曲轴连杆颈轴线位置误差的测量研究
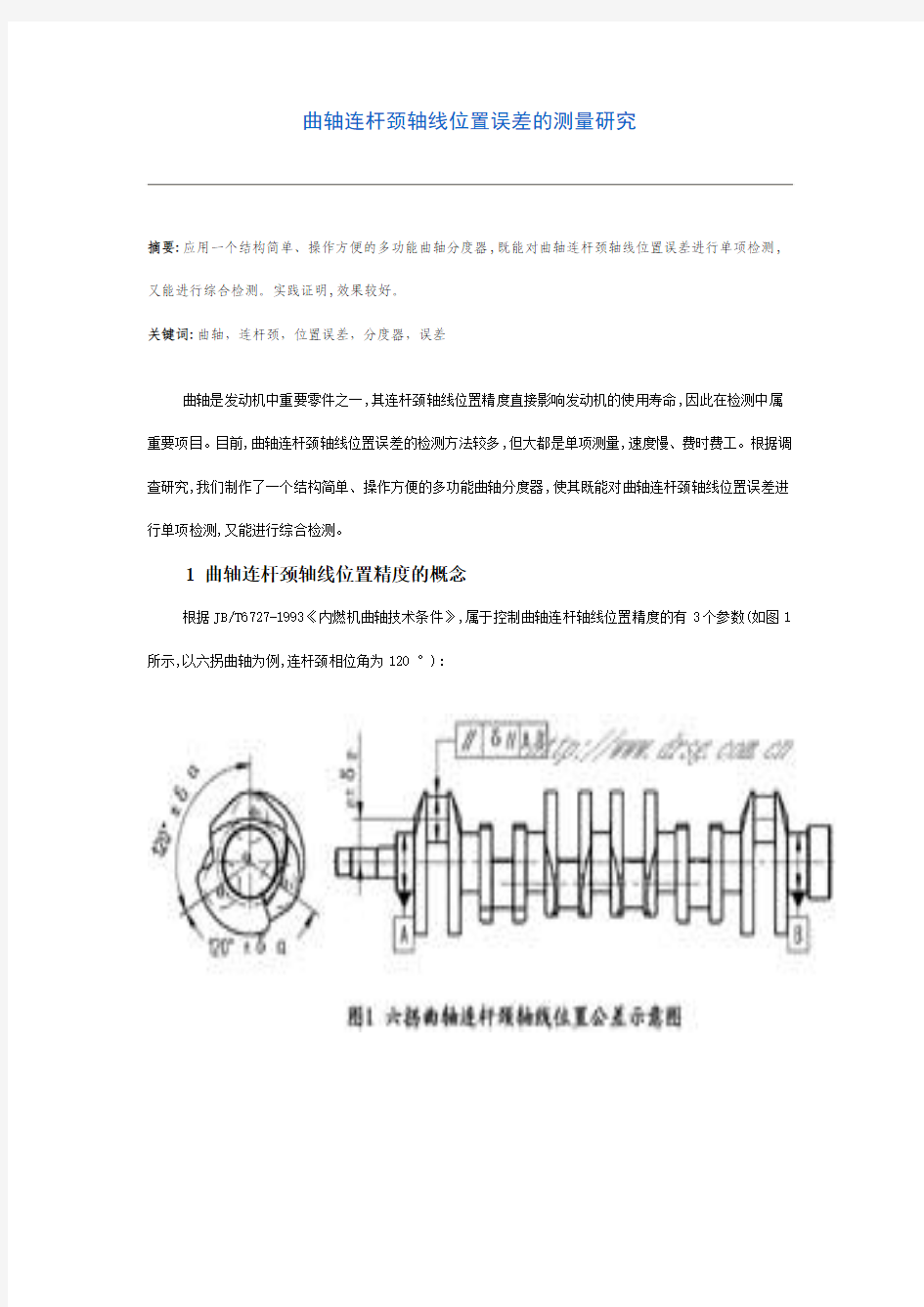

曲轴连杆颈轴线位置误差的测量研究
摘要:应用一个结构简单、操作方便的多功能曲轴分度器,既能对曲轴连杆颈轴线位置误差进行单项检测,又能进行综合检测。实践证明,效果较好。
关键词:曲轴,连杆颈,位置误差,分度器,误差
曲轴是发动机中重要零件之一,其连杆颈轴线位置精度直接影响发动机的使用寿命,因此在检测中属重要项目。目前,曲轴连杆颈轴线位置误差的检测方法较多,但大都是单项测量,速度慢、费时费工。根据调查研究,我们制作了一个结构简单、操作方便的多功能曲轴分度器,使其既能对曲轴连杆颈轴线位置误差进行单项检测,又能进行综合检测。
1 曲轴连杆颈轴线位置精度的概念
根据JB/T6727-1993《内燃机曲轴技术条件》,属于控制曲轴连杆轴线位置精度的有3个参数(如图1所示,以六拐曲轴为例,连杆颈相位角为120 °):
1、在垂直于主轴颈轴线平面内,连杆颈中心到主轴颈中心距离e (以下简称回转半径)公差±δe.
2、在垂直于主轴颈轴线平面内,各连杆颈轴线和主轴颈轴线组成的平面对第一连杆颈轴线和主轴颈轴线组成的平面的角度120 °(以下简称曲柄夹角)的公差±δα.
3、在主轴颈轴线方向,有连杆颈轴线对两端主轴颈公共轴线的平行度公差δ//.
