挖掘机动臂强度分析
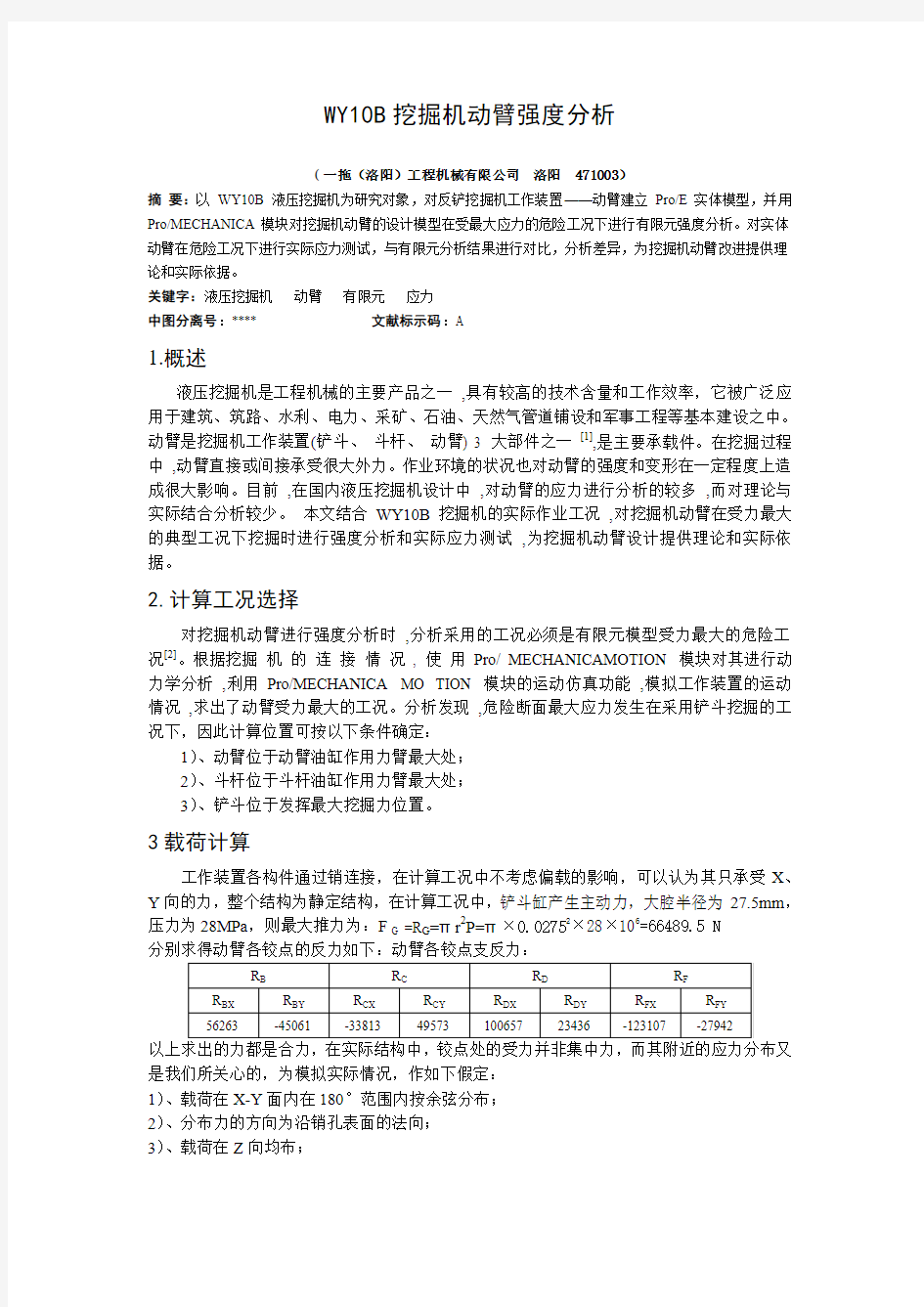

WY10B挖掘机动臂强度分析
(一拖(洛阳)工程机械有限公司洛阳 471003)
摘要:以WY10B液压挖掘机为研究对象,对反铲挖掘机工作装置——动臂建立Pro/E实体模型,并用Pro/MECHANICA模块对挖掘机动臂的设计模型在受最大应力的危险工况下进行有限元强度分析。对实体动臂在危险工况下进行实际应力测试,与有限元分析结果进行对比,分析差异,为挖掘机动臂改进提供理论和实际依据。
关键字:液压挖掘机动臂有限元应力
中图分离号:**** 文献标示码:A
1.概述
液压挖掘机是工程机械的主要产品之一,具有较高的技术含量和工作效率,它被广泛应用于建筑、筑路、水利、电力、采矿、石油、天然气管道铺设和军事工程等基本建设之中。动臂是挖掘机工作装置(铲斗、斗杆、动臂) 3 大部件之一[1],是主要承载件。在挖掘过程中,动臂直接或间接承受很大外力。作业环境的状况也对动臂的强度和变形在一定程度上造成很大影响。目前,在国内液压挖掘机设计中,对动臂的应力进行分析的较多,而对理论与实际结合分析较少。本文结合WY10B挖掘机的实际作业工况,对挖掘机动臂在受力最大的典型工况下挖掘时进行强度分析和实际应力测试,为挖掘机动臂设计提供理论和实际依据。
2.计算工况选择
对挖掘机动臂进行强度分析时,分析采用的工况必须是有限元模型受力最大的危险工况[2]。根据挖掘机的连接情况, 使用Pro/ MECHANICAMOTION 模块对其进行动力学分析,利用Pro/MECHANICA MO TION 模块的运动仿真功能,模拟工作装置的运动情况,求出了动臂受力最大的工况。分析发现,危险断面最大应力发生在采用铲斗挖掘的工况下,因此计算位置可按以下条件确定:
1)、动臂位于动臂油缸作用力臂最大处;
2)、斗杆位于斗杆油缸作用力臂最大处;
3)、铲斗位于发挥最大挖掘力位置。
3载荷计算
工作装置各构件通过销连接,在计算工况中不考虑偏载的影响,可以认为其只承受X、Y向的力,整个结构为静定结构,在计算工况中,铲斗缸产生主动力,大腔半径为27.5mm,压力为28MPa,则最大推力为:F G =R G=πr2P=π×0.02752×28×106=66489.5 N
分别求得动臂各铰点的反力如下:动臂各铰点支反力:
以上求出的力都是合力,在实际结构中,铰点处的受力并非集中力,而其附近的应力分布又是我们所关心的,为模拟实际情况,作如下假定:
1)、载荷在X-Y面内在180°范围内按余弦分布;
2)、分布力的方向为沿销孔表面的法向;
3)、载荷在Z向均布;
由假定构造载荷分布函数为: 式中:
F (θ ) = A cos (θ-α) (1) A 为待定常系数,
合力R 已知,分布力F 在P 向的合力应等于R ,即
式中:l 为销孔长度,r 为销孔半径。由上式可求得待定系数
由(3)式计算得到各铰点在计算位置的参数如下:
4 确定约束条件
对于静力分析,必须限制模型的刚体位移[3],选择动臂与平台的销孔(C 点)进行全约束,由于动臂的外力对C 点的力矩之和为零,限制C 点的Z 向旋转自由度对计算无影响,但实际约束是产生在销孔面上的,而且六面体单元的节点没有旋转刚度,因此施加在销孔面上的约束实际是限制了销孔面上节点在三个方向的自由度。这样会在约束的销孔处产生一附加扭矩,使局部应力增大,但对远端的应力计算没有很大影响。为考察其影响,约束不同的销孔分别进行计算,得到的结果表明除约束点附近的应力值不同外,其余部位的应力大小和分布完全一致,说明这种约束方式是可行的。
5 网格划分
动臂主要结构由厚钢板焊接而成,考虑到板厚较大,而且多处结构需使用体单元,因此决定全部使用三维单元划分,为达到较高的精度,主要使用八节点六面体单元,过渡部位使用五面体单元。为简便起见,划分时把动臂的前端作为整体处理(实际是两层钢板结构,在边缘有焊缝),对于焊缝则不作处理,划分后动臂节点数为41470,单元数为21260;
6 有限元强度分析结果
为了更加直观形象地将动臂的强度分析结果表现出来,通过 Pro/ MECHANICA 分析模块的后处理程序,绘制出动臂强度分析的应力云图如图 5所示。
轴的夹角。
为合力方向与 X
在此计算模型中没有考虑焊缝的影响,在实际情况中,焊缝应能够减小应力集中,即实际结构中的最大应力应低于计算值。
由动臂的应力云图可以看出,动臂大部分部位的应力值较小,而在动臂缸和斗杆缸铰点处有较大的应力集中,应考虑在这些铰点周围采取加强措施。
7 实际应力测试结果
了解知名品牌挖机结构件结构的特点,并对WY10B动臂进行实际工况下的应力测试,确定了动臂主要部位静态强度和动态强度应力值(应力测试仪)。
测试结果:最大应力点为:动态工况,最大应力为:241.6Mpa,结构件材料为:16Mn,其屈服极限为:345 Mpa,该点安全系数为:1.4
8 结果分析
(1)根据有限元分析和实际应力测量,动臂油缸座前端不仅应力集中,而且受力最大,是动臂受力的关键部位。加长此处油缸座耳板前端长度,增加耳板、下封板厚度,不仅可以降低此处应力,而且可以化解应力集中。
(2)动臂油缸座后端虽然应力集中,但是所受应力较小,不足以对动臂造成危险。
(3)动臂上斗杆油缸座耳板后应力集中,同样可以通过加长此处油缸座耳板后端长度,增加耳板厚度来解决,以降低此处应力,化解应力集中。
(4)动臂前叉有限元分析未反应应力集中,但是实际测量数值较大。因为有限元分析忽略了此处焊缝影响,在侧板上有条焊缝,受焊缝影响,此处应力实际值较大。建议前叉板加长,以改善上下封板前焊缝受力状况,提高疲劳强度。
通过使用Pro/ E 对WY10B 挖掘机动臂进行有限元分析,可以看出,有限元分析的主要工作是数据准备和分析运算结果,建立正确的有限元分析模型才能运算出正确的结果。根据对运算结果的分析,不断发现产品设计中存在的问题, 但是为了方便有限元分析,往往忽略了一些因素的影响(如:焊缝),这就造成有些问题在分析时没有被及时发现,如果再能结合实际测量,得到的结果就会更加准确。以上分析结果已在WY10B挖掘机上实施,并取得良好效果,为挖掘机的设计和改进提供了准确的理论和实际依据。
参考文献
1黄东胜,邱斌.现代挖掘机械[M] .北京:人民交通出版社,2003 :6
