铝及铝合金酸性脱脂工艺研究
铝及铝合金的铬酸阳极化

铝及铝合金的铬酸阳极化摘要:铝合金本身可以与氧气接触形成氧化膜,防止腐蚀。
但在工业和大气环境中酸性物质、盐类物质的侵蚀程度较强,而自身氧化膜远远不能够满足防腐蚀的需要,在生产中腐蚀会造成严重的经济损失和安全隐患,因此铝及铝合金的防腐研究越来越受到人们的重视。
关键词:铝合金;脱脂;铬酸阳极化;封闭处理;耐蚀性;铝合金铬酸氧化膜层不透明,颜色由灰白色到深灰色或彩虹色,比硫酸氧化膜和草酸氧化膜要薄得多,一般厚度只有1~5μm,能保持原来零件的精度和表面粗糙度;膜层质软、弹性高,基本上不降低原材料的疲劳强度;同时,铬酸氧化膜与有机物的结合力良好,是油漆的良好底层,因此,飞机上的结构件很多都需要铬酸阳极化处理。
一、铝合金腐蚀的类型1.点蚀。
当铝合金局部开始出现腐蚀,铝合金表面会生成氧化膜对点腐蚀进行修复。
当修复速度小于腐蚀速度时,点腐蚀从此处深度加强,面积增大。
2.应力腐蚀。
在外界拉应力或内应力及腐蚀的共同作用下,铝合金表面的氧化膜破损。
在局部的破损与非破损区会存在电势差,并且在腐蚀气体、液体的作用下形成电池结构,进一步促进腐蚀发生,特点是铝合金的断裂会在强度较大的一瞬间发生。
3.晶间腐蚀。
由于铝合金成分在表面和内部存在差异,因内外结构的不同形成了电势差。
这种腐蚀会导致晶粒间的强度减弱,使得铝合金的机械强度降低,但是由于腐蚀从表面不容易观察到,所以造成了极大的安全隐患。
4.缝隙腐蚀。
铝合金间或铝合金与其他材料接触时存在缝隙,腐蚀介质会在缝隙中存留,缝隙内部腐蚀加剧。
缝隙腐蚀与接触的合金类型无关,只要是在缝隙间存在电位差,腐蚀即可发生。
二、铬酸阳极化工艺流程1.表面预处理。
铝件经冲压、运输,表面存在污垢与缺陷,如灰尘、残留油污、人工搬运指印(主要成分为脂肪酸及含氮化合物)、金属毛刺、轻微的划擦伤等。
在阳极氧化前用物理方法进行清洗,一般使用乙醇或丙酮,使其露出纯净金属基体以获得与基体结合牢固、色泽厚度满足要求且具有最佳耐蚀、耐磨、耐侯性能的氧化膜,由于乙醇的挥发性强,容易使油污干涸在零件表面,建议使用丙酮。
无铬钝化处理主脱脂槽的分析方法
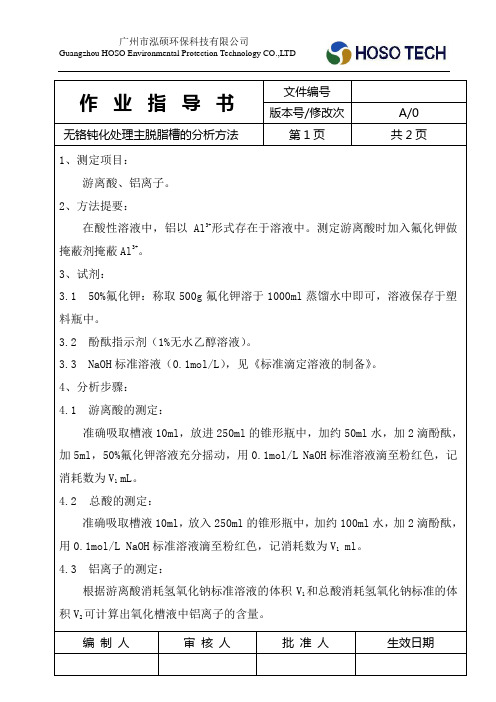
生效日期
作业指导书
文件编号
版本号/修改次
A/0
无铬钝化处理主脱脂槽的分析方法
第2页
共2页
5、结果计算:
游离酸(g/L)=4.9×V1×c(NaOH)
总酸(g/L)=4.9×V2×c(NaOH)
铝离子(g/L)=0.9×(V2-V1)×c(NaOH)
注意:以上公式一定要吸10ml作为样品,用已简化公式计算。
3.2酚酞指示剂(1%无水乙醇溶液)。
3.3 NaOH标准溶液(0.1mol/L),见《标准滴定溶液的制备》。
4、分析步骤:
4.1游离酸的测定:
准确吸取槽液10ml,放进250ml的锥形瓶中,加约50ml水,加2滴酚酞,加5ml,50%氟化钾溶液充分摇动,用0.1mol/L NaOH标准溶液滴至粉红色,记消耗数为V1mL。
编制人
审核人
批准人
生效日期
4.2总酸的测定:
准确吸取槽液10ml,放入250ml的锥形瓶中,加约100ml水,加2滴酚酞,用0.1mol/L NaOH标准溶液滴至粉红色,记消耗数为V1ml。
