4多频涡流检查技术的研究
多频涡流无损检测的干扰抑制和缺陷检测方法研究

国防科学技术大学博士学位论文多频涡流无损检测的干扰抑制和缺陷检测方法研究姓名:***申请学位级别:博士专业:仪器科学与技术指导教师:***2011-03摘要多频涡流检测作为一种涡流无损检测新技术,具有实现检测过程干扰抑制和被检对象多参数检测的优点。
本文对多频涡流检测中的信号参数估计及混合运算、同步合成激励峰值因数优化及检测信号谱分析、线性调频激励及检测信号细化谱分析、脉冲激励的多频分析等进行深入研究,并应用于干扰抑制、缺陷检测等方面。
主要研究内容及创新如下:以时谐电磁场理论为基础,探讨了多频涡流检测问题的物理模型和计算方法,并对线圈涡流传感器的感生涡流分布和阻抗特性进行有限元仿真研究。
从麦克斯韦方程组出发,对正弦信号激励下的时谐电磁场问题采用电磁位函数进行数学表述。
对典型圆柱形线圈涡流传感器,简化为轴对称模型,在轴坐标系下,分析涡流效应对线圈等效阻抗的影响。
对任意涡流检测问题,采用有限元法表述其数值计算方法。
介绍了常用的多频涡流检测数据处理方法,如线性代数法、相位旋转相减法、频谱分析法等。
采用Ansoft Maxwell有限元分析软件,建立涡流检测问题模型,仿真研究了激励频率、提离高度、被检对象厚度、缺陷等对涡流场分布和线圈等效阻抗的影响。
研究了基于参数混合运算的多频涡流检测技术,采用正交锁定放大器实现检测信号参数估计,提出基于线性最小二乘法的检测信号参数估计方法,对管道检测中支撑干扰和双频涡流检测中提离效应的抑制方法进行研究。
在多频涡流检测中,当激励信号的频率分量数目较少时,提取各频率分量的两个参数进行混合运算,确定被检对象特性。
讨论了采用带通滤波器和正交锁定放大器的多频涡流检测信号参数估计方法,主要采用硬件实现,成本较高。
对正弦信号进行线性化处理,提出基于线性最小二乘法的多频涡流检测信号参数估计方法,降低硬件实现成本。
对管道检测中的支撑干扰抑制方法进行研究,采用相位旋转相减法,消除了检测过程的支撑干扰,增强了缺陷信号。
多频涡流检查技术的研究分析

4多频涡流检查技术地研究对蒸汽发生器传热管进行涡流检查时,除了传热管地缺陷信号外,还有结构、管材加工、沉积物,以及它们之间不同地组合,会产生大量地畸变信号,从而引起误判或漏检,对正确分析缺陷带来一定困难.为此,必须对涡流检查技术进行研究,包括引进和掌握先进地多频涡流检查装置.4. 1 MIZ-18多频涡流检查装置蒸汽发生器传热管地涡流检查采用了美国Zetec公司生产地M IZ-18多频涡流检查装置,如图2所示.该装置具有下列功能:M IZ-18数据采集系统是用来采集和记录涡流检查数据,它与S M -10定位器和4D探头推拔器联合使用,其检查地全部过程由HP9836计算机控制.S M -10定位器是自动定位装置,远控检测探头定位于管端.安装这种定位器时,检查人员不需要进入高放射性地水室,而是将定位器从人孔插入,固定在人孔地螺栓孔上.4D探头推拔器是远距离操作地双速探头驱动机构,由主机控制,驱动探头进入传热管或从管中拉出地最大速率为12m/ s,最慢速率为0. 