图2所示的是曲轴连杆颈轴线位置公差带的几何框图。由图中可以看出:
1、第一连杆颈(基准)中心O1被限制在O1O线方向和以O1为中心的±δe线段内。
2、其它连杆颈中心(O1 、O3 ) ,分别被限制在各自的由±δe和±δα所组成的小扇形公差带内。
3、连杆颈轴线对两端主轴颈公共轴线的平行度公差带,为一直径是δ//,且平行于公共轴线的圆柱体。反映在横向图上,则是一个直径是δ//值的圆。
4、对于第一连杆颈(基准)轴线,也同样存在平行度误差,所以也存在(3)中所述的投影圆,但由于在建立公差带横向图时所选择的面是过去第一连杆颈轴线中点的截面,因此反映在图中O1的位置域为一线段。
2 多功能曲轴分度器
从分析曲轴连杆颈轴线公差带的几何框图可知,如果能实现曲轴置于平台上的几种特定角度的准确定位,就可以实现连杆颈轴线三个位置参数误差的精确测定。本文推荐一种结构简单、操作方便的多功能曲轴分度器,其结构如图3。其中零件2角度板为本分度器的功能件,由两个错位30°的正六边形组成,可以在件1上旋转,也可以用螺钉(件6)使之紧固。
使用时,将分度器固定于曲轴前端齿轮轴颈上。
将曲轴两端基准主轴颈架在平台上的两个等高V形块上,利用带架百分表、高度尺就可以进行各位置误
差的测量。这是因为角度板与曲轴定位后,利用角度板的12个平面中,总有1 个正矩形体正置于平台,因而可用百分表调平,实现曲轴30°整数倍的12个特定角的定位。
3 回转半径的检测
将被测连杆颈中心与主轴颈中心连线调成与平台平行,再用百分表将角度板上的一个平面与平台调整平行后,将角度板紧固。如图4所示,用百分表将被测轴颈先后调成上、下垂直位置(通过调整分度器相应角度而实现)。用高度尺测出对应高度a ,a′。
则回转半径e′=(a-a′)/2
评定时,|e′-e|≤δe为合格。
4 曲柄夹角的检测
从分析曲轴连杆颈轴线位置公差带的几何框图
可知:只有当被测角度要素处于与平台平行时,才能
最大限度地排除其它参数误差的影响,达到检测精度
高的目的。因此,对于不同分度的曲轴,检测时应使公
共平面相对于平台处于不同角度。以六拐曲轴(120°
分度)为例作一介绍(如图5所示):
先将公共平面、角度板上一平面调成与平台平
行后,将角度板紧固。通过分度器将公共平面调成与平台成下60°位置,用百分表测量被测轴颈O2(在水平位置)表面最高位置,然后再将曲轴调成上60°位置,继续对被测轴颈进行上述测量,百分表所反映的差值Δa的半值,即为一、二连杆颈角度误差的线性值α1-2。
评定时,Δa≤2esinδα为合格。
5 曲柄夹
角与回转半
径的综合检
测
(1)Δα-Δe依次检测
按曲柄夹角检测法调整公共平面与角度板的相
对位置,先进行各曲柄夹角误差的检测,并经判定合
格后,再进行回转半径的检测。
对第一曲柄(基准)回转半径,按前面所述回转半
径检测方法进行。对于其它连杆颈回转半径的检测,
可将公共平面先后调成上下30°位置(被测O2处于上、下两垂直位置)后
测定(如图6 所示),计算与评定办法与前面所述回转半径检测法相同。
这里需要说明的是,被测轴颈由于存在分度误差,测量其回转半径
时,不一定真正处于最高或最低位置,但因分度误差在公差范围内(≤2
0′)时,如图7所示,设其偏角为20′时,则Δa=(1-cosΔα)e=(1-cos2 0′)e=0.17×10-4e.对于一般中小型曲轴,e=60左右。则Δa=0.001 。相对于Δe来说,Δa值很小,可以忽略。可见本检测方法已有足够精度,且方法简捷。
(2)坐标测定法
将公共平面与角度板一平面调整与平台平行后
进行。
1)将公共平面调成上垂直位置(如图8a):分别
测出被测轴颈o2、o3表面最高点高度值m2、m3后,将
工件旋转180°,调成下垂直状态(如图8b),并测出m
2′、m3′。
则:Δm2=|m2′-m2|
Δm3=|m3′-m3|
2)将公共平面调成左平行位置(如图9a):分别测出被测轴颈O2、O3表面最高点高度值 n2、n3后,将工件旋转180°,调成右平行状态(如图9b),并测出 n2′、n 3′。
则:Δn2=|n2′-n2|
Δn3=|n3′-n3|
3)计算出各被测轴颈回转半径和曲柄夹角:
被测轴颈O2:e2=[(Δn2)2+(Δm22)]1/2/2
α1-2=90°+arctg(Δm2/Δn2)
被测轴颈O3:e3=[(Δn3)2+(Δm32)]1/2/2
α1-3=90°+arctg(Δm3/Δn3)
6 连杆颈轴线平行度误差的检测
将曲轴被测连杆颈先后置于垂直、水平两个位
置,用百分表沿轴向测量轴颈两端处(距离为L,让开
过渡圆角)的最高表面,分别记下两种位置下的百分
表的差值Δy,Δx(如图10所示)。
则L长度内平行度误差为:
f//=[(Δy)2+(Δx)2]1/2
必要时,应排除连杆颈圆柱度误差f//的影响,这时:
f//′=[(Δy)2+(Δx)2]1/2±f//
其中当f//增大方向与百分表测量值增大方向一致时,上式取“-”号,反之取“+”号。
7 误差分析
应用多功能曲轴分度器的特定角度测量曲轴连杆颈位置误差
时,用分度器内孔固定曲轴齿轮轴颈,曲轴齿轮轴颈轴线与分度器
上正六边形中心存在同轴度误差Δ,下面分析Δ对测量结果的影
响:
如图11所示,OO1=Δ,将正六边形上的一平面置于水平位置
(实线部分),O为中心,然后将曲轴绕O1转过一定角度∠OO1O2,使正
六边形相邻一面置于水平位置(虚线部分),O2为中心,很显然: ∠OO1O2=60°,因此Δ对测量结果没有影响。
8 结束语
(1)本文是以六拐曲轴(连杆颈相位角为120°)为例介绍曲轴连杆颈轴线位置误差的新型检测方法,对于连杆颈相位角为90°和180°的曲轴,测量和评定方法与此相同。
(2)应用多功能曲轴分度器,可方便快捷地测量连杆颈轴线位置误差,并能保证足够的检测精度。
发动机曲轴连杆实习报告范文
发动机曲轴连杆实习报告范文 实习是大学进入社会前理论与实际结合的最好的锻炼机会,也是大学生到从业者一个非常好的过度阶段,更是大学生培养自身工作能力的磨刀石,作为一名刚刚从学校毕业的大学生,能否在实习过程中掌握好实习内容,培养好工作能力,显的尤为重要。 发动机曲轴连杆实习报告一 今日实习目的地:南车柴油机二分厂 实习车间:曲轴加工车间 在王工的带领下,进入了曲轴加工车间,首先,向我们介绍了曲轴的用途,以及各个部位特点,如何加工而成、 曲轴是活塞式发动机中最重要、承受负荷最大的零件之一。其主要功用是将活塞的往复运动通过连杆变成回转运动,即把燃料燃烧的爆发力通过活塞、连杆转变成扭矩输送出去做功,同时还带动发动机本身的配气机构和相关系统工作 曲轴一般由主轴颈,连杆轴颈、曲柄、平衡块、前端和后端等组成。一个主轴颈、一个连杆轴颈和一个曲柄组成了一个曲拐,曲轴的曲拐数目等于气缸数(直列式发动机);V型发动机曲轴的曲拐数等于气缸数的一半。主轴颈是曲轴的支承部分,通过主轴承支承在曲轴箱的主轴承座中。主轴承的数目不仅与发动机气缸数目有关,还取决于曲轴的支承方式。曲轴的支承方式一般有
