-10 作者简介:潘丽梅(1977~),女,助理工程师,从事板带钢生产技术研究工作。 国内管线钢标准应用现状分析 潘丽梅 谢艳峰 (首钢技术研究院 北京 100041) (冶金工业信息标准研究院 北京 100730) 吴建伟 (中国标准出版社秦皇岛标准资料发行所 河北秦皇岛 066001) 摘 要:简要介绍了国内管线钢的组织分类及其特性要求,并对国内管线钢目前应用标准情况进行了分析研究。 关键词:管线钢;特性;标准应用 中图分类号:TG 335.7 文献标识码:B 文章编号:1003-0514(2005)06-0030-03 The actuality analyses about internal pipeline steel standard application PAN Li -mei (Shougang Research Institute of T echnology ,Beijing 100041,China ) XIE Y an -feng (China Metallurgical In formation &S tandardization Research Institute ,Beijing 100730,China ) W U Jian -wei (S tandards Press of China ,Qinhuangdao S tandards Fiter Issue Depantment ,Qinhuangdao 66001,China ) Abstract :Introduce the internal pipeline steel structure and characteristic ,and analysis the present situation about the inter 2nal pipeline steel standard. K ey w ords :pipeline steel ;characteristic ;standard application 在我国管道建设的不同阶段,管线钢的发展变化 非常迅速。20世纪50~70年代管线钢主要采用A3钢和16Mn 钢;70年代后期和80年代采用从日本进口的TS52K 钢(相当于X52级钢);90年代,管线钢主要采用的X52、X60、X65级热轧板卷大多数由宝钢和武钢生产供应。“八五”期间成功研制和开发了X52-X70级高韧性管线钢,并逐步得到广泛应用。西气东输工程采用了X70级管线钢。目前针对X80高钢级管材的研究和应用,石油部门与冶金部门联合开展了10余项国家基础攻关、应用基础研究和技术开发项目,其中包括国家“973”项目“高强度管线钢的重大工艺基础研究”,中油集团技术开发项目“X80管线钢管的开发与应用”,“X80管线钢的焊接及高韧性焊材选择”等等。本文针对目前国内管线钢标准应用现状 进行了系统研究。 1 管线钢的组织分类及其特性 随着合金设计、冶炼水平和轧制工艺的发展,具 有不同特性,适用于多种条件的管线钢已经生产,它应用了微合金钢发展的一切成果。铁素体-珠光体组织为第一代微合金管线钢,强度级别X42-X70;针状铁素体管线钢为第二代微合金管线钢,强度级别范围可覆盖X60-X90。其中管线钢的组织结构是决定其使用性能和安全服役的内部根据。目前,按照组织形态归类,管线钢具有以下3种典型的类型:1.1 铁素体-珠光体钢和少珠光体钢 60年代后期在国外发展起来的第一代管线系列钢(X52-X70强度级),称为铁素体-珠光体管线钢。 03冶金标准化与质量 第43卷
管线钢综述
