涡轴发动机组合压气机转子ANSYS参数化仿真系统开发
基于ANSYS和NUMECA的航空发动机涡轮风扇叶片结构仿真分析
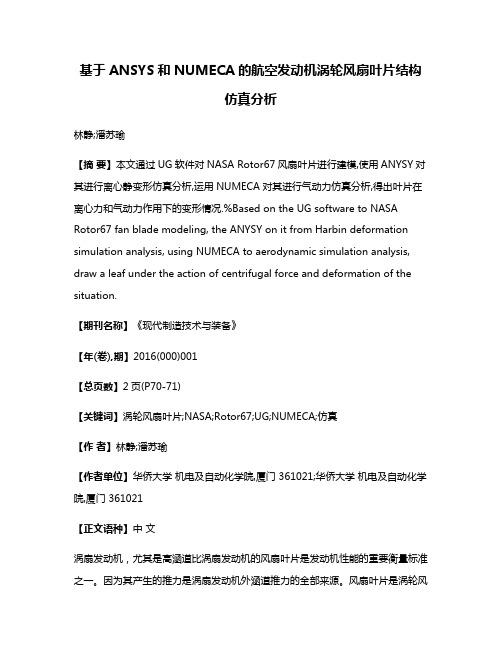
基于ANSYS和NUMECA的航空发动机涡轮风扇叶片结构仿真分析林静;潘苏瑜【摘要】本文通过UG软件对NASA Rotor67风扇叶片进行建模,使用ANYSY对其进行离心静变形仿真分析,运用NUMECA对其进行气动力仿真分析,得出叶片在离心力和气动力作用下的变形情况.%Based on the UG software to NASA Rotor67 fan blade modeling, the ANYSY on it from Harbin deformation simulation analysis, using NUMECA to aerodynamic simulation analysis, draw a leaf under the action of centrifugal force and deformation of the situation.【期刊名称】《现代制造技术与装备》【年(卷),期】2016(000)001【总页数】2页(P70-71)【关键词】涡轮风扇叶片;NASA;Rotor67;UG;NUMECA;仿真【作者】林静;潘苏瑜【作者单位】华侨大学机电及自动化学院,厦门 361021;华侨大学机电及自动化学院,厦门 361021【正文语种】中文涡扇发动机,尤其是高涵道比涡扇发动机的风扇叶片是发动机性能的重要衡量标准之一。
因为其产生的推力是涡扇发动机外涵道推力的全部来源。
风扇叶片是涡轮风扇发动机的重要零件。
NASA Rotor67是NASA Lewis研究中心设计的二级风扇中第一级轴流跨声速转子,是为数不多有详细公开发表测试数据的算例。
该风扇被广泛应用于气动计算。
本文选取跨声速风扇叶片NASA Rotor67叶片为算例,运用UG软件进行建模,利用ANSYS对其进行离心静变形仿真分析,利用NUMECA对其进行气动仿真分析。
为了缩短计算时间,提高效率,转子叶片绕旋转轴转动a=2π/N(N为叶片数)。
涡扇发动机整机振动特性仿真分析

涡扇发动机整机振动特性仿真分析发布时间:2021-10-19T08:53:24.157Z 来源:《城镇建设》2021年第5月15期作者:王淑金[导读] 针对涡扇发动机整机振动,开展了发动机整机三维建模、动力学特性仿真分析等工作。
王淑金海翔机械厂河北邯郸 057159摘要:针对涡扇发动机整机振动,开展了发动机整机三维建模、动力学特性仿真分析等工作。
建立了转子支承系统、静子承力系统动力学模型,对静子承力系统关键测点在转子不平衡量大小、分布及碰摩力作用下的振动响应特性进行了仿真分析。
仿真结果与实际发动机试验振动图谱的对比分析表明,特征频率点的响应吻合良好。
通过本研究,初步搭建起涡扇发动机整机振动机理仿真分析平台,对提高发动机振动机理研究能力和整机振动分析诊断水平有积极意义。
关键词:涡扇;发动机;振动分析1、前言在飞行过程中,发动机是动力保证,其工作的可靠性直接关系到飞行安全。
发动机振动不仅影响发动机本身的工作,而且影响配件和仪器的工作,结构的发动机振动应力较大,甚至会最终影响发动机的可靠性。
涡扇发动机的振动故障在军用和民用发动机上是不同的,导致大量的发动机提前返回工厂,降低了发动机的使用寿命,增加了维修费用。
据统计,90%以上的结构强度失效是由振动引起的或与振动有关的。
本文从飞机发动机研究的设计、生产、使用和维护方面研究了飞机发动机的振动问题。
2、飞机发动机振动源分析2.1转子故障引起的振动2.1.1转子不平衡“不平衡力”是涡扇发动机振动的重要原因之一。
由于不均匀的缺陷,转子材料的设计、热变形误差、制造、装配和转子在运行介质上的粘连转子或质量损失的过程中,使实际的转子中心的质量和重心产生偏移。
使转子出现质量不平衡[l]。
转子不平衡是影响涡扇发动机振动和噪声的一个重要因素。
它不仅直接威胁到飞机发动机的安全可靠运行,而且还能诱发其他类型的故障。