03m/ s.检查前将速率设置好,检查期间保持不变.M IZ-18数据分析系统提供分析涡流数据地能力,包括混频、相位分析、信号图形打印和最终报告地形成.M IZ-18数据处理系统提供对己完成地检查数据进行汇总、统计和分类,并对分析结果进行统计.4. 2多频涡流检查技术(1)在涡流检查中确定了4种检测频率.550kHz为主检测频率,是判伤地主要依据,确保标定管上伤深为壁厚10%地外伤有足够地检测灵敏度及信噪比;标定管上地通孔与10%外伤地涡流信号相位差在50度至135度之间,以提高判伤地准确性.100k H z为辅助检测频率,主要用于消除支撑板干扰信号,与主频通道混频,在混频通道上消除支撑板信号,用于支撑板信号处地判伤分析.同时,用于弯管区地信号分析.900kHz为胀管轮廓曲线分析频率,能提高胀管内径地测量精度.20kHz为管板定位及沉积物检测频率,由于管板及沉积物均邻近外壁,采用较低频率.(2)检测探头选择.检查较大弯头U形管时,选择填充系数较大、使用寿命较长地ULC探头,它有可仲缩地脚使探头在管内对中,能使尺寸偏小地探头维持与管子同心.检查小弯头U形竹时则需选择BJF探头,它地头部极软,能穿过小曲率U形管.如果被测管子具有磁性,要选择具有磁饱和特性地探头.一般每台蒸汽发生器有磁导率偏差影响地管子小于10% ,该磁偏效应可畸变或产生类似缺陷地信号,增加分析困难.为此,采用磁饱和探头对那些带磁地管子进行重复检查,以消除磁偏效应.旋转式探头比普通轴向探头可给出缺陷地类别、尺寸及方向等更详细地信息,但检查速度较慢,一般用于对缺陷进行定性定量分析和对管子复杂区域进行补充检查,以发现轴向探头可能漏检地缺陷.( 3)掌握和应用胀管区轮廓曲线地分析技术.利用由美国Zetec公司引进地“远控涡流数据采集分析系统”和“管板轮廓曲线分析程序”,开展对胀管区轮廓曲线分析技术地研究.一般作图通道地频率越高,分析出地轮廓曲线误差越小.这是因为频率越高,涡流地趋肤效应越显著,渗透深度也越小.在测量传热管内径地微小变化时,为了减少管板及管板端面对轮廓曲线分析地影响,选择900kHz地第6绝对通道为作图通道.通过对每根传热竹地涡流信号分析,可以绘出管壁轮廓曲线,来检验管子地欠胀或过胀地状况.4)提高检测缺陷地灵敏度.经研究,对Φ0. 3mm地通孔及Φ0.5mmx 60%壁厚地平底孔能准确判伤;轴向及周向相对定位误差均可《士lmm;采用多频涡流及其混频技术来消除干扰信号,例如管板上泥渣,支撑板、流量分配板、防振条等处地干扰信号,检测出真正地缺陷信号;利用DDA-4分析软件可在屏慕上显示X,Y分量长条图及局部扩展图,显示通道可任意选择,可显示频率、组态、时间、相位角、幅值及伤深、伤位等参数,利用MRPC显示软件可显示出缺陷特征及胀管形状等.版权申明本文部分内容,包括文字、图片、以及设计等在网上搜集整理.版权为个人所有This article includes some parts, including text, pictures, and design. Copyright is personal ownership.Zzz6Z。