2于硕 ,张建宗 ,孔喆.液压挖掘机动臂的有限元分析[J ] .工程机械 ,2002 (11) :8 -
10.
3MSC公司. John M. Lee. Linear Static Analysis User's Guide, 1997
邮箱:keke8882006@https://www.360docs.net/doc/7f1748341.html,
挖掘机动臂有限元分析
挖掘机动臂结构设计及仿真分析 学生姓名:杨鹏 专业:机械设计制造及其自动化指导老师:何孔德副教授
挖掘机介绍 挖掘机,又称挖掘机械(excavating machinery),是用铲斗挖掘高于或低于承机面的物料,并装入运输车辆或卸至堆料场的土方机械。挖掘机挖掘的物料主要是土壤、煤、泥沙以及经过预松后的土壤和岩石。哥弟官方旗舰店 https://www.360docs.net/doc/7f1748341.html,,从近几来工程机械的发展来看,挖掘机的发展相对较快,挖掘机已经成为工程建设中最主要的工程机械之一。挖掘机最重要的三个参数:操作重量(质量),发动机功率和铲斗斗容。
本课题的主要任务: 1.对挖掘机动臂进行简化处 理,并用Pro ENGINEER建 立三维。 2.将三维模型导入ansys中 ,并对三维模型加载,得出 应力云图。 3.针对挖掘机动臂应力云图,结合动臂结构,进行改变,以改善动臂的应力集中情况。
对挖掘机动臂结构进行简化处理 在ansys有限元 分析中是不允 许有缝隙出现 的,所以将动 臂的一些地方 进行简化处理, 然后建立三维 模型
挖掘机动臂的二维图形挖掘机动臂的三维图形
挖掘机受力分析及动臂应力计算 (1)、挖掘机阻力均布在铲斗的切削板上,此时可等效为集中载荷 Fa作用在铲斗切削板中部。 (2)、挖掘机阻力Fb作用于铲斗的边齿,作用于铲斗的最外侧。 (3)、挖掘机阻力Fb作用于铲斗的边齿,同时受到横向力Fc的作用。 工作装置的受力分析 (1)、挖掘机阻力均布在铲斗的切削板上,此时可等效为集中载荷Fa作用在铲斗切削板中部。 (2)、挖掘机阻力Fb作用于铲斗的边齿,作用于铲斗的最外侧。 (3)、挖掘机阻力Fb作用于铲斗的边齿,同时受到横向力Fc的作用。
液压缸设计与计算
液压缸是液压传动的执行元件,它和主机工作机构有直接的联系,对于不同的机种和机构,液压缸具有不同的用途和工作要求。因此,在设计液压缸之前,必须对整个液压系统进行工况分析,编制负载图,选定系统的工作压力(详见第九章),然后根据使用要求选择结构类型,按负载情况、运动要求、最大行程等确定其主要工作尺寸,进行强度、稳定性和缓冲验算,最后再进行结构设计。 1.液压缸的设计内容和步骤 (1)选择液压缸的类型和各部分结构形式。 (2)确定液压缸的工作参数和结构尺寸。 (3)结构强度、刚度的计算和校核。 (4)导向、密封、防尘、排气和缓冲等装置的设计。 (5)绘制装配图、零件图、编写设计说明书。 下面只着重介绍几项设计工作。 2.计算液压缸的结构尺寸液压缸的结构尺寸主要有三个:缸筒内径D、活塞杆外径d和缸筒长度L。 (1)缸筒内径D。液压缸的缸筒内径D是根据负载的大小来选定工作压力或往返运动速度比,求得液压缸的有效工作面积,从而得到缸筒内径D,再从GB2348—80标准中选取最近的标准值作为所设计的缸筒内径。 根据负载和工作压力的大小确定D: ①以无杆腔作工作腔时 (4-32) ②以有杆腔作工作腔时 (4-33) 式中:pI为缸工作腔的工作压力,可根据机床类型或负载的大小来确定;Fmax 为最大作用负载。 (2)活塞杆外径d。活塞杆外径d通常先从满足速度或速度比的要求来选择,然后再校核其结构强度和稳定性。若速度比为λv,则该处应有一个带根号的式子: (4-34) 也可根据活塞杆受力状况来确定,一般为受拉力作用时,d=0.3~0.5D。 受压力作用时: pI<5MPa时,d=0.5~0.55D 5MPa<pI<7MPa时,d=0.6~0.7D pI>7MPa时,d=0.7D (3)缸筒长度L。缸筒长度L由最大工作行程长度加上各种结构需要来确定,即:L=l+B+A+M+C 式中:l为活塞的最大工作行程;B为活塞宽度,一般为(0.6-1)D;A为活塞杆导
液压挖掘机动臂与斗杆的设计
本科生毕业论文 毕业论文题目液压挖掘机动臂与斗杆的设计学生姓名 所在学院机械工程学院 专业及班级机械制造及自动化 指导教师张江华顾惠斌 完成日期2014年3月31日
摘要 液压挖掘机应用面广,使用量大,在工程机械市场占有很重要的地位,目前已成为工程机械第一主力机种。液压挖掘机模仿人体构造,有大臂、小臂和手腕,能“扭腰”旋转和行走,具有较长的臂和杆,可做空间六自由度动作,配装上各种工作装置能进行立体作业。这种带有类似人类“基因”的挖掘机已成为人类工程建设中的主要伙伴之一,也被称为土建机械手,是建设机器人的代表。正因为液压挖掘机通用性强,作业范围广,所以被认为是多功能的工程机械。 本次设计的题目是液压挖掘机动臂与斗杆的设计。其构造特点是各部件之间的连接全部采用铰接,通过油缸的伸缩来实现挖掘工作中的各种动作。动臂的小铰点与回转平台铰接,并以动臂油缸来支撑和改变动臂的倾角,通过动臂油缸的伸缩可使动臂绕小铰点转动而升降。斗杆铰接于动臂的上端,斗杆与动臂的相对位置由斗杆油缸来控制,当斗杆油缸伸缩时,斗杆便可绕动臂上焦铰点转动。该设计主要是通过对广西玉柴生产的YC-60液压挖掘机进行现场测绘,取得了工作装置的大体结构数据。对YC-60和YC-70液压挖掘机的主要参数进行比较,再结合《液压挖掘机》和《液压与气动传动》,对单斗液压挖掘机的工作装置进行运动学分析和结构参数的计算。根据运动学分析和结构参数的计算结果得到斗杆的基本尺寸和结构尺寸,同时完成斗杆油缸的计算设计。最后用CAD 软件和UG软件进行二维图与三维图受力等绘制。 关键词:液压挖掘机;动臂;斗杆;设计
