不锈钢的车削加工
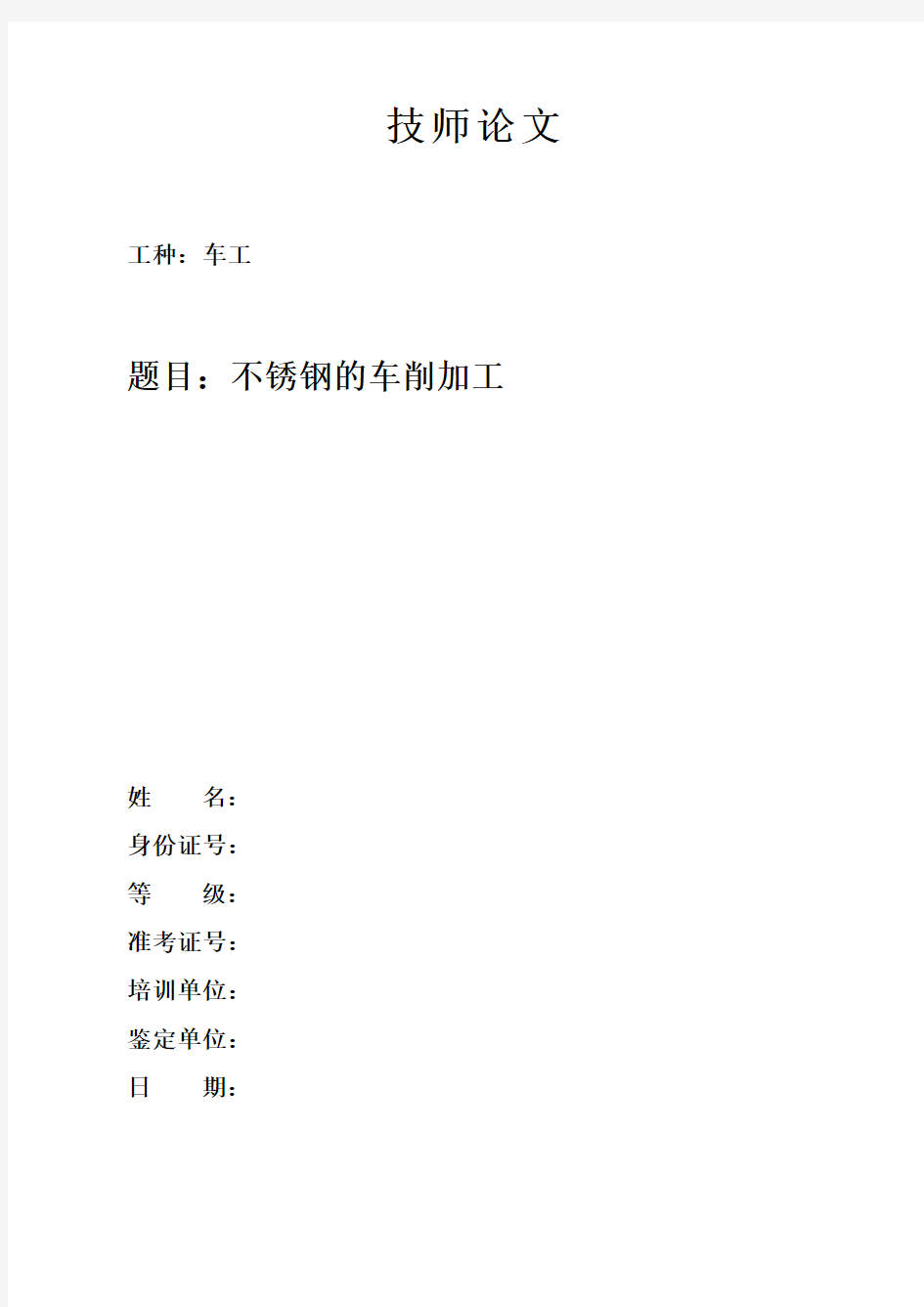

技师论文工种:车工
题目:不锈钢的车削加工
姓名:
身份证号:
等级:
准考证号:
培训单位:
鉴定单位:
日期:
目录
一、前言 (1)
二、不锈钢主要的特点 (3)
三、刀具选择 (4)
1、刀具材料选择 (4)
2、刀具几何角度选择 (4)
四、切削参数的选择 (6)
1、切削用量的选择 (6)
2、切削液的选择 (7)
五、不锈钢零件的车削实例 (7)
六、结束语 (8)
不锈钢的车削加工
摘要:经过多年的工作经验积累,本文简要分析概述了不锈钢基本加工特性,根据不锈钢零件锥面加工实例,详细分析了刀具选择、装夹、冷却方式等过程控制环节,对类似不锈钢零件的切削加工具有很高的借鉴价质。
关键字:不锈钢特性加工特点实例分析
一、前言
含铬量大于12%或含镍量大于8%的合金钢称为不锈钢。由于在合金钢中加入较多的金属元素(铬和镍),因而改变了合金的物理性质和化学性质,增强了抗腐蚀能力,在空气中和酸,盐的溶液中不易氧化生锈,因此被广泛用于航空,航天,化工,石油,建筑和食品加工等工业部门及日常生活中。
二、不锈钢的主要特点
不锈钢按其化学成分可分为两类:即铬不锈钢和镍不锈钢。常用的铬不锈钢含铬量有12%,17%和27%等,其抗腐蚀性能随着含铬量的增加而增加,常用的铬镍不锈钢,含铬量17%~20%,含镍量8%~11%这种不锈钢的抗腐蚀性能及机械性能比铬不锈钢高。
不锈钢的物理性能机械性能对切削过程的特性有很大的影响,其中导热性起着很大的作用。被加工钢材的导热性越低,由切屑带走的热量越少,而刀具上积聚的热量越多。由于不锈钢的韧性大,强度高,切削力大和导
热性差,因此切削时热量难于扩散,致使刀具易于发热,甚至用加工一般钢材低得多的切削速度进行加工,仍会使刀具产生大量的热,降低了刀具的切削性能。在不锈钢的金属组织中,由于有分散的碳化物质杂质,车削时会产生较高的磨蚀性,而使刀具容易磨损。不锈钢在高温时仍能保持其硬度和强度,而刀具材料则由于超过热硬性限度,而产生塑性变形。不锈钢有较高的粘附性,使材料“粘结”到刀具上而产生积屑瘤,给车削带来困难,影响零件表面粗糙度。不锈钢的强度高,使之作用在刀具上的切削力增大,不均衡的切削过程使刀具的振动增强。此外,不锈钢的铸件和锻件毛坯的表面有硬度较高的氧化皮以及不连续和不规则的外形,都会给车削带来困难,在车削不锈钢材料时,要保证刀具有较好的刚性和良好的刃磨质量。
三、刀具选择
1、刀具材料
正确地选用刀具材料,是保证高效率加工不锈钢的决定因素。要求刀具材料应具有耐热性好耐磨性高与不锈钢的亲和作用小等特点。常用的刀具材料有硬质合金和高速钢两大类。
(1)硬质合金宜选用YG类硬质合金加工。最好不选用YT类质合金,在车削时使用冷却润滑液进行冷却,以提高零件的表面粗糙度,减少刀具磨损。
(2)高速钢当工件的形状,尺寸结构不便使用硬质合金刀具或硬质合金刀具容易损坏时,应选用高性能高速钢刀具。
2、刀具几何角度
图 1
如图1所示刀具切削部分的几何角度,对于不锈钢切削加工的生产率,被加工表面的粗糙度切削力以及加工硬化等方面都有很大的影响。
(1)前角r 当前角过小时,切削力增大,振动增强,零件表面起波纹,切削不易变形,排屑困难,在高温下容易产生“积屑瘤”但前角过大时,刀具强度降低,刀具磨损快,而且容易崩刃。用硬质合金车刀车削不锈钢时前角r=12°~20°。
(2)后角α因不锈钢的弹性和塑性都比普通碳钢大,所以后角小时,其切削表面与车刀后角接触面积增大,剧烈摩擦产生的高温区集中于车刀后角,使车刀磨损加剧,被加工零件表面粗糙度降低以至产生毛刺。
故车刀后角要比车削普通碳钢车刀的后角稍大,但过大时又会降低刀刃强度,影响车刀耐用度。因此取α=8°~10°较为适宜。
(3)主偏角φ当主偏角小时,刀刃工作长度增加,散热性好,刀具耐用度相对提高,但在切削过程中容易产生振动。因此,在机床、零件、刀具系统刚性足够的条件下,可以使用较小的主偏角。
(4)刃倾角λ刃倾角影响切屑的形成和排屑方向。当λ为正值时,刀尖易受冲击,强度较差,切屑离开已加工表面。当λ为负值时,刀尖不受冲击,强度较好,切屑流向已加工表面。当λ为零度时,刀尖和刀刃同时受到冲击,切屑象钟表发条一样打卷。一般取刃倾角0°~5°在车削冲击性不锈钢零件时,其刃倾角取5°~10°。
(5)卷屑槽的选用由于车削不锈钢时不易断屑,如果排屑不好,切屑飞溅容易伤人,若切屑缠在零件上,则容易损坏车刀和己加工表面的粗糙度。因此,应在车刀前刃面上磨出圆弧形排屑槽,使切屑卷曲后沿一定方向排屑。其排屑槽的圆弧半径和槽的宽度随着被加工工件直径的增大而增大。在实际生产中,其圆弧半径一般取2~7mm,宽取3~6.5mm为宜。
四、切削参数的选择
1、切削用量的选择
为保证合理的刀具寿命,根据不锈钢的种类毛坯的硬度来选择切削用量,根据刀具材料,焊接质量和车刀刃磨条件零件直径大小、加工余量的大小和车床精度等来选择切削用量。常用量如表1所示加工不锈钢时推荐的切削用量。
粗车不锈钢的切削用量 表 1
2、切削液的选择
切削液皂化油具有一定的冷却性能和润滑性能,而且来源丰富,成本低。
五、不锈钢零件的车削实例
如图2所示不锈钢带锥度零件的车削材料为1Gr18Ni9Ti 毛坯为锻件,单件生产。技术要求是K 和M 的平行度不大于0.02mm ,φ100mm 和φ222mm 的同轴度度小于
0.02mm ,φ100mm 和φ
222mm 的同心度不大于
0.02mm 。零件的精度和
粗糙度要求高,零件结
构较薄在锥面处的壁
厚仅3.8mm 。
图 2
1、粗车,用四卡盘夹毛坯外圆,用划针校正外圆,用活动顶针带一有中心孔的盘类零件顶住端面,车外圆φ260mm和锥度,留余量1~1.5mm,长140mm至尺寸,放开活动顶针,车φ100mm,φ160mm×60mm,φ222mm ×18mm各內孔尺寸留余量1~1.5mm,长度至尺寸。零件调头用四爪卡盘夹φ260mm外圆,用划针校正己加工表面,用活动顶针带一有中心孔的盘类零件顶住端面,车φ180mm外圆留1~1.5mm。放开活动顶针车端面,车内外锥度至尺寸,车φ100mm×16mm留余量1~1.5mm。
2、精车,用四爪卡盘各爪放垫片夹φ180mm用丝表校正φ100mm和φ222mm其跳动不大于0.03mm,零件校正后夹紧,夹紧时用力要适量精车端面,车φ260mm,φ222mm×18mm,φ160mm×60mm和φ100mm至图纸要求。零件调头用四爪卡盘各爪放垫片夹φ26mm0用丝表校正零件适量夹紧精车φ180mm和总长160-0.1mm至尺寸。
