乙醇-正丙醇精馏塔设计说明书
乙醇正丙醇分离设计
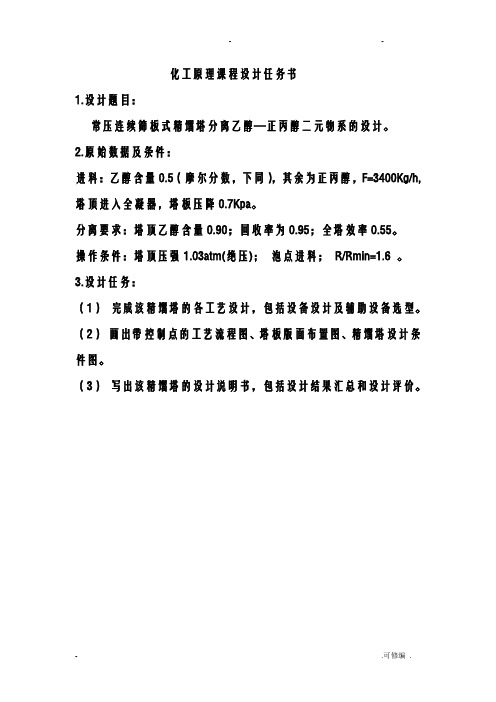
化工原理课程设计任务书1.设计题目:常压连续筛板式精馏塔分离乙醇—正丙醇二元物系的设计。
2.原始数据及条件:进料:乙醇含量0.5(摩尔分数,下同),其余为正丙醇,F=3400Kg/h,塔顶进入全凝器,塔板压降0.7Kpa。
分离要求:塔顶乙醇含量0.90;回收率为0.95;全塔效率0.55。
操作条件:塔顶压强1.03atm(绝压);泡点进料;R/Rmin=1.6 。
3.设计任务:(1)完成该精馏塔的各工艺设计,包括设备设计及辅助设备选型。
(2)画出带控制点的工艺流程图、塔板版面布置图、精馏塔设计条件图。
(3)写出该精馏塔的设计说明书,包括设计结果汇总和设计评价。
摘要在本次任务中,根据化工原理课程设计的要求设计的是乙醇----丙醇连续浮阀精馏塔,除了要计算其工艺流程、物料衡算、热量衡算、筛板塔的设计计算,以外,并对精馏塔的主要工艺流程进行比较详细的设计,并画出了精馏塔的工艺流程图和设备条件图。
本次设计选取回流比R=1.8Rmin=1.6×1.34=2.144应用图解法计算理论版数,求得理论塔板NT为12块(包括塔釜再沸器),第6块为进料板。
设计中采用的精馏装置有精馏塔,冷凝器等设备,采用间接蒸汽加热,物料在塔进行精馏分离,余热由塔顶产品冷凝器中的冷却介质带走,完成传热传质. 塔的附属设备中,所有管线均采用无缝钢管。
预热器采用管壳式换热器。
用99.97℃塔釜液加热。
料液走壳程,釜液走管程。
本设计采用了筛板塔对乙醇-丙醇进行分离提纯,塔板为碳钢材料,通过板压降、漏液、液泛、液沫夹带的流体力学验算,均在安全操作围。
关键字:乙醇-丙醇筛板塔物料衡算目录第一章概述51.1 精馏操作对塔设备的要求51.2 板式塔类型61.2.1 筛板塔61.2.2浮阀塔6第二章塔板的工艺设计 (7)2.1 精馏塔全塔物料衡算72.1.1 原料液及塔顶、塔底产品的摩尔分率与物料衡算72.1.2 原料液及塔顶、塔底产品的摩尔质量82.2 理论塔板数的确定82.2.1 理论板层数NT的求取82.2.2 实际板层数的求取10第三章精馏塔的工艺条件及有关物性数据的计算103.1 操作压力计算103.2 操作温度计算113.3 平均摩尔质量计算113.4 平均密度计算123.5 液体平均表面力的计算133.6 液体平均黏度计算15第四章精馏塔的塔体工艺尺寸的计算164.1 塔径的设计计算164.2 塔的有效高度的计算17第五章塔板主要工艺尺寸的计算175.1 溢流装置计算175.2 塔板布置18第六章筛板的流体力学验算196.1 塔板压强降206.1.1 干板阻力c h计算。
乙醇-正丙醇精馏塔设计说明书
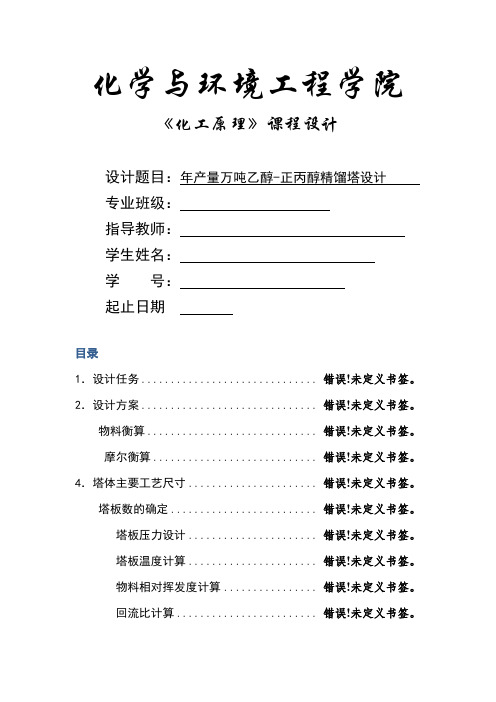
可得实际操作温度及组分饱和蒸汽压。
结果如下:
塔顶:PA= kPa PB= kPa tD=℃ 塔底:PA= Pa PB= kPa tD=℃ 进料板:PA= kPa PB= kPa tD=℃
4.1.3 物料相对挥发度计算
pA ,根据上文求出的数据可得: p
B
塔顶: D 塔底: W =
进料板: F =
4.1.6 实际塔板数的计算
4.1.6.1 黏度(通过液体黏度共线图差得)
乙醇、正丙醇黏度共线图坐标值
物质
X
Y
乙醇
正丙醇
全塔平均温度为:tm= ℃
物料在平均温度下的粘度,通过查表可得:
乙醇: A 0.381 mPa/s
正丙醇: B 0.578mPa / s
全塔平均黏度计算公式:lg x lg 1 x lg
F
A
F
B
代入数据可得平均粘度 0.47mPa / s
4.1.6.2 总塔板效率
普特拉—博伊德公式: E 0.490.245
代入相关数据得: E 0.493
4.1.7 实际塔板数计算
