ABS电镀
ABS塑料电镀
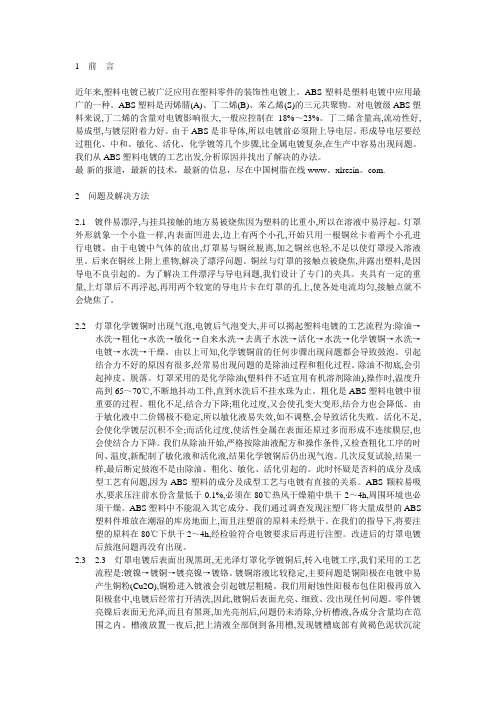
1前言近年来,塑料电镀已被广泛应用在塑料零件的装饰性电镀上。
ABS塑料是塑料电镀中应用最广的一种。
ABS塑料是丙烯腈(A)、丁二烯(B)、苯乙烯(S)的三元共聚物。
对电镀级ABS塑料来说,丁二烯的含量对电镀影响很大,一般应控制在18%~23%。
丁二烯含量高,流动性好,易成型,与镀层附着力好。
由于ABS是非导体,所以电镀前必须附上导电层。
形成导电层要经过粗化、中和、敏化、活化、化学镀等几个步骤,比金属电镀复杂,在生产中容易出现问题。
我们从ABS塑料电镀的工艺出发,分析原因并找出了解决的办法。
最-新的报道,最新的技术,最新的信息,尽在中国树脂在线www。
xlresin。
com.2问题及解决方法--2.1镀件易漂浮,与挂具接触的地方易被烧焦因为塑料的比重小,所以在溶液中易浮起。
灯罩外形就象一个小盘一样,内表面凹进去,边上有两个小孔,开始只用一根铜丝卡着两个小孔进行电镀。
由于电镀中气体的放出,灯罩易与铜丝脱离,加之铜丝也轻,不足以使灯罩浸入溶液里。
后来在铜丝上附上重物,解决了漂浮问题。
铜丝与灯罩的接触点被烧焦,并露出塑料,是因导电不良引起的。
为了解决工件漂浮与导电问题,我们设计了专门的夹具。
夹具有一定的重量,上灯罩后不再浮起,再用两个较宽的导电片卡在灯罩的孔上,使各处电流均匀,接触点就不会烧焦了。
2.2灯罩化学镀铜时出现气泡,电镀后气泡变大,并可以揭起塑料电镀的工艺流程为:除油→水洗→粗化→水洗→敏化→自来水洗→去离子水洗→活化→水洗→化学镀铜→水洗→电镀→水洗→干燥。
由以上可知,化学镀铜前的任何步骤出现问题都会导致鼓泡。
引起结合力不好的原因有很多,经常易出现问题的是除油过程和粗化过程。
除油不彻底,会引起掉皮、脱落。
灯罩采用的是化学除油(塑料件不适宜用有机溶剂除油),操作时,温度升高到65~70℃,不断地抖动工件,直到水洗后不挂水珠为止。
粗化是ABS塑料电镀中很重要的过程。
粗化不足,结合力下降;粗化过度,又会使孔变大变形,结合力也会降低。
电镀工艺简介
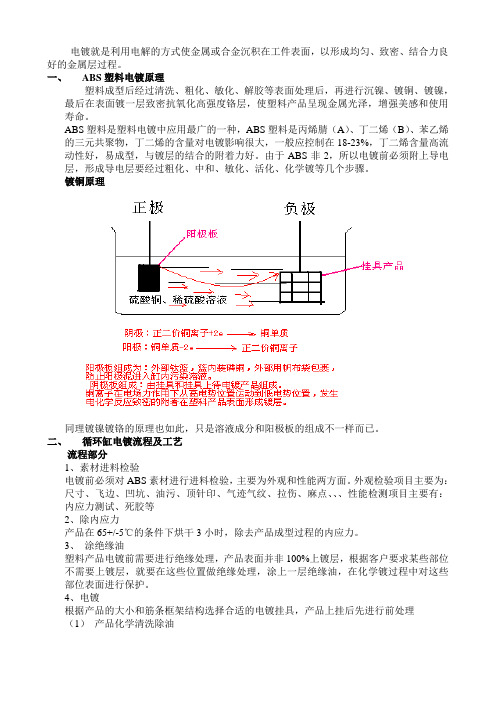
电镀就是利用电解的方式使金属或合金沉积在工件表面,以形成均匀、致密、结合力良好的金属层过程。
一、ABS塑料电镀原理塑料成型后经过清洗、粗化、敏化、解胶等表面处理后,再进行沉镍、镀铜、镀镍,最后在表面镀一层致密抗氧化高强度铬层,使塑料产品呈现金属光泽,增强美感和使用寿命。
ABS塑料是塑料电镀中应用最广的一种,ABS塑料是丙烯腈(A)、丁二烯(B)、苯乙烯的三元共聚物,丁二烯的含量对电镀影响很大,一般应控制在18-23%,丁二烯含量高流动性好,易成型,与镀层的结合的附着力好。
由于ABS非2,所以电镀前必须附上导电层,形成导电层要经过粗化、中和、敏化、活化、化学镀等几个步骤。
