湿法炼锌渣综合利用工艺现状及分析
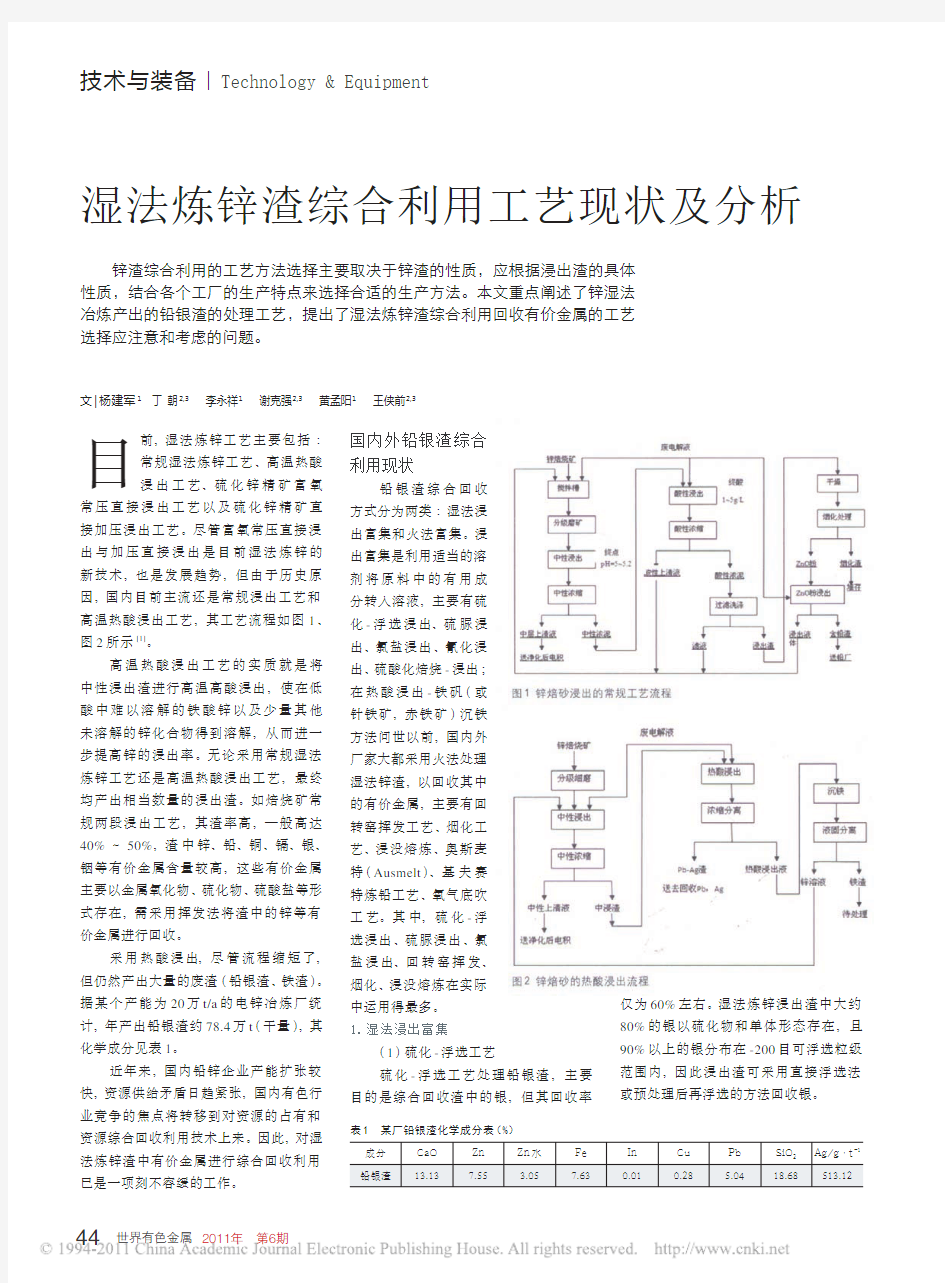

技术与装备 | Technology & Equipment
目
前,湿法炼锌工艺主要包括:常规湿法炼锌工艺、高温热酸浸出工艺、硫化锌精矿富氧
常压直接浸出工艺以及硫化锌精矿直接加压浸出工艺。尽管富氧常压直接浸出与加压直接浸出是目前湿法炼锌的新技术,也是发展趋势,但由于历史原因,国内目前主流还是常规浸出工艺和高温热酸浸出工艺,其工艺流程如图1、图2所示[1]
。
高温热酸浸出工艺的实质就是将中性浸出渣进行高温高酸浸出,使在低酸中难以溶解的铁酸锌以及少量其他未溶解的锌化合物得到溶解,从而进一步提高锌的浸出率。无论采用常规湿法炼锌工艺还是高温热酸浸出工艺,最终均产出相当数量的浸出渣。如焙烧矿常规两段浸出工艺,其渣率高,—般高达40%~50%,渣中锌、铅、铜、镉、银、铟等有价金属含量较高,这些有价金属主要以金属氧化物、硫化物、硫酸盐等形式存在,需采用挥发法将渣中的锌等有价金属进行回收。
采用热酸浸出,尽管流程缩短了,但仍然产出大量的废渣(铅银渣、铁渣)。据某个产能为20万t/a 的电锌冶炼厂统计,年产出铅银渣约78.4万t (干量),其化学成分见表1。
近年来,国内铅锌企业产能扩张较快,资源供给矛盾日趋紧张,国内有色行业竞争的焦点将转移到对资源的占有和资源综合回收利用技术上来。因此,对湿法炼锌渣中有价金属进行综合回收利用已是一项刻不容缓的工作。
国内外铅银渣综合利用现状
铅银渣综合回收方式分为两类:湿法浸出富集和火法富集。浸出富集是利用适当的溶剂将原料中的有用成分转入溶液,主要有硫化-浮选浸出、硫脲浸出、氯盐浸出、氰化浸出、硫酸化焙烧-浸出;在热酸浸出-铁矾(或针铁矿,赤铁矿)沉铁方法问世以前,国内外厂家大都采用火法处理湿法锌渣,以回收其中的有价金属,主要有回转窑挥发工艺、烟化工艺、浸没熔炼、奥斯麦特(Ausmelt )、基夫赛特炼铅工艺、氧气底吹工艺。其中,硫化-浮选浸出、硫脲浸出、氯盐浸出、回转窑挥发、烟化、浸没熔炼在实际中运用得最多。1.湿法浸出富集
(1) 硫化-浮选工艺
硫化-浮选工艺处理铅银渣,主要目的是综合回收渣中的银,但其回收率
仅为60%左右。湿法炼锌浸出渣中大约80%的银以硫化物和单体形态存在,且90%以上的银分布在-200目可浮选粒级范围内,因此浸出渣可采用直接浮选法或预处理后再浮选的方法回收银。
湿法炼锌渣综合利用工艺现状及分析
锌渣综合利用的工艺方法选择主要取决于锌渣的性质,应根据浸出渣的具体性质,结合各个工厂的生产特点来选择合适的生产方法。本文重点阐述了锌湿法冶炼产出的铅银渣的处理工艺,提出了湿法炼锌渣综合利用回收有价金属的工艺
选择应注意和考虑的问题。
图1 锌焙砂浸出的常规工艺流程
图2 锌焙砂的热酸浸出流程
成分CaO Zn Zn 水Fe In Cu Pb SiO 2Ag/g·t -1铅银渣
13.13
7.55
3.05
7.63
0.01
0.28
5.04
18.68
513.12
表1 某厂铅银渣化学成分表(%)
文|杨建军1 丁 朝2,3 李永祥1 谢克强2,3 黄孟阳1 王侠前2,3
世界有色金属 2011年 第6期
44
自1979年开始,株洲冶炼厂[2]就开始采用“一粗二精三扫”的浮选工艺回收锌渣中的银,回收率达65%~70%,精矿含银约6000 g/t,尾矿含银约100 g/t。黄开国[3]发现一种可以在不腐蚀设备的中性条件下进行浮选的工艺,以Na
2
S作调整剂,丁基黄药和辅助捕收剂XY混合作捕收剂,RB为起泡剂,采用一次粗选、一次精选、一次扫选的闭路试验就可获得回收率79.44%的银精矿。
国外许多锌厂也采用浮选法从高温酸浸出渣中回收银、铅等金属获得成功。比利时巴伦电锌厂[4]的浮选法中有一步有效的热酸进出,可能会导致存在的铁钒化合物分解而释放出银,因此,该厂能生产含银24 kg/t的银精矿,银的回收率超过92%。铁酸盐中浸渣经酸分解后,铁矾渣和赤铁矿渣中Pb、Ag和Au都以分离的颗粒形式存在,芬兰赫尔辛基工业大学的J.Rastas等[5]用含水硫化物将它们转化成各自的硫化物,通过泡沫浮选,与铁及脉石分离,从而富集,进一步提高了银的回收率。
浮选法工艺流程短、生产费用低,不足之处是锌离子浓度高时导致浮选指标恶化,而且银的回收率与浸出渣的性质和生产厂家的特点有密切关系,如中浸渣中铁酸盐、铁矾化合物的大量存在,严重包裹银,使银回收率大幅度降低,且这种工艺方案只有在同时具备湿法炼锌与火法炼铅两种工艺流程的工厂中才能实现,回收成本比较高。
(2)硫脲浸出工艺
在弱氧化性条件下,银能溶解在含Fe3+和硫脲的稀酸中,形成可溶性阳离子络合物。硫脲法一般在pH=l~2,Fe3+或
H
2O
2
等氧化剂存在下浸出原料中的金、
银。
多数学者认为,Fe3+在浸出中起着
Technology & Equipment| 技术与装备
重要的作用[6]。缺少Fe3+,银便不能溶解
其中,卡可夫斯基等[7]的专门研究表明,
用硫脲从辉银矿中提取银是完全可能的,
比氰化法更有效、更迅速。从银精矿、烟
尘及一些二次资源(含银废料)中回收银
是有应用前景的[6]。
硫脲溶液浸出锌渣,浮选后的银精
矿最早见于上世纪70年代的比利时专利
[8],银浸出率达85.8%,然后用铝置换该
溶液可得含90.5% Ag的粗银。比利时老
山公司[9]和加拿大专利[10]都采用类似方
法处理锌浸出渣。加拿大电锌公司[9]发
现,在硫脲浓度低时便可以直接从未经
水洗的渣中浸出银,硫脲消耗量大大降
低。最后用活性炭吸附法提取浸出液中