六、结束语
车削不锈钢的原则是刀具材料应用坚韧性好、强度高的硬质合金,刀具参数要合理,刀刃要锋利,前刀面和切削刃的粗糙度要高,便于切屑的卷曲和折断,合理使用切削用量和转速使不锈钢材料的车削加工质量和生产效率都较高。本人文化水平有限缺乏经验望各位领导和导师批评指正。
参考资料:
1、《车工工艺学》任杏化科学普及出版社出版
2、《金属切削原理与刀具》李保成云南省机械工业厅
不锈钢的切削加工
1 什么是不锈钢? 通常,人们把含铬量大于12%或含镍量大于8%的合金钢叫不锈钢。这种钢在大气中或在腐蚀性介质中具有一定的耐蚀能力,并在较高温度(>450℃)下具有较高的强度。含铬量达16%~18%的钢称为耐酸钢或耐酸不锈钢,习惯上通称为不锈钢。 钢中含铬量达12%以上时,在与氧化性介质接触中,由于电化学作用,表面很快形成一层富铬的钝化膜,保护金属内部不受腐蚀;但在非氧化性腐蚀介质中,仍不易形成坚固的钝化膜。为了提高钢的耐蚀能力,通常增大铬的比例或添加可以促进钝化的合金元素,加Ni、Mo、Mn、Cu、Nb、Ti、W、Co等,这些元素不仅提高了钢的抗腐蚀能力,同时改变了钢的内部组织以及物理力学性能。这些合金元素在钢中的含量不同,对不锈钢的性能产生不同的影响,有的有磁性,有的无磁性,有的能够进行热处理,有的则不能热处理。 由于不锈钢所具有的上述特性,越来越广泛地应用于航空、航天、化工、石油、建筑和食品等工业部门及日常生活中。所含的合金元素对切削加工性影响很大,有的甚至很难切削。 2 不锈钢可分为哪几类? 不锈钢按其成分,可分为以铬为主的铬不锈钢和以铬、镍为主的铬镍不锈钢两大类。 工业上常用的不锈钢一般按金相组织分类,可分为以下五大类: 1.马氏体不锈钢:含铬量12%~18%,含碳量0.1%~0.5%(有时达1%),常见的有1Cr13、2 Cr13、3Cr13、4Cr13、1Cr17Ni2、9Cr18、9Cr18MoV、30Cr13Mo等。 2.铁素体不锈钢:含铬量12%~30%,常见的有0Cr13、0Cr17Ti、0Cr13Si4NbRE、1Cr17、1 Cr17Ti、1Cr17M02Ti、1Cr25Ti、1Cr28等。 3.奥氏体不锈钢:含络量12%~25%,含镍量7%~20%(或20%以上),最典型的代表是1Cr1 8Ni9Ti,常见的还有00Cr18Ni10、00Cr18Ni14Mo2Cu2、0Cr18Ni12Mo2Ti、0Cr18Ni18Mo2 Cu2Ti、0Cr23Ni28M03Cu3Ti、1Cr14Mn14Ni、2Cr13Mn9Ni4、1Cr18Mn8Ni5N等。 4.奥氏体+铁素体不锈钢:与奥氏体不锈钢相似,仅在组织中含有一定量的铁素体,常见的 有0Cr21Ni5Ti、1Cr21Ni5Ti、1Cr18Mn10Ni5M03N、0Cr17Mn13Mo2N、1Cr17Mn9Ni3M03Cu2 N、Cr2bNi17M03CuSiN、1Cr18Ni11Si4AlTi等。 5.沉淀硬化不锈钢:含有较高的铬、镍和很低的碳,常见的有0Cr17Ni4Cu4Nb、0Cr17Ni7A l、0Cr15Ni7M02Al等。 前两类为铬不锈钢,后三类为铬镍不锈钢。 3 不锈钢有哪些物理、力学性能? 1.马氏体不锈钢:能进行淬火,淬火后具有较高的硬度、强度和耐磨性及良好的抗氧化性, 有的有磁性,但内应力大且脆。经低温回火后可消除其应力,提高塑性,切削加工较困 难,有切屑擦伤或粘结的明显趋向,刀具易磨损。 当钢中含碳量低于0.3%时,组织不均匀,粘附性强,切削时容易产生积屑瘤,且断屑困难,工件已加工表面质量低。含碳量达0.4%~0.5%时,切削加工性较好。
数控车削加工工艺分析之我见的论文
数控车削加工工艺分析之我见的论文【摘要】数控车床的使用的目的旨在加工出合格的零件,但是合格的零件的加工必须要依靠制定合理的加工工艺。本文针对当前数控车床使用者的工艺分析的不合理来进行对比,讲述合理的工艺分析的顺序问题。 【关键词】数控车床车削加工工艺工艺分析车削 一、问题的提出 数控车削加工主要包括工艺分析、程序编制、装刀、装工件、对刀、粗加工、半精加工、精加工。而数控车削的工艺分析是数控车削加工顺利完成的保障。 数控车削加工工艺是采用数控车床加工零件时所运用的方法和技术手段的总和。其主要内容包括以下几个方面: (一)选择并确定零件的数控车削加工内容;(二)对零件图纸进行数控车削加工工艺分析;(三)工具、夹具的选择和调整设计;(四) 切削用量选择;(五)工序、工步的设计;(六)加工轨迹的计算和优化;(七)编制数控加工工艺技术文件。 笔者观察了很多数控车的技术工人,阅读了不少关于数控车削加工工艺的文章,发现大部分的使用者采用选择并确定零件的数控车削加工内容、零件图分析、夹具和刀具的选择、切削用量选择、划分工序及拟定加工顺序、加工轨迹的计算和优化、编制数控加工工艺技术文件的顺序来进行工艺分析。 但是笔者分析了上述的顺序之后,发现有点不妥。因为整个零件的工序、工步的设计是工艺分析这一环节中最重要的一部分内容。工序、工步的设计直接关系到能否加工出符合零件形位公差要求的零件。https://www.360docs.net/doc/7718064526.html,工序、工步的设计不合理将直接导致零件的形位公差达不到要求。换言之就是工序、工步的设计不合理直接导致产生次品。
二、分析问题 目前,数控车床的使用者的操作水平非常高,并且能够独立解决很多操作上的难题,但是他们的理论水平不是很高,这是造成工艺分析顺序不合理的主要原因。 造成工艺分析顺序不合理的另一个原因是企业的工量具设备不足。 三、解决问题 其实分析了工艺分析顺序不合理的现象和原因之后,解决问题就非常容易了。需要做的工作只要将对零件的分析顺序稍做调整就可 以。 笔者认为合理的工艺分析步骤应该是: (一)选择并确定零件的数控车削加工内容;(二)对零件图纸进行数控车削加工工艺分析;(三)工序、工步的设计;(四)工具、夹具的选择和调整设计;(五)切削用量选择; (六)加工轨迹的计算和优化;(七)编制数控加工工艺技术文件。 本文主要对二、三、四、五三个步骤进行详细的阐述。 (一)零件图分析 零件图分析是制定数控车削工艺的首要任务。主要进行尺寸标注方法分析、轮廓几何要素分析以及精度和技术要求分析。此外还应分析零件结构和加工要求的合理性,选择工艺基准。 1.选择基准 零件图上的尺寸标注方法应适应数控车床的加工特点,以同一基准标注尺寸或直接给出坐标尺寸。这种标注方法既便于编程,又有利于设计基准、工艺基准、测量基准和编程原点的统一。 2.节点坐标计算