综述 管线钢指用于输送石油、天然气等的大口径焊接钢管用热轧卷板或宽厚板。管线钢在使用过程中,除要求具有较高的耐压强度外,还要求具有较高的低温韧性和优良的焊接性能。随着石油、天然气消费量的增长,其输送的重要性显越发突出,尤其是长距离输送。而提高输送效率,提高输送的经济效益就要通过加大输送管道口径,提高输送压力来解决。从而提高了对高级别、高性能管线钢的需求。 国外高级别管线钢呈现强劲的发展趋势,从20世纪70年代初期X65管线钢开始投入使用,80年代X70级管线钢逐渐被引入工程建设,1985年API标准中增加了X80钢级,随后X80开始部分在一些管线工程中使用,并很快就投入到X100和X120管线钢的开发试制工作。有关X100最早的研究报告发表于1988年,通过大量工作已形成很好的技术体系。高级别管线钢概述我国管道建设正处于大力发展阶段,因此管线钢的发展也非常迅速。20世纪50~70年代管线钢主要采用A3钢和16Mn钢;70年代后期和80年代采用从日本进口的TS52K钢(相当于X52级钢);90年代,管线钢主要采用的X52、X60、X65级热轧板卷主要由宝钢和武钢生产供应。“八五”期间成功研制和开发了X52~X70级高韧性管线钢,并逐步得到广泛应用。西气东输工程采用了X70级管线钢并逐渐向X80过度。国内管线钢生产技术现状分析由于市场要求单管输气量不断提高。我国早期四川、西北地区的天然气管道采用X52及以下钢级、426mm以下管径的管线钢管,设计年输气量在10亿m3/a以下;陕京一线第一次采用了X60钢级、
D660mm管线钢管设计年输量提高到33亿m3/a;西气东输一线采用X70钢级、D1016mm管线钢管,设计年输量提高到170亿m3/a;最近建设的西气东输二线管道,采用X80钢级、D1219 mm管线钢管,设计年输量提高到300亿m3/a。 这种单管输气量不断提高的趋势仍在持续。当前国际上新一轮巨型天然气长输管道,单管输气量将达到450亿-500亿m3/a的水平。干线一般采用X80钢级,具有输送距离长、采用更高工作压力和大管径输送的特点。 一个具有代表性的项目是正在建设的俄罗斯巴甫年科沃-乌恰天然气管道。管线长度1100km,采用1420mm管径和K65(类似于X80)钢级,输送压力11.8MPa,单管设计输气量约500亿m3/a,计划于2012年第三季度进行系统调试。 另一个有代表性的项目是拟在北美建设的阿拉斯加北坡天然气外输管道,管道的输送能力约465亿m3/a,管线长度2737km,采用1219mm管径和X80钢级,将阿拉斯加北坡丰富的天然气资源输送到加拿大和北美市场。 我国也已在规划研究未来多条西气东输管道(西三线~西八线)的方案。包括将单管输气量提高到400亿~500亿m3/a的多种方案都在研究之中。 由于西气东输二线采用的X80钢级、管径1219mm,12MPa工作压力的方案只能达到300亿m3/a的输气能力,要将输气能力进一步提高到400亿-500亿m3/a,只能进一步提高输送压力和管径。
常用焊接方法—焊接工艺
常用焊接方法——焊接工艺 我公司是生产自动焊接设备的大型厂家。作为公司员工,就更应该了解常用焊接方法及焊接工艺。结合设备调试,这里将常用的埋弧焊、气体保护焊、钨极氩弧焊作为简要的讲述,以供有关人员参考。 一、埋弧焊 电弧在焊剂层下燃烧进行焊接的方法称为埋弧焊。主要优点:劳动条件好,节省焊接材料和电能,焊缝质量好,生产效率高等。但不适合薄板焊接。(当焊接电流小于100A时,电弧稳定性差,目前板厚小于1mm的薄板还无法采用埋弧焊)只限于水平或倾斜度不大的位置施焊。 埋弧焊是高效焊接常用方法之一。主要用于:焊接各种钢板结构。焊接碳素结构钢、低合金结构钢、不锈钢、耐热钢和复合材料以及堆焊耐磨、耐蚀合金等。 焊接工艺参数对焊接质量影响较大的有:焊接电流、电弧电压、焊接速度、焊丝直径与伸出长度、焊丝倾角、装配间隙与坡口大小等。此外焊剂层厚度及粒度对焊接质量也有影响。下面分别讲述它们对焊接质量的影响: 1.焊接电流: 焊接电流是决定熔深的主要因素。在一定范围内,焊接电流增加,焊缝的熔深和余高都增加。而焊缝的宽度增加不大。增大焊接电流能提高生产率,但在一定的焊接速度下,焊接电流过大会使热影响区过大,并产生焊瘤及焊件被烧穿等缺陷。若焊接电流过小,测熔深不足,