4.3铝离子的测定:
根据游离酸消耗氢氧化钠标准溶计算出氧化槽液中铝离子的含量。
编制人
审核人
作业指导书
文件编号
版本号/修改次
A/0
无铬钝化处理主脱脂槽的分析方法
第1页
共2页
1、测定项目:
游离酸、铝离子。
2、方法提要:
在酸性溶液中,铝以Al3+形式存在于溶液中。测定游离酸时加入氟化钾做掩蔽剂掩蔽Al3+。
3、试剂:
3.1 50%氟化钾:称取500g氟化钾溶于1000ml蒸馏水中即可,溶液保存于塑料瓶中。
铝铸件表面处理脱脂工艺
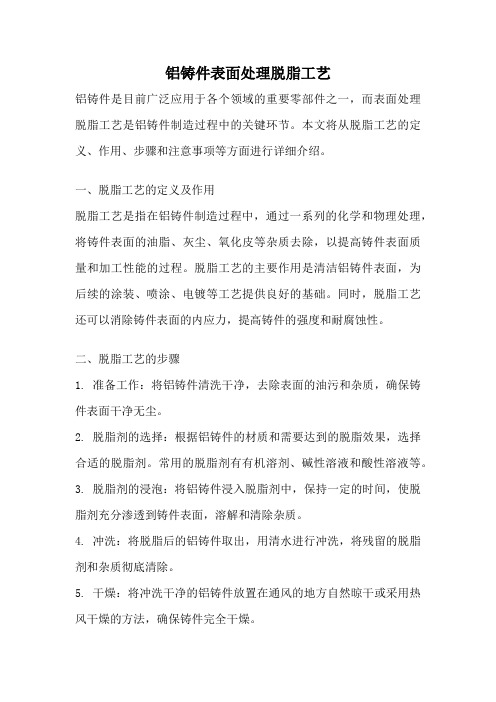
铝铸件表面处理脱脂工艺铝铸件是目前广泛应用于各个领域的重要零部件之一,而表面处理脱脂工艺是铝铸件制造过程中的关键环节。
本文将从脱脂工艺的定义、作用、步骤和注意事项等方面进行详细介绍。
一、脱脂工艺的定义及作用脱脂工艺是指在铝铸件制造过程中,通过一系列的化学和物理处理,将铸件表面的油脂、灰尘、氧化皮等杂质去除,以提高铸件表面质量和加工性能的过程。
脱脂工艺的主要作用是清洁铝铸件表面,为后续的涂装、喷涂、电镀等工艺提供良好的基础。
同时,脱脂工艺还可以消除铸件表面的内应力,提高铸件的强度和耐腐蚀性。
二、脱脂工艺的步骤1. 准备工作:将铝铸件清洗干净,去除表面的油污和杂质,确保铸件表面干净无尘。
2. 脱脂剂的选择:根据铝铸件的材质和需要达到的脱脂效果,选择合适的脱脂剂。
常用的脱脂剂有有机溶剂、碱性溶液和酸性溶液等。
3. 脱脂剂的浸泡:将铝铸件浸入脱脂剂中,保持一定的时间,使脱脂剂充分渗透到铸件表面,溶解和清除杂质。
4. 冲洗:将脱脂后的铝铸件取出,用清水进行冲洗,将残留的脱脂剂和杂质彻底清除。
5. 干燥:将冲洗干净的铝铸件放置在通风的地方自然晾干或采用热风干燥的方法,确保铸件完全干燥。
6. 检查:对脱脂后的铝铸件进行目测检查,确保铸件表面无油污、无杂质。
三、脱脂工艺的注意事项1. 脱脂剂的选择应根据铸件的材质和表面状态来确定,不同的铸件可能需要不同的脱脂剂。
2. 在脱脂过程中,应注意控制脱脂剂的浓度和温度,避免过高或过低对铝铸件造成损害。
3. 对于大型铝铸件,应采用悬挂或浸泡的方式进行脱脂,以确保铸件表面的均匀清洁。
4. 在冲洗过程中,要确保清水的质量和流量充足,以保证脱脂剂和杂质完全被冲洗掉。
5. 干燥过程中,应避免使用高温和直接暴晒的方式,防止铝铸件变形或表面氧化。
6. 在脱脂工艺中,应严格遵守安全操作规程,避免脱脂剂对人体和环境造成伤害。
铝铸件表面处理脱脂工艺是铝铸件制造过程中不可或缺的环节。
通过合理选择脱脂剂、严格控制工艺参数以及注意事项的遵守,可以确保铸件表面的清洁度和加工性能,提高铝铸件的质量和使用寿命。
门窗用铝材的酸蚀脱脂方法[发明专利]
![门窗用铝材的酸蚀脱脂方法[发明专利]](https://img.taocdn.com/s3/m/eaabfa28a1c7aa00b42acbb9.png)
专利名称:门窗用铝材的酸蚀脱脂方法专利类型:发明专利
发明人:李继升
申请号:CN201310488562.0
申请日:20131018
公开号:CN104562060A