不锈钢地车削加工
一切削难加工材料的综合分析 1.1不锈钢简介 通常,人们把含铬量大于12%或含镍量大于8%的合金钢叫不锈钢。这种钢在大气中或在腐蚀性介质中具有一定的耐蚀能力,并在较高温度(>450℃)下具有较高的强度。含铬量达16%~18%的钢称为耐酸钢或耐酸不锈钢,习惯上通称为不锈钢。 钢中含铬量达12%以上时,在与氧化性介质接触中,由于电化学作用,表面很快形成一层富铬的钝化膜,保护金属部不受腐蚀;但在非氧化性腐蚀介质中,仍不易形成坚固的钝化膜。为了提高钢的耐蚀能力,通常增大铬的比例或添加可以促进钝化的合金元素,加Ni、Mo、Mn、Cu、Nb、Ti、W、Co等,这些元素不仅提高了钢的抗腐蚀能力,同时改变了钢的部组织以及物理力学性能。这些合金元素在钢中的含量不同,对不锈钢的性能产生不同的影响,有的有磁性,有的无磁性,有的能够进行热处理,有的则不能热处理。 由于不锈钢所具有的上述特性,越来越广泛地应用于航空、航天、化工、石油、建筑和食品等工业部门及日常生活中。所含的合金元素对切削加工性影响很大,1.2不锈钢的分类 不锈钢按其成分,可分为以铬为主的铬不锈钢和以铬、镍为主的铬镍不锈钢两大类。工业上常用的不锈钢一般按金相组织分类,可分为以下五大类: 1)马氏体不锈钢:含铬量12%~18%,含碳量0.1%~0.5%(有时达1%),常见的有1Cr13、2Cr13、3Cr13、4Cr13、1Cr17Ni2、9Cr18、9Cr18MoV、30Cr13Mo等。 2)铁素体不锈钢:含铬量12%~30%,常见的有0Cr13、0Cr17Ti、0Cr13Si4NbRE、1Cr17、1Cr17Ti、1Cr17M02Ti、1Cr25Ti、1Cr28等。 3)奥氏体不锈钢:含络量12%~25%,含镍量7%~20%(或20%以上),最典型的代表是1Cr18Ni9Ti,常见的还有00Cr18Ni10、00Cr18Ni14Mo2Cu2、0Cr18Ni12Mo2
不锈钢加工刀具选择
不锈钢加工刀具选择 1.引言 随着航空、航天、石油、化工、冶金和食品等工业的蓬勃发展,不锈钢材料已得到广泛应用,而不锈钢材料由于韧性大、热强度高、导热系数低、切削时塑性变形大、加工硬化严重、切削热多、散热困难等原因,造成刀尖处切削温度高、切屑粘附刃口严重、容易产生积屑瘤,既加剧了刀具的磨损,又影响加工表面粗糙度。此外,由于切屑不易卷曲和折断,也会损伤已加工表面,影响工件的质量。为提高加工效率和工件质量,正确选择刀具材料、车刀几何参数和切削用量至关重要。 2.刀具材料的选择 正确选用刀具材料是保证高效率加工不锈钢的决定因素。根据不锈钢的切削特点,刀具材料应具备足够的强度、韧性、高硬度和高耐磨性且与不锈钢的粘附性要小。常用的刀具材料有硬质合金和高速钢两大类,形状复杂的刀具主要采用高速钢材料。由于高速钢切削不锈钢时的切削速度不能太高,因此影响生产效率的提高。对于较简单的车刀类刀具,刀具材料应选用强度高、导热性好的硬质合金,因其硬度、耐磨性等性能优于高速钢。常用的硬质合金材料有:钨钴类(YG3、YG6、YG8、YG3X、YG6X),钨钴钛类(YT30、YT15、YT14、YT5),通用类(YW1、YW2)。YG类硬质合金的韧性和导热性较好,不易与切屑粘结,因此适用于不锈钢粗车加工;而YW类硬质合金的硬度、耐磨性、耐热性和抗氧化性能以及韧性都较好,适合于不锈钢的精车加工。加工1Cr18Ni9Ti奥氏体不锈钢时,不宜选用YT类硬质合金,由于不锈钢中的Ti和YT类硬质合金中的Ti 产生亲合作用,切屑容易把合金中的Ti带走,促使刀具磨损加剧。 〕 3.刀具几何角度的选择 刀具切削部分的几何角度,对于不锈钢切削加工的生产率、刀具耐用度、被加工表面粗糙度、切削力以及加工硬化等方面都有很大的影响,合理选择和改进刀具几何参数是保证加工质量、提高效率、降低成本的有效途径。 (1)车刀前角γ0的选择 前角的大小决定刀刃的锋利与强度。增大前角可以减小切屑的变形,从而减小切削力和切削功率,降低切削温度,提高刀具耐用度。但是增大前角会使楔角减小,降低刀刃强度,造成崩刃,使刀具耐用度下降。车削不锈钢时,在不降低刀具强度的条件下,应把前角适当取大一些。在刀具前角大时其塑性变形小,切削力和切削热降低,减轻加工硬化趋势,提高刀具耐用度,一般刀具前角宜取12°~20°。
不锈钢螺纹的车削加工方法总结
不锈钢螺纹的车削加工方法全世界因锈蚀而消耗的金属制品约占金属产量的10%,因此提高金属抗蚀性和耐蚀性具有非常重要的意义。不锈钢能够达到相对较好的抗蚀要求,由起初的军用拓展到工业及民用各领域。因此,对各种复杂曲面的不锈钢工件要求量较大。但由于材质的特殊性,加工工艺成为制作产品的难题。 不锈钢材质本身的特殊性: 不同种类的不锈钢由于机械性能和化学成分的不同其数控 切削的难度也不相同。有的不锈钢在切削加工时,很难达到满意的加工表面粗糙度;而有的不锈钢,虽容易达到要求的加工表面粗糙度,但在切削加工过程中刀具却特别容易磨损。经总结,各类不锈钢很难切削的主要原因有以下几个方面: 热强度高、韧性大对数控高速切削不适应奥氏体类不锈钢与马氏体类不锈钢其硬度和抗拉强度不高,只相当于40 号钢,但延伸率、断面收缩率和冲击值却比较高。如 1Cr18Ni9Ti延伸率为40号钢的210%,这样在数控高速切削过程中就不容易被切断,切削变形时所消耗的功相当大。相对来说,不锈钢在高温下的强度降低较少,如45号钢在500°时其持久强度为7kg/mM2,而1Cr18Ni9Ti在550°时其持久强度仍保持在19~24kg /mM2。实践证明,在相同切削温度的作用下,不锈钢切削比普通碳素钢难加工,其热强
度高是一个极其重要的因素; 加工硬化趋势强对数控车削不利在数控高速车削的过 程中,由于刀尖对工件材料挤压的结果使切削区的金属产生变形,晶内发生滑移,晶格畸变,组织致密,机械性能也随着发生变化,一般切削硬度也能增加2~3倍。数控切削后加工硬化层深度可以从几十微米到几百微米不等,因此前一次走刀所产生的加工硬化现象又妨碍了下一次走刀时的切削,并且加工硬化层的高硬度导致刀具特别容易磨损; 切屑的粘附性强、导热差对数控切削有影响在数控切削过程中,切削碎屑很容易牢固地粘附或熔着在刀尖和刀刃上,形成积屑瘤,造成工件加工表面的表面粗糙度恶化,同时增加切削过程中的振动,加速刀具磨损。而且大量的切削热无法及时传导出来,甚至切削产生的热量也无法传导到切屑的整体上,造成传入刀具总热量比普通碳素钢多3~5倍,使切削刃在高温下失去切削性能。在数控切削过程中,所产生的大量热能未能迅速排出,必然会传递给刀具,使切削部位温度升高。同时由于排屑比较困难,尤其是不断屑,使被切削下来的切屑产生挤塞,特别是加工内孔,切屑挤塞更加严重。另外,刀具因受螺纹截面形状的限制,再加之本身强度较差,加工中容易产生振动,刀尖很容易在切削过程中由于局部温度过高而烧坏或因振动太大而崩裂。 数控切削不锈钢刀具的问题及解决对策