熔合不好、未焊透和夹渣,并使焊缝成形变坏。 2.电弧电压: 电弧电压是决定熔宽的主要因素。电弧电压增加时,弧长增加,熔深减小,焊缝宽度变宽,余高减小,电弧电压过大,溶剂熔化量增加,电弧不稳,严重时会产生咬边和气孔等。 3.焊接速度: 焊接速度增加,母材熔合比较小。焊接速度过高时,会产生咬边,未焊透,电弧偏吹和气孔等缺陷,焊缝余高大而窄成形不好。 4.焊丝直径与伸出长度: 当焊接电流不变时,减小焊丝直径,电流密度增加,熔深增大,成形系数减小。焊丝伸出长度增加时,熔深速度和余高都增加。 5.焊丝倾角: 焊丝前倾,焊缝成形系数增加,熔深变浅,焊缝宽度增加。焊丝后倾,熔深与余高增,。熔宽明显减小,焊缝成形不变。 6.装配间隙与坡口: 在其他工艺参数不变的条件下,装配间隙与坡口角度增大时,熔合比与余高减小,熔深增大,焊缝厚度基本保持不变。 7、焊机层厚度与粒度: 焊剂层太薄时,容易露弧,电弧保护不好,容易产生气孔或裂纹。焊剂层太厚,焊缝变窄,成形不好。 一般情况下,焊剂粒度对焊缝成形影响不大,但采用小直径焊丝焊薄板时,焊剂粒度对焊缝成形就有影响。若焊剂颗粒太大,电弧不
国内外海泥对管线钢腐蚀行为的研究现状及展望
国内外海泥对管线钢腐蚀行为的研究现状及展望 点击次数:4 发表时间:2012-12-4 16:24:49 所属分类:工作学习近年来,国内外对陆地土壤的腐蚀性开展了多种研究:从单项指标(土壤电阻率、含水量、含盐量、氧化还原电位)发展到多项综合指标(德国DVGV标准、美国ANSI标准等),提出了多种数学模型来评价和预测土壤的腐蚀性,如模式识别方法、模糊聚类分析方法、模糊灰色理论、人工神经网络方法等。 海底沉积物是一种特殊的土壤,对其腐蚀性进行研究对预防海底设施灾害性腐蚀破坏的发生具有战略性意义。 1、海泥腐蚀的研究现状 国外对海底沉积物腐蚀性的研究起步较早:20世纪80年代,King利用英国北海有关水文、地质因子资料,通过因子加权分析对其海底沉积物腐蚀性进行了区域性评估,并绘制了北海油田的海底沉积物定性腐蚀图;就钢铁在表层沉积物中腐蚀速率、SRB(硫酸盐还原菌)对腐蚀的影响进行研究发现,在SRB大量繁殖时,钢铁腐蚀速率可增加6~7倍,甚至15倍以上。 随着中国海洋石油事业的发展,有关大陆架海域海底沉积物腐蚀性的调查、评价以及相关结论的报道相继出现。
采用因子加权法对辽东湾海底沉积物的腐蚀性进行了评价与区划,绘制了辽东湾表层沉积物腐蚀性图谱。针对北部湾石油开发区海底沉积物腐蚀环境提出了具有定量性质的海底沉积物腐蚀性的二元评价法,并绘制了北部湾海域的腐蚀性图谱,还指出海泥类型是影响海泥腐蚀性的主要因素之一,与失重试验获得的钢腐蚀数据有明显的对应关系。通过多变量统计分析方法对南海珠江口东海海底沉积物腐蚀性进行了评价与区划。 对在海泥中的腐蚀产物(锈层)进行X射线衍射和穆斯堡尔图谱分析认为:海泥腐蚀初期氧的扩散作用对腐蚀速度影响不大,当有锈层存在时,氧的扩散控制作用明显增大;碳钢及低合金钢在海泥中的锈层相组成不同于在海水中形成的锈层,在海泥中只有一层锈,并粘结有海泥,碳钢的海泥锈层中α-FeOOH的含量明显少于海水锈层中的含量,而低合金钢的海泥锈层中几乎没有α-FeOOH的存在。 管线钢在海沙(不含SRB)和海泥(含有SRB)中出现了电偶效应,断电路电偶对电位差由正值变为负值,即随着时间的延长,电偶的极性发生逆转;海泥中初期电偶对阴极转变为电偶对阳极而加速腐蚀;海沙中初期电偶对阳极转变为电偶对阴极而受到一定程度的保护;这主要是由于土质充气不同而产生的氧浓差电池引起的。 利用电化学阻抗法研究了平台钢、管线钢在辽东湾海泥中的初期腐蚀
管线钢成分及标准
