镀铜常见故障

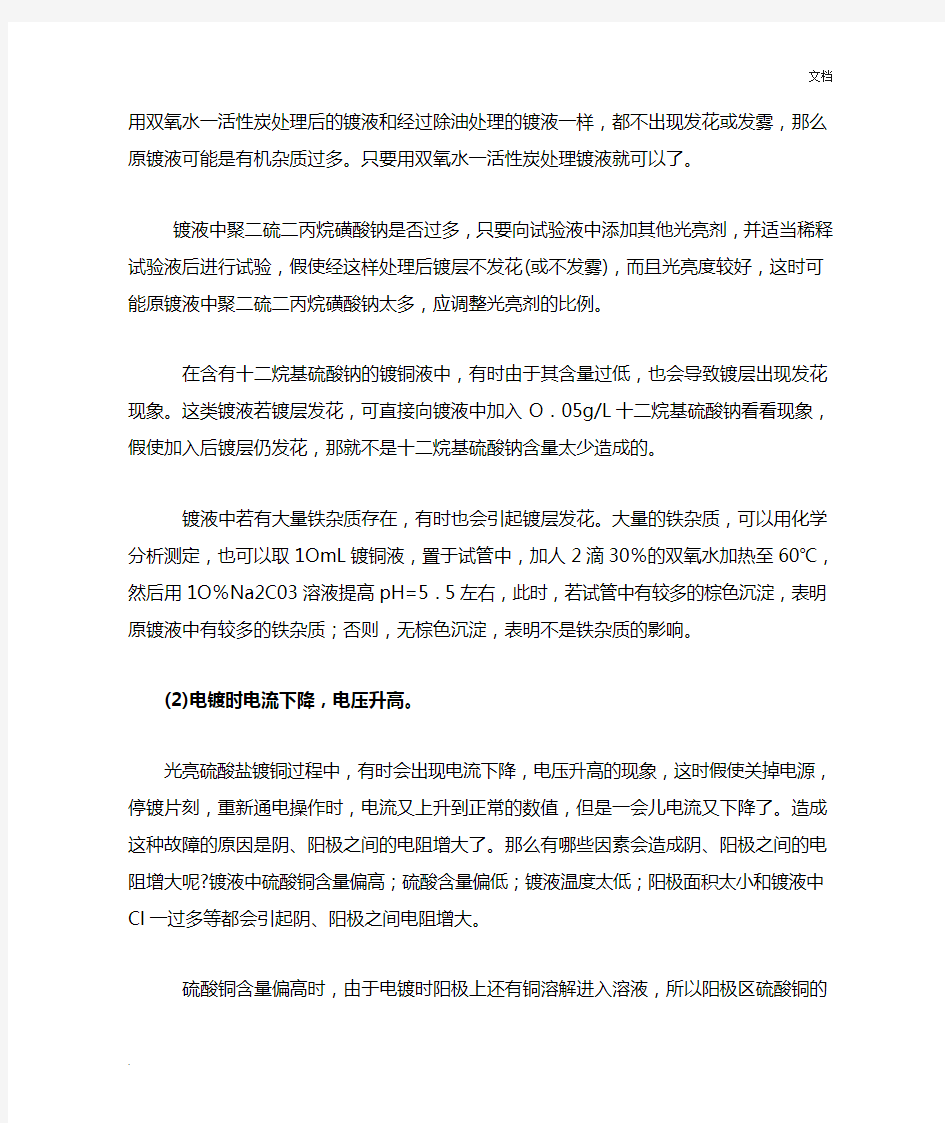
(1)镀层发花或发雾。
1镀前处理不良,零件表面有油;清洗水或镀液中有油;
2阳极面积太小或太短;
3镀液中聚二硫二丙烷磺酸钠太多;
4有机杂质太多;光亮剂没有搅均或十二烷基硫酸钠太少等会造成镀层发花或发雾。
分析故障,要先易后难,逐条进行。例如先搅拌一下镀液,检查一下阳极面积,这样就可以排除由于光亮剂没有搅均和阳极面积太小而造成的故障。同时也可从现象进行分析,假使发花现象仅出现在挂具下部的零件上,上部零件不发花,那就可能是阳极板太短而产生的,经检查并换上足够长的阳极板后,观察发花现象是否消失。倘若发花现象出现在零件的向下面或挂具上部的零件上,那可能是清洗水或镀液中有油而引起的。光亮硫酸盐镀铜对油污特别敏感,不管是毛坯上的油在镀前处理时未除净,还是镀前的清洗水或镀液中有微量的油,甚至是操作人员不干净的手摸了摸镀前的零件,都会使镀铜层发花。假使原来镀铜出现发花或发雾,采用良好的前处理后,镀层不出现发花或发雾现象厂,证明原来的镀前处理有问题,应加强镀前处理。否则,就应检查镀液中的情况。
镀液中是否有油,不但可以从现象进行判断,同时还可以通过小试验来了解。取一定量的故障液做烧杯试验,先要使阴极样板上能看到类似于生产中的故障现象,接着对试验液进行除油处理,另外再取相同体积的故障液进行双氧水一活性炭处理,然后分别进行试验(试验液中需补充各种光亮剂)。若用双氧水一活性炭处理过的镀液仍有发花或发雾,而经过除油处理的镀液不再出现发花或发雾,那么原镀液中有油,应进行除油处理。假使用双氧水一活性炭处理后的镀液和经过除油处理的镀液一样,都不出现发花或发雾,那么原镀液可能是有机杂质过多。只要用双氧水一活性炭处理镀液就可以了。
镀液中聚二硫二丙烷磺酸钠是否过多,只要向试验液中添加其他光亮剂,并适当稀释试验液后进行试验,假使经这样处理后镀层不发花(或不发雾),而且光亮度较好,这时可能原镀液中聚二硫二丙烷磺酸钠太多,应调整光亮剂的比例。
在含有十二烷基硫酸钠的镀铜液中,有时由于其含量过低,也会导致镀层出现发花现象。这类镀液若镀层发花,可直接向镀液中加入O.05g/L十二烷基硫酸钠看看现象,假使加入后镀层仍发花,那就不是十二烷基硫酸钠含量太少造成的。
镀液中若有大量铁杂质存在,有时也会引起镀层发花。大量的铁杂质,可以用化学分析测定,也可以取1OmL镀铜液,置于试管中,加人2滴30%的双氧水加热至60℃,然后用1O%Na2C03溶液提高pH=5.5左右,此时,若试管中有较多的棕色沉淀,表明原镀液中有较多的铁杂质;否则,无棕色沉淀,表明不是铁杂质的影响。
(2)电镀时电流下降,电压升高。
光亮硫酸盐镀铜过程中,有时会出现电流下降,电压升高的现象,这时假使关掉电源,停镀片刻,重新通电操作时,电流又上升到正常的数值,但是一会儿电流又下降了。造成这种故障的原因是阴、阳极之间的电阻增大了。那么有哪些因素会造成阴、阳极之间的电阻增大呢?镀液中硫酸铜含量偏高;硫酸含量偏低;镀液温度太低;阳极面积太小和镀液中Cl一过多等都会引起阴、阳极之间电阻增大。
硫酸铜含量偏高时,由于电镀时阳极上还有铜溶解进入溶液,所以阳极区硫酸铜的含量更高,当镀液温度较低时,它就有可能在阳极表面上或阳极袋上结晶析出,使阳极的有效表面积减小,阳极电流密度增大,阳极电位变正,从而造成阳极钝化而使操作电流下降。
硫酸含量偏低时,溶液的导电性差,而且不利于阳极活化,使阳极电位变正,有可能引起阳极钝化而使操作电流下降。
镀液温度低,溶液的导电性差,阴、阳极极化增大,同时硫酸铜的溶解度小,使硫酸铜容易在阳极上或阳极袋上结晶析出。
阳极面积小,其电流密度大,极化作用就大,使阳极容易钝化。
镀液中Cl一过多时,它会在阳极上形成白色的氯化物,粘附于阳极表面上,导致阳极有效表面积减小,使阳极容易钝化。
当出现这类故障时,应先检查阳极,观察阳极是否钝化或有白色的粘附物。若阳极钝化,应取出阳极经充分刷洗干净后重新挂人镀槽中,并尽量增大阳极面积。同时分析镀液成分,若硫酸铜含量偏高,可适当稀释镀液。在硫酸铜含量不太高的情况下,可适当提高硫酸的含量,以提高溶液的电导率,促进阳极活化。冬天若液温太低,可适当加温,提高溶液的温度;一般讲,经这样改进后,故障是能够排除的。假使经这样改进仍不能排除故障,那可能是镀液中Cl一过多(用O.1NAgN03粗略估计,观察Cl一是否过多),需要进行除Cl
一处理(方法见杂质的去除)。
(3)低电流密度区镀层不亮。
在电镀铜一铜一镍一铬或镍一铜一镍一铬的装饰性电镀体系中,光亮硫酸盐镀铜出现低电流密度区镀层不亮时,接着镀光亮镍和装饰铬,低电流密度区都不能获得光亮的镀层,从而使产品不合要求,次品率增加。引起这类故障的原因很多:预镀层低电流密度区镀层粗糙;挂具导电性不良;镀铜液中N、M或十二烷基硫酸钠含量偏低;聚二硫二丙烷磺酸钠含量过多;镀液中一价铜较多;温度过高;硫酸含量偏低;Cl一过多或有机杂质过多等都会使低电流密度区镀层不亮;虽然这类故障多数是镀液成分失调或镀液中的杂质引起的,但分析故障时,首先应检查预镀层的质量和挂具接触点的导电性。有时由于挂具装零件的钩子上镀层很厚,导电性很差,或是挂具各接触点的接触电阻较大,使零件表面上的真实电流密度太小而使低电流密度区镀层不亮。这些因素引起的故障与镀液成分无关,所以先检查预镀层和挂具导电情况,可以防止本来镀液没有问题而盲目地处理镀液,只有在排除了预镀层和挂具的接触点的影响后,着手处理镀液就不会走弯路。
镀液成分失调或光亮剂比例失调,可以根据前面叙述的方法进行纠正。
故障是否是一价铜引起的?可以向镀液中加入0.03mL/L~O.05mL/L30%的双氧水后试镀,观察低电流密度区镶层的光亮度有否改善,如有改善,表明镀液中一价铜较多,否则就不是一价铜的影响。假使添加双氧水后故障现象消失,但过了一会儿故障又重新出现,需要再加双氧水才能消除故障。表明镀液中一价铜很容易产生,那就要检查阳极状况,假使电镀时在正常电流密度下,其表面上没有棕黑色膜存在,说明该阳极质量不好或含磷量太少,必要时应更换阳极。
镀液中Cl一过多出现的现象是使镀层粗糙并出现条纹,阳极上粘附有白色的氯化物,同时还可用O.1 N AgN03溶液粗略估计Cl一的含量,发现其含量过多时,应进行除Cl 一处理。
镀液温度过高(一般光亮硫酸盐镀铜液在28℃以上,宽温度镀液在38℃以上),会使低电流密度区镀层不亮的区域扩大。必要时应采取降温。
有机杂质的影响可根据前面叙述的方法试验和纠正。
(4)镀层粗糙。
预镀层太薄或粗糙;预镀镍进入硫酸盐镀铜液中未及时通电;挂具钩子上的铬层未彻底退除掉;阳极含磷量少;镀液中硫酸铜含量过高、温度过高或有“铜粉”及其他悬浮物存在时会使镀层出现粗糙。
由于铁在硫酸盐镀铜液中的电位比铜负得多,所以预镀层太薄,铁可以通过镀层的孔隙置换溶液中的铜,形成点状疏松的置换层,使镀层呈现粗糙的外观,预镀镍进入硫酸盐镀铜液,若不及时通电,镍也能置换铜,形成疏松、粗糙的置换层,挂具钩子上若有铬层,因铬层上再镀上去的镀层结合不牢,它会以小颗粒的形式脱落下来,落在挂具下部的零件表面上,使下面的零件镀层粗糙。这些因素造成的粗糙都与镀液无关,应首先仔细检查。
正常的铜阳极,其含磷量在O.1%~O.3%之间,电镀时,表面会形成一层棕黑色的膜,它可以使铜阳极以二价铜的形式溶解,抑制“铜粉”和一价铜的产生。如果铜阳极中含磷量低,电镀时阳极表面难以形成棕黑色的膜,这样,“铜粉”就多,并会有一价铜溶解进入溶液,它较容易在阴极上还原而形成粗糙的镀层。所以含磷量少的阳极不宜在该镀液中使用。其含磷量的多少,可以从电镀时它表面上的色泽进行判断,有均匀棕黑色膜的阳极,其含磷量已经足够,相反,如没有均匀的棕黑色膜存在,则它的含磷量往往是太少了。