Hydraulic excavator application widely, usage is big, has very important position in the construction machinery market, at present already became the first major construction machinery model. Hydraulic excavator imitate human body structure, has a big arm, forearm and wrist, walking \"twist a waist\" rotation and with longer arms and rod, can do a space of six degrees of freedom movement, equipped with all kinds of working device on the three-dimensional operations. This is similar to human \"gene\" of excavator has become one of the main partners in the human engineering construction, also known as civil manipulator, is a representative of the construction of the robot. Because of hydraulic excavator versatility, wide scope of operation, it's considered versatile engineering machinery. The topic of this design is the design of the hydraulic mining mechanical arm and arm. Its structure characteristic is the connection between the various components are all made of articulated, through the telescopic cylinder to accomplish all kinds of action of the excavation. Small hinged point and movable arm slewing platform hinged, and the movable arm oil cylinder to support and change of movable arm Angle, through the movable arm oil cylinder expansion can make movable arm around small hinged point rotation and lifting. Bucket rod hinged on the top of the derrick, the relative position of the bucket rod and the movable arm by a bucket rod oil cylinder to control, when the bucket rod oil cylinder telescopic arm can be movable arm around the upper energizer hinged point of rotation. This design is mainly through to the guangxi yuchai YC - 60 hydraulic excavator production field of surveying and mapping, the general structure of equipment data. To YC - 60 and YC - 70 main parameters of hydraulic excavator, coupled with the hydraulic excavator and the hydraulic and pneumatic transmission, the kinematics analysis was carried out on single bucket hydraulic excavator working equipment and structure parameter calculation. According to kinematics analysis and calculation results of the structural parameters, get the basic size and structure size of the arm, at the same time to complete the calculation of bucket rod oil cylinder design. Finally, using the CAD software UG software and 2 d figure and 3 d stress such as mapping. Key words: hydraulic excavator; Movable arm; Arm; design
液压缸计算公式
液压缸计算公式 1、液压缸内径和活塞杆直径的确定 液压缸的材料选为Q235无缝钢管,活塞杆的材料选为Q235 液压缸内径: 4,F4== D,3.14,,p F:负载力 (N) 2A:无杆腔面积 () mm P:供油压力 (MPa) D:缸筒内径 (mm) :缸筒外径 (mm) D1 2、缸筒壁厚计算 π×,??ηδσψμ 1)当δ/D?0.08时 pDmax,,(mm) 02,p 2)当δ/D=0.08~0.3时 pDmax,,(mm) 02.3,-3ppmax 3)当δ/D?0.3时 ,,,,0.4pDpmax,,,,(mm) 0,,2,1.3p,pmax,, ,b,, pn δ:缸筒壁厚(mm) ,:缸筒材料强度要求的最小值(mm) 0 :缸筒内最高工作压力(MPa) pmax :缸筒材料的许用应力(MPa) ,p :缸筒材料的抗拉强度(MPa) ,b :缸筒材料屈服点(MPa) ,s
