8D Methods
8d8个步骤解决问题改善手法[1]
![8d8个步骤解决问题改善手法[1]](https://img.taocdn.com/s3/m/2963060404a1b0717ed5dd8f.png)
此方式可适用于任何效果,而且能促进相 关目的的各部门间有效的沟通。
第十三页,共59页。
13
8D 肉体(ròutǐ)
面对效果不可以(kěyǐ)各自为 面对效果应齐心协力,
政、自我本位主义,否
相互协助、相互选拔、
那么将无法有效处置效果。 如此才干彻底(chèdǐ)处置效果
第十四页,共59页。
14
何謂8D
此方式須经过〝8D 报告〞。
此方式可以为从统计进程控制造业,如何 走向质量实际(shíjì)提升之间,提供一项 详细的联络。
8D方法
运用(yù nyò ng)SPC
提升(tíshēng)制程才干
第十五页,共59页。
15
何謂8D
所谓〝八个步骤〞,其每个步骤意义及其流程请参 阅附图.该图虽已列出处置效果的各个步骤,但各 个步骤的先后順序可视效果的困难度及复杂水平而 异,不用拘泥于图示順序.且效果处置经过应有书面 记载.
8d8个步骤解决问题改善 (gǎishàn)手法[1]
2021/11/9
第一页,共59页。
8D方法(fāngfǎ)
8D:所谓8D方法(eight disciplines),又 称团队导向效果处置步骤,是福特公司处 置效果的一种方法,亦适用于制程才干指 数低于其应有(yīnɡ yǒu)值时有关效果的 处置。
第二十七页,共59页。
27
针对(zhēnduì)基本缘由
齐心协力、脑力激荡
提出(tí chū)一切能够的纠正 必要时,考慮選擇
措施
方案所触及的風險
消费前小批实验 纠正(jiūzhèng)措施
选择最正确方案
8D工作方法的介绍
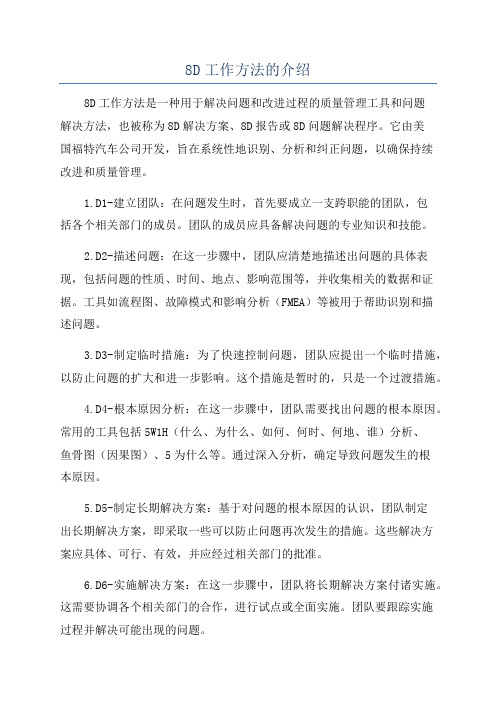
8D工作方法的介绍8D工作方法是一种用于解决问题和改进过程的质量管理工具和问题解决方法,也被称为8D解决方案、8D报告或8D问题解决程序。
它由美国福特汽车公司开发,旨在系统性地识别、分析和纠正问题,以确保持续改进和质量管理。
1.D1-建立团队:在问题发生时,首先要成立一支跨职能的团队,包括各个相关部门的成员。
团队的成员应具备解决问题的专业知识和技能。
2.D2-描述问题:在这一步骤中,团队应清楚地描述出问题的具体表现,包括问题的性质、时间、地点、影响范围等,并收集相关的数据和证据。
工具如流程图、故障模式和影响分析(FMEA)等被用于帮助识别和描述问题。
3.D3-制定临时措施:为了快速控制问题,团队应提出一个临时措施,以防止问题的扩大和进一步影响。
这个措施是暂时的,只是一个过渡措施。
4.D4-根本原因分析:在这一步骤中,团队需要找出问题的根本原因。
常用的工具包括5W1H(什么、为什么、如何、何时、何地、谁)分析、鱼骨图(因果图)、5为什么等。
通过深入分析,确定导致问题发生的根本原因。
5.D5-制定长期解决方案:基于对问题的根本原因的认识,团队制定出长期解决方案,即采取一些可以防止问题再次发生的措施。
这些解决方案应具体、可行、有效,并应经过相关部门的批准。
6.D6-实施解决方案:在这一步骤中,团队将长期解决方案付诸实施。
这需要协调各个相关部门的合作,进行试点或全面实施。
团队要跟踪实施过程并解决可能出现的问题。
7.D7-验证效果:实施解决方案后,团队需要验证其效果。
通过收集数据和实际观察,检查长期解决方案是否已经解决了问题。
如果发现问题仍然存在,那么团队需要重新审查并修正解决方案。
8.D8-预防措施实施:为了避免类似问题的再次发生,团队需要采取预防措施。
这可以包括流程改进、员工培训、设备更新等。
团队需要制定具体的预防计划,并确保其实施和有效性。
总结起来,8D工作方法是一种以问题为中心的质量管理工具和方法,可以帮助组织解决问题、改进过程,并实现持续改进。
VDA_Volume_4__8D-Method

Process D1 : Establish the team Objective : To determine the best possible team to solve the problem & to specify the team rulesNo. Input Process Output1 Decide to use the 8D methodto solve the problem Organise a small group of people as ateam. These people should haveprocess and/or product know-how.The team members must have the time,authority and ability in the technicaldisciplines to solve the problem and toimplement corrective actions. The groupmust have a designated champion and ateam leader. The group begins the team-building process.If possible the team should have 4 to 10members (not too big a team).The make-up of the team can vary duringthe process, depending on requirements.Enter the team members in the 8D report,ensuring traceability – i.e., first names andsurnames, telephone numbers and e-mailaddresses.Use the "assessment questions" todetermine whether step "D1" is complete.Step "D1" of the 8D reportcompleted : names androles of the team members :- Champion- Team leader- Each team member2 Champion As champion ……you are responsible for the system orprocess having the problem to besolved (the problem owner).…you have the authority to makeresources available to the team.…you support team decisions.…you ask the right questions in order todrive the progress of the team.…you are not actually a member of theteam but nevertheless you take part inteam meetings as necessary.…you are the interface between the teamand the rest of the company.…you can eliminate organisationalhindrances.…you ensure the right environment andthe empowerment of the team.Champion is appointed3 Team leader As team leader……you are the business manager of the team andresponsible for progress in the technical sphere.…you must have the technical expertise andnecessary leadership quality.…you should have mastered the 8D method andlead your team accordingly.…you ensure the ordered, organisational runningof the team meeting.…you draw up the agenda and papers for the teammeeting.…you are the spokesman for the team and theinterface to the champion.…you work with the team in setting out targets andtasks.…you request a summary of the contributions madeby the team members.…you focus on the reason for the meeting.…you provide information to the team.…you lead the decision-making process....you summarize the decisions.…you quit the role of leader when you take part inthe discussion.Team leader6 Team member As team member……you provide technical input.…you carry out tasks allotted to you.…you offer information and ideas.…you provide feedback and clarifyqueries. Activities / behaviour as team memberReference data : Assessment questions (Appendix); Elementary aids : VDA Volume 4Forms : 8D reportRules for decision-making :Many teams have a problem with decision-making because there is always the question of taking responsibility.At the beginning of operations, specify how you wish to come to decisions.•If you are the team leader you can set out briefly the various methods for making decisions.•If you have decided on a method for decision-making you should also decide how you wish to document the decisions and, if appropriate, how you arrive at them.•Within the team, consider whether and when exceptions can be permitted.•Specify who is responsible for carrying out the decision-making process.