不锈钢精密铸造

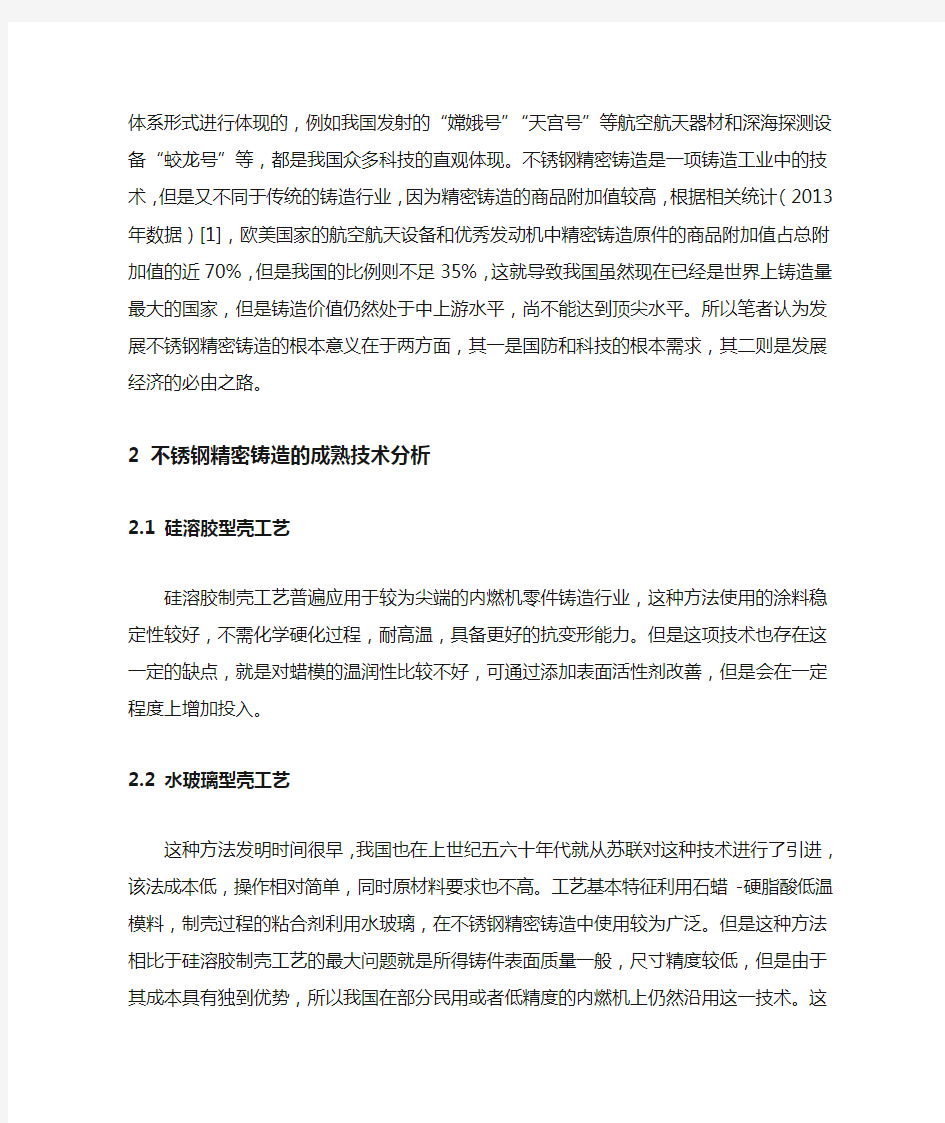
不锈钢精密铸造
摘要:不锈钢精密铸造不同于传统的铸造行业,我国虽然是铸造大国,但是精密铸造尚处于发展阶段,尚不能与发达国家相比。但是我国近年来大力发展工业化进程和科技水平,已经有一些相对成熟的技术手段,笔者将对这些较为成熟的技术进行重点分析,进而对我国未来不锈钢精密铸造的发展提出一些意见。
关键词:不锈钢精密铸造;技术分析
0 引言
不锈钢精密铸造又叫做熔模精密铸造,这种铸造工艺在铸造过程中尽量减少或者根本不进行切削,是一种适用范围广,铸件尺寸精度高,表面质量优异的铸造方法,同时铸造过程中并不处于超高温情况,更适于铸造航空航天、国防等高精尖产业的元件。最早的不锈钢精密铸造可以追溯到上世纪三四十年代,美国最早用不锈钢精密铸造法对其当时科技领先的航空发动机中的涡轮叶片进行铸造,成品受到了各方面的好评,进而使这种方法广为推广。我国对不锈钢精密铸造的研发和使用则是在新中国成立之后,后续随着我国国防工业的发展,不锈钢精密铸造在沈阳、贵州、北京、西安、湖南等地都开设了研究所或铸造厂。但是客观的看,我国的
不锈钢精密铸造行业仍然在发展阶段,尚不能满足我国航空航天、国防工业等行业的发展要求。
1 不锈钢精密铸造的重要意义
科技是一个国家、一个民族立足的根本,但是随着现代科技的不断发展我们发现,任何单独的科技发展都不能对当前社会造成巨大的变革和影响,因为新产品新科技往往是以体系形式进行体现的,例如我国发射的“嫦娥号”“天宫号”等航空航天器材和深海探测设备“蛟龙号”等,都是我国众多科技的直观体现。不锈钢精密铸造是一项铸造工业中的技术,但是又不同于传统的铸造行业,因为精密铸造的商品附加值较高,根据相关统计(2013年数据)[1],欧美国家的航空航天设备和优秀发动机中精密铸造原件的商品附加值占总附加值的近70%,但是我国的比例则不足35%,这就导致我国虽然现在已经是世界上铸造量最大的国家,但是铸造价值仍然处于中上游水平,尚不能达到顶尖水平。所以笔者认为发展不锈钢精密铸造的根本意义在于两方面,其一是国防和科技的根本需求,其二则是发展经济的必由之路。
2 不锈钢精密铸造的成熟技术分析
2.1 硅溶胶型壳工艺
硅溶胶制壳工艺普遍应用于较为尖端的内燃机零件铸造行业,这种方法使用的涂料稳定性较好,不需化学硬化过程,耐高温,具备更好的抗变形能力。但是这项技术也存在
这一定的缺点,就是对蜡模的温润性比较不好,可通过添加表面活性剂改善,但是会在一定程度上增加投入。
2.2 水玻璃型壳工艺
这种方法发明时间很早,我国也在上世纪五六十年代就从苏联对这种技术进行了引进,该法成本低,操作相对简单,同时原材料要求也不高。工艺基本特征利用石蜡-硬脂酸低温模料,制壳过程的粘合剂利用水玻璃,在不锈钢精密铸造中使用较为广泛。但是这种方法相比于硅溶胶制壳工艺的最大问题就是所得铸件表面质量一般,尺寸精度较低,但是由于其成本具有独到优势,所以我国在部分民用或者低精度的内燃机上仍然沿用这一技术。这项技术自引进以来,我国科研人员对其进行了比较大的改进,主要表现在如下几个方面:
①改善型壳涂料。
主要改进是在型壳的背部涂料中加入了一定量的耐火
黏土,让型壳的强度有了较大的提升,实现了单壳焙烧和烧注。
②硬化剂的优化。
传统硬化剂多用氯化铵,但是这种材料在铸造过程会释放大量氨气和氮氧化物气体,对大气造成污染,所以改用氯化铝溶液,进一步改用氯化铝结晶,这种硬化剂效果与氯化铵类似,但是近年来,氯化镁硬化剂的使用硬化速度和残留方面都具备比较大的优势,所以现在更加倾向于氯化镁做硬
化剂。
③复合型壳。
因为水玻璃涂料的型壳表面质量存在一定的缺陷,所以很多原件的铸造都采用多层模复合的形式进行铸造,一方面节约了成本,另一方面也提升了铸件的表面质量。
④新工艺发展。
目前较为成熟的新工艺应该是自吸铸工艺、泡沫塑料模、熔模型壳铸造等工艺,这些工艺在某些方面都是具备领先优势的,但是未来的改进仍然让科技工作者趋之若鹜。
3 多技术交叉使用探索
3.1 与快速成型技术的交叉使用
科学技术的交叉使用多半是进行互补,不锈钢精密铸造的蜡模制作过程中的设计和模具制造较为复杂和耗费时间,但是快速成型技术能够很好的弥补这一缺点,单独使用快速成型技术则是因为材料限制无法实施,所以近年来很多使用高分子技术获得铸件的圆形,进而制造蜡模,投入不锈钢精密铸造使用。例如光固化立体造型技术(SLA)和选择性激
光烧结技术(SLS),这两种技术是目前与熔模铸造术联合使用较为成熟的技术,SLA技术能够提供较高的尺寸精度,尤
其是零件外表面的精度,SLS在一定程度上原材料要稍微廉
价一些,但是精度情况也相较于SLA技术具备一定差距,适用于一些有成本要求的铸造工作。但是在使用过程中仍然要
注意控制好快速成型技术与不锈钢精密铸造技术的关键结
合点,例如成本控制和零件的铸造精度问题的综合考虑,选择合适的平衡点是快速成型技术与熔模铸造术有机结合的
关键问题。
3.2 计算机技术
不锈钢精密铸造过程中的方案设计和优化工作是一项
较为耗费人力和时间的工作,近年来随着计算机技术的不断发展,很多需要大量计算和精度计算的行业都引入了计算机工作,同时相应的开发了各种计算软件,例如ProCAST、AutoCAD、AFSolid、Anycasting等多种软件,这些软件可以对不锈钢精密铸造的设计和铸造过程进行计算或者模拟,通过数据计算的方式来现行优化方案,对不锈钢精密铸造的发展起到了良好的推动作用。
例如清华大学在常规的通用模拟软件开发上已经走在
了世界的前列,更是针对我国特色的航空发动机零件铸造模拟软件、TiAL合金涡轮叶片等高端铸造中的计算机模拟软件进行了研发;哈尔滨工业大学已经对空间站、火箭等航空铸造中的重要结构进行了实验室软件模拟铸造的研究工作;华中科技大学则是针对中高端的熔模铸造开发了华铸CAE系统,该系统具备更加广泛的适用面,也是我国当前较为领先的计算机技术与熔模铸造术交叉使用的典范。
但是在当前的使用过程中,我们也发现应当注重计算机
软件的建模适用性、材料本身的热物性参数等问题,这些问题良好的解决能够极大程度上缩短不锈钢精密铸造的研发
时间。
4 对我国未来不锈钢精密铸造行业发展的几点看法
我国通过“十一五”、“十二五”、“十三五”开始不断地对产业结构进行调整,高新板块在我国科技和经济的发展中越来越重要。因此笔者对未来的不锈钢精密铸造前景十分看好。
笔者对未来行业发展有几点建议如下:
①坚持自主研发,坚持自力更生。
虽然通过技术引进和改进的方式能够极大的缩短我国