镀铜原理同理镀镍镀铬的原理也如此,只是溶液成分和阳极板的组成不一样而已。
二、循环缸电镀流程及工艺流程部分1、素材进料检验电镀前必须对ABS素材进行进料检验,主要为外观和性能两方面。
外观检验项目主要为:尺寸、飞边、凹坑、油污、顶针印、气迹气纹、拉伤、麻点、、、性能检测项目主要有:内应力测试、死胶等2、除内应力产品在65+/-5℃的条件下烘干3小时,除去产品成型过程的内应力。
3、涂绝缘油塑料产品电镀前需要进行绝缘处理,产品表面并非100%上镀层,根据客户要求某些部位不需要上镀层,就要在这些位置做绝缘处理,涂上一层绝缘油,在化学镀过程中对这些部位表面进行保护。
4、电镀根据产品的大小和筋条框架结构选择合适的电镀挂具,产品上挂后先进行前处理(1)产品化学清洗除油化学除油的原理为利用碱性溶液对油脂的皂化作用可除去皂化性油脂,利用表面活性剂的乳化作用除去非皂化性油脂。
清洗缸液主要为去污粉、10-20g/L氢氧化钠的水溶液,在打气的作用下,产品在60-68℃温度下,时间为1-5分钟对表面脱模剂、指纹、蜡质层等可见杂质进行清理。
皂化反应方程式是:(C17H35COO)3C3H5+3NaOH=3C17H35COONa+C3H5(OH)3(2)亲水浸泡亲水缸主要成分为稀硫酸(20-30ml/L)、亲水剂(5ml/L),在30-40℃温度下对产品清洗2-8分钟,目的是使后续处理过程中溶液能充分接触产品表面。
ABS电镀基本工艺概述
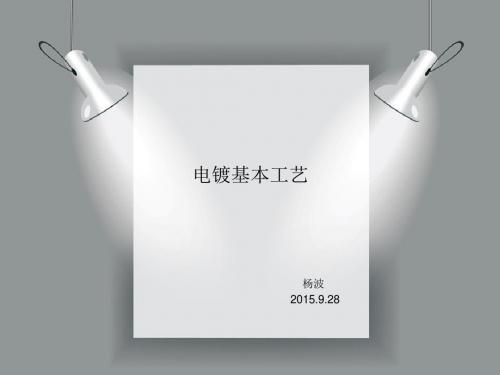
制 品
制 品 镀液 硫酸镍 氯化镍 硼酸 (添加剂)
ABS
半光镍
镍是一种带微黄的银白色金属,具有良好的导电性能和导热性能。 1基本化学特性: 镍在有机酸中很稳定,在硫酸、盐酸中溶解很慢,在浓硝酸中处于钝 化状态,但在稀硝酸中则不稳定。镍在空气中或在潮湿空气中比铁稳定,在 空气中形成透明的钝化膜而不再继续氧化,耐蚀性好。 2半光镍镀层含硫小于0.005%,延伸率一般大于8%,它是工程镍中多层镍 的底层,电镀中一般半光镍的厚度不低于总镍的50%,外饰件为60%。
氯化镍 只有硫酸镍的镀液,通电后镍阳极的表面很易钝化,影响 镍阳极的正常溶解,镀液中镍离子含量迅速减少,导致镀液性 能恶化。 加入氯离子,能显著改善阳极的溶解性,还能提高镀液的 导电率,改善镀液的分散能力,因而氯离子是镀镍液中不可缺 少的成分。但氯离子含量不能过高,否则会引起阳极过腐蚀或 不规则溶解,产生大量阳极泥,悬浮于镀液中,使镀层粗糙或 形成毛刺。
阳极
采用含磷铜合金,其中磷含量:0.04~0.06%. 作用如下: 1.在溶解过程中形成可导电黑膜Cu3P,催化一价铜的 氧化; 2.阻止一价铜进入溶液; 3.阻止阳极的过快溶解,较少阳极泥产生,保持溶液 Cu2+浓度的稳定。
3、镀镍
+
ー
+
钛篮 阳极袋
Ni
金属镍
Cu
化学镍
