机械制造基础习题集说课材料

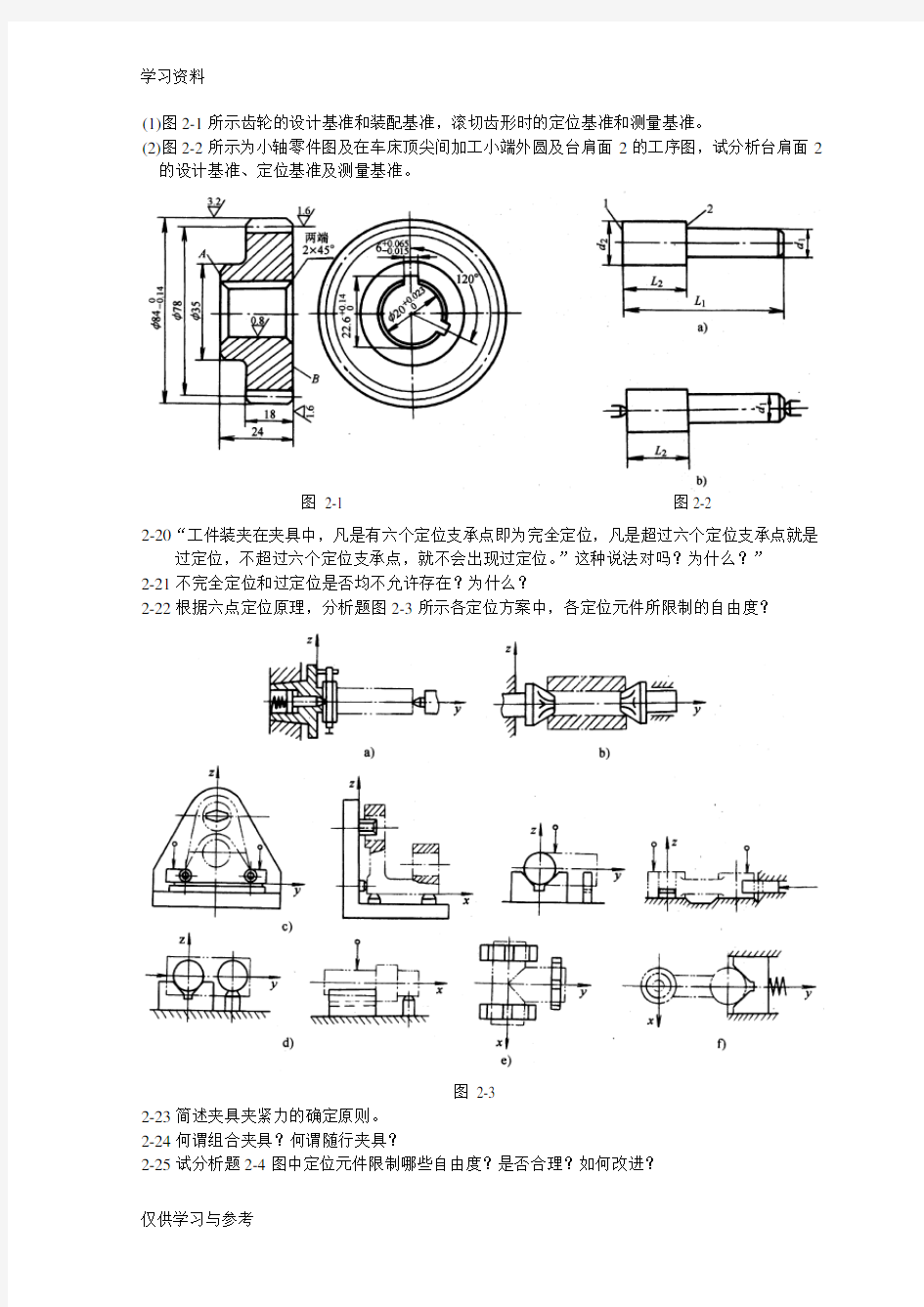
机械制造基础习题集
第一章生产过程与组织
1-1什么是制造和制造技术?
1-2机械制造业在国民经济中有何地位?为什么说机械制造业是国民经济的基础?
1-3如何理解制造系统的物料流、能量流和信息流?
1-4什么是机械制造工艺过程?机械制造工艺过程主要包括哪些内容?
1-5什么是生产纲领,如何确定企业的生产纲领?
1-6什么是生产类型?如何划分生产类型?各生产类型各有什么工艺特点?
1-7企业组织产品的生产有几种模式?各有什么特点?
1-8按照加工过程中质量m的变化,制造工艺方法可分为几种类型?并说明各类方法的应用范围和工艺特点。
1-9一个典型的机械制造企业是有哪几个系统组成?其含义分别是什么?
1-10简述机械制造技术的发展概况。
第二章机械加工方法与装备
2-l何谓加工中心?利用加工中心如何加工曲面?
2-2简述电火花加工、电解加工、激光加工和超声波加工的表面成形原理和应用范围。
2-3指出下列机床型号中各位字母和数字代号的具体含义:
CG6125B CW61100 M1432A Y3150E
2-4简述选用机床的原则。
2-5简述数控机床的组成及各部分的功用。
2-6数控机床加工有什么特点?
2-7从外圆车削来分析,υc、f、a p各起什么作用?它们与切削层厚度a c和切削层宽度a w各有什么关系?
2-8刀具正交平面参考系由哪些平面组成?它们是如何定义的?
2-9车刀的标注角度主要有哪几种?它们是如何定义的?
2-10已知一外圆车刀切削部分的主要几何角度为:γ1=151、α1=a1’=80、κr=750、κr’=150、λs=-50。
试绘出该刀具切削部分的工作图。
2-11刀具的工作角度和标注角度有什么区别?影响刀具工作角度的主要因素有哪些?试举例说明。
2-12刀具有哪些种类?试就每种常用刀具各举一个例子,并说明其加工范围。
2-13何谓顺铣?何谓逆铣?画图说明。
2-14刀具材料应具备哪些性能?书上介绍的四种常用刀具材料各有什么特点?
2-15刀具的前角、后角、主偏角、副偏角、刃倾角各有何作用?如何选用合理的刀具切削角度?2-16砂轮的特性主要由哪些因素所决定?如何选用砂轮?
2-17简述刀具管理系统的任务和内容。
2-18机床夹具由哪几个部分组成?各部分起什么作用?
2-19何谓基准?试分析下列零件的有关基准:
(1)图2-1所示齿轮的设计基准和装配基准,滚切齿形时的定位基准和测量基准。
(2)图2-2所示为小轴零件图及在车床顶尖间加工小端外圆及台肩面2的工序图,试分析台肩面2
的设计基准、定位基准及测量基准。
图2-1 图2-2
2-20“工件装夹在夹具中,凡是有六个定位支承点即为完全定位,凡是超过六个定位支承点就是过定位,不超过六个定位支承点,就不会出现过定位。”这种说法对吗?为什么?”
2-21不完全定位和过定位是否均不允许存在?为什么?
2-22根据六点定位原理,分析题图2-3所示各定位方案中,各定位元件所限制的自由度?
图2-3
2-23简述夹具夹紧力的确定原则。
2-24何谓组合夹具?何谓随行夹具?
2-25试分析题2-4图中定位元件限制哪些自由度?是否合理?如何改进?
2-26如何确定夹紧力的三个要素?
2-27分析三种基本夹紧机构的优缺点。
2-28何谓定心夹紧?定心夹紧机构有什么特点?
第三章 切削过程及控制
3-1金属切削过程有何特征,用什么参数来表示和比较?
3-2切削过程的三个变形区各有何特点?它们之间有什么关联?
3-3分析积屑瘤产生的原因及其对加工的影响,生产中最有效的控制积屑瘤的手段是什么? 3-4切屑与前刀面之间的摩擦与一般刚体之间的滑动摩擦有无区别?若有区别,二者有何不同之
处?
3-5金属切削原理对设计机床、工艺和刀具有何实用意义?
3-6金属切削过程中为什么会产生切削力?
3-7车削时切削合力为什么常分解为三个相互垂直的分力来分析?试说明这三个分力的作用。 3-8背吃刀量和进给量对切削力的影响有何不同?
3-9切削热是如何产生和传出的?仅从切削热产生的多少能否说明切削区温度的高低?
3-10切削温度的含义是什么?它在刀具上是如何分布的?它的分布和三个变形区有何联系? 3-11背吃刀量和进给量对切削力和切削温度的影响是否一样?为什么?如何运用这一规律指导
生产实践?
3-12增大前角可以使切削温度降低的原因是什么?是不是前角越大切削温度越低?
3-13刀具的正常磨损过程可分为几个阶段?各阶段的特点是什么?刀具使用时磨损应限制在哪
一阶段?
3-14刀具磨钝标准是什么意思?它与哪些因素有关?
3-15什么叫刀具寿命?刀具寿命和磨钝标准有什么关系?磨钝标准确定后,刀具寿命是否就确定
了?为什么?
