精馏
第三章 精馏

*
(3-8)
当操作压强不高时,气相仍遵循道尔顿分 压定律,式(3-7)可改写为
pyA x A y A x B y A ( 1 x A ) pyB x B y B x A ( 1 y A )x A
x y 1 ( 1) x
(5-12)
(3 - 11)
例3-2 由表3-3数据,求算苯-甲苯的相对 挥发度、平均相对挥发度及气液两相平衡 组成。
精馏是气液两相间的传质过程,传质是 以两相达到平衡为极限的。在分析和解 决精馏操作中所涉及的问题时,常以溶 液的气液相平衡关系为基础。
§3.1 双组分溶液的气液相平衡
3.1.1理想溶液 : 溶液中不同组分的分子间 作用力和相同分子的分子间作用力完全相 等的溶液.即 AA BB AB
图3-4 具有正偏差的非理想溶液的p-x相图
正偏差很大的体系
(a)T-x(y) 图
(b)
x-y图
图3-5 乙醇-水体系的气液相平衡组成图
负偏差很大的体系
(a)T-x(y) 图
(b)
x - y图
图4-6 硝酸-水体系的气液平衡组成图
4.1.3 相对挥发度
气液平衡关系除用相图表示之外还可用相对挥 发度来表示。 纯液体的挥发度通常指液体在一定温度下的饱 和蒸汽压 由于双组分溶液中一组分的蒸气压受另一组分 存在的影响,故溶液中各组分的蒸汽压比纯组 分的低,溶液中的挥发度可用它在蒸汽气中的 分压 pi 和与其成平衡的液相中的摩尔分数 xi 来表示。
表3-5 由平均相对挥发度计算所得苯-甲苯气液相平衡组成
T
xA yA
0
C
80.1 1.00 1.00
精馏

蒸 馏概述1.什么叫蒸馏?蒸馏操作的依据是什么?有何特点?答:蒸馏是分离液体混合物的单元操作。
利用混和物中各组分间挥发性不同的性质,通过加入或去除热量的方法,使混合物形成气液两相,并让他们相互接触进行质量传递,致使易挥发组分在气相中增浓,难挥发组分在液相中增浓,实现混合物的分离,这种操作统称为蒸馏。
由此可见,蒸馏分离的依据是混和物中各组分的挥发度不同。
分离的条件是必须造成气液两相系统。
蒸馏操作具有以下特点:①通过蒸馏操作,可以直接获得所需要的产品,因此蒸馏操作流程较简单。
②蒸馏分离的使用范围广,它不仅可以分离液体混合物,而且也可以分离气体混合物或固体混合物。
例如,可以将空气加压液化或将脂肪酸混合物加热熔化并减压,以建立气液两相系统,用蒸馏方法进行分离。
③在蒸馏中由于要产生大量的气相和液相,因此需消耗大量的能量。
或者为建立气液两相系统,通常有高压、真空、高温或低温等条件,也会带来技术问题等,这是不易采用蒸馏分离某些物系的原因。
2.蒸馏和精馏有何区别?答:蒸馏是这种单元操作的统称,精馏是其中一类,具体地说蒸馏按其操作方式可分为简单蒸馏、平衡蒸馏、精馏和特殊精馏等。
简单蒸馏和平衡是适用于易分离分离物系或分离要求不高的场合;精馏适用于难分离物系或对分离要求高的场合;特殊精馏适用于普通精馏难以分离或无法分离的系统。
工业生产中以精馏的应用最为广泛。
蒸馏和精馏的根本区别是精馏具有回流,因此将精馏称为具有回流的蒸馏。
可见蒸馏和精馏既有共性又有区别。
3.如何选定蒸馏操作压强?答:操作压强对物系的相平衡及蒸馏操作经济等都有影响,压强是由经济衡算或比较来加以确定的。
但是简而言之,蒸馏按其操作压强可分为常压蒸馏、减压蒸馏和加压蒸馏。
工业生产中多采用常压蒸馏。
对在常压下物系的沸点较高,或在高温下易发生分解、聚合等现象的物系(即热敏性物系),常用减压蒸馏。
对常压下物系的沸点在室温以下的混合物或为气态混合物,则采用加压蒸馏。
精馏的分类及精馏塔相关知识