普通车床加工的结构和操作流程
普通车床加工的结构和操作流程 普通车床结构 CA6140型普通车床的主要组成部件有:主轴箱、进给箱、溜板箱、刀架、尾架、光杠丝杠和床身。 主轴箱:又称床头箱,它的主要任务是将主电机传来的旋转运动经过一系列的变速机构使主轴得到所需的正反两种转向的不同转速,同时主轴箱分出部分动力将运动传给进给箱。主轴箱中等主轴是车床的关键零件。主轴在轴承上运转的平稳性直接影响工件的加工质量,一旦主轴的旋转精度降低,则机床的使用价值就会降低。 进给箱:又称走刀箱,进给箱中装有进给运动的变速机构,调整其变速机构,可得到所需的进给量或螺距,通过光杠或丝杠将运动传至刀架以进行切削。 丝杠与光杠:用以联接进给箱与溜板箱,并把进给箱的运动和动力传给溜板箱,使溜板箱获得纵向直线运动。丝杠是专门用来车削各种螺纹而设置的,在进工件的其他表面车削时,只用光杠,不用丝杠。同学们要结合溜板箱的内容区分光杠与丝杠的区别。 溜板箱:是车床进给运动的操纵箱,内装有将光杠和丝杠的旋转运动变成刀架直线运动的机构,通过光杠传动实现刀架的纵向进给运动、横向进给运动和快速移动,通过丝杠带动刀架作纵向直线运动,以便车削螺纹。刀架、尾架和床身。 普通车床附件 1.三爪卡盘(用于圆柱形工件),四爪卡盘(不规则工件) 2.活顶尖(用于固定加工件) 3.中心架(稳定加工件) 4.跟刀架 SAJ普通车床变频器应用的主要特点 1、低频力矩大、输出平稳 2、高性能矢量控制 3、转矩动态响应快、稳速精度高 4、减速停车速度快 5、抗干扰能力强 普通车床操作规程 1.开车前的检查 1.1根据机床润滑图表加注合适的润滑油脂。 1.2检查各部电气设施,手柄、传动部位、防护、限位装置齐全可靠、灵活。 1.3各档应在零位,皮带松紧应符合要求。 1.4床面不准直接存放金属物件,以免损坏床面。 1.5被加工的工件、无泥砂、防止泥砂掉入拖板内、磨坏导轨。 1.6未夹工件前必须进行空车试运转,确认一切正常后,方能装上工件。 2.普通车床操作程序 2.1上好工件,先起动润滑油泵,使油压达到机床的规定,方可开动。 2.2调整交换齿轮架,调挂轮时,必须切断电源,调好后,所有螺栓必须紧固,扳手应及时取下,并脱开工件试运转。 2.3装卸工件后,应立即取下卡盘扳手和工件的浮动物件。 2.4机床的尾架、摇柄等按加工需要调整到适当位置,并紧固或夹紧。 2.5工件、刀具、夹具必须装卡牢固。浮动力具必须将引刀部分伸入工件,方可启动机床。
不锈钢加工参数
不锈钢切削加工 不锈钢切削加工摘要:螺纹类零件10的数控车床加工编程NUM公司力推新一代Axium Power 数控系统数控铣削的编程与工艺分析基于细胞神经网络刀具磨损图像处理的研究中国最大乙烯装置的裂解气压缩机试车成功发动机盲孔除切屑机的研制与应用在不断变化时代的工具钢加工什么是智能变送器?机械故障的形成及其特性分析数控车间(机床)集成管理技术及产品浅谈CAD的特征造型技术轴承钢的表面强化方法如何进行电话销售?拉刀齿距及同时工作齿数的确定大型水轮机叶片的多轴联动数控加工编程技术张晓静:计算机在冲压领域的应用 PLC位控单元在精密磨削控制中的应用硬质材料铣削技术 CAD技术发展趋势数控机床软件界面人的因素分析 [标签:tag] 1 什么是不锈钢?通常,人们把含铬量大于12%或含镍量大于8%的合金钢叫不锈钢。这种钢在大气中或在腐蚀性介质中具有一定的耐蚀能力,并在较高温度(450℃)下具有较高的强度。含铬量达16%~18%的钢称为耐酸钢或耐酸不锈钢,习惯上通称为不锈钢。钢中含铬量达12%以上时,. 1?什么是不锈钢? 通常,人们把含铬量大于12%或含镍量大于8%的合金钢叫不锈钢。这种钢在大气中或在腐蚀性介质中具有一定的耐蚀能力,并在较高温度(>450℃)下具有较高的强度。含铬量达16%~18%的钢称为耐酸钢或耐酸不锈钢,习惯上通称为不锈钢。 钢中含铬量达12%以上时,在与氧化性介质接触中,由于电化学作用,表面很快形成一层富铬的钝化膜,保护金属内部不受腐蚀;但在非氧化性腐蚀介质中,仍不易形成坚固的钝化膜。为了提高钢的耐蚀能力,通常增大铬的比例或添加可以促进钝化的合金元素,加Ni、Mo、Mn、Cu、Nb、Ti、W、Co等,这些元素不仅提高了钢的抗腐蚀能力,同时改变了钢的内部组织以及物理力学性能。这些合金元素在钢中的含量不同,对不锈钢的性能产生不同的影响,有的有磁性,有的无磁性,有的能够进行热处理,有的则不能热处理。 由于不锈钢所具有的上述特性,越来越广泛地应用于航空、航天、化工、石油、建筑和食品等工业部门及日常生活中。所含的合金元素对切削加工性影响很大,有的甚至很难切削。2?不锈钢可分为哪几类? 不锈钢按其成分,可分为以铬为主的铬不锈钢和以铬、镍为主的铬镍不锈钢两大类。 工业上常用的不锈钢一般按金相组织分类,可分为以下五大类: 马氏体不锈钢:含铬量12%~18%,含碳量0.1%~0.5%(有时达1%),常见的有1Cr13、2Cr13、3Cr13、4Cr13、1Cr17Ni2、9Cr18、9Cr18MoV、30Cr13Mo等。?铁素体不锈钢:含铬量12%~30%,常见的有0Cr13、0Cr17Ti、0Cr13Si4NbRE、1Cr17、1Cr17Ti、1Cr17M02Ti、1Cr25Ti、1Cr28等。?奥氏体不锈钢:含络量12%~25%,含镍量7%~20%(或20%以上),最典型的代表是1Cr18Ni9Ti,常见的还有00Cr18Ni10、00Cr18Ni14Mo2Cu2、0Cr18Ni12Mo2Ti、0Cr18Ni18Mo2Cu2Ti、0Cr23Ni28M03Cu3Ti、1Cr14Mn14Ni、2Cr13Mn9Ni4、1Cr18Mn8Ni5N等。?奥氏体铁素体不锈钢:与奥氏体不锈钢相似,仅在组织中含有一定量的铁素体,常见的有0Cr21Ni5Ti、1Cr21Ni5Ti、1Cr18Mn10Ni5M03N、0Cr17Mn13Mo2N、1Cr17Mn9Ni3M03Cu2N、Cr2bNi17M03CuSiN、1Cr18Ni11Si4AlTi等。?沉淀硬化不锈钢:含有较高的铬、镍和很低的碳,常见的有0Cr17Ni4Cu4Nb、0Cr17Ni7Al、0Cr15Ni7M02Al等。 前两类为铬不锈钢,后三类为铬镍不锈钢。 3?不锈钢有哪些物理、力学性能? 马氏体不锈钢:能进行淬火,淬火后具有较高的硬度、强度和耐磨性及良好的抗氧化性,有的有磁性,但内应力大且脆。经低温回火后可消除其应力,提高塑性,切削加工较困难,有切屑擦伤或粘结的明显趋向,刀具易磨损。 当钢中含碳量低于0.3%时,组织不均匀,粘附性强,切削时容易产生积屑瘤,且断屑困难,