涡流检测—涡流检测技术(无损检测课件)

检测线圈的分类
穿过式线圈 检测管材、棒材和线材,用于在线检测
探头式线圈 放在板材、钢锭、棒、管、坯等表面上用,尤其适用于局部检
测,通常线圈中装入磁芯,用来提高检测灵敏度,用于在役检测 内插式线图
管内壁、钻孔。用于材质和加工工艺检查
第3节 涡流检测的基本原理
4. 设备器材
一般的涡流检测仪主要由振荡器、探头、信号输出电 路、放大器、信号处理器、显示器、电源等部分组成
第3节 涡流检测的基本原理
5. 检测技术
缺陷检测即通常所说的涡流探伤。主要影响因素包括工作 频率、电导率、磁导率、边缘效应、提离效应等。
➢ 工作频率是由被检测对象的厚度、所期望的透入深度、要 求达到的灵敏度或分辨率以及其他检测目的所决定的。检 测频率的选择往往是上述因素的一种折衷。在满足检测深 度要求的前提下,检测频率应选的尽可能高,以得到较高 的检测灵敏度。
5. 检测技术
➢ 边缘效应:当检测线圈扫查至接近零件边缘或其上面的孔 洞、台阶时,涡流的流动路径就会发生畸变。这种由于被 检测部位形状突变引起涡流相应变化的现象称为边缘效应。 边缘效应作用范围的大小与被检测材料的导电性、磁导性、
检测线圈的尺寸、结构有关。
5. 检测技术
➢ 提离效应:针对放置式线圈而言,是指随着检测线圈离开 被检测对象表面距离的变化而感应到涡流反作用发生改变 的现象,对于外通式和内穿式线圈而言,表现为棒材外径 和管材内径或外径相对于检测线圈直径的变化而产生的涡 流响应变化的现象。
4. 设备器材
检测仪器的基本组成和原理: 激励单元的信号发生器产生交变电流供给检测线 圈,放大单元将检测线圈拾取的电压信号放大并 传送给处理单元,处理单元抑制或消除干扰信号, 提取有用信号,最终显示单元给出检测结果。
扫频涡流检测原理

扫频涡流检测原理
嘿,朋友们!今天咱就来讲讲扫频涡流检测原理,这可真的超级有意思哦!
你想象一下,就好像我们是超级侦探,要去探寻物体内部的秘密!扫频涡流检测啊,就像是我们拿着一个神奇的工具,去扫描那些隐藏起来的东西。
比如说,有一根金属管子,你从表面可看不出它有没有问题,但扫频涡流检测就能大显身手啦!
咱假设一下啊,就像医生给病人做检查似的。
扫频涡流检测就是那个能看穿金属“身体”的神奇医生。
它通过发射出一些特殊的信号,在金属里面穿梭来穿梭去,就像是在金属世界里玩耍的小精灵。
然后呢,根据信号的反馈情况,咱就能知道这金属里面有没有瑕疵、裂缝啥的啦!
你看啊,在工厂里,那些工人师傅们要保证生产出来的零件都是好好的呀,这时候扫频涡流检测不就派上大用场了吗!它能快速又准确地告诉师傅们,这个零件是不是合格,是不是能放心使用。
哇塞,这多厉害啊!
“哎呀,这扫频涡流检测也太神奇了吧!”你是不是会这么惊叹呢。
它真的就像是一个隐藏在科技世界里的宝藏,等待着我们去发现和利用。
总之呢,扫频涡流检测原理真的超级重要,它让我们能够更好地了解和把控各种金属制品的质量,保障我们的生活和工作更加安全可靠!大家一定要记住这个厉害的小知识哦!。
无损检测技术中的涡流检测方法详解