• 2、常用的精馏塔有哪些结构形式呢? 对精馏过程来说,精馏设备是使过程得以进 行的重要条件。性能良好的精馏设备,为精馏过 程的进行创造了良好的条件。它直接影响到生产 装置的产品质量、生产能力、产品的收率、消耗 定额、三废处理以及环境保护等方面。 常用的精馏塔型式有填料塔和板式塔,填料 塔有拉西环填料塔、鲍尔环填料塔、鞍型填料塔、 波纹填料塔、丝网填料塔、丝网波纹填料塔等。 丝网波纹填料塔因其在保持高传质效率的前提下, 降低了造价,也越来越受到青睐。对于甲醇来说 予塔采用这种塔型的为数不少。
• 贮槽;另一部分送至塔底部的蒸发釜(再沸器) 加热气化。蒸发釜中产生的蒸气自塔底逐层上升, 使蒸气中易挥发组分逐渐增浓,然后进入塔顶分 凝器。一部分蒸气在分凝器中冷凝,所得的液体 送回塔顶作为回流;其余部分蒸气或者作为气相 产品直接引出,或者进入冷凝冷却器,将未冷凝 的蒸气全部冷凝,冷凝液流至产品贮槽。 • 这种把原料液不断地加入塔内,又从塔顶和塔釜 连续不断地采出的过程,就称为连续精馏。 • 4、怎样合理地选择精馏塔的操作条件? 精馏塔的操作条件主要是指温度、压力。一 般地说,主要是根据物料的性质,原料的组成, 对产品纯度的要求,设备材料的来源,工厂生产 的规模等具体情况,选择合理的操作条件。例如
• 8、什么是萃取精馏? 在被分离的混合物中加入萃取剂,萃取剂的 存在能使被分离混合物的组分间的相对挥发度增 大。精馏时,其在各板上基本保持恒定的浓度, 而且从精馏塔的塔釜排除,这样的操作称为萃取 精馏。 萃取剂的选择原则: (1)萃取剂的选择性要大。被分离组分在 萃取剂中相对挥发度的大小称为萃取剂的选择性。 被分离组分在萃取剂中相对挥发度增大的多,分 离就容易,也就是选择的萃取剂选择性大。选择 性是选择萃取剂最主要的依据。因为选择性的大 小也就是决定了被分离组分中轻重关键组分分离 的难易程度。因此塔板数的多少、回流
第六篇 精馏技术

第六篇精馏技术一、基本概念1.塔在化工生产中的作用A、实现气相和液相或液相和液相间传质的设备.B、在塔设备中主要完成精馏、吸收、解吸、萃取、工业气体的冷凝与回收等单元过程。
2.蒸馏利用互溶液体混合物中各个组分沸点不同而分离成较纯组分的一种操作。
目的是分离液体混合物。
3.蒸馏的分类简单蒸馏、精馏、特殊蒸馏。
(1)简单蒸馏将液体加热汽化,再将蒸汽引入冷凝的操作称之。
简单蒸馏是一个间歇操作过程.将一批原料液加入蒸馏釜中,在恒压下加热至沸腾,使液体不断汽化,产生的蒸汽冷凝后为顶部产物,其中易挥发组分较为富集。
- 62 -版权所有翻印必二、精馏利用混合物中各组分挥发能力的差异,通过液相和气相的回流,使气、液两相逆向多级接触,在热能驱动下,使得易挥发组分(轻组分)不断从液相往气相中转移,而难挥发组分却由气相向液相中迁移,使混合物得到不断分离,称该过程为精馏。
该过程中,传热、传质过程同时进行。
精馏是应用最广的一种蒸馏。
1.精馏原理:(1)精馏过程如图示,原料自塔的中部适当位置连续加入塔内,将塔分为两段,上段为精馏段,不含进料,下段含进料板为提留段。
塔顶设有冷凝器,将塔顶蒸汽冷凝为液体。
冷凝液的一部分回入塔顶,称为液相回流。
其余作为塔顶产品连续排出,塔底部装有再沸器以加热液体使之部分汽化产生蒸汽从塔底提供气相回流。
余下的液体作为塔底产品(残液)连续排出。
由加热釜或重沸器产生的蒸汽从塔底上升,回流液从塔顶流向塔底,原料液自加料板进入,在每层塔板上汽化,两相彼此接触,汽相被部分冷凝,液相则部分汽化,这样,汽化中易挥发组分的浓度越来越高,液相中难挥发组分越来越大,最后,将塔顶蒸汽冷凝,便得到符合要求的馏出液,将塔底液相引出。
便得到纯残液- 64 -版权所有翻印必(2)、精馏段:精馏段是指塔的加料位置以上部分塔体。
在精馏段,气相在上升的过程中,气相轻组分不断得到精制,在气相中不断地增浓,在塔顶获高浓度的轻组分产品。
塔的上半部分完成了蒸汽的精制,因而称为精馏段。
精馏的过程及连续精馏流程