两种,一种是全支承曲轴,另一种是非全支承曲轴。曲轴的形状和曲拐相对位置(即曲拐的布置)取决于气缸数、气缸排列和发动机的发火顺序。 轴典型加工工艺 曲轴的典型加工过程如下 铣端面打中心孔粗精车所有主轴颈及周轴颈铣角向定位面粗精车所有连杆颈粗磨第四主轴颈 车平衡块钻直斜油孔半精磨 1、主轴径7车铣割滚压精磨所有主轴颈及周轴颈淬火回火探伤精磨第四主轴颈喷丸钻工艺孔 两端孔的加工精磨所有连杆颈动平衡抛光所有轴颈清洗防锈 铣键槽 曲轴加工第一工序铣端面、钻中心孔。通常以两端主轴颈的外圆表面和中间主轴颈的轴肩为粗基准,这样钻出的中心孔可保证曲轴加工时径向和轴向余量均匀。 径向定位主要以中心线为基准,还可以两端主轴颈外圆为精基准。轴向定位用曲轴一段的端面或轴肩。角度定位一般用法兰盘端面上的定位销孔或曲柄臂上铣出的定位平台。采用不同的加工工艺方法和设备,定位基准的选用亦有不同。
三坐标测量位置度的方法及注意事项
摘要:位置度检测是机动车零部件检测中经常进行的一项常规检验。所谓“位置度”是指对被评价要素的实际位置对理想位置变动量的指标进行限制。在进行位置度检测时首先要很好地理解和消化图纸的要求,在理解的基础上选择合适的基准。位置度的检测就是相对于这些基准,它的定位尺寸为理论尺寸。 关键词:三坐标;位置度;方法 一、位置度的三坐标测量方法 1.1 计算被测要素的理论位置 ①根据不同零部件的功能要求,位置度公差分为给定一个方向、给定两个方向和任意方向三种,可以根据基准体系及确定被测要素的理论正确位置的两个理论正确尺寸的方向选择适当的投影面,如XY平面、XZ平面、YZ平面。②根据投影面和图纸要求正确计算被测要素在适当投影面的理论位置。 1.2 根据零部件建立合适的坐标系。在PC-DMIS软件中,可以把基准用于建立零件坐标系,也可以使用合适的测量元素建立零件坐标系,建立坐标的元素和基准元素可以分开。 1.3 测量被测元素和基准元素。在被测元素和基准元素取点拟合时,最好使用自动程序进行,以减少手动检测的误差。 1.4 位置度的评价。①在PC-DMIS软件中,位置度的评价可以直接点击位置度图标。②在位置度评价对话框中包含两个页面,特征控制框和高级,首先根据图纸要求设置相应的基准元素,在基准元素编辑窗口中只会出现在编辑当前光标位置以上的基准特征,如图1所示。 ③基准元素设置完成,回到特征控制框选择被测元素,设置基准,输入位置度公差。④在位置度评价的对话框中选择高级,在此对话框中可以设置特征控制框尺寸的信息输出方式和分析选项。如图2的对话框,在标称值一栏中手动键入被测要素的理论位置值,点击评价。 1.5 在报告文本中刷新就可以看到所评价的位置度结果。 二、三坐标测量位置度的注意事项
平行度误差的测量
实验四 测量平行度误差 一、实验目的 熟悉用水平仪测量垂直平面内的直线度误差的方法,和用作图法求直线度误差的方法。 二、实验内容 1、测量面对面平行度误差; 2、测量线对面平行度误差; 3、测量线对线平行度误差。 三、实验方法和步骤 1、测量面对面平行度误差 公差要求是测量面相对于基准平面的平行度误差。基准平面用平板体现,如图4-1所示。 测量时,双手推拉表架在平板上缓慢地作前后滑动,用百分表或千分表在被测平面内滑过,找到指示表读数的最大值和最小值。 图4-1 面对面平行度误差测量示意图 被测平面对基准平面的平行度误差可按公式计算为: f //=Mb Ma l 1 2 1 mm 2、测量线对面平行度误差 公差要求是测量孔的轴线相对于基准平面的平行度误差。需要用心轴模拟被测要素,将心轴装于孔内,形成稳定接触,基准平面用精密平板体现,如图4-2所示。 测量时,双手推拉表架在平板上缓慢地作前后滑动,当百分表或千分表从心轴上素线滑过,找到指示表指针转动的往复点(极限点)后,停止滑动,进行读数。 在被测心轴上确定两个测点a 、b ,设二测点距离为12,指示表在二测点的读数分别
图4-2 线对面平行度误差测量示意图 为Ma 、Mb ,若被测要素长度为l 1,那么,被测孔对基准平面的平行度误差可按比例折算得到。计算公式为: f //=Mb Ma l 12 1 mm 3、测量线对线平行度误差 公差要求是测量孔的轴线相对于基准孔的轴线的平行度误差。需要用心轴模拟被测要素和基准要素,将两根心轴装于基准孔和被测孔内,形成稳定接触,如图4-3所示。 测量前,要先找正基准要素,找正基准心轴上素线与平板工作面平行。实验时用一对等高支承支承基准心轴,就认为找正好了。也可以用一个固定支承和一个可调支承支承基准心轴,双手推拉表架在平板上缓慢地作前后滑动,调整可调支承,当指示表在基准心轴上素线左右两端的读数相同时,就认为找正好了。 图4-3 线对线平行度误差测量示意图 测量方法与计算公式与线对面平行度误差的测量方法与计算公式相同。
实验2 用游标卡尺和角尺测量位置度误差
实验二用游标卡尺和角尺测量位置度误差 一、实验目的 1.了解用游标卡尺和角尺测量位置度误差的方法及位置度误差的数据处理方法 2.加深对位置度误差的理解 二、实验内容 用游标卡尺、角尺、量块和圆柱销等测量孔轴线的位置度误差。 三、测量原理 图1所示零件上有一个四圆柱孔组,给出位置度公差Ф0.2mm。该四圆柱孔组的定位尺寸在水平方向为L1,在垂直方向为L2。按图1的标注,四圆柱孔组的位置度公差与定位尺寸及四圆柱孔的尺寸之间遵守独立原则。因此,只要各圆柱孔的实际轴线同时位于位置度公差带内和尺寸公差带内就算合格。测量分下列两个步骤进行。 1.测量各圆柱孔的位置度误差 图2为测量示意图。利用角尺、量块和圆柱销(以下简称销)建立以第1孔的孔心为原点,1、2两孔的孔心连线为x轴测量坐标系统,并由此确定量块组的尺寸L5和L6。然后,在此基础上,按图2所示用游标卡尺测出a1、a2、a3、a4等四个尺寸(尺寸a1可用游标卡尺测量)各孔轴线的坐标值按下列关系式计算: fx1=0 fy1=0 fx2=(a1-d)-L3 fy2=δ fx3=a3-d -L3 fy3=a2-d-L4+δ fx4=0 fy4=a4-d-L4 式中:fxi——第i孔实际轴线在x方向上的偏差; fyi——第i孔实际轴线在y方向上的偏差; d——检验所用销的大径 δ=L6-L5 已知:L3=76mm,L4=122mm,d=30mm 图1 图二
根据各孔的偏差坐标值,就可以利用作图法来求解各孔的位置度误差是否合格(见后面附例)。 四、测量步骤 1.测量各圆柱孔的位置度误差 (1)将销插入圆柱孔中,再将工件平放在平板上 (2)将角尺内侧的一边与1、2两孔中的销接触,并反复试选量块组尺寸L5和L6,放入1的y方向上与销接触,同时又能与角尺内侧的另一面紧贴。这样,测量坐标系统才能建立。记录 量块组的尺寸L5和L6,算出Δ值。 (3)用0.02mm读数的游标卡尺按图2所示分别测出a1、a2、a3、a4等四个尺寸。 (4)算出各孔轴线偏差的坐标值。 (5)作图求解各孔轴线的位置度误差,并判断合格与否。 图3 图4 示例:假设按前述步骤1的顺序,已求出图1所示各孔轴线偏差的坐标值如下: (mm) 用作图法求解位置度误差。 1.先在坐标纸上以孔心为圆心,以Ф0.2mm乘以放大倍数M为直径,M为作图时的放大倍
位置度测量方法
