炼钢
炼钢生产过程以及流程图详解(全)
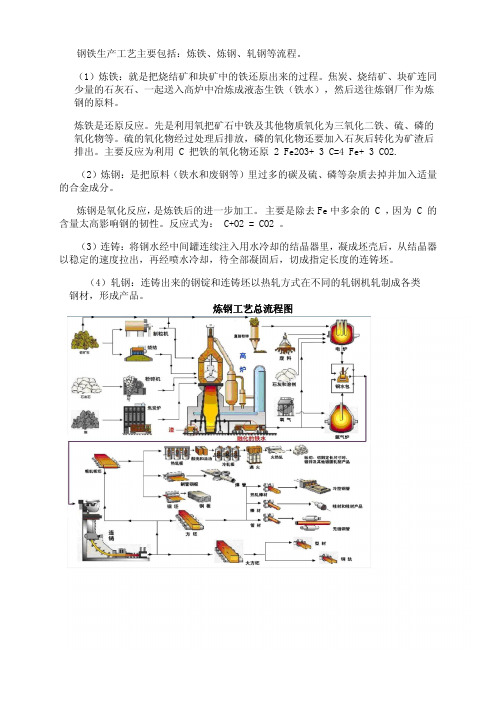
钢铁生产工艺主要包括:炼铁、炼钢、轧钢等流程。
(1)炼铁:就是把烧结矿和块矿中的铁还原出来的过程。
焦炭、烧结矿、块矿连同少量的石灰石、一起送入高炉中冶炼成液态生铁(铁水),然后送往炼钢厂作为炼钢的原料。
炼铁是还原反应。
先是利用氧把矿石中铁及其他物质氧化为三氧化二铁、硫、磷的氧化物等。
硫的氧化物经过处理后排放,磷的氧化物还要加入石灰后转化为矿渣后排出。
主要反应为利用 C 把铁的氧化物还原 2 Fe2O3+ 3 C=4 Fe+ 3 CO2.(2)炼钢:是把原料(铁水和废钢等)里过多的碳及硫、磷等杂质去掉并加入适量的合金成分。
炼钢是氧化反应,是炼铁后的进一步加工。
主要是除去Fe中多余的 C ,因为 C 的含量太高影响钢的韧性。
反应式为: C+O2 = CO2 。
(3)连铸:将钢水经中间罐连续注入用水冷却的结晶器里,凝成坯壳后,从结晶器以稳定的速度拉出,再经喷水冷却,待全部凝固后,切成指定长度的连铸坯。
(4)轧钢:连铸出来的钢锭和连铸坯以热轧方式在不同的轧钢机轧制成各类 钢材,形成产品。
炼钢工艺总流程图炼焦生产流程:炼焦作业是将焦煤经混合,破碎后加入炼焦炉内经干馏后产生热焦碳及粗焦炉气之制程。
烧结生产流程:烧结作业系将粉铁矿,各类助熔剂及细焦炭经由混拌、造粒后,经由布料系统加入烧结机,由点火炉点燃细焦炭,经由抽气风车抽风完成烧结反应,高热之烧结矿经破碎冷却、筛选后,送往高炉作为冶炼铁水之主要原料。
还原气体,还原铁矿石,产生熔融铁水与熔渣之炼铁制程。
转炉生产流程:炼钢厂先将熔铣送前处理站作脱硫脱磷处理,经转炉吹炼后,再依订单钢种特性及品质需求,送二次精炼处理站(RH真空脱气处理站、Ladle Injection盛桶吹射处理站、VOD真空吹氧脱碳处理站、STN搅拌站等)进行各种处理,调整钢液成份,最后送大钢胚及扁钢胚连续铸造机,浇铸成红热钢胚半成品,经检验、研磨或烧除表面缺陷,或直接送下游轧制成条钢、线材、钢板、钢卷及钢片等成品。
炼钢的基本流程

炼钢的基本流程
炼钢的基本流程主要包括以下步骤:
1. 炼焦:炼焦作业是将焦煤经混合、破碎后加入炼焦炉内经干馏后产生热焦碳及粗焦炉气。
2. 高炉生产:高炉作业是将铁矿石、焦炭及助熔剂由高炉顶部加入炉内,再由炉下部鼓风嘴鼓入高温热风,产生还原气体,还原铁矿石,产生熔融铁水与熔渣。
3. 炼钢:炼钢厂先将熔铣送前处理站作脱硫脱磷处理,经转炉吹炼后,再依订单钢种特性及品质需求,送二次精炼处理站(RH真空脱气处理站、Ladle Injection盛桶吹射处理站、VOD真空吹氧脱碳处理站、STN搅拌站等)进行各种处理,调整钢液成份,最后送大钢胚及扁钢胚连续铸造机,浇铸成红热钢胚半成品,经检验、研磨或烧除表面缺陷,或直接送下游轧制成条钢、线材、钢板、钢卷及钢片等成品。