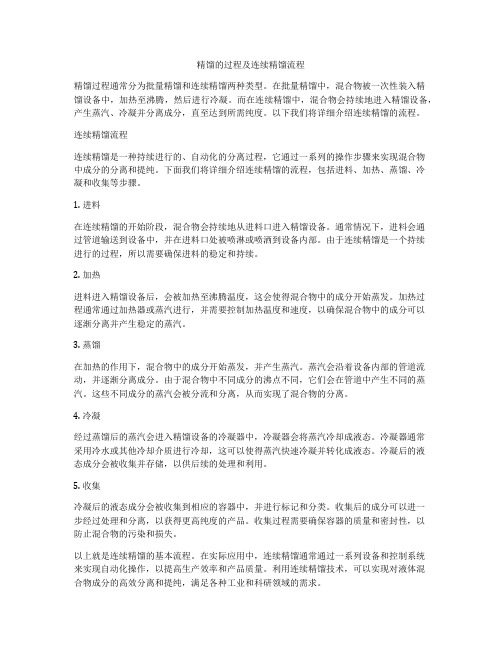
精馏的过程及连续精馏流程精馏过程通常分为批量精馏和连续精馏两种类型。
在批量精馏中,混合物被一次性装入精馏设备中,加热至沸腾,然后进行冷凝。
而在连续精馏中,混合物会持续地进入精馏设备,产生蒸汽、冷凝并分离成分,直至达到所需纯度。
以下我们将详细介绍连续精馏的流程。
连续精馏流程连续精馏是一种持续进行的、自动化的分离过程,它通过一系列的操作步骤来实现混合物中成分的分离和提纯。
下面我们将详细介绍连续精馏的流程,包括进料、加热、蒸馏、冷凝和收集等步骤。
1. 进料在连续精馏的开始阶段,混合物会持续地从进料口进入精馏设备。
通常情况下,进料会通过管道输送到设备中,并在进料口处被喷淋或喷洒到设备内部。
由于连续精馏是一个持续进行的过程,所以需要确保进料的稳定和持续。
2. 加热进料进入精馏设备后,会被加热至沸腾温度,这会使得混合物中的成分开始蒸发。
加热过程通常通过加热器或蒸汽进行,并需要控制加热温度和速度,以确保混合物中的成分可以逐渐分离并产生稳定的蒸汽。
3. 蒸馏在加热的作用下,混合物中的成分开始蒸发,并产生蒸汽。
蒸汽会沿着设备内部的管道流动,并逐渐分离成分。
由于混合物中不同成分的沸点不同,它们会在管道中产生不同的蒸汽。
这些不同成分的蒸汽会被分流和分离,从而实现了混合物的分离。
4. 冷凝经过蒸馏后的蒸汽会进入精馏设备的冷凝器中,冷凝器会将蒸汽冷却成液态。
冷凝器通常采用冷水或其他冷却介质进行冷却,这可以使得蒸汽快速冷凝并转化成液态。
冷凝后的液态成分会被收集并存储,以供后续的处理和利用。
5. 收集冷凝后的液态成分会被收集到相应的容器中,并进行标记和分类。
收集后的成分可以进一步经过处理和分离,以获得更高纯度的产品。
收集过程需要确保容器的质量和密封性,以防止混合物的污染和损失。
以上就是连续精馏的基本流程。
在实际应用中,连续精馏通常通过一系列设备和控制系统来实现自动化操作,以提高生产效率和产品质量。
利用连续精馏技术,可以实现对液体混合物成分的高效分离和提纯,满足各种工业和科研领域的需求。
精馏原理和流程

1-4精馏原理和流程1.掌握的内容:精馏分离过程原理及分析2.重点:精馏原理、精馏装置作用3.难点:精馏原理,部分气化和部分冷凝在实际精馏操作中有机结合的过程。
1.4.1 精馏原理精馏原理是根据图1-7所示的t-x-y图,在一定的压力下,通过多次部分气化和多次部分冷凝使混合液得以分离,以分别获得接近纯态的组分。
理论上多次部分气化在液相中可获得高纯度的难挥发组分,多次部分冷凝在气相中可获得高纯度的易挥发组分,但因产生大量中间组分而使产品量极少,且设备庞大。
工业生产中的精馏过程是在精馏塔中将部分气化过程和部分冷凝过程有机结合而实现操作的。
1.4.2 精馏装置流程一、精馏装置流程典型的精馏设备是连续精馏装置,包括精馏塔、冷凝器、再沸器等,如图1-8所示。
用于精馏的塔设备有两种,即板式塔和填料塔,但常采用的是板式塔。
连续精馏操作中,原料液连续送入精馏塔内,同时从塔顶和塔底连续得到产品(馏出液、釜残液),所以是一种定态操作过程。
二、精馏装置的作用精馏塔以加料板为界分为两段,精馏段和提馏段。
1.精馏段的作用加料板以上的塔段为精馏段,其作用是逐板增浓上升气相中易挥发组分的浓度。
2.提馏段的作用包括加料板在内的以下塔板为提馏段,其作用逐板提取下降的液相中易挥发组分。
3.塔板的作用塔板是供气液两相进行传质和传热的场所。
每一块塔板上气液两相进行双向传质,只要有足够的塔板数,就可以将混合液分离成两个较纯净的组分。
4.再沸器的作用其作用是提供一定流量的上升蒸气流。
5.冷凝器的作用其作用是提供塔顶液相产品并保证有适当的液相回流。
