机械制造技术基础 第二章 第八节 合理切削用量选择及材料加工性
合理选择切削用量
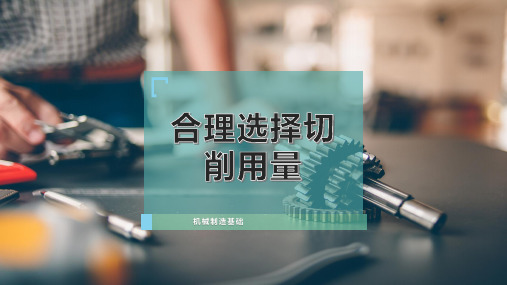
16
课堂实训——选择切削用量
机械制造基础
3)确定切削速度 vc 根据已知条件和已确定的 ap 和 f 值,由P139-140页表得切削速度 vc 130~160 m/min。由于该轴为
细长轴,应选取较小的切削速度,因此切削速度 vc 130 m/min。计算机床转速为
n 1 000vc 1 000 130 1 035 r/min πd 3.14 40
70~80
背吃刀量 ap/(mm)
2~6 进给量 f /(mm/r)
0.3~0.6
切削速度 vc /(m/min)
100~120 90~110 70~90 70~90 50~70 60~80 60~70
6~10
0.6~1
70~90 60~80 50~70 50~70 40~60 50~70 50~60
0.4~0.7 0.6~0.9
0.4~0.6
跳到 P144
5
二、进给量的选择
机械制造基础
续表
铸铁及 铜合金
16×25
20×30 25×25
40
0.4~0.5
60
0.6~0.8
0.5~0.8
0.4~0.6
100
0.8~1.2
0.7~1
0.6~0.8
0.5~0.7
400
1~1.4
1~1.2
0.8~1
0.6~0.8
寸为 46 mm×350 mm,加工尺寸为 39 mm×300 mm。在普通卧式车床CA6140上加工,使用焊接式硬
质合金YT15车刀,刀杆截面尺寸为16 mm×25 mm,刀具几何参数为
o 15,o 8,r 75, s 0,rε 1 mm,br1 0,
机械制造技术基础 第2章
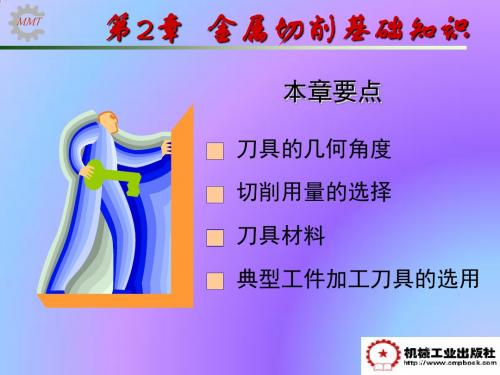
MMT
2.2.3 刀具工作角度
• 在横向进给切削或切断 工件时,随着进给量f值的增 加和加工直径d的减小,工作 后角不断减小,刀尖接近工 件中心位置时,工作后角的 减小特别严重,很容易因后 面和工件过渡表面剧烈摩擦 使刀刃崩碎或工件被挤断, 切削中应引起充分重视。因 此,切断工件时不宜选用过 大的进给量f,或在切断接近 结束时,应适当减小进给量 或适当加大标注后角。
MMT
2.2.3 刀具工作角度
当工件材料和加工性质不同时,常用硬质合金车刀的 合理前角如表2-1所示。
表2-1 合理前角 粗 车 精 车 硬质合金车刀合理前角的参考值 合理前角 粗 车 精 车
工件材料 低碳钢 中碳钢 合金钢 淬火钢
工件材料 灰铸铁 铜及铜合金 铝及铝合金 钛合金 ≤1.177 GP a
MMT
2.1.1 切削运动
3、合成切削运动
刀具与工件间的相对切削运 动是主运动和进给运动的合成运 动。切削刃上选定点相对于工件 的主运动的瞬时速度,称为切削 速度,以vc表示。切削刃上选定点 相对于工件的进给运动的瞬时速 度,称为进给速度,以vf表示。合 成切削运动的瞬时速度用ve表示。 则ve=vc+vf 。
MMT
2.2.2 刀具静止角度参考系及其坐标平面
MMT
2.2.2 刀具静止角度参考系及其坐标平面
刀具静止角度
2.
