现代数控镗床的研究与发展
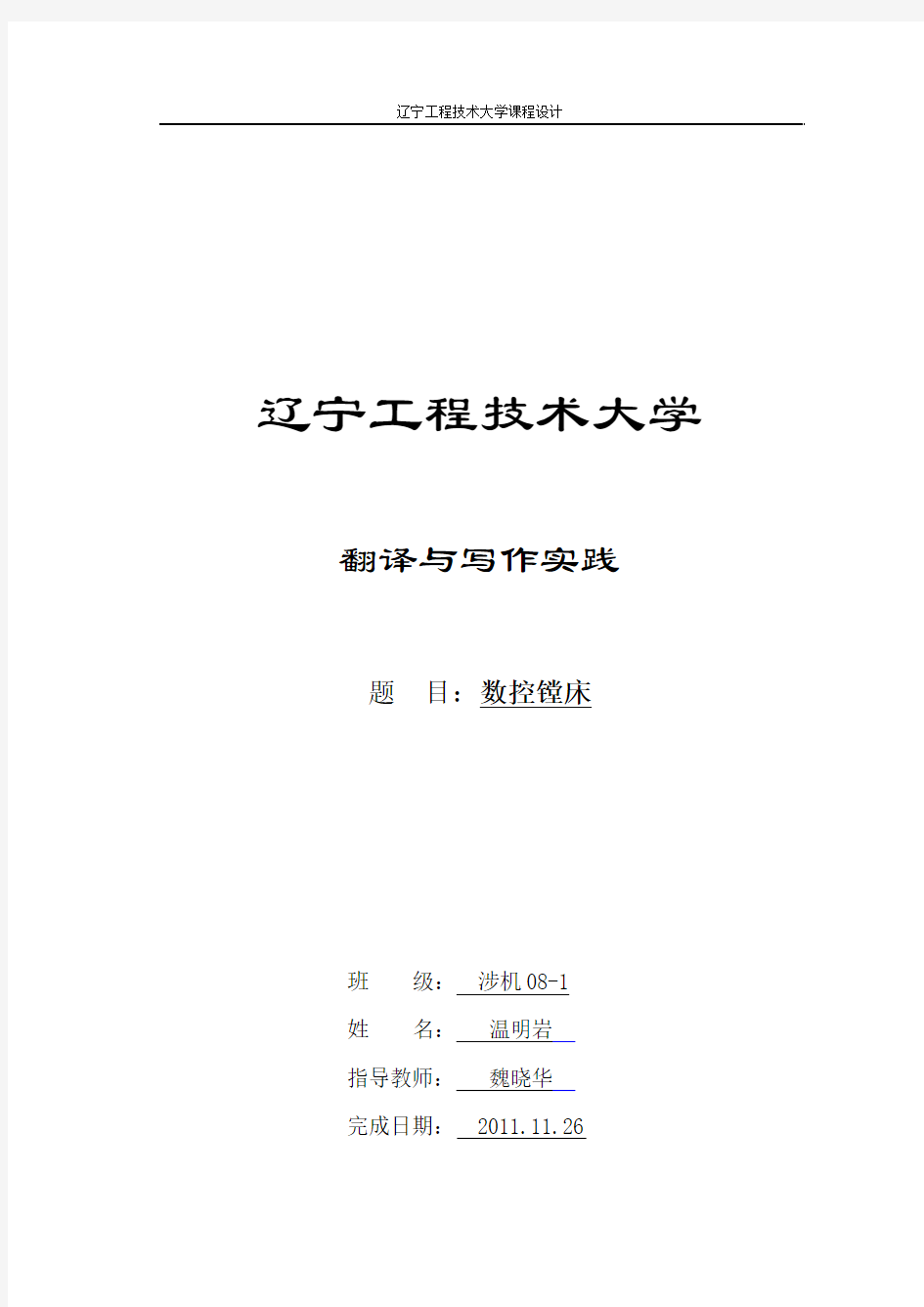

辽宁工程技术大学翻译与写作实践
题目:数控镗床
班级:涉机08-1
姓名:温明岩
指导教师:魏晓华
完成日期:2011.11.26
五、指导教师评语
成绩:
指导教师
日期
The demands and development of modern CNC boring
merchine
【Abstract】:CNC technology is a comprehensive application of electronic technology, computing technology. automatic detection and control and the development of modern scientific and technical achievements.So,this passage lists the introductions,devepments of and demands to the modern CNC boring machine.
【Key words】:CNC boring machine,gantry boring,development,demands
1.Introductions of CNC boring machine
1.1T he categories of CNC boring machine
Because of the high technology today,there comes to be CNC boring machine ,which is based on manually operated and controlled boring machine.And there are many kinds,such as CNC gantry boring machine,CNC horizontal boring machine, fixed 3-sides CNC gantry milling&boring machine,tKS63 Series twin spindles CNC boring machine and so on.
1.2The introduction of boring machine
1.2.1 The CNC gantry boring machine
It has five coordinates axis: X axis, Y axis, Z axis, W1 axis and W2 axis. The X, Y, Z axis are automatic positioning coordinate axis whilst W1 and W2 are synchronous coordinate axis. The XK(XH)21 series are available for various machining operation such as milling, drilling, tapping, and boring etc. This series machine are five axis controlling with three axis synchronous motion be applicable to various plates, chucks, housings etc. complex parts either for middle or small batch production. They are applicable to various tubes, plates and housings machining in such fields like freezing, petrochemical, metallurgic, boilers, prints and packing and also be applicable to cylinders and housings machining for automobile and diesel engines. It can be equipped with tools magazine, head magazine and various spindle heads for 5-face machining. It can also equipped with vertical & horizontal rotary tables.
1.2.2 The CNC horizontal boring machine
1.The machine’s layout features travel columns, side installed headstock and floor style. The main machine movement is made by spindle rotating along with five-axis linear motion: column
motion at traverse direction, X axis, upper and lower motion of spindle at vertical direction, Y
axis, ram motion at axial direction, Z axis, extendible motion of boring axis at axial direction, W axis, swing worktable motion at longitudinal direction, V axis and B axis, which can realize 360°positioning and with hydraulic clamping device.
2High-performance CNC system control includes AC spindle motor and servo motors for X, Y, Z (W, V) and B axis synchronous motion. The spindle has the accurate positioning function and the machine can implement rigidity tapping.
3.Main power is transmitted to the spindle from the spindle motor. Reducer (Two steps) and gear box, thus heavy cutting is made possible.
4.Driven axis of feeding: X axis is driven by rack connected with gear box reducer in which there are twin gear anti-backlash. Y and V axis are driven by ball screws after speed reducer. Z, W, axis
is driven by ball screw directly coupled by servo motors. X, Y, Z, V and B, five axis, are controlled by closed loop.
5.X, V and Z axis is made with linear ball and plastic covering guide ways. Y, W axis is consisted
of sliding guide ways with anti abrasive material.
1.2.3 The Fixed 3-sides CNC gantry milling&boring machine
1.This is a pallet change three sides CNC gantry milling and boring machine. It equips one vertical spindle and two horizontal spindles at left and right. When the machine is working, the three axes can work at the same time. This is a type of high efficient and multi-function CNC machine.
2.The machine adopts fixed gantry type structure with left and right columns. Also the whole machine is fixed on the ground. The protruding part of the two columns connected with the machine, at the connection point there are high strength bolts. On left and right columns there are horizontal spindles on each of them.
3.Machine big parts: left column, right column, machine bed, worktable, beam, cartridge and ram are all done with resin casting process, after that these parts are treated with ageing, it released inner force maximally.
1.2.4 The TKS63 Series twin spindles CNC boring machine
1. Optimized spindle structure design featuring high rigid and accuracy.
2.The spindle is structured with square sliding tram and spindle nose be applicable for variable right angle milling cutter.
