机床主轴拉刀机构故障解决

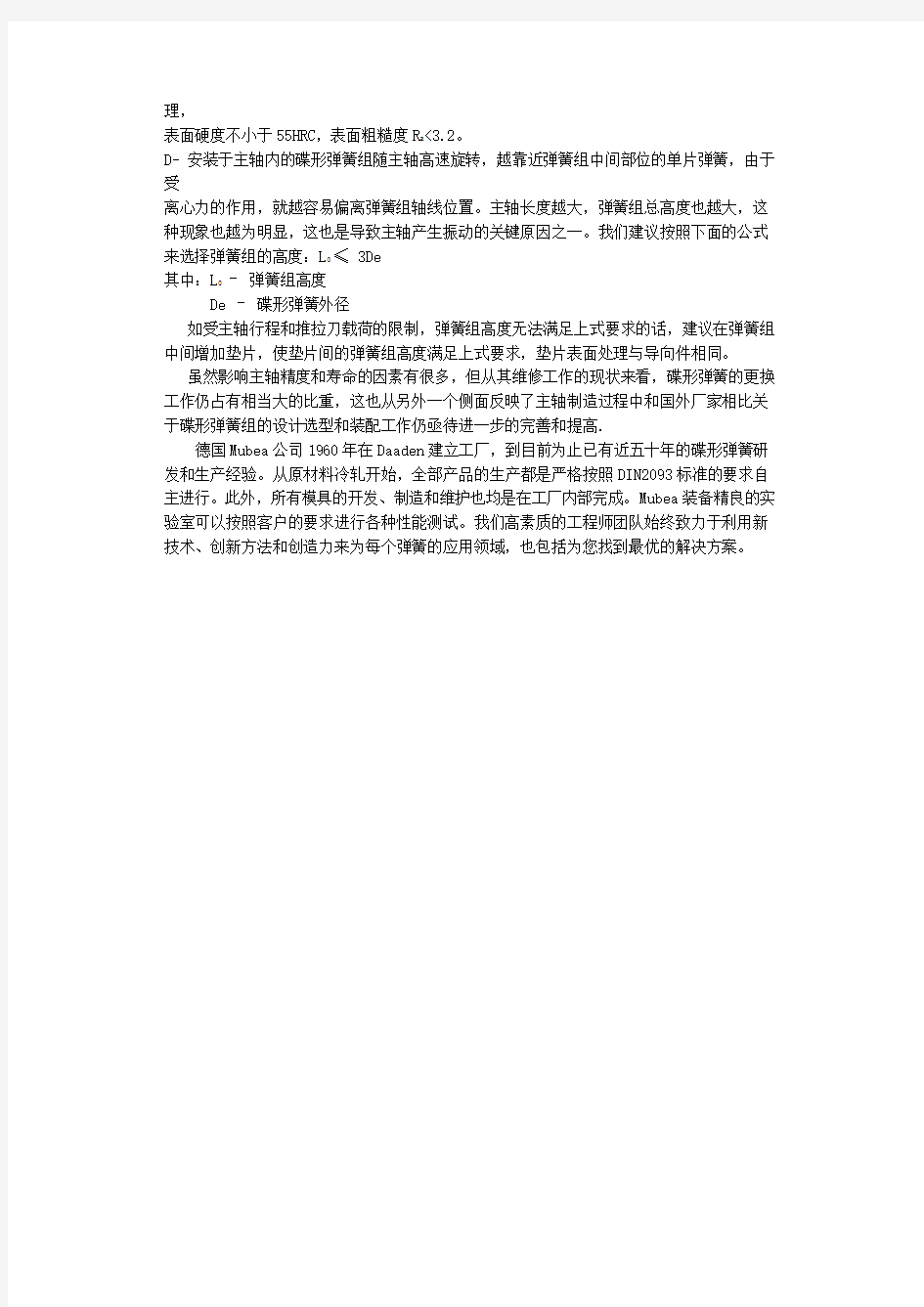
机床主轴拉刀机构的解决方法
在不断增长的竞争压力下,现代化机床的生产效率和加工精度的要求被不断提高,主轴的转动越来越快,主轴的高速化是目前精密机械的发展趋势,同时机床的稳定性和使用寿命也相应的变得越来越重要,这些变化直接导致了对机床组件要求的提高。作为主轴关键部件的碟形弹簧组,它的合理选型及装配可以提高机床的使用效率,减少主轴的维修频率.碟形弹簧具有小变形大承载力的特点,主轴拉刀机构采用碟形弹簧提供拉刀力,有效地解决了刀具转动过程中夹具系统夹持力不足的缺点。从国内主轴维修的现状来看,碟形弹簧失效主要表现为断裂和破碎,也就是说,在碟形弹簧未达到其设计的疲劳寿命时,弹簧已出现开裂或断裂现象。究其原因,主要有下述几个方面:
1. 原材料选取
按照新版碟形弹簧国家标准 GB1972 – 2005,碟簧材料可以选择 60Si2Mn 或 50CrV4。从原材料特性来看,硅锰钢系列材料中的硅能固溶于铁素体和奥氏体中,可提高钢的硬度、强度、弹性极限、屈强比和疲劳强度,还能提高材料的回火稳定性和抗氧化性;锰能提高材料的淬透性。但硅含量容易产生石墨化现象和增加表面脱碳倾向,并在钢种易生成硅酸盐夹杂物,该夹杂物在晶界析出,易导致淬火开裂现象。即便淬火过程中没有出现开裂,其开裂倾向也会在弹簧加载过程中逐渐放大,导致弹簧寿命降低,最终失效原因为开裂或碎裂。50CrV4中铬和钒能提高钢的韧性、强度和弹性极限,降低钢的过热敏感性和脱碳倾向,从而改善了碟簧表面质量,提高材料的疲劳强度。其淬透性也比硅锰钢要好。此外铬钒钢回火稳定性较高,500℃ - 550℃回火后仍有较高的强度和弹性极限,工作环境允许达200℃。因此,铬锰钢是碟形弹簧材料的首选钢种,也是 DIN2093标准规定的标准原材料。作为大型碟形弹簧生产厂德国Mubea公司原材料的冷轧和热处理是在公司内进行的,这样最大可能的保证了原材料质量.
2. 加工精度
随着转数的提高碟形弹簧的加工精度直接影响主轴的稳定性和使用寿命.过大的弹簧
内径造成主轴高速转动时弹簧过多的向外滑动(如图),由此形成的离心力(F=mω2r) 相应变大,轴承和主轴的负担加重.较小的平面度和平行度保证弹簧组内单片弹簧受力均匀,弹簧
横向位移变小,弹簧组的垂直性更好.对于碟形弹簧在主轴拉刀机构的应用Mubea公司专门开发了高精度碟形弹簧.通过它的特殊边缘结构导向杆和弹簧之间的摩擦被降低, 弹簧疲劳寿命也相应增加.
