液体静压蜗杆传动副的设计及油膜厚度计算
液体静压导轨支承油膜的有限元分析
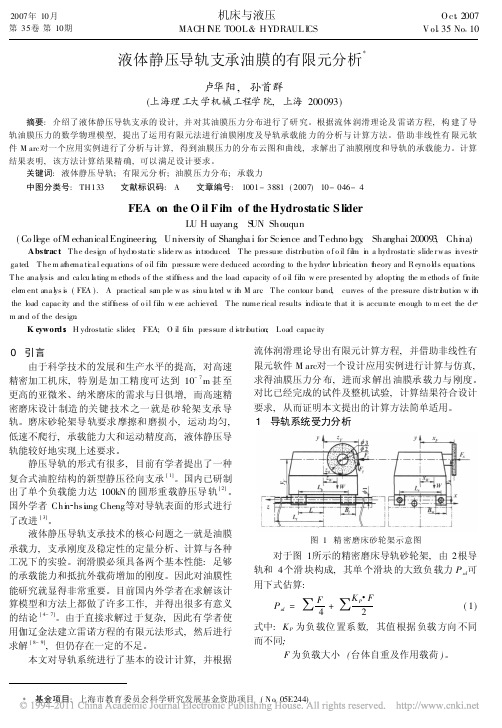
48
机床与液压
第 35卷
zm ), 用线性插值法容易推导出任一单元形状函数为
p = N ipi i, j, m
其中:
Ni
=
1 2e
( ai
+ biz + ci ),
1
e=
1 2
1
1
i zi j zj , m zm
ai = zj - zm, bi = m - j, ci = j zm - m zj。 由此求得
e
1
4
2 e
h3
e
ar a s +
1
2
br
bs
d dz
由于求解区域内的总压力泛函等于各单元压力泛
函之和, 从而有
E0
J ( p ) = J(e) (p ) e=1
式中 E0 为单元总数。
于是
式中:
E0
J(p) =
J( e) (p ) = [K ] {P } - {F } ( 9)
pi
e= 1
pi
i= 1, 2, , n, n 为节点总数;
个油腔的压力为
i 的第 i
pri
=
1+
Rg Rh0
ps ( 1- A
cos i ) 3
( 3)
式中: Rh0为在设计状态 ( = 0) 时的油腔液阻,
Rh0 =
6ab t h0 [ a ( L - a ) +
bD
0]
h 0 为导轨平均半径间隙;
b为周向封油面宽度;
t 为油膜动力粘度; Rg 为节流器液阻;
式中: D 为导轨直径;
L 为滑块长度;
a 为轴向封油面宽度;
数控机床液体静压导轨结构的优化设计
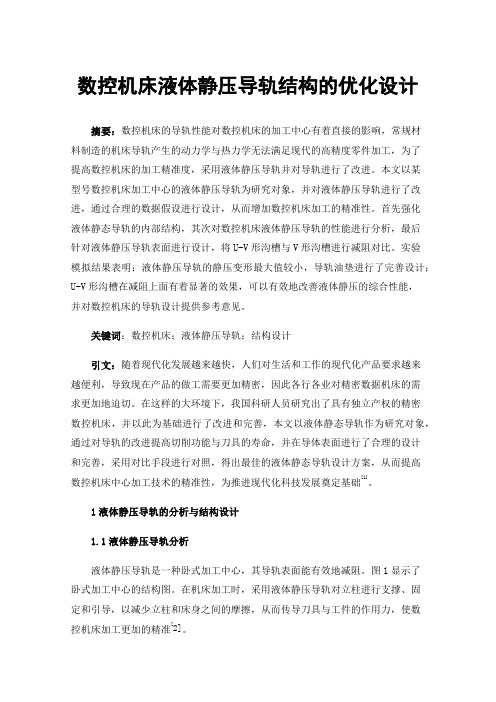
数控机床液体静压导轨结构的优化设计摘要:数控机床的导轨性能对数控机床的加工中心有着直接的影响,常规材料制造的机床导轨产生的动力学与热力学无法满足现代的高精度零件加工,为了提高数控机床的加工精准度,采用液体静压导轨并对导轨进行了改进。
本文以某型号数控机床加工中心的液体静压导轨为研究对象,并对液体静压导轨进行了改进,通过合理的数据假设进行设计,从而增加数控机床加工的精准性。
首先强化液体静态导轨的内部结构,其次对数控机床液体静压导轨的性能进行分析,最后针对液体静压导轨表面进行设计,将U-V形沟槽与V形沟槽进行减阻对比。
实验模拟结果表明:液体静压导轨的静压变形最大值较小,导轨油垫进行了完善设计;U-V形沟槽在减阻上面有着显著的效果,可以有效地改善液体静压的综合性能,并对数控机床的导轨设计提供参考意见。
关键词:数控机床;液体静压导轨;结构设计引文:随着现代化发展越来越快,人们对生活和工作的现代化产品要求越来越便利,导致现在产品的做工需要更加精密,因此各行各业对精密数据机床的需求更加地迫切。
在这样的大环境下,我国科研人员研究出了具有独立产权的精密数控机床,并以此为基础进行了改进和完善,本文以液体静态导轨作为研究对象,通过对导轨的改进提高切削功能与刀具的寿命,并在导体表面进行了合理的设计和完善,采用对比手段进行对照,得出最佳的液体静态导轨设计方案,从而提高数控机床中心加工技术的精准性,为推进现代化科技发展奠定基础[1]。