镀液温度过高或硫酸铜含量过高,都会使阴极极化降低,而且温度过高,不利于添加剂在阴极表面的吸附,使添加剂的作用减弱,从而隹镀层结晶粗糙。
“铜粉”或固体悬浮物会使镀层粗糙是众所周知的。当出现镀层粗糙时,要仔细观察现象:溶液中悬浮的固体微粒或“铜粉"造成的粗糙,出现在零件的向上面,因为这些粒子密度较大,在溶液中有下沉的趋势,容易沉积在向上面上。当出现这样的粗糙时,应检查阳极袋(或阳极框)是否破裂,如有破裂,应立即修补或更换。同时应过滤镀液,除去溶液中的固体微粒。挂具钩子上有铬层时,虽然也会使零件的向上面出现粗糙,但现象略有不同,它除了使零件向上面产生粗糙外,挂具上的镀层也是粗糙疏松的,用手一摸,挂具上的镀层即以粉末状的细粒脱落下来。发现这种现象,就应加强镀前挂具的退铬。
镀液温度过高或一价铜的影响特征是除了使镀层粗糙外,还使零件的低电流密度区镀层不亮。镀液温度大家都会检查。镀液中的一价铜,可以通过向镀液中加入0.05 mL/L30%的双氧水处理后进行判断。
预镀层太薄造成的粗糙是点状的,由于它与基体结合不牢,所以可用小刀将点状的粗糙刮破后观察现象,还可以从延长预镀时间,看看粗糙现象是否消失来判别。
预镀镍在镀铜液中未及时通电造成的粗糙是结合不牢的,一擦即能把镀层擦去,较容易区别。出现这种现象时,应刷洗所有的接触点,降低接触电阻,使各导电部位接触良好。
(5)镀层上有麻点。阳极质量不好;预镀层上有麻点;镀液中M太多或硫酸含量太低等会使镀层出现麻点。
磷铜阳极的质量好坏直接影响镀铜层质量。有些厂浇铸的磷铜阳极,不但含磷量忽高忽低,而且磷在铜中不能均匀的分布,使局部表面上含磷量偏低,这就有可能使镀层出现麻点或粗糙。
镀铜层上的麻点,有时在镀前处理过的毛坯上或预镀层上就有了,但当时还看不出,经过镀光亮铜后,由于镀层比较光亮,麻点就比较明显了。例如在化学碱液除油或电解除油时。由于除油液使用时间较长,液面上悬浮了一层小油滴。零件从除油液中取出,这种小油滴有可能吸附在零件表面上,因为当时零件的温度较高,油滴在空气中容易干燥,导致镀铜层出现麻点。还有某些研磨过的零件,表面粘有磨光膏,假使这类磨光膏在除油时未彻底除去,那么将会带入预镀镍的溶液中,长期操作,使预镀镍溶液中胶类杂质逐渐积累,致使预镀镍层产生麻点。
当镀层上出现麻点时,除了要检查阳极外,首先应确定故障的起源。假使故障起源于镀前,一方面应更换或净化除油液,另一方面要检验预镀镍溶液中是否有胶类杂质,方法是取1OOmL左右的预镀镍溶液,加热至65℃~75℃,然后加人5%丹宁酸溶液1mL,搅拌片刻,待静置后,若有絮状物产生,表明有胶类杂质。否则就不是预镀镍中胶类杂质的影响。倘若故障起源于镀铜液中:
①按分析调整硫酸的含量;
②通过小试验调整光亮剂的比例。一般来说,如M过多,可加入O.05mL/L~
O.1mL/L30%双氧水,搅拌片刻,再补充适量的聚二硫二丙烷磺酸钠即可调整。另外,有时溶液/镀件之间的界面张力太大也会使镀层产生麻点,这时可以向镀液中补充十二烷基硫酸钠,使其界面张力降低,从而消除麻点。
(6)镀层上有条纹。预镀镍溶液中有胶类杂质,使预镀层产生条纹,从而使镀铜层反映出条纹的现象;镀铜液中Cl一过多,N或四氢噻唑硫酮过多等会使镀铜层出现条纹。
有时向镀液中补充N或四氢噻唑硫酮后出现光亮的树枝状条纹,那是由于N或四氢噻唑硫酮加过量而造成的。这时可以向镀液中加入适量的双氧水(一般加入30%的双氧水
O.05mL/L~O.1mL/L),搅拌片刻,再加入适量的聚二硫二丙烷磺酸钠进行调整,或者电解一段时间就可消除。
镀液中Cl一过多,有时会产生树枝状的条纹,同时使镀层结晶粗糙和失去光泽。Cl一含量的多少可以用O.1NAgN03粗略地估计,也可以用小试验进行验证。发现Cl一含量过多,必须进行除Cl一处理。
有时镀液中硫酸铜含量过低,也会出现一些不太明显的条纹。由于硫酸铜含量过低时,溶液的颜色较浅,所以可从观察颜色进行判别,同时可用化学分析测定其含量.’然后按分析进行调整。
假使经过检查,故障都不是上述因素引起的,那就可能是预镀液或镀前处理有问题,可以取一些铜零件或铜片,经手工擦刷除油和活化后,跳越掉预镀槽,直接进入光亮硫酸盐镀铜液中电镀。如果跳越掉预镀槽后,镀层上没有条纹了,说明光亮镀铜液没有问题,应该从预镀液或镀前处理中寻找原因。
杂质的影响和去除
(1)氯离子的影响和去除。在光亮硫酸盐镀铜液中,虽然N(或四氢噻唑硫酮)和聚二硫二丙烷磺酸钠都能使镀层细化,配比得当能提高镀层的光亮度和整平性,但它们都使镀层的应力增大,然而在镀液中含有适量的(20mg/L~80mg/L)Cl一,可以使镀层的张应力降低,提高镀层的韧性,所以可以说Cl一是该镀液中的应力消减剂,同时适量的Cl一还能提高镀层的光亮度和整平性,使零件的低电流密度区镀层更亮。但它的含量超过120mg/L时,就使镀层粗化,更高的含量使镀层粗糙,产生树枝状条纹和失去光泽。去除氯离子的方法是:①银盐沉淀处理。
Cl一+Ag+→AgCl↓
选用哪一种银盐进行处理呢?有资料介绍用硫酸银,因为硫酸银与Cl一反应后,不会产生其它有害的阴离子:
2Cl一+Ag2S04→2AgCl↓+SO42-
但硫酸银不易买到,所以一般用AgN03与Na2C03作用,制成Ag2C03,然后用
Ag2C03处理Cl一:
2AgN03+Na2C03→Ag2C03↓+2NaN03
340 106(过量) 276
340份AgN03与过量的Na2 C03作用,可生成276份Ag2C03沉淀,这种沉淀用热的蒸馏水洗涤4次~5次,以洗去N03-,然后在搅拌下加入故障液中,使与Cl一反应:2HCl+Ag2C03→2AgCl↓+C02↑+H2O
73 276
根据理论计算,4.66份AgN03可去除1份Cl一。虽然实际操作过程中,由于部分银盐在洗涤时损失掉,用量应该要略高一些。不过,光亮硫酸盐镀铜液中的Cl一,不必全部除去,需要有20mg/L~80mg/L留在溶液中,所以可按理论计算进行处理。具体步骤如下:
a.将镀液加热至60℃左右;
b.在搅拌下加入计算量的Ag2C03,加完后继续搅拌30min左右;
c.加入3g/L~5g/L活性炭,搅拌30min左右;
d.静置后过滤;
e.加入配方量的所有光亮剂,搅匀后即可电镀。
②锌粉处理:据文献报道,用锌粉处理光亮硫酸盐镀铜液,可以降低镀液中Cl一的含量。现经工厂实际应用,锌粉确有降低Cl一的效果,具体处理步骤如下:
a.在搅拌下,加入lg/L~3g/L锌粉(要用试剂级锌粉,使用时先调成糊状)继续搅拌30min左右;
b.加入2g/L~3g/L活性炭,搅拌3 h左右;
c.静置片刻,过滤;
d.加入配方量的所有光亮剂,搅匀后即可电镀。
③用不溶性阳极电解处理:将阳极改为不溶性钛或石墨。在适当加热(40℃~50℃)的情况下,进行电解处理,使Cl一在阳极上氧化:
2 Cl一一2e→Cl↑
处理时,加温可降低Cl2在溶液中的溶解度,避免Cl2溶解在镀液中(Cl2+H2O→HCl+HClO)再影响镀液性能;同时需搅拌镀液,使Cl一到达阳极表面,在阳板上发生反应而被除去,还需适当提高阳极电流密度,加快Cl一的氧化。
(2)有机杂质的影响和去除。有机杂质会使镀层发花或发雾,降低镀层的光亮度和整平性。去除有机杂质通常用双氧水一活性炭处理。具体处理步骤如下:
①在搅拌下加人1mL/L~2mL/L30%的双氧水,加热至50℃~60℃.继续搅拌60min 左右,除去过量的双氧水;
②在搅拌下加入3g/L~5g/L活性炭,继续搅拌30min;
③静置后过滤;
④加入配方量的所有光亮剂,搅匀后即可电镀。
(3)油类杂质的影响和去除。油类杂质会使镀层发花或发雾,产生针孔,严重时影响镀层的结合力。去除油类杂质一般先用乳化剂将油乳化,然后用活性炭将乳化了的油和过量的乳化剂吸附除去。具体处理步骤如下:
①将镀液加热至50℃~60℃,在搅拌下加人溶解好的十二烷基硫酸钠O.3 g/L~O.5 g/L(用量视油污的多少而定),搅拌60min左右;