3.The SIEMENS840D system where X, Y1, Y2, Z1, Z2 are driven by AC servo motors. Each spindle can solely work as three axes synchronous motion with the table. The spindle is oriented spindle stop and be available for rigid tapping and heavy cutting.
4. The main casting is structured with intensive ribs provides as strong anti-vibration and overall rigidity. H-M dialogue, convenient language conversion, path tracking display, self-diagnosis, automatic alarm and floppy drive input-etc. all along. Reliable operation, stable accuracy and supreme cost-performance ratio
2.T he demand to and devepment of CNC boring machine
2.1The demands to CNC boring machine
The demand to and devepment of CNC machine tools are equal to CNC boring machine.
1.On the high-speed, high demand for numerical control equipment: High-speed cutting, the first high-speed, high spindle speed that is, on the other hand, it should be a high feed rate, in order to improve efficiency, but also a fast moving machines, fast tool change, spindle acceleration and high feed acceleration, high speed machining technology is the structure of CNC machine tools and materials, machine design and manufacturing technology, high-speed spindle system, fast feed system, high performance CNC control systems are put forward higher requirements.
2. On the versatile multi-axis CNC machining center needs: we must ensure that parts surface quality, but also to ensure the accuracy and shape of the location of processing accuracy, these parts typically require an installed card, forming an orientation process, only the multi-axis machining centers, to meet those requirements. At present, the aviation parts, five-axis CNC milling machine and a five-axis control, turntable structure of complex equipment such as CNC machine tools increased demand.
3. On the development of CNC machine tools to adapt to the needs of information technology: With CAD, CAPP, CAM and other information technology, to improve the processing efficiency, many companies have established a Centre for NC programming, data transmission, modular design and processing technology group hardware design of CNC machine tools put forward higher requirements.
2.2The devepment of CNC boring machine
CNC machine tool consumption has become a mainstream consumer CNC machine tools in 2015 is expected to remain more than six billion U.S. dollars, Taiwan, the number will exceed 10 million units. The rapid development of automobile industry development for the machine tool industry provides a rare opportunity. Expected in 2020, China's auto production will reach 18 million, the state required car manufacturers will be required for 80% of high-end CNC machine tools from China. Experts believe that the next 10 years is the development of China-made vehicles and equipment in China's best and final period of strategic opportunity.
参考资料
1龙门数控镗铣床
龙门数控镗铣床,是一台高效多功能大型数控机床。本系列机床有X轴、Y轴、Z轴、W1轴、W2轴五个坐标轴,X、Y、Z坐标轴可以自动定位,W1轴、W2轴为同步坐标轴。本系列机床能完成铣、钻、铰、攻丝及镗孔等各种工序的加工。本系列机床为五轴控制,三轴联动,适用于各种板件、盘件、壳体件、模具等复杂零件的多品种中小批量生产,适用于制冷、石化、冶金、锅炉、印刷、包装等行业的各种管板、壳体的加工,也适用于汽车、柴油机等行业的缸体、壳体等的加工。可配置刀库、头库和各种附件铣头,实现五面加工,还可以配置立、卧式数控回转工作台。
2数控落地镗床
1)采用立柱移动,主轴箱侧挂的落地式布局。机床主运动为主轴的回转运动。五个直线运动坐标轴为:立柱横向移动(X轴);主轴箱垂直上下移动(Y轴);滑枕轴向移动(Z轴);镗轴轴向伸缩移动(W轴);回转工作台纵向移动(V轴)。一个回转运动坐标轴为转台的回转运动(B轴)。可任意360°分度定位,带液压夹紧。
2)采用高性能数控系统控制,交流主轴电机,所有轴都采用交流伺服电机驱动。X、Y、Z (W、V)、B四轴可实现联动,主轴具有准确定位功能,机床能进行刚性攻丝。
3)主传动由主轴电机经两档减速箱及齿轮减速传动到主轴,满足强力切削要求。
4)进给驱动轴:X轴采用双齿轮消隙的齿轮减速箱带到齿条传动;Y、V轴经减速箱带动滚珠丝杠传动;Z、W轴由伺服电机经弹性联轴节直接带动滚珠丝杠驱动进给;X、Y、Z、V、B 五轴为闭环控制。
5)X、V、Z轴为贴塑滑动与滚动块相结合的复合导轨形式;Y、W轴采用耐磨材料的滑动导轨。
3龙门三面数控镗铣床
1)本机床是一台双交换定梁龙门三面数控镗铣床,具有立式、左右卧式各1个主轴,共3个主轴,机床铣削时可以三轴同时加工,是高效多功能型数控机床。
2)机床采用门式框架布局结构,固定式龙门左、右立柱上部与固定横梁相联结,与地基连接形成高刚性龙门框架。左、右立柱下部凸出的部位与床身相联结,其联结部位每处采用高强度螺栓紧固。在左右立柱上各带有一个可以上下移动的卧式主轴。
3)机床基础大件:左立柱、右立柱、床身、工作台、横梁、拖板、滑枕,全部采用树脂砂造型的铸铁件,铸铁件进行人工时效处理,最大限度的消除了铸造应力。
4 TKS63系列双主轴数控镗床
1)主轴结构采用优化设计,刚性好,精度高;
2)主轴采用方滑枕结构,端面可安装各种直角铣头;
3)采用SIMENS840D系统,X、Y1、Y2、Z1、Z2轴均由交流伺服电机控制,双面可单独与工作台实现三轴联动,主轴准停,具备刚性攻丝,可进行强力切削;
4)主要大件采用稠筋布置,抗震性好、整机刚性高;人机对话,中英文双语言切换,轨迹显示,故障自诊断,自动报警,带软驱输入;运行可靠,精度稳定,具有良好的性能价格比。
参考文献
[1] 钟闻斌.龙门式钻镗床数控化改造的研究[D].西北工业大学.2002
[2] 宋齐婴,臧昭农.落地镗铣床的数控化改造设计[J]. 制造技术与机床. 2006
[3] 贾九荣.数控机床的操作经验初探[J]. 科学之友. 2011
[4] 梁全.叶轮五坐标数控铣削CAM和CNC关键技术的研究[D]. 哈尔滨工业大学2010
[5] 薛玉霞.数控机床可用性关键技术研究[D]. 吉林大学.2009
[6] 朱春霞.基于虚拟样机的并联机床若干关键技术的研究[D]. 东北大学.2008
[7] 周城.数控机床高速液压动力卡盘的研究[D]. 浙江大学.2011
[8]Katja Nummiaro,Esther Koller-Meier,Luc Van Gool. 利用颜色的非刚性物体跟踪方法(英文) [J]. 自动化学报, 2003.03
[9].Wen Shen, eds. Machinery Manufacturing Industry taboo Manual [M]. Beijing: Mechanical Industry Press, 2003.
