第六章 压缩模设计
6.压缩模具设计.

第六章压缩模具设计第一节压缩模的结构组成及类型一、压塑模具的基本结构典型的压缩模具结构如图6-1所示,它可分为固定于压力机上工作台的上模和下工作台的下模两大部分,两大部分靠导柱导向开合。
其工作原理为加料前先将侧型芯复位,加料合模后,热固性塑料在加料腔和型腔中受热受压,成为熔融状态而充满型腔,固化成型后开模。
开模时,上工作台上移,上凸模3脱离下模一段距离,侧型芯18用手工将其抽出,下液压缸工作,推板15推动推杆11将塑件1推出模外。
侧型芯复位后加料,接着又开始下一个压缩成型循环。
一般根据模具中各零件所起的作用,可将压缩模具细分为以下几个基本组成部分。
1.型腔型腔是直接成型制品的部位,加料时与加料腔一同起装料作用。
图6-1中的模具型腔由上凸模3、下凸模8、型芯7和凹模4等组成。
2.加料腔图6—1中指凹模4的上半部,图中为凹模断面尺寸扩大的部分,由于塑料与塑件相比具有较大的比容,塑件成型前单靠型腔往往无法容纳全部原料,因此在型腔之上设有一段加料腔。
3.导向机构图6—1中由布置在模具上周边的四根导柱6和导套9组成。
导向机构用来保证上下模合模的对中性。
为了保证推出机构上下运动平稳,该模具在下模座板14上设有两根推板导柱,在推板上还设有推板导套。
4.侧向分型抽芯机构在成型带有侧向凹凸或侧孔的塑件时,模具必须设有各种侧向分型抽芯机构,塑件方能脱出,图6—1中的塑件有一侧孔,在推出之前用手动丝杠抽出侧型芯18。
5.脱模机构固定式压缩模在模具上必须有脱模机构,图6—1中的脱模机构由推板15、推杆固定板17、推杆11等零件组成。
6.加热系统热固性塑料压塑成型需在较高的温度下进行,因此模具必须加热。
图6-1中加热板5、10的圆孔中插入电加热棒分别对上凸模、下凸模和凹模加热。
在压缩成型热塑性塑料时,在型腔周围开设温度控制通道,在塑化和定型阶段,分别通入蒸汽进行加热或通入冷水进行冷却。
图6—1 压缩模结构1—上模座板;2—螺钉;3—上凸模;4—加料腔(凹模);5、10—加热板;6—导柱;7—型芯;8—下凸模;9—导套;11—推杆;12—支承钉;13—垫块;14—下模座板;15—推板;16—拉杆;17—推杆固定板;18—侧型芯;19—型腔固定板;20—承压板二、压缩模具类型压缩模的分类方法很多,可按分型面特征分类,可按模具在液压机上的固定方式分类,也可按模具加料室的形式进行分类。
第六章 压缩模设计.