转子不平衡引起的振动故障是涡扇发动机常见的有害故障,是降低发动机振动的重要措施。
某发动机燃气涡轮模型涡轮转子轴向预紧分析

某发动机燃气涡轮模型涡轮转子轴向预紧分析作者:陈欢欢赵艳云熊望骄来源:《中国科技纵横》2020年第09期摘要:基于ANSYS/Workbench软件建立了某涡轴发动机燃气涡轮模型涡轮转子的二维有限元模型,采用有限元方法计算了该转子的松弛力,并与成熟发动机试验件转子进行了对比分析,研究两者松弛力差异较大的具体原因,对发动机试验件转子结构设计提出了合理化建议。
关键词:燃气涡轮;模型涡轮;松弛力;轴向预紧中图分类号:V231.95 文献标识码:A 文章编号:1671-2064(2020)09-0117-02现代小型涡轴、涡桨发动机中各级转子之间多采用圆弧端齿及施加预紧力的中心拉杆连接,这种连接方式具有轴系同心精度好、装拆方便等优点[1-2]。
发动机工作时,由于转子承受离心力、气动力(包含轴向力和扭矩)、热载荷以及机动载荷等,转子零部件存在轴向收缩或伸长的现象。
为了保证转子安全可靠地工作,装配时需要通过调整压紧螺母的拧紧力矩来施加适当的轴向预紧力。
预紧力过小,转子不能正常连接和运转;预紧力过大,会降低中心拉杆及其他零部件的强度储备。
因此,进行转子轴向预紧力分析非常必要。
确定转子的轴向预紧力,须先确知转子的最大松弛力(压紧力),然后结合转子轴向预紧力规定值的确定准则和方法,计算并给出满足工程要求的转子轴向预紧力(拧紧力矩)。
端齿连接转子轴向预紧力的确定准则和确定方法[3]。
一种确定端齿连接转子各接触面上松弛力和压紧力的简化计算方法[4]。
本文基于ANSYS/Workbench软件采用二维轴对称模型对某涡轴发动机燃气涡轮模型涡轮转子轴向松弛力进行了计算,并与成熟发动机试验件转子进行了对比,分析了松弛力差异较大的原因。
1 模型涡轮转子松弛力计算1.1 结构简介某涡轴发动机燃气涡轮模型涡轮转子支承方式为简支形式,左侧有一棒轴承,右侧有一球轴承,转子结构示意图见图1。
两级涡轮整体叶片盘通过花键与涡轮轴连接,并通过螺母进行轴向预紧。
基于ANSYS的涡轴发动机参数化仿真系统开发

基于ANSYS的涡轴发动机参数化仿真系统开发项目名称:基于ANSYS的涡轴发动机参数化仿真系统开发用户单位:南京航空航天大学能源与动力学院所在行业:航空航天航空涡轴发动机是一种输出轴功率的涡轮喷气发动机。
涡轴发动机的压气机结构包含从纯轴流式、单级离心、双级离心到轴流与离心混装一起的组合式压气机等形式。
航空涡轴发动机压气机转子的复杂系统,每一次结构设计方案的调整和结构强度的分析都是一个新的过程,其中的重复劳动量将是非常巨大的。
将参数化的设计分析方法引入到涡轴发动机组合压气机设计过程中,使得设计分析工作集中在各类零件结构形式的选择和具体参数的调整,以及对每种设计方案的结构强度分析。
由此减少工作人员的工作量,缩短压气机的设计周期。
ANSYS是目前少数几种支持参数化设计的有限元分析软件之一,提供了三种二次开发工具:ν通过应用参数化程序设计语言(APDL)编制分析程序,实现有限元分析过程的全参数化驱动;ν通过应用用户界面设计语言(UIDL)编写或改造ANSYS图形界面,使其更符合行业分析特点;ν通过应用用户程序特性(UPFs)从开发程序源代码的级别上扩充ANSYS的功能。
ν如何实现全参数驱动的有限元分析方法核心内容:对有限元分析的前、后处理进行参数化,包括几何模型、有限元网格划分、约束边界条件、载荷、材料性能、单元类型、分析类型和后处理类型的参数化。
ν如何开发涡轴发动机组合压气机转子参数化有限元分析分析系统核心内容:参数化模型的定义和可变参数的有限元分析程序的编制;利用UIDL语言开发系统操作界面;将各零部件的参数化有限元程序集成于ANSYS环境。
ν参数化有限元模型的定义方法首先将涡轴发动机组合压气机这种复杂的非标准件分解为轴流轮盘、轴流叶片、离心轮盘、离心大小叶片等结构。
然后按特征结构对其定义参数。
例如各种形式的轮盘都具有轮缘、腹板和轮毂三大基本特征,称之为基盘,其余形状则为辅助特征包括突缘、鼓筒、轴径、安装边、均布孔或安装孔、环槽及篦齿等。
基于ANSYS的压气机叶轮振动特性有限元仿真分析