MMT
2.2.2 刀具静止角度参考系及其坐标平面
刀具在正交平面参考系中定义的标注角度有: (1)前角 γo :前刀面与基面间的夹角(正交平面中测量) 作用:影响切屑的变形程度; 影响刀刃强度
后角α0:后刀面与切削平面间的夹角(正交 平面中测量)
MMT
2.2.2 刀具静止角度参考系及其坐标平面
2[1].7切削用量的选择及工件材料加工性
![2[1].7切削用量的选择及工件材料加工性](https://img.taocdn.com/s3/m/3deab8f7ba0d4a7302763a03.png)
二、切削用量的合理选择 1.切削用量的选择原则 1.切削用量的选择原则
粗加工时,应在保证必要的刀具寿命的前提下, 粗加工时,应在保证必要的刀具寿命的前提下,以尽可能提 高生产率和降低成本为目的。 高生产率和降低成本为目的。根据刀具使用寿命与切削用量 影响最大, 的关系式,切削用量↑ 的关系式,切削用量↑, T ↓,其中速度v 对T 影响最大, 次之, 影响最小。 进给量f 次之,背吃刀量ap影响最小。 粗加工中选择切削用量时,应首先选择尽可能大的背吃刀 粗加工中选择切削用量时, 中选择切削用量时 量ap,其次在工艺条件允许下选择较大的进给量f ,最后根 据合理的刀具寿命, 据合理的刀具寿命,用计算法或查表法确定切削速度v 。这 的乘积最大,以获得最大的生产率. 样使v、f 、ap 的乘积最大,以获得最大的生产率. 精加工时则主要按表面粗糙度和加工精度要求确定切削用量。 精加工时则主要按表面粗糙度和加工精度要求确定切削用量。 时则主要按表面粗糙度和加工精度要求确定切削用量
2.7切削用量的选择及工件材料加工性 切削用量的选择及工件材料加工性 2.72.7-1 切削条件的合理选择
补充) 一、刀具寿命的合理选择(补充) 刀具寿命的合理选择 补充
生产目标:加工质量、加工效率、 生产目标:加工质量、加工效率、经济性 优化指标:单件生产时间、单件加工成本、利润率 优化指标:单件生产时间、单件加工成本、 切削参数:切削用量、刀具材料、几何参数、 切削参数:切削用量、刀具材料、几何参数、机床等 作中间控制因素把优化指标和切削参数联系起来。 常用T 作中间控制因素把优化指标和切削参数联系起来。
2.7- 2.7-2工件材料的切削加工性
工件材料切削加工性 指材料被加工成合格零件的难易程度 是一个相对的概念
机械制造技术基础复习资料
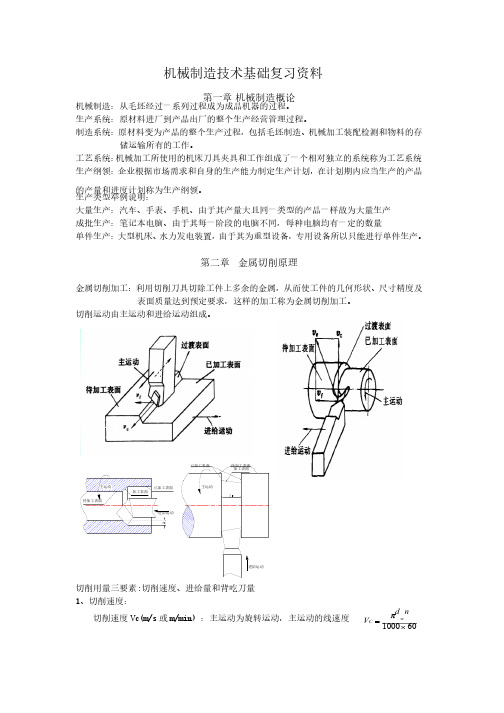
机械制造技术基础复习资料机械制造技术基础复习资料第一章第一章 机械制造概论机械制造概论机械制造:从毛坯经过一系列过程成为成品机器的过程。
机械制造:从毛坯经过一系列过程成为成品机器的过程。
生产系统:原材料进厂到产品出厂的整个生产经营管理过程。
