ITO透明导电薄膜的磁控溅射法制备工艺

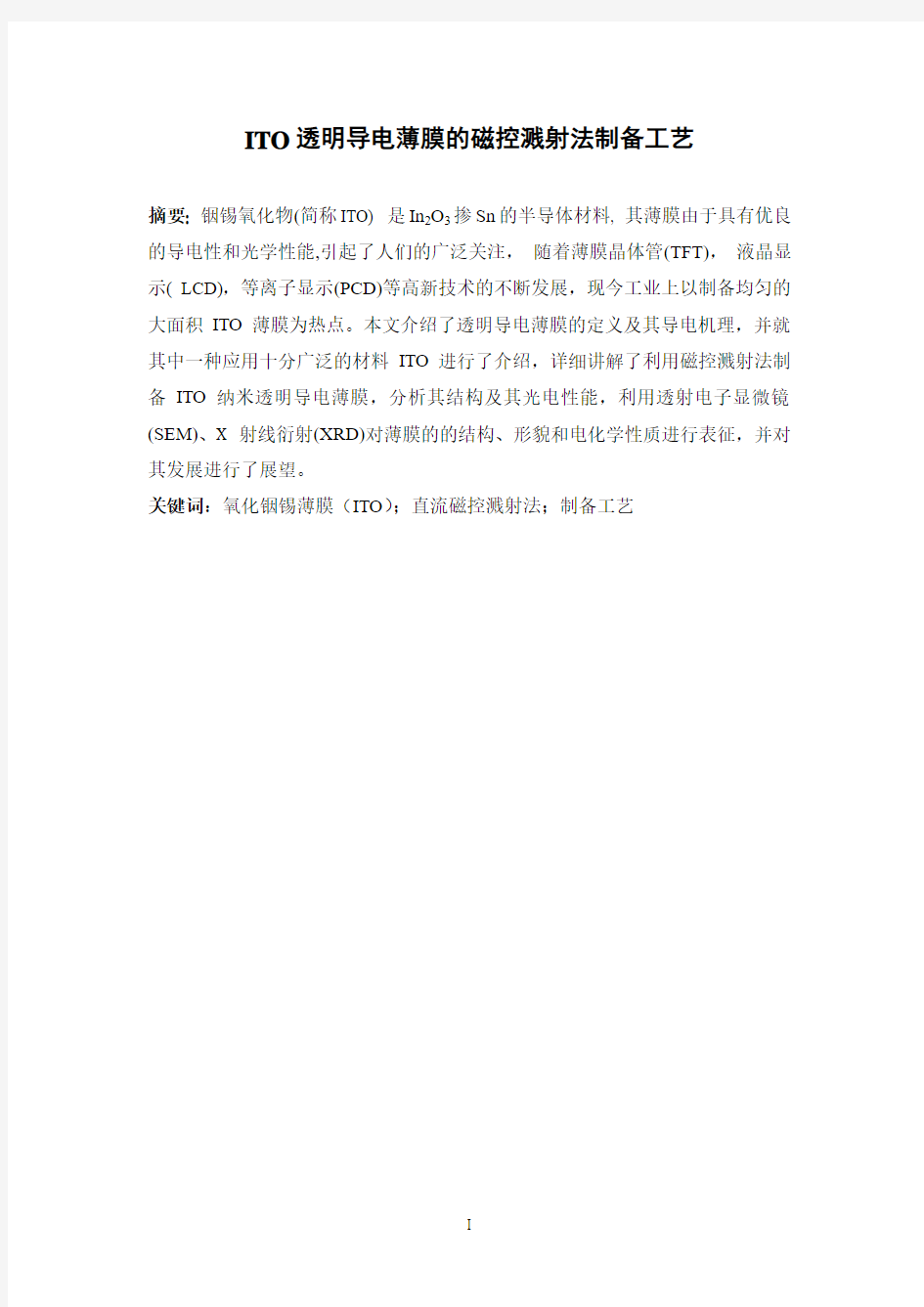
J I A N G S U U N I V E R S I T Y 课程设计论文
ITO透明导电薄膜的磁控溅射法制备工艺
学院名称: 材料学院
专业班级: 无机光电0902
学生姓名: 张亚平
指导教师姓名: 李保家
指导教师职称:
2012 年 6 月
摘要: 铟锡氧化物(简称ITO) 是In2O3掺Sn的半导体材料, 其薄膜由于具有优良的导电性和光学性能,引起了人们的广泛关注,随着薄膜晶体管(TFT),液晶显示( LCD),等离子显示(PCD)等高新技术的不断发展,现今工业上以制备均匀的大面积ITO薄膜为热点。本文介绍了透明导电薄膜的定义及其导电机理,并就其中一种应用十分广泛的材料ITO进行了介绍,详细讲解了利用磁控溅射法制备ITO纳米透明导电薄膜,分析其结构及其光电性能,利用透射电子显微镜(SEM)、X 射线衍射(XRD)对薄膜的的结构、形貌和电化学性质进行表征,并对其发展进行了展望。
关键词:氧化铟锡薄膜(ITO);直流磁控溅射法;制备工艺
1 引言
透明导电薄膜是一种既能导电又在可见光范围内具有高透明率的一种薄膜,透过性的标准是透过率60%以上,导电性的标准是表面电阻在1010Ω·cm 以下[1]。透明导电薄膜的种类主要有金属膜、氧化物膜、多层复合膜和高分子膜等, 其中氧化物薄膜占主导地位。透明导电氧化物( TCO) 薄膜主要包括In 、Sn 、Zn 、Cd 的氧化物及其复合多元氧化物薄膜。1907年Badeker 首先制备并报道了 CdO 透明导电薄膜, 将物质的透明性和导电性这一矛盾统一起来。在随后的几十年中,人们发现和研究了多种材料的 TCO 薄膜,并不断扩大它们的用途。目前研究人员主要集中在对SnO2基、In 2O 3基以及ZnO 基透明导电膜的研究[2]。 2 透明导电薄膜的导电机理
2.1 透明度
透明导电膜的透明度主要取决于膜的光纳N =n - i k 和光学厚度nd 。在基底的光纳N g =n g -ik g ,和透明光波的波长认确定的条件下,由光学薄膜的理论可计算出单层膜的透光率[3]
*))(()
(4000C B N C B N N R N T g e ++= (1)
式中N 0是光波入射介质的光纳,R e (N g ) 是基底光纳的实部,B 和C 是膜系特征矩阵的元素。
??
??????????=??????g N i N i C B 1c o s s i n /)s i n (c o s δδδδ (2) ()3cos )/2(θλπδnd = (3)
式中θ是折射角。一般情况 下 N 0= 1,N g =1.5 2,nd =λ/2,θ = 0o 。
In 2O 3-x 膜的光纳 N =n -i k ,其中n =2,在一定的工艺条件下和在可见光谱区域内,左k →O ,代入公式(1)可计算出 In 2O 3-x 膜对可见光的积分透光率T =90%。理论计算的结果与实测的结果非常接近。In 2O 3-x 膜的短波吸收限在0.38μm ,掺入适量的SnO 2后吸收限可推移到0.35μm 。
为了提高透明导电膜的透光率,将单层的膜再与一种或几种光学介质膜组
合,能够设计成多层增透膜系,从而达到高透明的目的。
2.2 导电性
透明导电膜的导电性可用能带理论进行解释。
金属薄膜的禁带宽度近似于零,如图1a所示[4]。电子很容易由满带跨跃到导带中去,形成了自由电子,因自由电子的浓度很高,因此金属薄膜的导电性非常好。有些金属膜的禁带尽管还是有一定的宽度,但它满带中的一些能级上没有充满电子,如图1b 所示,这类金属膜的导电性也较好。
介质膜的禁带宽度很宽,如图1c所示,满带中的电子在外电场作用下不能跨过禁带而进入导带中去,因而不能形成导电的电子。介质膜属于绝缘体。
半导体薄膜的禁带宽度较窄,通常约为1eV,如图1d所示。在较弱的外电场作用下一部分电子能够跃过禁带而进入导带中去,形成了导电的电子。而满带中失去电子的地方便成为一个空穴。在半导体理论中把导带中的电子和满带中的空穴统称为载流子。
结构完整和成份很纯的半导体薄膜属于电子和空穴混合导电的本征半导体膜层,其载流子浓度较低,导电性并不好,方电阻往往较大。为了改善半导体膜的导电性,需要将膜的结构具有适当的缺陷和膜成份中具有适量的掺杂。
图1 电子填充能带的情况
一种缺陷是膜层晶格点阵中缺少了负离子或者填隙了正离子,就如同那里有一个正电中心,能带理论认为,正电中心的能级一般地分布在禁带之中,并且靠近导带,正电中心能级上的电子能够较容易地跨跃到导带中去,使导带中的载流子浓度提高了,得到的是n型半导体膜层。如果膜层晶格点阵中缺少了正离子或者填隙了负离子,就如同那里有一个负电中心,负电中心的能级一般地分布在禁带之中,并且靠近满带,满带中的电子能够容易地跨跃到负电中心的能级上去,从而在满带中就出现了空穴,同样也提高了载流子浓度,得到的是p型半导体膜层。
在高真空下镀制半导体膜层时,由于缺氧,膜层晶格中金属离子的比例增多了,通常得到的是带正电中心的n型半导体膜层,在氧气中镀制半导体膜层时,由于氧过量,膜层晶格中氧离子的比例增多了,通常得到的是带负电中心的p 型半导体膜层[5]。
掺杂也能改善半导体薄膜的导电性,一种掺杂是使晶格中产生多余的非共有化运动的价电子,例如In203薄膜中掺杂适量的Sn02后,晶格点阵中一部分三价的锢离子In+3就被四价的锡离子Sn+4所占据,锡离子Sn+4中有三个价电子与相邻的铟离子共有化,还剩一个价电子不能参加共有化运动,这个非共有化价电子的能级分布在禁带之中并靠近导带,在常温下这个价电子很容易跃迁到导带上去变成自由电子,使得整个晶体的载流子(指电子)浓度提高了,从而改善了In2O3膜的导电性。另一种掺杂是在晶格中缺少了共有化运动的价电子,还是以In2O3薄膜内掺杂ZnO为例来说明这个问题。掺杂后,In2O3晶格中一部分三价的铟离子In3+被二价的锌离子Zn2+ 所占据,在晶格中为了维持锌离子与它周围铟离子之间具有共价键的结构,锌离子势必要成为饱和的共价键结构,也就是要吸引附近的一个价电子来构成饱和结构,被吸引去的电子原来所处的位置便成了空穴。出现空穴的根本原因是缺少了共有化价电子。这种缺少了共有化价电子的杂质能级也分布在禁带之中,并且靠近满带,在常温下满带中的电子很容易跃迁到杂质能级上去,使得满带中出现了空穴,整个膜层的载流子的浓度(指空穴)提高了,导电性变好了[6]。
由薄膜的导电机理可知,金属膜导电是由于组成膜的自由电子受到电场作用而定向运动的结果,方电阻主要取决于膜层的厚度,不会因为镀膜工艺条件变化而有较大的变化,半导体薄膜导电是由于载流子在外电场作用下做定向运动的结果,方电阻的大小除了与膜的几何厚度有关外,主要取决于镀膜的工艺技术。
3 ITO简介
3.1 ITO的基本性质
可见光透过率高而又有导电性的薄膜称为透明导电薄膜。透过性的标准是透过率60%以上,导电性的标准是表面电阻在1010Ω·cm以下[7]。透明导电薄膜的种类主要有金属膜、氧化物膜、多层复合膜和高分子膜等,其中氧化物薄膜占主导地位。目前研究人员主要集中在对SnO2基、In2O3基以及ZnO 基透明导电膜的研究,而掺锡In2O3(简称ITO)薄膜又是当前研究和应用最广泛的透明导电薄
膜。
锡掺杂的氧化铟是一种体心立方铁锰矿结构的n 型半导体透明导电薄膜,具有以下特性:①导电性能好( 电阻率可低达10-4Ω·cm),带隙宽(3.5~4.3 eV) ,载流子浓度(1021cm-3)和电子迁移率( 15~45 cm2V-1s-1) 较高;②在可见光波段透过率高,可达85%以上; ③对紫外线的吸收率较高,可达85%以上;④对红外线具有反射性,反射率高于80%;⑤对微波具有衰减性,衰减率可达85%以上;
