切削用量及选择
简述切削用量的选择原则

简述切削用量的选择原则
切削用量是指切削工艺中每一次切削的刀具转动次数和转动距离。
切削用量的选择是指在切削过程中,选择合适的切削用量,使切削工艺能够实现最终的加工目标,以保证产品的质量和产量。
切削用量的选择要考虑以下几个方面:
一、材料的特性。
不同材料有不同的力学性能,如强度、耐磨性、塑性等,这些性能会影响刀具的正确选择和使用,从而影响切削用量的选择。
二、切削工艺要求。
切削工艺要求包括切削速度、深度、面积、质量等,这些要求可以为切削用量的选择指明方向。
三、刀具性能。
刀具的极限切削速度、前角、切削力、耐磨性等将直接影响切削用量的选择。
四、机床技术参数。
切削机床的精度、平稳度、动态响应等性能都会影响刀具的使用,因此也会影响切削用量的选择。
根据以上几个方面,可以确定切削用量的尺寸大小、切削速度、转角等参数,以达到最终的加工目标。
在实际使用中,应该结合实际情况,有经验地运用这些原则,及时调整切削用量,才能保证加工质量和产量。
综上所述,切削用量的选择包括考虑材料的特性、切削工艺要求、刀具性能以及机床技术参数等因素,其最终目的是为了实现切削工艺中最终加工目标,确保产品的质量和产量。
此外,在实际使用中要根据实际情况,有经验地运用这些原则,及时调整切削用量,以保证加
工质量和产量。
合理选择切削用量
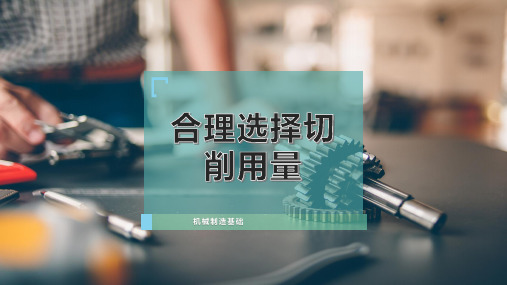
16
课堂实训——选择切削用量
机械制造基础
3)确定切削速度 vc 根据已知条件和已确定的 ap 和 f 值,由P139-140页表得切削速度 vc 130~160 m/min。由于该轴为
细长轴,应选取较小的切削速度,因此切削速度 vc 130 m/min。计算机床转速为
n 1 000vc 1 000 130 1 035 r/min πd 3.14 40
70~80
背吃刀量 ap/(mm)
2~6 进给量 f /(mm/r)
0.3~0.6
切削速度 vc /(m/min)
100~120 90~110 70~90 70~90 50~70 60~80 60~70
6~10
0.6~1
70~90 60~80 50~70 50~70 40~60 50~70 50~60
0.4~0.7 0.6~0.9
0.4~0.6
跳到 P144
5
二、进给量的选择
机械制造基础
续表
铸铁及 铜合金
16×25
20×30 25×25
40
0.4~0.5
60
0.6~0.8
0.5~0.8
0.4~0.6
100
0.8~1.2
0.7~1
0.6~0.8
0.5~0.7
400
1~1.4
1~1.2
0.8~1
0.6~0.8
寸为 46 mm×350 mm,加工尺寸为 39 mm×300 mm。在普通卧式车床CA6140上加工,使用焊接式硬
质合金YT15车刀,刀杆截面尺寸为16 mm×25 mm,刀具几何参数为
o 15,o 8,r 75, s 0,rε 1 mm,br1 0,
简述切削用量的选择原则
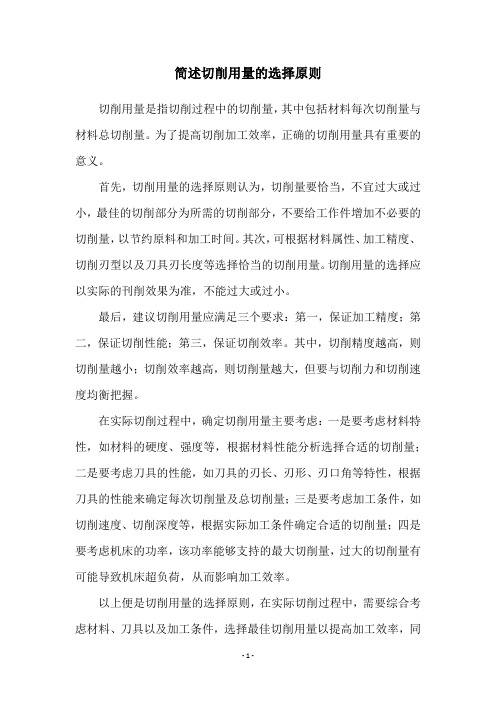
简述切削用量的选择原则
切削用量是指切削过程中的切削量,其中包括材料每次切削量与材料总切削量。
为了提高切削加工效率,正确的切削用量具有重要的意义。
首先,切削用量的选择原则认为,切削量要恰当,不宜过大或过小,最佳的切削部分为所需的切削部分,不要给工作件增加不必要的切削量,以节约原料和加工时间。
其次,可根据材料属性、加工精度、切削刃型以及刀具刃长度等选择恰当的切削用量。
