轧机主传动系统扭振分析
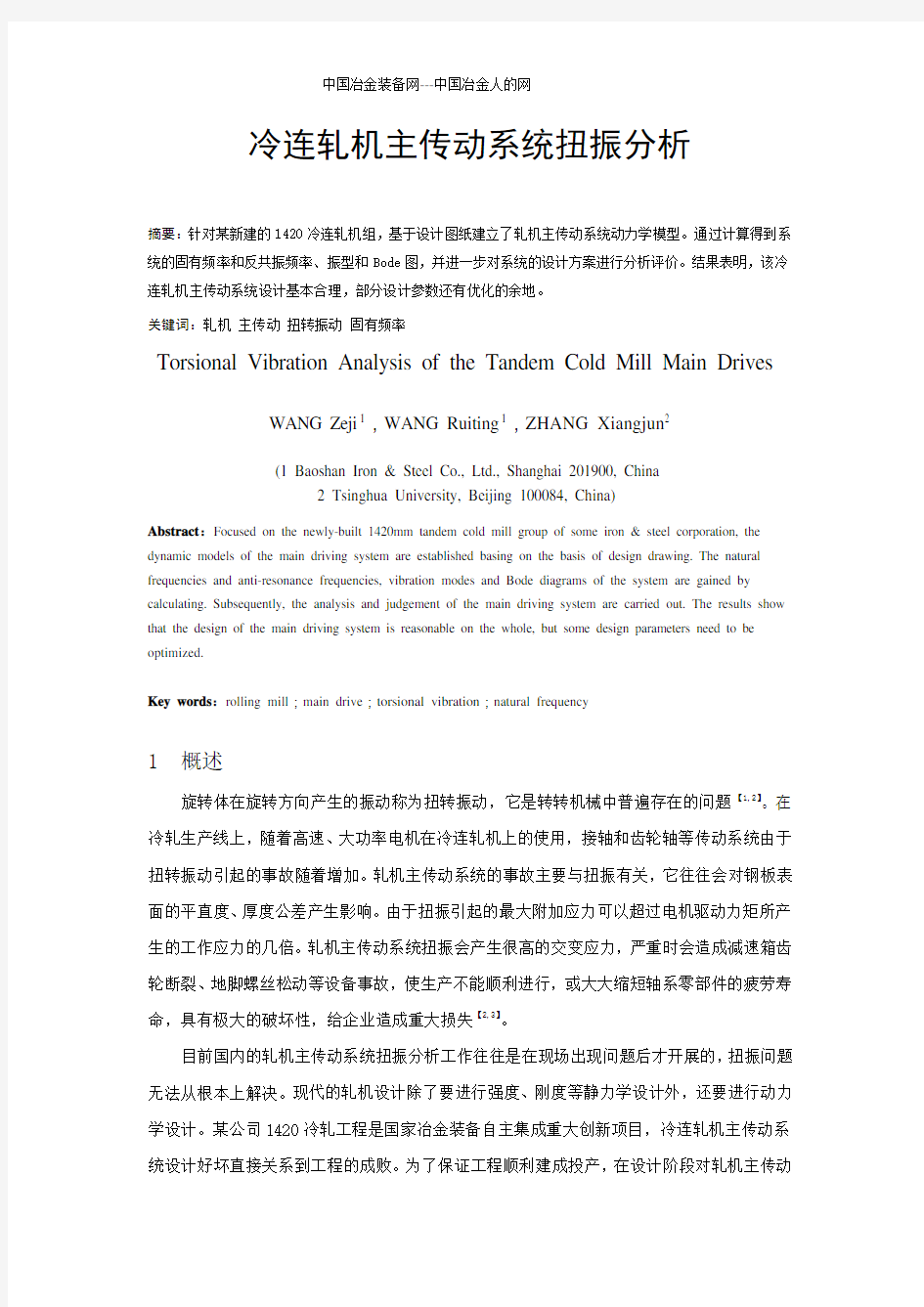

冷连轧机主传动系统扭振分析
摘要:针对某新建的1420冷连轧机组,基于设计图纸建立了轧机主传动系统动力学模型。通过计算得到系统的固有频率和反共振频率、振型和Bode图,并进一步对系统的设计方案进行分析评价。结果表明,该冷连轧机主传动系统设计基本合理,部分设计参数还有优化的余地。
关键词:轧机主传动扭转振动固有频率
Torsional Vibration Analysis of the Tandem Cold Mill Main Drives WANG Zeji1,WANG Ruiting1,ZHANG Xiangjun2
(1 Baoshan Iron & Steel Co., Ltd., Shanghai 201900, China
2 Tsinghua University, Beijing 100084, China)
Abstract:Focused on the newly-built 1420mm tandem cold mill group of some iron & steel corporation, the dynamic models of the main driving system are established basing on the basis of design drawing. The natural frequencies and anti-resonance frequencies, vibration modes and Bode diagrams of the system are gained by calculating. Subsequently, the analysis and judgement of the main driving system are carried out. The results show that the design of the main driving system is reasonable on the whole, but some design parameters need to be optimized.
Key words:rolling mill;main drive;torsional vibration;natural frequency
1 概述
旋转体在旋转方向产生的振动称为扭转振动,它是转转机械中普遍存在的问题【1,2】。在
冷轧生产线上,随着高速、大功率电机在冷连轧机上的使用,接轴和齿轮轴等传动系统由于
扭转振动引起的事故随着增加。轧机主传动系统的事故主要与扭振有关,它往往会对钢板表
面的平直度、厚度公差产生影响。由于扭振引起的最大附加应力可以超过电机驱动力矩所产
生的工作应力的几倍。轧机主传动系统扭振会产生很高的交变应力,严重时会造成减速箱齿
轮断裂、地脚螺丝松动等设备事故,使生产不能顺利进行,或大大缩短轴系零部件的疲劳寿
命,具有极大的破坏性,给企业造成重大损失【2,3】。
目前国内的轧机主传动系统扭振分析工作往往是在现场出现问题后才开展的,扭振问题
无法从根本上解决。现代的轧机设计除了要进行强度、刚度等静力学设计外,还要进行动力
学设计。某公司1420冷轧工程是国家冶金装备自主集成重大创新项目,冷连轧机主传动系
统设计好坏直接关系到工程的成败。为了保证工程顺利建成投产,在设计阶段对轧机主传动
系统进行扭振分析显得尤为重要。
2 系统建模
实际的冷轧机主传动系统是比较复杂的,为了对分析方便,需要对实际结构进行简化。通常是把质量部分按重心不变的原则集中为若干个具有等效转动惯量的圆盘,圆盘之间由具有等效扭转刚度的弹性轴段连接。这就构成一个多自由度的扭振系统。在此力学模型的基础上建立数学模型,然后对数学模型进行动力学求解,进而分析系统的固有特性和动态响应。 2.1 力学模型的建立
某公司1420冷连轧机前三机架主传动系统结构如图1所示。
据此,简化为只有转动惯量的结点,结点之间通过无转动惯量的扭簧连接(具有刚度和阻尼),为一个10自由度的力学模型,如图2所示。
图2中:
Ji (i=1,2,……,10)—各结点的等效转动惯量;
Kij (i=1,2,……,9;j=2,3,……,10)—相邻结点间等效扭转弹簧的刚度;
图2 轧机主传动系统简化模型
J 2 J 3 J 8
J 9 J 10
J 7
K 12 J 1 J 4 J 5
J 6
K 23 C 12
C 34
C 23 K 34 C 45 K 45
C 56 K 56 C 67 K 67 C 58 K 58 C 89
K 89
C 910 K 910 主传动电机 主联轴节 主减速机
十字万向轴
上辊系
下辊系
图1 轧机主传动系统结构简图
Cij (i=1,2,……,9;j=2,3,……,10)—相邻结点间等效扭转阻尼,文中等效阻尼值由设计直接给出。 2.2 数学模型的建立
在上述力学模型的基础上,我们建立了相应的10自由度的数学模型:
{}[]{}[]{}[]{}θθθK C J M ++= (1)
式中,[]J 、[]C 、[]K 分别表示转动惯量矩阵、阻尼矩阵和刚度矩阵;表达式如下:
[]????????