首先应确定型腔的总体结构、凹模和凸模之间的 配合形式以及成型零件的结构;
根据塑件尺寸确定型腔成型尺寸; 根据塑件重量和塑料品种确定加料腔尺寸; 根据型腔结构和尺寸、压缩成型压力大小确定型 腔壁厚等。 一、塑件在模具内加压方向的选择
所谓加压方向即凸模作用方向。加压方向对塑件 的质量、模具的结构和脱模的难易部有重要的影响, 在决定施压方向时要考虑下述因素:
适用范围:
小批量或试制、低精度和强度无严格要求的的扁
平塑件。
2.不溢式压缩模
结构特点:
加料腔是型腔向上的延续部分
又称封闭式压缩模
无挤压面
凸模与加料腔有小间隙的配合
优点:
塑件密度大、质量高 对塑料要求不严(以棉布、玻璃 布或长纤维填料的塑料均可) 塑件飞边薄且呈垂直状易于去除
缺点:
加料量必须精确,高度尺寸难于保证;
2、半固定式压缩模 开合模在机内进行,一般将上模固定在压力机上,下模可沿 导轨移动,用定位块定位,合模时靠导向机构定位。也可按 需要采用下模固定的形式,工作时则移出上模,用手工取件 或卸模架取件。 特点:该结构便于放嵌件和加料,适用于小批量生产,可减 小劳动强度。
3、固定式压缩模
上下模都固定在压力机上,开模、合模、脱模等工序均在压 力机内进行。 特点:生产效率高,操作简单,劳动强度小,开模振动小, 模具寿命长,但结构复杂,成本高,且安放嵌件不方便。适 用于成形批量较大或形状较大的塑件。
六、顶出机构的校核
压力机最大顶出行程应大于模具所
需的推出行程,且必须保证塑件推
出型腔后高于型腔表面10mm以上。
l = h塑+h加+(10~15)≤L
其中:
l——塑件需推出的高度 h塑——塑件最大高度
塑料成型工艺与模具设计概述

2. 收缩性
塑料在成型及冷却过程中发生的体积收缩性 质称为收缩性,塑料在熔融状态下的体积总比 其固态下的体积大。
影响塑料收缩性的因素有:塑料的组成及结 构、成型工艺方法、工艺条件、塑件几何形状 及金属镶件的数量、模具结构及浇口形状与尺 寸等。
三、塑料特性与应用 (一)热塑性塑料
热塑性塑料
主要性能
酸性
主要应用
PE聚乙烯
耐化学腐蚀、电绝 缘、吸水性小
小载荷齿轮、容器、轴承、阀件、 涂层、化工管道
PP聚丙烯
密度最小、耐腐蚀、 吸水性小、耐热
PVC聚氯乙烯 PS聚苯乙烯
耐腐蚀、电绝缘、 耐燃
电绝缘、透光、吸 湿低、硬度高、易
燃
ABS丙烯腈-丁 二烯-苯乙烯
(1)热收缩 (2)结构变化引起的收缩 (3)弹性恢复 (4)塑性变形
影响热固性塑料收缩率的原因还有:原材料、 模具结构、成型方法及成型工艺条件等。
2.流动性
热固性塑料的流动 性通常以拉西格流动性 来表示。
影响热固性塑料流 动性的主要因素有: (1)塑料原料 (2)模具及工艺条件的 影响
3.水分及挥发物含量 一是来自生产、运输和储存,二是来自化
安全在于心细,事故出在麻痹。20.10.2020.10.2017: 02:0517:02:05October 20, 2020
踏实肯干,努力奋斗。2020年10月20 日下午5 时2分2 0.10.20 20.10.2 0
追求至善凭技术开拓市场,凭管理增 创效益 ,凭服 务树立 形象。2020年10月20日星期 二下午5时2分5秒17:02:0520.10.20
模具设计与制造(压缩模)

3.4 压缩模设计压缩成型模具简称压缩模、压模,又称压制模,是塑料压缩成型所采用的模具,主要用于热固性塑料的成型。
其基本成型过程是将塑料粉料或粒料直接加在敞开的模具加料室内,再将模具闭合,通过加热、加压使塑料呈流动状态并充满型腔,然后由于化学或物理变化使塑料固化(或硬化)定型。
