NC数控加工
数控加工程序NC
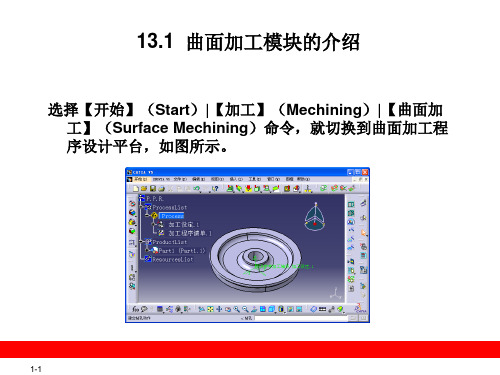
(5)单击【确定】按钮,完成毛坯的建立。
1-19
13.7.2 插入STL档案
【插入STL档案】工具,是将STL数据文件插入到零件中的 工具。该工具的操作步骤如下所示:
(1)单击【几何管理】工具栏上的【插入STL档案】工具 按钮,系统弹出STL档案输入对话框,如图13.49所示;
(2)单击【目的地】文本框,选择插入STL文件的位置; (3)单击【STL档案】文本框右侧按钮,选择STL档案; (4)单击【确定】按钮,完成STL档案的插入。
1-17
13.7 辅助几何元素
在建立加工操作过程中,需要用到一些辅助几何元素。本小 节将介绍如何建立零件上的毛坯、偏置的毛坯以及点、 线等参考元素。将使用到【几何管理工】具栏,如图 13.46所示。
1-18
13.7.1 建立毛坯零件
【建立生料】工具,是在零件周围建立最小的长方体毛坯的 工具。该工具的使用步骤如下所示:
1-2
13.3 建立制造程序
制造程序包括零件作业(PO):设定加工零件依附于特定 机器,并整合各辅助图素,治具等给予各种机器作业( 制造程序及加工法)设定;制造程序:用于安排NC加工 作业的流程,在各制造程序内包含程序的设定,辅助设 定等。经过计算与处理可以产生加工程序码。
数控加工技术概述

刀架); ➢铣镗钻磨复合—复合加工中心(ATC,动力磨头); ➢可更换主轴箱的数控机床—组合加工中心;
1.2 数控机床的产生与发展
۞控制智能化
随着人工智能技术的不断发展,并为满足制 造业生产柔性化、制造自动化发展需求,数控 技术智能化程度不断提高,具体体现在以下几 个方面:
3. 数控加工编程基础
3.1 机 床 坐 标 系
3.1.1 机床坐标系和主运动方向 1.标准坐标系的规定
对数控机床中的坐标系和运动方向的命名,ISO标准和我 国JB3052—82部颁标准都统一规定采用标准的右手笛卡儿直 角坐标系,一个直线进给运动或一个圆周进给运动定义一个 坐标轴。
(3)由于机床自动化程度大大提高,减轻了工人劳动强度, 改善了劳动条件
(4)加工能力提高,应用数控机床可以很准确的加工出曲线、 曲面、圆弧等形状非常复杂的零件,因此,可以通过编写 复杂的程序来实现加工常规方法难以加工的零件
1.5 数控系统的组成
现 代 数 控 机 床 一 般 由 数 控 装 置 (NC unit) 、 伺 服 系 统 (servo system) 、 位 置 测 量 与 反 馈 系 统 (feedback system)、辅助控制单元(accessory control unit)和机 床主机(main engine)组成,下图是各组成部分的逻辑结 构简图:
2.6 数控加工原理(续)
•当 F>0 时 , NC 发 出 移 动 微 指 令 , 使 控 如 如制何图轴确所向定示控,+制刀X轴具方X由、向OZ至移的A走,动向直一呢线?个OA是步其长理论;轨迹。 •当用F逐<点0比时较,法:N每C走发一出步与移理动论轨微迹指比较令一,下,使 控从制而轴确向定下+一Z步方的向走移向。动一个步长; •当起 于F点是=坐直0标线时(OA,0的,方可0程)以,为规终:点 X定/Z坐=NX标eC/(Z使eXe;,控Ze)制轴向 + X即或:+ZXeZ-方XZe向=0;移动一个步长 这 ① ②样可若 若点点以((不XX,,ZZ断))在在地直 直趋线 线向上 下方 方终, ,点则 则: :,ZZ图XXee--中XXZZee,><00;;带 箭 于头是的:折取F线=ZX轨e-X迹Ze是, 机床实际运动的插 补 在 由轨N插迹C判补,断运F算直的过符线程号O中。,A控是制理轴论每移轨动迹一,步之由前于,插先 补运算所取的步长很小,所以可以近 似地认为插补轨迹就是直线OA的理论