与外国的科技水平差距,但是这种引进方式仍然是一种“走别人的路”的方式,而且受其他国家掣肘。所以笔者建议在新形势下应当坚持以发展具备自己特色的科技为主,坚持掌握核心科技,才能让我国的精密铸造行业不断发展不断进步。
②坚持发展理念,树立企业榜样。
不锈钢精密铸造行业是一个较为尖端的行业,所以应当在众多企业中选出龙头和榜样,通过带动力量推动我国整体的行业发展。
③加强研发与生产的结合。
我国当前从事不锈钢精密铸造研究的高等学府并不多,但是往往与各大生产厂商的联系不紧密,只是在学校实验室
进行研发,对我国的不锈钢精密铸造行业大批量生产和大范围推广是一个弊端,所以笔者建议生产厂商可以和高校建立联合研发生产一条龙合作,让技术不仅仅生存在实验室里,更能够投入到生产线上。
参考文献
[1] 吕志刚.世界熔模精密铸造产业动态[J].特种铸造及
有色合金,2014(34):70-72.
[2] 王植.不锈钢精密铸造行业市场情况及招商分析[J].
经济管理,2015(05):99.
不锈钢饰品铸造的工艺流程
不锈钢饰品铸造的工艺流程 学院:机电学院 班级:Z1005 学号:0649100506 姓名:王治群
1、制版 失蜡浇铸需要蜡版,而蜡版的批量制作则需要用银版压制的橡胶模。它是不锈钢饰品制作工艺中要求最高的工序,要求所制银板的表面,镂空部位和背面光洁无痕,要求银板的各部分结构合理,镶嵌钻石的位置尺寸准确无误,有些还要求对镶嵌部位进行预加工。准备好银版后才可以进入失蜡浇铸工艺流程。 目前使用的制版工艺主要有:手工雕蜡版,电脑雕蜡版和手起银版。三种工艺各有优点,相互补充。 手工雕蜡版即用石蜡雕出设计图纸上的造型,再利用失蜡浇铸的方法倒出银版;电脑雕蜡版不同于手工雕蜡的是它是通过电脑3D软件与喷蜡机相结合,做出蜡模造型,再使用失蜡浇铸的方法倒出银版;而手制银版,就是制版师傅直接手工制作设计图上的模型。由于手工雕蜡版制版速度快,雕蜡过程修改容易,工具损耗相对小而被广泛使用。 2、失蜡铸造 失蜡铸造俗称倒模,是目前不锈钢饰品生产的重要手段。 (1)压制胶模 压制胶模的注意事项及过程: 1)压模框和生胶片要清洁,不要用手直接接触生胶片的表面。 2)保证原版和橡胶之间不会粘连,应优先使用银版,铜板应先镀银。 3)确定适当的硫化温度和时间,两者基本上符合一个函数关系,与胶模的厚度,长宽及原版的复杂程度有关。通常将压模温度定为150度左右,如果胶模厚度在3层(约 10mm),一般硫化时间为20-25分钟,如果是4层(约13mm),则硫化时间可为30-35分钟。依次类推。同时硫化温度与原版的复杂程度也有关系,如原版复杂,细小,应降低硫化温度,延长硫化时间。 4)压模时要保证原版和生胶片之间没有缝隙。采用塞、缠、补的方式将首版上的空隙位、凹位和镶石位等填满,用碎小的胶粒填满,用尖锐物质(如镊子)压紧。 5)先行预热。硫化时间到了以后迅速取出胶模,压好的胶模要求整体不变形、光滑、水线不歪斜,最好使其自然冷却到不烫手时,就可以趁热用锋利的手术刀进行开胶模的操作。 (2)开胶模和注蜡模 1)开胶模: 开胶模的技术要求很高。因为开胶模的好坏直接影响到蜡模以及金属毛坯的质量。开胶模的工具比较简单有手术刀,镊子,剪刀,尖嘴钳等。胶模通常采用四脚定位法,也就是说。开出的胶模有四个脚互相吻合固定,四脚之间的部分有采用直线切割的,也有采用曲线切割的。开好的胶模要注意检查,胶模内不能有任何缺陷如明显的破花,缺角,粘连等,这些都有可能造成蜡模的缺陷,因此对这些缺陷部位应进行修补,如切开未切的位置,用焊蜡器焊补破花,缺角的地方等。 2)注蜡模: 胶模开好后就可以进行注蜡操作了。注蜡操作应注意对蜡温,压力以及胶膜的压紧等因素的掌握。
不锈钢薄壁透空蝶板件精铸工艺
不锈钢薄壁透空蝶板件精铸工艺 蝶板是蝶阀装备中的核心零件,通过在阀体内绕其自身的轴线旋转从而达到启闭或调节流体流量的目的。传统的蝶板厚大而笨重,材料消耗多。随着金属资源越来越紧缺,市场竞争日益加剧,蝶板设计也日趋轻量化。主要表现在蝶板主体内部透空、厚度超薄、密封面缩小。这种结构的改变给蝶板铸造带来了极大的困难。不少客户这类结构设计的蝶板在其它铸造厂久试不成,主要存在的问题是铸件变形严重,无法校正,密封面加工后气孔、夹渣多。我们在接到此类铸件样品订单后,仔细分析此产品结构特点,结合使用先进的MAGMA模拟软件,采用中温蜡硅溶胶制壳精铸工艺,经过两轮试制,圆满地完成了客户的样品制造任务。目前已批量生产多个厂家的轻量化结构系列蝶板。 1 蝶板铸件结构特点及工艺设计要点 1.1 铸件结构特点及要求 图1所示为蝶阀装配图,其核心零件圆盘形蝶板属于典型的大平面薄壁件。这个零件对同轴度及圆周密封面加工精度要求非常高。图2为蝶板铸件图,从铸件结构上看:该件直径达φ600mm,蝶板壁厚10mm,圆周边缘厚度只有7mm,内腔是空心的,铸件热节在轴线两端头的位置。其技术要求铸件轴向变形量≤1mm,外径加工后无任何铸造缺陷,100%部位RT检测,蝶板非加工面缩松、气孔、夹杂缺陷符合二级验收标准,气密性要好,无渗漏。 图1 蝶阀装配图图2 蝶板平面图 1.2 工艺要点及对策 为满足铸件技术要求,保证客户的样件开发交期,接到样品订单后我们组织了详细的工艺讨论。此铸件壁薄平面大,内腔孔深长,为保证铸件壁厚均匀,变形量小,蜡模必须有足够的强度。采用中温蜡制模可达到此要求。熔模在靠近中间部位合适的位置开设两个工艺孔,可确保焙烧时型壳内外不发生相对位移。为保证圆周密封面加工零缺陷,工艺设计时必须保证铸件在充型时不会存在“水平大平面”现象,要设法减少钢液二次氧化,熔炼出钢前加精炼剂精炼,提高钢液纯净度。
对双相不锈钢铸造的要求(中英)
REQUIREMENTS For CASTED ITEMS made of Duplex St. Steel 双向钢铸件的要求 Document number 文件号: YYYY Issue date 发布日期: ------ Revision / Date 修订日期: 0 /
