拨叉课程设计---拨叉设计及夹具设计
拨叉夹具设计

一、零件的分析(一)零件的作用题目所给的零件是CA6140车床的拨叉。
它位于车床变速机构中,主要起换档,使主轴回转运动按照工作者的要求工作,获得所需的速度和扭矩的作用。
零件上方的φ22孔与操纵机构相连,二下方的φ55半孔则是用于与所控制齿轮所在的轴接触。
通过上方的力拨动下方的齿轮变速。
两件零件铸为一体,加工时分开。
(二)零件的工艺分析零件的材料为HT200,灰铸铁生产工艺简单,铸造性能优良,但塑性较差、脆性高,不适合磨削,为此以下是拨叉需要加工的表面以及加工表面之间的位置要求:1小头孔以及与此孔相通的的锥孔、螺纹孔2大头半圆孔Ф553小头孔端面、大头半圆孔上下Ф73端面,大头半圆孔两端面与小头孔中心线的垂直度误差为0.07mm,小头孔上端面与其中心线的垂直度误差为0.05mm。
由上面分析可知,可以粗加小头孔端面,然后以此作为粗基准采用专用夹具进行加工,并且保证位置精度要求。
再根据各加工方法的经济精度及机床所能达到的位置精度,并且此拨叉零件没有复杂的加工曲面,所以根据上述技术要求采用常规的加工工艺均可保证。
二工艺规程设计一确定生产类型已知此拨叉零件的生产类型为大批量生产,所以初步确定工艺安排为:加工过程划分阶段;工序适当集中;加工设备以通用设备为主,大量采用专用工装。
二,确定毛坯的制造形式确定毛坯种类:零件材料为HT200。
考虑零件在机床运行过程中所受冲击不大,零件结构又比较简单,生产类型为中批生产,故选择铸件毛坯。
查《机械制造工艺及设备设计指导手册》324页表15-5(后称《指导手册》)选用铸件尺寸公差等级CT9级。
三,基面的选择定位基准是影响拨叉零件加工精度的关键因素。
基准选择得合理可以使加工质量得到保证,生产率得以提高。
否则,加工过程中将问题百出,更有甚者,造成零件的大批报废,使生产无法正常进行。
(一)粗基准的选择在选择粗基准时,考虑的重点是如何保证各加工表面有足够多的余量,及保证不加工表面与加工表面间的尺寸,位置符合零件图样设计要求,粗基准的选择原则:(1)重要表面余量均匀原则必须首先保证工件重要表面具有较小的加工余量,应选择该表面为粗基准表面间的相互位置要求原则必须保工件上加工表面与不加工表面之间的相互位置要求,应以不加工表面作为粗基准,如果在工件上有很多不加工表面,应以其中与不加工表面相互位置要求较高的不加工表面作为粗基准,以求壁厚均匀外形对称等(2)定位可靠性原则作为粗基准的表面,应选用比较可靠,平整光洁的的表面,以便定位准确,夹紧可靠。
拨叉的工艺过程设计及专用铣床夹具设计—机械制造课程设计

拨叉的⼯艺过程设计及专⽤铣床夹具设计—机械制造课程设计优秀设计拨叉的⼯艺过程设计及专⽤铣床夹具设计——机械制造课程设计三级锥销孔装配时做配合⽤⽬录⼀、拨叉的分析 (2)1.拨叉的⽤途 (2)2.拨叉的技术要求 (2)3.拨叉的⼯艺性 (2)4.拨叉的⽣产类型 (2)⼆、确定⽑坯、绘制⽑坯简图............................................................. 错误!未定义书签。
1.选择⽑坯.............................................................................................. 错误!未定义书签。