(in this connection see also D5)Comments :The explanations are very comprehensive because the team process and the way team members work together are crucial in achieving a constructive solution. Activities / behaviour within the team :Specify team roles quickly.Ensure that team meetings start and finish on time. Define clear objectives for your work, both short-term and long-term.Agree within the team on the "rules of the game"under which you wish all team tasks to be carriedout in future. Set out these rules in writing.Set out clearly in writing what you consider to be acceptable and unacceptable behaviour within theteam.All team members should be clear that each individual person is responsible for the progress ofthe entire team.Process D2 : Describe the problem Objective : Describe the internal / external problem by identifying "What is wrong with what" and detail the problem in quantifiable terms.No. Input Process Output1 Symptom (measurable)Positive result of the check onthe pre-requisites for usingthe 8D method.Available documentsregarding similar problems,such as 8D reports, FMEAs,process flow plans, controlplans, layouts, drawings…) Define the problemCollect all the information regarding theproblem.Determine as precisely as possible,based on facts, what defective productor process is involved :What item shows the defect / failure ?Arrive at a clear statement of what thedefect / failure is.What is the defect / failure ?Look behind the symptom by posing thequestion :“Who noticed what first ?”Ask the first person who noticed thesymptom to describe exactly whathe/she observed.Collect all available documents onsimilar problems (8D reports, FMEAs,process flow plans, control plans,…)Responsible : Team leaderDefinition of the problemStatement regarding thedefective product or process.Statement regarding what thedefect / failure is.2 Definition of theproblemStatement regardingthe defective productor process.Statement regardingwhat the defect /failure is. Develop a definition of the description of the problem(Problem statement).A problem definition- is a simple, precise statement of the item and the defect,the cause of which is not known.In the case of complex symptoms, consider breaking downthe problem into sections for individual treatment.Draw up a list of "IS / IS NOT" facts.Describe the occurrence in terms of :- What ?- Where ?- When ?- How many (how often; how significant ?Do not draw any conclusions (don't ask why) !!!The form used for assembling the IS/IS NOT factscontains precisely those questions necessary in order tocollect comprehensive data :- What is the item revealing the defect ?- What is the defect / failure ?- Where on the item can the defect be seen ?- Where was the defect first observed ?- Where has the defect been seen since ?- How many items are affected ?- How much of the item is affected ?- How many defects per item can be seen ?- Does the occurrence of the defect follow a trend ?Use the "IS NOT" column to answer what, where, when,how many) the defect has not occurred.Does the quality department have data providing importantinformation : line diagrams, diagrams showing a pattern,Pareto charts, etc. ?Draw up a "To Do" list.Evaluate all the aids available, such as SPC data, machinelog books, production measurement data, …Check the make-up of the team.Document all decisions and changes to the problem orprocess.Agree the results of the collection of "IS/IS NOT" facts withthe customer.Check whether the collected data show clearly a differencebetween specification actual performance, or whether theproduct/process was never good.Complete step "D2" of the 8D report.Responsible : Team leaderDescription of theproblemCompleted "IS / ISNOT FACTS" form(what, where,when, how many)Up-dated 8D report“D2”Up-dated To DoListList of actions withitems outstanding("To Do" list).Character of thedefect. Briefstatement of whatthe defect is.Reference data : Assessment questions (Appendix); Elementary aids : VDA Volume 4Forms :8D reportCollection of "IS / IS NOT" facts (Appendix)Comments :In D2 the objective is to describe the problem to be processed, clearly and as comprehensively as possible, based on the facts available.Collecting data and facts in D2 often appears to demand a lot of time and effort and it requires trust in the system to cause this amount of work within the team. However, once it is seen how much more quickly and effectively all the later stages can be handled, the team members are happy to bring all the facts together.Be careful not to draw any conclusions. The sub-conscious mind will always look for reasons in order to answer a problem as quickly as possible. Too many open questions cause stress. Tools & techniques :Brainstorming (creative methods,…) 8D reports covering similar failures Customers' reportsReports of experienceDealers' reportsQuality studiesRework and repair reportsProcess, product and system auditsProcess D3 :Immediate containment action(s) Objective : To define, verify and implement the immediate containment action(s) (ICA) to isolate the effects of the problems from any internal / external customer until permanent corrective actions (PCA) are implemented and are effective.Validate the effectiveness of the ICA.No. Input Process Output1 8D report “D2” with acurrent description ofthe problemCurrent "To Do" listfrom “D2” Define actions which will provide 100% protection forthe customer.Use the quality tools (see elementary aids, VDA Volume4) to evaluate which action protects the customer best.