1-Scope 适用范围 This specification covers the requirements for duplex stainless steel casted and machined parts. 本规范提出了双向不锈钢铸件和机加工件的要求. This specification is limited to casting and machining of parts, functional tests or other performance tests are excluded from this specification. 本规范只规定了铸造和机加工的技术要求,其它的性能测试和性能试验的要求不包含其中。 Statements or specifications made in the PO have priority over this specification.在PO中提出的要求和说明优先级高于本规范。 2-Objective 目标 This specification shall ensure that manufacturing of parts and inspections on these parts will be carried out in accordance with applicable international standards.本技术要求主要是为确保所指的零件的生产和检查都能根据适用的国际标准进行。 3-Definitions 定义 NDE Non-Destructive Examination 无损检查(探伤) PT Liquid Penetrant Examination ( Dye Penetrant Examination )着色渗透检查 MT Magnetic Particle Examination 磁粉检查 UT Ultasonic Examination 超声波检查 RT Radiographic Examination 射线照片检查 Critical Sections关键部位Sections with abrupt changes in shape or wallthickniss,, lifting points included.形状或壁厚急剧变化的部位,包括起吊点。4-Quality Assurance 质量保证 The Manufacturer and his Sub-suppliers are obligued to operate an ISO 9001 Quality Management System. Consequently the manufacturerer and his sub vendors are using skilled and qualified personell and are capable to manufacture and perform examinations in accordance with international applicable standards. 生产厂家及其分供商必须依据ISO9901质量管理系统标准进行质量管理,这样就要求生产厂家和其分供商雇用熟练合格的人员进行操作并且能根据相 关的国际标准进行生产和检验操作。 5- Requirements要求 Material specifications and requirements and related standards are clearly
不同Al质量分数的铸造304不锈钢组织和性能_喇培清
文章编号:1673-5196(2016)02-0001-08 不同Al质量分数的铸造304不锈钢组织和性能喇培清1,马付良1,孟 倩1,2,撒兴瑞1,魏玉鹏1,郭 鑫1 (1.兰州理工大学省部共建有色金属先进加工与再利用国家重点实验室,甘肃兰州 730050;2.兰州交通大学机电工程学院,甘肃兰州 730070) 摘要:通过中频无芯感应炉,在无保护气氛的大气中熔炼铸造制备Al质量分数为0%、1.5%、2%、3%的304不锈 钢,并对其进行1 050℃,保温45min的固溶处理,利用X射线衍射仪、光学显微镜、电子探针(EPMA)、扫描电镜 (SEM)、拉伸试验和腐蚀试验,研究不同Al质量分数304不锈钢的组织和性能.结果表明:304不锈钢中加入Al元 素后合金的组织由奥氏体+少量的骨骼状的δ铁素体逐渐转变为奥氏体+铁素体双相组织,当含Al质量分数为3.0%时,304不锈钢的基体组织转变为铁素体和在铁素体晶界上分布着的少量奥氏体.固溶态高铝304不锈钢的 性能优于铸态性能,含Al质量分数1.5%的固溶态304不锈钢具有最优的力学性能和耐腐蚀性能,与未加铝的304相比,各种性能均得到较大提高. 关键词:Al;304不锈钢;中频熔炼;组织;力学性能;腐蚀 中图分类号:TG142.1 文献标识码:A Microstructure and performance of cast 304stainless steel with different aluminum content LA Pei-qing1,MA Fu-liang1,MENG Qian1,2,SA Xing-rui 1,WEI Yu-peng1,GUO Xin1(1.State Key Laboratory of Advanced Processing and Recycling of Nonferrous Metals,Lanzhou Univ.of Tech.,Lanzhou 730050,China;2.Mechanical and Electrical Engineering Institute,Lanzhou Jiaotong University,Lanzhou 730070,China) Abstract:304stainless steel with Al additions of 0%,1.5%,2%and 3%was prepared by means ofmelting it in medium frequency coreless furnace in atmosphere without protective gas and then casted insand mold and processed with solid solution treatment at1 050℃for 40min.The microstructure and per-formance of aluminum-added 304stainless steel were investigated with SEM,optical microscopy,XRD,EPMA,tensile test,and corrosion test.The result showed that the alloying structure of 304stainless steelwith addition of Al element would gradually transform from austenite plus a minute amount of skeleton-shapedδ-ferrite intoα+γbiphasic structure.When the mass-fraction of Al was 3.0%,its