模具热处理方法
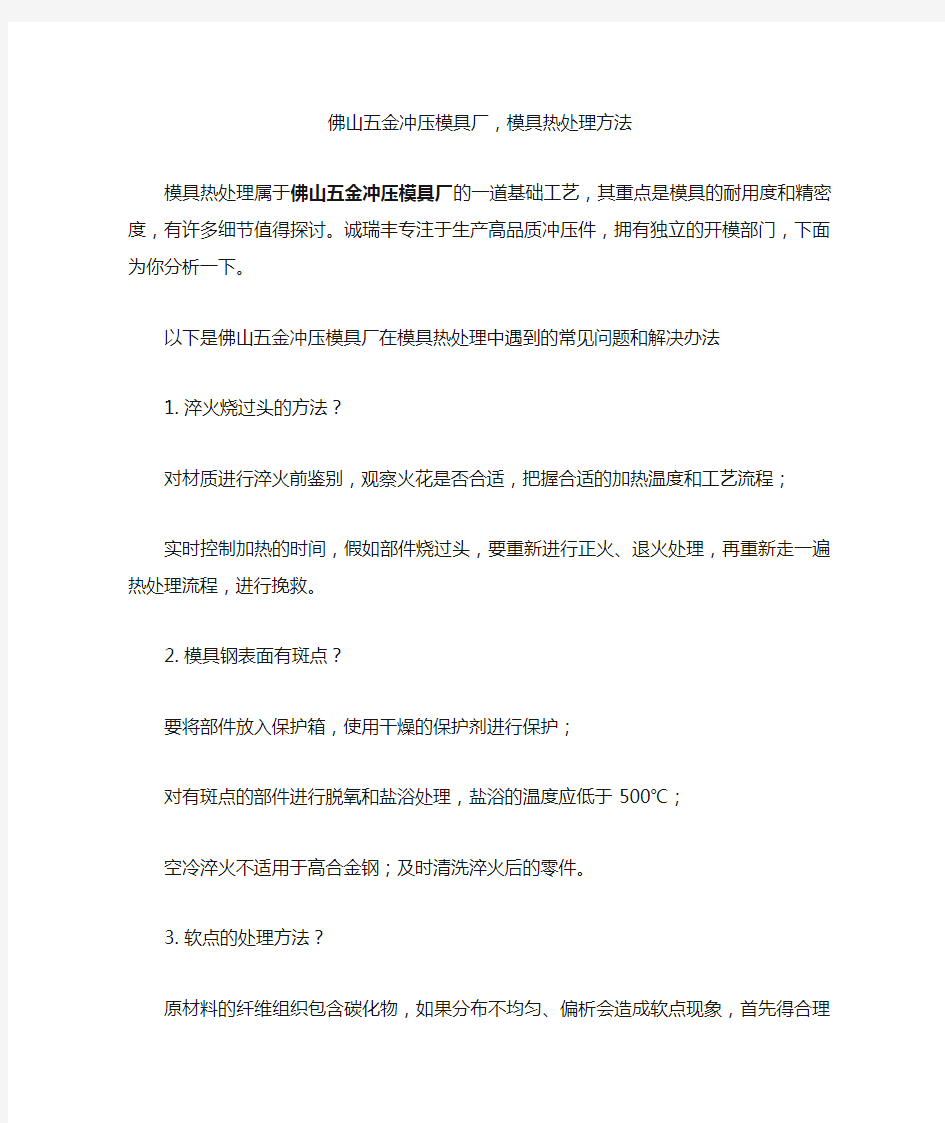

佛山五金冲压模具厂,模具热处理方法
模具热处理属于佛山五金冲压模具厂的一道基础工艺,其重点是模具的耐用度和精密度,有许多细节值得探讨。诚瑞丰专注于生产高品质冲压件,拥有独立的开模部门,下面为你分析一下。
以下是佛山五金冲压模具厂在模具热处理中遇到的常见问题和解决办法
1.淬火烧过头的方法?
对材质进行淬火前鉴别,观察火花是否合适,把握合适的加热温度和工艺流程;
实时控制加热的时间,假如部件烧过头,要重新进行正火、退火处理,再重新走一遍热处理流程,进行挽救。
2.模具钢表面有斑点?
要将部件放入保护箱,使用干燥的保护剂进行保护;
对有斑点的部件进行脱氧和盐浴处理,盐浴的温度应低于500℃;
空冷淬火不适用于高合金钢;及时清洗淬火后的零件。
3.软点的处理方法?
原材料的纤维组织包含碳化物,如果分布不均匀、偏析会造成软点现象,首先得合理选材;
加热时,工件表商有氧化皮、锈斑、造成表面脱碳,要认真检查,去除氧化皮、锈斑;
淬火介质老化或者杂质过多,需要定期清理、更换冷却介质,始终保持冷却介质;
操作要按照标准规范进行。
4.模具出现裂纹怎么办?
选材不当,要注意钢材的选择,加强管理,认真选择;
控制适当的加工温度,选择合理的工艺进行加工;
模片淬火前先去除应力;
在分级淬火时,要对模片进行分级冷却,放至室温才能进行清洗处理。
以上就是佛山五金冲压模具厂在热处理工艺上遇到的问题和解决办法,诚瑞丰生产高质量五金冲压件,拥有24年的开模下料经验,厂区面积达10万平米,欢迎联系合作。
常用热处理工艺【详情】
常用的几种热处理方法 内容来源网络,由深圳机械展收集整理! 更多相关表面处理及精密零件加工展示,就在深圳机械展! 1.常用热处理方式 1.1.退火 把钢加热到一定温度并在此温度下保温,然后缓慢冷却到室温。 退火有完全退火、球化退火、去应力退火等几种。 a.将钢加热到预定温度,保温一段时间,然后随炉缓慢冷却称为完全退火.目的是降 低钢的硬度,消除钢中不均匀组织和内应力. b.把钢加热到750度,保温一段时间,缓慢冷却至500度下,最后在空气中冷却叫球 化退火。目的是降低钢的硬度,改善切削性能,主要用于高碳钢。 c.去应力退火又叫低温退火,把钢加热到500~600度,保温一段时间,随炉缓冷到 300度以下,再室温冷却.退火过程中组织不发生变化,主要消除金属的内应力。 1.2.正火 将钢件加热到临界温度以上30-50℃,保温适当时间后,在静止的空气中冷却的热处理工艺称为正火。 正火的主要目的是细化组织,改善钢的性能,获得接近平衡状态的组织。 正火与退火工艺相比,其主要区别是正火的冷却速度稍快,所以正火热处理的生产周期短。故退火与正火同样能达到零件性能要求时,尽可能选用正火。 1.3.淬火 将钢件加热到临界点以上某一温度(45号钢淬火温度为840-860℃,碳素工具钢的淬火温度为760~780℃),保持一定的时间,然后以适当速度在水(油)中冷却以获得马氏体或贝氏体组织的热处理工艺称为淬火。 淬火与退火、正火处理在工艺上的主要区别是冷却速度快,目的是为了获得马氏体组织。马氏体组织是钢经淬火后获得的不平衡组织,它的硬度高,但塑性、韧性差。马氏体的硬度随钢的含碳量提高而增高。
1.4.回火 钢件淬硬后,再加热到临界温度以下的某一温度,保温一定时间,然后冷却到室温的热处理工艺称为回火。 淬火后的钢件一般不能直接使用,必须进行回火后才能使用。因为淬火钢的硬度高、脆性大,直接使用常发生脆断。通过回火可以消除或减少内应力、降低脆性,提高韧性;另一方面可以调整淬火钢的力学性能,达到钢的使用性能。根据回火温度的不同,回火可分为低温回火、中温回火和高温回火三种。 A 低温回火150~250.降低内应力,脆性,保持淬火后的高硬度和耐磨性。 B 中温回火350~500;提高弹性,强度。 C 高温回火500~650;淬火钢件在高于500℃的回火称为高温回火。淬火钢件经高温淬火后,具有良好综合力学性能(既有一定的强度、硬度,又有一定的塑性、韧性)。所以一般中碳钢和中碳合金钢常采用淬火后的高温回火处理。轴类零件应用最多。 淬火+高温回火称为调质处理。 2.Q235热处理工艺 Q235属于碳素结构钢,含碳量大概0.12%-0.2%之间,相当于普通的10、20钢,淬火后硬度改变不大。具有较高的强度,良好的塑性,韧性和焊接性能,综合性能好,能满足一般钢结构和钢筋混凝土结构用钢的要求。 Q235一般买来就用不热处理,一般它都用在工程上大量需要钢材的地方,数量巨大,一般是热轧后就使用,热轧也就是有正火这个热处理,不热处理的原因有几个: 1)这些场合不需要太高的力学要求。 2)这些钢构件的体积太大了,你想热处理也不现实。 3)这些钢很多情况下要被焊接使用的,你热处理了被焊接后也被焊接过程中将焊缝的 热处理给破坏了。 4)材料价格便宜,质量要求比较低,而且是低碳钢,热处理的效果也不太好。 5)如果非要用Q235淬出硬度那只能渗碳,但是一件很不划算的事情。 Q235在理论上是可以淬火得到马氏体的。但是由于马氏体碳过饱和度很低,淬火后的硬度很低,只有170HBS左右。而这种钢的供应状态硬度大概就有144HBS左右(出
常见的金属热处理
