沙钢5800m_3高炉供料系统工艺特点_范小刚
天丰3#580m3高炉增产降耗生产实践
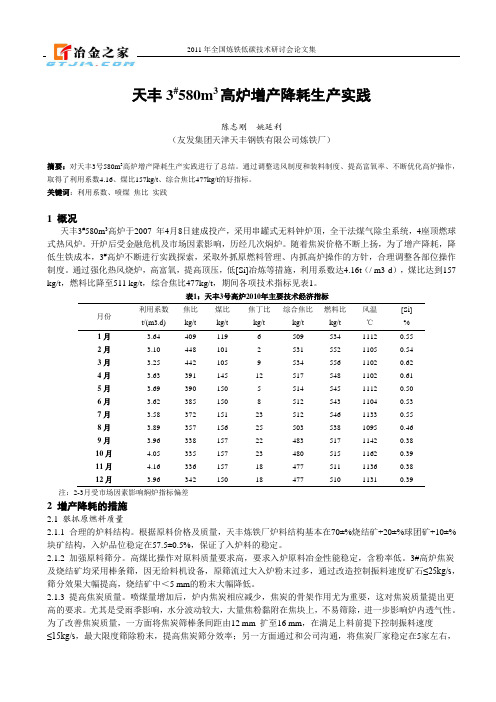
天丰3#580m3高炉增产降耗生产实践陈志刚姚廷利(友发集团天津天丰钢铁有限公司炼铁厂)摘要:对天丰3号580m3高炉增产降耗生产实践进行了总结。
通过调整送风制度和装料制度、提高富氧率、不断优化高炉操作,取得了利用系数4.16、煤比157kg/t、综合焦比477kg/t的好指标。
关键词:利用系数、喷煤焦比实践1 概况天丰3#580m3高炉于2007 年4月8日建成投产,采用串罐式无料钟炉顶,全干法煤气除尘系统,4座顶燃球式热风炉。
开炉后受金融危机及市场因素影响,历经几次焖炉。
随着焦炭价格不断上扬,为了增产降耗,降低生铁成本,3#高炉不断进行实践探索,采取外抓原燃料管理、内抓高炉操作的方针,合理调整各部位操作制度。
通过强化热风烧炉,高富氧,提高顶压,低[Si]冶炼等措施,利用系数达4.16t(/ m3·d),煤比达到157 kg/t,燃料比降至511 kg/t,综合焦比477kg/t,期间各项技术指标见表1。
表1:天丰3号高炉2010年主要技术经济指标月份利用系数焦比煤比焦丁比综合焦比燃料比风温[Si] t/(m3.d) kg/t kg/t kg/t kg/t kg/t ℃%1月 3.64 409 119 6 509 534 1112 0.552月 3.10 448 101 2 531 552 1105 0.543月 3.25 442 105 9 534 556 1102 0.624月 3.63 391 145 12 517 548 1102 0.615月 3.69 390 150 5 514 545 1112 0.506月 3.62 385 150 8 512 543 1104 0.537月 3.58 372 151 23 512 546 1133 0.558月 3.89 357 156 25 503 538 1095 0.469月 3.96 338 157 22 483 517 1142 0.3810月 4.05 335 157 23 480 515 1162 0.3911月 4.16 336 157 18 477 511 1136 0.3812月 3.96 342 150 18 477 510 1131 0.39 注:2-3月受市场因素影响焖炉指标偏差2 增产降耗的措施2.1 狠抓原燃料质量2.1.1 合理的炉料结构。
沙钢5800高炉投产20月实绩(刘琦)讲解

2011.02 56.94 4.91 10.37 1.79 8.68 1.71 2.11 79.34 4.50 22.46
2010年11月份开始,采用小烧结矿分级入炉,对槽下 烧结矿筛网进行改造,取4~6mm的烧结矿作为小矿入炉。
1.2.3 球团矿 沙钢球团矿一般为12%澳球+12%自产球团,自产球
富氧
铁水
指标
富氧量 富氧率 温度 Si
S
炉渣
CaO
SiO2
R2
Al2O3
Mg O
单位 m3/h
%
℃
%
%
%
%
%
%
%
实绩 45010.5 9.83 1493 0.37 0.03 38.78 33.18 1.169 14.11 9.15
三 关于技术思路的讨论
1. 关于精料 1.1 理念和措施 1.1.1 巨型高炉必须精料 1.1.2 并非高不可攀 1.1.3 多种措施适应高炉需求 1.2 树立精料理念的实践过程 1.2.1 焦炭 1.2.1.1 开炉初期干熄焦未跟上,焦炭质量欠佳。加之 精料理念不牢,高炉指标提升过程中,常随焦炭质量的 变化而波动。如2009年11月初到2010年01月初出现过 “三上两下”。