⑥膜层硬度高,耐磨,耐化学腐蚀(氢氟酸等除外);⑦膜层具有很好的酸刻、光刻性能,便于细微加工,可以被刻蚀成不同的电极图案。由于具有上述优良特性,ITO薄膜被广泛用于平面显示、电致变色(EC)窗、太阳能电池透明电极、微波屏蔽和防护镜、交通工具的风挡玻璃等[8]。
3.2ITO的制备
制备ITO薄膜的方法有很多种,几乎所有制备薄膜的方法都可用于制备ITO 薄膜。制备方法主要有物理法和化学法。物理法包括真空蒸发法、离子增强沉积、激光脉冲沉积等。化学法包括溶胶-凝胶法、喷雾热解法、化学气相沉积法、均相沉淀法等[9~11]。
3.2.1 真空蒸发法
真空蒸发镀膜法(简称真空蒸镀)是在真空室中,加热蒸发容器中待形成薄膜的原材料,使其原子或分子从表面气化逸出,形成蒸气流,入射到固体(称为衬底或基片)表面,凝结形成薄膜的方法,由于真空蒸发法或真空蒸镀法主要物理过程是通过加热蒸发材料而产生,所以又称为热蒸发法。按照蒸发源加热部件的不同,蒸发镀膜法可分为电阻蒸发、电子束蒸发、高频感应蒸发、电弧蒸发、激光蒸发法等。采用这种方法制造薄膜,已有几十年的历史,用途十分广泛。3.2.2 喷雾热解法
喷雾热解法( Spray Pyrolysis,SP)是将金属盐溶液雾化后喷入高温区同时进行干燥和热分解的工艺方法,可以用于氧化物陶瓷粉末(特别是复合粉末)合成、纤维合成和薄膜制备。用该法制备的ITO薄膜的电导率高,对可见光的透过率可达90%以上。自从1960年ChamLerlin和Skarman在用喷雾热分解法制取薄膜方面做了开创性工作以来,该方法已用于ZnO、ITO、ZnS: Mn等透明薄膜以及YBaCuO超导薄膜等的制备上[12]。
3.2.3 溶胶-凝胶( Sol-Gel)法
溶胶是指微小的固体颗粒悬浮分散在液相中,并且不停地进行布朗运动的体系。溶胶凝胶法制备涂层的基本原理是:以金属醇盐或无机盐为前驱体,溶于溶剂(水或有机溶剂)中形成均匀的溶液,溶质与溶剂产生水解或醇解反应,反应生成物聚集成几个纳米左右的粒子并形成溶胶,再以溶胶为原料对各种基材进行涂膜处理,溶胶膜经凝胶化及干燥处理后得到干凝胶膜,最后在一定的温度下烧结即得到所需的薄膜。
3.2.4 化学气相沉积法
化学气相沉积法(CVD)是一种或几种气态反应物(包括易蒸发的凝聚态物质在蒸发后变成的气态反应物)在衬底表面发生化学反应而沉积成膜的工艺。反应物质是由金属载体化合物蒸气和气体载体所构成,沉积在基体上形成金属氧化物膜,衬底表面上发生的这种化学反应通常包括铟锡原材料的热分解和原位氧化。
3.3ITO的应用
3.3.1 用于平面显示
ITO薄膜大量应用于平面显示器,例如液晶显示(LCD)、电致发光显示(ELD)、电致彩电显示(ECD)等。随着液晶显示器件的大面积化、高等级化和彩色化,LCD将超过CRT成为显示器件中的主流产品[13]。
3.3.2 用于电致变色(EC)灵巧窗
ITO薄膜对光波具有选择性,可用于寒冷地区和高层建筑的视窗,使建筑物内暖气、冷气和照明等能耗减少50%以上,将使热量保存在封闭的空间里,起到热屏蔽作用,并使外界热量难以辐射入室内。
3.3.3 用于太阳能电池
在ITO的实际应用方面,还有一个十分重要又颇具发展前景的领域:太阳能技术。由涂覆在半导体材料(如Si、GaAs、InP等)表面上的ITO膜所形成的杂结构体,已经成功地用于把太阳能转换为电能的一种有效的能源转换器上面。ITO薄膜用于异质结SIS太阳能电池顶部氧化物层,可以得到高的能量转换效率。
3.3.4 用于微波屏蔽和防护镜
ITO薄膜具有良好的微波屏蔽作用,能防静电,也用于屏蔽电磁波的地方,如微波暗室消除设备、计算机房和雷达的屏蔽保护区,防雷达隐形飞机的涂层等。ITO透明导电薄膜玻璃对微波的衰减可达-30dB。茶色ITO薄膜是铟、锡氧化物
的新品种,它能防紫外线和红外线,滤去对人体有害的紫外波段,因此镀ITO 膜的玻璃镜片可用做特殊防护镜。
3.3.5 用于军事上的隐身技术
ITO材料具有良好的光学性能,在可见光区具有高透过率,由于基本能带的原因,在紫外光区具有高吸收率,同时由高自由载流子浓度决定的等离子体吸收在中远红外区,使其具有高反射率。这是ITO能应用于伪装隐身技术的根本原因。
3.3.6 用于传感器方面
在ITO薄膜的表面吸附了气体之后,薄膜的导电性就会发生变化,因此可用于各种高灵敏度的传感器,专门用于发现和测量各种气体的浓度。自1993年以来,特别是2000年以来,对In2O3气敏性能的研究出现了大量的文献报道,研究表明,ITO薄膜对NH3、CO、O3、NO2有很高的灵敏度。
3.4 我国ITO技术现状和发展趋势
为了充分了解ITO薄膜的特性并利用其优良性能,今后研究人员至少需要在以下几个方面加强研究:①多元TCO 薄膜的性质;②低温和室温ITO薄膜的制备;③ ITO 薄膜的导电机理;④纳米尺度ITO材料的特性;⑤ In2O3基的掺杂化合物的性能[14]。
我国的ITO产业十分发达,是ITO导电玻璃的主要生产国。但是在纳米级别的ITO制备上,中国则落后于美国、日本等发达国家,他们已经可以制备出10nm以下的ITO薄膜,因此,我们仍需要继续努力研究,突破瓶颈。
4 直流磁控溅射法制备纳米ITO薄膜
现在制备ITO薄膜的方法有很多,不同的方法原理不同,产物的形貌结构会有很大的差异,产量的也会相差很大。在如此众多的方法中,磁控溅射法比较适用于工业上的大规模生产,磁控溅射法的优点在于:成膜面积大,沉积速度快,可适用于大规模生产;获得的ITO薄膜密度高,而且薄膜的纯度较高(在溅射过程不存在污染) ;溅射镀膜的膜厚可控性和多次溅射的膜厚再现性好;薄膜与衬底的附着性好;工艺稳定性好。下面探讨直流磁控溅射法制备纳米ITO薄膜的工艺细节。
4.1 工艺简介
磁控溅射法是目前工业上应用较广的镀膜方法。磁控溅射沉积可分为直流磁
控溅射沉积和射频磁控溅射沉积,而直流磁控溅射沉积是当前发展最成熟的技术。该工艺的基本原理是在电场和磁场的作用下,被加速的高能粒子( Ar+)轰击铟锡合金(IT)靶材或氧化铟锡(ITO)靶材表面,能量交换后,靶材表面的原子脱离原晶格而逸出,溅射粒子沉积到基体表面与氧原子发生反应而生成氧化物薄膜。
4.2 工艺原理
电子在电场的作用下加速飞向基片的过程中与氩原子发生碰撞,电离出大量的氩离子和电子,电子飞向基片。氩离子在电场的作用下加速轰击靶材,溅射出大量的靶材原子,呈中性的靶原子(或分子)沉积在基片上成膜。二次电子在加速飞向基片的过程中受到磁场洛仑磁力的影响,被束缚在靠近靶面的等离子体区域内,该区域内等离子体密度很高,二次电子在磁场的作用下围绕靶面作圆周运动,该电子的运动路径很长,在运动过程中不断的与氩原子发生碰撞电离出大量的氩离子轰击靶材,经过多次碰撞后电子的能量逐渐降低,摆脱磁力线的束缚,远离靶材,最终沉积在基片上。
4.3 生产设备
图2所示为磁控溅射镀膜生产线。其主体设备的主要组成部分如下。
图2TD-750型透明导电膜玻璃镀膜生产线[15]
(1)真空室:304不锈钢材料制造,立式结构,外壁通冷却水。所有箱体均通过退火处理。
(2)真空系统:涡轮分子泵抽气系统。
(3)镀膜系统:直流及中频磁控溅射阴极,配合环控制系统。配备先进的平面溅射阴极。
(4)烘烤系统:采用不锈钢管状加热器配合均热板,确保基片加热均匀性。
(5)充气系统:高精度气体质量流量计及均匀布气装置。
(6)电气控制系统:工程机及PLC自动控制,安装中文全自动控制软件。15寸彩色触摸屏操控界面。
(7)水冷系统:真空室冷却和阴极冷却,有水压和水流保护开关。
4.4 生产流程
先将靶材放进真空室,一边将真空室抽成真空状态,一边通入氩气,在外壁通上冷却水。在镀膜系统中,经过溅射将从靶材料中溅射出的原子沉积在基片上成膜,同时均匀加热基片。镀膜完成后通过水冷系统了却。