公开日:
20150429
专利内容由知识产权出版社提供
摘要:本发明公开了一种门窗用铝材的酸蚀脱脂方法,配制酸蚀处理液,酸蚀处理液的组分以及各组分的浓度为:硫酸:35g/L-48g/L;氟化氢铵:4g/L-6g/L;柠檬酸:2g/L-4g/L;硝酸钠:1g/L-3g/L;硫酸铁:0.6g/L-1.2g/L;二丙二醇:1g/L-2g/L;脱脂剂:0.1g/L-0.5g/L;将待处理的铝材放入氧化槽内,采用步骤(1)所述处理液进行处理,处理温度为20—30℃,处理时间为4—8min;处理之后进行水洗即可,水洗喷淋压力为0.1MPa-0.2MPa。
方法简单,表面处理干净。
申请人:青岛市首胜实业有限公司
地址:266317 山东省青岛市胶州市胶东街道办事处纺织染整工业园
国籍:CN
更多信息请下载全文后查看。
铝合金酸性除油清洗剂配方研发性能优势及成熟技术转让
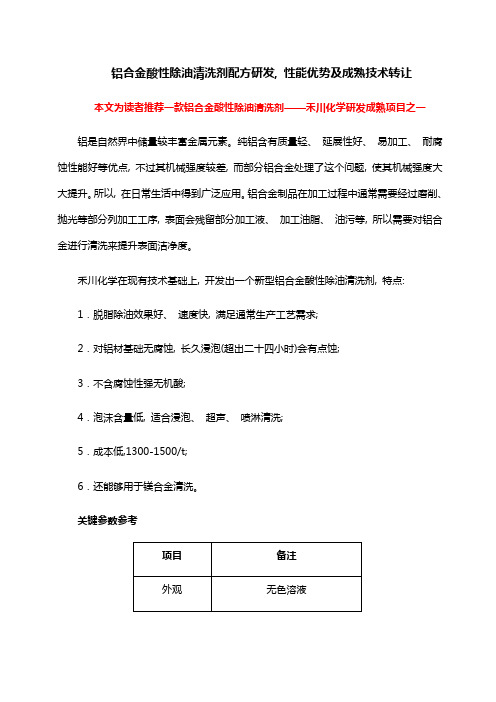
铝合金酸性除油清洗剂配方研发, 性能优势及成熟技术转让本文为读者推荐一款铝合金酸性除油清洗剂——禾川化学研发成熟项目之一铝是自然界中储量较丰富金属元素。
纯铝含有质量轻、延展性好、易加工、耐腐蚀性能好等优点, 不过其机械强度较差, 而部分铝合金处理了这个问题, 使其机械强度大大提升。
所以, 在日常生活中得到广泛应用。
铝合金制品在加工过程中通常需要经过磨削、抛光等部分列加工工序, 表面会残留部分加工液、加工油脂、油污等, 所以需要对铝合金进行清洗来提升表面洁净度。
禾川化学在现有技术基础上, 开发出一个新型铝合金酸性除油清洗剂, 特点:1.脱脂除油效果好、速度快, 满足通常生产工艺需求;2.对铝材基础无腐蚀, 长久浸泡(超出二十四小时)会有点蚀;3.不含腐蚀性强无机酸;4.泡沫含量低, 适合浸泡、超声、喷淋清洗;5.成本低,1300-1500/t;6.还能够用于镁合金清洗。
关键参数参考铝合金酸性光亮清洗对比图(铝合金酸性除油清洗剂为成熟优势项目, 可做配方技术转让, 禾川化学提供配方定制服务, 处理生产研发企业配方技术难题)禾川介绍苏州禾川化学技术服务有限企业(简称“禾川化学”); 成立于, 前后为全球500企业在内近3500家企业、科研所, 提供了整套配方技术服务方案。
经历近五年积淀, 在精细化学品领域(工业清洗、表面处理、水处理、纺织印染、加工制造、日化洗涤、胶黏剂、功效性助剂)形成本身专长; 在精细化学品领域已形成含有一定影响力配方服务机构。
试验室介绍禾川试验室由2间前处理试验室, 6间研发室、4间大型光谱仪器室、1间常见原材料仓库组成; 拥有国外尖端红外、TGA光谱仪器在内上百种检测仪器; 高效进行未知物定性、定量分析、复杂物质结构表征, 性能检测、性能评定、优化。
禾川试验室及试验照片发明专利技术首次提出利用大型光谱仪器分析技术, 辅助企业自主创新、产业升级转型理念; 同时把配方研发技术外包服务全新概念高效推广应用到企业研发、生产中, 有效缩短企业研发周期, 降低研发成本; 加紧了企业产品升级, 产业转型步伐。
铝材脱脂工艺及酸性脱脂剂的研发
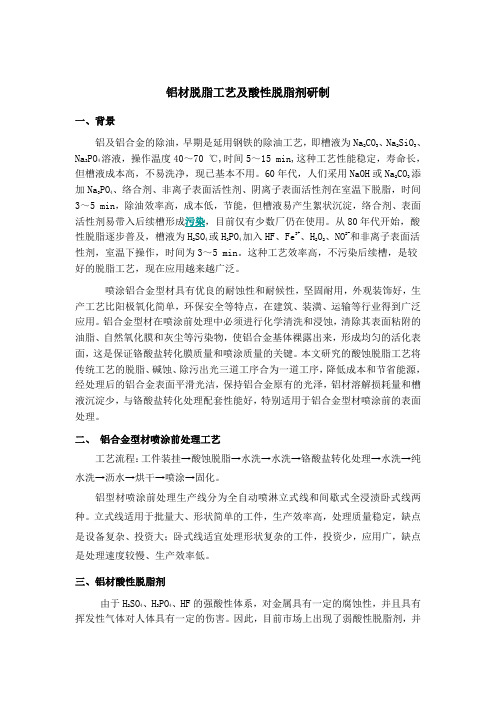