数控加工程序(NC)设计

确定加工工艺和切削参数
根据工件材料、加工要求和机床性能, 选择合适的刀具、切削参数和加工工 艺。
建立工件几何模型
根据设计图纸或实体的测量数据,使 用CAD软件建立工件的三维几何模型。
生成。
验证与优化
通过模拟仿真或试切实验,验证NC 程序的正确性和加工效果,根据需要 进行调整和优化。
进一步加工工件表面,为精加 工做准备。
精加工
达到最终尺寸和表面质量要求 的加工。
优化加工顺序
遵循先粗后精、先主后次、先 面后孔的原则。
合理使用G代码和M代码
G代码用于控制机床的移动和切削参数。
M代码用于控制机床辅助功能,如冷却液和主轴 转速。
根据加工需求选择合适的G代码和M代码,提高加 工精度和效率。
02
它具有高精度、高效率、高柔性 等特点,广泛应用于机械制造、 航空航天、汽车、模具等领域。
NC程序在数控加工中的作用
NC程序是数控加工的核心,它通过一 系列代码指令控制机床的运动和加工 过程。
NC程序能够精确地描述工件的几何形 状、加工工艺和切削参数,从而实现 高精度、高效率的加工。
NC程序的设计流程
复杂曲面加工的NC程序
总结词
用于加工复杂曲面的NC程序,如球面、 抛物面和自由曲面。
VS
详细描述
复杂曲面加工的NC程序需要使用更高级 的编程语言,如CAM软件,通过定义复 杂的刀具路径和切削参数,实现复杂曲面 的加工。
多轴联动加工的NC程序
总结词
用于加工多轴联动零件的NC程序,如斜面、 曲面和异形零件。
02 NC程序的基本结构与元 素
程序头和程序尾
程序头
通常包含程序名称、程序编号、 编程者信息等,用于标识程序的 来源和用途。
nc程序讲解

nc程序讲解NC程序是数控机床加工过程中的一种控制指令,用于告诉机床如何进行加工。
下面是对NC程序的讲解:1. 程序格式:NC程序由一系列的指令组成,每条指令占一行。
指令由字母、数字和符号组成,可以使用空格或制表符进行分隔。
2. 指令分类:根据功能的不同,NC程序可以分为几何指令、辅助功能指令和机床控制指令。
- 几何指令用于描述加工图形的形状和尺寸,如直线插补、圆弧插补等。
- 辅助功能指令用于控制机床的辅助功能,如刀具半径补偿、切削速度等。
- 机床控制指令用于控制机床的动作,如进给速度、主轴转速等。
3. 坐标系:NC程序中使用坐标系来描述加工零件的位置和运动。
常用的坐标系有绝对坐标系和相对坐标系。
- 绝对坐标系是以机床坐标原点为参考点,确定零件位置和运动的坐标系。
- 相对坐标系是以当前位置为参考点,确定零件位置和运动的坐标系。
4. 指令示例:下面是一个简单的NC程序示例,用于描述机床沿x轴方向进行直线插补运动。
N10 G00 X10 Y20 ;快速定位到起始点N20 G01 X50 Y20 F100 ;以给定进给速度进行直线插补N30 M30 ;程序结束- N10是程序起始行号,用于标识程序的执行顺序。
- G00是快速定位指令,用于将机床迅速移动到指定位置。
- X10 Y20表示目标位置的坐标。
- N20是下一条指令的行号。
- G01是直线插补指令,用于按给定速度和轨迹进行直线插补运动。