4.5ITO薄膜的结构和表面形貌
图3( a) 为溅射功率比较小的ITO薄膜SEM 图片,图3( b)为溅射功率比较大的ITO薄膜SEM图片,通过( a)和( b)比较可以看到,溅射功率小的ITO颗粒容易在基体表面团聚,成岛状不连续分布,颗粒度大小不均匀,致密度差,当溅射功率大时,ITO颗粒结晶度越高,均匀性好,致密度越好。通过图3( a)和3( b) 的比较同时也验证了随着溅射功率的增大,ITO表面电阻减小;随着溅射功率增大,ITO薄膜致密性增大透光率减小[16]。
图3 不同溅射功率下ITO薄膜的SEM图(图a,b)[17]
图4为不同溅射功率下ITO薄膜的X射线衍射( XRD)测试图谱。对照标准的PDF卡可知,图谱中的衍射峰与In2O3的( 211)、( 222)、( 400)、( 440) 和( 622) 等特峰对应,没有发现In、Sn单质及其亚氧化物的衍射峰,由于In3+和Sn4+的离子半径相差不大,并且m( In2O3) :m( SnO2) = 9:1,所以Sn4+离子取代了In3+的位置,SnO2溶入In2O3晶格形成固溶体结构,因此ITO薄膜保持In2O3晶体结
构[16]。随着溅射功率增大,(222)峰的强度降低,(400)峰强度增大,功率的增强改变晶体的结构,在溅射功率为110W时,ITO薄膜沿( 222)和( 400)择优取向。
图4 不同溅射功率下ITO薄膜的XRD谱[18]
4.6 影响ITO薄膜性能的因素
1 溅射功率对ITO薄膜的影响
ITO的载流子主要来源是氧空位和Sn4+代替In3+放出的一个电子。理想的In203结构中In3+是满态,与O2-结合完全。当部分四面体间隙中的O2一成为无序后,会留出空位,形成氧空位,即InZO3-X,存在过剩的自由电子。同时,Sn4+代替In3+会提供电子到导带,形成n型掺杂。图5所示为氧分压为0.02Pa、沉积气压为1.2Pa时,ITO薄膜的R□与ρ随溅射功率的变化,由图可看出,随着功率的增大,R□逐渐减小。当功率较低时,从靶上溅射到基底的原子数量和动能很小,在基底表面具有较大的表面迁移能,从而可以与周围的氧气进行充分反应,导致氧空位的减少和吸附氧原子的存在,从而使R□较大。图6为厚度与沉积速率随溅射功率的变化图,随着功率的增加,薄膜的沉积速率加快,相应的厚度也逐渐增大。薄膜的厚度主要决定于溅射功率与时间,当溅射功率和时间一定时,厚度基本保持不变。当功率较小时,薄膜的厚度较小,电子将在界面发生漫反射,根据sondhermer的薄膜导电理论:ρ=ρ0(1+3λ0/8d)(式中d为厚度,场为厚度无穷大时的电子平均自由程,ρ0为厚膜远远大于场时的电阻率),平均自由程效应会导致电阻率ρ随厚度的增加而减小,从而薄膜的R□减小。考虑到后续器件(太阳电池)的制备,ITO薄膜厚度在150~200nm为宜,在33w时可获得R□约8~10Ω/□、
厚度在150nm左右的ITO薄膜。
图5 ITO的R□与ρ随功率的变化[19]
图6 薄膜厚度与沉积速率随功率的变化[19]
图7为不同功率下沉积的ITO的XRD测试图。图中21.30°、30.3°、35.3°、60.30°的衍射峰分别对应(211)、(222)、(400)、(622)晶面。在功率较低时(13w),薄膜的结晶性能较差,虽出现结晶峰,但衍射峰并不明显,薄膜处于非晶与多晶掺杂的阶段,相应的R□较大,导电性较差。随着功率的增大,ITO薄膜出现了较强的衍射峰,结晶性进一步完善。随着功率的升高,薄膜的择优取向也发生了明显的变化,(222)晶面衍射峰逐渐减弱,(400)衍射峰逐渐增强,薄膜由(222)的
择优取向转变为沿(222)和(400)随机生长,相应地,R
逐渐减小,导电性提高,
口
这可能与载流子的散射机制有关。
图7 不同功率下沉积的IT0的XRD图[20]
2 氧分压对ITO薄膜的影响
图8为溅射功率为33w、沉积气压为1.2Pa时,在不同氧分压下沉积的ITO 和ρ的变化图。由图可看出,随着氧分压的升高,薄膜的导电性变差。薄膜的R
口
O2浓度的升高使In氧化充分,形成接近标准化学计量比的氧化锢,从而使薄膜内的氧空位减少,同时导致掺杂锡的氧化,造成载流子浓度降低,从而使得薄膜的导电性变差。当氧分压高达0.04Pa时,溅射到基底上的In203受到大量氧负离子的轰击而发生分解生成低价的氧化物(InO),即:In2O3离子轰击2lnO+O;同时,大量的氧负离子的轰击还可能使沉积到基底上的薄膜颗粒脱离薄膜,导致薄膜中存在大量的位错和吸附氧原子。因此,氧分压很高时,薄膜的导电性和透过率均较差。随着氧分压的降低,In2O3分解生成低价的氧化物的程度减弱,吸附
逐渐减小、透光率也逐步增加。当氧分氧原子的数量逐渐减少,使得薄膜的R
口
压为0.0lPa时,薄膜的导电性和透过率达到最优,R
约为8Ω/□,在400~800nm
口
的波长范围内的平均透光率达到了82%。
图8 ITO的R口和ρ随氧分压的变化[241
3 沉积气压对ITO薄膜的影响
选定溅射功率为33w、氧分压为0.01Pa不变,在不同气压下沉积的ITO薄膜的导电性与透过谱的变化见图9、10所示。由图可知,当气压较低时,ITO的导电性能与透光性均相对较差,这是因为气压较低时,ITO受到的散射较小,同时,低气压下平均自由程较大,导致赶Ar+的动能较大,因此从靶上溅射出来的原子的动能大,氧原子可以和溅射到基底上的原子进行充分反应,从而导致氧空位的减少和掺杂锡的氧化,使得薄膜的导电性能相对较差。随着气压的升高,沉积形成带有较高氧空位和掺杂锡的ITO膜,在1.0~1.6Pa的范围,均可获得
6~78Ω/□的ITO膜,电阻率低至1.0~1.2×l04Ω·cm。
图9 ITO的R口和ρ随沉积气压的变化[22]
图10 不同氧分压下沉积的ITO的透过谱[22]
随着气压的升高,薄膜表面的平整度增加,导致光散射更少,因此增加了可见光区域的透射。在1.2~1.6Pa,透过率基本无变化,在400~800nm的波长范围内,平均透过率均达到了82%。
4 溅射压强对ITO膜的影响
在保持氧流量为0.62 seem,溅射功率为130w不变的条件下改变溅射压强。电阻率和透过率随溅射压强的变化如图11所示。
图11 ITO薄膜的透过率和电阻率随溅射压强的变化关系图[23] 当溅射压强较小(0.3 Pa)时,由于气体稀薄,在溅射过程中,Ar+受到的散射较小,同时,低气压下长的平均自由程导致Ar+离子高的动能,因此从靶上溅射出的原子的动能大,氧原子能够和溅射到基底的原子充分反应,这时膜的结晶状况比较好,透过率较高。这一充分氧化反应,造成氧空位的下降,因为ITO薄膜中氧空位对导电性起很大的作用。因此导致制备的ITO薄膜的电阻率较大,导电性较差。当溅射压强较大(1 Pa)时,由于中性气体和已经电离的气体离子会
频繁的撞击,因此,腔体内的Ar+受到强烈的散射作用使其动能较小,导致溅射出的靶原子的动能较小,靶原子飞向基底时遭到气体分子和等离子体散射的几率大,使得沉积到基底的原子能量较小,降低了高价铟锡氧化物的反应活性,会生成一些铟锡的低价氧化物,使薄膜呈暗棕色,同时,影响薄膜的结晶程度,使薄膜的电阻率变大,透过率变差。当溅射压强介于中间某个值(0.7Pa)时,ITO膜的透过率很高,而电阻率很小,为最佳的溅射压强值。
4.7 ITO薄膜的性能评价
4.7.1 ITO薄膜的电学性能
利用四探针电阻仪测试不同沉积参数下制备的ITO薄膜的方块电阻,其变化如图12所示。
图12 ITO薄膜方块电阻随溅射参数变化曲线[24]
图12中A曲线为其他参数不变(沉积气压0.15Pa,O2流量0 sccm),单纯改变功率时,薄膜方块电阻变化曲线。从图5中A曲线可以看出,当功率为100W 时,薄膜的方块电阻为46Ω\□,薄膜方块电阻随功率的增加而降低,当功率增大到350W时,薄膜的方块电阻减小到了24Ω/□。溅射功率增大时,薄膜沉积速率增加,氧化反应不充分,ITO薄膜中的氧空位增大,导致方块电阻的降低。