②在搅拌下加入3g/L~5g/L活性炭,继续搅拌30min左右,接下去同处理有机杂物的③和④的方法进行操作。
(4)铁杂质的影响和去除。铁杂质会降低阴极电流效率,较多的铁会影响镀层结构,形成不均匀的光亮镀层。去除铁杂质至今没有好方法,但当镀液中铜含量偏低(硫酸铜在
1OOg/L以下)时,可用下法处理:
①向镀液中加入1mL/L~2mL/L30%双氧水,使Fe2+氧化为Fe3+:
②将镀液加热至50℃~60℃,在搅拌下,用Cu(OH)2[Cu(OH)2可以用
CuS04·5H2O和NaOH自制:CuS04+2 NaOH→Cu(OH)↓NaSO提高镀液pH=5.O,使Fe3+生成Fe(OH);
③加入1g/L~2g/L活性炭,搅拌30min;
④静置后过滤:
⑤用硫酸提高溶液的酸度(降低镀液pH),按分析调整镀液成分;
⑥加入配方量的所有光亮剂,搅匀后即可电镀。
此法在提高pH时,相当于补充了硫酸铜(H2 S04+Cu(OH)2→CuS04+2H2O),但也中和掉了大量的硫酸,所以在沉淀除掉铁杂质以后,还需补充硫酸,使溶液保持足够的酸度。所以用此法除铁,经济上是不合算的。
此法只可用于镀液中硫酸铜含量偏低的镀液,对于镀液成分正常的镀液,除了用稀释镀液来降低铁杂质的含量(稀释后再补充其他成分)以外.至今没有其他除铁方法。
电镀铜二
电镀铜(二) 3.4操作条件的影响 3.4.1温度 温度对镀液性能影响很大,温度提高,会导致允许的电流密度提高,加快电极反应速度,但温度过高,会加快添加剂的分解,使添加剂的消耗增加,同时镀层光亮度降低,镀层结晶粗糙。温度太低,虽然添加剂的消耗降低,但允许电流密度降低,高电流区容易烧焦。一般以20-300C为佳。 3.4.2电流密度 当镀液组成,添加剂,温度,搅拌等因素一定时,镀液所允许的电流密度范围也就一定了,为了提高生产效率,在保证镀层质量的前提下,应尽量使用高的电流密度。电流密度不同,沉积速度也不同。表8-5给出了不同电流密度下的沉积速度(以阴极电流效率100%计)。
表8-5 电流密度与沉积速度 镀液的最佳电流密度一定,但由于印制电板的图形多种多样,难以估计出准确的施镀面积,也就难以得出一个最佳的电流值。问题的症结在于正确测算图形电镀的施镀面积。下面介绍三种测算施镀面积的方法。 1)膜面积积分仪: 此仪器利用待镀印制板图形的生产底版,对光通过与阻挡不同,亦即底版黑色部分不透光,而透明部分光通过,将测得光通量自动转换成面积,再加上孔的面积,即可算出整个板面图形待镀面积。需指出的
是,由于底片上焊盘是实心的,多测了钻孔时钻掉部分的面积,而孔壁面积只能计算,孔壁面积S=πDH,D一孔径,H一板厚,每种孔径的孔壁面积只要算出一个;再乘以孔数即可。此法准确,但价格较贵,在国外已推广使用,国内很多大厂家也在使用。 2)称重计量法: 剪取一小块覆铜箔单面板,测量出一面的总面积,将板子在800C烘干1小时,干燥冷至室温,用天平称取总重量(Wo).在此板上作阴纹保护图形,蚀掉电镀图形部分的铜箔,清洗后按上法烘干称重,得除去电镀图形铜箔后的重量(W1),最后全部蚀刻掉剩余铜箔,清洗后按上法干燥称重,得无铜箔基体的净重(W2),按下式可算出待电镀图形的面积S: S=S0X(W0-W1)/(W0-W2) 式中:S0 覆铜箔板的面积。 (W0-W1) 电镀图形部分铜箔重量。 (W0-W2) 铜箔总重量。
CPU常见的故障现象及其排除方法
CPU常见的故障现象及其排除方法1 1、机箱的噪音: 故障现象:电脑在升级CPU后,每次开机时噪声特别大。但使用一会后,声音恢复正常。 故障分析与处理:首先检查CPU风扇是否固定好,有些劣质机箱做工和结构不好,容易在开机工作时造成共振,增大噪音,另外可以给CPU风扇、机箱风扇的电机加点油试试。如果是因为机箱的箱体单簿造成的,最好更换机箱。 2、温度上升太快: 故障现象:一台电脑在运行时CPU温度上升很快,开机才几分钟左右温度就由31℃上升到51℃,然而到了53℃就稳定下来了,不再上升。 故障分析与处理:一般情况下,CPU表面温度不能超过50℃,否则会出现电子迁移现象,从而缩短CPU寿命。对于CPU来说53℃下温度太高了,长时间使用易造成系统不稳定和硬件损坏。根据现象分析,升温太快,稳定温度太高应该是CPU风扇的问题,只需更换一个质量较好的CPU风扇即可。 3、夏日里灰尘引发的死机故障: 故障现象:电脑出现故障,现象为使用平均每20分钟就会死机一次,重新开机后过几分钟又会再次死机。 故障分析与处理:开始估计是机箱内CPU温度过高造成死机,在BIOS中检查CPU的温度,发现显示温度只有33℃。后来发现这台电脑开机时BIOS中检查的温度也就只有31℃,开机使用1小时后,温度仅仅上升2℃,当时室温在35℃左右。看来测得的CPU温度不准确。打开机箱发现散热片上的风扇因为上面积累的灰尘太多,已经转不动了,于是更换了CPU风扇,这时再开机,电脑运行了数个小时的游戏也没有发生死机现象。后来发现这块主板的温度探针是靠粘胶粘在散热片上来测量CPU温度的,而现在这个探头并没有和散热片紧密地接触,分开有很大的距离,散热片的热量无法直接传到温度探针上,测到的温度自然误差很大。更换CPU风扇时,把探针和散热片贴在一起固定牢固,这样在开机20分钟以后,在BIOS中测得的温度是45℃,之后使用一切正常。 CPU常见的故障现象及其排除方法2 4、CPU针脚接触不良导致电脑无法启动: 故障现象:一台Intel CPU的电脑,平时使用一直正常,近段时间出现问题。 故障分析与处理:首先估计是显卡出现故障。用替换法检查后,但有时又正常。最后拔下插在主板上的CPU,仔细观察并无烧毁痕迹,但发现CPU的针脚均发黑、发绿,有氧化的痕迹和锈迹(CPU的针脚为铜材料制造,外层镀金),对CPU针脚做了清除工作,电脑又可以加电工作了。 5、CPU引起的死机:
酸性光亮镀铜工艺及配方模板
酸性光亮镀铜工艺及配方 一、酸性镀铜光亮剂特点: 1、快速出光, 特好的填平度, 即使低电流密度区也可得到极高的填平度。 2、广泛的电流密度范围均可得到镜面亮度。 3、工作温度范围宽, 18—< xmlnamespace prefix ="st1" ns ="urn:schemas-microsoft-com:office:smarttags" />40℃都可得到镜面亮度。 4、镀层内应力低, 延展性好, 电阻率低, 可应用于各种不同的基体材料电镀。铁件、锌合金件、塑胶件等同样适用。 5、光亮剂对杂质容忍度高, 性能稳定, 易于控制。一般在使用一段长时间( 约800-1000安培小时/升) 后, 才需用活性碳粉处理。 6、沉积速度快。在4.5安培/平方分米的电流密度下,每分钟可镀1微米的铜层,电镀时间因而缩短。 ( 酸性镀铜溶液是一种强酸性的简单盐电镀溶液, 镀液中没有使用络合剂。) 二、电镀工艺条件: 原料范围标准 硫酸铜200-240g/L220 g/L 硫酸55-75g/L65 g/L 氯离子15-70mg/L20-40mg/L BFJ-210Mμ5-12ml/L8 ml/L BFJ-210A0.5-1.0ml/L0.6 ml/L BFJ-210B0.5-1.0ml/L0.6 ml/L 温度18-40℃24-28℃ 阴极电流密度0.5-10A/dm2 阳极电流密度 1.5-8A/dm2