日产量 t
13500 14000 14500 15 m3/h 45000 49000 54000 59000
需风量 m3/min
7635 7794 7826 7856
炉腹煤气量 m3/min 14347 14673 14878 15081
湿法:PW环缝洗涤装置 TRT:装机容量32500KW,透平机由日本三井公司引进 8. 鼓风机 风机规格型号:AV100-17,QA=10500Nm3/min,PA=0.55Mpa
沙钢集团2500m3高炉热风炉烘炉方案介绍

沙钢集团2500m3高炉热风炉烘炉方案1、意义和目的热风炉砌筑完毕后,在高炉投产前,对其进行烘炉作业,主要目的是为了脱去耐火砌体的水份,并使其升温,具备向高炉输送热风的能力,为保证烘炉时使水脱尽以及气体在受热膨胀时不影响砌体的稳定,升温过程应缓慢进行,特别对采用硅砖的热风炉而言,因硅砖内残余石英的晶体转换过程中,其膨胀系数较大,导致硅砖的强度消弱,若升温不合理,极易损坏砌体,影响到热风炉以后的寿命,因此,对热风炉的烘炉从升温曲线到制定升温的控制均有严格的要求。
2、烘炉时间确定热风炉烘炉的开始时间宜安排在高炉投产前约50天,具体时间按沙钢高炉投产计划表执行,热风炉烘炉结束后,如不能尽快投入生产,将给热风炉的保温工作带来较大困难,因此,在950℃时可转换为高炉煤气。
3、热风炉的烘炉方案3.1 热风炉本体烘烤采用逐炉点火烘烤方法进行,(根据烟囱抽力情况定和沙钢高炉投产计划表)。
3.2 热风炉烘烤方法3.2.1 采用国外先进的烘炉装置燃用焦炉煤气烘烤热风炉。
3.2.2 将燃用轻质柴油的内燃式烘炉器备用3台,已备煤气不稳定时备用。
3.2.3 备用的燃油系统的设备必须备到现场,如油灌、油泵、鼓风系统供油系统等。
3.2.4 现场的安装图在鉴定合同后,根据现场实测绘制完毕后提供给甲方。
4、烘炉的必要条件4.1 外围公用设施4.1.1 有关介质管网(包括烘炉用临时介质管道)全部安装完毕并经检查试验合格。
4.1.2 热风炉冷却水系统投入正常运转,水量、水压均达到烘炉所需要求。
4.1.3 各种动力(蒸气、压缩空气、N2等)保障供应,用量、压力均达到烘炉所需要求。
4.1.4 烘炉用焦炉煤气,压力8Kpa;流量,3000~4000m3/h。
4.1.5 高炉外围公用设施、各联络系统已经具全。
4.1.6 热风炉区域环境整治干净,通道畅通。
4.2 热风炉机械设备4.2.1 热风炉及各工艺管道打压合格。
4.2.2 热风炉系统联动试车完毕、PLC系统调试完毕(已经过192小时联动、正常)。
宝钢湛江5050m_3高炉工艺技术特点

、 、
, ,
置 烟 气 余热 回 收 并 配 置 前 置 预 热 炉 进
。
一
步 提 高 助 特 点 充 分 研 究 海 边 建 厂 的 经 验 组 织 专 家 团 队 进 行
, ,
燃 空 气 温 度 论 证 综 合 研究 复 杂 地 基 处 理 的 各 种 技 术 采 用 抗 台
。
,
6
)
热风炉 系统
。
采用
4
座 顶 燃 式 热 风 炉 两 的 纪 录 大 幅 减 少 了 物 流 运 输 成本 结 合 湛 江 地 区 地
, , ;
烧 两送 交 错 并 联 的 送风 制 度 设 计 风 温
, ,
1
3 00
T
。
设 质 复 杂 台 风 多 雷 雨 多 空 气 潮 湿 大 气 有 腐 蚀性 等
,
2 0 1
6 th e B F p
,
r o du ct i v i t
r ea c he s m ax 2 y
.