图12中B曲线为其他参数不变(沉积气压0.5Pa,溅射功率为100W ),单纯改变O2流量时,薄膜方块电阻变化曲线。从图5B曲线可以看出,当O2流量为0时,ITO薄膜的方块电阻为46Ω/□,当O2流量为0.2 sccm时,ITO薄膜的方块电阻又降为30Ω/□,随后ITO薄膜的方块电阻随着O2流量的增大而增大,当O2流量达到2.0 sccm时,薄膜的方块电阻已经达到156Ω/□。当不通入O2的时候,In未充分氧化,存在较多的黑色InO,导致方块电阻较大,同时可见光平均透过
率较低。当稍微通入O2时,薄膜氧化较充分,方块电阻降低,但是当O2流量过高时,氧空位和载流子的浓度较低,导致方块电阻增高,降低薄膜导电性能,因此存在最佳的O2流量范围使得薄膜的方块电阻最低。
图12中C曲线为其他参数不变( O2流量为0sccm,溅射功率为250W ),单纯改变沉积气压时,薄膜方块电阻变化曲线。从图12中C曲线可以看出,当沉积气压为0.5Pa时,薄膜的方块电阻为31.7Ω/□,薄膜方块电阻随沉积气压的升高明显增大,当沉积为2.5 Pa时,薄膜的方块电阻达到1980Ω/□。当沉积气压增大时,溅射出来的靶材粒子被Ar气散射的几率大大增加,这样就没有足够的能量在基体上结晶和迁移,导致了薄膜缺陷的增加,因此薄膜的方块电阻随着沉积气压的升高而增大,导电性能变差。
4.7.2 ITO薄膜的光学性能
采用紫外-可见分光光度计检测出在不同O2流量参数下制备的ITO薄膜的可见光平均透过率(波长在400~ 800 nm),如图13所示。
图13 ITO薄膜可见光平均透过率随溅射参数变化曲线[25]
图13曲线为其他参数不变(压强为0.5Pa,溅射功率为100W ),单纯改变O2流量时的薄膜平均透过率曲线,可以看出薄膜的可见光透过率随着O2流量的增加而略有增加,因为在溅射过程中主要发生的反应是[21]:
直接氧化:4In+ 3O2= 2In2O3
二次氧化:2In+ O2 = 2InO;4InO + O2 =2In2O3
当O2分压较低时,氧化反应不太充分,主要发生的反应是二次氧化:2In+ O2= 2InO,这样会生成较多的黑色的InO,薄膜的透过率下降,当O2分压增大时,主要发生的反应是直接氧化反应:4In+ 3O2= 2In2O3,反应比较充分,生成较多灰白色的In2O3,使得薄膜的透过率增加。
当O2流量为0 sccm,溅射功率为250W,单纯改变沉积气压时,经检测发现薄膜平均透过率没有明显的变化,始终维持在84% ~ 86% ,沉积气压对可见光平均透过率几乎没有影响。同样当单纯改变功率时(沉积气压为0.5Pa,O2流量为0sccm ),经检测薄膜的平均透过率在84% 左右,可以说明功率对薄膜可见光平均透过率没有影响。
5 结束语
本文概述了透明导电薄膜的种类及其导电机理。对作为其中重要一支的ITO 透明导电薄膜的制备方法和应用进行了详细的介绍,对ITO有了更深的了解。
ITO透明导电薄膜作为重要的现代信息产业基础产品,在许多领域都扮演着重要的角色,鉴于ITO薄膜的优异特性, 有必要组织科研人员进行更深层次的技术攻关。这不仅有利于ITO薄膜的使用, 更主要的一点是对ITO复杂结构及机理的研究, 可以促进对其它氧化物薄膜的认识随着科学技术研究的不断深入和高新技术及现代国防发展应用的需要, ITO透明导电薄膜必将在新型的电子薄膜材料中占有越来越重要的地位。
参考文献
[1]段学臣, 陈振华, 周立等. 超细氧化铟-氧化锡( ITO)复合粉末的研制与结构
特性[J]. 稀有金属, 1998, 22(5): 396~399
[2]张维佳, 王天民, 吴小文等. 纳米ITO粉末制备工艺优化设计[J]. 稀有金属
材料与工程, 2005, 9(34): 1353~1356
[3]毛黎明, 李历历, 段学臣. 两种不同分散剂对ITO纳米粉末粒度和团聚的影
响[J]. 稀有金属与硬质合金, 2005, 33(1): 5~7
[4]周洪庆, 吕军华, 沈晓冬. ITO纳米粉制备及表面修饰研究[J]. 南京工业大
学学报, 2004, 26(4): 28~30
[5]朱协彬, 段学臣. 在纳米ITO 粉末共沉淀法制备过程中pH值的影响[J]. 稀
有金属与硬质合金, 2006, 34(2): 8~11
[6]姜辛, 张超, 洪瑞江, 戴达煌, 透明导电氧化物薄膜[M]. 北京: 高等教育版
社, 2008
[7]王树林. ITO薄膜的制备及性能研究[D]. 武汉: 武汉理工大学, 2004
[8]李世涛. 透明导电ITO及其复合薄膜的研究[D]. 武汉: 华中科技大学, 2006
[9]王树林, 夏冬林. ITO薄膜的制备工艺及进展[J]. 玻璃与搪瓷, 2004, 32(5):
50~54
[10]茅昕辉, 陈国平, 陈公乃等. 直流磁控反应溅射沉积ITO透明导电膜的研究
[J]. 光电子技术, 1995,15(1): 72~77
[11]林钰, 辛荣生, 贾晓林. 淀积温度和氧含量对ITO膜结构及性能的影响
[J]. 稀有金属, 2003, 27(4): 510~512
[12]来冰, 丁训民, 袁泽亮. 同步辐射光电能谱对ITO 膜表面的研究[J]. 半导
体学报, 1999, 20(7): 543~547
[13]吴浪, 肖定全, 孙勇等. 铌酸钾钠基无铅压电陶瓷的相变特性和掺杂改性研
究进展[J]. 功能材料, 2007, 38(9): 1400~1404
[14]王刚, 刘宏宇, 赵超等. 低阻高透过率ITO薄膜的制备与性能[J]. 液晶与显
示, 1999, 14(1): 23227~23230
[15]杨志伟, 韩圣浩, 杨田林等. 柔性衬底ITO膜的性质与制备参数关系的研究
[J]. 太阳能学报, 2001, 22(3): 25~27
[16]马瑾, 赵俊卿, 叶丽娜等. 柔性衬底ITO导电膜的低温制备及特性研[J]. 半
导体光电, 1999, 20(6): 47~52
[17]Kentaro Utsumi, Osamu. Matsunaga and Tsutomu Takahata [J]. Thin solid Films,
1998, 334(4): 30~34
[18]I Baia, M Quintela, L. Mendes, P. Nunes and R. M artins [J]. Thin Solid Films,
1999, 337(6): 171~175
[19]史济群, 周京英, 马洪磊. 电子束法沉积ITO 透明导电膜的研究[J]. 华中
理工大学学报, 1998, (3): 10~12
[20]扬志伟, 韩圣浩, 马洪磊等. 柔性衬底ITO膜的性质与制备参数关系的研究
[J]. 太阳能学报, 2001,15 (3): 256~261
[21]张正勇, 张耀华. ITO薄膜的气敏特性[J]. 传感技术学报, 1999, 29 (3): 52~56
[22]徐曼, 邱家稳, 贺德衍.退火对反应磁控溅射制备ITO薄膜性能影响[J].真
空科学与技术, 2003, 23(4):161~164
[23]周引穗, 王俊, 陆治国等. 透光导电ITO膜的制备及其光电特性的研究[J] .
光子学报, 2002, 31(9): 1077~1080
[24]范志新, 孙以材, 陈玖琳. 氧化物半导体透明导电薄膜的最佳掺杂含量理论
计算[J]. 半导体学报, 2001, 22(11): 1382~1386
[25]马颖, 张方辉, 靳宝安等. ITO透明导电薄膜的制备及光电特性研究[J]. 液晶
与显示, 2004, 19(5): 376~379.