搅拌空气搅拌空气搅拌 三、镀液的配制: 1、先在镀槽中( 待用缸或备用缸) 加入1/2体积蒸馏水或去离子水, 加热至40-50°。( 所用水的氯离子含量应低于70mg/L( ppm) ) 。 2、加入计算量的硫酸铜, 搅拌至完全溶解。 3、加入活性炭2g/L, 搅拌1小时后静止8小时用过滤泵, 把溶液滤入清洁的电镀槽内。加去离子水至规定体积。 4、在不断搅拌下慢慢加入计算量的化学纯硫酸, ( 注意: 此时会产生大量热能, 故需强力搅拌, 慢慢添加, 以使温度不超过60℃。添加硫酸时要特别小心, 应穿上保护衣服, 及戴上手套、眼罩等, 以确保安全) 。 5、镀液冷却至25℃时, 加入标准量氯离子。( 分析镀液中氯离子含量, 如不足应加入适量的盐酸或氯化钠, 使氯离子含量达到标准。) 6、加入光亮剂并搅拌均匀, 在正常操作规程条件下, 把镀液电解3-5安培小时/L, 便可正式试镀、生产。 四、镀液的成份及作用: 1、硫酸铜: 在镀液中提供铜离子。铜离子含量低, 容量在高电流密度区造成烧焦现象及出光慢, 铜离子过高时, 硫酸铜有可能结晶析出。 2、硫酸: 在镀液中起导电作用。硫酸含量低时, 槽电压会升高, 易烧焦; 硫酸含量太多时, 阳极易钝化, 槽电压会升高, 槽下部镀不亮, 上部易烧焦。 3、氯离子: 在镀液中起催化作用。氯离子含量过低, 镀层容易在高中电流区出现条纹, 在低电流区有雾状沉积; 氯离子含量过高时, 光亮度及填平度减弱, 在阳极上形成氯化铜, 引起阳极钝化, 槽电压会升高。 4、开缸剂。开缸转缸或添加硫酸时使用, 开缸剂不足时, 会使镀层的高中电流区出现条纹状凹凸不平, 过多时, 低电流区发雾、对光亮度无明显影响。
八种常见CPU故障现象的分析与处理
八种常见CPU故障现象的分析与处理 214小游戏http: 1、机箱的噪音: 故障现象: 电脑在升级CPU后,每次开机时噪声特别大。但使用一会后,声音恢复正常。 故障分析与处理: 首先检查CPU风扇是否固定好,有些劣质机箱做工和结构不好,容易在开机工作时造成共振,增大噪音,另外可以给CPU风扇、机箱风扇的电机加点油试试。如果是因为机箱的箱体单簿造成的,最好更换机箱。 2、温度上升太快: 故障现象: 一台电脑在运行时CPU温度上升很快,开机才几分钟左右温度就由31℃上升到51℃,然而到了53℃就稳定下来了,不再上升。 故障分析与处理: 一般情况下,CPU表面温度不能超过50℃,否则会出现电子迁移现象,从而缩短CPU寿命。对于CPU来说53℃下温度太高了,长时间使用易造成系统不稳定和硬件损坏。根据现象分析,升温太快,稳定温度太高应该是CPU风扇的问题,只需更换一个质量较好的CPU风扇即可。 3、夏日里灰尘引发的死机故障: 故障现象: 电脑出现故障,现象为使用平均每20分钟就会死机一次,重新开机后过几分钟又会再次死机。
故障分析与处理: 开始估计是机箱内CPU温度过高造成死机,在BIOS中检查CPU的温度,发现显示温度只有33℃。后来发现这台电脑开机时BIOS中检查的温度也就只有31℃,开机使用1小时后,温度仅仅上升2℃,当时室温在35℃左右。看来测得的CPU温度不准确。打开机箱发现散热片上的风扇因为上面积累的灰尘太多,已经转不动了,于是更换了CPU风扇,这时再开机,电脑运行了数个小时的游戏也没有发生死机现象。后来发现这块主板的温度探针是靠粘胶粘在散热片上来测量CPU温度的,而现在这个探头并没有和散热片紧密地接触,分开有很大的距离,散热片的热量无法直接传到温度探针上,测到的温度自然误差很大。更换CPU风扇时,把探针和散热片贴在一起固定牢固,这样在开机20分钟以后,在BIOS中测得的温度是45℃,之后使用一切正常。 4、CPU针脚接触不良导致电脑无法启动: 故障现象: 一台IntelCPU的电脑,平时使用一直正常,近段时间出现问题。 故障分析与处理: 首先估计是显卡出现故障。用替换法检查后,但有时又正常。最后拔下插在主板上的CPU,仔细观察并无烧毁痕迹,但发现CPU的针脚均发黑、发绿,有氧化的痕迹和锈迹(CPU的针脚为铜材料制造,外层镀金),对CPU针脚做了清除工作,电脑又可以加电工作了。 5、CPU引起的死机: 故障现象: 一台电脑开机后在内存自检通过后便死机。 故障分析与处理: 按[Del]键进入BIOS设置,仔细检查各项设置均无问题,然后读取预设的BIOS参数,重启后死机现象依然存在。用替换法检测硬盘和各种板卡,结果所
燃烧器常见故障现象的原因分析及排除方法
冬季在低温下进行喷漆或烘漆作业时,需要用燃烧器对烘漆房进行升温。由于冬季燃烧器的工作时间长且所用燃料(柴油)又处在低温环境下,因而是燃烧器故障的多发季节。燃烧器的点火燃烧类似于汽油机的点火工作过程,尽管它比较简单但也有其自身的特点。 一、燃烧器常见故障现象的原因分析及排除方法 1.能够正常点火但着火几十秒钟后自行熄灭 这种故障现象的典型原因是火焰传感器脏污。火焰传感器是一个光敏电阻当受光照射时其自身电阻值下降呈低阻抗状态当无光照射时电阻值上升呈高阻抗状态。燃烧器中的控制器根据火焰传感器的电阻值来判断燃烧过程是否持续若燃烧停止火焰传感器呈高阻抗则立即停止供油以防止未燃烧的柴油积存。火焰传感器探头位于燃烧器的风道内,由于冒黑烟、回火、送风尘土等原因其表面很容易脏污从而失去感光功能。检查传感器探头,必要时用酒精或清洗剂清洁其表面。 2.着火正常但排气烟色不正常 喷入燃烧器的柴油是一边混合一边燃烧的当送风量合适时雾化CO2和水蒸气排气是无色的。当送风量不足时会造成柴油不完全燃烧生成CO和碳粒从而出现排气冒黑烟现象。但如果进风量过大强大的风力可能会把来不及燃烧的油雾吹走,形成白色烟雾排出。 排气冒黑烟的常见原因是燃烧的进风门开度过小,冒白烟的见原因是进风门开度过大,这两种情况均应重新调整进风门。调整时可一边观察排气烟色一边调节风门的开度直到排气烟色接近于无色。 排气冒黑烟还有一种原因是柴油雾化不良,油雾中含有较大的液滴,不能与空气充分混合由于局部燃烧不完全而产生黑烟。造成柴油雾化不良的原因有: 1)喷嘴老化或堵塞使其雾化量能力严重下降; 2)油泵出油压力过高或过低。油泵压力过低则喷嘴出油压力低当然雾化效果差,但油泵出油压力过高,也会造成喷油压力低。这是因为,油泵的输油量与输油压力是成反比的,油压过高,出油量必然降低由于喷嘴的量孔是不变的所以喷嘴两端的压力差减小,造成喷油 常伴有冒黑烟现象,这是因为供油雾化不良。可根据排气烟色对油泵的出油压力进行调节,顺时针拧动调压螺钉压力升高出油量下降;反之压力下降出油量上升。油泵压力的正常范围是0.98~1.18MPa,使用中不可随意调节。 3.火焰不稳定常常灭火后又自动重燃 这种现象一般是燃料供应不足造成的。燃烧器工作时若柴油供给不及时断油后必然导致灭火。灭火后火焰传感器呈高阻抗状态,控制器指令停止喷油,并预吹风约10s,后开始喷油若能建立起烧器重新点燃。若开始喷射后柴油仍供应不上不能正常点火则延时约10s后控制器自动采取措施停止喷油和点火,送风电机也停止工作并点亮红色警告灯。等待1~2min后,热延时结束,可人工将红灯复位,自动开始下一次点火过程。 当燃油供给不足时,随着火焰的忽强忽弱,燃烧器中常伴有“呼哧、呼哧的声音。这时供油管道内的液可能伴有气泡使喷油压力不稳燃烧也就不稳定。另外当油管内有气泡存在时,油泵的运转阻力会随之忽大忽小,因此出现前述的“呼哧、呼哧的声音。当着火不稳时也常伴有冒黑烟现象,这是因为供油不足时油压建立不起来,使柴油雾化不好不能完全燃烧。造成着火不稳的常见原因有: 1)吸油管漏气吸油时外部空气随之进入油管内形成气泡; 2)吸油管狭窄、堵塞、压瘪,使油路不畅柴油供应不足; 3)供油系统滤网(包括吸油管进口滤网、柴油滤芯、油泵滤网等)堵塞。 冬季经常出现的情况是供油系统堵塞,因为气温低时柴油的流动性差,易析出蜡质,堵塞管道、柴油滤芯、油泵滤网、喷嘴滤网等,使供油系统不畅通,造成着火不稳或灭火。若车间
酸性镀铜光亮剂