压缩成型的特点是塑料直接加入型腔内,压机压力通过凸模直接传递给塑料,模具是在塑料最终成型时才完成闭合。
其优点是无需设置浇注系统,耗料少,使用的设备和模具都比较简单,适用于流动性差的塑料,宜成型大型塑件,塑料的收缩率小,变形小,各向异性比较均匀;其缺点是生产周期长,效率低,不易压制形状复杂、壁厚相差较大、尺寸精度高且带有精细或易碎嵌件的塑件。
3.4.1 压缩模的结构组成及分类1.压缩模的结构组成压缩模的典型结构如图3-96所示。
模具的上模和下模分别安装在压力机的上、下工作台上,上、下模通过导柱导套导向定位。
上工作台下降,使上凸模3进入下模加料室4与装入的塑料接触并对其加热。
当塑料成为熔融状态后,上工作台继续下降,熔料在受热受压的作用下充满型腔。
塑件固化(或硬化)成型后,上工作台上升,模具分型,同时压机下面的辅助液压缸开始工作,脱模机构将塑件脱出。
压缩模按各零部件的功能作用可分为以下几大部分。
(1)成型零件成型零件是直接成型塑件的零件,加料时与加料室一同起装料的作用,模具闭合时形成所要求的型腔。
图3-96中模具型腔由上凸模3、凹模4、型芯8、下凸模9等构成。
(2)加料室图3-96中凹模4的上半部,为凹模截面尺寸扩大的部分。
由于塑料与塑件相比具有较大的比容,塑件成型前单靠型腔往往无法容纳全部原料,因此一般需要在型腔之上设有一段加料腔室。
(3)导向机构导向机构的作用是保证上模和下模两大部分或模具内部其他零部件之间准确对合。
图3-96中,由布置在模具上周边的四根导柱6和导套10组成导向机构,为保证推出机构上下运动平稳,该模具在下模座板15上设有两根推板导柱,在推板上还设有推板导套。
第6章 塑料压缩模具
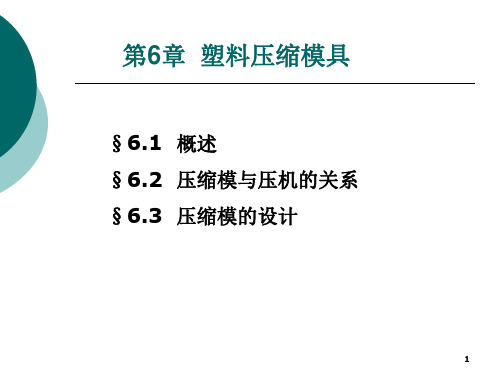
人力来拖动的。此外还有双曲柄杠杆式压机等,机械式压机的压力不
准确,运动噪声大,容易磨损,特别是用人力驱动的手扳压机,劳动
强度很大,现在在工厂中已极少采用。
液压机是热固性塑料压缩成型的主要设备,按其结构可分为上压
式液压机和下压式液压机。
下一页
15
§ 6.2 压缩模与压机的关系
用于生产塑料制品的多为下工作台固定不动的上压式液压机,因为这 种设备使用起来比下压式方便。
§6.1 概述
为了保证推出机构上下运动平稳,该模具在下模座板16上设有两根 推板导柱14,在推板17和推杆固定板19上还设有推板导套15
4.侧向分型抽芯机构 在成型带有侧向凹凸或侧孔的塑件时,模具必须设有各种侧向分 型抽芯机构,塑料制品才能脱出。图6-7中的塑料制品带有一侧孔, 在该模具结构中使用手动丝杆带动侧型芯20来完成侧向抽芯和复位。 5.脱模机构 固定式压缩模在模具上必须有脱模机构(推出机构)。图6-7中的 脱模机构由推杆11、推板17、推杆固定板19、压机顶杆18等零件 组成。
(3)不溢式压缩模。不溢式压缩模如图6-6所示。该模具的加料腔 是型腔上部截面的延续,凸模与加料腔有较高精度的间隙配合,故塑 料制品的径向壁厚尺寸的精度较高。理论上讲压机所施加的压力将全 部作用在制品上,塑料的溢出量很少,制品在垂直方向上可能形成很 薄的飞边。
上一页 下一页
8
§6.1 概述
凸模与凹模的配合高度不宜过大,不配合部分可以如图6-6中所示将 凸模上部截面尺寸减小,也可将凹模对应部分尺寸逐渐增大形成锥面 (15‘~20’)。
工人劳动强度大,所以模具的质量不宜太大,以不超过20kg为宜。 该类压缩模适用于压制成型批量不大的中小型塑料制品以及形状复杂、 嵌件较多、加料困难、带螺纹的塑料制品。
压缩模具.