铝材脱脂工艺及酸性脱脂剂研制一、背景铝及铝合金的除油,早期是延用钢铁的除油工艺,即槽液为Na2CO3、Na2SiO3、Na3PO4溶液,操作温度40~70 ℃,时间5~15 min,这种工艺性能稳定,寿命长,但槽液成本高,不易洗净,现已基本不用。
60年代,人们采用NaOH或Na2CO3添加Na3PO4、络合剂、非离子表面活性剂、阴离子表面活性剂在室温下脱脂,时间3~5 min,除油效率高,成本低,节能,但槽液易产生絮状沉淀,络合剂、表面活性剂易带入后续槽形成污染,目前仅有少数厂仍在使用。
从80年代开始,酸性脱脂逐步普及,槽液为H2SO4或H3PO4加入HF、Fe3+、H2O2、NO2-和非离子表面活性剂,室温下操作,时间为3~5 min。
这种工艺效率高,不污染后续槽,是较好的脱脂工艺,现在应用越来越广泛。
喷涂铝合金型材具有优良的耐蚀性和耐候性,坚固耐用,外观装饰好,生产工艺比阳极氧化简单,环保安全等特点,在建筑、装潢、运输等行业得到广泛应用。
铝合金型材在喷涂前处理中必须进行化学清洗和浸蚀,清除其表面粘附的油脂、自然氧化膜和灰尘等污染物,使铝合金基体裸露出来,形成均匀的活化表面,这是保证铬酸盐转化膜质量和喷涂质量的关键。
本文研究的酸蚀脱脂工艺将传统工艺的脱脂、碱蚀、除污出光三道工序合为一道工序,降低成本和节省能源,经处理后的铝合金表面平滑光洁,保持铝合金原有的光泽,铝材溶解损耗量和槽液沉淀少,与铬酸盐转化处理配套性能好,特别适用于铝合金型材喷涂前的表面处理。
二、铝合金型材喷涂前处理工艺工艺流程:工件装挂→酸蚀脱脂→水洗→水洗→铬酸盐转化处理→水洗→纯水洗→沥水→烘干→喷涂→固化。
铝型材喷涂前处理生产线分为全自动喷淋立式线和间歇式全浸渍卧式线两种。
立式线适用于批量大、形状简单的工件,生产效率高,处理质量稳定,缺点是设备复杂、投资大;卧式线适宜处理形状复杂的工件,投资少,应用广,缺点是处理速度较慢、生产效率低。
铝合金材料新型表面处理工艺技术研究

铝合金材料新型表面处理工艺技术研究本文针对铝合金材料新型表面处理工艺新型技术,重点介绍了其工艺流程与参数控制,以及控制要点、常见问题与解决办法。
该工艺技术具有可调控的颜色调配技术、以及稳定的耐蚀性、耐候性等质量效果,并且符合国家绿色环保政策方针,对市场开发与生产实践具有很强的指导意义。
标签:铝合金材料;表面处理技术;电解着色1 前言本文重点对铝合金材料产品的新型表面处理工艺的各流程工序进行工艺优化或改进,并对常见缺陷及控制要点进行介绍。
2 实验方案2.1 材料本研究试验材料主要为6063合金挤压生产出的各种类型型材,合金成分见表1。
2.2 试验方法工艺流程试验优化路线方案见图1。
本研究对每一步工序进行不同程度地工艺优化,或降低成本、或适合环保发展需要等,每天现场生产试验记录各槽液工艺指标,所有产品进行性能测试,分析各指标对产品质量的影响,探索最佳工艺流程技术路线。
3 工艺流程优化与讨论3.1 预处理预处理工序主要包括脱脂、碱蚀、中和等三部分,属于阳极氧化前处理,预处理效果的好坏直接影响铝合金材料最终表面处理质量。
3.1.1 脱脂过去主要采用碱性脱脂工艺,该工艺需要消耗化学药剂,加装蒸汽管路加热消耗能源。