切削用量的选择应以实际的刊削效果为准,不能过大或过小。
最后,建议切削用量应满足三个要求:第一,保证加工精度;第二,保证切削性能;第三,保证切削效率。
其中,切削精度越高,则切削量越小;切削效率越高,则切削量越大,但要与切削力和切削速度均衡把握。
在实际切削过程中,确定切削用量主要考虑:一是要考虑材料特性,如材料的硬度、强度等,根据材料性能分析选择合适的切削量;二是要考虑刀具的性能,如刀具的刃长、刃形、刃口角等特性,根据刀具的性能来确定每次切削量及总切削量;三是要考虑加工条件,如切削速度、切削深度等,根据实际加工条件确定合适的切削量;四是要考虑机床的功率,该功率能够支持的最大切削量,过大的切削量有可能导致机床超负荷,从而影响加工效率。
以上便是切削用量的选择原则,在实际切削过程中,需要综合考虑材料、刀具以及加工条件,选择最佳切削用量以提高加工效率,同
时节约切削原料,以降低切削成本。
第七章 切削用量的选择

在选择合理切削用量时,必须考虑加工性质。 由于粗加工和精加工要完成的加工任务和追求的目 标不同,因而切削用量选择的基本原则也完全不同。
7.7.1
粗加工时切削用量选择的基本原则
粗加工时高生产效率是追求的基本目标。这个目 标常用单件机动时最少或单位时间切除金属体积最多 来表示。下面以外圆纵车为例加以说明(图7-1)。
3.确定切削速度vc 当刀具使用寿命T、背吃刀量ap与进给量f确定 后,即可按式(7.4)计算切削速度vc
(7.4) 式中 k vc——切削速度修正系数,与刀具材料和几 何参数、工件材料等有关。 Cv 、 xv 、yv 、m及K vc值见表7.3.加工其他工件 材料时的系数及指数可查切削用量手册。
由式(6.6)可知,在选择切削用量时:应首先 选择最大的ap,其次要在机床动力和刚度允许的前提 下,选用较大的f,最后再根据式(6.6)选择合理的 vc值。
当刀具使用寿命为一定值用高速钢车刀切钢时,切削用量之间有式(7.3) 关系
(7.3)
式(7.3)表明,为保证刀具合理使用寿命,
不参与优化。因此,切削用量的优化主要是指切削切 削速度vc与进给量f的优化组合。 以单件成本最低为目标的优化目标函数的建 立过程如下: 当ap一定时,由式(7.1)
式中 由式(6.5)得
式中
将tm 、T值代入式(6.14),得 式中
式( 7.9 )即为所建立的单件成本最低的目标函 数。求该函数的极值,得
合理切削用量的选择可按下列方法进行:
1.确定背吃刀量ap
ap一般根据性质与加工余量来确定。
切削加工一般分为粗加工、半精加工和精加工
粗加工时,在保留半精与精加工余量的前提下,若机 床刚度允许,加工余量应尽可能一次切掉,在中等功 率机床上采用硬质合金刀具车外圆时,粗车取ap=2 ~ 6mm,半精车去ap=0.2 ~ 3mm,精车取ap=0.1 ~ 0.3mm。
2[1].7切削用量的选择及工件材料加工性
![2[1].7切削用量的选择及工件材料加工性](https://img.taocdn.com/s3/m/3deab8f7ba0d4a7302763a03.png)
二、切削用量的合理选择 1.切削用量的选择原则 1.切削用量的选择原则