加料量应超出制品重量的5%以内,原料有一定浪费;
有时可不设脱模机构,而由手工取出或用压缩空气吹出制品。
优点:
无加料室,便于嵌件的安放;
结构简单,价廉耐用; 特别适合成型扁平小型薄壁制品(如钮 扣、装饰品及各种小零件)。
西安航空技术高等专科学校
机械工程系
任务五
2、不溢式压缩模
不溢式压模缺点:
西安航空技术高等专科学校 机械工程系
任务五
压缩成型优点:
压缩模具
与注射相比,使用的设备和模具较为简单价廉; 适用于流动性差的塑料,较易成型大中型制品; 适宜成型热固性塑料制品,制品收缩率较小、变形小、各向性能较均匀。
压缩成型缺点:
与注射相比,生产周期长,效率低,厚壁件生产周期更长; 生产自动化程度低,粉尘多,环境条件差,劳动强度大;
3、半溢式压缩模
压缩模具
半溢式压模特点:
型腔上方设有断面尺寸较大的加料室(可 简化断面形状),加料室底部有环形挤压 面(约4~5mm),型芯与加料室间隙配合; 余料可通过配合间隙和溢料槽溢出,制品 密度较溢式压模的好; 操作方便,原料计量简单,制品尺寸由型 腔决定; 制品脱模容易,不易与侧壁刮擦; 不适宜成型以布片或长纤维作填料的塑料;
挤压面每次应清理干净,以免变形和破坏。
西安航空技术高等专科学校
机械工程系
任务五
半溢式压模改进:
压缩模具
将加料腔制成可移动式,方便挤压面和模具型腔的清理。
西安航空技术高等专科学校
机械工程系
任务五
4、多型腔压缩模
压缩模具
多型腔压模:可为溢式或半溢式结构,图a)、b)需对每 个型腔单独加料,个别型腔损坏不影响模具工作。
机械工程系
工程类压缩成型工艺及模具设计

汇报人:XX
目录
添加目录标题
压缩成型工艺概述
压缩成型工艺流程
模具设计基础
模具设计实例分析
压缩成型工艺及模具 设计的未来发展
添加章节标题
压缩成型工艺概述
压缩成型工艺的定义: 将塑料原料置于模具型 腔中,通过加热和加压 的方式使原料熔化并流 动,最终冷却固化形成 所需形状的塑料制品的 工艺过程。
实例特点:适用于中小型塑件 生产,具有高效、灵活等优点
实例效果:提高生产效率,降 低生产成本,保证产品质量
压铸模具设计原 理
压铸模具结构设 计
压铸模具材料选 择
压铸模具制造工 艺流程
挤出模具设计原理:利用螺杆旋转 产生的压力,将塑料熔体从模具口 挤出,形成所需的形状和尺寸。
挤出模具设计流程:根据产品要求进 行模具设计,选择合适的材料和热塑 性塑料,进行模具制造、试模、调整 和生产。
模具材料:钢材、硬质合 金等
热处理:淬火、回火、表 面处理等
材料选择依据:模具工作 条件、生产批量等
热处理工艺:温度、时间、 冷却方式等
确定设计任务和要求
进行模具总体方案设计
绘制模具总装配图
绘制模具零件图
模具设计实例分析
模具类型:注塑模具
设计流程:分析产品、确定模 具结构、设计分型面、浇注系 统等
试模目的:验证 模具设计的正确 性和可行性
试模过程:在生 产线上进行小批 量试制,观察产 品成型效果
问题分析与调整: 针对试模过程中 出现的问题,进 行模具结构、材 料等方面的调整