2.确定⽑坯的尺⼨和机械加⼯余量 (3)3.⽑坯锻件图.......................................................................................... 错误!未定义书签。
三、拟定⼯艺路线................................................................................. 错误!未定义书签。
1.定位基准的选择 (4)2.各表⾯的加⼯⽅案.............................................................................. 错误!未定义书签。
3.确定⼯艺路线...................................................................................... 错误!未定义书签。
四、计算加⼯余量、切削⽤量和时间定额 (5)⼯序05——粗铣拨叉叉⽖内侧⾯ (5)1.确定加⼯余量...................................................................................... 错误!未定义书签。
拨叉夹具的课程设计

拨叉夹具的课程设计一、课程目标知识目标:1. 让学生理解拨叉夹具的基本结构及其在机械加工中的应用;2. 掌握拨叉夹具的安装、调整和使用方法;3. 了解拨叉夹具的维护与保养知识。
技能目标:1. 培养学生能够独立安装和调整拨叉夹具的能力;2. 提高学生运用拨叉夹具进行机械加工操作的熟练度;3. 培养学生分析并解决拨叉夹具使用过程中出现的问题。
情感态度价值观目标:1. 培养学生严谨、细致的工作态度,提高对机械加工操作的安全意识;2. 增强学生的团队合作精神,学会在团队中分享、交流、协作;3. 激发学生对机械加工领域的兴趣,培养其探究精神和创新意识。
课程性质:本课程为实践性较强的技术学科课程,注重理论联系实际,强调学生在操作实践中掌握拨叉夹具的相关知识。
学生特点:学生具备一定的机械基础知识,动手能力强,对新鲜事物充满好奇心,但可能缺乏实际操作经验。
教学要求:结合学生特点,注重启发式教学,引导学生通过实践操作掌握拨叉夹具的使用方法,并在实际应用中培养解决问题的能力。
同时,关注学生的情感态度价值观培养,使其形成良好的职业素养。
通过分解课程目标为具体的学习成果,为后续的教学设计和评估提供依据。
二、教学内容1. 拨叉夹具的基本结构及其功能:介绍拨叉夹具的组成部分,包括拨叉、底座、夹具主体等,分析各部分在机械加工中的作用。
2. 拨叉夹具的安装与调整:详细讲解拨叉夹具的安装步骤,强调注意事项;介绍调整方法,确保加工精度。
3. 拨叉夹具的使用方法:讲解如何正确使用拨叉夹具进行机械加工,包括装夹、定位、加工等环节。
4. 拨叉夹具的维护与保养:介绍拨叉夹具的日常维护方法和保养技巧,提高使用寿命。
5. 拨叉夹具应用案例:分析实际加工中拨叉夹具的应用案例,让学生了解其在生产中的重要性。
教材章节关联:1. 《机械加工基础》第三章:机械加工工艺装备;2. 《机械加工工艺》第五章:机床夹具及其应用;3. 《机床夹具设计》第二章:机床夹具的分类与结构。
课程设计:拨叉机械加工工艺规程及夹具设计

70
H
3.0 孔,降一级,单侧加工