1.基准﹔ 2.理論位置值﹔ 3.位置度公差 三、位置度公差帶 位置度公差帶是一以理論位置為中心對稱的區域。
四、位置度的標注與測量方法
3﹑以中心线左边第二根端子为例﹐测出实际尺寸D1(0.82)﹑D2(1.02)﹐根据位置定义﹐ DE=abs(Da-Dt) =abs{(D1+D2)/2-Dt)} =abs[(0.85+1.00)/2-0.90}] =0.025<0.05 其中﹐DE表示实际偏差 abs表示绝对值 Da表示实际位置尺寸 Dt表示理论位置尺寸﹐对于不同的端子﹐它们的理论位置尺寸是不测量时测量者须自行计算 DE=abs(Da-Dt) =abs{(D1+D2)/2-Dt)} =abs{[(d1+Dt)+(Dt-d2)]/2-Dt)} =abs[(d1-d2)/2]
(二)﹑IDE44P垂直位置度的标注与测量 如图﹐IDE44P端子在垂直方向上具有以下特点﹕排数少(只有两排)﹐每排端多(达22PIN)﹐长度值为端子材厚值﹐对于不同的端子﹐其值差异极小﹐因此我们排端子和下排端子分别看成两个整体。下面以下排端子为例介绍其测量方法。 一、测出角柱垂直方向上Φ1.70的实际尺寸﹐然后置中归零﹔ 二、往下偏移2.00﹐然后归零﹔ 三、
为基准﹐用于控制端子锡脚与与PCB板的配合﹐现其位置度公差0.18﹔另一个是端子域的位置度﹐此位置度以KEY为基准﹐用于控制端子接触区域与对插件的配合﹐现其度公差0.3。对于第一个位置度﹐其标注方式已统一﹔对于第二个位置度﹐有如下两种式﹕
以上两种标注方式中﹐第一种直接对124根端子接触区域一一测量其位置度﹐由接触区域是包在主体内部﹐若采用这种方式﹐测量繁琐困难﹔对于第二种测量方式﹐子是下料成型﹐且插在主体插槽中﹐插槽控制了端子的平面度﹐因此只须控制KEY相POST的位置度与端子锡脚相对POST的位置度﹐相应地也就控制了端子接触区域相对 水平位置度Th和垂直位置度Tv后﹐須再驗証其是否滿足公式Th2+Tv2≦0.152。
10第十单元平行度误差、平面度误差的测量
第十单元平行度误差、平面度误差的测量 一、单项选择题 1.被测平面必须位于距离为公差值t且平行于基准平面的两平行平面之间的区域的公差是 D A线对线的平行度公差 B.线对面的平行度公差 C.面对线的平行度公差 D.面对面的平行度公差 2可调千斤顶适用检查 B A.平行度公差 B.平面度公差 C.直线度公差 D.圆度公差 3测量平面度误差需要()可调千斤顶建立测量基面。 B A.2个 B.3个 C.4个 D.5个 4涂色法检测大平面时如果基准块在平面上滑动后平面中间呈现亮点,说明工件B A.表面平整 B.中间凸起 C.中间凹陷 D无法判别 5.下列()公差带形状不是距离为公差值t的两平行平面内区域。B A.平面度 B任意方向的线对线的平行度 C.给定方向的线的倾斜度 D面对面的平行度 6公差带形状可能是直径为公差值t,且平行于基准轴线的圆柱面内的区域。()A A.线对线的平行度 B线对面的平行度 C.面对线的平行度 D.面对面的平行度 7根据如图回答下列问题
第7题图 (1)测量项目是 B A线对线的平行度 B线对面的平行度 C.面对线的平行度 D.面对面的平行度 (2)图中被测要素是(),基准要素是() BA A.轮廓要素 B.中心要素 (3)测量时需用心轴模拟体现的是 C A.被测孔的素线 B.基准孔的轴线 C.被测孔的轴线 D基准平面 (4)测量此几何误差最后的数据处理公式是()。 A 8.根据图示回答下列问题 (1)测量项目是A A线对线的平行度
B线对面的平行度 C.面对线的平行度 D.面对面的平行度 (2)图中被测要素是 (),基准要素是()BB A轮廓要素 B.中心要素 (3)测量时需用心轴模拟体现的是 B A.被测孔的素线 B.基准孔的轴线 C.被测孔的轴线 D.基准孔的素线 (4)测量此几何误差最后的数据处理公式是 B 第8题图 二、是非选择题 X1.平行度是限制被测实际要素对基准要素在垂直方向上变动量的一项指标。() X2面对面的平行度公差带是距离为公差值t且平行于基准直线的两平行平面之间的区域 3测量面对面平行度误差常采用打表法 4.面对线平行度误差的测量可以采用心轴来模拟基准轴线,用支座支承心轴,采用打表法测量。 X5.平行度公差带是距离为公差值t且平行于基准的两平行平面之间的区域。( 6.平面度是指平面加工后实际形状的不平程度。 X7.平面度的公差带是距离为公差值t的两平行直线之间的区域。 X8.平行度分线对线,线对面、面对线、面对面等情况,但它们测量时的数据处理方法都一样。 9钳工车间对于较小平面的平面度误差通常采用刀口形直尺通过透光法来检测10.刮削平面的平面度误差生产现场多用涂色法做合格性检验。 三、分析、计算题 量公 如图所示,测量该零件平行度误差时采用心轴模拟孔的轴线。已知该零件孔的长
形位公差检测方法
一、轴径 在单件小批生产中,中低精度轴径的实际尺寸通常用卡尺、千分尺、专用量表等普通计量器具进行检测;在大批量生产中,多用光滑极限量规判断轴的实际尺寸和形状误差是否合格;;高精度的轴径常用机械式测微仪、电动式测微仪或光学仪器进行比较测量,用立式光学计测量轴径是最常用的测量方法。 二、孔径 单件小批生产通常用卡尺、内径千分尺、内径规、内径摇表、内测卡规等普通量具、通用量仪;大批量生产多用光滑极限量规;高精度深孔和精密孔等的测量常用内径百分表(千分表)或卧式测长仪(也叫万能测长仪)测量,用小孔内视镜、反射内视镜等检测小孔径,用电子深度卡尺测量细孔(细孔专用)。 三、长度、厚度 长度尺寸一般用卡尺、千分尺、专用量表、测长仪、比测仪、高度仪、气动量仪等;厚度尺寸一般用塞尺、间隙片结合卡尺、千分尺、高度尺、量规;壁厚尺寸可使用超声波测厚仪或壁厚千分尺来检测管类、薄壁件等的厚度,用膜厚计、涂层测厚计检测刀片或其他零件涂镀层的厚度;用偏心检查器检测偏心距值,用半径规检测圆弧角半径值,用螺距规检测螺距尺寸值,用孔距卡尺测量孔距尺寸。 四、表面粗糙度 借助放大镜、比较显微镜等用表面粗糙度比较样块直接进行比较;用光切显微镜(又称为双管显微镜测量用车、铣、刨等加工方法完成的金属平面或外圆表面;用干涉显微镜(如双光束干涉显微镜、多光束干涉显微镜)测量表面粗糙度要求高的表面;用电动轮廓仪可直接显示Ra0.025~6.3μm 的值;用某些塑性材料做成块状印模贴在大型笨重零件和难以用仪器直接测量或样板比较的表面(如深孔、盲孔、凹槽、内螺纹等)零件表面上,将零件表面轮廓印制印模上,然后对印模进行测量,得出粗糙度参数值(测得印模的表面粗糙度参数值比零件实际参数值要小,因此糙度测量结果需要凭经验进行修正);用激光测微仪激光结合图谱法和激光光能法测量Ra0.01~0.32μm的表面粗糙度。 五、角度 1.相对测量:用角度量块直接检测精度高的工件;用直角尺检验直角;用多面棱体测量分度盘精密齿轮、涡轮等的分度误差。 2.直接测量:用角度仪、电子角度规测量角度量块、多面棱体、棱镜等具有反射面的工作角度;用光学分度头测量工件的圆周分度或;用样板、角尺、万能角度尺直接测量精度要求不高的角度零件。 3.间接测量:常用的测量器具有正弦规、滚柱和钢球等,也可使用三坐标测量机。 4.小角度测量:测量器具有水平仪、自准直仪、激光小角度测量仪等。 六、直线度