- F100表示进给速度为100。
- N30是下一条指令的行号。
- M30是程序结束指令,用于标识程序的结束。
以上是对NC程序的基本讲解,NC程序的具体内容和格式还有很多,需要根据具体机床和加工要求进行编写。
nc程序的名词解释

nc程序的名词解释NC程序,即数控程序,是一种调控机床进行加工工作的程序。
通过编写NC程序,可以精确控制机床在指定坐标轴上的运动以及实施各种加工操作,例如切削、钻孔、铣削等。
在现代制造业中,NC程序发挥着重要的作用,为自动化生产提供了便捷和高效的方式。
1. NC程序的历史起源NC程序的发展与计算机技术的进步密切相关。
20世纪50年代初,人们开始尝试使用计算机对机床进行控制。
最初的NC程序由串联的数字信号编码指令组成,用于控制机床的运动。
随着计算机技术的飞速发展,NC程序逐渐演变为具有更强大功能和灵活性的指令系统,并且现代的NC程序通常采用G代码和M代码进行编写。
2. G代码:控制机床的运动G代码是NC程序中最常用的指令之一,用于控制机床在各个坐标轴上的直线、圆弧等运动。
G代码中的指令可以指定机床的起点、终点、切削速度、切削深度等参数,从而实现精确的加工操作。
例如,G01指令表示进行直线插补,G02和G03指令分别表示进行顺时针和逆时针的圆弧插补。
3. M代码:控制机床的功能M代码用于控制机床的具体功能和附件操作。
比如,M03表示启动主轴的正转,M04表示启动主轴的反转,而M05表示停止主轴运转。
此外,M代码还可以控制冷却液的供给、刀具的换刀、进给轴的暂停等功能,提供了更多灵活的操作方式。
4. 坐标系:标定机床的位置坐标系是NC程序中至关重要的概念,用于标定机床的位置和方向。
常用的坐标系有绝对坐标系和相对坐标系。
绝对坐标系是以机床的参考点为原点,通过设定坐标轴的长度来确定机床各个位置的坐标。
相对坐标系则是以当前机床的位置为参照点,按照相对偏移量进行定位。
5. 其他辅助指令除了G代码和M代码外,NC程序还包含一些辅助指令,用于实现更全面的控制和管理。
例如,F指令用于设定切削进给速度,S指令用于设置主轴转速,T指令用于选择刀具。
这些辅助指令可以根据具体加工要求进行灵活调整,提高加工效率和质量。
6. NC程序编写和优化编写一个高效的NC程序是一项挑战性的工作。
NC与CNC的区别是什么2

NC与CNC的区别是什么?NC machine tool 数控机床NC用数字信息对机床运动及其加工过程的进行控制的一种技术,为硬线数控装置,她的输入处理、插补运算和控制功能,都由专用的固定组合逻辑电路来实现,不同功能的机床,其组合逻辑电路也不同。
改变或增减控制、运算功能时,需要改变数控装置的硬件电路。
因此通用性、灵活性差,制造周期长,成本高;CNC(Computer Numerical Control),是以计算机为核心的数控系统,为软线数控装置。
这种数控装置的硬件电路是由小型或微型计算机再加上通用或专用的大规模集成电路制成,数控机床的主要功能几乎全部由系统软件来实现,而修改或增减系统功能时,也不需变动硬件电路,只需改变系统软件。
因此,具有较高的灵活行,同时由于硬件电路基本上是通用的,这就有利于大量生产,提高质量和可靠行,缩短制造周期和降低成本。
CNC装置主要由哪几部分组成?. 答:计算机数控装置主要由计算机系统,位置控制板,PLC接口板,通信接口板,扩展功能模块,控制软件块组成。