matrix structurewould transform into ferrite and a minute amount of austenite on the grain boundary.The performance ofsolid-solution-state 304stainless steel would be superior to that of as-cast steel.When the aluminum con-tent was 1.5%,the aluminum-added 304stainless steel would have most excellent mechanical propertiesand intergranular corrosion resistance.Compared with the 304stainless steel without aluminum,its vari-ous performance would be improved to a larger extent. Key words:aluminum;304stainless steel;medium frequency smelting;microstructure;mechanicalproperty;corrosion 304不锈钢是目前应用最为广泛的一种铬-镍不锈钢,具有良好的耐蚀性、耐热性、低温强度、加工性能和可焊性,主要应用在医疗器具、汽车、建筑、石 收稿日期:2015-03-10 基金项目:国家自然科学基金(51164022) 作者简介:喇培清(1971-),男,甘肃临夏人,博士,研究员.油化工和家用器皿等行业.正是由于其广泛的应用,304不锈钢出现了各种失效问题,其中晶间腐蚀是常见的失效形式.目前提高不锈钢耐腐蚀性的工艺主要是涂层和添加合金元素,涂层处理的合金不宜进行焊接和热加工,并且一些零件不易进行表面处理,所以,在304不锈钢中添加合金元素改善其耐腐 第42卷第2期2016年4月 兰 州 理 工 大 学 学 报 Journal of Lanzhou University of Technology Vol.42No.2 Apr.2016
水玻璃精密铸造
水玻璃精密铸造 蜡料制备 1.工艺要求: 1.1 蜡液温度:70-90℃,严禁超过90℃。 1.2 稀蜡温度:65-80℃。 1.3 蜡膏保温缸水温:48-50℃。 1.4 蜡膏应搅拌均匀呈糊状,温度控制在45-48℃,其中不允许有颗粒状蜡料。 1.5 蜡料配方 1.5.2 在生产过程中必须根据蜡模质量分析结果,适量增加或减少硬脂酸量,冬 季的酸值取下限,夏季的酸值取上限。 2操作程序 2.1 启动设备,检查运转是否正常,是否漏水、漏气、漏蜡,有问题应及时排除。 检查保温缸水温是否符合工艺要求。 2.2 按蜡料配比把石蜡、硬脂酸和回收蜡分别称好,加入化蜡槽内,加热至全熔状 态,其温度不得超过90℃。 2.3 把蜡液送到蜡膏搅拌机盛蜡槽内。 2.4 将搅蜡缸内加入三分之二的蜡片,启动搅拌机进行搅蜡直至呈糊状蜡料为止。3注意事项 3.1 稀蜡需用100目筛过滤,去掉杂质后方能使用。 3.2 不允许有影响质量的空气和水分混入蜡膏中。 3.3 化蜡槽和盛蜡槽每月清理两次。 3.4 蜡膏保温缸、搅蜡缸属于压力容器,应定期检查有关紧固件及密封机构的使用 情况,发现问题应及时处理,正常工作压力严禁超过0.50MPa。 4检查项目 每班必须测量蜡液温度和保温水温度3-4次,控制在工艺要求范围内并做好原始记录。
蜡模制造 1 工艺要求 1.1 室温:16-28℃(最高不超过30℃)。 1.2 蜡膏压注温度:45~48℃,压力:0.3~0.5 MPa,保压时间:3~10秒。 1.3 压蜡冷却水温,14~24℃,冷却时间:20~100秒。 1.4蜡模冷却水温,14~24℃,冷却时间:10~60min。 1.5蜡模清洗液温度,20~28℃,清洗液中加入0.01% JFC。 1.6 脱模剂:ZF201. 1.7蜡模表面光洁度,形状完整,轮廓清洗,尺寸合格,不允许有缩陷,凸包裂 纹等缺陷。 2操作程序 2.1 手工制模 2.1.1检查压型的分型面、型腔、脱模机构、定位销、紧固件应完整清洁。涂擦 分型剂,装配并紧固压型。 2.1.2注蜡:把蜡抢嘴对准压型的注蜡孔,旋开阀门使蜡膏注入型腔并保压 3~10s,关闭阀门,移走蜡枪。 2.1.3冷却:把注满蜡膏的压型濅入水内或放在工作台上冷却,冷却时间视蜡模 形状与质量要求具体掌握,一般冷却20~100s。 2.1.4取模:拆开冷却过的压型,取出蜡模并及时放入水中继续冷却。有特殊要 求的蜡模应放在专用夹辅具上冷却。 2.1.5清型:用压缩空气吹除型腔、型芯上的水和蜡渣,视取模状况涂擦脱模剂。 2.1.6合型:装配清理干净的压型,按 3.1.2~3.1.5的程序再次制模。 2.1.7交班:工作完毕应把压型清理干净,打扫工作环境后交班,若不在生产时, 压型应及时交还压型库保管。 2.2 机械制模 2.2.1检查压蜡机的润滑,电器、气动系统是否正常,调整限位,顶模机构,调 节循环水系统和蜡膏输送系统。根据不同产品的压型注蜡孔,调整固定压蜡抢嘴的位置。 2.2.2用压缩空气吹除压型型腔内的水和蜡渣,吹刷分形剂,启动压蜡机。 2.2.3压蜡机按自控程序完成:取出蜡模,按要求放置冷却。 2.2.4按 3.2.2~3.2.4的程序连续制模。 2.2.5工作完毕应用压缩空气清除压蜡和压型上的水和蜡渣,水槽中的蜡渣和注 蜡道必须清理干净,打扫工作环境后交班,并作好交接班记录。
不锈钢的锻造工艺
不锈钢的锻造工艺(马氏体、奥氏体) 一奥氏体不锈钢的锻造 1.概述 奥氏体不锈钢的碳质量分数小于0.25%,铬的质量分数17~19%,镍的质量分数为8%~18%,如12Cr18Ni9等。为节镍,用锰或氮代替部分镍而获得的Cr-Ni-Mn或Cr-Ni-Mn-N不锈钢。 奥氏体不锈钢不发生组织转变,不能用热处理强化,只能通过热锻成形和再结晶获得高的强度。奥氏体不锈钢通常在固溶状态下使用,具有最佳的塑性、韧性、良好的加工成型性及良好的耐蚀性和抗氧化性,因此一般用于要求耐腐蚀、抗氧化或在较高温度下工作,对强度要求不高,以及在较低温度下使用的零部件。 奥氏体不锈钢在高温下晶粒易长大,但长大倾向不如铁素体不锈钢强烈。 2.锻造温度选择及加热要求 (1)变形温度选择: 奥氏体不锈钢的锻造加热温度受高温铁素体(α-相)形成温度的限制,加热温度过高,α-相铁素体的量会显着增多,使钢塑性降低,使塑性变形不均匀,在两相界面产生裂纹。因此奥氏体不锈钢的始锻温度一般控制在1150~1200℃。 为防止组织中因洗出碳化物使变形抗力增加,产生锻造裂纹。所以终锻温度不应太低,一般不低于850℃。
