钢铁冶炼过程气体激光原位分析技术的应用
钢铁冶金废气处理分解课件

加强操作人员的培训和 管理,提高处理效果和 安全性。
05
钢铁冶金废气处理未来发展
技术发展趋势
高效过滤技术
利用高效过滤材料和设备,对废气中 的颗粒物进行过滤和去除,提高净化 效率。
活性炭吸附技术
利用活性炭的吸附性能,对废气中的 有害气体进行吸附和净化,实现废气 的减排和治理。
生物处理技术
利用微生物的代谢作用,对废气中的 有害物质进行降解和转化,实现废气 的生物净化。
正渗透技术
利用正渗透原理,使水分子通过半透膜,而有害气体被截留,从而 达到净化废气的目的。
03
钢铁冶金废气处理设备
燃烧炉
总结词
通过高温燃烧将废气中的有害物质转 化为无害物质。
适用范围
适用于处理含有可燃性有害物质的废 气,如挥发性有机物、硫氧化物等。
详细描述
燃烧炉是一种常见的废气处理设备, 通过提供高温环境,使废气中的有害 物质在氧气的作用下充分燃烧,生成 二氧化碳和水等无害物质。
技术特点
吸收塔处理效率较高,操作简便,但吸收剂的消耗和再生问题需要关 注。
吸附罐
总结词
利用吸附剂吸附废气中的有害物质。
适用范围
适用于处理低浓度、低流速的有害气体,如苯、甲苯等挥 发性有机物。
详细描述
吸附罐内部填充了特定的吸附剂,如活性炭、分子筛等, 通过物理吸附作用将废气中的有害物质吸附在吸附剂表面 ,从而达到净化废气的目的。
企业应积极与政府和社会合作,参与相关环保公益活动和技术交流 ,共同推动钢铁冶金废气处理技术的发展和应用。
THANKS。
技术特点
吸附罐具有处理效率高、能耗低等优点,但吸附剂的更换 和再生成本较高。
冷凝器
AOD精炼法分析

AOD精炼法分析
在冶炼阶段,熔融钢水首先被移入AOD炉中,并制造适当的温度和条件。
接下来,注入氩气,通过氩气的作用将一部分碳氧化成一氧化碳,达到提高熔融钢水中一氧化碳浓度的目的。
这些一氧化碳能够与含氧的金属氧化物反应,将其还原成金属形式。
在调整阶段,通过控制炉内的温度、压力和气氛等参数,来控制钢水中的氧化物含量。
同时,适量的氧气也被注入到炉内,以进一步改变钢水中非金属杂质的浓度。
在精炼阶段,氩气和氧气的注入将继续。
炉内的温度会进一步升高,从而促进金属间的反应。
此时,大部分的碳和其他非金属杂质已经被氧气氧化成气体形式,并通过喷嘴排出炉外。
这个阶段非常重要,因为它确保了最终产品的质量。
然而,AOD精炼法也存在一些问题。
首先,由于氧气和氩气的注入,炉内的温度升高,可能会导致一些金属蒸汽的生成。
这些金属蒸汽会通过排放系统释放到大气中,对环境造成影响。
其次,AOD精炼法的投资和运营成本较高,对于规模较小的钢铁企业可能难以负担。
总之,AOD精炼法是一种高效、低能耗的炼钢方法,为钢铁工业中非金属杂质的去除提供了有效的解决方案。
随着环保意识的提高,AOD精炼法在未来的发展中可能需要更多的技术改进,以减少对环境的影响,同时降低运营成本,使其更具竞争力。
铁合金冶炼过程中的气体分离与净化技术