第八章酸性镀铜及表面镀(涂)覆工艺;第一节酸性镀铜;1.概述;铜镀层呈粉红色,具有良好的延展性,导电性和导热性;1.1铜镀层的作用;在双面或多层板的生产过程中,铜镀层的作用有两方面;化学沉铜层一般0;图形电镀以铜作为Sn-Pb镀层和低应力镍镀层的底;1.2对铜镀层的基本要求;1)镀层均匀、细致、整平、无麻点、无针孔,有良好;层;2)镀层厚度均匀,板面镀层厚度 第八章酸性镀铜及表面镀(涂)覆工艺 第一节酸性镀铜 1. 概述 铜镀层呈粉红色,具有良好的延展性,导电性和导热性.铜镀层在空气中极易被氧化而失去光泽.铜镀层容易活化,实践表明,在铜镀层上电沉积其它金\属能够获得良好的结构合力,因此铜可以作为很多金属电沉积的底层.镀铜在印制线路板生产中占有很重要的位置. 1. 1铜镀层的作用 在双面或多层板的生产过程中,铜镀层的作用有两方面:作为化学沉铜的加厚镀层和作为图形电镀的底镀层. 化学沉铜层一般0。5~2微米,必须经过电镀铜后才可进行下一步加工,加厚铜是全板电镀,厚度5~8微米。 图形电镀以铜作为Sn-Pb镀层和低应力镍镀层的底层,其厚度20~25微米。 1.2对铜镀层的基本要求
1)镀层均匀、细致、整平、无麻点、无针孔,有良好外观的光亮或半光亮镀 层。 2)镀层厚度均匀,板面镀层厚度Ts与孔壁镀层厚度之比接近1:1。这需要 镀液有良好的分散能力和深镀能力。3)镀层与铜基体结合牢固,在镀后和后续工序的加工过程中,不会出现起泡、 起皮等现象。 4)镀层导电性好,这就要求镀层纯度要高。 5)镀层柔软性好,延伸率不低于10%,抗张强度20~50Kg/mm2,以保证在后 工序波峰焊(260~2700C)和热风整平(通常2320C)时,不至于因环氧树脂基材上铜镀层的膨胀系数不同导致铜镀层产生纵向断裂(环氧树脂膨胀系数1 2。8X10-5/0C,铜的膨胀系数0。68X10-5/0C)。 1.3对镀铜液的基体要求 1)有良好的分散能力和深镀能力,即使在很低的电流密度下,也能得到均匀细致的 镀层,经保证印制板的板厚孔径比比较大时,仍能达到Ts:Th接近1:1。2)电流密度范围宽,如在赫尔槽2A下,全板镀层均匀一致。
切割机常见故障现象及处理方法
切割机常见故障现象及处理方法 一机器不通电:1,检查电源是否接好及电源线是否通电2,检查保险管是否熔断,如有熔断,请更换同规格保险管3,检查机箱里面的电子元件有没有明显的烧毁痕迹,如果有,请立即关机,联系供应商协助解决4,故障表现:6A保险管熔断,打开切割机电源开关,驱动器电源指示灯不亮,可看到切割机一直显示等待状态, 2,如果2A保险管熔断,切割机不通电. 处理方法:检查保险管,若保险管完好,电笔测量保险管接线是否有电.若有电但开机没响应,可能是保险座松动间隔太大,更换测试. 以上都检查没有异常,故障没能排除,请立即关机,联系供应商协助解决。 二开机显示等待状态(Intializing please wait…):①打开机箱,打开电源开关,查看X Y Z驱动器电源指示灯是否亮: 如果各指示灯都正常: 第一:关机状态下拔出打印线,再开机,如果正常,可能是由于静电引起,接地线或者先开切割机再开电脑可解决此现象. 如果全不亮: 第一:检查切割机2A保险管是否熔断,如有熔断,更换同规格的保险管。 第二:检查驱动器连接线是否断开或松动,可在接线头部位轻压. 如果某一驱动器不亮: 第一:可能是此驱动器保险管已烧或驱动器主板故障, 请立即关机,联系供应商协助解决第二②关机状态下拔出打印线,如果正常,可能是由于静电引起,接地线或者先开切割机再开电脑可解决此现象 经以上检查测试问题不能排除,请立即关机,联系供应商协助解决. 三切割机校准 1,现象:校正数据引起的样版不准: 在切割机上割一个长宽均为200mm正方形,用尺量一下长与宽是否接近200mm,更改X和Y 的校正值把长宽尽量加到相等的长度。切割机校准应以钢尺校准。 2, 现象:大对角引起样版不准(横梁与水平(即X轴)不垂直了): 在切割机上割一个长宽均为200mm正方形,然后拿起来转90度方向放下,视偏差情况,通过调整切割机X同步带与齿轮位置来使横梁与水平(X轴)保持垂直,如果相差2mm以下可以通过X横轴上的微调来调整.注意调整好两边同步带的松紧度一致。如果相差在2mm以上,可以在X轴同步齿轮与同部带间垫一片纸片,然后移动同步带,同步带与齿轮跳一个齿位个调节. 3, 现象:软件引起的样版不准: 重装软件,重装注意设置好切割参数。 4,现象:扫描仪数据不准引起样版不准: 校正扫描仪与它的阀值参数。 5,现象:切割出来的样版不好看: 第二:检查刀片是否坏了,换一把刀试切割;第二:刀座里面的刀是否不能自如转动,如果不能,请刀套加润滑油;第三:露出的刀尖比要切割的材料厚度长0.5MM为宜;第四:刀的压力是否太大,调整刀降到刚好切断材料;第五:切割的速度是否过快,调整切割或移动速度到合适状态6,清洁塑料轮与导轨,如果塑料轮与导轨有间隔,调整塑料轮位置使塑料轮与
酸性镀铜光亮剂配方浅谈
酸性镀铜光亮剂配方浅谈 广东科斯琳酸性镀铜光亮剂配方: 此工艺用作装饰性酸性镀铜,适用广泛,不仅可用于钢铁件、锌合金工件上电镀,得到极佳的光亮度、整平性。在塑料等工件上使用也能达到同样优良的效果。 特点 1.在广阔的电流密度范围内,可获得快速镜面光亮及特高整平性。并且不容 易产生针孔及麻点。 2.镀层延展性能良好,内应力低,对镍层的结合力好,是理想的电镀层。 3.温度较高时,在低电流区不会明显降低光亮度,并在较短时间内获得高光亮镀层。 4.工作温度范围广,18-38℃都可得到较好的效果。 5.操作简便,光剂消耗量少。 6.光亮剂稳定性较高。 光亮剂加入染料,研究者对十几种染料进行了筛选,最终确认甲基紫和藏花红对扩展低DK区光亮性有效,但同时指出,加入染料后使用一些时间后,镀层易起麻点。 下述是酸铜M N型的配方 配方1:(替代M N) H1 0.2mg/l~1mg/l; SP 10mg/l~20mg/l P 5mg/l~50mg/l; GISS 10mg/l~20mg/l PN 20~40mg/l. 配方2:(替代M SP) TFS 30~60mg/l; N 0.3~0.6mg/l; P 50~80mg/l; GISS 10~20mg/l PN 20~40mg/l 配方3:(替代M SP) H1 0.2~1mg/l; BSP 10~30mg/l; P 50~100mg/l GISS 10~20mg/l; PN 20~40mg/l; H1(四氢噻唑硫铜)GISS(聚乙烯亚胺烷基化合物) PN(聚乙烯亚胺烷基盐)BSP(苯基聚二硫丙烷磺酸钠)
氯离子 过多过少的氯离子都会影响镀层的光泽和整平性。最佳浓度范围为60-90毫克/升。请先分析当地水质中的氯离子含量,再调整到最佳范围内。必要时要用纯水配制。当氯离子过少会出现树枝状条纹,过多时影响低电流区光亮度及整平性。 本人从事研究电镀添加剂配方,寻有市场者合作,转让酸铜市场成熟配方 酸铜添加剂配方只供参考更多资料登"广东科斯琳博客"
10硫酸盐光亮镀铜工艺
全光亮酸性镀铜 全光亮酸性镀液,是在硫酸盐镀铜镀液的基础成分中加入有机组合的光亮剂和添加剂。所镀得的镀层光亮、柔软、孔隙率低、镀液的整平性好,但还存在着操作温度不能高于40℃、形状复杂的零件在低电流密度区光亮较差,槽液维护比较复杂等不足之处,因此,近几年来国内许多研究单位和工厂针对这些不足作进一步研究,以期开发出更高水平的新型组合光亮剂(具有全光亮酸性的操作温度在40℃以上时稳定性能优越、光亮电流密度范围宽、光亮剂用量少、维护操作方便、镀后不需除膜等优良性能)。 (一)全光亮酸性镀铜光亮剂 有二大系列:一类是非染料体系(如传统非染料体系由M、N、SP、P组成),另一类是染料体系(如日本进口的210),现就非染料体系的组成、性能作简要的介绍。 1.含巯基的杂环化合物或硫脲衍生物 通式为:R—SH 这一类化合物,既是光亮剂又是整平剂。市售有代表性的有:乙撑硫脲(N),乙基硫脲,甲基咪唑啉硫酮,2-四氢噻唑硫酮,2-巯基苯骈噻唑,2-巯基苯骈咪唑(M)…… 2.聚二硫化合物 通式为:R1—S—S—R2 式中R1为芳香烃(苯基)、烷烃、烷基磺酸盐或杂环化合物;R2为烷基磺酸盐或杂环化合物。 这一类化合物是良好的光亮剂。市售有代表性的有:聚二硫二丙烷磺酸钠(SP),苯基聚二硫丙烷磺酸钠…… 2.聚醚化合物 通式为:(-CH2-CH20-)。 这类光亮剂实质为表面活性剂,采用的是非离子型和阴离子型。这类表面活性剂除了它的润湿作用可以消除镀铜层产生针孔和麻砂现象外,还可以提高阴极极化作用,使镀铜层的晶粒更为均匀、细致和紧密,并且还有增大光亮范围的效果。其不足之处是,因为在阴极上产生一层肉眼看不见的憎水膜,所以镀铜后必须在除膜溶液中除膜,然后方可进行,以保证镀层的结合力。市售有代表性的有:聚乙二醇(分子量为6000),OP10或OP21,乳化剂,