基于ANSYS 的压气机叶轮振动特性有限元仿真分析*黄新忠赵俊生(中北大学机械工程与自动化学院,太原030051)Vibration characteristic simulation and analysis of compressorimpeller based on finite elementHUANG Xin-zhong ,ZHAO Jun-sheng(School of Mechanical Engineering and Automation ,North University of China ,Taiyuan 030051,China )文章编号:1001-3997(2012)02-0012-02【摘要】车用涡轮增压器的压气机叶轮常常因为振动而导致破坏,对压气机叶轮进行模态分析是避免叶轮与激振频率发生共振的常用手段,能有效避免因发生共振而导致的叶轮破坏问题。
利用AN -SYS 软件,采用子结构分析方法对压气机叶轮的中低阶固有频率进行了数值仿真计算,获得了不同转速和不同节径时的频率,并根据计算结果绘制了Campbell 图,找出了与压气机叶轮固有频率产生共振的转速,为压气机叶轮的优化设计提供了依据,同时说明采用子结构分析的方法可以较精确地获得整体模型的低阶固有频率解。
关键词:压气机叶轮;振动特性;模态分析;子结构【Abstract 】The compressor impeller of the automotive turbocharger is often damaged by the vibration,while model analysis for the compressor impeller is a kind of common means to avoid resonance between theimpeller and natural frequency ,which can effectively avoid the damage caused by the resonance.Based on the software of ANSYS ,the mid and low order nature frequency was simulated and calculated by the method ofsubstructure ,and the frequency of different speed and different nodal diameter were obtained.In addition ,Campbell chart was drawn according to the results to find the resonance speed of the compressor impeller ,which provided reference for optimal design of the compressor impeller.At the same time ,the method of sub -structure was proved to be able to obtain accurately the low order natural frequency of whole model.Key words :Compressor impeller ;Vibration characteristic ;Modal analysis ;Substructure中图分类号:TH16,TK421.8文献标识码:A*来稿日期:2011-04-29*基金项目:山西省高校科技项目资助项目(0805113)1引言随着人们对内燃机强化要求的不断提高,涡轮增压已被公认为内燃机技术的主要发展方向之一。
ANSYS飞机仿真方案

ANSYS航空发动机仿真方案第三章航空发动机仿真方案 1.航空发动机行业概况1903年12月17日,美国莱特兄弟实现了人类历史上首次有动力、载人、持续、稳定和可操作的重于空气飞行器的飞行。
