邹伟斌半终端粉磨系统新工艺新技术的应用
栏目寄语

主持人:邹伟斌#廣技术^协办单位:淄博赛纳新材料科技有限公司栏目寄语这个冬天的雾霾,催生了很多调侃的段子。
我们这个栏目没有一点幽默感,实实在在地在为粉磨系统节能降耗出点子想办法,搭建交流平台,却是在为减少雾霾天气尽微薄之力。
冬还没去,我们就在准备迎接春天的到来。
我们初定3月底在昆明举办“第三届中国水泥工业粉磨系统优化改造技术研讨会”,筹备工作已经展开。
这得益于去年西安会议的成果在企业收到实效的鼓舞。
在走访企业中,一些西安“中国水泥工业粉磨系统优化改造技术研讨会”代表反映,会议上学到的东西,投入不多,见效明显。
我们十分欣慰。
粉磨系统节电,能挖掘的空间依然很大。
本期涉及的漏料、跑粗现象,都是发生在管磨机里,必须在管磨机内部配件结构上做文章。
管磨机制备煤粉,满足不了烧成系统提产的需求,改造管磨机煤粉制备系统,可以借鉴水泥粉磨系统提产降耗的经验,完全可以在少投入的情况下获得目标产量。
辊压机半终粉磨系统,是把辊压机挤压的合格细粉部分分离出来作为成品,实现增产、节电效果。
实际生产过程中不宜追求过高产量,须考虑水泥标准稠度需水量等质量问题,必须摸索调整合格细粉在成品中的合适比例。
跟踪报道粉磨系统节能降耗的消息是本栏目永恒的任务。
最近,不少大集团开始试用陶瓷研磨体替代部分钢球粉磨水泥,以求进一步降低电耗。
H集团YY公司水泥制成采用170-120辊压机+V选+04. 2m X13m双仓管磨机+〇-s e p a N-4000选粉机组成的双闭路联合粉磨系统,改造前,P*〇42.5R水泥产量230t/h,吨水泥电耗31. 6kWh/t。
采用淄博赛纳新材料科技有限公司高强耐磨陶瓷研磨体替代二仓钢球,系统产量微降至222 t/h,电耗却降到27kWh/t,表现出很好的节能降耗效益。
第三届中国水泥工业粉磨系统优化改造技术研讨会将在昆明举办本刊讯由本刊主办,淄博赛纳新材料科技有限公司、江苏鹏飞集团股份有限公司、郑州机械研宄所协办的“第三届中国水泥工业粉磨系统优化改造技术研讨会”将于3月29日在昆明举办,相关筹备工作已经展开。
磨内隔仓板改造失误后粉磨系统的再改进

21中图分类号:TQ172.632.9 文献标识码:B 文章编号:1008-0473(2019)01-0021-04 DOI 编码:10.16008/ki.1008-0473.2019.01.003磨内隔仓板改造失误后粉磨系统的再改进邹伟斌1 邹 健21. 中国建材工业经济研究会水泥专业委员会,北京 100024;2. 浙江鸿盛化工有限公司,浙江 绍兴 312300摘 要 RS公司在管磨机筛分隔仓板改造过程中,采用了篦缝宽度尺寸偏小的内筛板,导致磨内一仓(粗磨仓)至二仓(细磨仓)之间通风与过料能力明显下降,随之出现了系统产量降低、粉磨电耗增加的异常状况。
结合现场实际工况,首先解决管磨机筛分隔仓板的内筛板过料与通风能力;其次改造打散分级机下锥体筛板,然后调整研磨体级配。
改造后,系统产量提高,电耗明显降低。
关键词 管磨机 隔仓板 内筛板 下锥体筛板 研磨体级配 产量 电耗0 引言RS公司建有一套辊压机双闭路水泥联合粉磨系统,在Φ3.8 m×13 m双仓管磨机筛分隔仓板的改造过程中,选用了内筛板,投产后系统产量降低、粉磨电耗增加。
经过现场技术诊断分析,导致该不良现象产生的主要原因是:筛分隔仓板配置的内筛板篦缝小,过料能力不足。