精馏段板数 N 精 11 E 23 提馏段板数 N 提 12 E 25
总板数 N=48 (包括塔釜再沸器)
塔板数的确定 4.1.1 塔板压力设计
常压操作,即塔顶气相绝对压力 p=110.925 kPa 预设塔板压力降: 0.6 kPa 估计理论塔板数:18 估计进料板位置:12 塔底压力:Pw=+×18 = kPa 进料板压力: P进 +×12 = kPa 精馏段平均压力: Pm
4.1.2 塔板温度计算
xD yq
yq xq
0.9846 0.68925 0.68925 0.5163
乙醇精馏塔设计说明书
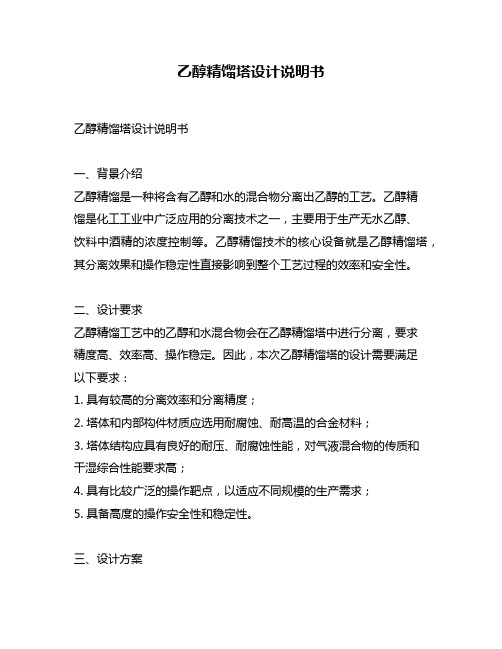
乙醇精馏塔设计说明书乙醇精馏塔设计说明书一、背景介绍乙醇精馏是一种将含有乙醇和水的混合物分离出乙醇的工艺。
乙醇精馏是化工工业中广泛应用的分离技术之一,主要用于生产无水乙醇、饮料中酒精的浓度控制等。
乙醇精馏技术的核心设备就是乙醇精馏塔,其分离效果和操作稳定性直接影响到整个工艺过程的效率和安全性。
二、设计要求乙醇精馏工艺中的乙醇和水混合物会在乙醇精馏塔中进行分离,要求精度高、效率高、操作稳定。
因此,本次乙醇精馏塔的设计需要满足以下要求:1. 具有较高的分离效率和分离精度;2. 塔体和内部构件材质应选用耐腐蚀、耐高温的合金材料;3. 塔体结构应具有良好的耐压、耐腐蚀性能,对气液混合物的传质和干湿综合性能要求高;4. 具有比较广泛的操作靶点,以适应不同规模的生产需求;5. 具备高度的操作安全性和稳定性。
三、设计方案为满足以上设计要求,本文提出一种高效、稳定的乙醇精馏塔设计方案,具体如下:1. 采用反流式精馏工艺,即底部引入加热蒸气,使气液混合物在塔内进行分馏,分离后的乙醇从顶部出流管流出,水则从底部洛氏冷凝器中排出。
2. 塔体结构采用不锈钢材料,采用内塞式塔板进行分离。
内塞式塔板具有压降小、分离效率高、适应性强等优点,能够保证塔内物料充分分离。
3. 为提高分离效率和干湿综合性能,本方案在塔体上设置进液口和出液口、进气口和出气口等。
进液口通过操作调节,能够使物料的进入量和化学组成进行调节。
出液口则负责排出经过分馏后的乙醇。
进气口可以保证塔内气相的通畅,而出气口则能够将废气和杂质的气体排出。
4. 本方案采用内加热式蒸汽进行底部加热,可通过蒸汽的进入量来调整加热的温度和量,对塔内气相的传质起到重要作用。
相比外加热的方式,内加热可以供热均匀,减少冷凝器堵塞和热分解等问题的发生。
5. 本方案采用湿式冷凝器进行水的收集和回收,具有结构简单、运行可靠、操作维护方便等优点。
四、结论乙醇精馏工艺要求精度高、效率高、操作稳定,而乙醇精馏塔是其核心设备。
乙醇精馏塔设计手册

乙醇精馏塔设计手册乙醇精馏塔设计手册1. 引言乙醇精馏塔是工业生产中常见的设备,用于乙醇的提纯和分离。
本文将探讨乙醇精馏塔的设计原理和操作指南,并提供一些有关乙醇精馏的实用建议。
2. 基本原理乙醇精馏是利用乙醇和水之间的沸点差异进行分离的过程。
在乙醇精馏塔中,乙醇和水混合物首先进入塔顶,经过加热,液体汽化为气体,然后向下运行到塔底。
在这个过程中,乙醇和水以及其他杂质逐渐分离,纯度更高的乙醇会向塔顶方向移动,而水和杂质则会向塔底方向移动。
3. 设计要点乙醇精馏塔的设计需要考虑以下几个要点:3.1 塔板设计塔板是乙醇精馏塔中实现液体和气体传质的关键结构。
塔板的数量和间距将直接影响乙醇的分馏效果。
一般情况下,塔板数目越多,分离效果越好。
然而,添加过多的塔板会增加系统的压降,从而影响塔的性能。
在设计中需要进行合理的平衡。
3.2 温度控制乙醇精馏塔中的温度控制对于分馏效果非常关键。
过高的温度会导致醇汽过量,降低乙醇纯度;过低的温度则会造成不完全汽化,减少塔的分离效果。
需要通过控制塔底和塔顶的温度来达到最佳的分馏效果。
3.3 精馏剂的选择精馏剂在乙醇精馏中发挥重要的作用,它不仅可以提高系统的分馏效率,还可以降低系统的能耗。