3、画零件毛坯图(图附后)
四、 机械加工工艺过程设计
(一)选择定位基准 (1)、选择粗基准 为了方便装夹,以及依据以不加工表面为基准和毛坯表 面质量较好者为基准的原则,选底端面为粗基准。 (2)、选择精基准 依据基准重合原则,应选用统一的基准有利于保证零件 的精度。多用“一面两孔”的定位方式定位,所以选择小头孔轴线和底面为精基 准。 (二)制订工艺过程 1、根据各表面加工要求和各种加工方法所能达到的经济精度(查表 15-32、 15-33、15-34),选择加工方法: (1)、上端面 T1:粗铣(R6.3)——精铣(R3.2) (2)、上端面 T2:粗铣(R6.3)——精铣(R3.2) (3)、底端面 T3:粗铣(R6.3)——精铣(R3.2) (4)、切断面 T4:粗铣(R6.2) (5)、小端头孔 D1:扩孔(R6.3、IT10)——铰孔(R1.6、IT7)
优良,但塑性较差,脆性高,不适合磨削。 2、该零件主要加工表面及技术要求分析如下: (1)、零件上端面及孔φ50H13 的上下端面与孔φ22H7 的垂直度公差等级为
9-10 级。表面粗糙度为 Ra≤3.2um。加工时应以上端面与孔φ22H7 的内表面为基 准。又由于上端面须加工,根据“基准先行”的规则,故应先加工上端面,再加 工孔φ22H7,最后加工孔φ50H13 的上下端面。
1
表面 基本尺 加工余 加工余 代号 寸(mm) 量等级 量(mm)
说明
T1
40
H
3.5 顶面,降一级,单侧加工
T2
70
H
3.0
顶面,单侧加工
T3
70
H
3.0
底面,单侧加工
D1
拨叉课程毕业设计论文拨叉设计及夹具设计

十字头工艺规程及夹具设计内容详细拨叉的建模与加工仿真《机械制造与自动化》毕业设计题目:CA6140车床拨叉加工工艺夹具设计课题设计内容: 1.零件图一张2.零件毛配图一张3.机械加工工艺工程工艺卡片若干份4.工艺装备(夹具)设计装配图一张5.法兰盘设计说明书一份目录目录 (1)摘要 (2)1.绪论 (3)1.1课题背景及意义 (5)1.2CA6140型普通车床简介 (6)1.3夹具的发展趋势 (7)1.4拨叉的加工工艺 (8)1.5小结…………………………………………………………2.拨叉C的加工工艺规程设计 (8)2.1零件的分析 (9)2.1.1零件的作用………………………………………………2.2确定生产类型 (9)2.3确定毛坯 (9)2.3.1确定毛坯种类2.3.2确定铸件加工余量及形状2.3.3绘制铸件零件图2.4工艺工程设计 (10)2.4.1选择定位基准2.4.2制定工艺路线2.4.3选择加工设备和工艺设备2.4.4机械加工余量、工序尺寸及公差的确定2.5确定切削用量及基本尺寸 (10)2.6小结3.铣床专用夹具设计 (10)3.1铣床夹具 (11)3.11铣床夹具的主要类型 (11)3.12铣床夹具设计要点 (11)3.2夹紧装置 (12)3.2.1夹紧装置的组成 (12)3.2.2对夹紧装置的基本要求 (12)3.2.3夹紧力的作用点及其方向3.2.4基本夹具结构3.3夹具的设计3.4.1定位基准的选择3.4.2制定夹具方案3.4.3夹具元件的选择3.4.4定位元件的选择3.5小结4.结论 (13)5.致谢 (13)6.参考文献 (14)一.拨叉的三维建模采用SolidWorks2008完成拨叉的三维建模的过程如下:1.绘制圆柱首先,选择“前视基准面”进入草图绘制界面,以原点为圆心绘制直径为 的圆,如图1所示。