铁合金冶炼过程中的气体分离与净化技术1. 背景铁合金的冶炼过程是钢铁工业的重要组成部分,其产品的质量和效率直接影响到整个产业链的性能在铁合金的冶炼过程中,气体的分离与净化是关键环节之一它不仅关系到产品的质量,还影响到生产效率和环境污染问题本文将详细分析铁合金冶炼过程中气体分离与净化的技术2. 铁合金冶炼过程铁合金的冶炼过程主要包括矿石的还原、熔炼、精炼和合金化等步骤在这个过程中,矿石经过还原反应转化为铁合金,同时产生大量的气体,如CO、CO2、N2等这些气体部分可以用于冶炼过程,部分则需要进行分离和净化3. 气体分离技术气体分离技术主要包括吸收法、吸附法、冷凝法和膜分离法等在铁合金冶炼过程中,吸收法和吸附法主要用于分离和净化CO和CO2,而冷凝法和膜分离法则用于分离和净化N2和其他惰性气体3.1 吸收法吸收法是通过溶剂的选择性溶解来实现气体的分离在铁合金冶炼过程中,常用的吸收剂有碱液和海水碱液主要用于吸收CO2,而海水则用于吸收CO吸收法简单易行,但需要大量的溶剂和能源消耗吸附法是利用吸附剂的选择性吸附来实现气体的分离在铁合金冶炼过程中,常用的吸附剂有活性炭和分子筛活性炭主要用于吸附CO,而分子筛则用于吸附CO2吸附法具有较高的分离效率和较低的能耗,但需要定期更换吸附剂3.3 冷凝法冷凝法是通过降低气体的温度使其冷凝来实现气体的分离在铁合金冶炼过程中,冷凝法主要用于分离和净化N2和其他惰性气体冷凝法简单易行,但需要大量的冷却能源3.4 膜分离法膜分离法是通过膜的选择性透过来实现气体的分离在铁合金冶炼过程中,膜分离法主要用于分离和净化N2和其他惰性气体膜分离法具有较高的分离效率和较低的能耗,但需要定期更换膜材料4. 气体净化技术气体净化技术主要包括燃烧法、吸收法和吸附法等在铁合金冶炼过程中,燃烧法主要用于净化CO,而吸收法和吸附法则用于净化CO2和N24.1 燃烧法燃烧法是通过氧化反应将有害气体转化为无害气体在铁合金冶炼过程中,燃烧法主要用于净化CO燃烧法简单易行,但需要大量的氧气和能源消耗吸收法是通过溶剂的选择性溶解来实现气体的分离在铁合金冶炼过程中,常用的吸收剂有碱液和海水碱液主要用于吸收CO2,而海水则用于吸收CO吸收法简单易行,但需要大量的溶剂和能源消耗4.3 吸附法吸附法是利用吸附剂的选择性吸附来实现气体的分离在铁合金冶炼过程中,常用的吸附剂有活性炭和分子筛活性炭主要用于吸附CO,而分子筛则用于吸附CO2吸附法具有较高的分离效率和较低的能耗,但需要定期更换吸附剂以上内容为本文的相关左右后续内容将详细分析各种技术的优缺点,以及在实际生产中的应用情况和效果5. 技术优缺点分析在铁合金冶炼过程中,各种气体分离与净化技术的优缺点如下:5.1 吸收法优点:操作简单,设备成本低,可以同时去除多种气体缺点:能耗较高,需要大量的溶剂,产生的废液需要处理5.2 吸附法优点:分离效率高,能耗较低,可以实现深度净化缺点:吸附剂需要定期更换,操作相对复杂优点:简单易行,能耗较低,可以实现大规模的气体分离缺点:对温度控制要求较高,冷却设备占地面积大5.4 膜分离法优点:分离效率高,能耗较低,可以实现连续运行缺点:膜材料需要定期更换,对压力要求较高6. 