1.退火 操作方法:将钢件加热到Ac3+30~50度或Ac1+30~50度或Ac1以下的温度(可以查阅有关资料)后,一般随炉温缓慢冷却。 目的:1.降低硬度,提高塑性,改善切削加工与压力加工性能;2.细化晶粒,改善力学性能,为下一步工序做准备;3.消除冷、热加工所产生的内应力。 应用要点:1.适用于合金结构钢、碳素工具钢、合金工具钢、高速钢的锻件、焊接件以及供应状态不合格的原材料;2.一般在毛坯状态进行退火。 2.正火 操作方法:将钢件加热到Ac3或Accm 以上30~50度,保温后以稍大于退火的冷却速度冷却。 目的:1.降低硬度,提高塑性,改善切削加工与压力加工性能;2.细化晶粒,改善力学性能,为下一步工序做准备;3.消除冷、热加工所产生的内应力。 应用要点:正火通常作为锻件、焊接件以及渗碳零件的预先热处理工序。对于性能要求不高的低碳的和中碳的碳素结构钢及低合金钢件,也可作为最后热处理。对于一般中、高合金钢,空冷可导致完全或局部淬火,因此不能作为最后热处理工序。 3.淬火 操作方法:将钢件加热到相变温度Ac3或Ac1以上,保温一段时间,然后在水、硝盐、油、或空气中快速冷却。 目的:淬火一般是为了得到高硬度的马氏体组织,有时对某些高合金钢(如不锈钢、耐磨钢)淬火时,则是为了得到单一均匀的奥氏体组织,以提高耐磨性和耐蚀性。 应用要点:1.一般用于含碳量大于百分之零点三的碳钢和合金钢;2.淬火能充分发挥钢的强度和耐磨性潜力,但同时会造成很大的内应力,降低钢的塑性和冲击韧度,故要进行回火以得到较好的综合力学性能。 4.回火
操作方法:将淬火后的钢件重新加热到Ac1以下某一温度,经保温后,于空气或油、热水、水中冷却。 目的:1.降低或消除淬火后的内应力,减少工件的变形和开裂;2.调整硬度,提高塑性和韧性,获得工作所要求的力学性能;3.稳定工件尺寸。 应用要点:1.保持钢在淬火后的高硬度和耐磨性时用低温回火;在保持一定韧度的条件下提高钢的弹性和屈服强度时用中温回火;以保持高的冲击韧度和塑性为主,又有足够的强度时用高温回火;2.一般钢尽量避免在230~280度、不锈钢在400~450度之间回火,因为这时会产生一次回火脆性。 5.调质 操作方法:淬火后高温回火称调质,即将钢件加热到比淬火时高10~20度的温度,保温后进行淬火,然后在400~720度的温度下进行回火。 目的:1.改善切削加工性能,提高加工表面光洁程度;2.减小淬火时的变形和开裂;3.获得良好的综合力学性能。 应用要点:1.适用于淬透性较高的合金结构钢、合金工具钢和高速钢;2. 不仅可以作为各种较为重要结构的最后热处理,而且还可以作为某些紧密零件,如丝杠等的预先热处理,以减小变形。 6.时效 操作方法:将钢件加热到80~200度,保温5~20小时或更长时间,然后随炉取出在空气中冷却。 目的:1. 稳定钢件淬火后的组织,减小存放或使用期间的变形;2.减轻淬火以及磨削加工后的内应力,稳定形状和尺寸。 应用要点:1. 适用于经淬火后的各钢种;2.常用于要求形状不再发生变化的紧密工件,如紧密丝杠、测量工具、床身机箱等。 7.冷处理 操作方法:将淬火后的钢件,在低温介质(如干冰、液氮)中冷却到-60~-
模具材料及热处理
模具材料及热处理模具材料及热处理 1.金属组织 1.1金属 具有不透明、金属光泽良好的导热和导电性并且其导电能力随温度的增高而减小,富有延性和展性等特性的物质。金属内部原子具有规律性排列的固体(即晶体)。 1.2合金 由两种或两种以上金属或金属与非金属组成,具有金属特性的物质。 相:合金中成份、结构、性能相同的组成部分。 1.3固溶体 是一个(或几个)组元的原子(化合物)溶入另一个组元的晶格中,而仍保持另一组元的晶格类型的固态金属晶体,固溶体分间隙固溶体和置换固溶体两种。 1.4固溶强化 由于溶质原子进入溶剂晶格的间隙或结点,使晶格发生畸变,使固溶体硬度和强度升高,这种现象叫固溶强化现象。 1.5化合物 合金组元间发生化合作用,生成一种具有金属性能的新的晶体固态结构。 1.6机械混合物 由两种晶体结构而组成的合金组成物,虽然是两面种晶体,却是一种组成成分,具有独立的机械性能。2.金属硬度 2.1硬度 金属的硬度,是指金属表面局部体积内抵抗外物压入而引起的塑性变形的抗力,硬度越高表明金属抵抗塑性变形的能力越强,金属产生塑性变形越困难。硬度试验方法简单易行,又无损于零件。实际常使用的硬度试验方法有:布氏硬度、洛氏硬度和维氏硬度三种。三种硬度试验值有大致的换算关系,见表一。 布氏硬度HB:布氏硬度是用载荷为P的力把直接D的钢球压入金属表面,并保持一定的时间,测量金属表面上的压痕直径d,据此计算出的压痕面积AB,求出每单位面积所受力,用作金属的硬度值,叫布氏硬度,记作HB。布氏硬度的使用上限是HB450,适用于测定退火、正火、调质钢、铸铁及有色金属的硬度。 2.1.1洛氏硬度HRA、HRC: 洛氏硬度是工业生产中最常用的硬度测量的方法,因为操作简便、迅速,可以直接读出硬度值,不损伤工件表面,可测量的硬度范围较宽。但洛氏硬度也有一些缺点,如因压痕小,对材料有偏析及组织不均匀的情况,测量结果分离度大,再现性较差。洛氏硬度(HR)也是用压痕的方式试验硬度。它是用测量凹陷深度来表示硬度值。洛氏硬度试验用的压头分硬质和软质两种。硬质压头为顶角为120o的金刚石圆锥体,使用于淬火钢等硬的材料。HRA硬度有效范围是>70,适用于硬质合金、表面淬火层及渗碳层;HRC硬度有效范围是20-68(相当于HB230-700,HB450-700超出了布氏硬度的使用上限),适用于淬火钢及调质钢。 2.1.2洛氏硬度HRB 洛氏硬度HRB的测量采用直径1.588mm(1/16")的钢球,适用于退火钢、有色金属等,硬度有效范围是25-100(相当于HB60-230)。 2.1.3维氏硬度HV 维氏硬度也是利用压痕面积上单位应力作为硬度值计量。维氏硬度所使用的压头是锥面夹角为136o的金刚石四方锥体。试验时,在载荷P的作用下,在试样试验面上压出一个正方形压痕。测量压痕两对角线的平均长度d,借以计算压痕面积A V,以P/A V的数值表示试样的硬度,以HV表示。维氏硬度的优缺点:维氏硬度有一个连续一致的标度;试验负荷可任意选择,所得的硬度值相同。试验时加载的压力小,压入深度浅,对工件损伤小。特别适用于测量零件的表面淬硬层及经过表面化学处理的硬度,精度比布氏、洛氏硬度精确。但是维氏硬度的试验操作较麻烦,一般在生产上很少使用,多用于实验室及科研方面。