1液体静压导轨的分析与结构设计1.1液体静压导轨分析液体静压导轨是一种卧式加工中心,其导轨表面能有效地减阻。
图1显示了卧式加工中心的结构图。
在机床加工时,采用液体静压导轨对立柱进行支撑、固定和引导,以减少立柱和床身之间的摩擦,从而传导刀具与工件的作用力,使数控机床加工更加的精准[2]。
图1 卧式加工中心结构示意图例如,在一个经典的车床加工过程中,其主要的加工程序中:切削量f=0.5mm/r,则切削速度 vc=150 m/min,其它的参数都是通过参考相关的设计手册得到的。
液体静压导轨油膜厚度的控制及理论分析
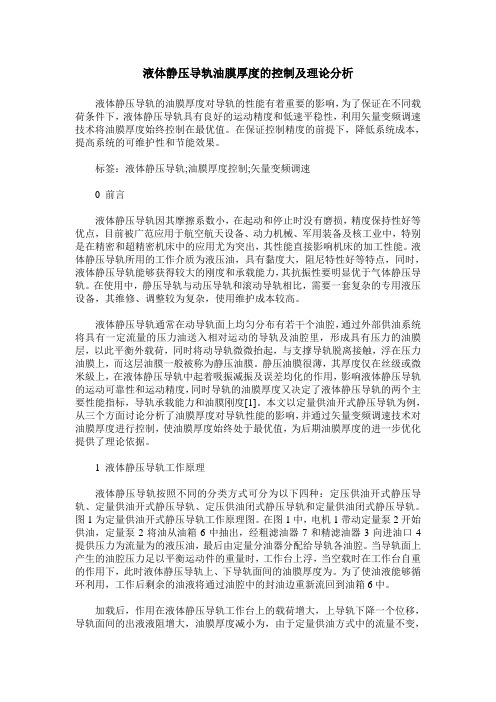
液体静压导轨油膜厚度的控制及理论分析液体静压导轨的油膜厚度对导轨的性能有着重要的影响,为了保证在不同载荷条件下,液体静压导轨具有良好的运动精度和低速平稳性,利用矢量变频调速技术将油膜厚度始终控制在最优值。
在保证控制精度的前提下,降低系统成本,提高系统的可维护性和节能效果。
标签:液体静压导轨;油膜厚度控制;矢量变频调速0 前言液体静压导轨因其摩擦系数小,在起动和停止时没有磨损,精度保持性好等优点,目前被广范应用于航空航天设备、动力机械、军用装备及核工业中,特别是在精密和超精密机床中的应用尤为突出,其性能直接影响机床的加工性能。
液体静压导轨所用的工作介质为液压油,具有黏度大,阻尼特性好等特点,同时,液体静压导轨能够获得较大的刚度和承载能力,其抗振性要明显优于气体静压导轨。
在使用中,静压导轨与动压导轨和滚动导轨相比,需要一套复杂的专用液压设备,其维修、调整较为复杂,使用维护成本较高。
液体静压导轨通常在动导轨面上均匀分布有若干个油腔,通过外部供油系统将具有一定流量的压力油送入相对运动的导轨及油腔里,形成具有压力的油膜层,以此平衡外载荷,同时将动导轨微微抬起,与支撑导轨脱离接触,浮在压力油膜上,而这层油膜一般被称为静压油膜。
静压油膜很薄,其厚度仅在丝级或微米級上,在液体静压导轨中起着吸振减振及误差均化的作用,影响液体静压导轨的运动可靠性和运动精度,同时导轨的油膜厚度又决定了液体静压导轨的两个主要性能指标,导轨承载能力和油膜刚度[1]。
本文以定量供油开式静压导轨为例,从三个方面讨论分析了油膜厚度对导轨性能的影响,并通过矢量变频调速技术对油膜厚度进行控制,使油膜厚度始终处于最优值,为后期油膜厚度的进一步优化提供了理论依据。
1 液体静压导轨工作原理液体静压导轨按照不同的分类方式可分为以下四种:定压供油开式静压导轨、定量供油开式静压导轨、定压供油闭式静压导轨和定量供油闭式静压导轨。
图1为定量供油开式静压导轨工作原理图。
静压蜗杆预升量及蜗杆箱上垫板厚度的计算

再将 式 ( 代 入式 ( , 一 步可得 3) 4) 进
.
