不锈钢车削

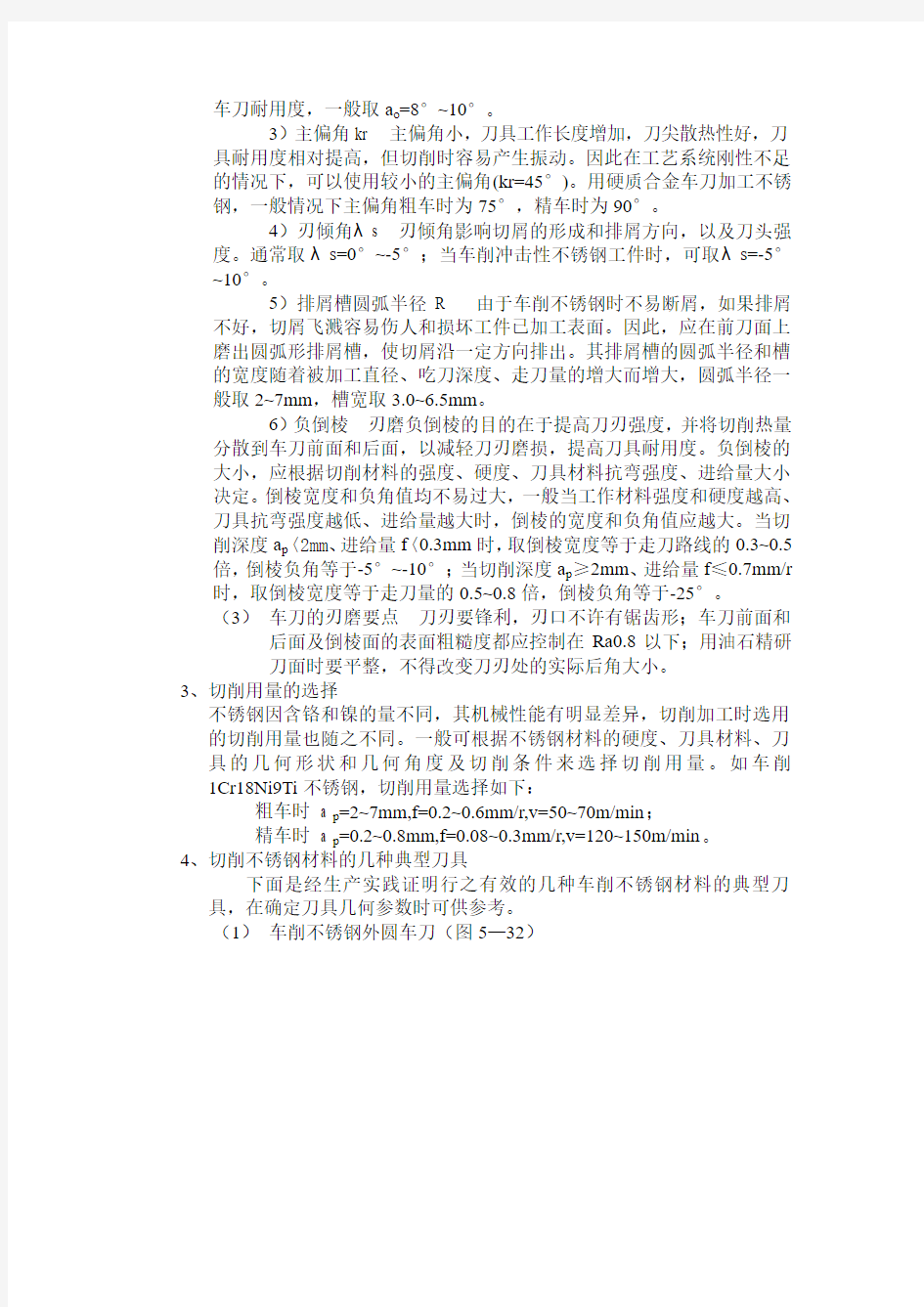
5~4 不锈钢材料的车削
一、教学要求
1、了解不锈钢材料的车削特性。
2、掌握车削不锈钢材料刀具的几何形状和刃磨要点。
3、合理选择车削不锈钢的切削用量。
二、相关工艺知识
1、不锈钢的车削特性
不锈钢按其化学成分可分为两类:即铬不锈钢和铬镍不锈钢。常用的铬
不锈钢,含铬量为12%、17%和27%等,其抗腐蚀性能随着含铬量的增
加而增加。常用的铬镍不锈钢含量17%~20%,含镍量8~11%,这种铬镍
不锈钢的抗腐蚀性能及机械性能都比铬不锈钢高。
由于不锈钢的韧性大、强度高、导热性差,因此在切削时热量难于扩散,致使刀具易于发热,降低了刀具的切削性能;在不锈钢的金属组织
中,由于有分散的碳化物杂质,车削时回产生较高的腐蚀性,因而使刀
具容易磨损;不锈钢有较高的粘附性,切削时易产生切削瘤,使加工表
面粗糙度加大,同时,切削瘤时大时小,时时生时灭,使切削力不断变
化,引起振动。
此外,不锈钢铸件和锻件毛坯有硬度较高的氧化皮以及具有较大的刚性和良好的刃磨质量。
2、车削不锈钢材料的刀具
(1)刀具材料常用的刀具材料有硬质合金和高速钢,两大类。在硬质合金材料中,YG6和YG8用于粗车、半精车及切断,其切削
速度v=50~70m/min,若充分冷却,可以提高刀具的耐用度,YT5、
YT15和YG6X用于半精车和精车,其切削速度v=120~150m/min,
当车削薄壁零件时,为减少热变形,要充分冷却;YW1和YW2
用于粗车和精车,切削速度可提高10%~20%,且刀具耐用度较高。
高速钢W12Cr4V4Mo和W2Mo9Cr4Vco8用于具有较高精度螺纹、
特形面及沟槽等的精车,其切削速度v≤25m/min,在车削时,使
用切削液进行冷却,以减少零件的表面粗糙度和刀具磨损;
W18Cr4V用于车削螺纹、特型面、沟槽及切断等,其切削速度
v=20m/min。
(2)刀具几何参数刀具切削部分的几何角度,对于不锈钢切削加工的生产率、刀具的耐用度、被加工表面的表面粗糙度、切削力以
及加工硬度等方面都有很大的影响。
1)前角r o前角过小时,切削力增大,振动增强,工件表面起波纹,切削不易排出,在切削温度较高的情况下,容易产生刀瘤;当前
角过大时,刀具强度降低,刀具磨损加快,而且易打刀。因此用硬质合
金车刀在车削不锈钢材料时,若工件为轧制锻坯,则可取r o=12°~20°;
若工件为铸件,则可取a o=10°~15°。
2)后角a o因不锈钢的弹性和塑性都比普通碳钢大,所以后角过小时,其切削表面与车刀后面接触面积增大,摩擦产生的高温区集中于
车刀后面,使车刀磨损加快,被加工表面的表面粗糙地增大。因此车刀
后角要比车削普通钢材的后角稍大,但过大时又会降低刀刃强度,影响
车刀耐用度,一般取a o=8°~10°。
3)主偏角kr 主偏角小,刀具工作长度增加,刀尖散热性好,刀具耐用度相对提高,但切削时容易产生振动。因此在工艺系统刚性不足的情况下,可以使用较小的主偏角(kr=45°)。用硬质合金车刀加工不锈钢,一般情况下主偏角粗车时为75°,精车时为90°。
4)刃倾角λs 刃倾角影响切屑的形成和排屑方向,以及刀头强度。通常取λs=0°~-5°;当车削冲击性不锈钢工件时,可取λs=-5°~10°。
5)排屑槽圆弧半径R 由于车削不锈钢时不易断屑,如果排屑不好,切屑飞溅容易伤人和损坏工件已加工表面。因此,应在前刀面上磨出圆弧形排屑槽,使切屑沿一定方向排出。其排屑槽的圆弧半径和槽的宽度随着被加工直径、吃刀深度、走刀量的增大而增大,圆弧半径一般取2~7mm,槽宽取3.0~6.5mm。
6)负倒棱刃磨负倒棱的目的在于提高刀刃强度,并将切削热量分散到车刀前面和后面,以减轻刀刃磨损,提高刀具耐用度。负倒棱的大小,应根据切削材料的强度、硬度、刀具材料抗弯强度、进给量大小决定。倒棱宽度和负角值均不易过大,一般当工作材料强度和硬度越高、刀具抗弯强度越低、进给量越大时,倒棱的宽度和负角值应越大。当切削深度a p〈2mm、进给量f〈0.3mm时,取倒棱宽度等于走刀路线的0.3~0.5倍,倒棱负角等于-5°~-10°;当切削深度a p≥2mm、进给量f≤0.7mm/r 时,取倒棱宽度等于走刀量的0.5~0.8倍,倒棱负角等于-25°。
(3)车刀的刃磨要点刀刃要锋利,刃口不许有锯齿形;车刀前面和后面及倒棱面的表面粗糙度都应控制在Ra0.8以下;用油石精研
刀面时要平整,不得改变刀刃处的实际后角大小。
3、切削用量的选择
不锈钢因含铬和镍的量不同,其机械性能有明显差异,切削加工时选用的切削用量也随之不同。一般可根据不锈钢材料的硬度、刀具材料、刀具的几何形状和几何角度及切削条件来选择切削用量。如车削1Cr18Ni9Ti不锈钢,切削用量选择如下:
粗车时 a p=2~7mm,f=0.2~0.6mm/r,v=50~70m/min;
精车时 a p=0.2~0.8mm,f=0.08~0.3mm/r,v=120~150m/min。
4、切削不锈钢材料的几种典型刀具
下面是经生产实践证明行之有效的几种车削不锈钢材料的典型刀具,在确定刀具几何参数时可供参考。
(1)车削不锈钢外圆车刀(图5—32)
①刀具特点
1)刀片材料为YW1、YW2,刀杆材料为45钢。
2)前角γo=20°,并具有(0.5~0.8)f负倒棱,刃倾角γs=-3°~-5°,增加了刀具强度,又减小了切屑变形。
3)主偏角kr=75°,kr`=5°,并以R50mm大圆弧圆滑接转,刀头强度好,具有抗冲击性能。
4)后角a o=10°,较大的后角,减少了刀具后刀面与工件之间的摩擦。
②使用条件
1)粗车时,切削速度Vc=60~80m/min,切削深度a p=3~7mm,进给量f=0.3~0.6mm/r.
2)精车时,切削速度Vc=100~150m/min,切削深度a p=0.5~1mm,进给量f=0.15~0.3mm/r。
(2)90°机夹不锈钢定前角外圆车刀。