喷墨打印机连供系统十一种常见故障现象及解决方法
喷墨打印机连供系统十一种常见故障现象及解决方法 连续供墨系统简称连供,它是最近几年在喷墨打印机领域才出现的新的供墨方式.连续供墨系统,它采用外置墨水瓶再用导管与打印机的墨盒相连,这样墨水瓶就源源不断地向墨盒提供墨水,正所谓"连供"。连续供墨系统最大的好处是实惠,价格比原装墨水便宜很多。其次供墨量大,加墨水方便,一般一色的容量100ml,比原装墨盒墨水至少多5倍。其三连供墨水质量正稳步上升,较好的连供墨水也不会堵喷头,有断线清洗几次也就OK了,这为连供的生存发展提供了有力的保障。 连续供墨系统经典故障十一例 一、墨盒中产生气泡 故障现象: ◇连续供墨系统已正常工作几个月,而现在不能打印了。 ◇每天在正常打印前要执行很多遍清洗命令。 ◇打印的测试线总是有不固定的断线。 ◇刚开始打印的测试线正常,但在打印几页后就出现断线。 ◇打印总是缺一色(通常是黑色) ◇外置墨盒放在低位已经很长时间,现在输墨管线不进墨了。 解决方法: 以上故障现象都是由于墨盒中的墨水泡沫化所致。连续供墨系统在使用六个月后,来自墨水中的少量微小空气泡和从打印喷头进入打印墨盒的少量空气泡的积聚,会逐渐将墨水泡沫化。维护的办法并不复杂,抽出这些泡沫换之以正常的墨水即可。错误地将外置墨盒放低同样会加速墨腔泡沫的形成,即使使用了EPSON原装墨盒的连续供墨系统,同样会发生以上故障。 排除这种故障,请按以下步骤操作:
1、把连续供墨系统从打印机上拆下来,拆除后,打印墨盒不要倒置,要放在与外置墨盒相同的水平面上。如果在初安装时使用了密封塞,请将密封塞插入到墨盒底部的每个出墨口内。对于EPSON后期生产的墨盒上带有记忆芯片的机型,因出墨口装有阀门,所以不需要密封塞。在打印机上安装一个新的或正在使用的EPSON原装墨盒,这个墨盒必须是未开过孔、未注过墨、标签未损坏的原装墨盒,正品的原装EPSON墨盒在测试时能保证正确的测试结果,这一步必不可少。 2、打印墨车归位后,打印机会执行自然清洗一次,请执行喷嘴检查打印测试线。可以再重复执行清洗与打印测试线3次,直到测试线完全正常。然后打印四色或六色色块测试图(视您的机型而定,打印设置在360DPI /普通纸方式),色块测试图必须连续打印3~5张,同时观察打印机工作是否正常。如果打印有异常,可重复以上步骤。 如果执行了9~12次的清洗后,打印机仍然不正常,可让打印机休息12小时再测试。多数情况打印机可以恢复正常。 当打印机打印的色块测试图稳定正常时,可以确定您的打印机喷头是完好的。一旦得出您的打印机是正常的结论,就可以继续以下步骤来维护您的连续供墨系统。 如果您采用上述方法后仍然不能正常打印,请与EPSON维修中心联系保修或与打印机维修店联系维修。虽然此时非连续供墨系统故障,与我们联系仍然可以得到相应的帮助。在确定要交付EPSON维修中心修复前,请把有关连续供墨系统的部件和标贴拆除,并不要向EPSON提及使用第三方的墨水或连续供墨系统,仅说明您在使用EPSON原装墨盒并解释故障现象即可。 3、当您的打印机工作正常时,以下步骤可使您的连续供墨系统恢复正常。将50毫升的一次性注射器管(去掉针头)的管头插入与连续供墨系统连接的打印墨盒底部的出墨口内,稍稍倾斜注射器管,开始从墨盒中慢慢抽墨出来,这时墨水应该会通过输墨管线从外置墨盒中吸入到打印墨盒内,而后被源源不断的吸入到注射器管中。当注射器管抽满时,观察抽出的墨水和泡沫的多少就会知道是什么原因引起的连续供墨系统打印不畅了。打印机是不会把泡沫状的墨水正常打印出来的,您必须把它们通过注射器抽出来。
酸性镀铜光亮剂配方
酸性镀铜光亮剂配方 摘要:要获得良好的酸性镀铜层,关键在于选择性能优良的酸铜光亮剂,而酸铜光亮剂开发的关键在于中间体的选择和复配。本文介绍了酸铜光亮剂一般组成、常用的中间体及其作用以及复配方法。详细说明了SF-610酸性光亮镀铜的工艺配方和操作条件,通过对比试验,对SF-610酸铜光亮剂进行了综合评价,结果表明,SF-610光亮剂性能优良,能和高质量的进口酸铜添加剂相媲美。 关键词:酸性镀铜;光亮剂;中间体;复配方法;评价试验1前言 酸性镀铜工艺适用于作为装饰电镀层的中间镀层,用于电镀各种灯饰、五金工具和日用品,也广泛用于塑料电镀、PCB电镀和电铸等[1]。由于镀液成分简单、成本低、电流效率高、允许电流密度大、沉积速度快、能获得极光亮和整平的镀层,且极具装饰效果而在生产中获得了广泛的应用,特别在装饰性电镀中,采用厚铜薄镍,是应对高价镍时代的有效方法。要达到酸性镀铜良好的效果和充分发挥其长处,关键在于光亮剂[2]。 酸铜光亮剂的开发关键在于中间体的选择和复配。性能优良的光亮剂应具有光亮整平能力强、光亮范围宽、镀层应力小、延展性和韧性好、稳定且分解产物少、工作温度范围宽、不容易产生针孔麻点等特点。 近几年来染料体系的酸铜光亮剂在生产上得到广泛的应用,但生产高质量的产品仍然需要使用价格较贵的进口添加剂。这些添加剂分解产物少,填平较好,不易起针孔麻砂。 采用高质量的中间体原材料,复配出质优价廉的以染料为基础的酸铜添加剂,是国内电镀工作者的当务之急。我司通过几年的试验和实践,引进国外高特种原材料,开发出SF-610酸性镀铜系列添加剂,性价比高于同级别的进口添加剂。 酸性镀铜光亮剂中间体 酸铜光亮剂一般由载体、光亮剂、整平剂、润湿剂组成。 载体(分散剂):快速地吸附到所有受镀表面并均一地抑制电沉积,整平剂(a)和光亮剂(b)的交互作用导致产生均匀的表面光亮度。 载体在酸性镀铜电解液中,若单独加入光亮剂,对镀层的光亮效果不显著,还必须加入表面活性剂才能获得光亮和具有一定整平性的镀层[3]。常用的有聚乙二醇、AE(多胺与环氧乙烷加成物)、DAE(脂肪胺与环氧乙烷加成物)、AEO(脂肪胺聚氧乙烯醚)、辛基酚聚氧乙烯醚(OP系列)等。除作为光亮剂的载体,有些还具有润湿、分散染料、细化晶粒的作用。 光亮剂(降低低电流区电阻,帮助低电流区铜增长):光亮剂主要成分为有机磺酸盐。常用的有SP(聚二硫二丙烷磺酸钠),它可以单独作为光亮剂使用,也可以和其它含-S-S-键的光亮剂配合使用,如BSP(苯基二硫丙烷磺酸钠)、HP(醇硫基丙烷磺酸钠)、TPS(聚二甲基酰胺基磺酸钠)等。 整平剂(抑制凸出区域的沉积,扩展了光亮剂的控制范围):整平剂多为杂环化合物和染料。常用的染料有甲基紫、藏花红、噻嗪类染料、三苯甲烷染料、聚合硫代染料(碱性黄)、吩嗪类染料等。最佳的吩嗪染料是健拿绿B、健拿黑R,它们具有较高的整平能力和较宽的光亮电镀范围[4]。有的杂环化合物可以明显改善低区的光亮度和填平性能,又称低区光亮剂,如LEVELLER135Cu(聚乙烯亚胺的丙基磺酸盐)、EXP2887(聚酰胺的交链物)、JHP(交联聚酰胺水溶液)、GISS(聚乙烯亚胺烷基化合物)等。 润湿剂:(防止针孔产生,其走位性、整平性特别优良,亲水性好无憎水膜,且能有效地抑制光剂的分解,提高槽液的稳定性,是染料体系光剂及传统M、N体系光剂的优良载体,可完全取代聚乙二醇):润湿剂主要作用是减少镀层针孔麻点。如十二烷基硫酸钠、聚乙二醇等。 酸性镀铜光亮剂复配方法 染料型酸性镀铜光亮剂一般由开缸剂(Mu)、整平剂(A)、光亮剂(B)组成。
酸性电镀铜基本文件