“Buy time“ for the analysis of cause(s).Protect the customer from the effects of the problem.Restrict the problem in terms of costs, quality and time.Check whether a service action is necessary (by thevehicle maker).Responsible : Team leaderDefined ICA whichprovide 100%protection for thecustomer (thecustomer no longersees the symptom)Service action ifnecessary2 Defined ICA whichprovide 100%protection for thecustomer(the customer nolonger sees thesymptom)Up-dated 8D report(up to "D3" withoutverification) Verification of ICA :Before implementation, demonstrate that the action- achieves what is intended (by comparing databefore and after) and- no new problem occurs.Verification activities may include :- Tests and demonstrations- comparison of the new action with similar, provenimprovements- review of newly developed documents beforeapproval/release :All documents (procedures, drawings, specifications,etc.) must be checked for accuracy before they arereleased. Verification is a process which evaluates thatthe intended change is made without causing a newproblem.Verification can, for example, be carried out by a cross-departmental team which assesses the change and itseffect, including any effects on the organisation.If possible a pilot introduction should be carried out inorder to demonstrate the effects of the change.There should be team consensus on the decision.Implement the ICA.Responsible : Team leaderVerification results,in 8D report (D3)Approved/releaseddocuments.ICA implemented.3 Verification results inthe 8D report (D3)Approved/releaseddocuments.ICA implemented. Validate the ICA.- Demonstrate continuously that the action has theintended effect without causing a new problem.- Although the customer is the last testing point forvalidation, validation by the customer is not the rightway to carry out validation.Validation before release to the customer- Demonstrate continuously the expected effect of theactions before introducing the change to thecustomer.- The activities may include tests , inspection,observations and other quality tests.Validation by the customer- Demonstrate continuously the expected effect of theactions after introducing the change to thecustomer.Proof of effectiveness is achieved when improvementsare seen at the same indicators which indicated thesymptom.The improvements can be observed and demonstratedwith a flow diagram.Responsible : Team leaderUp-dated 8D reportwith :Verification andvalidation data for theICA.Reasons (if applicable)why an ICA is notnecessary.Reasons for theselected ICA (decisionand criteria method).Action plan forcoordinating the ICA("to do" list)Action plan for the nextsteps ("to do" list)Reference data : Assessment questions (Appendix); Elementary aids : VDA Volume 4 Forms :8D reportDecision criteria method (Appendix)Comments :Characteristics of an immediate containment action (ICA)Temporary elimination of the effect / symptom.An action which prevents symptoms arising from one or more problems from having any effects on personnel, organisations or specific vehicle drivers.An ICA makes use of the data collected at the D2 stage.An immediate action ……attacks the symptom.…is verified for effectiveness before implementation. …is observed for its effect.…is not merely a quick solution which is then forgotten. …is replaced by the selected permanent correctiveaction (D6) - not to be forgotten !…generates costs.Process D4 : Root cause(s) Objective : to determine all possible causes, decide on and demonstrate the main (root) cause, indicate the point where the fault slipped through (the "escape point".No. Input Process Output1 8D report completed up to andincluding D3 :Verification and validation datafor the ICA.Reasons (if applicable) why anICA is not necessary.Reasons for the selected ICA(decision and criteria method).Action plan for coordinatingthe ICA (decision-makingwork-sheet)Action plan for the next steps(if involved in the managementreview) ("to do" list).e.g., current problemdescription, processsequence, FMEA, workinstructions, maintenancerecords, SPC, … D4 is the actual analysis of the cause(s). Itmust be carried out with care and withoutallocating blame. Facts are all that count –no deductions or subjective assessments.Make sure that the problem has been causedby a change – here, "change" means suddenand continuous and not a problem whichoccurred on the first day.Measurements are carried out, which showthat the specified requirements are not met.Determine