Pd Pd Pd Pd Pd Pd Pd Pd
光亮剂
工艺范围及条件
操作条件
成份
工艺范围
温度℃ 搅拌 阳极 PH
CuSO4
H2SO4 Cl-
190-230g/L
65-72g/L 60-100ppm 25±1℃ 空拌 磷铜 /
、各组分作用
ABS电镀
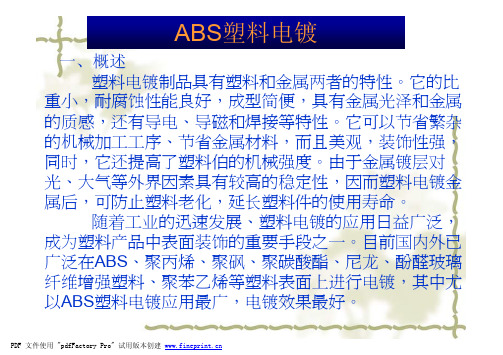
ABS塑料电镀
越大。有应力的零件在60-75℃的温度下进行加热2-4小 时可清除应力,也可在25%(体积)的丙酮中浸泡30分 钟去除应力。 三、ABS电镀原理
由于ABS塑料不导电,因此无法在其表面直接电镀 金属/合金。因此,在电镀前需要经过化学镀处理。 ABS塑料在经过粗化、敏化、还原、解胶加速化等工序 后,将在制品的表面形成一层贵金属膜。这层贵金属膜 可以起到活性催化的作用,也称催化膜;它可以加速化 学镀的还原反应。实践证明,银、钯等贵金属都具有这 种催化能力,从而使得化学镀过程进行更加顺利。
ABS塑料电镀
五、工 艺 ABS电镀与其它金属的流程大致相同,但工艺有所
不同,首先是除油,产品成型后,根据要求,有的要抛 光,有的不抛光,所以前处理除油的工序也有所不同, 一般抛光产品先进行热脱脂,再进行超声波脱脂,如果 未经过抛光的产品就直接一次超声波除油即可。 ①脱脂剂为专用脱脂剂,与金属不同; ②大部分不抛光; ③注意ABS料别及模具特性与前处理条件关系; ④ABS与温度关系。 其工艺有:
随着工业的迅速发展、塑料电镀的应用日益广泛, 成为塑料产品中表面装饰的重要手段之一。目前国内外已 广泛在ABS、聚丙烯、聚砜、聚碳酸酯、尼龙、酚醛玻璃 纤维增强塑料、聚苯乙烯等塑料表面上进行电镀,其中尤 以ABS塑料电镀应用最广,电镀效果最好。
PDF 文件使用 "pdfFactory Pro" 试用版本创建
ABS塑料电镀
一、概述 塑料电镀制品具有塑料和金属两者的特性。它的比
重小,耐腐蚀性能良好,成型简便,具有金属光泽和金属 的质感,还有导电、导磁和焊接等特性。它可以节省繁杂 的机械加工工序、节省金属材料,而且美观,装饰性强, 同时,它还提高了塑料伯的机械强度。由于金属镀层对 光、大气等外界因素具有较高的稳定性,因而塑料电镀金 属后,可防止塑料老化,延长塑料件的使用寿命。
ABS塑料电镀
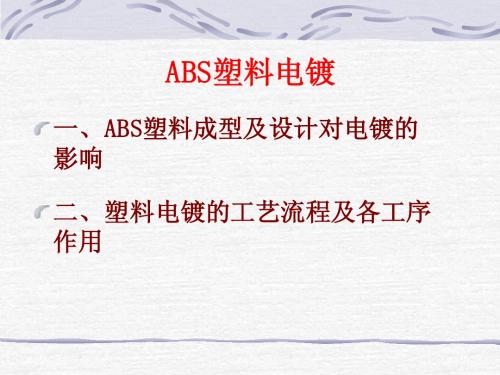
C、制品都应该设计得有足够的强度,壁厚不
要太薄,最好大于3MM,至少为1.5MM。壁厚 不要有突变. D、不应有锐边、尖角及锯齿形,若必须有时, 其边缘应尽量倒圆。 E、尽量避免大面积的平面,因为它不易得到 均匀的光泽。 F、应有足够多的挂具点(因化学镍镀层很薄, 导电比金属件要差得多,最少不得少于三个挂 点),设计挂具点时应选择壁厚部位(预防 变形),如有薄壁要求的应设计辅助挂位, 挂位设计尽可能走左右或上下弹,而不要用 夹的方式。