1简述常用的热处理的方法及时效处理
1简述常用的热处理的方法及时效处理。 答:常用热处理方法:退火,正火,淬火,回火,渗碳,渗氮,碳氮共渗,渗硼。时效处理有人工时效处理,自然时效处理。 退火,将工件加热至Ac3以上30~50度,保温一定时间后,随炉缓慢冷却至500度一下在空间中冷却。 正火,将钢件加热至Ac3或Acm以上,保温后从炉中取出在空气中冷却的一种操作。 淬火,将钢件加热至Ac3或Ac1以上,保温后在水或油等冷却液中快速冷却,已获得不稳定的组织。 回火,将淬火后的钢重新加热到Ac1以下的温度,保温后冷却至室温的热处理工艺。 自然时效处理,将工件放置在室温或自然条件下长时间存放而发生的时效现象,称为自然时效处理。 人工时效处理,采用将工件加热到较高温度,并较短时间进行时效处理的时效处理工艺,叫人工时效处理。 2简述钢回火的目的 答:回火又称配火。将经过淬火的工件重新加热到低于下临界温度的适当温度,保温一段时间后在空气或水、油等介质中冷却的金属热处理。或将淬火后的合金工件加热到适当温度,保温若干时间,然后缓慢或快速冷却。目的:一般用以减低或消除淬火钢件中的内应力,或降低其硬度和强度,以提高其延性或韧性。根据不同的要求可采用低温回火、中温回火或高温回火。通常随着回火温度的升高,硬度和强度降低,延性或韧性逐渐增高。 3简述钢的表面淬火的作用及分类。 答:有些零件在工件时在受扭转和弯曲等交变负荷、冲击负荷的作用下,它的表面层承受着比心部更高的应力。在受摩擦的场合,表面层还不断地被磨损,因此对一些零件表面层提出高强度、高硬度、高耐磨性和高疲劳极限等要求,只有表面强化才能满足上述要求。由于表面淬火具有变形小、生产率高等优点,因此在生产中应用极为广泛。 根据供热方式不同,表面淬火主要有感应加热表面淬火、火焰加热表面淬火、电接触加热表面淬火等。 4简述感应热处理技术的工作原理及特点。简述超音频感应淬火的工作频率及频率和淬硬层厚度的关系。 答:基本原理将工件放入感应器(线圈)内,当感应器中通入一定频率的交变电流时,周围即产生交变磁场。交变磁场的电磁感应作用使工件内产生封闭的感应电流──涡流。感应电流在工件截面上的分布很不均匀,工件表层电流密度很高,向内逐渐减小, 这种现象称为集肤效应。工件表层高密度电流的电能转变为热能,使表层的温度升高,即实现表面加热。电流频率越高,工件表层与内部的电流密度差则越大,加热层越薄。在加热层温度超
4Cr5MoSiV热挤压模具热处理工艺参考word
4Cr5MoSiV热挤压模具热处理工艺 §1 热处理工艺课程设计的目的 热处理工艺课程设计是高等学校金属材料工程专业一次专业课设计练习,是热处理原理与工艺课程的最后一个教学环节。其目的是:(1)培养学生综合运用所学热处理课程的知识去解决工程问题的能力,并使其所学知识得到巩固和发展。 (2)学习热处理工艺设计的一般方法、热处理设备选用和夹具设计等。 (3)进行热处理设计的基本技能训练,如计算、零件绘图和学习使用设计资料、手册、标准和规范。 因此,本课程设计要求我们综合运用所学知识来解决生产实践中的热处理工艺制定问题,包括工艺设计中的细节问题,如设备的选用,夹具的设计等。要求我们设计工艺流程,这需要翻查大量的文献典籍。如何灵活使用资料、手册,怎样高效查找所需信息,以及手册的查找规范和标准等,均不是一蹴而就的事情,需要我们在实践中体会并不断地总结,才能不断进步。 材料热处理工艺课程设计是培养材料专业学生在热处理原理方面能力的重要环节,纸上谈兵是经不起考验的,扎实的理论唯有通过实践才能够证明,且科学的实践能够有效巩固甚至发展原有的理论,因此,本课程设计通过给出20余种不同牌号的材料,要求学生以个人(允许讨论)或组队的方式完成热处理工艺的设计,对学生巩固已学热处理知识、学习使用工具书、增强团队合作意识等是大有裨益的。
§2零件的技术要求及选材 2.1热挤压模具的工作条件 热挤压模具用于机器零件和型材的挤压成型,主要有冲头、凹模及其他辅助部分组成,其工作条件决定于挤压设备的类型、被挤压材料的性质、加热温度及挤压工艺等因素。 (1)热挤压模具的工作温度热挤压模具在挤压铜合金、钛合金时,工作温度可达600~800℃,甚至更高。 (2)热挤压模具工作时的冷却条件在工作过程中,热挤压模具都被强制冷却,以免模具的温升过高。 (3)热挤压模具的受力条件热挤压冲头在工作时要受到大的压力、弯矩及循环热应力的作用。凹模的模腔受大的压应力和拉应力的作用, 易生脆裂,还要受到摩擦和热疲劳的作用。 2.2热挤压模具的失效形式 热挤压模具常见的失效形式有早期脆断、热疲劳、疲劳断裂、堆塌及磨损等。热挤压模具由于工作温度较高,因此,除脆断外,型腔堆塌及磨损就成为热挤压模具的主要失效形式。 2.3热挤压模具材料的选用 影响热作模具寿命的因素很多,例如模具的受力情况、工作温度、冷却方式,被加工材料的性质、变形量、变形速度以及润滑条件等。因此,在选择材料时,应根据模具的类型及具体工作条件合理的选用。