[26]
磁控溅射法制备薄膜材料综述
磁控溅射法制备薄膜材料综述 摘要薄膜材料的厚度是从纳米级到微米级,具有尺寸效应,在国防、通讯、航空、航天、电子工业等领域有着广泛应用,其有多种制造方法,目前使用较多的是溅射法,其中磁控溅射的应用较为广泛。本文主要介绍了磁控溅射法的原理、特点,以及制备过程中基片温度、溅射功率、溅射气压和溅射时间等工艺条件对所制备薄膜性能的影响。 关键字磁控溅射;原理;工艺条件;影响 Brief Introduction to Thin Films by Magnetron Sputtering Abstract: The thickness of thin films is from the nano to the micron level.With its size effect, the films are widely used in the defense, telecommunication, aviation, aerospace, electronics and other fields.It can be prepared by many ways,of which the sputtering is used mostly.And magnetron sputtering is popular.The principle and characteristics of magnetron sputtering, and how substrate temperature, sputtering power, sputtering pressure and sputtering time influence the the properties of the films during the preparing process are introduced in this paper. Key Words: magnetron sputtering; principles; conditions; lnfluence 1 引言 薄膜是指尺度在某个一维方向远远小于其他二维方向,厚度可从纳米级到微 米级的材料,由于薄膜的尺度效应,它表现出与块体材料不同的物理性质,有广 泛应用。薄膜的制备大致可分为物理方法和化学方法两大类[1]。物理方法主要包 括各种不同加热方式的蒸发,溅射法等,化学方法则包括各种化学气相沉积 (CVD)、溶胶-凝胶法(sol-gel)等。 溅射沉积法由于速率快、均一性好、与基片附着力强、比较容易控制化学剂 量比及膜厚等优点,成为制备薄膜的重要手段。溅射法根据激发溅射离子和沉积 薄膜方式的不同又分直流溅射、离子溅射、射频溅射和磁控溅射,目前多用后两 种。本文主要介绍磁控溅射制备薄膜材料的原理及影响因素。 2 磁控溅射法 2.1磁控溅射基本原理
磁控溅射法制备的纳米金薄膜的工艺条件和结构分析_许小亮
磁控溅射法制备的纳米金薄膜的工艺条件和结构分析* 许小亮1,2,王 烨1,2,赵亚丽1,2,牟威圩1,2,施朝淑1,2 (1.中国科学院中国科学技术大学结构分析重点实验室,安徽合肥230026; 2.中国科学技术大学物理系,安徽合肥230026) 摘 要: 通过直流溅射沉积法在玻璃衬底上制备了不同生长条件下的纳米金薄膜,利用X射线衍射(XRD)和原子力显微镜(AFM)对其进行表面形貌分析。XRD图显示Au膜具有(111)面择优取向;AFM 图显示,在不同的生长阶段Au膜具有不同的表面微结构。总结了不同的工艺条件对薄膜晶粒生长的影响,这项研究对实现金属薄膜的可控性生长有重要意义。 关键词: 晶粒生长;纳米金;表面形貌;磁控溅射 中图分类号: O782.9文献标识码:A 文章编号:1001-9731(2006)08-1216-04 1 引 言 纳米金颗粒薄膜的非线性光学研究在国际上引起高度重视,这是因为入射光可在金属颗粒间产生的很强的近场表面等离子激元(SP)共振增强效应[1,2],具备102~106倍的局域增强效果[3,4]。但既往研究中的金薄膜是处于高度无序状态的准连续颗粒薄膜,而没有开展对有序微晶体系薄膜的研究。这是因为技术上还没有做到对薄膜取向度和晶粒尺寸的可控性生长[5]。根据已有的SP理论,组成薄膜的颗粒大小及其结晶度对SP有很大的影响,因此实现纳米金颗粒薄膜的可控性生长对于推动SP的研究是十分重要的。 从一般理论模拟的结果[6~14]来看,薄膜的生长可分为3个阶段:晶粒的成核与核生长过程、正常晶粒生长过程和反常晶粒生长过程[6]。这3个阶段之间并没有严格的界限,只是在特定阶段时某种过程占主导地位。各晶粒相互接触,晶界形成后,晶粒开始柱状生长,横向直径由早期在衬底表面上发生的成核过程决定[7,8]。随着薄膜厚度的增加,柱状晶粒的平均直径不断增加,这就是薄膜的正常晶粒生长过程[9]。当晶粒半径可以和薄膜厚度相比拟时,正常晶粒生长将会停滞,这被称为厚度效应[10]。整体上所有晶粒的平均尺寸将继续增长,主要是反常晶粒的生长[11,12],速率更快,这是吸收了周边的正常晶粒所致,这种生长状态将持续到正常晶粒全部被吸收。薄膜晶粒的优势取向生长是由晶粒间自由表面能和接触面能的差异造成的[13]。晶粒的正常生长过程对晶粒的优势取向生长及薄膜的织相结构并没有影响;而在反常生长阶段,具有优势取向的晶粒边界迁移能力更强,会以相对更快的速度生长,并吸收周围的晶粒,生长成为大晶粒,形成薄膜的最优取向和织相结构[14]。 2 实 验 本实验采用直流磁控溅射仪制备Au膜,用洁净的载玻片作为衬底,靶材为纯度5N的金靶,本底真空控制在10-3~10-2Pa,起辉电压0.26kV,电流25mA。溅射过程中,功率控制在6.5~10W,所生长的薄膜厚度分别为3、6、12和24nm。本实验的目的是总结不同的工艺条件对薄膜生长的影响,而影响纳米金属颗粒的可控性生长的主要因素有:溅射气体压强,衬底温度,薄膜厚度以及溅射功率和溅射电流等,我们将实验样品分组,进行组合式分析。具体的实验参数见表1。 表1 纳米金薄膜的不同生长条件 Table1Different grow th conditions of the nano-Au film s 样品号 厚度 (nm) A r气压 (Pa) 温度 ( ) 功率 (W) 13,6,12,24 3.02008.7 212 0.5, 1.0, 3.0, 6.0 200 6.5 312 3.0 RT,150,200, 250,300 10.0 利用XRD和AFM对各种样品进行了结构和表面形貌分析。 3 实验结果及分析 对3组样品分别作了X射线衍射谱研究(图1~ 3)。谱中的4个峰分别对应于Au薄膜的(111)、(200)、(220)、(311)面。研究指出:具有面心立方结构(f.c.c.)的金属薄膜,其晶粒的自由表面和底部的表面自由能在(111)面上达到最小值[13],这表明金膜本身的性质决定它有(111)的优势取向。结合本实验的XRD测试结果,薄膜厚度为24nm(3.0Pa,200 ,8.7 W)时,各特征峰的相对强度比为I(111) I(200) I(220) *基金项目:国家自然科学基金资助项目(50472008);安徽省人才开发基金资助项目(2003Z021);安徽省高新技术基金资助项目(04022001) 收到初稿日期:2005-11-09收到修改稿日期:2006-04-12通讯作者:许小亮 作者简介:许小亮 (1960-),男,江苏南京人,教授,博士,主要从事纳米光电功能材料的研究。
关于磁控溅射发展历程的综述
磁控溅射 1852年,格洛夫(grove)发现阴极溅射现象,自此以后溅射技术就开始建立起来了!磁控溅射沉积技术制取薄膜是上世纪三四十年代发展起来的,由于当时的溅射技术刚刚起步,其溅射的沉积率很低,而且溅射的压强基本上在1pa以上,因此溅射镀膜技术一度在产业话的竞争中处于劣势。1963年,美国贝尔实验室和西屋电气公司采用长度为10米的连续溅射镀膜装置。1974年,j.chapin发现了平衡磁控溅射。这些新兴发展起来的技术使得高速、低温溅射成为现实,磁控溅射更加快速地发展起来了,如今它已经成为在工业上进行广泛的沉积覆层的重要技术,磁控技术在许多应用领域包括制造硬的、抗磨损的、低摩擦的、抗腐蚀的、装潢的以及光电学薄膜等方面具有重要的影响。 磁控溅射的发展历程: 溅射沉积是在真空环境下,利用等离子体中的荷能离子轰击靶材表面,使靶材上的原子或离子被轰击出来,被轰击出的粒子沉积在基体表面生长成薄膜。 溅射沉积技术的发展历程中有几个具有重要意义的技术创新应用,现在归结如下: (1)二级溅射: 二级溅射是所有溅射沉积技术的基础,它结构简单、便于控制、工艺重复性好主要应用于沉积原理的研究,由于该方法要求工作气压高(>1pa)、基体温升高和沉积速率低等缺点限制了它在生产中的应用。 (2)传统磁控溅射(也叫平衡磁控溅射): 平衡磁控溅射技术克服了二级溅射沉积速率低的缺点,使溅射镀膜技术在工业应用上具有了与蒸发镀膜相抗衡的能力。但是平衡磁控溅射镀膜同样也有缺点,它的缺点在于其对二次电子的控制过于严密,使等离子体被限制在阴极靶附近,不利于大面积镀膜。 (3)非平衡磁控溅射: B.Window在1985年开发出了“非平衡磁控溅射技术”,它克服了平衡磁控溅射技术的缺陷,适用于大面积镀膜。并且在上世纪90年代前期,在非平衡磁控溅射的基础上发展出了闭合非平衡系统(CFUBMS),采用多个靶以及非平衡结构构成的闭合磁场可以对电子进行有效地约束,使整个真空室的等离子体密度得以提高。这样可以使磁控溅射技术更适合工业生产。 (4)脉冲磁控溅射: 由于在通过直流反应溅射来制得高密、无缺陷的绝缘膜(尤其是氧化物薄膜)时,经常存在不少的问题。其结果会严重的影响膜的结构和性能。但是通过脉冲磁控溅射可以与制得金属薄膜同样的效率来制得高质量的绝缘体薄膜。近年来,随着脉冲中频电源的研发成功,使镀膜工艺技术又上了一个新的台阶;利用中频电源,采用中频对靶或者孪生靶,进行中频磁控溅射,有效地解决了靶中毒严重的现象,特别是在溅射绝缘材料的靶时,克服了溅射过程中,阳极消失的现象。 (5)磁控溅射技术新型应用: 磁控溅射技术的新型应用是指在以上基础上,再根据应用的需要,对磁控溅射系统进行改进而衍生出的多种多样的设备和装置。这些改进主要是在系统内磁力线的分布上以及磁控溅射靶的设置和分布上。
磁控溅射金属薄膜的制备