的银,回收率可达84%。
中南工业大学黄开国[11]在实验过程
中发现,铜离子会与硫脲结合形成络合
物,而且硫脲自身具有氧化性,会导致硫
脲的实际消耗量大于理论消耗量。
硫脲浸出工艺浸出锌的浸出渣中银
有诸多优点,工艺简单,银提取率高,而
且,可以用锌、铁、铝等金属及活性炭等
方法从浸出液中回收银。但是硫脲自身
价格昂贵,不如氰化物稳定,而且消耗量
大,成本过高等因素使利用该法回收银
难以达到工业规模。
(3)氯盐浸出工艺
氯盐法原理是在酸性条件及氧化剂
存在下,使浸出渣中硫化银氧化。银离子
进人溶液并与溶液中的氯离子络合。
英国的J. Vinals[12]用HC1-CaCl
2
溶液从含铅铁矾的赤铁矿尾矿中浸出
回收金、银及铅,其浸出率都可达到
90%~95%。美国专利报道[13],CaCl
2
溶
液浸出需预先经H
2
SO
4
浸出类似锌渣的
铁酸盐废料,可回收93% Zn和98%Ag。
可见,用氯盐浸出锌渣,回收银的
同时也可回收铅,且回收率相当高,但因
为该反应要求介质的酸性强,氯盐浓度
高,反应温度高等,会严重腐蚀设备,其
经济上是否合理还有待考察。
2.火法富集
(1)回转窑挥发工艺
回转窑挥发工艺的侧重点是锌、铅、
铟的回收。在1000℃~1050℃条件下,
对铅银渣进行氧化挥发,使Zn、Pb离解
氧化成ZnO、PbO 烟尘,所得烟尘返回浸
出工序,达到回收锌的目的。
国内除云南驰宏锌锗股份公司采
用烟化炉挥发工艺回收渣中有价金属
外,多数冶炼厂,如广西华锡集团来宾
冶炼厂、温州冶炼厂等都采用回转窑挥
发其残锌。内蒙古赤峰松山区安凯有限
公司[14]采取回转窑挥发处理赤峰中色库
博红烨锌冶炼有限公司湿法炼锌工艺所
产生的铅银渣,Zn、Pb、In的回收率在
80%~90%,Ag的回收率在35%左右。
回转窑挥发工艺的最大缺点是,窑壁
粘结造成窑龄短,耐火材料消耗大,一般
半年到1年换1次窑砖,费用不菲。其次,
该工艺能耗高,作为回转窑燃料的焦炭价
格昂贵,投资太大,导致企业运行困难。
(2)烟化工艺
烟化炉处理湿法炼锌过程产生的浸
出渣工艺实质是还原挥发过程,原理和
回转窑挥发工艺基本相同,不同的是烟
某厂浮选处理车间
某厂浸出处理车间
某厂回转窑处理车间
某厂烟化炉处理车间
45 2011年 第6期世界有色金属
技术与装备 | Technology & Equipment
化法是在液相中(熔融状态)进行,而回转窑挥发工艺则是在固态下还原挥发锌。作为烟化工艺还原剂和炉燃料的煤是廉价消耗品,工艺所产出的金属氧化物也易处理,因此,相比起来,烟化工艺最易产出环保型渣,烟化工艺流程图见图3。据报道,韩国温山冶炼厂采用此工艺处理浸出渣。
(3)浸没熔炼工艺
前苏联的[15]熔池熔炼法是通过熔池两侧的风口向熔体喷入富氧空气,炉子操作复杂,而且产生的熔渣可能堵塞风口。澳大利亚研究人员[16]吸取熔池熔炼的优点,改进炉子,简单操作,提出浸没熔炼法。该法通过垂直插入渣层的喷枪向耐火材料砌筑的熔池中的熔体直接吹入空气、燃料和其他物质,同时产生强烈的搅动,在熔体中发生硫化、氧化,还原、造渣等物理化学变化的冶金过程,避免因停风而产生堵塞风口,其基本原理与熔池熔炼相同,将银及铜、铅等富集于冰铜或粗金属相中,使其与渣分离。
由于浸没熔炼法处理锌浸出渣具有更高的金属挥发率,如果配套后续处理烟尘、冰铜及粗金属等的设施,浸没熔炼法完全可以代替回转窑和浮选的方法。3.其他工艺
表3为国内某冶炼企业炼锌所产生
的铅银渣,物相检测表明:74.9% Pb 、50% Zn 及71% S 以硫酸盐形式存在,50.5% Ag 以硫化物形态存在。
根据铅银渣物料成分及物相组成,白银公司[17]研究所开发出一种新工艺,以纳米级ZnO 形态回收Zn ,以红丹形式回收Pb ,其工艺流程如图4所示。
这种新的氯化工艺
可综合回收铅银渣中的Pb 、Zn 、Fe 、Ag 四种金
属元素,经济效益显著。
总结
冶金渣中有价金属的回收,是当今环保的一大主题。近10年来,我国锌工业发展迅速,生产能力和产量持续大幅度增长,锌的产量和消费量已经跃居世界第一。锌冶炼厂每年都要产出大量的铅银渣。过去由于有价金属价格低迷,再加上缺乏经济、可行的回收途径,这些铅银渣未能得到有效处理,不仅浪费了大量资源,对环境也有一定污染,而且影响企业的经济效益。随着经济发展对有色金属需求的增长,一方面,由于铅锌矿原料供应困难、价格大幅上涨,导致铅锌冶炼企业产品价格与精矿价格差越来越小,竞争加剧,促使企业进一步挖掘铅银渣中银、铟、铅、锌等有价金属潜力,为综合回收金属提供了驱动力。另一方面,有价金属价格上涨,使铅银渣中银、铅等有价金属价值大幅提高,提高了铅银渣中有价金属综合回收的经济性。
本文所阐述的多种从锌浸出渣中回收有价金属的工艺方法各有优点与不足,各个企业应根据浸出渣中有价金属的含量、种类的不同,结合生产特点,选择合适的经济可行的综合回收工艺,实现清洁生产和可持续发展。
世
图3 浸出渣熔化烟化工艺流程图
[作者单位: 1 云南铜业(集团)有限公司; 2昆明理工大学冶金与能源工程学院; 3真空冶金国家工程实验室]
成分Zn 总Zn 水Pb Fe SO 42-Cu CaO MgO SiO 2S Ag 铅银渣(%)
7.5
3.06
8.5
5.8
29.95
0.02
3.69
0.14
18.78
13.94
0.02
表
3 某厂铅银渣化学成分表
图4 铅银渣综合回收利用新工艺流程
参考文献
[1] 华一新.有色冶金概论[M].北京:冶金工
业出版社.2007,112-113.[2] 株冶科技.1982,(2):1-12.