①刀具特点
1)刀具材料可选用YW1、YG6,刀杆材料可选用45钢,调质HB235~250,断屑块材料选取YG8。
2)采用固定前角(γo=23°~25°),且前角较大,切削轻快。
3)刀具装有断屑块,其位置可任意调整,使切屑排出通畅,断屑呈“C”字形;刀片不需要磨出断屑槽,能增加刀片使用
寿命,节约刀片材料。
4)刀具几何参数:前角γo=23°~25°,后角a o=4°~6°。主偏角kr=90°;副偏角kr`=4°~6°。
②使用条件
1)工件材料为1Cr18Ni9Ti,调质HB137~190。
2)切削用量:切削速度Vc=60~80 m/min,进给量f=0.4~0.7mm/r,切削深度a p=5~10mm。
3)使用机床:CA6140普通车床。
4)切削液:硫化油或乳化液。
5)适用于粗车和半精车刚性较好的外圆。
(3)不锈钢切断刀之一(图5—41)
①刀具特点
1)刀片材料为YW1、YW2,刀杆材料为45钢。
2)前面磨有圆弧卷屑槽,前角大,排屑顺利。刀刃有半径R0.5的消振槽,不仅能消除振动,而且保证了零件的平直度。
②使用条件
1)切削用量:切削速度Vc=80~100m/min,进给量f=0.25~0.3mm/r,切削深度a p=4mm。
2)适用于加工铬镍不锈钢,刀具寿命可提高6~8倍。
(4)不锈钢切断刀
①刀具特点
1)刀片材料为YW1、YW2,刀杆材料为45钢。
2)在前面磨有R1.5~2mm的圆弧槽,具有消振作用,切削稳定,刀刃不易偏移,排屑顺利,断屑好,不易崩刃,可提高刀具
寿命2~3倍。
②使用条件
1)切削用量:切削速度Vc=90~120m/min,进给量f=0.1~0.3mm/r,切削深度a p=5mm。
2)适于1Cr18Ni9Ti不锈钢套类零件φ500~700直径的切断。内外径的差值不大于60mm。
不锈钢的切削加工
1 什么是不锈钢? 通常,人们把含铬量大于12%或含镍量大于8%的合金钢叫不锈钢。这种钢在大气中或在腐蚀性介质中具有一定的耐蚀能力,并在较高温度(>450℃)下具有较高的强度。含铬量达16%~18%的钢称为耐酸钢或耐酸不锈钢,习惯上通称为不锈钢。 钢中含铬量达12%以上时,在与氧化性介质接触中,由于电化学作用,表面很快形成一层富铬的钝化膜,保护金属内部不受腐蚀;但在非氧化性腐蚀介质中,仍不易形成坚固的钝化膜。为了提高钢的耐蚀能力,通常增大铬的比例或添加可以促进钝化的合金元素,加Ni、Mo、Mn、Cu、Nb、Ti、W、Co等,这些元素不仅提高了钢的抗腐蚀能力,同时改变了钢的内部组织以及物理力学性能。这些合金元素在钢中的含量不同,对不锈钢的性能产生不同的影响,有的有磁性,有的无磁性,有的能够进行热处理,有的则不能热处理。 由于不锈钢所具有的上述特性,越来越广泛地应用于航空、航天、化工、石油、建筑和食品等工业部门及日常生活中。所含的合金元素对切削加工性影响很大,有的甚至很难切削。 2 不锈钢可分为哪几类? 不锈钢按其成分,可分为以铬为主的铬不锈钢和以铬、镍为主的铬镍不锈钢两大类。 工业上常用的不锈钢一般按金相组织分类,可分为以下五大类: 1.马氏体不锈钢:含铬量12%~18%,含碳量0.1%~0.5%(有时达1%),常见的有1Cr13、2 Cr13、3Cr13、4Cr13、1Cr17Ni2、9Cr18、9Cr18MoV、30Cr13Mo等。 2.铁素体不锈钢:含铬量12%~30%,常见的有0Cr13、0Cr17Ti、0Cr13Si4NbRE、1Cr17、1 Cr17Ti、1Cr17M02Ti、1Cr25Ti、1Cr28等。 3.奥氏体不锈钢:含络量12%~25%,含镍量7%~20%(或20%以上),最典型的代表是1Cr1 8Ni9Ti,常见的还有00Cr18Ni10、00Cr18Ni14Mo2Cu2、0Cr18Ni12Mo2Ti、0Cr18Ni18Mo2 Cu2Ti、0Cr23Ni28M03Cu3Ti、1Cr14Mn14Ni、2Cr13Mn9Ni4、1Cr18Mn8Ni5N等。 4.奥氏体+铁素体不锈钢:与奥氏体不锈钢相似,仅在组织中含有一定量的铁素体,常见的 有0Cr21Ni5Ti、1Cr21Ni5Ti、1Cr18Mn10Ni5M03N、0Cr17Mn13Mo2N、1Cr17Mn9Ni3M03Cu2 N、Cr2bNi17M03CuSiN、1Cr18Ni11Si4AlTi等。 5.沉淀硬化不锈钢:含有较高的铬、镍和很低的碳,常见的有0Cr17Ni4Cu4Nb、0Cr17Ni7A l、0Cr15Ni7M02Al等。 前两类为铬不锈钢,后三类为铬镍不锈钢。 3 不锈钢有哪些物理、力学性能? 1.马氏体不锈钢:能进行淬火,淬火后具有较高的硬度、强度和耐磨性及良好的抗氧化性, 有的有磁性,但内应力大且脆。经低温回火后可消除其应力,提高塑性,切削加工较困 难,有切屑擦伤或粘结的明显趋向,刀具易磨损。 当钢中含碳量低于0.3%时,组织不均匀,粘附性强,切削时容易产生积屑瘤,且断屑困难,工件已加工表面质量低。含碳量达0.4%~0.5%时,切削加工性较好。
不锈钢地车削加工
一切削难加工材料的综合分析 1.1不锈钢简介 通常,人们把含铬量大于12%或含镍量大于8%的合金钢叫不锈钢。这种钢在大气中或在腐蚀性介质中具有一定的耐蚀能力,并在较高温度(>450℃)下具有较高的强度。含铬量达16%~18%的钢称为耐酸钢或耐酸不锈钢,习惯上通称为不锈钢。 钢中含铬量达12%以上时,在与氧化性介质接触中,由于电化学作用,表面很快形成一层富铬的钝化膜,保护金属部不受腐蚀;但在非氧化性腐蚀介质中,仍不易形成坚固的钝化膜。为了提高钢的耐蚀能力,通常增大铬的比例或添加可以促进钝化的合金元素,加Ni、Mo、Mn、Cu、Nb、Ti、W、Co等,这些元素不仅提高了钢的抗腐蚀能力,同时改变了钢的部组织以及物理力学性能。这些合金元素在钢中的含量不同,对不锈钢的性能产生不同的影响,有的有磁性,有的无磁性,有的能够进行热处理,有的则不能热处理。 