[10] 隋冬杰,常英丽.双面镗床的设计制造及使用[J]. 煤矿机械. 2006(07)
[11]吕红巧.加工中心/数控铣床常用的对刀方法[J]. 装备制造. 2009(06)
镗床操作规程
镗床操作规程 一、认真执行《金属切削机床通用操作规程》有关规定。 二、认真执行相述有关镗床通用规定: (一)工作中认真做到: 1工件的安置,应使工作台受力均匀,毛坯面不准直接放到工作台面上,装夹用的垫板,压析等必须平正。 2拆卸带锥度的刀具时,须用标准楔冲下,不准用其他工具随意敲打。 3、使用镗杆制动装置时,应在镗杆惯性转速降低后再进行。 4不准同时作两个以上的机构运动,如主轴箱升降时,不准移动镗杆。 5、不准用机动对刀,当刀具快接近工件时,应改为手动。 6、使用花盘径向刀架作径向进给时,镗杆应退回主轴箱内,同时径向刀架不准超出极限。 7、机床上的光学装置或清密刻度尺,应小心使用,目境用后应将盖子盖住,保持目境和刻度尺清洁。不准用一般布料和不清洁的擦料擦试,不准任意拆卸和调正光学装置和刻度尺。 8、在主轴旋转时,主轴与主轴套筒的间隙随温升而缩小,操作时要特别注意,若主轴移动困难时,必须立即停车,待一段时间湿度下降间隙恢复增大后再工作。 9、严禁利用工作台面或落地镗床的大平台面,进行其他作业如校正工件或焊接工件等。 (二)工作后,将工作台放在中间位置,镗杆退回主轴内。 三、认真执行下述有关特殊规定: (一) T68,T611镗床:
1、主变速手柄及走刀变速手柄未扳转到180?时,不准回转的柄。当主轴降到最低转数是,方准将手柄推下。 2、将工作台回转90?时,不准用力过大撞击定位挡铁。 (二) BFT-13CW1镗床: 1、镗孔时,镗杆伸出长度不得超过500毫米。使用花盘和径向刀架时,转数不得超过180转/分。只有径向刀架在平衡的情况下,转数才能提高到250转/分。 2、主轴连续运转的情况下,最高转速不得超过350转/分。若工作需要使用最高速时,其连续运转时间不得超过30分钟。 3、往加油器中加油时,绝不允许加到红色指标线以上。
数控镗铣床操作规程
数控落地镗铣床操作规程 一、操作 操作前请阅读全套《使用说明书》,包括电气系统及关键特殊配套件的全套说明书,掌握操作元件的功能,用途及具体操作位置和方法,尤其是红色急停按钮的位置。在人身安全受到危害或在会损坏机床和工件的情况下,请速按红色急停按钮,机床会瞬时停止运行。 允许受过正规培训或授权的个人来操作本设备,未受过培训和授权的人员不得进行操作,即使是暂时的也不允许。 二、编程 编程人员要熟读数控系统的《编程指南》,掌握编程方法和技巧。编程时应注意下列事项: 1、坐标体系的确定。 2、对刀点与退刀点的确定。 3、零件数控加工内容的确定。 4、对零件图纸进行数控加工分析。 5、加工轨迹的计算和优化。 6、正确测量和计算工件坐标系,并对所得结果进行验证和计算。 7、正确输入工件坐标系。 8、刀具补偿值的输入与刀具实际长度相符。
9、走刀路线、加工余量、工序尺寸及其公差、切削用量的确定。 10、刀具移动不应与夹具发生干涉。 11、走刀路线应能保证零件加工精度和表面粗糙度,应使走刀路线最短。 12、力求设计、工艺、编程基准统一。 13、切削顺序应遵守基面先行、先粗后精、先主后次、先面后孔的基本原则。 三、刀具选择 切削刀具的选择应符合下述原则: 1、铣削平面时,采用可转位硬质合金铣刀,一般采用两次走 刀,一次粗铣、一次精铣。连续切削时,粗铣刀直径要选取小些,减小切削扭矩。精铣时,刀直径要选大些,最好包容得加工表面的整个宽度。加工余量大而加工表面又不均匀时,刀具直径要选得小些,避免粗加工时刀痕过深影响加工质量。 2、高速钢刀用于加工凸台与凹槽,最好不用于加工毛坯表面, 硬化层和夹砂会加速刀具的磨损。 3、加工余量小,表面质量要求高时,应采用立方氮化硼 (CBN)刀片端铣刀或陶瓷刀片端铣刀。 4、加工精度要求较高的凹槽时,可采用直径比槽宽小一些的
数控机床发展史
数控机床的发展史 1.第一代数控机床产生于 1952年(电子管时代)美国麻省理工学院研制出一套试验性数字控制系统,并把它装在一台立式铣床上,成功地实现了同时控制三轴的运动。这台数控机床被大家称为世界上第一台数控机床,但是这台机床毕竟是一台试验性的机床。到了1954年11月,在帕尔森斯专利基 础上,第一台工业用的数控机床由美国本迪克斯公司。 2.第二代数控机床产生于1959年(晶体管时代)电子行业研制出晶体管元器件,因而数控系统中广泛采用晶体管和印制电路板,使数控机床跨入了第二代。同年3月,由美国克耐·杜列克公司(Keaney &Trecker Corp)发明了带有自动换刀装置的数控机床,称为“加工中心”。现在加工中心已成为数控机床中一种非常重要的品种,在工业发达的国家中约占数控机床总量的l/4左右。生产出来。 3. 第三代数控机床产生于1960年(集成电路时代)研制出了小规模集成电路。由于它的体积小,功耗低,使数控系统的可靠性得以进一步提高,数控系统发展到第三代。以上三代,都是采用专用控制的硬件逻辑数控系统(NC)。 4.第四代数控机床产生于 1970年前后随着计算机技术的发展,小型计算机的价格急剧下降、小型计算机开始取代专用控制的硬件逻辑数控系统(NC),数控的许多功能由软件程序实现。由计算机作控制单元的数控系统(CNC),称为第四代。1970年,在美国芝加哥国际展览会上,首次展出了这种系统。 5.第五代数控机床产生于1974年美、日等国首先研制出以微处理器为核心的数控系统的数控机床。30多年来,微处理机数控系统的数控机床得到飞速发展和广泛的应用,这就是第 五代数控(MNC)。后来,人们将MNC也统称为CNC。 柔性制造系统 1967年,英国首先把几台数控机床联接成具有柔性的加工系统,这就是最初的FMS—Flexible Manufacturing System柔性制造系统。之后,美、欧、日等国也相继进行了开发和应
Φ160数控落地镗铣床技术规格
Φ160数控落地镗铣床技术规格 1 设备名称 Φ160数控落地镗铣床 2 设备数量 1台 3 机床的技术要求 3.1机床主轴主要技术参数 主轴直径:Φ160mm 铣轴直径:≥Φ260mm 主轴锥孔:ISO 50 主轴转速:2~1000r/min(无级) *主轴电机功率:≥50KW(连续) *主轴最大恒扭拒:≥ 7000N.m 滑枕截面:≥480mm×480mm 3.2 坐标轴行程要求 X轴:≥6000mm (立柱沿床身导轨移动的行程) 注:机床有效加工行程为6000mm。附件自动交换区所占用的X轴行程由投标方确定并增加在X轴行程内。 Y轴:≥3000mm (主轴箱沿立柱导轨移动的行程) Z轴:≥1000mm (主轴移动行程) W轴:≥1000mm (方滑枕移动行程) Z、W轴行程允许迭加:总行程≥2000mm 3.3机床主轴及方滑枕技术要求 请投标方设计方滑枕截面尺寸。根据方滑枕行程要求,计算并提供方滑枕特性曲线图。设计方滑枕挠度自动补偿曲线。 注:滑枕刚性必须确保在安装机床附件后加工时的平稳性。 3.4 坐标轴运动速度 快速进给:
X轴:≥6000mm/min Y轴:≥6000mm/min Z轴:≥3000mm/min W轴:≥3000mm/min 切削进给: X轴: 1~6000mm/min Y轴: 1~6000mm/min Z轴: 1~3000mm/min W轴: 1~3000mm/min 3.5 精度 按GB/T 5289.3-2006 《卧式铣镗床检验条件精度检验》标准执行。*3.5.1 机床精度 镗轴锥孔的径向跳动: 靠近主轴端≤ 0.012mm 距离300mm处≤ 0.02 mm 镗轴的径向跳动: 靠近主轴端≤ 0.015 mm 距离300mm处≤ 0.02 mm 镗轴的轴向窜动:≤ 0.015 mm 定位精度: X轴:≤0.02mm/1000mm ≤0.05mm/全长 Y轴:≤0.02mm/1000mm ≤0.03mm/全长 Z轴:≤0.02mm/1000mm ≤0.025mm/全长 W轴:≤0.02mm/1000mm ≤0.025mm/全长 重复定位精度: X/Y/W/Z轴:≤0.015mm 反向误差:≤0.01mm
数控技术现状与发展
数控技术现状与发展 讲课目录提纲 华南理工大学机械与汽车工程学院 李伟光教授 2010年5月
目录
一数控技术概述 1.1数控技术与国民经济 1.2数控技术的起源 1.3研究数控技术的科技动力 1.4研究数控技术的社会环境 1.5数控技术的应用 1.6有关数控技术产业的国家政策 1.7国内外数控技术与设备行业情况介绍二数控设备的控制系统 2.1 数控系统概述 2.2 数控系统的组成、性能与体系结构2.2.1 数控系统性能的现状与发展趋势 2.2.2 数控系统功能的现状与发展趋势 2.2.3 数控系统体系结构的现状与发展趋势2.2.4 基于PC技术的智能开放式数控系统三数控技术发展与数控设备应用 3.1数控技术的发展与数控设备的应用 3.2应用数控设备的社会需求 3.3应用数控设备的工业环境 3.4应用数控设备的技术支持 3.5国内外应用数控技术的现状与差距 3.6数控机床领域的装置种类及技术发展
3.6.1 高速、高刚度大功率电主轴技术 3.6.2 多功能双摆角数控铣头技术 3.6.3 高刚度大扭矩双摆角数控铣头技术 3.6.4 车铣复合主轴头技术 3.6.5 高速、精密数控回转工作台 3.6.6 全数字交流伺服驱动装置 3.6.7 高速、精密、重载直线导轨精度保持性技术 3.6.8 高速、精密、重载滚珠丝杠精度保持性技术3.6.9 盘式结构大扭矩力矩电机及驱动装置 3.6.10 精密直线电机驱动装置及全闭环控制技术 3.6.11 复合加工技术 3.6.12 切削表面完整性技术 3.6.13 高速切削技术 3.6.14 高速、超高速磨削技术 3.6.15 五轴联动高速高精加工工艺技术 3.6.16 高精度刀具测量技术 3.6.17 刀具动平衡技术 3.6.18 柔性工装关键技术 四培养掌握数控技术与设备的人才 4.1国内外研究数控技术人才的基础与现状 4.1.1国外研究数控技术的现状与成果 4.1.2国内研究数控技术的机构与人才培养现状
落地铣镗床常见故障分析与排除方法
落地铣镗床常见故障分析与排除方法 摘要:数控落地铣镗床具有镗孔、钻孔、铣削、切槽等加工功能;配上高精度回转工作台、直角铣头等功能附件,可以实现五面加工,是冶金、能源、电力等行业用于汽轮机、发电机和重型机械等大型零件加工的理想设备。在使用过程中,它的每个部分出现故障,都可能导致加工精度降低,甚至出现停机、生产停顿,从而带来不必要的损失。本文试以T6925/1落地数显镗铣床为例,分析常见故障及排除方法。 关键词:故障分析排除 数控落地铣镗床具有镗孔、钻孔、铣削、切槽等加工功能;配上高精度回转工作台、直角铣头等功能附件,可以实现五面加工,它常用加工:批量小而多次生产的零件;形状复杂加工精度高,通用机床无法加工或很难保证加工质量的零件;在加工过程中,必须进行多工序加工,如必须在一次装夹中完成铣、镗、锪铰或攻丝等工序;必须严格控制公差的零件;具有难测量、难控制进给、难控制型腔尺寸的壳体或箱型零件。因此,了解数控落地铣镗床常见故障并及时排除故障是提高加工效率的关健。 1、常见与液压系统有关的故障原因及排除方法 1.1 噪音过大故障 噪音过大产生原因一方面由于滤油器堵塞,吸油管路漏气,油的粘度太高或油温度太低等原因,造成油泵吸空;另一方面由于油面过低,滤油器外露,吸油管路漏气,油泵轴密封环漏气等原因,使油产生泡沫;油泵磨损或损坏,油泵与电机间联轴器松动,产生机械振动等也可以引起噪音过大。 1.2 压力不足或不稳定故障 压力不足或不稳定产生原因:油泵吸入空气或油泵旋转方向不对;由于油泵损坏或磨损,油粘度过低,造成油泵过度发热;溢流阀或减压阀失灵,表现在调节时,压力无变化或有卡住现象;油泵吸空,油产生泡沫、机械振动等。 压力不足或不稳定排除方法要以采用检查油管和油泵转向;更换油泵,根据气温选择适当的工作油液;清洗溢流阀、减压阀,检查阀的磨损情况,适当修整、检查油路是否堵塞,分析溢流油阻力过大原因。 1.3 静压导轨浮不起来故障 静压导轨浮不起来产生原因一般情况是由于节流器堵塞,静压油无法进入油
数控镗铣工安全操作规程
编号:SM-ZD-64720 数控镗铣工安全操作规程Through the process agreement to achieve a unified action policy for different people, so as to coordinate action, reduce blindness, and make the work orderly. 编制:____________________ 审核:____________________ 批准:____________________ 本文档下载后可任意修改
数控镗铣工安全操作规程 简介:该规程资料适用于公司或组织通过合理化地制定计划,达成上下级或不同的人员 之间形成统一的行动方针,明确执行目标,工作内容,执行方式,执行进度,从而使整 体计划目标统一,行动协调,过程有条不紊。文档可直接下载或修改,使用时请详细阅 读内容。 一、工作前: 1、穿戴好劳保护品,每台设备必须配备专门的操作者,非操作者严禁操作设备。 2、不允许超范围、超负荷使用设备。 3、电气柜由操作者管理,非专门的电气维修人员不许随意打开。 4、工作前操作人员应检查工件零点、刀补参数是否正确,以免由于计算机故障、工作零点、刀补参数丢失而起撞车事故及伤人事故。 5、如中途离开要将操作面板电源开关以及电气柜电源开关放至零位。 6、开机前将压缩空气油水分离器阀门打开,放尽冷凝水。 7、正确安装角铣头,并点车试转,确认正常方能运转。 二、工作中:
1、任何时候必须清楚紧急停止按钮的正确位置。 2、不允许将身体任何部位靠近或置于旋转部位或移动部件上。 3、在机床启动和运转时不允许打开防护门或任何护盖。 4、如需带电维修,必须用专门培训过的人员。 5、操作人员要精力集中,应随时注意机床的运转情况以及故障信号显示状况,发现异常及时停机向有关人员报告。 6、在装卸大件或重活时,要注意人身安全并保护好工作台面,不准砸、撞或碰伤。 7、工作中使用的工、卡、量具、在制品不准随意放在机床工作台面和油漆面上。 8、切削刀具没有夹紧在主轴上之前,禁止启动主轴。工件在工作台上没有固定夹紧之前禁止切削。 9、设备如发生事故,要了立即切断电源,保护现场,及时上报,按事故程序办理。 三、工作后: 1、停止控制开关、切断液压电路。 2、擦拭机床各部位。并选用专用敷料擦拭主轴锥杆,将