3-16何谓最高生产率刀具寿命和最低成本刀具寿命?粗加工和精加工所选用的刀具寿命是否相
同?为什么?
3-17切削用量对刀具磨损有何影响?在VT m =C 0关系中,指数m 的物理意义是什么?不同刀具m
值为什么不同?
3-18选择切削用量的原则是什么?从刀具寿命出发时,按什么顺序选择切削用量?从机床动力出
发,按什么顺序选择切削用量?为什么?
图 2-4
3-19粗加工时进给量的选择受哪些因素限制?当进给量受到表面粗糙度限制时,有什办法能增加进给量,而保证表面粗糙度要求?
3-20如果选完切削用量后,发现所需的功率超过机床功率时,应如何解决?
3-21提高切削用量可采取哪些措施?
3-22在CA6140车床上粗车、半精车一套筒的外圆,材料为45钢(调质),抗拉强度δb=681.5MPa,硬度为200~230HBS,毛坯尺寸d w×l w=80mm×350mm,车削后的尺寸为d=φ(75-0.25)mm,L=340mm,表面粗糙度值均为及Ra3.2μm。试选择刀具类型、材料、结构、几何参数及切削用量。
3-23钛合金切削加工性较差的原因是什么?
3-24试比较磨削和单刃刀具切削的异同。
3-25在定进给量切人磨削的一个循环中,存在哪些切削特点?
第四章机械制造质量分析与控制
4-1什么叫主轴回转误差?它包括哪些方面?为什么磨床头架主轴采用死顶尖,而车床主轴采用活顶尖?
4-2在卧式镗床上采用工件送进方式加工直径为φ200mm的通孔时,若刀杆与送进方向倾斜α=l031’,则在孔径横截面内将产生什么样的形状误差?其误差大小为多少?
4-3在车床上车一直径为φ80mm、长为2000mm的长轴外圆,工件材料为45钢,切削用量为ν=2m/s,αp=0.4mm、f=0.2mm/r,刀具材料为YTl5,如只考虑刀具磨损引起的加工误差,问该轴车后能否达到IT8的要求?
4-4什么是误差复映?误差复映系数的大小与哪些因素有关?
4-5已知某车床部件刚度为k主=44500N/mm,k刀架=13330N/mm,k尾座=30000N/mm,k刀具很大。
1.如果工件是一个刚度很大的光轴,装夹在两顶尖间加工,试求:
(1)刀具在床头处的工艺系统刚度;
(2)刀具在尾座处的工艺系统刚度;
(3)刀具在工件中点处的工艺系统刚度;
(4)刀具在距床头为2/3工件长度处的工艺系统刚度;
并画出加工后工件的大致形状。
2.如果F y=511N,工艺系统在工件中点处的实际变形为0.05mm,求工件的刚度?
4-6在车床上用前后顶尖装夹,车削长为800mm,外径要求为φ500-0.04mm的工件外圆。已知k主=10000N/mm,k尾=5000N/mm,k刀架=4000N/mm,Fy=300N,试求:
(1)仅由于机床刚度变化,所产生的工件最大直径误差,并按比例画出工件的外形;
(2)仅由于工件受力变形所产生的工件最大直径误差,并按同样比例画出工件的外形;
(3)上述两种情况综合考虑后,工件最大直径误差多大?能否满足预定的加工要求?若不符合
要求,可采取哪些措施解决?
4-7已知车床车削工件外圆时的k系=20000N/mm,毛坯偏心e=2mm,毛坯最小背吃刀量a p2=lmm,C=C y f y HBS=1500N/mm,问:
(1)毛坯最大背吃刀量a pl=?
(2)第一次走刀后,反映在工件上的残余偏心误差Δ工1多大?
(3)第二次走刀后的Δ工2多大?
(4)第三次走刀后的Δ工3多大?
(5)若其它条件不变,让k 系=10000N /mm ,求Δ‘工1、Δ’工2、Δ‘
工3各为多大?并说明k 系对残余偏心的影响规律。
4-8在卧式铣床上按图4-1所示装夹方式用铣刀A 铣削键槽,经测量发现,工件两端处的深度大
于中间的,且都比未铣键槽前的调整深度小。试分析产生这一现象的原因。
4-9在外圆磨床上磨削图4-2所示轴类工件的外圆φ,若机床几何精度良好,试分析所磨外圆出
现纵向腰鼓形的原因?并分析A-A 截面加工后的形状误差,画出A-A 截面形状,提出减小上述误差的措施。
4-10批量生产图4-3所示零件,设A 、B 两尺寸已加工好,今以底面定位镗D 孔,求此工序基准不重合误差。
4-11有一批套筒零件如图4-4所示,其它加工面已加工好,今以内孔D 2在圆柱心轴d 上定位,用
调整法最终铣削键槽。若定位心轴处于水平位置,试分析计算尺寸乙的定位误差。已知:
D 1=φ500-0.06mm ,D 2=φ300+0.021mm ,心轴直径007.0020.030--Φ=d mm 。
图 4-1
图 4-2
图 4-4 图 4-3
4-12在某车床上加工一根长为1632mm的丝杠,要求加工成8级精度,其螺距累积误差的具体要求为:在25mm长度上不大于18μm;在100mm长度上不大于25μm;在300mm长度上不大于35μm;在全长上不大于80μm。在精车螺纹时,若机床丝杠的温度比室温高20C,工件丝杠的温度比室温高70C,从工,件热变形的角度分析,精车盾丝杠能否满足预定的加工要求?
4-13在外圆磨床上磨削某薄壁衬套A,见图4-5a,衬套A在心轴上后,用垫圈、螺母压紧,然后顶在顶尖上磨衬套A的外圆至图样要求。卸下工件后发现工件呈鞍形,如图4-5b所示,试分析其原因。
4-14有一板状框架铸件,壁3薄,壁1和壁2厚,当采用宽度为B的铣刀铣断壁3后(见图4-6),断口尺寸B将会因内应力重新分布产生什么样的变化?为什么?
4-15什么样性质的误差服从偏态分布?什么样性质的误差服从正态分布?请各举一例说明之。4-16在调整好的自动机上加工一批小轴,加工中又调整了一次刀具,试分别画出这批小轴加工后以概率密度为纵坐标和以频数为纵坐标的尺寸误差分布曲线,并简述这两条曲线的异同点。4-17车削一批轴的外圆,其尺寸要求为φ200-0.1mm,若此工序尺寸按正态分布,均方差δ=0.025mm,公差带中心小于分布曲线中心,其偏移量ε=0.03mm。试指出该批工件的常值系统性误差及随机误差多大?并计算合格品率及不合格品率各是多少?
4-18在均方差δ=0.02mm的某自动车床上加工一批φ11mm土0.05mm小轴外圆:问:
(1)这批工件的尺寸分散范围多大?
(2)这台自动车床的工序能力系数多大?
若这批工件数n=100分组间隙Δx=0.02mm,试画出这批工件以频数为纵坐标的理论分布曲线。
4-19在自动车床上加工一批外径为φ11土0.05mm的小轴。现每隔一定时间抽取容量n=5的一个小样本,共抽取20个顺序小样本,逐一测量每个顺序小样本每个小轴的外径尺寸,
并算出顺序小样本的平均值
-
xi和极差Ri,其值列于表4-1。试设计
-
x-R点图,并判断该图4-5
图4-6
工艺过程是否稳定?
表4-1 顺序小样本数据表(单位:mm)
4-20为什么机器零件一般都是从表面层开始破坏?
4-21试述表面粗糙度、表面层物理机械性能对机器使用性能的影响。
4-22为什么在切削加工中一般都会产生冷作硬化现象?
4-23什么是回火烧伤?什么是淬火烧伤?什么是退火烧伤?为什么磨削加工时容易产生烧伤?4-24试述机械加工中工件表面层产生残余应力的原因。
4-25试述机械加工中产生自激振动的条件。并用以解释再生型颤振、耦合型颤振的激振机理。4-26车刀按图4-7a方式安装加工时如有强烈振动发生,此时若将刀具反装(图b)、或采用前后刀架同时车削4-7c、或设法将刀具沿,工件旋转方向转过某一角度装夹在刀架上(图d),加工中的振动就可能会减弱或消失,试分析其原因。
图4-7
第五章工艺规程设计
5-1什么是生产过程、工艺过程和工艺规程?
5-2试简述工艺规程的设计原则、设计内容及设计步骤。
5-3拟订工艺路线须完成哪些工作?
5-4试简述粗、精基准的选择原则,为什么在同一尺寸方向上粗基准通常只允许用一次?
5-5加工图5-1所示零件,其粗基准、精基准应如何选择(标有符号的为加工面,其余为非加工面)?图a、b及c所示零件要求内外圆同轴,端面与孔心线垂直,非加工面与加工面间尽可能保持壁厚均匀;图d所示零件毛坯孔已铸出,要求孔加工余量尽可能均匀。
5-6为什么机械加工过程一般都要划分为几个阶段进行?