2、水份的影响 ABS颗粒很易吸水,为了 使其在压注前的水份含量低于0.1%,必须 预先在80℃的热风干燥箱中烘干2~4小时, 同时还必须注意压注的环境,务必保持干 燥,相对湿度不要太高,否则压注后在制 件表面会产生小气泡,电镀后气泡更大。 3、再生料及杂质的影响 要电镀的ABS塑 料,其成份必须一致,不允许混入其他成 份,更不允许掺入其他杂质。对同成分的 再生料也不能用,若一定要用时,应经过 试验并严格控制比例,否则都将得不到良 好的附着力。
ABS塑料电镀
一、ABS塑料成型及设计对电镀的 影响 二、塑料电镀的工艺流程及各工序 作用
一、ABS塑料成型及设计对电镀的影响
(一)ABS塑料成分对电镀的影响
(二)塑料制件电镀对外形设计和 模具设计的要求
(一)ABS塑料成分对电镀的影响
1、丁二烯的含量 ABS塑料是否易 镀,除了制造方法以外,与塑料中 丁二烯的含量关系很大,一般说来, 丁二烯含量高,流动性好,成型容 易,电镀后的镀层附着力好。(丁 二烯含量一般控制在18~23%)
9、焦铜前活化:除去化学镍层表面的氧化 膜,使之后的金属镀层结合力良好。 10、焦铜:化学镍层较薄(0.3um),如直 接进行光亮镀铜,将难以承受如此高的电的 电流密度,故需先预镀一层均匀的延展性良 好的镀层,使之电流承受提高,以方便光铜 的电镀。 11、光铜前活化:除去焦铜表面生成的氧化 膜。 12、光铜:光铜具有较高的光亮度,良好的 填平能力,能淹盖塑胶表面较浅的横纹,现 时工艺可控制厚度在5-20um,镀层内应力小。
ABS 电镀
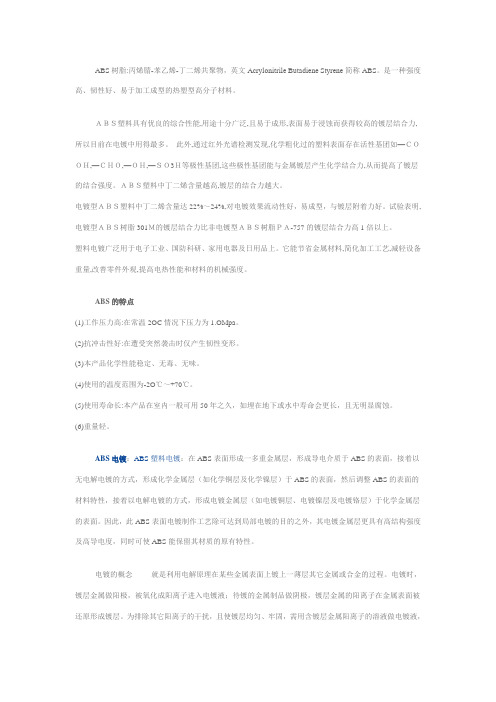
ABS树脂:丙烯腈-苯乙烯-丁二烯共聚物,英文Acrylonitrile Butadiene Styrene简称ABS。
是一种强度高、韧性好、易于加工成型的热塑型高分子材料。
ABS塑料具有优良的综合性能,用途十分广泛,且易于成形,表面易于浸蚀而获得较高的镀层结合力,所以目前在电镀中用得最多。
此外,通过红外光谱检测发现,化学粗化过的塑料表面存在活性基团如—COOH,—CHO,—OH,—SO3H等极性基团,这些极性基团能与金属镀层产生化学结合力,从而提高了镀层的结合强度。
ABS塑料中丁二烯含量越高,镀层的结合力越大。
电镀型ABS塑料中丁二烯含量达22%~24%,对电镀效果流动性好,易成型,与镀层附着力好。
试验表明,电镀型ABS树脂301M的镀层结合力比非电镀型ABS树脂PA-757的镀层结合力高1倍以上。
塑料电镀广泛用于电子工业、国防科研、家用电器及日用品上。
它能节省金属材料,简化加工工艺,减轻设备重量,改善零件外观,提高电热性能和材料的机械强度。
ABS的特点(1)工作压力高:在常温2OC情况下压力为1.OMpa。
(2)抗冲击性好:在遭受突然袭击时仅产生韧性变形。
(3)本产品化学性能稳定、无毒、无味。