实际应用与效果在实际生产中,各种气体分离与净化技术都有广泛的应用,并且取得了良好的效果6.1 吸收法在铁合金冶炼过程中,吸收法主要用于去除CO2,取得了显著的效果例如,某铁合金生产企业采用碱液吸收法去除CO2,使得产品中的CO2含量降低了50%以上6.2 吸附法吸附法在铁合金冶炼过程中主要用于去除CO,取得了良好的效果例如,某铁合金生产企业采用活性炭吸附法去除CO,使得产品中的CO含量降低了80%以上冷凝法在铁合金冶炼过程中主要用于分离和净化N2和其他惰性气体,取得了良好的效果例如,某铁合金生产企业采用冷凝法分离和净化N2,使得产品中的N2含量降低了60%以上6.4 膜分离法膜分离法在铁合金冶炼过程中主要用于分离和净化N2和其他惰性气体,取得了良好的效果例如,某铁合金生产企业采用膜分离法分离和净化N2,使得产品中的N2含量降低了70%以上以上内容为本文的约60%左右后续内容将详细分析各种技术的经济性和环境影响,以及未来的发展趋势和挑战7. 经济性与环境影响在铁合金冶炼过程中,各种气体分离与净化技术的经济性和环境影响如下:7.1 吸收法经济性:设备投资较低,运行成本较高,主要取决于溶剂的消耗和废液的处理成本环境影响:废液处理对环境有一定影响,需要妥善处理以减少污染7.2 吸附法经济性:设备投资较高,运行成本较低,主要取决于吸附剂的更换频率和成本环境影响:吸附剂的更换会产生废弃物,需要妥善处理以减少环境污染7.3 冷凝法经济性:设备投资较低,运行成本较低,主要取决于冷却能源的消耗环境影响:冷却水的使用对水资源的消耗较大,需要考虑环境影响7.4 膜分离法经济性:设备投资较高,运行成本较低,主要取决于膜材料的更换频率和成本环境影响:膜材料的更换会产生废弃物,需要妥善处理以减少环境污染8. 发展趋势与挑战随着环境保护的日益重视和生产效率的要求提高,铁合金冶炼过程中的气体分离与净化技术面临着新的发展趋势和挑战8.1 技术创新为了提高分离效率和降低运行成本,气体分离与净化技术需要不断创新例如,开发新型吸收剂、吸附剂和膜材料,以提高分离效率和降低成本8.2 环保要求随着环保法规的日益严格,铁合金冶炼企业需要采取更加环保的气体分离与净化技术例如,采用零排放技术,减少废液的产生和处理8.3 节能减排为了降低能源消耗和减少温室气体排放,铁合金冶炼企业需要采用更加节能的气体分离与净化技术例如,利用可再生能源进行冷却和供电9. 结论铁合金冶炼过程中的气体分离与净化技术对于产品的质量和生产效率具有重要意义吸收法、吸附法、冷凝法和膜分离法等各种技术在实际生产中都有广泛应用,并且取得了良好的效果然而,各种技术都存在一定的优缺点,需要根据实际情况选择合适的方法同时,气体分离与净化技术面临着环保要求提高和节能减排的挑战,需要不断创新和改进以上内容为本文的全部内容后续无续写内容。
激光气体分析仪在钢铁企业烟气监测中的应用

2 激光气 体 分析 仪功 能及 应用
中的应用 , 极大地节约了人力物力 , 提高了效率 , 提 升了对钢铁企业的实时监测能力 ,在污染刚刚出现 的时候 , 即予 以预警和控制 , 提高环境保护的反应速
度 和效率 。 在 钢 铁 企业 的各 项 生产 环 节 中 , 烧结 、 球 团、 炼
总第 1 6 4期 2 0 1 6年 第 6 期
山西 冶 金
S HANXI ME TAL L U RGY
T 0 t a l l 6 4 No . 6, 2 0 1 6
DO I : 1 0 . 1 6 5 2 5 0 . c n k i . c n 1 4 - 1 1 6 7 / f. 2 0 1 6 . 0 6 . 4 2