TK6913落地镗铣床性能特点及技术参数
TK6913落地镗铣床性能特点及技术参数 TX6913落地镗铣床用途及性能: TX6913落地镗铣床为万能型机床,该机床性能完善,有较高刚度和精度,可对大型零件进行钻孔、镗孔、铣平面等加工,能满足零件精加工要求,广泛应用于能源、 交通、重型机械等行业,是加工床身、立柱及箱体类零件的关键设备。机床有自由伸出的方滑枕,内装有铣轴和镗轴。适应大型零件的强力铣削,增强了镗削时的刚性,在铣轴端部可装平旋盘,方滑枕的端部可以安装垂直铣头、万能铣头等机床附件,扩大了机床的使用功能。落地镗铣床与回旋工作台配合使用,在一次装夹内能完成多种工序的平面铣削和镗削加工。 TK6913落地镗铣床产品图片
TK6913落地镗铣床技术参数 技术规格单位TX6913 TX6913 镗轴直径mm 221.4 221.4 铣轴端部直径mm ISO50(h或莫 氏6#) ISO50 主轴转速r/min 2-700 2-700 主电机功率kw 22 22 滑枕断面尺寸mm 380*380 380*380 立柱横向行程mm 6000(可加长) 6000(可加 长) 主轴箱垂直向 行程mm 2000(可加长) 2000(可加 长) 滑枕伸缩行程mm 600 600 主轴轴向行程mm 800 800 进给电机功率 kw X 5.5 5.5 Y 5.5 5.5 Z 3.7 3.7 3.7 3.7
W 进给电机扭距 N.n x 36.9 36.9 Y 36.9 36.9 Z 24.8 24.8 W 24.8 24.8 给进速度 mm/min X 1-2000 1-2000 Y 1-2000 1-2000 Z 1-1500 1-1500 W 1-1500 1-1500 定位精度 mm X.Y ---- 0.035/100 Z.W ---- 0.045/100 重负定位精度mm ---- 0.03
数控机床的现状与发展
数控机床现状及发展趋势分析 数控机床的概念 数控机床就是在数字控制下,能在尺寸精度和几何精度两方面完成金属毛坯零件加工成所需要形状的工作母机的总称。数控机床通常由控制系统、伺服系统、检测系统、机械传动系统及其他辅助系统组成。 国产数控机床的发展现状 一、国产数控机床与国际先进水平差距逐渐缩小 数控机床是当代机械制造业的主流装备,国产数控机床的发展经历{HotTag}了30年跌宕起伏,已经由成长期进入了成熟期,可提供市场1,500种数控机床,覆盖超重型机床、高精度机床、特种加工机床、锻压设备、前沿高技术机床等领域,产品种类可与日、德、意、美等国并驾齐驱。特别是在五轴联动数控机床、数控超重型机床、立式卧式加工中心、数控车床、数控齿轮加工机床领域部分技术已经达到世界先进水平。其中,五轴(坐标)联动数控机床是数控机床技术的制高点标志之一。 它集计算机控制、高性能伺服驱动和精密加工技术于一体,应用于复杂曲面的高效、精密、自动化加工,是发电、船舶、航天航空、模具、高精密仪器等民用工业和军工部门迫切需要的关键加工设备。
五轴联动数控机床的应用,其加工效率相当于2台三轴机床,甚至可以完全省去某些大型自动化生产线的投资,大大节约了占地空间和工作在不同制造单元之间的周转运输时间及费用。国产五轴联动数控机床品种日趋增多,国际强手对中国限制的五轴联动加工中心、五轴数控铣床、五轴龙门铣床、五轴落地铣镗床等均在国内研制成功,改变了国际强手对数控机床产业的垄断局面。 二、国产数控机床存在的问题 由于中国技术水平和工业基础还比较落后,数控机床的性能、水平和可*性与工业发达国家相比,差距还是很大,尤其是数控系统的控制可*性还较差,数控产业尚未真正形成。因此加速进行数控系统的工程化、商品化攻关,尽快建成与完善数控机床和数控产业成为当前的主要任务。目前主要问题有: 三、核心技术严重缺乏 统计数据表明,数控机床的核心技术—数控系统,由显示器、控制器伺服、伺服电机和各种开关、传感器构成,中国90%需要国外进口。如在上海设厂的德国吉特迈集团和意大利利雅路机床集团,在烟台建厂的韩国大宇综合机械株式会社,所有的核心技术都被外方掌握。国内能做的中、高端数控机床,更多处于组装和制造环节,普遍未掌握核心技术。国产数控机床的关键零部件和关键技术主要依赖进口,国内真正大而强的企业并不多。目前世界最大的3家厂商是:日
卧式镗床操作规程通用版
操作规程编号:YTO-FS-PD998 卧式镗床操作规程通用版 In Order T o Standardize The Management Of Daily Behavior, The Activities And T asks Are Controlled By The Determined Terms, So As T o Achieve The Effect Of Safe Production And Reduce Hidden Dangers. 标准/ 权威/ 规范/ 实用 Authoritative And Practical Standards
卧式镗床操作规程通用版 使用提示:本操作规程文件可用于工作中为规范日常行为与作业运行过程的管理,通过对确定的条款对活动和任务实施控制,使活动和任务在受控状态,从而达到安全生产和减少隐患的效果。文件下载后可定制修改,请根据实际需要进行调整和使用。 适用机型: 1、卧式镗床:T616,T617,T618,75型,T68(262G),T611(262Д),T612(2630),JT68, 2A613,WH80,BFT100/iV,BFT-13CM1,BFT125/5。 2、落地镗床:AFM150,T6210。 3、专用镗床:AY2-020,AY217,AY218, SF73009。 一、认真执行《金属切削机床通用操作规程》有关规定。 二、认真执行相述有关镗床通用规定: (一)工作中认真做到: 1、工件的安置,应使工作台受力均匀,毛坯面不准直接放到工作台面上,装夹用的垫板,压析等必须平正。 2、拆卸带锥度的刀具时,须用标准楔冲下,不准用其他工具随意敲打。
数控技术的最新发展趋势
数控技术的最新发展趋势 数控技术是以数字化进行控制机床运作及加工过程的一种方法,由数控装置、进给装置、可编程控制器、主轴驱动器等部分组成。信息技术、计算机技术、传统控制技术的优化结构及有机结合,给数控技术发展现代化提供了新的契机和空间。数控技术的不断发展和应用领域的不断扩大,对关系国计民生的重要行业的发展起着越来越重要的作用。 一、数控技术的发展现状 目前,数控技术正在发生根本性变革,由专用型封闭式开环控制模式向通用型开放式实时动态全闭环控制模式发展。在集成化基础上,数控系统实现了超薄型、超小型化;在智能化基础上,综合了计算机、多媒体、模糊控制、神经网络等多学科技术,数控系统实现了高速、高精、高效控制,加工过程中可以自动修正、调节与补偿各项参数,实现了在线诊断和智能化故障处理;在网络化基础上,CAD/CAM 与数控系统集成为一体,机床联网,实现了中央集中控制的群控加工。长期以来,我国的数控系统为传统的封闭式体系结构,CNC只能作为非智能的机床运动控制器。加工过程变量根据经验以固定参数形式事先设定,加工程序在实际加工前用手工方式或通过CAD/CAM及自动编程系统进行编制。CAD/CAM和CNC之间没有反馈控制环节,整个制造过程中CNC 只是一个封闭式的开环执行机构。在复杂环境以及多变条件下,加工过程中的刀具组合、工件材料、主轴转速、进给速率、刀具轨迹、切削深度、步长、加工余量等加工参数,无法在现场