曲轴连杆轴颈的铣削
4D型曲轴连杆轴颈的铣削 曲轴连杆轴颈的铣削是机械加工中效率相对较高的一种基础加工方法,通过多刃刀具的高速旋转运动和进给运动对所加工的工件进行切削操作,根据实际的要求加工的工件可以固定,也可以做进给运动,经过刀具在工件表面进行切削去去屑后逐渐铣出粗加工后的表面。 铣削一般具有以下三个特征: ①刀具的每个刀齿在进行切削加工过程中的切削厚度是随时变化的。 ②在加工过程中,用每齿进给量af(mm/齿)来表示工件在铣削刀具每次转过一个刀齿的时间内所经过的相对位移量。 ③铣刀的各个刀齿在加工的过程中会周期性地进行间断切削。 铣削可以适用于沟槽、平面和螺纹等的加工,一般在镗床或铣床上进行加工操作,加工机床一般有立式的铣床和卧式的铣床,可以是普通或者数控机床。 铣削加工相对于车削加工来说具有较高的生产效率,一般为车削加工生产效率的3倍左右,所以铣削加工的采用可以达到降低生产设备的投资的目的。 车削加工的稳定性在现实生产中也不如铣削加工,同时车削工件在进行车削加工时需要高速的回转,这样对生产机床就不可避免地产生较大的离心力,长期进行的车削加工操作的机床相对发生的故障率也要比铣床多一些。 根据铣削刀具的不同,铣削一般可分为外铣和内铣两种,下面我们通过对两种不同的铣削方式来研究适用于4D型曲轴连杆轴颈加工的具体操作方式。 1、4D型曲轴连杆轴颈的外铣加工 曲轴的外铣加工方式主要适用于小排量的车辆,对曲轴的主轴颈和曲轴的连杆轴颈去除毛坯余量不大的加工处理。按曲轴外铣加工的铣床铣的数量可以分为双头铣加工和单头铣加工两种。
曲轴的外铣加工示意图 曲轴在外铣加工时,在机床上将曲轴两端的主轴颈要进行位置和角度定位并夹紧,通过止推面进行轴向定位,在加工的过程中铣刀高速旋转在径向进给到曲轴连杆轴颈所规定的直径尺寸后,外铣刀具进行跟踪曲轴连杆轴颈作仿行铣削运动(这个过程也可称为数控),同时曲轴需要围绕曲轴主轴颈的中心低速旋转三百六十度,这样一个完整的工序就可以将曲轴连杆轴颈的各面加工出来了。 由于普通的曲轴外铣加工在性能上存在有许多的缺陷,基本上已经被曲轴的内铣加工所取代,所以4D型曲轴连杆轴颈在现实生产中不采用外铣加工。 2、4D型曲轴连杆轴颈的内铣加工 曲轴的内铣加工示意图 曲轴的连杆轴颈的内铣加工根据实际情况可以分为加工工件不旋转和加工
垂直度误差、位置度误差的测量教程文件
任务五垂直度误差、位置度误差的测量 【课题名称】 平面零件的误差测量 【教学目标与要求】 一、知识目标 了解线、面垂直度误差和面对称度误差的检测工具及测量方法。 二、能力目标 能够正确使用百分表进行测量,并准确计算误差值。 三、素质目标 熟悉平面零件形位误差的检测原理、测量工具和使用方法,并能准确计算其误差。 四、教学要求 能够按照误差要求正确地选择检测工具,并能够掌握测量工具的使用方法,对工件进行准确的测量。 【教学重点】 百分表的使用,各种形位误差的检测方法。 【难点分析】 百分表的使用,各种形位误差的检测方法。 【分析学生】 该内容的难度较大,比较难理解,需要多做解释,学生才能够掌握。 【教学设计思路】
本次课内容较多,且内容难懂,建议分成2学时,以保证有更多的练习机会,由于实训条件所限,可以分组进行测量,对于垂直度的检测也应先讲测量原理和方法,再让学生实测,最后介绍如何调零位计算误差值,边讲边练再总结提高。 【教学安排】 2学时 先讲后练,以练为主,加强巡视指导。 【教学过程】 一. 复习旧课 在形状和位置误差中,直线度、平面度的误差在平面零件中出现比较多,大家是否还能记住这些形位公差的含义呢? 二、导入新课 需要应用什么测量工具来检测零件的垂直度和对称度呢?对于测量出来的数值又需要进行怎么样的处理才能得出正确的误差值?这是本次课程的主要内容。 三、讲授新课 垂直度和对称度误差的测量应用百分表或千分表作为量具,用标准平扳为基准面,借助于表座、方箱或直角尺座工具,将被测工件安放在基准面上进行检测。 线与面和面与面之间垂直度的检测方法相同,后者需要多测量几次。 1.测量平面之间的垂直度,需要借助于方箱或直角尺座,将被
形位误差测量与实验
形位误差测量与实验 实验3-1直线度误差的测量 (一)实验目的 1.掌握用水平仪测量直线度误差的方法及数据处理。 2.加深对直线度误差含义的理解。 3.掌握直线度误差的评定方法。 (二)实验内容 用合象或框式水平仪按节距法测量导轨在给定平面内的直线度误差,并判断其合格性。(三)实验器具: 1.合象水平仪或框式水平仪 2.桥板 (四)测量原理及器具介绍 为了控制机床、仪器导轨及长轴的直线度误差,常在给定平面(垂直平面或水平平面)内进行检测,常用的测量器具有框式水平仪、合象水平仪、电子水平仪和自准直仪等测定微小角度变化的精密量仪。 由于被测表面存在直线度误差,测量器具置于不同的被测部位上时,其倾斜角将发生变化,若节距(相邻两点的距离)一经确定,这个微小倾角与被测两点的高度差就有明确的函数关系,通过逐个节距的测量,得出每一变化的倾斜度,经过作图或计算,即可求出被测表面的直线度误差值。合象水平仪因具有测量准确、效率高、价格便宜、携带方便等特点,在直线度误差的检测工作中得到广泛采用。 合象水平仪的结构,主要由微动螺杆、螺母、底盘水准仪、棱镜、放大镜、杠杆以及具有平面和V形工作面和底座等组成。 合象水平仪是利用棱镜将水准器中的气泡像复合放大,以提高读数时的对准精度,利用杠杆和微动螺杆传动机构来提高读的精度和灵敏度,其工作原理见本指导书第二篇。合象水平仪置于被测工件表面上,若被测两点相对自然水平线不等高时,将引起两端的气泡像不重合,转动度盘使气泡像重合,此时合象水平仪的读数值即为该两点相对自然水平面的高度差,刻度盘读数与桥板跨距L之间的关系为: h=i·L·a 框式水平仪是一种测量偏离水平面的微小角度变化量的常用量仪,它的主要工作部分是水准器。水准器是一个封闭的玻璃管,内表面的纵剖面具有一定的曲率半径,管内装乙醚或酒精,并留有一定长度的气泡。由于地心引力作用,玻璃管内的液面总是保持水平,即气泡总是在圆弧玻璃管的最上方。当水准器的下平面处于水平时,气泡处于玻璃管外壁刻度的正中间,若水准器倾斜一个角度α,则气泡就要偏离最高点,移动的格数与倾斜的角度α成正比。由此,可根据气泡偏离中间位置的大小来确定水准器下平面偏离水平的角度。 框式水平仪的分度值有0.1mm/m,0.05mm/m,0.02mm/m三种。如果水平仪分度值为0.02mm/m,则气泡每移动一格,表示导轨面在1m长度上两测量点高度差为0.02mm(或倾斜角为4〞)。
用打表法测量阀体的平面度及平行度.doc