.
3 7 with min f u el rat e o f 4 8 0 kg/t
.
,
m ax c o al r at e o f 1 8 3 k
第
36
卷第
3
期 Vo
I
l
.
36
,
No
.
3
20 1 7
年 6 月 R O NM A K
I NG J un e 20
1
7
宝钢湛江
廖建 锋
(
5 05 0 m
3
高 炉工 艺 技术特 点
炼铁高炉工艺知识点总结
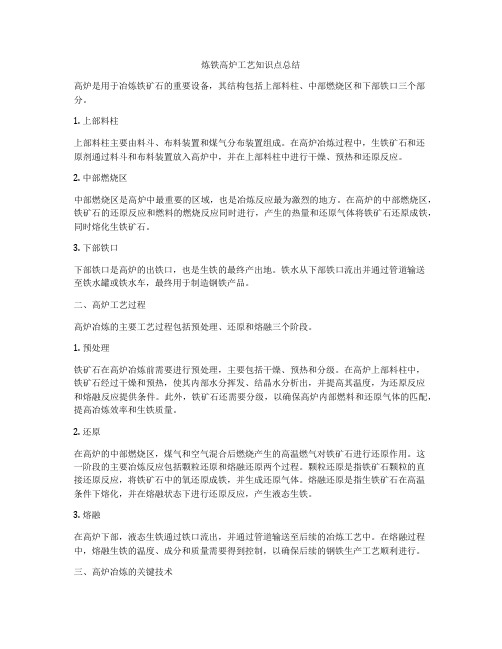
炼铁高炉工艺知识点总结高炉是用于冶炼铁矿石的重要设备,其结构包括上部料柱、中部燃烧区和下部铁口三个部分。
1. 上部料柱上部料柱主要由料斗、布料装置和煤气分布装置组成。
在高炉冶炼过程中,生铁矿石和还原剂通过料斗和布料装置放入高炉中,并在上部料柱中进行干燥、预热和还原反应。
2. 中部燃烧区中部燃烧区是高炉中最重要的区域,也是冶炼反应最为激烈的地方。
在高炉的中部燃烧区,铁矿石的还原反应和燃料的燃烧反应同时进行,产生的热量和还原气体将铁矿石还原成铁,同时熔化生铁矿石。
3. 下部铁口下部铁口是高炉的出铁口,也是生铁的最终产出地。
铁水从下部铁口流出并通过管道输送至铁水罐或铁水车,最终用于制造钢铁产品。
二、高炉工艺过程高炉冶炼的主要工艺过程包括预处理、还原和熔融三个阶段。
1. 预处理铁矿石在高炉冶炼前需要进行预处理,主要包括干燥、预热和分级。
在高炉上部料柱中,铁矿石经过干燥和预热,使其内部水分挥发、结晶水分析出,并提高其温度,为还原反应和熔融反应提供条件。
此外,铁矿石还需要分级,以确保高炉内部燃料和还原气体的匹配,提高冶炼效率和生铁质量。
2. 还原在高炉的中部燃烧区,煤气和空气混合后燃烧产生的高温燃气对铁矿石进行还原作用。
这一阶段的主要冶炼反应包括颗粒还原和熔融还原两个过程。
颗粒还原是指铁矿石颗粒的直接还原反应,将铁矿石中的氧还原成铁,并生成还原气体。
熔融还原是指生铁矿石在高温条件下熔化,并在熔融状态下进行还原反应,产生液态生铁。
3. 熔融在高炉下部,液态生铁通过铁口流出,并通过管道输送至后续的冶炼工艺中。
在熔融过程中,熔融生铁的温度、成分和质量需要得到控制,以确保后续的钢铁生产工艺顺利进行。
三、高炉冶炼的关键技术1. 燃料配比高炉冶炼所需的燃料包括焦炭、焦炉煤气和其他燃料。
为了提高冶炼效率和生铁质量,需要合理确定燃料的配比,保证还原气体的成分和温度符合冶炼工艺的要求。
2. 熔炼温度在高炉冶炼过程中,熔炼温度对生铁的成分和质量具有重要影响。
沙钢2500m3高炉喷煤系统优化技术与实践的开题报告

沙钢2500m3高炉喷煤系统优化技术与实践的开题报告一、选题背景高炉是炼钢的核心设备之一,其决定了炼钢产量和质量。
喷煤系统是高炉冶炼过程中的重要组成部分,喷煤技术的优化可以提高高炉的生产效率和节约能源。
沙钢集团是一家大型钢铁企业,其拥有中国最大的2500m3高炉,在高炉喷煤系统优化方面具有丰富的实践经验和技术储备。