优化与改进:根 据试模结果,对 模具进行优化和 改进,提高生产 效率和产品质量
压缩成型工艺流程: 包括塑料原料、模 具设计、成型工艺、 冷却定型等环节
《塑料成型工艺及模具设计》习题与答案
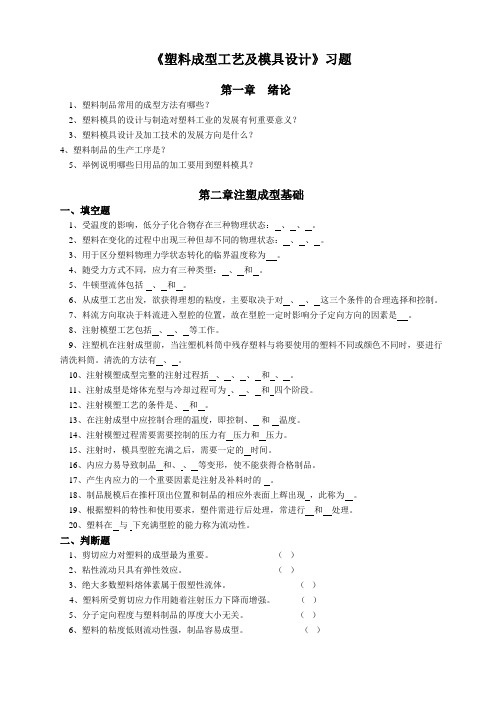
《塑料成型工艺及模具设计》习题第一章绪论1、塑料制品常用的成型方法有哪些?2、塑料模具的设计与制造对塑料工业的发展有何重要意义?3、塑料模具设计及加工技术的发展方向是什么?4、塑料制品的生产工序是?5、举例说明哪些日用品的加工要用到塑料模具?第二章注塑成型基础一、填空题1、受温度的影响,低分子化合物存在三种物理状态:、、。
2、塑料在变化的过程中出现三种但却不同的物理状态:、、。
3、用于区分塑料物理力学状态转化的临界温度称为。
4、随受力方式不同,应力有三种类型:、和。
5、牛顿型流体包括、和。
6、从成型工艺出发,欲获得理想的粘度,主要取决于对、、这三个条件的合理选择和控制。
7、料流方向取决于料流进入型腔的位置,故在型腔一定时影响分子定向方向的因素是。
8、注射模塑工艺包括、、等工作。
9、注塑机在注射成型前,当注塑机料筒中残存塑料与将要使用的塑料不同或颜色不同时,要进行清洗料筒。
清洗的方法有、。
10、注射模塑成型完整的注射过程括、、、和、。
11、注射成型是熔体充型与冷却过程可为、、和四个阶段。
12、注射模塑工艺的条件是、和。
13、在注射成型中应控制合理的温度,即控制、和温度。
14、注射模塑过程需要需要控制的压力有压力和压力。
15、注射时,模具型腔充满之后,需要一定的时间。
16、内应力易导致制品和、、等变形,使不能获得合格制品。
17、产生内应力的一个重要因素是注射及补料时的。
18、制品脱模后在推杆顶出位置和制品的相应外表面上辉出现,此称为。
19、根据塑料的特性和使用要求,塑件需进行后处理,常进行和处理。
20、塑料在与下充满型腔的能力称为流动性。
二、判断题1、剪切应力对塑料的成型最为重要。
()2、粘性流动只具有弹性效应。
()3、绝大多数塑料熔体素属于假塑性流体。
()4、塑料所受剪切应力作用随着注射压力下降而增强。
()5、分子定向程度与塑料制品的厚度大小无关。
()6、塑料的粘度低则流动性强,制品容易成型。
()7、结晶型塑料比无定型塑料的收缩率小,增加塑料比未增加塑料的收缩大。
- 1、下载文档前请自行甄别文档内容的完整性,平台不提供额外的编辑、内容补充、找答案等附加服务。
- 2、"仅部分预览"的文档,不可在线预览部分如存在完整性等问题,可反馈申请退款(可完整预览的文档不适用该条件!)。
- 3、如文档侵犯您的权益,请联系客服反馈,我们会尽快为您处理(人工客服工作时间:9:00-18:30)。
凸模与加料腔内壁有摩擦,易划伤加料腔内部,进而 影响塑件外观质量;
模具必须设置推出机构; 一般为单型腔,生产效率低。
适用范围:
压制形状复杂,薄壁及深形塑件。
3.半溢式压缩模
结构特点:
加料腔是型腔向上的扩大延续部分 又称半封闭式压缩模 有挤压面
优点:
不必严格控制加料量