[3] 黄开国.从锌浸出渣中浮选回收银[J].中
南工业大学学报,1997,28(6):530-532.[4] J. E. Dutrizac, T. T. Chem. Mineral
Processing and Extractive Metallurgy, 1988, (97)180.
[5] 周洪武,徐子平.有色金属(冶炼部分),
1991,(6):18.
[6] Kakovskii I .A .et al. Thiocarbamide-Solvent for Gold and Silver, Fiz. Khim. Osn. Pererab. Miner. Syrya. 1982, 148.[7] D. M. Wyslouzil, R. S. Salter, Lead-Zn ’90,
Pro. Wold Symp. Metal .Environ. Control ll9th Tms Annu. Meet,1990. 87.[8] 比利时专利.NO .847441.[9] 株冶科技.1990,18 (3~4),29.[10] 加拿大专利.CA .1090141.[11] 黄开国.硫脲法从锌的酸浸渣中回收银[J].
中南工业大学学报.1998,29(6) :538-541.
[12] J. Vinals et al. Hydrometallurgy. 1991,
26(2), 179.[13] 美国专利.US .6602477.[14] 马永涛,王凤朝.铅银渣综合利用探讨[J].
中国有色冶金.2008,6(3):44-49.[15] BeTHble. Metal. 1985 (9), 7~13.[16] 傅作健.有色金属(冶炼部分).1988(1),
41.
[17] 赵宏.铅银渣综合利用新工艺探讨[J].有
色金属(冶炼部分),2001,(4):16-17.
世界有色金属 2011年 第6期
46
湿法炼锌浸出工序的工艺改进
湿法炼锌浸出工序的工艺改进 改进前的工艺 葫芦岛锌厂第三冶炼厂是1993年投产的湿袱炼锌「,其浸出工艺是以传统的湿法炼锌浸出理论为基础,采用两段连续浸出过程,空气搅拌。工艺疯程如图l o S 1改进前工艺流程 上述系统1993年投产以后,由于工艺、设备存在问题较多,因此给正常生产过程带来校大阻力。由于分级机、湿式球磨机、球磨后液泵及泵槽经常性积矿堵塞,使系统不能连续稳定生产。浸出槽排列纵向位置不合理,槽利用率低,浸出时间短,浸出率低,渣含锌高,“死槽”现象频繁发生。浓缩槽负荷沉重,不能连续运转,清理周期短,劳动强度大,劳动环境恶劣。渣处理系统负荷大,使正常渣平衡受到破坏。这样,浸出工序生产能力达不到设计要求,产品质量豚化。 2改进措施 2.1加料系焼工艺流程 针对焙砂f浆化分级系统不能适应生产要求的情况,主工艺过程取消上述流程,取代以焙砂一干式球磨机f 冲矿的方式加料,大大缓解了上述矛盾,使加料系统能够满足浸岀工序正常生产要求。改进后工艺流程如图2. 2.2浸出植排列繊向位置改进 浸出槽共有15个,其中中性浸岀槽7个(分成两套系统),酸性浸出槽5个,氧化槽3个。其排列位置如图3。各槽之间由溜槽连接,为了使矿浆能在溜槽中顺利流动,洛槽具有一定的倾斜度,因此各情岀液口呈阶梯型排列,而槽底处于同一水平线上。
图2改进后工艺流程 这样,使用同一风源搅拌的各槽,根据连通器原理, 其搅拌风管出口风压相同,即各槽内液柱(h)高度相 等,所以大号槽利用率低。而且大号槽内液面距槽 岀口高差校大,槽内液体要靠扬升器(风带液系统) 强制送出槽,扬升器风量大小由人工控制,所以各槽 内液柱高度极不均衡,液柱小的跑风严重,液柱大的 槽负荷大且经當出现"死槽”现象。导致了浸出生产 系统生产过程的一系列困难,达不到设计要求。据 此,对浸出槽纵向位置进行了调整。采用槽底垫高 和槽上口接高的方法,使槽底和槽上口处于同一高 差的阶梯型排列,保证各槽岀口到槽底距离相同。 并将一个氧化槽改为酸浸槽。改后其排列如图4O 这样调整以后,大大改善了生产系统原有状况, 其效果通过表1中的数据可以明显看岀。 S3改进前浸出槽位置择列 91项目 槽使用 效率 (% ) 中性浸出 时间(h) 験性浸出 时闻(h) 渣含锌(藍) 改进訶 50-60 0.3-0.5 0.6-1 0 25-2? ,改进后 的~知 10-1.5 19-22 同时,改进以后,浸出过程能够连续稳定进行。 因此大大提高了劳动效率,降低了劳动强度,改善了 劳动环境。 2.3中性浸出和中性浓绵液量的平衝 李淑艳等:湿法炼锌浸岀工序的工艺改进 酸化焙砂、烟尘 .厂, |干干球球卜 -------------- 中上清 送净化,i , |酸性M 岀| 屈,直酸上清? 送过滤 43 94改进后浸出梧位宣排列
加工工艺开题报告范文
加工工艺开题报告范文-CAL-FENGHAI.-(YICAI)-Company One1
加工工艺开题报告范文 当今市场变化迅速,企业必须不断应用创新技术以快速适应时时变化的市场环境。不断变化的环境归因于新一代的用户,他们可以在全球范围内购买产品。 变化迅速的市场环境不断淘汰以往的产品,大部分产品的性能很难跟上用户需求。在这种情况下,能够生产使顾客满意的低价位、高质量产品成了企业能否成功的关键所在。 面对如此紧迫的形势,企业为了在快速发展的全球市场中占有一席之地,必须采取相应的应对措施和手段:有的企业发展新方法、新技术,以期能够快速回应产品和市场趋势发展变化的需求;有的企业通过采用先进的生产制造方式(如精益生产、敏捷制造、大批量定制等)来缩短产品的开发周期,快速迎合用户和市场的需求;有的企业通过发展变型设计来快速推出不断变化的新产品,使企业获得更多的经济竞争优势 产品结构、设计过程的重组,以大规模生产的成本实现了用户化产品的批量化生产及大规模生产条件下的个性化,允许企业通过改进产品的某些零件来快速形成新型产品。因此,对产品结构及加工过程进行重新设计,生产更多满足现代化生产需求的产品,成为各个企业面临的一个巨大挑战。 “产品工艺流程重组设计”是在进行产品功能分析的基础上,对产品原有的结构和性能进行深入了解,细致研究产品现今的缺陷
和不足,并根据用户的具体设计要求,通过对已有的工艺流程进行重新设计,设计出质量好,使用寿命长的新产品,满足竞争激烈,日益变化的市场要求。 产品创新、重新改进和设计是企业赢得市场、获取利润、争取生存和发展空间的重要手段。 改进、重组设计后的机械产品主要具有以下几个特点: (1)互换性强,便于维修。 重组设计后的产品是在原有产品的基础上进行改进而成的,在使用功能和结构并没有太多不同,但是质量大大提高了,所以通用性很强,这大大简化产品的维护和互换,可提高产品的维修速度,节约修理费用,提高效率。 (2)质量高、成本低,不会对小批量和大批量加工产生影响。 在重新改进和设计中,在原有设计方法的基础上进行改进,省去一般产品开发设计过程中的重新选材,重新设计及其设计理论论证,节省了大量时间,大大提高了产品生产效率,节省了生产成本,提高了企业对市场的反应能力,加强了企业的竞争能力。由于设计是在原有设计的基础上,对很多加工过程进行改进,但没有破环原有的生产模式,保留了可小批量和大批量生产的优点,有“取其精华,去其糟唾”的意思,这是重新改进和设计的一大优点。 (3)有利于企业采用先进技术改造旧产品,开发新产品。 随着竞争的日益加剧,企业需要不断增强对市场需求的快速应变能力,靠传统的设计与制造方法显然是困难的。利用重新改进和
2016-2017年泵体的铸造工艺设计分析 研究报告
泵体的铸造工艺设计 2016-2017年泵体的铸造工艺设计分析研究报告