常用的精馏剂包括乙醇、水和乙二醇等。
选择适当的精馏剂需要考虑乙醇和精馏剂之间的相容性以及经济性。
4. 操作指南在操作乙醇精馏塔时,需要注意以下几个方面:4.1 塔顶和塔底压力控制塔顶和塔底的压力控制是确保乙醇精馏正常运行的关键。
过高的塔顶压力会导致乙醇冷凝回流,降低乙醇的纯度;而过低的塔顶压力则会影响分馏效果。
塔底压力的控制对于去除水和杂质也是至关重要的。
4.2 进料流量控制进料流量的控制也会直接影响乙醇精馏的效果。
过大的进料流量可能导致过度充填塔板,而过小的进料流量可能会导致塔板间的不连续汽液流动。
需要根据实际情况选择合适的进料流量。
4.3 塔板温度和液位监控塔板温度和液位的监控对于乙醇精馏的稳定运行非常重要。
乙醇-正丙醇溶液连续板式精馏塔的设计-化工原理课程设计书最终版
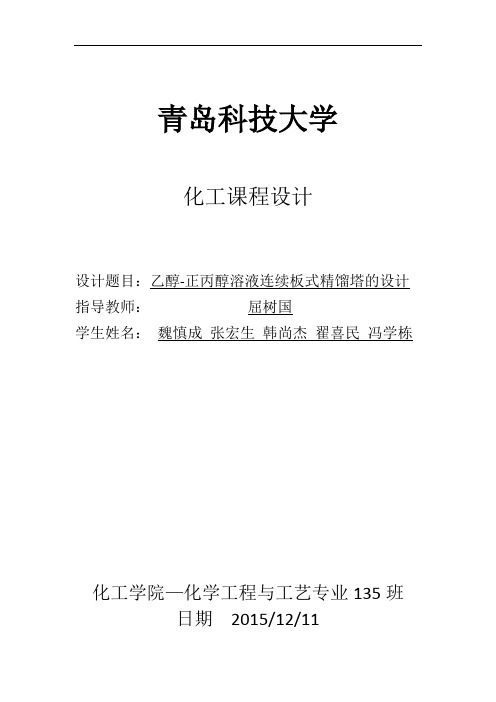
青岛科技大学化工课程设计设计题目:乙醇-正丙醇溶液连续板式精馏塔的设计指导教师:屈树国学生姓名:魏慎成张宏生韩尚杰翟喜民冯学栋化工学院—化学工程与工艺专业135班日期2015/12/11目录一设计任务书二塔板的工艺设计(一)设计方案的确定(二)精馏塔设计模拟(三)塔板工艺尺寸计算1)塔径2)溢流装置3)塔板分布、浮阀数目与排列(四)塔板的流体力学计算1)气相通过浮阀塔板的压强降 2)淹塔3)雾沫夹带(五)塔板负荷性能图1)雾沫夹带线2)液泛线3)液相负荷上限4)漏液线5)液相负荷上限(六)塔工艺数据汇总表格三塔的附属设备的设计(一)换热器的选择1)预热器2)再沸器的换热器3)冷凝器的换热器(二)泵的选择四塔的内部工艺结构(一)塔顶(二)进口①塔顶回流进口②中段回流进口(三)人孔(四)塔底①塔底空间②塔底出口五带控制点工艺流程图六主体设备图七附件(一)带控制点工艺流程图(二)主体设备图八符号表九讨论十主要参考资料一设计任务书【设计任务】设计一板式精馏塔,用以完成乙醇-正丙醇溶液的分离任务【设计依据】如表一表一【设计内容】1)塔板的选择;2)流程的选择与叙述;3)精馏塔塔高、塔径与塔构件设计;4)预热器、再沸器热负荷及加热蒸汽消耗量,冷凝器热负荷及冷却水用量,泵的选择;5)带控制点工艺流程图及主体设备图。
二塔板的工艺设计(一)设计方案的确定本设计的任务是分离乙醇—正丙醇混合液,对于二元混合物的分离,应采用连续精馏流程,运用Aspen软件做出乙醇—正丙醇的T-x-y 相图,如图一:图一:乙醇—正丙醇的T-x-y相图由图一可得乙醇—正丙醇的质量分数比为0.5:0.5时,其泡点温度是84.40o C(二)精馏塔设计模拟1.初步模拟过程运用Aspen软件精馏塔Columns模块中DSTWU模型进行初步模拟,并不断进行调试,模拟过程及结果如下:图二:初步模拟模块图三:塔规格初步设计结果由此塔得到的组分如下:图四:塔规格初步设计所得到流股及其组成由上图看出重组分中乙醇的质量分数是 2.0%,其结果是并不符合分离要求,因此运用精馏塔Columns模块中RadFrac模型进行精确模拟设计,并不断进行调试,模拟过程及结果如下:图五:精确模拟模块图六:塔规格精确设计结果图七:塔规格精确设计所得到流股及其组成由图七看出在塔顶乙醇含量和塔底乙醇含量均达到分离要求,因此软件所得计算结果数据如表二:表二对表二数据简单的处理和从软件中可得到如下数据:表三(三)塔板工艺尺寸计算1)塔径空塔气速u=(安全系数)⨯max u ,安全系数=0.6-0.8,max u =(1) 横坐标数值:0.50.50.0029734.067()()0.0481.28 1.644s L s V L V ρρ⨯=⨯= 取板间距:0.40T H m =, 取板上液层高度:0.07L h m = , 则 0.33T L H h m =- 查图可知C 20=0.12 , 0.20.212017.52()0.12()0.1162020C C σ==⨯= (2)max 0.116 2.45u ==/m s取安全系数为0.6,则空塔气速为:max 0.60.6 2.45 1.47u u ==⨯=/m s塔径:1.053D ===m 按标准塔径圆整为: 1.1D m =,则 横截面积:222/40.785 1.10.95T A D m π==⨯=实际空塔气速: '1 1.281.350.95u ==/m s 2)溢流装置选用单溢流弓形降液管,不设进口堰。