不会伤及凹模侧壁 塑件外形复杂时,凸模和加料
首先应确定型腔的总体结构、凹模和凸模之间的 配合形式以及成型零件的结构;
根据塑件尺寸确定型腔成型尺寸; 根据塑件重量和塑料品种确定加料腔尺寸; 根据型腔结构和尺寸、压缩成型压力大小确定型 腔壁厚等。 一、塑件在模具内加压方向的选择
所谓加压方向即凸模作用方向。加压方向对塑件 的质量、模具的结构和脱模的难易部有重要的影响, 在决定施压方向时要考虑下述因素:
(三)计算加料腔的高度
H---加料室高度(mm); Vj---挤压边以下型腔体积(mm3); ∑Vd---下凸模成型部分的体积之和(mm3); A---加料室截面积
例 有一塑件如下图所示,物料密度为1.4g/cm3,压 缩比为3,飞边重量按塑件净重的10%计算,求半溢式压 缩模加料室的高度。
解 (1)计算塑件的体积Vs
模具与压机关系
一、最大压力的校核
已知压机公称压力和塑件尺寸时确定型腔数目 n=(k·F机)/(pA型) 已知型腔数目和塑件尺寸时确定公称压力 F机=(p·A型n)/ k 模压所需的成型总压力:F模≤kF机
其中: k——修正系数,一般取0.75—0.90;
而:F模=pA型n 其中 : p——单位成型压力(MPa),可查表
六、顶出机构的校核
压力机最大顶出行程应大于模具所
需的推出行程,且必须保证塑件推
出型腔后高于型腔表面10mm以上。
l = h塑+h加+(10~15)≤L
其中:
l——塑件需推出的高度 h塑——塑件最大高度
h加——加料腔高度mm
L——压力机顶出杆最大顶出行程mm
压缩模成型零部件设计
与塑料直接接触用以成型塑件的零件叫成型零件。 在设计压缩模时:
(二)固定式压缩模脱模机构 固定式压缩模的脱模可分为气吹脱模和机动脱模, 而通常采用的是机动脱模。当采用溢式压缩模或少 数半溢式压缩模时,如对型腔的粘附力不大,可采 用气吹脱模,如下图所示。
机动脱模一般应尽量让塑件在分型后留在压机上 有顶出装置的模具一边。
(三)半固定式压缩模脱模机构
半固定式压缩模分型 后,塑件随可动部分 (上模或下模)移出模 外,然后用手工或简单 工具脱模。
(2)塑件所需原料的体积Vsl
(3)加料室截面积A
(4)挤压边下面型腔体积Vj
(5)凸模及型芯占用的体积∑Vd
(6)加料室高度H
加料室高度取 H=80mm
四、导向机构 与注射模具相同,压缩模最常用的导向零件是 在上模设导柱,在下模设导向孔。压缩模导向装置 还具有下述特点: 1)除溢式压缩模的导向单靠导柱完成外,半溢 式和不溢式压缩模的凸模和加料腔的配合段还能起 导向和定位的作用,一般加料腔上段设有10mm的 锥形部分导向环,因此后者比溢式压缩模有更好的 对中性。 2)压制中央带有大通孔的壳体塑件时,为提高 压缩成型质量,可在孔中安置导柱,见下图
b嵌件安装在下 模,操作方便,且 可利用嵌件顶出塑 件。
4.便于塑料流动,如下图所示;
加压时应使料流方向与加压方向 一致,避免反向流动。
5.保证凸模的强度,如下图所示;
上凸模 受力较大, 因此上凸模 形状越简单 越好,
6.保证重要尺寸的精度