由于不锈钢所具有的上述特性,越来越广泛地应用于航空、航天、化工、石油、建筑和食品等工业部门及日常生活中。所含的合金元素对切削加工性影响很大,1.2不锈钢的分类 不锈钢按其成分,可分为以铬为主的铬不锈钢和以铬、镍为主的铬镍不锈钢两大类。工业上常用的不锈钢一般按金相组织分类,可分为以下五大类: 1)马氏体不锈钢:含铬量12%~18%,含碳量0.1%~0.5%(有时达1%),常见的有1Cr13、2Cr13、3Cr13、4Cr13、1Cr17Ni2、9Cr18、9Cr18MoV、30Cr13Mo等。 2)铁素体不锈钢:含铬量12%~30%,常见的有0Cr13、0Cr17Ti、0Cr13Si4NbRE、1Cr17、1Cr17Ti、1Cr17M02Ti、1Cr25Ti、1Cr28等。 3)奥氏体不锈钢:含络量12%~25%,含镍量7%~20%(或20%以上),最典型的代表是1Cr18Ni9Ti,常见的还有00Cr18Ni10、00Cr18Ni14Mo2Cu2、0Cr18Ni12Mo2
不锈钢螺纹的车削加工方法总结
不锈钢螺纹的车削加工方法全世界因锈蚀而消耗的金属制品约占金属产量的10%,因此提高金属抗蚀性和耐蚀性具有非常重要的意义。不锈钢能够达到相对较好的抗蚀要求,由起初的军用拓展到工业及民用各领域。因此,对各种复杂曲面的不锈钢工件要求量较大。但由于材质的特殊性,加工工艺成为制作产品的难题。 不锈钢材质本身的特殊性: 不同种类的不锈钢由于机械性能和化学成分的不同其数控 切削的难度也不相同。有的不锈钢在切削加工时,很难达到满意的加工表面粗糙度;而有的不锈钢,虽容易达到要求的加工表面粗糙度,但在切削加工过程中刀具却特别容易磨损。经总结,各类不锈钢很难切削的主要原因有以下几个方面: 热强度高、韧性大对数控高速切削不适应奥氏体类不锈钢与马氏体类不锈钢其硬度和抗拉强度不高,只相当于40 号钢,但延伸率、断面收缩率和冲击值却比较高。如 1Cr18Ni9Ti延伸率为40号钢的210%,这样在数控高速切削过程中就不容易被切断,切削变形时所消耗的功相当大。相对来说,不锈钢在高温下的强度降低较少,如45号钢在500°时其持久强度为7kg/mM2,而1Cr18Ni9Ti在550°时其持久强度仍保持在19~24kg /mM2。实践证明,在相同切削温度的作用下,不锈钢切削比普通碳素钢难加工,其热强
度高是一个极其重要的因素; 加工硬化趋势强对数控车削不利在数控高速车削的过 程中,由于刀尖对工件材料挤压的结果使切削区的金属产生变形,晶内发生滑移,晶格畸变,组织致密,机械性能也随着发生变化,一般切削硬度也能增加2~3倍。数控切削后加工硬化层深度可以从几十微米到几百微米不等,因此前一次走刀所产生的加工硬化现象又妨碍了下一次走刀时的切削,并且加工硬化层的高硬度导致刀具特别容易磨损; 切屑的粘附性强、导热差对数控切削有影响在数控切削过程中,切削碎屑很容易牢固地粘附或熔着在刀尖和刀刃上,形成积屑瘤,造成工件加工表面的表面粗糙度恶化,同时增加切削过程中的振动,加速刀具磨损。而且大量的切削热无法及时传导出来,甚至切削产生的热量也无法传导到切屑的整体上,造成传入刀具总热量比普通碳素钢多3~5倍,使切削刃在高温下失去切削性能。在数控切削过程中,所产生的大量热能未能迅速排出,必然会传递给刀具,使切削部位温度升高。同时由于排屑比较困难,尤其是不断屑,使被切削下来的切屑产生挤塞,特别是加工内孔,切屑挤塞更加严重。另外,刀具因受螺纹截面形状的限制,再加之本身强度较差,加工中容易产生振动,刀尖很容易在切削过程中由于局部温度过高而烧坏或因振动太大而崩裂。 数控切削不锈钢刀具的问题及解决对策
不锈钢车削方法
1切削过程中的难点及原因分析 在零件试生产时,我们按车削普通碳钢的工艺方法对3Cr13不锈钢进行了车削试验,结果是刀具磨损非常严重,生产率极低,零件表面质量达不到要求。 比较3Cr13钢与40钢、45钢等碳素结构钢的机械性能可知,3Cr1 3钢的强度比40钢和45钢高,它是一种强度高、塑性好的中碳马氏体不锈钢。由于切削时加工硬化严重,切削抗力大,切削温度高,导致刀具磨损严重,磨刀次数增多,增加了停机时间和机床调整时间,降低了生产率。同时又容易粘刀,产生积屑瘤,引起工件尺寸的变化并影响表面粗糙度,而且切屑不易卷曲和折断,易损伤工件已加工表面,影响零件质量。所以,不能用切削45钢的工艺来切削3Cr13,也不能把通用车床上的加工方法照搬到自动车床上来。因为一般自动车床装刀较少,要求最好一次走刀就能使被加工表面达到要求的尺寸和表面粗糙度,以保证较高的生产率。 2主要技术措施 1. 通过热处理,改变材料的硬度 马氏体不锈钢在热处理后的不同硬度,对车削加工的影响很大。表1是用YW2材料的车刀对热处理后不同硬度的3Cr13钢的车削情况。可见,退火状0.10.10.1态的马氏体不锈钢虽然硬度低,但车削性能差,这是因为材料塑性和韧性大,组织不均匀,粘附,熔着性强,切削过程易产生刀瘤,不易获得较好的表面质量。而调质处理后硬度在HRC30以下的3Cr13材料,车削加工性较好,易达到较好的表面质量。用硬度在HRC30以上的材料加工出的零件,表面质量虽然较好,但刀具易磨损。所以,在条件允许的情况下,可以在材料进厂后,先进行调质处理,硬度达到HRC25~HRC30,然后再进行切削加工。 表1 3Cr13钢材料切削用 量刀具 耐用 度 min 加工表 面粗糙 度 μm ν m/ mi n s m m /r HB240(退火)45 ~ 55 . 1 90~ 115 Ra6.3~ Ra3.2 HRC25~30(调质)45 ~ 55 . 1 95~ 110 Ra3.2 HRC35~38(调质)45 ~ 55 . 1 60~ 75 Ra3.2 2. 刀具材料的选择 在自动车床上车削不锈钢,一般使用的硬质合金的刀具材料有:YG6、YG8、YT15、YT30、YW1、YW2等材料。 常用的高速钢刀具有:W18Cr4V、W6M05Cr4V2AL等材料。我们在切削参数相同的条件