通过试验摸索总结,本研究对除油工艺进行酸性工艺改造,利用氧化槽废酸作为除油主要介质(浓度不低于120g/L),不再添加其他化学药剂,对比见表2。
酸性脱脂除油工艺处理方式能够达到铝材表面除油效果,对铝合金材料产品的光泽度也起到了促进作用,同时降低了化学药剂成本以及因常温处理节约能源消耗费用。
3.1.2 碱蚀在实验过程中,本课题研究了槽液不同铝离子浓度对型材表面暗纹率的影响,见图2。
当槽液铝离子浓度超过50g/L,铝型材表面会产生碱流痕致使中和后出现表面色斑缺陷,生产运行中要每天分析槽液铝离子浓度指标、严格控制铝离子浓度在50g/L以下,一旦超出就必须更换部分或全部槽液降低铝离子浓度。
本课题同时研究了碱蚀后水洗对型材表面质量的影响,通过实验总结出:碱蚀后第一道水洗温度应保持在35±2℃,水洗时间及空中滴水时间控制在1~3s,能够有效防止铝型材表面出现色斑现象。
铝及铝合金前处理工艺

铝及铝合金前处理工艺1.本工艺适用于铝及其合金的磷化处理,处理后的膜层与各种涂装层(油漆、塑粉等)有极强的附着力,经本工艺处理后的工件所形成的膜层有较强的抗蚀性能,与涂装层组合后能大幅度提高工件的整体抗腐蚀性能。
2.铝材在喷涂前处理中必须进行化学清洗和浸蚀,清除其表面粘附的油脂、自然氧化膜和灰尘等污染物,使铝合金基体裸露出来,形成均匀的活化表面,这是保证转化膜质量和喷涂质量的关键.3.工艺流程:工件装挂→酸脱→水洗→磷化处理→水洗→烘干.4.主要设备设备名称:酸脱槽,水洗槽,磷化槽;内衬要求:PVC ;加热设施:0℃左右。
5.工艺条件5.1铝脱Yj-1360酸脱剂25~50 g/L 温度常温时间5~20min5。
2磷化Yj-6104磷化剂25~50g/L 氧化剂5~15点温度5~40℃时间5-20min 注:槽液配制方法很简单,先在槽中加入约一半体积的水,然后加入Yj—1360 50Kg 或Yj-6104 50Kg,再加足量水。
6。
工艺操作说明6。
1 预检: 零件表面不应有胶类、漆类、铝屑、砂粒、毛刺等缺陷。
6。
2 酸脱: 将工件浸入酸脱液中脱脂,为了加快脱脂速度可晃动工件.检验标准:目视检查,经酸脱液处理后铝合金表面露出金属本色,平整光亮,油污和自然氧化膜全部除净,水洗后水膜连续、完整,表面完全润湿,不挂水珠,无黑色挂灰和过腐蚀现象.6.3 水洗:将工件在水中清洗干净。
6。
4 磷化:将工件浸入磷化液中进行磷化,为了磷化膜的均匀可上下移动工件。
6.5 水洗: 将磷化后的零件用流水清洗干净,零件内不能有未清洗的磷化液。
7。
注意事项7。
1 热处理和焊接件:工件经过热处理或焊接后表面形成油污烧结的焦化物,延长脱脂时间或加大脱脂液浓度可彻底除净。
7.2 零件的绑扎:7.2.1 绑扎用的材料宜选用铝线,禁止使用铜线和镀锌线,可用退去锌层的铁线。
7。
2。
2 稍大的单件绑扎好,尽可能绑在离零件边沿最近的孔眼中,以减少对工件表面的影响。
- 1、下载文档前请自行甄别文档内容的完整性,平台不提供额外的编辑、内容补充、找答案等附加服务。
- 2、"仅部分预览"的文档,不可在线预览部分如存在完整性等问题,可反馈申请退款(可完整预览的文档不适用该条件!)。
