苯胺装置简介重要
苯胺装置:事故原因不在你
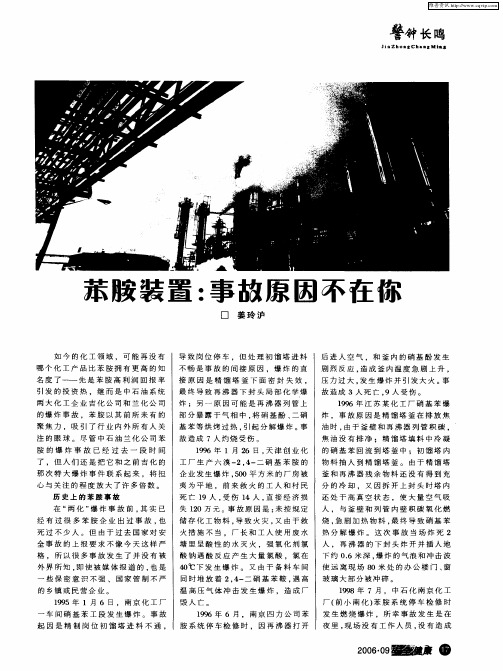
企 业 发 生 爆 炸 。0 50平 方 米 的 厂 房 被
夷 为 平 地 ,前 来 救 火 的 工 人 和 村 民 死亡 1 人, 伤 1 9 受 4人 , 接 经 济 损 直 失 10万 元 。事 故 原 因 是 : 按 规 定 2 未 火 措 施 不 当 . 厂 长 和 工 人 使 用 废 水
个 月 。事 故 发 生 时 , 修 工 作 已 基 本 检 完 成 , 入 最 后 的 清 理 阶 段 。而 吉 林 进
石 化 的苯 胺 事故 则 是发 生在 刚 完成 停 车 大 修 后 。 这 必 须 引 起 我 们 的 高 度 重 视 和 汲 取 足 够 的 教 训 , 同 时 也
! 故 , 苯 胺 以 其 前 所 未 有 的 事
7 吸 引 了 行 业 内 外 所 有 人 关 。
l 。 尽 管 中 石 油 兰 化 公 司 苯 故 造 成 7人 灼 烧 受 伤 。 球
炸 事 故 已 经 过 去 一 段 时 间 人 们 还 是 把 它 和 之 前 吉 化 的 } 爆 炸 事 件 联 系 起 来 , 将 担 大 19 9 6年 1月 2 日 . 津 创 业 化 6 天 工厂 生 产 六 溴 一 4 2. 一二 硝 基 苯 胺 的
焦 油 没 有 排 净 : 精 馏 塔 填 料 中 冷 凝
的 硝 基 苯 回 流 到 塔 釜 中 ; 初 馏 塔 内
物 料 抽 人 到 精 馏 塔 釜 。 由 于 精 馏 塔 釜 和 再 沸 器 残 余 物 料 还 没 有 得 到 充 分 的 冷 却 . 又 因 拆 开 上 封 头 时 塔 内
胺 系 统 停 车 检 修 时 . 因 再 沸 器 打 开
20・ 墓 06 9 0
。
维普资讯
论安全在苯胺装置长周期运行中的重要性
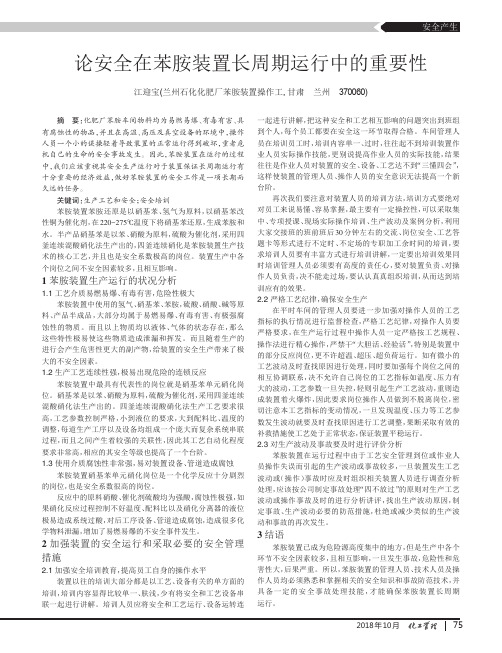
2018年10月论安全在苯胺装置长周期运行中的重要性江迎宝(兰州石化化肥厂苯胺装置操作工,甘肃兰州370060)摘要:化肥厂苯胺车间物料均为易燃易爆、有毒有害、具有腐蚀性的物品,并且在高温、高压及真空设备的环境中,操作人员一个小的误操轻着导致装置的正常运行得到破坏,重者危机自己的生命的安全事故发生。
因此,苯胺装置在运行的过程中,我们应该重视其安全生产运行对于装置保证长周期运行有十分重要的经济效益,做好苯胺装置的安全工作是一项长期而久远的任务。
关键词:生产工艺和安全;安全培训苯胺装置苯胺还原是以硝基苯、氢气为原料,以硝基苯改性铜为催化剂,在220-275℃温度下将硝基苯还原,生成苯胺和水。
半产品硝基苯是以苯、硝酸为原料,硫酸为催化剂,采用四釜连续混酸硝化法生产出的,四釜连续硝化是苯胺装置生产技术的核心工艺,并且也是安全系数极高的岗位。
装置生产中各个岗位之间不安全因素较多,且相互影响。
1苯胺装置生产运行的状况分析1.1工艺介质易燃易爆、有毒有害,危险性极大苯胺装置中使用的氢气、硝基苯、苯胺,硫酸、硝酸、碱等原料、产品半成品,大部分均属于易燃易爆、有毒有害、有极强腐蚀性的物质。
而且以上物质均以液体、气体的状态存在,那么这些特性极易使这些物质造成泄漏和挥发。
而且随着生产的进行会产生危害性更大的副产物,给装置的安全生产带来了极大的不安全因素。
1.2生产工艺连续性强,极易出现危险的连锁反应苯胺装置中最具有代表性的岗位就是硝基苯单元硝化岗位。
硝基苯是以苯、硝酸为原料,硫酸为催化剂,采用四釜连续混酸硝化法生产出的。
四釜连续混酸硝化法生产工艺要求很高,工艺参数控制严格,小到液位的要求,大到配料比、温度的调整,每道生产工序以及设备均组成一个庞大而复杂系统串联过程,而且之间产生着较强的关联性,因此其工艺自动化程度要求非常高,相应的其安全等级也提高了一个台阶。
1.3使用介质腐蚀性非常强,易对装置设备、管道造成腐蚀苯胺装置硝基苯单元硝化岗位是一个化学反应十分剧烈的岗位,也是安全系数很高的岗位。
苯胺装置工艺流程叙述