5-7试简述按工序集中原则、工序分散原则组织工艺过程的工艺特征,各用于什么场合? 5-8什么是加工余量、工序余量和总余量?
5-9试分析影响工序余量的因素,为什么在计算本工序加工余量时必须考虑本工序装夹误差的影
响?
5-11图5-2所示尺寸链中(图中A 0、B 0、C 0、D 0是封闭环),那些组成环是增环?那些组成环是减
环?
5-11试分析比较用极限法解尺寸链计算公式与用统计法解尺寸链计算公式的异同。
5-12图5-3a 为一轴套零件图,图5-3b 为车削工序简图,图5-3c 为钻孔工序三种不同定位方案的
工序简图,均需保证图a 所规定的位置尺寸11土0.1mm 的要求,试分别计算工序尺寸A1、A2与A3的尺寸及公差。为表达清晰起见,图a 、图b 只标出了与计算工序尺寸A1、A2、A3有关的轴向尺寸。
5-13图5-4为齿轮轴截面图,要求保证轴径尺寸024
.0008.028++Φ mm 和键槽深t=40+0.16mm 。其工艺过
程为:1)车外圆至φ28.50-0.10mm ;2)铣键槽槽深至尺寸H ;3)热处理;4)磨外圆至尺寸 图 5-1 图 5-2
024.0008.028+
-Φmm 。试求工序尺寸H 及其极限偏差。
5-14加工图5-5a 所示零件的轴向尺寸500-0.1mm ,250-0.3mm
及50+0.4mm 其有关工序如图5-5b 、c 所示,试求工序尺寸
A1、A2、A3及其极限偏差。
5-15什么是生产成本、工艺成本?什么是可变费用、不变
费用?在市场经济条件下,如何正确运用经济分析方法合
理选择工艺方案?
5-16什么是成组技术?如何实施?
5-17为图5-6所列零件进行编码?并将其转换为零件特征
矩阵。
5-18试述用样件法进行计算机辅助工艺规程设计的方法步骤。
5-19在认真分析图5-7所示车床尾座装配关系的基础上画车床尾座部件的装配工艺系统图,标准
件编号自定。
5-20什么是完全互换装配法?什么是统计互换装配法?试分析其异同,各适用于什么场合。 图 5-3 图 5-4
图 5-5
图 5-6
5-21设有一轴孔配合,若轴的尺寸为φ800-0.10mm,孔的尺寸为φ800+0.20mm,设轴、孔尺寸均按正态分布,试用完全互换法和统计互换法分别计算封闭环尺寸及极限偏差。
5-22图5-8所示减速器某轴结构的尺寸分别为:A l=41mm,A2=36mm;A3=4mm;要求装配后齿轮端部间隙A。保持在0.10~0.25mm范围内,如选用完全互换法装配,试确定A l、A2、A3的精度等级和极限偏差。
5-23图5-9所示为车床溜板与床身导轨的装配图,为保证溜板在床身导轨上准确移动,压板与床身下导轨面间间隙须保持在0.1~0.3mm范围内,如选用修配法装配,试确定图示修配环A 和其它有关尺寸的尺寸公差和极限偏差。
5-24图5-10所示传动装置,要求轴承端面与端盖之间留有A0=0.3-0.5mm的间隙;已知:A1=420-0.25mm (标准件),A2=1580-0.08mm,A3=400-0.25mm (标准件),A4=230+0.045mm,A5=2500+009mm,A6=3800.05mm,B=50-0.10mm;如采用固定调整法装配,试确定固定调整环B 的分组数和调整环B的尺寸系列。
图 5--7
图5-8 图5-9
图5-10
第六章先进制造技术
6-1 简述先进制造技术的概念与涉及的主要内容。
6-2 简述特种加工的涵义、特点及其常用的方法。
6-3 什么是超精密加工?实现超精密加工的主要技术条件有哪些?6-4 什么是微机械?微机械加工主要方法有哪些?
6-5 简述快速原型技术涵义及其常用的方法。
6-6 简述数控技术的涵义与发展趋势。
6-7 试述工业机器人的结构组成、分类以及在生产中的应用。
6-8 简述FMS的组成与分类。
6-9 什么是CIMS?简述其功能模块与作用。
6-10 简述智能制造的涵义。
6-11 试述精益生产的特征。
6-12 实现并行工程的条件有哪些?
6-12 敏捷制造与CIMS、网络化制造有和不同?
6-12 ERP与MRPⅡ有何不同?
6-12 简述数字化技术的涵义。
6-13 何为反求工程技术?计算机实物反求的过程有哪些?
6-14 计算机仿真和虚拟设计有何不同?
西工大19秋《机械制造基础(含材料)》在线作业
西工大19秋《机械制造基础(含材料)》在线作业 C6132表示________类机床,其中32表示________;M1432表示_________类机床,其中32表示__________。() A:车床,被加工工件最大旋转直径为320mm;车床,最大磨削工件直径为320mm B:车床,被加工工件最大旋转直径为320mm;磨床;最大磨削工件直径为320mm C:车床,最大磨削工件直径为320mm;磨床;被加工工件最大旋转直径为320mm D:磨床;最大磨削工件直径为320mm;车床,被加工工件最大旋转直径为320mm 答案:B 零件的结构工艺性是指零件的____________________________是否符合对质量、生产率高的要求,它是评价零件结构设计优劣的重要指标。( )。 A:形状 B:尺寸 C:形状和尺寸 D:大小 答案:C 铸铁的铸造工艺性比铸钢的要好,其主要原因是( )。 A:铸铁的浇注温度高,凝固温度范围小,收缩率大 B:铸铁的浇注温度低,凝固温度范围小,收缩率小 C:铸铁的浇注温度低,凝固温度范围大,收缩率小 D:铸铁的浇注温度高,凝固温度范围大,收缩率大
答案:B 厚度较大的焊接容器、精度和尺寸稳定性要求高的重要焊接结构焊后应进行的热处理方法是( )。 A:低温回火 B:完全退火 C:去应力退火选项 D:扩散退火选项 答案:C 在设计和制造零件时,应使其工作时的最大正应力与锻件的纤维方向( )。A:呈45°角 B:垂直 C:平行 D:垂直或平行均可 答案:C 目前砂型铸造仍在金属毛坯的制造中占有相当的份额,其主要原因是( )。A:毛坯的成品率高 B:毛坯的机械性能高 C:生产成本低 D:生产的自动化程度高 答案:C 淬硬工件表面的精加工,一般采用()。 A:车削 B:铣削 C:磨削
机械制造基础课程设计
课程设计说明书 系别机电工程系 专业机械设计制造及其自动化 方向机电一体化 课程名称《制造技术基础课程设计》 学号 06080729 姓名张森 指导教师 题目名称 CA6140车床拨叉 设计时间 2011年3-6月 2011 年 5 月日
目录 一、序言 (1) 二、零件的工艺分析及生产类型的确定 (2) 三、选择毛坯,确定毛坯尺寸,设计毛坯图 (4) 四、选择加工方法,制定工艺路线 (8) 五、工序设计 (10) 六、确定切削用量及基本时间 (12) 七、专用机床夹具设计 (15) 八、设计心得 (17) 九、参考文献 (18) 十、附图 (19)
序言 一、序言 机械制造技术基础课程设计在学完了机械制造基础和大部分专业课,并进行了生产实习的基础上进行的又一次实践性教学环节。这次课程程设计是我们能综合运用机械制造技术基础中的基本理论,并结合生产实习中学到的实践知识,独立地分析和解决了机械制造工艺问题,设计了机床专用夹具这一典型的工艺装备,提高了结构设计能力,为今后的毕业设计及未来从事的工作打下了良好基础。 由于能力有限,经验不足,设计中还有血多不足之处,希望各位老师多加指教。
二、零件的工艺分析及生产类型的确定 1.零件的作用 本次设计所给的零件是CA6140车床变速齿轮拨叉,用于双联变换齿轮的啮合,输出不同的转速,已达到变速的目的。该拨叉应用在CA6140车船的变速箱变速机构中机构中。拨 孔与变速叉轴联结,拨叉脚则夹在双叉头以φ22mm孔套在变速叉轴上,并用销钉经8mm 联变换齿轮的槽中。当需要变速时,操纵变速杆,变速操纵机构就通过拨叉头部的操纵槽带动拨叉与变速叉轴一起在变速箱中滑动,拨叉脚拨动双联变换齿轮在花键轴上滑动以改换转速,从而改变车床的主轴转度。 该拨叉在改换转速时要承受弯曲应力和冲击载荷的作用,因此该零件应具有足够的强度、刚度和韧性,以适应拨叉的工作条件。该零件的主要工作表面为拨叉脚两端面、叉轴孔mm(H7)和锁销孔φ8mm,在设计工艺规程时应重点予以保证。 图1-1 拨叉零件图 2.零件的技术要求 CA6140车床拨叉技术要求表1-1