对于普通18-8型不锈钢始锻温度取1200℃,当含钼或含高硅则取低于1150℃,对于25-12型和25-20型,始锻温度不高于1150℃,终端温度不低于925℃。(2)加热要求: 不锈钢导热性差,加热时要严格按照温度和速度进行:800℃以下缓慢加热(0.3~0.5mm/min),到920℃后可快速加热。 为确保耐蚀性,加热时应严格避免渗碳,因此奥氏体不锈钢不宜在还原性气氛或过分氧化气氛中加热,也不许火焰直接喷射在毛坯上,否则使钢增碳或使晶界区贫铬,提高钢的晶间腐蚀敏感性。 锻件在高温区停留时间不宜过长,否则易造成严重过氧化、元素贫化和晶粒粗化,具体可按锻压手册P217表2-3-15选择,一般不少于10~20min。 3.奥氏体不锈钢锻造要点 (1)钢锭锻造时,开始轻压,当变形量达到30%后才能重压。锻造时,应单向送进,避免在一处重复压制,以防止出现中心十字裂纹。 (2)钢锭锻造比采用4~6,钢坯取2~4,视原材料晶粒度而定。奥氏体不锈钢晶粒度大小对钢的耐蚀性有很大影响。为获得细晶粒并充分焊合中心区的微裂纹和孔隙,应保证最后一火有足够大的锻造比,变形量应大于再结晶临界变形程度,变形量一般应大于12%~20%。 (3)变形过程中要求变形均匀,以得到较均匀的晶粒组织,圆饼锻件可考虑下列措施:
不锈钢铸造的四个注意事项
不锈钢铸造的四个注意事项 时间:2012-07-19 14:22来源:本站作者:admin 点击: 167 次 (1)为防止不锈钢铸造时产生白口,除从工艺上采取措施外,必须使其壁厚不能过薄(有些资料指出,壁厚在15mm以上时,用金属型铸造铸件的转角处都必须采用圆角,对于铝合金、镁 (1)为防止不锈钢铸造时产生白口,除从工艺上采取措施外,必须使其壁厚不能过薄(有些资料指出,壁厚在15mm以上时,用金属型铸造铸件的转角处都必须采用圆角,对于铝合金、镁合金金属型铸造铸件的铸造圆角不应小于3-4m,对于铸铁、铸钢、铜合金金属型铸造件的铸造圆角可参见表1.1-32选取; (2)由于金属型和芯无让性,为便于取出铸件和抽出型,不锈钢铸造铸件的铸造斜度应比砂型铸造件的适当大一些,一般应大30%-50%,应该指出:铸造斜度大小除与合金种类、壁的高度有关外,还与铸件表面的位置有关,凡在铸件冷却收缩时与金属型表面有脱离倾向的铸件表面可设计较小的斜度,而在铸件收缩时趋向于压紧在金属型上的铸件表面应给予较大的斜度,各种合金的不锈钢铸造的铸造斜度; (3)由于金属型散热快,因此不锈钢铸造的最小壁厚应比砂型铸造铸件的要大一些,各种铸造合金、不同大小的铸造最小壁厚; (4)不锈钢铸造铸件内壁和内肋的厚度一般应取相连外壁厚度的0.6-0.7,否则由于内壁(肋)冷得慢,在铸件收缩时易在内外壁交接处产生裂纹。 最小壁厚(不小于)单位(mm)
金属型 ~70×70 >70×70~150×150 >150×150 5 — 10 4 5 6 — — — 2.5~ 3.5 — — 2~3 4 5 — 2.5 — 3 4~5 6~8 注:1.一般铸造条件下,各种灰铸铁的最小允许壁厚: HT100,HT150,δ=4~6mm HT200,δ=6~8mm HT250,δ=8~15mm HT300,HT350,δ=15mm HT400,δ≥20mm 2.当改善铸造条件时,灰铸铁最小壁厚可达3mm ,可锻铸铁可小于3mm 。 一、壁厚和铸造圆角和脱模斜度 (2009-11-27 13:07:50) 标签: 分类:压铸件设计规范 一、 壁厚 压铸件的壁厚对铸件质量有很大的影响。以铝合金为例,薄壁比厚壁具有更高的强度和良好的致密性。因此,在保证铸件有足够的强度和刚性的条件下,应尽可能减少其壁厚,并保持壁厚均匀一致。 铸件壁太薄时,使金属熔接不好,影响铸件的强度,同时给成型带来困难;壁厚过大或严重不均匀则易产生缩瘪及裂纹。随着壁厚的增加,铸件内部气孔、缩松等缺陷也随之增多,同样降低铸件的强度。 压铸件的壁厚一般以2.5~4mm 为宜,壁厚超过6mm 的零件不宜采用压铸。推荐采用的最小壁厚和正常壁厚见表1。
不锈钢标准件
不锈钢标准件概况 硅溶胶工艺属于称熔模精密铸造或精密铸造,是一种少切削或无切削的铸造工艺,是铸造行业中的一项优异的工艺技术,其应用非常广泛。它不仅适用于各种类型、各种合金的铸造,而且生产出的铸件尺寸精度、表面质量比其它铸造方法要高,甚至其它铸造方法难于铸得的复杂、耐高温、不易于加工的铸件,均可采用熔模精密铸造铸得。 不锈钢标准件历史 熔模精密铸造是在古代蜡模铸造的基础上发展起来的。作为文明古国,中国是使用这一技术较早的国家之一,远在公元前数百年,我国古代劳动人民就创造了这种失蜡铸造技术,用来铸造带有各种精细花纹和文字的钟鼎及器皿等制品,如春秋时的曾侯乙墓尊盘等。曾侯乙墓尊盘底座为多条相互缠绕的龙,它们首尾相连,上下交错,形成中间镂空的多层云纹状图案,这些图案用普通铸造工艺很难制造出来,而用失蜡法铸造工艺,可以利用石蜡没有强度、易于雕刻的特点,用普通工具就可以雕刻出与所要得到的曾侯乙墓尊盘一样的石蜡材质的工艺品,然后再附加浇注系统,涂料、脱蜡、浇注,就可以得到精美的曾侯乙墓尊盘。 不锈钢五金铸件发展 现代熔模铸造方法在工业生产中得到实际应用是在二十世纪四十年代。当时航空喷气发动机的发展,要求制造象叶片、叶轮、喷嘴等形状复杂,尺寸精确以及表面光洁的耐热合金零件。由于耐热合金材料难于机械加工,零件形状复杂,以致不能或难于用其它方法制造,因此,需要寻找
一种新的精密的成型工艺,于是借鉴古代流传下来的失蜡铸造,经过对材料和工艺的改进,现代熔模铸造方法在古代工艺的基础上获得重要的发展。所以,航空工业的发展推动了熔模铸造的应用,而熔模铸造的不断改进和完善,也为航空工业进一步提高性能创造了有利的条件。我国是于上世纪五、六十年代开始将熔模铸造应用于工业生产。其后这种先进的铸造工艺得到巨大的发展,相继在航空、汽车、机床、船舶、内燃机、气轮机、电讯仪器、武器、医疗器械以及刀具等制造工业中被广泛采用,同时也用于工艺美术品的制造。 所谓熔模铸造工艺,简单说就是用易熔材料(例如蜡料或塑料)制成可熔性模型(简称熔模或模型),在其上涂覆若干层特制的耐火涂料,经过干燥和硬化形成一个整体型壳后,再用蒸汽或热水从型壳中熔掉模型,然后把型壳置于砂箱中,在其四周填充干砂造型,最后将铸型放入焙烧炉中经过高温焙烧(如采用高强度型壳时,可不必造型而将脱模后的型壳直接焙烧),铸型或型壳经焙烧后,于其中浇注熔融金属而得到铸件。 