然后,点击“退出草图”,选择特征栏里的“拉伸mm40凸体/基体”,输入拉伸长度为85mm,如图2所示。
毕业设计说明书拨叉加工工艺及夹具设计
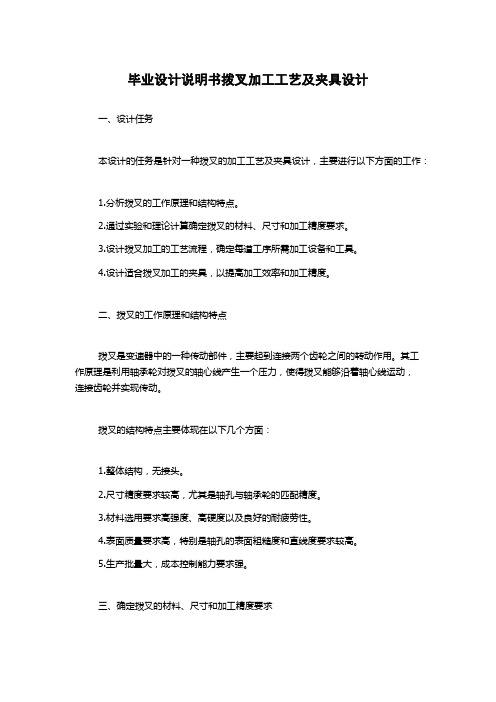
毕业设计说明书拨叉加工工艺及夹具设计一、设计任务本设计的任务是针对一种拨叉的加工工艺及夹具设计,主要进行以下方面的工作:1.分析拨叉的工作原理和结构特点。
2.通过实验和理论计算确定拨叉的材料、尺寸和加工精度要求。
3.设计拨叉加工的工艺流程,确定每道工序所需加工设备和工具。
4.设计适合拨叉加工的夹具,以提高加工效率和加工精度。
二、拨叉的工作原理和结构特点拨叉是变速器中的一种传动部件,主要起到连接两个齿轮之间的转动作用。
其工作原理是利用轴承轮对拨叉的轴心线产生一个压力,使得拨叉能够沿着轴心线运动,连接齿轮并实现传动。
拨叉的结构特点主要体现在以下几个方面:1.整体结构,无接头。
2.尺寸精度要求较高,尤其是轴孔与轴承轮的匹配精度。
3.材料选用要求高强度、高硬度以及良好的耐疲劳性。
4.表面质量要求高,特别是轴孔的表面粗糙度和直线度要求较高。
5.生产批量大,成本控制能力要求强。
三、确定拨叉的材料、尺寸和加工精度要求1.材料选用根据拨叉的工作原理和结构特点,应选用高强度、高硬度以及耐疲劳性良好的材料。
常用的材料有 20CrMnTi、42CrMo、45# 钢等,其中,20CrMnTi 是同时满足强度、硬度和韧性要求的理想材料。
2.尺寸和加工精度要求拨叉的轴孔和轴承轮是关键部位,其匹配精度应达到 IT6 级别,轴孔表面粗糙度≤ Ra0.4μm,轴孔中心线垂直度≤ 0.05mm,轴孔中心线与轴承轮的轴心线平行度≤0.08mm。
此外,整体尺寸公差应控制在±0.03mm 以内。
四、拨叉加工的工艺流程及设备工具针对拨叉的结构特点和加工精度要求,可设计以下的加工流程:1.铣削面采用立式铣床进行加工,分两次进行铣削。
先将工件安装在夹具上,进行端面精加工,保证铣削面的平行度和面质量。
然后再进行一次常规铣削,使铣削面的粗糙度达到要求。
2.车削轴孔采用车床进行加工。
在结合具有稳定性的夹具上进行定位,以保证轴孔的精度和平行度。
拨叉零件机械加工工艺规程及其夹具设计(课程设计)

课程设计(论文)任务及评语目录第一章零件工艺性分析 0第二章生产纲领计算及生产类型的确定 0第三章毛坯种类及制造方法 0第四章拟定工艺路线 (1)4.1定位基准确定 (1)4.2各表面加工方案确定 (1)4.3工序安排 (1)第五章计算各工序的加工余量、工序尺寸及公差 (3)5.1粗铣,半精铣,精铣右端面工序尺寸及公差确定 (3)5.2粗铣,半精铣,精铣左端面工序尺寸及公差确定 (3)5.3Φ20孔工序尺寸及公差确定 (4)5.4拨叉脚内表面工序尺寸及公差确定 (4)5.5Φ5销孔工序尺寸及公差确定 (5)第六章各工序机床、刀具、量具、夹具的选择 (6)第七章工序切削用量和时间定额计算 (7)7.1粗铣,半精铣,精铣右端面 (7)7.2粗铣,半精铣,精铣右端面 (9)7.3粗扩,精扩,铰Φ20孔 (9)7.4粗铣、半精铣拨叉脚内表面 (11)7.5钻,粗铰,精铰Φ5孔 (12)第八章工艺规程的编制 (15)第九章专用夹具设计 (15)9.1方案分析 (15)9.2定位误差的计算: (15)9.3夹紧力的计算: (15)第十章设计体会 (16)参考文献 (16)附录 (17)第一章零件工艺性分析拨叉零件的作用:用在变速箱换挡机构中,通过叉轴孔Φ20安装在变速叉轴上,销钉经拨叉上Φ5孔与叉轴固定,齿轮在拨叉脚内,操纵拨叉头部带动拨叉使拨叉脚内表面拨动齿轮换挡≥745MPa ,硬度HB 231-304。