????????=10210
000000J J J J
[]???
????????????
?
????????
????????--+--+--+--+--+--+--+--=910910
9109108989898958676767675656565645454545343434342323232312121212
0000000000000000000000C C C C C C C C C C C C C C C C C C C C C C C C C C C C C C C C C C
[]???
???
??????????
????????
????????--+--+--+--+--+--+--+--=910910
9109108989898958676767675656565645454545343434342323232312121212
0000000000000000000
000K K K K K K K K K K K K K K K K K K K K K K K K K K K K K K K K K K
{}θ、{}M 为n 阶列矩阵,分别表示各结点的转角和外载荷扭矩,表达式如下:
{}[]
T
102
1θθθθ =;
{}[]
T
M M M M 1021
=
对(1)式两边进行拉普拉斯变换
{}[][][]{}[]{})()()()()(2s s Z s K C s J s s M θθ=++= (2)
其中[()]Z s 就是系统的阻抗矩阵,只要确定了系统转动惯量矩阵、刚度矩阵和阻尼矩阵,也就等于确定了系统的阻抗矩阵。由于轧钢机系统可以简化为多自由度弹性系统(由三种基本元件组成),因此其阻抗矩阵的建立可以适用于结点阻抗法。
在建立的轧机主传动系统阻抗矩阵的基础上,可以进行相应的固有频率计算、振型分析、动态响应分析等一系列的分析。
2.3 参数计算
建立轧机主传动动力学数学模型以后,关键的问题是如何根据设计图纸得到相应的
][J 、][C 、][K 这三个参数矩阵。][J 、][K 这两个矩阵可以先利用三维设计软件
SolidWorks 对主传动链上各零部件分别进行造型计算得到各自的转动惯量和刚度值,图3为典型部件的三维模型。
(a) 减速箱输入轴齿轮
(b) 减速箱输出轴上轴齿轮轴
(c) 减速箱输出轴下轴齿轮轴
(d) 工作辊
图3 典型部件三维模型
最后,根据力学模型划分折算各结点和弹簧上,得到轧机主传动系统力学模型中各元件的计算参数,如表1所示。
表1 轧机主传动系统扭振计算参数表
J(kg·m2) J_reduce(kg·m2) K(N·m/rad) K_reduce(N·m/rad) 电机(J1)1650.9 1650.9 6.86E+07
1-->2(K12) 6.06E+07
联轴器(J2) 136.3 136.3 2.35E+08
2-->3(K23) 7.27E+07
输入级齿轮(J3) 12.5 12.5 4.37E+07
3-->4(K34) 1.00E+08
传动齿轮(J4) 563.24 58.57696 4.64E+10
4-->5(K45) 7.15E+06
下辊齿轮(J5) 46.6 4.8464 3.44E+07
5-->6(K56) 1.15E+06
5-->8(K58) 1.00E+08
下辊万向节(J6) 21 2.184 6.57E+06
6-->7(K67) 1.37E+06
下工作辊系(J7) 519 53.976
上辊齿轮(J8) 34.28 3.56512 3.93E+07
8-->9(K89) 1.17E+06
上辊万向节(J9) 21 2.184 6.57E+06
9-->10(K910) 1.37E+06
上工作辊(J10) 519 53.976
表中:J表示各部件的转动惯量,J_reduce表示各结点的等效转动惯量;K表示各部件的扭转刚度,K_reduce表示各结点之间的等效扭转刚度。
3 分析结果
3.1 固有率和反共振频率
系统的固有频率指的是没有阻尼的共振频率,因此在分析固有频率时需要忽略阻尼项的影响。一般而言,对于轧机来说最重要的是其中的低阶(1、2、3阶)频率,它们对系统的影响最大,在设计时需要重点关注。
所谓反共振是指弹性系统在某些特定频率的谐和激励作用下,系统某些部位出现谐和反应等于零的情形[4]。反共振频率通常又称吸振频率,是系统第i个结点输入激励,对应的
第j结点的振动为零(实际是振动最小)的激励的频率。当i=j时为原点反共振,当i≠j
时为跨点反共振。如果系统具有原点反共振频率fAi,即意味着当系统在某结点有同频激励信号时,系统发生反共振,该结点振幅为零。本文只分析电机轴的原点反共振频率。
反共振频率中最重要的是最低的一阶反共振频率,它与电机转矩紧密联系。
基于系统运动微分方程(1)和频域方程(2),通过分析计算,分别得到每架轧机主传动系统的各阶固有频率和反共振频率,如表2所示。
表2 冷连轧机主传动系统的扭振固有频率和反共振频率
1#轧机2#轧机3#轧机4#轧机5#轧机
阶数i
fN i(Hz) fA i(Hz) fN i(Hz) fA i(Hz) fN i(Hz) fA i(Hz) fN i(Hz) fA i(Hz) fN i(Hz) fA i(Hz)
1 15.84 15.33 16.0
2 14.82 16.28 13.77 13.89 11.44 13.89 11.44
2 17.04 17.04 16.99 16.99 16.91 16.90 15.59 13.92 15.59 13.92
3 81.57 77.36 72.35 68.28 63.11 59.61 83.2
4 80.2
5 83.24 80.25
4 139.03 138.66 138.13 137.50 138.27 137.63 167.52 166.82 167.52 166.82
5 172.08 172.08 171.49 171.32 170.65 170.64 201.13 201.13 201.13 201.13
6 177.04 176.6
7 171.84 171.62 175.2
8 174.8
9 215.51 215.47 215.51 215.47
7 202.40 202.37 203.58 203.56 205.79 205.71 307.18 307.17 307.18 307.17
8 617.80 617.80 429.44 429.43 295.99 295.97 472.32 471.32 472.32 471.32
注:表中fN i和fA i分别表示第i阶固有频率和反共振频率。
3.2 振型分析
图4为F1~F5主传动系统前三阶扭振振型。
由于F4、F5主传动结构及设计参数完全相同,因此扭振固有频率及振型等动力学分析结果也完全相同。 3.3 Bode 图计算
Bode 图反映了系统的频率响应特性,图5给出了冷连轧机主传动系统在电机输入转矩和轧辊负载转矩作用下,电机轴以及工作辊的速度振动响应的Bode 图。
(c) F3前三阶扭振振型
(d) F4、F5前三阶扭振振型
图4 冷连轧机主传动系统扭振振型
(a) F1电机输入单位扭矩
(b) F1
工作辊输入单位扭矩
图5(e )~(f )中每一个Bode 图包括两个部分,上面是幅频特性,下面是相频特性。
4 设计方案评价
4.1 频率分析
【5】
根据轧机动力学设计准则,相邻扭振固有频率的比值需满足以下三个条件(共振频率以fNi 表示,i 表示频率阶数):
(1)1、2、3阶固有频率相差要足够大; (2)fN3/fN2大于2;
(3)fN(i+1)/fNi 大于1.2~1.3(i=3,4,5,……)。
从表2看出,除了第1阶和第2阶固有频率略微靠近外,其余均具有合适的间隔。表2是基于上下工作辊分开的模型计算得到,而实际往往是轧机处于轧制带钢状态,可以认为上
图5 冷连轧机主传动系统Bode 图
(e) F3
电机输入单位扭矩
(f) F3工作辊输入单位扭矩
(g) F4、F5电机输入单位扭矩