1
、
⑥ 测 出 下 导 轨 板 3和 l 1处 的 实 际 同 隙 6 即 蜗 杆 ,
和蜗母 条无 间隙结合 时 , 杆 箱下 垫板 的厚度 。 蜗 当 系 统 建 立 静 压 时 , 座 7 应 相 对 床 身 浮 起 △.约 滑 ( OO mm ) 同 时 要 求 静 压 蜗 杆 和 蜗 母 条 的 每 齿 两 删 面 闭 ,2 , 隙 与 滑 座 的 静 压 浮 起 量 △. 同 ( 图 5所 示 ) 由 于 蜗 相 如 。 母 条 齿 面 与 导 轨 面 存 在 夹 角 , 所 以 只 有 当 蜗 杆 箱 相 对 蜗 母 条 升 起 时 , 能满 足 上述 两 处 △ 才 的 要 求 ( 如
式 中 △ — — 蜗 母 条 副 单 齿 两 侧 间 隙
浮起 量 )
一
( 滑 座 静 压 即
l
bt =( b -
成 品精度 均 达到 了合格 品的要求 。
门 ’
盆
( 辑 编 跃 华 )
蜗 母 条 压 力 角 ( 般 为 2 。 一 0)
经 实 践证 明 , 这 种 方 法调 整后 , 消 除 蜗杆 箱及 用 可 滑 座 的爬 行现 象 , 静 压 蜗 母条 副 传 动精度 稳 定 , 项 使 各
镗 铣 床 滑 座 与 床 身 结 合 是 通 过 一 对 滑 动 导 轨 副 实
现 的 ,传 递 动 力 的 蜗 杆 箱 穿 人 滑 座 并 用 螺 栓 借 助 箱 口
面 紧 固 在 滑 座 上 , 母 条 则 装 配 在 床 身 上 , 杆 箱 与 滑 蜗 蜗 座 之 间 插 人 垫 板 ( 图 1所 示 ) 这 样 滑 动 导 轨 副 和 蜗 如 , 母 条 副 就 构 成 一 个 封 闭 的 尺 寸 链 。 当 机 床 液 压 系 统 建
蜗杆各部分尺寸计算公式
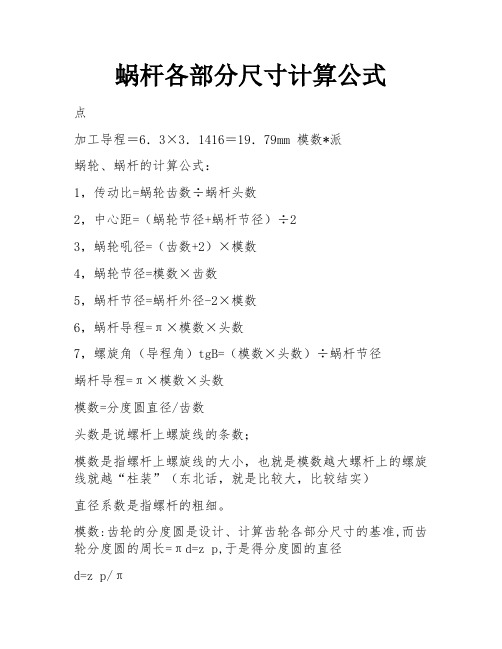
蜗杆各部分尺寸计算公式点加工导程=6.3×3.1416=19.79mm 模数*派蜗轮、蜗杆的计算公式:1,传动比=蜗轮齿数÷蜗杆头数2,中心距=(蜗轮节径+蜗杆节径)÷23,蜗轮吼径=(齿数+2)×模数4,蜗轮节径=模数×齿数5,蜗杆节径=蜗杆外径-2×模数6,蜗杆导程=π×模数×头数7,螺旋角(导程角)tgB=(模数×头数)÷蜗杆节径蜗杆导程=π×模数×头数模数=分度圆直径/齿数头数是说螺杆上螺旋线的条数;模数是指螺杆上螺旋线的大小,也就是模数越大螺杆上的螺旋线就越“柱装”(东北话,就是比较大,比较结实)直径系数是指螺杆的粗细。
模数:齿轮的分度圆是设计、计算齿轮各部分尺寸的基准,而齿轮分度圆的周长=πd=z p,于是得分度圆的直径d=z p/π由于在上式中π为一无理数,不便于作为基准的分度圆的定位.为了便于计算,制造和检验,现将比值p/π人为地规定为一些简单的数值,并把这个比值叫做模数(module),以m表示,即令其单位为mm.于是得:模数m是决定齿轮尺寸的一个基本参数.齿数相同的齿轮模数大,则其尺寸也大.为了便于制造,检验和互换使用,齿轮的模数值已经标准化了.建筑模数建筑模数指建筑设计中选定的标准尺寸单位。