3. 装配
作为一种相对较新的弹簧形式,碟形弹簧的特性和装配要求还不太为国内机床行业的客户所熟知。我们在帮助客户做选型工作的时候,通常会提醒客户在装配过程中注意以下问题:
A- 碟形弹簧组装配时,弹簧组两端要保证弹簧外径(而不是内径)与安装空间附件相接触,如受设计要求所限,至少要保证受力端是弹簧外径与安装空间附件相接触。
B- 导向杆或导向套与弹簧组间保留一定间隙,具体要求请参照Mubea碟形弹簧手册第50
页图
3.20和表3.2,也可查询DIN2093标准或中国国家标准GB1972–2005。
C- 导向件导向表面以及与碟形弹簧组两端相接触的安装空间附件表面须做硬化和抛光处
理,
表面硬度不小于55HRC,表面粗糙度R a<3.2。
D- 安装于主轴内的碟形弹簧组随主轴高速旋转,越靠近弹簧组中间部位的单片弹簧,由于受
离心力的作用,就越容易偏离弹簧组轴线位置。主轴长度越大,弹簧组总高度也越大,这种现象也越为明显,这也是导致主轴产生振动的关键原因之一。我们建议按照下面的公式来选择弹簧组的高度:L0 ≤ 3De
其中:L0 –弹簧组高度
De –碟形弹簧外径
如受主轴行程和推拉刀载荷的限制,弹簧组高度无法满足上式要求的话,建议在弹簧组中间增加垫片,使垫片间的弹簧组高度满足上式要求,垫片表面处理与导向件相同。
虽然影响主轴精度和寿命的因素有很多,但从其维修工作的现状来看,碟形弹簧的更换工作仍占有相当大的比重,这也从另外一个侧面反映了主轴制造过程中和国外厂家相比关于碟形弹簧组的设计选型和装配工作仍亟待进一步的完善和提高.
德国Mubea公司1960年在Daaden建立工厂,到目前为止已有近五十年的碟形弹簧研发和生产经验。从原材料冷轧开始,全部产品的生产都是严格按照DIN2093标准的要求自主进行。此外,所有模具的开发、制造和维护也均是在工厂内部完成。Mubea装备精良的实验室可以按照客户的要求进行各种性能测试。我们高素质的工程师团队始终致力于利用新技术、创新方法和创造力来为每个弹簧的应用领域,也包括为您找到最优的解决方案。
加工中心主轴松拉刀机构的基本原理
加工中心主轴拉刀机构的基本原理 1-拉钉2-拉杆3-带轮4-碟形弹簧5-锁紧螺母6-调整垫7-螺旋弹簧8-活塞9、10-行程开关11-带轮12-端盖13-调整螺钉 主轴内部有刀杆的自动夹紧机构,它由拉杆2和头部的4个钢球、碟形弹簧4、活塞杆8和螺旋弹簧7组成。夹紧时活塞8的上端无油压,弹簧7使活塞8向上移至图示位置。碟形弹簧4使拉杆2上移至图示位置,钢球进入到刀杆尾部拉钉1的环形槽内,将刀杆拉紧。放松时,液压使活塞8下移,推拉杆2下移。钢球进入主轴后锥孔上部的环形槽内,把刀杆放开。当机械手把刀杆从主轴中拔出后,压缩空气通过活塞和拉杆的中孔,把主轴锥孔吹净。 行程开关9和10用于发出夹紧和放松刀杆的信号。 刀杆夹紧机构用弹簧、液压夹紧,液压放松,以保证停电刀杆不会松脱。夹紧时活塞8和拉杆2的上端之间有一定间隙(约4mm),以防止主轴旋转时端面摩擦。 机床采用锥柄刀具,锥部的尾端安装有拉钉1,有拉杆2通过4个5/16in 的钢球拉住拉钉1的凹槽,使刀具在主轴锥孔内定位及夹紧。拉紧力由碟形弹簧4产生。碟形弹簧共有34对68片。拉紧刀具的拉紧力等于10kN,最大为13kN。 换刀时,活塞8的行程为12mm。前进约4mm后,它开始推动拉杆2,直到钢球进入主轴锥孔上部的Φ37mm的环槽。这时钢球已不能约束拉钉的头部。拉杆继续下降,拉杆的a面与拉钉的顶端接触,把刀具从主轴锥孔中推出。行程开关10发出信号,机械手即可将刀具取出。修磨调整垫块6就可保证当活塞的行程到达终点时拉杆的a面与拉钉的顶端接触。 活塞8推动拉杆把刀具推出,故活塞的最大推力应等于13kN加弹簧7的弹力。 4个钢球与拉钉锥面、主轴孔表面、钢球所在孔的接触应力是相当大,因此对这些部位的材料及表面硬度要求很高。4个钢球所在孔应在同一平面内,为了保证钢球受力的一致性。 1/ 1
加工中心主轴松拉刀机构的基本原理
加工中心主轴拉刀机构的基本原理 1-拉钉 2-拉杆3-带轮 4-碟形弹簧5-锁紧螺 母6-调整垫7-螺旋弹簧8-活塞 9、10-行程开关 11-带 轮12-端盖 13-调整螺钉 主轴内部有刀杆的自动夹紧机构,它由拉杆2和头部的4个钢球、碟形弹簧4、活塞杆8和螺旋弹簧7组成。夹紧时活塞8的上端无油压,弹簧7使活塞8向上移至图示位置。碟形弹簧4使拉杆2上移至图示位置,钢球进入到刀杆尾部拉钉
1的环形槽内,将刀杆拉紧。放松时,液压使活塞8下移,推拉杆2下移。钢球进入主轴后锥孔上部的环形槽内,把刀杆放开。当机械手把刀杆从主轴中拔出后,压缩空气通过活塞和拉杆的中孔,把主轴锥孔吹净。 行程开关9和10用于发出夹紧和放松刀杆的信号。 刀杆夹紧机构用弹簧、液压夹紧,液压放松,以保证停电刀杆不会松脱。夹紧时活塞8和拉杆2的上端之间有一定间隙(约4mm),以防止主轴旋转时端面摩擦。 机床采用锥柄刀具,锥部的尾端安装有拉钉1,有拉杆2通过4个5/16in的钢球拉住拉钉1的凹槽,使刀具在主轴锥孔内定位及夹紧。拉紧力由碟形弹簧4 产生。碟形弹簧共有34对68片。拉紧刀具的拉紧力等于10kN,最大为13kN。 换刀时,活塞8的行程为12mm。前进约4mm后,它开始推动拉杆2,直到钢球进入主轴锥孔上部的Φ37mm的环槽。这时钢球已不能约束拉钉的头部。拉杆继续下降,拉杆的a面与拉钉的顶端接触,把刀具从主轴锥孔中推出。行程开关10发出信号,机械手即可将刀具取出。
修磨调整垫块6就可保证当活塞的行程到达终点时拉杆的a面与拉钉的顶端接触。 活塞8推动拉杆把刀具推出,故活塞的最大推力应等于13kN加弹簧7的弹力。 4个钢球与拉钉锥面、主轴孔表面、钢球所在孔的接触应力是相当大,因此对这些部位的材料及表面硬度要求很高。4个钢球所在孔应在同一平面内,为了保证钢球受力的一致性。
数控机床故障诊断与维修试题
数控机床故障诊断与维修试题 一、填空题(每空1分,共20分) 1、滚珠丝杠螺母副,按滚珠返回的方式不同可以分为(内循环式)和(外循环式)两种。 2、导轨副的维护一般包括(导轨副的润滑)、(滚动导轨副的预紧)和(导轨副的防护)。 3、数控机床自动换刀装置的形式有(回转刀架换刀)、(更换主轴头换刀)和(带刀库的自动换刀)。 4、数控机床上常用的刀库形式有(直线式刀库)、(盘式刀库)、(链式刀库)和(密集形格子式刀库)。 5、刀具常用交换方式有(顺序选刀)和(任意选刀)两类。 6、滚珠丝杠螺母副的润滑油为(一般机油或90~180#透平油、140#或N15主轴油),而润滑油一般采用(锂基润滑脂)。 7、数控机床按控制运动轨迹可分为点位控制、(直线控制)和(轮廓控制)等几种。 8、数控机床的自动换刀装置中,实现(刀库)和机床(主轴)之间传递和装卸刀具的装置称为刀具交换装置。 二、选择题(每小题2分,共20分) 1、数控车床床身中,排屑性能最差的是(A)。 A、平床身 B、斜床身 C、立床身 2、一般数控铣床是指规格(B)的升降台数控铣床,其工作台宽