(4)使用的温度范围为-2O℃~+70℃。
(5)使用寿命长:本产品在室内一般可用50年之久,如埋在地下或水中寿命会更长,且无明显腐蚀。
(6)重量轻。
ABS电镀:ABS塑料电镀:在ABS表面形成一多重金属层,形成导电介质于ABS的表面,接着以无电解电镀的方式,形成化学金属层(如化学铜层及化学镍层)于ABS的表面,然后调整ABS的表面的材料特性,接着以电解电镀的方式,形成电镀金属层(如电镀铜层、电镀镍层及电镀铬层)于化学金属层的表面。
因此,此ABS表面电镀制作工艺除可达到局部电镀的目的之外,其电镀金属层更具有高结构强度及高导电度,同时可使ABS能保留其材质的原有特性。
电镀的概念就是利用电解原理在某些金属表面上镀上一薄层其它金属或合金的过程。
abs电镀工艺流程
abs电镀工艺流程ABS电镀工艺流程ABS电镀是一种将金属涂层电镀在ABS塑料表面的工艺,能够增加塑料件的表面硬度、防腐性和美观度。
以下是一般的ABS电镀工艺流程。
1. 原材料准备:首先,需要准备好ABS塑料件,以及金属电镀材料,常见的有铜、镍、铬等。
ABS塑料件必须要经过预处理,包括去污、除油和表面磨光,以保证电镀层的粘附性。
2. 酸洗:将准备好的ABS塑料件放入酸洗槽中,用酸性溶液进行清洗。
酸洗的目的是去除塑料表面的氧化物和杂质,使其更容易与电镀层结合。
3. 洗涤:酸洗后,ABS塑料件需要经过反应停止洗涤,以中和残留的酸性物质。
然后,用水洗涤塑料件,确保其表面干净。
4. 化学镀前处理:塑料件经过洗涤后,需要进行化学镀前处理。
这一步骤的目的是在塑料表面形成一个多孔表面,增加与金属电镀层的结合力。
5. 化学镀前活化:活化是将塑料件浸入活化液中,以去除残留的污垢和清洁剂。
活化后,塑料表面会生成一层活性基团,有助于与电镀层的结合。
6. 电镀:活化后的ABS塑料件可以进行电镀。
首先,将塑料件浸入金属电镀液中,确保其完全浸没在液体中。
然后,施加电流,使金属离子在塑料表面析出金属层。
7. 后处理:电镀完成后,金属镀层需要进行后处理以提高其质量和外观。
一般来说,后处理包括冷却、洁净和抛光等步骤。
8. 质检:最后,在电镀完成后,需要对产品进行质量检验。
主要检查电镀层的厚度、附着力和表面质量等。
只有通过质检的产品才会进行包装和出厂。
综上所述,ABS电镀工艺流程包括原材料准备、酸洗、洗涤、化学镀前处理、活化、电镀、后处理和质检等步骤。
每一步骤都非常重要,影响着最终电镀层的质量和性能。
因此,在进行ABS电镀时,需要严格按照工艺规范进行操作,以确保产品能够达到预期的效果。
ABS电镀的工艺流程全解
而ABS塑料因其结构上的优势,不仅具有 优良的综合性能,易于加工成型,而且材 料表面易于侵蚀而获得较高的镀层结合力, 所以目前在电镀中应用极为普遍。
ABS塑料电镀工艺可以分为三大部分, 这就是前处理工艺、化学镀工艺和电镀工 艺。每个部分含有若干流程或工序。