西工大15春《机械制造基础(含材料)》在线作业 答案
15春《机械制造基础(含材料)》在线作业 一、单选题(共10 道试题,共25 分。) 1. 机床主轴要求具有良好的综合力学性能,制造时,应选用的材料及热处理工艺是( )。 A. 20钢,淬火+高温回火 B. 45钢,淬火+高温回火 C. T8钢,淬火+低温回火 D. 45钢,正火 正确答案:B 2. 切削力常分解到三个相互垂直的方向上:__________力与主切削刃上某点的切削速度方向一致;与工件轴线平行的为__________力;与工件半径方向一致的是__________力。() A. 主切削力;走刀抗力;切深抗力 B. 主切削力;切深抗力;走刀抗力 C. 切深抗力;走刀抗力;主切削力 D. 走刀抗力;主切削力;切深抗力 正确答案:A 3. 设计落料模具时,应使( )。 A. 凸模刃口尺寸等于落料件尺寸 B. 凹模刃口尺寸等于落料件尺寸 C. 凸模刃口尺寸等于落料件尺寸加上模具间隙 D. 凹模刃口尺寸等于落料件尺寸加上模具间隙 正确答案:B 4. 零件的结构工艺性是指零件的____________________________是否符合对质量、生产率高的要求,它是评价零件结构设计优劣的重要指标。( )。 A. 形状 B. 尺寸 C. 形状和尺寸 D. 大小 正确答案:C 5. 铸造合金在凝固过程中,液、固相混杂的双相区域的宽窄,即凝固区域的宽度,对合金的流动性有较大的影响。下列不会影响到凝固区域宽度的因素是( )。 A. 铸型的激冷能力 B. 合金的凝固温度范围 C. 合金的导热系数 D. 合金的固态收缩量 正确答案:D 6. 零件的制造一般要经过____________________________________等阶段。()
ca6140车床套机械制造基础课程设计工序卡片【6张】
机械加工工序卡片生产类型大批生产工序号 2 零件名称车床套零件号 零件重量同时加工零件 数 1 材料毛坯 牌号硬度型式重量 45 HB190~ 210 圆钢 设备夹具和辅助工具名称型号 三爪卡盘 车床CA6140 工序工 步 工步说明 刀 具 量 具 走刀 长度 (mm) 走刀 次数 切削 深度 (mm) 进给量 (mm/z) 主轴 转速 (r/ min) 切削 速度 (mm/s ) 基本工 时min 2 1 2 3 夹φ75外圆,粗车一端面,车 外圆φ42.4,长43,外圆φ45.4, 长41,外圆φ70,长5 钻内孔φ23 扩孔φ24.8 掉头装夹,粗车相同参数 切断 45°硬质合金 车刀 Φ23麻花钻 Φ24.8扩孔钻 切断刀 游标卡尺43 45 5 90 90 35 6 4 2 1 1 1 3 3 2 0.6 0.6 0.6 0.20 0.56 500 500 560 200 250 117.8 117.8 122.1 14.45 17.85 1.92 1.60 0.06 2.65 0.714 10.1
卧式铣床X62W 工序工 步 工步说明 刀 具 量 具 走刀 长度 (mm) 走刀 次数 切削 深度 (mm) 进给量 (mm/r) 主轴转 速 (r/mi n) 切削 速度 (m/mi n) 基本工 时min 5 1 铣开挡5H9,保证尺寸2 6 φ63三面 刃铣刀游标 卡尺 9 1 4 0.06 750 148 0.04 机械加工工序卡片生产类型大批生产工序号 6 零件名称车床套零件号
零件重量同时加工零件数 1 材料毛坯 牌号硬度型式重量 45 HB190~ 210 圆钢 设备夹具和辅助工具名称型号 专用钻床夹具摇臂钻床Z35 工序工 步 工步说明 刀 具 量 具 走刀 长度 (mm) 走刀 次数 切削 深度 (mm) 进给量 (mm/r) 主轴转 速 (r/mi n) 切削 速度 (mm/r ) 基本工 时min 6 1 钻孔φ7,钻锥孔φ13 φ7麻花 钻 φ13x90 度锪钻游标 卡尺 4.5 2 1 1 4.5 2 0.20 0.20 530 530 11.65 11.65 0.108 0.047 0.155 机械加工工序卡片生产类型大批生产工序号7 零件名称车床套零件号
工程材料与机械制造基础答案
`第一章金属材料的力学性能 1、在测定强度上σs和σ0.2有什么不同? 答:σs用于测定有明显屈服现象的材料,σ0.2用于测定无明显屈服现象的材料。 2、什么是应力?什么是应变?它们的符号和单位各是什么? 答:试样单位截面上的拉力称为应力,用符号σ表示,单位是MPa。 试样单位长度上的伸长量称为应变,用符号ε表示,应变没有单位。 3、画出低碳钢拉伸曲线图,并指出缩颈现象发生在拉伸图上哪一点?断裂发生在哪一点?若没 有出现缩颈现象,是否表示试样没有发生塑性变形? 答: b点发生缩颈现象,k点发生断裂。 若没有出现缩颈现象,试样并不是没有发生塑 形性变,而是没有产生明显的塑性变形。 4、将钟表发条拉直是弹性变形还是塑性变形?怎样判断它的变形性质? 答:将钟表发条拉直是弹性变形,因为当时钟停止时,钟表发条恢复了原状,故属弹性变形。 5、在机械设计时采用哪两种强度指标?为什么? 答:(1)屈服强度。因为大多数机械零件产生塑性变形时即告失效。 (2)抗拉强度。因为它的数据易准确测定,也容易在手册中查到,用于一般对塑性变形要求不严格的零件。 6、设计刚度好的零件,应根据何种指标选择材料?采用何种材料为宜?材料的E值愈大,其塑 性愈差,这种说法是否正确?为什么? 答:应根据弹性模量选择材料。要求刚度好的零件,应选用弹性模量大的金属材料。 金属材料弹性模量的大小,主要取决于原子间结合力(键力)的强弱,与其内部组织关系不大,而材料的塑性是指其承受永久变形而不被破坏的能力,与其内部组织有密切关系。两者无直接关系。故题中说法不对。 7、常用的硬度测定方法有几种?其应用范围如何?这些方法测出的硬度值能否进行比较?答:工业上常用的硬度测定方法有:布氏硬度法、洛氏硬度法、维氏硬度法。 其应用范围:布氏硬度法应用于硬度值HB小于450的毛坯材料。 洛氏硬度法应用于一般淬火件、调质件。 维氏硬度法应用于薄板、淬硬表层。 采用不同方法测定出的硬度值不能直接比较,但可以通过经验公式换算成同一硬度后,再进行比较。 8、布氏硬度法和洛氏硬度法各有什么优缺点?各适用于何种场合。下列情况应采用哪种硬度法 测定其硬度? 答:布氏硬度法:(1)优点:压痕面积大,硬度值比较稳定,故测试数据重复性好,准确度较洛氏硬度法高。 (2)缺点:测试费时,且压痕较大,不适于成品、小件检验。
机械制造基础习题解答
第一部分金属材料与热处理 (非机类专业用) 1.(1)理化性能:根据材料使用中工作条件不同,对材料的理化性能要求不同。如飞机上的一些零部件,需要密度小的材料,如铝合金制造,在腐蚀介质中工作 的零件要选用耐腐蚀性好的材料制造。 (2)机械性能:根据材料在使用过程中受力情况不同,选用不同机械性能指标的材料。(3)工艺性能:根据材料使用中加工方法不同,选用不同的工艺性能的材料。如机床床身应选用铸造性能好的灰铸铁等。 2.σb—强度极限 σs—屈服极限 8%—延伸率 4%—断面收缩率 a k—冲击韧性 A k—冲击功 HB—布氏硬度 HRC—洛氏硬度 HV—维氏硬度 3.有一定的关系。硬度可以表示金属材料在一个小体积范围内抵抗弹性变形、塑性变形和破坏的能力。而抗拉强度亦是指材料在拉力作用下抵抗变形和破坏的能力。 4.