度多在400mm以下。 A、较大 B、较小 C、齐全 D、系列化 3、采用数控机床加工的零件应该是(B)。 A、单一零件 B、中小批量、形状复杂、型号多变的零件 C、大批量零件 4、数控机床四轴三联动的含义是( B)。 A、四轴中只有三个轴可以运动 B、有四个控制轴,其中任意三个轴可以联动 C、数控系统能控制机床四轴运动,其中三个轴能联动 5、数控机床主轴锥孔的锥度通常为7:24,之所以采用这种锥度是为了(C)。 A、靠摩擦力传递扭矩 B、自锁 C、定位和便于装卸刀柄 D、以上几种情况都是 6、目前,在我国数控机床的自动换刀装置中,机械手夹持刀具的方法多采用( A) A、轴向夹持 B、径向夹持 C、法兰盘式夹持 7、数控机床导轨按接触面的摩擦性质可分为滑动导轨、滚动导轨和(B)导轨三种。 A、贴塑B、静压C、动摩擦D、静摩擦 8、数控机床自动选择刀具中任选刀具的方法是采用(A)来选刀换刀。 A、刀具编码 B、刀座编码 C、计算机跟踪
加工中心电主轴
D 1 D 2D 3D 4 D L1L L2 轴端连接 N-d1d2×L3 加工中心电主轴 Machining centre High Frequency Spindles 主轴型号 spindle type 转速 speed (r/min) 电机 Motor 润滑 Lub 冷却 Cool 轴端连接 Joint of nose 轴承型号 Bearings type 特点 character 额定功率KW 电压 V 电流A 频率 Hz SDS80-20-24Z/1.5 24000 1.5 220 5.4 400 油脂 水冷 ISO20锥孔 2×30BNR P4 1×7004C P4 带传感器及松拉刀机构 SDS80-20-30Z/1.8 30000 1.8 220 6.4 500 油脂 水冷 ISO20锥孔 2×30BNR P4 1×7004C P4 带传感器及松拉刀机构 SDS110-30-18Z/3.2 18000 3.2 380 6.9 600 油脂 水冷 BT30锥孔 2×35BNR P4 1×25BNR P4 带传感器及松拉刀机构 SDS110-30-24Z/4.5 24000 4.5 380 9.2 800 油脂 水冷 BT30锥孔 2×35BNR P4 1×25BNR P4 带传感器及松拉刀机构 SDS110-30-30Z/5.5 30000 5.5 380 11.5 1000 油脂 水冷 BT30锥孔 2×35BNR P4 1×25BNR P4 带传感器及松拉刀机构 SDS150-40-12Z/6.0 12000 6.0 380 11.9 400 油脂 水冷 ISO40锥孔 2×60BNR P4 2×40BNR P4 带传感器及松拉刀机构 SDS150-30-18Z/7.5 18000 7.5 380 14.9 600 油脂 水冷 BT30锥孔 2×60BNR P4 2×40BNR P4 带编码器、传感器及松 拉刀机构 特别说明:本公司可以为用户设计各种加工中心并联机床用电主轴
数控机床主轴部件结构
数控机床主轴部件结构 主轴部件是数控机床的核心部件,其运转精确度、耐磨性能、防震性能、机械强度等都会影响到工件加工的质量,再加上操作过程中还会有环境的影响以及人为因素的影响,工件加工的质量就更难得到保证。所以要从可控的方面着手,将一切可控因素都调整到位,比如数控机床的主轴结构设计以及主轴结构的日常维护等。 目前所使用的数控机床类型主要包括数控车床、数控铣床以及工件加工中心。 1.数控车床主轴部件结构特点 (1)主轴的主体结构是一个空心阶梯轴。 (2)主轴的前面部分主要由法兰盘和专门的卡盘结构组成。 (3)主轴的后面部分放置回转油缸。 (4)主轴空心部分用于设置油缸的活塞杆。 (5)车床的传动装置主要有齿轮传动、传送带传送以及齿轮-传送带组合传动等方式。 (6)驱动器主要作用是连接电动机,驱动数控车床的运转。 (7)光电脉冲编码器,用于测量主轴的转动速度,并
及时反馈信息至数控系统。 (8)回转油缸的主要作用是通过调整液压来控制卡盘装置与法兰盘的结合与分离。 2.数控铣床主轴部件结构特点 (1)同数控车床一样,主轴的中心是空心的。 (2)主轴的前面部分是一个比例为7:24的锥型孔洞,并且在端面上设有一对专门的主轴转矩检测装置将主轴转矩数据传输给铣刀。 (3)主轴的后面部分设有液压缸装置用于放松铣刀。 (4)主轴中间的空心部分用于弹簧的安装、以及铣刀固定刀爪的安装等。 (5)主轴的传动装置主要是齿轮传动,而且是变速传动。 (6)电气结构与数控车床相似,驱动器用于连接电动机,驱动数控铣床的运转;光电脉冲编码器,用于测量主轴的转动速度,并及时反馈信息至数控系统;液压缸的主要作用是通过调整液压来控制回路。 3.工件加工中心主轴部件结构特点 工件加工中心主轴部件的大致结构与数控铣床相类似,唯一不同的地方在于工件加工中心自带刀库和自动换刀的装置,自动化程度相对较高,在控制结构上与数控铣刀会有所不同,具体表现在:
OTT拉刀机构在高速电主轴中的应用
OTT拉刀机构在高速电主轴中的应用 作者:徐成勇 标准HSK拉刀装置几乎适用于所有场合。特别是在要 求快速、频繁进行刀具更换的汽车制造业中,特种涂层的拉杆机构已经被多次证明了其价值所在。 模块化的拉刀装置 OTT公司生产的通用拉刀装置系统面向全世界,可用于各种标准轮廓的SK接口(大斜度锥柄7:24)以及现代化的HSK接口(空心轴锥柄)。由于采用了模块化的结构,OTT-JAKOB拉刀装置的夹紧系统几乎可应用于所有的场合,能够满足用户的不同需求,并能够按照用户的不同要求提供机床主轴动力拉刀系统。SK拉刀装置系统由带有支撑套的卡爪、一个整体倍力放大机构的牵引头及一个液压或者气动的推刀机构组成,且需要一个旋转组合装置来用于内冷却、或空气的传输。HSK拉刀装置系统有相同的模块化结构,但不同于SK动力拉杆头,它们由HSK夹紧刀柄装置和一个不带倍力放大机构的牵引头组成。 HSK的发展趋势 实际上,SK拉刀装置在世界范围内的使用是非常普遍的。由于新型刀柄需要昂贵的投资,在SK工具比较便宜的情况下,中、小型公司一般不会轻易更换新的刀具接口。 尽管如此,使用HSK接口的电动主轴的销量仍在不断增长,这是因为其刀柄轴向的凸缘面接触和锥形面配合接触的连接刚度高,从而可以获得高精度的定位和重复性好的定位精度。 由于HSK刀架的质量较小且尺寸适宜,使得刀具的操纵变得更加容易。HSK系统的刀具更换快、转速较高,代表了高速应用场合的最新技术水平。