Climb milling: 顺铣铣刀对工件的作用力在进给方向上的分力与工件进给方向相同的铣削方式。
Conventional milling: 逆铣铣刀对工件的作用力在进给方向上的分力与工件进给方向相反的铣削方式。
顺铣与逆铣的区别:A 顺铣:铣刀对工件作用力 Fc在垂直方向分力 FN始终向下,对工件起压紧作用,切削平稳,适于不易夹紧或细长薄板形工件。
逆铣:垂直分力FN向上,工件需较大的夹紧力。
B 顺铣:铣刀刀刃切入工件初,切屑厚度最大,逐渐减小到0。
后刀面与已加工表面挤压、摩擦小,刀刃磨损慢,表面质量好。
逆铣:切屑厚度从0到最大,因刀刃不能刃磨绝对锋利,故开始时不能立即切入工件,存在对工件挤压与摩擦。
工件出现加工硬化,降低表面质量。
此外,刀齿磨损快耐用度降低。
C 顺铣:水平分力Ff与工作台进给方向相同,当工作台进给丝杠与螺母间隙较大,工作台易出现轴向窜动。
NC加工编程

1.NC加工编程随着数控加工技术的普及,技术市场上对NC编程人员的需求量也呈现出快速增长的势头。
从技术特点上看,NC编程比三维造型更程式化,即它的实现过程相对来说更模式化一些。
然而,要想成为一个优秀的NC编程人员也并非一件易事。
高水平的NC程序员应当具备以下的条件:(1)掌握一定的基础知识,包括数控机床基本结构、 NC加工基本原理、机械加工工艺及必要的CAD基础等;(2)全面地理解和掌握 NC编程的基本过程和关键技术。
(3)熟练运用一种CAD/CAM软件;(4)有丰富的实际加工经验。
有时,还需要掌握一些相关学科的知识和经验(如模具等)。
数控编程种类较多,如数控铣、车、钻等。
由于其中以三坐标数控铣最为常用,因此将予以重点介绍。
在以后的文章中,如无特别说明则NC编程均指对三坐标数控铣加工的编程。
应当指出的是,NC编程是一门经验性很强的技术,仅靠书面的学习是远远不够的,更重要的是在实践中不断总结和提高。
本文主要介绍NC编程的一般技术要求、操作过程和技术要点。
2 NC程序的质量标准程序的质量标准我们认为,判别一个NC程序员水平的依据主要有以下几条:(1)NC程序的质量;(2)NC编程的工作效率;(3)NC编程的可靠性和规范化程度(包括工艺规划、数据文件管理、保存和交接的规范化程度等)。
其中,NC程序的质量是衡量NC程序员水平的关键指标,其判定标准又可归纳为:(1)完备性:即不存在加工残留区域。
(2)误差控制:包括插补误差控制、残余高度(表面粗糙度)控制等。
(3)加工效率:即在保证加工精度的前提下加工程序的执行时间。
(4)安全性:指程序对可能出现的让刀、漏刀、撞刀及过切等不良现象的防范措施和效果。
(5)工艺性:包括进退刀设置、刀具选择、加工工艺规划(如加工流程及余量分配等)、切削方式(刀轨形式选择)、接刀痕迹控制以及其它各种工艺参数(如进给速度、主轴转速、切削方向、切削深度等)的设置等。
(6)其它:如对机床及刀具的损耗程度、程序的规范化程度等。
nc 常用计算公式

nc 常用计算公式NC常用计算公式。
在数控加工领域,常用的计算公式是非常重要的工具,它们可以帮助工程师和操作人员快速准确地进行计算,从而保证加工的精度和效率。
本文将介绍一些常用的NC计算公式,希望能对大家有所帮助。
1. 切削速度公式。
切削速度是指工件在切削过程中单位时间内被切削下来的长度,通常用m/min来表示。
切削速度公式为:Vc = π×D×n。
其中,Vc为切削速度,D为刀具直径,n为主轴转速。
通过这个公式,我们可以根据刀具直径和主轴转速来计算出切削速度,从而选择合适的切削参数。