如何解决不锈钢螺纹车削问题
如何解决不锈钢螺纹车削问题 螺纹是机械工程中常见的几何特征之一, 应用广泛。螺纹的加工工艺较多, 如基于塑性变形的滚丝与搓丝, 基于切削加工的车削、铣削、攻螺纹与套螺纹、螺纹磨削、螺纹研磨等。 不同种类的不锈钢由于机械性能和化学成分的不同,其数控切削的难度也不相同。有的不锈钢在切削加工时,很难达到满意的加工表面粗糙度;而有的不锈钢,虽容易达到要求的加工表面粗糙度,但在切削加工过程中刀具却特别容易磨损。经总结,各类不锈钢很难切削的主要原因有以下几个方面: 1 热强度高、韧性大 奥氏体类不锈钢与马氏体类不锈钢其硬度和抗拉强度不高,只相当于40号钢,但延伸率、断面收缩率和冲击值却比较高,这样在数控高速切削过程中就不容易被切断,切削变形时所消耗的功相当大。相对来说,不锈钢在高温下的强度降低较少,如45号钢在500°时其持久强度为7kg/mm2,而1Cr18Ni9Ti在550°时其持久强度仍保持在19——24kg/mm2。实践证明,在相同切削温度的作用下,不锈钢切削比普通碳素钢难加工,其热强度高是一个极其重要的因素。 2 加工硬化趋势强 在数控高速车削的过程中,由于刀尖对工件材料挤压的结果使切削区的金属产生变形,晶内发生滑移,晶格畸变,组织致密,机械性能也随着发生变化,一般切削硬度也能增加2——3倍。数控切削后加工硬化层深度可以从几十微米到几百微米不等,因此前一次走刀
所产生的加工硬化现象又妨碍了下一次走刀时的切削,并且加工硬化层的高硬度导致刀具特别容易磨损。 3 切屑的粘附性强、导热差 在数控切削过程中,切削碎屑很容易牢固地粘附或熔着在刀尖和刀刃上,形成积屑瘤,造成工件加工表面的表面粗糙度恶化,同时增加切削过程中的振动,加速刀具磨损。而且大量的切削热无法及时传导出来,甚至切削产生的热量也无法传导到切屑的整体上,造成传入刀具总热量比普通碳素钢多3——5倍,使切削刃在高温下失去切削性能。在数控切削过程中,所产生的大量热能未能迅速排出,必然会传递给刀具,使切削部位温度升高。同时由于排屑比较困难,尤其是不断屑,使被切削下来的切屑产生挤塞,特别是加工内孔,切屑挤塞更加严重。另外,刀具因受螺纹截面形状的限制,再加之本身强度较差,加工中容易产生振动,刀尖很容易在切削过程中由于局部温度过高而烧坏或因振动太大而崩裂。 4 螺纹粗糙度差的原因及对策 数控切削后螺纹表面粗糙度太差,鱼鳞斑状波纹及啃刀现象是不锈钢螺纹车削中最常遇到的现象,产生这些现象的原因有: (1)螺纹车刀两侧刃后角太小,两侧刃与后面的螺纹表面相摩擦使加工表面恶化,加工时必须考虑螺纹旋转角对两侧刃实际后角的影响。 螺纹车刀的前角太小,刃口不够锋利,切屑不能顺利地被切断,而是部分地被挤压或撕裂下来,必定造成螺纹表面非常粗糙。当前角太大时,刀刃强度削弱且容易磨损、崩裂、扎刀,更容易引起振动而使螺纹表面产生波纹。因此,应根据不锈钢的不同材质选择适当的前角。车削耐浓硫酸用不锈钢螺纹时,应比车削2Cr13不锈钢螺纹采用较小的前角,车
如何加工不锈钢
不锈钢切削加工 不锈钢切削加工摘要:螺纹类零件10的数控车床加工编程NUM公司力推新一代Axium Power数控系统数控铣削的编程与工艺分析基于细胞神经网络刀具磨损图像处理的研究中国最大乙烯装置的裂解气压缩机试车成功发动机盲孔除切屑机的研制与应用在不断变化时代的工具钢加工什么是智能变送器?机械故障的形成及其特性分析数控车间(机床)集成管理技术及产品浅谈CAD的特征造型技术轴承钢的表面强化方法如何进行电话销售?拉刀齿距及同时工作齿数的确定大型水轮机叶片的多轴联动数控加工编程技术张晓静:计算机在冲压领域的应用 PLC位控单元在精密磨削控制中的应用硬质材料铣削技术 CAD技术发展趋势数控机床软件界面人的因素分析 [标签:tag] 1 什么是不锈钢?通常,人们把含铬量大于12%或含镍量大于8%的合金钢叫不锈钢。这种钢在大气中或在腐蚀性介质中具有一定的耐蚀能力,并在较高温度(450℃)下具有较高的强度。含铬量达16%~18%的钢称为耐酸钢或耐酸不锈钢,习惯上通称为不锈钢。钢中含铬量达12%以上时,. 1 什么是不锈钢? 通常,人们把含铬量大于12%或含镍量大于8%的合金钢叫不锈钢。这种 钢在大气中或在腐蚀性介质中具有一定的耐蚀能力,并在较高温度 (>450℃)下具有较高的强度。含铬量达16%~18%的钢称为耐酸钢或耐酸 不锈钢,习惯上通称为不锈钢。 钢中含铬量达12%以上时,在与氧化性介质接触中,由于电化学作用, 表面很快形成一层富铬的钝化膜,保护金属内部不受腐蚀;但在非氧化 性腐蚀介质中,仍不易形成坚固的钝化膜。为了提高钢的耐蚀能力,通 常增大铬的比例或添加可以促进钝化的合金元素,加Ni、Mo、Mn、Cu、Nb、Ti、W、Co等,这些元素不仅提高了钢的抗腐蚀能力,同时改变了 钢的内部组织以及物理力学性能。这些合金元素在钢中的含量不同,对 不锈钢的性能产生不同的影响,有的有磁性,有的无磁性,有的能够进 行热处理,有的则不能热处理。 由于不锈钢所具有的上述特性,越来越广泛地应用于航空、航天、化工、石油、建筑和食品等工业部门及日常生活中。所含的合金元素对切削加 工性影响很大,有的甚至很难切削。 2 不锈钢可分为哪几类? 不锈钢按其成分,可分为以铬为主的铬不锈钢和以铬、镍为主的铬镍不 锈钢两大类。 工业上常用的不锈钢一般按金相组织分类,可分为以下五大类: 马氏体不锈钢:含铬量12%~18%,含碳量0.1%~0.5%(有时达1%), 常见的有1Cr13、2Cr13、3Cr13、4Cr13、1Cr17Ni2、9Cr18、 9Cr18MoV、30Cr13Mo等。铁素体不锈钢:含铬量12%~30%, 常见的有0Cr13、0Cr17Ti、0Cr13Si4NbRE、1Cr17、1Cr17Ti、 1Cr17M02Ti、1Cr25Ti、1Cr28等。奥氏体不锈钢:含络量12%~ 25%,含镍量7%~20%(或20%以上),最典型的代表是1Cr18Ni9Ti, 常见的还有00Cr18Ni10、00Cr18Ni14Mo2Cu2、0Cr18Ni12Mo2Ti、 0Cr18Ni18Mo2Cu2Ti、0Cr23Ni28M03Cu3Ti、1Cr14Mn14Ni、 2Cr13Mn9Ni4、1Cr18Mn8Ni5N等。奥氏体铁素体不锈钢:与奥 氏体不锈钢相似,仅在组织中含有一定量的铁素体,常见的有 0Cr21Ni5Ti、1Cr21Ni5Ti、1Cr18Mn10Ni5M03N、0Cr17Mn13Mo2N、