数控车床加工工艺分析
数控车床加工工艺分析 摘要:随着数控加工的日益成熟越来越多的零件产品都用数控机床来加工,因此如何改进数控加工的工艺问题就越来越重要。在数控机床上由于机床空间及机床的其他局限了数控加工的灵活性,这样就要求我们要懂得如何改进加工工艺,提高数控机床的应用范围和加工性能。从而达到提高生产效率和产品质量。 关键词:数控加工加工工艺薄壁套管、护轴 前言:数控加工作为一种高效率高精度的生产方式,尤其是形状复杂精度要求很高的模具制造行业,以及成批大量生产的零件。因此数控加工在航空业、电子行业还有其他各行业都广泛应用。然而在数控加工从零件图纸到做出合格的零件需要有一个比较严谨的工艺过程,必须合理安排加工工艺才能快速准确的加工出合格的零件来,否则不但浪费大量的时间,而且还增加劳动者的劳动强度,甚至还会加工出废品来。下面我将结合某一生产实例对数控加工的工艺进行分析。以便帮助大家进一步了解数控加工,对实际加工起到帮助作用。 一般数控机床的加工工艺和普通机床的加工工艺是大同小异的,只是数控机床能够通过程序自动完成普通机床的加工动作,减轻了劳动者的劳动强度,同时能比较精准的加工出合格的零件。由于数控加工整个加工过程都是自动完成的,因此要求我们在加工零件之前就必须把整个加工过程有一个比较合理的安排,其中不能出任何的差错,
否则就会产生严重的后果。 1、1 零件图样分析 因为薄壁加工比较困难,尤其是内孔的加工,由于在切削过程中,薄壁受切削力的作用,容易产生变形。从而导致出现椭圆或中间小,两头大的“腰形”现象。另外薄壁套管由于加工时散热性差,极易产生热变形,使尺寸和形位误差。达不到图纸要求,需解决的重要问题,是如何减小切削力对工件变形的影响。薄壁零件的加工是车削中比较棘手的问题,原因是薄壁零件刚性差,强度弱,在加工中极容易变形,使零件的形位误差增大,不易保证零件的加工质量。可利用数控车床高加工精度及高生产效率的特点,并充分地考虑工艺问题对零件加工质量的影响,为此对工件的装夹、刀具几何参数、程序的编制等方面进行试验,有效地克服薄壁零件加工过程中出现的变形,保证了加工精度,为今后更好的加工薄壁零件提供了好的依据及借鉴。 无论用什么形式加工零件,首先都必须从查看零件图开始。由图看见该薄壁零件加工,容易产生变形,这里不仅装夹不方便,而且所要加工的部位也那难以加工,需要设计一专用薄壁套管、护轴。
不锈钢车削方法
1切削过程中的难点及原因分析 在零件试生产时,我们按车削普通碳钢的工艺方法对3Cr13不锈钢进行了车削试验,结果是刀具磨损非常严重,生产率极低,零件表面质量达不到要求。 比较3Cr13钢与40钢、45钢等碳素结构钢的机械性能可知,3Cr1 3钢的强度比40钢和45钢高,它是一种强度高、塑性好的中碳马氏体不锈钢。由于切削时加工硬化严重,切削抗力大,切削温度高,导致刀具磨损严重,磨刀次数增多,增加了停机时间和机床调整时间,降低了生产率。同时又容易粘刀,产生积屑瘤,引起工件尺寸的变化并影响表面粗糙度,而且切屑不易卷曲和折断,易损伤工件已加工表面,影响零件质量。所以,不能用切削45钢的工艺来切削3Cr13,也不能把通用车床上的加工方法照搬到自动车床上来。因为一般自动车床装刀较少,要求最好一次走刀就能使被加工表面达到要求的尺寸和表面粗糙度,以保证较高的生产率。 2主要技术措施 1. 通过热处理,改变材料的硬度 马氏体不锈钢在热处理后的不同硬度,对车削加工的影响很大。表1是用YW2材料的车刀对热处理后不同硬度的3Cr13钢的车削情况。可见,退火状0.10.10.1态的马氏体不锈钢虽然硬度低,但车削性能差,这是因为材料塑性和韧性大,组织不均匀,粘附,熔着性强,切削过程易产生刀瘤,不易获得较好的表面质量。而调质处理后硬度在HRC30以下的3Cr13材料,车削加工性较好,易达到较好的表面质量。用硬度在HRC30以上的材料加工出的零件,表面质量虽然较好,但刀具易磨损。所以,在条件允许的情况下,可以在材料进厂后,先进行调质处理,硬度达到HRC25~HRC30,然后再进行切削加工。 表1 3Cr13钢材料切削用 量刀具 耐用 度 min 加工表 面粗糙 度 μm ν m/ mi n s m m /r HB240(退火)45 ~ 55 . 1 90~ 115 Ra6.3~ Ra3.2 HRC25~30(调质)45 ~ 55 . 1 95~ 110 Ra3.2 HRC35~38(调质)45 ~ 55 . 1 60~ 75 Ra3.2 2. 刀具材料的选择 在自动车床上车削不锈钢,一般使用的硬质合金的刀具材料有:YG6、YG8、YT15、YT30、YW1、YW2等材料。 常用的高速钢刀具有:W18Cr4V、W6M05Cr4V2AL等材料。我们在切削参数相同的条件
如何解决不锈钢螺纹车削问题
如何解决不锈钢螺纹车削问题 螺纹是机械工程中常见的几何特征之一, 应用广泛。螺纹的加工工艺较多, 如基于塑性变形的滚丝与搓丝, 基于切削加工的车削、铣削、攻螺纹与套螺纹、螺纹磨削、螺纹研磨等。 不同种类的不锈钢由于机械性能和化学成分的不同,其数控切削的难度也不相同。有的不锈钢在切削加工时,很难达到满意的加工表面粗糙度;而有的不锈钢,虽容易达到要求的加工表面粗糙度,但在切削加工过程中刀具却特别容易磨损。经总结,各类不锈钢很难切削的主要原因有以下几个方面: 1 热强度高、韧性大 奥氏体类不锈钢与马氏体类不锈钢其硬度和抗拉强度不高,只相当于40号钢,但延伸率、断面收缩率和冲击值却比较高,这样在数控高速切削过程中就不容易被切断,切削变形时所消耗的功相当大。相对来说,不锈钢在高温下的强度降低较少,如45号钢在500°时其持久强度为7kg/mm2,而1Cr18Ni9Ti在550°时其持久强度仍保持在19——24kg/mm2。实践证明,在相同切削温度的作用下,不锈钢切削比普通碳素钢难加工,其热强度高是一个极其重要的因素。 2 加工硬化趋势强 在数控高速车削的过程中,由于刀尖对工件材料挤压的结果使切削区的金属产生变形,晶内发生滑移,晶格畸变,组织致密,机械性能也随着发生变化,一般切削硬度也能增加2——3倍。数控切削后加工硬化层深度可以从几十微米到几百微米不等,因此前一次走刀