酸性镀铜溶液的常见故障及处理方法
氯离子含量高会阻碍酸性亮铜层质量 酸性光亮镀铜溶液中含有适量的氯离子(30~90mg/L)能提高陵层的光亮度和平坦性,还能降低镀层应力。但不可过多,否则镀层失去光泽,光亮度下降,光亮范围狭窄,镀层还会产生树枝状的条皎,阳极发生钝化,电压明显上升,电流升不上去。 为幸免过多的氯离子进入镀液,配制溶液用水必须用去离子水,瓯然配方中有少量的氯离子要求,但也无需单独加入,因为配制材料即会有少量氯离子存在,差不多能满足要求。 若溶液中有过高的氯离子存在,可加入计算量的氧化亚铜予以群决。 某厂新配制的1000L酸性亮铜溶液,使用的材料除去离子水之阶,所有材料差不多上试剂级的,配成试镀时发觉镀出样板平坦性专门差,也不太光亮,还见有条纹。 依照试样情况,经多方检查,不管是配制过程,依旧使用材料均.无可疑之处,最后考虑到可能与氯离子含量有关。可能氯
离字含量过高的可能性不大,因为使用的材料差不多上试剂级的,因此吸出5L溶液,先在此小槽中镀出样板,然后加入250mg 氯化钠(当时无试剂级的盐酸)约含30mg/L氯离子,然后在同样工艺条件下再镀样板,结果表面质量明显不一样。 由此可见,凡是用试剂级材料配制的光亮酸性镀铜溶液,若试镀结果质量不够理想的,有可能是氯离子浓度太低,但补充时依旧先做小试为好,以免因其他缘故而加入过高氯离子后引出苦恼。 用水不当引起酸性镀铜层的质量故障 由水质不符合酸性光亮镀铜工艺要求而引起镀层质量或溶液遭到污染的例子专门多,在此仅举一例。 某乡办电镀厂发生一起光亮酸性镀铜的槽端电压升高、电流升不上去,接着升高电压时电流虽临时能上去,但不久又回落下来,镀层光亮区狭窄,补充光亮剂也无济于事。阳极上还蒙有一层灰白色的膜等质量故障。
热控常见故障现象及原因分析
生产培训教案 生产培训教案 培训题目:热控常见故障现象及原因分析 培训目的:交流热工软硬件常见故障及判断故障的简单方法。 内容摘要:热控故障 培训内容: 热控每个信号回路基本上可由四部分组成:传感器、信号传输、信号采集及控制设备。因此,每个热控故障现象及原因分析都可以从以上四部分进行排除判断。以下从传感器、信号采集卡件、传输介质、执行机构等四个部分分别分析热控故障现象及原因。
1、传感器 1.1、温度信号故障判断和分析 目前现场温度检测设备主要包括热电阻、热电偶、就地温度表。热电阻元件一般运用于低于200摄氏度以下的介质检测;热电偶一般运用于高于200度以上的介质测量。一般情况下,监视电机、泵轴承,油介质,闭冷水等温度采用热电阻,监视蒸汽温度、高温烟气、高温给水温度等采用热电偶元件。 1.1.1 、DCS操作员站画面上温度测点显示“U”并闪烁,表示DCS采集卡件采集到超出正常范围的信号。故障原因:(1)就地温度传感器接线松动或元件回路接地。(2)温度信号传输电缆断路。(3)DCS卡件通道故障。(4)温度元件已损坏。目前,DCS系统对于温度信号出现该类型故障都自动采用屏蔽剔除方法,将故障温度直接从逻辑运算中剔除或保持温度值不变。 温度坏点图 1.1.2、DCS操作员站画面上温度测点快速上下波动,一般情况下热电阻传感器1秒钟变化5度以上可认为该温度显示值不可信。故障原因:传感器接线
不良。目前,温度单点保护一般设置温度飞升逻辑,当出现该类型故障时,逻辑保护自动屏蔽。 1.1.3、操作员站画面上室外的高温管道温度测点突然下降。如果发生在雨天,则很大原因是温度传感器的护套内进雨水,造成温度降低。 1.1.4、操作员站画面上高温高压管道同一组相邻温度测点偏差大,主要原因可能为同一组温度元件在管道的插入深度不同,造成各支温度元件反应速度不同。电机、轴承的同一组温度测点偏差大,主要原因温度元件回路绝缘差或接触不良。 6号机组高旁阀后温度偏差大 1.2、压力(差压)信号故障判断和分析 目前现场压力信号一般采用压力变送器作为传感器。
光亮酸性镀铜的故障处理
光亮酸性镀铜的故障处理 光亮酸性镀铜是上世纪60年代由于塑料电镀的推广,重新开发了由主光亮剂、表面活性剂和整平剂三大成分组成的添加剂(如多种有机硫化物、染料及聚合高分子化合物等),使镀铜层具有镜面光泽。从而迅速普及作为钢铁件的防护一装饰性镀层的中间层。同时也用于印制板上镀铜,无需抛光直接制板。近年来,随着电镀向高科技、高品位方向发展,对光亮酸性镀铜工艺提出了更高的要求。影响光亮酸性镀铜质量故障的原因很多,要防患于未然,就必须严格执行工艺规范,平时要注意镀液管理及设备的维护;出现故障时,仔细查找原因并加以处理。本文列举了光亮酸性镀铜常见故障,产生原因及处理方法,供同仁参考。 光亮酸性镀铜-镀层粗糙和毛刺。 1.1产生原因 (1)镀液中硫酸铜浓度过高或过低; (2)阳极含磷量不足或过多; (3)镀液中混进了固体微粒或硫酸铜原料中有不溶性物质; (4)镀液中氯离子含量过高; (5)在氰化物镀铜打底的镀层上出现粗糙或毛刺; (6)微粒从压缩空气搅拌中混入。 1.2处理方法 (1)分析调整硫酸铜(150~220g/L)与硫酸(50~70g/L)质量浓度之比,一般为3:1。硫酸铜的质量浓度过高,尤其是冬季,电极上、
槽壁上会析出硫酸铜结晶,镀层产生毛刺;过低,则镀层粗糙。 (2)检验阳极的含磷量。其磷的质量分数应在0.04%~0.07%范围内。若磷的质量分数低于0.02%时,形成的膜难以阻止一价铜离子的产生,而使镀液中铜粉增多;若磷的质量分数超过0.1%时,影响铜阳极的溶解,使镀液中二价铜离子的含量下降,并生成大量阳极泥。平时要使用聚丙烯阳极袋,最好经过拉毛处理的,防止阳极泥污染镀液而造成镀层粗糙和毛刺。 (3)过滤溶液,如倒缸后仍引起毛刺,应检查过滤机、阳极袋。检查硫酸铜中有无不溶性物质,可将硫酸铜原料溶解于水中,如呈混浊状,说明有不溶物质,应改用高纯度优质硫酸铜。平时镀液最好采用连续过滤,既能消除一价铜,又能将悬浮物滤掉。如在过滤机里加入少量大颗粒活性炭,还能把镀液中有机物一并除去,使镀液更清洁。 (4)去除多余氯离子的方法很多,如锌粉法、银盐沉淀及去氯剂处理。建议采用比较经济的稀释法,即根据分析氯离子的含量,先取出部分镀液,然后加水稀释,再补充硫酸铜、硫酸和光亮剂至工艺范围。平时要采取各种措施,防止镀液中氯离子的积累。一般氯离子控制在20~80mg/L,也有控制在50~120mg/L,视镀层质量而定。 (5)检查氰化物镀铜后的工件表面,如有毛刺,过滤氰化物镀铜液。 (6)检查,并清洗送风机、管道、空气过滤器。 2光亮酸性镀铜-镀层出现针孔 2.1产生原因 (I)清洗槽、酸洗槽、活化槽、氰化物镀铜槽和酸性镀铜槽被油污
FF-510酸性光亮镀铜工艺
FF-510 酸性光亮镀铜工艺 ?用途和特点: ?快速光亮和特高的填平度、光亮度。 ?广泛的电流密度范围都可得到镜面光亮镀层,低电流密度区也可得到极高的填平性和光亮度的镀。 ?工作温度范围宽,18 -40 摄氏度都可得到较好镀层。 ?杂质容忍生气勃勃高,镀层不易起针孔、麻点、白雾。 ?操作简便,光亮剂消耗电少。 ?光亮剂稳定性特高,兼容性能好,能与任何光亮剂混用,转缸易。 ?操作简单,维护方便。材料来源广泛,成本较低。 ?工艺配方及操作条件: 范围标准 硫酸铜120 -200g /L 180g /L 硫酸40 -90g /L 70g /L 氯离子50-90mg/L 60mg/L FF-510 开缸剂2-8mg/L 4ml/L FF -510A 剂0.3~0.6ml/L 0.5ml/L FF-510B 剂0.4~0.8ml/L 0.5ml/L 温度18~ 40 摄氏度28 摄氏度 阴极电流密度 1.5~ 8A /dm2 阳极( 磷铜板) 含磷0.1~0.3% 搅拌阴极移动或空气搅拌 电压2~10V ?溶液的配制: ?在备用槽内,将谁知盘中餐量的硫酸铜用总体积1/2 的热水(已用硫酸调PH 为1 左右)溶解。 ?加入2g /L 活性炭,搅拌 1 小时,静置后用过滤机过滤溶液到镀槽内。 ?将计算量中余下的浓硫酸在搅拌条件下慢慢加到上述溶液内,加水到规定体积,搅拌并冷却到室。