一、管线钢概述 1、简介 管线要求含碳量较低,而靠提高锰含量,添加铌、钛、钒、钼等微量元素来保证其强度。对于管线钢,除了要求强度、塑性指标外,对于韧性指标的要求是它的一个突出特点,包括了钢板的冲击功、冲击转变温度和焊接热影响区与焊接金属的韧性指标。此外,还有应变时效、可焊性、应力腐蚀等指标要求。 2、管线钢类型 管线钢可分为高寒、高硫地区和海底铺设三类。从油气输送管的发展趋势、管线铺设条件、主要失效形式和失效原因综合评价看,不仅要求管线钢有良好的力学性能(厚壁、高强度、高韧性、耐磨性),还应具有大口径、可焊接性、耐严寒低温性、耐腐蚀性)、抗海水和HIC、SSCC性能等。这些工作环境恶劣的管线,线路长,又不易维护,(CO 2 对质量要求都很严格。 二、技术要求 1、性能要求 现代管线钢属于低碳或超低碳的微合金化钢,是高技术含量和高附加值的产品,管线钢生产几乎应用了冶金领域近20多年来的一切工艺技术新成就。目前管线工程的发展趋势是大管径、高压输送、高冷和腐蚀的服役环境、海底管线的厚壁化,因此目前对管线钢的性能要求主要有以下几方面: (1) 高强度。管线钢的强度指标主要有抗拉强度和屈服强度;在要求高强度的同时,对管线钢的屈强比(屈服强度与抗拉强度)也提出了要求,一般要求在0.85-0.93的范围内。 (2)高冲击韧性。管线钢要求材料应具有足够高的冲击韧性(起裂、止裂韧性)。对于母材,当材料的韧性值满足止裂要求时,其韧性一般也能满足防止起裂的要求。 (3)低的韧脆转变温度。严酷地域、气候条件要求管线钢应具有足够低的韧脆转变温度。DWTT(落锤撕裂试验)的剪切面积已经成为防止管道脆性破坏的主要控制指标。一般规范要求在最低运行温度下试样断口剪切面积≥极85%。 (4)优良的抗氢致开裂(HIC)和抗硫化物应力腐蚀开裂(SSCC)性能。 (5)良好的焊接性能。钢材良好的焊接性对保证管道的整体性和焊接质量至关重要。 管线钢的发展最显着的特征之一就是不断降低钢中的C含量,随着C含量的降低,
15CrMoG耐热钢管道焊接施工工法
15CrMoG耐热钢管道焊接施工工法 1 前言 耐热钢中以珠光体铬钼耐热钢应用最广,因为这类钢一般适用于 350-550℃之间,同时,这类钢的合金元素含量相对较少,一般都属于低合金钢的范畴,因为合金钢是在碳钢中加入少量的合金元素,钢的性能就发生了变化,就得到了碳钢所没有的性能,即耐高温、抗氧化、抗蠕化和良好的持久强度,由于合金元素小于3.5%,所以称作低合金,简称合金钢。它的耐热性和强度均超过不锈钢,但是价格比不锈钢便宜得多,适用于在各种高温高压条件下工作的介质管道。例如在攀钢煤化工厂外线工艺管道施工项目中,该工程管道φ273×11共1200米,其设计温度为480℃,设计压力为5.5Mpa,并且管道材质为15CrMoG耐热合金钢,这类高温高压的特殊材质管道以前我公司未施工过,所以还没有完善和成熟的施工工艺 及经验可以借鉴。由于合金钢的化学成分和性能与碳素钢、不锈钢存在较大的区别,所以施工15CrMoG耐热合金钢的焊接工艺及步骤都比碳素钢、不锈钢要求更高,也更严格和复杂。因此掌握此项新技术、新工艺中所有技术参数是具有较大的技术难题。 为了保证焊接质量,公司成立了专题攻关技术小组,开展科技创新,取得了“15CrMoG耐热钢管道焊接技术”这一新成果,并且该技术于2006年通过攀钢冶金技术有限公司(原攀冶建公司)科技质量部组织的科技成果鉴定,获公司科技进步一等奖;在2007年4月全国冶金施工系统QC成果发布会上获得二等奖。该技术填补了我公司在15CrMoG耐热合金钢焊接
技术方面的空白,优化了生产工艺,提高了劳动生产率,保证了焊接质量,为公司创造了良好的社会效益和经济效益。 2 工法特点 2.1由于15CrMoG钢中含有较高含量的Cr、C和其它合金元素,钢材的淬硬倾向较明显,焊接接头淬硬倾向大,可能出现冷裂纹,因此15CrMoG 钢焊接时,焊接材料的选择和严格的工艺措施,对于防止焊缝产生裂纹,保证管道使用性能至关重要。所以15CrMoG耐热合金钢与碳素钢、不锈钢等管道相比不管从施工工艺还是施工时所使用的工机具要求都更高,也更复杂。因此通过本工法的实施,使我公司的管道施工综合能力得到很大的提高,填补了我公司在15CrMoG耐热合金钢安装技术方面的空白,优化了生产工艺,提高了劳动生产率,保证了焊接质量,为公司创造良好的社会效益。更为今后公司施工同类管道奠定了坚实的基础,提高了 1 市场竞争能力。 2.2本工法贯彻实施后,使我公司得以熟练掌握15CrMoG材质高温高压蒸汽管道的打磨、预热、焊接、层间温度、焊后缓冷、焊缝及管道的热处理等所有工序及每个工序的具体要求及相关参数。为今后公司施工同类合金管道将起到较大的指导作用。 3 适用范围 适用于管道介质在10MPa、550℃以下的15CrMoG材质或同类型材质的高温、高压蒸汽管道或其它介质管道的焊接。 4工艺原理 为了保证耐热钢具有较好的高温强度和高温抗氧化性能,要加入一定