环境下根据外部干扰和随机因素实时动态调整,更无法通过反馈控制环节随机修正CAD/CAM 中的设定量,因而影响CNC 的工作效率和产品加工质量。由此可见,传统CNC 系统的这种固定程序控制模式和封闭式体系结构,限制了CNC 向多变量智能化控制发展,已不适应日益复杂的制造过程,因此,对数控技术实行变革势在必行。二、数控技术发展趋势 进入20 世纪90 年代以来, 由于计算机技术的飞速发展, 推动了数控机床技术更快的更新换代。 2.1 数控技术体系结构的发展 首先,体系结构的网络化。通过机床联网的形式,可以在任一台机床上对其它机床进行操作、编程、运行、设定,而且不同机床的画面可以同时显示在每台机床的屏幕上。因此,机床联网可以进行无人化操作和远程控制。其次,体系结构的集成化。采用高度集成化的RISC、CPU 芯片和大规模可编程集成电路EPLD、FPGA、CPLD 及专用集成电路ASIC芯片,可以提高软硬件运行速度和数控系统的集成度。而且应用FPD 平板显示技术,还可提高显示器的性能。 2.2 数控技术的性能发展方向 首先,工艺复合性及多轴化。数控机床的工艺复合化,是指工件在一台机床上经一次装夹后,通过旋转主轴头、自动换刀或转台等各种措施,完成多表面、多工序的复合加工。其次,性能的高速高精高效化。速度、精度及效率是机械制造技术的主要性能指标。采用RISC 芯片、高速CPU 芯片、带高分辨率绝对式检测元件以及多CPU 控制
镗床安全操作规程
镗床安全操作规程 1.操作机床前必须认真阅读该设备的说明书,了解掌握机床结构性能和机床上所有“警告标牌”的内容,严格按要求操作,否则会造成人身伤亡事故! 2.机床的安装、操作、保养、检修要经过专门培训过的专业人员按照使用说明书中规定的步骤进行。 3.操作者使用机床时,要穿好劳动保护服,禁止穿宽松外衣,佩戴各种饰物,以免发生安全事故。 4.开动机床前检查各部件的安全防护装置和周围工作环境,各移动部件的限位开关是否起作用,在行程范围内是否畅通,是否有障碍物,是否能保证机床在任何时候都具有良好的安全状况。 5.工作进行中严禁触摸旋转的刀具。进行测量,调整和清洁时必须停机。对电机等电气件要经常打扫积尘,以免防碍通风(禁止使用压缩空气清扫机床)。 6.操作人员在机床运转中应注意:禁止将身体任何部位靠近或置于旋转移动部件;机床运转时严禁打开防护门或任何护盖:工件和切削刀具必须夹持牢固;严禁超负荷工作等。 7.接通电源前必须做好相关的安全检查工作,了解各开关功能。打开电柜门,护盖门或维修前必须切断或锁住电源,如需带电维修时,必须由专门培训的专业人员进行。 8.机床工作环境周围禁止堆放易燃物品,切削运转时严禁使用容易燃烧的冷却液。工作结束后必须切断机床总电源,避免无人照管时有着火的危险。 9.机床工作过程中,必须远离移动部件。 使用用应严格执行下列要求: 1.工件的安置,应使工作台受力均匀,毛坯面不准直接放到工作台面上,装夹用的垫板,压析等必须平正。
2.拆卸带锥度的刀具时,须用标准楔冲下,不准用其他工具随意敲打。 3.使用镗杆制动装置时,应在镗杆惯性转速降低后再进行。 4.不准同时作两个以上的机构运动,如主轴箱升降时,不准移动镗杆。 5.不准用机动对刀,当刀具快接近工件时,应改为手动。 6.使用花盘径向刀架作径向进给时,镗杆应退回主轴箱内,同时径向刀架不准超出极限。 7.机床上的光学装置或清密刻度尺,应小心使用,目境用后应将盖子盖住,保持目境和刻度尺清洁。不准用一般布料和不清洁的擦料擦试,不准任意拆卸和调正光学装置和刻度尺。 8.在主轴旋转时,主轴与主轴套筒的间隙随温升而缩小,操作时要特别注意,若主轴移动困难时,必须立即停车,待一段时间湿度下降间隙恢复增大后再工作。 9.严禁利用工作台面或落地镗床的大平台面,进行其他作业如校正工件或焊接工件等。 10.工作后,将工作台放在中间位置,镗杆退回主轴内。
数控镗床操作规程
?数控镗床操作规程 1、操作者必须熟悉本设备结构性能,传动原理以及控制程序,经考试合格取得操作证后方可独立操作。 2、操作者要认真做到“三好”(管好、用好、修好)“四会”(会使用、会保养、会检查、会排除故障). 3、操作者必须遵守使用设备得“五项纪律"与维护设备得“四项要求”得规定. 4、操作者要随时按照“巡回检查内容”得要求对设备进行检查。 5、严格按照设备用油要求进行加油,做到润滑“五定”(定时、定点、定量、定质、定人). 6、禁止两人或多人同时操作。 7、严禁超负荷、超规范使用设备. 8、当设备停机八小时以上,应先启动机床液压润滑5—10分钟,然后再用手动方式运转各运动轴,查瞧各部运转就是否正常;确认运转正常、润滑良好、无任何报警、方能开始工作. 9、工作前应根据工件材质、技术要求、刀具材料合理选择切削用量,正确编写加工程序,核对无误后方能进行试切及工件加工。 10、主轴变档必须在停车状态下进行,如果齿轮位置挂不上,可将电机点动一下,停机后,再进行换档,直到正确。进给变速也应在停车或低速时进行。 11、在开动机床各运动轴时,应注意观察周围环境有无障碍物,确认安全后方能开动。 12、在调整对刀时,刀具距离加工面50mm内不得使用快速,应使用手动对刀。 13、当机床各运动轴距离极限位置100mm处,不得再使用快速移动。 14、严禁在切削过程中停止主电机。停止主轴应先停自动走刀,退出刀具,降低转速,方能停车。 15、切削过程中绝不允许测量尺寸、对样板、手摸加工面或将头贴近主轴观察,避免发生人身安全事故。 16、任何情况下禁止用镗杆与方滑枕(花盘)顶撞或校正工件。 17、在工作中应爱护主轴(镗杆),避免碰伤与研伤。在装刀时应将镗杆及附件铣头锥孔、刀具锥面清擦干净,避免研伤。 18、在铣削加工过程中经常注意刀具与工件得紧固情况,刀刃磨钝了,不得继续使用。 19、因切削时间长,热膨胀使镗轴或滑枕移动困难时,不准强行移动。 20、更换刀具时,不应转动主轴。。 21、必须清楚机床“紧急停车按钮”得位置,遇到紧急情况应及时按下“紧急停车按钮”以断开主电源。 22、应经常保持镗杆、方滑枕及立柱裸露导轨清洁,严禁在操作面板、方滑枕、操作室、导轨护板上堆放杂物,不允许踩踏机床护板。 23、高速镗杆一般只用于钻孔,轻铣及铣槽时使用. 24、设备开动时,严禁操作者离开岗位或托人代管。 25、停机前,各轴应低速运动,将镗轴、方滑枕缩回,其她移动部件运行至安全位置。 26、未经许可禁止打开电控柜. 27、注意观察机床稳压柜、电柜空调、油制冷单元、排削装置等辅助设施运行就是否正常;及时倒掉制冷设施得冷凝水,避免油质乳化,保持环境整洁。 28、工作中如发生异常情况,如声音不正常,局部温度升高、电流增大、油路不畅通、运动不均匀、指示信号不正常等都应停车检查,如不能判断排除时,应停止使用设备,报告维修人员处理.当设备发生事故时,应保持现场并及时报告公司与设备科。 29、设备长期不使用,应注意防潮,停机两周以上应给数控系统通电八小时,以保证相关数据不丢失.