一般要加热到再结晶温度以上才进行轧制。
炼钢的基本流程需要经过多道复杂的工序,而且需要严格控制温度和化学成分等参数,才能生产出高质量的钢材。
炼钢学
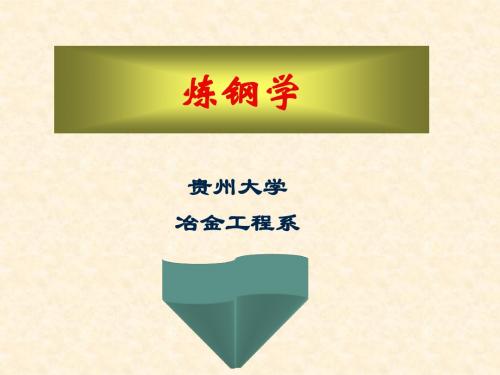
外来夹杂是指冶炼和浇铸过程中,带入钢
液中的炉渣和耐火材料以及钢液被大气氧
化所形成的氧化物。
内生夹杂包括:
脱氧时的脱氧产物;
钢液温度下降时,硫、氧、氮等杂质元素溶解 度下降而以非金属夹杂形式出现的生成物; 凝固过程中因溶解度降低、偏析而发生反应的 产物; 固态钢相变溶解度变化生成的产物。 钢中大部分内生夹杂是在脱氧和凝固过程中产 生的。
蚀性。硫还是连铸坯中偏析最为严重的元素。
不同钢种对硫含量有严格的规定:
非合金钢中普通质量级钢[S]≤0.045%
优质级钢 [S]≤0.035%,
特殊质量级钢
有的钢种要求如管线钢
[S]≤0.025%
[S]≤0.005%,甚至更
低。
有些钢种,如易切削钢硫则作为合金元素加入,
要求[S]=0.08%-0.20%。
钢中加入适量的铝,可生成稳定的AlN,能够
压抑Fe4N生成和析出,不仅改善钢的时效性,还可以阻止奥氏体晶粒的长大。 Nhomakorabea可以作为合
金元素起到细化晶粒的作用.在冶炼铬钢,镍 铬系钢或铬锰系等高合金钢时,加入适量的氮, 能够改善塑性和高温加工性能。
五、钢中的夹杂
钢中非金属夹杂按来源分可以分成外来夹 杂和内生夹杂。
广泛;
用途不同对钢的性能要求也不同,从而对钢
的生产也提出了不同的要求。
石油、化工、航天航空、交通运输、 农业、国防等许多重要的领域均需要各 种类型的大量钢材,我们的日常生活更 离不开钢。
总之,钢材仍将是21世纪用途最 广的结构材料和最主要功能材料。
炼钢技术的发展(1)
最早出现的炼钢方法是1740年出现的 坩埚法,它是将生铁和废铁装入由石墨 和粘土制成的坩埚内,用火焰加热熔化 炉料,之后将熔化的炉料浇成钢锭。此 法几乎无杂质元素的氧化反应。
炼钢工艺流程图
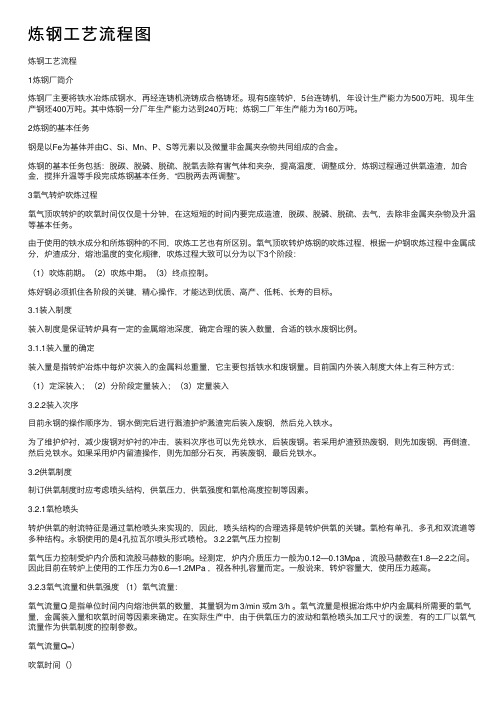
炼钢⼯艺流程图炼钢⼯艺流程1炼钢⼚简介炼钢⼚主要将铁⽔冶炼成钢⽔,再经连铸机浇铸成合格铸坯。
现有5座转炉,5台连铸机,年设计⽣产能⼒为500万吨,现年⽣产钢坯400万吨。
其中炼钢⼀分⼚年⽣产能⼒达到240万吨;炼钢⼆⼚年⽣产能⼒为160万吨。
2炼钢的基本任务钢是以Fe为基体并由C、Si、Mn、P、S等元素以及微量⾮⾦属夹杂物共同组成的合⾦。