金属材料热处理方法有几种
金属材料热处理方法有几种?各有什么特点? 金属材料热处理方法有退火、谇火及回火,渗碳、氮化及氰化等。 (1) 退火处理 退火处理按工艺温度条件的不同,可分为完全退火、低温退火和正火处理。 ①完全退火是把钢材加热到Ac3 (此时铁素体开始溶解到奥氏体中,指铁碳合金平衡图中Ac3,即临界温度)以上20?30℃,保温一段时间后,随炉温缓冷到400?500(,然后在空气中冷却。 完全退火适用于含碳量小于0.83%的铸造、锻造和焊接件。目的是为了通过相变发生重结晶,使晶粒细化,减少或消除组织的不均匀性,适当降低硬度,改善切削加工性,提高材料的韧性和塑性,消除内应力。 ②低温退火是一种消除内应力的退火方法。对钢材进行低温退火时.先以缓慢速度加热升温至500?600匸,然后经充分的保温后缓慢降温冷却。 低温退火(消除内应力退火)主要适用于铸件和焊接件,是为了消除零件铸造和焊接过程中产生的内应力,以防止零件在使用工作中变形。采用这种退火方法,钢材的结晶组织不发生变化。 ③正火是退火处理中的一种变态,它与完全退火不同之处在于零件的冷却是在静止的空气中,而不是随炉缓慢降温冷却。正火处理后的晶粒比完全退火更细,增加了材料的强度和韧性,减少内应力,改善低碳钢的切削性能。 正火处理主要适合那些无需调质和淬火处理的一般零件和不能进行淬火和调质处理的大型结构零件。正火时钢的加热温度为753?900°C。 (2) 淬火及回火处理 淬火可分整体淬火和表面淬火,淬火后的钢一般都要进行回火。回火是为了消除或降低淬火钢的残余应力,以使淬火后的钢内纟且织趋于稳定。钢材淬火后为了得到不同的硬度,回火温度可采用几种温度段。 ①淬火后低温回火目的是为了降低钢中残余应力和脆性、而保持钢淬火后的高硬度和耐磨性,硬度在HRC58?64范围内。适合于各种工具、渗碳零件和滚动轴承。回火温度为150?250匸。 ②淬火后中温回火目的是为了保持钢材有一定的韧性、在此基础上提高其弹性和屈服极限。适合于各种弹簧、锻模及耐冲击工具等。回火温度为350?500",淬火后回火得到的钢材硬度为HRC 35?45。 ③淬火后高温回火这种回火温度处理通常称之为调质处理。回火温度为500?650℃,材料的硬度为HRC25?35。 调质处理广泛应用在齿轮与轴的机械加工工艺中,以使零件在塑性、韧性和强度方面有较好的综合性能。 表面淬火是使零件的表面有较髙的硬度和耐磨性,而零件的内部(心部)有足够的塑性和韧性。如承受动载荷及摩擦条件下工作的齿轮、凸轮轴、曲轴颈等,均应进行表面淬火处理。 表面淬火用钢材的含碳量应大于35%,如45、40Cr、40Mn2 等钢材,都比较适合表面淬火。表面谇火的方法可分为表面火焰淬火和表面髙频淬火。 a. 表面火焰淬火是用高温的氧-乙块火焰,把零件表面加热到Ac3线以上温度,
s136模具钢热处理工艺
S136热处理工艺 在保护状态下,加热至780℃,然后在炉中以每小时10℃的速度,冷却至650℃,接着再置于空气中冷却。 应力消除 经过粗加工后,必须加热至650℃,均热2小时,缓慢冷却至500℃,然后置于空气中冷却 保温时间=当钢材的表面及中心达到一致的淬火温度后,才开始计算在炉中的保温时间。 淬火时必须保护,以避免脱碳及氧化。 冷却介质 ●油 ●流动粒子炉或盐裕炉250-550℃分级淬火,然后冷却于高速空气中●高速气体/真空炉中具有足够正压的气体为求模具达到最适当的特性,在模具的变形程度可接受的条件下,冷速越快越好。于真空炉中热处理时推荐使用4-5b a r的气压。
钢材冷却至50-70℃应立即回火。 硬度、晶粒大小、残余奥氏体数量于奥氏体化温度的关系图。 回火 参照回火曲线图按所需硬度值选择回火温度。回火两次,每次回火后,必须冷却到室温,最低的回火温度为180℃(适用于小件)。保温时间至少两小时。 回火曲线图
注1:建议250℃回火求韧性,硬度及抗腐蚀性的最好组合。 注2:以上的曲线数据只适宜小型模具。模具可达的硬度要视模具的尺寸。 注3:应避免选用过高的奥氏体化温度与过低的回火温度<250℃的组合,皮棉模具产生太大的应力。 尺寸变形 淬火及回火时的温度,不同种类的炉具及淬冷介质,会影响模具尺寸的改变。模具的尺寸与几何形状也同样重要。模具在加工时应预留加工量以弥补热处理后的尺寸变形。 在粗加工与半精加工之间建议预留0.15%作为S TAVA X E S T(S-136)的加工预留指标。 淬火过程的尺寸改变 试片100*100*25毫米经正规的热处理程序,在淬火时的尺寸改变。
常见的热处理方法
常见的热处理方法、目的和工序位置的安排 由于热处理工序安排对车削类工艺影响较大,更重要的是往往由于热处理工序安排颠倒,使工件无法继续加工,而且所产生的废品往往是无法挽回的。为此对热处理工序的安排要加以了解,并引起重视。 下面将常见的热处理方法、目的和工序位置的安排分别介绍如下: 一、预备热处理 预备热处理包括退火、正火、调质和时效等。这类热处理的目的是改善加工性能,消除内应力和为最终热处理做好组织准备。退火、正火、调质工序多数在粗加工前后,时效处理一般安排在粗加工、半精加工以后,精加工之前。 1.退火和正火 目的是改善切削性能,消除毛坯内应力,细化晶粒,均匀组织;为以后热处理作准备。 例如:含碳量大于0.7%的碳钢和合金钢,为降低硬度便于切削加工采用退火处理; 含碳量低于0.3%的低碳钢和低合金钢,为避免硬度过低切削时粘刀,而采用正火适当提高硬度。 一般用于锻件、铸件和焊接件。退火一般安排在毛坯制造之后,粗加工之前进行。