SK动力拉杆系列 OTT公司可提供SK30、SK40、SK50及SK60各种标准尺寸的带刀架的大斜度锥面卡爪,所有符合DIN 69871/72(1SO 7388/1/2类型A)、ANSIB5.50-78(1SO 7388/1/2类型B)和MAS403-1982(PTl和PT2)标准尺寸的刀具都可使用。OTT卡爪的特点是,其主轴的内轮廓是统一的,与各个标准无关。因此,机床及主轴制造商无需对主轴设计做任何更改就能够按照客户的需求交付产品。 SK牵引头 图2 大斜度锥面的倍力放大机构 SK牵引头在最小的空间内可以得到最大的拉入力。OTT公司的牵引头使用了一个传动装置(图2),该装置可以
数控机床故障诊断与维修现状和发展趋势
数控机床故障诊断与维修现状和发展趋势 数控机床故障诊断数控机床是个复杂的系统,组成数控机床的这些部分,由于种种原因,不可避免地会发生不同程度、不同类型的故障,导致数控机床不能正常工作。故障诊断是进行数控机床维修的第一步,它不仅可以迅速查明故障原因,排除故障,也可以起到预防故障发生与扩大的作用。 一、数控机床故障诊断的基本方法 数控设备是一种自动化程度较高,结构较复杂的先进加工设备,是企业的重点、关键设备。要发挥数控设备的高效益,就必须正确的操作和精心的维护,才能保证设备的利用率。正确的操作使用能够防止机床非正常磨损,避免突发故障;做好日常维护保养,可使设备保持良好的技术状态,延缓劣化进程,及时发现和消灭故障隐患,从而保证安全运行,故障诊断是进行数控机床维修的第一步,它不仅可以迅速查明故障原因,排除故障,也可以起到预防故障的发生与扩大的作用。一般来说,数控机床的故障诊断方法主要有以下几种: (一)常规诊断法 对数控机床的机、电、液等部分进行的常规检查,通常包括:(1) 检查电源的规格(包括电压、频率、相序、容量等)是否符合要 求;(2)CNC、伺服驱动、主轴驱动、电机、输入/输出信号的连接是否正确、可靠;(3)CNC、伺服驱动等装置内的印制电路板是否安装牢固,接插部位是否有松动;(4)CNC、伺服驱动、主轴驱动等部分的设定端、电位器的设定、调整是否正确;(5)液压、气动、润滑部件的油压、气压等是否符合机床要求;(6)电器元件、机械部件是否有明显的损坏。(二)状态诊断法 通过监测执行元件的工作状态判定故障原因。在现代数控系统中伺服进给系统、主轴驱动系统、电源模块等部件主要参数的动、静态检测,及数控系统全部输入输出信号包括内部继电器、定时器等的状态,也可以通过数控系统的诊断参数予以检查。(三)动作诊断法通过观察、监视机床的实际动作,判断动作不良部位,并由此来追溯故障源。 (四)系统自诊断法 这是利用系统内部自诊断程序或专用的诊断软件,对系统内部的关键硬件以及系统的控制软件进行自我诊断、测试的诊断方法。主
40#拉刀机构的设计及控制
摘要 40#刀柄拉刀机构为小型数控机床主轴内部的自动拉紧与自动松开刀具的机构。通过预压缩碟形弹簧,产生足够的向上的拉刀力。当需要换刀时,数控系统发出松刀信号,通过控制液压系统的电磁换向阀,液压系统将压力油通入主轴上端的油缸上腔,油缸活塞推动拉刀部件向下移动,继续压缩碟形弹簧,刀柄向下运动,通过与换刀机械手配合完成换刀。在油缸上端,有两个接近开关检测油缸活塞是否到位;如果油缸活塞没有到位,那么两个接近开关就不会发出信号,数控系统就不能继续执行下一个程序,以确保数控机床的安全。此外,拉杆是空心的,为的是每次换刀时要用压缩空气清洁主轴孔和刀具锥柄,以保证刀具的准确安装。 关键词:40#刀柄;拉刀机构;PLC;控制
ABSTRACT 40th shaft tool for small spindle of CNC machine tools, automatic tensioning and automatic release tool within the institution. By pre-compressed disk spring, generate enough upward broach. When tool change is needed, loose knife signal from the CNC system through control solenoid valve in hydraulic system, hydraulic system pressure on oil fuel tank into the upper end of the spindle, and oil moves the piston push broach part down, continue to compress disk spring, shaft moving down, through tool change manipulator and complete tool change. In the top of the cylinder, there are two proximity sensors detect whether the cylinder piston in place if cylinder Pistons are not yet in place, then the two proximity does not signal, NC system cannot continue to perform the next procedure, to ensure the safety of CNC machine tools. In addition, the levers are hollow, so that when the tools change spindle hole and compressed air to clean the tool taper shank to ensure accurate installation of the tool. Keywords:40#knife hilts;broachmechanism;PLC;Control