最新乙醇-正丙醇连续筛板式精馏塔的设计方案

乙醇-正丙醇连续筛板式精馏塔的设计方案乙醇-正丙醇连续筛板式精馏塔的设计方案流程的设计及说明1 设计思路蒸馏方式的确定蒸馏装置包括精馏塔,原料预热器,精馏釜(再沸器),冷凝器,釜液冷却器和产品冷却等设备,蒸馏过程按操作方式不同可分为连续蒸馏和间歇蒸馏两种流程,连续蒸馏具有生产能力大,产品质量稳定等优点,工业生产中以连续精馏为主,间歇蒸馏具有操作灵活,适应性强等优点,适合小规模,多品种或多组分物系的初步分离。
本次设计采用连续筛板精馏塔,常压精馏。
2 装置流程的确定(1)物料的储存和输送在流程中设置原料罐,产品罐及离心泵。
原料可泵直接送入塔内,使程序连续稳定的进行。
(2)参数的检测和调控流量,压力和温度是生产中的重要参数,必须在流程中的适当位置装设仪表,以测量这些参数。
同时,在生产过程中,物料的状态。
加热剂和冷却剂的状态都不可能避免的会有一些波动,因此必须在流程中设置一定的阀门。
(3)冷凝装置的确定本设计采用塔顶全凝器,以便于准确地对控制回流比。
(4)热能的利用精馏过程是组分多次部分汽化和多次部分冷凝的过程,耗能较多,因此选择适宜的回流比使过程处于最佳条件下进行,可使能耗至最低。
3 操作条件的确定 (1) 操作压力的选取本次设计采用常压操作。
除热敏性物料外,凡通过常压精馏不难实现分离要求,并能利用江河水或循环水将镏出物冷凝下来的系统。
(2)加料状态的选择本设计选择q=1时进料,原因是使塔的操作稳定,精,提镏段利用相同塔径,便于制造。
(3) 加料方式蒸馏大多采用间接蒸汽加热,设置再沸器。
(4)回流比的选择一般经验值为min )0.21.1(R R -=。
本设计采用min 5.1R R =,初步设定后经过流体力学验算,负荷条件,故选择合理。
塔顶冷凝器的冷凝方式与冷却介质的选择塔顶冷凝温度不要求低于30℃,工业上多用水冷 (5)板式塔类型的选择本次设计采用连续筛板式精馏塔 4 设计方案的确定(1)满足工艺和操作要求(2)满足经济上的要求,安全生产,保护环境。
分离乙醇-正丙醇
100
乙醇
0.601
0.495
0.361
正丙醇
0.899
0.619
0.444
根据内差法求不同温度下的粘度
B 查表,得 ,
查表,得 ,
(1)精馏段粘度:
(1)提留段粘度:
2.2.5相对挥发度
(1)精馏段的平均相对挥发度:
(2)提留段的平均相对挥发度:
2.2.6气液相体积流量计算
kmol/s
(1)精馏段
2.6.2浮阀数目与排列
(1)精馏段
取阀孔动能因子F0=12.则孔速
每层塔板上浮阀数目为
取边缘区宽度 破沫区宽度
计算塔板上的鼓泡区面积,即
其中
所以
浮阀排列方式采用等腰三角形叉排,取同一个横排的孔心距t=75mm
则排间距:
按t=75mm , 以等腰三角形叉排方式作图,排得阀数154个
按N=154重新核算孔速及阀孔动能因子
3.1通过浮阀塔板的压降
气体通过塔板时,需克服塔板本身的干板阻力、板上充气液层的阻力及液体表面张力造成的阻力,这些阻力即形成了塔板的压降。气体通过塔板的压降△Pp可由 和 计算
式中hc——与气体通过塔板的干板压降相当的液柱高度,m液柱;
hl——与气体通过板上液层的压降相当的液柱高度,m液柱;
hσ——与克服液体表面张力的压降相当的液柱高度,m液柱。