粗加工时,应在保证必要的刀具寿命的前提下, 粗加工时,应在保证必要的刀具寿命的前提下,以尽可能提 高生产率和降低成本为目的。 高生产率和降低成本为目的。根据刀具使用寿命与切削用量 影响最大, 的关系式,切削用量↑ 的关系式,切削用量↑, T ↓,其中速度v 对T 影响最大, 次之, 影响最小。 进给量f 次之,背吃刀量ap影响最小。 粗加工中选择切削用量时,应首先选择尽可能大的背吃刀 粗加工中选择切削用量时, 中选择切削用量时 量ap,其次在工艺条件允许下选择较大的进给量f ,最后根 据合理的刀具寿命, 据合理的刀具寿命,用计算法或查表法确定切削速度v 。这 的乘积最大,以获得最大的生产率. 样使v、f 、ap 的乘积最大,以获得最大的生产率. 精加工时则主要按表面粗糙度和加工精度要求确定切削用量。 精加工时则主要按表面粗糙度和加工精度要求确定切削用量。 时则主要按表面粗糙度和加工精度要求确定切削用量
2.7切削用量的选择及工件材料加工性 切削用量的选择及工件材料加工性 2.72.7-1 切削条件的合理选择
补充) 一、刀具寿命的合理选择(补充) 刀具寿命的合理选择 补充
生产目标:加工质量、加工效率、 生产目标:加工质量、加工效率、经济性 优化指标:单件生产时间、单件加工成本、利润率 优化指标:单件生产时间、单件加工成本、 切削参数:切削用量、刀具材料、几何参数、 切削参数:切削用量、刀具材料、几何参数、机床等 作中间控制因素把优化指标和切削参数联系起来。 常用T 作中间控制因素把优化指标和切削参数联系起来。
2.7- 2.7-2工件材料的切削加工性
工件材料切削加工性 指材料被加工成合格零件的难易程度 是一个相对的概念
切削 用量的合理选择
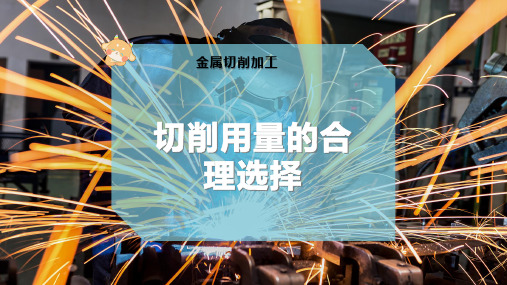
2)根据机床说明书,取机床实际进给量 =0.51mm/r。 3)检验机床进给机构允许的进给量。参考CA6140车床说 明书,查出机床进给机构允许的最大进给抗力为:FMfmax= 3528N。 计算切削时进给力为:
统、工件刚度以及精加工时表面粗糙度要求,确定进给量。
3)根据刀具寿命,确定切削速度。 4)所选定的切削用量应该是机床功率所允许的。
1.2切削用量的合理选择方法
1.背吃刀量的合理选择
背吃刀量一般是根据加工余量来确定。 粗加工(表面粗糙度Ra=50~12.5μm)时,尽可能一 次走刀即切除全部余量,在中等功率的机床上加工,取 ap=8~10mm;加工余量太大或余量不均匀、工艺系统刚性 不足或者断续切削时,可分几次走刀。 半精加工(Ra=6.3~3.2μm)时,取ap=0.5~2mm。 精加工(Ra=1.6~0.8μm)时,取ap=0.1~0.4mm。
1.5切削用量的优化概念
切削用量的优化是指在一定的预定目标及约束条件下, 选择最佳的切削用量。
在实际生产中,由于各种条件(加工零件、机床、刀 具、夹具等)都在变化,很难确定出一组最合理的切削用 量数值。
利用切削用量优化的方法,在确定加工条件下,综合 考虑各个因素,通过计算机辅助设计,能找出满足高效、 低成本、高利润和达到表面质量要求的一组最佳的切削用 量参数。实际切削用量的优化过程就是建立优化目标的数 学模型,用计算机求极值。主要目标函数有三个。
床功率是否允许。 在实际生产中,切削用量的合理选择,既可参照有关 手册的推荐数据,也可凭经验根据选择原则确定。
1.3车削用量的合理选择例题
切削用量的合理选择
切削用量的合理选择切削用量的合理选择(2021-07-1315:37:22)标签:刀具寿命用量生产率切削性能杂谈分类:数控刀具技术切削用量不仅就是在机床调整前必须确认的关键参数,而且其数值合理是否对加工质量、加工效率、生产成本等有著非常关键的影响。
所谓“合理的”切削用量就是指充分利用刀具切削性能和机床动力性能够(功率、扭矩),在保证质量的前提下,赢得低的生产率和高的加工成本的切削用量。
一制订切削用量时考虑的因素切削加工生产率在焊接加工中,金属切除率与切削用量三要素ap、f、v均维持线性关系,即为其中任一参数减小一倍,都可以并使生产率提升一倍。