本题目零件材料为球墨铸铁Q745-5,其力学性能:σb毛坯形式为铸件,轻型零件,生产纲领为大量批生产。
分析零件图,此零件需加工表面为拨叉两端面,Φ20通孔,Φ5销孔以及拨叉脚内表面。
拨叉两端面和拨叉内表面加工精度可由铣削加工保证,Φ20孔和Φ5销孔加工精度可由钻,扩,铰一次加工就可以达到要求,所有加工表面都可在正常生产条件下,采用较经济的方法保质保量地加工出来。
由此可见,该零件的工艺性很好。
第二章生产纲领计算及生产类型的确定生产纲领:N=Qn(1+a%)(1+b%)=10000×(1+0.001)(1+0.001)=10020.01 件/年生产类型:查《机械制造基础课程设计指导教程》∵质量0.15kg<4kg∴由表1-4知该零件属于轻型零件(P5)∵10020大于5000∴由表1-5知该零件属于大批生产第三章毛坯种类及制造方法毛坯材料为球墨铸铁Q745-5,根据零件生产类型,制造精度,原材料,加工余量等综合选择砂型铸造,因为是大批生产,采用砂型机器铸造。
拨叉的加工工艺及夹具设计
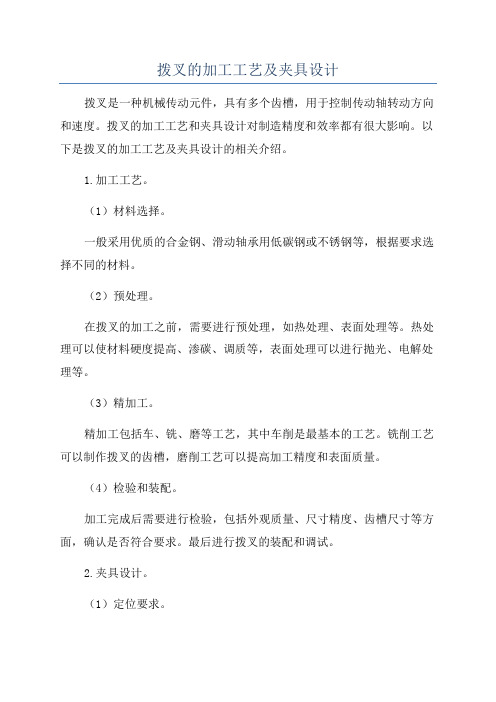
拨叉的加工工艺及夹具设计
拨叉是一种机械传动元件,具有多个齿槽,用于控制传动轴转动方向和速度。
拨叉的加工工艺和夹具设计对制造精度和效率都有很大影响。
以下是拨叉的加工工艺及夹具设计的相关介绍。
1.加工工艺。
(1)材料选择。
一般采用优质的合金钢、滑动轴承用低碳钢或不锈钢等,根据要求选择不同的材料。
(2)预处理。
在拨叉的加工之前,需要进行预处理,如热处理、表面处理等。
热处理可以使材料硬度提高、渗碳、调质等,表面处理可以进行抛光、电解处理等。
(3)精加工。
精加工包括车、铣、磨等工艺,其中车削是最基本的工艺。
铣削工艺可以制作拨叉的齿槽,磨削工艺可以提高加工精度和表面质量。
(4)检验和装配。
加工完成后需要进行检验,包括外观质量、尺寸精度、齿槽尺寸等方面,确认是否符合要求。
最后进行拨叉的装配和调试。
2.夹具设计。
(1)定位要求。
夹具设计的第一个要求是准确定位,保证加工精度。
可以采用中央定位孔、三点定位、夹具块定位等方法。
(2)夹紧方式。
夹具要采用可靠的夹紧方式,避免工件滑动或变形,常用的夹紧方式有机械夹紧、气动夹紧等。
(3)切削力。
在夹具设计中要考虑切削力大小和方向,以保证加工过程中的稳定性和安全性。
(4)材料选择和加工精度。
夹具的材料选择应符合要求,一般采用高强度钢材或铸铁等,夹具的加工精度也需要达到高精度。
总之,拨叉的加工工艺和夹具设计都需要进行精细的规划和调整,以达到高质量、高效率的加工要求。
- 1、下载文档前请自行甄别文档内容的完整性,平台不提供额外的编辑、内容补充、找答案等附加服务。
- 2、"仅部分预览"的文档,不可在线预览部分如存在完整性等问题,可反馈申请退款(可完整预览的文档不适用该条件!)。
- 3、如文档侵犯您的权益,请联系客服反馈,我们会尽快为您处理(人工客服工作时间:9:00-18:30)。