不锈钢法兰加工方法
不锈钢法兰加工方法 对刀具几何参数的要求: 加工不锈钢时,刀具切削部分的几何形状,一般应从前角、后角方面的选择来考虑。在选择前角时,要考虑卷屑槽、有无倒棱和刃倾角的正负角度大小等因素。不论何种刀具,加工不锈钢时都必须采用较大的前角。增大刀具的前角可减小切屑切离和清出过程中所遇到的阻力。对后角选择要求不十分严格,但不宜过小,后角过小容易和工件表面产生严重摩擦,使加工表面粗糙度恶化,加速刀具磨损。并且由于强烈摩擦,增强了不锈钢表面加工硬化的效应;刀具后角也不宜过大,后角过大,使刀具的楔角减小,降低了切削刃的强度,加速了刀具的磨损。通常,后角应比加工普通碳钢时适当大些。对刀具切削部分表面粗糙度的要求: 提高刀具切削部分的表面光洁度可减少切屑形成卷曲时的阻力,提高刀具的耐用度。与加工普通碳钢相比较,加工不锈钢时应适当降低切削用量以减缓刀具磨损;同时还要选择适当的冷却润滑液,以便降低切削过程中的切削热和切削力,延长刀具的使用寿命。对刀杆材料的要求 加工不锈钢时,由于切削力较大,故刀杆必须具备足够的强度和刚性,以免在切削过程中发生颤振和变形。这就要求选用适当大的刀杆截面积,同时还应采用强度较高的材料来制造刀杆,如采用调质处理的45号钢或50号钢。对刀具切削部分材料的要求:加工不锈钢时,要求刀具切削部分的材料具有较高的耐磨性,并能在较高的温度下保持其切削性能。目前常用的材料有:高速钢和硬质合金。由于高速钢只能在600°C以下保持其切削性能,因此不宜用于高速切削,而只适用于在低速情况下加工不锈钢。由于硬质合金比高速钢具有更好的耐热性和耐磨性,因此用硬质合金材料制成的刀具更适合不锈钢的切削加工。硬质合金分钨钴合金(YG)和钨钴钛合金(YT)两大类。钨钴类合金具有良好的韧性,制成的刀具可以采用较大的前角与刃磨出较为锋利的刃口,在切削过程中切屑易变形,切削轻快,切屑不容易粘刀,所以在一般情况下,用钨钴合金加工不锈钢比较合适。特别是在振动较大的粗加工和断续切削加工情况下更应采用钨钴合金刀片,它不象钨钴钛合金那样硬脆,不易刃磨,易崩刃。钨钴钛合金的红硬性较好,在高温条件下比钨钴合金耐磨,但它的脆性较大,不耐冲击、振动,一般作不锈钢精车用刀具。 2刀具材料牌号的选择刀具材料的切削性能关系着刀具的耐用度和生产率,刀具材料的工艺性影响着刀具本身的制造与刃磨质量。宜选择硬度高、抗粘结性和韧性好的刀具材料,如YG类硬质合金,最好不要选用YT类硬质合金,尤其是在加工1Gr18Ni9Ti奥氏体不锈钢应绝对避免选用YT类硬质合金,因为不锈钢中的钛(Ti)和YT类硬质合金中的Ti产生亲合作用,切屑容易把合金中的Ti带走,促使刀具磨损加剧。生产实践表明,选用YG532、YG813及YW2三种牌号材料加工不锈钢具有较好的加工效果,,三种硬质合金牌号的性能比较牌号密度g/cm3抗弯强度Mpa硬度HRA性能即用途相当于ISO YG532 14≥1760≥91.5红硬性高,韧性好,抗粘能力强,适用于奥氏体、马氏体不锈钢、无磁钢、高温合金钢等大型工件的粗、精加工;合金耐用度高,高温性好,被加工工件表面质量高。K10~K20M20 YG813 14.05~14.1≥1570≥91耐磨性好,有较高的抗弯强度和抗粘结能力,适于高温合金钢;对容易产生加工冷作硬化现象的奥氏体不锈钢、高锰钢等,加工效果优于YW2。K10~K20M20 YW2 12.4~13.5≥1320≥90.5使用强度高,红硬性较好,能承受较大的冲击载荷。适用于耐热钢、高锰钢、不锈钢等材料的粗、精加工。3刀具几何参数的选择前角的选择:从切
不锈钢的切削加工总结
不锈钢的切削加工 在不锈钢的切削加工中,首先要对被加工件的被切削性能有所了解,不锈钢在切削过程中有如下几方面特点: 1. 加工硬化严重:在不锈钢中,以奥氏体和奥氏体+铁素体不锈钢的加工硬化现象最为突出。因为不锈钢的塑性大,塑性变形时晶格歪扭,强化系数很大;且奥氏体不够稳定,在切削应力的作用下,部分奥氏体会转变为马氏体;再加上化合物杂质在切削热的作用下,易于分解呈弥散分布,使切削加工时产生硬化层。 2. 切削力大:不锈钢在切削过程中塑性变形大,尤其是奥氏体不锈钢(其伸长率超过45号钢的1.5倍以上),使切削力增加。同时,不锈钢的加工硬化严重,热强度高,进一步增大了切削抗力,切屑的卷曲折断也比较困难。 3. 切削温度高:切削时塑性变形及与刀具间的摩擦都很大,产生的切削热多;大量切削热都集中在切削区和刀削接触的界面上,散热条件差。在相同的条件下切削温度比45号钢高200℃左右。 4. 切削不易折断、易粘结:不锈钢的塑性、韧性都很大,在高温、高压下,不锈钢与其他金属的亲和性强,易产生粘附现象,并形成积削瘤,既加剧刀具磨损,又会出现撕扯现象而使已加工表面恶化。含碳量较低的马氏体不锈钢的这一特点更为明显。 5. 刀具易磨损:切削不锈钢过程中的亲和作用,使刀削间产生粘结、扩散,从而使刀具产生粘结磨损、扩散磨损,致使刀具前刀面产生月牙洼,切削刃还会形成微小的剥落和缺口;加上不锈钢中的碳化物(如TiC)微粒硬度很高,