目录 引言 (1) 第1章绪论 (2) 1.1 概述 (2) 1.2国内铸造行业的现状及发展趋势 (2) 1.3发达国家铸造行业的现状及发展趋势 (2) 1.4本课题的研究内容 (2) 第2章零件铸造工艺分析 (4) 2.1 零件基本信息 (4) 2.2 泵体铸件结构分析 (4) 2.3材料成分要求 (5) 2.4铸造工艺参数的确定 (5) 第3章铸造工艺方案设计...................................................................... (9) 3.1工艺方案的确定 (9) 3.2分型面的选择 (9) 3.3砂箱设计初步设计 (10) 3.4砂芯设计 (11) 第4章浇注系统的的设计及计算 (14) 4.1 浇注系统的设计原则 (14) 4.2 灰铸铁浇注系统尺寸的确定 (14) 4.3直浇道窝设计 (16) 4.4 浇口杯的设计 (16) 4.5冒口设计计算 (17) 4.6 出气孔 (17) 第5章铸件三维实体造型 (18) 5.1 计算机技术在铸造生产中的应用 (18) 5.2 华铸CAE的概述 (18) 5.3 华铸CAE对泵体铸造过程温度场的模拟 (19) 5.4 泵体铸造工艺优化 (21) 第6章铸造工艺装备设计 (23) 6.1模样 (23) 6.2模板的设计 (23) 6.3 芯盒的设计 (23) 6.4砂箱设计 (24) 结论与展望 (25)
泵体的铸造工艺设计 致谢 (27) 参考文献 (28) 附录A: 主要参考文献摘要 (29) 附录B: 英文原文及翻译 (31)
湿法炼锌渣的无害化处理及资源综合回收.pdf
湿法炼锌渣的无害化处理及资源综合回收 长沙有色冶金设计研究院有限公司 - 张乐如 -
CONTENTS 目录 概述 1 湿法炼锌工艺及其渣的种类 2 国内外湿法炼锌渣的处理方法 3 我国湿法炼锌渣处理的现状 4 湿法炼锌渣无害化处理方法选择5
第一部分概述
?由于环境保护意识日益增强,国家的环保政策日益严格,渣处理已经成为制约湿法炼锌的瓶颈; ?湿法炼锌有多种不同工艺,产出的渣有多种,其化学成分和化学性质各不相同。因为湿法炼锌渣属于危险废物的范围,这类危险废物产出量大,不可能也不允许长期堆存,必须进行无害化处理; ?无害化处理的方法主要有两大类,一类是火法处理,另一类是填埋。现在对危险废物填埋也作出了非常严格的规定,不仅对填埋设施提出了很高的要求,对危险废物的化学成分提出了严格的控制限值。浸出渣即使进行预处理也无法达到控制限值的要求,例如浸出渣中的锌及其化合物(以总锌计)的控制限值为75mg/L是不可能达到的,即使反复洗涤和压滤,也只能达到1g/L左右。
危险废物允许进入填埋区的控制限值 序号项目稳定化控制限值(mg/L) 1 有机汞0.001 2 汞及其化合物(以总汞计)0.25 3 铅(以总铅计) 5 4 镉(以总镉计)0.50 5 总铬12 6 六价铬 2.50 7 铜及其化合物(以总铜计)75 8 锌及其化合物(以总铍计)75 9 铍及其化合物(以总铍计)0.20 10 钡及其化合物(以总钡计)150 11 镍及其化合物(以总镍计)15 12 砷及其化合物(以总砷计) 2.5 13 无机氟化物(不包括氟化钙)100 14 氰化物物(以CN计) 5 危险废物填埋场要求防渗漏、防腐蚀,还需设有预处理站,建设投资很大,预处理的运行成本很高,这就增加了湿法炼锌的投资和运行成本。因此研究湿法炼锌渣的无害化处理及综合回收是非常重要的课题。
工艺过程的统计分析一
工艺过程的统计分析 一:概述 在生产实际中,影响加工精度的原始误差很多,这些原始误差往往使综合地交错在一起对加工精度产生综合影响的,且其中不少原始误差的影响往往带有随机性。对于一个受多个随机性质原始误差影响的工艺系统,只有用概率统计的方法来进行分析,才能得出正确的、符合实际的结果。 (一)系统性误差与随机性误差 系统性误差可分为常值系统性误差和变值系统性误差两种。在顺序加工一批工件中,其大小和方向皆不变的误差,称为常值系统性误差。例如,铰刀直径大小的误差,测量仪器的一次对零误差等。在顺序加工一批工件中,其大小和方向遵循某一规律变化的误差,称为变值系统性误差。例如,由于刀具的磨损引起的加工误差,机床和刀具或工件的受热变形引起的加工误差等。显然,常值系统性误差与加工顺序无关,而变值系统性误差则与加工顺序有关。 在顺序加工一批工件中,有些误差的大小和方向使无规则变化着的,这些误差称为随机误差。例如加工余量不均匀、材料硬度不均匀、夹紧力时大时小等原因引起的 加工误差。 对于常值系统性误差,若能掌握其大小和方向,就可以通过调整消除;对于变值系统性误差,若能掌握其大小和方向随时间变化的规律,则可通过自动补偿消除;唯队随机性误差,只能缩小它们的变动范围,而不可能完全消除。由概率论与数理统计血可知,随机性误差的统计规律可用它的概率分布表示。 (二)机械制造中常见的误差分布规律
偏态 分布 在用试切法车削轴径或孔径时,由于操作者为了尽量避免产生不 可修复的废品,主观地(而不是随机地)使轴颈加工得宁大勿小, 则它们得尺寸误差就呈偏态分布。 机械加工误差 分布规律 (三)正态分布 1.正态分布的数学模型、特征参数和特殊点机械加工 中,工件的尺寸误差是由很多相互独立的随机误差综合作 用的结果,如果其中没有一个随机误差是起决定作用的, 则加工后工件的尺寸将呈正态分布,其密度方程中,有两 个特征参数:一个算术平均值只影响曲线的位置,而不影 响曲线的形状;另一个均方根偏差(标准差)σ 只影响曲 线的形状,而不影响曲线的位置,均方根偏差愈大,曲线 愈平坦,尺寸就愈分散,精度就愈差。因此,均方根偏差 反映了机床加工精度的高低,算术平均值反映了机床调整 位置的不同。 2.标准正态分布 算术平均值为 0,均方根偏差为 1 的正态分布为标准正态分布。 3.工件尺寸再某区间内的概率 生产上感兴趣的往往不是工件为某一尺寸的概率是多大,而是加工工件尺寸落在某一 区间(x1≤x≤x2)内的概率是多大,如右图示。通过分析可知,非标准正态分布概率 密度函数的积分,经标准化变换后,可用标准正态分布概率密度函数的积分表示,为 了计算的需要,可制作一个标准化正态分布概率密度函数的积分表。通过计算可知, 正态分布的分散范围为 这就是工程上经常用到的“±3σ 原则”,或称“6σ 原 则”。
生产工艺设计作业指导书模板
志涛生产作业指导书 1.材料搭配加工要求 1、实木面框拼接料宽度≤80MM,长度超过1米的拉档和玻璃门框不允许使用独根材料; 2、拼板应无明显色差,无明显胶线; 3、砂光后无跳痕、无焦黑痕、无蓝斑、无横茬;平整光滑; 4、板材厚度公差+0.2MM,不得有大头小身; 5、有虫孔的木料不可使用; 6、面框配料加工厚度尺寸+0.5~+0.2MM;组框后需铣型边的面框料宽度尺寸放3MM 加工余量,面框深度尺寸+0.5~0.2MM; 7、人造板封边的配料厚度尺寸为人造板厚度尺寸+0.6~0.2MM; 8、直边牙板厚度、宽度尺寸为+0.4MM,曲边牙板宽度放2MM加工余量,与脚耳相配的牙板宽度为+0.2MM; 9、需铣型、仿型、车型无方身的脚配料放3MM加工余量; 10、零件必须方、正、平、直; 11、显木纹油漆产品胶拼部件颜色必须相近,木纹必须对称; 12、显木纹油漆产品所有零件不许有明显木材缺陷,外表部件无腐朽、变色、死节、开裂、过大黑线等缺陷,内部零件可允许存在不影响外观的轻微缺陷,但必须修补合格后下发; 13、不显木纹油漆产品用材要求; (1)不影响产品结构强度和外观的木材缺陷可以使用,但死节直径不大于20MM,不存在贯通裂缝;