熔模铸件尺寸精度较高,一般可达CT4-6(砂型铸造为CT10~13,压铸为CT5~7),当然由于熔模铸造的工艺过程复杂,影响铸件尺寸精度的因素较多,例如模料的收缩、熔模的变形、型壳在加热和冷却过程中的线量变化、合金的收缩率以及在凝固过程中铸件的变形等,所以普通熔模铸件的尺寸精度虽然较高,但其一致性仍需提高(采用中、高温蜡料的铸件尺寸一致性要提高很多)。 压制熔模时,采用型腔表面光洁度高的压型,因此,熔模的表面光洁度也比较高。此外,型壳由耐高温的特殊粘结剂和耐火材料配制成的耐火涂料涂挂在熔模上而制成,与熔融金属直接接触的型腔内表面光洁度高。所以,熔模铸件的表面光洁度比一般铸造件的高,一般可达Ra.1.6~3.2μm。 熔模铸造最大的优点就是由于熔模铸件有着很高的尺寸精度和表面光洁度,所以可减少机械加工工作,只是在零件上要求较高的部位留少许加工余量即可,甚至某些铸件只留打磨、抛光余量,不必机械加工即可使用。由此可见,采用熔模铸造方法可大量节省机床设备和加工工时,大幅度节约金属原材料。 熔模铸造方法的另一优点是,它可以铸造各种合金的复杂的铸件,特别可以铸造高温合金铸件。如喷气式发动机的叶片,其流线型外廓与冷却用内腔,用机械加工工艺几乎无法形成。用熔模铸造工艺生产不仅可以做到批量生产,保证了铸件的一致性,而且避免了机械加工后残留刀纹的应力集中。
不锈钢铸造中熔炼和金属处理
不锈钢铸造中熔炼和金属处理 铸造基本定义 珠光体――由铁素体和渗碳体片交替组成的共折组织 铁素体――即δ组、α组,由碳在铁中形成的间隙固溶体,纬心立方晶格,δ相存在于1392℃~1536℃;α相存在于911℃以下。 奥氏体――即γ相,符号γ或а,由碳在γ铁中形成的间隙固溶体,而心立方晶格,存在于727℃~1483℃ 石墨――铸铁中以游离状态存在的碳,有折石墨,共晶石墨及共折石墨,共形态可呈片状、蠕虫状、团絮状及球状。 渗碳体――即fe3c,铁与碳形成的间隙化合物,复杂的正交晶格,有一次渗碳体、共晶渗碳体、二次渗碳体和共折渗碳体,开头可呈片状、扳条状及网状。 莱氏体――由奥氏体及其轻变产物和渗碳体组成的混合物。为共晶组织。 马氏体相变――替换原子经无扩散切变位移而产生的形状改变,形核-长大型的相变 马氏体――马氏体相变的产物贝氏体――由铁素体和碳休物组成的针状聚合物,存在于马氏体温度以下珠光体温度以下 索氏体――属于珠光体类型,共组织比珠光体细小,具有良好的综合机械性能 屈氏体――极细的珠光体组织,比索氏体还细 灰铸铁――基体组织和片状石墨组成,断口呈灰口 球墨铸铁――基体组织和球状石墨组成,断口呈银白色 蠕墨铸铁――基体组织和蠕状石墨组成,也会伴有少量球状石墨,断口呈胶状,断口呈白色 可锻铸铁――组织为珠光体和莱氏体组成,退火后组织为基体和团絮状石墨组成,断口呈黑绒状 控磨铸铁――基体组织和碳化物组成,断口呈白口 耐热铸铁――基体组织和片状或球状石墨组成,断口呈灰口 耐腐蚀铸铁――基体组织和片状或球状石墨组成,断口呈灰口 碳钢――即碳素钢,指含碳量<2%,并含有少量si、mn、p、s等元素的铁碳合金,工业使用一般含碳量<1。4%,分为低碳钢、中碳铜和高碳钢
不锈钢精密铸造工艺的特性
不锈钢精密铸造工艺的特性 根据长期生产制做,在多次失败中总结出,比较合理的科学的新经验,加入一定量的稀土元素改善钢的合金质量。在电力、矿山、冶金等行业,物料的输送、输出、都是采用近距离、高压输送,管道承受着相当大的压力,并经受很严重的磨损,单一材质的管道很难满意此工况的要求。 2009年国内不锈钢精密铸造,不锈钢管件生产将被迫进入收缩状态,但是,投资的高增长将使得产能进一步扩大,对不锈钢精密铸造企业而言,2009年是一个十分痛苦而压抑之年,如果原材料成本能够大幅下降,还可以缓解钢企一定压力,无非开工率有所下降。还起细化晶粒作用,在表面形成保护膜,加入一定量Mo使合金在一定高温下,具有一定抗氧化作用,增加使用寿命。不锈钢精密铸造除含碳外一般还含有少量的硅、锰、硫、磷按用途可以把碳钢分为碳素结构钢、碳素工具钢和易切削结构钢三类,碳素结构钢又分为建筑结构钢和机器制造结构钢两种;冲压所使用的模具称为冲压模具,简称冲模.冲模是将材料(金属或非金属)批量加工成所需冲件的专用工具.冲模在冲压中至关重要,没有符合要求的冲模,批量冲压生产就难以进行;没有先进的冲模,先进的冲压工艺就无法实现. 不锈钢精密铸造的高频焊接正是利用交流电的趋肤效应和邻近效应,钢材经滚压成型后,形成一个截面断开的圆形管坯,在管坯内靠近感应线圈中心附近旋转一个或一组阻抗器(磁棒),阻抗器与管坯开口处形成一个电磁感应回路,在趋肤效应和邻近效应的作用下,管坯开口处边缘产生强大而集中的热效应,使焊缝边缘迅速加热到焊接所需温度经压辊挤压后,熔融状态的金属实现晶间接合,冷却后形成一条牢固的对接焊缝. 不锈钢精密铸造高频焊接是根据电磁感应原理和交流电荷在导体中的趋肤效应,邻近效应和涡流热效应,使焊缝边缘的钢材局部加热到熔融状态,经滚轮的挤压,使对接焊缝实现晶间接合,从而达到焊缝焊接的目的.高频焊是一种感应焊(或压力接触焊),它无需焊缝填充料,无焊接飞溅,焊接热影响区窄,焊接成型美观,焊接机械性能良好等优点,因此在钢管的生产中受到广泛的应用 要想完成一件精密铸造产品所需的工序很复杂,首先制模→熔炼(温度1600℃)→浇注→振壳→切割(切割浇口)→粗磨(磨去浇口)→酸洗(目的:去除铸造氧化皮酸洗液:硝酸50%、氢氟
铸造奥氏体不锈钢的铬镍当量比和相对磁导率_范修谦
铸造奥氏体不锈钢的铬镍当量比和相对磁导率 范修谦 (保定风帆精密铸造制品有限公司) 摘 要 介绍了铸造奥氏体不锈钢中各元素的作用;通过铬当量和镍当量经验公式计算CrE/NiE。使用不锈钢的CrE/NiE(成分当量)图估算铸造奥氏体不锈钢中的铁素体含量;使用磁导率检测仪检测相应铸件的相对磁导率,从而验证了铬镍当量CrE/NiE、铁素体量与相对磁导率的非线性关系。关键词 铬镍当量比;铁素体;相对磁导率 中图分类号 TG249.5 文献标志码 A 文章编号 1001-2249(2011)05-0439-03DOI:10.3870/tzzz.2011.05.016 收稿日期:2010-11-29;修改稿收到日期:2010-12- 25作者简介:范修谦,男,1956年出生,研究员级高级工程师,河北保定风帆精密铸造制品有限公司,河北保定(071051),电话:13703362617,E-mail :fan218@126.com 奥氏体不锈钢在常温下一般具有单一的奥氏体组 织, 是非磁性的。但在铸造状态下,由于成分偏析及合金含量不同,在奥氏体基体上还会产生其他相,如奥氏体(γ相)的同素异位体(铁素体,F)等。