all the differences between what"IS" and what "IS NOT".Allocate all the differences to the relevantchanges and date these changes.Within the team, develop all possible theoriesregarding potential causes. Use theexperience and creativity of the teammembers.Each theory which might explain how theproblem could have occurred is identified asa possible cause.Isolate the root cause by testing all thetheories of causes against ALL the factsfrom the "IST / IS NOT" exercise.Isolate the "escape point" – the point in theprocess where some-one could haverecognized the problem and prevent itseffects but did not do so. Use the cause &effect diagram, the process flow chart andproblem-solving sheets:Work-sheet :IS / IS NOT differences / changes.Write down all the differences:Ask what is unusual, strange, striking orunique about the "IS" data.Consider the influence of personnel,methods, materials, machines, measure-ments and the environment (revise the cause& effect diagram).Ask what has changed with regard to thedifferences.Keep asking “Why?” as you work toward theroot cause (the "why" staircase) until there isno longer a clear answer to the question.Completed work-sheet :IS / IS NOT differences /changes- cause & effect diagram- action planUse the work-sheet :Testing the theories for causes Responsible : Team leader2 - cause & effect diagram- action plan- 8D report Verify the causeVerification of the “most probable cause”can take place only in the real world,where the problem occurs.Verification of the cause is theconfirmation that the cause has actuallycaused the problem.Verification should be carried out in twostages :- passive verification- active verificationPassive verification is carried out byobservation.With passive verification a check is madeas to whether the cause is present.If it cannot be demonstrated that the causeis present, there is every chance that the"most probable cause” is not the real cause.Active verification is a process, in whichthe effect of the cause can be “switched onand off”.Responsible : Team leader- Verified cause- Up-dated 8D report3Process D5 :Planned permanent corrective action(s) Objective : Select the best permanent correctiveaction in order to eliminate the cause of the problem No. Input Process Output1 - Cause & effect diagram- Verified cause- Action plan- Up-dated 8D reportSelect the best corrective action toeliminate the cause of the problem.Select the best corrective action toprevent the problem from slippingthrough at the "escape point".Verify that both these decisions areeffective, once they have beenintroducedEnsure that no new causes ofproblems have been introduced asa result of the corrective action.Eliminate the cause of the problem. Verifythis in D5 and validate it in D6.Criteria for the permanent corrective action :•Solve the problem at the level of thecause.•Do not generate any new problems.•Verify the effectiveness of theaction.Responsible : Team leader- Action plan- Up-dated 8D report2 - Verified cause- Action plan- Up-dated 8D report Use the attached work-sheet :DECIDE ON THE CRITERIA METHODEssential criteria :WhatEssential criteria are objectively measurable,non-negotiable, realistic features regardingthe decision.They often involve money, completiondates, company regulations and legislation.WhyEssential criteria are minimum criteria. Thismeans that some decisions are filtered out.HowEssential criteria must be objectivelymeasurable and realistic.Desirable criteria :WasDesirable criteria are features which aredesirable in decision-making.They are subjectively / objectivelymeasurable.WhyDesirable criteria enable you to determinewhich of the remaining decisions should bepreferred.HowDesirable criteria generate the criteriarequired to make the ideal decision, takingresources into account, in order to reach thenecessary end-result.Responsible : Team leaderCriteria entered in the work-sheet : DECISION ON THECRITERIA METHOD.3 Criteria entered in thework-sheet : DECISIONON THE CRITERIAMETHOD Decide on the relative importance of thedesirable criteria :WhatDesirable criteria have a relative importanceto each other in terms of the end-result.WhyThe relative importance enables the effectof each available option to be evaluated inorder to determine the relative advantages.HowSome desirable criteria are more desirablethan others. Award 10 points to the mostimportant criteria, compare the other criteriato it and award them points accordingly(scoring (1-10).Responsible : Team leaderCriteria and importanceentered in the work-sheet :DECISION ON THECRITERIA METHOD4 Work-sheet : DECISION ONTHE CRITERIA METHODwith criteria and importance Select a decision :WhatGenerate a list of the alternatives.WhyThe "band-width" gives you a high-valueselection.HowSome of the alternatives may havealready been suggested – for example,by the manager. Others may alreadyhave been considered on the basis ofthe personal experience of other people.Some examples may have been takenfrom technical