苯胺装置工艺流程叙述英文回答:The process flow of the aniline plant involves several steps. Firstly, the raw material for aniline production, benzene, is fed into the system. Benzene is a hydrocarbon compound that is obtained from crude oil or natural gas. It is a colorless liquid with a sweet aroma. In the aniline plant, benzene undergoes a series of chemical reactions to convert it into aniline.The next step in the process is the nitration of benzene. Nitric acid, which is a strong acid, is added tothe benzene to introduce a nitro group (-NO2) into the benzene ring. This reaction is carried out in the presenceof a catalyst, such as sulfuric acid. The nitration of benzene is an exothermic reaction, meaning it releases heat.After the nitration step, the mixture is subjected to a separation process. This involves separating the desiredproduct, nitrobenzene, from the reaction mixture. Several techniques can be used for separation, such as distillation or extraction. Distillation involves heating the mixture to vaporize the components with different boiling points and then condensing them back into liquid form. Extraction, on the other hand, utilizes a solvent to selectively dissolve the desired product.Once nitrobenzene is obtained, it undergoes a reduction reaction to convert it into aniline. Reduction is the process of adding hydrogen atoms to a molecule, and in this case, hydrogen gas is used as the reducing agent. The reduction reaction is typically carried out in the presence of a catalyst, such as iron or platinum. The hydrogen gas reacts with the nitro group in nitrobenzene, resulting in the formation of aniline.After the reduction step, the aniline is further purified to remove any impurities or by-products. This purification