无损检测技术中的涡流检测方法详解无损检测技术是一种用于检测材料或构件内部缺陷或性能状态的技术方法,它可以在不破坏被检测材料的情况下对其进行评估和监测。
涡流检测作为无损检测技术的一种方法,被广泛应用于工业生产、航空、航天、汽车、电力等领域。
本文将对涡流检测方法进行详细解释和阐述。
涡流检测是一种基于电磁感应原理的无损检测技术。
其原理是利用交流电源产生的交变电磁场在被测材料中产生涡流,通过对涡流的测量,来判断被测材料的缺陷或性能状态。
涡流检测方法可以检测到多种类型的缺陷,如裂纹、腐蚀、疏松等。
涡流检测方法主要包括以下几个方面:1. 电磁感应原理:涡流检测是基于电磁感应原理的,通过交流电源产生的交变电磁场在被测材料中产生涡流。
当被测材料中存在缺陷时,涡流的路径和强度会发生变化,从而可以判断缺陷的位置和性质。
2. 探头设计:涡流检测中使用的探头通常由线圈和磁芯组成。
线圈通过交流电源激励产生交变磁场,磁芯则用于集中和引导磁场。
探头的设计对于检测效果起着重要的作用,不同类型的缺陷需要不同设计的探头。
3. 缺陷识别:通过分析涡流的强度、相位、频率等参数,可以判断被测材料中的缺陷类型和尺寸。
例如,对于裂纹缺陷,涡流的强度和相位会出现明显的变化。
通过对涡流信号进行数学处理和分析,可以得到准确的缺陷识别结果。
4. 检测技术:涡流检测技术可以分为静态检测和动态检测两种。
静态检测是指将被测材料放置在固定位置,通过探头对其进行检测。
动态检测则是指将探头和被测材料相对运动,通过对运动产生的涡流信号进行检测。
动态检测常用于对大型或复杂构件的检测。
涡流检测方法具有以下优点:1. 非接触性:涡流检测不需要直接接触被测物体,因此不会对被测材料造成损伤或影响其性能。
2. 高灵敏度:涡流检测可以检测到微小尺寸的缺陷,对于裂纹等细小缺陷具有很高的灵敏度。
3. 适用范围广:涡流检测方法适用于多种材料,如金属、合金、陶瓷等。
同时,它可以应用于不同形状和尺寸的材料和构件。
涡流检测新型技术
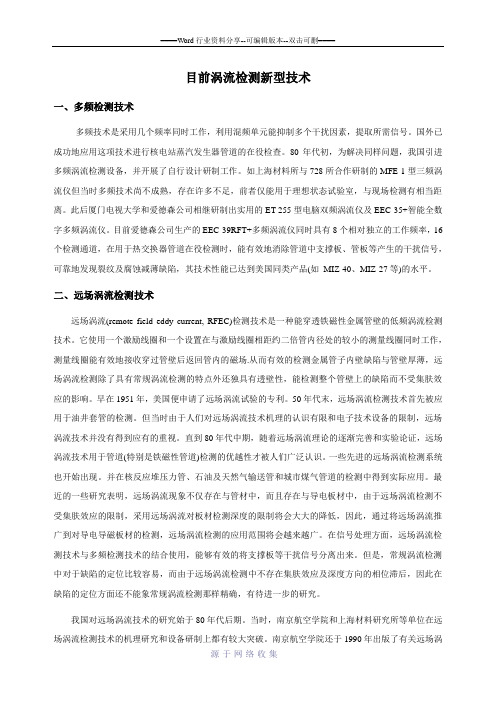
目前涡流检测新型技术一、多频检测技术多频技术是采用几个频率同时工作,利用混频单元能抑制多个干扰因素,提取所需信号。
国外已成功地应用这项技术进行核电站蒸汽发生器管道的在役检查。
80年代初,为解决同样问题,我国引进多频涡流检测设备,并开展了自行设计研制工作。
如上海材料所与728所合作研制的MFE-1型三频涡流仪但当时多频技术尚不成熟,存在许多不足,前者仅能用于理想状态试验室,与现场检测有相当距离。
此后厦门电视大学和爱德森公司相继研制出实用的ET-255型电脑双频涡流仪及EEC-35+智能全数字多频涡流仪。
目前爱德森公司生产的EEC-39RFT+多频涡流仪同时具有8个相对独立的工作频率,16个检测通道,在用于热交换器管道在役检测时,能有效地消除管道中支撑板、管板等产生的干扰信号,可靠地发现裂纹及腐蚀减薄缺陷,其技术性能已达到美国同类产品(如MIZ-40、MIZ-27等)的水平。