(h) F4、F5工作辊输入单位扭矩
下工作辊闭合。重新分析,得到上下工作辊闭合后的固有频率,如表3所示。
表3 轧辊闭合状态轧机主传动系统的扭振固有频率
阶数i
1#轧机固有
频率fN i(Hz)
2#轧机固有
频率fNi(Hz)
3#轧机固有
频率fNi(Hz)
4#轧机固有
频率fNi(Hz)
5#轧机固有
频率fNi(Hz)
1 15.84 16.0
2 16.29 15.62 15.57
2 81.57 72.3
3 63.11 83.2
4 83.24
3 139.03 138.10 138.27 167.52 167.50
4 172.0
5 171.65 169.61 201.13 200.50
5 177.04 171.9 175.27 215.51 215.47
6 202.39 204.1
7 205.7
8 307.18 307.18
7 617.81 429.44 295.99 472.32 472.31
分析比较表2和表3,轧辊分开模型中原来靠得很近的第1、2阶扭振固有频率在闭合模型中变为1阶,而其余阶固有频率基本没有改变;表3中1、2阶固有频率相差较大,二者比值大于3,说明系统的扭矩放大系数(TAF)会比较小。
对于复杂机械系统而言,只有前3阶固有频率和振型起主要作用,所以从固有频率角度分析,主传动系统设计是合理的。
4.2 主传动系统放大系数分析
4.2.1 典型工况的系统TAF分析
轧机主传动系统在突然加载或卸载情况下会产生扭振。由扭振造成的连接轴上的最大扭矩值比正常轧制时的静态扭矩要大得多,严重时会超过连接轴、齿轮等的强度,造成轧机设备的破坏,影响生产的正常进行。因此分析主传动系统扭矩变化十分必要。扭矩放大效应通常用扭矩放大系数TAF来描述。在线性系统中,TAF为最大扭矩和平均扭矩的比值。
下面分析了轧机主传动系统在两种典型工况下的TAF值:轧辊端载荷为阶跃函数和斜坡
函数(斜坡上升时间为:t=0.08s )。图6表示F1轧机主传动系统TAF 分布规律,其中横坐标为轴号,纵坐标为TAF 值。
图6中轴号i (i=1,2,……,9)代表图2力学简化模型中相邻两个结点Ji 和Jj (j >i )之间的连接轴。从图可以看出,在载荷为阶跃函数时各轴段的TAF 值均没有超过2.0,说明系统的设计偏安全。载荷为斜坡函数时的TAF 值明显比阶跃函数小,说明系统对轧辊端斜坡函数的响应,明显比对阶跃函数的响应弱,引起系统TAF 增大的因素主要来源于加工过程中的各种冲击载荷。
对于F2~F5主传动系统分别进行相应分析,均与F1有相同的结论。 4.2.2 关键设计参数对TAF 的影响
轧机主传动系统设计参数直接影响系统的TAF 值,尤其是电机和轧辊的设计参数。由于轧辊端输入阶跃载荷时系统的TAF 值较大,因此下面分析阶跃载荷下电机和轧辊设计参数对TAF 的影响。由于篇幅限制,还是以F1为例进行分析说明。 (1)电机设计参数对TAF 的影响
图6 F1轧机主传动系统在两种典型工况下的TAF 分布
图7为电机参数对系统TAF的影响曲线,图中各个轴段以不同的颜色曲线表示其TAF
随电机设计参数变化的规律。从图中可以得出以下基本结论:
第一,增大电机转动惯量对不能降低系统的TAF值;大幅减低电机转动惯量的值可以有效降低系统的TAF值,但是工程意义有待进一步研究。
第二,当电机输出轴刚度扩大为原有设计的1倍以上时,系统各轴段的TAF趋于稳定,与该刚度无关,即单纯增加刚度已经没有效果;减小该刚度值,将有效减小轴段4以后各轴段的TAF值,但电机输出轴本身TAF增加。
因此,现有电机的设计参数较为合理。
(2)轧辊设计参数对TAF的影响
图8 轧辊参数对TAF的影响
图8为轧辊参数对系统TAF的影响曲线,图中各个轴段以不同的颜色曲线表示其TAF
随轧辊设计参数变化的规律。从图中可以得出以下基本结论:
第一,目前的轧辊转动惯量可以适度的降低,以寻求系统的TAF极小值。但是由于模拟计算存在误差,以及复杂的工况条件,原设计较为合理。
第二,小幅降低轧目前的辊端刚度设计值,即横坐标为小于1.0的点,各轴段的TAF
值均出现极小值,说明当前参数的设计可以小幅降低;轧辊刚度再降低或者提高到6倍以上,
也会出现TAF的优选点,但工程意义需要分析确认。
4 结论
在设计阶段对轧机主传动机械系统进行扭振计算和分析评价,可以及时地发现设计中存在的问题,为进一步优化设计提供相应的对策措施,真正做到未雨绸缪。
该冷连轧机工程项目建成投产以后,没有出现因轧机主传动系统扭振而导致的设备和质量事故,表明设计阶段的扭振分析是十分必要和有效的。
参考文献
【1】沈标正,陈践等. 轧机扭振控制策略与实施(上). 冶金自动化,2002(3):17~20
【2】清华大学工程力学系固体力学教研组振动组.机械振动(上).北京:机械工业出版社,1980.120~123 【3】邹家祥,徐乐江等. 冷连轧机系统振动控制. 北京:冶金工业出版社,1998.1~22
【4】方同. 多自由度系统中的反共振. 力学学报,1979(4):360~366
【5】邹家祥等. 轧钢机现代理论设计. 北京:冶金工业出版社,1991.354~356
文章来源:中国冶金装备网 https://www.360docs.net/doc/916728049.html,
工程车辆传动系统扭转振动特性研究与分析
1工程车辆扭转振动动力学模型的建立 工程车辆传动系统一端通过离合器与发动机相连,输出端通过轮胎与工程车辆平动质量相连,组成了一个多质量的弹性扭转振动系统。在计算整个系统的固有频率和振型时,通常可忽略系统的阻尼,将整个传动系统看成是由多个刚性圆盘通过弹性轴连接的无阻尼振动系统。现在某型装备四缸柴油机的中型装载机传动系统为例,其扭转振动力学模型如图1-1所示。 1.1 当量转动惯量的计算 当量转动惯量J 是指将传动系统中与发动机曲轴不同转速旋转的零部件的转动惯量换算成与曲轴同转速旋转下的转动惯量,这种换算方法的原理是能量守恒。设传动轴的转动惯量为J,实际转速为ω曲轴转速为0ω,则将传动轴换算成曲轴转速0ω的当量转动惯量为 2 2 2 0212121??? ? ??=???? ??==g d d i J J J J J ω ωωω 式中,g i 为变速器的传动比。 1.2当量扭转刚度的计算 设两圆盘之间弹性轴的当量扭转刚度为d K ,则可以根据弹性变形量守恒的原理将系统中的时间扭转刚度K 换算过来。现以后桥半轴为例,相应的当量扭转刚度为 2 01??? ? ??=i i K K g d
式中,0i 为主减速器的传动比。 2传动系统扭转动力学方程 根据图1-1所示的简化的传动系统模型,可建立系统动力学方程组为 -0-)-)()(-----111010111111101010991010343332233232221122121111=+=+-=-+-=+=+)()(()()() (。。。。。。。。 。。 θθθθθθθθθθθθθθθθθθθθθK J K K J T K K J T K K J T K J (1) 方程组(1)中,111-θθ分别为对应质量的扭转角位移;41-T T 分别为发动机1-4缸的有效输出转矩。 为了简单起见,可以将(1)改为矩阵形式的动力学方程一般式,即 T K C J =++θθθ。 。。 式中,当量转动惯量矩阵??????? ? ????? ?? ?=111021 00J J J J J 阻尼矩阵C=[0];刚度矩阵; 圆盘的角位移矩阵[]T 114321 0θθθθθθ =。 一般以发动机振动激励为系统输入矩阵,则 []T T T T T T 004 321 = 2.1扭转系统固有特性的分析 这里的固有特性是指固有频率和主振型,多自由度系统的固有频率和主振型可以根据系统的无阻尼自由振动方程得到,即 0=+θθK J 。。 (2) 假设方程的解为 t n i e ωθA = (3) 式中,A 为系统自由振动时的振幅列向量,[]T m m m m A A A A A 1132 1 =。
数值计算方法实验分析报告