管线钢知识
管线钢知识 石油和天然气的需求迅速增长,2011-2015年世界范围内管道建设的工程投资每年近400亿美元。 西气东输二线管道以高强度X80为管材,管径1219mm,压力12MPa,主干线全长4895km。2010年底的统计资料显示,我国已建立原油管道1.9*104km,天然气管道3.3*104km,成品油管道1.6*104km,油气管道总里程已达6.8*104km,2020年有望达到20*104km。同时,与我国的能源需求和先进国家的管道水平相比,我国管道建设还有巨大的需求和潜力。 一、管道工程面临的挑战与管线钢发展方向 ●管道的大管径、高压输送与高强度管线钢 由建立在流体力学基础上的设计计算可知,原油管道单位时间输送量与输送压力梯度的平方根成正比,与略大于管道直径的平方成正比。加大管道直径,提高管道工作压力是提高管道输送量的有力措施和油气管道的基本发展方向。 目前认为,输油管道合适的最大管径为1220mm,输气管道合适的最大管径为1420mm。在输送压力方面,提高压力的追求仍无止境。20世纪50-60年代的最高输送压力为6.3MPa(X52),70-80年代的最高输送压力为10MPa(X60-65),90年代后的最高输送压力达14MPa(X70-80)。近年来,国外一些新建天然气管道压力一般为10-15MPa,一些管道压力已超过20MPa(X100-X120)。 由管道设计准则可知,管道工程的大口径、高压输送这一目标可以通过增加钢管壁厚和钢管强度来实现。然而,提高管线钢的强度才是一种理想的选择。这是因为高强度管线钢的采用不仅可减少钢管壁厚和重量,节约钢材成本,而且由于钢管管径和壁厚的减少,可以产生许多连带的经济效益。据统计,在大口径管道工程中,25%-40%的工程成本与材料有关。一般认为,管线钢每提高一个级别,可使管道造价成本降低5%-15%。 ●管道的低温环境与高韧性管线钢 随着管道工程的发展,对管线钢韧性的技术要求日益提高,韧性已成为管线钢最重要的性能指标。为获取高韧性管线钢,可通过多种韧化机制和韧化方法,其中低碳或超低碳、纯净或超纯净、均匀或超均匀、细晶粒或超细晶粒以及针状铁素体为代表的组织形态是高韧性管线钢最重要的特征。 超纯净管线钢:S≤0.0005%、P≤0.002%、N≤0.002%、O≤0.001%和H≤0.0001%; 超细晶粒管线钢:通过严格控制控轧、控冷条件,目前可获得这种有效晶粒 大都在尺寸达到1-2um,因而赋予了管线钢优良的韧性。现代管线钢的A kv 可高达200-300J以上,50%FATT可达-45℃以下。经过精心控制的管线钢,其A kv 400-500J以上,DWTT的85%FATT可降至-60℃以下。 ●管道的大位移环境与大变形管线钢 所谓大变形管线钢是一种适应大位移服役环境的,在拉伸、压缩和弯曲载荷下具有较高极限应变能力和延性断裂抗力的管道材料。这种管线钢既可满足管道高压、大流量输送的强度要求和满足防止裂纹起裂和止裂的韧性要求,同时又具有防止管道因大变形而引起的屈曲、失稳和延性断裂的极限变形能力,因此大变形管线钢是管道工程发展的迫切需要,也是传统油、气输送管道材料的一种重要补充和发展。 大变形管线钢的主要性能特征是在保证高强韧性的同时,具有低的屈强比
耐热钢焊接焊条选用及说明