生产系统:原材料进厂到产品出厂的整个生产经营管理过程。
制造系统:原材料变为产品的整个生产过程,原材料变为产品的整个生产过程,包括毛坯制造、包括毛坯制造、机械加工装配检测和物料的存 储运输所有的工作。
储运输所有的工作。
储运输所有的工作。
工艺系统:机械加工所使用的机床刀具夹具和工作组成了一个相对独立的系统称为工艺系统机械加工所使用的机床刀具夹具和工作组成了一个相对独立的系统称为工艺系统 生产纲领:企业根据市场需求和自身的生产能力制定生产计划,在计划期内应当生产的产品的产量和进度计划称为生产纲领。
的产量和进度计划称为生产纲领。
生产类型举例说明:生产类型举例说明:大量生产:汽车、手表、手机、由于其产量大且同一类型的产品一样故为大量生产大量生产:汽车、手表、手机、由于其产量大且同一类型的产品一样故为大量生产 成批生产:笔记本电脑、由于其每一阶段的电脑不同,每种电脑均有一定的数量成批生产:笔记本电脑、由于其每一阶段的电脑不同,每种电脑均有一定的数量单件生产:大型机床、水力发电装置,由于其为重型设备,专用设备所以只能进行单件生产。
第二章第二章 金属切削原理金属切削原理金属切削加工:利用切削刀具切除工件上多余的金属,利用切削刀具切除工件上多余的金属,从而使工件的几何形状、从而使工件的几何形状、尺寸精度及 表面质量达到预定要求,这样的加工称为金属切削加工。
表面质量达到预定要求,这样的加工称为金属切削加工。
表面质量达到预定要求,这样的加工称为金属切削加工。
切削运动由主运动和进给运动组成。
切削运动由主运动和进给运动组成。
切削用量三要素切削用量三要素::切削速度、进给量和背吃刀量切削速度、进给量和背吃刀量1、切削速度:、切削速度:切削速度Vc(m/s 或m/min) m/min) :主运动为旋转运动,主运动的线速度:主运动为旋转运动,主运动的线速度:主运动为旋转运动,主运动的线速度 601000´=nd V wC p进给运动加工表面待加工表面待加工表面主运动已加工表面加工表面进给运动已加工表面主运动主运动为往复直线运动6010002´=rC Ln V2、进给量:工件或刀具每回转一周时二者沿进给方向相对位移。
(完整版)机械制造技术基础(第2版)第二章课后习题答案(2)
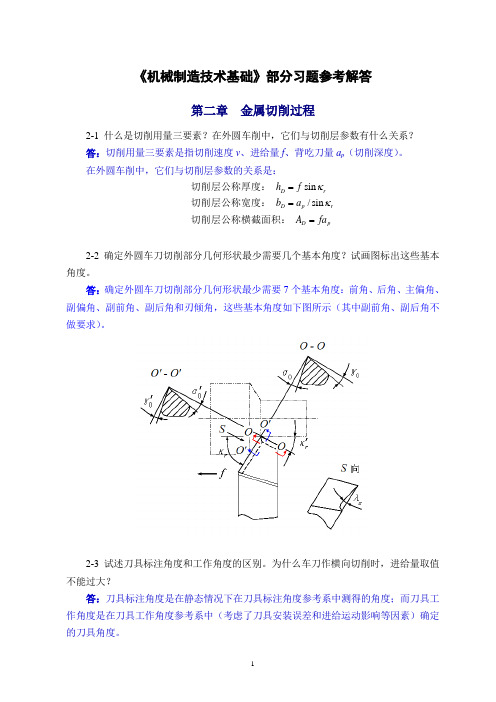
《机械制造技术基础》部分习题参考解答第二章 金属切削过程2-1 什么是切削用量三要素?在外圆车削中,它们与切削层参数有什么关系? 答:切削用量三要素是指切削速度v 、进给量f 、背吃刀量a p (切削深度)。
在外圆车削中,它们与切削层参数的关系是:sin /sin D rD p r D ph f b a A fa κκ===切削层公称厚度: 切削层公称宽度: 切削层公称横截面积:2-2 确定外圆车刀切削部分几何形状最少需要几个基本角度?试画图标出这些基本角度。