切削时直接与刀具接触、摩擦,擦伤刀具,还有加工硬化现象,均会使刀具磨损加剧。 切削不锈钢时应怎样选择刀具的材料: 合理选择刀具材料是保证高效率切削加工不锈钢的重要条件。根据不锈钢的切削特点,要求刀具材料应具有耐热性好、耐磨性高、与不锈钢的亲和作用小等特点,YG类硬质合金的韧性较好,可采用较大的前角,刀刃也可以磨得锋利些,使切削轻快,且切屑与刀具不易产生粘结,较适于加工不锈钢。另外,YG类合金的导热性较好,其导热系数比高速钢高将近两倍,比YT类合金高一倍。 切削不锈钢时怎样选择刀具几何参数? 前角:不锈钢的硬度、强度并不高,但其塑性、韧性都较好,热强性高,切削时切屑不易被切离。在保证刀具有足够强度的前提下,应选用较大的前角,这样不仅能够减小被切削金属的塑性变形,而且可以降低切削力和切削温度,同时使硬化层深度减小。 后角:加大后角能减小后刀面与加工表面的摩擦,但会使切削刃的强度和散热能力降低。后角的合理值取决于切削厚度,切削厚度小时,宜选较大后角,我们三轨由于切削量大,所以选用20°的后角。 选择合适的涂层对于金属切削来说能起到非常重要的作用,TiAICRN(碳氮化铝钛)涂层在不锈钢切削加工中起着非常重要的作用涂层材料作为化学屏障和热屏障,减小了月牙洼磨损,耐磨性良好。与未涂层刀具相比,涂层刀具加工精度提高0.5~1级,刀具消耗费用降低20%~50%,耐磨性提高2~10倍,切削速度提高25%~70%,使用寿命延长3~5倍。
不锈钢加工的难点及对策
不锈钢加工的难点及对策 1 切削过程中的难点及原因分析 在零件试生产时,我们按车削普通碳钢的工艺方法对3Cr13不锈钢进行了车削试验,结果是刀具磨损非常严重,生产率极低,零件表面质量达不到要求。比较3Cr13钢与40钢、45钢等碳素结构钢的机械性能可知,3Cr1 3钢的强度比40钢和45钢高,它是一种强度高、塑性好的中碳马氏体不锈钢。由于切削时加工硬化严重,切削抗力大,切削温度高,导致刀具磨损严重,磨刀次数增多,增加了停机时间和机床调整时间,降低了生产率。同时又容易粘刀,产生积屑瘤,引起工件尺寸的变化并影响表面粗糙度,而且切屑不易卷曲和折断,易损伤工件已加工表面,影响零件质量。所以,不能用切削45钢的工艺来切削3Cr13,也不能把通用车床上的加工方法照搬到自动车床上来。因为一般自动车床装刀较少,要求最好一次走刀就能使被加工表面达到要求的尺寸和表面粗糙度,以保证较高的生产率。 2 主要技术措施 1.通过热处理,改变材料的硬度 马氏体不锈钢在热处理后的不同硬度,对车削加工的影响很大。表1是用YW2材料的车刀对热处理后不同硬度的3Cr13钢的车削情况。可见,退火状0.10.10.1态的马氏体不锈钢虽然硬度低,但车削性能差,这是因为材料塑性和韧性大,组织不均匀,粘附,熔着性强,切削过程易产生刀瘤,不易获得较好的表面质量。而调质处理后硬度在HRC30以下的3Cr13材料,车削加工性较好,易达到较好的表面质
量。用硬度在HRC30以上的材料加工出的零件,表面质量虽然较好,但刀具易磨损。所以,在条件允许的情况下,可以在材料进厂后,先进行调质处理,硬度达到HRC25~HRC30,然后再进行切削加工。 表1 3Cr13钢材料 切削用量 刀具耐用度 min 加工表面粗糙度 μm ν m/min s mm/r HB240(退火) 45~55 0.1 90~115 Ra6.3~Ra3.2 HRC25~30(调质) 45~55 0.1
不锈钢的车削加工方法
不锈钢的车削加工 关键词:刀具材料、刀具参数、切削用量、涂层刀具 目前应用的不锈钢,按其组织状态主要分为马氏体不锈钢、铁素体不锈钢和奥氏体不锈钢,常把含鉻量超过11.7%或含镍量大于8%的合金钢,叫不锈钢,在合金钢种加入较多的金属元素(Cr和Ni),而改变了合金的物理性质和化学性质。增强了抗腐蚀能力,无论在空气中还是在酸盐的溶液中,均不易氧化生锈并在较高温度(>450℃)下仍具有较高的强度,因此被广泛应用于航空,航天、化工、石油、建筑和食品等工业部门及日常生活中。 1不锈钢的主要切削特点 (1)切削力大 其中奥氏体不锈钢尤为突出,这种材料虽然硬度不高,以牌号1Cr18Ni9Ti 为例,其硬度≤187HBW,但塑性很好(断后伸长率δ=40%,断面收缩率Ψ=60%),因此在切削过程中塑性变形大,使切削力增加。在切削用量相同时,切奥氏体不锈钢耗能比低碳钢约高50%。 (2)加工硬化严重 在不锈钢中,以奥氏体和奥氏体铁素体不锈钢的加工硬化现象最为突出。他们塑性大,塑性变形时晶格产生强烈歪扭;同时奥氏体稳定性差,在切削力的作用下,部分奥氏体会转变为马氏体;再加上化合物杂质在切削热的作用下,易于分解呈弥散分布,使切削加工时产生硬化层。这一切均使加工硬化现象更为明显。(3)刀具易产生粘附磨损 不锈钢材料在切削过程中产生高温下,与刀具材料的亲和性较大,使刀具与切削间产生粘结、扩散,易形成“刀瘤”,而造成刀具粘附磨损,降低刀具的使用寿命。 (4)切削区局部温度高 这类材料所需切削力大,分离切削消耗的功率也大,产生的切削热也就多,传入刀具的热量可达20%,而加工碳素钢时仅占9%,同时由于不锈钢的导热性不好(不锈钢的导热系数约为碳钢的1/3左右),大量切削热都集中在切削区和刀-屑接触的界面上,从而是切削区局部温度很高。 2.刀具材料的选择 根据前述不锈钢的切削特点,要求刀具材料应具有耐热性好、耐磨性高、与不锈钢的亲和作用小等特点。目前常用的刀具材料有硬质合金、高速钢和涂层刀具。 (1)硬质合金 通常情况下,多数难加工材料都宜选用YG类硬质合金加工。最好不选用YT 类硬质合金,尤其是在加工1Cr18Ni9Ti奥氏体不锈钢时,应绝对避免选用YT
不锈钢管件加工流程