5 用铁制造:铁锅。 用有色金属制造:铝锅、铝盆、铜制自来水龙头等。 6.车床中钢制零件:主轴、各传动轴、高速齿轮等。 铁制零件:床身、齿轮箱、尾架等。 7.塑性变形是一种永久性变形,外力去除后变形并不消失,而弹性变形在外力去除后变形消失,物体恢复原状。 8.同素异晶转变——固态金属在不同的温度下具有不同的晶格类型的现象。 例如纯铁在912℃以下具有体心立方晶格,在912℃~1300℃之间具有面心立方晶格。9.金属在结晶过程当中,晶粒的粗细与晶核数目的多少及晶核长大的速度有关。 10.固溶体:溶质原子融入溶剂晶格而保持溶剂晶格类型的金属晶体称之为固溶体。 化合物:指两个或两个以上的组元按一定的原子比相互化合而成的新物质。 机械混合物:组成合金的组元在互配的情况下既不溶解也不化合,而是按一定的重量比例,以混合的方式存在着,形成各组元晶体的机械混合物。 具有固溶体结构的金属材料其强度和硬度比纯金属高,而具有化合物结构的金属材料通常硬度很高,而且脆性大,具有机械混合物机构的金属材料不仅决定各组成的 性能,还与各数量大小,形状及分布情况有关,通常它比单一固溶体强度、 硬度高,塑性、韧性差。 11.合金状态图即是表明合金系结晶过程的简明图体。其用途是利用合金状态图可以分析合金随成分及温度的变化,其组织及性能的变化情况。 12.铁素体:碳原子溶入α—Fe的固溶体。含碳量为小于0.02%。特点:强度、硬度低,塑性、韧性好。 渗碳体:铁和碳化合形成的化合物,含碳量为6.69%。特点:硬度高,脆性大。 珠光体:一定含量的铁素体和渗碳体组成的共析的机械混合物,含碳量为0.77%。特点:性能介于铁素体与渗碳体之间。 奥氏体:指碳原子溶入α—Fe的固溶体。含碳量小于2.11%。特点:塑性很好,不具碳性。 13.成分上的区别:碳钢含碳量小于2.11%,铸铁含碳量大于2.11%。 组织上的区别:常温下,含碳量小于0.77%的碳钢其组织为铁素体+珠光体;含碳量等于0.77%的碳钢其组织为珠光体;含碳量大于0.77%的碳钢其组织为珠光体+渗碳体。 铸铁在常温下的内部组织为珠光体+渗碳体。 14.A1——共析反应线,亦是一条恒温线(727℃)。 A cm——奥氏体冷却到A cm时开始析出铁素体 A3——奥氏体冷却到A3时,开始析出铁素体 15. 45钢由液态至AC线时,一部分液体转变为固体,其组织为奥氏体。另一部分液体状态 不变,继续冷却,冷至AE线时,所有液体全部转变为固体,其组织为奥氏体;温度继
机械制造基础课程设计夹具设计工艺设计要点
机械制造基础课程设计 设计题目:制订轴承端盖工艺及直径为10mm孔夹具设计 班级: 学生: 指导教师:
目录 设计任务书 一、零件的分析……………………………………… 二、工艺规程设计…………………………………… (一)、确定毛坯的制造形式…………………… (二)、基面的选择……………………………… (三)、制订工艺路线…………………………… (四)、机械加工余量、工序尺寸及毛坯尺 才的确定…………………………………………… (五)、确定切削用量及基本工时……………… 三、夹具设计………………………………………… 四、参考文献………………………………………… 订做机械制造基础课程设计工艺及夹具设计- 1 -
一、零件的分析 (一)零件的工艺分析 轴承端盖具有密封,定位的作用,因此结合面要有比较高的表面质量,孔系加工也要求有比较高位置精度和形状精度,这个零件从零件图上可以看出,所有加工表面是以?16mm为中心的,包括:?32H7mm及倒角,尺寸为?11mm,?7mm的沉头孔及螺纹孔,M5螺纹底孔,?11mm,?10mm进油孔,以及?56mm圆柱面,?16mm孔与?56mm柱面同心度为0.025; 由以上分析可知,对于这些加工表面而言,我们首先加工出?56mm外圆柱面,并以此为粗基准加工出关键部分孔?16mm,并以此为基准加工其它表面,并且保证其它表面与孔之间的位置精度要求。 二、工艺规程设计 (一)确定毛坯的制造形式 零件材料为HT200,考虑到该零件在车床中的受力并保证零件的工作可靠性,零件为中批生产,而且零件的尺寸不大,因此,毛坯可采用金属模砂型铸造。 (二)基面的选择 1 基准选择原则 ①粗基准的选择 选择粗基准时,主要要求保证各加工面有足够的余量,使加工面与不加工面间的位置符合图样要求,并特别注意要尽快获得精基面。具体选择时应考虑下列原则: 1) 选择重要表面为粗基准 2) 选择加工余量最小的表面为粗基准 3) 选择较为平整光洁、加工面积较大的表面为粗基准以便工件定位可靠、夹紧方便。 4) 粗基准在同一尺寸方向上只能使用一次因为粗基准本身都是未经机械加工的毛坯面,其表面粗糙且精度低,若重复使用将产生较大的误差。 订做机械制造基础课程设计工艺及夹具设计- 2 -
工程材料及机械制造基础大作业(DOC)
《工程材料及机械制造基础》 课程结业论文 学院机械工程学院 专业 班级 学号 姓名 指导老师 完成日期2015年 5 月 15 日
卧式和面机典型零件的选材及加工工艺 一、前言 1.课程背景 工程材料及机械制造基础是研究常用机械零件的制造过程及制造方法的一门综合性技术基础课。是高等工业学校机械类专业和一些非机械类专业必修的技术基础课。课程内容包含工程材料、成型工艺基础和机械加工工艺基础三部分,主要介绍常用工程材料的组织、性能、应用和选用原则;各种毛坯的成型方法及零件的切削加工方法的基本原理和工艺特点;零件的结构工艺性以及机械加工工艺过程的基础知识;机械制造新材料、新技术及新工艺。通过本课程的学习,我们获得了常用工程材料、材料成形工艺及现代机械制造的基础知识,为学习其它相关课程及以后从事工程技术工作和科学研究奠定必要的基础。 本文以卧式和面机为例,通过初步分析卧式和面机典型零件的材料选择、毛坯生产方法、热处理工艺、零件制造工艺流程和结构工艺性,以加深对工程材料及机械制造基础课程的理解。 2.卧式和面机简介 和面机是一种食品加工机械,在食品机械的设计、制造、维护及材料等方面都要考虑到食品的特殊要求,要有切实可行的密封,简单方便的洗涤,以及彻底干净的杀菌的机构。通常我们应该注意以下几点。 1)结构上,接触食品的各个部件要能简单迅速的分解组合,分解的零件能便于洗涤; 2)材料上,对接触食品的零部件尽可能地采用不锈钢或其他防锈无污染材料; 3)环境保护上,必须有可靠的密封措施,严防杂物混入食品和物料散失; 4)在温度上,要有可靠的控温措施; 5)在工作环境上,机器应放置在空气流通、光线、温度和湿度适宜的地方。 和面机作用是进行面团的调制,既将各种原、辅料加水搅拌,调制成即符合质量要求,又适合机械加工成形的面团,主要用于面包、饼干、糕点、膨松食品、夹馅饼等食品生产过程中的面团调制。和面机可分为卧式和面机和立式和面机。 卧式和面机主要是指搅拌容器轴线与搅拌器回转轴线都处于水平位置,它的特点是,结构简单,制造成本低,卸料清洗方便,所以在食品加工中,如面包、饼干、糕点及一些饮食行业的面食中得到了广泛的应用。 根据食品生产的种类和特点不同,面团的各种性质各不相同,可分为韧性面团、水面团及酥性面团,一般来讲,对面团拉伸作用较强时,易于形成韧性面团,而对面团拉捏作用较强时,易于形成酥性面团。卧式和面机一般是在一根轴上安装几片浆叶,它对面团的拉伸作用较弱。适用于调制酥性面团。
机械制造基础课后作业说课讲解