答:确定外圆车刀切削部分几何形状最少需要7个基本角度:前角、后角、主偏角、副偏角、副前角、副后角和刃倾角,这些基本角度如下图所示(其中副前角、副后角不做要求)。
2-3 试述刀具标注角度和工作角度的区别。
为什么车刀作横向切削时,进给量取值不能过大?答:刀具标注角度是在静态情况下在刀具标注角度参考系中测得的角度;而刀具工作角度是在刀具工作角度参考系中(考虑了刀具安装误差和进给运动影响等因素)确定的刀具角度。
车刀作横向切削时,进给量取值过大会使切削速度、基面变化过大,导致刀具实际工作前角和工作后角变化过大,可能会使刀具工作后角变为负值,不能正常切削加工(P23)。
2-4 刀具切削部分的材料必须具备哪些基本性能?答:(P24)(1) 高的硬度和耐磨性;(2) 足够的强度和韧性;(3) 高耐热性;(4) 良好的导热性和耐热冲击性能;(5)良好的工艺性。
2-5 常用的硬质合金有哪几类?如何选用?答:(P26)常用的硬质合金有三类:P类(我国钨钴钛类YT),主要用于切削钢等长屑材料;K类(我国钨钴类YG),主要用于切削铸铁、有色金属等材料;M类(我国通用类YW),可以加工铸铁、有色金属和钢及难加工材料。
2-6 怎样划分切削变形区?第一变形区有哪些变形特点?答:切削形成过程分为三个变形区。
第一变形区切削层金属与工件分离的剪切滑移区域,第二变形区前刀面与切屑底部的摩擦区域;第三变形区刀具后刀面与已加工表面的摩擦区域。
切削用量的合理选择

切削用量的合理选择切削用量不仅是在机床调整前必须确定的重要参数,而且其数值合理与否对加工质量、加工效率、生产成本等有着非常重要的影响。
在确定了刀具几何参数后,还需选定合理的切削用量参数才能进行切削加工。
所谓“合理的”切削用量是指充分利用刀具切削性能和机床动力性能(功率、转矩),在保证质量的前提下,获得高的生产率和低的加工成本的切削用量。
选择合理的切削用量时,必须考虑合理的刀具寿命。
切削用量的选择原则切削用量与刀具使用寿命有密切关系。
在制定切削用量时,应首先选择合理的刀具使用寿命,而合理的刀具使用寿命则应根据优化的目标而定。
一般分最高生产率刀具使用寿命和最低成本刀具使用寿命两种,前者根据单件工时最少的目标确定,后者根据工序成本最低的目标确定。
粗车切削用量的选择对于粗加工,在保证刀具一定使用寿命前提下,要尽可能提高在单位时间内的金属切除量。
在切削加工中,金属切除率与切削用量三要素绝保持线性关系,即其中任一参数增大一倍。
都可使生产率提高一倍。
然而由于刀具使用寿命的制约,当任一参数增大时,其他二参数必须减少。
因此,在制定切削用量时,三要素的最佳组合,此时的高生产率才是合理的。
由刀具寿命经验公式知,切削用量各因素对刀具使用寿命的影响程度不同,切削速度对使用寿命的影响最大,进给量次之,被吃刀量影响最小。