作者简介 : 杜增 荣( 1 9 7 3 一) , 男, 从 事环境监 测 中空气和废 气
监测、 噪声监测 的研究工作。
2 0 1 6年第 6期
杜增荣 : 激光气体分析仪在钢铁企业 烟气监测 中的应用
或 离线 ( o fl i n e ) 考 核 。L a s I R T M 系统 快速 、 实 时原地 对 气体浓 度进 行监 测 , 检测 线性 达 到动 态 5级 ( 1 0 ,
铁厂烟 气测量 、 监 测方 面具有较强的 实用性 , 避免 了气体抽样测量带来的一些问题 。
关键词 : 排放 监测 环境保护 中图分类号 : 钢铁企业 气体分析仪 文章编号 : 1 6 7 2 — 1 1 5 2 【 2 0 1 6) 0 6 — 0 1 2 0 — 0 2 文献标识码 : A
2 . 1 激光气体分析仪的功能实现
光谱分析在金属冶炼中的应用

汇报人:可编辑 2024-01-06
目录
• 光谱分析简介 • 光谱分析在金属冶炼中的应用 • 光谱分析的优势与局限性 • 光谱分析技术的发展趋势 • 实际应用案例
01
光谱分析简介
光谱分析的定义
总结词
光谱分析是一种基于物质与电磁辐射 相互作用的测量方法,通过测量物质 发射或吸收光谱来分析其成分和结构 。
光谱分析的分类
总结词
光谱分析可以根据不同的分类标准进行分类,如根据光谱产生的机制可分为发射光谱法和吸收光谱法;根据光谱 的测量方式可分为直接测量法和间接测量法。
详细描述
发射光谱法是通过测量物质发射的光谱来进行分析的方法,而吸收光谱法则是通过测量物质吸收特定光波长后的 光谱来进行分析的方法。直接测量法是通过测量物质与光源直接相互作用后的光谱,而间接测量法则需要借助其 他介质或技术手段来测量光谱。
。
局限性
样品制备要求高
光谱分析对样品的制备 要求较高,需要将样品 研磨、混合均匀等处理
。
干扰因素多
光谱分析可能会受到基 体效应、光谱干扰等因 素的影响,导致分析结
果不准确。
仪器成本高
光谱分析仪器通常价格 较高,增加了应用成本
。
操作技术要求高
光谱分析需要专业的操 作人员和技术支持,以 保证分析结果的准确性
VS
智能决策支持
系统具备智能决策功能,能够根据历史数 据和算法预测金属的冶炼过程和产品质量 。
光谱数据库的建立与完善
数据共享与标准化
光谱数据库的建立和完善有助于实现数据共享和标准化,提高光谱分析的可比性和可靠 性。
数据库更新与维护
随着技术的进步和知识的更新,光谱数据库需要不断更新和维护,以确保其准确性和可 靠性。
钢铁冶金新工艺技术目录

钢铁冶金新工艺技术目录钢铁冶金是现代工业中应用最广泛的材料之一,其技术不断发展和创新,推动了钢铁行业的高效生产和质量提升。
下面是一份钢铁冶金新工艺技术目录。
一、高炉冶炼新技术1. 高效节能热风炉技术:采用高效燃烧器和余热回收装置,提高燃烧效率和热风温度,降低燃料消耗和排放。
2. 富氧预处理技术:通过对冶炼矿石进行富氧预处理,提高还原效率和高炉产能,减少煤耗和焦耗。
3. 燃料灰渣精煤技术:通过对燃料灰渣中的可燃物质进行精煤,提高燃烧效率和热量利用率,降低煤耗和废气排放。
二、转炉冶炼新技术1. 高效氧枪技术:采用高效氧枪和透氧技术,提高氧枪吹氧效率和转炉熔化过程中的氧气利用率,降低氧气消耗和炉渣中的氧化铁含量。