结合现场实际工况分三步对粉磨系统实施改进:第一步,重点解决管磨机筛分隔仓板的内筛板过料与通风能力;第二步,改造辊压机预粉磨系统中打散分级机下锥体筛板,大幅度降低了入磨物料最大颗粒的比例以及颗粒群的整体粒径,为系统增产、降耗创造先决条件;第三步,根据入磨物料粒径与综合水分,对磨内研磨体级配进行针对性调整。
改造后,管磨机产量稳定提高,粉磨系统电耗明显降低。
本文对这次磨内隔仓板改造失误后粉磨系统的再改进进行总结。
1 系统配置与基本状况RS公司水泥制成工序配置RP120-80辊压机(物料处理能力180~230 t/h,主电机功率500 kW×2)+600/140打散分级机(物料处理能力≥380 t/h,打散电机功率55 kW+分级电机功率45 kW)+Φ3.8 m×13 m双仓管磨机(主电机功率2 500 kW-10 kV-额定电流185 A,主减速机型号JS130C,速比i =44.588∶1;磨机筒体工作转速16. 6r/min;磨机一仓有效长度3.75 m,仓长比例30%;二仓有效长度8.75 m,仓长比例70%;设计研磨体总装载量175 t)+O-Sepa N-3000高效涡流选粉机(主轴电机功率132 kW,最大喂料能力540 t/h,最大选粉能力180 t/h;配置系统风机风量210 000 m 3/h,风压5 600 Pa,风机电机功率500 kW-10 kV-额定电流35A)+磨尾收尘风机(风机风量45 000 m 3/h,风压3 500 Pa,风机电机功率90kW)组成的双闭路联合粉磨系统(见图1)。
我国水泥粉磨技术现状调查分析(三)

我国水泥粉磨技术现状调查分析(三)邹伟斌【期刊名称】《新世纪水泥导报》【年(卷),期】2014(000)006【总页数】13页(P4-16)【作者】邹伟斌【作者单位】中国建材工业经济研究会水泥专业委员会,北京 100024【正文语种】中文【中图分类】TQ172.632国内水泥粉磨成品分级系统选择应用O-Sepa高效选粉机的较多。
O-Sepa高效选粉机于1979年由小野田公司研发推出,是笼式选粉机的代表,属于第三代空气选粉机,其技术核心环节由“分散、分级、收集”三个部分组成,“分散是关键、分级是根本、收集是保证”,三个环节互为关联与约束。
O-Sepa高效选粉机采用负压抽吸式操作,成品经上部出风管道进入尾部的布袋收尘器集中收集,不同规格O-Sepa高效选粉机设计有两个或四个进料口及三个(或两个)进风管道,其中,一次风为主风,进风比例约占总风量的67.5%,二次风占22.5%,三次风占10%。
O-Sepa高效选粉机进风形式:一次风、二次风由水平方向切向进入,随导风叶片分配及笼型转子旋转形成平面涡流形式空气流场,入机物料先经撒料盘进行分散,再完成分级;三次风则由下部锥体圆周上水平180°均布的两个风管或水平120°均布的三个风管进入机内,实施再次清洗、分选(大型O-Sepa高效选粉机无三次风管)。
O-Sepa选粉机在水泥粉磨系统中的配置,分为磨尾单风机和磨尾双风机两种系统(见图35)。
两种系统各有特点:磨尾单风机系统中少用一台收尘器,磨尾通风管道接入O-Sepa选粉机一次风管,实际生产中调节不太方便,需在磨尾至选粉机风管上增设辅助风阀,否则,不易平衡磨机通风与选粉机用风,两路相互干扰。
磨尾双风机系统中磨机通风与选粉机用风各自单列,互不干扰,调节自由度大,方便快捷;现有大型闭路水泥粉磨系统都采用磨尾双风机配置。
O-Sepa选粉机外形及笼型转子与耐磨钢板制作的切向导风静叶片结构见图36。
联合粉磨开路磨系统增产与调整