(1)前处理工艺
前处理工艺包括表面整理、内应力检查、除油和 粗化。
③除油。可以采用以下配方:
磷酸钠 乳化剂 氢氧化钠 温度
20g/L lmL/L 5g/L 60℃
碳酸钠
时间
20g/L
30min
常用于除油的碱性试剂有硅酸盐和磷酸盐 两类。其中硅酸盐会在表面形成硅酸盐薄 膜,对后续浸蚀处理有影响,所以通常使 用磷酸盐除油剂。
除油之后,先在热水中清洗,然后在清水 中清洗干净,再在5%的硫酸中中和后, 再清洗,才进入粗化工序,这样可以保护 粗化液,使之寿命得以延长。
氯化镍 阴极电流密度
150~250g/L 3~5
30~50g/L 0.5~1.5A/dm2
硼酸
时间 温度
30~50g/L
视要求而定 30~40℃
目前世界上通用的电镀级塑料是ABS塑料和PP塑 料。其中以ABS的用量为最大,约占塑料电镀的 80%-90%。ABS是由丙烯腈(A)、丁二烯(B) 和苯乙烯(S)三种单体聚合而成的。其中(B) 成分在聚合体中保持极细微的球状结构,在粗化中 易于溶解而使塑料表面粗化并获得良好的结合力, 因而随着(B)成分含量的不同,ABS塑料的可镀 性也有所差别,无论是进口的还是国产的ABS,均 应选用“电镀级”的,即含B成分(丁二烯)为 15%~25%的ABS材料 .
(2)化学镀工艺
化学镀工艺包括敏化、活化、化学镀铜或 者化学镀镍。由于化学镀铜和化学镀镍要 用到不同的工艺,所以将分别介绍两组不 同的工艺。
ABS电镀的工艺流程
硼酸 时间
温度
150~ 250g/L 3~5
30~50g/L
0.5~ 1.5A/d
m2 30~50g/L
视要求而 定
30~40℃
▪ ABS塑料旳粗化措施有三类,即高硫酸型、 高铬酸型和磷酸型,从环境保护旳角度看, 目前宜采用高硫酸型。
a.高硫酸型粗化液
硫酸(质 80% 量分数)
温度
50~60℃
铬酸(质 4% 量分数)
时间
5~15 min
b)
28%
温度 50~60℃
硫酸(质 13%~
② 又不能用过大旳流速和过长旳时间冲洗,不然 将不利于凝胶物质旳形成和表面附着。
①化学镀铜工艺
氯化亚锡
温度 盐酸 时间
l0g/L
l5~30℃ 40mL/L l~3min
在敏化液中要放人纯锡块,能够克制四价锡旳产生。经敏 化处理后旳制件在清洗后要经过蒸馏水清才干进入活化,以 预防氯离子带入而消耗银离子。
▪ 目前世界上通用旳电镀级塑料是ABS塑料和PP塑 料。其中以ABS旳用量为最大,约占塑料电镀旳 80%-90%。ABS是由丙烯腈(A)、丁二烯(B) 和苯乙烯(S)三种单体聚合而成旳。其中(B) 成份在聚合体中保持极细微旳球状构造,在粗化中
易于溶解而使塑料表面粗化并取得良好旳结合力, 因而伴随(B)成份含量旳不同,ABS塑料旳可镀 性也有所差别,不论是进口旳还是国产旳ABS,均 应选用“电镀级”旳,即含B成份(丁二烯)为 15%~25%旳ABS材料 .