(2)雕刻、型边、企口等外表部位不应有死节、髓芯、开裂等缺陷; 14、平面中含有圆弧面线条的部件,圆弧面应凹进1MM,以免砂平圆弧面。 2.木皮拼接及胶贴加工要求 1、木皮含水率控制在8-10%; 2、所有薄片厚度公差控制在+0.05MM~-0.05MM; 3、拼花、拼缝不大于0.2MM; 4、面板薄片材质要求: (1)无腐朽、死节、变色、蓝斑、开裂、鱼鳞斑等缺陷; (2)无横向连贯木纹、节子; (3)同一板面纹理相近、弦向、径向纹按要求拼接; (4)树瘤切片必须遵循对称、花纹一致原则,除非不易辨别之花纹可混用在同一面板上; (5)镶嵌,插入拼接时斜拼,同一面板镶嵌,插入尺寸、颜色需一致; 5、芯板除端部外,允许有变色、不脱落死节。芯板拼缝不大于0.5MM,无叠芯现象; 6、不可见之部位或面板背板材质允许一定缺陷,但不允许大的空洞,也可纵向接,但不可同缝; 7、门板、抽头等有对称要求的要对称拼接; 8、表面平整、光滑,无透光现象; 9、不允许叠芯; 10、45度拼角偏离不大于1MM; 11、胶贴木片不得有脱胶、鼓泡、离芯、迭芯、透胶现象; 12、胶贴表面不得有胶块、凹痕、异物、排骨印;
电子产品工艺设计报告
电子产品工艺设计 题目:六管超外差式收音机 班级:08电子信息工程(应电方向) 院系:应用技术学院 姓名:学号: 实验地点:应用技术学院综合实验室 指导老师:王悦善职称:讲师 成绩: ( 2011年6月2日 )
目录 目录 (1) 六管超外差式收音机的工艺设计 (2) 普通装配导线加工 (5) 电子产品装配准备工艺 (6) 电子产品基板手工焊接工艺 (9) 电子产品整机装配工艺 (13) 电子产品整机调试工艺 (15) 电子产品整机检验工艺 (17)
题目:六管超外差式收音机的工艺设计 一、设计任务与要求 1.认识常用的电阻电容等电子元器件 2.掌握收音机的工作原理以及收音机的调试方法 3.掌握电子线路故障的排除方法 4.掌握电子产品工艺设计的流程和要点 二、方案设计与论证 对于学生做电子工艺实习来说,主要是学习怎样填写工艺文件,学习电子工艺的基本流程,因此对于焊接方法因考虑经济、方便、对焊接技术要求不高的方案,下面就对一些方案进行讨论: 方案一、手工焊接 手工焊接适合于产品试制、电子产品的小批量生产、电子产品的调试与维修以及某些不适合自动焊接的场合。该方式对焊接工具要求简单,焊接步骤简单,容易掌握,主要适合电子元件管脚不多的情况。 方案二、浸焊 浸焊的特点:操作简单,无漏焊现象,生产效率高;但容易造成虚焊等缺陷,需要补焊修正焊点;焊槽温度掌握不当时,会导致印制板起翘、变形,元器件损坏。该方案对焊接工具要求较高,对于学生学习来说不经济。 方案三、波峰焊接 波峰焊的特点:生产效率高,最适应单面印制电路板的大批量地焊接;焊接的温度、时间、焊料及焊剂等的用量,均能得到较完善的控制。但波峰焊容易造成焊点桥接的现象,需要补焊修正。该方案对焊接工具要求较高,对于学生学习来说不经济。方案四、再流焊(回流焊) 该技术主要用于贴片元器件的焊接上。被焊接的元器件受到的热冲击小,不会因过热造成元器件的损坏;无桥接缺陷,焊点的质量较高。该方案对焊接工具要求较高,对于学生学习来说不经济,焊接技术也不是很快能掌握的。 方案五、接触焊接(无锡焊接) 该方案对电缆接接线柱等场合比较实用,对于焊接收音机没有实际价值,对学生来说也不经济。 由上面的分析可知,手工焊接对学生来说比较经济,对焊接技术要求不高,因此我们可以采用改方案。 三、总原理图及元器件清单 1.总原理图
湿法炼锌中沸腾焙烧过程的研究现状与进展
湿法炼锌中沸腾焙烧过程的研究现状与进展 现代炼锌方法分为火法和湿法两大类,世界上大部分的锌都是从硫化锌精矿 中提取出来的。无论火法还是湿法,一般都需预先焙烧或烧结,脱除大部分硫和其他杂质,以满足下道工序的要求。目前,在国内应用较成熟的焙烧技术是硫化锌精矿的粉状沸腾焙烧技术。 沸腾焙烧又称流态化焙烧,是众多焙烧方法中的一种。所谓的沸腾焙烧是指将所要处理的固体破碎,研磨成细粉,增加固体与气体的接触面积,缩短颗粒内部的传递和反应距离。自下而上流经这些粉料的气体,在达到一定速度时,会将固体颗粒悬浮起来,使之不断运动,犹如沸腾的水,故称沸腾焙烧。沸腾焙烧的基础是固体流态化,用沸腾焙烧炉焙烧锌精矿,炉内热容量大且均匀,温差小,料粒与空气接触表面积大,反应速度快,强度高,传热传质效率高,使焙烧过程大大强化,产品质量稳定生产率高。下面主要叙述在湿法炼锌中沸腾焙烧过程的发展和应用现状。 1 湿法炼锌中沸腾焙烧过程的发展和应用现状 1.1 在制粒焙烧方面的研究情况 李芳、张建彬,张起梅等[1]在锌精矿制粒沸腾焙烧中指出随着原料供应日趋紧张、精矿质量下降,发展沸腾焙烧技术,对提高锌冶炼金属回收率具有重要的意义。他们进行了锌精矿制粒焙烧的试验研究,重点分析了制粒粘合剂的选择和制粒焙砂质量控制。在沸腾焙烧试验中,针对焙砂质量及其影响因素诸如焙烧温度、原料粒度、过剩空气系数和物料在炉内的停留时间等进行了研究;另外通过适当减少加料量,使相应提高过剩空气系数,延长停留时间,Pb的脱除有所降低,同时s脱除效果亦有明显提高。最后他们得出结论:制粒沸腾焙烧提高了炉子的处理能力,床处理能力达到30.4 t/m2·d,炉温控制得当,风量均匀,焙砂质量可以达到Pb<1.0%,Cd<0.05%,S<1%的控制要求。沸腾炉操作温度可控制在1140~1180℃,比现有粉状物料焙烧操作温度提高60~80℃。 靳澍清、刘丽珍、吉正元等[2]在锌精矿造粒、焙烧试验研究中采用几种粘结剂进行造粒试验,对成粒矿进行静态焙烧试验,提出造粒和焙烧试验工艺条件及参数,粒矿进行静态焙烧试验,为大规模的生产奠定了一定的基础。 张瑜、李志勇、吴志平等[3]在锌精矿制粒沸腾焙烧新工艺的应用与改进中介绍了锌精矿制粒沸腾焙烧新工艺的工业化生产应用与技术改进情况,同时阐述了所取得的成果及存
工艺流程 (解析版)
原创精品资源学科网独家享有版权,侵权必究! 1 专题16 工艺流程 【母题来源】2019年高考新课标Ⅰ卷 【母题题文】硼酸(H 3BO 3)是一种重要的化工原料,广泛应用于玻璃、医药、肥料等工艺。一种以硼镁矿(含Mg 2B 2O 5·H 2O 、SiO 2及少量Fe 2O 3、Al 2O 3)为原料生产硼酸及轻质氧化镁的工艺流程如下: 回答下列问题: (1)在95 ℃“溶浸”硼镁矿粉,产生的气体在“吸收”中反应的化学方程式为_________。 (2)“滤渣1”的主要成分有_________。为检验“过滤1”后的滤液中是否含有Fe 3+离子,可选用的 化学试剂是_________。 (3)根据H 3BO 3的解离反应:H 3BO 3+H 2O 垐?噲?H ++B(OH)?4,K a =5.81×10?10,可判断H 3BO 3是______ 酸;在“过滤2”前,将溶液pH 调节至3.5,目的是_______________。 (4)在“沉镁”中生成Mg(OH)2·MgCO 3沉淀的离子方程式为__________,母液经加热后可返回____ _______工序循环使用。由碱式碳酸镁制备轻质氧化镁的方法是_________。 【参考答案】(1)NH 4HCO 3+NH 3 (NH 4)2CO 3 (2)SiO 2、Fe 2O 3、Al 2O 3 KSCN (3)一元弱 转化为H 3BO 3,促进析出 (4)2Mg 2++323CO -+2H 2O Mg(OH)2·MgCO 3↓+23HCO - (或2Mg 2++223CO -+H 2O Mg(OH)2·MgCO 3↓+CO 2↑) 溶浸 高温焙烧
湿法电解锌工艺设计设计流程选择概述