第一章工程材料的基本知识 1,说明下列符号的含义及其所表示的机械性能指标的物理意义:σs,σb,HRC,180HBS10/1000/30 答:σs屈服强度符号,材料产生屈服现象时的最小应力值称为屈服强度。σs=F S/S O. σb 抗拉强度符号,材料被拉断前承受最大载荷时的应力值称为抗拉强度。σb= F b/S O. HRC洛氏硬度符号,压头为1200金刚石圆锥体。180HBS10/1000/30表示用直径为10mm的淬火钢球在1000Kgf的载荷作用下,时间保持30s所测得的布氏硬度值为180。 2,为什么冲击韧性值不直接用于设计计算?它与塑性有何关系? 答:冲击韧性值是通过一次摆锤冲击试验测得的,测试时要求一次冲断,而生产实地中的工件大多数都是多次冲击后才被破坏的,这与冲击试验中一次冲断的情况相差较大,所以冲击韧性值常规下只用于判定材料是塑性的还是韧性的,而不用于直接设计。韧性是材料强度和塑性的综合指标,当材料的强度和塑性都很好时,材料的韧性才会很好。 3,何谓金属的疲劳和蠕变现象?它们对零件的使用性能有何影响? 答:金属在连续交变载荷的作用下发生突然性的断裂称为疲劳断裂。金属在高温长时间应力作用下产生明显的塑性变形直至断裂的现象称为蠕变。在设计零件时,必须考虑疲劳强度和蠕变强度及持久强度。 4.Fe—Fe3C相图在生产实践中有何指导意义?有何局限性? 答:铁碳合金相图的指导意义:(1),选择材料方面的应用;(2),铸造方面的应用;(3),锻造方面的应用;(4),热处理方面的应用; 由于铁碳相图是以无限缓慢加热和冷却速度得到的,而在实际加热和冷却都有不同程度的滞后现象。 第二章钢的热处理 一,何为钢的热处理?钢的热处理有哪些基本类型? 答:钢在固态下采用适当方式进行加热、保温,并以一定的冷却速度冷却到室温,改变钢的组织从而改变其性能的一种工艺方法。 类型包括退火、正火。淬火、回火四种基本类型。 二,退火和正火的主要区别是什么?生产中如何选择正火和退火? 答:正火比退火的冷却速度快些,故正火的组织比较细,硬度强度比退火高。 根据其加工性、使用性、经济性来选择。 三,常用的淬火方法有哪些,说明它们的主要特点及应用范围。 答:1,单液淬火法:操作简单,易于实现机械化,自动化。 2,双液淬火法:适用于高碳工具钢制造的易开裂工件,如丝锥、板牙等。 3,分级淬火法:适用于由合金钢制造的工件或尺寸较小、形状复杂的碳钢工件。 4,等温淬火法:适用于形状复杂、且要求具有较高硬度和韧性的工具、模具等工件。 5,局部淬火法:对要求局部有高硬度的工件。 四,回火的目的是什么?常用的回火方法有哪几种?指出各种回火方法得到的组织、性能及应用范围。 答:回火的目的有四个: 1,降低脆性,消除或减少内应力。 2,获得工件所要求的机械性能。 3,稳定工件的尺寸。 4,降低工件硬度,利于切削加工。低温回火组织为回火马氏体,一般为工模具钢要求高硬度高强度的工艺。
现代工程材料成形与机械制造基础-第二版 -册-部分题库与答案
1.分析图示轨道铸件热应力的分布,并用虚线表示出铸件的变形方向。工艺上如何解决? 轨道上部较下部厚,上部冷却速度慢,而下部冷却速度快。因此,上部产生拉应力,下部产生压应力。变形方向如图。 反变形法 5.如图一底座铸铁零件,有两种浇注位置和分型面方案,请你选择一最佳方案,并说明理由。 方案(Ⅱ)最佳.。 理由:方案(Ⅰ)是分模造型,上下铸件易错边,铸件尺寸精度差。 方案(Ⅱ)是整模造型, 铸件尺寸精度高。内腔无需砂芯成型,它是靠 上、下型自带砂芯来成形。 6.下图为支架零件简图。材料HT200,单件小批量生产。 (1)选择铸型种类 (2)按模型分类应采用何种造型方法? (3)在图中标出分型面、浇注位置、加工余量 (1) 砂型铸造,(2)整模造型 (3)分型面、浇注位置、加工余量:见图 9.如图,支架两种结构设计。 (1)从铸件结构工艺性方面分析,何种结构较为合理?简要说明理由。 (2)在你认为合理的结构图中标出铸造分型面和浇注位置。
(1)(b)结构较为合理。因为它可省去悬臂砂芯。 (2)见图。分型面。浇注位置(说明:浇注位置上、下可对调) `12.如图所示铸件结构是否合理?如不合理,请改正并说明理由。 铸件上部太厚,易形成缩孔,壁厚不均匀易造成热应力。可减小上部壁厚,同时设加强筋。 无结构圆角,拐弯处易应力、开裂。设圆角。 3.某厂铸造一个Φ1500mm的铸铁顶盖,有图示两个设计方案,分析哪个方案的结构工艺性 好,简述理由。 (a)图合理 (b)图结构为大的水平面,不利于金属液体的充填,易造成浇不足、冷隔等缺陷;不利于金属夹杂物和 气体的排除,易造成气孔、夹渣缺陷;大平面型腔的上表面,因受高温金属液的长时间烘烤,易开裂使铸件产生夹砂结疤缺陷。 7.图示铸件的两种结构设计,应选择哪一种较为合理?为什么?
机械制图说课稿
机械制图说课稿 《机械制图》说课稿 机电工程系刘萍 各位领导、老师,大家好,《机械制图》课程为机电、数控、汽修专业第一学年所开设的专业基础课程,周课时4节,总课时128节。下面我将从以下六个方面进行说课:一、课程定位;二、课程目标;三、学生情况;四、课程设计;五、教学实施;六、教学资源。 一、课程定位 《机械制图》课程在机电一体化专业培养目标中应达到的岗位关键能力。从近三年,我院机电一体化专业毕业生就业岗位为,生产一线的机械加工与装配,工厂电气设备的维护、机电设备的安装与操作。我对机械制图能力要求较高的机械加工与装配工作岗位进行了分析调查,下面是实习单位万兴集团提供的一份机械零件加工工作过程表。 见表1-1 机械零件加工工作表 与图样的工作过程过程内容关系 接受 1、接受零件加工任务书(零件图纸图号、零件数量、完成工作期限)。 直接工作任务 2、接受加工零件图直接 3、接受其他工艺技术资料间接 4、仔细阅读加工任务书间接 5、仔细阅读图纸 初步了解 a、将图纸和加工任务书进行核对是否有误 任务内容 b、图纸本身是否清晰、完整,是否影响阅读直接 c、了解加工零件的名称、形状、大小、重量、材料及数量
d、了解预定完工的期限,估算工作进度 6、领取材料,清点数量直接 7、按加工任务书、图纸核对材料是否相符直接材料准备 8、检查、测量材料是否符合加工前的要求,外形尺寸是否正确,是否直接有足够的加工余量 材料准备 9、材料的材质是否正确,材料是否有裂纹、气孔、碰伤等缺陷直接技术准备 10、按照加工图纸,对照材料确定加工内容,即哪些地方要加工,哪些直接地方不要加工 首台机床 11、按加工位置和内容的特点分类选择加工机床设备直接 加工 12、编排机床设备加工顺序间接 13、根据每台机床的特点,对照图纸和材料确定加工方法 更换机床 ,、确定零件加工尺寸基准直接加工 ,、确定零件在首台机床上的全部加工位置 ;、确定零件加工步骤 自检、送检 14、按图纸尺寸标注要求,选择量具的种类规格及精度直接总结、调整 1 15、按图纸形位公差要求选择加工装夹方法直接 16、按图纸标注的材质和表面要求选择切削刀具,切削用量,润滑冷却直接 剂等 17、刀具的准备 ,、品种齐全间接 ,、必要的磨制 18、装夹具及辅助工具的准备间接技术准备
机械制造基础-题目及答案
《机械制造基础》 一、名词解释 7、晶体原子(离子)在空间呈有规则排列的物质。 8、晶格为便于描述晶体中原子排列的情况,将每个原子抽象为一个质点,并用假想的直线连结起来,构成的一个假想的空间格架。 9、晶胞晶格中能代表其原子排列规律的最小单元 10、合金两种或两种以上的金属元素(或金属元素与非金属元素)熔合在一起所形成的具有金属特性的物质。 11、过冷奥氏体指冷到A1温度以下暂时存在的不稳定状态的奥氏体 12、残余奥氏体指过冷奥氏体冷却至MS线以下,未能全部转变为马氏体,仍保留下来的部分奥氏体。 13、淬透性钢在一定条件下淬火后获得淬透层深度的能力 14、淬硬性指钢经淬火后所能达到的最大硬度值。 15、回火抗力钢在回火时抵抗硬度下降的能力。 17、石墨化铸铁中的碳以石墨形式析出的过程 18、复合材料由两种以上在物理和化学不同的物质组合起来得到的一种新型多相固体材料 19、落砂将铸件从砂型内取出的工序。 20、冷裂指铸件在较低温度金属进入弹性状态时产生的裂纹。 21、液态收缩指从浇注温度至开始凝固时的收缩。 22、凝固收缩指从凝固开始到凝固完毕的收缩。 23、固态收缩指从凝固终了温度到室温之间的收缩 24、特种铸造除砂型铸造外的其余各种铸造方法的统称 25、塑性变形将引起晶体变形的外力消除后,变形也不能完全消失的现象 26、加工硬化金属的塑性变形导致其强度、硬度提高,而塑性和韧性下降的现象。27、锻造比指金属坯料在锻造前的横截面积与锻造后的横截面积之比。 28、纤维组织热加工时,铸态组织中的各种夹杂物,由于在高温下具有一定塑性,它们会沿着变形方向伸长,是纤维分布,当再结晶时,这些夹杂物依然沿被伸长的方向保留下来,称为纤维组织。 29、锻造温度范围始锻温度与终锻温度的区间。 30、自由锻指利用冲击力和压力,使金属坯料在两个抵铁之间产生自由变形而获得毛坯的一种加工方法。 31、熔滴焊接时,在焊条(或焊丝)端部形成的向熔池过渡的液体金属滴。 32、焊接电弧焊件与焊条之间(或二电极之间,电极与焊件之间)的气体介质产生的强烈而持久的放电现象 33、酸性焊条指焊条熔渣的成分主要是酸性氧化物(如TiO2Fe2O3)的焊条。35、焊接性焊接性是指金属材料对焊接加工的适应能力 二、填空题 3、三种常见的金属晶格类型是(体心立方晶格)、(面心立方晶格)、(密排六方晶格)。4、理论结晶温度T0与实际结晶温度Tn之差,称为(过冷度)。
机械制造基础课程设计