?通过分析,补加盐酸,使氯离子达到标准。 ?用小电流将镀液电解3~5 小时。 ?在搅拌条件下,加入FF-510 添加剂,再电解数小时后,投入正式生产。 ?槽液的维护管理: ?槽液浓度:25 摄氏度时约25Be ?镀液温度10 -40 摄氏度。( 取中间温度20 -28 摄氏度为宜) ?阳极含磷量0.1~0.3%( 其它铜阳极会导致泥渣产生,这些泥渣很细微,难过滤,易引起镀层粗糙及麻点。) ?搅拌最好用空气搅拌,同时配合阴极摇摆。 ?镀液成分及添加剂的作用及管理。 硫酸铜:是铜离子的主要来源,过量及温度低时,易在阳极结晶沉淀出来,使电阴增大,电流下跌,低电流区光亮度及填平度下隆,含量过低,高区易烧焦,光亮剂消耗量增大。硫酸:能提高镀液导电率。但浓度太高,会使硫酸铜溶解度下降,在阳极结晶沉淀出来,光亮剂消耗大,填平度下降。硫酸太小,低电流区光亮度及填平度差,阴极溶解不良,电阴大。 氯离子:做催化剂用,开缸时添加,平时一般不加( 因为有自来水的氯离子补充,但应保持在30~120mg/L) ,如不足,高电流会有一块不亮,出现树状条纹。太高,镀层光亮及填平度差。 ?添加剂的作用和控制: 添加剂的消耗以每千安培小时计: FF-510 开缸剂:开缸、黑心缸或加硫酸铜时使用,支持光亮剂,A 、B 做出高填平光亮镀层,并消除针孔。 FF -510A :使低电流区施镀良好,A 剂过多会造成麻砂及针孔,高区烧焦,可加入B 剂抵消。
镀铜常见故障
(1)镀层发花或发雾。 1镀前处理不良,零件表面有油;清洗水或镀液中有油; 2阳极面积太小或太短; 3镀液中聚二硫二丙烷磺酸钠太多; 4有机杂质太多;光亮剂没有搅均或十二烷基硫酸钠太少等会造成镀层发花或发雾。 分析故障,要先易后难,逐条进行。例如先搅拌一下镀液,检查一下阳极面积,这样就可以排除由于光亮剂没有搅均和阳极面积太小而造成的故障。同时也可从现象进行分析,假使发花现象仅出现在挂具下部的零件上,上部零件不发花,那就可能是阳极板太短而产生的,经检查并换上足够长的阳极板后,观察发花现象是否消失。倘若发花现象出现在零件的向下面或挂具上部的零件上,那可能是清洗水或镀液中有油而引起的。光亮硫酸盐镀铜对油污特别敏感,不管是毛坯上的油在镀前处理时未除净,还是镀前的清洗水或镀液中有微量的油,甚至是操作人员不干净的手摸了摸镀前的零件,都会使镀铜层发花。假使原来镀铜出现发花或发雾,采用良好的前处理后,镀层不出现发花或发雾现象厂,证明原来的镀前处理有问题,应加强镀前处理。否则,就应检查镀液中的情况。 镀液中是否有油,不但可以从现象进行判断,同时还可以通过小试验来了解。取一定量的故障液做烧杯试验,先要使阴极样板上能看到类似于生产中的故障现象,接着对试验液进行除油处理,另外再取相同体积的故障液进行双氧水一活性炭处理,然后分别进行试验(试验液中需补充各种光亮剂)。若用双氧水一活性炭处理过的镀液仍有发花或发雾,而经过除油处理的镀液不再出现发花或发雾,那么原镀液中有油,应进行除油处理。假使用双氧水一活性炭处理后的镀液和经过除油处理的镀液一样,都不出现发花或发雾,那么原镀液可能是有机杂质过多。只要用双氧水一活性炭处理镀液就可以了。 镀液中聚二硫二丙烷磺酸钠是否过多,只要向试验液中添加其他光亮剂,并适当稀释试验液后进行试验,假使经这样处理后镀层不发花(或不发雾),而且光亮度较好,这时可能原镀液中聚二硫二丙烷磺酸钠太多,应调整光亮剂的比例。 在含有十二烷基硫酸钠的镀铜液中,有时由于其含量过低,也会导致镀层出现发花现象。这类镀液若镀层发花,可直接向镀液中加入O.05g/L十二烷基硫酸钠看看现象,假使加入后镀层仍发花,那就不是十二烷基硫酸钠含量太少造成的。
常见故障现象及处理方法
4、采用了串联式PWM 充电主电路,使充电回路的电压损失较使用二极管的充电电路降低近一半, 充电效率较非PWM 高3%-6%,增加了用电时间;过放恢复的提升充电,正常的直充,浮充自动控制方式使系统有更长的使用寿命;同时具有高精度温度补偿。 5、直观的LED 发光管指示当前电瓶状态,让用户了解使用状况。 6、所有控制全部采用工业级芯片,能在寒冷、高温、潮湿环境运行自如。同时使用了晶振定时控制,定时控制精确。 7、使用了直观的LED数码管显示设置,一键式操作即可完成所有设置,定时时间与数码管显示数字一一对应,显示更直观。 8、利用先进电源技术,大大提高单位面积的有效功率,结构更紧凑。 9、采用大口径、大间隔接线端子,可安装最大6mm2 导线,导线间隔9.5 mm,增强了绝缘性能及安装可靠性,不易滑丝。 ■控制器面板图:
■ 系统说明: 本控制器专为太阳能直流供电系统、太阳能直流路灯系统设计,并使用了专用电脑芯片的智能化控制器。采用一键式轻触开关,完成所有操作及设置。具有短路、过载、独特的防反接保护,充满、过放自动关断、恢复等全功能保护措施,详细的充电指示、蓄电池状态、负载及各种故障指示。本控制器通过电脑芯片对蓄电池的端电压、放电电流、环境温度等涉及蓄电池容量的参数进行采样,通过专用控制模型计算,实现符合蓄电池特性的放电率、温度补偿修正的高效、高准确率控制,并采用了高效PWM 蓄电池的充电模式,保证蓄电池工作在最佳的状态,大大延长蓄电池的使用寿命。具有多种工作模式、输出模式选择,满足用户各种需要。 ■ 安装及使用: 1.控制器的固定要牢靠。 外形尺寸:133 X 70(mm) 安装孔尺寸:126 X 50(mm) 2.导线的准备:建议使用多股铜芯绝缘导线。先确定导线长度,在保证安装位置的情况下, 尽可能减少连线长度,以减少电损耗。按照不大于4A/mm 2 的电流密度选择铜导线截面积, 将控制器一侧的接线头剥去5mm 的绝缘。 3.将蓄电池连线接入控制器上蓄电池的接线端子,注意+,—极,不要反接。如果连接正确, 指示灯(2)应亮,可按按键来检查。否则,需检查连接对否。如发生反接,不会烧保险及损 坏控制器任何部件。保险丝只作为控制器本身内部电路损坏短路的最终保护。 4.连接光电池导线,先连接控制器上光电池的接线端子,再将另外的端头连至光电池上,注 意+,—极,不要反接,如果有阳光,充电指示灯应亮。否则,需检查连接对否。 5.将负载的连线接入控制器上的负载输出端,注意+,—极,不要反接,以免烧坏用电器。 ■使用说明: 充电及超压指示:当系统连接正常,且有阳光照射到光电池板时,充电指示灯(1)为绿色常亮,表示系统充电电路正常;当充电指示灯(1)出现绿色快速闪烁时,说明系统过电压,处理见故障处理内容;充电过程使用了PWM 方式,如果发生过放动作,充电先要达到提升充电电压,达到后立即停充,而后直到降至充电返回电压,恢复充电,达到直充电压后,维持30min 。如果没有发生过放,将不会有提升充电方式,以防蓄电池失水。这些自动控制过程将使蓄电池达到最佳充电效果并保证或延长其使用寿命。 蓄电池状态指示:蓄电池电压在正常范围时,状态指示灯(2)为绿色常亮;充满后状态指示灯为绿色闪;当电池电压降低到过放返回电压时状态指示灯变成橙黄色;当蓄电池电压继续降低到欠压时,状态指示灯(2)变为红色,此时系统禁止启动负载,并关闭已经启动的负载输出,如果电压进一步降低到过放电压,此时红灯闪,提醒用户及时补充电能。当电池电压恢复到正常工作范围内时,直到状态指示灯(2)变为(绿色),将自动使能输出开通动作; 负载指示:当负载开通时,负载指示灯(3)为绿色常亮。负载关闭时,负载指示灯(3)熄灭,负载过载时,负载指示灯(3)绿色慢闪,负载短路时,负载指示灯(3)绿色快闪。 ■工作模式设置: 按键定义:短键:按下按健时间 < 1.5 秒,图示▲;长键:按下按健时间 > 1.5,图示●; 光控+延时方式:启动过程参考同纯光控(不同之处在于必须从白天进入夜晚才能启动,如果系统