数控机床故障诊断与维修基本概念(上)
数控机床故障诊断与维修第1章数控机床故障诊断与维修的基本概念 1.1 数控机床故障诊断与维修的意义 一、数控机床的组成 数控机床由数控装置、伺服驱动装置、检测反馈装置和机床本体四大部分组成,再加上程序的输入/输出设备、可编程控制器、电源等辅助部分。 1. 数控装置(数控系统的核心)由硬件和软件部分组成,接受输入代码经缓存、译码、运算插补)等转变成控制指令,实现直接或通过PLC对伺服驱动装置的控制。 2. 伺服驱动装置是数控装置和机床主机之间的联接环节,接受数控装置的生成的进给信号,经放大驱动主机的执行机构,实现机床运动。 3. 检测反馈装置是通过检测元件将执行元件(电机、刀架)或工作台的速度和位移检测出来,反馈给数控装置构成闭环或半闭环系统。 4. 机床本体是数控机床的机械结构件(床身箱体、立柱、导轨、工作台、主轴和进给机构等。 二、数控机床故障诊断 1.故障的基本概念 故障——数控机床全部或部分丧失原有的功能。 故障诊断——在数控机床运行中,根据设备的故障现象,在掌握数控系统各部分工作原理的前提下,对现行的状态进行分析,并辅以必要检测手段,查明故障的部位和原因。提出有效的维修对策。 2.故障的分类 1)从故障的起因分类 关联性故障——和系统的设计、结构或性能等缺陷有关而造成(分固有性和随机性)。 非关联性故障——和系统本身结构与制造无关的故障。 2)从故障发生的状态分类 突然故障——发生前无故障征兆,使用不当。 渐变故障——发生前有故障征兆,逐渐严重。 3)按故障发生的性质分类 软件故障——程序编制错误、参数设置不正确、机床操作失误等引起。 硬件故障——电子元器件、润滑系统、限位机构、换刀系统、机床本体等硬件损坏造成。 干扰故障——由于系统工艺、线路设计、电源地线配置不当等以及工作环境的恶劣变化而产生。 4)按故障的严重程度分类
机床主轴拉刀机构故障解决
机床主轴拉刀机构的解决方法 在不断增长的竞争压力下,现代化机床的生产效率和加工精度的要求被不断提高,主轴的转动越来越快,主轴的高速化是目前精密机械的发展趋势,同时机床的稳定性和使用寿命也相应的变得越来越重要,这些变化直接导致了对机床组件要求的提高。作为主轴关键部件的碟形弹簧组,它的合理选型及装配可以提高机床的使用效率,减少主轴的维修频率.碟形弹簧具有小变形大承载力的特点,主轴拉刀机构采用碟形弹簧提供拉刀力,有效地解决了刀具转动过程中夹具系统夹持力不足的缺点。从国内主轴维修的现状来看,碟形弹簧失效主要表现为断裂和破碎,也就是说,在碟形弹簧未达到其设计的疲劳寿命时,弹簧已出现开裂或断裂现象。究其原因,主要有下述几个方面: 1. 原材料选取 按照新版碟形弹簧国家标准 GB1972 – 2005,碟簧材料可以选择 60Si2Mn 或 50CrV4。从原材料特性来看,硅锰钢系列材料中的硅能固溶于铁素体和奥氏体中,可提高钢的硬度、强度、弹性极限、屈强比和疲劳强度,还能提高材料的回火稳定性和抗氧化性;锰能提高材料的淬透性。但硅含量容易产生石墨化现象和增加表面脱碳倾向,并在钢种易生成硅酸盐夹杂物,该夹杂物在晶界析出,易导致淬火开裂现象。即便淬火过程中没有出现开裂,其开裂倾向也会在弹簧加载过程中逐渐放大,导致弹簧寿命降低,最终失效原因为开裂或碎裂。50CrV4中铬和钒能提高钢的韧性、强度和弹性极限,降低钢的过热敏感性和脱碳倾向,从而改善了碟簧表面质量,提高材料的疲劳强度。其淬透性也比硅锰钢要好。此外铬钒钢回火稳定性较高,500℃ - 550℃回火后仍有较高的强度和弹性极限,工作环境允许达200℃。因此,铬锰钢是碟形弹簧材料的首选钢种,也是 DIN2093标准规定的标准原材料。作为大型碟形弹簧生产厂德国Mubea公司原材料的冷轧和热处理是在公司内进行的,这样最大可能的保证了原材料质量. 2. 加工精度 随着转数的提高碟形弹簧的加工精度直接影响主轴的稳定性和使用寿命.过大的弹簧 内径造成主轴高速转动时弹簧过多的向外滑动(如图),由此形成的离心力(F=mω2r) 相应变大,轴承和主轴的负担加重.较小的平面度和平行度保证弹簧组内单片弹簧受力均匀,弹簧 横向位移变小,弹簧组的垂直性更好.对于碟形弹簧在主轴拉刀机构的应用Mubea公司专门开发了高精度碟形弹簧.通过它的特殊边缘结构导向杆和弹簧之间的摩擦被降低, 弹簧疲劳寿命也相应增加. 3. 装配 作为一种相对较新的弹簧形式,碟形弹簧的特性和装配要求还不太为国内机床行业的客户所熟知。我们在帮助客户做选型工作的时候,通常会提醒客户在装配过程中注意以下问题: A- 碟形弹簧组装配时,弹簧组两端要保证弹簧外径(而不是内径)与安装空间附件相接触,如受设计要求所限,至少要保证受力端是弹簧外径与安装空间附件相接触。 B- 导向杆或导向套与弹簧组间保留一定间隙,具体要求请参照Mubea碟形弹簧手册第50 页图 3.20和表3.2,也可查询DIN2093标准或中国国家标准GB1972–2005。 C- 导向件导向表面以及与碟形弹簧组两端相接触的安装空间附件表面须做硬化和抛光处
数控机床常见故障诊断及维修
数控机床常见故障诊断及维修 摘要:数控机床是集机、电、液、气、光高度一体化的现代技术设备,数控机床维修技术不仅是保障数控机床正常运行的前提,对数控机床的发展和完善也起到了巨大的推动作用。数控机床出现的故障多种多样,机械磨损、机械锈蚀、机械失效、加工误差大、工件表面粗糙度大、插件接触不良、电子元器件老化、电流电压波动、温度变化、干扰、滚珠丝杠副有噪声、软件丢失或本身有隐患、灰尘、操作失误等都可导致数控机床出故障。 关键词:数控机床故障诊断维修机械电子 数控机床是一种集自动控制、计算机、微电子、伺服驱动、精密机械等技术于一身的高技术产物。一旦系统的某些部分出现故障,就势必使机床停机,影响生产。所以,如何正确维护设备和出现故障时迅速诊断,确定故障部位,及时排除解决,保证正常使用,是保障生产正常进行的必不可少的工作。 1 数控机床故障诊断原则 1.1 先外部后内部 数控机床是集机械、液压、电气为一体的机床,故其故障的发生也会由这三者综合反映出来。维修人员应先由外向内逐一进行排查,尽量避免随意地启封、拆卸,否则会扩大故障,使机床大伤元气,丧失精度,降低性能。 1.2 先静后动