由于铁素体和奥氏体基体之间的化学成分、力学性能以及热稳定性等方面的差异,在某些场合下铁素体的出现会对奥氏体不 锈钢的性能带来不利影响[ 1~3 ]。对奥氏体不锈钢材料的力学性能和各元素的含量都有较详细的规定,但对铁素体的含量没有明确的说明。为了保证特殊用途下不锈钢的性能,有客户提出了控制奥氏体铸造不锈钢相对磁导率(μ≤0.2)的要求。可以通过控制不锈钢中起主要作用的合金含量即铬镍当量比来控制奥氏体不锈钢的相对磁导率, 从而也控制了奥氏体不锈钢中的铁素体含量。1 合金元素在奥氏体不锈钢中的作用 奥氏体不锈钢中形成铁素体的Cr、Si、Mo等元素和促进形成奥氏体的Ni、C、Mn等元素相互作用和补充,使奥氏体不锈钢在多种腐蚀介质中有较好的耐腐蚀性和良好的力学性能。一般地可使用铬镍当量经验公式:铬当量CrE=w(Cr)+w(Mo)+w(Si)×1.5%+w(Nb)×0.5%;镍当量NiE=w( Ni)+w(c)×30%+w(Mn)×0.5%定性地估计奥氏体不锈钢中铁素体形成的可能性及相对含量,见图1。另外也可用不锈钢的CrE/NiE成分当量比对铁素体的含量进行估算,见图2。但上述两种方法使用起来很不方便。而不锈钢磁导率主要取决于钢的化学成分、晶体结构、晶粒组织内应力。奥氏体不锈钢的组织结构、化学成分和钢的铬镍当量紧密相关,因此在不锈钢熔化时取样,使用磁导率测量仪控制磁导率大小,也就控制了奥氏体铸造不锈钢中奥氏体和铁素体的质量分数,也就使奥氏体不锈钢的综合性能达到预期要求 。 图1 室温下不锈钢的组织与铬、镍当量的关系(Hammond 图 ) 图2 不锈钢的CrE/NiE当量比与铁素体含量的关系 2 铬镍当量比CrE/NiE与相对磁导率的关系 使用光谱分析仪对不同铸件的化学成分进行分析(见表1 )。根据铸件化学成分计算出铸件的铬镍当量比CrE/NiE。使用CrE/NiE成分当量图( 见图2)或不锈钢组织状态图(见图1)估算出铸件的铁素体量,估算值见表1。 使用美国Permabltiy omdicator#6373磁导率称对铸件的磁导率进行检验,数据见表1。根据表1数据,分别制作CrE/NiE与相对磁导率μ关系, 见图3。铁素体含量与磁导率μ关系见图4。从CrE/NiE与相对磁导率关系图3,可看出铬镍当量比CrE/NiE与相对磁导率μ的关系为非线性关系,随铬镍当量CrE/NiE的增大,铸造不锈钢的相对磁导率也相应增大。 9 34精密铸造 特种铸造及有色合金 2011年第31卷第5期
精密铸造过程工艺流程图
精密铸造过程工艺流程图 本文由灵寿县洞里矿产加工厂整理制作,转载请注明出处,公司网址https://www.360docs.net/doc/fe13265990.html, 公司专业生产铸造用石英砂、石英粉、铝矾土,质优价廉,真诚期待与您的合作 具设计-----磨具制造----压蜡-----修蜡-----组树-------制壳(沾浆)-----脱蜡----型壳焙烧------化性分析---浇注----清理-----热处理-------机加工-----成品入库。 如过在详细点就是: 压蜡(射蜡制蜡模)---修蜡----蜡检----组树(腊模组树)---制壳(先沾浆、淋沙、再沾浆、最后模壳风干)---脱蜡(蒸汽脱蜡)-------模壳焙烧--化性分析--浇注(在模壳内浇注钢水)----震动脱壳---铸件与浇棒切割分离----磨浇口---初检(毛胚检)---抛丸清理-----机加工-----抛光---成品检---入库 铸造生产流程大体就是这样总的来说可以分为压蜡、制壳、浇注、后处理、检验 压蜡包括(压蜡、修蜡、组树) 压蜡---利用压蜡机进行制作腊模 修蜡---对腊模进行修正 组树---将腊模进行组树 制壳包括(挂沙、挂浆、风干) 后处理包括(修正、抛丸、喷砂、酸洗、) 浇注包括(焙烧、化性分析也叫打光谱、浇注、震壳、切浇口、磨浇口) 后处理包括(喷砂、抛丸、修正、酸洗) 检验包括(蜡检、初检、中检、成品检) 现代熔模精密铸造方法在工业生产中得到实际应用是在二十世纪四十年代。当时航空喷气发动机的发展,要求制造象叶片、叶轮、喷嘴等形状复杂,尺寸精确以及表面光洁的耐热合金零件。由于耐热合金材料难于机械加工,零件形状复杂,以致不能或难于用其它方法制造,因此,需要寻找一种新的精密的成型工艺,于是借鉴古代流传下来的失蜡精密铸造,经过对材料和工艺的改进,现代精密铸造方法在古代工艺的基础上获得重要的发展。所以,航空工业的发展推动了精密铸造的应用,而精密铸造的不断改进和完善,也为航空工业进一步提高性能创造了有利的条件。 我国是于上世纪五、六十年代开始将精密铸造应用于工业生产。其后这种先进的精密铸造工艺得到巨大的发展,相继在航空、汽车、机床、船舶、内燃机、气轮机、电讯仪器、武器、医疗器械以及刀具等制造工业中被广泛采用,同时也用于工艺美术品的制造。 所谓精密铸造工艺,简单说就是用易熔材料(例如蜡料或塑料)制成可熔性模型(简称熔模或模型),在其上涂覆若干层特制的耐火涂料,经过干燥和硬化形成一个整体型壳后,再用
精密铸造304不锈钢铸件黑点缺陷的解决措施
精密铸造304不锈钢铸件黑点缺陷的解决措施 徐州市热卡铸造材料有限公司张云郑申涛 一、综述 熔模精密铸造不锈钢典型的材质是304,也就是1Cr19Ni9Ti,通常的金相组织是奥氏体,机械加工后铸件表面会出现小黑点而导致铸件成批报废,耽误交期不说,订单甚至客户会因此丢失,根据黑点的形态我们把黑点分为两类,一类是不规则黑点,另一是形态接近圆形(扫描断面是圆形,铸件中的形态是球状)的规则黑点,这类黑点较多特别是抛光后清晰可见,焊补几乎不可能,有的客户要求不允许焊补,一旦发现焊补立刻终止合同。以下具体分析黑点的成因和解决措施,欢迎批评指正。 二、不锈钢黑点的成因 根据对黑点成分取样分析得知,无论是不规则黑点还是规则黑点缺陷,都有氧元素的踪迹,其他成分包括碳、锰、硅、铬等。 碳的来源很少,所加入的不锈钢原料和合金没有碳,唯一的可能是脱蜡不干净所致,蜡料高温碳化粘附在型壳上,浇注后和氧、硅等元素结合形成复杂的碳化物或者多元氧化物夹杂。 生产实践中,不规则的黑点多发生在靠近浇冒口附近,这是因为氧化夹渣颗粒小比重小容易上浮。这部分黑点的解决办法能够肯定是完善脱蜡工艺,不利于脱蜡的铸件可以设置脱蜡孔,另外保证脱蜡的温度压力时间严格按照工艺文件执行,应该都能得到顺利解决。 另一部分圆形的黑点的成因可以进行如下判断,首先是脱氧失败或者效果不彻底,大量游离的氧和钢液中的锰硅元素(可能来自铁合金也可能来自炉衬或者除渣剂)还有其他元素比如铬等形成多元的复杂的氧化夹渣,由于圆形应该说是球状体表面能最小,所以形成大量的球状氧化物颗粒,由于时间或者钢液粘度的影响未来得及上浮到液面,含有球状氧化物夹渣的钢水浇注后凝固成铸件从而形成黑点缺陷。 对于圆形的黑点缺陷这里多说几句,首先硅、锰、铬等元素是必须出现在钢液中,有的是合金有的竟然是为了脱氧加入的,而除渣剂中的各种成分复杂而多样化,又不可能不加除渣剂。 三、不锈钢黑点解决措施 以下脱氧熔炼工艺经过现场测试和多家工厂使用,是一种效果好成本低的成熟工艺,特别对于304、316不锈钢黑点的解决效果非常明显,建议推广使用。 1、初脱氧用锰铁和硅铁依然没错,加入量根据各工厂的情况,注意不要过量,另外加入时间是熔化基本结束即可加入或者熔化结束加入也是可以的。 2、加入钢花牌复合脱氧剂,有的工厂采用硅钙脱氧,实际脱氧效果还是不错的,但是对于经常出现黑点的情况,硅钙的脱氧力度似乎不够,特别是能到达的钢水深度受到质疑,其中之一就是不能彻底解决黑点缺陷,或者问题有反复。而加入钢花牌复合脱氧剂再加上合理的