炼钢的基本任务包括:脱碳、脱磷、脱硫、脱氧去除有害⽓体和夹杂,提⾼温度,调整成分,炼钢过程通过供氧造渣,加合⾦,搅拌升温等⼿段完成炼钢基本任务,“四脱两去两调整”。
3氧⽓转炉吹炼过程氧⽓顶吹转炉的吹氧时间仅仅是⼗分钟,在这短短的时间内要完成造渣,脱碳、脱磷、脱硫、去⽓,去除⾮⾦属夹杂物及升温等基本任务。
由于使⽤的铁⽔成分和所炼钢种的不同,吹炼⼯艺也有所区别。
氧⽓顶吹转炉炼钢的吹炼过程,根据⼀炉钢吹炼过程中⾦属成分,炉渣成分,熔池温度的变化规律,吹炼过程⼤致可以分为以下3个阶段:(1)吹炼前期。
(2)吹炼中期。
(3)终点控制。
炼好钢必须抓住各阶段的关键,精⼼操作,才能达到优质、⾼产、低耗、长寿的⽬标。
3.1装⼊制度装⼊制度是保证转炉具有⼀定的⾦属熔池深度,确定合理的装⼊数量,合适的铁⽔废钢⽐例。
3.1.1装⼊量的确定装⼊量是指转炉冶炼中每炉次装⼊的⾦属料总重量,它主要包括铁⽔和废钢量。
⽬前国内外装⼊制度⼤体上有三种⽅式:(1)定深装⼊;(2)分阶段定量装⼊;(3)定量装⼊3.2.2装⼊次序⽬前永钢的操作顺序为,钢⽔倒完后进⾏溅渣护炉溅渣完后装⼊废钢,然后兑⼊铁⽔。
为了维护炉衬,减少废钢对炉衬的冲击,装料次序也可以先兑铁⽔,后装废钢。
若采⽤炉渣预热废钢,则先加废钢,再倒渣,然后兑铁⽔。
如果采⽤炉内留渣操作,则先加部分⽯灰,再装废钢,最后兑铁⽔。
3.2供氧制度制订供氧制度时应考虑喷头结构,供氧压⼒,供氧强度和氧枪⾼度控制等因素。
3.2.1氧枪喷头转炉供氧的射流特征是通过氧枪喷头来实现的,因此,喷头结构的合理选择是转炉供氧的关键。
炼钢工艺流程
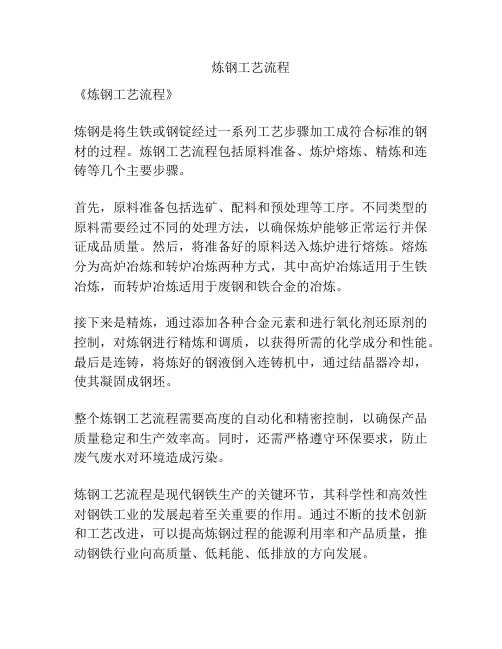
炼钢工艺流程
《炼钢工艺流程》
炼钢是将生铁或钢锭经过一系列工艺步骤加工成符合标准的钢材的过程。
炼钢工艺流程包括原料准备、炼炉熔炼、精炼和连铸等几个主要步骤。
首先,原料准备包括选矿、配料和预处理等工序。
不同类型的原料需要经过不同的处理方法,以确保炼炉能够正常运行并保证成品质量。
然后,将准备好的原料送入炼炉进行熔炼。
熔炼分为高炉冶炼和转炉冶炼两种方式,其中高炉冶炼适用于生铁冶炼,而转炉冶炼适用于废钢和铁合金的冶炼。
接下来是精炼,通过添加各种合金元素和进行氧化剂还原剂的控制,对炼钢进行精炼和调质,以获得所需的化学成分和性能。
最后是连铸,将炼好的钢液倒入连铸机中,通过结晶器冷却,使其凝固成钢坯。
整个炼钢工艺流程需要高度的自动化和精密控制,以确保产品质量稳定和生产效率高。
同时,还需严格遵守环保要求,防止废气废水对环境造成污染。