磁控溅射薄膜金属的制备 黎明 烟台大学环境与材料工程学院山东烟台111 E-mail:1111111@https://www.360docs.net/doc/e34849887.html, 摘要: 金属与金属氧化物在气敏、光催化与太阳能电池等方面有着极为重要的应用,通过磁控溅射法制备的金属氧化物薄膜,具有纯度高、致密性好、可控性强、与基底附着性好等优点,因此磁控溅射技术被广泛应用于工业化生产制备大面积、高质量的薄膜。我们通过磁控溅射法制备了氧化铜纳米线阵列薄膜,并研究了其气敏性质;除此之外,我们还通过磁控溅射法制备了TiO2/WO3复合薄膜,研究了两者之间的电荷传输性质 关键词:磁控溅射;气敏性质;光电性质 Magnetron sputtering metal film preparation LiMing Environmental and Materials Engineering, Yantai UniversityShandong Yantai111 E-mail:1111111@https://www.360docs.net/doc/e34849887.html, Abstract:GAasMetal and metal oxide have important applications in gas-sensing, photocatalyst and photovoltaics, etc. The metal oxide film prepared by magnetron sputtering technique possesses good qualities, such as high purity, good compactness, controllability and excellent adhesion. Therefore magnetron sputtering technique is widely used to prepare large area and high quality films in industrial production. In our work, CuOnanowires (NWs) array films were synthesized by magnetron sputtering. Their gas-sensing properties were also investigated. Except this, WO3/ TiO2nanocomposite films were synthesized by magnetron sputtering and their dynamic charge transport properties were investigated by the transient photovoltage technique. KeyWords :Gmagnetron Sputtering, Photo-electric Properties, Gas-sensing Properties 1绪论 磁控溅射由于其显著的优点应用日趋广泛,成为工业镀膜生产中最主要的技术之一,相应的溅射技术与也取得了进一步的发展!非平衡磁控溅射改善了沉积室内等离子体的分布,提高了膜层质量;中频和脉冲磁控溅射可有效避免反应溅射时的迟滞现象,消除靶中毒和打弧问题,提高制备化合物薄膜的稳定性和沉积速率;改进的磁控溅射靶的设计可获得较高的靶材利用率;高速溅射和自溅射为溅射镀膜技术开辟了新的应用领域。
金属氧化物透明导电材料地基本原理
金屬氧化物透明導電材料的基本原理 一、透明導電薄膜簡介 如果一種薄膜材料在可見光範圍內(波長380-760 nm)具有80%以上的透光率,而且導電性高,其比電阻值低於1×10-3 ·cm,則可稱為透明導電薄膜。Au, Ag, Pt, Cu, Rh, Pd, A1, Cr等金屬,在形成3-15 nm厚的薄膜時,都有某種程度的可見光透光性,因此在歷史上都曾被當成透明電極來使用。但金屬薄膜對光的吸收太大,硬度低而且穩定性差,因此人們開始研究氧化物、氮化物、氟化物等透明導電薄膜的形成方法及物性。其中,由金屬氧化物構成的透明導電材料(transparent conducting oxide, 以下簡稱為TCO),已經成為透明導電膜的主角,而且近年來的應用領域及需求量不斷地擴大。首先,隨著3C產業的蓬勃發展,以LCD為首的平面顯示器(FPD)產量逐年增加,目前在全球顯示器市場已佔有重要的地位,其中氧化銦錫(In2O3:Sn, 意指摻雜錫的氧化銦,以下簡稱為ITO)是FPD的透明電極材料。另外,利用SnO2等製成建築物上可反射紅外線的低放射玻璃(low-e window),早已成為透明導電膜的最大應用領域。未來,隨著功能要求增加與節約能源的全球趨勢,兼具調光性與節約能源效果的electrochromic (EC) window (一種透光性可隨施加的電壓而變化的玻璃)等也可望成為極重要的建築、汽車及多種日用品的材料,而且未來對於可適用於多種場合之透明導電膜的需求也會越來越多。 二、常用的透明導電膜
一些目前常用的透明導電膜如表1所示,我們可看出TCO佔了其中絕大部分。這是因為TCO具備離子性與適當的能隙(energy gap),在化學上也相當穩定,所以成為透明導電膜的重要材料。 表1 一些常用的透明導電膜 三、代表性的TCO材料 代表性的TCO材料有In2O3, SnO2, ZnO, CdO, CdIn2O4, Cd2SnO4,Zn2SnO4和In2O3-ZnO等。這些氧化物半導體的能隙都在3 eV以上,所以可見光(約1.6-3.3 eV)的能量不足以將價帶(valence band)的電子激發到導帶(conduction band),只有波長在350-400nm(紫外線)以下的光才可以。因此,由電子在能帶間遷移而產生的光吸收,在可見光範圍中不會發生,TCO對可見光為透明。
用磁控溅射制备薄膜材料的概述
用磁控溅射制备薄膜材料的概述 1.引言 溅射技术属于PVD(物理气相沉积)技术的一种,是一种重要的薄膜材料制备的方法。它是利用带电荷的粒子在电场中加速后具有一定动能的特点,将离子引向欲被溅射的物质制成的靶电极(阴极),并将靶材原子溅射出来使其沿着一定的方向运动到衬底并最终在衬底上沉积成膜的方法。磁控溅射是把磁控原理与普通溅射技术相结合利用磁场的特殊分布控制电场中的电子运动轨迹,以此改进溅射的工艺。磁控溅射技术已经成为沉积耐磨、耐蚀、装饰、光学及其他各种功能薄膜的重要手段。 2.溅射技术的发展 1852年,格洛夫(Grove)发现阴极溅射现象,从而为溅射技术的发展开创了先河。采用磁控溅射沉积技术制取薄膜是在上世纪三四十年代开始的,但在上世纪70年代中期以前,采蒸镀的方法制取薄膜要比采用磁控溅射方法更加广泛。这是凶为当时的溅射技术140刚起步,其溅射的沉积率很低,而且溅射的压强基本上在lpa以上但是与溅射同时发展的蒸镀技术由于其镀膜速率比溅射镀膜高一个数量级,使得溅射镀膜技术一度在产业化的竞争中处于劣势溅射镀膜产业化是在1963年,美国贝尔实验室和西屋电气公司采用长度为10米的连续溅射镀膜装置,镀制集成电路中的钽膜时首次实现的。在1974年,由J.Chapin发现了平衡磁控溅射后,使高速、低温溅射成为现
实,磁控溅射更加快速地发展起来。 溅射技术先后经历了二级、三级和高频溅射。二极溅射是最早采用,并且是目前最简单的基本溅射方法。二极溅射方法虽然简单,但放电不稳定,而且沉积速率低。为了提高溅射速率以及改善膜层质量,人们在二极溅射装置的基础上附加热阴极,制作出三极溅射装置。 然而像这种传统的溅射技术都有明显的缺点: 1).溅射压强高、污染严重、薄膜纯度差 2).不能抑制由靶产生的高速电子对基板的轰击,基片温升高、淀积速率低 3).灯丝寿命低,也存在灯丝对薄膜的污染问题 3.磁控溅射的原理: 磁控溅射就是以磁场束缚和延长电子的运动路径,改变电子的运动方向,提高工作气体的电离率和有效利用电子的能量。具有低温、高速两大特点。 电子在加速的过程中受到磁场洛仑兹力的作用,被束缚在靠近靶面的等离子体区域内: F=-q(E+v×B) 电子的运动的轨迹将是沿电场方向加速,同时绕磁场方向螺旋前进的复杂曲线。即磁场的存在将延长电子在等离子体中的运动轨迹,提高了它参与原子碰撞和电离过程的几率,因而在同样的电流和气压下可以显著地提高溅射的效率和沉积的速率。 具体地说来磁控溅射系统在真空室充入0.1~1OPa压力的惰性气
磁控溅射镀膜技术的发展
第46卷第2期2009年3月 真空VACUUM Vol.46,No.2Mar.2009 收稿日期:2008-09-03 作者简介:余东海(1978-),男,广东省广州市人,博士生 联系人:王成勇,教授。 *基金项目:国家自然科学基金(50775045);东莞市科技计划项目(20071109)。 磁控溅射镀膜技术的发展 余东海,王成勇,成晓玲,宋月贤 (广东工业大学机电学院,广东 广州 510006) 摘 要:磁控溅射由于其显著的优点应用日趋广泛,成为工业镀膜生产中最主要的技术之一,相应的溅 射技术与也取得了进一步的发展。 非平衡磁控溅射改善了沉积室内等离子体的分布,提高了膜层质量;中频和脉冲磁控溅射可有效避免反应溅射时的迟滞现象,消除靶中毒和打弧问题,提高制备化合物薄膜的稳定性和沉积速率;改进的磁控溅射靶的设计可获得较高的靶材利用率;高速溅射和自溅射为溅射镀膜技术开辟了新的应用领域。 关键词:镀膜技术;磁控溅射;磁控溅射靶中图分类号:TB43 文献标识码:A 文章编号:1002-0322(2009)02-0019-07 Recent development of magnetron sputtering processes YU Dong-hai,WANG Cheng-yong,CHENG Xiao-ling,SONG Yue-xian (Guangdong Universily of Technology,Guangzhou 510006,China ) Abstract:Magnetron sputtering processes have been widely appleed to thin film deposition nowadays in various industrial fields due to its outstanding advantages,and the technology itself is progressing further.The unbalanced magnetron sputtering process can improve the plasma distribution in deposition chamber to make film quality better.The medium -frequency and pulsed magnetron sputtering proceses can efficiently avoid the hysteresis during reactive sputtering to eliminate target poisoning and arcing,thus improving the stability and depositing rate in preparing thin compound films.Higher utilization of target can be obtained by improved target design,and the high -speed sputtering and self -sputtering provide a new field of applications in magnetron sputtering coating processes. Key words:coating technology;magnetron sputtering;magnetron sputtering target 溅射镀膜的原理[1]是稀薄气体在异常辉光 放电产生的等离子体在电场的作用下,对阴极靶材表面进行轰击,把靶材表面的分子、原子、离子及电子等溅射出来,被溅射出来的粒子带有一定的动能,沿一定的方向射向基体表面,在基体表面形成镀层。 