然而由于刀具寿命的制约,当任一参数减小时,其它二参数必须增大。
因此,在制定切削用量时,三要素获得最佳女团,此时的高生产率才就是合理的。
刀具寿命切削用量三要素对刀具寿命影响的大小,按顺序为v、f、ap。
因此,从保证合理的刀具寿命出发,在确定切削用量时,首先应采用尽可能大的背吃刀量;然后再选用大的进给量;最后求出切削速度。
加工表面粗糙度精加工时,减小进给量将减小加工表面粗糙度值。
因此,它就是精加工时遏制生产率提升的主要因素。
二刀具寿命的选择原则切削用量与刀具寿命存有密切关系。
在制订切削用量时,应当首先挑选合理的刀具寿命,而合理的刀具寿命则应当根据优化的目标而的定。
通常分后最低生产率刀具寿命和最高成本刀具寿命两种,前者根据单件工时最少的目标确认,后者根据工序成本最高的目标确认。
挑选刀具寿命时可以考量如下几点:根据刀具复杂程度、制造和磨刀成本来选择。
复杂和精度高的刀具寿命应选得比单刃刀具高些。
对于机夹可以移调刀具,由于再加刀时间长,为了充分发挥其切削性能,提升生产效率,刀具寿命附加得高些,通常挑15-30min。
对于装刀、换刀和调刀比较复杂的多刀机床、组合机床与自动化加工刀具,刀具寿命应选得高些,尤应保证刀具可靠性。
车间内某一工序的生产率管制了整个车间的生产率的提升时,该工序的刀具寿命必须挑选得高些;当某工序单位时间内所分摊至的全厂支出m很大时,刀具寿命也高文瑞得高些。
切削用量的选择和计算公式
切削用量的选择和计算公式切削用量的选择和计算是机械加工中非常重要的一环,它直接影响到加工效率、加工质量和工具的使用寿命。
正确选择和计算切削用量可以使加工过程更加稳定和高效。
本文将介绍切削用量的选择和计算公式,并探讨其在机械加工中的应用。
切削用量的选择。
切削用量是指在切削加工过程中,刀具与工件之间的相对运动距离。
切削用量的选择需要考虑到工件材料、刀具材料、切削速度、进给速度等因素。
一般来说,切削用量越大,切削效率越高,但是过大的切削用量会导致刀具磨损加剧,甚至损坏刀具。
因此,在选择切削用量时需要在保证加工效率的前提下,尽量减小刀具的磨损。
切削用量的计算公式。
切削用量的计算公式通常包括切削速度、进给速度和刀具的切削刃数。
切削速度是指刀具在工件表面的相对运动速度,通常用Vc表示,单位为m/min。
进给速度是指刀具在工件表面的进给速度,通常用f表示,单位为mm/r。
刀具的切削刃数是指刀具上切削刃的数量,通常用z表示。
根据切削速度、进给速度和刀具的切削刃数,切削用量的计算公式可以表示为:切削用量 = 切削速度×进给速度×刀具切削刃数。
在实际应用中,切削用量的计算公式可以根据具体的加工情况进行调整,以满足加工的要求。
切削用量的应用。
切削用量的选择和计算在机械加工中具有重要的应用价值。
正确选择切削用量可以提高加工效率,降低成本,提高产品质量。
同时,合理的切削用量还可以延长刀具的使用寿命,减少刀具的更换次数,降低加工成本。
在实际加工中,切削用量的选择和计算需要结合具体的加工情况进行调整。
例如,在加工硬质材料时,可以适当增大切削用量,以提高加工效率;在加工精密零件时,可以适当减小切削用量,以保证加工精度。
此外,切削用量的选择还需要考虑到刀具的类型、刀具的磨损情况、工件的材料和形状等因素。
总之,切削用量的选择和计算是机械加工中非常重要的一环。
正确选择和计算切削用量可以提高加工效率、降低成本、提高产品质量。
数控切削用量的选择方法
1.切削用量的选择原则切削用量的选择,对生产效率、加工成本和加工质量均有重要影响。