数控技术的发展及国内外现状
数控技术的发展及国内外现状 数控技术的发展及国内外现状 摘要:数控技术(Numerical Contrl)是一种采用计算机对生产过程中各种控制信息进行数字化运算、处理,并通过高性能的驱动单元对机械执行构件进行自动化控制的高新技术。本文对数控技术的发展经行了研究,并比较对比了国内外数控技术的发展现状,对国内数控未来的发展提出了建议。 关键词:数控技术;发展;国内外现状 数控技术集传统的机械制造技术、计算机技术、现代控制技术、传感检测技术、网络通信技术和光、电技术于一体的现代制造业的基础技术。它具有高精度、高效率、柔性自动化等特点,对制造业实现柔性自动化、集成化和智能化起着举足轻重的作用。数控技术是制造自动化的基础,是现代制造装备的灵魂核心,是国家工业和国防工业现代化的重要手段,关系到国家战略地位,体现国家综合国力水平,其水平的高低和数控装备拥有量的多少是衡量一个国家工业现代化的重要标志。 1.数控技术的发展概述 1948年,美国帕森斯公司接受美国空军委托,研制直升飞机螺旋桨叶片轮廓检验用样板的加工设备。由于样板形状复杂多样,精度要求高,一般加工设备难以适应,于是提出采用数字脉冲控制机床的设想。1949年,该公司与美国麻省理工学院(MIT)开始共同研究,并于1952年试制成功第一台三坐标数控铣床,当时的数控装置采用电子管元件。1959年,数控装置采用了晶体管元件和印刷电路板,出现带自动换刀装置的数控机床,称为加工中心( MC Machining Center),使数控装置进入了第二代。60年代末,先后出现了由一台计算机直接控制多台机床的直接数控系统(简称 DNC),又称群控系统;采用小型计算机控制的计算机数控系统(简称 CNC),使数控装置进入了以小型计算机化为特征的第四代。 1974年,研制成功使用微处理器和半导体存贮器的微型计算机
数控落地镗铣床项目可行性研究报告(可编辑)
数控落地镗铣床项目可行性研究报告 规划设计 / 投资分析
摘要 该数控落地镗铣床项目计划总投资18711.69万元,其中:固定资产投 资13866.48万元,占项目总投资的74.11%;流动资金4845.21万元,占项目总投资的25.89%。 达产年营业收入40195.00万元,总成本费用31603.31万元,税金及 附加363.06万元,利润总额8591.69万元,利税总额10139.81万元,税 后净利润6443.77万元,达产年纳税总额3696.04万元;达产年投资利润 率45.92%,投资利税率54.19%,投资回报率34.44%,全部投资回收期 4.40年,提供就业职位674个。 重视环境保护的原则。使投资项目建设达到环境保护的要求,同时, 严格执行国家有关企业安全卫生的各项法律、法规,并做到环境保护“三废”治理措施以及工程建设“三同时”的要求,使企业达到安全、整洁、 文明生产的目的。 项目总论、项目建设必要性分析、市场分析、调研、建设规划方案、 选址评价、项目土建工程、工艺技术分析、清洁生产和环境保护、安全卫生、投资风险分析、节能评估、计划安排、项目投资估算、项目经济评价、总结说明等。
数控落地镗铣床项目可行性研究报告目录 第一章项目总论 第二章项目建设必要性分析 第三章市场分析、调研 第四章建设规划方案 第五章选址评价 第六章项目土建工程 第七章工艺技术分析 第八章清洁生产和环境保护 第九章安全卫生 第十章投资风险分析 第十一章节能评估 第十二章计划安排 第十三章项目投资估算 第十四章项目经济评价 第十五章项目招投标方案 第十六章总结说明
镗床安全操作规程
镗床安全操作规程 1、操作前要穿紧身防护服,袖口扣紧,上衣下摆不能敞开,不得在开动的机床旁穿、脱换衣服,或围布于身上,防止机器绞伤。女工必须戴好安全帽,不得留长辫子,辫子应放入帽内,不得穿裙子、拖鞋。高速切削和产生崩碎切屑时,要戴好防护镜;以防铁屑飞溅伤眼,并在机床周围安装挡板使之与操作区隔离。 2、操作者必须熟悉设备的结构和性能,严禁超规格使用设备。 3、工作前必须检查油箱储油量,并按设备润滑图表规定注油,注油后应将油杯(池)盖好。 4、停车八小时再开动设备应先低速转3—5分钟,确认润滑系统畅通,各部分运转正常后再开始工作。 5、禁止在镗杆锥孔内安装与其锥度不符或锥面有划痕、不清洁的工具。 6、机床各部分的夹紧装置、在部件不动时应将其夹紧。 7、在移动主轴箱、主轴工作台上滑板、下滑板前必须松开夹紧装置,并保证其滑动面、丝杆、牙条的清洁和润滑良好,同时还必须检查移动方向是否会和主轴相碰,确认安全后方可开车。 8、不得用开反车的方法制动回转的花盘或镗杆。 9、工作中进给(或快速)有报警时,应立即停止主电机并查明原因。 10、手动手柄不能放在机动位置上走快车。 11、在工作台回转90°时不允许用力撞击定位档块。 12、主轴变换转速时将手柄拉到相反位置,然后按表牌转到所需位置把手柄转盘推上,若有阻力,可将手柄推拉几次即可完成变速。 13、只有在机床停车时,才可以操纵变换速度和进给量的手柄转盘。 14、禁止使用磨钝的刀具进行切削。禁止在工作台上敲打和校直工件。 15、禁止操作者离开或托人代管开动着的设备。 16、工作中必须注意经常清除上下滑板及工作台导轨上的铁屑和油污,并保持周围环境整洁。、 17、使用铣刀盘铣削平面时,刀盘上安装的刀具一般不得少于二把。 18、使用花盘径向刀架单独切削时,镗杆需退后到极限位置。 19、在切削过程中刀具未退开工件前不得停车。 20、工作完毕时需将各手柄置于非工作位置上,工作台退到中间位置,镗杆退回,并切断电源。 21、工作完毕,做好机器的保养和清洁工作。
数控镗床操作规程正式样本
文件编号:TP-AR-L3336 There Are Certain Management Mechanisms And Methods In The Management Of Organizations, And The Provisions Are Binding On The Personnel Within The Jurisdiction, Which Should Be Observed By Each Party. (示范文本) 编制:_______________ 审核:_______________ 单位:_______________ 数控镗床操作规程正式 样本
数控镗床操作规程正式样本 使用注意:该操作规程资料可用在组织/机构/单位管理上,形成一定的管理机制和管理原则、管理方法以及管理机构设置的规范,条款对管辖范围内人员具有约束力需各自遵守。材料内容可根据实际情况作相应修改,请在使用时认真阅读。 1开机后要明确开机、关机的工作顺序,首先要 用手动或程序指令使各轴自动检测参考点。 2空车试运转确认机床自动润滑正常后,进入加 工程序。 3编制新程序,应采取慢速接近工件形式,输入 后检查程序的准确性,模拟运行,未经试验不允许进 入自动循坏操作,以防止碰撞。 4机床开动前,检查平旋盘刀盘、镗刀、工件确 保装卡牢固,装卡工件压板必须水平,垫铁不宜过高 或过多。 5加工时,严禁超性能、规格使用机床,严禁工
作台超重、超长安装工件,特殊情况超长加工工件时,工件自由端应有可调支撑装置,并不得危及周围人和物。 6机床运转时,严禁进入危险区域量尺寸、对样板或身体任何部位碰触加工面、旋转件或停留在移动件上,更要防止衣物绞缠。 7镗孔、扩孔时不准将头贴近加工孔观察吃刀情况,更不准隔着转动的镗杆取东西。 8启动工作台自动回转时(B轴),必须将镗杆缩回,保障工作台旋转时不碰撞机床其它部件或周围的人和物,回转时工作台上禁止站人。 9当机床的主轴箱、工作台处于或接近极限位置时,操作者不得进入运动件和静止件之间的狭窄区域,防止挤压伤发生。 10两人以上操作一台镗床时,应密切联系,互
国内外数控技术发展