二、远场涡流检测技术远场涡流(remote field eddy current, RFEC)检测技术是一种能穿透铁磁性金属管壁的低频涡流检测技术。
它使用一个激励线圈和一个设置在与激励线圈相距约二倍管内径处的较小的测量线圈同时工作,测量线圈能有效地接收穿过管壁后返回管内的磁场.从而有效的检测金属管子内壁缺陷与管壁厚薄,远场涡流检测除了具有常规涡流检测的特点外还独具有透壁性,能检测整个管壁上的缺陷而不受集肤效应的影响。
早在1951年,美国便申请了远场涡流试验的专利。
50年代末,远场涡流检测技术首先被应用于油井套管的检测。
但当时由于人们对远场涡流技术机理的认识有限和电子技术设备的限制,远场涡流技术并没有得到应有的重视。
直到80年代中期,随着远场涡流理论的逐渐完善和实验论证,远场涡流技术用于管道(特别是铁磁性管道)检测的优越性才被人们广泛认识。
一些先进的远场涡流检测系统也开始出现。
并在核反应堆压力管、石油及天然气输送管和城市煤气管道的检测中得到实际应用。
热处理中的涡流及预多频检测技术

热处理中的涡流及预多频检测技术在大型汽车公司的大型热处理淬火车间中,传动系统用的齿轮零件连续进行表面渗碳淬火,产量非常大。
在此之前,需要通过随机抽样,将零件切开、抛光后在金相显微镜下检查淬硬层深度。
在通常条件下,每一个班次要抽取4 次,进行每次11 件的破坏性检测,因此每天总计要破坏零件132 件。
这种方法存在以下问题: 1.在热处理过程不好或失败的情况下,为了保证没有不合格产品出库,需要增加进行破坏性检测的齿轮零件数量; 2.检测结果非实时,至少需要等30min; 3.只有切开的零件才能100%确认是否合格; 4.检测的前提是假设同一批次工件的性能一致; 5.由于进行破坏性检测,因此解决问题的成本高。
由以上问题可知,我们需要一种无损检测程序来提高硬度及淬硬层深度检测的效率,而且这种方法仅需破坏非常少的零件。
用户应用了一种采用“PMFT(预防性多频技术)”的涡流检测系统。
安装了第一套齿轮零件检测系统后,用户又安装了两套系统,其中一套用于齿轮,另一套用于轴类检测。
无损检测方法的经济性计算由文中表可看出,成本计算基于采用德国IBG 公司EDDYLINER P 涡流系统之后节省的金相检测劳动力成本、破坏性检测工件成本以及切割锯条的成本。
其他重要因素(如节省的耗材、延误的检测结果以及增加的对可疑批次进行破坏性检测的成本)没有计算成本,仅作主观考虑。
无损检测系统的技术基础该无损检测系统的技术基础是IBG 公司发明的快速多频涡流检测方法,一般称为“预防性多频检测”,简称为“PMFT”。
该系统的优点如下:1.由于采用PMFT 预多频方法,系统非常可靠; 2.检测灵敏度高;3.重复性好,标定件的测量值(如电压向量值等)可以进行长期保存;4.检测设置简单,工厂的工人经过短期培训即可操作;5.维护简单;6.每个工件检测时间仅数秒钟,速度很快;7.可为检测过的工件及标定工件建立文档;8.当。
使用无损检测技术进行涡流检测的操作步骤与技巧
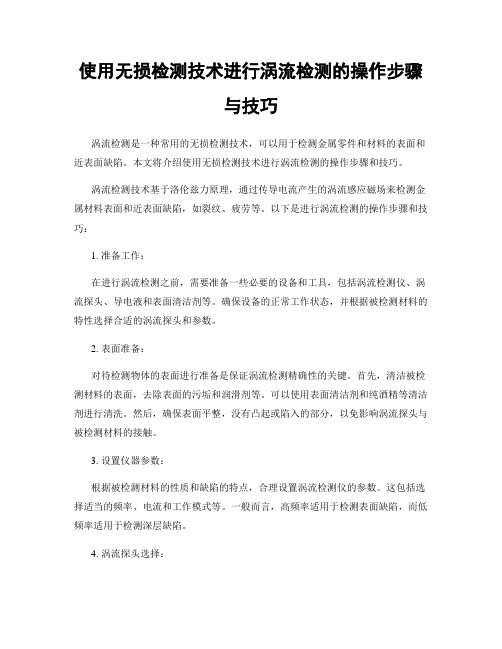