- 3、如文档侵犯您的权益,请联系客服反馈,我们会尽快为您处理(人工客服工作时间:9:00-18:30)。
chinainfo.gif (3898 bytes)材料保护MATERIALS PROTECTION1999年 第32卷 第2期 No.2vol.32 1999铝及铝合金酸性脱脂工艺研究毕 艳 谢蕴丹 李 捷 李鑫庆 摘 要 研究了铝及铝合金在室温条件下的脱脂工艺,槽液以15%的硫酸为主,加入少量的高价金属离子、氧化剂、表面活性剂等,脱脂效率高,槽液成本低,寿命长,对不锈钢设备腐蚀小。
关键词 铝合金 酸性脱脂1 前 言 铝及铝合金的除油,早期是延用钢铁的除油工艺,即槽液为Na2CO3、Na2SiO3、Na3PO4溶液,操作温度40~70 ℃,时间5~15 min,这种工艺性能稳定,寿命长,但槽液成本高,不易洗净,现已基本不用。
60年代,人们采用NaOH或Na2CO3添加Na3PO4、络合剂、非离子表面活性剂、阴离子表面活性剂在室温下脱脂,时间3~5 min,除油效率高,成本低,节能,但槽液易产生絮状沉淀,络合剂、表面活性剂易带入后续槽形成污染,目前仅有少数厂仍在使用。
从80年代开始,酸性脱脂逐步普及,槽液为H2SO4或H3PO4加入HF、Fe3+、H2O2、NO-2和非离子表面活性剂,室温下操作,时间为3~5 min。
这种工艺效率高,不污染后续槽,是较好的脱脂工艺,现在应用越来越广泛。
本研究以硫酸为基液,加特制的脱脂剂,在室温条件下,勿需机械搅拌等辅助,即可获得良好的脱脂效果。
该脱脂剂含氧化剂、表面活性剂、高价金属离子等成分,对铝金属有弱浸蚀能力,可长期使用,脱脂性能稳定可靠。
本工艺特别适用于铝型材的阳极氧化处理,槽液可以取自阳极氧化废酸,成本较低,并可以防止油污量大时油污布满液面、将油污带入后序槽的危险。
本文研究了脱脂剂含量、温度、时间及游离酸浓度对铝合金表面清洗效果的影响。
2 实验材料制备 (1) 试片的规格及预处理 选用工业纯铝作标准试片,其规格为50 mm×50 mm×(1~2) mm。
将试片在30%的HNO3溶液中脱脂,水洗,4%的NaOH溶液腐蚀,水洗,30%HNO3中和、出光,热风吹干。
经此处理后,试片表面原有的油污和自然氧化皮被除净,从而使每个试片的表面状态均匀一致。
(2) 人造工业油污的配制 将工业凡士林、20#、30#机油混合,加热到120 ℃,使固体物完全熔化,搅拌均匀,冷却到室温,加入3%食盐水和细砂,搅匀备用。
3 实验方法及步骤 将准备好的铝试片浸入人造工业油污中静置1 h,取出后垂直悬挂于空气中老化24 h,再用自来水沸煮3 min,除去试片表面的浮油,吹干,油污涂覆量应控制在0.08~0.19 g/dm2。
把上述涂覆油污的试片垂直放置于脱脂溶液中浸泡,不施加机械搅拌进行脱脂处理,水洗,热风吹干,待试片冷却至室温后,用分析天平准确称重,重量为W1。
再将试片浸入三氯乙烷中,在室温下不断摇动试片,浸泡3 min,将试片上的残余油污完全洗净。
吹干,准确称重,重量为W2。
试片的两次重量差(W1-W2)即为残余油量,计算试片单位面积的残余油量,就可比较脱脂溶液的脱脂性能,单位面积的残余油量愈小,脱脂性能愈佳。
4 实验结果与讨论 酸性脱脂剂主要由无机酸、氧化剂、高价金属离子及表面活性剂等成分组成。