用打表法测量阀体的平面度和平行度的方法 一 实验目的 本实验所用测量方法是工厂里常用的方法,有助于学生对平面度公差、面对面的平行度公差概念的理解,训练学生的动手能力(仅一台三坐标测量机,做不到人人动手操作),训练学生数据处理能力,以及对平面度评定方法的理解。 二 实验仪器 测量平台,作为测量的基准使用,精度要求高。磁力表架和表座、千分表、V 型块、被测零件阀体。 三 操作过程 1 将磁力表架和V 型块放置于测量平台上,将被测零件阀体放置于V 型块上。 2 将千分表安装在磁力表架上,调整磁力表架,使千分表的测头与阀体的被测平面垂直接触,且具有一定的接触力,并保证测量过程中千分表不超量程。 3 固定磁力表座,推动V 型块,并保证其与测量平台稳定接触,使千分表测头与 测量平台 阀体 表架 表座 千分表 V 型块
被测平面上3X3分布的点接触,记录9个数据,如下所示。 四数据处理 1 误差评定准则(见教材) 将测得数据处理成上述三个准则中的任意一种,各点数据中的最大值减去最小值即为平面度误差。而平行度误差评定较简单,在测得原始数据中,用最大值减去最小值即是。 2 平面度数据处理方法(见学习指导) 测得数据不会是三个准则中的任意一种,需要进行处理才行,处理方法按照如下例题所示。 例用打表法测量一块350mmx350mm的平板,各测点的读数值如下图所示。试用最小包容区域法求平面度误差值。 解:此题旨在训练培养大家进行数据处理,求解几何误差的能力。观察检测数据,最大值为20,最小值为-12 ,次小值为-10,决定采用三角形准则求解平面度误差。保留中间的最大值,求出3个相等的最小值,三个最小值位置选定-12、-10、+7,将3个数值相加除3等于-5,即3个数的平均值。利用矩阵变换方法,将3个最小值变为-5,即将第1列的数都加+7,而将第三列的数都加-7,将结果列表后,再将第一行都加-5,而第三行都加+5,再将结果列表,即得下图所示。 经过两次坐标变换后,故平面度误差值为() f=+--= 205μm25μm
位置度公差带
第一步:确定公差带的大小和形状。公差带大小及形状是由公差框格中的公差值来确定的,公差值的大小就是公差带的大小,其形状则由公差值有无直径符号来确定,如果公差值前有直径符号,它的公差带就是一个直径等于公差值的圆柱;如果公差值前没有直径符号,它的公差带就应该是相距公差值的两平行平面。从上面的例子中可以看出,6个φ8的孔的位置度公差带是直径为0.1的圆柱,而4个φ12的孔的位置度公差带是直径为0.2的圆柱。 第二步:根据公差带的实体状态修正符号确定补偿公差。公差带的实体状态由公差值后面的修正符号来确定。如果没有任何修正符号,则表示位置度公差带在RFS状态,即公差带的大小与被测孔的实际尺寸无关;如果带MMC符号,则表示公差带适用于被测孔在MMC时,当被测孔的实际尺寸从MMC向LMC偏离时,该偏离量将允许被补偿到位置度公差带上;如果带LMC 符号,则表示公差带适用于被测孔在LMC时,当被测孔的实际尺寸从LMC向MMC偏离时,该偏离量将允许被补偿到位置度公差带上。上图中两个位置度公差均是MMC状态,因此它们的公差带的大小与被测孔的实际尺寸相关。比如对φ8的孔来说,当它的实际尺寸在MMC时(φ8),它的位置度要求为φ0.1,当它的实际尺寸在LMC时(φ8.25),它的位置度公差带就变成了φ0.1+(φ8.25-φ8)=φ0.35。同样道理,对φ12的孔来说,当它的实际尺寸在LMC时,允许的最大位置度误差可以达到φ0.6。 第三步:参照基准体系的建立。参照基准体系是由形位公差框格内的参照基准按序指定基准形体来建立的。图中两个位置度的参照基准体系相同,均由基准A和B指定的基准形体建立,其中基准A的是由零件的端面建立的基准平面,它作为第一基准约束了零件的三个自由度(两个旋转自由度及一个平移自由度),基准B是由零件的外圆建立的基准轴线,它作为第二基准约束了零件的两个自由度。这样基准A和B定位后,零件就只剩下绕B轴旋转的一个自由度。由于这两组孔的位置与这个自由度没有关系,因此本例就没有对这个自由度作出限制。同时要注意的是,基准B是带MMB修正符的,因此它模拟基准就是基准形体B的MMB边界。当基准形体B的实际尺寸向它的LMB偏离时,将允许有基准的漂移。(至于基准漂移对位置度公差的影响,我们可以另行专题讨论) 第四步:确定位置度公差带在参照基准系统内的方向和位置。公差带位于是由基本尺寸定义的相对于参照基准的理论正确位置。例中6个φ8的孔的6个位置度公差带应与整体与A基准平面平行,并相距8mm,并沿B基准轴线径向均匀分布(60°夹角);而四个φ12的孔的四个位置度公差带绕B轴径向均匀分布,其中心线交于B轴,交点距A基准20mm,并与A基准平面成30°角。 第五步:确定被测形体的被测要素。形位公差框格的标注方式决定了被测形体的被测要素。另外如果形位公差框格下有BOUNDARY的注释,则被测要素是指形体的周边轮廓。例中的两个形位公差框格均标注在尺寸的下面,它表示被测形体的被测要素是孔的中心,因此它要求的是孔的中心线满足在理论位置的公差带的要求。 第六步:考虑同步要求。同步要求的条件是:1)参照基准相同,2)基准的顺序相同,3)基准的修正符号相同。当我们在评估图纸上的一个形位公差时,要考虑是否与其它形位公差符合同步要求的条件。本例中的两个位置度的参照基准,基准顺序及修正符号均相同,因此它们符合同步要求的条件,这就要求我们对这两个位置度公差同时评价,同时满足。如果用检具测量的话,就要求我们对这两个位置度在一次装夹后同时评判。 第七步:测量方法及评估依据的确定。经过前面六步的分析,我们对位置度具体要求已经很清晰了。最后一步的目的是找出一种合适的测量方法来评价这个位置度以能更深入地理解它。从设计的角度来说,如果我们用形位公差清晰地定义了一张图纸却找不到一种合适的测量方法来评价它,那这种设计也是失败的。从上面这个例子来说,我们已经了解了基准形体及其状态,公差带的大小形状及其修正符号,公差带的位置及被测要素;并且我们也知道了这两个位置度要满足同步要求,这样我们就可设计一个功能检具来同时测量这两个位置度。基准形体A可以用一平
平行度误差平面度误差的测量
任务四平行度误差、平面度误差的测量 【课题名称】 零件的平行度、平面度误差测量 【教学目标与要求】 知识目标 了解平面度误差、平行度误差的检测工具及测量方法。 能力目标 能够正确使用框式水平仪、自准直仪和百分表进行测量,并准确计算误差值。 素质目标 熟悉平面零件形位误差的检测原理、测量工具和使用方法,并能准确计算其误差。 教学要求 能够按照误差要求正确地选择检测工具,并能够掌握测量工具的使用方法,对工件进行准确的测量。 【教学重点】 框式水平仪、自准直仪和百分表的使用,各种形位误差的检测方法。 【难点分析】 平面度测量出9点误差值的调零方法及误差值计算。 【分析学生】 该内容的难度较大,特别是直线度误差值的计算和平面度零位调整比较难以理解,需要多做解释,学生才能够掌握。尤其是零位调整的方法更难懂,一定要把原理讲透。 【教学设计思路】 本次课内容较多,且内容难懂,建议分成4学时,以保证有更多的练习机会,由于实训条件有限,可以分组进行测量,然后按结果来讲述如何计算平行度和平面度的误差值。对于平面度的检测也应先讲测量原理和方法,再给学生实测,最后介绍如何调零位计算误差值,边讲边练再总结提高。本次课教学一定要做好预习工作。 【教学安排】 4学时 先讲后练,以练为主,加强巡视指导。 【教学过程】 一. 复习旧课 在形状和位置误差中,直线度误差在零件中出现比较多,大家是否还能记住这些形位公差的含义呢? 二、导入新课 需要应用什么测量工具来检测零件的直线度、平面度、平行度、呢?对于测量出来的数值又需要进行怎么样的处理才能得出正确的误差值呢?这是本次课程的主要内容。 三、讲授新课 1. 平行度误差的测量 平行度误差是工件的位置误差,一般是指工件两直线之间的平行度偏差值。它影响加工工件的精确度,因此控制平行度误差在允许的范围内就显得更为重要。 平行度误差分线与线和线与面之间的误差两种。 平行度误差的测量主要使用百分表。以一条线或面为基准,将百分表座放在基准上,沿基准来回移动,百分表针的最大值与最小值之差就是平行度误差值。