2. 进给速度公式。
进给速度是指工件在切削过程中单位时间内沿着切削方向移动的距离,通常用mm/min来表示。
进给速度公式为:F = f×n×z。
其中,F为进给速度,f为每齿进给量,n为主轴转速,z为刀具齿数。
通过这个公式,我们可以根据每齿进给量、主轴转速和刀具齿数来计算出进给速度,从而确定合适的进给参数。
3. 主轴转速公式。
主轴转速是指主轴每分钟旋转的圈数,通常用r/min来表示。
主轴转速公式为:n = 1000×Vc/(π×D)。
其中,n为主轴转速,Vc为切削速度,D为刀具直径。
通过这个公式,我们可以根据切削速度和刀具直径来计算出主轴转速,从而确定合适的主轴转速参数。
4. 加工时间公式。
加工时间是指完成一道工序所需的时间,通常用分钟来表示。
加工时间公式为:T = L/F。
其中,T为加工时间,L为工件长度,F为进给速度。
通过这个公式,我们可以根据工件长度和进给速度来计算出加工时间,从而合理安排生产计划。
5. 切削力公式。
切削力是指刀具在切削过程中对工件所施加的力,通常用N来表示。
切削力公式为:Fc = k×ap×f。
其中,Fc为切削力,k为切削力系数,ap为切削深度,f为进给量。
通过这个公式,我们可以根据切削力系数、切削深度和进给量来计算出切削力,从而选择合适的刀具和加工参数。
- 1、下载文档前请自行甄别文档内容的完整性,平台不提供额外的编辑、内容补充、找答案等附加服务。
- 2、"仅部分预览"的文档,不可在线预览部分如存在完整性等问题,可反馈申请退款(可完整预览的文档不适用该条件!)。
- 3、如文档侵犯您的权益,请联系客服反馈,我们会尽快为您处理(人工客服工作时间:9:00-18:30)。
基于Pro/E的数控加工实例
1、数控加工概述
Pro/E 提供了数控加工模块Pro/E NC,运用该模块可进行模具各零件的CAM,通过对加工模型、工件、刀具、机床及加工参数等进行合理的设置,经Pro/E NC处理为刀位数据文件;通过模拟加工,检测加工中的误差、干涉及过切等问题,设计出合理的制造流程文件;通过Pro/E NC后置处理模块,生成能驱动数控机床加工的数控代码,从而完成零件的数控加工过程。
2、Pro/E NC加工步骤
Pro/E NC设计加工程序的流程与实际加工的思维逻辑是相似的。
Pro/E NC有多种加工方法,可满足加工中的多种需要,它们设置加工的步骤基本相同,总结如下:
(1) 建立数控加工文件。
(2) 创建制造模型。
(3) 定义操作。
(4) 选择加工方法。
(5) 定义刀具。
(6) 定义加工参数。
(7) 选择加工区域。
(8) 显示刀具轨迹。
(9) 生成数控代码。
3、Pro/E NC加工法
Pro/E NC加工法包括:车削加工、铣削加工、线切割、雕刻加工等。
注塑模主要采用铣削加工,重点介绍铣削加工。
依次点击【制造/加工/辅助加工】命令,系统弹出Pro/E NC 加工菜单,常用的铣削加工方法有以下几种:
【体积块】:又称等高铣削。
【曲面铣削】:用于水平或倾斜曲面的铣削。
【表面】:用于平面的精铣。
【轮廓】:用于轮廓曲面的精、粗加工。
【轨迹】:用于较规则轮廓面的铣削。
【孔加工】:用于模板孔系的加工。
【螺纹】:用于螺纹的铣削。
4、建立加工模型
1)建立加工文件
单击文件工具栏中的(新建)按钮新建一个制造类型文件,弹出“新建”对话框。