联合粉磨开路磨系统增产与调整邹伟斌中国建材工业经济研究会水泥专业委员会(100831)赵家胤湖北省黄石市产品质量监督检验所(435000)王新四川南威水泥有限公司(四川南江)(636600)题要:本文以生产规模60万吨/年水泥粉磨生产线配置120-50辊压机与动态分级设备(打散分级机)和Ф3.2×13m开路三仓高细管磨机组成的单闭路粉磨工艺系统为例,论述总结了实际生产过程中粉磨系统存在的共性问题及其改进所采取的技术与调整措施,并进行了相关的技术经济分析。
关键词:分级效果磨内改造级配调整分段粉磨1、导言近几年来,设计生产规模60万吨/年的水泥粉磨站,大多采用Ф3.2×13m管磨机。
生产工艺流程中,既有双闭路粉磨工艺系统(辊压机+动态或静态分级机+管磨机+高效选粉机,其中辊压机与动态分级机(打散分级机)或静态分级机(V形选粉机)组成磨前闭路、管磨机与高效选粉机组成闭路);也有单闭路粉磨工艺系统(辊压机+动态或静态分级机+开路管磨机);此外还有普通的一级闭路和开路粉磨系统,在此不赘述。
前两种粉磨工艺系统各有其特点:单闭路系统总装机功率低于双闭路系统,且流程较简单;从大幅度增产角度来看,双闭路粉磨工艺系统大多采用静态分级机(V形选粉机)对辊压机挤压后的物料进行风选分级,入磨物料切割粒径一般≤0.5mm且颗粒较均匀,因粉磨过程中“过粉磨”现象减少,其系统产量潜力发挥明显高于单闭路粉磨工艺系统,系统粉磨电耗一般在28 kwh -33kwh/t水泥左右;当然,若单闭路粉磨工艺系统优化调整方法得当,其增产幅度也较大(>50%以上),系统粉磨电耗也可控制在27kwh -30kwh/t左右。
以国内某单位双闭路粉磨工艺系统为例,其配置的辊压机功率+静态分级机(V形选粉机)循环风机功率=1220kw;另一单位的单闭路粉磨工艺系统中辊压机功率+静态分级机(V 形选粉机)循环风机功率=1320kw;上述两个系统中Ф3.2×13m磨机台时产量均在120t/h 左右。
邹伟斌辊压机预粉磨系统增产调整

辊压机预粉磨系统增产降耗优化调整与探讨邹伟斌中国建材工业经济研究会水泥专业委员会(100024)汪海滨建筑材料工业技术情报研究所(100024)邹捷南京工业大学粉体科学与工程研究所 (210009)摘要:目前,国内尚有部分水泥企业应用带有辊压机通过式挤压预粉磨的水泥粉磨系统,由于该系统原配辊压机能力较小且无分级设备配置,入磨物料粒度分布范围较宽,均齐性较差,虽后续管磨机系统增产幅度一般达到20%-60%,平均节电幅度10%-20%,但系统粉磨电耗仍较高。
在辊压机预粉磨系统采用机械筛分技术,降低入磨物料粒度,提高均齐性的同时,优化调整磨内研磨体级配及成品选粉机技术参数,最终达到了较理想的增产、降耗效果。
关键词:辊压机预粉磨机械筛分分级增产降耗1.基本慨况某公司水泥制成工序原采用Ф4.2×13m双仓水泥管磨机(主电机功率3550KW、两仓研磨体均使用钢球、一仓采用曲面阶梯衬板、二仓采用风机衬板;双层筛分隔仓板、同心圆状粗筛缝宽度10mm、内筛缝宽度4.0mm;磨尾出料同心圆状篦板缝宽度8mm)+选粉机的一级闭路粉磨系统,台时产量只有90t/h。
之后,为实施磨前物料处理,配置一台120-80辊压机(电机功率500KW×2、通过量260t/h)作为预粉磨(无分级)设备,由于缺乏维护,辊压机动、静辊面及侧挡板磨损较严重、两侧边部漏料、工作压力低、挤压效果差,入磨物料中大于8mm以上颗粒比例达到30%以上,粒度分布范围较宽,系统产量较低。