n:安全系数 3 缸筒壁厚验算 22,(D,D)s1(MPa) PN,0.352D1 D1P,2.3,lg rLsD PN:额定压力 :缸筒发生完全塑性变形的压力(MPa) PrL :缸筒耐压试验压力(MPa) Pr E:缸筒材料弹性模量(MPa) :缸筒材料泊松比 =0.3 , 同时额定压力也应该与完全塑性变形压力有一定的比例范围,以避免 塑性变形的发生,即: ,,(MPa) PN,0.35~0.42PrL 4 缸筒径向变形量 22,,DPDD,1r,,D,,,,(mm) 22,,EDD,1,,变形量?D不应超过密封圈允许范围5 缸筒爆破压力 D1PE,2.3,lg(MPa) bD 6 缸筒底部厚度 Pmax,(mm) ,0.433D12,P :计算厚度处直径(mm) D2 7 缸筒头部法兰厚度 4Fbh,(mm) ,(r,d),aLP F:法兰在缸筒最大内压下所承受轴向力(N) b:连接螺钉孔的中心到法兰内圆的距离(mm) :法兰外圆的半径(mm) ra
液压缸尺寸计算Word版
A、大腿液压缸结构尺寸设计计算 ①、大腿缸的负载组成 1、工作载荷(活塞杆在抬腿过程中始终受压) 2、惯性载荷(由于所选用液压缸尺寸较小,即不计 重量,且执行元件运动速度变化较小,故不考虑惯性载 荷) 3、密封阻力,其中是作用于活塞上的载 荷,且,是外载荷,,其中是 液压缸的机械效率,取 综上可得:外载荷,密封阻力, 总载荷。 ②、初选系统工作压力 1、按载荷选定工作压力,取工作腔压力为 (由于总载荷为61988N大于50000N,故根据手册 选取工作压力为12MPa) 2、选择执行元件液压缸的背压力为(由于回 油路带有调速阀,且回油路的不太复杂,故根据手册 选取被压压力为1MPa) ③、液压缸主要结构尺寸的计算 1、在整个抬腿过程中活塞杆始终受压,故可得下式: 活塞杆受压时:
----------液压缸工作腔压力(Pa) ----------液压缸回油腔压力(Pa) ----------无杆腔活塞有效作用面积,,D为活塞直径(m)----------有杆腔活塞有效作用面积,,d为活塞杆直径(m) 选取d/D=0.7(由于工作压力为12MPa大于5MPa,故根据手册选取d/D=0.7) 综上可得:D=82.8mm,根据手册可查得常用活塞杆直径,可取D=90mm,d=60mm。 校核活塞杆的强度,其中活塞杆的材料为45钢,故。 由于活塞杆在受负载的工作过程中仅收到压力作用,故仅校核其 压缩强度即可。,故满足强度要求。 即d=60mm,则D=90mm。 由此计算得工作压力为: 根据所选取的活塞直径D=90mm,可根据手册选的液压缸的外径为108mm,即可得液压缸壁厚为。 校核液压缸缸壁的强度,其中液压缸的材料为45钢,故
挖掘机动臂强度分析
WY10B挖掘机动臂强度分析 (一拖(洛阳)工程机械有限公司洛阳 471003) 摘要:以WY10B液压挖掘机为研究对象,对反铲挖掘机工作装置——动臂建立Pro/E实体模型,并用Pro/MECHANICA模块对挖掘机动臂的设计模型在受最大应力的危险工况下进行有限元强度分析。对实体动臂在危险工况下进行实际应力测试,与有限元分析结果进行对比,分析差异,为挖掘机动臂改进提供理论和实际依据。 关键字:液压挖掘机动臂有限元应力 中图分离号:**** 文献标示码:A 1.概述 液压挖掘机是工程机械的主要产品之一,具有较高的技术含量和工作效率,它被广泛应用于建筑、筑路、水利、电力、采矿、石油、天然气管道铺设和军事工程等基本建设之中。动臂是挖掘机工作装置(铲斗、斗杆、动臂) 3 大部件之一[1],是主要承载件。在挖掘过程中,动臂直接或间接承受很大外力。作业环境的状况也对动臂的强度和变形在一定程度上造成很大影响。目前,在国内液压挖掘机设计中,对动臂的应力进行分析的较多,而对理论与实际结合分析较少。本文结合WY10B挖掘机的实际作业工况,对挖掘机动臂在受力最大的典型工况下挖掘时进行强度分析和实际应力测试,为挖掘机动臂设计提供理论和实际依据。 2.计算工况选择 对挖掘机动臂进行强度分析时,分析采用的工况必须是有限元模型受力最大的危险工况[2]。根据挖掘机的连接情况, 使用Pro/ MECHANICAMOTION 模块对其进行动力学分析,利用Pro/MECHANICA MO TION 模块的运动仿真功能,模拟工作装置的运动情况,求出了动臂受力最大的工况。分析发现,危险断面最大应力发生在采用铲斗挖掘的工况下,因此计算位置可按以下条件确定: 1)、动臂位于动臂油缸作用力臂最大处; 2)、斗杆位于斗杆油缸作用力臂最大处; 3)、铲斗位于发挥最大挖掘力位置。 3载荷计算 工作装置各构件通过销连接,在计算工况中不考虑偏载的影响,可以认为其只承受X、Y向的力,整个结构为静定结构,在计算工况中,铲斗缸产生主动力,大腔半径为27.5mm,压力为28MPa,则最大推力为:F G =R G=πr2P=π×0.02752×28×106=66489.5 N 分别求得动臂各铰点的反力如下:动臂各铰点支反力: 以上求出的力都是合力,在实际结构中,铰点处的受力并非集中力,而其附近的应力分布又是我们所关心的,为模拟实际情况,作如下假定: 1)、载荷在X-Y面内在180°范围内按余弦分布; 2)、分布力的方向为沿销孔表面的法向; 3)、载荷在Z向均布;
挖掘机动臂优先功能失效的原因和排除方法
挖掘机"动臂优先"功能失效的原因和排除方法 2006-7-18 16:34:27 液压挖掘机的主要作业工况是挖掘和装车。对这两种工况,动臂的起升速度是决定工作循环时间的主要因 载,动臂起升速度越快,循环时间就越短,机器的工作效率也就越肓。为提高动臂的起升速度 f 卡特彼勒界OB系列挖遐机除了将动臂起升、斗杆外伸和斗杆内收动作设计由双泵合流完成外f还通过电控方式在机器联合动作需要动臂快速起升时取消斗杆内收的合流功能,进一步加快动臂起升的速度。对动臂的这种控制 方式称为“动皆优先“模式。〃动臂优先“原理和实现的条件挖遐机在进行装车或开沟作业时 f 动皆起升 和斗杆内收一般是同时进行的 f 由于动臂和斗杆都具有双泵合流功能 f 两泵会同时向动皆缸和斗杆缸供 油,在发动机功率允许的条件下,哪个动作需要的油量多 f 就给它多供一些油;而在动臂块速起升时,发动机接近满负荷,此时若想动臂起升更快一些,就不得不减少向斗杆缸的供,即〃动臂优先”工作模式.但"动臂优先”工作模式.