所谓合理的切削用量是指在保证加工质量的前提下,能取得较高的生产效率和较低成本的切削用量。
约束切削用量选择的主要条件有:工件的加工要求,包括加工质量要求和生产效率要求;刀具材料的切削性能;机床性能,包括动力特性(功率、扭矩)和运动特性;刀具寿命要求。
(1)切削用量与生产效率、刀具寿命的关系机床切削效率可以用单位时间内切除的材料体积 (mm3/min)表示,切削用量三要素均与呈正比关系,三者对机床切削效率影响的权重是完全相同的。
从提高生产效率考虑,切削用量三要素中任一要素提高一倍,机床切削效率都提高一倍,但提高一倍与提高一倍对刀具寿命带来的影响却是完全不相同的。
切削用量三要素中对刀具寿命影响最大的是背吃刀量,其次是进给量,再其次是切削速度;在保持刀具寿命一定的条件下,提高背吃刀量比提高进给量的生产效率高,比提高切削速度的生产效率更高。
(2)切削用量的选用原则选择切削用量的基本原则是:首先选取尽可能大的背吃刀量;其次根据机床进给机构强度、刀杆刚度等限制条件(粗加工时)或已加工表面粗糙度要求(精加工时),选取尽可能大的进给量f;最后根据查取或根据公式计算确定切削速度。
(3)切削用量三要素的选用1)背吃刀量背吃刀量根据加工余量确定。
粗加工时,只要机床功率许可,粗加工余量应争取在一次走刀中全部切除。
下面几种情况,可几次走刀分切:①加工余量太大,导致机床动力不足或刀具强度不够;②工艺系统刚性不足;③断续切削。
切削表层有硬皮的锻铸件或切削冷硬倾向较为严重的材料(例如不锈钢)时,应尽量使值超过硬皮或冷硬层深度,以防刀具过快磨损。
半精加工时,可取为0.5~2mm 。
精加工时,可取0.1~0.4 。
2)进给量粗加工时,对表面质量没有太高要求,合理的进给量应是工艺系统所能承受的最大进给量。
限制粗加工进给量的因素是:机床进给机构的强度、刀杆的强度和刚度、硬质合金或陶瓷刀片的强度等。
第四节 切削用量选择讲解
π dn
切削速度示意图
①车削光轴切削速度 Vs=1000Vc/πd Vs—主轴转速,r/min Vc—切削速度,m/min d—工件待加工表面直径,mm
②车削螺纹主轴转速n 在切削螺纹时,车床的主轴转速过高会使螺
纹破牙,因此对于一般数控车床车螺纹时主轴转 速计算公式:
注意:切断、车槽时的切削深度为车刀主切削刃 的宽度
① 背吃刀量aP(mm)的选择
粗加工(Ra10~80μm)时,一次进给应尽可能切除全部
余量。在中等功率机床上,背吃刀量可达8~l0mm。
半精加工(Ra1.25~l0μm)时,背吃刀量取为0.5~2mm。 精加工(Ra0.32~1.25μm)时,背吃刀量取为
第四节 切削用量的选择
切削用量(又叫切削三要素)是衡量车削运动大小 的参数。
包括: 主轴转速(切削速度) 进给速度(进给量) 背吃刀量(侧吃刀量)
(1) 背吃刀量(切削深度)
切削深度为工件上已加工表面和待加工表面间的 垂直距离,单位为mm。即:ap=(dw-dm)/2 其中:
dw—工件待加工表面的直径,(mm) dm—工件已加工表面的直径,(mm)
表面特征
表面粗糙度值 加工方法举例
明显可见刀痕
Ra100、Ra50、 粗车、粗刨、粗
Ra25、
铣、钻孔
微见刀痕
12.5、Ra6.3、 精车、精刨、精
Ra3.2、
铣、粗铰、粗磨
看不见加工痕迹, Ra1.6、Ra0.8、 微辩加工方向 Ra0.4、
精车、精磨、精 铰、研磨
暗光泽面
Ra0.2、Ra0.1、 研磨、珩磨、超
例3:车削直径为300mm的铸铁带轮外圆,若切削速 度为60m/ min,试求车床主轴转速。