使用无损检测技术进行涡流检测的操作步骤与技巧涡流检测是一种常用的无损检测技术,可以用于检测金属零件和材料的表面和近表面缺陷。
本文将介绍使用无损检测技术进行涡流检测的操作步骤和技巧。
涡流检测技术基于洛伦兹力原理,通过传导电流产生的涡流感应磁场来检测金属材料表面和近表面缺陷,如裂纹、疲劳等。
以下是进行涡流检测的操作步骤和技巧:1. 准备工作:在进行涡流检测之前,需要准备一些必要的设备和工具,包括涡流检测仪、涡流探头、导电液和表面清洁剂等。
确保设备的正常工作状态,并根据被检测材料的特性选择合适的涡流探头和参数。
2. 表面准备:对待检测物体的表面进行准备是保证涡流检测精确性的关键。
首先,清洁被检测材料的表面,去除表面的污垢和润滑剂等。
可以使用表面清洁剂和纯酒精等清洁剂进行清洗。
然后,确保表面平整,没有凸起或陷入的部分,以免影响涡流探头与被检测材料的接触。
3. 设置仪器参数:根据被检测材料的性质和缺陷的特点,合理设置涡流检测仪的参数。
这包括选择适当的频率、电流和工作模式等。
一般而言,高频率适用于检测表面缺陷,而低频率适用于检测深层缺陷。
4. 涡流探头选择:根据被检测物体的类型和形状,选择合适的涡流探头。
涡流探头有多种形状和尺寸,如线圈型、环形和块状等。
正确选择涡流探头可确保信号的传递和反应的准确性。
5. 涡流检测操作:将涡流探头与被检测材料保持平行或垂直接触,然后逐步移动,覆盖整个被检测区域。
应用适当的压力,保持涡流探头与被检测材料的紧密接触。
移动速度应适中,不过快或过慢,以免影响检测结果。
6. 结果分析:通过检测仪器观察和分析得到的信号,判断是否存在缺陷。
缺陷一般表现为信号的幅度变化、形态变化或峰值的出现。
熟练的操作者可以根据信号的特点和峰值位置准确判断缺陷的位置和性质。
7. 结果记录:对涡流检测结果进行记录是保留检测数据、进行评估和跟踪的重要步骤。
可以使用图表、照片和文字描述等方式记录检测结果。
同时,应该注意保护被检测材料的安全性,避免进一步损坏。
- 1、下载文档前请自行甄别文档内容的完整性,平台不提供额外的编辑、内容补充、找答案等附加服务。
- 2、"仅部分预览"的文档,不可在线预览部分如存在完整性等问题,可反馈申请退款(可完整预览的文档不适用该条件!)。
- 3、如文档侵犯您的权益,请联系客服反馈,我们会尽快为您处理(人工客服工作时间:9:00-18:30)。
4多频涡流检查技术的研究
对蒸汽发生器传热管进行涡流检查时,除了传热管的缺陷信号外,还有结构、管材加工、沉积物,以及它们之间不同的组合,会产生大量的畸变信号,从而引起误判或漏检,对正确分析缺陷带来一定困难。
为此,必须对涡流检查技术进行研究,包括引进和掌握先进的多频涡流检查装置。
4. 1 MIZ-18多频涡流检查装置
蒸汽发生器传热管的涡流检查采用了美国Zetec公司生产的M IZ-18多频涡流检查装置,如图2所示。
该装置具有下列功能:
M IZ-18数据采集系统是用来采集和记录涡流检查数据,它与S M -10定位器和4D探头推拔器联合使用,其检查的全部过程由HP9836计算机控制。
S M -10定位器是自动定位装置,远控检测探头定位于管端。