它是建筑设计、建筑施工、建筑材料与制品、建筑设备、建筑组合件等各部门进行尺度协调的基础。
就象随便来个尺寸,建筑构件就无法标准化了,难统一。
基本模数的数值规定为100mm,以M表示,即1M= 100mm。
导出模数分为扩大模数和分模数,扩大模数的基数为3M,6M,12M,15M,30M,60M共6个;分模数的基数为1/10M,1/5M,1/2M共3个.使用3M是《中华人民共和国国家标准建筑统一模数制》中为了既能满足适用要求,又能减少构配件规格类型而规定的。
蜗杆蜗轮传动设计计算
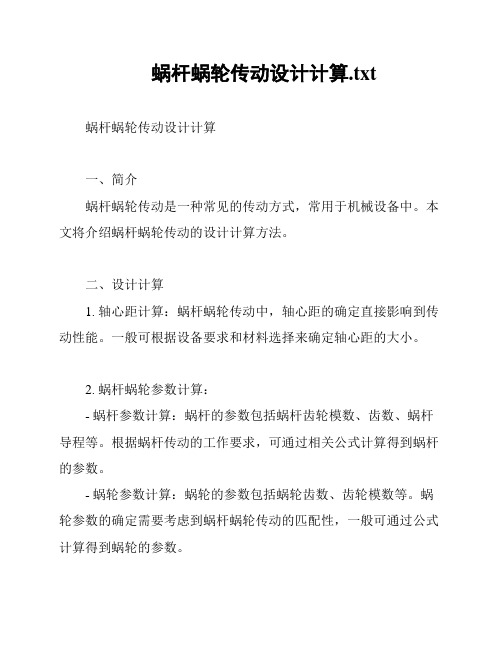
蜗杆蜗轮传动设计计算.txt蜗杆蜗轮传动设计计算一、简介蜗杆蜗轮传动是一种常见的传动方式,常用于机械设备中。
本文将介绍蜗杆蜗轮传动的设计计算方法。
二、设计计算1. 轴心距计算:蜗杆蜗轮传动中,轴心距的确定直接影响到传动性能。
一般可根据设备要求和材料选择来确定轴心距的大小。
2. 蜗杆蜗轮参数计算:- 蜗杆参数计算:蜗杆的参数包括蜗杆齿轮模数、齿数、蜗杆导程等。
根据蜗杆传动的工作要求,可通过相关公式计算得到蜗杆的参数。
- 蜗轮参数计算:蜗轮的参数包括蜗轮齿数、齿轮模数等。
蜗轮参数的确定需要考虑到蜗杆蜗轮传动的匹配性,一般可通过公式计算得到蜗轮的参数。
3. 力学计算:- 扭矩计算:根据传动功率和旋转速度,可以计算传动中所需的扭矩。
- 轴强度计算:蜗杆蜗轮传动的轴强度是设计中需要考虑的重要因素之一。
根据传动扭矩、材料强度等参数,可以进行轴强度的计算。
4. 效率计算:蜗杆蜗轮传动的效率影响着传动的能量损失。
通过相关公式和参数,可以计算蜗杆蜗轮传动的效率。
三、注意事项在进行蜗杆蜗轮传动设计计算时,需要注意以下几点:1. 使用合理的参数值和公式,确保计算结果准确可靠。
2. 考虑到材料的强度和耐磨性等因素,在选择蜗杆和蜗轮的材料时要谨慎。
3. 需要根据实际情况对设计参数进行适当调整,以满足工作要求和设备性能。
四、总结蜗杆蜗轮传动设计计算是机械设备设计中的重要内容,通过合理的设计计算能够确保传动的准确性和可靠性。
要注意选择合适的参数和材料,并根据实际情况对设计参数进行调整。
以上为蜗杆蜗轮传动设计计算的简要介绍,希望对您有所帮助。
蜗杆蜗轮基本参数计算
5.8.3 蜗杆蜗轮基本参数及几何尺寸计算
蜗杆蜗轮的设计计算是以主剖面内的参数和几何关系为基准,在主剖面内有基本参数m,α,z
还可以有无数个不同值。
由于工程中是采用与蜗杆尺寸c*=0.2。
但对于蜗杆而言,其分度圆直径d
1
的滚刀来加工蜗轮的,如果对应一种模数和压力角有无数个蜗杆直径,那么意味着一种模数和压力有无数把滚刀,这显然是不经济的。
为了限制蜗轮滚刀的数目及便于滚刀的标准化,工程上每一标准模数规定了一定数目的蜗杆分,也即规定比值
d
1
(5. q称为蜗杆直径系数(diametric quotient),且已规定有标准值。
模数m和直径系数q的标准值见表
由上式可得
蜗杆的分度圆半径为 (5.