耐热钢焊接焊条选用及说明 在高温下工作的钢叫做耐热钢,耐热钢应具备高温化学稳定性和高温强度,耐热钢按显微组织可分为珠光体耐热钢、铁素体耐热钢、马氏体耐热钢和奥氏体耐热钢四类;珠光体耐热钢通常热强钢,另有专篇,不再叙述,这里只讲铁素体耐热钢、马氏体耐热钢和奥氏体耐热钢。 一般来说,钢中含Cr达到5%,在600℃下具备了抗氧化能力,当Cr达到12%时,抗氧化能力可达800℃,当Cr达到20%时,抗氧化能力可达950℃,当Cr达到25%时,在1050℃高温下耐热钢表面不起氧化皮,高温化学稳定性非常强;铬金属是耐热钢中最主要的合金元素,所以耐热钢含铬量大都在12%以上。 相对而言,铁素体耐热钢和马氏体耐热钢高温强度低且塑韧性不好,耐热性能不如奥氏体耐热钢,奥氏体耐热钢与奥氏体不锈钢相比,含碳量高一些,有些钢种既是不锈钢又是耐热钢。 本文依据GB/T 4238-2015《耐热钢钢板与钢带》和GB/T 983-2012《不锈钢焊条》标准,选出14种代表性耐热钢材料及其适用的12种焊条,基本涵盖适用温度范围,其余耐热钢焊接时焊条选择也可以参照使用。 一、焊条选用原则 1、耐热性对等 焊缝与母材都在同一个温度下服役,若焊缝耐热性差就会影响整体功能,若焊缝耐热性过剩则会造成浪费,只有两者对等才是最适宜的。 2、化学成分相近 为确保焊缝金属与母材具备相同的耐热性,焊条熔敷金属化学成份与母材应尽量相近;同时两者化学成份相近使得它们膨胀系数相近,避免了因膨胀系数不同在焊接接头处产生内应力。 3、保证抗裂性 对抗裂性差的耐热钢可以用化学成分差异化来选择焊条,防止冷裂纹,确保施工可焊性。如马氏体耐热钢、沉淀硬化耐热钢。
国内管线钢生产技术现状分析
3月5日 国内管线钢生产技术现状分析 我国管道建设正处于大力发展阶段,因此管线钢的发展也非常迅速。20世纪50~70年代管线钢主要采用A3钢和16Mn钢;70年代后期和80年代采用从日本进口的TS52K钢(相当于X52级钢);90年代,管线钢主要采用的X52、X60、X65级热轧板卷主要由宝钢和武钢生产供应。“八五”期间成功研制和开发了X52~X70级高韧性管线钢,并逐步得到广泛应用。西气东输工程采用了X70级管线钢。目前针对X80高钢级管材的研究和应用,石油部门与冶金部门联合开展了10余顶国家基础研究与攻关、应用基础研究和技术开发项目;其中包括国家“973”项目“高强度管线钢的重大工艺基础研究”,中油集团技术开发项目“X80管线钢管的开发与应用”、“X80管线钢的焊接及高韧性焊材选择”等等。本文针对目前国内管线钢生产技术要求及其标准应用现状进行了系统研究。 1、管线钢的组织分类及其特性 随着合金设计、冶炼水平和轧制工艺的发展,具有不同特性、适用于多种条件的管线钢已经生产,它应用了微合金钢发展的一切成果。铁素体-珠光体组织为第一代微合金管线钢,强度级别X42-X70;针状铁素体管线钢为第二代微合金管线钢,强度级别范围可覆盖X60-X90。其中管线钢的组织结构是决定其使用性能和安全服股的内部根据。目前,按照组织形态归类,管线钢具有以下3种典型的类型:(1)铁素体-珠光体钢和少珠光体钢 60年代后期在国外发展起来的第一代管线系列钢(X52-X70强度级),称为铁素体+珠光体管线钢。它以高纯净(S≤0.010%,N≤60ppm,N+O+P+S≤150ppm)和细晶粒(10~15μm)的铁素体+(5%~15%)珠光体为基体,综合使用微量碳(C 0.05%~0.10%),微量的铌,钒,钛 (Nb+V+Ti≤0.12%)。国产的X52-X65级管线钢为控轧C-Mn-Nb-Ti或C-Mn-Nb-Ti-V系列铁素体-珠光体型微合金钢。少珠光体管线钢的典型化学成分有Mn-Nb,Mn-V,Mn-Vb-V等。一般含碳量小于0.1%,铌、钒、钛的总含量小于0.10%,代表钢钟是60年代末的X56、X60和X65。这类钢突破了传统铁素体-珠光体钢热轧正火的生产工艺,进入了微合金化钢控轧的生产阶段。具有铁素体-珠光体和少珠光体的管线钢,通过采用微合金化和控制轧制等强化手段,在保证高韧性和良好焊接性的条件下,可将20mm的宽厚板提高到500~550MPa的极限水平。 (2)针状铁素体和超低碳贝氏体钢 典型成分为C-Mn-Nb-Mo,一般碳含量小于0.06%。为了把碳当量保持在较低水平上,强度在X70级以上的制管带钢必须采用贝氏体铁素体组织,钼合金化是获得这种组织最成功的技术。依靠成分调整,降碳、提锰和添加钼以及轧后采取较高的冷却强度,易形成这种贝氏体类型的铁素体组织,是X65-X80级高强度韧性管线钢的主要成分规范。