硝化反应案例
第三章硝化反应

OH
3.1
概述
随着与H或被取代基相连接的原子不同, 硝化包括:
C-硝化 N-硝化 O-硝化
产物:
硝基物 硝(基)胺 硝酸酯
R-NO2 RNH-NO2 RO-NO2
3.1
概述
硝化反应包括范围极广,芳烃、烷烃、 烯烃及它们的胺、酰胺、醇等衍生物都可 在适当条件下硝化。
但制备脂肪族硝基化合物要比芳香族硝 基物困难得多。 Why 1935年才合成得到脂肪族硝基物,主要 用作炸药、火箭燃料和溶剂。 本章主要讨论芳环和杂环化合物的硝化。
HNO3 + H2SO4 + H2NO3 H2SO4 + H2O H2NO3 + HSO4 + NO2 + H2O + HSO4 + H3O
+ -
3.2 硝化反应历程
• 混酸解离总式:
HNO3 + 2H2SO4 NO2 + 2HSO4 + H3O
+ +
因此,HNO3中加入强质子酸(H2SO4) 可提高HNO3离解为NO2+的程度,大大提 高其硝化能力。 混酸是使用最广泛的硝化剂。
3.3.1 均相硝化动力学 ⑴ 在有机溶剂中的硝化
活泼芳烃(如甲苯、二甲苯或三甲苯) 在有机溶剂和大量过量的无水硝酸中低温 均相硝化,硝化速度服从零级反应(与芳 烃浓度无关)。
3.3 硝化反应动力学
⑵ 在硫酸存在下硝化 有吸电子取代基的芳烃(如硝基苯)在 浓硫酸介质中的均相硝化是二级反应。
v k[ ArH ][ HNO3 ]
3.2 硝化反应历程
3.2.1 硝化质点 已证实:多数情况下,硝化剂参加硝 化反应的活泼质点是硝基阳离子NO2+。 1903年,Euler最早提出NO2+为硝化 反应的进攻质点,直到二十世纪40年代, 通过各种光谱数据、物理测定及动力学研 究,才得到了证明。
1.4硝化反应应用实例

一、硝基苯的合成
NO 2
硝基苯的主要用途是制取苯胺和 聚氨酯泡沫塑料。
1.低温混酸连续硝化
图 苯连续一硝化流程示意图
1,2-硝化锅 3,5,9,11-分离器 4-萃取器 6,7-泵 8,10-文丘里管混合器
优点:工艺成熟,反应平稳,易于控制, 产品质量稳定。
主要缺点:产生大量待浓缩的废硫酸和含 酚类及硝基物废水;要求硝化设备具有 足够的冷却面积且能耗高;安全性差。
1-氨基蒽醌的两种方法
蒽醌磺化-氨解 产品质量好 但是汞害严重
蒽醌一硝化
过量硝酸硝化法
容易发生爆炸
非均相混酸硝化法
三、邻硝基苯酚的合成
邻硝基苯酚的合成 以稀硝酸为硝化剂 以水蒸气蒸馏分离对位异构体
3. 硝基苯生产的安全技术
生产工段属甲级防爆工区 硝酸的腐蚀 温度控制 冷却水引入管装压力计,引入
和引出管都要安装温度计, 保证夹套不 渗漏Fra bibliotek拌要求 不得中断
氧化的危险 搅拌轴采用硫酸做润滑 剂,温度计套管用硫酸做导热剂
设备的密封性 有毒(在空气中硝基 苯最大允许含量5ppm)
二、1-硝基蒽醌的合成
2.绝热硝化
图 苯的绝热硝化流程示意图
1,2,3,4-硝化器 5-酸槽 6-闪蒸器 7-除沫器 8-分离器 9-热交换器 10-泵
绝热硝化工艺:
(1)混酸:HNO35~8%,H2SO458~ 68%, H2O>25%;
(2)苯过量5~10%; (3)硝化温度:132~136℃; (4)无冷却; (5)利用反应热闪蒸废酸。
绝热硝化优点:
(1)反应温度高,硝化速度快; (2)硝酸反应完全,副产物少; (3)混酸含水量高,酸浓度低,酸量大,安全 性好; (4)利用反应热浓缩废酸并循环利用,无需加 热、冷却,能耗低; (5)设备密封,原料消耗少; (6)废水和污染少。
反硝化硝化工艺
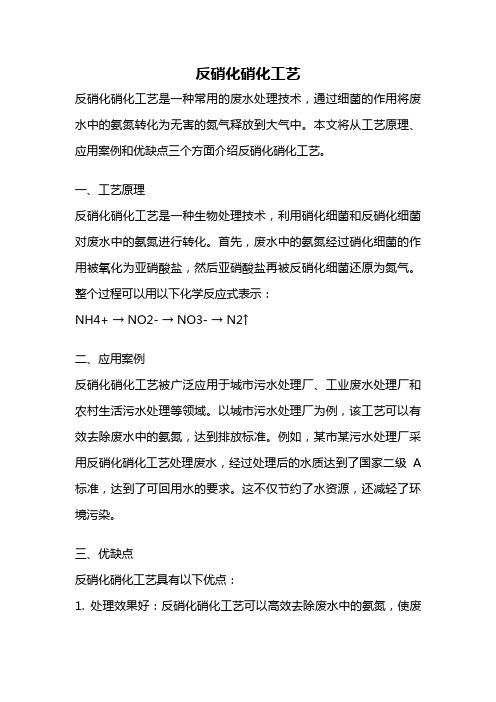
反硝化硝化工艺反硝化硝化工艺是一种常用的废水处理技术,通过细菌的作用将废水中的氨氮转化为无害的氮气释放到大气中。
本文将从工艺原理、应用案例和优缺点三个方面介绍反硝化硝化工艺。
一、工艺原理反硝化硝化工艺是一种生物处理技术,利用硝化细菌和反硝化细菌对废水中的氨氮进行转化。
首先,废水中的氨氮经过硝化细菌的作用被氧化为亚硝酸盐,然后亚硝酸盐再被反硝化细菌还原为氮气。
整个过程可以用以下化学反应式表示:NH4+ → NO2- → NO3- → N2↑二、应用案例反硝化硝化工艺被广泛应用于城市污水处理厂、工业废水处理厂和农村生活污水处理等领域。
以城市污水处理厂为例,该工艺可以有效去除废水中的氨氮,达到排放标准。
例如,某市某污水处理厂采用反硝化硝化工艺处理废水,经过处理后的水质达到了国家二级A 标准,达到了可回用水的要求。
这不仅节约了水资源,还减轻了环境污染。
三、优缺点反硝化硝化工艺具有以下优点:1. 处理效果好:反硝化硝化工艺可以高效去除废水中的氨氮,使废水达到排放标准。
2. 节能环保:该工艺利用细菌的作用进行废水处理,不需要添加化学药剂,节约能源并减少化学物质对环境的污染。
3. 适应性强:反硝化硝化工艺适用于不同类型的废水处理,适用于不同规模的污水处理厂。
4. 运行成本低:与其他废水处理工艺相比,反硝化硝化工艺的运行成本较低。
然而,反硝化硝化工艺也存在一些缺点:1. 对操作要求高:该工艺需要精确控制废水中的氧气含量和温度等参数,对操作人员的要求较高。
2. 需要一定的运行时间:反硝化硝化工艺需要一定的时间来完成氨氮的转化,处理效率相对较低。
3. 对初始废水质量要求高:反硝化硝化工艺对废水的初始质量要求较高,若废水中含有较高浓度的重金属离子或有毒物质,可能会对细菌的生长产生不利影响。
反硝化硝化工艺是一种有效的废水处理技术,具有处理效果好、节能环保等优点。
然而,对操作要求高和需要一定的运行时间等缺点也需要我们在实际应用中加以注意。
某厂TNT生产线硝化车间发生特大爆炸事故
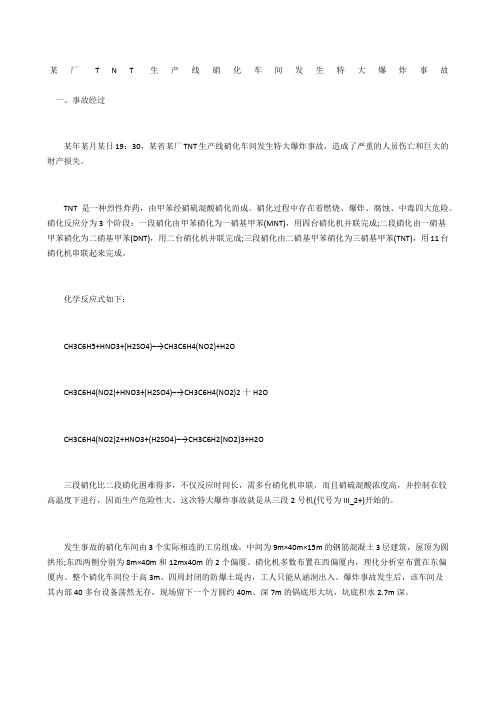
某厂T N T生产线硝化车间发生特大爆炸事故一、事故经过某年某月某日19:30,某省某厂TNT生产线硝化车间发生特大爆炸事故,造成了严重的人员伤亡和巨大的财产损失。
TNT是一种烈性炸药,由甲苯经硝硫混酸硝化而成。
硝化过程中存在着燃烧、爆炸、腐蚀、中毒四大危险。
硝化反应分为3个阶段:一段硝化由甲苯硝化为一硝基甲苯(MNT),用四台硝化机并联完成;二段硝化由一硝基甲苯硝化为二硝基甲苯(DNT),用二台硝化机并联完成;三段硝化由二硝基甲苯硝化为三硝基甲苯(TNT),用11台硝化机串联起来完成。
化学反应式如下:CH3C6H5+HNO3+(H2SO4)─→CH3C6H4(NO2)+H2OCH3C6H4(NO2)+HNO3+(H2SO4)─→CH3C6H4(NO2)2十H2OCH3C6H4(NO2)2+HNO3+(H2SO4)─→CH3C6H2(NO2)3+H2O三段硝化比二段硝化困难得多,不仅反应时间长,需多台硝化机串联,而且硝硫混酸浓度高,并控制在较高温度下进行,因而生产危险性大。