学生实验报告 实验课程名称数值计算方法 开课实验室数学实验室 实验五解线性方程组的直接方法 实验(主元的选取与算法的稳定性) 问题提出:消去法是我们在线性代数中已经熟悉的。但由于计算机的数值运算是在一个有限的浮点数集合上进行的,如何才能确保消去法作为数值算法的稳定性呢?消去法从理论算法到数值算法,其关键是主元的选择。主元的选择从数学理论上看起来平凡,它却是数值分析中十分典型的问题。 实验内容:考虑线性方程组 n n R n ∈ =?, Ax∈ , R b A b
编制一个能自动选取主元,又能手动选取主元的求解线性方程组的消去过程。 实验要求: ()取矩阵 ?? ????? ?????????=????????????? ?? ?=1415157,68 16 8 1 681 6M O O O b A ,则方程有解 T x )1,,1,1(*Λ=。取计算矩阵的条件数。让程序自动选取主元, 结果如何? ()现选择程序中手动选取主元的功能。每步消去过程总选取按模最小或按模尽可能小的元素作为主元,观察并记录计算结果。若每步消去过程总选取按模最大的元素作为主元,结果又如何?分析实验的结果。 ()取矩阵阶数或者更大,重复上述实验过程,观察记录并分析不同的问题及消去过程中选择不同的主元时计算结果的差异,说明主元素的选取在消去过程中的作用。 ()选取其他你感兴趣的问题或者随机生成矩阵,计算其条件数。重复上述实验,观察记录并分析实验结果。 实验(线性代数方程组的性态与条件数的估计) 问题提出:理论上,线性代数方程组b Ax =的摄动满足 ??? ? ???+??-≤ ?-b b A A A A A cond x x 11)( 矩阵的条件数确实是对矩阵病态性的刻画,但在实际应
太阳能热水器计算分析报告书
太阳能热水系统设计计算书
设计计算书 设计依据: 1、《民用建筑太阳能热水系统技术手册草案》 2、《民用建筑太阳能热水系统应用技术规范》(GB 50364-2005) 3、《建筑给水排水设计规范》(GB50015-2003) 2009版本 4、《太阳能热利用原理与计算机模拟》(西北工业大学出版社 张鹤飞主编) 5、《太阳能供热采暖应用技术手册》(化学工业出版社 何梓年 朱敦智主编) 系统方案:条件冷水供水水质硬度小于等于150mg /L(以计)。用户对冷热水压差稳定要求不严。因此太阳能热水系统采用单水箱强制循环直接加热电辅助加热系. 按照建筑给水排水设计规范 (GB 50015-2003)(2009年版) T t t C mq K Q r l r r h h ρ)-(==144291.6 (KJ/h)=40.1KW 式中: Q h -- 设计小时耗热量(KJ/h ); m -- 用水计算单位数;(62人) q r -- 热水用水定额80(L/人·d ); C -- 水的比热 ,C=4.187(KJ/kg ·℃); t r -- 热水温度,t r =60℃ t l -- 冷水温度,t l =7℃; ρr -- 热水密度(kg/L ),ρr =0.9832; T -- 每日使用时间(h );24 K h -- 小时变化系数;3.2 r l r h rh C t t Q q ρ)(-= ≈605 (L/h) 式中: q rh -- 设计小时热水量(L/h ); Q h -- 设计小时耗热量(KJ/h );144291.6 t l -- 设计热水温度,t l =65℃; t r -- 设计冷水温度,t r =7℃; 总计如下 设计小时热水量:605.00 (L/h) 设计小时耗热量:144291.6 (KJ/h) 直接系统集热器总面积可根据用户的每日用水量和用水温度确定,按下式计算:
传动系统振动
汽车动力传动系振动分析 [ 摘要]综述了车辆动力传动系振动的研究进展从振动的角度看,车辆动力传动系可分为 弯曲振动系统和扭转振动系统目前主要采用试验模态分析和有限元等研究方法对动力传动系弯曲振动特性进行研究,建立了较为理想的弯曲振动分析模型在动力传动系扭转振动的 研究方面,许多学者对此进行了有益探索研究,并取得了一定的进展但限于分析条件,车辆 动力传动系弯曲、扭转振动耦合的研究尚不十分完善,尤其在国内,这一研究尚处于起步阶段因此,在动力传动系弯曲、扭转振动的研究已相对成熟的基础上,动力传动系的弯曲、扭 转振动耦合对其振动特性影响的研究将是今后一段时间的主要研究内容车辆是一个复杂的振动系统,它是由多个具有固有振动特性的子系统组成,作为子系统之一 的动力传动系,即包括动力总成、传动轴、驱动桥总成组成的系统是车辆振动和噪声的重要激励源从振动的角度看,车辆动力传动系可分为两个振动系统:弯曲振动系统和扭转振动系 统车辆动力传动系的弯曲振动系统和扭转振动系统不仅有各自的固有振动特性,而且还存 在一定程度的振动耦合这些不同形式的振动及其耦合,是影响车辆行驶平顺性,乘坐舒适性及动力传动系零部件使用寿命的主要原因之一,因此对车辆动力传动系的整体振动进行深入细致的研究,显得十分必要 1 动力传动系弯曲振动研究车辆动力传动系弯曲振动在很大的频率段内对车辆振动和噪声有着重要影响,动力传动系低频段内的刚体振动直接影响车辆的乘坐舒适性, 而较高频段内的弹性振动将会引起车辆 的结构共振和声学共振近年来,随着对提高乘坐舒适性、减小汽车振动要求的提高,对动力传动系弯曲振动特性的进一步研究,已显得十分迫切,国内外对动力传动系弯曲振动的研究 起步较早,在理论研究方面取得一定进展,试验研究也较为成熟建立由离散的集中质量、弹 簧、阻尼器组成的力学模型是对动力传动系弯曲振动特性进行研究分析的一种行之有效的方法後藤进[1 ]建立了具有1 1个自由度的动力传动系的弯曲振动力学模型,并通过试验验证 试验结果和计算结果取得较好一致文献[2 ]也建立了动力传动系弯曲振动多自由度力学模型,指出系统的弯曲振动是由发动机运动部件往复惯性力、传动轴的不平衡等引起的, 并通 过实验测定有关参数值,计算系统的固有频率、振型隋军[3、4]建立包括动力总成及传动轴的 5 个自由度的弯曲振动力学模型,计算系统的固有振动特性和响应, 指出动力总成的弯 曲振动是汽车飞轮壳损坏的主要原因这种建模方法及其实用性已为大量的计算和试验分析结果所证实,并且已总结出了确定模型集中质量、弹性和阻尼的一般原则,能有效地用于分析解决车辆动力传动系弯曲振动问题日臻完善的试验模态分析技术,在动力传动系弯曲振动特性的研究中得到广泛应用试验模态分析在动力传动系弯曲振动特性研究中的应用, 经历了从单个总成发展到多个总成直至整个动力传动系的过程隋军[4] 、张建文[5]对动力传动 系动力总成进行了试验模态分析,认为动力总成的弯曲振动是造成汽车离合器壳开裂的主 要原因余龄[6] 利用试验模态分析技术测定了包括动力总成及传动轴的组合系统的一阶弯曲振动频率,张金换[7]则通过模态试验分析研究动力传动系传动轴的临界转速孙方宁[8, 9] 、俄延华[1 0 ] 在整车条件下,对动力传动系弯曲振动进行模态试验,得到整个动力传动系弯曲 振动的模态参数高云凯[1 1 ] 在台架及整车条件下,对汽车动力总成弯曲振动试验模态分析中的非线性特性进行研究,结果表明这一非线性特性仅存在于整车条件下的试验模态分析 试验模态分析具有快速、简便地识别结构固有特性的特点,但其精度主要取决于试验者的经 验和所使用的测试仪器、分析程序模态综合法是对动力传动系弯曲振动进行分析的有效方法,其基本思想是将动力传动系分为若干个子系统,在完成对各子系统的模态分析后, 建立 自由模态的综合方程,再利用平衡条件和约束条件将自由度简化,最后获得一个自由度大为
CATIA有限元分析报告地报告材料计算实例完整版
CATIA有限元分析计算实例 CATIA有限元分析计算实例 11.1例题1 受扭矩作用的圆筒 11.1-1划分四面体网格的计算 (1)进入【零部件设计】工作台 启动CATIA软件。单击【开始】→【机械设计】→【零部件设计】选项,如图11-1所示,进入【零部件设计】工作台。 图11-1单击【开始】→【机械设计】→【零部件设计】选项 单击后弹出【新建零部件】对话框,如图11-2所示。在对话框输入新的零件名称,在本例题中,使用默认的零件名称【Part1】。点击对话框的【确定】按钮,关闭对话框,进入【零部件设计】工作台。 (2)进入【草图绘制器】工作台 在左边的模型树中单击选中【xy平面】, 如图11-3所示。单击【草图编辑器】工具栏的【草图】按钮,如图11-4所示。这时进入【草图绘制器】工作台。