不锈钢的精密铸造的工艺
不锈钢的紧密铸造 一、什么是不锈钢的紧密铸造 在生产不锈钢产品时,有些产品的形状怪异,无法用弯管等工艺进行生产时,为生产这类不规则形状(内部为空心或实心)的产品,采用的一种利用蜡模→做砂模→液态材料填充成型的工艺。 优点:可以根据不同的蜡模做出款式多变的产品。 缺点:成型坯料精度不高,表面粗糙度较大。 二、精铸工艺流程 1、根据不同形状的产品做模具。模具分上下凹模方式,通过车、刨、铣、蚀、电火花等 综合工序完成。凹坑形状、尺寸跟产品半边一致。因为腊模主要用于工业蜡压型使用,因此选用熔点不高,硬度不高、要求较低、价格较便宜、重量较轻的铝合金材料做模具。 2、利用铝合金模具生产出大量的工业蜡实芯模型。在正常情况下一只工业蜡实芯模型只能 对应出一只毛坯产品。 3、对蜡模周边余量进行精修,去毛刺后将多个单一蜡模粘在(又称组树)预先准备好的 模头上,此模头也是用蜡模生产出的工业蜡实芯模型。(外形很像一棵树)
4、将已固定在模头上的多个蜡模涂上工业胶水后均匀喷上第一层细砂(一种耐火砂、耐高 温,通常用的是硅沙)。此砂颗粒很小、很细,这样能确保最终毛坯表面尽量的光滑。 5、在设定的室温(或恒温)下让喷了第一层细砂的蜡模自然风干,但不能影响内部蜡模形 状变化,自然风干的时间取决于产品本身内部的复杂程度,一般精铸件第一次的风干时间大约在5—8小时左右。 6、第一次砂喷完并自然风干后,在蜡模的表面继续上工业胶水(硅溶浆),并喷上第二层 砂,第二层砂颗粒大小要比之前的第一层砂来的大、来的粗。喷完第二层砂后也是在设定的恒温下让蜡模自然风干。 7、第二次砂喷完并自然风干后,依次类推进行第三次喷砂,第四次喷砂,第五次喷砂等工 序。要求: -根据产品表面要求,体积大小,自重等相应调节喷砂次数。一般情况下喷砂次数为3-7次。 -每次喷砂的砂粒大小均不一样,通常后道工序的砂粒均较前道工序砂粒粗,风干的时间长短也不一样。一般一个完整的蜡模上砂的生产周期为3~4天左右。 8、将已完成喷砂工序的蜡模在烘烤工序前,再均匀涂上一层白色的工业乳胶(硅溶浆), 以起到粘结和固化砂型,以及密封蜡模作用,为后道烘烤工序做准备。同时在烘烤工序后,还能提高砂型的脆性,便于敲碎砂层,取出毛坯。
不锈钢铸造工艺
主要的工艺环节简述如下: 1. 配砂型砂( 包括芯砂) 是多种造型材料的混合物。根据铸件对型砂的要求, 将造型材料按一定的比例均匀地混和, 这项工作叫做配砂。 型砂通常是由砂子和粘结剂所组成。砂子是耐高温的材料,是型砂中的主体。粘结剂的作用是把砂粒粘结在一起。粘结剂中应用最广泛的为粘土。有时为了满足某些性能要求,型砂中还加入其它造型材料,如煤粉、术屑等。型砂性能对铸件产量和质量的影响很大。例如型砂的可塑性不好,就不易得到清晰的型腔; 型砂的强度不高,则容易在起模和搬运过程中发生损坏,在浇注过程中发生冲砂等; 型砂的透气性差,就不能将浇注过程中产生的大量气体及时排出,而这些气体进入金属液, 就会使铸件产生气孔; 型砂的耐火性不好, 在浇入高温的金属液后,型砂就会因熔化而粘结在铸件的表面上, 形成粘砂; 型砂的退让性不好,会对凝固后的铸件收缩产生较大的阻力, 由此可能使铸件形成裂纹等 造型材料的质量, 配砂工作的好坏等,将影响型砂的性能, 进而影响铸件的质量。生产中对配制好的型砂,经常用仪器进行测定, 以保证型砂的各项附合要求。较为简便的检验方法, 用手抓起一把型砂,紧捏后放开,如砂团不松散而且不粘手,手印清楚,把它折断时,断面平整均匀, 则表示型砂的强度、可塑性等性能较好。 2. 造型利用铸模或其它方法制成所需的砂型, 这项工作叫做造型。实际生产中, 铸件的形状、大小和技术要求等,变化很大,因而造型方法也是多种多样的。现粗略分类简述如下: (1) 按造型方法分,有手工造型和机器造型。虽然手工造型没有机器造型产量高、质量好, 但由于需要准备的工作量较少, 灵活性和适应性又较大,所以当铸件生产的批量不大时,目前还是采用手工造型。 (2) 按造型用的铸模分, 有实样模造型和刮板造型。对造型来说, 实样模造型比刮板造型容易,但做铸模的工时和所用去的材料较多。生产中一般是采用实样模造型, 特别是铸件的生产数量较多时。 (3) 按砂型所处的地点分, 有砂箱造型和地面造型。把砂型做在地坑内,可以节省砂箱,但不能搬移, 造型较不方便。一般情况下,宜采用砂箱造型。 (4) 按砂型是否烘干分,有湿型和干型。砂型在浇注前不进行烘干的叫湿型( 又叫潮模), 在浇注前要进行烘干的叫干型( 又叫烘模〉。两者相比较, 干型的强度等性能较好,但要多经一道烘干工序。重量较大,质量要求较高的铸件常用干型浇注。 造型工作中,不仅要用经济、简便的方法把砂型制造出来, 而且要根据具体的铸件, 采取有效的措施, 防止铸件产生缺陷。例如: 浇注的金属液在型腔内流动时, 温度要不断下降, 如果浇口大小开得不合适,就有可能在金属液还未充满型腔, 就停止流动, 使铸件某些部分,尤其是细薄或是棱角的部分浇不足。为了使金属液能很好地充满型腔,对于薄壁的铸件,造型时,浇口就要开得大些。还要指出的,各种金属液的流动性是不相同的,例如灰铸铁比铸钢的流动性要好得多,所以灰铸铁可以浇出壁厚更薄的铸件。金属液从高温冷却到凝固,再冷却到室温,在体积或尺寸方面都要缩小, 也就是说具有收缩性。收缩性大的铸件, 当表层凝固而内部金属液继续收缩时, 往往会在铸件厚大的部分形成孔洞, 即所谓缩孔,为防止铸件产生缩孔,造型时要考虑补缩的问题, 最常用的方法就是设置冒口。 当铸件凝固后继续收缩时, 如果受到砂型和泥芯的阻碍,就可能产生裂纹。为此,造型时常需要采用一定的防裂措施。各种金属的收缩性是不相同的, 例如: 灰铸铁的收缩性比铸钢小得多,是常用金属中最小的一种, 所以灰铸铁件比较不容易产生缩孔、裂纹缺陷。