所以在选择粗加工切削用量时,当确定刀具使用寿命合理数值后,应首先考虑增大被吃刀量,其次增大进给量,然后根据使用寿命、被吃刀量和进给量的值计算出切削速度,这样既能保持刀具使用寿命,发挥刀具切削性能,又能减少切削时间,提高生产率。
被吃刀量应根据加工余量和加工系统的刚性确定。
精加工切削用量的选择选择精加工或半精加工切削用量的原则是在保证加工质量的前提下,兼顾必要的生产率。
进给量根据工件表面粗糙度的要求来确定。
精加工时的切削速度应避开积屑瘤区,一般硬质合金车刀采用高速切削。
大件精加工时,为保证至少完成一次走刀,避免在切削时中途换刀,刀具使用寿命应按零件精度和表面粗糙度来确定。
机械制造技术基础课后答案第二章

a2-1.金属切削过程有和特征?用什么参数来表示和比较?p答:金属切削过程是指刀具与工件相互作用形成切屑的过程。
在这一过程中会出现许多物理现象:如切削刀,切削热,积屑瘤,刀具磨损和加工硬化等。
切削要素包括切削用量和切削层几何参数:切削用量:1.切削速度V 2.进给量f 3.背吃刀量a切削层几何参数1.切削宽度a 2切削厚度a 3切削面积A2-2.切削过程的三个变形区各有何特点?他们之间有什么关联?答:第一变形区,﹙基本变形区﹚.变形量最大。
常用它来说明切削过程的变形情况.第二变形区,﹙摩擦变形区﹚.切屑形成后与前面之间存在压力.所以沿前面流出时必然有很大的摩擦.因而使切屑底层又一次产生塑性变形。
第三变性区﹙加工表面变形区﹚:工件已加工表面与后面接触的区域.产生加工硬化这三个变形区汇集在切削刀附近.此处的应力比较集中而且复杂.金属的被切削层就在此处与工件基本发生分离.大部分变形切屑.很小一部分留在已加工表面上。
2-3分析积屑瘤产生的原因及其对加工的影响。
生产中最有效的控制积屑瘤的手段是什么?答:产生的原因:在切削速度不高而又能形成连续切屑情况下。
加工一般钢料或其它塑性材料时。
常常在道具前面粘着一块剖面有时呈三角状的硬块。
在处于比较稳定的状态时。
能够代替切削刀进行切削。
影响:引起道具实际角度的变化,如可增大前角,延长道具寿命等。
积屑瘤不稳定,增大到一定程度后破碎。
容易嵌入已加工表面内,增大表面粗糙度值。
手段1.降低切削速度,使温度降低,不易粘结。
2.增加切削速度,使温度高于产生切屑瘤的温度。
3.采用润滑性比较好的切屑液。
4.增大切屑前角,有效降低铁屑和前刀面挤切。
5.适当提高工件硬度,减小加工硬化。
2-4有区别切屑形成后与前面之间存在压力。
所以沿前面流出时必有很大的摩擦,因而使切屑层又一次产生塑性变形,而一般刚体之间的滑动摩擦是两刚体之间的相对运动引起的。
2-5道具要从工件上切下金属,必须具有一定的切削速度,也正是由于切削角度才决定了道具切削部分各表面的空间位置。
如何选择合适的切削用量?