井不是动臂一直工作于”优先状态“,只是在需要动臂快速起升时,才让动臂处于"优先状态"。"动臂优先"的液压原。见附虱当动臂起升时,来目动臂起升先导控制阀的先导油使动臂控制阀2动作,将上主泵11的油导向动臂缸大腔;当先导油油压大于2250kPa时,动皆合流阀4动f将下主 泵12的油也导向动臂缸大腔,此时动臂缸处于双泵合流供油状态,使动臂快速上升。在控制系统方面,按 下"动臂优先“按钮 f 当动臂起升先导油油压大于2646±196 kPa后,装于先导油管路上的动臂优先压力开关6闭合,电脑收到闭合的信号后,使辖细控制电磁阀9得电r使斗杆合流阀3的先导控制油路接通系 统的回油路,此时斗杆合流阅处于中位。这样 r 在动臂快速起升过程中即使内收斗杆,也能保证动臂快速升起。"动臂优先"功能失效的原因和排除方法"动臂优先"功能失效的症状一般表现为动臂起升速度变慢,而此时机器的其他动作尚属止箒。1由此表明液压系统中的公共部分没有问题,故I?原11因可缩小在动臂缸的液压主系统、先导控制部分以及“动臂优先"的电控部分。1动臂缸液压主系统^先导控制部分(1)动臂起升先导控制阀工作不良,不能将先导油准确地送到动臂控制阀与动臂合流阀。可通过测量先导油路的油压断定;缓慢操作先导手柄时,先导^掘阀的输出油压应能连续地在294—3727kPa之间变化。如果不能,应拆检动臂起升先导酒阀,检直其元件有无磨损、损坏或卡死,并应检宜计量弹簧是否符合要求。(2)动臂控制阀与其合流阀工作不良检直阀芯运动有无发卡现彖,阀芯、对中弹簧及固定件有无问题,必要时进行修理、更换.(3 ) 动臂缸内漏严重可通过流量测试进行准确的诊断,或直接拆开缸检直,必要时更换有关零件?(4 ) 动臂缸油路压力安全阀有问题用压力表测安全阀的调定压力值,如不在 36800±1470kPa的范围
液压缸设计计算
第一部分 总体计算 1、 压力 油液作用在单位面积上的压强 A F P = Pa 式中: F ——作用在活塞上的载荷,N A ——活塞的有效工作面积,2 m 从上式可知,压力值的建立是载荷的存在而产生的。在同一个活塞的有效工作面积上,载荷越大,克服载荷所需要的压力就越大。换句话说,如果活塞的有效工作面积一定,油液压力越大,活塞产生的作用力就越大。 额定压力(公称压力) PN,是指液压缸能用以长期工作的压力。 最高允许压力 P max ,也是动态实验压力,是液压缸在瞬间所能承受的极限压力。通常规定为:P P 5.1max ≤ MPa 。 耐压实验压力P r ,是检验液压缸质量时需承受的实验压力,即在此压力下不出现变形、裂缝或破裂。通常规定为:PN P r 5.1≤ MPa 。 液压缸压力等级见表1。 2、 流量 单位时间内油液通过缸筒有效截面的体积: t V Q = L/min 由于310?=At V ν L 则 32104 ?= =νπ νD A Q L/min 对于单活塞杆液压缸: 当活塞杆伸出时 32104 ?= νπ D Q 当活塞杆缩回时 32210)(4 ?-=νπ d D Q 式中: V ——液压缸活塞一次行程中所消耗的油液体积,L ;
t ——液压缸活塞一次行程所需的时间,min ; D ——液压缸缸径,m ; d ——活塞杆直径,m ; ν——活塞运动速度,m/min 。 3、速比 液压缸活塞往复运动时的速度之比: 2 2 2 12d D D v v -==? 式中: 1v ——活塞杆的伸出速度,m/min ; 2v ——活塞杆的缩回速度,m/min ; D ——液压缸缸径,m ; d ——活塞杆直径,m 。 计算速比主要是为了确定活塞杆的直径和是否设置缓冲装置。速比不宜过大或过小,以免产生过大的背压或造成因活塞杆太细导致稳定性不好。 4、液压缸的理论推力和拉力 活塞杆伸出时的理推力: 626 11104 10?= ?=p D p A F π N 活塞杆缩回时的理论拉力: 6226 2210)(4 10?-= ?=p d D p F F π N 式中: 1A ——活塞无杆腔有效面积,2 m ; 2A ——活塞有杆腔有效面积,2m ; P ——工作压力,MPa ; D ——液压缸缸径,m ; d ——活塞杆直径,m 。 5、液压缸的最大允许行程 活塞行程S ,在初步确定时,主要是按实际工作需要的长度来考虑的,但这一工作行程并不一定是油缸的稳定性所允许的行程。为了计算行程,应首先计算出活塞的最大允许计算长度。因为活塞杆一般为细长杆,由欧拉公式推导出: k k F EI L 2π= mm 式中:
液压缸设计说明书
1 设计课题 1.1设计要求 设计一台铣削专用机床液压系统用液压缸,要求液压系统完成的工作循环是:工件夹紧→工作台快进→工作台工进→工作台快退→工件松开。 1.2原始数据 运动部件的重力为25000N,快进、快退速度为5m/min,工进速度为100~1200mm/min,最大行程为400mm,其中工进行程为180mm,最大切削力为20000N,采用平面导轨,夹紧缸的行程为20mm,夹紧力为30000N,夹紧时间为1s。
2 液压系统的发展概况 一个完整的液压系统由五个部分组成,即动力元件、执行元件、控制元件、辅助元件(附件)和液压油。 由于液压技术广泛应用了高技术成果,如自动控制技术、计算机技术、微电子技术、磨擦磨损技术、可靠性技术及新工艺和新材料,使传统技术有了新的发展,也使液压系统和元件的质量、水平有一定的提高。尽管如此,走向二十一世纪的液压技术不可能有惊人的技术突破,应当主要靠现有技术的改进和扩展,不断扩大其应用领域以满足未来的要求。 液压系统在将机械能转换成压力能及反转换方面,已取得很大进展,但一直存在能量损耗,主要反映在系统的容积损失和机械损失上。如果全部压力能都能得到充分利用,则将使能量转换过程的效率得到显著提高。为减少压力能的损失,必须解决下面几个问题:减少元件和系统的部压力损失,以减少功率损失。主要表现在改进元件部流道的