磨尾为系统风机与收尘风机各自单列配置,O-SePa N-3500高效选粉机(主轴电机功率200KW、最大喂料能力630t/h、选粉能力210t/h、理论配风量210000m3/h、实际配置系统风机风量250000m3/h、风压7500Pa),粉磨P.O42.5水泥(熟料、石灰石、粉煤灰、脱硫石膏,成品比表面积≥360m2/kg)产量120t/h,系统粉磨电耗36kwh/t左右。
辊压机水泥半终粉磨工艺系统的增产调试
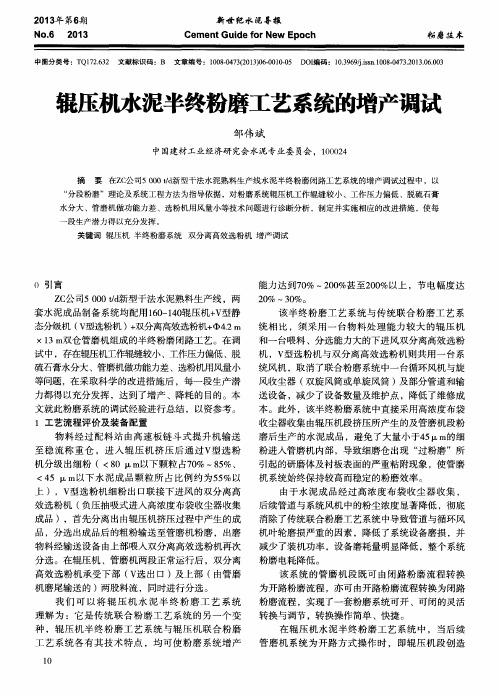
2 0 1 3 年 第6 期 N o . 6 2 0 1 3 邹 伟斌 :辊 压机 水泥 半终 粉磨 工艺 系统 的增产 调试 物 磨丝木
的成品与开路管磨机粉磨系统生产的成 品共 同混合 成 品性 能满 足混凝 土 制备技 术要 求 。
入 库 ,成 品颗粒 级 配范 围 比闭路操 作 时要 宽 。当后
至稳 流 称 重 仓 ,进 入 辊 压 机挤 压 后 通 过 v型 选 粉 机 分 级 出细粉 (<8 0 m以下 颗粒 占7 0 % ~8 5 %、 <4 5 m以 下 水 泥成 品颗 粒 所 占 比例 约 为5 5 %以 上 ),V型选 粉机 细粉 出 口联 接下进 风 的双 分离 高
辊压机水泥半终粉磨工艺系统的增产调试
邹伟 斌
中国建材工业经济研 究会水泥专业委 员会 ,1 0 0 0 2 4
摘 要 在Z C 公 司5 0 0 0 t / d 新型干法水泥熟料生产线水 泥半终粉磨 闭路工艺 系统 的增产调试过程 中,以
“ 分段粉磨”理论及系统工程方 法为指导依据 ,对粉磨系统辊压机工作辊缝较小 、工作压力偏低 、脱硫石膏 水分大 、管磨机做功能力差 、选 粉机用风量小等技术问题进行诊断分析 ,制定并实施相应 的改进措施 ,使每
套水泥成品制备系统均配用1 6 0 — 1 4 0 辊压机+ V 型静 该 半 终 粉磨 工 艺 系 统 与传 统联 合 粉 磨 工 艺 系 态分级机 ( V 型选粉机 )+ 双分离高效选粉机+ 4 . 2 m 统 相 比 ,须 采 用 一 台物 料 处 理能粘附现象 ,使管磨 机 系统始 终保持 较高 而稳定 的粉磨 效率 。
由于水 泥 成 品经 过 高浓 度 布 袋 收 尘 器 收集 ,
效选粉机 ( 负压抽吸式进入高浓度布袋收尘器收集 成 品 ),首 先分 离 出由辊压机 挤压 过程 中产生 的成 品 ,分选 出成 品后 的粗 粉输送 至管磨 机粉 磨 ,出磨 物料 经输送 设备 由上部 喂入 双分 离高效 选粉机 再次
水泥联合(半终)粉磨系统管磨机一仓仓长的探讨
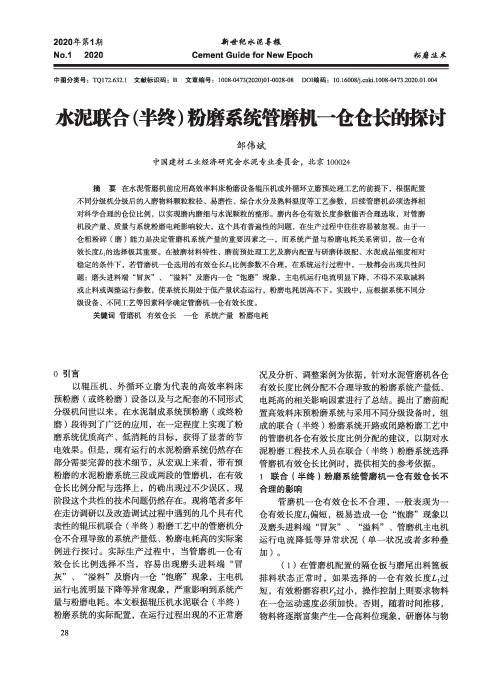
2020年第4期No.1 2020韧磨抜术新世他水猊專报Cement Guide for New Epoch中图分类号:TQ172.632.1 文献标识码:B 文章编号:1008-0473(2020)01-0028-08 DOI 编码:10.16008/ki.l008-0473.2020.01.004水泥联合(半终)粉磨系统管磨机一仓仓长际讨邹伟斌中国建材工业经济研究会水泥专业委员会,北京100024摘要在水泥管磨机前应用高效率料床粉磨设备辐压机或外循环立磨预处理工艺的前提下,根据配置不同分级机分级后的入磨物料颗粒粒径、易磨性、综合水分及熟料温度等工艺参数,后续管磨机必须选择相对科学合理的仓位比例,以实现磨内磨细与水泥颗粒的整形。
磨内各仓有效长度参数能否合理选取,对管磨机段产量、质量与系统粉磨电耗影响较大,这个具有普遍性的问题,在生产过程中往往容易被忽视。