magazines, literature, etc.Bear in mind that this process mayrequire several team meetings, if dataneed to be collected from outside theteam.Responsible : Team leaderWork-sheet : DECISION ONTHE CRITERIA METHODwith criteria and importance5 Work-sheet : DECISION ONTHE CRITERIA METHODwith criteria and importance Compare the choice against thedecision-making criteria :WhatA comparison enables you to determinehow well the possible decision fulfils thedecision-making criteria.WhyYou carry out the comparison so thatyou can select the best solution from allthe possible solutions.How1. Compare the essential criteria,checking the solutions (variants) tosee if they are appropriate (yes orno).2. Then check the solutions against thedesirable criteria. Award the bestsolution 10 points and evaluate theother solutions in relation to this, withscores of 1 to 10.3. Multiply these "how good" values withthe importance of each desirablecriterion. Enter the result of thismultiplication in the “Points” column.4. Produce total figures for each variant(solution).Consider the following :Write down objective informationWork-sheet : DECISION ONTHE CRITERIA METHODwith criteria, importance andtotals for the individualvariants.regarding the desirable criteria and not merely “yes, no, good or bad”.Try to use the entire points band-width, from 1 to 10.Responsible : Team leader6 Work-sheet : DECISION ONTHE CRITERIA METHODwith criteria, importance andtotals for the individualvariants. Analyse the riskWhatIn the risk assessment, consider whatcan "go wrong".WhyIt is essential to consider the risk. Oftensolutions will bring not only advantagesbut also negative side-effects (the"network" theory).HowDraw up a statement of risk : “If an event… occurs, it will have the followingconsequences…” ("FMEA thinking“)Examine the probability of occurrenceand the severity of the possible effects.Relate the results of theseconsiderations to the essential anddesirable criteria. Is the solution really asolution ? Or does it also contain apossible new problem ?Responsible : Team leaderWork-sheet : DECISION ONTHE CRITERIA METHODwith criteria, importance andtotals for the individualvariants.Work-sheet : DECISION ON THE CRITERIA METHOD with criteria, importance and totals for the individual variants.Completed risk analysis work-sheet. Come to a fully-weighed decision.WhatA fully-weighed decision is based on allthe information and the conclusionswhich have been drawn.WhyYou make the fully-weighed decision inorder to make the best possible decision.HowWhen weighing up the advantages and disadvantages you may find that thesolution initially proposed is no longer theoptimum solution.Responsible : Team leaderDecision7 Decision Verification, feasibility test Justification of the finalCheck to make sure that the solution works in practice.Examples : experiments, trial runs, tests. Responsible : Team leader decisionVerification data for the permanent correctiveaction(s).Risk analysis, FMEAAction plan for the next steps. Up-dated 8D report8 - Action plan- Up-dated 8D report Describe the result of the decision :What – the result is a brief statementcontaining the desired end-result ofthe decision.Why – the end-result must be knownin order to determine the range, orscope of the decision and also tofocus thinking and further action onthis.How – you describe the end-resultby defining the actions and theitem(s) involved.Responsible : Team leaderBrief description of thedecision, including the range,the actions and the item(s)involved.Up-dated 8D reportReference data : Assessment questions (Appendix); Elementary aids : VDA Volume 4 Forms :8D report,Work-sheet : decision criteria methodTools & techniquesFMEAProcess capability methodsProcess flow diagramDesign of experiments (DOE)Creativity techniquesTRIZBenchmarkingOrganisation chartsProcess control checksWeibull analysis SummaryImportant factors in D5 are :Take the right decisionWeigh the advantages and risksNo hasty introductionVerify that the selected action will be successfulProcess D6 :Implement and validate permanent corrective actions (PCAs)Objective : Plan and implement the chosen permanent corrective actions (PCA) and stop the immediate containment actions (ICA).Validate the PCA. Observe the long-term results.Continuing the ICA would use important resources (causing unnecessary costs). The ICA would also hinder the validation Responsible : Team leaderTools & techniques :Action planProcess flow chartFMEAInitial sample inspection report (ISIR)(Production Part Approval Process, PPAP) Process descriptionsWork descriptionsSPCFlow chartsProcess capability checks Forms / information :8D reportElementary aids : VDA Volume 4Summary :If you cannot prove that the problem is solved, it is not solved !Process D7 : Objective : Prevent the recurrence of the failurePrevent recurrence which has been eliminated in the system. Giverecommendations for improvements, also coveringother systems in which the problem might occur. No. Input Process Output1 - Confirmation that thevalidation is successful.