机械制造基础课程设计书明书 课程名称:机械制造基础课程设计 题目名称:设计“阶梯轴”的机械加工工艺班级: 姓名: 学号: 指导老:
工序号工序名称工序内容 1 备料锻造 2 车 1 三爪卡盘夹持工件,车端面见平,钻中心孔。 用尾顶尖顶住,粗车三个台阶,直径、长度均 留2mm余量. 2调头,三爪卡盘夹持工件另一端,车端面, 保证总长259mm,钻中心孔。用尾顶尖顶住, 粗车另外四个台阶,长度、直径均留2mm余 量 3 热处理调质处理硬度24~28HRC 4 钳修研中心孔 5 粗车 1 双顶尖装夹半精车三个台阶,长度达到尺 寸要求,螺纹大径车到 mm,其余两个台阶直径上留 0.5mm余量,切槽三个,倒角三个 2调头,双顶尖装夹半精车余下的五个台阶。 mm及mm 台阶车到图样规
定的尺寸。螺纹大径车到mm, 其余两个台阶直径上留0.5mm余量,切槽三 个,倒角四个 6 修中心孔用金刚石或硬质合金顶尖加压修研 7 精车双顶尖装夹,车一端螺纹M24×1.6-6g 调头,车另一端M24×1.6-6g 8 划线划出键槽及?5位置 9 铣铣两个键槽及一个止动垫圈槽,键槽深度比图 样规定尺寸大0.25mm,作为外圆磨削的余量 10 磨磨外圆Q、M并用砂轮端面靠磨台肩H、I 调头,磨外圆N、P,靠磨台肩G 11 检验按图纸检验 工序说明: 1、该零件先以外圆作为粗基准,车端面和钻中心孔,再以中心孔为定位基准粗车外又以粗车外圆为定位基准加工孔,此即为互为基准原则,使加工有一次比一次精度更高的定位基准面。
2、螺纹因淬火后,在车床上无法加工,如先车好螺纹后再淬火,会使螺纹产生变形。因此,螺纹一般不允许淬硬,所以在工件的螺纹部分的直径和长度上必须留去碳层。 3、为保证中心孔精度,工件中心孔也不允许淬硬。 4、为保证工件外圆的磨削精度,热处理后需安排研磨中心孔的工序,并要求达到较细的表面粗糙度。 5、为消除磨削应力,磨后安排低温时效工序。
西工大19春《机械制造基础(含材料)》在线作业答案
西工大19春《机械制造基础(含材料)》在线作业 试卷总分:100 得分:100 一、单选题(共10 道试题,共25 分) 1.厚度较大的焊接容器、精度和尺寸稳定性要求高的重要焊接结构焊后应进行的热处理方法是( )。 A.低温回火 B.完全退火 C.去应力退火选项 D.扩散退火选项 答案:C 2.在压力加工过程中,为改善坯料塑性时,下列( )情况最好。 A.坯料三向受压 B.坯料两向受压 C.坯料三向受拉 D.坯料两向受拉 答案:A 3.电渣焊是一种熔化焊方法,其焊接热源是( )。 A.电流通过液态熔渣时所生产的电阻热 B.电流通过工件时所生产的电阻热 C.焊接电弧 D.光能 答案:A 4.目前砂型铸造仍在金属毛坯的制造中占有相当的份额,其主要原因是( )。 A.生产的自动化程度高 B.生产成本低 C.毛坯的机械性能高 D.毛坯的成品率高 答案:B 5.大型铸钢件在批量生产时,适合采用的铸造方法是( )。 A.离心铸造 B.砂型铸造 C.熔模铸造 D.压力铸造 答案:B 6.Fe-Fe3C相图中的GS线是( )。 A.加热时从A析出F的开始线 B.加热时A溶入F的开始线 C.冷却时从A析出F的开始线 D.冷却时从A析出Fe3C的开始线
答案:C 7.2. 锤上模锻时,能使坯料某一部分截面减小而使另一部分截面增大的模膛是( )。 A.拔长模膛 B.滚压模膛 C.切断模膛 D.弯曲模膛 答案:B 8.铸造合金在凝固过程中,液、固相混杂的双相区域的宽窄,即凝固区域的宽度,对合金的流动性有较大的影响。下列不会影响到凝固区域宽度的因素是( )。 A.铸型的激冷能力 B.合金的导热系数 C.合金的固态收缩量 D.合金的凝固温度范围 答案:C 9.零件的制造一般要经过____________________________________等阶段。() A.毛坯生产、切削加工、热处理、装配 B.毛坯生产、热处理、切削加工、装配 C.毛坯生产、热处理、装配、切削加工 D.毛坯生产、装配、热处理、切削加工 答案:A 10.现要加工一批小光轴的外圆,材料为45钢,淬火硬度为HRC40~45,批量为2000件,宜采用的加工方法是()。 A.纵磨 B.深磨 C.横磨 D.无心外圆磨 答案:D 二、多选题(共10 道试题,共25 分) 11.主运动是由刀具执行的机床有:()。 A.龙门刨床 B.镗床 C.牛头刨床 D.磨床 答案:BCD 12.切削用量三要素指的是:()。 A.切削速度 B.进给量 C.切削深度
机械制造基础课程设计--一阶梯状轴
机械制造基础课程设计--一阶梯状轴
1序言------------------------------------------(1) 2机械加工工艺规程设计步骤---------------------(2-7) 2.1 生产类型及零件分析-------------------------------------- (2) 2.2确定毛坯及各表面加工方法--------------------------------(2-3) 2.3确定定位基准及划分加工阶段------------------------------(3-4) 2.4热处理及工艺路线----------------------------------------(4-5) 2.5工序设计及加工余量选择----------------------------------(6) 3工艺说明----------------------—-------------(7-17) 3.1 工序一 --------------------------------------------(7) 3.2 工序二 --------------------------------------------(7) 3.3 工序三 --------------------------------------------(7-17) 塞规 -------------------------------------------(7-14)深浅样板 -------------------------------------------(15-16)成型车刀 -------------------------------------------(16-17) 3.4 工序四 -------------------------------------------(17) 4课设总结-------------------------------------(18)
工程材料与机械制造基础复习题参考样本
《机械制造基础》复习题 1.什么叫材料的塑性? 塑性有哪两个指标, 如何用公式表示? 试述塑性的两个 作用。 答: 塑性是指金属材料在外力作用下, 产生永久变形而不致引起断裂的性能。指 标: 伸长率δ和断面收缩率Ψ。公式表示δ=(L 1-L 0 )/L 0*100% Ψ =(F 0-F 1 )/F 0*100% 式中 L 0—试样原始长度 L 1—试样拉断后的长度 F 0—试 样原始横截面积 F 1 试样拉断后的横截面积 作用: 1、 方便加工2、 提高 材料的可靠性 2.说明下列力学性能指标的名称、 单位、 含义: k s b αδσσσσ,,,,,12.0-。分别 指出哪些指标是动载下的力学性能, 哪些是静载下的力学性能。 答: δb 抗拉强度, 单位MPa , 指金属材料拉断前所能承受的最大应力。 δs 屈服极限 单位MPa , 指出现明显塑性变形时的应力。 δ0.2 条件屈服强度 单位MPa , 指试样产生0.2%残余塑性变形时的应力值。 δ-1 疲劳强度 单位MPa , 指最大应变力δmax 低于某一值时, 曲线与横坐标平 行, 表示循环周次N 能够达到无穷大, 而试样仍不发生疲劳断裂时的交变应力 值。 δ 伸长率 单位: 无δ=( L 1-L 0/L 0) *100% 式中L 1指试样拉断后的长度 L 0指试 样原始长度 a k 冲击韧性 单位 J/cm 2 指金属材料在冲击载荷作用下, 抵抗断裂的能力。 动载荷下的力学性能: δ-1, a k 静载荷下的力学性能: δb , δs , δ0.2 , δ 3.从压头的材料、 形状、 载荷大小、 硬度值计算方法、 应用等方面简要说明 布氏硬度、 洛氏硬度、 微氏硬度三种测量硬度的方法的特点。 答: 布氏硬度: 压头材料: 淬火钢球或硬质合金球、 形状: 球形、 载荷大小: 3000kgf 、 硬度值计算方法: 载荷除以压痕表面积的值、 应用: 铸铁、 有色金 属、 低合金结构钢等毛坯材料。