由于一仓粗粉碎(磨)能力是决定管磨机系统产量的重要因素之一,而系统产量与粉磨电耗关系密切,故一仓有效长度厶的选择极其重要。
在被磨材料特性、磨前预处理工艺及磨内配置与研磨体级配、水泥成品细度相对 稳定的条件下,若管磨机一仓选用的有效仓长厶比例参数不合理,在系统运行过程中,一般都会出现共性问题:磨头进料端“冒灰”、“溢料”及磨内一仓“饱磨”现象,主电机运行电流明显下降,不得不采取减料或止料或调整运行参数,使系统长期处于低产量状态运行,粉磨电耗居高不下。
实践中,应根据系统不同分级设备、不同工艺等因素科学确定管磨机一仓有效长度。
关键词管磨机有效仓长一仓系统产量粉磨电耗0引言以辐压机、外循环立磨为代表的高效率料床预粉磨(或终粉磨)设备以及与之配套的不同形式 分级机问世以来,在水泥制成系统预粉磨(或终粉 磨)段得到了广泛的应用,在一定程度上实现了粉磨系统优质高产、低消耗的目标,获得了显著的节 电效果。
但是,现有运行的水泥粉磨系统仍然存在部分需要完善的技术细节,从宏观上来看,带有预粉磨的水泥粉磨系统三段或两段的管磨机,在有效仓长比例分配与选择上,的确出现过不少误区,现阶段这个共性的技术问题仍然存在。
邹伟斌中国水泥工业水泥粉磨系统现状调查分析(连载二)

中国水泥工业水泥粉磨系统现状调查分析邹伟斌中国建材工业经济研究会水泥专业委员会(北京100024)(连载二)摘要:本文以水泥企业调查的实际生产设备配置及运行技术参数为依据,在水泥生产线采用不同粉磨工艺条件下,水泥粉磨系统的主、辅机设备配置及粉磨电耗水平进行了调查分析,列举了不同粉磨系统实现较低粉磨电耗的优秀案例,探讨了水泥行业高效粉磨技术的发展方向。
本文以连载方式刊发,第一部分论述了辊压机系统配置的各种分级设备技术性能特点、水泥粉磨系统低能耗优秀案例分析及辊压机应用过程中出现的问题与处理措施等。
第二部分论述了CKP立磨预粉磨以及筒辊磨、立磨料床水泥终粉磨案例分析以及管磨机运行中出现的异常状况与处理措施;第三部分论述了水泥粉磨系统成品选粉机使用过程中出现的技术问题及解决办法以及其他水泥粉磨系统(辊压机预粉磨系统、辊压机半终粉磨系统;球破磨、棒磨机、破碎机、柱磨机或单传动辊压机预处理组成的粉磨系统)与案例分析;总结了水泥联合粉磨系统实现高产、低能耗的技术关键与措施。
关键词:水泥制成工艺粉磨电耗调查分析(接上期)3.CKP立磨(料床)预粉磨机以及带有CKP立磨(料床)预粉磨的水泥粉磨系统(工艺流程见图15)由日本秩父小野田与川崎重工推出的CKP立磨(料床)预粉磨系统配套于管磨机,对入管磨机前水泥熟料进行连续碾压预粉磨,有效降低入磨物料粒度,可提高系统产量50%--100%、节电20%--30%。
用于预粉磨水泥生料,可使系统增产100%—200%,节电幅度达30%—40%。
CKP立磨和一般风扫立磨的主要区别是取消了顶部成品选粉机与风机及收尘器,系统装机功率低。
其主要功能是作为预粉磨,碾磨后的物料不经任何分级直接入磨,虽颗粒粒径分布较宽,但碾磨后的物料具有“晶格微裂纹”,易磨性显著改善。
与后续管磨机可以组成开路或闭路粉磨等系统;CKP立磨特点:顶部无选粉机、采用边部机械卸料(30%物料参与循环以密实料床、70%物料入管磨机)、固定料床粉磨、运行能耗低、工作性能稳定、磨辊与磨盘采用高性能耐磨材料,使用寿命达30000h以上,实现了长寿命、高效率运转。
- 1、下载文档前请自行甄别文档内容的完整性,平台不提供额外的编辑、内容补充、找答案等附加服务。
- 2、"仅部分预览"的文档,不可在线预览部分如存在完整性等问题,可反馈申请退款(可完整预览的文档不适用该条件!)。