process can involve techniques such as distillation, crystallization, or filtration. The goal is to obtain pure aniline that meets the requiredspecifications for its intended use.Finally, the purified aniline is collected and packaged for distribution or further processing. Aniline is a versatile chemical compound that is used in various industries, such as the production of dyes, pharmaceuticals, and rubber processing.中文回答:苯胺装置的工艺流程涉及几个步骤。
MDI装置的简介
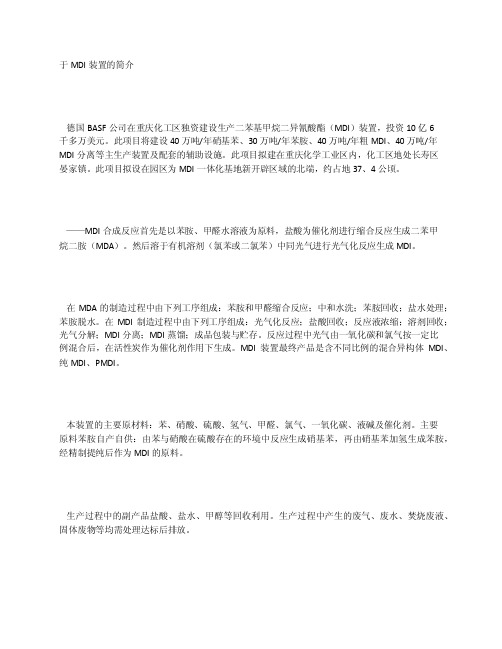
于MDI装置的简介德国BASF公司在重庆化工区独资建设生产二苯基甲烷二异氰酸酯(MDI)装置,投资10亿6千多万美元。
此项目将建设40万吨/年硝基苯、30万吨/年苯胺、40万吨/年粗MDI、40万吨/年MDI分离等主生产装置及配套的辅助设施。
此项目拟建在重庆化学工业区内,化工区地处长寿区晏家镇。
此项目拟设在园区为MDI一体化基地新开辟区域的北端,约占地37、4公顷。
——MDI合成反应首先是以苯胺、甲醛水溶液为原料,盐酸为催化剂进行缩合反应生成二苯甲烷二胺(MDA)。
然后溶于有机溶剂(氯苯或二氯苯)中同光气进行光气化反应生成MDI。
在MDA的制造过程中由下列工序组成:苯胺和甲醛缩合反应;中和水洗;苯胺回收;盐水处理;苯胺脱水。
在MDI制造过程中由下列工序组成:光气化反应;盐酸回收;反应液浓缩;溶剂回收;光气分解;MDI分离;MDI蒸馏;成品包装与贮存。
反应过程中光气由一氧化碳和氯气按一定比例混合后,在活性炭作为催化剂作用下生成。
MDI装置最终产品是含不同比例的混合异构体MDI、纯MDI、PMDI。
本装置的主要原材料:苯、硝酸、硫酸、氢气、甲醛、氯气、一氧化碳、液碱及催化剂。
主要原料苯胺自产自供:由苯与硝酸在硫酸存在的环境中反应生成硝基苯,再由硝基苯加氢生成苯胺,经精制提纯后作为MDI的原料。
生产过程中的副产品盐酸、盐水、甲醇等回收利用。
生产过程中产生的废气、废水、焚烧废液、固体废物等均需处理达标后排放。
MDI用于生产聚氨酯塑料、聚氨酯弹性体。
还可以用于制造合成纤维、人造革、无溶剂涂料等。
——MDI是高毒、高危、高风险项目。
为确保安全,在人口稠密处、在重要的水资源地附近、在环境容量有限地区、在地处工业、社会、经济、交通的重要密集区内是不宜布局建设此类项目的。
尤其在长江三峡库区上游布局这样大型的高危项目显然是不妥的。
异氰酸酯是具有刺激味道的有毒物质,易挥发的异氰酸酯还是强催泪剂。
异氰酸酯的蒸气一般通过呼吸道及皮肤进入人体,并极易与皮肤、呼吸器官各组织中的蛋白质引起皮炎、灼伤和过敏。
乙苯、苯乙烯装置简介和重点部位及设备.docx

乙苯、苯乙烯装置简介和重点部位及设备一、装置简介(一)装置发展及其类型1.装置发展自1937年美国陶氏化学公司和德国巴斯夫公司同时实现乙苯脱氢制苯乙烯的工业化生产以来,苯乙烯已有50多年的工业化生产历史。
苯乙烯是重要的有机化工原料。
它作为重要的合成单体与其他烯烃单体发生共聚反应,可生产丁苯橡胶、聚苯乙烯树脂、ABS和SAN树脂、离子交换树脂及不饱和聚酯树脂;此外还用于制药,染料行业,或制取农药乳化剂及选矿剂等。
苯乙烯的主要生产方法为乙苯脱氢法和环氧丙烷共氧化法,前者约占苯乙烯生产能力的90%,乙苯催化脱氢制苯乙烯的工艺有孟山都/鲁姆斯法、巴斯夫法、Fina/Badger法、Cdf法和三菱油化/环球化学法。
而共氧化法步骤多,流程长,又存在环氧丙烷的联产问题,因此国内外生产和研究重点多放在乙苯脱氢法上。