2. 喷吹粉煤技术:通过将粉煤喷吹到转炉中,在燃烧过程中释放高热值的挥发分,提高炉内温度和燃烧效率,减少焦耗和燃料消耗。
3. 渣液脱锰技术:通过添加适量的石灰和石膏等物质,控制转炉渣中的碱度和碳酸锰含量,降低转炉渣锰损失和锰冶炼成本。
三、连铸新技术1. 水模连铸技术:采用水模铸坯,提高结晶器冷却效果和铸坯的表面质量,降低铸坯变形和裂损率,提高铸坯质量和连铸效率。
2. 轧辊调整技术:通过轧辊调整系统自动化控制,实现辊型调整和轧件形状控制,提高轧件尺寸精度和表面质量,降低轧制能耗和加工成本。
3. 涂层技术:在连铸过程中,对铸坯和轧件表面进行涂层处理,减少表面氧化、脱碳和损伤,提高产品质量和附加值。
四、高温热处理新技术1. 连续退火技术:采用连续退火设备,对钢材进行高温退火处理,实现均匀结构和优良性能,提高钢材的塑性和韧性。
2. 淬火技术:采用先进的淬火设备和工艺,快速冷却钢材,形成细小、均匀的马氏体组织,提高钢材的硬度和耐磨性。
3. 氮化处理技术:通过将钢材置于含氮气氛中,在高温下进行氮化处理,提高钢材的表面硬度和耐腐蚀性。
五、环保技术1. 高效除尘技术:采用先进的除尘设备和技术,减少钢铁冶炼过程中的烟尘和废气排放,改善环境污染问题。
激光技术在冶金行业的应用

激光技术在冶金行业的应用引言冶金行业是指利用金属、非金属和合金等材料进行加工和熔炼的领域。
随着科技的不断发展,激光技术作为一项新兴的加工技术,逐渐在冶金行业中得到了广泛的应用。
本文将介绍激光技术在冶金行业中的应用,并探讨其优势和挑战。
1. 激光切割技术激光切割技术利用高能激光束将金属材料进行切割。
相比传统的切割方法,激光切割具有精度高、效率高和无损伤等优势。
在冶金行业中,激光切割技术广泛应用于金属板材的加工中,如剪切、切割和定型等。
激光切割技术的工作原理是通过将高能量的激光束聚焦在金属表面,使其局部区域加热并熔化,然后通过气体喷射将熔化的金属吹散。
由于激光束具有高聚焦性和高能量密度,激光切割可以在短时间内完成对金属材料的高精度切割,同时可以减少材料的损伤和变形。
2. 激光焊接技术激光焊接技术是利用激光束将金属材料的表面加热至熔点,使其熔化并与其他材料进行连接的技术。
在冶金行业中,激光焊接技术被广泛应用于金属材料的连接和修复中,如焊接管道、焊接接头和焊接构件等。
激光焊接技术具有热影响区小、焊缝质量高和焊接速度快等优势。
由于激光束具有高能量密度和高聚焦性,激光焊接可以在短时间内完成金属材料的焊接,并且可以减少热影响对材料的损伤。
然而,激光焊接技术也面临一些挑战,如焊缝的形貌控制、焊接参数的优化和焊接接头的质量检测等问题。
因此,在实际应用中,需要综合考虑各种因素并进行合理的优化,以确保激光焊接技术在冶金行业中的稳定和可靠性。
3. 激光表面处理技术激光表面处理技术是利用激光束对金属材料的表面进行加工和改性的技术。
在冶金行业中,激光表面处理技术被广泛应用于金属材料的清洗、去除氧化层和改善表面质量等方面。
激光表面处理技术具有高精度、高效率和无损伤等优势。
激光束的高能量密度可以加热金属表面并使其迅速蒸发,从而清除表面的杂质和氧化层。
此外,激光束的高聚焦性可以精确控制加工区域,从而改善金属材料的表面质量和性能。