2.调质 目的是使材料获得较好的强度、塑性和韧性等方面的综合机械性能,并为以后热处理作准备。 用于各种中碳结构钢和中碳合金钢。调质一般安排在粗加工之后,半精加工之前。 调质是最常用的热处理工艺。大部分的零件都是通过调质处理来提高材料的综合机械性能,即提高拉伸强度、屈服强度、断面收缩率、延伸率、冲击功。调质处理能大大提高材料的拉伸和屈服强度,提高屈强比和冲击功,使材料具有强度和塑韧性的良好配合。由于屈服强度、疲劳强度、冲击强度的提高,在零件设计时就可以采用更小的材料截面,从而减少机械设备的整体重量,节省零件占用空问和能量消耗。因此在某些场合为了减少机械空间和机械重量在设计过程中要有意识地利用调质工艺。 需要强调的是,一般来讲调质钢应该为中碳钢( C = 0.3%~0.6%);碳钢中像30、 35、40、45、50等钢种则既可以调质处理又可以正回火使用;而对高碳钢和低碳钢则 不宜采用调质工艺 调质过程是淬火加高温回火。首先需要将零件加热到材料的Acl点以上30~50℃ (800.950℃),保温一定时间,然后在油中或水中冷却。冷却后立即入炉进行回火(500~650℃),以降低淬火应力、调整组织成份,进而达到机械性能要求。而回火温度的制定是根据硬度或性能高低而定的,硬度和强度越高,回火温度越低。调质工序后的任何高于回火温度的加热,都将降低已达到的强度。 选择调质处理时应特别注意以下几点: (1)图纸中应明确要求 应明确写明“调质”。若只写“热处理…H B”外协厂家可能采用其他热处理工艺,比如正回火达到所要求的硬度。而正回火所达到的同样硬度的材料其屈服强度和冲击功会非常低。实际工作中曾发生过地脚螺栓使用时发生早期断裂的事故就是由此导致的。 (2)调质的硬度和硬度范围 要按材料标准选择调质的硬度和硬度范围。这一方面有利于工厂配炉生产,另一方面过窄的硬度范围要求在实际生产中根本无法满足。
关于模具热处理的一些经验
关于模具热处理的一些经验分享~ 2016-01-01 1. H13模具钢如何热处理硬度才能达到58度? 进行1050~1100度加热淬火,油淬,可以达到要求,但一般热作模具是不要求这么高的硬度的,这么高的硬度性能会很差,不好用,一般在HRC46~50左右性能好、耐用。 2. 模具热处理过后表面用什么洗白? 问题补充:我是开模具抛光店的,一般模具都用油石先打过再拿去渗氮,渗氮回来又要用油石把那一层黑的擦白,再抛光很麻烦,不擦白打不出镜面来,材料有H13 的,有进口的好多种,如果有药水能洗白的话,就可以直接抛光了。 (1)可以用不锈钢酸洗液,或者盐酸清洗。喷砂处理也可以。磨床磨的话费用高,而且加工量大,有可能使尺寸不达标的。盐酸洗不掉的话,估计您用的是高铬的模具钢?是D2还是H13?高铬模具钢的氧化层比较难洗掉。用不锈钢酸洗液应该可以,磨具商店或者不锈钢商店都有卖的。 (2)你们没有不锈钢酸洗膏吗?那种可以。H13这类含铬比较高的模具钢,氧化层是难以用盐酸洗掉的。还有一个办法,我自己也在用。你们的模具既然已经油石磨过,表面就是比较光滑的。实际上,可以先只用粗的油石打磨,或者用
砂带打磨,之后就去热处理。回来之后再用细油石打磨。而我用的办法是,用纤维轮先打磨,就可以有效的把黑皮去除,再研磨抛光。或者喷砂,用800 目的碳化硼做一遍喷砂试试,应该就能够去除黑皮,还不需要化太多功夫重磨。 3.热处理厂对金属是怎么热处理的? 热处理厂的设备非常多,炉子大概有箱式炉,井式炉,箱式炉用的最多,很多热处理都可以在这里面处理,比如退火,正火和淬火的加热过程,回火这些常见的热处理。 其实就是一个用电加热的炉子,先将炉子升温到预定温度,然后把工件丢进去,等待一段时间到预定温度,然后保温一段时间,然后取出,或者在炉子里一起冷却,井式炉一般是作为渗碳处理设备,是一个埋到地下的炉子,工件放进去之后,密封,然后往炉子里面滴入一些富碳液体,比如煤油或则甲醇,然后在高温下这些液体分解成碳原子渗入工件表面。 淬火池是淬火的场所,就是一个池子,里面有水溶液或者是油,就是箱式炉出来的工件淬火的冷却的地方,一般就是直接丢进去,然后等一段时间捞出来。还有其他的一些设备,比如高频机,就是一个可以将50 赫兹的工频电变成一个200K 赫兹电流的超大功率的设备,比如常见的有200 千瓦的最大功率,然后用一个内部通冷却水的铜管做的线圈放在工件的外面,一般几十毫米的工件,几秒种到十几秒的时候你就看到工件表面变红,表面温度到预定值的时候,然后有一个水套升上来喷淬火液到工件表面,完成淬火过程。常见的就这些了。 4.我们最近的Cr12 或Cr12MoV 的材料热处理和裂了几次了,为什么
常见零件的热处理方式
一、齿轮 1.渗碳及碳氮共渗齿轮的工艺流程 毛坯成型→预备热处理→切削加工→渗碳(碳、氮共渗)、淬火及回火→(喷丸)→精加工2.感应加热和火焰加热淬火齿轮用钢及制造工艺流程 配料→锻造→正火→粗加工→精加工→感应或火焰加热淬火→回火→珩磨或直接使用调质 3.高频预热和随后的高频淬火工艺流程 锻坯→正火→粗车→高频预热→精车(内孔、端面、外圆)滚齿、剃齿→高频淬火→回火→珩齿 二、滚动轴承 1.套圈工艺流程 棒料→锻制→正火→球化退火 棒料→钢管退火磨→补加回火→精磨→成品 2.滚动体工艺流程 (1)冷冲及半热冲钢球 钢丝或条钢退火→冷冲或半热冲→低温退火→锉削加工→软磨→淬火→冷处理→低温回火→粗磨→补加回火→精磨→成品 (2)热冲及模锻钢球 棒料→热冲或模锻→球化退火→锉削加工→软磨→淬火→冷处理→低温回火→粗磨→补加回火→精磨→成品 (3)滚子滚针 钢丝或条钢(退火)→冷冲、冷轧或车削→淬火→冷处理→低温回火→粗磨→附加回火→精磨→成品 三、弹簧 1.板簧的工艺流程