这使得几千年来由少数人从事的飞行探索事业在后来的百年中发展成为对世界政治、经济、军事和技术,甚至人们的生活方式都有重要影响的航空业。
因此,从狭义上说,航空发动机是航空器飞行的动力,是航空器的“心脏”;从广义上说,航空发动机是航空事业发展的推动力,对航空器的性能和研制有着决定性的影响。
1.1.世界航空发动机发展历史航空发动机百余年的发展历史大致可分为两个时期:第一个时期从莱特兄弟的首次飞行开始到二次世界大战结束为止。
这个时期内,活塞式发动机统治了40年左右的时间。
第二个时期是从二次世界大战结束至今,燃气涡轮发动机取代了活塞式发动机,居航空动力的主导地位,开创了喷气时代。
在燃气涡轮发动机的60多年发展历程中,大致经历了四次更新换代:第一代是单转子亚音速喷气发动机。
这一代发动机大多数在20世纪30~40年代研制,40年代末50年代初投入使用。
压气机采用离心式和轴流式两种,总增压比在5左右,单管燃烧室,单级涡轮;推重比3左右。
有代表性的机种有:美国的J47(TG-190)、前苏联的VK-1和法国的阿塔(Atar)发动机。
第二代是超声速涡喷发动机。
这些发动机在第一代发动机的基础上有了许多创新,大都在50年代研制。
主要技术特点是:双转子、进口导流叶片可调、超声速压气机、高温涡轮、推重比达到5左右。
用这一代发动机装配的飞机都是超声速战斗机。
代表机种有:美国的J79和前苏联的R11-300R。
第三代是超声速涡扇发动机。
这一代发动机的研制始于60年代,主要技术特点是:涡扇发动机、核心机技术,2D设计、环形燃烧室、气冷涡轮、结构完整性设计、新材料、推重比8。
这一代发动机的成长得益于全世界各种大型试验设备的建设、计算技术和制造技术的发展。
基于ANSYS与optiSLang的压气机叶轮的优化设计

原始流道(主叶片) 优化流道(主叶片)
叶高 10%
叶高 50%
叶高 90%
子午线流道
• 优化(主)叶片前缘几何角度通体变小以迎合由流量影响的入口速度,减小入射损失 • 优化(主)叶片后缘叶根处较叶尖处稍微向后突出,有利于增加压比,提高等熵效率 • 主叶片中部稍向前倾斜,可使迁移流避免由于离心力作用而进入叶轮间隙,影响增压 • 优化叶片厚度与原始模型类似
等熵效率[%] 压比[-]
优化叶型
修正流量[kg/s]
• 优化叶轮在设计点处等熵效率小幅提高1.45%,增压比提高4.85% • 阻塞流量较原始模型增加6.64%,喘振线也稍微向左移动 • 优化后叶片最大应力降低1.33%,最大变形量降低2.52%
18
优化结果分析-优化叶型与原始叶型比较
原始叶型(主叶片) 优化叶型(主叶片)
优化后 最优解
循环
步骤2
模拟计算 (CFX,FEM)
模拟结果 (等熵效率,压比,最大应力等)
验证
遗传算法 模型优化
MOP 1. 灵敏度分析 2. 近似模型
步骤1: 参数化实验模型;与实验数据比较;原始模型的确立 步骤2: optiSLang与Ansys耦合;三维流场及静力学模型;求得最优解 步骤3: 通过整体增压模型对最优解验证
压比[-] 等熵效率[-]
优化点
优化点
• 在设计点工况下,由近似模型所得压比与验证模拟结果差值约为0.05bar,等熵效率增幅约为 0.025,验证结果与近似结果相近,近似模型准确度较高。
17
优化结果分析-最优解在整体增压模型中的验证
压比与等熵效率比较
最大应力
[Pa]
阻塞流量
原始叶型
最大变形 [m]
CAE-ANSYS航空发动机解决方案

解决方案
内容概要
ANSYS公司及其产品简介 几何模型处理及CAD接口方案 全面分析方案
结构分析方案 复杂流动传热分析方案 耦合分析方案
网格处理方案 ANSYS公司售后服务介绍 国内国际应用情况
• 世界最著名CAE软件提供商及服务商之一 • 1970年创始于美国宾州钢铁之城匹兹堡 • 产品面向整个研发过程,从系统级样机仿真平台到CAE软件开发平台 • 2000年收购顶级前后处理软件ICEMCFD • 2001年收购领先优化技术公司CADOE • 2003年收购著名CFD软件CFX
通用结构力学分析-形状和拓扑优化
形状优化
在满足给定条件下优化结构,使之达 到:重量最轻、或应力最小、或寿命 最长、或温度分布最均匀……