炼钢工艺流程是现代钢铁生产的关键环节,其科学性和高效性对钢铁工业的发展起着至关重要的作用。
通过不断的技术创新和工艺改进,可以提高炼钢过程的能源利用率和产品质量,推动钢铁行业向高质量、低耗能、低排放的方向发展。
炼钢8步工艺流程

炼钢8步工艺流程
《炼钢8步工艺流程》
炼钢是一项重要的冶金工艺,用于生产高质量的钢材。
它需要经过一系列复杂的步骤才能完成。
以下是炼钢的典型8步工艺流程:
1. 预处理:原料是铁矿石和废钢,它们需要进行预处理,去除杂质和控制化学成分。
2. 熔炼:预处理后的原料被放入大型高炉中,通过高温熔炼达到融化状态。
3. 脱硫:在熔炼过程中,加入脱硫剂,以去除铁水中的硫和磷等杂质。
4. 脱氧:通过加入脱氧剂,去除铁水中的氧化物,提高钢的质量。
5. 合金化:根据生产需求,加入合金元素,如铬、镍和钛等,来调整钢的化学成分。
6. 精炼:在精炼炉中,对合金成分进行精密调整,以确保钢的质量和性能。
7. 结晶器:通过冷却处理,控制钢材的晶粒结构,使其获得理想的物理性能。
8. 成型:将高纯度的钢水倒入模具中,冷却后得到成品。
以上8步工艺流程是炼钢的基本工艺,每一步都至关重要,需要高度的技术和经验支持。
通过严格执行这些步骤,可以生产出高品质的钢材,满足各种工业领域的需求。
炼钢基本原理(课堂PPT)
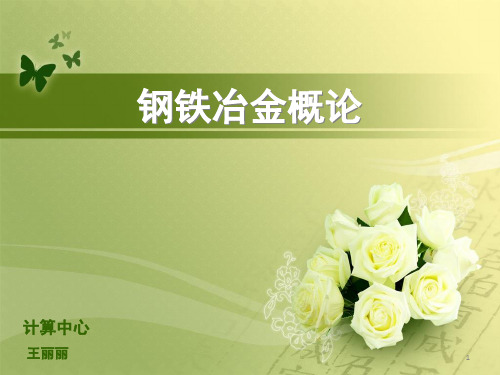
B、工具钢,包括碳素工具钢和合金工具钢及高速钢。
碳素工具钢的硬度主要以含碳量的高低来调整 (0.65%≤[C]≤1.30%),为了提高钢的综合性能,有 的钢中加入0.35%~0.60%的锰。
合金工具钢不仅含有很高碳,有的高达2%,而且含有较 高的铬(达13%)、钨(达9%)、钼、钒等合金元素, 这类钢主要用于各式模具。
13
废钢应清洁干燥不得混有泥沙,水泥,耐火材料,爆炸 物和易燃易爆品以及有毒物品等。废钢的硫、磷含量均 不大于0.050%。不同性质的废钢分类存放。
高速工具钢除含有较高的碳(1%左右)外,还含有很高 的钨(有的高达19%)和铬、钒、钼等合金元素,具有 较好的赤热硬性。
7
C、特殊性能钢,指的是具有特殊化学性能或力学性能的 钢,如轴承钢、不锈钢、弹簧钢、高温合金钢等。
轴承钢是指用于制造各种环境中工作的各类轴承圈和滚动 体的钢,这类钢含碳1%左右,含铬最高不超过1.65%,要 求具有高而均匀的硬度和耐磨性,内部组织和化学成分均 匀,夹杂物和碳化物的数量及分布要求高。
10
铁水成分:
Si:铁水Si含量过高,会因石灰消耗量的增大而使渣量 过大,易产生喷溅并加剧对炉衬的侵蚀,影响石灰熔 化,从而影响脱磷、脱硫。如果铁水Si含量过低,则 不易成渣,对脱磷、脱硫也不利,因此通常铁水中的 硅含量为0.30%-0.70%为宜。