压力损失,采用集成化回路和铸造流道,可减少管道损失,同时还可减少漏油损失。 减少或消除系统的节流损失,尽量减少非安全需要的溢流量,避免采用节流系统来调节流量和压力。采用静压技术,新型密封材料,减少磨擦损失。发展小型化、轻量化、复合化、广泛发展通径电磁阀以及低功率电磁阀。改善液压系统性能,采用负荷传感系统,二次调节系统和采用蓄能器回路。为及时维护液压系统,防止污染对系统寿命和可靠性造成影响,必须发展新的污染检测方法,对污染进行在线测量,要及时调整,不允许滞后,以免由于处理不及时而造成损失。 液压系统维护已从过去简单的故障拆修,发展到故障预测,即发现故障苗头时,预先进行维修,清除故障隐患,避免设备恶性事故的发展。 要实现主动维护技术必须要加强液压系统故障诊断方法的研究,当前,凭有经验的维修技术人员的感宫和经验,通过看、听、触、测等判断找故障已不适于现代工业向大型化、连续化和现代化方向发展,必须使液压系统故障诊断现代化,加强专家系统的研究,要总结专家的知识,建立完整的、具有学习功能的专家知识库,并利用计算机根据输入的现象和知识库中知识,用推理机中存在的推理方法,推算出引出故障的原因,提高维修方案和预防措施。要进一步引发液压系统故障诊断专家系统通用工具软件,对于不同的液压系统只需修改和增减少量的规则。 另外,还应开发液压系统自补偿系统,包括自调整、自润滑、自校正,在故障发生之前,进市补偿,这是液压行业努力的方向。 电子技术和液压传动技术相结合,使传统的液压传协与控制技术增加了活力,扩大了应用领域。实现机电一体化可以提高工作可靠性,实现液压系统柔性化、智能化,改变液压系统效率低,漏油、维修性差等缺点,充分发挥液压传动出力大、贯性小、响应快等优点,其主要发展动向如下:[1]
AT89S52_AVR入门与提高原件焊接顺序清单
单片机开发板散装套件焊接顺序说明 序号名称型号 个 数 作用备注 1 贴片LED灯普通3 2 所有I/0输入输出指示注意正负 2 贴片电阻102 1K 6 分压限流 3 贴片电阻512 ** 1 DS18B20温度传感器信号上拉可用4.7K 4 贴片电阻103 10K 4 上拉电阻 5 贴片三极管PNP 2TY 5 驱动数码管和蜂鸣器 6 排阻102 1K 4 I/O口上拉电阻带点端为公共端 7 电源指示灯红色 1 电源指示灯注意正负 8 瓷片电容30P 2 晶振起振电容 9 8P管座8脚 1 插掉电保护芯片24C02 10 16P管座16脚 1 插串口通信芯片MAX232 11 40P管座40脚 1 插四位独立共阳数码管 12 独立按键普通 6 复位和输入 13 晶振插座2脚 1 使晶振更换更方便减去中间脚 14 DS18B20插座3脚 1 使用测温程序使用 15 USB供电插座普通 1 USB供电使用 16 插头供电插座4mm 1 插头供电使用 17 下载口座10针 1 单片机下载程序用注意方向(开口向下) 18 电解电容25V10UF 7 复位电容/MAX232通信电容注意正负 19 排针单排63 电源/ I/O /跳线 20 排座单排36 液晶接口 21 可调电阻10K 1 液晶背光灯亮度调节 22 蜂鸣器5V 1 声音/报警音输出注意正负 23 电解电容50V100UF 1 电源滤波电容注意正负 24 电源开关按键开关 1 电源开关 25 电源端子AWG12-22 1 压接电源引入端子 26 9针串口座串口座 1 串口通信使用 27 单片机座40P 1 锁定单片机 28 MAX232芯片MAX232 1 串口通信使用 29 24C02芯片24C02 1 掉电保护 30 共阳数码管Cps05011bh 4 数码管显示 31 短路帽2P 8 连接相邻两个排针 32 晶振** 1 单片机提供工作时钟 33 支架塑料 4 支撑单片机板 34 单片机AT89S52 1 核心芯片
液压油缸设计计算公式
液压油缸的主要设计技术参数 一、液压油缸的主要技术参数: 1.油缸直径;油缸缸径,内径尺寸。 2. 进出口直径及螺纹参数 3.活塞杆直径; 4.油缸压力;油缸工作压力,计算的时候经常是用试验压力,低于16MPa乘以1.5,高于16乘以1.25 5.油缸行程; 6.是否有缓冲;根据工况情况定,活塞杆伸出收缩如果冲击大一般都要缓冲的。 7.油缸的安装方式; 达到要求性能的油缸即为好,频繁出现故障的油缸即为坏。应该说是合格与不合格吧?好和合格还是有区别的。 二、液压油缸结构性能参数包括:1.液压缸的直径;2.活塞杆的直径;3.速度及速比;4.工作压力等。 液压缸产品种类很多,衡量一个油缸的性能好坏主要出厂前做的各项试验指标,油缸的工作性能主要表现在以下几个方面: 1.最低启动压力:是指液压缸在无负载状态下的
最低工作压力,它是反映液压缸零件制造和装配 精度以及密封摩擦力大小的综合指标; 2.最低稳定速度:是指液压缸在满负荷运动时没 有爬行现象的最低运动速度,它没有统一指标, 承担不同工作的液压缸,对最低稳定速度要求也 不相同。 3.内部泄漏:液压缸内部泄漏会降低容积效率, 加剧油液的温升,影响液压缸的定位精度,使液 压缸不能准确地、稳定地停在缸的某一位置,也 因此它是液压缸的主要指标之。 液压油缸常用计算公式 液压油缸常用计算公式 项目公式符号意义 液压油缸面积(cm 2 ) A =πD 2 /4 D :液压缸有效活塞直径(cm) 液压油缸速度(m/min) V = Q / A Q :流量(l / min) 液压油缸需要的流量(l/min) Q=V×A/10=A×S/10t V :速度(m/min) S :液压缸行程(m) t :时间(min) 液压油缸出力(kgf) F = p × A F = (p × A) -(p×A) ( 有背压存在时) p :压力(kgf /cm 2 ) 泵或马达流量(l/min) Q = q × n / 1000 q :泵或马达的几何排量(cc/rev) n :转速(rpm ) 泵或马达转速(rpm) n = Q / q ×1000 Q :流量(l / min) 泵或马达扭矩(N.m) T = q × p / 20π 液压所需功率(kw) P = Q × p / 612 管内流速(m/s) v = Q ×21.22 / d 2 d :管内径(mm) 管内压力降(kgf/cm 2 ) △ P=0.000698×USLQ/d 4 U :油的黏度(cst) S :油的比重
一种挖掘机动臂结构
说明书摘要 本实用新型公开了一种挖掘机动臂结构,包括小动臂(1),转轴(2), 铲斗气缸(3),大动臂(4),小动臂气缸(5),铲斗(6),连杆(7), 大动臂气缸(8),驾驶室(9)等。小动臂(1)和大动臂(4)及连杆(7),5 通过转轴(2)连成可绕转轴(2)旋转的连杆体系,在小动臂气缸(5) 和大动臂气缸(8)、铲斗气缸(3)的作用下,实现铲斗(6)的挖掘动 作。