近年来许多公司研究用甲苯代替苯制苯乙烯的方法,如孟山都公司和三菱油化公司的甲苯—甲醇、甲苯—甲烷直接合成苯乙烯方法,是一种全新的工艺路线。
在1992年第10届国际催化剂会议的大会专题报告中,该工艺开发研究列为当代4大烃化技术之一,值得引起苯乙烯技术研究者的重视。
目前,我国苯乙烯生产方法多采用乙苯催化脱氢法。
60年代和70年代建设的小型装置能耗和物耗较高,缺少市场竞争能力,随着国外技术的引进,大部分已停产,剩下的几套经多次技术改造,能耗和物耗有所下降,同时,利用地区差价和本企业下游产品的需求仍维持生产。
2.苯乙烯的主要生产方法及特点目前,世界范围内苯乙烯生产的主要工艺有脱氢法和环氧丙烷法。
脱氢工艺包含Fina/Badger工艺和鲁姆斯/环球化学工艺。
一些生产苯乙烯的公司拥有自身的技术,如陶氏、巴斯夫,其他大部分生产商采用UnitedCatalysts(UCl)和Criterion的催化剂。
UCI占据了70%的脱氢催化剂市场份额,Criterion占20%,其他生产厂家占10%。
在乙苯脱氢制苯乙烯的工艺技术方面,除德国巴斯夫公司外,各家外商技术基本相同,大都是采用高真空绝热脱氢反应和反应热能回收技术,蒸馏都是真空高效填料塔技术(EB/SN分离塔),各项经济指标大体相同。
制苯装置简介和重点部位及设备
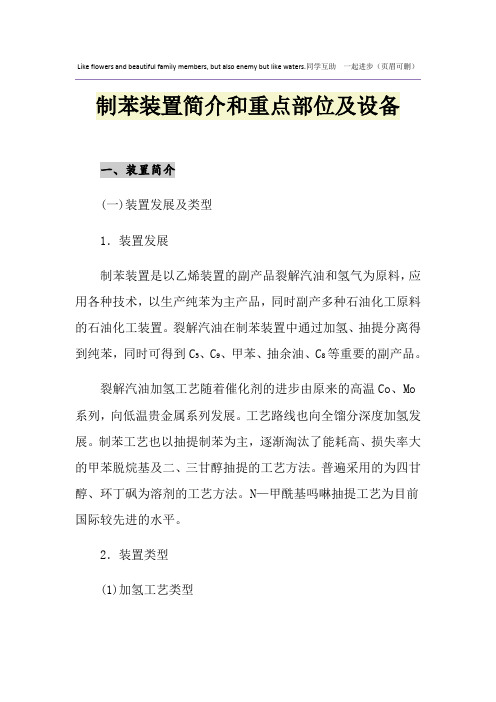
Like flowers and beautiful family members, but also enemy but like waters.同学互助一起进步(页眉可删)制苯装置简介和重点部位及设备一、装置简介(一)装置发展及类型1.装置发展制苯装置是以乙烯装置的副产品裂解汽油和氢气为原料,应用各种技术,以生产纯苯为主产品,同时副产多种石油化工原料的石油化工装置。
裂解汽油在制苯装置中通过加氢、抽提分离得到纯苯,同时可得到C5、C9、甲苯、抽余油、C8等重要的副产品。
裂解汽油加氢工艺随着催化剂的进步由原来的高温Co、Mo 系列,向低温贵金属系列发展。
工艺路线也向全馏分深度加氢发展。
制苯工艺也以抽提制苯为主,逐渐淘汰了能耗高、损失率大的甲苯脱烷基及二、三甘醇抽提的工艺方法。
普遍采用的为四甘醇、环丁砜为溶剂的工艺方法。
N—甲酰基吗啉抽提工艺为目前国际较先进的水平。
2.装置类型(1)加氢工艺类型裂解汽油中除含苯、甲苯、二甲苯外,还含有单烯烃、双烯烃、饱和烃(直链烷烃、环烷烃)以及含硫、氧、氮的有机化合物,根据色谱分析,有200多种组分,组成相当复杂。
这种油的特点为稳定性差,存放过程中易聚合生成低聚合度产物(即胶质),故在应用中必须先经过加氢工艺处理。
鉴于从裂解汽油中除去双烯烃、单烯烃和硫、氧、氮有机化合物的条件不同,国内外普遍采用两段加氢法。
一段加氢主要是双烯烃加氢;二段加氢主要是单烯烃加氢,同时将硫、氧、氮有机化合物加氢转变为相应的硫化氢、水和氨而被除去。
裂解汽油选择性加氢过程中催化剂起着关键性的作用,随着乙烯丙烯工业的飞速发展和裂解汽油加氢装置的不断增加,国内外对此类催化剂,尤其是一段加氢催化剂的研究开发和工业应用高度重视。
从催化剂类型分为两段高温加氢和一段低温二段高温加氢工艺。
从加工物料分为全馏分加氢和分馏加氢。
由油品的不同使用目的又可分为一段加氢和两段加氢。
加氢工艺类型比较如表3—12所示。
万吨苯胺装置
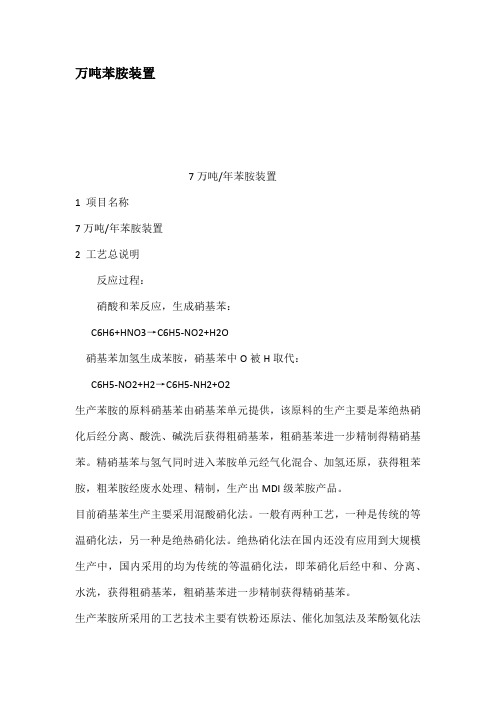
万吨苯胺装置7万吨/年苯胺装置1 项目名称7万吨/年苯胺装置2 工艺总说明反应过程:硝酸和苯反应,生成硝基苯:C6H6+HNO3→C6H5-NO2+H2O硝基苯加氢生成苯胺,硝基苯中O被H取代:C6H5-NO2+H2→C6H5-NH2+O2生产苯胺的原料硝基苯由硝基苯单元提供,该原料的生产主要是苯绝热硝化后经分离、酸洗、碱洗后获得粗硝基苯,粗硝基苯进一步精制得精硝基苯。
精硝基苯与氢气同时进入苯胺单元经气化混合、加氢还原,获得粗苯胺,粗苯胺经废水处理、精制,生产出MDI级苯胺产品。