这次特大爆炸事故就是从三段2号机(代号为III_2+)开始的。
发生事故的硝化车间由3个实际相连的工房组成。
中间为9m×40m×15m的钢筋混凝土3层建筑,屋顶为圆拱形;东西两侧分别为8m×40m和12mx40m的2个偏厦。
硝化机多数布置在西偏厦内,理化分析室布置在东偏厦内。
整个硝化车间位于高3m、四周封闭的防爆土堤内,工人只能从涵洞出入。
爆炸事故发生后,该车间及其内部40多台设备荡然无存,现场留下一个方圆约40m、深7m的锅底形大坑,坑底积水2.7m深。
爆炸不仅使本工房被摧毁,而且精制、包装工房,空压站及分厂办公室遭到严重破坏,相邻分厂也受到严重影响。
位于爆炸中心西侧的三分厂、南侧的五分厂、北侧的六分厂和热电厂,凡距爆炸中心600m范围内的建筑物均遭严重破坏;1200m范围内的建筑物局部破坏,门窗玻璃全被震碎;3000m范围内的门窗玻璃部分振碎。
硝化反应与氮化反应

硝化反应与氮化反应氮是地球上最丰富的元素之一,而氮化物是一类广泛存在的化合物。
氮化反应和硝化反应是两个与氮相关的重要化学反应。
本文将分别介绍硝化反应和氮化反应的定义、过程、应用以及相关实验。
硝化反应是指将氨气或氨盐氧化生成硝酸盐的反应。
在硝化反应中,氨氧化而成为硝酸根离子(NO3-),同时还产生水和氢离子。
该反应一般是在强氧化剂的作用下进行,如过氧化氢或二氧化氮。
硝化反应的化学方程式如下所示:NH3 + 2O2 -> HNO3 + H2O硝化反应在农业领域具有重要应用。
硝酸盐是一种植物可利用的氮源,可以作为肥料施加在农田中,促进植物生长。
此外,硝酸盐也是火药的重要成分之一,用于军事和爆破行业。
氮化反应是指将氮气与其他元素或化合物进行反应,形成氮化物的过程。
氮化反应的一个重要例子是将氮气与金属反应生成金属氮化物。
例如,通过氮化反应可以制备氮化硅、氮化铝和氮化钛等化合物。
氮化反应通常需要高温和高压条件下进行,因为氮气具有很高的键能,不易与其他物质反应。
在实验室中,常用的方法是将金属与氮气在800-1000°C的高温环境下进行反应。
氮化反应的化学方程式可以用以下反应为例:2Al + N2 -> 2AlN氮化反应具有重要的材料制备应用。
氮化物具有优异的物理和化学性质,如高熔点、高硬度和良好的导电性等。
因此,氮化物广泛应用于材料科学领域,如制备高性能陶瓷、涂层和电子元件等。
除了硝化反应和氮化反应,还存在其他与氮相关的重要反应,如还原反应、氨解反应等。
这些反应都在不同的领域有着广泛的应用,包括农业、材料科学、环境保护等。
总结而言,硝化反应和氮化反应是两个与氮相关的重要化学反应。
硝化反应是将氨氧化为硝酸盐的反应,对农业和爆破行业有重要应用;氮化反应是将氮气与其他物质反应生成氮化物,用于材料制备和电子元件等领域。
对于深入理解这些反应的机理和应用,还需要进一步的研究和实验。
c C2.硝化反应

23
F.N.A.=
废酸中硫酸的质量 废酸的总质量
×100%
w(H2SO4) = ×100% 100-5w(HNO3)/7Φ
24
D.V.S.与F.N.A.的关系(Φ=1)
D.V.S.= F.N.A. 100-F.N.A. D.V.S. 1+D.V.S. ×100%
F.N.A.=
25