先在机床断电的静止状态,通过了解、观察测试、分析确认为非破坏性故障后,方可给机床通电。在运行工况下,进行动态的观察、检验和测试,查找故障。而对破坏性故障,必须先排除危险后,方可通电。 1.3 先简单后复杂 当出现多种故障互相交织掩盖,一时无从下手时,应先解决容易的问题,后解决难度较大的问题。往往简单问题解决后,难度大的问题也可能变得容易。 1.4 先机械后电气 一般来说,机械故障较易发觉,而数控系统故障的诊断则难度较大些。在故障检修之前,首先注意排除机械性的故障,往往可达到事半功倍的效果。 2 数控机床常见故障分析 根据数控机床的构成,工作原理和特点,将常见的故障部位及故障现象分析如下。 2.1 数控系统故障 2.1.1 位置环这是数控系统发出控制指令,并与位置检测系统的反馈值相比较,进一步完成控制任务的关键环节。它具有很高的工作频度,并与外部设备相联接,容易发生故障。 常见的故障有: ①位控环报警:可能是测量回路开路;测量系统损坏,位控单元
数控机床故障诊断及排除方法
龙源期刊网 https://www.360docs.net/doc/c95996060.html, 数控机床故障诊断及排除方法 作者:郭茂滨 来源:《中国新技术新产品》2013年第05期 摘要:作为当今效率非常优秀的自动化机床设备,数控机床包括了多项优秀的技术要 素,文章简要的论述了其问题分析以及处理相关的内容。 关键词:数控机床;故障;排除方法 中图分类号:TG659 文献标识码:A 1 分析问题时要遵循的原则内容 1.1 首先是外在然后是里面 数控机床是机械、液压、电气一体化的机床,因此问题的出现肯定是上述的三项内容的全面体现。因此规定维修者要按照先外在然后里面的规定来开展分析活动,也就是说如果机床出现不利现象的话,工作者要从外面开始逐渐的进行到里面。 外在的硬件活动导致的问题是所有的问题中出现几率较高的。一般都是由于检测开关、液压系统、气动系统、电气执行元件、机械装置出现问题引起的。该种问题中的一些能够经由报警体系分析。针对常见的数控体系来说,都具备问题诊断以及预警之类的特征。工作者能够结合此类措施减少诊断的领域。虽说个别问题有报警装置,不过不能够体现出全面的的要素。此时就要结合报警内容以及问题状态来研究。 1.2 先分析机械然后分析电气 因为其是一项具有高度的自动化水平的装置。机械的问题比较的易于察觉,但是体系中的问题就相对来讲要困难多了。 1.3 首先是分析静止的然后动态的 工作者应该先进行静止的,进而分析动态的,不能没有目标的胡乱进行,要询问有关人员问题出现的详细情况,查阅相关材料,才能够分析问题的所在,继而研究应对方法。 1.4 先分析共同用途的然后分析专项的 主要是由于前者是关系到整个体系的,而后者只是一个单独的部分的。 1.5 首先分析简单的然后是繁琐的
加工中心电主轴
N- d1 力口工中心电主轴Machi ning centre High Freque ncy Spin dles 技术参数Tech nical Data 主轴型号spindle type 转速 speed (r/min) 电机 Motor 润滑 Lub 冷却 Cool 轴端连接 Joint of nose 轴承型号 Bearings type 特点 character 额定 功率 KW 电 压 V 电 流 A 频率 Hz SDS80-20-24Z/1.5 24000 1.5 220 5.4 400 油脂水冷ISO20锥孑L 2X 30BNR P4 1 X 7004C P4 带传感器及松拉刀机构 SDS80-20-30Z/1.8 30000 1.8 220 6.4 500 油脂水冷ISO20锥孑L 2X 30BNR P4 1 X 7004C P4 带传感器及松拉刀机构 SDS110-30-18Z/3.2 18000 3.2 380 6.9 600 油脂水冷BT30锥孔2X 35BNR P4 1 X 25BNR P4 带传感器及松拉刀机构 SDS110-30-24Z/4.5 24000 4.5 380 9.2 800 油脂水冷BT30锥孔2X 35BNR P4 1 X 25BNR P4 带传感器及松拉刀机构 SDS110-30-30Z/5.5 30000 5.5 380 11.5 1000 油脂水冷BT30锥孔2X 35BNR P4 1 X 25BNR P4 带传感器及松拉刀机构 SDS150-40-12Z/6.0 12000 6.0 380 11.9 400 油脂水冷ISO40锥孑L 2X 60BNR P4 2X 40BNR P4 带传感器及松拉刀机构 SDS150-30-18Z/7.5 18000 7.5 380 14.9 600 油脂水冷BT30锥孔2X 60BNR P4 2X 40BNR P4 带编码器、传感器及松 拉刀机构 特别说明:本公司可以为用户设计各种加工中心并联机床用电主轴 d2x L3
数控机床故障诊断与维修
数控机床故障诊断与维修 实训报告 系别: 班级: 姓名: 学号: 实训时间:
实训内容项目一主轴传动系统的故障维修与保养任务一变频主轴常见故障维修与保养 任务二伺服主轴常见故障与保养 项目二进给传动系统的故障维修与保养任务一超程故障维修 任务二进给系统电气故障维修 项目三数控系统的故障维修与保养 任务一数据传输与备份 任务二机床无法回参考点故障维修 任务三参数设置 项目四数控机床电气控制故障维修与保养任务一数控车床电气故障排除与保养项目五数控机床的安装与调试 任务一滚珠丝杆的安装与调试 任务二编码器的安装 任务三数控机床性能调试
项目一主轴传动系统的故障维修与保养 一实训目的 1 了解变频主轴的组成 2 熟悉主轴的机械机构及变频器的接线,主要参数意义及设置方法 3 能够进行变频主轴常见故障维修 二实训设备 THWLBF-1 型数控车床维修技能实训考核装置 图1-1THWLBF-1 型数控车床维修技能实训考核装置 本装置由数控车床系统交流伺服模块、变频调速模块、冷却控制模块、刀架控制模块、变压器、网孔板、其它辅助功能模块和十字滑台等组成,通过此设备进行项目训练,能检验学生的团队协作能力,计划组织能力、交流沟通能力、职业素养和安全意识等。
三变频主轴常见故障维修与保养 1.变频器的功能、连接与调试 1)变频器操作面板说明 图1-2 变频器操作面板2)端子接线操作说明 图1-3 变频器接线端子图3)参数设置方法
( ( (