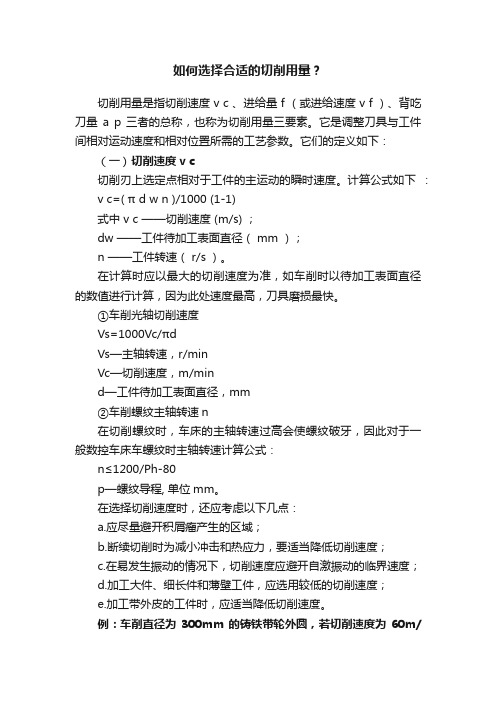
如何选择合适的切削用量?切削用量是指切削速度 v c 、进给量 f (或进给速度 v f )、背吃刀量a p 三者的总称,也称为切削用量三要素。
它是调整刀具与工件间相对运动速度和相对位置所需的工艺参数。
它们的定义如下:(一)切削速度 v c切削刃上选定点相对于工件的主运动的瞬时速度。
计算公式如下:v c=( π d w n )/1000 (1-1)式中 v c ——切削速度 (m/s) ;dw ——工件待加工表面直径( mm );n ——工件转速( r/s )。
在计算时应以最大的切削速度为准,如车削时以待加工表面直径的数值进行计算,因为此处速度最高,刀具磨损最快。
①车削光轴切削速度Vs=1000Vc/πdVs—主轴转速,r/minVc—切削速度,m/mind—工件待加工表面直径,mm②车削螺纹主轴转速n在切削螺纹时,车床的主轴转速过高会使螺纹破牙,因此对于一般数控车床车螺纹时主轴转速计算公式:n≤1200/Ph-80p—螺纹导程, 单位mm。
在选择切削速度时,还应考虑以下几点:a.应尽量避开积屑瘤产生的区域;b.断续切削时为减小冲击和热应力,要适当降低切削速度;c.在易发生振动的情况下,切削速度应避开自激振动的临界速度;d.加工大件、细长件和薄壁工件,应选用较低的切削速度;e.加工带外皮的工件时,应适当降低切削速度。
例:车削直径为300mm的铸铁带轮外圆,若切削速度为60m/min,试求车床主轴转速。
解:根据公式Vs=1000Vc/πd=1000 ×60/3.14 ×300=63.69r/min注意:在实际生产中,理论上计算出的主轴转数应从车床转速表中最接近的一档选取。
(二)进给量 f工件或刀具每转一周时,刀具与工件在进给运动方向上的相对位移量。
进给速度v f 是指切削刃上选定点相对工件进给运动的瞬时速度。
v f=fn ( 1-2 )式中 v f ——进给速度( mm/s );n ——主轴转速( r/s );f ——进给量( mm )。
- 1、下载文档前请自行甄别文档内容的完整性,平台不提供额外的编辑、内容补充、找答案等附加服务。
- 2、"仅部分预览"的文档,不可在线预览部分如存在完整性等问题,可反馈申请退款(可完整预览的文档不适用该条件!)。
- 3、如文档侵犯您的权益,请联系客服反馈,我们会尽快为您处理(人工客服工作时间:9:00-18:30)。
二、合理刀具寿命
1、理论上应根据优化目标函数而定。
有最高生产率刀具寿命Tp(单件工时最短),最低成本刀具寿命Tc (工序加工成本最低)。 Tp <Tc. 一般情况下取Tc,生产任务紧急时取TP 。 2、 生产实际中,刀具寿命的选择 ⑴ 刀具复杂制造刃磨成本高,刀具寿命可适当高些。 ⑵ 机夹可转位刀片,换刀时间短,为发挥其切削性能,刀具寿 命可适当 低些。 ⑶ 某一工序生产率限制了整个生产,该工序的刀具寿命可适当低些。 ⑷ 大型零件精加工时,避免中途换刀,刀具寿命可适当高些。
⑶ 以断屑性能衡量切削加工性 在对工件材料断屑性能要求很高的机床,如自动机床及自动线上进行加工时,或者 对断屑性能要求很高的工序,如深孔钻削、盲孔镗削等,可采用这种衡量指标 ⑷ 以刀具寿命衡量切削加工性 以刀具寿命衡量切削加工性,是比较通用的,它包括: ① 在保证相同的刀具寿命的前提下,考察切削这种工件材料的切削速度的高低; ② 在保证相同的切削条件下,看切削这种工件材料时刀具寿命的大小。