由Excel计算结果见表2.3:
表2.3逐板法计算理论塔板数结果
x编号
x的值
y编号
y的值
x1
0.983913
y1
0.9923
x2
0.969513
y2
0.985295
x3
0.945348
化工原理课程设计精馏塔
化工原理课程设计任务书1.设计题目:分离乙醇—正丙醇二元物系旳浮阀式精馏塔2.原始数据及条件:进料:乙醇含量45%(质量分数,下同),其他为正丙醇分离规定:塔顶乙醇含量 93%;塔底乙醇含量 0.01%生产能力:年处理乙醇-正丙醇混合液 25000 吨,年动工 7200 小时操作条件:间接蒸汽加热;塔顶压强 1.03atm(绝压);泡点进料; R=53.设计任务:⑴完毕该精馏塔旳各工艺设计,包括设备设计及辅助设备选型。
⑵画出带控制点旳工艺流程图、塔板版面布置图、精馏塔设计条件图。
⑶写出该精馏塔旳设计阐明书,包括设计成果汇总和设计评价。
概述本次设计针对二元物系旳精馏问题进行分析、计算、核算、绘图,是较完整旳精馏设计过程。
精馏设计包括设计方案旳选用,重要设备旳工艺设计计算、辅助设备旳选型、工艺流程图旳制作、重要设备旳工艺条件图等内容。
通过对精馏塔旳核算,以保证精馏过程旳顺利进行并使效率尽量旳提高。
本次设计成果为:理论板数为 20 块,塔效率为 42.2%,精馏段实际板数为 40块,提馏段实际板数为 5 块,实际板数 45 块。
进料位置为第 17 块板,在板式塔重要工艺尺寸旳设计计算中得出塔径为 0.8 米,设置了四个人孔,塔高 22.19 米,通过浮阀板旳流体力学验算,证明各指标数据均符合原则。
关键词:二元精馏、浮阀精馏塔、物料衡算、流体力学验算。
目录第一章绪论 (5)第二章塔板旳工艺设计 (7)一、精馏塔全塔物料衡算 (7)二、乙醇和水旳物性参数计算 (7)1.温度 (7)2.密度 (8)三、理论塔板旳计算 (11)四、塔径旳初步计算 (12)五、溢流装置 (14)六、塔板分布、浮阀数目与排列 (15)第三章塔板旳流体力学计算 (16)一、气相通过浮阀塔板旳压降 (16)二、淹塔 (17)三、物沫夹带 (18)四、塔板负荷性能图 (19)1.物沫夹带线 (19)2.液泛线 (19)3.液相负荷上限 (20)4.漏液线 (20)5.液相负荷下限 (20)第四章塔附件旳设计 (21)一、接管 (21)二、筒体与封头 (23)三、除沫器 (23)四、裙座 (24)五、人孔 (24)第五章塔总体高度旳设计 (24)一、塔旳顶部空间高度 (24)二、塔总体高度 (24)第六章附属设备旳计算 (24)8.1热量衡算 (24)8.1.10℃旳塔顶气体上升旳焓Qv (24)258.1.2回流液旳焓QR..................................................................8.1.3塔顶馏出液旳焓Q D (25)8.1.4冷凝器消耗旳焓Q C (25)8.1.5进料口旳焓Q F (25)8.1.6塔釜残液旳焓Q W (26)8.1.7再沸器Q B (26)8.2冷凝器旳设计 (26)8.3冷凝器旳核算 (27)8.4泵旳选择 (27)浮阀塔工艺设计计算成果列表 (28)重要符号阐明 (29)参照文献 (31)第一章绪论精馏旳基本原理是根据各液体在混合液中旳挥发度不一样,采用多次部分汽化和多次部分冷凝旳原理来实现持续旳高纯度分离。
乙醇_正丙醇精馏塔设计说明书