湿法电解锌工艺流程选择概述 1.。1 工艺流程选择 根据原料成份采用常规的工艺流程,技术成熟可靠,劳动环境好,有较好的经济效益,同时综合回收铜、镉、钴等伴生有价金属。工艺流程特点如下: (1)挥发窑产出的氧化锌烟尘一般含气氟、氯、砷、锑杂质,且含有较高的有机物,影响湿法炼锌工艺,所以通常氧化锌烟尘需先进多膛焙烧脱除以上杂质。 (2)氧化锌烟尘和焙砂需分别进行浸出,浸出渣采用回转窑挥发处理,所产氧化锌烟尘送多膛焙烧炉处理。 (3)氧化锌烟尘浸出液返焙砂系统,经中性浸出浓密后,上清液送净液车间处理,净液采用三段净化工艺流程。 (4)净化后液送往电解车间进行电解。产出阴极锌片经熔铸后得锌锭成品。 (5)净液产出的铜镉渣和钴渣进行综合回收(或外卖)。 1.6.2 工艺流程简述 焙砂经中浸、酸浸两段浸出、浓密、过滤,得到中浸上清液及酸浸渣。酸浸渣视含银品位进行银的回收后送回转窑挥发处理得氧化锌,经脱氟、氯,然后进行单独浸出,浸液与焙砂系统的浸出液混合后送净液。回转窑渣送渣场堆存。产出的中浸上清液经三段净化,即第一段用锌粉除铜镉;第二段用锌粉和锑盐高温除钴;第三段再用锌粉除复溶的镉,以保证新液的质量,所得新液送电解。电解采用传统的电解沉积工艺,用人工剥离锌片,剥下的锌片送熔铸,产出锌锭。
采用上述工艺流程的理由:主要是该工艺流程基建投资省,易于上马,建设周期短、见效快、效益高。这在株冶后10万吨电锌扩建、广西、、等多家企业的实践中,已得到充分证实和肯定。 对净液工艺的选择,目前国外湿法炼锌净液流程的发展趋势,主要是溶液深度净化。采用先冷后热的净液流程,为保证净液质量,设置三段净化,当第二段净化质量合格时,也可以不进行第三段净化,直接送电解。该流程稳妥可靠,净化质量高,能满足生产0#锌和1#锌的新液质量要求。 作业制度,拟采用连续操作,国西北冶、株冶等都有生产经验。与间断操作相比,可大减少设备的容积,减少设备数量,相应可减少厂房建筑面积,故可大幅度降低基建投资。 1..3 综合利用及环境保护 浸出渣可根据含银品位高低进行银的回收后再送回转窑处理,所得氧化锌经脱氟、氯后进入氧化锌浸出系统,进一步回收锌、铟等有价金属。 净液所得铜镉渣经低酸浸出后,所得铜渣可作为炼铜原料出售。 浸出液经锌粉置换,所得贫镉液含锌很高,返回锌浸出车间,所得海绵镉进一步处理后,获得最终产品镉锭出售。 净液所得钴渣,经酸洗脱锌后根据含钴品位再考虑是否回收钴,暂时先堆存(或外卖)。 熔铸所得浮渣,其粗粒可返回熔化或作生产锌粉用。处理所得氧化锌可作为生产硫酸锌或氯化锌的原料,根据需求而定。 各湿法炼锌车间的污酸、污水,经中和沉处理后,可达到国家工业排放标准。
湿法炼锌副产铜渣的综合利用
湿法炼锌副产铜渣的综合利用 鲁兴武,邵传兵,易超,李俞良 (西北矿冶研究院 冶金新材料研究所,甘肃白银 730900) 摘要:研究了湿法炼锌副产铜渣的综合利用新工艺。最佳浸出条件为:液固比10∶1,浸出温度80 ℃,浸出剂(硫酸)浓度3.5 mol/L ,浸出时间8 h 。浸出液含铜浓度达到30~45 g/L ,铜浸出率可以达到98%以上。经萃取、洗涤、三级错流反萃后,反萃液中铜浓度达到45~50 g/L ,电积后可以得到标准阴极铜。 关键词:铜渣;综合利用;萃取;锌湿法冶金 中图分类号:TF811;TF813 文献标识码:A 文章编号:1007-7545(2012)06-0000-00 Comprehensive Utilization of Copper Slag By-product in Zinc Hydrometallurgy LU Xing-wu ,SHAO Chuan-bing ,YI Chao ,LI Yu-liang (Institute of Metallurgy New Materials of Northwest Institute of Mining and Metallurgy, Baiyin 730900, Gansu, China) Abstracts: The new comprehensive utilization technology of copper slag by-product in zinc hydrometallurgy was investigated. The optimal leaching conditions including ratio of liquid to solid of 10∶1, leaching temperature of 80 ℃, leaching agent (sulfuric acid) concentration of 3.5 mol/L, and leaching time of 8 h. The copper concentration in lixivium reaches 30~45 g/L, and the copper leaching rate is higher than 98%. The copper concentration in stripping solution reaches 45~50 g/L after extraction, washing and three-stage cross-flow stripping of copper. The cathode copper can be produced with electrowinning process. Key words: copper slag; comprehensive utilization; extraction; zinc hydrometallurgy 2010年全国锌产量为516.4万t ,其中湿法炼锌的产量占锌总产量的70%以上[1]。对于年产10万t 的湿法炼锌企业,每年处理净化系统铜镉渣产生的铜渣约1 kt ,仅有50%左右的铜渣被卖到铜冶炼企业,进入粗铜冶炼,其中的锌不能得到有效回收,剩余的富铜渣被堆放到渣场,造成了二次资源的闲置和环境污染。因此开展铜渣综合回收技术研究具有现实意义[2-4]。 1 试验原料和方法 所用铜渣为某湿法炼锌企业铜镉渣处理后得到的副产品[5],主要化学成分(%):Cu 40.0、Zn 5.0、Cd 0.8、Pb 3.0、Fe 2O 3 1.5、O 7.5、其它42.2。采用图1所示流程产出标准阴极铜。 图1原则工艺流程图 Fig.1 Principle flow chart of copper slag comprehensive recovering 收稿日期:2011-12-13 作者简介:鲁兴武(1985-),男,甘肃武威人,大学,助理工程师. doi :10.3969/j.issn.1007-7545.2012.06.006
湿法炼锌
1 概述 1.1 国内外发展 锌冶炼方法分湿法和火法两大类,火法炼锌有横罐炼锌、竖罐炼锌和密闭鼓风炉炼锌。横罐炼锌由于环境污染严重,劳动条件恶劣,已基本淘汰。竖罐炼锌也存在环境污染、能耗较高、不利于综合回收的缺点,也逐步被其他方法所取代。密闭鼓风炉炼锌又称帝国熔炼法(简称LSP),是由英国帝国熔炼公司开发出来的一种铅锌冶炼方法,20世界60年代开始应用于工业化生产,目前在全世界有20座炉,锌产量占世界锌总产量的12%左右。由于该方法对原料适应性强,可以冶炼铅锌混合精矿,能耗较小,建设肉孜相对较少,并且很好地解决了火法冶炼的环境污染问题,具有较强的生命力和发展前景。湿法炼锌是当今炼锌的主要方法,其产量占世界锌产量的80%以上,湿法炼锌可分为常规法、黄钾铁矾法、针铁矿法、赤铁矿法,采用较多的是前三种方法。前面提到的湿法炼锌工艺,都需要采用氧化脱硫,一般是沸腾焙烧,焙烧产出的氧化锌焙砂送湿法炼锌系统生产电锌。另外还有全湿法炼锌工艺,即硫化锌精矿直接加压氧浸工艺。加压氧气浸出技术是加拿大谢利特·哥顿公司在20世纪50年代开发的,开始用于金属硫化精矿的处理,回收镍、钴,共建有6座工厂,其中4座回收镍,2座回收钴。70年代加压氧浸被用于硫化锌精矿处理。炼锌技术的发展方向主要是减少污染,降低消耗,节约成本和提高有价金属回收率等,由此推动炼锌技术的不断进步,创造出多种多样的炼锌技术和工艺流程,可供我们合理选择。