注:①.括号内的模数尽可能不用。
②.带括号的q值用于套在轴上的齿圈,需要提高蜗杆的刚度或蜗轮齿数较多的场合。
图5.8.3-1
如图5.8.3-1所示,蜗杆螺度圆柱面的交线为螺旋线,设有两条螺旋线。
将分度圆柱展则螺旋线展成斜直线。
图中与λ有关的参数有:H ──导程,且H=z
1
P
a1
P
a1
──轴面齿距,即 P
a1
=πm 由图得
由此看出影响λ大小的因素有z
1
、q。
①.当q一定,蜗杆的齿数z
1
增多,螺旋线导程角λ增大;
②.当z
1一定,蜗杆的直径系数q增大(也即直径d
1
增大),螺旋线导程角λ减小。
螺旋线导程角λ的大小直接影响到蜗杆蜗轮传动的自锁性,λ越小,机构越易自锁。
标准阿基米德蜗杆蜗轮机构的几何尺寸计算公式见表5.8.3-2。
滑动轴承油膜厚度计算
稳健设计理论在液体动压滑动轴承中的应用滑动轴承是各种传动装置中广泛采用的支承件,特别是在高速运转机械中,为了减小摩擦,提高传动效率,要求轴承与轴颈间脱离接触并具有足够的油膜厚度,以形成液体间的摩擦状态。
在滑动轴承设计中,只有当轴承尺寸、轴承载荷、相对运动速度、润滑油的粘度、轴承间隙以及表面粗糙度之间满足一定关系时,才能实现液体摩擦。
任一参数取值不当,将出现非液体摩擦状态,导致液体摩擦的失效。
以上参数的优化设计对轴承的使用性能及寿命有十分重要的作用。
通常,在设计中,往往对轴承的各设计参数和使用条件提出更高要求。
轴承的设计参数或误差对轴承的性能的影响是非线性的,在不同的设计方案中,同样的误差程度,所产生的性能波动不尽相同。
稳健设计就是找到一种设计方案,使得液体动压轴承的性能对误差不十分敏感,同时达到较宽松的加工经济精度而降低成本的目的。
本文对某液体动压滑动轴承进行稳健设计,建立相应的数学模型,并求得优化的设计方案。
1滑动轴承的工程分析下面是径向动压滑动轴承的一组计算公式。
1.最小油膜厚度h minh min=C-e=C(1-ε)=rψ(1-ε)(1)式中C=R-r——半径间隙,R轴承孔半径;r轴颈半径;ε=e/C——偏心率;e为偏心距;ψ=C/r——相对间隙,常取ψ=(0.6-1)×10-3(v)1/4,v 为轴颈表面的线速(m/s )设计时,最小油膜厚度h min 必须满足:h min /(R z1+R z2)≥2-3[1](2)式中R z1、R z2为轴颈和轴承的表面粗糙度。
2.轴承的特性系数(索氏系数)S=μn /(p ψ2)(3)式中μ——润滑油在轴承平均工作温度下的动力粘度(Pa ·s );n ——轴颈的转速(r/s );p ——平均压强(N/m 2)用来检验轴承能否实现液体润滑。
ε值可按下面简化式求解。
A ε2+E ε+C=0(4)其中A=2.31(B/d)-2,E=-(2.052A +1),C=1+1.052A -6.4088S.上式中d ——轴径的直径(m );B ——轴承的宽度(m )通常ε选在0.5-0.95之间,超出0-1间的值,均非ε的解[1]。
蜗轮蜗杆的设计及其参数计算
7 蜗轮蜗杆的设计及其参数计算5.1 传动参数蜗杆输入功率P=5.3 kW ,蜗杆转速min /r 960n 1=,蜗轮转速m i n /r 5.56n 2=,理论传动比i=16.75,实际传动比i=17,蜗杆头数2Z 1=,蜗轮齿数为34217 Z i Z 12=⨯==,蜗轮转速min /r 5.5617960i n n 12=== 5.2 蜗轮蜗杆材料及强度计算减速器的为闭式传动,蜗杆选用材料45钢经表面淬火,齿面硬度 >45 HRC,蜗轮缘选用材料ZCuSn10Pb1,砂型铸造。
蜗轮材料的许用接触应力,由《机械设计基础》表4-5可知,[]H σ=180MPa. 估取啮合效率: 10.8η= 蜗轮轴转矩:6651122 5.250.89.55109.55107.110mm n 56.5P T N η⨯=⨯=⨯⨯=⨯⋅ 载荷系数:载荷平稳,蜗轮转速不高,取K=1.1.计算21m d 值 []22122480m d HKT Z σ⎛⎫≥⎪ ⎪⎝⎭=2534801.17.110mm 34180⎛⎫⨯⨯⨯ ⎪⨯⎝⎭=34804mm模数及蜗杆分度圆直径由《机械设计基础》表4-1取标准值,分别为: 模数 m=8 mm蜗杆分度圆直径 1d 80m m = 5.3 计算相对滑动速度与传动效率蜗杆导程角11mz 82=arctanarctan 11.31d 80γ⨯==蜗杆分度圆的圆周速度111d n 80960m /s 4.02m /s 601000601000ππυ⨯⨯===⨯⨯相对活动速度1s 4.024.098m/s cos cos11.31υυγ===当量摩擦角 取v 230 2.5ρ== 验算啮合效率()()1v tan tan11.31081tan tan 11.31 2.5γηγρ===++(与初取值相近)。