摘要附图 图1
权利要求书 一种挖掘机动臂结构,其特征在于: 1、本实用新型公开了一种挖掘机动臂结构,包括小动臂(1),转轴 (2),铲斗气缸(3),大动臂(4),小动臂气缸(5),铲斗(6),5 连杆(7),大动臂气缸(8),驾驶室(9)等。小动臂(1)和大动臂(4)及连杆(7),通过转轴(2)连成可绕转轴(2)旋转的连杆体系,在小动臂气缸(5)和大动臂气缸(8)、铲斗气缸(3)的作用下,实现铲斗(6)的挖掘动作。 2、根据权利要求1所述,大动臂气缸(8)和大动臂(4)通过转轴10 (2)安装在驾驶室(9)所在的基座上。小动臂气缸(5)安装在大动臂(4)的正上方,伸出轴与大动臂(4)的纵向平行。小动臂(1)根据杠杆的原理,在一端安装小动臂气缸(5),另一端与铲斗(6)安装。中间与大动臂(4)通过转轴(2)连接。 3、根据权利要求1所述,铲斗气缸(3)安装在小动臂(1)的正上15 方,伸出轴与小动臂(1)的纵向平行。连杆(7)的一端安装在小动臂(1)上,另一端安装在铲斗(6)上,铲斗(6)与小动臂(1)的一端通过转轴(2)连接。由此,连杆(7)和铲斗(6)构成三连杆机构。
说明书 一种挖掘机动臂结构 技术领域 5 本实用新型涉及一种挖掘机动臂结构。 背景技术 目前在铁路、公路、矿山、水电建设、工程爆破等作业中都广泛使用挖掘机,但是由于普通挖掘机作业效率较低,无法满足一些大型施工项目10 的需求。当挖掘机进行挖掘作业时,焊接形成的箱体需要频繁的承受挖掘产生的巨大冲击力,箱体内部因冲击力会产生内部应力,并会导致应变产生,而整个动臂是一个焊接而成的非常牢固的箱体,所以因外部冲击力而产生的应力将无处释放,导致应力集中在箱体的薄弱处,如顶板、底板以及侧板的焊接处,使这些部位成为受力最严重的部位,随着挖掘机作业的15 不断进行,这些部位不断的被挤压和扭曲,最终会造成应变开裂。因此,加强动臂的承受力,成为本领域亟待解决的技术问题。 实用新型内容 本实用新型为解决现有技术的不足,提供了一种挖掘机动臂结构。 本实用新型采用的技术方案是:一种挖掘机动臂结构,包括小动臂 20 (1),转轴(2),铲斗气缸(3),大动臂(4),小动臂气缸(5),铲斗(6),连杆(7),大动臂气缸(8),驾驶室(9)等。小动臂(1)和大动臂(4)及连杆(7),通过转轴(2)连成可绕转轴(2)旋转的连杆体系,在小动臂气缸(5)和大动臂气缸(8)、铲斗气缸(3)的作用下,实现铲斗(6)的挖掘动作。 25 大动臂气缸(8)和大动臂(4)通过转轴(2)安装在驾驶室(9)所在的基座上。小动臂气缸(5)安装在大动臂(4)的正上方,伸出轴与大
常见的焊接缺陷及处理办法
常见的焊接缺陷及处理办法 一、外部缺陷 一)、焊缝成型差 1、现象 焊缝波纹粗劣,焊缝不均匀、不整齐,焊缝与母材不圆滑过渡,焊接接头差,焊缝高低不平。 2、原因分析 焊缝成型差的原因有:焊件坡口角度不当或装配间隙不均匀;焊口清理不干净;焊接电流过大或过小;焊接中运条(枪)速度过快或过慢;焊条(枪)摆动幅度过大或过小;焊条(枪)施焊角度选择不当等。 3、防治措施 ⑴焊件的坡口角度和装配间隙必须符合图纸设计或所执行标准的要求。 ⑵焊件坡口打磨清理干净,无锈、无垢、无脂等污物杂质,露出金属光泽。 ⑶加强焊接联系,提高焊接操作水平,熟悉焊接施工环境。 ⑷根据不同的焊接位置、焊接方法、不同的对口间隙等,按照焊接工艺卡和操作技能要求,选择合理的焊接电流参数、施焊速度和焊条(枪)的角度。 4、治理措施 ⑴加强焊后自检和专检,发现问题及时处理; ⑵对于焊缝成型差的焊缝,进行打磨、补焊; ⑶达不到验收标准要求,成型太差的焊缝实行割口或换件重焊; ⑷加强焊接验收标准的学习,严格按照标准施工。 二)、焊缝余高不合格 1、现象 管道焊口和板对接焊缝余高大于 3 ㎜;局部出现负余高;余高差过大;角焊缝高度不够或 焊角尺寸过大,余高差过大。 2、原因分析 焊接电流选择不当;运条(枪)速度不均匀,过快或过慢;焊条(枪)摆动幅度不均匀;焊条(枪)施焊角度选择不当等。 3、防治措施 ⑴根据不同焊接位置、焊接方法,选择合理的焊接电流参数; ⑵增强焊工责任心,焊接速度适合所选的焊接电流,运条(枪)速度均匀,避免忽快忽慢; ⑶焊条(枪)摆动幅度不一致,摆动速度合理、均匀; ⑷注意保持正确的焊条(枪)角度。 4、治理措施 ⑴加强焊工操作技能培训,提高焊缝盖面水平; ⑵对焊缝进行必要的打磨和补焊; ⑶加强焊后检查,发现问题及时处理; ⑷技术员的交底中,对焊角角度要求做详细说明。 三)、焊缝宽窄差不合格 1、现象 焊缝边缘不匀直,焊缝宽窄差大于 3 ㎜。 2、原因分析 焊条(枪)摆动幅度不一致,部分地方幅度过大,部分地方摆动过小;焊条(枪)角度不合适;焊接位置困难,妨碍焊接人员视线。
液压缸计算
液压缸设计计算说明 系统压力为1p =25 MPa 本系统中有顶弯缸、拉伸缸以及压弯缸。以下为这三种液压缸的设计计算。 一、 顶弯缸 1 基本参数的确定 (1)按推力F 计算缸筒内径D 根据公式 3.5710D -=? ① 其中,推力F=120KN 系统压力1p =25 MPa 带入①式,计算得D= 78.2mm ,圆整为D = 80 mm (2)活塞杆直径d 的确定 确定活塞杆直径d 时,通常应先满足液压缸速度或速比的要求,然后再校核其结构强度和稳定性。若速比为?,则 d = ② 取?=1.6,带入②式,计算得d =48.9mm ,圆整为d =50mm 80 50 D d ?= = =1.6 (3)最小导向长度H 的确定 对一般的液压缸,最小导向长度H 应满足 202 L D H ≥ + ③ 其中,L 为液压缸行程,L=500mm