例: MA: S 65%, N 31%, W 4%, 求 D.V.S 值 和 F.N.A。 (设φ=1) 解: D.V.S = 65 /(100 – 65 – 5 × 31 / 7)= 5.0 F.N.A(%)= [ D.V.S /(1+ D.V.S)] × 100 = 83.3(%)
30
四. 配混酸工艺
配混酸是首道工序
p21
1、配酸锅工艺条件的考虑(安全)
a、有效的搅拌混合装置
b、好的冷却换热装置
c、防腐能力:可搪玻璃
#
31
2、间隙式配酸操作 ☆
p21
安全的配混酸方法应是:
在有效的混合搅拌和冷却条件下,将硫酸先慢、
后渐快地加入水或废酸中,并控制温度在40度以下,
最后再先慢、后渐快地加入硝酸。 配制的混酸须分析、调整至合格!
快速型——慢速传质型
甲苯在质量分数为66.6%~71.6%的硫酸中的硝化属于此种类型。
瞬间型——快速传质型
甲苯在质量分数为71.6%~77.4%的硫酸中的硝化属于此种类型。
18
2.4 混酸硝化工艺
一.优点:
硝化力强,速度快,硝酸用量近理论量;
混酸中硝酸的氧化性低,氧化副反应少; 硫酸热容量大使反应较平稳;
图 间歇硝化釜
39
第5章 硝化反应

6、气相硝化法
工业实例: 苯与NO2在80~190℃通过分子筛处理可转化为硝基苯。
2017/2/22
15
5.2 硝化反应历程
+ X-NO X + NO 2 2 一、硝化剂的活泼质点
2017/2/22
13
4、非均相混酸硝化法
当被硝化物和硝化产物在反应温度下都是液态时,常 常采用非均相混酸硝化的方法。通过剧烈的搅拌,有 机相被分散到酸相中而完成硝化反应。这种硝化方法 有很多优点,是目前工业上最常用、最重要的硝化方 法.也是本章讨论的重点。
2017/2/22
14
5、有机溶剂中的硝化法
能够生成硝基正离子(NO2+)的试剂
二、硝化反应历程 以苯的硝化为例,其反应历程可以用下式表示:
H + NO2+ NO2+ + NO2 快 NO2 + H+
2017/2/22
16
硝化反应的特点
反应不可逆 反应速度快,无需高温 放热量大,需要及时移除反应热
多数为非均相反应,需要加强传质
6、硝酸盐与硫酸
硝酸盐和硫酸作用产生硝酸与硫酸盐。实际上它是无水硝酸与 硫酸的混酸: MNO3十H2SO4= HNO3十MHSO4 M为金属。常用的硝酸盐是硝酸钠、硝酸钾,硝酸盐与硫酸 的配比通常是 (0.1~0.4):1(质量比)左右。按这种配比,硝酸盐 几乎全部生成NO2+离子.所以最适用于如苯甲酸、对氯苯甲酸 等难硝化芳烃的硝化。
空间位阻效应不明显
硝烟反应案例

硝烟反应案例
硝烟反应是一种化学反应,通常发生在含硝酸盐的物质中。
这种反应通常是一
种爆炸性的化学反应,因此在实验室和工业生产中需要特别小心和谨慎。
下面我们将介绍几个硝烟反应的案例,以便更好地理解这种反应的特点和应用。
第一个案例是硝酸铵和硫的反应。
硝酸铵是一种常见的硝酸盐,而硫是一种常
见的非金属元素。
当它们混合在一起并受热时,会发生激烈的化学反应,产生大量的氮气和硫化氢气体,同时释放出大量的热量和光线。
这种反应非常危险,因为它会产生爆炸,并释放出有毒的气体。
因此,在实验室中进行这种反应时,需要采取严格的安全措施,以防止事故的发生。
第二个案例是硝酸和有机化合物的反应。
硝酸也是一种常见的硝酸盐,而有机
化合物通常含有碳、氢和氧等元素。
当硝酸和有机化合物发生反应时,通常会产生硝基化合物,这些化合物通常具有很高的爆炸性。