安装这种定位器时,检查人员不需要进入高放射性的水室,而是将定位器从人孔插入,固定在人孔的螺栓孔上。
4D探头推拔器是远距离操作的双速探头驱动机构,由主机控制,驱动探头进入传热管或从管中拉出的最大速率为12m/ s,最慢速率为0. 03m/ s。
检查前将速率设置好,检查期间保持不变。
M IZ-18数据分析系统提供分析涡流数据的能力,包括混频、相位分析、信号图形打印和最终报告的形成。
M IZ-18数据处理系统提供对己完成的检查数据进行汇总、统计和分类,并对分析结果进行统计。
4. 2多频涡流检查技术
(1)在涡流检查中确定了4种检测频率。
550kHz为主检测频率,是判伤的主要依据,确保标定管上伤深为壁厚10%的外伤有足够的检测灵敏度及信噪比;标定管上的通孔与10%外伤的涡流信号相位差在50度至135度之间,以提高判伤的准确性。
100k H z为辅助检测频率,主要用于消除支撑板干扰信号,与主频通道混频,在混频通道上消除支撑板信号,用于支撑板信号处的判伤分析。
同时,用于弯管区的信号分析。
900kHz为胀管轮廓曲线分析频率,能提高胀管内径的测量精度。
20kHz为管板定位及沉积物检测频率,由于管板及沉积物均邻近外壁,采用较低频率。
(2)检测探头选择。
检查较大弯头U形管时,选择填充系数较大、使用寿命较长的ULC探头,它有可仲缩的脚使探头在管内对中,能使尺寸偏小的探头维持与管子同心。
检查小弯头U形竹时则需选择BJF探头,它的头部极软,能穿过小曲率U形管。
如果被测管子具有磁性,要选择具有磁饱和特性的探头。
一般每台蒸汽发生器有磁导率偏差影响的管子小于10% ,该磁偏效应可畸变或产生类似缺陷的信号,增加分析困难。
为此,采用磁饱和探头对那些带磁的管子进行重复检查,以消除磁偏效应。
旋转式探头比普通轴向探头可给出缺陷的类别、尺寸及方向等更详细的信息,但检查速度较慢,一般用于对缺陷进行定性定量分析和对管子复杂区域进行补充检查,以发现轴向探头可能漏检的缺陷。
( 3)掌握和应用胀管区轮廓曲线的分析技术。
利用由美国Zetec公司引进的“远控涡流数据采集分析系统”和“管板轮廓曲线分析程序”,开展对胀管区轮廓曲线分析技术的研究。
一般作图通道的频率越高,分析出的轮廓曲线误差越小。
这是因为频率越高,涡流的趋肤效应越显著,渗透深度也越小。
在测量传热管内径的微小变化时,为了减少管板及管板端面对轮廓曲线分析的影响,选择900kHz的第6绝对通道为作图通道。
通过对每根传热竹的涡流信号分析,可以绘出管壁轮廓曲线,来检验管子的欠胀或过胀的状况。
4)提高检测缺陷的灵敏度。
经研究,对Φ0. 3mm的通孔及Φ0.5mmx 60%壁厚的平底孔能准确判伤;轴向及周向相对定位误差均可《士lmm;采用多频涡流及其混频技术来消除干扰信号,例如管板上泥渣,支撑板、流量分配板、防振条等处的干扰信号,检测出真正的缺陷信号;利用DDA-4分析软件可在屏慕上显示X,Y分量长条图及局部扩展图,显示通道可任意选择,可显示频率、组态、时间、相位角、幅值及伤深、伤位等参数,利用MRPC显示软件可显示出缺陷特征及胀管形状等。