- 3、如文档侵犯您的权益,请联系客服反馈,我们会尽快为您处理(人工客服工作时间:9:00-18:30)。
半终粉磨系统新工艺及其应用总结何活权新疆屯河水泥有限责任公司(831100)邹伟斌中国建材工业经济研究会水泥专业委员会(100024)提要:本文介绍了一种新型半终粉磨系统及其在生产中的应用,探讨了该粉磨系统节电效果;关键词:半终粉磨系统多级分选分段粉磨水泥粉磨工艺、设备的配置对水泥生产效率及经济效益影响极大,为提高水泥粉磨工艺水平,该公司和选粉机制造企业共同探讨,结合现有条件制订由联合粉磨改造成半终粉磨系统的新工艺技术。
重点是采用“多级分选、分段粉磨”的新工艺,将一台成品分离专用选粉机设置在辊压机预粉磨系统中的v型选粉机出风口处,将辊压机系统挤压预粉磨过程中产生的合格品及时分选出来。
通过安装调试与生产运行证明:P·O42.5级水泥由技改前的200~220t/h提高到目前的280t/h,成品比表面积在370m2/kg以上,粉磨系统电耗由35.2kwh/t 降至27kWh/t,为公司水泥粉磨系统的节能降耗探索了一条新路子。
1 新工艺新技术探讨研究与启示1.1 通过对球破磨--管磨机粉磨系统研究得到的启示:在物料粗破碎阶段的效率最高,采用大钢球破碎大块物料,小钢球粉磨小颗粒物料。
若在粗破碎过程中采用风选原理,把细小颗粒及时带走,实现“边粉磨、边分选”,大大降低由细颗粒物料导致缓冲垫层所产生的无用功浪费,同时能够显著减少“过粉磨”。
使其集破碎、研磨、分级功能为一体,提高了系统的破碎效率及后续细磨设备的粉磨能力,而且具有自动粗、细分级功能,分级精度较高,可不再单独配套分级设备。
1.2配套预粉磨系统成品分离专用选粉机对辊压机+V型静态选粉机+双仓管磨机+O-SePa选粉机组成的联合粉磨闭路系统进行改造。
运用“多级分选、能选早选、分段粉磨”理论及系统工程方法为指导依据,并对粉磨系统中各段存在的技术问题进行了诊断分析,进而充分挖掘粉磨系统中每一段生产潜力,以求取得理想的效果。
在伊犁天山公司技改的基础上,经过与选粉机制造厂家技术人员共同努力,在现有水泥成品制备系统辊压机+V型选粉机至管磨机之间增设一台专用成品选粉机,即形成:由180-120辊压机+V型静态分级机(V型选粉机)+预粉磨系统成品分离专用选粉机+Φ4.2×13m双仓管磨机组成的新型半终粉磨闭路工艺系统,P·O42.5级水泥产量由技改前200~220 t/h提高到280t/h,水泥比表面积≥370m2//kg,粉磨系统电耗由35.2kWh/t降低到27 kWh/t,吨水泥粉磨电耗降低8.2kwh/t,增产节电效果显著。
2. 屯河水泥伊犁分公司项目实施情况2.1 水泥粉磨工艺线基本概况水泥成品制备系统配用180-120辊压机+V型静态分级机(V型选粉机)+预粉磨系统成品分离专用选粉机+Φ4.2×13m双仓管磨机组成的半终粉磨闭路工艺;其具体工艺流程为:物料经过配料站由高速板链斗式提升机输送至V型选粉机再入稳流称重仓,进入辊压机挤压后通过V型选粉机分级出细粉(<80um以下颗粒占70%~85%、<30um以下水泥成品颗粒所占比例约为20%以上),V型选粉机细粉出口联接侧进风型式的预粉磨系统成品分离专用选粉机,首先分离出由辊压机挤压过程中产生的≤30um的成品。
分选出成品后,通过V 型选粉机的一些30~200um中等粉状物料进入管磨机粉磨。
出磨物料经提升机喂入O-Sepa N-4000选粉机分选,选出的成品与辊压机挤压过程中产生的成品共同进入水泥库,粗粉回磨头入磨机再次粉磨。