六、影响工件材料切削加工性的因素及改善切削加工性的途径
㈠ 影响工件材料切削加工性的因素 1、工件材料的硬度对切削加工性的影响 ⑴ 工件材料常温硬度对切削加工性的影响 一般情况下,同类材料中硬度高的加工性差。 ⑵ 工件材料高温硬度对切削加工性的影响 工件材料高温硬度越高,切削加工性越低。高温合金、耐热钢切削加工性低,这是 一个原因。 ⑶ 工件材料中硬质点对切削加工性的影响 工件材料中硬质点愈多,形状愈尖锐,分布愈广,则工件材料切削加工性愈低。 ⑷ 材料的加工硬化性能对切削加工性的影响 工件材料的加工硬化性能愈高,则切削加工性愈低。某些高锰钢及奥氏体不锈钢 切 削后的表面硬度,比原始基体高1.4~2.2倍。 2、工件材料的强度对切削加工性的影响 工件材料的强度包括常温和高温强度。一般情况下,工件材料的强度愈高,其切削 加工性愈低。 3、工件材料的塑性与韧性对切削加工性的影响 塑性过大或过小都使切削加工性下降。 韧性对切削加工性的影响与塑性相似。韧性对断屑的影响比较明显,在其它条件相 同时,材料的韧性愈高,断屑愈困难。
三、切削用量的选择原则
1、背吃刀量ap ⑴ 粗加工(Ra50~12.5um) 在系统刚性和机床功率允许的条件下,一次走刀尽可能切除全部余量,在中等功率 的 机床上,背吃刀量可达8~10mm。 若加工余量太大、工艺系统刚性不足、加工余量极不均匀或断续切削时,粗车可分几 次走刀,背吃刀量应依次递减。 ⑵ 半精加工( Ra6.3~3.2um) 通常背吃刀量ap=0.5~2mm。 ⑶ 精加工( Ra1.6~0.8um)或更小 通常背吃刀量ap=0.1~0.4mm。 ⑷ 若工件表皮有硬皮或硬化层,背吃刀量ap应越过硬皮或硬化层深度。 2、进给量f 粗加工:在加工工艺系统刚度、强度允许的条件下,取大值。 精加工:受加工精度及表面粗糙度限制。通常按粗糙度要求,根据工件材料,刀尖圆弧半 径,切削速度查切削用量手册来选取。 3、切削速度V 根据选定的背吃刀量ap、进给量 f 及刀具寿命T,就可按下述公式计算切削 速度V: T=CT/Vx f yapz。 在生产中,通常根据刀具材料和工件材料等查切削用量手册,作为参考。通常选择切 削速度应按下列规则: ⑴ 粗车时,背吃刀量ap和进给量 f均较大 应取较低的切削速度V。 精车时,背吃刀量ap和进给量 f均较小 应取较高的切削速度V。
⑵ 加工材料的强度及硬度较高时 通常应选较低的切削速度 V。反之则选高速度 。 ⑶ 刀具材料的切削性能(主要为耐热性)越好 切削速度就可选的越高。如:硬 质合金刀具的切削速度比高速钢刀具高好几倍,而涂层硬质合金刀具的切削速度又比未 涂层的刀片明显提高,陶瓷、金刚石和立方氮化硼刀具的切削速度又比硬质合金高很 多。 ⑷ 精加工时 应尽量避免积屑瘤产生的区域。 ⑸ 断续切削时,为减小冲击和热应力 应适当降低切削速度。 ⑹ 在易发生振动的情况下 切削速度应避开自激振动的临界速度。 ⑺ 加工大件、细长件和薄壁工件 时 应适当降低切削速度。 4、 综合切削用量的影响,粗、精加工切削用量一般选择原则 粗加工时,以提高生产率为主,同时还要保证规定刀具的寿命 一般选去较大 的背吃刀量和进给量,不高的切削速度。 精加工时,以保证加工精度和表面质量为主,同时考虑刀具寿命和生产率 常 选 用较小的背吃刀量和进给量,较高的切削速度。
四、提高切削用量的途径
1、选用切削性能更好的刀具材料。 采用耐热性和耐磨性高的刀具材料是提高切削用量的主要途径。 2、改善工件材料的加工性。 如添加硫、铅的易切钢;对钢材进行不同热处理以改善其金相显微组织。