电弧炉炼钢复合吹炼技术研究及应用
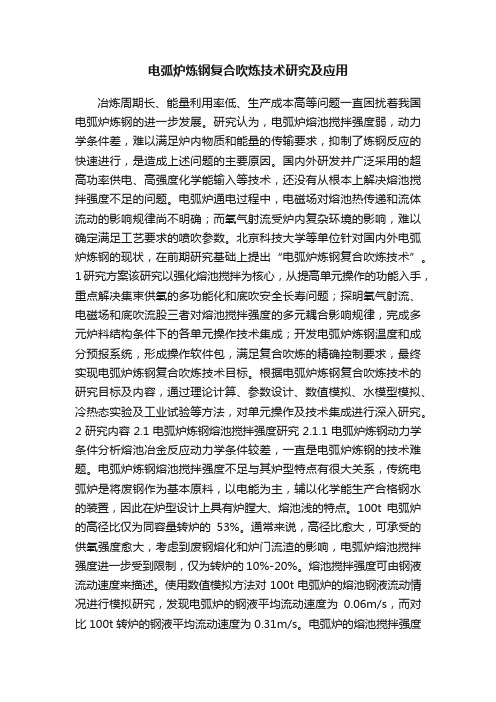
电弧炉炼钢复合吹炼技术研究及应用冶炼周期长、能量利用率低、生产成本高等问题一直困扰着我国电弧炉炼钢的进一步发展。
研究认为,电弧炉熔池搅拌强度弱,动力学条件差,难以满足炉内物质和能量的传输要求,抑制了炼钢反应的快速进行,是造成上述问题的主要原因。
国内外研发并广泛采用的超高功率供电、高强度化学能输入等技术,还没有从根本上解决熔池搅拌强度不足的问题。
电弧炉通电过程中,电磁场对熔池热传递和流体流动的影响规律尚不明确;而氧气射流受炉内复杂环境的影响,难以确定满足工艺要求的喷吹参数。
北京科技大学等单位针对国内外电弧炉炼钢的现状,在前期研究基础上提出“电弧炉炼钢复合吹炼技术”。
1研究方案该研究以强化熔池搅拌为核心,从提高单元操作的功能入手,重点解决集束供氧的多功能化和底吹安全长寿问题;探明氧气射流、电磁场和底吹流股三者对熔池搅拌强度的多元耦合影响规律,完成多元炉料结构条件下的各单元操作技术集成;开发电弧炉炼钢温度和成分预报系统,形成操作软件包,满足复合吹炼的精确控制要求,最终实现电弧炉炼钢复合吹炼技术目标。
根据电弧炉炼钢复合吹炼技术的研究目标及内容,通过理论计算、参数设计、数值模拟、水模型模拟、冷热态实验及工业试验等方法,对单元操作及技术集成进行深入研究。
2研究内容2.1电弧炉炼钢熔池搅拌强度研究2.1.1电弧炉炼钢动力学条件分析熔池冶金反应动力学条件较差,一直是电弧炉炼钢的技术难题。
电弧炉炼钢熔池搅拌强度不足与其炉型特点有很大关系,传统电弧炉是将废钢作为基本原料,以电能为主,辅以化学能生产合格钢水的装置,因此在炉型设计上具有炉膛大、熔池浅的特点。
100t电弧炉的高径比仅为同容量转炉的53%。
通常来说,高径比愈大,可承受的供氧强度愈大,考虑到废钢熔化和炉门流渣的影响,电弧炉熔池搅拌强度进一步受到限制,仅为转炉的10%-20%。
熔池搅拌强度可由钢液流动速度来描述。
使用数值模拟方法对100t电弧炉的熔池钢液流动情况进行模拟研究,发现电弧炉的钢液平均流动速度为0.06m/s,而对比100t转炉的钢液平均流动速度为0.31m/s。
- 1、下载文档前请自行甄别文档内容的完整性,平台不提供额外的编辑、内容补充、找答案等附加服务。
- 2、"仅部分预览"的文档,不可在线预览部分如存在完整性等问题,可反馈申请退款(可完整预览的文档不适用该条件!)。
- 3、如文档侵犯您的权益,请联系客服反馈,我们会尽快为您处理(人工客服工作时间:9:00-18:30)。
现代仪器(www 1moderni n strs 1org 1cn)二〇〇七年#第三期钢铁冶炼过程气体激光原位分析技术的应用邱历军 赵永平 酆 烽(济南钢铁集团股份有限公司燃气发电厂 济南 250101)摘 要 基于半导体激光吸收光谱技术的激光原位气体分析系统响应速度快且无需采样预处理装置,可较好地满足钢铁行业对过程气体的实时在线检测要求。
在转炉煤气回收系统应用中,激光原位气体分析系统的响应速度比采样气体分析系统快约20s ,从而可以多回收约418%的能源气。