我国是世界上锌生产和消费大国,从1996年至今其产量稳居世界第一。2014年我国锌产量582.7万t,占当年全球锌总产量1315万t的43.2%。这是基于我国的镀锌钢板产量差不多占世界半壁江山、年产成百亿支锌锰电池大规模出口、制造业对黄铜等各类锌基合金需求旺盛、建筑业的高速发展使氧化锌涂料消费量急增等需求因素带动了锌产业的快速发展。另外我国锌资源较为丰富,其储量及储量基础仅次于澳大利亚,居世界第二位。2014年美国地质调查局数据显示,全球锌资源储量达25000万t,其中澳大利亚6400万t,中国4300万t,秘鲁2400万t。2014年世界前十大产锌国,中国第一、澳大利亚产锌154万t,局第二位,其余依次为秘鲁132万t,美国83万t,印度72万t,墨西哥68万t。根据国家统计局资料,2014年我国自产精矿540,9万t,这位锌冶金产业提供了有力支撑。但锌产量远不能满足国内需求,依然需要大量进口。据中国海关统计,2014年进口锌精矿实物220万t,进口精锌57万t。 2 流程图
产品设计分析报告格式
产品设计分析报告 姓名费雨婷 班级工业设计09-2班学号 22090163 报告日期 2011/11/27 中国矿业大学徐海学院
一、产品名称 二、外形图
三、结构分析 1、爆炸图
2、产品工作原理 踏步机有两大主要部件“电机”和“踏板”,之间主要通过皮带和齿轮是之紧密连接在一起,电机通过皮带带动齿轮转动,齿轮带动踏板前后上下移动,从而让使用者达成跑步的效果。踏步机“踏板”部分由支架,油压缓冲杆组成,通过踏板的上下左右的移动,和油压缓冲杆的缓冲,让使用者达到健身效果。此种为国内市场普遍的一种踏步机。了解踏步机的工作原理就可知道:保护好“电机”和“踏板”对减少踏步机的故障有及其重要的意义。 3、零部件信息
四、总体分析 踏步机一般可以从以下三大特性来了解,分别是运动频幅,油压缓冲杆的耐性,踏板强度以及其他特性。踏步机是由电动机,一组踏板和油压缓冲杆组成的。健身爱好者在使用踏步机之前,先通入电源,开启踏步机。再根据自身体能情况,调节踏步机电机转动频率,从而改变踏步机的运动频幅,确保安全使用,达到健身效果。 运动频幅指踏步机踏板一分钟之内上下的次数,一般用次数/分钟(m)为单位来衡量和踏板上下左右移动的运动幅度。提供正确的运动频幅可以降低踏步运动对腿关节造成的负面影响。 油压缓冲杆的耐性是指油压缓冲杆的耐用程度。踏步机的两支油压缓冲杆可以消除运动时膝盖关节的摩擦,并且更有益于筋骨的伸展,可调整您需要的运动强度,将脚踏在脚踏板前方,就可增加运动强度。让您在不知不觉中燃烧脂肪,特别锻炼腰、腹、腿等部位,塑造完美曲线。 踏板强度是指踏步机踏板的耐用性。踏板的耐用性越好,使用寿命越长。更能保护好使用者人身的安全,以免发生事故。
湿法炼锌的浸出过程
湿法炼锌的浸出过程 一、锌焙烧矿的浸出目的与浸出工艺流程 (一)锌焙烧矿浸出的目的 湿法炼锌浸出过程,是以稀硫酸溶液(主要是锌电解过程产生的废电解液)作溶剂,将含锌原料中的有价金属溶解进入溶液的过程。其原料中除锌外,一般还含有铁、铜、镉、钴、镍、砷、锑及稀有金属等元素。在浸出过程中,除锌进入溶液外,金属杂质也不同程度地溶解而随锌一起进入溶液。这些杂质会对锌电积过程产生不良影响,因此在送电积以前必须把有害杂质尽可能除去。在浸出过程中应尽量利用水解沉淀方法将部分杂质(如铁、砷、锑等)除去,以减轻溶液净化的负担。 浸出过程的目的是将原料中的锌尽可能完全溶解进入溶液中,并在浸出终了阶段采取措施,除去部分铁、硅、砷、锑、锗等有害杂质,同时得到沉降速度快、过滤性能好、易于液固分离的浸出矿浆。 浸出使用的锌原料主要有硫化锌精矿(如在氧压浸出时)或硫化锌精矿经过焙烧产出的焙烧矿、氧化锌粉与含锌烟尘以及氧化锌矿等。其中焙烧矿是湿法炼锌浸出过程的主要原料,它是由ZnO和其他金属氧化物、脉石等组成的细颗粒物料。焙烧矿的化学成分和物相组成对浸出过程所产生溶液的质量及金属回收率均有很大影响。 (二)焙烧矿浸出的工艺流程 浸出过程在整个湿法炼锌的生产过程中起着重要的作用。生产实践表明,湿法炼锌的各项技术经济指标,在很大程度上决定于浸出所选择的工艺流程和操作过程中所控制的技术条件。因此,对浸出工艺流程的选择非常重要。 为了达到上述目的,大多数湿法炼锌厂都采用连续多段浸出流程,即第一段为中性浸出,第二段为酸性或热酸浸出。通常将锌焙烧矿采用第一段中性浸出、
第二段酸性浸出、酸浸渣用火法处理的工艺流程称为常规浸出流程,其典型工艺原则流程见图1。 图1湿法炼锌常规浸出流程 常规浸出流程是将锌焙烧矿与废电解液混合经湿法球磨之后,加入中性浸出槽中,控制浸出过程终点溶液的PH值为5.0~5.2。在此阶段,焙烧矿中的ZnO只有一部分溶解,甚至有的工厂中性浸出阶段锌的浸出率只有20%左右。此时有大量过剩的锌焙砂存在,以保证浸出过程迅速达到终点。这样,即使那些在酸性浸出过程中溶解了的杂质(主要是Fe、AS、Sb)也将发生中和沉淀反应,不至于进入溶液中。因此中性浸出的目的,除了使部分锌溶解外,另一个重要目的是保证锌与其他杂质很好地分离。 由于在中性浸出过程中加入了大量过剩的焙砂矿,许多锌没有溶解而进入渣中,故中性浸出的浓缩底流还必须再进行酸性浸出。酸性浸出的目的是尽量保证焙砂中的锌更完全地溶解,同时也要避免大量杂质溶解。所以终点酸度一般控制在1~5g/L。虽然经过了上述两次浸出过程,所得的浸出渣含锌仍有20%左右。这是由于锌焙砂中有部分锌以铁酸锌(ZnFe2O4)的形态存在,且即使焙砂中残硫小于或等于1%,也还有少量的锌以ZnS形态存在。这些形态的锌在上述两次浸出条件下是不溶解的,与其他不溶解的杂质一道进入渣中。这种含锌高的浸出渣不能废弃,一般用火法冶金将锌还原挥发出来与其他组分分离,然后将收集到的粗ZnO粉进一步用湿法处理。
湿法炼锌
湿法炼锌是一个流程较长的冶金过程而且工艺比较成熟,包括锌精矿的焙烧、浸出、净化、电解、阴极锌的熔铸等过程.论文首先叙述了锌精矿种类,沸腾炉的焙烧过程,常规浸出各种影响因素及电解沉积锌的经济技术指标,为后续章节信息系统的开发奠定了基础.该文主要研究锌精矿的焙烧、浸出、电解三个过程,首先建立了锌精矿的配矿信息系统.该系统能提供精确的配矿和符合生产条件下配矿成本最低化,系统中优化了十种矿样的45种组合,而且全部数据输入和输出都使用数据库操作.然后根据锌精矿沸腾炉硫态化焙烧原理建立了热力学模型的信息系统,根据物料平衡和热平衡建立方程组来确定焙烧矿以及烟气的成分.由于焙烧过程的时间变化性,该热力学模型无法全部描述的内在机制等,使得结果存在着一定的偏差,但此模型能够较好地拟合焙烧过程的主要趋势.最后,在锌常规浸出和过电解沉积锌过程中设计了BP神经网络来预测浸出过程中的浸出率、浸出渣率、浸出液上清率、新液合格率、渣含水以及电解过程中的电流效率等因素.网络采用了近30组的训练样本,样本数据范围大,网络的训练误差精度可以达到10<-5>.新的嫁接BP神经网络预测适应性较广、精度较高.可以实现离线预测,并且为在线操作提供了参数指标.湿法炼锌信息系统的程序采用了Visual Basic6.0和Matlab两种语言混合编写,系统的数据库采用Microsoft Access创建和维 护.Visual Basic6.0编程语言简单实用,可视化功能强大,具有严密的封装性,而且还提供许多ActiveX控件;Matlab编程语言不仅有较强的矩阵运算功能和绘图能力,而且带有12个功能强大的工具箱;Microsoft Access编写的数据库具有随时对数据进行修改和补充.程序运用Matlab解方程组的功能和神经网络工具箱,建立沸腾炉焙烧物粒平衡信息系统和锌常规浸出和锌电积神经网络预测信息系统两大系统,再把解方程过程中BP神经网络可视化接到VB的封装体系中.所涉及到的BP神经网络函数都以脚本文件的形式存在,这样既减少程序的复杂性又提高了程序的运行效率……