回流主要补充塔板上易挥发组分的浓度,是精馏连续定态进行的必要条件。
精馏是一种利用回流使混合液得到高纯度分离的蒸馏方法。
1-5两组分连续精馏的计算1.掌握的内容:(1)精馏塔物料衡算的应用。
(2)操作线方程和q线方程及其在x-y图上的作法和应用。
(3)理论板和实际板数的确定(逐板计算法和图解法)、塔高和塔径的计算。
精馏基本知识

精馏原理和流程3.3.1精馏原理精馏:把液体混合物进行多次部分气化,同时又把产生的蒸气多次部分冷凝,使混合物分离为所要求组分的操作过程称为精馏。
一、全部气化或全部冷凝设在1个大气压下,苯~甲苯混合液的温度为,其状况以A点表示,将此混合液加热,当温度到达(J点),液体开始沸腾,所产生的蒸气组成为(如D点),与成平衡,而且> ,当继续加热,且不从物系中取出物料,使其温度升高到(E点),这时物系内,汽液两相共存,液相的组成为(F点),蒸气相的组成为与成平衡的(G点),且> 。
若再升高温度达到(H点),液相终于完全消失,而在液相消失之前,其组成为(C点)。
这时蒸气量与最初的混合液量相等,蒸气组成为,并与混合液的最初组成相同。
倘再加热到H点以上,蒸气组成为过热蒸气,温度升高而组成不变的为。
自J点向上至H点的前阶段,称为部分气化过程,若加热到H点或H点以上则称全部汽化过程,反之当自H点开始进行冷凝、则至J点以前的阶段称为部分冷凝过程,至J点及J点以下称为全部冷凝过程。
部分汽化和部分冷凝过程实际上是混合液分离过程。
二、部分汽化、部分冷凝全部汽化、全部冷凝与部分汽化、部分冷凝的区别:(1)不从物系中取出物料,(2)温度范围不同。
部分汽化:将混合液自A点加热到B点,使其在B点温度下部分汽化,这时混合液分成汽液两相,气相浓度为,液相为(< ),汽液两相分开后、再将饱和液体单独加热到C点,在温度下部分气化,这时又出现新的平衡或得的液相及与之平衡的气相,最终可得易挥发组分苯含量很低的液相,即可获得近似于纯净的甲苯。
部分冷凝:将上述蒸气分离出来冷凝至,即经部分冷凝至E点,可以得到浓度为的汽相及液相,与成平衡> ,依次类推、最后可得较近于纯净的气态苯。
三、一部分气化、部分冷凝将液体进行一次部分气化,部分冷凝,只能起到部分分离的作用,因此这种方法只适用于要求粗分或初步加工的场合。
显然,要使混合物中的组分得到几乎完全的分离,必须进行多次部分气化和部分冷凝的操作过程。
精馏培训讲义PPT课件

目录
• 精馏技术简介 • 精馏流程与设备 • 精馏操作与控制 • 精馏分离效率与能耗分析 • 精馏安全与环保 • 精馏案例分析与实践
01 精馏技术简介
精馏的定义与原理
精馏的定义
精馏是一种利用混合物中各组分 挥发度的不同,通过加热、冷凝 、分馏等操作将液体混合物进行 分离的物理过程。
回收率
表示实际产品中目标组分 的比例,数值越高,目标 组分的回收效果越好。
热力学效率
反映精馏过程热力学有效 性的指标,数值越高,热 力学效率越高。
能耗分析的方法与意义
能耗分析方法
通过测量和计算精馏过程中的各种能 耗,如加热、冷却、压缩等,分析能 耗的分布和影响因素。
能耗分析意义
有助于优化精馏过程,降低能耗,提 高经济效益和环境可持续性。
精馏设备中的搅拌器、 泵等机械设备可能导致 夹击、割伤等事故。应 保持设备清洁,定期维 护保养,确保安全防护 装置完好。
精馏区域可能存在电气 安全隐患,如潮湿、腐 蚀等。应采用防爆、防 水等电气设备和电缆, 定期检查电气线路和设 备。
精馏过程的环保要求与处理方法
01 总结词
02 废气处理
03 废水处理
填料
填充在塔体内,增加接触面积 ,促进传热和传质。
塔板
设置在塔体内,形成不同的汽 液分离区域。
进料口和出料口
控制原料和产品的进入和流出 。
辅助设备
热源
提供加热所需的热量。
冷源
用于冷却回流液和产品。
泵