不锈钢管件制造工艺流程 下料成形(焊接)热处理表面处理切削加工无损检测表面防护标志 ① 下料 管件所用材料主要为管子、板材和棒材,根据材料特性和产品所用坯料的形状选择下料方法。坯料的形状、尺寸和其它要求根据不同产品的工艺规定进行。 对于管子,常用的下料方法有带锯床或弓锯床切割、气割、等离子切割。 对于板材,常用的下料方法有气割、等离子切割、冲床冲切。 对于棒材,常用的下料方法有带锯床或弓锯床切割、冲剪切割。 ② 成形(焊接) 对所有管件的制造工艺来说,成形是其不可缺少的工序。因不同产品的成形工艺不尽相同,需要的篇幅较长,将在第15.2.4节中另外予以描述。这里,对部分成形工序中所包括的加热及焊接作一概略介绍。 a.. 加热 对采用热成形方法制造管件而言,为满足成形工艺中对材料变形的要求,成形时需要对坯料进行加热。加热温度通常视材料和工艺需要确定。 热推弯头或热弯弯管成形时,通常采用中频或高频感应加热的方法,也有采用火焰加热的方法。这种加热方式是与弯头或弯管成形过程同步进行的连续加热,管坯在运动中被加热并完成成形过程。 热压弯头、热压三通或锻件成形时,通常采用反射炉加热的方法、火焰加热的方法、感应加热的方法或电炉加热的方法等。这种加热是先行将管坯加热到所需要的温度,再放入模具中压制或锻制成形。 b. 焊接 带焊缝的管件包括两种情况,一种是用焊管制造的管件,对管件制造厂来说,采用焊管的成形工艺与采用无缝管的成形工艺基本相同,管件成形过程不包括焊接工序;另一种是由管件制造厂完成管件成形所需要的焊接工序,如单片压制后再进行组装焊接成形的弯头、用钢板卷筒后焊接成管坯再进行压制的三通等。 管件的焊接方法常用的有手工电弧焊、气体保护焊以及自动焊等。 制造厂应编制焊接工艺规程用以指导焊接工作,并应按相应规范要求进行焊接工艺评定,以验证焊接工艺规程的正确性和评定焊工的施焊能力。
不锈钢的铣削加工
不锈钢的铣削加工 铣削不锈钢的特点是:不锈钢的粘附性及熔着性强,切屑容易粘附在铣刀刀齿上,使切削条件恶化;逆铣时,刀齿先在已经硬化的表面上滑行,增加了加工硬化的趋势;铣削时冲击、振动较大,使铣刀刀齿易崩刃和磨损。 铣削不锈钢除端铣刀和部分立铣刀可用硬质合金作铣刀刀齿材料外,其余各类铣刀均采用高速钢,特别是钨—钼系和高钒高速钢具有良好的效果,其刀具耐用度可比W18Cr4V提高1~2倍。适宜制作不锈钢铣刀的硬质合金牌号有YG8、YW2、813、798、YS2T、YS30、YS25等。 铣削不锈钢时,切削刃既要锋利又要能承受冲击,容屑槽要大。可采用大螺旋角铣刀(圆柱铣刀、立铣刀),螺旋角β从20°增加到45°(n=5°),刀具耐用度可提高2倍以上,因为此时铣刀的工作前角γ0e由11°增加到27°以上,铣削轻快。但β值不宜再大,特别是立铣刀以β≤35°为宜,以免削弱刀齿。 采用波形刃立铣刀加工不锈钢管材或薄壁件,切削轻快,振动小,切屑易碎,工件不变形。用硬质合金立铣刀高速铣削、可转位端铣刀铣削不锈钢都能取得良好的效果。 用银白屑(SWC)端铣刀铣削1Cr18Ni9Ti,其几何参数为γf=5°、γp=15°、αf=15°、αp=5°、κr=55°、κ′r=35°、γ01=-30°、bγ=0.4mm、rε=6mm,当V c=50~90 m/min、V f=630~750mm/min、a′p b可达20γ=2~6mm,铣削功率下降44%,效率也大大提高。其原理是在主切削刃上磨出负倒棱,铣削时人为地产生积屑瘤,使其代替切削刃进行切削,积屑瘤的前角~~302,由于主偏角的作用,积屑瘤受到一个前刀面上产生的平行于切削刃的推力作用而成为副屑流出,从而带走了切削热,降低了切削温度。 铣削不锈钢时,应尽可能采用顺铣法加工。不对称顺铣法能保证切削刃平稳地从金属中切离,切屑粘结接触面积较小,在高速离心力的作用下易被甩掉,以免刀齿重新切入工件时,切屑冲击前刀面产生剥落和崩刃现象,提高刀具的耐用度。 采用喷雾冷却法效果最为显著,可提高铣刀耐用度一倍以上;如用一般10%乳化液冷却,应保证切削液流量达到充分冷却。硬质合金铣刀铣削不锈钢时,取Vc=70~150 m/min,Vf=37.5~150 mm/min,同时应根据合金牌号及工件材料的不同作适当调整。(end) 几种主要不锈钢材料主要用途 许多易变的因素表示腐蚀介质的特征,即化学制品和其浓度、大气状态、温度、时间,所以如果不了解介质的正确的性质,要使用材料、选择材料是困难。但是,以下可作为选择指南: 304型广泛使用的材料。在建筑中能经受一般的锈蚀,可抵抗食品加工介质浸蚀(但含有浓酸和氯化物成分的高温状态可能出现腐蚀),能抵抗有机化合物、染料和广泛的各种各样的无机化合物。304L型(低碳),耐硝酸性好,并耐用中等温度和浓度的硫酸,广泛地用作液
不锈钢材料的车削加工
图4 一稳定数值。(2)图2中 转矩转速传感器5测得的转矩T 2要小于转矩转速传感器2测得的转矩T 1,即T 2
不锈钢车削加工工艺
不锈钢车削加工工艺 1 什么是不锈钢? 通常,人们把含铬量大于12%或含镍量大于8%的合金钢叫不锈钢。这种钢在大气中或在腐蚀性介质中具有一定的耐蚀能力,并在较高温度(>450℃)下具有较高的强度。含铬量达16%~18%的钢称为耐酸钢或耐酸不锈钢,习惯上通称为不锈钢。 钢中含铬量达12%以上时,在与氧化性介质接触中,由于电化学作用,表面很快形成一层富铬的钝化膜,保护金属内部不受腐蚀;但在非氧化性腐蚀介质中,仍不易形成坚固的钝化膜。为了提高钢的耐蚀能力,通常增大铬的比例或添加可以促进钝化的合金元素,加Ni、Mo、Mn、Cu、Nb、Ti、W、Co等,这些元素不仅提高了钢的抗腐蚀能力,同时改变了钢的内部组织以及物理力学性能。这些合金元素在钢中的含量不同,对不锈钢的性能产生不同的影响,有的有磁性,有的无磁性,有的能够进行热处理,有的则不能热处理。 由于不锈钢所具有的上述特性,越来越广泛地应用于航空、航天、化工、石油、建筑和食品等工业部门及日常生活中。所含的合金元素对切削加工性影响很大,有的甚至很难切削。 2 不锈钢可分为哪几类? 不锈钢按其成分,可分为以铬为主的铬不锈钢和以铬、镍为主的铬镍不锈钢两大类。 工业上常用的不锈钢一般按金相组织分类,可分为以下五大类: 1. 马氏体不锈钢:含铬量12%~18%,含碳量0.1%~0.5%(有时达1%),常见的有1Cr13、2Cr13、3Cr13、4Cr13、1Cr17Ni2、9Cr18、9Cr18MoV、30Cr13Mo等。 2. 铁素体不锈钢:含铬量12%~30%,常见的有0Cr13、0Cr17Ti、0Cr13Si4NbRE、1Cr17、1Cr17Ti、1Cr17M02Ti、1Cr25Ti、1Cr28等。 3. 