国内外数控技术发展 20世纪人类社会最伟大的科技成果是计算机的发明与应用,计算机及控制技术在机械制造设备中的应用是世纪内制造业发展的最重大的技术进步。自从1952年美国第1台数控铣床问世至今已经历了50个年头。数控设备包括:车、铣、加工中心、镗、磨、冲压、电加工以及各类专机,形成庞大的数控制造设备家族,每年全世界的产量有10~20万台,产值上百亿美元。世界制造业在20世纪末的十几年中经历了几次反复,曾一度几乎快成为夕阳工业,所以美国人首先提出了要振兴现代制造业。90年代的全世界数控机床制造业都经过重大改组。如美国、德国等几大制造商都经过较大变动,从90年代初开始已出现明显的回升,在全世界制造业形成新的技术更新浪潮。如德国机床行业从2000年至今已接受3个月以后的订货合同,生产任务饱满。 我国数控机床制造业在80年代曾有过高速发展的阶段,许多机床厂从传统产品实现向数控化产品的转型。但总的来说,技术水平不高,质量不佳,所以在90年代初期面临国家经济由计划性经济向市场经济转移调整,经历了几年最困难的萧条时期,那时生产能力降到50%,库存超过4个月。从1995年“九五”以后国家从扩大内需启动机床市场,加强限制进口数控设备的审批,投资重点支持关键数控系统、设备、技术攻关,对数控设备生产起到了很大的促进作用,尤
其是在1999年以后,国家向国防工业及关键民用工业部门投入大量技改资金,使数控设备制造市场一派繁荣。从2000年8月份的上海数控机床展览会和2001年4月北京国际机床展览会上,也可以看到多品种产品的繁荣景象。但也反映了下列问题: (1)低技术水平的产品竞争激烈,互相靠压价促销; (2)高技术水平、全功能产品主要靠进口; (3)配套的高质量功能部件、数控系统附件主要靠进口;(4)应用技术水平较低,联网技术没有完全推广使用; (5)自行开发能力较差,相对有较高技术水平产品主要靠引进图纸、合资生产或进口件组装。 当今世界工业国家数控机床的拥有量反映了这个国家的经济能力和国防实力。目前我国是全世界机床拥有量最多的国家(近300万台),但我们的机床数控化率仅达到1.9%左右,这与西方工业国家一般能达到20%的差距太大。日本不到80万台的机床却有近10倍于我国的制造能力。数控化率低,已有数控机床利用率、开动率低,这是发展我国21世纪制造业必须首先解决的最主要问题。每年我们国产全功能数控机床3000~4000台,日本1年产5万多台数控机床,每年我们花十几亿美元进口7000~9000台数控机床,即使这样我国制造业也很难把行业中数控化率大幅度提上去。因此,国家计委、经贸委从“八五”、“九五”就提出数控化改造的方针,在“九五”期间,我协会也曾做过调研。当时提出数控化改造的设备可达8~10万台,需投入80~100亿资金,但得到的经济效益将
卧式镗床操作规程
XXX 有限公司 质 量 管 理 体 系 Quality Management System 卧式镗床操作规程 Working Instruction (依据GB/T19016-2000 idt ISO9001:2015 《质量管理体系-要求》 标准而制定) FL-WI-19 (第A/0版) 拟编: 审核: 批准: 发布日期: 实施日期: 地址:中国. 福建. 电话:++86-592- 传真:++86-592- 邮政编码: 受 控 状 态 发 放 编 号
适用机型: 1、卧式镗床:T616,T617,T618,75型,T68(262G),T611(262Д),T612(2630),JT68,2A613,WH80,BFT100/iV,BFT-13CM1,BFT125/5。 2、落地镗床:AFM150,T6210。 3、专用镗床:AY2-020,AY217,AY218,SF73009。 一、认真执行《金属切削机床通用操作规程》有关规定。 二、认真执行相述有关镗床通用规定: (一)工作中认真做到: 1、工件的安置,应使工作台受力均匀,毛坯面不准直接放到工作台面上,装夹用的垫板,压析等必须平正。 2、拆卸带锥度的刀具时,须用标准楔冲下,不准用其他工具随意敲打。 3、使用镗杆制动装置时,应在镗杆惯性转速降低后再进行。 4、不准同时作两个以上的机构运动,如主轴箱升降时,不准移动镗杆。 5、不准用机动对刀,当刀具快接近工件时,应改为手动。 6、使用花盘径向刀架作径向进给时,镗杆应退回主轴箱内,同时径向刀架不准超出极限。 7、机床上的光学装置或清密刻度尺,应小心使用,目境用后应将盖子盖住,保持目境和刻度尺清洁。不准用一般布料和不清洁的擦料擦试,不准任意拆卸和调正光学装置和刻度尺。 8、在主轴旋转时,主轴与主轴套筒的间隙随温升而缩小,操作时要特别注意,若主轴移动困难时,必须立即停车,待一段时间湿度下降间隙恢复增大后再工作。 9、严禁利用工作台面或落地镗床的大平台面,进行其他作业如校正工件或焊接工件等。 (二)工作后,将工作台放在中间位置,镗杆退回主轴内。 三、认真执行下述有关特殊规定: (一) T68,T611镗床: 1、主变速手柄及走刀变速手柄未扳转到180°时,不准回转的柄。当主轴降到最低转数是,方准将手柄推下。 2、将工作台回转90°时,不准用力过大撞击定位挡铁。 (二) BFT-13CW1镗床: 1、镗孔时,镗杆伸出长度不得超过500毫米。使用花盘和径向刀架时,转数不得超过180转/分。只有径向刀架在平衡的情况下,转数才能提高到250转/分。 2、主轴连续运转的情况下,最高转速不得超过350转/分。若工作需要使用最高速时,其连续运转时间不得超过30分钟。 3、往加油器中加油时,绝不允许加到红色指标线以上。 (三) T6216落地镗床: 1、当花盘紧固在空心轴上时,旋转速度不易太高,用径向刀架时不得超过120转/分,径向刀架在"0"
数控镗床操作规程(2021年)
The prerequisite for vigorously developing our productivity is that we must be responsible for the safety of our company and our own lives. (安全管理) 单位:___________________ 姓名:___________________ 日期:___________________ 数控镗床操作规程(2021年)
数控镗床操作规程(2021年)导语:建立和健全我们的现代企业制度,是指引我们生产劳动的方向。而大力发展我们生产力的前提,是我们必须对我们企业和我们自己的生命安全负责。可用于实体印刷或电子存档(使用前请详细阅读条款)。 1开机后要明确开机、关机的工作顺序,首先要用手动或程序指令使各轴自动检测参考点。 2空车试运转确认机床自动润滑正常后,进入加工程序。 3编制新程序,应采取慢速接近工件形式,输入后检查程序的准确性,模拟运行,未经试验不允许进入自动循坏操作,以防止碰撞。 4机床开动前,检查平旋盘刀盘、镗刀、工件确保装卡牢固,装卡工件压板必须水平,垫铁不宜过高或过多。 5加工时,严禁超性能、规格使用机床,严禁工作台超重、超长安装工件,特殊情况超长加工工件时,工件自由端应有可调支撑装置,并不得危及周围人和物。 6机床运转时,严禁进入危险区域量尺寸、对样板或身体任何部位碰触加工面、旋转件或停留在移动件上,更要防止衣物绞缠。 7镗孔、扩孔时不准将头贴近加工孔观察吃刀情况,更不准隔着转动的镗杆取东西。
8启动工作台自动回转时(B轴),必须将镗杆缩回,保障工作台旋转时不碰撞机床其它部件或周围的人和物,回转时工作台上禁止站人。 9当机床的主轴箱、工作台处于或接近极限位置时,操作者不得进入运动件和静止件之间的狭窄区域,防止挤压伤发生。 10两人以上操作一台镗床时,应密切联系,互相配合,并由主操作人员统一指挥操作,严禁实习等无独立操作资格人员擅自开动机床。 11严禁踩踏机床道轨和在其上放置物品,严禁在工作台上校工件,严禁任意拆除机床装置。 XX设计有限公司 Your Name Design Co., Ltd.