所产生的加工硬化现象又妨碍了下一次走刀时的切削,并且加工硬化层的高硬度导致刀具特别容易磨损。 3 切屑的粘附性强、导热差 在数控切削过程中,切削碎屑很容易牢固地粘附或熔着在刀尖和刀刃上,形成积屑瘤,造成工件加工表面的表面粗糙度恶化,同时增加切削过程中的振动,加速刀具磨损。而且大量的切削热无法及时传导出来,甚至切削产生的热量也无法传导到切屑的整体上,造成传入刀具总热量比普通碳素钢多3——5倍,使切削刃在高温下失去切削性能。在数控切削过程中,所产生的大量热能未能迅速排出,必然会传递给刀具,使切削部位温度升高。同时由于排屑比较困难,尤其是不断屑,使被切削下来的切屑产生挤塞,特别是加工内孔,切屑挤塞更加严重。另外,刀具因受螺纹截面形状的限制,再加之本身强度较差,加工中容易产生振动,刀尖很容易在切削过程中由于局部温度过高而烧坏或因振动太大而崩裂。 4 螺纹粗糙度差的原因及对策 数控切削后螺纹表面粗糙度太差,鱼鳞斑状波纹及啃刀现象是不锈钢螺纹车削中最常遇到的现象,产生这些现象的原因有: (1)螺纹车刀两侧刃后角太小,两侧刃与后面的螺纹表面相摩擦使加工表面恶化,加工时必须考虑螺纹旋转角对两侧刃实际后角的影响。 螺纹车刀的前角太小,刃口不够锋利,切屑不能顺利地被切断,而是部分地被挤压或撕裂下来,必定造成螺纹表面非常粗糙。当前角太大时,刀刃强度削弱且容易磨损、崩裂、扎刀,更容易引起振动而使螺纹表面产生波纹。因此,应根据不锈钢的不同材质选择适当的前角。车削耐浓硫酸用不锈钢螺纹时,应比车削2Cr13不锈钢螺纹采用较小的前角,车
不锈钢零件机加工工艺
不锈钢零件机加工工艺 1不锈钢材料加工难点 1.1切削力大,切削温度高 该类型材料强度大,切削时切向应力大、塑性变形大,因而切削力大。此外材料导热性极差,造成切削温度升高,且高温往往集中在刀具刃口附近的狭长区域内,从而加快了刀具的磨损。 1.2加工硬化严重 奥氏体不锈钢以及一些高温合金不锈钢均为奥氏体组织,切削时加工硬化倾向大,通常是普通碳素钢的数倍,刀具在加工硬化区域内切削,使刀具寿命缩短。 1.3容易粘刀 论是奥氏体不锈钢还是马氏体不锈钢均存在加工时切屑强韧、切削温度很高的特点。当强韧的切屑流经前刀面时,将产生粘结、熔焊等粘刀现象,影响加工零件表面粗糙度。 1.4刀具磨损加快 上述材料一般含高熔点元素、塑性大,切削温度高,使刀具磨损加快,磨刀、换刀频繁,从而影响了生产效率,提高了刀具使用成本。 2 不锈钢零件加工工艺 通过上述加工难点分析,不锈钢的加工工艺及相关刀具参数设计与普通结构钢材料应具有较大的不同,其具体加工工艺如下: 2.1钻孔加工 在钻孔加工时,由于不锈钢材料导热性能差,弹性模量小,孔加工起来也比较困难。解决此类材料的孔加工难题,主要是选用合适的刀具材料,确定合理的刀具的几何参数以及刀具的切削用量。钻削上述材料时,钻头一般应选用W6Mo5Cr4V2Al、W2Mo9Cr4Co8等材质的钻头,这些材质钻头缺点是价格比较昂贵,而且难以采购。而采用常用的W18Cr4V普通标准高速钢钻头钻孔时,由于存在顶角较小、切屑太宽而不能及时排出孔外、切削液不能及时冷却钻头等缺点,再加上不锈钢材料导热性差,造成集中在刀刃上的切削温度升高,容易导致两个后刀面和主刃烧伤及崩刃,使钻头的使用寿命降低。 (1)刀具几何参数设计在采用W18Cr4V普通高速钢钻头钻孔时,切削力及切削温度均集中在钻尖上,为提高钻头切削部位的耐用度,可以适当增大顶角角度,顶角一般选135°~140°,顶角增大也将使外缘前角减小,钻屑变窄,以利于排屑。但是加大顶角后,钻头的横刃变宽,造成切削阻力增大,因而必须对钻头横刃进行修磨,修磨后横刃的斜角为47°~55°,横刃前角为3°~5°,修磨横刃时,应将切削刃与圆柱面转角处修磨成圆角,以增加横刃强度。由于不锈钢材料弹性模量较小,切屑层下的金属弹性恢复大,加之加工过程中加工硬化严重,后角太小会加快钻头后刀面的磨损,而且增加了切削温度,降低钻头的寿命。因此须适当加大后角,但后角太大,将使钻头的主刃变得单薄,减小了主刃的刚性,所以后角应以12°~15°为宜。为使钻屑变窄,利于排屑,还需要在钻头两个后刀面上开交错分布的分屑槽。 (2)切削用量选择钻削时,切削用量的选择应从降低切削温度的基本点出发,因为高速切削将会使切削温度升高,而高的切削温度将加剧刀具磨损,因而切削用量中最重要的是选择切削速度。一般情况下,切削速度以12~15m/min较为合适。进给量对刀具寿命影响较小,但进给量选择太小将会使刀具在硬化层内切削,加剧磨损;而进给量如果太大,又会使表面粗糙度变差。综合上述两个因素,进给量选择为0.32~0.50mm/r为宜。 (3)切削液选择钻削时,为降低切削温度,可采用乳化液作为冷却介质。 2.2铰孔加工 (1)刀具几何参数设计不锈钢材料的铰削加工大部分使用硬质合金铰刀。铰刀的结构和几何参数与普通铰刀有所不同。为增强刀齿强度并防止铰削时产生切屑堵塞现象,铰刀齿数一般比较少。铰刀前角一般为8°~12°,但在某些特定情况,为了实现高速铰削,也可采用0°~
数控加工工艺毕业设计论文
日照职业技术学院毕业设计(论文) 数控加工工艺 姓名 : 付卫超 院部:机电工程学院 专业:数控设备应用与维护 指导教师:张华忠 班级: 11级数控设备应用与维护二班 2014年05月
随着数控技术的不断发展和应用领域的扩大,数控加工技术对国计民生的一些重要行业(IT、汽车、轻工、医疗等)的发展起着越来越重要的作用,因为效率和质量是先进制造技术的主体。高速、高精加工技术可极大提高效率,提高产品的质量和档次,缩短生产周期和提高市场竞争能力。而对于数控加工,无论是手工编程还是自动编程,在编程前都要对所加工的零件进行工艺分析,拟定加工方案,选择合适的刀具,确定切屑用量,对一些工艺问题(如对刀点、加工路线等)也需要做一些处理,并在加工过程掌握控制精度的方法,才能加工出合格的产品。 本文根据数控机床的特点。针对具体的零件,进行了工艺方案的分析,工装方案的确定,刀具和切屑用量的选择,确定加工顺序和加工路线,数控加工程序编制。通过整个工艺的过程的制定,充分体现了数控设备在保证加工精度、加工效率、简化工序等方面的优势。 关键词工艺分析加工方案进给路线控制尺寸