十字头工艺规程及夹具设计内容详细拨叉的建模与加工仿真《机械制造与自动化》毕业设计题目:CA6140车床拨叉加工工艺夹具设计目录目录 (1)摘要 (2)1.绪论 (3)1.1课题背景及意义 (5)1.2CA6140型普通车床简介 (6)1.3夹具的发展趋势 (7)1.4拨叉的加工工艺 (8)1.5小结…………………………………………………………2.拨叉C的加工工艺规程设计 (8)2.1零件的分析 (9)2.1.1零件的作用………………………………………………2.2确定生产类型 (9)2.3确定毛坯 (9)2.3.1确定毛坯种类2.3.2确定铸件加工余量及形状2.3.3绘制铸件零件图2.4工艺工程设计 (10)2.4.1选择定位基准2.4.2制定工艺路线2.4.3选择加工设备和工艺设备2.4.4机械加工余量、工序尺寸及公差的确定2.5确定切削用量及基本尺寸 (10)2.6小结3.铣床专用夹具设计 (10)3.1铣床夹具 (11)3.11铣床夹具的主要类型 (11)3.12铣床夹具设计要点 (11)3.2夹紧装置 (12)3.2.1夹紧装置的组成 (12)3.2.2对夹紧装置的基本要求 (12)3.2.3夹紧力的作用点及其方向3.2.4基本夹具结构3.3夹具的设计3.4.1定位基准的选择3.4.2制定夹具方案3.4.3夹具元件的选择3.4.4定位元件的选择3.5小结4.结论 (13)5.致谢 (13)6.参考文献 (14)一.拨叉的三维建模采用SolidWorks2008完成拨叉的三维建模的过程如下:1.绘制圆柱首先,选择“前视基准面”进入草图绘制界面,以原点为圆心绘制直径为Φ的圆,如图1所示。
然后,点击“退出草图”,选择特征栏里的“拉伸40mm凸体/基体”,输入拉伸长度为85mm,如图2所示。
图1 图22.建立拨叉的外轮廓选择“右视基准面”进入草图绘制界面,绘制如图3所示的草图,并添加相关的尺寸约束和几何约束。
然后,点击“退出草图”,选择特征栏里的“拉伸凸体/基体”,选择“两侧对称”,拉伸长度为40mm如图4所示。
图3 图43.建立拨叉的花键选择拨叉的圆柱端面进入草图绘制界面,绘制如图5所示的直径为mmΦ22的圆。
然后,点击“退出草图”,选择特征栏里的“拉伸切除”,选择“完全贯穿”,如图6所示。
图5 图64.建立花键孔两端倒角选择孔的一端倒角,尺寸如图7所示,孔的另一端也进行倒角,结果如图8所示。
图7 图85.建立花键的槽首先,选择“前视基准面”进入草图绘制界面,绘制如图9所示的草图。
然后,点击“退出草图”。
然后,选择特征栏里的“拉伸切除”,选择“完全贯穿”,如图10所示。
图9 图106.建立拨叉的槽选择拨叉的一侧面进入草图绘制界面,绘制如图11所示的草图。
然后,点击“退出草图”。
然后,选择特征栏里的“拉伸切除”,选择“完全贯穿”,如图12所示。
图11 图127.添加肋板和倒圆角图13二.拨叉的二维图通过采用SolidWorks2008完成拨叉的三维建模,并通过其三维模型生成如下图14所示拨叉的二维图。
图14 拨叉的二维图三.零件的分析1.零件的作用图纸中所给的零件是CA6140车床的拨叉。
它位于车床变速机构中,主要起换档,使主轴回转运动按照工作者的要求工作,工作过程:拨叉零件是在传动系统中拨动滑移齿轮,以实现系统调速,转向。
其花键孔mm 25Φ通过与轴的配合来传递凸轮曲线槽传来的运动,零件的两个叉头部位与滑移齿轮相配合。