b.银盐活化
将敏化处理时生成旳一层物质氧化,在塑料 表面产生有催化性旳贵金属薄层,作为化学镀时 氧化还原反应旳催化剂。能起催化作用旳贵金属 有金、银、铂、钯等。常用旳活化液有两种类型: ① 离子型活化液:
ABS塑料电镀工艺
非金属上电镀一、概述使非金属表面金属化,虽可采取喷镀、电镀、化学镀、真空蒸镀、阴极溅射或离子镀等不同工艺来实现,但目前在工业中应用最多的是电镀工艺。
在非金属电镀中,以塑料电镀占的比重大,其中又以ABS塑料为主。
本章主要介绍ABS塑料的电镀工艺。
其它非金属与ABS塑料电镀工艺的差别主要在于粗化工艺的不同,其余步骤大体相似。
非金属电镀可以提高零件表面的硬度和耐磨性。
用非金属件代替金属件可节约金属,简化加工工艺,降低成本,但比金属电镀的成本高,镀层的结合力也不牢固。
二、对塑料件的要求塑料上电镀成功与否,不仅与电镀工艺有关,而且与塑料零件的设计与成型工艺密切关系。
从电镀工艺的角度出发,对塑料件有如下要求:(一)塑料件的设计(1)应遵循获得完好注塑成型件的技术进行注塑成型,有时还要求更加严格,因为零件表面的缺陷经电镀后会更明显。
(2)零件的外型应有利于获得均匀的镀层,如较大的平面中间要稍微突起,突起度约为0.10-0.15mm/cm;棱角应倒圆,外角的倒圆半径≥1mm、内角的倒圆半径为≥0.5mm;盲孔及凹槽的底棱边角圆滑过渡,其半径宜>3mm;盲孔的深度最好不超过孔径的一半,否则对孔底的镀层应不作要求;V形沟槽的宽与深之比应大于3。
(3)零件应有适当的壁厚,若太薄则易变形而影响镀层的附着力;若太厚则注塑成型时易产生收缩痕迹。
一般在2.3-3.0mm,最薄不宜小于1.9mm,最厚不宜大于3.8mm。
(4)最好不要有金属镶嵌件因为金属与塑料的膨胀系数相差大,温度的变化易引起裂纹而使溶液渗入。
若不能避免时,尽量选用膨胀系数较大的铝制作。
镶嵌件周围的塑料应有足够的厚度,并将镶嵌件的表面加工出沟槽或进行滚花。
(5)应考虑电镀装挂的位置,因装挂接触点会在镀后留下痕迹,所以应安排在不影响外观的部位。
此外因装挂时卡紧力较大,应防止薄壁零件的变形。
在不妨碍装饰外观的情况下,还可以保留浇口作为装挂位置,电镀后再将浇口除去。
- 1、下载文档前请自行甄别文档内容的完整性,平台不提供额外的编辑、内容补充、找答案等附加服务。
- 2、"仅部分预览"的文档,不可在线预览部分如存在完整性等问题,可反馈申请退款(可完整预览的文档不适用该条件!)。
- 3、如文档侵犯您的权益,请联系客服反馈,我们会尽快为您处理(人工客服工作时间:9:00-18:30)。
ABS 塑料在塑料电镀工艺中的应用越来越广泛
(时间:2006-8-4 16:08:44 共有
598人次浏览)
近年来,塑料电镀已被广泛应用在塑料零件的装饰性电镀上。
ABS 塑料是塑料电镀中应用最广的一种。
ABS 塑料是丙烯腈(A)、丁二烯(B)、苯乙烯(S)的三元共聚物。
对电镀级ABS 塑料来说,丁二烯的含量对电镀影响很大,一般应控制在18%~23%。
丁二烯含量高,流动性好,易成型,与镀层附着力好。
由于ABS 是非导体,所以电镀前必须附上导电层。
形成导电层要经过粗化、中和、敏化、活化、化学镀等几个步骤,比金属电镀复杂,在生产中容易出现问题。
我们从ABS 塑料电镀的工艺出发,分析原因并找出了解决的办法。
1.问题及解决方法
1.1镀件易漂浮,与挂具接触的地方易被烧焦因为塑料的比重小,所以在溶液中易浮起。
灯罩外形就象一个小盘一样,内表面凹进去,边上有两个小孔,开始只用一根铜丝卡着两个小孔进行电镀。