第1章前言-----------------------------------第2页第2章工艺方案的分析-------------------------第3页 2.1 零件图-------------------------------第3页 2.2 零件图分析---------------------------第3页 2.3 零件技术要求分析---------------------第3页 2.4 确定加工方法-------------------------第3页 2.5 确定加工方案-------------------------第4页第3章工件的装夹-----------------------------第5页 3.1 定位基准的选择-----------------------第5页 3.2 定位基准选择的原则-------------------第5页 3.3 确定零件的定位基准-------------------第5页 3.4 装夹方式的选择-----------------------第5页 3.5 数控车床常用的装夹方式---------------第5页 3.6 确定合理装夹方式---------------------第5页第4章刀具及切削用量-------------------------第6页 4.1 选择数控刀具的原则-------------------第6页 4.2 选择数控车削刀具---------------------第6页 4.3 设置刀点和换刀点---------------------第6页 4.4 确定切削用量-------------------------第7页第5章轴类零件的加工-------------------------第8页 5.1 轴类零件加工工艺分析-----------------第8页 5.2 轴类零件加工工艺---------------------第11页 5.3 加工坐标系设置-----------------------第13页 5.4 保证加工精度方法---------------------第14页 参考文献 ---------------------------------第15页
不锈钢法兰加工方法
不锈钢法兰加工方法 对刀具几何参数的要求: 加工不锈钢时,刀具切削部分的几何形状,一般应从前角、后角方面的选择来考虑。在选择前角时,要考虑卷屑槽、有无倒棱和刃倾角的正负角度大小等因素。不论何种刀具,加工不锈钢时都必须采用较大的前角。增大刀具的前角可减小切屑切离和清出过程中所遇到的阻力。对后角选择要求不十分严格,但不宜过小,后角过小容易和工件表面产生严重摩擦,使加工表面粗糙度恶化,加速刀具磨损。并且由于强烈摩擦,增强了不锈钢表面加工硬化的效应;刀具后角也不宜过大,后角过大,使刀具的楔角减小,降低了切削刃的强度,加速了刀具的磨损。通常,后角应比加工普通碳钢时适当大些。对刀具切削部分表面粗糙度的要求: 提高刀具切削部分的表面光洁度可减少切屑形成卷曲时的阻力,提高刀具的耐用度。与加工普通碳钢相比较,加工不锈钢时应适当降低切削用量以减缓刀具磨损;同时还要选择适当的冷却润滑液,以便降低切削过程中的切削热和切削力,延长刀具的使用寿命。对刀杆材料的要求 加工不锈钢时,由于切削力较大,故刀杆必须具备足够的强度和刚性,以免在切削过程中发生颤振和变形。这就要求选用适当大的刀杆截面积,同时还应采用强度较高的材料来制造刀杆,如采用调质处理的45号钢或50号钢。对刀具切削部分材料的要求:加工不锈钢时,要求刀具切削部分的材料具有较高的耐磨性,并能在较高的温度下保持其切削性能。目前常用的材料有:高速钢和硬质合金。由于高速钢只能在600°C以下保持其切削性能,因此不宜用于高速切削,而只适用于在低速情况下加工不锈钢。由于硬质合金比高速钢具有更好的耐热性和耐磨性,因此用硬质合金材料制成的刀具更适合不锈钢的切削加工。硬质合金分钨钴合金(YG)和钨钴钛合金(YT)两大类。钨钴类合金具有良好的韧性,制成的刀具可以采用较大的前角与刃磨出较为锋利的刃口,在切削过程中切屑易变形,切削轻快,切屑不容易粘刀,所以在一般情况下,用钨钴合金加工不锈钢比较合适。特别是在振动较大的粗加工和断续切削加工情况下更应采用钨钴合金刀片,它不象钨钴钛合金那样硬脆,不易刃磨,易崩刃。钨钴钛合金的红硬性较好,在高温条件下比钨钴合金耐磨,但它的脆性较大,不耐冲击、振动,一般作不锈钢精车用刀具。 2刀具材料牌号的选择刀具材料的切削性能关系着刀具的耐用度和生产率,刀具材料的工艺性影响着刀具本身的制造与刃磨质量。宜选择硬度高、抗粘结性和韧性好的刀具材料,如YG类硬质合金,最好不要选用YT类硬质合金,尤其是在加工1Gr18Ni9Ti奥氏体不锈钢应绝对避免选用YT类硬质合金,因为不锈钢中的钛(Ti)和YT类硬质合金中的Ti产生亲合作用,切屑容易把合金中的Ti带走,促使刀具磨损加剧。生产实践表明,选用YG532、YG813及YW2三种牌号材料加工不锈钢具有较好的加工效果,,三种硬质合金牌号的性能比较牌号密度g/cm3抗弯强度Mpa硬度HRA性能即用途相当于ISO YG532 14≥1760≥91.5红硬性高,韧性好,抗粘能力强,适用于奥氏体、马氏体不锈钢、无磁钢、高温合金钢等大型工件的粗、精加工;合金耐用度高,高温性好,被加工工件表面质量高。K10~K20M20 YG813 14.05~14.1≥1570≥91耐磨性好,有较高的抗弯强度和抗粘结能力,适于高温合金钢;对容易产生加工冷作硬化现象的奥氏体不锈钢、高锰钢等,加工效果优于YW2。K10~K20M20 YW2 12.4~13.5≥1320≥90.5使用强度高,红硬性较好,能承受较大的冲击载荷。适用于耐热钢、高锰钢、不锈钢等材料的粗、精加工。3刀具几何参数的选择前角的选择:从切
不锈钢的切削加工总结