Mn:锰是发热元素,铁水中Mn氧化后形成的MnO能 有效促进石灰溶解,加快成渣,减少助熔剂的用量和 炉衬侵蚀。同时铁水含Mn高,终点钢中余锰高,从而 可以减少合金化时所需的锰铁合金,有利提高钢水纯 净度。
B、合金钢是指钢中除含有硅和锰作为合金元素或脱氧元
素外,还含有其他合金元素如铬、镍、钼、钛、钒、铜、
钢的冶炼方法

钢的冶炼方法钢是一种重要的金属材料,广泛应用于各个领域。
其冶炼方法主要有两种:炼铁法和电弧炉法。
一、炼铁法1. 原料准备:炼钢的原料主要是铁矿石、焦炭和石灰石。
其中,铁矿石是主要原料,焦炭作为还原剂,而石灰石则用于脱硫。
2. 烧结:将铁精粉和焦粉混合后在高温下进行加压成型,形成硬块。
这些硬块称为“球团”。
3. 熔融还原:将球团放入高温的高炉中,在高温下加入空气或氧化剂使焦碳发生氧化反应,产生一定量的一氧化碳和二氧化碳。
这些气体与球团中的铁氧化物反应生成纯铁,并排除非金属杂质。
4. 合金添加:在得到纯铁后,需要添加其他元素来制造不同种类的钢。
常见的合金元素包括锰、镍、钒等。
5. 脱硫处理:如果需要制造高品质的钢,需要进行脱硫处理。
将石灰石投入高炉中,与产生的硫化物反应生成硫酸钙,从而去除硫。
6. 炼钢:将纯铁和合金元素加入到特殊的容器中,在高温下进行混合和搅拌,使其充分融合。
这样就得到了所需的钢。
二、电弧炉法1. 原料准备:电弧炉法所用的原料与炼铁法相似,包括废旧钢材、废旧车辆和船只等。
2. 加料:将废旧钢材等原料放入电弧炉中,并加入适量的生铁或铁合金。
3. 熔化:通过高温电弧加热,使原料快速融化,并不断搅拌混合。
4. 合金添加:在得到一定质量的钢液后,需要添加其他元素来制造不同种类的钢。
常见的合金元素包括锰、镍、钒等。
5. 调质处理:通过控制温度和搅拌速度等参数来调整钢液成分和结构,从而达到所需性能。
6. 出钢:将炉中的钢液倒入铸模中,冷却后得到所需的钢材。
总之,炼铁法和电弧炉法都是制造钢材的重要方法。
二者在原料、工艺和成本等方面存在差异,但都能够满足不同领域对于钢材性能的要求。
- 1、下载文档前请自行甄别文档内容的完整性,平台不提供额外的编辑、内容补充、找答案等附加服务。
- 2、"仅部分预览"的文档,不可在线预览部分如存在完整性等问题,可反馈申请退款(可完整预览的文档不适用该条件!)。
- 3、如文档侵犯您的权益,请联系客服反馈,我们会尽快为您处理(人工客服工作时间:9:00-18:30)。
炼钢脱硫反应
desulphurization in steelmaking