传动总效率10.960.960.810.78ηη==⨯=总 (在表4-4所列范围内)。
蜗轮蜗杆基本参数计算
5.8.3 蜗杆蜗轮基本参数及几何尺寸计算蜗杆蜗轮的设计计算是以主剖面内的参数和几何关系为基准,在主剖面内有基本参数m,α,z2,=1,c*=0.2。
但对于蜗杆而言,其分度圆直径d1还可以有无数个不同值。
由于工程中是采用与蜗杆尺寸基本相同的滚刀来加工蜗轮的,如果对应一种模数和压力角有无数个蜗杆直径,那么意味着一种模数和压力角就得备有无数把滚刀,这显然是不经济的。
为了限制蜗轮滚刀的数目及便于滚刀的标准化,工程上每一标准模数规定了一定数目的蜗杆分度圆直径d1,也即规定比值(5.8.3-1)q称为蜗杆直径系数(diametric quotient),且已规定有标准值。
模数m和直径系数q的标准值见表5.8.3-1。
由上式可得蜗杆的分度圆半径为 (5.8.3-2)注:①.括号内的模数尽可能不用。
②.带括号的q值用于套在轴上的齿圈,需要提高蜗杆的刚度或蜗轮齿数较多的场合。
图5.8.3-1如图5.8.3-1所示,蜗杆螺旋面与分度圆柱面的交线为螺旋线,设z1=2,则有两条螺旋线。
将分度圆柱展成平面,则螺旋线展成斜直线。
图中与λ有关的参数有:H ──导程,且H=z1P a1P a1──轴面齿距,即 P a1=πm由图得由此看出影响λ大小的因素有z1、q。
①.当q一定,蜗杆的齿数z1增多,螺旋线导程角λ增大;②.当z1一定,蜗杆的直径系数q增大(也即直径d1增大),螺旋线导程角λ减小。
螺旋线导程角λ的大小直接影响到蜗杆蜗轮传动的自锁性,λ越小,机构越易自锁。
标准阿基米德蜗杆蜗轮机构的几何尺寸计算公式见表5.8.3-2。
残阳渐逝,血红冲天。
半是夕阳余光,半是狰狞血雨。
是的,血,到处都是冷腥的鲜血。
整个皇宫之内,血流成河,白玉理石全被洗涮成黑红之色,到处是断壁残肢,尸横一片,到处是厮杀后的痕迹。
“为什么?”百里冰左手紧捂着胸口,瞪大着眼睛看着对面十米敌对方处,挥手点兵之人。
那是她的未婚夫,她倾尽一生所爱之人。
亦是绝杀她百里一族,将她迫入绝境之人。
- 1、下载文档前请自行甄别文档内容的完整性,平台不提供额外的编辑、内容补充、找答案等附加服务。
- 2、"仅部分预览"的文档,不可在线预览部分如存在完整性等问题,可反馈申请退款(可完整预览的文档不适用该条件!)。
- 3、如文档侵犯您的权益,请联系客服反馈,我们会尽快为您处理(人工客服工作时间:9:00-18:30)。
+,
!$ "
&* &( &) &"
&* &( +, +, &) &"
# ( %-" . ’)( ( )
) * "
考
文
献
卜炎等 8 机械传动装置设计手册 8 北京: 机械工业出版社, )!!!8 机械设计手册电机工程手册编辑委员会 8 机械工程手册 8 北京: 机 械工业出版社, )!!18 彭文生等 8 机械设计 8 武汉: 华中理工大学出版社, )!!18
第一作者: 吴晓明, 湖北武汉, 湖北工学院机械工 程系, 邮编: ("$$1B ( 编辑 (*)
力的润滑油输送到油腔中去。压力油从油腔经过四周 的封油面流出, 在封油面形成具有压力的润滑油膜, 利 用油腔和封油面的压力油来承受载荷。
"
液体静压蜗杆蜗母条的结构
($ ) 几何形状 为了提高蜗杆蜗母条承受轴向载
荷的能力, 蜗母条轴向半角可取 %& ’( , 并适当加大蜗 杆螺纹部分的工作高度。蜗杆蜗母条螺纹的啮合高度 通常取螺距的 )& % * $ 倍
[ $]
。蜗杆的螺纹圈数一般不
超过 $" , 油腔可开在蜗母条牙齿侧面或蜗杆螺纹侧面 上。当油腔开在蜗母条牙齿侧面上时, 每个齿的一侧 开一个油腔。当油腔开在蜗杆螺纹侧面上时, 采用间 断分布的多油腔形式。在后一情况下, 为使其承载能 力的波动不致过大, 要求同时位于蜗母条一个齿侧啮 合区域的完整油腔数不得少于 + * , 个。实践证明, 油 腔设在蜗母条上时, 其承载能力要比油腔设在蜗杆上 高 ")- * "’- 。空载时油腔工作压力一般为 " * "& ’ ./0。 (") 配油方式 由于蜗杆蜗母条的结构限制, 无 论油腔开在蜗杆上或蜗母条上, 压力油均由配油器通 过蜗杆体内的油孔和蜗杆两侧面的出油孔进入油腔。 配油器保证了蜗杆与蜗母条只在相啮合的部分供给压 力油。 (+ ) 轴向间隙 蜗杆和蜗母条之间的单面轴向间
[ "] 率小、 传动效率高 。液体静压蜗杆蜗母条传动副能
够满足这些要求, 近年来在数控机床上得到了广泛的 应用。
!