拓扑优化
提供概念设计,在满足给定条件下 获得最佳的拓扑外型……
通用结构力学分析
螺栓预紧力单元模拟各种螺栓连接,直接施加螺栓预紧力载荷
通用结构力学分析-其它
单元生模死拟材料增加或材料 减少的过程,如:隧道或矿 井的开挖过程、分阶段建造 (大型桥梁)、顺序装配、 焊接、大坝施工等等
航
空
发
动
机
榫
头
榫
槽
接
触
热
分
装
析
配
摩 擦 生 热
通用结构力学分析-非线性示例
蠕 变
超 弹
某型发动机高压涡轮盘弹塑性分析
扭转屈曲
形状记忆合金
粘弹
通用结构力学分析-动力学
时域动力学
模态叠加法
瞬态动力分析:外载荷、边界条件、 结构空间位置等随时间任意全变方化法,凝聚法
求解运动方程 直接积分法 全方法 凝聚法
- 1、下载文档前请自行甄别文档内容的完整性,平台不提供额外的编辑、内容补充、找答案等附加服务。
- 2、"仅部分预览"的文档,不可在线预览部分如存在完整性等问题,可反馈申请退款(可完整预览的文档不适用该条件!)。
- 3、如文档侵犯您的权益,请联系客服反馈,我们会尽快为您处理(人工客服工作时间:9:00-18:30)。
涡轴发动机组合压气机转子ANSYS参数化仿真系统开发
作者:纪福森吴铁鹰陈伟
摘要:本文分析了航空涡轴发动机组合压气机转子的结构特点和设计特点,并将近年来广泛提及的参数化设计思想引入到组合压气机的设计分析中,利用ANSYS 提供的APDL (ANSYS Parametric Design Language)和UIDL(User Interface Design Language)开发工具,开发了涡轴发动机组合压气机参数化有限元分析系统。
实现了某涡轴发动机组合压气机转子各级叶片、各级轮盘、各级叶盘以及整级组件的全参数驱动的有限元建模及分析。
关键词:涡轴发动机,组合压气机,整体叶盘,参数化设计分析
1 前言
参数化设计是一种解决设计约束问题的数学方法,它是在结构形状比较定型时,用一组参数来约定尺寸的关系,然后通过尺寸驱动达到改变结构形状的目的。
参数化设计广泛应用于机械产品的建模中。
近年来开始将参数化的思想融入到有限元分析中,提出了基于结构参数化的有限元分析。
但是,由于只能进行几何模型的参数化,参数化程度比较浅。
于是,提出了全参数驱动的有限元分析方法,即对有限元分析的前、后处理进行参数化,包括几何模型、有限元网格划分、约束边界条件、载荷、材料性能、单元类型、分析类型和后处理类型的参数化,自动化程度高,具有发展前途。
ANSYS是目前少数几种支持参数化设计的有限元分析软件之一。
ANSYS功能强大、通用性好,同时还具有良好的开放性,用户可以根据具体需要在其标准版本上开发出具有行业分析特点的专用系统。
ANSYS提供了三种二次开发工具:参数化程序设计语言(APDL),通过该语言编制参数化有限元分析程序,实现有限元分析过程的全参数化驱动;用户界面设计语言(UIDL),通过该语言编写或改造ANSYS图形界面,使其更符合行业分析特点;用户程序特性(UPFs),通过该语言可以从开发程序源代码的级别上扩充ANSYS的功能。
本文涡轴发动机组合压气机转子参数化有限元分析分析系统,其核心内容是参数化模型的定义和可变参数的有限元分析程序的编制,然后利用UIDL语言开发系统操作界面,将各零部件的参数化有限元程序集成于ANSYS环境。
2 涡轴发动机压气机结构特点和设计特点
涡轴发动机,是一种输出轴功率的涡轮喷气发动机。
法国是最先研制涡轴发动机的国家。
50年代初,透博梅卡公司研制成世界上第一台航空涡轮轴发动机,定名为“阿都斯特—l”。
涡轴发动机的压气机结构形式,从纯轴流式、单级离心、双级离心到轴流与离心混装一起的组合式压气机。
当前,直升机的涡轴发动机大多采用的是若干级轴流加一级离心所构成的组合压气机。
例如,国产涡轴6、涡轴8发动机;“黑鹰”直升机上的T700发动机。
涡轴发动机的轴流压气机大量采用整体结构,结构简单,零组件数量少。
如将转子叶片和轮盘做成一体,形成叶盘结构。
法国阿赫耶发动机,美国T700发动机均采用了整体叶盘结构。
压气机的设计过程是一个气动设计和结构设计反复修正、协调、计算与实验的过程。