1 iangang tuoliu fanying 炼钢脱硫反应(desulphurization in Steel- making)在炼钢以及钢液炉外精炼过程中脱除有害杂质硫的物理化学反应。
硫在钢凝固时成为硫化物析出在晶粒界上,如果硫化物是FeS,其熔点为1195℃,在轧钢时晶界熔化而钢破裂,称为“热脆”。
钢中加入锰后,析出的硫化物变为MnS,熔点提高到1530℃,热脆现象可以避免,但Mns在轧钢时沿轧向延伸,使钢材在横向上失去连续性。
对于条、棒类钢材的危害还不严重,但对于要求各个方向的性能均为良好的板、管类钢材,硫的危害就大了。
硫还恶化钢的韧性,图1为德国生产的管线用钢之含硫量随年代的变化,与之相对应,冲击韧性水平自然也随着时代而提高。
生产低硫钢要在高炉炼铁、铁水预处理、炼钢、钢液炉外精炼各个环节均进行认真的脱硫。
还要依据产品对硫的不同要求,对整个生产流程的脱硫操作进行最优化控制,以使脱硫成本达到最低。
200resesesesr-~es-下-----下----门尸-~一…飞一一一一-丁--一-了一--门150卜--卜一一-卜一一一卜一-寸一俘100卜一+一--卜一-十一一曰一J,..书丫…一嘴一一一」‟阵宝夔工工二亘~_ 0 1960 1965 1970 1975 1980 1985 I99() 1995 年份图1钢的硫含量和韧性的历史变化氧化渣的脱硫脱硫以在还原条件下进行最为有利,从以下各生产环节的硫分配比可以看出: 高炉铁水预处理顶吹转炉炉外精炼(%S)/〔写S〕.30~40 400~5005一8~1000 氧化熔炼操作的转炉炼钢过程中硫分配比最小。
然而碱性氧化渣也有脱硫能力。
对此可用炉渣离子理论清楚地说明。
根据离子理论,硫在渣中以52一形态存在,碱性氧化物分解成为02一和各种金属阳离子。
钢液中的硫吸收2个电子才能进入渣中成为52--,这是一个阴极反应。
为了保持电中性,同时要有一个释放电子的阳极反应同时发生: 阴极反应仁S〕+Ze二(S卜) 井业臀瑞攀澎豁笋。
l) 或者阴极反应[s〕+2e一(52一) 二哑嚷察下共华装界粤鑫(2) [S]+(02一)=〔O〕+(52一) 式(2)写成分子反应形式,得出〔S」+(CaO)=[O〕+(CaS)(3) 但这个写法不如离子反应写法的含意全面。
脱硫反应式(2)的平衡常数。
_色互兰二理也习凡一~蕊厂称言(4) 硫的平衡分配比;一鱼一。
兰之上当立卫面玩一面一凡一二荞舀亡死碗荔,(5,根据以上脱硫反应的特点,要想提高硫分配比,也就是增强脱硫效果,需要的基本条件有:( )增大渣一钢反应平衡常数K一。
Ks一m与温度成正比,即脱硫是放热反应,提高温度有利于脱硫。
(2)增大渣中O卜浓度。
碱性氧化物产生02一,所以增大炉渣碱度有利于脱硫。