三坐标测量位置度的方法及注意事项
三坐标测量位置度的方法及注意事项 位置度检测是机动车零部件检测中经常进行的一项常规检验。所谓“位置度”是指对被评价要素的实际位置对理想位置变动量的指标进行限制。在进行位置度检测时首先要很好地理解和消化图纸的要求,在理解的基础上选择合适的基准。位置度的检测就是相对于这些基准,它的定位尺寸为理论尺寸。 标签:三坐标;位置度 1 位置度的三坐标测量方法 1.1 计算被测要素的理论位置 ①根据不同零部件的功能要求,位置度公差分为给定一个方向、给定两个方向和任意方向三种,可以根据基准体系及确定被测要素的理论正确位置的两个理论正确尺寸的方向选择适当的投影面,如XY平面、XZ平面、YZ平面。②根据投影面和图纸要求正确计算被测要素在适当投影面的理论位置。 1.2 根据零部件建立合适的坐标系。在PC-DMIS软件中,可以把基准用于建立零件坐标系,也可以使用合适的测量元素建立零件坐标系,建立坐标的元素和基準元素可以分开。 1.3 测量被测元素和基准元素。在被测元素和基准元素取点拟合时,最好使用自动程序进行,以减少手动检测的误差。 1.4 位置度的评价。①在PC-DMIS软件中,位置度的评价可以直接点击位置度图标。②在位置度评价对话框中包含两个页面,特征控制框和高级,首先根据图纸要求设置相应的基准元素,在基准元素编辑窗口中只会出现在编辑当前光标位置以上的基准特征,如图1所示。③基准元素设置完成,回到特征控制框选择被测元素,设置基准,输入位置度公差。④在位置度评价的对话框中选择高级,在此对话框中可以设置特征控制框尺寸的信息输出方式和分析选项。如图2的对话框,在标称值一栏中手动键入被测要素的理论位置值,点击评价。 1.5 在报告文本中刷新就可以看到所评价的位置度结果。 2 三坐标测量位置度的注意事项 2.1 评价位置度的基准元素选择和建立坐标系的元素选择有相似之处,都要用平面或轴线作为A基准,用投影于第一个坐标平面的线作为B基准,用坐标系原点作为C基准。如果这些元素不存在,可以用构造功能套用、生成这些元素。 2.2 对位置度公差的理解。如位置度公差值t前加注φ,表示公差带是直径
平行度误差检测方法介绍
平行度误差检测方法介绍
摘要:平行度是属于形位公差中的一种,平行度评价直线之间、平面之间或直线与平面之间的平行状态。下面我们将对平行度的误差检测方法进行讲解。 什么是平行度? 指两平面或者两直线平行的程度,指一平面(边)相对于另一平面(边)平行的误差最大允许值。 平行度公差 平行度公差是一种定向公差,是被测要素相对基准在方向上允许的变动全量。所以定向公差具有控制方向的功能,即控制被测要素对准基准要素的方向。 平行度公差的分类 1、面对面的平行度公差 该项平行度公差为:所指表面必需位于距离为0.05mm,且平行于基准平面的两平行平面之间。公差带是距离为公差值t且平行于基准平面的两平行平面之间的区域。 2、面对线的平行度公差 指平面必须位于距离为0.05mm,且平行于基准轴线的两平行平面之间。公差带是距离为公差值t且平行于基准轴线的两平行平面之间的区域。 3、线对线的平行度公差 ●给定方向线对线的平行度公差 平行度公差为孔D的实际轴线必须位于距离为公差值0.2mm,平行位于基准轴线A且垂直于给定方向的两平行平面之间。公差带是距离为公差值t且平行于基准轴线且垂直于给定方向的两平行平面之间的区域。 ●任意方向上线对线的平行度公差 平行度公差为孔D的实际轴线必须位于直径为公差值0.1mm,轴线平行于基准轴
线A的圆柱面所构成的公差带区域内。任意方向上线对线的平行度公差带是直径为公差值t,轴线平行于基准轴线的圆柱面内的区域。 平行度误差检测方法 传统测量方法 1、测量面对面平行度误差 公差要求是测量面相对于基准平面的平行度误差。基准平面用平板体现,如下图所示。测量时,双手推拉表架在平板上缓慢地作前后滑动,用百分表或千分表在被测平面内滑过,找到指示表读数的最大值和最小值。 被测平面对基准平面的平行度误差可按公式计算为: 2、测量线对面平行度误差 公差要求是测量孔的轴线相对于基准平面的平行度误差。需要用心轴模拟被测要素,将心轴装于孔内,形成稳定接触,基准平面用精密平板体现,如下图所示: 测量时,双手推拉表架在平板上缓慢地作前后滑动,当百分表或千分表从心轴上素线滑过,找到指示表指针转动的往复点(极限点)后,停止滑动,进行读数。 在被测心轴上确定两个测点a、b,设二测点距离为1 ,指示表在二测点的 2 读数分别
三坐标测量位置度的方法及注意事项
三坐标测量位置度的方法及注意事项 三坐标测量位置度的方法及注意事项 摘要:位置度检测是机动车零部件检测中经常进行的一项常规检验。所谓"位置度";是指对被评价要素的实际位置对理想位置变动量的指标进行限制。在进行位置度检测时首先要很好地理解和消化图纸的要求,在理解的基础上选择合适的基准。位置度的检测就是相对于这些基准,它的定位尺寸为理论尺寸。 关键词:三坐标;位置度;方法 一、位置度的三坐标测量方法 1.1 计算被测要素的理论位置 ①根据不同零部件的功能要求,位置度公差分为给定一个方向、给定两个方向和任意方向三种,可以根据基准体系及确定被测要素的理论正确位置的两个理论正确尺寸的方向选择适当的投影面,如XY平面、XZ平面、YZ平面。②根据投影面和图纸要求正确计算被测要素在适当投影面的理论位置。 1.2 根据零部件建立合适的坐标系。在PC-DMIS软件中,可以把基准用于建立零件坐标系,也可以使用合适的测量元素建立零件坐标系,建立坐标的元素和基准元素可以分开。 1.3 测量被测元素和基准元素。在被测元素和基准元素取点拟合时,最好使用自动程序进行,以减少手动检测的误差。