- Up-dated 8D report.- Other information sources :- FMEA- ISO and VDA documents- Process flow charts- Timing plans- Control plans- Report of experience fromthe teams (lessons learned)- Provisional solutions Prevent recurrenceThis is an action to prevent theoccurrence of current problems,similar problems and systemicproblems.The current problem is the problemcovered by the present 8D process.In "D7" the team examines the sameproblem from the systemic perspective.Similar problems are problems of asimilar nature to the problem coveredby the present 8D process.The team leader for the current 8Dprocess initiates the necessary actionsif appropriate.Show what practices and proceduresin the system allowed the problem tooccur and to slip through without beingdetected.Identify possible practices andprocedures for preventing the problemin the current system.Identify possible practices andprocedures for preventing similarproblems in other systems.Modify the necessary systems preventcurrent or similar problems fromoccurring.Preventive actions fall within the areaof responsibility of the current teamleader !Possible improvements topractices, procedures, etc.Up-dated FMEA, control plan,process flow chart (ifappropriate) and layout.2 Possible improvements topractices, procedures, etc. As a team, give recommendations forsystemic improvements if necessary /possible.It may be necessary to appoint adifferent team champion in the case ofsystemic problems.Recommendations forsystemic improvements,procedures, etc.3 Recommendations forsystemic improvements,procedures, etc. Possible reaction to improvementproposals from the teams :"D7" results are the area ofresponsibility of the current teamchampion.1. The champion authorizes thecurrent 8D team to implementappropriate action; or2. The champion authorizes others toAction (1 to 5) by the teamchampion, depending on hisdecision.。
8D手法讲义

•←選擇 •←事先驗證 •←執行
•←確認產品以及讓客戶 •不滿意已不存在
•确认临时措施采取后是否 •完全有效
书山有路勤为径, 学海无涯苦作舟
•←執行後的確認
•
D4确定并验证根本原因
对问題之何以發生, 指出其一切可能形 成的原因<魚骨圖 ﹕4M1E>.再分別 针对每一可能原因 予以測試,以验证真 正之根因.然后找出 消除该项根本原因 的各项纠正措施 <5why法>。
Why:Identify known explanations 为何;识別已知的解释,為何才發現﹐為何要解決﹔ How:In what mode or situation did the problem occur? 如何;在什么模式或状态下发生这问題,是否有規律﹔
How many<much>:Magnitude quantify problem 多少;量化问题的程度,范圍多大﹐比例多少﹔
8D手法讲义
书山有路勤为径, 学海无涯苦作舟
2020年4月13日星期一
8D方法
8D:所谓8D方法(eight disciplines),又称 团队导向问题解决步骤, 亦适用于制程能力 指数低于其目標值时有关问题的解决。
书山有路勤为径, 学海无涯苦作舟
•
執行8D的好處
此方式是团队运作导向以事实为基础,避免 个人主见的介入,使问题的解决能更具条理 。
如:某一问题发生及团队组成时,可能制造人员已 经先行采取临时緊急对策,惟其永久解决方案,则可 能尚需小组人员的共同参与,经多方研讨后才能产 生。
书山有路勤为径, 学海无涯苦作舟
•
•了解問題
•1、成立小組
详解8D方法

详解8D方法工具的种类有多种,据日本企业不完全统计常用的工具有58种之多。
在实际使用中,太多太少均不妥:或者繁冗没必要、或者单薄不充分;但不管多还是少,相同之处是每种工具所能完成的功能是特定的,比如有的长于记录、有的长于分析、有的长于决策等。
问题的解决需要多种工具的配套使用,从而逐渐形成了问题解决套路或模板。
同时为了使经验教训易于记录和共享、减少问题重复发生的概率,通常特定的企业或行业会有大家共同认可的、行之有效的、标准的问题解决套路,最为著名的是QCC、6Sigma、8D等模型——其实它们的本质都一样,都是PDCA循环,具体原理见下图:8D的起源二战期间,美国政府率先采用一种类似8D的流程——“军事标准1520”,又称之为“不合格品的修正行动及部署系统”。
1987年,福特汽车公司首次用书面记录下8D法,在其一份课程手册中这一方法被命名为TOPS(Team Oriented Problem Solving)即“团队导向问题解决法”。
8D问题求解法(8D Problem Solving),D是Discipline(步骤、原则)的首字母。
当时,福特的动力系统部门正被一些经年累月、反复出现的生产问题搞得焦头烂额,因此其管理层提请福特集团提供指导课程,帮助解决难题。
8D最先在福特内部使用、成熟后福特逐渐要求其供应商遇到问题也用此法。
后来名气大了,其它车厂也移植了福特的做法、使之成为汽车行业的标准做法。
再后来8D家喻户晓,各行业通吃。
而且不仅仅解决工作问题,解决家庭生活问题也很有效。
8D的适用范围•该方法适用于解决各类可能遇到的简单或复杂的问题;•8D方法就是要建立一个体系,让整个团队共享信息,努力达成目标;•8D本身不提供成功解决问题的方法或途径,但它是解决问题的一个很有用的工具;•亦适用于过程能力指数低于其应有值时有关问题的解决;•面对顾客投诉及重大不良时,提供解决问题的方法;•8D法是美国福特公司解决产品质量问题的一种方法,曾在供应商中广泛推行,现已成为国际汽车行业(特别是汽车零部件产家)广泛采用来解决产品质量问题最好的、有效的方法。
8D实施方法含实例

D6、验证纠正措施
1. 换完电线后,至今尚没有发现连接点松动的迹象。 2. 断开电流接触器的电路进行试验,一旦电压不正常,转子 将自动停止工作,直至没电镀的产品从线上取下。 以上工作,小组共同进行了验证,并提请顾客事先的批准。
32
D7、防止再发生的措施
❖电镀工作指导书被修改增加了如下内容: 1)当生产线不正常停止时,操作者不仅要挑选出缺陷产品 ,而且要在工作记录记下数量及当班QC的名字。 2)在电镀线在每天早上启动前,电流接触器的连接点和电 线必须检查。以上,由杨星在12月15日完成。 ❖开发一个包括每天需检查事项的检查清单,例如生产线停 止,不管缺陷产品是否被挑选,制造部和QA需进行审核。 ❖ 依次类推,如果有类似问题,该小组负责纠正并采取适当 的预防措施。
检查数量
状态 缺陷数量
MT001206 19308片
19308片
OK
0
MT001208 14274片
14274片
OK
0
总计
33582片
33582片
OK
0
•2. 我们对操作者进行培训和教育,以让其知道最重要的事情:
•遵守工作程序和指导书以保持顾客产品质量。使其意识到他们在 产品质量保证中的重要职责。我们强调,任何由于不小心引起的错 误是不允许的并且不能重复发生,因为那样将会给顾客带来不必要 的损失。因此我们把给顾客造成损失的错误展示以教育员工。
生管课、销售课、库管课、品保课 • 责属人员:
贾正羽、庄卫年、赵晓明、许 丽
36
D2.问题描述
• 何时 : 1999年11月4日; • 何人 : 浙江精密机械厂; • 何地 : 浙江精密机械厂—包装车间; • 何事 : 包装ALT-5检测器时,使用20μMHT
8D分析方法

8D分析方法
do
something
8D的由来
8D(8 Disciplines)即问题解决8步法,最早是福特公司使用的经典质量问题分析手法,对于解决工厂中存在的问题是一个很有用的工具,尤其在面对重大不良时,它能建立一个体系,让整个团队共享信息,并引导团队提供解决问题的方法。
工作中有过这样的感触
8D方法由8个步骤和1个准备步骤组成,客观地确定、定义和解决问题并防止相似问题的再次发生。
8D方法应用流程
D1组建问题解决团队
8D原名就是叫团队导向问题解决步骤,8D小组需要由具备产品及制程知识,能支配时间且拥有职权及技能的人士组成,必须指定一名8D团队组长。
不具备以上条件的8D是失败的8D,它没法在你需要资源解决问题时提供帮助。若一个体系出现了质量异常,绝非单一部门职能失效,否则整个体系需要重新进行完善。
十二项工作原则之解决问题4步骤
1. 解决问题2. 修改相关程序文件3. 相关人员培训4. 相关问题追溯
D8 8D过程总结
恭贺小组的每一成员,问题解决完成,对小组成员的努力予以肯定。8D项目正式关闭文件定案和存档
记录过程中学到的教训
提交8D问题分析报告表达对成员的感谢
感谢阅读
感谢阅读
D2描述问题
以客户的角度和观点详细描述其所感受到的问题现象,将所遭遇的问题,以量化的方式,明确出所涉及的人、事、时、地、为何、如何、多少。
如何进行问题描述?
要找到问题的根源而不是表现症状的简单描述;要定义问题的边界(不要将问题范围扩大到不可控的范围之外
5W2H方法
Who~谁发现的问题?When~什么时间发现的问题?Where~在何处发现的问题?What~有什么问题发生?Why~为何问题此时发生?How~问题如何发生?How many~问题发生的程度(多大?范围?比例?)