12 P125 50 可调端子2频率设定增益频率 13 P160 9999 0 扩展功能显示选择 14 P161 0 1 频率设定、键盘锁定操作选择 15 P178 60 60 STF端子功能选择 16 P179 61 61 STR端子功能选择 17 P180 0 0 RL端子功能选择 18 P181 1 1 RM端子功能选择 19 P182 2 2 RH端子功能选择 四伺服主轴常见故障维修与保养 1伺服驱动系统 1)本装置采用FANUC公司的伺服驱动系统,具有如下特点: (1)供电方式为三相200V-240V供电。 (2)智能电源管理模块,碰到故障或紧急情况时,急停链生效,断开伺服电源,确保系统安全可靠。 (3)控制信号及位置、速度等信号通过FSSB光缆总线传输,不易被干扰。 (4)电机编码器为串行编码信号输出。 图1-4 驱动连接图
《数控机床故障诊断与维修》期末考试试卷试卷
2012—2013学年度第一学期 《数控机床故障诊断与维修》期末考试试卷试卷(A卷) 一、单选题(每小题2分,共10分) 1. FANUC数控系统采用系统存储卡方式进行数据输入输出操作,请问系统的I/O通道应该设定为()。 A.1通道B.2 通道 C. 3通道 D. 4通道 2. 数控机床主轴驱动系统是主运动的()装置部分 A.动力B.执行C.传动D.接收 3. 在数控机床主轴变频调整中,主轴零速信号( )接入液压卡盘控制回路中。A.并联B.串联C.串联或并联D.反接 4. 对于提供给数控机床的压缩空气,通常会有以下哪些要求()。 A.压力B.流量C.清洁度D.以上都是 5. FANUC数控系统出现#400报警,请问产生的原因是()。 A.伺服不能就绪B.伺服移动误差过大 C.伺服过热D.伺服停止误差过大 二、填空题(每空1.5分,共30分) 6. 回转刀架自动换刀工作的四个步骤是、刀架转位、、转位油缸复位。 7. 国家标准GB9061—1998中规定,数控车床的自动运行考验时间为 h ,加工中心的自动运行考验时间为 h。 8. 主轴的密封形式有和。 9. 数控机床集、计算机、气动、传感检测、液压、等于一体的设备。 10. 数控机床中电子元件的工作温度一般要求在oC~oC以下。 11. 数控机床主轴轴承的配置形式主要有组合、组合、同向组合三种形式。 12. 数控机床伺服电动机与丝杆联接形式有通过直联、联接和经过减速器联接三种形式。 13. 数控机床原点是机床厂家调整的,具体机床原点的位置是由 设定的。 14. 数控机床超程报警有报警和两种情况。 15. 数控机床精度验收的内容主要包括:、和切削精度。 三、简答题:(共30分) 16. 简述数控机床主轴齿轮换档通常采用什么方法实现自动换档切换控制?每一档之间如何实现调速?换档的意义何在?(每问3分,共9分) 答:
数控机床的故障诊断
摘要 科学技术的发展,对机械产品提出了高精度、高复杂性的要求,而且产品的更新换代也在加快,这对机床设备不仅提出了精度和效率的要求,而且也对其提出了通用性和灵活性的要求。数控机床就是针对这种要求而产生的一种新型自动化机床。数控机床集微电子技术、计算机技术、自动控制技术及伺服驱动技术、精密机械技术于一体,是高度机电一体化的典型产品。它本身又是机电一体化的重要组成部分,是现代机床技术水平的重要标志,坚持做好数控机床的日常保养和维修工作,可以有效地提高元器件的使用寿命,避免产生或及时消除事故隐患,使机床保持良好的运行状态。 关键词:数控机床;故障;维修
目录 文摘................................................................................................... 错误!未定义书签。目录. (2) 1 数控机床的故障诊断概述 (3) 1.1 数控机床维修的基本概念 (3) 1.2 数控机床的故障规律 (3) 1.3 数控机床故障诊断的一般步骤 (5) 1.4 维修中的注意事项 (5) 2 数控机床常用的故障诊断方法 (7) 2 .1 数控机床常见故障分类 (7) 2.2 数控机床常用故障诊断方法 (8) 3 数控系统的故障诊断与维修 (13) 3.1. 数控系统的故障诊断技术 (13) 3.2 数控系统常见故障和处理 (14) 4 伺服系统的故障诊断与维修 (18) 4.1 进给伺服系统的故障诊断与维修 (18) 4.2 主轴伺服系统常见故障的处理 (20) 结论 (23) 致谢 (24) 参考文献 (25)
数控机床常见故障分析与排除
数控机床常见故障分析与排除 摘要:由于数控机床是技术密集和知识密集的自动化设备,一旦出现故障,维修困难的问题将严重影响数控机床开动率,造成设备闲置,资源浪费。本文阐述了数控机床故障分析与排除的一般方法,提出了对维修人员的技术培训是尽快解决数控机床故障的重要措施。 关键词:数控机床;故障诊断;维修;排除 数控机床技术集机械制造技术、控制技术、伺服驱动、精密测量、数据通信等各项技术于一体,是机加工领域中典型的机电一体化技术。由于数控机床能按程序自动加工零件,无须使用复杂和专用的工模夹具,能比较好地解决中小批量、多品种和复杂零件的自动化加工,生产率高,加工零件一致性好,质量稳定,便于产品的更新换代,同时具有柔性、高精、高速的特点。因而在机械制造业中的应用越来越广泛。但是,数控机床在使用过程中,不可避免地会出现一些故障而影响生产,因此,数控机床的故障诊断与维修是数控机床在使用过程中的重要组成部分,是数控机床长期可靠运行的重要保障。 一、数控机床故障的分类 数控机床是机、电、液一体化的技术密集和知识密集的自动化设备,其故障发生的原因比较复杂,根据数控机床的故障起因、故障性质、发生部位以及有无报警等可对数控机床常见故障作如下分类: (1)按故障起因的相关性可分为非关联性故障和关联性故障。非关联性故障与系统本身无关,是由于运输、安装等原因造成的;而关联性故障又可分为系统故障和随机故障,系统故障是指机床或数控系统部分在一定条件下必然出现的故障,是一种可重演的故障;随机故障是指偶然出现的故障,是由于机械结构和局部松动、系统控制软件不完善、硬件工作特性曲线下降、电气元器件品质因数降低等原因造成的,这类故障在同样条件下只偶然出现一两次。 (2)按故障有无诊断显示可分为有诊断显示故障和无诊断显示故障。有诊断显示的故障一般都与控制部分有关,较易排除;无诊断显示的故障,维修人员只能根据出现故障前后的情况来分析判断,所以排除故障的难度较大。 (3)按故障发生的性质可分为破坏性故障和非破坏性故障。破坏性故障是指由于伺服系统失控造成“飞车”、短路烧保险等故障,只能根据操作者提供的情况
FANUC数控机床主轴故障诊断与维护