液体静压蜗杆蜗母条的工作原理
液体静压蜗杆蜗母条的工作原理与静压丝杠螺母
液体静压蜗杆蜗母条传动副, 利用专用的供油装 置 ( 其原理见图 ) ) , 将具有一定压力的润滑油输送到 蜗杆与蜗母条的齿面之间, 保证在预定载荷范围内以 及任何相对运动速度下, 齿面间始终被一层油膜隔开, 实现纯液体润滑。它具有以下优点: (" ) 摩擦阻力小, 功率消耗少, 传动效率高, 在很 低的速度下运动也很平稳。 ()) 使用寿命长。齿面不直接接触, 不容易磨损, 能长期保持精度。 (* ) 抗振性能好。齿面间的压力油层有良好的吸 振能力。 (+) 有足够的轴向刚度。
万方数据
・# !" ・
!
油膜的形成
液体静压润滑是利用专用的供油装置, 将具有压
($ ) 为了保证静压蜗杆及静压蜗母条加工齿距的 正确, 用同一台专用机床精加工蜗杆和蜗母条。此机 床自身的精度较高, 能够保证加工零件齿距的精度要 求。用同一台机床加工两种相配合的零件, 其误差方 向是一致的, 确保了静压蜗杆副配合齿距几何精度的 一致性。 (" ) 为了保证静压蜗杆与静压蜗母条齿形角的一 致性, 按精加工蜗母条滚刀的齿形角来配磨蜗杆齿形 角, 保证了齿形角的一致性。在保证齿距单齿及全长 累积误差与齿形角误差相一致的情形下, 能准确保证 静压油膜厚度单边 )& ), * )& )’ 11 的均匀性。 (+) 为保证静压蜗杆副油膜厚度的准确性, 按滚 刀齿厚的实际尺寸, 将蜗杆齿厚磨小 )& )2 * )& $) 11。 (, ) 安装静压蜗母条的基础零件精度直接影响静 压蜗母条与蜗杆的配合精度, 因此必须保证基础零件 的加工精度。 (’ ) 装配时需保证两块蜗母条的接头齿距衔接精 度。拼接两蜗母条时采用弥补误差的方法来满足蜗母 条齿距精度的要求。
#
影响静压蜗杆、 蜗母条正确啮合的因素及 其解决措施
保证静压油膜厚度为 )& ), * )& )’ 11 ( 图 $) 是静 静压 蜗 杆 精 度 要 求 如 下: 轴 向 齿 距 ,) 5 )& ))6 11; 齿距全长累积误差不大于 )& )$’ 11; 轴向齿形角 半 角 %( +)7 5 +)8;齿 面 粗 糙 度 为 )& 2 "1,材 料 +29:.;<= 或铝铁青铜 ( 图 +) 。 静压蜗母条 ( 如图 , ) 的尺寸精度要求: 轴向齿距 ,) 5 )& ))6 11; 齿距全长累积误差不大于 )& )" 11; 轴向齿形半角 %(+)7 5 +)8; 齿面粗糙度为 )& 2 "1, 材 料 .> ? " , 静压蜗杆蜗母条工作时油膜厚度为 )& ), * )& )’ 11 ( 单边) 。
液体静压蜗杆传动副的设计及油膜厚度计算
!"#$%& ’( )*+,’#-.-$/ 0’,1 $ +,$2" 3.$,# .&+ 4.5/65.-$’& ’( 7$5 8$51 9:$/;&"##
吴晓明
沈邦兴
( 湖北工学院) 关键词: 蜗杆 蜗母条 油膜
为了提高精度、 减少功率消耗、 消除爬行现象, 很 多重型机床都采用了液体静压导轨。液体静压导轨的 静摩擦系数很小, 在运动方向几乎没有任何阻尼, 因此 对进给传动元件提出了很高要求。现代机床对进给传 动元件要求无间隙、 磨损小、 刚度好、 抗阻尼性能好、 功
[ $] 隙 !) 应满足下式: !) ,+ !" , 式中: — —蜗杆全长 !"—
பைடு நூலகம்
$
设计实例
以 34"$ 系列数控龙门镗铣床工作台传动部件所
采用的静压蜗杆蜗母条为例, 静压蜗杆连同蜗杆箱一 起装在床身上, 静压蜗母条每块长 2)) 11, 安装在工 作台上。
上的螺距累积误差。蜗杆一般用铸造青铜制造, 蜗母 条用钢制造。
・# !" ・ 万方数据
# # 定压供油静压蜗杆蜗母条的有关计算公式, 以对 置推力静压轴承的计算原理为基础。蜗母条的包容面 不是完整的圆周, 因此计算中引入了包容角的影响。 空载时一个齿侧向外流出的流量 !$ 为 !$ #$ $ %&’ " % ・ )* #%&’$ %
" $ (