2.零件的工艺分析CA6140车床共有两处加工表面,分述如下: 1.以花键孔的中心线为基准的加工面这一组面包括mm 25023.00+Φ的六齿方花键孔、mm 220.200+Φ花键底孔两端的015x 2到角、工件右端面和距离中心线为27mm 的平面。
2.以工件右端面为基准的mm 80.030+的槽和mm 18012.00+Φ的槽经上述分析可知,对于两组加工表面,可先加工其中一组表面,然后借助于专用夹具加工另一组表面。
四.拨叉工艺规程设计1.确定毛坯的制造形成零件材料为HT200。
考虑零件在机床运行过程中所受冲击不大,零件结构又比较简单,故选择铸件毛坯。
2.基准的选择基面选择是工艺规程设计中的重要工作之一。
基面选择得正确与合理可以使加工质量得到保证,生产率得以提高。
(1)粗基准的选择对于零件而言,尽可能选择不加工表面为粗基准。
而对有若干个不加工表面的工件,则应以与加工表面要求相对位置精度较高的不加工表面作粗基准。
根据这个基准选择原则,现选取mmΦ孔的不加工外轮廓底面作为粗基准,利用圆22柱来定位,另外四爪握住两边来限制六个自由度,达到完全定位,然后进行铣削。
(2)精基准的选择主要应该考虑基准重合的问题。
当设计基准与工序基准不重合时,应该进行尺寸换算。
3.制定工艺路线制定工艺路线,在生产纲领确定的情况下, 根据零件的几何形状、尺寸精度及位置精度等技术要求来制定工艺路线。
可以考虑采用万能性机床配以专用工卡具,并尽量使工序集中来提高生产率。
除此之外,还应当考虑经济效果,以便使生产成本尽量下降。
(1)工艺路线方案工序一铸坯。
工序二粗铣圆柱底面。
工序三钻圆柱成20Φ的孔。
工序四扩铰孔20Φ。
Φ到22工序五粗车圆柱孔口斜度为15度。
工序六粗铣右槽1侧平面和宽度为8mm,粗铣宽度为18mm的左槽2。
工序七精铣槽1的上下面和和里面、侧面,精洗槽2的上下面和里面。
工序八拉销孔22Φ成花键。
工序九去毛刺。
工序十检验。
(2)选择机床工序二、工序六、工序七都为铣表面,可用XA5032铣床。
工序三为钻孔,工序四为扩孔工艺,可采用摇臂钻床Z305B。
工序八为拉花键,采用普通拉床。
工序五用车床。
(3)选择夹具:每个工序都可以采用专用的夹具。
(4)选择刀具:在铣床上用高速钢立铣刀,铣上下两槽用三面刃铣刀,在车床上选普通车刀,内拉床选矩形齿花键拉刀。
(5)选择量:精度要求较高的可用内径千分尺量程50~125mm,其余都用游标卡尺分度值为0.02mm。
4.机械加工余量、工序尺寸及毛坯的确定“CA6140车床拨叉”,零件材料为HT200,硬度190~210HB,生产类型大批量,铸造毛坯。
据以上原始资料及加工路线,分别确定各加工表面的机械加工余量、工序尺寸及毛坯尺寸如下:1. 查《机械制造工艺设计简明手册》(以下称《工艺手册》)铣削加工余量为:粗铣2-4mm半精铣1-2mm精铣0-1mm2. 圆柱(40Φ用铸成)内孔22Φ用钻和扩成,加工余量:扩孔 1.2mm3.粗车加工余量:粗车 1.2mm半精车0.8mm4.右凹槽:对于右凹槽的加工,由于事先未被铸出,要满足其槽的深度先需要粗铣,现确定其加工余量取8mm。
为了保证槽两边的表面粗糙度和槽的水平尺寸03.08+的精度要求,需要进行精铣槽的两侧面,加工余量取0.5mm。
5.左凹槽:由于此平面没有加工,只加工平面的凹槽,其基本尺寸为槽宽.001218+mm (精度较高,IT6级),槽的深度为23mm,可事先铸出该凹槽,该槽的0Ra,在粗铣后→精铣就能达到粗糙度要求。