(3)减小钢中氧活度,也就是说环原茶件右利千脱一门协井斌一硫,而氧化条件不利于脱硫。
(4)渣中(F eo)对脱硫有CS:。
在氧化熔炼中,钢液中的硫直接被氧化成50:而双重作用。
一方面,(Feo)产生Fe2+,它们是氧化性的去掉是不可能的,因为在炼钢条件下,硫对氧的亲和力标志,增大(Feo)使[%O〕增加,不利于脱硫;另一方比碳对氧的亲和力小得多。
只有进入渣中的硫,在铁离面,(F eo)又可分解产生0卜,对于低碱度渣,(FeO)的子的参与下,可能被氧化成气体而脱除,反应如下: 有利作用可更凸显一些。
实验室试验表明,纯氧化铁渣和钢液间硫分配比仍有3.6。
所以说,氧化渣有一定的…。
_ 脱硫能力。
(5)增大渣量有利于脱硫。
因为大渣量可以}、r_,//} 容纳较多的硫。
有些炼钢操作者为了确保钢中硫合格,50L\…一‟论多}//} 往往采取大渣量操作。
然而大渣量增加了石灰消耗,也芝!,\宋叼} 增加了铁的损失,恶化了传热条件,增大能量消耗。
所类4。
仁\让划)嘿黔七,} 以大渣量是一种不应提倡的操作。
暴j、s)民冬\} 金属成分对脱硫的影响从式(5)可以看出,增大30F环列、、刘金属中硫活度系数frs:可以增大硫分配比。
钢液中各{l乙./〕} 元素对f[s〕的影响是不同的,根据实验测定,增大fls〕ZOt,…se~尔一一亩~甲.谕一一翁的元素是B、C、si、Alj等,减小fls〕的元素有Ti、Mn、终渣《Feo丫% V等。
生铁中含有很多的碳和硅,所以炼铁时硫活度系图2硫的分布与终渣(Feo)的关系数比炼钢时高得多。
据计算,生铁中九〕二3一4,钢中f[s〕、1。
这就是说,使用同样的脱硫熔剂,对生铁脱硫“二3+、
二…QZ一、二。
…n卜、_二…。
2+、二。
_ 比对钢脱硫其效率要高3一4倍。
铁水预处理之所以成所以气化脱硫的比例随渣中氧化铁的增大而增大。
然为非常理想的脱硫方法,这也是原因之一。
而过高的氧化铁意味着铁耗增加,脱硫操作仍应以高还原渣的脱硫在电弧炉炼钢还原期和炉外精炼碱度渣脱硫为主。
特别是铁水预处理和炉外精炼的发时,用还原渣处理钢液,脱硫能力显著增大。
最常用的展,有效脱硫的方法更多了,气化脱硫并没有特别重要还原渣是白渣和铝酸钙渣,其典型成分(%)如下:的意义。
eaoA一203 510:Mgo eaFZ Feo Mno炉渣硫容量影响硫在渣钢间分配比的因素,除白渣60一“2一315~20<103一5镇。
.5簇0.4前面列举的各项外,由式(5)可以看出还有渣中硫和氧铝酸钙渣5。
一5540一45簇3簇。
·5离子的活度系数。
测定渣中组元活度比较困难,而且还原渣有很强的脱硫能力,硫分配比可达50一80或更孙一和yoz一要分别测量,使问题复杂化。