化学与环境工程学院《化工原理》课程设计设计题目:年产量1.5万吨乙醇-正丙醇精馏塔设计专业班级:指导教师:学生姓名:学号:起止日期 2011.06.13-2011.06.24目录1.设计任务 (2)2.设计方案 (3)3.1 物料衡算 (6)3.2 摩尔衡算 (7)4.塔体主要工艺尺寸 (7)4.1 塔板数的确定 (7)4.1.1 塔板压力设计 (7)4.1.2 塔板温度计算 (8)4.1.3 物料相对挥发度计算 (9)4.1.4 回流比计算 (9)4.1.5 塔板物料衡算 (10)4.1.6 实际塔板数的计算 (11)4.1.7 实际塔板数计算 (12)4.2 塔径计算 (12)4.2.1 平均摩尔质量计算 (12)4.2.2 平均密度计算 (13)4.2.3 液相表面张力计算 (14)4.2.4 塔径计算 (14)4.3 塔截面积 (15)4.4 精馏塔有效高度计算 (15)4.5 精馏塔热量衡算 (16)4.5.1 塔顶冷凝器的热量衡算 (16)4.5.2 全塔的热量衡算 (18)5.板主要工艺尺寸计算 (21)5.1 溢流装置计算 (21)5.1.1 堰长l (21)w5.1.2 溢流堰高度h (21)W5.1.3 弓形降液管宽度W d和截面积A f (22)5.1.4 降液管底隙高度h0 (22)5.2 塔板布置 (22)5.2.1 塔板的选用 (22)5.2.2 边缘宽度和破沫区宽度的确定 (23)5.2.3 鼓泡区面积的计算 (23)5.2.4 浮阀的数目与排列 (23)5.3 阀孔的流体力学验算 (25)5.3.1 塔板压降 (25)5.3.2 液泛 (26)5.3.3 液沫夹带 (27)5.3.4 漏液 (29)6.设计筛板的主要结果汇总表 (30)1.设计任务物料组成:为乙醇45%、正丙醇55%(质量分数);产品组成:塔顶乙醇含量98%,塔顶易挥发组分回收率99%;操作压力:101.325kPa(塔顶绝对压力);加热体系:间接蒸汽加热,加热蒸汽压力为5kgf/cm2(绝压);冷凝体系:冷却水进口温度25℃,出口温度45℃;热量损失:设备热损失为加热蒸汽供热量的5%;料液定性:料液可视为理想物系;年产量(乙醇):1.5万吨;每年实际生产时间:7200h;进料方式:饱和液体进料,q值为1;塔板类型: 浮阀塔板。
乙醇-正丙醇连续筛板式精馏塔的设计方案
乙醇-正丙醇连续筛板式精馏塔的设计方案乙醇-正丙醇连续筛板式精馏塔的设计方案流程的设计及说明1 设计思路蒸馏方式的确定蒸馏装置包括精馏塔,原料预热器,精馏釜(再沸器),冷凝器,釜液冷却器和产品冷却等设备,蒸馏过程按操作方式不同可分为连续蒸馏和间歇蒸馏两种流程,连续蒸馏具有生产能力大,产品质量稳定等优点,工业生产中以连续精馏为主,间歇蒸馏具有操作灵活,适应性强等优点,适合小规模,多品种或多组分物系的初步分离。
本次设计采用连续筛板精馏塔,常压精馏。
2 装置流程的确定 (1)物料的储存和输送在流程中设置原料罐,产品罐及离心泵。
原料可泵直接送入塔内,使程序连续稳定的进行。
(2)参数的检测和调控流量,压力和温度是生产中的重要参数,必须在流程中的适当位置装设仪表,以测量这些参数。
同时,在生产过程中,物料的状态。
加热剂和冷却剂的状态都不可能避免的会有一些波动,因此必须在流程中设置一定的阀门。
(3)冷凝装置的确定本设计采用塔顶全凝器,以便于准确地对控制回流比。
(4)热能的利用精馏过程是组分多次部分汽化和多次部分冷凝的过程,耗能较多,因此选择适宜的回流比使过程处于最佳条件下进行,可使能耗至最低。
3 操作条件的确定 (1) 操作压力的选取本次设计采用常压操作。
除热敏性物料外,凡通过常压精馏不难实现分离要求,并能利用江河水或循环水将镏出物冷凝下来的系统。
(2)加料状态的选择本设计选择q=1时进料,原因是使塔的操作稳定,精,提镏段利用相同塔径,便于制造。
(3) 加料方式蒸馏大多采用间接蒸汽加热,设置再沸器。
(4)回流比的选择一般经验值为min )0.21.1(R R -=。
本设计采用min 5.1R R =,初步设定后经过流体力学验算,负荷条件,故选择合理。
塔顶冷凝器的冷凝方式与冷却介质的选择塔顶冷凝温度不要求低于30℃,工业上多用水冷 (5)板式塔类型的选择本次设计采用连续筛板式精馏塔 4 设计方案的确定(1)满足工艺和操作要求(2)满足经济上的要求,安全生产,保护环境。