溅射镀膜最初出现的是简单的直流二极溅射,它的优点是装置简单,但是直流二极溅射沉积速率低;为了保持自持放电,不能在低气压(<0.1Pa )下进行;不能溅射绝缘材料等缺点限制了其应用。在直流二极溅射装置中增加一个热阴极和辅助阳极,就构成直流三极溅射。增加的热阴极和辅助阳极产生的热电子增强了溅射气体原子的电离,这样使溅射即使在低气压下 也能进行;另外,还可降低溅射电压,使溅射在低 气压,低电压状态下进行;同时放电电流也增大,并可独立控制,不受电压影响。在热阴极的前面增加一个电极(栅网状),构成四极溅射装置,可使放电趋于稳定。但是这些装置难以获得浓度较高的等离子体区,沉积速度较低,因而未获得广泛的工业应用。 磁控溅射是由二极溅射基础上发展而来,在靶材表面建立与电场正交磁场,解决了二极溅射沉积速率低,等离子体离化率低等问题,成为目前镀膜工业主要方法之一。磁控溅射与其它镀膜技术相比具有如下特点:可制备成靶的材料广,几乎所有金属,合金和陶瓷材料都可以制成靶材;在适当条件下多元靶材共溅射方式,可沉积
磁控溅射镀膜简介
磁控溅射镀膜简介 溅射薄膜靶材按其不同的功能和应用可大致分为机械功能膜相物理功能膜两大类。前者包括耐摩、减摩、耐热、抗蚀等表面强化薄膜材料、固体润滑薄膜材料, 后者包括电、磁、声、光等功能薄膜材料靶材等, 具体应用在玻璃涂层(各种建筑玻璃、ITO透明导电玻璃、家电玻璃、高反射后视镜及亚克力镀膜), 工艺品装饰镀膜, 高速钢刀具镀膜, 切削刀具镀膜, 太阳能反光材料镀膜, 光电、半导体、光磁储存媒体、被动组件、平面显示器、微机电、光学组件、及各类机械耐磨、润滑、生物医学, 各种新型功能镀膜(如硬质膜、金属膜、半导体膜、介质膜、碳膜、铁磁膜和磁性薄膜等) 采用Cr,Cr-CrN等合金靶材或镶嵌靶材,在N2,CH4等气氛中进行反应溅射镀膜,可以在各种工件上镀Cr,CrC,CrN等镀层。纯Cr的显微硬度为425~840HV,CrN为1000~350OHV,不仅硬度高且摩擦系数小,可代替水溶液电镀铬。电镀会使钢发生氢脆、速率慢,而且会产生环境污染问题。 用TiN,TiC等超硬镀层涂覆刀具、模具等表面,摩擦系数小,化学稳定性好,具有优良的耐热、耐磨、抗氧化、耐冲击等性能,既可以提高刀具、模具等的工作特性,又可以提高使用寿命,一般可使刀具寿命提高3~10倍。 TiN,TiC,Al2O3等膜层化学性能稳定,在许多介质中具有良好的耐蚀性,可以作为基体材料保护膜。溅射镀膜法和液体急冷法都能制取非晶态合金,其成分几乎相同,腐蚀特性和电化学特性也没有什么差别,只是溅射法得到的非晶态膜阳极电流和氧化速率略大。
在高温、低温、超高真空、射线辐照等特殊条件下工作的机械部件不能用润滑油,只有用软金属或层状物质等固体润滑剂。常用的固体润滑剂有软金属(Au,Ag,Pb,Sn等),层状物质(MoS2,WS2,石墨,CaF2,云母等),高分子材料(尼龙、聚四氟乙烯等)等。其中溅射法制取MoS2膜及聚四氟乙烯膜十分有效。虽然MoS2膜可用化学反应镀膜法制作,但是溅射镀膜法得到的MoS2膜致密性好,附着性优良。MoS2溅射膜的摩擦系数很低,在0.02~0.05范围内。MoS2在实际应用时有两个问题:一是对有些基体材料如Ag,Cu,Be等目前还不能涂覆;二是随湿度增加,MoS2膜的附着性变差。在大气中使用要添加Sb2O3等防氧化剂,以便在MoS2表面形成一种保护膜。 溅射法可以制取聚四氟乙烯膜。试验表明,这种高分子材料薄膜的润滑特性不受环境湿度的影响,可长期在大气环境中使用,是一种很有发展前途的固体润滑剂。其使用温度上限为5OoC,低于-260oC时才失去润滑性。 MoS2、聚四氟乙烯等溅射膜,在长时间放置后性能变化不大,这对长时间备用、突然使用又要求可靠的设备如防震、报警、防火、保险装置等是较为理想的固体润滑剂。 内容来源:宝钢代理商https://www.360docs.net/doc/e34849887.html, 欢迎多多交流!!!
实验磁控溅射法制备薄膜材料
实验磁控溅射法制备薄 膜材料 GE GROUP system office room 【GEIHUA16H-GEIHUA GEIHUA8Q8-
实验4 磁控溅射法制备薄膜材料 一、实验目的 1. 掌握真空的获得 2. 掌握磁控溅射法的基本原理与使用方法 3. 掌握利用磁控溅射法制备薄膜材料的方法 二、实验原理 磁控溅射属于辉光放电范畴,利用阴极溅射原理进行镀膜。膜层粒子来源于辉光放电中,氩离子对阴极靶材产生的阴极溅射作用。氩离子将靶材原子溅射下来后,沉积到元件表面形成所需膜层。磁控原理就是采用正交电磁场的特殊分布控制电场中的电子运动轨迹,使得电子在正交电磁场中变成了摆线运动,因而大大增加了与气体分子碰撞的几率。用高能粒子(大多数是由电场加速的气体正离子)撞击固体表面(靶),使固体原子(分子)从表面射出的现象称为溅射。 1. 辉光放电: 辉光放电是在稀薄气体中,两个电极之间加上电压时产生的一种气体放电现象。溅射镀膜基于荷能离子轰击靶材时的溅射效应,而整个溅射过程都是建立在辉光放电的基础之上的,即溅射离子都来源于气体放电。不同的溅射技术所采用的辉
光放电方式有所不同,直流二极溅射利用的是直流辉光放电,磁控溅射是利用环状磁场控制下的辉光放电。 如图1(a)所示为一个直流 气体放电体系,在阴阳两极之间 由电动势为的直流电源提供电压 和电流,并以电阻作为限流电 阻。在电路中,各参数之间应满 足下述关系: V=E-IR 使真空容器中Ar气的压力保持一定,并逐渐提高两个电极之间的电压。在开始时,电极之间几乎没有电流通过,因为这时气体原子大多仍处于中性状态,只有极少量的电离粒子在电场的作用下做定向运动,形成极为微弱的电流,即图(b)中曲线的开始阶段所示的那样。 图1 直流气体放电 随着电压逐渐地升高,电离粒子的运动速度也随之加快,即电流随电压上升而增加。当这部分电离粒子的速度达到饱和时,电流不再随电压升高而增加。此时,电流达到了一个饱和值(对应于图曲线的第一个垂直段)。
磁控溅射法制备薄膜材料综述
磁控溅射法制备薄膜材料综述 材料化学张召举 摘要薄膜材料的厚度是从纳米级到微米级,具有尺寸效应,在国防、通讯、航空、航天、电子工业等领域有着广泛应用,其有多种制造方法,目前使用较多的是溅射法,其中磁控溅射的应用较为广泛。本文主要介绍了磁控溅射法的原理、特点,以及制备过程中基片温度、溅射功率、溅射气压和溅射时间等工艺条件对所制备薄膜性能的影响。 关键字磁控溅射;原理;工艺条件;影响 正文 薄膜是指尺度在某个一维方向远远小于其他二维方向,厚度可从纳米级到微米级的材料,由于薄膜的尺度效应,它表现出与块体材料不同的物理性质,有广泛应用。薄膜的制备大致可分为物理方法和化学方法两大类。物理方法主要包括各种不同加热方式的蒸发,溅射法等,化学方法则包括各种化学气相沉积(CVD)、溶胶-凝胶法(sol-gel)等。 溅射沉积法由于速率快、均一性好、与基片附着力强、比较容易控制化学剂量比及膜厚等优点,成为制备薄膜的重要手段。溅射法根据激发溅射离子和沉积薄膜方式的不同又分直流溅射、离子溅射、射频溅射和磁控溅射,目前多用后两种。本文主要介绍磁控溅射制备薄膜材料的原理及影响因素。 磁控溅射是70年代迅速发展起来的新型溅射技术,目前已在工业生产中实际应用。这是由于磁控溅射的镀膜速率与二极溅射相比提高了一个数量级。具有高速、低温、低损伤等优点。高速是指沉积速率快;低温和低损伤是指基片的温升低、对膜层的损伤小。1974年Chapin发明了适用于工业应用的平面磁控溅射靶,对进人生产领域起了推动作用。 磁控溅射基本原理 磁控溅射是20世纪70年代迅速发展起来的一种高速溅射技术。对许多材料,利用磁控溅射的方式溅射速率达到了电子术蒸发的水平,而且在溅射金属时还可避免二次电子轰击而使基板保持冷态,这对使用怕受温度影响的材料作为薄膜沉
磁控溅射镀膜技术的发展_余东海
第46卷第2期2009年3月 真 空 VACUUM Vol.46,No.2Mar.2009 收稿日期:2008-09-03 作者简介:余东海(1978-),男,广东省广州市人,博士生 联系人:王成勇,教授。 *基金项目:国家自然科学基金(50775045);东莞市科技计划项目(20071109)。 磁控溅射镀膜技术的发展 余东海,王成勇,成晓玲,宋月贤 (广东工业大学机电学院,广东 广州 510006) 摘 要:磁控溅射由于其显著的优点应用日趋广泛,成为工业镀膜生产中最主要的技术之一,相应的溅 射技术与也取得了进一步的发展。 非平衡磁控溅射改善了沉积室内等离子体的分布,提高了膜层质量;中频和脉冲磁控溅射可有效避免反应溅射时的迟滞现象,消除靶中毒和打弧问题,提高制备化合物薄膜的稳定性和沉积速率;改进的磁控溅射靶的设计可获得较高的靶材利用率;高速溅射和自溅射为溅射镀膜技术开辟了新的应用领域。 