8D method(8D报告)教材中英文讲解
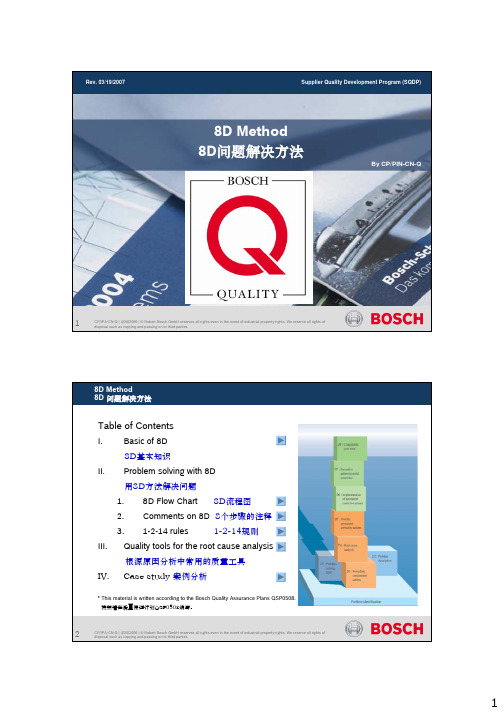
8D Method 8D 问题解决方法
1. 8D Flow Chart 8D流程图
Comments/注释
-Solve complex problems with (but not only) the: 用以下方法(但不 限于)解决复杂问题:
-5x why questioning technique/5"why"法
2
8D Method 8D 问题解决方法
I. Basic of 8D 8D基本知识
¾ Complaint 抱怨8D问题解决方法
„Complaint” is understood here as a deviation (e.g. of products, processed, organizational procedures) that is reported by an internal or external customer. “抱怨”在这里理解为由内部或者外部客户反馈的某种特性的偏差( 比如产品,过程,有组织的程序)。
4
CP/IPA-CN-Q | 4/20/2006 | © Robert Bosch GmbH reserves all rights even in the event of industrial property rights. We reserve all rights of disposal such as copying and passing on to third parties.
8D Method 8D 问题解决方法
I. Basic of 8D 8D基本知识
¾ Why 8D 8D的目8D的问题解决方法
1. Rapid, lasting and systematic processing of internal and external complaints, locating and eliminating the root defect cause. 快速、持续并且系统的处理内部以及外部的抱怨,定位并消除根 源缺陷原因。
- 1、下载文档前请自行甄别文档内容的完整性,平台不提供额外的编辑、内容补充、找答案等附加服务。
- 2、"仅部分预览"的文档,不可在线预览部分如存在完整性等问题,可反馈申请退款(可完整预览的文档不适用该条件!)。
- 3、如文档侵犯您的权益,请联系客服反馈,我们会尽快为您处理(人工客服工作时间:9:00-18:30)。
相差多少 ppm
LQFP 14x20
99.8903
99.8971
68
QFP 28x28
99.8363
99.8393
Page 38 of 110
30
Excursions 的偵測
• 公司並非以SPC偵測出Excursions, 請問公司 以何機制得知 Excursions.
0.250
0.200
0.150 UCL=0.1253 0.100 Avg=0.0704 0.050 LCL=0.0155 0.000 Lot
Page 25 of 110
CA-PDCA 循環輪
3.要因解析
7.效果維持
2.現況的把握
A Action C Check
P Plan D
8.反省及今後計劃
1.主題選定 6.效果確認
A C
P D
4.對策擬定
5.對策實施
Page 26 of 110
S-D-C-A
• 標準化Standardization-實行-檢核-行動 • 所有製程在開始運作時都會不穩定, 在這個 階段, 穩定製程使產量固定是很重要的 • 待標準建立了並且穩定了, PDCA 則是用來 改變製程提昇水準. 但是一旦製程一改變, 又會馬上變得不穩定, 需要以SDCA加以穩 定化
衡量、追蹤及控制改善成效
G8D 步驟
D0
D1 D2
徵兆/ 緊急反應措施 成立改善小組
描述問題
暫時性的對策實施及確認 原因分析及証實
D3
D4 D5 D6 D7 D8
永久改善行動效果確認
永久改善行動的對策實施及確認 避免再發生/ 系統性預防建議 完成
G8D Additional Portions
D0
QA未執行 分散抽樣
Rework產品 未確實check
加班 疏忽 精神不佳
Loading 過多
熬夜
規格認識 不夠
打帶動作 不確實
方法缺失 平面度 良率不佳
人員疏失
BUY OFF檢 查動作不確實
工作 不專心
材料問題
職前訓練 不足 模具異常
設備問題
TRAY 設計不良 產品定位 不良 機台操作 不熟悉
磨損
• 答1:因為機器超載, 保 險絲燒斷了 • 答2: 因為軸承的潤滑 不足 • 答3: 因為潤滑幫浦失 靈了 • 答4: 因為幫浦的輪軸 耗損了
5 Why 範例: 為何停機
• 問1:為什麼機器停了?
• 問2:為什麼機器會超 載? • 問3:為什麼軸承會潤 滑不足? • 問4: 為什麼潤滑幫浦 會失靈? • 問5: 為什麼潤滑幫浦 的輪軸會耗損?
Page 12 of 110
5 Why 範例: 為何停機
• 問1:為什麼機器停了? • 答1:因為機器超載, 保 險絲燒斷了
5 Why 範例: 為何停機
• 問1:為什麼機器停了?
• 問2:為什麼機器會超 載?