为了表示炉渣大。
(FeO)对脱硫有很大影响,(FeO)由O,89%降到一…‟一阳‟…一“一”“”“””‟“一‟“一…--一‟~‟ o·44%,硫分配比由62增大至。
87。
还原渣脱硫同时也合52(g)十(02一)一(52一)+音。
2。
) 进行钢液的脱氧,会使钢中si、Al等含量增加,它们也该反应的平衡常数寨与时脯际亩,罗习]Jj“明“外“…p岁f(s)(肠S) :s:+令仁51〕+:(eao)一(eas)+令(Zeao·5102)KS一,葵夏叹石不一一…一“…2…一习…一、一一、一一/…2、一一一-一一…厂。
2~(。
一) …旅…介等,氧化性气氛中是502,还原性气氛中是COS或上述反应平衡存在于PoZ<1『,MPa(1J6a…m)条件382 下。
当poZ>10一6MPa(10一、tm)时,渣中硫以S以一形式存在,气渣反应为1~.3~.,~,一、,一~。
一言52…·,+言02…g,+(O“一)一(50犷) 反应的平衡常数a(so誉一) a()户oZpsZ 参照上述定义法,导出炉渣的硫酸盐容量c叽的定义式: 。
…二a(o,一)(%S) C明2一一K八_。
、…书一之-一一气卜共气一“…L一g,Zf(s)一,彭2户鸳因渣中硫浓度不大,。
(so复一。
一。
(52一。
一。
(s,一f(s。
(%S) 对于表示炉渣脱硫能力来说,Cs和Cso4没有本质区别。
所不同的是测定它们时所用的气渣反应不同。
现在在一些手册中已收集了许多种渣的硫容量数据,便于为选择脱硫熔剂时所应用。
硫容量概念亦可用于渣一钢反应,由式(4)和式(5)得c‟s 一凡一粉一恶瑟凳(6) 式中C‟:和CS有一定比例关系,其比值就是渣钢反应和气渣反应平衡常数的比。
由式(6)可得出硫的分配比和硫容量有以下关系;__至丝翌_。
,细Ls一亡茹药一C产S瑞也就是说,要想有效脱硫,必须选用脱硫能力强(硫容量大)的渣,利用生铁中的C、Si提高硫活度,降低金属中的氧位。
脱硫反应的速率炼钢脱硫是渣一钢界面反应,反应包括3个环节:(l)钢液中硫向界面传质;(2)在界面上的化学反应;(3)硫在渣相内传质离开界面。
脱硫反应是电化学反应,在高温下进行得很快,不是脱硫速率的限制环节。
渣和钢两相中的传质均可能是速率控制环节。
根据一些人对钢液中硫的传质系数所作的测定,证明传质速率决定于界面上的流动速度。
流动速度越大,传质越快。
另外渣一钢界面反应和界面积大小有关,增大界面积的有效方法是使渣、钢乳化。
电弧炉还原渣下出钢时,增大钢流落差,加大渣、钢接触,可促进脱硫的进行。
钢液炉外精炼时,必须吹氢或用电磁搅拌,才能使渣子有效脱硫。
钢包喷吹脱硫粉剂,具有极大的反应面积,脱硫速率快,是有效的脱硫方法。