目前硝基苯生产主要采用混酸硝化法。
一般有两种工艺,一种是传统的等温硝化法,另一种是绝热硝化法。
绝热硝化法在国内还没有应用到大规模生产中,国内采用的均为传统的等温硝化法,即苯硝化后经中和、分离、水洗,获得粗硝基苯,粗硝基苯进一步精制获得精硝基苯。
生产苯胺所采用的工艺技术主要有铁粉还原法、催化加氢法及苯酚氨化法等。
还原后的粗苯胺经进一步精制得到精苯胺。
2.1 硝化工艺技术路线a) 传统硝化法(等温硝化法)传统硝化法是将苯与用硫酸和硝酸配制的混酸在釜式硝化器(硝化锅)中进行硝化,所用硝化器一般为带有强力搅拌的耐酸铸铁或碳钢釜。
消化器内装有冷却蛇管,以导出硝化反应热。
硝基苯生产采用连续化生产工艺技术。
硝化时苯和混酸同时进料,硝化器串联操作,硝化温度控制在68~78℃。
因硝化反应是强放热反应,及时有效地排除热量,是硝化器设计的首要前提。
当反应体系温升过高会引起副反应,使硝基酚类副产物增加,而这些酚类副产物是造成硝基苯生产发生爆炸事故的主要原因。
因此硝化器应设有充分的搅拌和冷却装置,严格控制反应温度和搅拌效果。
为保证安全操作,需设有自控仪表及安全连锁系统。
在连续硝化生产工艺中,硝化器除釜式串联形式外,还有环形硝化器形式。
环形硝化器是将两个列管式硝化器串联,在一侧硝化器上用立式轴流泵进行强制循环,用冷却水移出反应热。
目前在国内,环形硝化器的生产能力均不大,还没有在大型的硝基苯生产装置上使用。
苯胺C6H7N检测仪

苯胺C6H7N检测仪苯胺C6H7N检测仪特点:★是款内置微型气体泵的安全便携装置★整机体积小,重量轻,防水,防爆,防震设计.★高精度,高分辨率,响应迅速快.★采用大容量可充电锂电池,可长时间连续工作.★数字LCD背光显示,声光、振动报警功能.★上、下限报警值可任意设定,自带零点和目标点校准功能,内置温度补偿,维护方便.★宽量程,最大数值可显示到50000ppm、100.00%Vol、100%LEL.★数据恢复功能,免去误操作引起的后顾之忧.★显示值放大倍数可以设置,重启恢复正常.★外壳采用特殊材质及工艺,不易磨损,易清洁,长时间使用光亮如新.苯胺C6H7N检测仪产品特性:★是款内置微型气体泵的高精度的手式安全便携装备;★进口电化学传感器具有良好的抗干扰性能,使用寿命长达3年;★采用先进微处理器技术,响应速度快,测量精度高,稳定性和重复性好;★检测现场具有现场声光报警功能,气体浓度超标即时报警,是危险现场作业的安全保障;★现场带背光大屏幕LCD显示,直观显示气体浓度/类型/单位/工作状态等;★全量程范围温度数字自动跟踪补偿,保证测量准确性;★半导体纳米工艺超低功耗32位微处量器;★全软件自动校准,传感器多达6级目标点校准功能,保证测量的准确性和线性,并且具有数据恢复功能;★全中文/英文操作菜单,简单实用,带温度补偿功能;★防高浓度气体冲击的自动保护功能;苯胺C6H7N检测仪技术参数:检测气体:空气中的苯胺C6H7N检测范围:0-100ppm、500ppm、1000ppm、5000ppm、0-100%LEL分辨率:0.1ppm、0.1%LEL显示方式:液晶显示温湿度:选配件,温度检测范围:-40~120℃,湿度检测范围:0-100%RH检测方式:扩散式、流通式、泵吸式可选安装方式:壁挂式、管道式检测精度:≤±3%线性误差:≤±1%响应时间:≤20秒(T90)零点漂移:≤±1%(F.S/年)恢复时间:≤20秒重复性:≤±1%信号输出:①4-20mA信号:标准的16位精度4-20mA输出芯片,传输距离1Km②RS485信号:采用标准MODBUS RTU协议,传输距离2Km③电压信号:0-5V、0-10V输出,可自行设置④脉冲信号:又称频率信号,频率范围可调(选配)⑤开关量信号:标配2组继电器,可选第三组继电器,继电器无源触点,容量220VAC3A/24VDC3A传输方式:①电缆传输:3芯、4芯电缆线,远距离传输(1-2公里)②GPRS传输:可内置GPRS模块,实时远程传输数据,不受距离限制(选配)接收设备:用户电脑、控制报警器、PLC、DCS、等报警方式:现场声光报警、外置报警器、远程控制器报警、电脑数据采集软件报警等报警设置:标准配置两级报警,可选三级报警;可设置报警方式:常规高低报警、区间控制报警电器接口:3/4″NPT内螺纹、1/2″NPT内螺纹,同时支持2种电器连接方式防爆标志:ExdII