切割→弯制主片卷耳→加热→弯曲→余热淬火→回火→喷丸→检查→装配→试验验收 2.热卷螺旋弹簧工艺流程 下料→锻尖→加热→卷簧及校正→淬火→回火→喷丸→磨端面→试验验收 3.冷卷螺旋弹簧工艺流程 下料→锻尖→加热→卷簧及校正→去应力回火→淬火→回火→喷丸→磨端面→试验验收 四、汽车、拖拉机零件的热处理 1.铸铁活塞环的工艺流程 (1)单体铸造→机加工→消除应力退火→半精加工→表面处理→精加工→成品 (2)简体铸造→机加工→热定型→内外圆加工→表面处理→精加工→成品 2.活塞销的工艺流程 棒料→粗车外圆→渗碳→钻内孔→淬火、回火→精加工→成品 棒料→退火→冷挤压→渗碳→淬火、回火→精加工→成品 热轧管→粗车外圆→渗碳→淬火、回火→精加工→成品 冷拔管→下料→渗碳→淬火、回火→精加工→成品 3.连杆的工艺流程 锻造→调质→酸洗→硬度和表面检验→探伤→校正→精压→机加工→成品 4.渗碳钢气门挺杆的工艺流程 棒料→热镦→机加工成型→渗碳→淬火、回火→精加工→磷化→成品 5.合金铸铁气门挺杆的工艺流程 合金铸铁整体铸造(间接端部冷激)→机械加工→淬火、回火→精加工→表面处理→成品合金铸铁整体铸造(端部冷激)→机械加工→消除应力退火→精加工→表面处理→成品钢制杆体→堆焊端部(冷激)→回火→精加工→成品 钢制杆体→对焊→热处理→精加工→表面处理→成品 6.马氏体型耐热钢排气阀的工艺流程 马氏体耐热钢棒料→锻造成型→调质→校直→机加工→尾部淬火→抛光→成品 7.半马氏体半奥氏体型耐热钢(Gr13Ni7Si2)排气阀的工艺流程
(数控模具设计)冷冲压模具的热处理工艺精编
(数控模具设计)冷冲压模具的热处理工艺
5.1冷冲压模具的常规热处理工艺 1退火 将组织偏离平衡状态的钢加热到适当温度,保温壹定时间,然后缓慢冷却(壹般为随炉冷却),以获得接近平衡状态组织的热处理工艺叫做退火。 根据处理的目的和要求不同,钢的退火可分为完全退火、等温退火、球化退火、扩散退火和去应力退火等等。各种退火的加热温度范围和工艺曲线如图5-1所示。 (1)完全退火 完全退火又称重结晶退火,是把钢加热至Ac3之上20-30℃,保温壹定时间后缓慢冷却(随炉冷却或埋入石灰和砂中冷却),以获得接近平衡组织的热处理工艺。亚共析钢经完全退火后得到的组织是F+P。 完全退火的目的在于,通过完全重结晶,使热加工造成的粗大,不均匀的组织化和细化,以提高性能;或使中碳之上的碳钢和合金钢得到接近平衡状态的组织,以降低硬度,改善切削加工性能。由于冷却速度缓慢,仍能够消除内应力。 45钢经锻造及完全退火后的性能见表5-1 表5-145钢锻造后和完全退火后的机械性能比较
完全退火主要用于亚共析钢,过共析钢不宜采用,因为加热到Accm之上慢冷时,二次渗碳体会以网状形式沿奥氏体晶界析出,使钢的韧性大大下降,且可能在以后的热处理中引起裂纹。 (2)等温退火 等温退火是将钢件或毛坯加热到高于Ac3(或Ac1)的温度,保温适当时间后,较快地冷却到珠光体区的某壹温度,且等温保持,使奥氏体转变为珠光体组织,然后缓慢冷却的热处理工艺。 等温退火的目的和完全退火相同,但转变较易控制,能获得均匀的预期组织;对于奥氏体较稳定的合金钢,常可大大缩短退火时间。 (3)球化退火 球化退火为使钢中碳化物球状化的热处理工艺。 球化退火主要用于过共析钢如工具钢、滚珠轴承钢,目的是使二次渗碳体及珠光体中的渗碳体球状化(退火前正火将网状渗碳体破碎),以降低硬度,改善切削加工性能;且为以后的淬火作组织准备。 球化退火壹般采用随炉加热,加热温度略高于Ac1,壹边保留较多的未溶碳化物粒子或较大的奥氏体中的碳浓度分布不均匀性,促进球状碳化物的形成。若加热温度过高,二次渗碳体易在慢冷时以网状的形式析出。球化退火需要较长的保温时间来保证二次渗碳体的自发球化。保温后随炉冷却,在通过Ar1温度范围时,应足够缓慢,以使奥氏体进行共析转变时,以未溶渗碳体粒子为核心形成粒状渗碳体。 (4)扩散退火
常用热处理方法
一、退火 将钢件加热到临界温度以上(不同钢号它的临界温度也不同,一般是 710-750℃,个别合金钢到800或900℃),在此温度停留一段时间,然后缓慢冷却的过程叫做退火 退火的目的是: 1、降低硬度,便于切削加工; 2、细化晶粒,均匀组织,以改善钢件毛坯的机械性能,或者为下一步淬火 做好准备; 3、消除内应力 二、正火 将钢件加热到临界温度以上,在此温度停留一段时间,然后放在空气中冷却的过程称为正火。 正火的冷却速度比退火快,加热和保温时间与退火一样。 正火的目的是使低碳和中碳钢件及渗碳机件的组织细化,增加强度与韧性,减少内应力,改善切削性能。 正火实质上是退火的一种特殊形式具有与退火相似的目的所不同的是冷却 速度比退火快,可以缩短生产周期,比较经济。 三、淬火 将钢件加热到临界点以上,保温一段时间,然后在水、盐水或油中(个别材料在空气中)急速冷却的过程叫做淬火。 淬火的目的是提高钢件的硬度和强度。对于工具刚来说,淬火的主要目的是提高它的硬度,以保证刀具的切削性能和冲模工具及量具的耐磨性。对于中碳钢制造的机件来说,淬火是为以后的回火做好结构和性能上的准备,因为高强度和高韧性并不能在淬火后同时得到,而是在回火处理后才得到的。 有很多零件如齿轮、曲轴等,他们在工作时一方面要受磨,另一方面又要受到冲击作用,因此要求零件表面有很高的硬度,而中心有较好的韧性。这时可以利用表面淬火的方法来达到上述要求。 