- 1、下载文档前请自行甄别文档内容的完整性,平台不提供额外的编辑、内容补充、找答案等附加服务。
- 2、"仅部分预览"的文档,不可在线预览部分如存在完整性等问题,可反馈申请退款(可完整预览的文档不适用该条件!)。
- 3、如文档侵犯您的权益,请联系客服反馈,我们会尽快为您处理(人工客服工作时间:9:00-18:30)。
切削用量的选择:总的要求
保证安全,不致发生人身事故或设备事故;保证加工质量。 在上述 两项要求的前提下充分发挥机床的潜力和刀具的切 削性能,选用较大的切削用量以提高生产率;不应超负荷 工作,不能产生过大的变形和震动。
切削用量的选择:基本原则
进给量 f
(1)进给量 f 进给量是工件或刀具每转一周时两者沿进给运动方向的 相对位移,单位是mm/r(毫米/转) (2)进给速度 Vf 进给速度是单位时间的进给量,单位是mm/min(毫米/分钟)
进给量 f
(3)每齿进给量 fz 对于铣刀、铰刀、拉刀、齿轮滚刀等多刃切削工具,在它们进 行工作时,还规定每一个刀 齿的进给量fz,即后一个刀齿相对于前一个刀齿的进给量,单位 是mm/z(毫米/齿)。
切削用量的确定
前言
切削用量是指切削速度 Vc 、进给量 f (或进给速度Vf ) 、背吃刀量 ap 三者的总称。
切削用量的选择就是确定工序的背吃刀量 ap,进给量 f、 切削速度 Vc,以及刀具耐用度。合理选择切削用量,对充分 发挥机床和刀具的性能,提高生产效率,降低生产成本有很 大的益处。
一、切削用量三要素
1.主轴转速
因数控机床系统和结构等原因,车削螺纹时主轴的 转速有一定的限制,该限制因机床的种类而异。大多数 经济型数控车床的数控系统,推荐切削螺纹时的主轴转 速为:
2.螺纹牙型高度(螺纹总切深)
螺纹牙型高度是指在螺纹牙型上,牙顶到牙底之间 垂直于螺纹轴线的距离。螺纹实际牙型高度可按下式计 算:
h=0.6495P
解:查表得:VC = 55 m/min , fz = 0.1 mm/min 由Vc =πdn/1000 得 n = 1000 Vc/πd n = 1000Vc /πd = 1000*55/(3.14*20)= 875 r/min
Vf=fn=fzzn=0.1*2*875=175mm/min
三、螺纹车削切削用量的确定
3、切削用量对刀具耐用度的影响
(3) 进给量f与刀具耐用度的关系
当增大进给量后,切屑厚度增大,由切屑带着走的热量增 多,同时切屑与前刀面的接触长度增加,散热面积增大。 通过测试得知,切削温度随进给量的增加而升高,但温度 的升高幅度不及切削速度显著。
(4 )背吃刀量ap与刀具耐用度的关系
背吃刀量对切削温度的影响很小。这是因为背吃刀量增大 后,切削区产生的热量虽然成正比增加,但因为切削刃参 加切削工作的长度也成正比增加,从而改善了散热条件, 因此切削温度上升甚微。
(3)进给量 f 工件或刀具每转一周,刀具与工件在进给运动方向上的 相对位移量。
(4)背吃刀量 ap 已加工表面与待加工表面间垂直距离。
(5)进给速度Vf 进给速度是指切削刃上选定点相对工件进给运动的即时 速度。
切削用量、切削用量三要素(vc,f,ap)
切削速度Vc
(1)切削速度 Vc
金属切削过程中,刀具相对于工件的瞬间移动速度。通 常以Vc表示。 切削速度对刀具的使用寿命影响很大,随着切削速度提 高,切削温度提高很快,摩擦加剧,使刀具迅速磨损。
① 采用切削性能更好的新型刀具材料; ② 在保证工件机械性能的前提下,改善工件材料加工性; ③ 改善冷却润滑条件; ④ 改进刀具结构,提高刀具制造质量。
作业
1.什么是切削三要素?如何确定?