针状铁素体钢通过微合金化和控制轧制,综合利用晶粒细化、微合金化元素的析出相与位错亚结构的强化效应,可使钢的屈服强度达到650MPa以上,-60℃的冲击韧性达80J。 针状铁素体管线钢是西气东输工程选用的管线钢种。这种钢从合金设计、冶炼工艺、轧制工艺到管材显微组织状态都与第一代的管线钢不同。该钢特征是进一步提高纯净度(C≤0.05%,S≤0.005%, P≤0.010%,N≤30ppm,P+S++N≤100ppm),使用钙处理硫化物,在连铸过程中采用电磁搅拌和动态软压下措施。在钢的基体中加入微量钼(0.2%~0.4%)以促使针状铁素体的形成,并用适量铜、镍、铬强化基体;在高温动态再结晶临界温度上下温度区间进行控制轧制,通过在线强制加速冷却,进一步细化晶粒度(平均3~8μm),使其铁素体基体的均匀化程度提高,位错密度增加。这种钢具有比铁素体- 珠光体型管线钢更好的焊接性能(Pcm≤0.20),其对脆性断裂,硫化氢或二氧化碳引起的阳极腐蚀(点蚀),应力腐蚀(SCC),硫化氢应力腐蚀断裂(SSC),氢诱发裂纹(HIC),延性断裂(DDF)六个方面的“抗力”要比其它钢种高得多。 超低碳贝氏体钢在成分设计上,选择上碳、锰、铌、钼、硼、钛的最佳配合,从而在较大冷却速度范围内部都形成完全的贝氏体组织。超低碳控轧贝氏体钢的屈服强度可望提高至700~800MPa,因而超低碳贝氏体钢被誉为21世纪的控轧钢。
焊接热输入对X100管线钢粗晶区组织及性能的影响
第31卷第3期2010年3月 焊 接 学 报 TRANSACTI ONS OF T HE C H I N A W ELDI NG I N STI TUTI ON Vo.l 31 No .3M arch 2010 收稿日期:2009-04-09 基金项目:国家自然科学基金资助项目(50874090) 焊接热输入对X100管线钢粗晶区组织及性能的影响 张骁勇1,2 , 高惠临2 , 庄传晶3 , 吉玲康 3 (1.西安建筑科技大学材料科学与工程学院,西安 710048;2.西安石油大学材料科学与工程学院,西安 710065; 3.中国石油天然气集团公司管材研究所,西安 710065)摘 要:采用热模拟技术、显微分析方法和力学性能测试等手段,对X100管线钢在不同焊接热输入下粗晶区的组织及性能的变化规律进行了研究.结果表明,随着焊接热输入的增加,X100管线钢的强韧性降低.当热输入为10kJ/c m 左右时,焊接粗晶热影响区的显微组织以贝氏体铁素体和粒状贝氏体为主,这种组织赋予材料以最佳的强韧性水平;当热输入为20kJ/c m 左右时,焊接粗晶热影响区的显微组织以粒状贝氏体和准多边形铁素体为主,材料有较好的强韧配合;而当热输入大于30kJ/c m 时,由于多边形铁素体增多,材料的强韧性降低.因此可将10~20kJ/c m 作为X 100管线钢的推荐热输入. 关键词:X100管线钢;焊接热输入;组织;性能中图分类号:TG 142.1 文献标识码:A 文章编号:0253-360X (2010)03-0029- 04 张骁勇 0 序 言 X100是超高强度管线钢中的一种典型钢种.采用X100作为高压、大流量天然气输送管线管材, 具有较大的经济效益.资料显示[1,2] ,在油气管道建设中,采用X80代替X70,可降低成本7%;采用X100代替X70,则可降低成本30%.所以X100管线钢的研究和开发,日益受到人们的关注.X100是一种新型的微合金化管线钢,在国内外的研究历史不长.在已有的文献中 [3-5] ,多限于管线钢钢板性 能的研究,对X100管线钢在焊接热过程中组织及 性能的特征及其变化规律却知之不多.焊接热影响区粗晶区是整个焊接接头中性能最为薄弱的区域,因此研究X100管线钢在不同焊接热输入条件下的粗晶区组织及性能的变化规律及其焊接脆化的特征,对掌握X100管线钢焊接冶金的基本规律和推动X100管线钢的工业应用具有重要的意义. 