选中“类型”选项栏中的“制造”单选钮,选中“子类型”选项栏中的“NC组件”单选钮,并在“名称”文本框中输入“xiangkuai”作为文件名进行保存,把“使用缺省模块”勾去,单击按钮,系统弹出“新文件选项”对话框,选择“mmns-mfg-nc”,单击“新文件选项”对话框的按钮。
2)创建制造模型
如图1所示,依次单击“制造模型”→“装配”→“参考模型”命令,打开如图2的镶块参考模型,单击“完成/返回”命令。
在没有特殊要求的情况下,可以不建立工件这一可选项,至此制造模型建立完成。
图1 制造菜单图2 参考模型
在系统弹出的【元件放置】对话框中,单击图标按钮,【元件参照】和【组件参照】选项接受系统默认的设置,【约束】栏显示为【固定】,单击【确定】按钮,再单击【菜单管理器】中的【完成/返回】选项。
3)制造设置
①单击“制造设置”命令,弹出如图3所示的对话框,单击对话框中的(打开机床对话框)按钮,弹出“机床设置”对话框进行机床设置,如图4填写对话框中的各项参数。
填完后单击“切削刀具”选项卡,单击(打开切削刀具设置对话框)
按钮进行刀具设置。
当然,刀具设置也可在后续的NC序列中进行。
图3 “操作设置”对话框
图4 “机床设置”对话框
②刀具设置如图5所示,其中HSS为高速工具钢,其他选项卡
可暂时不进行设置。
设置完后单击按钮,最后单击
按钮完成刀具设置。
单击“机床设置”对话框中的按钮
完成机床设置。
图5 “刀具设置”对话框
③单击“一般”选项卡中“参照”选项栏中的按钮以确定工件的加工零点。
如图6所示,单击“选取”命令,系统提示“选取一个坐标系”。
选择图形区中的CSO坐标系,如图7。
图6 选取坐标系菜单图7 完成的坐标系
④单击“一般”选项卡中的“推刀”选项栏中的按钮以确定退刀平面,弹出如图8所示的“退刀选取”对话框。
在“输入
Z深度”文本框中输入10,单击按钮,建立的退刀面
如图9所示。
图8 “退刀选取”对话框图9 建立的退刀面
4)创建NC序列
①单击“制造”菜单中的“加工”→“NC序列”命令,弹出“辅助加工”菜单,单击“轮廓”→“完成”命令,如图10所示。
显示如图11所示的“序列设置”菜单,单击“完成”命令。
图10 “辅助加工”菜单图11 “NC序列”菜单
②单击“制造参数”菜单中“设置”命令,弹出“参数树”对话框,各参数设置如图12所示。
图12 “参数树”对话框
③单击“曲面拾取”菜单中的“模型”→“完成”命令,系统提示“选取要加工模型的曲面”。
选择零件的竖直侧面,如图13。
再单击完成“选取”→“完成”→“完成/返回”命令。
图13 选择加工曲面
④演示刀具路径轨迹
单击【菜单管理器】中的【制造/加工/NC序列/演示轨迹/屏幕演示】选项。
系统弹出【播放路径】对话框。
刀位轨迹菜单设置
刀位轨迹演示如图所示。
单击【播放路径】对话框中的【文件/保存】命令,保存本序列的刀位文件,再单击【关闭】按钮。
图14 “演示路径”对话框
5)后置处理
①单击“制造”→“CL数据”→“输出”→“选取一”→“操作”→“op01”命令,单击“文件”命令,如图15,图16。
图15 “轨迹”菜单 图16 “后置处理选项”菜单 ② 弹出如图17所示“后置处理列表”菜单,单击“UNCX01.P12”,关闭“信息窗口”。
单击“轨迹”菜单中的“确认输出”命令,再单击“CL 数据”菜单中的“完成/返回”命令。
完成后置处理后,可在工作目录中用记事本程序打开op010.tap 文件,查看生成的NC 程序,如图18。
图17 “后置处理列表”菜单
图18 生成的NC程序。