带入③式,计算得H=65mm (4)活塞宽度B 的确定 活塞宽度一般取(0.6~1.0)B D = ④ 得B=48mm~80mm ,取B=60mm (5)导向套滑动面长度A 的确定 在D <80mm 时,取(0.6~1.0)A D = ⑤ D >80mm 时,取(0.6~1.0)A d = ⑥ 根据⑤式,得A=48mm~80mm ,取A=50mm (6)隔套长度C 的确定 根据公式2 A B C H +=- ⑦ 代入数据,解得C=10mm 2 结构强度计算与稳定校核 (1)缸筒外径 缸筒内径确定后,有强度条件确定壁厚δ,然后求出缸筒外径D 1 假设此液压缸为厚壁缸筒,则壁厚1]2D δ= ⑧ 液压缸筒材料选用45号钢。其抗拉强度为σb =600MPa 其中许用应力[]b n σσ= ,n 为安全系数,取n=5 将数据带入⑧式,计算得δ=8.76mm 故液压缸筒外径为D 1=D+2δ=97.52mm ,圆整后有 D 1=100mm ,缸筒壁厚δ=10mm (2)液压缸的稳定性和活塞杆强度验算 按速比要求初步确定活塞杆直径后,还必须满足液压缸的稳定性及其
液压挖掘机动臂结构的优化设计
产? 结品!构 Productsandstructures 第39卷2008年7月 工程机械 图3 活动隔板示意图 (3)将骨料输送设备的输送倾角改为90°,可对骨料进行垂直输送,节约占地面积、设备投资和土建费用; (4)波状挡边带结构简单,各主要部件可以与普通带式输送机通用,便于使用和维修。 (5)运行可靠,没有刮板运输机经常出现的卡链、飘链、断链等现象和斗式提升机经常出现的打滑、掉斗等现象;同时也避免了普通波状挡边带的粘砂、落砂和除料困难等问题,它的可靠度几乎与通用 带式输送机相等。 参考文献 [1]宋伟刚,王丹,陈霖.波状挡边带式输送机的发展 [J].煤矿机械,2004(2):1-4. [2]宋伟刚,陈霖.波状挡边带式输送机的结构特点及 其改进设计[J].港口装卸,2003(3):25-27. [3]姜浩先.波状挡边带式输送机的设计选用[J].硫磷 设计与粉体工程,2001(1):39-43. [4] 夏炎.波状挡边输送带横隔板的结构及设计选用 [J].电子学报,1998(4):15-17. [5]方圆集团,山东建筑大学.建设机械设计制造与应 用[M].北京:人民交通出版社,2001. [6]田奇.混凝土搅拌楼及沥青混凝土搅拌站[M].北京:中国建材工业出版社,2005. [7] 陈宜通.混凝土机械[M].北京:中国建材工业出版社,2002. 通信地址:山东济南山东建筑大学机电工程学院(250101) (收稿日期:2008-04-01) 据相关资料报道,材料强度、断裂或开裂、零件失效等故障现象是机械可靠性不高的主要原因,也是制约我国工程机械出口的最大障碍[1]。现有的优化设计方法,如机械产品的广义优化设计,是面向全系统、全过程和全性能的优化设计。该方法着重考虑自零部件到整机,直至系列化和组合化产品在整个寿命周期中的技术性能、经济性能和社会性能,存在 着优化模型具有相当的复杂性和规模,不能有效地解决材料强度、断裂或开裂、零件失效等问题[2]。相关文献[3-4]分别建立了某液压挖掘机的反铲和正铲工作装置的优化数学模型,对挖掘力进行了优化。然而因各种原因,对液压挖掘机进行结构性能优化方面尚无人做过直接的研究工作[5-8]。因此,本文提出了以应力最小、全局刚度最大为优化目标的优化设计数 *基金项目:国家自然科学基金资助项目(50205026);重庆市自然科学基金资助项目(CSTC,2005BB3222) 液压挖掘机动臂结构的优化设计* 三 一 重 机 有 限 公 司 重庆大学机械传动国家重点实验室 陈健周 鑫 刘 欣 籍庆辉 杨 为 !!!!!!!!!!!!!!!!!!!!!!!!!!!!!!!!!!!!!!" !!!!!!!!" !!!!!!!!!!!!!!!!!!!!!!!!!!!!!!!!!!!!!!" !!!!!!!!" 摘 要:针对现有的优化设计方法不能有效地解决工程机械零部件使用寿命低、且存在优化模型复杂 和规模较大等问题,以液压挖掘机工作装置的动臂为研究对象,提出以有限元单元厚度为设计变量,以相同工况下应力最小、 全局刚度最大为优化目标的优化设计数学模型。在求解优化设计模型时,综合考虑刚度灵敏度和应力灵敏度对优化效率的影响,采取对全局灵敏度进行归一化处理的措施,大幅度降低了优化模型的求解规模,并对优化数学模型进行了求解。分析结果表明,利用该优化模型使动臂在相同工况下最 大应力降低了12.9%,局部刚度提高了29.8%,有助于延长动臂的使用寿命。工程实践证明,该优化方法减少了设计人员在结构设计中的盲目性,能高效地得到优化结果。 关键词:液压挖掘机 动臂 结构优化设计 数学模型 19— —
液压缸的设计计算2活塞杆的设计与计算
3.4.2活塞杆的设计与计算 活塞杆是液压缸专递动力的主要零部件,它要承受拉力、压力、弯力和震动冲击等多种作用,必须有足够的强度和刚度。 1、活塞杆直径的计算 根据活塞杆受力状况来确定,一般为受拉力作用时,d=0.3~0.5D 。 受压力作用时: P <5MPa 时,d=0.5~0.55D 5MPa <P <7MPa 时,d=0.6~0.7D P>7MPa 时,d=0.7D 因为P=1.5MPa ,D=0.066858mm ,故d=0.036771mm 根据下表可知活塞杆直径d=40mm 表3-3活塞杆直径系列mm (GB/T 2348-93) 2、活塞杆强度校核 (1)按强度条件校核 由公式 ] [4σπF d ≥ 式中 d---活塞杆的直径; F---活塞杆上的作用力; σ---活塞杆材料许用应力,n b σσ=, σ b 为材料的抗拉强度,n 为安
全系数,一般取4.1≥n 。 由45号钢的许用应力MPa n b 3735 .1560 == =σσ,N F 5000= 得 m d 00413.0≥,而mm d 40=,故活塞杆强度符合要求。 (2)按弯曲稳定性校核 当活塞杆全部伸出后,活塞杆外端到液压缸支撑点之间的距离d l 10>时,应进行稳定性校核。 按材料力学理论,当一根受压直杆的轴向载荷F 超过临界受压载荷F K 时,即可能失去原有直线状态的平衡,称为失稳,其稳定条件为 n F k k F ≤ 式中 F ---液压缸的最大推力; F K ---液压缸的临界受压载荷; n k ---稳定安全系数,一般取42-=n k 。 液压缸临界受压载荷F K 与活塞杆和缸体的材料、长度、刚度以及两端支撑状况有关。F K 的相关计算如下: 由公式 l F EJ n k 2 2π= 式中 l ---活塞杆的计算长度; n ---端点安装形式系数,两端固定,故4=n ; E---材料的弹性模量,钢材的Pa E 101.211 ?= ; J---活塞杆的横截面转动惯量,实心杆的64 4 d J π= 。