- 1、下载文档前请自行甄别文档内容的完整性,平台不提供额外的编辑、内容补充、找答案等附加服务。
- 2、"仅部分预览"的文档,不可在线预览部分如存在完整性等问题,可反馈申请退款(可完整预览的文档不适用该条件!)。
- 3、如文档侵犯您的权益,请联系客服反馈,我们会尽快为您处理(人工客服工作时间:9:00-18:30)。
.
4.2.3 液相表面张力计算 ............................................................14 4.2.4 塔径计算 ............................................................................14 4.3 塔截面积 .....................................................................................15 4.4 精馏塔有效高度计算 ................................................................15 4.5 精馏塔热量衡算 ........................................................................16 4.5.1 塔顶冷凝器的热量衡算 ....................................................16 4.5.2 全塔的热量衡算 ................................................................18 5.板主要工艺尺寸计算 ........................................................................21 5.1 溢流装置计算 ............................................................................21 5.1.1 堰长 lw .................................................................................21 5.1.2 溢流堰高度 hW ....................................................................21 5.1.3 弓形降液管宽度 Wd 和截面积 Af.....................................22 5.1.4 降液管底隙高度 h0 ............................................................22 5.2 塔板布置 ....................................................................................22 5.2.1 塔板的选用 ........................................................................22 5.2.2 边缘宽度和破沫区宽度的确定 ........................................23 5.2.3 鼓泡区面积的计算 ............................................................23 5.2.4 浮阀的数目与排列 ...............................23 5.3 阀孔的流体力学验算 ...........................................................25 5.3.1 塔板压降 ............................................................................25 5.3.2 液泛 ....................................................................................26 5.3.3 液沫夹带 ............................................................................27 5.3.4 漏液 ....................................................................................29 6.设计筛板的主要结果汇总表 ............................................................30
化学与环境工程学院
《化工原理》课程设计
设计题目:年产量 1.5 万吨乙醇-正丙醇精馏塔设计 专业班级: 指导教师: 学生姓名: 学 号: 起止日期 2011.06.13-2011.06.24
目录 1.设计任务............................................................................................... 2 2.设计方案............................................................................................... 3
4.1.1 塔板压力设计 ......................................................................7 4.1.2 塔板温度计算 ......................................................................8 4.1.3 物料相对挥发度计算 ..........................................................9 4.1.4 回流比计算 ..........................................................................9 4.1.5 塔板物料衡算 ....................................................................10 4.1.6 实际塔板数的计算 ............................................................11 4.1.7 实际塔板数计算 ................................................................12 4.2 塔径计算 ....................................................................................12 4.2.1 平均摩尔质量计算 ............................................................12 4.2.2 平均密度计算 ....................................................................13