图11-2【新建零部件】对话框 图11-3单击选中【xy平面】 (3)绘制两个同心圆草图 点击【轮廓】工具栏的【圆】按钮,如图11-5所示。在原点点击一点,作为圆草图的圆心位置,然后移动鼠标,绘制一个圆。用同样分方法再绘制一个同心圆,如图11-6所示。 图11-4【草图编辑器】工具栏 图11-5【轮廓】工具栏 下面标注圆的尺寸。点击【约束】工具栏的【约束】按钮,如图11-7所示。点击选择圆,就标注出圆的直径尺寸。用同样分方法标注另外一个圆的直径,如图11-8所示。
图11-6两个同心圆草图 图11-7【约束】工具栏 双击一个尺寸线,弹出【约束定义】对话框,如图11-9所示。在【直径】数值栏输入100mm,点击对话框的【确定】按钮,关闭对话框,同时圆的直径尺寸被修改为100mm。用同样的方法修改第二个圆的直径尺寸为50mm。修改尺寸后的圆如图11-10所示。 图11-8标注直径尺寸的圆草图 图11-9【约束定义】对话框 (4)离开【草图绘制器】工作台 点击【工作台】工具栏的【退出工作台】按钮,如图11-11所示。退出【草图绘制器】工作台,进入【零部件设计】工作台。
含有故障的齿轮系统扭转振动分析
第22卷 第4期2007年12月 北京机械工业学院学报 Journa l of Be ijing Institute o fM ach i nery V o.l22N o.4 D ec.2007 文章编号:1008-1658(2007)04-0013-05 含有故障的齿轮系统扭转振动分析 朱艳芬1,陈恩利1,申永军1,王翠艳2 (1.石家庄铁道学院 机械工程分院,石家庄050043;2.石家庄铁道学院 工程训练中心,石家庄050043) 摘 要:建立了故障单自由度齿轮系统扭转振动的数学模型,采用加入脉冲的形式进行故障模拟,并利用数值方法进行对该模型进行仿真,进行定性研究。作出了系统模型的幅频响应曲线,与无故障时的曲线相比较,发现在低速时脉冲对系统的影响较大。另外,还对该模型进行了参数研究,分别比较了在不同阻尼比和不同激振力情况下的脉冲对系统幅频曲线的影响。 关 键 词:单自由度直齿轮系统;扭转振动;数值方法;幅频响应曲线;参数研究 中图分类号:TH113 文献标识码:A Analysis of torsional vibration of a spur gear system w ith faults ZHU Y an-fen1,C H E N Een-li1,SH E N Yong-jun1,WANG Cu-i yan2 (1.Schoo l ofM echan i calEng i neeri ng,Shiji az huang Rail w ay Ins tit u te,Sh iji az huang050043; 2.Eng i neeri ng Tra i n i ng C enter,Sh iji az hu ang Rail w ay I n stitute,Sh ijiazhuang050043) Abstract:The torsional v i b ration m odel o f the spur sing le-DOF gear syste m w it h fau lts is bu il,t and the for m o f the pulses is adop ted to si m u late the faults.Th i s m ode l is ca lculated by usi n g the num erica l m ethod.The response o f the m ode l is ana lyzed,and the Am p litude frequency Curves are p l o tted,and t h e greater fl u ence of the pu lse is found in the lo w frequency.The para m eters of the mode l are researched, and the Am plitude-frequency Curves under vari o us da m pi n g ratio and under vari o us exc iting-v ibration force are co m pared respectively. Key w ords:spur si n gle-DOF gear syste m;torsi o na l v ibration;num erica lm ethod;t h e Am plitude-fre-quency Curves;para m eters study 齿轮作为机械系统中的重要传动装置,在机械、化工、航天等行业的装备中起着非常关键的作用。为了满足航空、航天及机器人等技术发展的需要,采用传统的线性分析和控制理论已难以满足这一要求。由于零部件间的间隙、运动负重的摩擦及时变刚度等因素,实际的齿轮传动系统都是非线性系统,传统的线性分析和控制是对其进行的一种近似处理,只有对齿轮传动系统实施非线性分析和非线性控制才能获得精度高、振动小和噪声低等性能的齿轮传动系统。齿轮的工作状态正常与否对运动和动力的传输具有重要的影响[1]。因此,研究齿轮系统的动力学与故障诊断具有重要的理论价值和工程意义。 关于带故障的齿轮系统动力学建模及动力学分析则见于Parey的文章[2],其中的缺陷主要包括摩擦、磨损、点蚀和剥落等,介绍了带有故障的各种齿轮动力学模型等,另外,Kuang[3]等人建立了考虑齿面磨损的齿轮动力学方程,齿面磨损会影响啮合过程中的齿面轮廓,从而会影响到啮合刚度、阻尼力以及摩擦力等,这样将会使得系统的方程非常复杂。 本文从单自由度齿轮系统入手,经过模型简化,模拟了齿轮系统故障引起的刚度变化后的齿轮模型,并定性地分析了其动力学特性。 1故障单自由度齿轮系统理论模型 首先建立正常直齿轮副扭转振动的数学模型。扭转振动模型是仅考虑系统扭转振动的模型,在齿轮系统的振动分析中,若不考虑传动轴的横向和轴向弹性变形以及支承系统的弹性变形,则可将系统简化成纯扭转的振动系统,在实际工程中许多复杂 收稿日期:2007-09-04 基金项目:国家自然科学基金资助项目(10602038) 作者简介:朱艳芬(1976-),女,河北藁城人,石家庄铁道学院机械工程分院硕士研究生,主要从事机械系统动力学控制等研究。
船舶柴油机的轴系扭转振动的分析与研究
船舶柴油机的轴系扭转振动的分析与研究 【摘要】本文通过一些国内因轴系扭转振动而引起的断轴断桨的事故实例,来分析引起轴系扭转振动的主要原因,分析扭振主要特性,并提取一些减振和防振的基本控制措施。 【关键词】船舶柴油机轴系扭振危害分析措施 在现代船舶机械工程中,船舶柴油机轴系扭转振动已经成为一个很普遍的问题,它是引起船舶动力装置故障的一个很常见的原因,国内外因轴系扭转而引起的断轴断桨的事故也屡见不鲜,随着科学水平的提高和航运业的发展,人们越来越重视船舶柴油机组的轴系扭转振动,我国《长江水系钢质船舶建造规范》和《钢质海船入级与建造规范》(简称《钢规》)和也均规定了在设计和制造船舶过程中,必须要向船级社呈报柴油机组的轴系扭转振动测量和计算报告,以此来表明轴系扭转振动的有关测量特性指标均在“规范”的允许范围内。 1 船舶柴油机轴系扭转振动现象简介 凡具有弹性与惯性的物体,在外力作用下都能产生振动现象。它在机械,建筑,电工,土木等工程中非常普遍的存在着。振动是一种周期性的运动,在许多场合下以谐振的形式出现的,船舶振动按其特点和形式可分为三种,船体振动,机械设备及仪器仪表振动,和轴系振动。船舶柴油机轴系振动按其形式可分为三种:扭转振动,纵向振动,横向振动。