因此,在工业生产中,需要特别小心处理这些化合物,以防止意外爆炸的发生。
第三个案例是硝酸和金属的反应。
硝酸和金属的反应通常会产生相应的硝酸盐
和氢气。
在一些情况下,这种反应会产生大量的热量,并释放出可燃的氢气。
因此,在实验室和工业生产中,需要特别小心处理这些反应,以防止火灾和爆炸的发生。
总的来说,硝烟反应是一种非常危险的化学反应,需要特别小心和谨慎。
在实
验室和工业生产中,必须严格遵守安全操作规程,采取必要的安全措施,以防止意外事故的发生。
同时,对于硝烟反应的特点和应用,也需要进行深入的研究和探讨,以便更好地理解和应用这种化学反应。
- 1、下载文档前请自行甄别文档内容的完整性,平台不提供额外的编辑、内容补充、找答案等附加服务。
- 2、"仅部分预览"的文档,不可在线预览部分如存在完整性等问题,可反馈申请退款(可完整预览的文档不适用该条件!)。
- 3、如文档侵犯您的权益,请联系客服反馈,我们会尽快为您处理(人工客服工作时间:9:00-18:30)。
5.4.3硝化反应事故案例
1991年2月9日19时30分,辽宁省辽阳市国营庆阳化工厂二
分厂一工段硝化工房发生特大爆炸事故,造成17人死亡,13人重伤,98人轻伤,直接经济损失2266.6万元。
事故经过:国营庆阳化工厂二分厂装配有生产TNT炸药的生产线,1991年2月9日,硝化工段当日一班的生产不正常,曾在上午8时
10分停机修理,15时开机生产。
16时30分二班接班后,硝化三段
6#、7#机的硝酸阀出现泄漏,致使2#至7#机硝酸含量高于工艺规定
指标。
仪表维修工对泄漏的硝酸阀进行了修理,并于17时修好。
此时,各硝化机的温度均在规定的范围内。
19时15分左右,操作工牛某从分析室送样返回机台,发现三段2#机分离器压盖冒烟,随即打
开了分离器雨淋和硝化机冷却水旁路阀进行降温,并去仪表室找班长。
班长告诉牛某打开机前循环阀,并随即带仪表工张某、牛某来到工房南大门打开备用水阀,同时告诉李某停止加料。
班长又叫牛某打开安全硫酸阀,牛某返身回去将安全硫酸阀打开1周,并发现分离器压盖由冒烟变成喷火。
火势迅速蔓延且越来越大,最终导致硝化机全部发生剧烈爆炸。
事故原因分析:
1、事故的直接原因
(1)设备和生产上的原因。
二班硝化组在生产过程中,由于硝
化三段6#、7#机硝酸加料阀泄漏,造成硝化系统硝酸含量增高和硝
化物最低凝固点前移(由4#机前移至1#机),致使发生事故的2#机
反应剧烈。
硝化机温度略高,表明机内的硝化反应并不充分。
硝化物被提升到分离器后,继续反应,而分离器内又没有搅拌和冷却装置,反应不均匀,局部过热,从而造成分离器内硝化物分解冒烟。
分离器压盖冒烟后,一种可能是由于进行剧烈的硝化反应,局部过热加剧,硝化物分解燃烧,分离器由冒烟变为喷火;另一种可能是由于高温、高浓度的硝硫混酸与使用了不符合工艺要求的石棉绳接触成为火种,使分离器由冒烟变为喷火。
(2)人为因素。
这起爆炸事故是由于生产出现异常情况,即硝
化三段2#机分离器冒烟,而后变为喷火,火势扩大而引起的。
在处
理事故过程中,2#机操作工牛某和班长张某,没有完全按照《岗位操作与技安防火守则》的要求去做。
虽然采取了一些措施,但是在分离器起火之后,没有采取切断该设备与其他设备的联系,打开分离器废酸循环阀及硝化机安全开关往安全池放料等关键措施,却撤离了现场,致使火势蔓延,导致爆炸。