其中,无机酸可以是H2SO4、H3PO4、HF、亚磷酸、硼酸等。
H2SO4对铝合金有弱浸蚀能力,能润湿整个金属表面,使自然氧化膜溶解,油污松动。
高价金属离子一般选用Fe3+,一般以硫酸铁、硝酸铁等铁盐形式加入,以加速铝的腐蚀,铁离子可以在铝表面发生置换反应,形成微电池,使铝表面产生微量氢气,将油污带出铝表面;同时,铁离子还可以抑制脱脂液对不锈钢设备的腐蚀。
氧化剂主要是H2O2或NO-2(如NaNO2)等,作为Fe3+的稳定剂,将还原产生的二价铁离子氧化成为三阶铁离子,并起到Fe3+类似的功能。
由于亚硝酸盐在酸性溶液中容易释放出NO x有毒气体,所以最好使用H2O2作为氧化剂。
加入表面活性剂可以提高铝合金表面的润湿性,降低油污的附着力,使油污乳化均匀地分散在脱脂液中,在酸性脱脂液中,选择耐酸性强的非离子或阴离子表面活性剂如长链脂肪醇聚氧乙烯醚、烷基酚聚氧乙烯醚、烷基二甲基胺氧化物为最佳。
4.1 脱脂剂用量的影响 脱脂剂用量对残余油量的影响见图1。
由图可见,脱脂剂的添加范围应为20~30 ml/L,最佳为25 ml/L,如果用量低于20 ml/L,脱脂剂中各有效成分含量不足,在上述工艺条件下,不能有效溶解自然氧化膜,油污不能完全松动,随着脱脂剂含量的添加,残余油污迅速减少。
脱脂剂含量达到25 ml/L时,自然氧化膜即能完全溶解,油污绝大部分得到松动脱除,继续增加脱脂剂的含量,残余油量几乎不变,说明含量25 ml/L以后继续添加脱脂剂只会增加物料消耗,不能进一步改善脱脂效果。
17.gif (1650 bytes) 图1 脱脂剂用量对残余油量的影响(35 ℃,5 min)4.2 温度的影响 铝及铝合金能在相当宽的温度范围内进行脱脂,使用适当的温度有利于保证脱脂性能的稳定和脱脂效果的可靠性。
温度过低时,脱脂液对金属氧化物的溶解能力相对较弱,提高脱脂剂浓度并不能显著提高其清洗能力,而使脱脂时间拖得过长,通常温度每提高10 ℃,化学反应速度增加1倍,所以提高温度,有助于提高脱脂液对铝的浸蚀能力和表面活性剂的乳化能力,并降低油污的粘度,使油污迅速离开金属表面。
一般来说,温度愈高,脱脂效果愈佳。
但是,温度太高会增加能量消耗,使脱脂剂对金属的腐蚀太强,产生局部过腐蚀,如变色、雪花斑、点蚀等。
如果温度超过表面活性剂的浊点,脱脂剂的乳化能力显著下降,脱脂效果反而变差。
同时,温度太高槽液会产生酸雾,腐蚀车间设备,并促使脱脂液中的Fe3+水解和沉淀,污染槽液,增加物料消耗。
因此,脱脂槽液的温度必须适当,应从除油效果、基体腐蚀、能量消耗、操作条件等多方面因素考虑。
图2显示了脱脂温度对残余油量的影响,脱脂剂用量25 ml/L,处理时间5 min。
结果表明,脱脂温度控制在35 ℃为最佳。
18-1.gif (1520 bytes) 图2 温度对残余油量的影响4.3 处理时间的影响 铝及铝合金表面有一层自然氧化膜,附有油污、铝屑泥沙汗水等杂质。
氧化膜的溶解速度取决于Al2O3和酸反应的速度及铝离子的扩散速度,并与酸的浓度和操作温度有关,增加脱脂处理的时间,有利于提高脱脂效果。
但是,处理时间太长,会使整个生产工艺过程过长,降低生产效率。
图3显示了处理时间对残余油量的影响。