该半终粉磨工艺系统仅增加一台喂料、分选能力大的侧进风型式的预粉磨系统专用成品选粉机,V型选粉机与预粉磨系统成品分离专用选粉机则共用一台循环风机。
该系统取消了原系统中部分管道和输送设备,直接采用四个旋风筒收集由辊压机段挤压所产生的水泥成品,避免了大量<30um细粉进入管磨机内部,导致细磨仓出现“过粉磨”所引起的研磨体及衬板表面严重粘附现象,使管磨机系统始终保持较高而稳定的粉磨效率。
由于水泥成品经过四个旋风筒收集,后续管道与系统风机中的粉尘浓度及水泥温度显著降低,消除了原粉磨工艺系统中导致管道与循环风机叶轮磨损严重的因素,降低了系统设备磨损,设备运转率明显提高、系统粉磨电耗明显降低。
粉磨工艺系统主、辅机设备配置及技术性能参数见表1:表1 粉磨系统主、辅机设备配置2.2、生产调试中遇到的问题2.2.1、新加选粉机过料问题投产调整初期,出现选粉机通风阻力非常大,进口与出口之间负压高达3000Pa、辊压机挤压出来的物料进磨量较少,满足不了磨机需求,投料量也小。
2.2.2、辊压机工作压力偏低受辊压机工作辊缝偏小的影响,工作压力上不去,挤压效果较差,辊压机工作压力在6.5MPa-8.0MPa左右波动,挤压后细粉明显偏少。
2.2.3、管磨机做功能力差一般来讲,带有选粉机的水泥半终粉磨系统,由于预先分离出成品,入磨物料中的细粉量极大地减少,能够较好地避免细粉在磨内产生的“过粉磨”以及细磨仓研磨体与衬板表面的粘附现象,研磨体磨细做功能力提高,每米研磨体创造出磨物料比表面积能力至少应≥10m2/kg/m。
由预粉磨系统成品分离专用选粉机分离出成品后的入磨物料(粗粉)比表面积平均在130m2/kg左右,而在管磨机有效长度12.5m范围内研磨体做功少,出磨水泥比表面积仅在220m2/kg左右,计算得知:每米研磨体粉磨出的比表面积为7.2m2/kg/m,说明管磨机段研磨能力相对不足;2.2.4、选粉机用风量小辊压机段与管磨机段做功能力均不理想,即挤压处理与研磨两段的成品量相对不足,以致不能增加V选与四分离高效选粉机拉风量,一般在50%左右。
中控操作增加系统风机风量时,造成水泥成品比表面积低、细度粗;由此判断:辊压机与管磨机两段创造成品量低时,系统风机拉风量必须降低,由此导致系统产量降低。
2.3、原因分析及处理措施2.3.1、新加装入磨前的选粉机导风叶片调节距离只有25mm(厂家规定)造成选粉机内部通风阻力大,影响物料进入选粉机转笼进行分级分选,针对这个问题决定把导风叶片调整到50mm 后开机拉风,阻力明显下降,物料也能随着投料量的比例进入选粉机内部分级分选,同时能够满足磨机的粉磨需求。
2.3.2辊压机工作压力及辊缝辊压机水泥部分终粉磨工艺系统(或联合粉磨工艺系统)的共同特点是:辊压机及分级设备的投入,实现了系统中的“分段粉磨”,必须充分发挥辊压机系统料床粉磨的技术优势及其较大的处理能力,辊压机段做功越多,对系统增产节电越有利;辊压机的吸收功耗越多,后续管磨机段节电效果越显著;辊压机吸收功耗一般在8kwh/t-15kwh/t,在此范围内吸收功耗越多,管磨机段节电幅度越大。
基本规律是:辊压机吸收功多投入1kwh/t,则后续管磨机系统节电1.5kwh/t--2kwh/t;在相对稳定的工艺条件下,辊压机工作压力越大,挤压处理物料过程中产生的粉料越多,成品量显著增加,被分离出的合格品也越多。