CT6(隔爆型)壳体材料:压铸铝+喷砂氧化/氟碳漆,防爆防腐蚀防护等级:IP66工作温度:-30~60℃工作电源:24VDC(12~30VDC)工作湿度:≤95%RH,无冷凝尺寸重量:183×143×107mm(L×W×H)1.5Kg(仪器净重)工作压力:0~100Kpa标准配件:说明书、合格证质保期:一年苯胺C6H7N检测仪简单介绍:苯胺C6H7N检测仪报警器高精度、高分辨率,响应快速,超大容量锂电充电电池,采样距离远,LCD背光显示,声光报警功能,上、下限报警值可任意设定,可进行零点和任意目标点校准,操作简单,具有误操作数据恢复功能.苯胺C6H7N检测仪应用场所:医药科研、学校科研、制药生产车间、烟草公司、环境检测、楼宇建设、消防报警、污水处理、石油石化、化工厂、冶炼厂、钢铁厂、煤炭厂、热电厂、锅炉房、加气站、垃圾处理厂、隧道施工、输油管道、航空航天、工业气体过程控制、室内空气质量检测、地下燃气管道检修、危险场所安全防护、军用设备检测等。
- 1、下载文档前请自行甄别文档内容的完整性,平台不提供额外的编辑、内容补充、找答案等附加服务。
- 2、"仅部分预览"的文档,不可在线预览部分如存在完整性等问题,可反馈申请退款(可完整预览的文档不适用该条件!)。
- 3、如文档侵犯您的权益,请联系客服反馈,我们会尽快为您处理(人工客服工作时间:9:00-18:30)。
7万吨/年苯胺装置1 项目名称7万吨/年苯胺装置2 工艺总说明反应过程:硝酸和苯反应,生成硝基苯:C6H6+HNO3→C6H5-NO2+H2O硝基苯加氢生成苯胺,硝基苯中O被H取代:C6H5-NO2+H2→C6H5-NH2+O2生产苯胺的原料硝基苯由硝基苯单元提供,该原料的生产主要是苯绝热硝化后经分离、酸洗、碱洗后获得粗硝基苯,粗硝基苯进一步精制得精硝基苯。
精硝基苯与氢气同时进入苯胺单元经气化混合、加氢还原,获得粗苯胺,粗苯胺经废水处理、精制,生产出MDI级苯胺产品。
目前硝基苯生产主要采用混酸硝化法。
一般有两种工艺,一种是传统的等温硝化法,另一种是绝热硝化法。
绝热硝化法在国内还没有应用到大规模生产中,国内采用的均为传统的等温硝化法,即苯硝化后经中和、分离、水洗,获得粗硝基苯,粗硝基苯进一步精制获得精硝基苯。
生产苯胺所采用的工艺技术主要有铁粉还原法、催化加氢法及苯酚氨化法等。
还原后的粗苯胺经进一步精制得到精苯胺。
2.1 硝化工艺技术路线a) 传统硝化法(等温硝化法)传统硝化法是将苯与用硫酸和硝酸配制的混酸在釜式硝化器(硝化锅)中进行硝化,所用硝化器一般为带有强力搅拌的耐酸铸铁或碳钢釜。
消化器内装有冷却蛇管,以导出硝化反应热。
硝基苯生产采用连续化生产工艺技术。
硝化时苯和混酸同时进料,硝化器串联操作,硝化温度控制在68~78℃。
因硝化反应是强放热反应,及时有效地排除热量,是硝化器设计的首要前提。
当反应体系温升过高会引起副反应,使硝基酚类副产物增加,而这些酚类副产物是造成硝基苯生产发生爆炸事故的主要原因。
因此硝化器应设有充分的搅拌和冷却装置,严格控制反应温度和搅拌效果。
为保证安全操作,需设有自控仪表及安全连锁系统。
在连续硝化生产工艺中,硝化器除釜式串联形式外,还有环形硝化器形式。
环形硝化器是将两个列管式硝化器串联,在一侧硝化器上用立式轴流泵进行强制循环,用冷却水移出反应热。
目前在国内,环形硝化器的生产能力均不大,还没有在大型的硝基苯生产装置上使用。
釜式串联形式的硝化器目前在国内应用比较广泛,目前吉林石化分公司现有装置的硝化反应器即为四釜串联形式的传统的等温硝化反应器,其单线生产能力可达到10万吨/年硝基苯。
b) 绝热硝化法德国PLINKE公司的绝热硝化工艺有三个主要阶段:硝化、废酸浓缩、产品分离。
其反应过程是将过量的苯预热到100℃后与混酸一同加到硝化器中,在一定压力下进行反应。