表面淬火是应用将工件的表面迅速加热到淬火温度(这时金属内部的温度仍比较低),随后立即用水喷到工件表面上,进行急速冷却。这样就能获得表面硬、中心韧的要求。 表面加热时,可用氧炔焰、高频电流或中频电流加热。 四、回火 将淬硬的钢件加热到临界点以下的温度,保温一段时间,然后在空气中或油中冷却下来的过程叫做回火。 回火的目的是消除淬火后的脆性和内应力,调整组织,提高钢件的塑性和冲击韧性。对于工具来说,是为了尽可能减少脆性保留硬度。对于零件来说是为了提高韧性,但不可避免的会使硬度降低。 五、调质 淬火后高温回火,叫做调质。 调质的目的是使钢件获得很高的韧性和足够的强度,使其具有良好的综合机械性能。很多重要零件如主轴、丝杠、齿轮等都是经过调质处理的。 调质一般是在零件机械加工后进行的,也可把锻坯或经过粗加工的光坯调质后再进行机械加工。 六、时效
模具加工与材料热处理
材料與熱處理 一、填空題 1).金屬在加熱或冷卻過程中,發生相變的溫度稱為臨界點。(H0200F001A) 2).鐵素體為體心立方晶格。(H0200F002A) 3).自行回火是利用淬火冷卻后零件內部尚存的熱量,待其返回淬火層, 使淬火層得到回火。(H0200F003A) 4)常用的熱處理“四把火”是指、正火、退火、淬火、回火。(H0200F004A) 5).過冷奧氏體是指冷卻到A1溫度下,尚未轉變的奧氏體。(H0200F005A) 6).碳在a--Fe中的過飽和固溶體稱為馬氏體。(H0200F006A) 7).工業用的金屬材料可分為黑色金屬、有色金屬兩大類。(H0200F007A) 8).布氏硬度的符號用HR A和HRB 表示。(H0200F008A) 9).描述原子在晶體中排列方式的空間格架稱為晶格。(H0200F009A) 10).金屬在固態下,隨溫度的改變,由一种晶格轉變為另一种晶格的現象稱 為同素異構轉變。(H0200F010A) 11).鋼中最常見的雜質元素有S、Mn、Si、P等,其中Si和Mn是有益元素。 (H0200F011A) 12).45鋼按碳的質量分數WC分類屬于中碳鋼。(H0200F012A) 13)淬火的目的是為了獲得馬氏體或貝氏體組織。(H0100F013A) 14).馬氏體的硬度隨著含碳量的增加而增高。(H0200F014A)
15).淬火溫度過高,滲碳體全部溶解,淬火后殘余奧氏體增多,硬度偏低,則性能變 差。(H0200F015A) 16).深冷處理的目的主要是提高硬度、穩定尺寸以及提高鋼的磁性。 (H0200F016A) 17).時效處理的目的,使馬氏體繼續析出碳化物降低其正方度,使殘餘奧氏 體穩定化並消除殘餘應力。(H0200F017A) 18).感應加熱淬火后的零件也需進行回火處理,這是減少內應力、防止裂 紋發生及防止變形的重要工序。(H0200F018A) 19)熱處理就是將工件放在一定的介質中加熱、保溫和冷卻,通過改 變金屬材料表面或內部的組織結構來控制其性能的工藝方法. (H0200F019A) 20)退火是將鋼加熱至適當溫度,保溫一定時間,然后緩慢冷卻以獲得近于平衡態組織的熱處理工藝。(H0200F020A) 21)正火是將鋼材加熱到臨界點以上適當溫度,保溫一定時間,然后在空氣中冷卻,得到以索氏體為主的組織。(H0200F021A) 22)最常用的陽极氧化工藝是硫酸陽极氧化工藝。(H0200F022A) 23)淬火變形包括尺寸變化和形狀變化兩種。(H0200F023A) 24).灰鑄鐵中的碳是以片狀石墨形式存在的。(H0100F024A) 25).磨削裂紋的特征是,裂紋總是垂直於磨削方向或是裂紋呈龜甲狀。 (H0200F025A)
模具热处理
一.技术先进 QPQ盐浴复合处理技术是世界最新金属表面强化技术。该技术通过在金属表面渗入多种合金元素,从而大幅度提高产 品的耐磨性能。它被广泛用于汽车、机车、工程机械、纺织机械、轻工机械、仪表、工模具等各种行业。自德国DEGUSSA 公司推出QPQ技术后,其用户遍及德、美、英、日等国约800多家.如:美国的通用电器[GE]公司有该工艺不仅成功的取代了镀硬铬工艺,改善了机车柴油机缸套的耐磨、耐蚀性、而且降低了成本,同时消除了六价铬的公害;日本本田公司有数套自动化的QPQ设备分设国内外,有150多种汽车、摩托车零件采用了此技术,年处理量6万吨;丰田和日本公司每月数百吨零件采用此技术处理.国内的杀害大众汽车等众多厂家采用此技术有于大量处理曲轴、模具、工具、汽车、柴油机、摩托车、纺织配件等. 二.性能优良 1.比较的表面硬度 产品经QPQ处理2-3小时,总渗层可到达0.4-0.6MM,下面是部分材料 经QPQ处理后的白亮深度和硬度: 材料牌号举列前处理处理温度处理时间表面硬度Hv0.1 白亮层深度 纯铁 570 2-4小时 500-650 12-25μ 底碳钢 A3,20,20Cr 570 2-4小时 550-770 12-25μ 中碳钢 45,40Cr 570 2-4小时 550-770 12-25μ 高碳钢 T8,T12 570 2-4小时 550-770 2-25μ 氮化钢 38CrMoAL调质 570 2-4小时 950-1050 12-20μ 铸模钢 3Cr2W8V 淬火 570 2-3小时 950-1000 10-17μ 热模钢 5CrMnMo淬火 570 2-3小时 770-900 10-20μ 冷模钢 Cr12MoV高温淬火 520 2-3小时>950 10-20μ 高速钢 W6Mo5Cr4V2[刀具] 淬火 550 4-45分钟 1000-1300
常用热处理方法.