# # 观测静压蜗杆副油压为: #$ / "8 9 673 ( 平均值) , 变量泵输出给蜗杆副的最大流量 ( 已考 虑 配 油 阀 损 失) 为 ! -3: / ! . / "$ ; . -<,。 现根据 !$ 、 # 和观察到的 #$ 计算出 $$ :
)$ , () ) 、 (*) 得: $$ !$ / )8 =(9 234。将以上数据代入式 / $ / $9) --。 工作台、 蜗母条、 蜗杆装好后, 测得轴向单边间隙 $$ 为 $8 $( ? $8 $(*9 --, 工作台运行平稳无振动。计
0 比 $$( $8 $( ? $8 $(*9 -- ) 大, 说 算出 $( $ $8 $9) -- ) 0
万方数据
[ *]
明静压蜗杆副在加工与装配时有误差, 但误差相差不 大。因此, @A*) 系列数控龙门铣镗床静压蜗杆副的 设计结构合理, 传动平稳, 无振动, 位置精度高。 采用液体静压蜗杆蜗母条传动副, 用作工作台进 给或立柱滑座的进给传动元件, 效果很好, 完全可以满 足数控重型机床和现代机床的要求。 参
! # # # # # !$ / ’ ( ! # 0 ! ( ) # ( 234) "1$ 式中 ’— — —油腔的有效面积利用系数。当油腔设 ’ / ); 当油腔设在蜗杆 在蜗母条上时, 上时, ’/ () 5 )) *) ( ) 为同时位于蜗母 条一个齿侧啮合区域内最多的油腔数) # !+ — — —蜗母条张角, ( ,) — —啮合区内油腔张角, ( ,) !( — #$ — — —空载时油腔压力, 673 — —蜗杆齿形半角, ( ,) "% — — —蜗杆螺旋升角, ( ,) $% — &* — — —油腔内边圆半径, -&( — — —蜗杆外圆半径, -$$ — — —空载时蜗杆蜗母条单面轴向间隙, -— —润滑油动力粘度, 673・’ #— &$ — — —蜗母条齿顶圆半径, -&" — — —油腔外边圆半径, -若蜗杆有 - 个工作齿数, 则 ! . " -!$
压蜗杆副正确啮合的根本条件。其最重要的影响因素 是静压蜗杆及蜗母条的加工齿距 ( 单齿及全长累计) 精度是否精确, 两蜗母条接头齿距误差是否一致, 安装 位置尺寸几何精度是否合理。其次是安装静压蜗杆蜗 母条的基础零件精度是否精确等。静压蜗杆与静压蜗 母条正常啮合的主要因素有两个: 一是齿距误差 (单 齿误差及全长累积误差) ; 二是齿形角是否正确。为 了保证静压蜗杆副的啮合质量, 在生产加工及装配工 艺上采取了许多相应措施。
基本相同。不同的是, 静压丝杠螺母不存在配油问题, 而蜗母条相当于螺母的一部分, 因此存在配油问题。 也就是与蜗母条相啮合的那部分蜗杆需供给压力油, 而不啮合部分不能供油。因此, 在蜗杆的端面处或蜗 杆轴的径向需设专门的配油器, 以使啮合区域内的油 腔能连续供油。 图 " 所示为油腔开在蜗母条上的液体静压蜗杆蜗 母条传动副一个齿的工作简图。启动油泵后, 当传动 副未受轴向载荷时, 蜗杆两侧蜗母条油腔内压力相等, 等于 !% 。两侧向间隙均为 "% , 油腔内的压力油经四周 封油间隙 "% &’(! # 流出。由于油腔四周封油面间隙很 小, 润滑油流出时受到很大阻力, 使油腔内的润滑油保 持一定的压力 !% 。当工作台受轴向载荷 $ 后, 如果蜗 杆没有轴向位移, 蜗母条和工作台一起移动一个微小 距离, 受压的一侧间隙减小为 "" 。由于间隙减小, 润 滑油流出时的阻力就加大, 使油腔压力升高到 !" 。背 压一侧的间隙增加为 ") , 油流出时的阻力减小, 油腔 压力降低到 !) 。因此在齿的两侧形成了压力差, 与载 就能带动蜗母条作直线运 荷 $ 平衡。当蜗杆转动时, 动。根据结构的需要, 也可将蜗母条固定在床身上, 蜗 杆箱与移动部件相连接。由于齿面与轴线的垂线间有 一个交角, 所以在垂直方向还有一个附加力 %。