2.已知:外圆车削,切削前工件直径dw=80mm,要求切削 后工件直径dm=78 mm,一次切除余量,假定工件转速 n=300 r/min,刀具进给速度Vf=60mm/min,求:切削用量 三要素。
4.分段切削背吃刀量
如果牙型较深,螺距较大,可分几次进给。每次进给 背吃刀量用螺纹深度减精加工背吃刀量所得的差按递减规 律分配。
螺纹分段切削示意图 常用螺纹切削进给次数与背吃刀量可参考表3-7~表3-9
总结
1. 切削用量确定的步骤
背吃刀量的选择 →进给量的选择→切削速度的确定→校验 2. 提高切削用量的途径
但是当加工余量太大、加工余量不均匀或工艺系统刚性不 足时,为避免振动需要分两次或多次走刀完成。
提示:在刀具强度,机床刚性保证的情况下,尽可能增加
背吃刀量 ap、进给量 f 、适中的切削速度vc。
2、切削用量对零件精度、表面粗糙度的影响
对零件精度、表面粗糙度,首先从进给量 f (进给速度 Vf)
着手分析,进给量 f 的确定,主要受到表面粗糙度的制约, 为提高零件的粗糙度,进给量必须选择得当。在三要素中,
背吃刀量 ap
二、切削用量的选择
1、 切削用量对劳动生产率的影响
切削用量三要素vc、f 、ap 虽然对加工质量、刀具耐用
度和生产效率均有直接的影响,但影响程度却不同,且它 们又是相互联系,相互制约,不可能都选择的很大,因此, 就存在着从不同角度出发,去优先选择三者之中的某一个 切削要素。
为提高生产效率,可以适当增加背吃刀量ap,减少走刀数,
(1)切削用量及切削用量三要素 切削用量是指切削速度 Vc 、进给量 f (或进给速度Vf )、 背吃刀量ap三者的总称,也称为切削用量三要素。它是调 整刀具与工件间相对运动速度和相对位置所需的工艺参数。 在切削加工中,需要根据不同的工件材料、刀具材料和其 他技术、经济要求来选择适宜的切削用量。
(2)切削速度Vc 金属切削过程中,刀具相对于工件的瞬间移动速度。通常 以Vc表示。
解:由 Vf=fn=fzzn 得 fz=Vf/Zn,Vf=F fz=Vf/Zn=25/(3*200)=0.0416 mm/r Vc= πdn/1000=3.14*20*200/1000=12.566(m/min)
例4:求进给量 F及 转速 n 已知:∮20,2刃硬质合金立铣刀,加工材料:40Cr 求: 进给量F及转速n
吃刀量 ap 通常根据加工余量确定,在吃刀量和进给量确定
后,在保证刀具的耐用度的前提下,确定合理的切削速度 vc 。
3、 切削用量对刀具耐用度的影响 (1)刀具耐用度 所谓刀具耐用度,是指一把新刀从开始切削直到磨损量 达到磨损标准为止,在这期间所使用的总的切削时间, 用T表示。
(2) 切削速度vc与刀具耐用度的关系 切削速度是影响刀具耐用度的主要因素,其原因是当提高 切削速度时,单位时间的金属去除率会成正比例增加,刀 具与工件间的摩擦加剧,消耗于金属变形和摩擦的无用功 增加,因而产生过多的热量。因此,提高切削速度的结果 是:摩擦热大量的积聚在切屑底层而来不及传导出去,从 而使切削温度急剧升高,使刀具的耐用度大大降低。
切削速度Vc
(2)切削速度 Vc 计算公式 Vc=π*d*n