因此,对沙钢2500m3高炉喷煤系统的优化技术进行研究和实践,对于提高其生产效率和降低能源消耗具有重要意义。
二、选题意义当前,我国钢铁工业正处于转型升级的阶段,推进高质量发展是必然趋势。
在炼钢过程中,高炉是最为核心的设备,而其喷煤系统的优化则可以提高高炉的生产效率和节约能源。
沙钢集团作为我国钢铁企业的领军者,通过对其2500m3高炉喷煤系统的优化技术进行研究和实践,可以推广推广先进的喷煤技术,为我国钢铁工业的转型升级提供有力的支持。
三、研究内容本次研究将从以下几个方面对沙钢2500m3高炉喷煤系统的优化技术展开研究:1. 喷煤系统的原理和结构分析;2. 喷煤系统的参数化模型建立;3. 喷煤系统的优化方案设计;4. 喷煤系统的实践应用和效果评估。
四、研究方法本次研究采用实验研究和仿真模拟相结合的方法,其中包括:1. 对喷煤系统进行原理和结构分析;2. 利用仿真软件建立喷煤系统的参数化模型;3. 设计不同的喷煤系统优化方案,并通过实验验证和仿真模拟评估其效果。
五、预期成果1. 对沙钢2500m3高炉喷煤系统的优化技术进行深入研究,获得相关技术知识和数据;2. 建立喷煤系统的参数化模型,提供仿真模拟工具;3. 设计不同的喷煤系统优化方案,并通过实验验证和仿真模拟评估其效果;4. 总结研究结果,撰写相关研究成果报告。
六、研究进度安排1. 喷煤系统的原理和结构分析(2022年1月-2月);2. 喷煤系统的参数化模型建立(2022年3月-5月);3. 喷煤系统的优化方案设计(2022年6月-8月);4. 喷煤系统的实践应用和效果评估(2022年9月-10月);5. 研究成果报告撰写(2022年11月-12月)。
沙钢5800m3高炉供料系统工艺特点
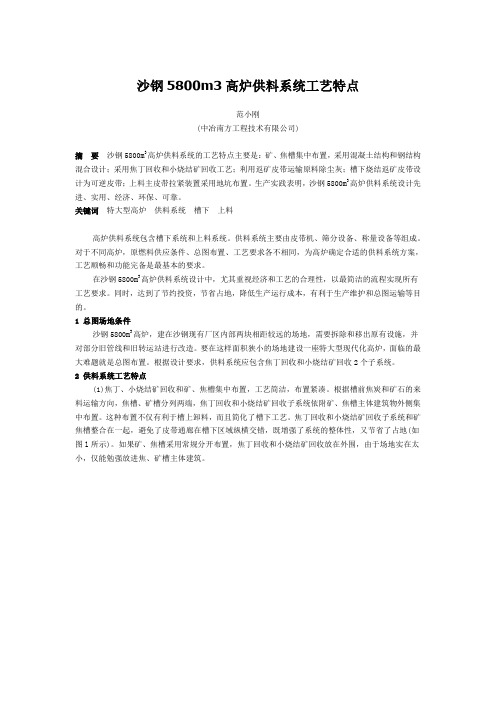
沙钢5800m3高炉供料系统工艺特点范小刚(中冶南方工程技术有限公司)摘要沙钢5800m3高炉供料系统的工艺特点主要是:矿、焦槽集中布置,采用混凝土结构和钢结构混合设计;采用焦丁回收和小烧结矿回收工艺;利用返矿皮带运输原料除尘灰;槽下烧结返矿皮带设计为可逆皮带;上料主皮带拉紧装置采用地坑布置。
生产实践表明,沙钢5800m3高炉供料系统设计先进、实用、经济、环保、可靠。
关键词特大型高炉供料系统槽下上料高炉供料系统包含槽下系统和上料系统。
供料系统主要由皮带机、筛分设备、称量设备等组成。
对于不同高炉,原燃料供应条件、总图布置、工艺要求各不相同,为高炉确定合适的供料系统方案,工艺顺畅和功能完备是最基本的要求。
在沙钢5800m3高炉供料系统设计中,尤其重视经济和工艺的合理性,以最简洁的流程实现所有工艺要求。
同时,达到了节约投资,节省占地,降低生产运行成本,有利于生产维护和总图运输等目的。
1 总图场地条件沙钢5800m3高炉,建在沙钢现有厂区内部两块相距较远的场地,需要拆除和移出原有设施,并对部分旧管线和旧转运站进行改造。