由于反应产生大量的热,物料的出口温度在120~140℃之间。
反应物经分离后,分出的废酸进入闪蒸器,利用本身热量将废酸浓度提高到70%,与60%的硝酸混合后循环使用。
有机相经酸洗、碱洗、水洗及分离后,得粗硝基苯。
粗硝基苯经气提后,蒸出未反应的过量苯,可得到精硝基苯。
c) 传统硝化法和绝热硝化法的比较绝热硝化与传统硝化方法相比,存在着重要的差别即:用稀硝酸替代浓硝酸,增加了混酸中水的含量;取消硝化器中的冷却装置,在压力下完成硝化反应。
采用绝热硝化法具有以下特点:(1)由于取消冷却装置,减少了水的消耗;(2)利用反应热在真空闪蒸器中进行废酸的浓缩,取消了传统硝化法的废酸浓缩过程,与传统硝化法比既节省了90%左右的能源,又减少了很多昂贵的设备投资;(3)硝化反应是在封闭系统和压力下进行的,可以避免苯的挥发;(4)苯经气提、冷凝、分层后回收循环使用,减少了苯的损失。
分出的水用于硝化的水洗,节省了水资源。
(5)废气中的氮氧化物和微量苯均经处理后排放,污染物排放较少,有利于环境保护和降低原料的消耗定额;(6)硝化时采用过量苯和高含水量的混酸,既避免了副反应的发生,又提高产品质量、收率,降低了成本。
传统硝化法和绝热硝化法各有优缺点,具体工艺条件及消耗定额比较列于表2.1及表2.2。
表2.1 绝热硝化法与传统硝化法消耗定额比较(以吨硝基苯计)表2.2 绝热硝化法与传统硝化法工艺条件的比较a) 硝基苯铁粉还原法此法生产工艺大都采用间歇法生产。
将苯胺废水和部分铁粉与盐酸投入还原锅中,用直接蒸汽加热,经一段时间后分批加入硝基苯和铁粉,反应直至回流冷凝物无硝基苯为止。
产物经蒸馏,获得粗苯胺,再经精馏获得成品,铁泥经处理后排放。
此法目前只有一些中小厂还在使用。
b) 硝基苯催化加氢还原法硝基苯催化加氢分为气相法和液相法,但工业生产多采用气相法。
液相法工业化的较少。
硝基苯气相催化加氢所用的反应器有流化床和固定床两种。
国外70年代以后建设的装置以固定床或固定床和流化床相串联的反应器为主,有代表性的是日本住友的固定床生产工艺。
其工艺是将新鲜氢和循环氢一起送至预热器中预热,预热器内保持一定压力。
经预热的氢和硝基苯进入蒸发器,调整配料比后进入反应器。
反应产物与进料氢换热,经冷凝、分离获得粗苯,粗苯胺进入脱水塔脱水,再经精馏塔脱除高沸物,由塔上部出成品苯胺。
固定床反应器为列管式,管内装铜-铬催化剂,必要时可掺入瓷环。
管间用载热体带出反应热,该热量用于付产蒸汽。
国内装置大多采用流化床加氢工艺。
流化床反应器设有气体分布器,硝基苯经汽化后与氢气混合,经分布器进入反应器。
反应器内装有铜-硅胶催化剂,床层内设冷却管。
为防止气体夹带催化剂,流化床内设有气固分离结构。
反应后的气体产物经冷凝去分离器,氢气去循环压缩机;粗苯胺再进入苯胺精制系统,获得成品苯胺。
2.3 苯胺废水回收技术的选择目前国内及吉林石化分公司现有的7万吨/年苯胺装置的苯胺废水回收均采用精馏方式回收其中的苯胺。
废水中苯胺的含量占3.5%-4.5%,由于大量水的存在,采用精馏工艺回收苯胺,其蒸汽消耗量较高,为此,吉林石化分公司研究院自行研究开发了用硝基苯萃取废水中苯胺的工艺技术。
此工艺是经过三级萃取、分离后,废水中的苯胺与精硝基苯一并去加氢还原,分离后的废水中苯胺含量小于50ppm。
2.4 苯胺的用途:80年代中期以前,橡胶助剂、医药及染料工业是苯胺三大传统消费领域。
1988年以后,聚氨酯塑料工业快速发展,MDI的需求急剧增长,需要MDI级苯胺。
在苯胺的下游产品中,环己胺、香兰素、对苯二酚、橡胶助剂等产品。
在染料行业中,还原靛蓝和色酚AS两个染料品种。
在医药工业中,以苯胺为原料生产的药品主要有两大类,一种是磺胺类抗菌药,另一种是安替比林类镇痛药。
苯胺在农药中主要用做生产水田除草剂丁草胺的中间体2,6-二乙基苯胺的主要原料。
用于生产炸药稳定剂的二苯胺,生产香兰素的N,N-二甲基苯胺,生产橡胶防老剂、染料中间体及感光材料的对苯二酚等。
3 装置构成和工艺流程3.1 装置组成装置由工艺生产装置(硝基苯单元、苯胺单元)、储运设施(化苯库、硝酸罐区、成品库及铁路)、辅助设施(综合楼、冷冻站、循环水站、空压站)、公用工程等组成3.2工艺流程说明苯胺的生产工艺分为硝基苯单元和苯胺单元。