π是圆周率,取3.14 d 是工件直径或刀具直径,单位是:毫米 n是转速,单位是:转/分
一般Vc的单位用米/分,而d的单位一般用毫米,所以有 时候也写成:
Vc=π*d*n/1000 在加工中,切削线速度Vc和工件直径d(或刀具直径d) 及转速n成正比。所以在切削速度一定的情况下,工件 或刀具直径越大,在加工时通常要采用较低的转速。
解:由Vc=πdn/1000 得 n=1000Vc/πd
n=1000Vc/πd=1000*180/(3.14*30) =1910r/min
例3:求进给量 fz 及 Vc 已知:∮20 高速钢立铣刀,转速n=200r/min, F=25mm/min,加工材料:40Cr
求: 每齿进给量 fz ,切削速度 Vc
精车进给量参数表
铣削钢的进给量参数表
切削参数表
切削参数表
实例
例1:计算切削速度Vc 已知: d=20 mm, n=1500r/min, 求Vc
解:Vc= πdn/1000=3.14*20*1500/1000=94.2(m/min) 例2:求转速n 已知:Vc=180 m/min d=30mm 求:转速n
切削用量的选择:吃刀量的选择
背吃刀量根据加工余量确定。 ★ 在粗加工时,一次走刀应尽可能切去全部加工余量。
★下列情况可分几次走刀:
① 加工余量太大,一次走刀切削力太大,会产生机床功率不足或刀具强 度不够时;
② 工艺系统刚性不足,或加工余量极不均匀,以致引起很大振动时,如 加工细长轴或薄壁工件;
③ 断续切削,刀具受到很大的冲击而造成打刀时。
★ 分二次走刀,第一次的ap应比第二次大,第二次的ap可取加工余量 的1/3~1/4左右。 ★ 切削表层有硬皮的铸锻件或切削不锈钢等冷硬较严重的材料时,应 尽量使背吃刀量超过硬皮或冷硬层厚度,以防刀刃过早磨损或破损。 ★在半精加工时,ap=0.5~2 mm 。 ★在精加工时,ap=0.1~0.4 mm 。
(4)进给速度 Vf 计算公式
Vf = fn = fzzn
背吃刀量 ap (1)背吃刀量 背吃刀量ap为工件上已加工表面和待加工表面间的垂直距 离,单位为mm.
(2)背吃刀量的计算方法
外圆柱表面车削的背吃刀量:ap=(dw-dm)/2(mm) 钻孔加工的背吃刀量为:ap=dm/2(mm) 其中:dm已加工表面直径(mm) dw待加工表面直径(mm)
切削用量的选择:进给量的选择
粗加工时,对工件表面质量没有太高要求,这时切削力往 往很大,合理的进给量应是工艺系统所能承受的最大进给 量。这一进给量要受到下列一些因素的限制:机床进给机 构的强度、刀具的强度和刚度、硬质合金或陶瓷刀片的强 度及工件的装夹刚度等。
精加工时,最大进给量主要受加工精度和表面粗糙度的限制。
实际生产中,进给量常常根据经验选取。然而,按经验 确定的粗加工进给量在一些特殊情况下,如切削力很大、 工件长径比很大、刀杆伸出长度很大时,有时还需对选 定的进给量进行修正。
切削速度的选择
根据已选定的背吃刀量 ap、进给量 f,查《切削手册》可得切削 速度 Vc
① 粗加工时,ap 、f 较大,所以Vc较低,精加工时,ap 、f较小,所以 Vc较高。 ② 工件材料强度、硬度较高时,应选较低的Vc;反之,Vc较高。 ③ 刀具材料的切削性能愈好,Vc也选得愈高。