结果表明,在35 ℃时,适宜的脱脂时间为5~7min。
18-2.gif (1731 bytes) 图3 脱脂时间对残余油量的影响(35 ℃,用量25 ml/L)4.4 游离酸浓度的影响 为了提高脱脂效率,在酸性脱脂工艺中常采用混合酸如H2SO4+H3PO4,H2SO4+HF等,所以一般不用某种酸的每升克数来表示酸的浓度,而是取一定量的脱脂液,用1 mol/L的NaOH溶液中和滴定,用滴定至中性时NaOH溶液的消耗量来表示脱脂剂中游离酸的浓度。
NaOH溶液的消耗量愈大,游离酸的浓度愈高,其关系符合当量定律。
本研究取5 ml脱脂液,用0.967 1 mol/L的NaOH溶液滴定,脱脂剂25 ml/L,温度35 ℃,处理时间5 min。
消耗NaOH溶液的毫升数与残余油量的关系见表。
表消耗NaOH的体积3.90 5.4510.4516.2521.7026.6036.60(ml)残余含油量30.4726.9611.4910.43 6.120.47 2.42(mg/dm2) 从表可以看出,游离酸大于26.6点时,残余油量极少,而且变化趋于平缓,这时酸的浓度与15%的H2SO4相当,而常用硫酸阳极氧化槽液即为15%的H2SO4,所以酸性脱脂液可以采用废旧的阳极氧化槽液配制,从而大大降低酸性脱脂的成本。
5 结 论 本文研究的酸性脱脂剂在含油污的铝及铝合金制品表面清洗工艺中具有特别的优点,在常温下能保持其浸蚀能力,对各种铝制品都有极好的清洗效果。
脱脂液能允许铝离子有极高的含量,去污能力有良好的耐久性。
本脱脂剂能抑制酸对不锈钢设备的腐蚀,保证清洗设备的使用寿命。
本脱脂工艺适用于铝及铝合金的阳极氧化、化学氧化、电镀、涂漆等工艺的前处理,特别是铝型材的阳极氧化处理,可以缩短碱腐蚀时间,使基体在碱腐蚀后保持较高的金属光泽。
对后续槽液不会产生不良影响。
脱脂槽液采用阳极氧化废硫酸配制,减少了废酸的环保处理和排放,降低了生产成本。
本文研究的酸性脱脂工艺规范如下: H2SO4100~180 g/L 脱脂剂20~30 ml/L 温 度20~40 ℃ 时 间3~7 min作者单位:武汉材料保护研究所(430030) (收稿日期 1998-11-05 责任编辑 魏兆军)铝及铝合金酸性脱脂工艺研究作者:毕艳, 谢蕴丹, 李捷, 李鑫庆作者单位:武汉材料保护研究所,430030刊名:材料保护英文刊名:MATERIALS PROTECTION年,卷(期):1999,32(2)引用次数:2次1.期刊论文张华.ZHANG Hua铝合金型材阳极氧化前酸处理工艺-电镀与精饰2009,31(10)讨论了铝合金型材阳极氧化前处理中常用的碱腐蚀工艺的不足.为解决碱腐蚀工艺的不足,研究前处理中用酸腐蚀而不用碱腐蚀,探讨了其中各组分作用和工艺参数的影响,对铝合金型材阳极氧化前处理中的酸性脱脂工艺加以改善,并对其特点和应用进行了阐述.1.蒙文坚铝合金型材喷涂前的酸蚀脱脂工艺[期刊论文]-轻合金加工技术 2006(07)2.李凝.江雄知.朱华平铝及铝合金化学着黄红色探讨[期刊论文]-桂林工学院学报 2003(02)本文链接:/Periodical_clbh199902008.aspx下载时间:2010年3月2日。