3、提高刀具刃磨质量。 4、改善冷却润滑化条件 5、改进刀具结构和选用合理刀具几何参数。
五、工件材料的切削加工性及改善途径
4、工件材料的导热性对切削加工性的影响 在一般情况下,导热系数高的材料,其切削加工性都比较高;而导热性低的材料, 切削加工性都较低。但,导热性高的工件材料,在加工过程中温升较高,会影响工件尺 寸。 5、化学成分对切削加工性的影响
含硫、含铅易切钢。含Cr、Ni、V、Mo、W、Mn等大都能使钢的强度硬度提高。 6、金属的金相组织对切削加工性的影响 ㈡ 改善工件材料切削加工型的途径 1、调整工件材料化学成分 在满足使用要求的前提下,通过调整工件材料化学成分来改善切削加工性。如:S—Pb 易切钢,切削力小、容易断屑,刀具寿命高及加工表面质量好。 2、通过热处理改变工件材料的金相组织而改善切削加工性 如:高碳钢硬度偏高,且有较多的网状和片状渗碳组织,较难切削。通过球化退火, 可降低它的硬度,并能得到球状渗碳体,因而改善了切削加工性。低碳钢的塑性过高,也 不好切削。通过正火处理,可以适当降低塑性,提高硬度使其加工性得到改善。
1、对加工生产率(加工基本时间)的影响 在不考虑辅助工时的前提下,切削用量三要素对加工生产率的影 响是相同的。任何一个要素增 加一倍,加工生产率均可增大一倍。 2、对加工质量的影响 ⑴ 进给量f↑ 已加工表面粗糙度显著↑,工件加工精度↓。 ⑵ 背吃刀量ap ↑ 已加工表面粗糙度↑,工件加工精度↓。 ⑶ 切削速度v ↑ 通常是已加工表面粗糙度↓ ,工件加工精度↑ 3、对刀具寿命的影响 刀具寿命经验公式:T=CT/Vx f yapz ,且x>y>z .所以, 在切 削用量中,切削速度对刀具寿命影响最大,进给量次之,背吃刀量影 响最小。
※ 生产中通常使用一定刀ห้องสมุดไป่ตู้寿命下的切削速度VT及相对加工性KV来衡量工件材
料 切削加工性。 一定刀具寿命下的切削速度VT的含义: 当刀具寿命为T(min)时,切削某种工件材料所允许的最大切削速度值。 VT越高,则 切削加工性越好。一般可取T=60min。 相对加工性: 以正火状态45钢的V60作为基准,写作(V60)j,其它被切削的工件材料的V60与之 相比的数值,记为kV,即相对加工性: KV=V60/(V60)j 目前常用的工件材料,按相对加工性分为8级,KV越大,切削加工性越好; KV越小, 切削加工性越差。
第八节 切削用量选择及工件材料加工性
一、制定合理切削用量应考虑的因素 二、合理刀具寿命 三、合理切削用量的选择 四、提高切削用量的途径 五、工件材料加工性 六、影响工件材料切削加工性的因素及改善切削加工 性的途径
一、制定合理切削用量应考虑的因素
合理切削用量:指充分利用刀具的切削性能和机床性能(功率、扭矩), 在保证质量的前提下,获得高的生产率和低的加工成本。
1、工件材料切削加工性 是指在一定的切削条件下,对工件材料进行切削加工的难易程度。 2、衡量工件材料切削加工性指标 ⑴ 以加工质量衡量切削加工性 一般零件的精加工,以表面粗糙度衡量切削加工性,易获得很小的表面粗糙度的工 件材料,其切削加工性高。 对一些特殊精密零件以及有特殊要求的零件,则以已加工表面变质层深度、残余 应力和硬化程度来衡量其切削加工性。因为变质层的深度、残余应力和硬化程度对零件 尺寸和形状的稳定性以及导磁、导电和抗蠕变等性能有很大的影响。 ⑵ 以单位切削力衡量切削加工性 在机床动力不足或机床—夹具—刀具—工件系统刚性不足时,常用这种衡量指标。