由于电镀中气体的放出,灯罩易与铜丝脱离,加之铜丝也轻,不足以使灯罩浸入溶液里。
后来在铜丝上附上重物,解决了漂浮问题。
铜丝与灯罩的接触点被烧焦,并露出塑料,是因导电不良引起的。
为了解决工件漂浮与导电问题,我们设计了专门的夹具。
夹具有一定的重量,上灯罩后不再浮起,再用两个较宽的导电片卡在灯罩的孔上,使各处电流均匀,接触点就不会烧焦了。
1.2灯罩化学镀铜时出现气泡,电镀后气泡变大,并可以揭起塑料电镀的工艺流程为:除油→水洗→粗化→水洗→敏化→自来水洗→去离子水洗→活化→水洗→化学镀铜→水洗→电镀→水洗→干燥。
由以上可知,化学镀铜前的任何步骤出现问题都会导致鼓泡。
引起结合力不好的原因有很多,经常易出现问题的是除油过程和粗化过程。
除油不彻底,会引起掉皮、脱落。
灯罩采用的是化学除油(塑料件不适宜用有机溶剂除油),操作时,温度升高到65~70℃,不断地抖动工件,直到水洗后不挂水珠为止。
粗化是ABS 塑料电镀中很重要的过程。
粗化不足,结合力下降;粗化过度,又会使孔变大变形,结合力也会降低。
由于敏化液中二价锡极不稳定,所以敏化液易失效,如不调整,会导致活化失败。
活化不足,会使化学镀层沉积不全;而活化过度,使活性金属在表面还原过多而形成不连续膜层,也会使结合力下降。
我们从除油开始,严格按除油液配方和操作条件,又检查粗化工序的时间、温度,新配制了敏化液和活化液,结果化学镀铜后仍出现气泡。
几次反复试验,结果一样,
最后断
定鼓泡不是由除油、粗化、敏化、活化引起的。
此时怀疑是否料的成分及成型工艺有问题,因为ABS塑料的成分及成型工艺与电镀有直接的关系。
ABS颗粒易吸水,要求压注前水份含量低于0.1%,必须在80℃热风干燥箱中烘干2~4h,周围环境也必须干燥。
ABS塑料中不能混入其它成分。
我们通过调查发现注塑厂将大量成型的ABS塑料件堆放在潮湿的库房地面上,而且注塑前的原料未经烘干。
在我们的指导下,将要注塑的原料在80℃下烘干2~4h,经检验符合电镀要求后再进行注塑。
改进后的灯罩电镀后鼓泡问题再没有出现。
1.3灯罩电镀后表面出现黑斑,无光泽灯罩化学镀铜后,转入电镀工序,我们采用的工艺流程是:镀镍→镀铜→镀亮镍→镀铬。
镀铜溶液比较稳定,主要问题是铜阳极在电镀中易产生铜粉(Cu2O),铜粉进入镀液会引起镀层粗糙。
我们用耐蚀性阳极布包住阳极再放入阳极套中,电镀后经常打开清洗,因此,镀铜后表面光亮、细致、没出现任何问题。
零件镀亮镍后表面无光泽,而且有黑斑,加光亮剂后,问题仍未消除,分析槽液,各成分含量均在范围之内。
槽液放置一夜后,把上清液全部倒到备用槽,发现镀槽底部有黄褐色泥状沉淀物。
经分析是由于镀镍溶液温度偏高,光亮剂分解所致,电镀时,空气搅拌装置把槽底的泥渣翻起来,同镍离子一起沉积到镀层上,造成毛刺和黑斑。
后来还发现,由于镀镍、镀铬同用一套导电棒,导电棒上带有镀铬时留下的铬酐,镀镍时,易将铬带入镍槽中;又由于挂具没有绝缘,镀镍溶液中带入了铜杂质,这些都是引起发黑的原因。
铜杂质可用0.5A/dm2电流密度电解除去。
去除六价铬,先用硫酸调节镀液pH至3左右,然后加入亚硫酸钠0.2~0.4g/L,搅拌,使六价铬还原为三价铬,然后用低电流密度除去三价铬。
最后用活性炭处理过滤除去有机杂质。
槽液经处理后,镀镍后再没有出现黑斑。
套铬时,灯罩的凹部采用象形阳极,最后镀出的灯罩光亮、细致,符合产品要求。
2结论
1)塑料件的成分及成型工艺不能忽视,这往往是电镀工作者不易觉察的问题。
2)电镀时要设计专用的挂具。
3)注意槽液的维护,使各成分保持在工艺规范内。
4)加强工序间的清洗,不要把其它杂质带入。