精度要求很高的尺寸不宜设计在施压方向上(因为 溢边的存在)
2、半固定式压缩模 开合模在机内进行,一般将上模固定在压力机上,下模可沿 导轨移动,用定位块定位,合模时靠导向机构定位。也可按 需要采用下模固定的形式,工作时则移出上模,用手工取件 或卸模架取件。 特点:该结构便于放嵌件和加料,适用于小批量生产,可减 小劳动强度。
3、固定式压缩模
上下模都固定在压力机上,开模、合模、脱模等工序均在压 力机内进行。 特点:生产效率高,操作简单,劳动强度小,开模振动小, 模具寿命长,但结构复杂,成本高,且安放嵌件不方便。适 用于成形批量较大或形状较大的塑件。
二、按模具加料室形式分
1.溢式压缩模
结构特点: 无加料腔 凸模与凹模无配合部分 有环形挤压面b 优点: 结构简单,成本低 塑件易取出,易排气 安放嵌件方便 加料量无严格要求 模具寿命长
又称敞开式压缩模
缺点:
合模太快时,塑料易溢出,浪费原料;合模
太慢时,易造成飞边增厚; 水平面的飞边难于去处,且影响塑件外观; 凸、凹模配合精度较低; 不适用于压制带状、片状或纤维填料的塑 料和薄壁或壁厚均匀性要求高的塑件。
校核 F脱<F顶
F顶——压力机顶出杆的最大顶出力N
(压力机的顶出力是保证压缩模提出机构脱出塑件的动力)
四、闭合高度的校核
模具完全开模取件的高度<压力机的最大开距Hmax
模具闭合时的高度>压力机的最小开距Hmin
五、装模尺寸的校核
压缩模的宽度应小于压力机立柱或框架之间的距离 压缩模用螺钉与压力机连接 压缩模用压板螺钉与压力机压紧固定,则模具只需设有 宽15~30mm的凸缘台阶即可,如图4—8。
腔的形状可以简化;
缺点: 不适用于压制布片或纤维填料的塑料。 适用范围: 流动性较好的塑料和形状较复杂的带小嵌件的塑件。
三.压缩模类型选用原则
塑件批量大 —— 固定式模具 批量中等 —— 固定式或半固定式模具
小批量或试生产 —— 移动式模具
水平分型面模具结构简单,操作方便,优先选用。 流动性差的塑料,塑件形状复杂 ——不溢式模具 塑件高度尺寸要求高,带有小型嵌件 —— 半溢式模具 形状简单,大而扁平的盘形塑件 —— 溢式压缩模
1.便于加料(如图6-12所示);
a加料腔 直径小而深, 不便于操作; b加料腔 直径大而浅, 便于操作;
2.有利于压力传递,如图6-13所示;
B将塑件 横放,采用 横向加压的 方法。
A圆筒太 长,上部施 压,下部易 出现疏松、 填充不足现 象。
3.便于安放和固定嵌件,如图6-14所示;
A嵌件可 能安装不牢 落下损坏模 具。
3.半溢式压缩模的配合形式:最大特点是带有水平的 挤压环,同时凸模与加料腔间的配合间隙或溢料槽可以排气 溢料。
三、加料腔尺寸的计算 设计压缩模加料腔时,必须进行高度尺寸计 算,以单型腔模具为例,其计算步骤如下: (一)计算塑件的体积 (二)计算塑件所需原料的体积 Vsl=(1+K)kVs Vsl---塑料所需原料的体积; K---飞边溢料的重量系数,根据塑件分型面大 小选取,通常取塑件净重的5%~10%; k---塑料的压缩比(查表); Vs ---塑件的体积 根据塑件的重量 Vsl=(1+K)mv m---塑件的重量;v---塑件的比容(查表)