柴油机扭转振动主要是由气缸内燃气压力周期性变化引起的,它的主要表现是轴系上各质点围绕轴系的旋转方向来回不停的扭摆,各轴段产生不相同的扭角。纵向振动主要是由螺旋桨周期性的推力所引起的。横向振动主要是由转抽的不平衡,如螺旋桨的悬重以及伴流不均匀产生的推力不均匀等的力的合成。 船舶由于振动引起的危害不但可以产生噪音,严重影响旅客和船员休息,还会造成仪器和仪表的损害,严重的时候甚至出现船体裂缝断轴断桨等海损事故,直接影响船舶的航行安全。而在船舶柴油机轴系的三种振动中,产生危害最大的便是扭转振动,因扭转振动而引起的海损事故也最多,因此对扭转振动的研究也最多。而且当柴油机轴系出现扭转振动时,一般情况下,船上不一定有振动的不适感,因此这种振动也是最容易被忽视的一种振动形式,一旦出现扭转振动被忽视,往往意味着会发生重大的事故。更应该注意的是,当发动机运转在主临界速度时,自由端的传动齿轮箱往往容易发生齿击或噪声大的现象,这时检查时会发现齿轮有点蚀或剥落等磨损现象,严重时会有断齿事故。有时在强共振的情况下,轴系中的某些位置只要数分钟运行就能自行发热,稍有疏忽,就可能造成断轴断桨的海损事故。 2 船舶柴油机因扭振而引起的断轴断桨的事故及分析 (1)广西海运局北海分局所属沿海货轮400吨桂海461、462、463,三条
财务指标计算与分析报告
财务指标计算及分析 A、偿债能力分析: 一、资产负债率 资产负债率(debt to assets ratio)是期末负债总额除以资产总额的百分比,也就是负债总额与资产总额的比例关系。资产负债率反映在总资产中有多大比例是通过借债来筹资的,也可以衡量企业在清算时保护债权人利益的程度。资产负债率这个指标反映债权人所提供的资本占全部资本的比例,也被称为举债经营比率。 资产负债率=总负债/总资产。 表示公司总资产中有多少是通过负债筹集的,该指标是评价公司负债水平的综合指标。同时也是一项衡量公司利用债权人资金进行经营活动能力的指标,也反映债权人发放贷款的安全程度。 如果资产负债比率达到100%或超过100%说明公司已经没有净资产或资不抵债! 1、使用者 债权人:从债权人的立场看,他们最关心的是各种融资方式安全程度以及是否能按期收回本金和利息等。如果股东提供的资本与企业资产总额相比,只占较小的比例,则企业的风险主要由债权人负担,这对债权人来讲是不利的。因此,债权人希望资产负债率越低越好,企业偿债有保证,融给企业的资金不会有太大的风险。 投资者:从投资者的立场看,投资者所关心的是全部资本利润率是否超过借入资本的利率,即借入资金的利息率。假使全部资本利润率超过利息率,投资人所得到的利润就会加大,如果相反,运用全部资本利润率低于借入资金利息率,投资人所得到的利润就会减少,则对投资人不利。因为借入资本的多余的利息要用投资人所得的利润份额来弥补,因此在全部资本利润率高于借入资本利息的前
提下,投资人希望资产负债率越高越好,否则反之。 经营者:从经营者的立场看,如果举债数额很大,超出债权人的心理承受程度,企业就融不到资金。借入资金越大(当然不是盲目的借款),越是显得企业活力充沛。因此,经营者希望资产负债率稍高些,通过举债经营,扩大生产规模,开拓市场,增强企业活力,获取较高的利润。 2、影响因素 (1)利润及净现金流量的分析 企业资产负债率的增长,首先要看企业当年实现的利润是否较上年同期有所增长,利润的增长幅度是否大于资产负债率的增长幅度。如果大于,则是给企业带来的是正面效益,这种正面效益使企业所有者权益变大,随着所有者权益的变大,资产负债率就会相应降低。其次要看企业净现金流入情况。当企业大量举债,实现较高利润时,就会有较多的现金流入,这说明企业在一定时间有一定的支付能力,能够偿债,保证债权人的权益,同时说明企业的经营活动是良性循环的。 (2)资产分析 流动资产分析:企业资产负债率的高低与流动资产所占总资产的比重、流动资产的结构以及流动资产的质量有着至关重要的联系。如果流动资产占企业总资产的比重较大,说明企业资金周转速度较快、变现能力强的流动性资金占据了主导位置,即使资产负债率较高也不十分可怕了。流动资产结构主要是指企业的货币资金、应收账款、应收账款、存货等资产占全部流动资产的比重。这些是企业流动资产中流动性最快、支付能力最强的资产。我们知道货币资金是即付资金,应收账款是随时回笼兑现的资金,存货是随着销售的实现而变现的资金,这些资产的多少直接影响着企业付现的能力。如果该比重大,说明企业流动资产结构比较合理,有足够的变现资产作保证。反之,则说明企业流动资产中待处理资产、待摊费用以及相对固化或费用化挂账资产居多,这些资产都是尚待企业自行消化的费用,不仅不能变现偿债,反而会耗用、侵蚀企业利润,这也是一个危险的信号。流动资产的质量,主要看企业应收账款中有无呆坏账,其比重有多大,存货中有无滞销商品、长期积压物资,企业是否计提了坏账准备、销价准备,所提坏账准备、销价准备是否足以弥补呆坏账损失、滞销商品损失和积压物资损失。
汽车传动系统练习答案课案
汽车传动系统练习答案 一、填空题 1.离合器;变速器;万向传动装置;主减速器、差速器;半轴。 2.主动部分;从动部分;压紧机构;操纵机构。 3.自锁钢球;弹簧;特殊齿形;互锁钢球;互锁销;带有弹簧的倒档锁销。 4.两种;先挂前桥、后挂低速档;先摘低速档、后摘前桥。 5.万向节;传动轴;中间支承。 6.15°~20°。 7.主减速器;差速器;半轴;桥壳。 8.绕自身轴线转动;绕半轴轴线转动。 9.锥齿轮组成;锥齿轮;圆柱齿轮。 10.差速器壳;十字轴;行星齿轮;半轴齿轮;半轴。 11.全浮式半轴;半浮式半轴;半轴齿轮;驱动车轮。
12.主减速器;差速器;半轴;轮毂;钢板弹簧;整体式桥壳;分段式桥壳;整体式桥壳。 二、解释术语 1.汽车的车轮数×驱动轮数,第一个数字代表汽车的车轮数,后一个数代表驱动轮数,如EQ2080(原EQ240)E型汽车有6个车轮,而6个车轮都可以驱动,即表示为6×6。 2.发动机发出的转矩经过传动系传给驱动车轮,驱动车轮得到转矩便给地面一个向后的作用力,根据作用力与反作用力的原理,地面给驱动车轮一个向前的反作用力,这个反作用力就是驱动力。 3.传动比既是降速比又是增矩比。=7.31表示汽车变速器一档的传动比,曲轴转7.31转,传动轴转1转;同时还表示,发动机发出的转矩经过变速器挂一档后传到传动轴时的转矩增大了7.31倍。 4.由于在分离轴承与分离杠杆内端之间存在一定量的间隙,驾驶员在踩下离合器踏板后,首先要消除这一间隙,然后才能开始分离离合器,为消除这一间隙所需的离合器踏板的行程,就是离合器踏板自由行程。 5.膜片弹簧是用薄钢板制成并带有锥度的碟形弹簧。靠中心部位开有辐条式径向槽形成弹性杠杆。使其在离合器分离时兼起分离杠杆的作用。
某船舶推进轴系扭振计算分析-不错的论文(精)
第22卷 第5期(总第131期)2011年10月 船舶 SHIP&BOAT Vol.22No.5October,2011 [船舶轮机] 某船舶推进轴系扭振计算分析 金立平 (吉林省地方海事局 [关键词]船舶推进轴系;有限元;转动惯量;扭振[摘 要]提高轴系扭振计算精度,必须有精确的原始参数,以准确掌握船舶轴系扭振情况。在有限元分析软件 中,建立曲柄半拐等的三维模型,用有限元分析方法精确的确定了各质量、轴段的转动惯量、扭转刚度等精确原始参数。基于建立的实船轴系当量系统,计算出了各结自由振动的频率及对应的共振转速,自由端和飞轮输出端的振幅,分析了轴段应力和扭矩随曲轴转角及转速的变化关系。结果表明在整个转速范围内,扭转振幅小于限定值,轴段的最大扭矩和应力均小于材料许用值,本船舶轴系扭转振动状况是良好的。 [中图分类号]U664.21 [文献标志码]A [文章编号]1001-9855(2011)05-0046-04 长春130061)Torsionalvibrationcalculationandanalysisofashippropulsionshaft JINLi-ping (JiLinLocalMaritimeSafetyAdministration,Changchun130061) Keywords:marinepropulsionshafting;FEM;inertiamoment;torsionalvibration Abstract:Thepreciseoriginalparametersarecriticalforimprovingthecalculationaccuracyofshafttorsi onalvibration.Athree-dimensionalmodeofahalfcrankisestablishedinthefiniteelementanalysissoftwaretoaccurate lycalculatetheoriginalparameterssuchasthemomentofinertiaandtorsionalstiffnessofeachs haftsection.Basedontheestablishedrealshipshaftingequivalentsystem,thispapercalculatedt hefreevibrationfrequencyandthecorrespondingresonancespeed,aswellasthevibrationampl itudeofthefreeendandtheflywheeloutputend,analyzedtherelationshipofthestressandtorque ofshaftsandthecrankangleandenginespeed.Theresultsshowthatinthewholespeedrange,thet
结构设计pkpm软件SATWE计算结果分析报告
学习笔记 PMCAD中--进入建筑模型与荷载输入: 板荷:点《楼面恒载》会有对话框出来,选上自动计算现浇楼板自重,然后在恒载和活载项输入数值即可,一般恒载要看楼面的做法,比如有抹灰,找平,瓷砖,吊顶什么的,在民用建筑中可以输2.0,活载就是查荷载规范。梁间荷载:PKPM中梁的自重是自己导入的,所以梁间荷载是指梁上有隔墙或者幕墙或者女儿墙之内在建模时不建的构建,把他们折算成均布荷载就行。比如,一根梁上有隔墙,墙厚200mm,层高3000mm,梁高500mm,如果隔墙自重为11KN/m3,那么恒载为11*(3000-500)*200+墙上抹灰的自重什么的即可。 结构设计pkpm软件SATWE计算结果分析 SATWE软件计算结果分析 一、位移比、层间位移比控制 规范条文: 新高规的4.3.5条规定,楼层竖向构件的最大水平位移和层间位移角,A、B级高度高层建筑均不宜大于该楼层平均值的1.2倍;且A级高度高层建筑不应大于该楼层平均值的1.5倍,B级高度高层建筑、混合结构高层建筑及复杂高层建筑,不应大于该楼层平均值的1.4倍。高规4.6.3条规定,高度不大于150m的高层建筑,其楼层层间最大位移与层间之比(即最大层间位移角)Δu/h应满足以下要求: 结构休系Δu/h限值 框架 1/550 框架-剪力墙,框架-核心筒 1/800 筒中筒,剪力墙 1/1000 框支层 1/1000 名词释义: (1)位移比:即楼层竖向构件的最大水平位移与平均水平位移的比值。 (2)层间位移比:即楼层竖向构件的最大层间位移角与平均层间位移角的比值。 其中: 最大水平位移:墙顶、柱顶节点的最大水平位移。 平均水平位移:墙顶、柱顶节点的最大水平位移与最小水平位移之和除2。 层间位移角:墙、柱层间位移与层高的比值。 最大层间位移角:墙、柱层间位移角的最大值。 平均层间位移角:墙、柱层间位移角的最大值与最小值之和除2。 控制目的: 高层建筑层数多,高度大,为了保证高层建筑结构具有必要的刚度,应对其最大位移和层间位移加以控制,主要目的有以下几点:
SATWE计算结果分析报告
SATWE软件计算结果分析 一、位移比、层间位移比控制 规范条文: 新高规的4.3.5条规定,楼层竖向构件的最大水平位移和层间位移角,A、B级高度高层建筑均不宜大于该楼层平均值的1.2倍;且A级高度高层建筑不应大于该楼层平均值的1.5倍,B级高度高层建筑、混合结构高层建筑及复杂高层建筑,不应大于该楼层平均值的1.4倍。 高规4.6.3条规定,高度不大于150m的高层建筑,其楼层层间最大位移与层间之比(即最大层间位移角)Δu/h应满足以下要求: 结构休系Δu/h限值 框 架 1/55 0 框架-剪力墙,框架-核心筒1/800 筒中筒,剪力墙1/1000 框支层1/1000 名词释义: (1)位移比:即楼层竖向构件的最大水平位移与平均水平位移的比值。 (2)层间位移比:即楼层竖向构件的最大层间位移角与平均层间位移角的比值。其中: 最大水平位移:墙顶、柱顶节点的最大水平位移。 平均水平位移:墙顶、柱顶节点的最大水平位移与最小水平位移之和除2。 层间位移角:墙、柱层间位移与层高的比值。 最大层间位移角:墙、柱层间位移角的最大值。 平均层间位移角:墙、柱层间位移角的最大值与最小值之和除2。 控制目的: 高层建筑层数多,高度大,为了保证高层建筑结构具有必要的刚度,应对其最大位移和层间位移加以控制,主要目的有以下几点: 1.保证主体结构基本处于弹性受力状态,避免混凝土墙柱出现裂缝,控制楼面梁板的裂缝数量,宽度。 2.保证填充墙,隔墙,幕墙等非结构构件的完好,避免产生明显的损坏。 3.控制结构平面规则性,以免形成扭转,对结构产生不利影响。 结构位移输出文件(WDISP.OUT) Max-(X)、Max-(Y)----最大X、Y向位移。(mm) Ave-(X)、Ave-(Y)----X、Y平均位移。(mm) Max-Dx ,Max-Dy : X,Y方向的最大层间位移 Ave-Dx ,Ave-Dy : X,Y方向的平均层间位移 Ratio-(X)、Ratio-(Y)---- X、Y向最大位移与平均位移的比值。 Ratio-Dx,Ratio-Dy : 最大层间位移与平均层间位移的比值 即要求:
传动系统振动
汽车动力传动系振动分析 [摘要 ]综述了车辆动力传动系振动的研究进展从振动的角度看 ,车辆动力传动系可分为弯曲振动系统和扭转振动系统目前主要采用试验模态分析和有限元等研究方法对动力传动系弯曲振动特性进行研究 ,建立了较为理想的弯曲振动分析模型在动力传动系扭转振动的研究方面 ,许多学者对此进行了有益探索研究 ,并取得了一定的进展但限于分析条件 ,车辆动力传动系弯曲、扭转振动耦合的研究尚不十分完善 ,尤其在国内 ,这一研究尚处于起步阶段因此 ,在动力传动系弯曲、扭转振动的研究已相对成熟的基础上 ,动力传动系的弯曲、扭转振动耦合对其振动特性影响的研究将是今后一段时间的主要研究内容 车辆是一个复杂的振动系统,它是由多个具有固有振动特性的子系统组成,作为子系统之一 的动力传动系,即包括动力总成、传动轴、驱动桥总成组成的系统是车辆振动和噪声的重要激励源从振动的角度看,车辆动力传动系可分为两个振动系统:弯曲振动系统和扭转振动系统车辆动力传动系的弯曲振动系统和扭转振动系统不仅有各自的固有振动特性,而且还存在一定程度的振动耦合这些不同形式的振动及其耦合,是影响车辆行驶平顺性,乘坐舒适性及动力传动系零部件使用寿命的主要原因之一,因此对车辆动力传动系的整体振动进行深入细致的研究,显得十分必要 1 动力传动系弯曲振动研究 车辆动力传动系弯曲振动在很大的频率段内对车辆振动和噪声有着重要影响,动力传动系低频段内的刚体振动直接影响车辆的乘坐舒适性,而较高频段内的弹性振动将会引起车辆的结构共振和声学共振近年来,随着对提高乘坐舒适性、减小汽车振动要求的提高,对动力传动系弯曲振动特性的进一步研究,已显得十分迫切,国内外对动力传动系弯曲振动的研究起步较早,在理论研究方面取得一定进展,试验研究也较为成熟建立由离散的集中质量、弹簧、阻尼器组成的力学模型是对动力传动系弯曲振动特性进行研究分析的一种行之有效的方法後藤进[1 ]建立了具有 1 1个自由度的动力传动系的弯曲振动力学模型,并通过试验验证,试验结果和计算结果取得较好一致文献[2 ]也建立了动力传动系弯曲振动多自由度力学模型,指出系统的弯曲振动是由发动机运动部件往复惯性力、传动轴的不平衡等引起的,并通过实验测定有关参数值,计算系统的固有频率、振型隋军[3、4]建立包括动力总成及传动轴的5个自由度的弯曲振动力学模型,计算系统的固有振动特性和响应,指出动力总成的弯曲振动是汽车飞轮壳损坏的主要原因这种建模方法及其实用性已为大量的计算和试验分析结果所证实,并且已总结出了确定模型集中质量、弹性和阻尼的一般原则,能有效地用于分析解决车辆动力传动系弯曲振动问题日臻完善的试验模态分析技术,在动力传动系弯曲振动特性的研究中得到广泛应用试验模态分析在动力传动系弯曲振动特性研究中的应用,经历了从单个总成发展到多个总成直至整个动力传动系的过程隋军[4]、张建文[5]对动力传动系动力总成进行了试验模态分析,认为动力总成的弯曲振动是造成汽车离合器壳开裂的主要原因余龄[6]利用试验模态分析技术测定了包括动力总成及传动轴的组合系统的一阶弯曲振动频率,张金换[7]则通过模态试验分析研究动力传动系传动轴的临界转速孙方宁[8, 9]、俄延华[1 0 ]在整车条件下,对动力传动系弯曲振动进行模态试验,得到整个动力传动系弯曲振动的模态参数高云凯[1 1 ]在台架及整车条件下,对汽车动力总成弯曲振动试验模态分析中的非线性特性进行研究,结果表明这一非线性特性仅存在于整车条件下的试验模态分析试验模态分析具有快速、简便地识别结构固有特性的特点,但其精度主要取决于试验者的经验和所使用的测试仪器、分析程序模态综合法是对动力传动系弯曲振动进行分析的有效方法,其基本思想是将动力传动系分为若干个子系统,在完成对各子系统的模态分析后,建立自由模态的综合方程,再利用平衡条件和约束条件将自由度简化,最后获得一个自由度大为缩减又保持了系统特性的运动方程,即组合系统方程孙方宁[8, 9]将一大型客车动力传动系划分为五个子系统,通过试验模态分析获得各子系统的模态参数,然后利用模态综合方法建立整个系统的理论分析模型,编制计算程序,对该大型客车动力传动系弯曲振动的固有振动特性进行计算,并在激振试验台上进行整个动力传动系弯曲振动的试验模态分析,结果表明理论计算和试验结果具有很好的一致性应用模态综合方法,只需获得动力传动系各子系统的模态参数,就可以通
统计学计算题例题及计算分析报告
计算分析题解答参考 1.1.某厂三个车间一季度生产情况如下: 计算一季度三个车间产量平均计划完成百分比和平均单位产品成本。 解:平均计划完成百分比=实际产量/计划产量=733/(198/0.9+315/1.05+220/1.1) =101.81% 平均单位产量成本 X=∑xf/∑f=(15*198+10*315+8*220)/733 =10.75(元/件) 1.2.某企业产品的有关资料如下: 试分别计算该企业产品98年、99年的平均单位产品成本。 解:该企业98年平均单位产品成本 x=∑xf/∑f=(25*1500+28*1020+32*980)/3500 =27.83(元/件) 该企业99年平均单位产品成本x=∑xf /∑(m/x)=101060/(24500/25+28560/28+48000/32) =28.87(元/件) 年某月甲、乙两市场三种商品价格、销售量和销售额资料如下: 1.3.1999 解:三种商品在甲市场上的平均价格x=∑xf/∑f=(105*700+120*900+137*1100)/2700 =123.04(元/件) 三种商品在乙市场上的平均价格x=∑m/∑(m/x)=317900/(126000/105+96000/120+95900/137) =117.74(元/件) 2.1.某车间有甲、乙两个生产小组,甲组平均每个工人的日产量为22件,标准差为 3.5件;乙组工人日产量资料:
试比较甲、乙两生产小组中的哪个组的日产量更有代表性? 解:∵X 甲=22件 σ甲=3.5件 ∴V 甲=σ甲/ X 甲=3.5/22=15.91% 列表计算乙组的数据资料如下: ∵x 乙=∑xf/∑f=(11*10+14*20+17*30+20*40)/100 =17(件) σ 乙=√[∑(x-x)2 f]/∑f =√900/100 =3(件) ∴V 乙=σ乙/ x 乙=3/17=17.65% 由于V 甲<V 乙,故甲生产小组的日产量更有代表性。 2.2.有甲、乙两个品种的粮食作物,经播种实验后得知甲品种的平均产量为998斤,标准差为162.7斤;乙品种实验的资料如下: 试研究两个品种的平均亩产量,确定哪一个品种具有较大稳定性,更有推广价值? 解:∵x 甲=998斤 σ甲=162.7斤 ∴V 甲=σ甲/ x 甲=162.7/998=16.30% 列表计算乙品种的数据资料如下:
轧机主传动系统扭振分析
冷连轧机主传动系统扭振分析 摘要:针对某新建的1420冷连轧机组,基于设计图纸建立了轧机主传动系统动力学模型。通过计算得到系统的固有频率和反共振频率、振型和Bode图,并进一步对系统的设计方案进行分析评价。结果表明,该冷连轧机主传动系统设计基本合理,部分设计参数还有优化的余地。 关键词:轧机主传动扭转振动固有频率 Torsional Vibration Analysis of the Tandem Cold Mill Main Drives WANG Zeji1,WANG Ruiting1,ZHANG Xiangjun2 (1 Baoshan Iron & Steel Co., Ltd., Shanghai 201900, China 2 Tsinghua University, Beijing 100084, China) Abstract:Focused on the newly-built 1420mm tandem cold mill group of some iron & steel corporation, the dynamic models of the main driving system are established basing on the basis of design drawing. The natural frequencies and anti-resonance frequencies, vibration modes and Bode diagrams of the system are gained by calculating. Subsequently, the analysis and judgement of the main driving system are carried out. The results show that the design of the main driving system is reasonable on the whole, but some design parameters need to be optimized. Key words:rolling mill;main drive;torsional vibration;natural frequency 1 概述 旋转体在旋转方向产生的振动称为扭转振动,它是转转机械中普遍存在的问题【1,2】。在 冷轧生产线上,随着高速、大功率电机在冷连轧机上的使用,接轴和齿轮轴等传动系统由于 扭转振动引起的事故随着增加。轧机主传动系统的事故主要与扭振有关,它往往会对钢板表 面的平直度、厚度公差产生影响。由于扭振引起的最大附加应力可以超过电机驱动力矩所产 生的工作应力的几倍。轧机主传动系统扭振会产生很高的交变应力,严重时会造成减速箱齿 轮断裂、地脚螺丝松动等设备事故,使生产不能顺利进行,或大大缩短轴系零部件的疲劳寿 命,具有极大的破坏性,给企业造成重大损失【2,3】。 目前国内的轧机主传动系统扭振分析工作往往是在现场出现问题后才开展的,扭振问题 无法从根本上解决。现代的轧机设计除了要进行强度、刚度等静力学设计外,还要进行动力 学设计。某公司1420冷轧工程是国家冶金装备自主集成重大创新项目,冷连轧机主传动系 统设计好坏直接关系到工程的成败。为了保证工程顺利建成投产,在设计阶段对轧机主传动 系统进行扭振分析显得尤为重要。 2 系统建模