• 答1:因為機器超載, 保 險絲燒斷了 • 答2: 因為軸承的潤滑 不足
5 Why 範例: 為何停機
Page 23 of 110
PDCA 循環輪
1.主題選定 2.課題明確化與目標設定 7.效果維持 3.方策擬定
A P 管理人員 管理人員
6.效果確認
4.最適策追究
C D 檢驗人員 作業人員
5.最適策實施
8.反省及今後計劃
Page 24 of 110
C-A-P-D-C-A
• • • • 檢視現狀-再對策-企劃-實行-檢核-行動 是問題解決型QC改善歷程 注重在已發生問題的處理 在PDCA循環注重在Do, 故Do的內部尚有小 型的PDCA循環,直到問題改善為止 • 小規模的改進,非大刀闊斧的改革
P D
(-)
列出問題點
Page 29 of 110
PDCA 與CA-PDCA實施步驟
PDCA
活動計劃的製作
2. 課題明確化 3. 方策擬定 4. 最適策追究 5. 最適策實施 6. 效果確認 1.主題選定 適用 何種 QC STORY 的判定
CA-PDCA
活動計劃的製作
2. 現況把握 3. 要因分析 4. 對策擬定 5. 對策實施
5. 最適策實施 6. 效果確認
7. 效果維持
8. 反省及今後計劃 Page 31 of 110
解決問題的QC Story種類
• 1.課題達成型QC Story: 著重 PDCA • 2.問題解決型QC Story: 著重 CA-PDCA • 3.8D 及異常一覽表: 著重在於預防再發
Page 32 of 110
8D:8 DISCIPLINES
• 8D: 8 Discplines of Problem Solving 解決問題的8個步驟 • 8D 是解決問題一種工具,通常是客戶所抱 怨的問題要求公司分析,並提出永久解決 及改善的方法 • 比改善行動報告 (Corrective Action Report) 更加地嚴謹
Sigma Rule
99-100%
90-98%
60-75%
-3s
-2s
-s
+s
+2s
+3s
異常的定義
0.27%/2= 0.135%
99.73%
0.27%/2= 0.135%
6s
Excursions 對整體良率的影響
未去除 Excursions 的良率% 移除 Excursiห้องสมุดไป่ตู้ns的 良率%
7. 效果維持
8. 反省及今後計劃 Page 30 of 110
PDCA 與CA-PDCA實施步驟
PDCA
活動計劃的製作
2. 課題明確化 1.主題選定 適用 何種 QC STORY 的判定
CA-PDCA
活動計劃的製作
2. 現況把握 3. 要因分析 4. 對策擬定 5. 對策實施
最適策.由Plan 開始即多角度去尋 3. 方策擬定 求解決問題的對策, 與CA-PDCA 4. 最適策追究 的邊尋找對策處理問題有所不同
問
題
分析原因 WHY
原
因
設定改善目標 並形成解決方案
人員出勤率的目標為95% 低了2個百分比,而此差 異幅度根據以往資料判斷 差異過大為異常狀況。 請假人數太多
如何改善異常 ? 如何控制發生異 常的 原因 ?
對
策
處置:問題發生立即採 公佈人員出勤狀況取 的措施 治標:解決問題的手段 強化請假 管制 治本:避免問題再發生加強員工向心力的方法
如何管理異常良率
• 有效管理異常可以 – 將干擾降低 – 提昇 Xbar 水準 (幫助不大, 因為屬於少數) • 暫時管制措施是重要的 – 第一件事就是將產品 “Hold” – 再來才是解決問題, 預防問題的再發 • 異常管理 – 三現: 現時, 現地, 現物 – 以Problem 7 Steps 來解決及預防問題 – SDCA
Cpk=1.694
Cpk=0.852
-5
5
15 25 35 45 55 65
-6
4 14 24 34 44 54 64 74
把問題想像成一座冰山
現象
現在
看得到的, 可感覺 , 可測量
why
問題
why
緊急處理
真因
一次因 (近因)
why
治標對策 (暫時)
過去
真因
why
真因
真因
why
真因
n 次因 (遠因)
Page 1 of 110
8D 的本質: 問題解決程序
當我們觀察到 或發現………時 這現象是否正常 跟標準或目標比較的差 異(偏離程度) 其差異是否不該在 為什麼會發生異常 ?
現
象
確認並定義問題 WHAT, WHEN, WHERE, WHO, WHY, HOW, HOW MUCH
例如: 人員出勤率93%
改善範例
105 100 95 90 85 80 75 70 65 60 Ä @g ² ¤ ¶ Ä Gg ² ¤ ¶ Ä T g ² ¤ ¶ Ä ¥ ¶ ² | g 80 90 102 101
目標=100元
-20元 -10元
Page 33 of 110
兩種不同類型的良率損失
• 異常良率損失 Excursions: 良率損失的獨立 跳昇,由突然且嚴重的良率損失所引起, 影響範圍導致特別低良率的有限批數
治本對策 (永久)
5 Why 1H 工具
• • • • • • 豐田生產方式: “反覆提出五次為什麼” 垂直式思考, 針對問題一層又一層地深入 通常第一個答案不會是真正的答案 5 Why 可以找出真正的原因 找原因用5Why+想方法用1How 簡單的案子可能4W,3W或2W即找出root cause,但複雜的或許要5 Why, 6 Why, 7 Why…最後要加 1H,How to fix it.
• 問1:為什麼機器停了?
• 問2:為什麼機器會超 載? • 問3:為什麼軸承會潤 滑不足?
• 答1:因為機器超載, 保 險絲燒斷了 • 答2: 因為軸承的潤滑 不足 • 答3: 因為潤滑幫浦失 靈了
5 Why 範例: 為何停機
• 問1:為什麼機器停了?
• 問2:為什麼機器會超 載? • 問3:為什麼軸承會潤 滑不足? • 問4: 為什麼潤滑幫浦 會失靈?
Page 5 of 110
先提昇製程水準 (Xbar ) 還是降低異常 (s )
變異很小, 但卻不準確
Page 7 of 110
準確, 但變異卻很大
Page 8 of 110
Cpk=0.816
Cpk=0.852
0
10 20 30 40 50 60
-6