输送原料和产品。
仪表
监测温度、压力等参数。
精馏流程的优化与改进
控制进料速度和温度
调整进料速度和温度,提高分离效果。
04 噪声控制
- 1、下载文档前请自行甄别文档内容的完整性,平台不提供额外的编辑、内容补充、找答案等附加服务。
- 2、"仅部分预览"的文档,不可在线预览部分如存在完整性等问题,可反馈申请退款(可完整预览的文档不适用该条件!)。
- 3、如文档侵犯您的权益,请联系客服反馈,我们会尽快为您处理(人工客服工作时间:9:00-18:30)。
R 1 yn+1 = xn + xD R +1 R +1
= ym+1 L + qF W xm xW L + qF W L + qF W
17
多晶硅生产技术
18
13
多晶硅生产技术
进料热状况 冷液体 饱和液体 气液混合物 饱和蒸气
进料的焓IF I F< I L I F= I L IL< IF < IV I F= I V
q值
>1
1 0<q<1 0
过热蒸气
q=
IF> IL
<0
IV -I F 将1kmol进料变为保护蒸气所需的热量 IV -I L 原料液的千摩尔汽化热
IV -I F L-L = IV -I L F
IV -I F 将1kmol进料变为保护蒸气所需的热量 q= IV -I L 原料液的千摩尔汽化热 12
多晶硅生产技术
L=L+qF
提馏段操作线方程 :
L W ym+1 = xm xW L W L W
L + qF W = ym+1 xm xW L + qF W L + qF W
6
多晶硅生产技术
进料板以上称为精馏段 —— 精制汽相中的易挥发组分。
进料板以下(包括进料板)称为提馏段
—— 料
—— 富含易挥发组分。
塔底产品称为釜液
板式塔
7
釜液
—— 富含难挥发组分。
多晶硅生产技术
2、两组分连续精馏的计算 (1) 理论板的概念及恒摩尔流假定 所谓理论板是指离开这种板的气液两相互成平衡,而且塔 板上的液相组成也可视为均勾。 恒摩尔气流
Ⅲ)提馏段操作线方程
L = V +W
+WxW Lxm = V ym+1
L W = ym+1 xm xW L W L W
11
多晶硅生产技术
(3) 进料热状况的影响 Ⅰ)进料板上的物料衡算和热量衡算
F +V +L = V + L
FI F +V IV +LI L =VIV + LI L
14
多晶硅生产技术
Ⅱ)精馏塔的进料热状态
15
多晶硅生产技术
(4)理论板层数的求法
Ⅰ)逐板计算法
R 1 yn+1 = xn + xD R +1 R +1
= ym+1
L + qF W xm xW L + qF W L + qF W
16
多晶硅生产技术
(4)理论板层数的求法
Ⅱ)图解法
V1 =V2 =
恒摩尔液流
=Vn V
΄ V1΄ V2
΄ Vm V΄
L1 =L2 =
=Ln L
8
L΄1 L΄2
L΄m L΄
多晶硅生产技术
(2) 物料衡算和操作线方程 Ⅰ)全塔物料衡算
F=D+W F xF =D xD + W xW
DxD 塔顶易挥发组分回收率= 100% FxF
多晶硅生产技术
精馏
陈玉伟
1
多晶硅生产技术
蒸馏
2
多晶硅生产技术
简单蒸 馏
3
多晶硅生产技术
4
多晶硅生产技术
简单特点:
① 操作过程是一动态过程; ②瞬时蒸气与釜中液体处于平衡状态;
③易挥发组分更多地传递到气相中去,釜液温度不断升高;
④产品与釜液组成随时间而改变(降低)。
5
多晶硅生产技术
1、精馏原理
W 1-xW 塔底难挥发组分回收率= 100% F 1 xF
9
多晶硅生产技术
Ⅱ)精馏段操作线方程
V = L+ D
Vyn+1 = Lxn + DxD
1 D yn+1 = xn + xD L +1 L +1 D D
L
R 1 yn+1 = xn + xD R +1 R +1
10
多晶硅生产技术