从压气机气动、结构设计流程图[6]中可以看出在两个过程中都存在着大量的结构强度分析的内容。
此外,从流程图中还可以看出设计流程存在大量的反复性。
作为航空涡轴发动机压气机转子这样一个复杂的系统,如果每一次结构设计方案的调整和结构强度的分析都是一个新的过程,其中的重复劳动量将是非常巨大的。
于是,我们将参数化的设计分析方法引入到涡轴发动机组合压气机设计过程中,使得设计分析工作主要是各类零件结构形式的选择和具体参数的调整,以及对每种设计方案的结构强度分析。
这样可以减少工作人员的工作量,缩短压气机的设计周期。
3 参数化有限元分析模型的定义
对于涡轴发动机组合压气机这种复杂的非标准件,我们首先对其进行结构分解,可分为轴流轮盘、轴流叶片、离心轮盘、离心大小叶片。
我们知道叶盘结构非常复杂,在定义几何参数时具有一定的难度,这样我们引入了特征结构的概念,按特征结构对其定义参数。
对叶盘结构进行特征分析,各种形式的轮盘都具有轮缘、腹板和轮毂三大基本特征,称之为基盘,其余形状则为辅助特征包括突缘、鼓筒、轴径、安装边、均布孔或安装孔、环槽及篦齿等[7]。
基于这种思想我们对某轴流叶盘结构进行研究(图1),在满足分析要求的条件下,对结构进行适当简化并提取结构的几何参数(表1)。
图1 某轴流叶盘结构简图表1 结构特征参数表
表2 有限元分析参数表
4 APDL参数化有限元分析方法
ANSYS参数化有限元分析程序设计方法与步骤:
(1) 利用参数化设计思想, 根据模型的几何结构抽象出描述模型的特征参数, 并对实际模型在不影响精度的情况下适当简化。
同时,设置单元类型、单元网格精度、材料参数等有限元分析参数。
(2) 用APDL语言编制包含实体建模、分析过程、结果处理过程的有限元分析程序。
(3) 引入设计分析参数, 构成可变参数的有限元分析程序。
(4) 根据设计分析要求,将参数赋予具体的特征值,进行有限元分析。
图2 参数化有限元设计分析流程
这样,在进行结构设计分析时只需重复(4) 就可不断获得新的结果, 对于具体使用人员甚至无需了解有限元的具体分析过程与方法, 就可得到有限元分析结果。
另外,根据设计要求我们可以增加各种分析功能和后处理功能,也可自己开发新的功能模块与ANSYS集成,如开发新的优化算法程序等。
5 涡轴发动机组合压气机参数化仿真实例
在进行复杂零部件参数化设计分析时,首先,将复杂零部件按特征分解;然后引入模块拼合关系作为约束,建立零部件参数间函数关系,从而实现了复杂三维零部件实体模型的参数化设计分析。
基于上述思想我们实现了涡轴发动机组合压气机转子的参数化仿真,其由三级轴流式,一级离心式叶盘组成。
图3 UIDL 开发的系统界面
6 结论
(1)将参数化设计思想引入到涡轴发动机组合压气机整体叶盘的设计分析中,设计人员每次只需调整具体结构参数及有限元分析参数,进行有限元计算。
而无需进行重复建模,这样,节省了大量时间,可以缩短组合压气机的设计周期。
(2)参数化设计思想引入,使得设计人员,可以根据设计要求对各分结构进行有限元分析,如各级叶片、各级轮盘、各级叶盘等的有限元分析。
(3)在基于结构参数化的基础上,设计人员可以方便的进行结构的2D/3D优化设计。
(4)随着我们各种结构形式叶盘参数化模型库的丰富,设计人员只需根据设计要求选择某种结构,进行参数调整,即可组合成整个压气机进行分析,可以实现设计分析的半自动化。
参考文献
[1] 王坚,黄金国,向文等.参数化特征造型系统FMT[J].高技术通讯,1994.(7).
[2] 平雪良,朱广平,周来水.一种新的参数化设计方法[J].东南大学学报,1997.27(5).
[3] 陈德人.参数化设计模型与方法[J].浙江大学学报,1995.29(2).
[4] 陈伟,何飞,温卫东.基于结构参数化的有限元分析方法[J].机械科学与技术,2003.6.
[5] 黄菊花等.材料成形计算机模拟中的参数化有限元法[J].中国机械工程,2003.1.
[6] 航空发动机设计手册(压气机分册).北京:航空工业出版社,2000.
[7] 马枚等.并行工程环境下基于约束的叶盘结构建模与分析[J].航空动力学报,
1998.10.(end)。