2、事故的间接原因
(1)设备老化、工艺落后。
庆阳化工厂这条TNT生产线是国内
唯一尚存的一条卧式生产线,存在搅拌不均匀、反应不完全、易产生局部高温过热等问题。
在发生异常情况时,不易控制和处理。
硝化机分离器没有自动放料装置。
(2)生产秩序不正常,劳动纪律涣散。
(3)企业对工人进行安全生产知识、操作技能培训教育不够。
工人技术素质低,遇到异常情况时,不能熟练有效地采取措施进行处理。
依据对上述事故原因的分析,可以认为这起特大爆炸事故是一起在本质安全条件差情况下的责任事故。
事故教训与防范措施:设备的本质安全是实现设备安全的一个重要途径。
设备的本质安全是指当操作失误时,设备能自动保证安全;当设备出现故障时,能自动发现并自动消除,能确保操作人员和设备的安全。
就这起事故而论,事故的发生有两个主要因素:一是工人技术素质低,遇到异常情况时,不能熟练有效地采取措施进行处理;二是设备本质安全化程度低,在发生异常情况时,不易控制和处理,即硝化机分离器没有自动放料装置。
预防此类事故,一方面需要提高工人的技术素质,提高遇到异常情况时有效处理的水平与能力;另一方面需要提高设备的本质安全化程度,实现自动化控制。
两个方面相比较,提高设备的本质安全化程度更为重要。
总之,设备本质安全化要从控制导致事故的“物源”方面入手,提出防止事故发生的有效方法,对于从根本上发现和消除事故与危害的隐患,防止误操作及设备故障可能发生的伤害具有重要的作用。
5.4.4蒸馏事故案例
1998年10月22日15分,江苏南京助剂厂防老剂DBH车间乙醇蒸馏釜因超压发生爆炸,造成4人死亡,3人重伤,直接经济损失11.2万元。
事故经过:
江苏南京助剂厂防老剂DBH生产实行两班制。
10月22日18点45分,两班交接后,乙醇蒸馏工做完准备工作后开始抽料,当班班长去各岗位巡回检查。
20点15分乙醇蒸馏釜突然发生爆炸,并燃起大火。
事故原因:
1、事故的直接原因
乙醇蒸馏釜出料阀没有开启是造成这起事故的直接原因。
由于出料阀未打开,当开通蒸汽加热后乙醇蒸发,使蒸馏釜从常压状态变为受压状态,当釜内乙醇蒸气压力超过釜盖螺栓的密封力时,将釜盖冲开,大量的乙醇蒸气冲出后与空气混合,形成爆炸混合物,遇火源瞬间发生化学爆炸。
2、事故的间接原因
(1)防老剂DBH生产设施扩建,未严格按“三同时”要求进行设计审查。
设计未报有关部门审查批准,设计不规范,没有正规图样,部分电气设备不符合防爆要求。
生产厂房未考虑泄压等问题,不符合《建筑设计防火规范》的要求。
(2)制度不严,管理不善。
企业未健全和完善必要的规章制度。
无章可循、有章不循现象普遍存在,生产管理混乱。
工人素质低,缺乏安全生产知识,操作不够熟练,事故应变能力差。
(3)扩建项目没有很好地组织,缺乏严密的计划。
没有制订试车计划,也没有制定与扩建装置相应的安全和工艺操作规程,更没有认真地向维修人员和操作人员进行设备、工艺交底,即仓促投入试生产。
事故教训与防范措施:
1、应严格遵守“三同时”要求,请专业设计、安装单位进行生产厂房和生产装置的设计与安装。
2、对安全规程和制度进行整理,重新修订工艺规程和安全操作规程。
3、整顿用工制度,加强职工的教育培训。
从社会上择优录用高素质的职工队伍,并加强工艺和技术等方面的培训,配备专业的技术人员。
建立安全管理机构及配备专职的安全管理人员。