7.长型芯位于施压方向
抽拔距离长的位于施压方向,抽拔距离短的放在侧 向做侧向分型抽芯。
二、凸模与加料室的配合形式 (-)凸凹模各组成部分及其作用 以半溢式压缩模为例,凸凹模一般有引 导环、配合环、挤压环、储料槽、排气 溢料槽、承压面、加料腔等部分组成, 它们的作用如下:
1.引导环(L1)引导环为导正凸模进人凹 模的部分。 引导环的作用是: 减少凸凹模之间的摩擦,避免塑件顶出 时擦伤表面,并可延长模具寿命,减少 开模阻力, 便于排气。
1.带活动上模的压缩 模(见右图) 2.带活动下模的压缩 模 这类模具其上模是 固定的,下模可移出。
(四)移动式压缩模脱模机构 1.撞击架脱模 (如下图)
2.卸模架卸模 (1)单分型面卸模,如下图所示;
(2)双分型面卸模架卸模
(3)垂直分 型卸模架 卸模
(五)压缩模的手柄 为了使移动式或半固定式压缩模搬运方便,可在模具的l两侧装 上手柄。
A型——每一型腔的水平投影面积(m2)
n——压缩模内型腔的个数
二、开模力的校核
开模力计算
F开=k1F模 其中:F开——开模力N
F模——模压所需的成型总压力N
k1——压力损耗系数0.1~0.2
三、脱模力的校核
脱模力计算
F脱=A件p结
其中:F脱——脱模力N A件——塑件侧面积之和m2
p结——塑件与金属的结合力MPa
适用范围:
小批量或试制、低精度和强度无严格要求的的扁
平塑件。
2.不溢式压缩模
结构特点:
加料腔是型腔向上的延续部分
又称封闭式压缩模
无挤压面
凸模与加料腔有小间隙的配合
优点:
塑件密度大、质量高 对塑料要求不严(以棉布、玻璃 布或长纤维填料的塑料均可) 塑件飞边薄且呈垂直状易于去除
缺点:
加料量必须精确,高度尺寸难于保证;
3)由于压缩模在高温下工作,因此一般不采用带 加油槽的加油导柱。
五、压缩模的脱模结构 压缩模的脱模机构与注射模具的脱模机构相 似,常见的有推杆脱模机构,推管脱模机构、推 件板脱模机构等,此外还有二级脱模机构和上下 模均带有脱模装置的双脱模机构。 (-)脱模机构与压机的连接方式 多数压机都带有顶出装置,压缩模的脱模机 构和压机的顶杆(活塞杆)有下述两种连接方式: 1.压机顶杆与压缩模脱模机构不直接连接 2.压机项杆与压缩模脱模机构直接连接
压缩模结构组成及分类
压缩模结构组成 1、成型零件:包括上凸模、凹模、型 芯、下凸模等组成。 2、加料室: 凹模的上半部。 3、导向机构: 导柱、导套。 4、侧向分型与抽芯机构 5、脱模机构 6、加热系统 7、支承零部件
压缩模的分类
一、按模具在压机上的固定形式分
1、移动式压缩模 模具不固定在压力机上,成形后将模具移出 压力机,先抽出侧型芯,再取出塑件。在清 理加料腔后,将模具重新组合好,然后放入 压力机内再进行下一个循环的压缩成形。 特点:其结构简单,制造周期短。但因加料、 开模、取件等工序均为手工操作,模具易磨 损,劳动强度大,模具重量一般不宜过大 (20㎏)。这种压缩模目前只供试验及新产 品试制时制造样品用,正式生产中已经淘汰。