2.3.2.1、首先,对入辊压机熟料采取先进入V选分选的措施,多采用颗粒状料、减少粉状料;其次,称重仓必须保持一定的仓容,料位比例一般控制在60%-70%,以有效形成入机料压,实现过饱和喂料,确保挤压效果;同时将辊压机工作压力由6.0MPa-8.0MPa,调整至8.0MPa-9.0MPa;辊压机工作辊缝由原25mm左右,调整至40mm 左右;入料斜插板比例拉开至85%以上,以实现过饱和喂料;调整后辊压机主电机工作电流(额定电流89.2A)由50A-60A(56%-67%)提高至70A-80A(78.5%-89.6%),挤压做功能力显著提高,合格品比例大幅度增加。
(<80um以下颗粒占70%~85%、<30um以下水泥成品颗粒所占比例约为20%以上,而经第一段成品选粉机分选出的水泥比表面积也达到了≥390 m2/kg)2.3.2.2、最大限度的提高进辊压机物料的颗粒均匀性,尤其是细颗粒物料比例应控制在一定的范围,过多的细颗粒(特别是<0.2mm以下的细料)会极大的影响辊压机的做功;通过调整,预粉磨系统专用选粉机的粗料回料量找到一个最佳的平衡点,让辊压机多出合格的成品料(确保细度指标)可进一步提高系统产量。
2.4、V型选粉机及预粉磨系统专用选粉机用风量在半终粉磨系统中,由于V型选粉机与预粉磨系统成品分离专用分级机共用一台循环风机,在满足水泥质量控制指标的前提下,应尽量采用大风操作方式,最大程度上将辊压机段及管磨机段创造的成品分选出来,系统风机的拉风比例由原60%提高至90%以上。
2.5、管磨机研磨体级配及通风参数管磨机的特点是磨细能力有余而粗碎能力较差,而由辊压机+V 型静态分级设备组成的磨前预粉磨系统,能够充分发挥辊压机高效率料床粉磨优势,高压挤压处理后的入磨物料微观裂纹多、易磨性明显提高,物料在辊压机段处理时产生的成品已被V型选粉机与预粉磨系统专用分级机预先分选出来,粗粉再进入管磨机粉磨,由此实现了良好的“分段粉磨”。
生产实践早已证明:采用“分段粉磨”工艺比一段粉磨工艺所需能量更低、系统增产、节电效果更显著。
在改造半终粉磨系统的同时,对管磨机内部结构也作了一些优化和改进,把原来设计不合理且存在质量问题的隔仓板、出料筛板更换(原来经常堵塞)。
投产初期,由于设备磨合及研磨体级配等方面的原因,管磨机粉磨效果较差,根据入磨物料细度、比表面积等参数,重新设计、调整了各仓级配,在管磨机段粉磨过程中,主要依靠研磨体的“集群研磨效应”从而实现物料磨细。
同时,根据磨机主电机及主减速机的驱动功率富裕系数,合理增加细磨仓微锻研磨体装载量、增大填充率,能够有效提高微锻的总研磨面积,提高细磨仓内微型研磨体对物料的细研磨能力;总之,在管磨机段必须凸显“磨内磨细”为根本要素;调整研磨体级配后,出磨物料比表面积达到300m2/kg,已接近一般成品水泥的比表面积,在管磨机有效长度范围内平均每米研磨体创造比表面积为:300m2/kg-130m2/kg/12.5m=13.6m2/kg/m,比调整前提高了6.4m2/kg/m。
改进前、后水泥产量、比表面积及系统粉磨电耗对比:表2 改进前、后系统技术经济指标对比由表2可知:系统改进后,P.O42.5级水泥系统产量提高70t/h、增产幅度33.3%;粉磨系统电耗降低8.2kwh/t、节电幅度达23.3%;出磨水泥比表面积提高6.4m2/kg/m;通过合理的改进与调整,该半终粉磨工艺系统增产、节电效果显著,水泥实物质量指标较改进前有所提高。
以年产150万吨水泥计算,年可节电1200万kwh,按平均电价0.60元/kwh计,粉磨系统改进后,仅年节电效益就可达720万元,经济效益显著。
3、可行性和经济分析水泥生产是一个高能耗的行业,尤其水泥粉磨系统平均电耗与先进水平相比仍然较高。