不锈钢的切削加工 在不锈钢的切削加工中,首先要对被加工件的被切削性能有所了解,不锈钢在切削过程中有如下几方面特点: 1. 加工硬化严重:在不锈钢中,以奥氏体和奥氏体+铁素体不锈钢的加工硬化现象最为突出。因为不锈钢的塑性大,塑性变形时晶格歪扭,强化系数很大;且奥氏体不够稳定,在切削应力的作用下,部分奥氏体会转变为马氏体;再加上化合物杂质在切削热的作用下,易于分解呈弥散分布,使切削加工时产生硬化层。 2. 切削力大:不锈钢在切削过程中塑性变形大,尤其是奥氏体不锈钢(其伸长率超过45号钢的1.5倍以上),使切削力增加。同时,不锈钢的加工硬化严重,热强度高,进一步增大了切削抗力,切屑的卷曲折断也比较困难。 3. 切削温度高:切削时塑性变形及与刀具间的摩擦都很大,产生的切削热多;大量切削热都集中在切削区和刀削接触的界面上,散热条件差。在相同的条件下切削温度比45号钢高200℃左右。 4. 切削不易折断、易粘结:不锈钢的塑性、韧性都很大,在高温、高压下,不锈钢与其他金属的亲和性强,易产生粘附现象,并形成积削瘤,既加剧刀具磨损,又会出现撕扯现象而使已加工表面恶化。含碳量较低的马氏体不锈钢的这一特点更为明显。 5. 刀具易磨损:切削不锈钢过程中的亲和作用,使刀削间产生粘结、扩散,从而使刀具产生粘结磨损、扩散磨损,致使刀具前刀面产生月牙洼,切削刃还会形成微小的剥落和缺口;加上不锈钢中的碳化物(如TiC)微粒硬度很高,
切削时直接与刀具接触、摩擦,擦伤刀具,还有加工硬化现象,均会使刀具磨损加剧。 切削不锈钢时应怎样选择刀具的材料: 合理选择刀具材料是保证高效率切削加工不锈钢的重要条件。根据不锈钢的切削特点,要求刀具材料应具有耐热性好、耐磨性高、与不锈钢的亲和作用小等特点,YG类硬质合金的韧性较好,可采用较大的前角,刀刃也可以磨得锋利些,使切削轻快,且切屑与刀具不易产生粘结,较适于加工不锈钢。另外,YG类合金的导热性较好,其导热系数比高速钢高将近两倍,比YT类合金高一倍。 切削不锈钢时怎样选择刀具几何参数? 前角:不锈钢的硬度、强度并不高,但其塑性、韧性都较好,热强性高,切削时切屑不易被切离。在保证刀具有足够强度的前提下,应选用较大的前角,这样不仅能够减小被切削金属的塑性变形,而且可以降低切削力和切削温度,同时使硬化层深度减小。 后角:加大后角能减小后刀面与加工表面的摩擦,但会使切削刃的强度和散热能力降低。后角的合理值取决于切削厚度,切削厚度小时,宜选较大后角,我们三轨由于切削量大,所以选用20°的后角。 选择合适的涂层对于金属切削来说能起到非常重要的作用,TiAICRN(碳氮化铝钛)涂层在不锈钢切削加工中起着非常重要的作用涂层材料作为化学屏障和热屏障,减小了月牙洼磨损,耐磨性良好。与未涂层刀具相比,涂层刀具加工精度提高0.5~1级,刀具消耗费用降低20%~50%,耐磨性提高2~10倍,切削速度提高25%~70%,使用寿命延长3~5倍。
不锈钢加工的难点及对策
不锈钢加工的难点及对策 1 切削过程中的难点及原因分析 在零件试生产时,我们按车削普通碳钢的工艺方法对3Cr13不锈钢进行了车削试验,结果是刀具磨损非常严重,生产率极低,零件表面质量达不到要求。比较3Cr13钢与40钢、45钢等碳素结构钢的机械性能可知,3Cr1 3钢的强度比40钢和45钢高,它是一种强度高、塑性好的中碳马氏体不锈钢。由于切削时加工硬化严重,切削抗力大,切削温度高,导致刀具磨损严重,磨刀次数增多,增加了停机时间和机床调整时间,降低了生产率。同时又容易粘刀,产生积屑瘤,引起工件尺寸的变化并影响表面粗糙度,而且切屑不易卷曲和折断,易损伤工件已加工表面,影响零件质量。所以,不能用切削45钢的工艺来切削3Cr13,也不能把通用车床上的加工方法照搬到自动车床上来。因为一般自动车床装刀较少,要求最好一次走刀就能使被加工表面达到要求的尺寸和表面粗糙度,以保证较高的生产率。 2 主要技术措施 1.通过热处理,改变材料的硬度 马氏体不锈钢在热处理后的不同硬度,对车削加工的影响很大。表1是用YW2材料的车刀对热处理后不同硬度的3Cr13钢的车削情况。可见,退火状0.10.10.1态的马氏体不锈钢虽然硬度低,但车削性能差,这是因为材料塑性和韧性大,组织不均匀,粘附,熔着性强,切削过程易产生刀瘤,不易获得较好的表面质量。而调质处理后硬度在HRC30以下的3Cr13材料,车削加工性较好,易达到较好的表面质
量。用硬度在HRC30以上的材料加工出的零件,表面质量虽然较好,但刀具易磨损。所以,在条件允许的情况下,可以在材料进厂后,先进行调质处理,硬度达到HRC25~HRC30,然后再进行切削加工。 表1 3Cr13钢材料 切削用量 刀具耐用度 min 加工表面粗糙度 μm ν m/min s mm/r HB240(退火) 45~55 0.1 90~115 Ra6.3~Ra3.2 HRC25~30(调质) 45~55 0.1
车削工艺流程
车削工艺流程 1.模具的准备,把从烘干箱里取出冷却后的成型模具用专用 工具(简称板卡)使模具头与模具盒分离、清理干净放在盛器里(以下 简称半成品)。 2.车床的准备,在空压机正常工作的情况下,运作机床空转 5到10分钟,目的是磨合机器将机器气阀、控制器中可能残留的余 压释放(简称预热)。预热结束后是车削铜头,取掏过丝的铜棒一枚,旋进车床上拧紧。用普通刀头换下单晶片刀头,运转机器。以剖开 的半成品为样本车削铜棒直至得到匹配的铜头(目前的匹配要求是用 手能够轻松套上、用手取时费劲但是可以取下、机器能够轻松取下)。再用单晶片换下普通刀头。 3.调试运行,将半成品倒入自动上料池里。取一颗半成品嵌 进铜头,如果知道上一次加工的半成品度数,就以上次度数加工参 数为基准调试机器。如果不知道上一次的参数,就运转车床加工一 个以这个加工过的半成品的参数为基准调试机器。调试结束后,转 自动试做几个,选第三个、第五个(跟个人习惯)检查参数是否和预 设参数一致(因为是气动多少会有出入这里都是取接近值。干片参数 区间: 度数+0.15 -0.1 透光区直径±0.5中心厚度±0.5边 缘厚度极点落差≤2,除度数外单位均是0.01㎜)。如果一致运转 机器转自动开始正式加工。如果不一致把第一、二、四个加工后的 半成品也检测一下,如果都与预设参数不一致且前者一致,就以前 者参数为基准调试机器,重复前一步奏;如果都与预设参数不一致 且出入浮动很大(一般没有这种情况),检查气压是否稳定,自动上 料机器运转有没有异常,工作台有没有被异物卡住,观察刀头运行 轨迹是否合理找出问题所在。解决问题后重新调试机器检验参数直 至参数一致转自动开始加工。 4.抽验,车床转自动开始加工运行中,随机抽验(数量没有一 定一般是每100个抽验1到2个)车削过的半成品的参数和当前度数 的标准参数是否一致。如果一致继续生产;如果不一致取最新一颗 加工过的半成品检验参数与前者参数对比。如果一致关闭机器退回 到步奏3以当前镜片参数为基准重新调试机器;如果不一致且与当 前度数镜片标准参数也不一致关闭机器退回步奏3以当前镜片参数 为基准重新调试机器,反之继续运转机器生产。 (完)