机械制造基础形成性考核册答案
机械制造基础形成性考核册答案 第一章 一、填空题 1.金属材料的力学性能是指在外载荷作用下其抵抗( 变形) 或( 破坏) 的能力。 2.材料的性能一般分为( 使用性能) 和( 工艺性能) 。 3.材料的使用性能包括( 力学性能) 、 ( 物理性能) 和( 化学性能) 。 4.材料的工艺性能包括( 铸造性) 、 ( 锻造性) 、 ( 焊接性) 、 ( 切削加工性) 和热处理性等。 5.强度是指金属材料在外载荷作用下, 抵抗( 塑性变形) 和( 断裂) 的能力。 6.金属材料在外载荷作用下产生( 断裂前) 所能承受( 最大塑性变形) 的能力称为塑性。 7.金属塑性的指标主要有( 伸长率) 和( 断面收缩率) 两种。 8.金属抵抗冲击载荷的作用而不被破坏的能力称为( 冲击韧性) , 其数值( 愈大) , 材料的韧 性愈好。其数值的大小与试验的温度、试样的形状、表面粗糙度和( 内部组织) 等因素的影响有关。 9.在铁碳合金中, 莱氏体是由( 珠光体) 和( 渗碳体) 所构成的机械混合物。 10.疲劳强度是表示材料经无数次( 交变载荷) 作用而不引起( 断裂) 的最大应力值。 11.低碳钢拉伸试验的过程能够分为弹性变形、 ( 塑性变形) 和( 断裂) 三个阶段。 12.表征金属材料抵抗冲击载荷能力的性能指标是( 冲击韧性) 。 13.表征金属材料抵抗交变载荷能力的性能指标是( 疲劳强度) 。 14.铁碳合金的基本组织有( 铁素体) , ( 奥氏体) , ( 渗碳体) , ( 珠光体) , ( 莱氏体) 五种 二、判断题 1.冲击韧性值随温度的降低而增加。( X) 2.抗拉强度是表示金属材料抵抗最大均匀塑性变形或断裂的能力。( √) 3.硬度是指金属材料抵抗其它物体压入其表面的能力。( X) 4.金属材料在外载荷作用下产生断裂前所能承受最大塑性变形的能力称为塑性。( √) 5.冲击韧性值随温度的降低而减小。( √) 6.强度越高, 塑性变形抗力越大, 硬度值也越高。( √) 7.屈服强度是表示金属材料抵抗微量弹性变形的能力。( X) 8.冲击韧性值愈大, 材料的韧性愈好。( √) 9.硬度是指金属材料抵抗比它更硬的物体压入其表面的能力。( √) 10.一般材料的力学性能是选材的主要指标。( √) 11.一般来说, 材料的硬度越高, 耐磨性越好。( √) 12.测量布氏硬度时, 压头为淬火钢球, 用符号HBW表示。( X) 13.测量布氏硬度时, 压头为淬火钢球, 用符号HBS表示。( √) 14.测量布氏硬度时, 压头为硬质合金球, 用符号HBW表示。( √) 15.测量洛氏硬度时, 压头为120°金刚石圆锥体, 用符号HRC表示。( X) 16.疲劳强度是表示在冲击载荷作用下而不致引起断裂的最大应力。( X) 17.受冲击载荷作用的工件, 考虑力学性能的指标主要是疲劳强度。( X) 18.冲击韧性是指金属材料在静载荷作用下抵抗破坏的能力。( X) 第二章 一、填空题 1.钢的热处理工艺由( 加热) 、 ( 保温) 和( 冷却) 三个阶段组成, 一般来说, 它不改变热处 理工件的( 形状) , 而改变其( 内部组织) 。 2.钢的化学热处理常见的工艺方法有( 渗碳) 、 ( 氮化) 和( 碳氮共渗) 三种。 3.钢的渗碳方法能够分为( 固体渗碳) 、 ( 液体渗碳) 、 ( 气体渗碳) 三种。
工程材料及机械制造基础复习(工程材料)
工程材料及机械制造基础复习(Ⅰ) ——工程材料 工程材料 1.1 材料的力学性能 1.2.1 金属的晶体结构 (1)基本概念 ①晶体与非晶体: 两者的主要区别是: a.晶体中原子(或分子)按一定的几何规律作周期的重复排列; b.晶体具有固定的熔点; c.晶体具有各向异性。 ②晶格;为了便于表明晶体内部的原子排列规律,把每个原子看成一个点,点与点之间用直线连接起来而形成的空间格子。 ③晶胞:能完全反映晶格原子排列特征的最小几何单元。 ④晶格常数;晶胞的棱边长度,晶格常数和棱面夹角表示晶胞的形状和大小。 (2)常见金属晶格类型 单晶体的各项异性:由于各晶面和各晶向上的原子排列密度不同,因而导致在同一晶体的不同晶面和晶向上的各种性能也不同——各项异性。 多晶体 晶粒大小对材料性能影响很大,在常温下,晶粒愈细,材料的强度高,塑性、韧性愈好。 晶体的缺陷形式:点缺陷、线缺陷、面缺陷。 晶体的缺陷对金属的许多性能有很大的影响,特别对金属的塑性变形、强化、固态相变等都有重要的影响。 1.2.2 金属的结晶 (1)结晶的概念 物质从液态转变为固态的过程称为凝固。而结晶是指由液态转变为晶体的过程,即金属与合金从液态的无序状态转变为原子有规则排列的晶体结构的过程。理解结晶的概念应着重掌握以下几点: ◆纯金属的结晶在恒温下进行,其结晶过程可用冷却曲线表示。 ◆纯金属的结晶需要一定的过冷度,即过冷是金属结晶的必要条件。过冷度△T是指理论结晶温度To与实际结晶温度Tn之差(△T=To—Tn)。冷却速度越大,过冷度越大。 ◆金属的结晶包括两个过程:晶核的形成和晶核的长大。 (2)晶粒大小及其控制 晶粒越细,则金属的强度、硬度、塑性和韧性越好。控制晶粒大小的方法有:增加过冷度(或增加冷却速度,如用金属型代替砂型、降低浇注温度、慢速浇注等)、变质处理、附加振动(机械振动、超声波振动、电磁搅拌等)。 (3)金属的同素异晶转变 金属在固态下发生晶格类型改变的过程称为同索异晶转变。它与液态金属结晶相比具有以下特点: ①遵循金属结晶的一般规律(生核与长大);
机械制造基础课程设计
机械制造基础课程设计 题目:设计气门摇杆轴支座零件的机械加工工艺规程学校:九江职业技术学院 班级:机电1002班 设计:詹志峰 辅导:李殿亚 设计时间:2012 年06 月04日
目录 前言 (2) 课程设计任务书 (4) 一.加工工艺设计 (11) 1.1蜗杆轴零件图 (5) 1.2蜗杆轴的特点 (6) 1.3蜗杆轴的应用及技术要求 (6) 二.夹具设计 (17) 三.后记 (18) 四.参考文献 (19) 附表 艺过程卡、加工工艺卡、工序卡 前言 课程设计是考察学生全面在掌握基本理论知识的重要环节机械制造工艺学课程设计是在我们学完这学期基础课、技术基础课以及部
分专业课之后进行的。这是我们毕业之前对所学各课程的一次深入的综合性的链接,也是一次性理论联系实际的训练。 在学完机械制造基础的基础上进行这样的设计和练习,我们觉得是很有必要的,它对我们的理论知识有了一定的提高,让我们知道了学习知识的重要性和怎么根据具体的情况设计出实用的零件。 就我个人而言,我希望能通过这次课程设计对自己未来将从事的工作进行一次适应性训练。从中锻炼自己分析问题、解决问题、提高自己、对此专业课有更深刻的认识和了解,为今后参加社会现代化建设奠定一个良好的基础。 机械制造基础课程设计任务书 设计题目设计“气门摇杆轴支座”零件的机械加工
一、题目 1、设计_气门摇杆轴支座零件的机械加工工艺规程。 2、生产类型:单件、成批(小批、中批、大批)、大量生产。 3、课程设计的具体要求如下。 (1)毛坯图:1张。 (2)机械加工工艺过程卡片:1份。 (3)机械加工工序卡片:3份。 (4)课程设计说明书一份。 二、具体内容。 1、确定生产类型,对零件进行工艺分析; 2、确定毛坯种类及制造方法,绘制毛坯图; 3、确定零件各表面的加工方法及其定位基准; 4、拟定零件的机械加工工艺过程,选定各工序的加工内容、加工设备及工 艺装备(刀具、夹具、量具和辅具); 5、确定工序尺寸及公差,各工序切削用量,计算某一代表工序的工时定额, 画出工序简图; 6、填写工艺文件,包括工艺过程卡片、工序卡片; 7、撰写设计说明书。 三、上交内容装订顺序(全部用A4纸打印)。 1、封面; 2、目录; 3、任务书; 4、说明书; 5、参考文献目录; 6、附件(零件图、毛坯图、机械加工工艺过程卡片及工序卡片); 7、结束语。 二、零件的工艺分析及生产类型的确定 1.1零件用途 气门摇杆轴支座是柴油机一个主要零件。是柴油机摇杆座的结合部,?20(+0.10—+0.16)孔装摇杆轴,轴上两端各装一进气门摇杆,摇杆座通过两个?13mm孔用M12螺杆与汽缸盖相连,3mm轴向槽用于锁紧摇杆轴,使之不转动。汽缸盖内每缸四阀使燃烧室充气最佳,气门由摇杆凸轮机构驱动,摩擦力小且气门间隙由液压补偿。这种结构可能减小燃油消耗并改善排放。另外一个优点是减小噪音,这种结构使3.0升的TDI发动机运转极端平稳。