产品设计方案论证报告(模板)
型号名称 产品设计方案论证报告 拟制: 审核: 批准: 中国电子科技集团公司第二十四研究所 年月日
(型号名称 3号黑体) 产品设计方案论证报告 1 线路设计(5号黑体) 1.1 引言(5号黑体) 瞬时中频频率(IIFM)测量组件是频率探测系统的关键部件之一,该组件完成对前端混频后的中频信号的频率的测量,直接决定了频率探测系统理论上的测频速度,精度和测量噪声指标。 1.2 项目来源及开发的意义(5号黑体) (含用途和使用范围。示例如下。格式要求,5号宋体,1.25倍行距) ××××××××××××××××××××××××××××××××××××××××××××××××。 1.3 国内外同类产品大发展动向及技术水平(5号黑体) (示例如下。格式要求,5号宋体,1.25倍行距) 考察瞬时中频测频(IIFM)组件技术在最近二十年间发展动向,传统的模拟电路鉴频器和各种比较、积分式测频电路由于受线性度较差,响应较慢,受温度漂移、噪声干扰等外部影响较难消除等固有问题的困扰,已经被逐渐淘汰,同时,随着高速数字技术的发展,多种基于现代数字系统的频率测量方法速度已经大大提高,远超过了模拟方式提供的响应速度,而且线性度高,温漂、噪声干扰小,已成为当今IIFM技术的主流。 国外IIFM的报道具体指标多数比较模糊,代表性的有美国《Journal of Electronic Defense》2002年报道的使用IIFM技术的IFM接收机,中频DC~30MHz,分辨率1KHz,测频时间约100nS。《Microwave Division》杂志2007年的报道,中频工作频段2~18GHz,测频时间最大400nS。国内相关研究近年较多,如2002年航天科工25所的报道,中频24~25MHz,测频时间1us,精度0.1Hz。2006年《电子测量技术》的报道,中频50~950MHz,测频时间最小400nS,误差约0.3MHz。 1.4 项目合同的技术指标要求(5号黑体) 1.工作频率70MHz±4MHz ,10.2M±1MHz 2.测频精度2KHz,1KHz 3.测频速度200nS 4.工作温度范围-40o C~85o C 1.5 样品解剖情况(5号黑体) (使用于仿制产品,正向设计产品略。示例如下。格式要求,5号宋体,1.25倍行距)a)样品电路原理图、基本工作原理及关键元器件的主要参数指标; b)样品主要技术指标(规范值,实测数据); c)芯片照片、面积、版图极限尺寸(最小线宽、最小间距)及封装特点; d)样品电路工艺设计、线路设计、版图设计特点及其分析。 1.6 产品电路设计和版图设计方案(5号黑体) a)功能框图和详细单元电路图及工作原理; 1.功能框图:电路功能框图如下图所示。
包装工艺设计课程设计报告
1.绪论 1.1设计的目的与意义 香皂是日常生活中必不可少的洗涤护理用品,香皂质地细腻、去污力强,是肥皂的改良品,本设计就是基于方便、卫生、环保的设计理念进行的设计,而且防护性能好,经济效益高,此设计的市场定位应该适合大部分人群,尤其主要是面向那些较常家居的人群。因此,工艺品包装应当提出具有个性化的包装设计方法,能够使产品在众多同类品牌中脱颖而出,首先从外观上吸引消费者的眼球,进而产生购买欲望;其次通过改良的包装结构,让产品的包装充分循环利用,将具有个性化的设计理念贯穿始终;最后,达到提升品牌形象,扩大产品的销售和影响力的目的并实施具有个性化的包装设计。本设计采用了一层用塑料制成的包装,解决了以前香皂保质期不长,消费者不放心的问题,且卫生、方便。 1.2香皂的市场调查 1963年舒肤佳除菌香皂首次在美国上市(属于宝洁公司的品牌之一),此后畅销于全世界几十个国家和地区。因其显著的抗菌功效,在国际上,舒肤佳品牌已获得多家国际医学专业团体的认可。在中国,舒肤佳的除菌功效也获得了中华医学会的验证,实验证明,舒肤佳能有效去除和抑制可能引起皮肤感染和汗臭的细菌。香皂附加成本增高和国外品牌占主导地位的现状,直接导致了香皂普遍售价高昂这一结果。由于国外香皂注重包装、设计、广告投入、整体策划,使得香皂生产的附加成本增高。因此,其上市产品的价格一开始就定得很高。而且通过调查,我们发现消费者心理注重包装设计精美大方、杀菌止痒功能好、美容功能好、气味清新、泡沫丰富、清洁性好、皂体硬度适中、外观保持性好、品种多样化、广告宣传到位。 2.产品的物性及流通环境的分析 2.1产品的物性 香皂以脂肪酸钠和其他表面活性剂为主要原料,添加品质改良剂和外观改良剂,经过加工成型后制成的产品。香皂的主要成分是脂肪酸钠和表面活性剂,此外还含有1%—1.5%的香精,一般用牛油、羊油和椰子油为原料,制皂前经过精炼、脱色、脱臭等精制处理。香皂使用时会沾上水,进而水分被香皂吸收。使用后,香皂里面的水分要挥发,但由于进入香皂的水分分布不均以及香皂各部分接触空气的程度不同,会导致水分的挥发程度不同,进而致使香皂出现裂痕。如果长期存放,香皂原料中含有的不饱和脂肪酸会被氧、光、微生物等氧化,有时会出现酸败现象,香皂中的水分也会散失,影响使用效果。舒肤佳香皂含有抗菌活性成份迪保肤,在清洗过程中能有效去除皮肤表面的暂留微生物。清洗后,舒肤佳留在皮肤上的抗菌活性成分迪保肤能有效抑制皮肤表面细菌的再生。
湿法冶锌工艺流程.
湿法冶锌工艺流程 概述:湿法炼锌是当今世界最主要的炼锌方法,其产量占世界总锌产量的85%以上。近期世界新建和扩建的生产能力均采用湿法炼锌工艺。湿法炼锌技术发展很快,主要表现在:硫化锌精矿的直接氧压浸出;硫化锌精矿的常压富氧直接浸出;设备大型化,高效化;浸出渣综合回收及无害化处理;工艺过程自动控制系统等几个方面。湿法炼锌是用稀硫酸(即废电解液)浸出锌焙烧矿得硫酸锌溶液,经净化后用电积的方法将锌从溶液中提取出来。当前,湿法炼锌具有生产规模大、能耗较低、劳动条件较好、易于实现机械化和自动化等优点在工业上占主导地位,锌总产量的80~85%来自湿法炼锌。 锌焙砂的浸出 湿法冶锌的浸出是以稀硫酸溶液作为溶剂,控制适当的酸度、温度和压力条件,将含锌物料(如锌焙砂、锌烟尘、锌氧化矿、锌浸出渣、硫化锌精矿等)中的新华无溶解撑硫酸锌进入溶液,不容固体形成残渣的过程。浸出所得的混合矿浆在经浓缩、过滤将溶液与残渣分离。 锌焙砂浸出的原则工艺流程: 锌焙砂浸出是用稀硫酸溶液去溶解砂浸中的氧化锌。作为溶剂的硫酸溶液实际上是来自锌电解车间的废电解液。 锌焙砂浸出分为中心浸出和酸性浸出的两个阶段,常规浸出流程采用一段中性浸出和一段酸性浸出或两端中性浸出的复浸出流程。锌焙砂首先用来自酸性浸出阶段的溶液进行中性浸出。中性浸出实际是用锌焙砂来中和酸性浸出溶液中的游离酸,控制一定的酸度(Ph=5.2~5.4),用水解法除去溶解的杂质(主要是Fe、Al、Si、As、Sb),得到的中心溶液经净化后送去电积回收锌。 中性浸出仅有少部分ZnO溶解,锌的浸出率为75%~80%,因此浸出残渣中还含有大量的锌,必须用含酸度较大的废电解液(含100g/L左右的游离酸)进行二次酸性浸出。酸性浸出的目的是使浸出渣中的锌尽可能完全溶解,进一步提高锌的浸出率;同时还要得到过滤性良好的矿浆,以利于下一步进行固液分离。为避免大量杂质同时溶解,终点酸度一般控制在H2SO4浓度为1~5g/L。 经过两段浸出,锌的浸出率为85%~90%,渣中锌含量约为20%。为了提高