常用热处理方法 一、热处理是通过加热、保温、冷却三个环节来实现的。加热、保温、冷却是热处理的三要素。 二、热处理的基本工艺 1、钢的退火 将钢加热到一定温度并保温一段时间,然后使它慢慢冷却,称为退火。钢的退火是将钢加热到发生相变或部分相变的温度,经过保温后缓慢冷却的热处理方法。退火的目的,是为了消除组织缺陷,改善组织使成分均匀化以及细化晶粒,提高钢的力学性能,减少残余应力;同时可降低硬度,提高塑性和韧性,改善切削加工性能。所以退火既为了消除和改善前道工序遗留的组织缺陷和内应力,又为后续工序作好准备,故退火是属于半成品热处理,又称预先热处理。 2、钢的正火 正火是将钢加热到临界温度以上,使钢全部转变为均匀的奥氏体,然后在空气中自然冷却的热处理方法。它能消除过共析钢的网状渗碳体,对于亚共析钢正火可细化晶格,提高综合力学性能,对要求不高的零件用正火代替退火工艺是比较经济的。 3、钢的淬火 淬火是将钢加热到临界温度以上,保温一段时间,然后很快放入淬火剂中,使其温度骤然降低,以大于临界冷却速度的速度急速冷却,而获得以马氏体为主的不平衡组织的热处理方法。淬火能增加钢的强度和硬度,但要减少其塑性。淬火中常用的淬火剂有:水、油、碱水和盐类溶液等。 4、钢的回火 将已经淬火的钢重新加热到一定温度,再用一定方法冷却称为回火。其目
的是消除淬火产生的内应力,降低硬度和脆性,以取得预期的力学性能。回火分高温回火、中温回火和低温回火三类。回火多与淬火、正火配合使用。 ⑴调质处理:淬火后高温回火的热处理方法称为调质处理。高温回火是指在500-650℃之间进行回火。调质可以使钢的性能,材质得到很大程度的调整,其强度、塑性和韧性都较好,具有良好的综合机械性能。 ⑵时效处理:为了消除精密量具或模具、零件在长期使用中尺寸、形状发生变化,常在低温回火后(低温回火温度150-250℃)精加工前,把工件重新加热到100-150℃,保持5-20小时,这种为稳定精密制件质量的处理,称为时效。对在低温或动载荷条件下的钢材构件进行时效处理,以消除残余应力,稳定钢材组织和尺寸,尤为重要。
模具加工方法与热处理
1.模具加工方法: 平面加工:龙门刨床刨刀 牛头刨床刨刀对模具坯料进行六面加工 龙门铣床断面铣刀 车削加工:车床车刀 数控车床车刀各种模具零件的回转面和平面 立式车床车刀 钻孔加工:钻床钻头、铰刀 横臂钻床钻头、铰刀 铣床: 钻头、铰刀 数控铣床钻头、铰刀加工模具的各种孔 加工中心钻头、铰刀 深孔钻:深孔钻头 镗孔加工:加工中心镗刀 卧室镗床镗刀镗削模具中的各种孔 铣床镗刀 坐标镗床镗刀 铣削加工:铣床立铣刀、断面铣刀 数控铣床立铣刀、球头铣刀铣削各种模具平面和曲面 加工中心立铣刀、球头铣刀 仿形加工球头铣刀 雕刻机小直径立铣刀
磨削加工:平面磨床砂轮 成型磨床砂轮 数控磨床砂轮磨削模具精密孔 光学曲线磨床砂轮 坐标磨床砂轮 内外圆磨床砂轮 万能磨床砂轮 电加工:型腔电加工电极电蚀切削难以加工的 线切割加工线电极部位精密轮廓加工 电解加工电极型腔和平面加工 切削加工:抛光加工抛光机砂轮、锉刀、砂纸、油石和抛光剂。 去除铣削痕迹,对模具零件进行抛光 非切削加工:挤压加工压力机挤压凸模难以切削加工的型腔 铸造加工铍铜压力铸造 精密铸造铸造设备、石膏模型铸造设备 铸造注塑模型腔 电铸加工电铸设备电铸母型精密注塑模型腔 表面装饰纹加工蚀刻装置蚀刻纹样板在注塑模型腔表面
2模具零件的热处理工序 1退火:将钢件加热到临界温度以上‘保温一定时间后随炉温或在土灰、石英砂中缓慢冷却的操作过程。 目的:消除模具的铸、锻件或冷压件的内应力,改善组织,降低硬度,提高塑性,以利于切削加工。 分类:扩散退火、完全退火、球化退火等。 扩散退火目的:适用于合金钢锭,消除合金钢锭中的成分不均匀性,故又称为均匀化退火。完全退火目的:主要用于含碳量在0.77%以下的亚共析钢,降低硬度,细化晶粒,消除冷 热加工应力。 球化退火目的:主要用于含碳量≥0.77%的钢,使碳化铁成球状,降低硬度,改善切削性 能,为淬火做准备。 不完全退火目的:主要用于含碳量高于0.77%的高碳钢,降低硬度,消除内应力。 等温退火目的:改善金相组织,降低硬度,改善切削加工性能。 再结晶退火目的:主要是消除冷加工后的组织变形,消除加工硬化。 2正火:将钢件加热到临界温度以上,保温一定时间后取出,放在空气中自然冷却的操作过程。 目的:消除钢件的残余应力,降低硬度,细化晶粒,改善组织,为最终热处理做准备。 应用:1.消除高碳钢中的网状碳化物; 2.代替低碳钢的完全退火,提高其韧性,改善其切削加工性能; 3.代替某些中碳钢、铸钢及铸铁件的完全退火,缩短加工周期。 4.作为预先热处理和随后热处理,为其他热处理做准备。 3.淬火:将钢件加热到临界温度以上,保温一定时间,随后放入淬火介质(水、油及盐
模具热处理工艺流程【详情】
模具热处理工艺流程 模具热处理是指材料在固态下,通过加热、保温和冷却的手段,以获得预期组织和性能的一种金属热加工工艺。 模具热处理工艺技术对于模具制造来说,最大的用处是进一步提高模具的精度,比如防止加热氧化和不脱碳、真空脱气或除气,消除氢脆,从而提高材料(零件)的塑性、韧性和疲劳强度;真空加热缓慢、零件内外温差较小等因素,决定了真空热处理工艺造成的零件变形小等。 模具热处理工艺的方式有: (1)软化退火:其目的主要在于分解碳化物,将其硬度降低,而提高加工性能,对于球状石磨铸铁而言,其目的在于获得具有甚高的肥力铁组织。 (2)正常化处理:主要用于改进或是使完全是波来铁组织的铸品而获得均匀分布的机械性质。 (3)淬火:主要为了获得更高的硬度或磨耗强度,同时的到甚高的表面耐磨特性。 (4)表面硬化处理:主要为获得表面硬化层,同时得到甚高的表面耐磨特性。 (5)析出硬化处理:主要是为获得高强度而伸长率并不因而发生激烈的改变。 模具材料及热处理硬度: ⑴拉延模:板料厚度t≤1.2mm,凸、凹模及压边圈采用Mo-Cr合金铸铁(GM246或 GM241),表面火焰处理,其硬度不低于HRC50。板料厚度1.2mm
热处理硬度为HRC58-62。 切边模:板料厚度t≤1.2mm,切边刀块刃口采用铸造或锻造的空冷钢7CrSiMnMoV(ICD5),刃口火焰处理硬度为HRC50-55;板料厚度1.2mm