要在这样面积狭小的场地建设一座特大型现代化高炉,面临的最大难题就是总图布置。
根据设计要求,供料系统应包含焦丁回收和小烧结矿回收2个子系统。
2 供料系统工艺特点(1)焦丁、小烧结矿回收和矿、焦槽集中布置,工艺简洁,布置紧凑。
根据槽前焦炭和矿石的来料运输方向,焦槽、矿槽分列两端,焦丁回收和小烧结矿回收子系统依附矿、焦槽主体建筑物外侧集中布置。
这种布置不仅有利于槽上卸料,而且简化了槽下工艺。
焦丁回收和小烧结矿回收子系统和矿焦槽整合在一起,避免了皮带通廊在槽下区域纵横交错,既增强了系统的整体性,又节省了占地(如图l所示)。
如果矿、焦槽采用常规分开布置,焦丁回收和小烧结矿回收放在外围,由于场地实在太小,仅能勉强放进焦、矿槽主体建筑。
(2)采用焦丁回收和小烧结矿回收工艺,节约资源、节能降耗。
筛下的碎焦和烧结返矿经皮带运至槽上,分别装入碎焦槽和小烧槽。
阿钢1080m3高炉工艺流程设计特点

阿钢1080m3高炉工艺流程设计特点作者:石小钊戴丹来源:《科技视界》2012年第31期0 引言西林钢铁集团阿城钢铁有限公司(简称阿钢)根据发展需要,决定新建2座1080m3高炉,一期投产一座。
为实现高风温、高煤比、高顶压、高煤气利用、高利用系数、低能耗及长寿、环保的生产目标,1080m3高炉主要设计指标:利用系数2.7t/m3.d,入炉矿综合品位58%,焦比360kg/t,煤比200kg/t,风温1200℃,炉顶压力0.20MPa,富氧率2.3%,吨铁渣量不大于360kg,年产生铁100万t,高炉一代炉龄不低于12年。
1 高炉本体炉体框架设计采用自立式框架结构(17m×17m)。
炉顶采用框架式结构,考虑阿城当地的气候条件,炉顶从31.9米大平台至炉顶受料斗区域设计为封闭式结构。
高炉车间工艺流程见图1。
1.1 高炉内型高炉内型对高炉冶炼起着重要作用。
在总结国内外同类型容积高炉内型尺寸的基础上,结合阿钢原燃料条件,设计采用适宜强化冶炼的矮胖炉型,合理的内型能促使冶炼指标的改善。
高炉炉型主要参数见表1。
其特点如下:1)采用矮胖型炉型,减小炉腹角、炉身角。
较大的炉身角有利于受热膨胀后的炉料下降,较小的炉腹角有利于煤气流的均匀分布,减小对炉腹生成渣皮的冲刷,保护炉腹冷却壁,延长其寿命。
2)加深死铁层厚度。
加深死铁层会增加炉缸侵蚀面积,但环流的减弱,将延缓炉墙厚度方向的侵蚀速度,无疑对高炉是有利的。
同时较深的死铁层可多贮存铁水,保证炉缸有充足的热量储备,稳定铁水温度和成分。
3)加大了炉缸高度。
可保证风口前有足够的风口回旋区,有利于煤粉的充分燃烧及改善高炉下部中心焦的透气(液)性,有利于改善气体动力学条件。
4)高炉设有20个风口,2个铁口(夹角170℃)。
1.2 炉体冷却系统及冷却结构1)为最大限度地节约用水并考虑到方便检测,高炉炉体冷却分三个系统:软水密闭循环冷却系统、高压工业水冷却系统、常压工业水冷却系统。