FANUC数控机床主轴故障诊断与维护 作者:李刚指导老师:楚雪平摘要:数控机床的故障包括很多方面,本文主要以FANUC数控机床为例对主轴故障诊断与维修进行分析。本文作者认为,数控机床主轴故障诊断与维修的一般步骤为:①观察故障现象并做好记录,②分析故障现象,③结合数控系统自诊断功能进一步确定故障原因,④排除故障。经过实践验证,该方法切实有效。 关键词:FANUC数控机床;主轴故障;诊断维修; 主轴是数控机床的重要零件之一,主轴旋转产生切削的主运动是形成切削的重要条件。因此,本文作者认为研究主轴故障诊断与维修的方法是很有必要的。 一、FANUC数控机床主轴常见故障类型 FANUC数控机床主轴故障有很多种,造成这些故障的原因也非常多。但最常见的故障类型包括以下几种:主轴电机不转、电机转速异常、主轴电机振动或噪声太大、主轴电机过热等。在分析故障的起因时,一定要开阔思路,尽可能考虑各种因素。 二、FANUC数控机床主轴故障诊断的方法 (一)、FANUC数控机床主轴控制原理
FANUC数控机床的主轴控制方式有串行控制和模拟控制两种,可以通过特定参数的设置进行选择。无论采用哪种主轴控制方式,都要对主轴的方向和速度进行控制,也就是说主轴的控制包括两个方面:速度和方向。 1、FANUC数控机床主轴速度控制原理 在串行主轴输出有效的情况下,S指令的执行主要由CNC控制来实现。而在模拟主轴输出有效的情况下,则只可以使用主轴转速指令控制和基于PMC的主轴速度指令控制。这里,本文作者只对串行主轴S指令控制原理进行分析。如图一所示,第1次执行数控加工程序中的S指令时,CNC将首先以二进制代码形式把S代码信号输出到PMC特定的代码寄存器F22~F25中。第1次之后,CNC再执行S指令时将不再发出S指令选通信号SF;然后经过S代码延时时间TMF(由系统参数设定,标准设定时间为16ms)后发出S指令选
数控机床故障诊断作业及参考答案
数控机床故障诊断作业及参考答案 情境一 简述FANUC-0i MA系统的组成及各部分功能。 答:FANUC-0i MA系统由CNC装置、主轴驱动单元、进给伺服驱动单元、可编程控制器PMC、系统显示装置和操作面板、辅助控制装置、通信装置等部分组成。 CNC装置是数控系统的核心部分。主要由主CPU、各种存储器、主轴控制模块、伺服控制模块、PLC控制模块、显示卡控制模块等组成。主CPU 通过BUS总线实现数据的算术运算和逻辑运算及指令的操作控制。存储器用来存储系统程序(CNC控制软件、数字伺服控制软件、PLC控制软件和梯形图、宏程序执行软件等)和用户程序(CNC参数、PLC参数、加工程序、刀具补偿量及用户宏变量等)。主轴控制模块通过子CPU实现对主轴的位置、转速及功能指令的控制。伺服控制模块由子CPU(FANUC系统的1个子CPU 控制2个轴)通过BUS总线与数字伺服装置通信,实现对数控机床进给轴的位置、速度及电动机电流的控制。PLC控制模块由PLC控制的CPU、存储器、PLC管理软件及控制电路等组成,FANUC数控系统的PLC均采用内装型PLC(又称PMC),通过PMC可实现数控机床的辅助控制及PMC轴的控制。显示卡控制模块为数控机床的显示装置(CRT/LCD)提供视频信号,新型数控系统把图形显示功能芯片及MDI信号信息功能芯片和显示卡做成一体,通过FSSB 总线与CNC 装置进行通信控制。 主轴驱动单元由主轴放大器、主轴电动机、主轴传动机构、主轴位置和速度检测装置(主轴编码器)等组成。实现数控机床主轴的速度和位置控制、主轴与进给轴的同步控制、主轴准停与定向控制。 进给伺服驱动单元由伺服放大器、伺服电动机、机械传动组件和检测装置等组成。实现数控机床进给装置的速度与位置控制。 可编程控制器PMC除了实现机床的各种辅助功能的控制之外,新型数控系统还可实现数控机床的附加轴的PMC控制。 系统显示装置用来显示各种信息及图形画面。操作面板的功能是实现操作者与CNC装置及机床的人机对话。
数控机床故障诊断与维修学习心得
数控机床故障诊断与维修 摘要:数控机床促进我国机械制造业的发展,数控机床是机电一体化技术在机械加工领域中应用的典型产品,具有高精度、高效率和高适应性的特点,适于多种、中小批量复杂零件的加工。数控机床故障诊断与维修的基本目的是提高数控设备的可靠性。数控设备的外部故障可以分为软故障和外部硬件损坏引起的硬故障。软故障是指由于操作、调整处理不当引起的,这类故障多发生在设备使用前期或设备使用人员调整时期。 关键字:数控故障数控维修 一数控机床的维护和保养 1.1数控机床的日常维护 1)严格遵守维护制度 数控系统的编程,操作人员和维修人员必须进行严格的专门培训,熟悉所用数控机床的功能和使用方法,正确的使用机床,避免因操作不当引起的故障。 2)数控柜和强电柜的门应尽量少开少关 加工车间一般的空气中都有油雾,灰尘金属粉末等颗粒物,当它们落在数控系统内的电子器件或电路板上,容易引起元器件或电路板的损坏,因此数控柜和强电柜的门应尽量少开少关。如果数控系统超长时间负载工作时,要用正确的散热方法,想办法将对数控系统的外部温度。不得随意开关柜门。 3)经常检查电网电压 一般数控系统允许的电网电压波动范围内进行,否则是数控系统不稳定,有可能造成重要元器件的损坏。要经常注意电压电网的波动,特别是电网质量比较差的地区,应及时配置数控系统用的交流稳压装置。 4)定时清扫数控柜的散热通风系统 应每天检查数控系统柜上各个冷却风扇工作是否正常,应视工作环境状况,每半年或每季度检查一次风道过滤器是否有堵塞现象。如果过滤网上灰尘积聚过多,需及时清理,否则将会引起数控系统柜内温度高(一般不允许超过55℃),造成过热报警或数控系统工作不可靠1.2数控机床的3级保养 1)数控机床的1级保养主要内容有:班前、班中、班后检查并严格遵守每天检查对于数控机床来说,合理的日常维护措施,可以有效的预防和降低数控机床的故障发生几率。针对每一台机床的具体性能和加工对象制定操作规程建立工作、故障、维修档案是很重要的。包括保养内容以及功能器件和元件的保养周期。 2)数控机床的2级保养主要内容有:对主轴箱、各坐标进给传动系统、液压系统、中心润滑系统、冷却系统、气动系统、外观的清理并按照保养的要求去做。 3)数控机床的3级保养主要内容有:对主轴箱、刀塔、尾座要求清理、清洁。对整体外观和各个系统要求清洁,检查和校验。 1.3 数控机床维修 1)数控机床故障的种类 数控机床诊断一般是机床提供的自诊断报警信息来排除,在故障排除的过程中也会采用一些典型的方法来辅助,主要有:启动自诊断,在线诊断和离线诊断。 二数控机床典型故障与诊断 2.1数控机床主轴故障排除的方法