三个表面的粗糙度都为2.36.孔:钻孔其尺寸为20mm,加工余量取2mm,扩孔钻,保留0.5mm的拉刀加工余量。
孔里的花键槽用组合装配式拉刀成型式的加工方式一次拉出。
7.其他尺寸直接铸造得到由于本设计规定的零件为大批量生产,应该采用调整加工。
因此在计算最大、最小加工余量时应按调整法加工方式予以确认。
五.数控加工仿真采用数控铣削加工槽1的上下面和和里面、侧面。
步骤如下所示:1.启动UG NX 5.0后,打开拨叉的模型文件“bocha.x-t”。
选择“开始—加工”命令,打开“加工环境”对话框。
在“CAM设置”框中选择“mill-planar”选项,然后单击“初始化”按钮,进入加工环境。
2.单击“创建几何体”工具按钮,打开“创建几何体”对话框。
设置各个选项,然后单击“应用”按钮,打开“工件”对话框,设置部件和毛坯。
如图15所示。
图15 “创建几何体”对话框和“工件”对话框3.在“加工创建”工具条中单击“创建刀具”工具按钮,打开“创建刀具”对话框。
在对话框中设置各个选项,然后单击“应用”,在新的对话框中设置刀具的各个参数。
4.单击“创建操作”按钮,打开“创建操作”对话框。
设置各个选项后,单击“应用”,打开“Face Milling Area”对话框,设置相应的各个选项。
如图16所示。
图16“创建操作”对话框和“Face Milling Area”对话框5.在“Face Milling Area”对话框中单击“切削区域”按钮,然后在模型部件中指定要进行铣削的区域。
如图17所示。
图17“切削区域”对话框和指定铣削的区域6.在“Face Milling Area”对话框中,设置其它选项,然后在“操作”面板中单击“生成”按钮,在模型部件中显示生成的刀轨。
如图18所示。
图18“Face Milling Area”对话框和生成的刀轨7.在“操作”面板中单击“确认”按钮,打开“刀轨可视化”对话框,进行3D 动画加工模拟演示,如图19所示。
最后,在“刀轨可视化”对话框中单击“确定”,完成操作。
图19“刀轨可视化”对话框和加工模拟的演示效果参考文献[1] 李洪.机械加工工艺手册[M] .北京出版社,1996.1.[2] 陈宏钧.实用金属切削手册[M] .机械工业出版社,2005.1.[3] 上海市金属切削技术协会.金属切削手册[M].上海科学技术出版社,2002.[4] 杨叔子.机械加工工艺师手册[M].机械工业出版社,2000.[5] 徐鸿本.机床夹具设计手册[M] .辽宁科学技术出版社,2003.10.[6] 都克勤.机床夹具结构图册[M] .贵州人民出版社,1983.4.[7] 胡建新.机床夹具[M] .中国劳动社会保障出版社,2001.5.[8] 冯道.机械零件切削加工工艺与技术标准实用手册[M] .安徽文化音像出版社,2003.[9] 王先逵.机械制造工艺学[M].机械工业出版社,2000.[10] 马贤智.机械加工余量与公差手册[M].中国标准出版社,1994.12.[11] 刘文剑.夹具工程师手册[M].黑龙江科学技术出版社,1987.[12] 王光斗.机床夹具设计手册[M].上海科学技术出版社,2002.8.[13] Ball and Roller Screws.Engineering Material and Design.19(12,)1975[14] Patton W.J. Mechanical Power Transmission.New Jersey:Pri。