1.4 位置度的评价。①在PC-DMIS软件中,位置度的评价可以直接点击位置度图标。 ②在位置度评价对话框中包含两个页面,特征控制框和高级,首先根据图纸要求设置相应的基准元素,在基准元素编辑窗口中只会出现在编辑当前光标位置以上的基准特征,如图1所示。③基准元素设置完成,回到特征控制框选择被测元素,设置基准,输入位置度公差。 ④在位置度评价的对话框中选择高级,在此对话框中可以设置特征控制框尺寸的信息输出方式和分析选项。如图2的对话框,在标称值一栏中手动键入被测要素的理论位置值,点击评价。 1.5 在报告文本中刷新就可以看到所评价的位置度结果。 二、三坐标测量位置度的注意事项 2.1 评价位置度的基准元素选择和建立坐标系的元素选择有相似之处,都要用平面或轴线作为A基准,用投影于第一个坐标平面的线作为B基准,用坐标系原点作为C基准。如果这些元素不存在,可以用构造功能套用、生成这些元素。 2.2 对位置度公差的理解。如位置度公差值t前加注φ,表示公差带是直径为t的圆内的区域,圆心的位置由相对于基准A和B的理论值确定。(如图3) 如位置度公差值前加注Sφ,表示公差带是直径为t的球内的区域,球心的位置由相对于基准A、B和C的理论值确定。(如图4) 2.3 对于深度小于5mm的孔,可以直接计算测量其位置度。对于深度大于5mm的孔,必须采用先测量圆柱,然后与上、下端面求相交,再对交点求位置度的方法来控制测量误差,上、下端面一般是指整个孔的两端面。或者尽量取靠近两端面孔的截面位置,如果仅测量一个截面,求其位置度是不能保证此孔在整个长度范围上所有截面的位置度都合格的。因为交点是圆柱轴线与两端平面相交得到,不管轴线方向往哪个方向倾斜,如果两端交点位置度合格,中间各截面的位置度也应该是合格的。 2.4 对于有延伸公差带要求的,评价时要包含延伸的长度。 2.5 在位置度公差设置时,有时会出现[M] [L] 图标,它们的含义各不相同,其主要目的是为了尺寸公差和形状、位置度公差之间的相互补偿。 ①孔的最小实体位置度公差。
曲轴的结构
曲轴的结构如图1.1所示:它由主轴颈,连杆轴颈曲轴臂,平衡块,前轴端和后轴端等部分组成。其中一个连杆颈和它两端的曲臂以及前后两个主轴颈合在一起,称为曲拐。曲轴的形式有整体式和组合式两种。下面分析大多数汽车发动机采用的整体式曲轴的结构。 图1.1 1.主轴颈 图1.2所示,用来支撑曲轴,曲轴几即绕其中心线旋转。主轴颈支撑于滑动主轴承上,主轴颈结构和连杆轴颈类似,不同点于滑动主轴承上,主轴颈结构和连杆轴颈类似,不同点是内表面有油槽。主轴承盖用螺栓与上曲轴箱的主轴承座紧固在一起。为了使各主轴颈磨损相对均匀,对于受力交大的中部和两端的主轴颈制造得较宽。 在连杆轴颈的两侧都有主轴颈者,称为全支撑曲轴。全支撑曲轴钢度好,主轴颈负荷小,但它比较长。如果主轴颈数目比连杆轴颈少,则称为非全支撑曲轴。其特点和全支撑主轴相反。 图1.2
2.连杆轴颈 用来安装连杆大头,如图1.3所示。直列式发动机的连杆轴项数与汽缸数相等;V型发动机因为两个连杆共同装在一个连杆轴颈上,故连杆轴颈数为汽缸数的一半。连杆轴颈通常被制成中空,其目的是为了减轻曲拐旋转部分的质量,以减小离心力。中空的部分还可兼作油道和油腔,如图所示。油腔不钻通,外端用螺塞封闭,并用开口销锁住。连杆中部插入一弯管,管口位于油腔中心。当曲轴旋转时,在曲轴油管机油中的较重的杂质被甩向油腔壁,而洁净的机油则经弯管流向连杆轴向表面,减轻了轴颈的磨损。 图1.3 3.曲轴臂 用来连接主轴颈和连杆轴颈,如图1.4所示。有的发动机曲轴臂上加有平衡块,用来平衡曲轴的不平衡的离心力和离心力矩,有的还可平衡一部分往复惯性力。图示1.5为四缸发动机曲轴受力情况。1.4道连杆轴颈的离心力F1.F4与2.3道连杆轴颈的离心力F2.F3大小相等,方向相反。从整体上看,似乎在内部能相互平衡,但由于在F1与F2形成的力偶MF2和F3与F4形成的力偶M3-4作用下,如果曲轴的刚度不足,则发生弯曲变形,加剧主轴颈的磨损。为此,需加宽轴颈,增加刚度,以减少磨损。但更有效的措施是在曲轴臂反方向延伸一块平衡块。平衡块与曲轴制成一体,也可单独制造,再用螺栓固装在曲轴臂上,加平衡块会导致曲轴质量和材料消耗增加,制造工艺复杂。因此,曲轴是否要加平衡块,应视具体情况而定。
公差实验指导书(平行度误差测量)
实验二平行度误差的测量 一、实验目的 1.了解指示表的结构及通用测量工具并熟悉使用它们测量箱体孔与底面的平行度误差的方法。 2.掌握平行度误差的评定方法。 3.掌握被测要素对基准要素的平行度误差值的评定方法和数据处理方法。 二、平行度误差的测量与评定 1.平行度误差的测量的原理 1)平行度误差的定义 给定方向的平行度误差为包容实际要素 并平行于基准要素,且距离为最小的两平行平 面之间的距离f。任意方向的平行度误差为包 容实际轴线并平行于基准轴线,且直径为最小 的圆柱面的直径Φf。 2)平行度误差的测量原理 实际基准要素都是有误差的,由实际轮廓 要素建立基准时,是以轮廓实际基准要素最小 包容区域的体外边界作为理想基准要素;由实 际中心要素建立基准时,是以实际基准要素的 最小区域的中心要素作为理想基准要素。对平 行度误差(位置误差)基准的体现方法有分析 法、直接法、模拟法和目标法。 (1)分析法分析法是对实际基准要素进 行测量后,根据测量的数据用图解或计算法确 定基准的方向或位置。(参见直线度误差的评 定方法)然后,根据理想基准方向,作实际被 测轮廓的包容平行平面(和理想基准面平行), 此平行平面纵座标距离,即为被测面的平行 度误差如图2.1所示。 用分析法体现基准评定位置误差的方法,图2.1用分析法体现基准评定平行度误差 符合最小条件的原则。 (2)模拟法模拟法是采用形状精度足够精确的实际基准要素(如精确平板的工作面,圆柱形心轴、球面中心等)来体现基准。如图2.2所示,在基准面A上放一精确平行平尺,指示器的测量架置于精确平行平尺上并沿被测面长向某一测量线方向移动,指示器的最的最大与最小读数差即为平行度误差。 (3)直接法直接法体现基准是将形状精度足够精确的基准实际要素直接作为基
最新垂直度误差、位置度误差的测量
垂直度误差、位置度误差的测量
任务五垂直度误差、位置度误差的测量 【课题名称】 平面零件的误差测量 【教学目标与要求】 一、知识目标 了解线、面垂直度误差和面对称度误差的检测工具及测量方法。 二、能力目标 能够正确使用百分表进行测量,并准确计算误差值。 三、素质目标 熟悉平面零件形位误差的检测原理、测量工具和使用方法,并能准确计算其误差。 四、教学要求 能够按照误差要求正确地选择检测工具,并能够掌握测量工具的使用方法,对工件进行准确的测量。 【教学重点】 百分表的使用,各种形位误差的检测方法。 【难点分析】 百分表的使用,各种形位误差的检测方法。 【分析学生】 该内容的难度较大,比较难理解,需要多做解释,学生才能够掌握。
【教学设计思路】 本次课内容较多,且内容难懂,建议分成2学时,以保证有更多的练习机会,由于实训条件所限,可以分组进行测量,对于垂直度的检测也应先讲测量原理和方法,再让学生实测,最后介绍如何调零位计算误差值,边讲边练再总结提高。 【教学安排】 2学时 先讲后练,以练为主,加强巡视指导。 【教学过程】 一. 复习旧课 在形状和位置误差中,直线度、平面度的误差在平面零件中出现比较多,大家是否还能记住这些形位公差的含义呢? 二、导入新课 需要应用什么测量工具来检测零件的垂直度和对称度呢?对于测量出来的数值又需要进行怎么样的处理才能得出正确的误差值?这是本次课程的主要内容。 三、讲授新课 垂直度和对称度误差的测量应用百分表或千分表作为量具,用标准平扳为基准面,借助于表座、方箱或直角尺座工具,将被测工件安放在基准面上进行检测。 线与面和面与面之间垂直度的检测方法相同,后者需要多测量几次。