1 试验方法 试验用X100管线钢板厚度为14.3mm,化学成 分见表1,力学性能见表2,其基本金相组织为针状铁素体. 表1 X100的化学成分(质量分数,%) Tab l e 1 C hem i c a l composition o f X100p ipe li n e s t ee l C S i M n P S C r M o 0.050.252.000.0120.00320.330.33N i Nb V T i Cu A l Fe 0.46 0.055 0.007 0.022 0.20 0.046 余量 表2 X100的常规力学性能 Tab l e 2 Mechan ica l p roper ties o f X100p ipe li n e st ee l 屈服强度R e L /M Pa 抗拉强度R m /M Pa 断后伸长率A (%)屈强比R eL /R m 冲击吸收功A KV /J 730 805 20.5 0.91 191 采用热模拟试验获取X100管线钢在不同焊接热输入条件下粗晶热影响区(coarse gra i n hea t affect zone ,CGHAZ)的组织结构.热模拟试验在G leeble 1500型热模拟机上进行,热模拟参数如表3所示.其中热循环的几种t 8/5覆盖了石油、天然气输送钢管在制管焊接和野外施工焊接过程中所采用的不同焊接热输入下的冷却参数. 热模拟试样分别采用 10mm 65mm 和10.5mm 10.5mm 55mm 的初始试样,试样于板厚中部(沿板厚方向两面对称加工)横向截取.热模拟试验后再将试样加工 5mm 25mm 的标准比例拉伸试样和10mm 10mm 55mm 的标准Charpy 冲击试样,沿板厚方向开制V 形缺口.拉伸试验在
管线钢
管线钢 一、管线钢的概述 1、概念 管线钢主要用于石油、天然气的输送。制造石油天然气集输和长输管或煤炭、建材浆体输送管等用的中厚板和带卷称为管线用钢(LPS)。石油钢的强度一般要求达到600~700MPa;钢中O、S、P、N、C总含量不大于0.0092%;钢中脆性Al2O3夹杂和条状Mn夹杂为痕迹状态。 管线钢主要用于加工制造油气管线。油气管网是连接资源区和市场区的最便捷、最安全的通道,它的快速建设不仅将缓解铁路运输的压力,而且有利于保障油气市场的安全供给,有利于提高能源安全保障程度和能力。 2、管线钢类型 管线钢可分为高寒、高硫地区和海底铺设三类。从油气输送管的发展趋势、管线服役条件、主要失效形式和失效原因综合评价看,不仅要求管线钢有良好的力学性能,还应具有耐负温性、耐腐蚀性、抗海水和HSSCC性能等。这些工作环境恶劣的管线,线路长,又不易维护,对质量要求都很严格。 3、管线钢的消费和生产现状 (1)消费状况 为了把这些自然气输送到主要的消费区域,建设输送管线是必不可少的。目前“西气东输”项目已经建成,今后还将建设的主要管线有陕京二期、中俄自然气管线(东线、西线)、以及中亚或俄罗斯至上海自然气管线,终极与“西气东输”管线形成“两横、两纵”的自然气干线。 目前,原油、自然气管网已经具有相当规模,成品油输送管道相对较少,目前仅占全部输送量的40%,将来计划修建3万km,管径在Ф500mm左右,壁厚在10mm以下,以X65为主。未来10年,我国将建设5万km的油气管道,均匀每年需要展设近5000km,每年自然气管道需要钢材近400万t。 随着管道输送压力的不断进步,油气输送钢管也相应迅速向高钢级方向发展。在国际发达国家,20世纪60年代一般采用X52钢级,70年代普遍采用X60~X65钢级,近年来以X70为主,而国内城市管网以X52、X65为主。目前国内主干线输气管最大压力为10MPa,最大直径能够达到Ф1016~1219mm,以X65、X70应用为主,X80也有应用,但用量未几。随着国内输气管的延长和要求压力的进步,X70、X80将成为主流管线钢。 (2)管线管的生产情况 随着国内冶金技术装备水平的进步,我国能生产管线钢板卷的企业逐渐增多,但是能够生产X70及以上级别的钢厂仅有宝钢、武钢、鞍钢、舞钢、