3.2.1 硝基苯单元a) 反应工序在硝基苯单元中,硝化部分采用的是苯绝热硝化工艺技术。
由罐区苯贮罐来的石油苯沿外管架送入苯中间罐,经输送泵打入硝化器中,与泵打入的混酸进行绝热硝化反应,反应后的反应液进入分离罐,分离出的酸性硝基苯经冷却后去精制工序,废酸进入蒸发器利用自身带的热量进行废酸浓缩。
浓缩后的废酸浓度可达70%,再循环使用。
浓缩过程中产生的废气进入精制工序的苯回收塔进一步回收。
b) 精制工序自硝化分离器来的酸性硝基苯流入酸洗槽中,用废酸浓缩分离出的废水进行洗涤,洗涤后的酸性废水排掉,酸性硝基苯再进入碱洗槽中进行碱洗,碱洗后的碱性废水排掉,硝基苯进入水洗槽中进行水洗,水洗后的废水循环使用。
水洗至中性的硝基苯进入苯提取塔,在真空的条件下将苯从塔顶蒸出,进入苯水分层器,经分层器将苯、水分离,水做硝基苯的洗水用,苯回反应工序循环使用。
分层器出来的气体与废酸浓缩过程产生的废气一并进入苯回收塔,用精硝基苯回收苯,其它不凝气去尾气处理工。
提取塔塔釜得合格的精硝基苯,做为苯胺单元的原料。
c) 尾气处理工序来自硝化反应的尾气经压缩机升压后进入氮氧化物气体吸收塔,被用泵送来的脱盐水吸收成稀硝酸,在吸收过程中,吸收塔用冷却水冷却,塔顶未被吸收的不凝气经升压后进入催化氧化器内处理,处理合格后排入大气。
塔釜的稀硝酸浓度达到50%-55%后被送至反应工序循环使用。
废酸循环泵图4.2-1硝化及废酸浓缩流程示意图废气鼓风机图4.2-2硝基苯精馏流程示意图z放空排大气图4.2-3尾气处理工艺流程示意图3.2.2 苯胺单元a) 加氢还原工序来自氢气球罐的新鲜氢气与氢压机升压的循环氢在氢气缓冲罐混合之后进入氢气第一、第二换热器,在此与来自流化床的反应后气体进行两次热交换,进入硝基苯汽化器和混合气体加热器。
硝基苯在汽化器被热氢气流所汽化,混合气体继续升温至190℃,送入流化床内,硝基苯在此进行气相催化加氢反应,反应在245~295℃进行。
加氢反应所放出的热量被汽包送入流化床内换热管的软水带出。
水被汽化副产1.0MPa(G)蒸汽,该蒸汽量除满足装置需用量外,剩余部分送入装置外的蒸汽管网。
流化床反应器的气体经第二氢气换热器和第一氢气换热器,被由氢气缓冲罐来的混合氢气在换热器中进行间接冷却至120℃后,进入第一、二冷凝器,苯胺与水被冷凝为液体。
在触媒沉降槽中除去液体中的触媒颗粒,再经冷却器冷却至30℃后流入苯胺-水分层器静止分层。
未被冷凝的反应气体经捕集器后回收,含氢气90%(v)的气体作为循环氢使用。
从冷凝器出来的循环氢压力为3.92~6.86kPa(G),经捕集器进行两次捕集,再经管式除尘器过滤后,气体进入氢压机升压至160kPa(G),与新氢在氢气缓冲罐混合。
由硝基苯精制工序制取的纯度为99.94%硝基苯,由泵送入加热器升温至170~180℃后,进入硝基苯汽化器。
从分层器上部流出来的水(含苯胺 3.6%)进入苯胺水储槽,从分层器下部流出的粗苯胺(含水5%),储存于粗苯胺储槽内,去苯胺单元精馏工序。
流化床所用冷却水系中压膨胀槽和低压膨胀槽蒸汽冷凝后产生的105℃的冷凝水,由热水给水泵送至汽包后,利用热水循环泵打入流化床换热管内。
b) 苯胺废水处理工序苯胺废水罐内的废水用泵以一定流量送入一级萃取的静态混合器内,同时用泵打入萃取剂精硝基苯,在静态混合器中进行液-液传质后,进入分层器中进行分层,上层萃余相进入贮罐,作为下一级萃取的萃取剂,下层的物料去加氢还原单元,作为加氢原料。
经三级萃取后,废水中苯胺浓度将在50ppm以下,排入下水。
c) 苯胺精馏工序粗苯胺罐内的粗苯胺用粗苯胺泵以一定流量输送到脱水塔内,控制脱水塔顶温、釜温和塔顶压力,进行精馏,塔顶蒸出物经共沸物冷凝器冷凝后流入苯胺水分层器内进行分层,塔釜高沸物进入精馏塔内。
在一定的顶温、釜温及真空下进行精馏,塔顶蒸出物(苯胺)经精馏塔冷凝器冷凝后,一部分以一定的回流比从塔顶送入精馏塔内作为回流,其余再经冷凝器进一步冷凝后进入苯胺成品罐。