关键词:镀膜技术;磁控溅射;磁控溅射靶中图分类号:TB43 文献标识码:A 文章编号:1002-0322(2009)02-0019-07 Recent development of magnetron sputtering processes YU Dong-hai,WANG Cheng-yong,CHENG Xiao-ling,SONG Yue-xian (Guangdong Universily of Technology,Guangzhou 510006,China ) Abstract:Magnetron sputtering processes have been widely appleed to thin film deposition nowadays in various industrial fields due to its outstanding advantages,and the technology itself is progressing further.The unbalanced magnetron sputtering process can improve the plasma distribution in deposition chamber to make film quality better.The medium -frequency and pulsed magnetron sputtering proceses can efficiently avoid the hysteresis during reactive sputtering to eliminate target poisoning and arcing,thus improving the stability and depositing rate in preparing thin compound films.Higher utilization of target can be obtained by improved target design,and the high -speed sputtering and self -sputtering provide a new field of applications in magnetron sputtering coating processes. Key words:coating technology;magnetron sputtering;magnetron sputtering target 溅射镀膜的原理[1]是稀薄气体在异常辉光 放电产生的等离子体在电场的作用下,对阴极靶材表面进行轰击,把靶材表面的分子、原子、离子及电子等溅射出来,被溅射出来的粒子带有一定的动能,沿一定的方向射向基体表面,在基体表面形成镀层。 溅射镀膜最初出现的是简单的直流二极溅射,它的优点是装置简单,但是直流二极溅射沉积速率低;为了保持自持放电,不能在低气压(<0.1Pa )下进行;不能溅射绝缘材料等缺点限制了其应用。在直流二极溅射装置中增加一个热阴极和辅助阳极,就构成直流三极溅射。增加的热阴极和辅助阳极产生的热电子增强了溅射气体原子的电离,这样使溅射即使在低气压下 也能进行;另外,还可降低溅射电压,使溅射在低 气压,低电压状态下进行;同时放电电流也增大,并可独立控制,不受电压影响。在热阴极的前面增加一个电极(栅网状),构成四极溅射装置,可使放电趋于稳定。但是这些装置难以获得浓度较高的等离子体区,沉积速度较低,因而未获得广泛的工业应用。 磁控溅射是由二极溅射基础上发展而来,在靶材表面建立与电场正交磁场,解决了二极溅射沉积速率低,等离子体离化率低等问题,成为目前镀膜工业主要方法之一。磁控溅射与其它镀膜技术相比具有如下特点:可制备成靶的材料广,几乎所有金属,合金和陶瓷材料都可以制成靶材;在适当条件下多元靶材共溅射方式,可沉积 DOI:10.13385/https://www.360docs.net/doc/e34849887.html,ki.vacuum.2009.02.026
磁控溅射法制备薄膜材料实验报告
实验一磁控溅射法制备薄膜材料 一、实验目的 1、详细掌握磁控溅射制备薄膜的原理和实验程序; 2、制备出一种金属膜,如金属铜膜; 3、测量制备金属膜的电学性能和光学性能; 4、掌握实验数据处理和分析方法,并能利用 Origin 绘图软件对实验数据进行处理和分析。 二、实验仪器 磁控溅射镀膜机一套、万用电表一架、紫外可见分光光度计一台;玻璃基片、金属铜靶、氩气等实验耗材。 三、实验原理 1、磁控溅射镀膜原理 (1)辉光放电 溅射是建立在气体辉光放电的基础上,辉光放电是只在真空度约为几帕的稀薄气体中,两个电极之间加上电压时产生的一种气体放电现象。辉光放电时,两个电极间的电压和电流关系关系不能用简单的欧姆定律来描述,以气压为的 Ne 为例,其关系如图 5 -1 所示。 图 5-1 气体直流辉光放电的形成 当两个电极加上一个直流电压后,由于宇宙射线产生的游离离子和电子有限,开始时只有很小的溅射电流。随着电压的升高,带电离子和电子获得足够能量,与中性气体分子碰撞产生电离,使电流逐步提高,但是电压受到电源的高输出阻抗限制而为一常数,该区域称为“汤姆森放电”区。一旦产生了足够多的离子和电子后,放电达到自持,气体开始起辉,出现电压降低。进一步增加电源功率,电压维持不变,电流平稳增加,该区称为“正常辉光放电”区。当离子轰击覆盖了整个阴极表面后,继续增加电源功率,可同时提高放电区内的电压和电流密度,形成均匀稳定的“异常辉光放电”,这个放电区就是通常使用的溅射区域。随后继续增加电压,当电流密度增加到~cm 2时,电压开始急剧降低,出现低电压大电流的弧光放电,这在溅射中应力求避免。 (2)溅射
磁控溅射制备铝薄膜毕业论文
磁控溅射制备铝薄膜毕业论文 目录 第1章绪论 (1) 1.1 引言 (1) 1.1.2 薄膜研究的发展概况 (1) 1.1.3 薄膜的制备方法 (4) 1.1.4 薄膜的特征 (5) 1.1.5 薄膜的应用 (7) 第2章射频反应磁控溅射制备方法机理分析 (8) 2.1 射频反应磁控溅射法原理 (8) 2.1.1 直流辉光放电 (8) 2.1.2 射频辉光放电 (9) 2.1.3 射频原理 (9) 2.1.4 磁控原理 (11) 2.1.5 反应原理 (12) 2.2. 溅射机理 (13) 2.2.1 基本原理 (13) 2.2.2 基本装置 (13) 2.3 溅射的特点和应用 (15) 2.3.1 溅射的特点 (15) 2.3.2 溅射的应用 (16) 第3章实验 (17) 3.1 课题的研究线路 (17) 3.2 实验材料以及设备 (17) 3.3 实验仪器的原理 (18) 3.3.1 磁控溅射镀膜仪的原理 (18) 3.3.2 椭圆偏振测厚仪的原理 (19) 3.3.3 原子力显微镜的原理 (23) 3.3.4 表面预处理 (27) 3.3.5 薄膜制备 (28) 第4章实验结果及数据分析 (30) 4.1 薄膜测试与分析 (30) 4.1.1 衬底温度对于铝薄膜属性的影响 (30) 4.1.2 衬底温度对于铝薄膜生长的影响 (31)
4.1.3 不同的气压对于铝薄膜生长的影响 (34) 结论 (40) 致 (41) 参考文献 (42) 附录X 译文 (43) 利用CO/SiC衬底上制备单层石墨薄膜 (43) 附录Y 外文原文 (48)
第一章绪论 1.1 薄膜概述 1.1.1 引言 人工薄膜的出现是20世纪材料科学发展的重要标志。自70年代以来,薄膜材料、薄膜科学、与薄膜技术一直是高新技术研究中最活跃的研究领域之一,并已取得了突飞猛进的发展。薄膜材料与薄膜技术属于交叉学科,其发展几乎涉及所有的前沿学科,其应用与推广渗透到了各相关技术领域。正是由于薄膜材料和薄膜技术的发展才极促进了微电子技术、光电子技术、计算机技术、信息技术、传感器技术、航空航天技术和激光技术的发展,也为能源、机械、交通等工业部门和现代军事国防部门提供了一大批高新技术材料和器件。 薄膜是不同于其它物质(气态、液态、固态和等离子态)的一种新的凝聚态,有人称之为物质的第五态。顾名思义,薄膜就是薄层材料。它可以理解为气体薄膜,如吸附在固体表面的气体薄层;也可理解为液态薄膜,如附着在液体和固体表面的油膜。我们这里所指的薄膜是固体薄膜,即使是固体薄膜,也可分为薄膜单体和附着在某种基体上的另一种材料的固体薄膜,这里所指的薄膜属于后者[1]。 薄膜的基底材料有绝缘体,如玻璃、瓷等;也有半导体,如硅、锗等;也各种金属材料。薄膜材料也可以是各种各样的,如从导电性来分,可以是金属、半导体、绝缘体或超导体。从结构上来分,它可以是单晶、多晶、非晶(无定形)、微晶或超晶格的。从化学组成上来看,它可以是单质,也可以是化合物,它可阻是无机材料,也可以是有机材料。 1.1.2 薄膜研究的发展概况 薄膜科学是由多个学科交叉、综合、以系统为特色,逐步发展起来的新兴学科,以“表面”及“界面”为研究核心,在有关学科的基础上,应用表面技术及其复合表面技术为特点,逐步形成了与其他学科密切相关的薄膜科
磁控溅射金属薄膜的制备
磁控溅射金属薄膜的制 备 公司标准化编码 [QQX96QT-XQQB89Q8-NQQJ6Q8-MQM9N]
磁控溅射薄膜金属的制备 黎明 烟台大学环境与材料工程学院山东烟台 111 E-mail 摘要: 金属与金属氧化物在气敏、光催化与太阳能电池等方面有着极为重要的应用,通过磁控溅射法制备的金属氧化物薄膜,具有纯度高、致密性好、可控性强、与基底附着性好等优点,因此磁控溅射技术被广泛应用于工业化生产制备大面积、高质量的薄膜。我们通过磁控溅射法制备了氧化铜纳米线阵列薄膜,并研究了其气敏性质;除此之外,我们还通过磁控溅射法制备了 TiO2/WO3复合薄膜,研究了两者之间的电荷传输性质 关键词:磁控溅射;气敏性质;光电性质 Magnetron sputtering metal film preparation LiMing Environmental and Materials Engineering, Yantai University Shandong Yantai 111 E-mail Abstract: GAas Metal and metal oxide have important applications in gas-sensing, photocatalyst and photovoltaics, etc. The metal oxide film prepared by magnetron sputtering technique possesses good qualities, such as high purity, good compactness, controllability and excellent adhesion. Therefore magnetron sputtering technique is widely used to prepare large area and high quality films in industrial production. In our work, CuO nanowires (NWs) array films were synthesized by magnetron sputtering. Their gas-sensing properties were also investigated. Except this, WO3/ TiO2 nanocomposite films were synthesized by magnetron sputtering and their dynamic charge transport properties were investigated by the transient photovoltage technique. Key Words : Gmagnetron Sputtering, Photo-electric Properties, Gas-sensing Properties 1绪论