奥氏体不锈钢:含络量12%~25%,含镍量7%~20%(或20%以上),最典型的代表是1Cr18Ni9Ti,常见的还有00Cr18Ni10、00Cr18Ni14Mo2Cu2、0Cr18Ni12Mo2Ti、0Cr18Ni18Mo2Cu2Ti、0Cr23Ni28M03Cu3Ti、1Cr14Mn14Ni、2Cr13Mn9Ni4、1Cr18Mn8Ni5N等。 4. 奥氏体+铁素体不锈钢:与奥氏体不锈钢相似,仅在组织中含有一定量的铁素体,常见的有0Cr21Ni5Ti、1Cr21Ni5Ti、1Cr18Mn10Ni5M03N、0Cr17Mn13Mo2N、1Cr17Mn9Ni3M03Cu2N、Cr2bNi17M03CuSiN、1Cr18Ni11Si4AlTi等。 5. 沉淀硬化不锈钢:含有较高的铬、镍和很低的碳,常见的有0Cr17Ni4Cu4Nb、0Cr17Ni7Al、0Cr15Ni7M02Al等。 前两类为铬不锈钢,后三类为铬镍不锈钢。
数控车削不锈钢螺纹的加工方法
数控车削不锈钢螺纹的加工方法 newmaker 全世界因锈蚀而消耗的金属制品约占金属产量的10%,因此提高金属抗蚀性和耐蚀性具有非常重要的意义。不锈钢能够达到相对较好的抗蚀要求,由起初的军用拓展到工业及民用各领域。因此,对各种复杂曲面的不锈钢工件要求量较大。但由于材质的特殊性,加工工艺成为制作产品的难题。 不锈钢材质本身的特殊性 对数控切削加工的影响 不同种类的不锈钢由于机械性能和化学成分的不同其数控切削的难度也不相同。有的不锈钢在切削加工时,很难达到满意的加工表面粗糙度;而有的不锈钢,虽容易达到要求的加工表面粗糙度,但在切削加工过程中刀具却特别容易磨损。经总结,各类不锈钢很难切削的主要原因有以下几个方面:
热强度高、韧性大对数控高速切削不适应奥氏体类不锈钢与马氏体类不锈钢其硬度和抗拉强度不高,只相当于40号钢,但延伸率、断面收缩率和冲击值却比较高。如,1Cr18Ni9Ti延伸率为40号钢的210%,这样在数控高速切削过程中就不容易被切断,切削变形时所消耗的功相当大。相对来说,不锈钢在高温下的强度降低较少,如45号钢在500°时其持久强度为7kg/mM2,而1Cr18Ni9Ti在550°时其持久强度仍保持在19~24kg/mM2。实践证明,在相同切削温度的作用下,不锈钢切削比普通碳素钢难加工,其热强度高是一个极其重要的因素。 加工硬化趋势强对数控车削不利在数控高速车削的过程中,由于刀尖对工件材料挤压的结果使切削区的金属产生变形,晶内发生滑移,晶格畸变,组织致密,机械性能也随着发生变化,一般切削硬度也能增加2~3倍。数控切削后加工硬化层深度可以从几十微米到几百微米不等,因此前一次走刀所产生的加工硬化现象又妨碍了下一次走刀时的切削,并且加工硬化层的高硬度导致刀具特别容易磨损。 切屑的粘附性强、导热差对数控切削有影响在数控切削过程中,切削碎屑很容易牢固地粘附或熔着在刀尖和刀刃上,形成积屑瘤,造成工件加工表面的表面粗糙度恶化,同时增加切削过程中的振动,加速刀具磨损。而且大量的切削热无法及时传导出
不锈钢的车削加工
技师论文工种:车工 题目:不锈钢的车削加工 姓名: 身份证号: 等级: 准考证号: 培训单位: 鉴定单位: 日期:
目录 一、前言 (1) 二、不锈钢主要的特点 (3) 三、刀具选择 (4) 1、刀具材料选择 (4) 2、刀具几何角度选择 (4) 四、切削参数的选择 (6) 1、切削用量的选择 (6) 2、切削液的选择 (7) 五、不锈钢零件的车削实例 (7) 六、结束语 (8)
不锈钢的车削加工 摘要:经过多年的工作经验积累,本文简要分析概述了不锈钢基本加工特性,根据不锈钢零件锥面加工实例,详细分析了刀具选择、装夹、冷却方式等过程控制环节,对类似不锈钢零件的切削加工具有很高的借鉴价质。 关键字:不锈钢特性加工特点实例分析 一、前言 含铬量大于12%或含镍量大于8%的合金钢称为不锈钢。由于在合金钢中加入较多的金属元素(铬和镍),因而改变了合金的物理性质和化学性质,增强了抗腐蚀能力,在空气中和酸,盐的溶液中不易氧化生锈,因此被广泛用于航空,航天,化工,石油,建筑和食品加工等工业部门及日常生活中。 二、不锈钢的主要特点 不锈钢按其化学成分可分为两类:即铬不锈钢和镍不锈钢。常用的铬不锈钢含铬量有12%,17%和27%等,其抗腐蚀性能随着含铬量的增加而增加,常用的铬镍不锈钢,含铬量17%~20%,含镍量8%~11%这种不锈钢的抗腐蚀性能及机械性能比铬不锈钢高。 不锈钢的物理性能机械性能对切削过程的特性有很大的影响,其中导热性起着很大的作用。被加工钢材的导热性越低,由切屑带走的热量越少,而刀具上积聚的热量越多。由于不锈钢的韧性大,强度高,切削力大和导
热性差,因此切削时热量难于扩散,致使刀具易于发热,甚至用加工一般钢材低得多的切削速度进行加工,仍会使刀具产生大量的热,降低了刀具的切削性能。在不锈钢的金属组织中,由于有分散的碳化物质杂质,车削时会产生较高的磨蚀性,而使刀具容易磨损。不锈钢在高温时仍能保持其硬度和强度,而刀具材料则由于超过热硬性限度,而产生塑性变形。不锈钢有较高的粘附性,使材料“粘结”到刀具上而产生积屑瘤,给车削带来困难,影响零件表面粗糙度。不锈钢的强度高,使之作用在刀具上的切削力增大,不均衡的切削过程使刀具的振动增强。此外,不锈钢的铸件和锻件毛坯的表面有硬度较高的氧化皮以及不连续和不规则的外形,都会给车削带来困难,在车削不锈钢材料时,要保证刀具有较好的刚性和良好的刃磨质量。 三、刀具选择 1、刀具材料 正确地选用刀具材料,是保证高效率加工不锈钢的决定因素。要求刀具材料应具有耐热性好耐磨性高与不锈钢的亲和作用小等特点。常用的刀具材料有硬质合金和高速钢两大类。 (1)硬质合金宜选用YG类硬质合金加工。最好不选用YT类质合金,在车削时使用冷却润滑液进行冷却,以提高零件的表面粗糙度,减少刀具磨损。 (2)高速钢当工件的形状,尺寸结构不便使用硬质合金刀具或硬质合金刀具容易损坏时,应选用高性能高速钢刀具。 2、刀具几何角度