关键词 半导体激光吸收光谱 转炉煤气 在线分析仪钢铁的冶炼过程实质上是原材料、燃料和成品的流转过程,在流转中伴随着大量气体产生,而在线检测分析这些过程气体是冶金工业生产工艺优化控制、安全和环保监控必不可少的关键技术之一,对降低能源消耗、保证生产安全等起着十分重要的作用。
从发展历程来看,气体检测技术经历人工取样分析、在线连续取样分析和实时原位分析三个阶段,其代表产品分别为人工采样的电化学分析仪,需配套采样预处理装置的红外气体分析仪、磁氧表以及可实现实时原位分析的激光气体分析仪。
其中人工采样分析方法因钢铁生产自动化程度的提高,已逐渐被在线分析方式取代。
本文对两种不同在线气体分析技术进行比较,并对聚光科技(杭州)有限公司研发生产的基于半导体激光吸收光谱(DLAS)技术的LGA 系列激光原位气体分析仪在冶金行业的应用作重点阐述。
图1 两种分析系统结构1 两种在线分析技术比较钢铁冶金行业对过程气体的分析方式主要分为连续shape -preser v i n g 采样分析和实时原位分析两种(见表1)。
连续采样分析系统主要包括复杂的采样预处理、分析仪表及仪表盘柜;实时原位分析系统主要包括安装在现场的发射、接收单元及安装在现场或仪控室的中央分析单元。
连续采样分析系统一般采用带预处理装置的红外气体分析仪或磁氧表,实时原位分析系统一般采用激光气体分析系统,其基本结构(见图1)。
激光原位气体分析系统直接安装在过程气体管道,管径相对位置的发射和接收单元通过发射和采集激光信号,并将光信号转化为电信号,通过电缆传输到中央分析仪器进行分析和输出。
整个分析系统无需复杂的采样和预处理系统,结构简单、无运动部件,解决在线采样气体分析系统的众多弊病〔1〕。
尽管原位气体分析系统具有上述性能优势,但是要满足原位测量,就需要解决被测环境中背景气体交叉干扰,被测环境中粉尘干扰和被测环境参数如温度、压力等变化干扰问题。
而DLAS 技术可以很好地解决上述难题,因此可以被广泛应用于过程气体原位分析。
与非分光红外气体分析技术相同,DLAS 技术也是一种吸收光谱技术,它利用B eer -La m bert 〔1〕关系来定量分析半导体激光能量被被测气体选择吸收产生的衰减来获得气体的浓度。
与传统非分光红外分析技术使用谱宽很宽且固定波长的红外光源不同,16二〇〇七年#第三期新技术应用表1 在线光谱分析系统比较指标LGA 系列激光原位气体分析系统在线采样气体分析系统预处理系统无需必需测量方法现场、连续、实时测量采样预处理后间断测量环境适应性恶劣环境适应能力强恒温、恒压、恒流、干燥及干净的气体响应速度快:仅取决于仪表响应时间,小于1s慢:为样品气传输和仪表响应时间总和准确性原位测量,气体信息不失真气体信息失真连续性连续测量间断测量:反吹时无法测量可靠性无运动器件,可靠性高较多运动部件,可靠性低介质干扰不受背景气体交叉干扰;自动修正粉尘及光学视窗污染干扰受背景气体的交叉干扰,无法定量修正粉尘及光学视窗污染干扰样气排放无样气排放,安全无污染有样气排放,危险有污染维护标定维护:1~4次/年;标定:1~2次/年维护:经常;标定:一个月2~3次运行费用无需备品备件;运行费用接近于零需要较多备品备件;年运行费用高DLAS 技术使用谱宽非常小(也就是单色性非常好)且波长可调谐的半导体激光器作为光源。
另外,DLAS 技术使用的单线光谱分析也使修正温度、压力变化等对测量的影响变得较容易〔2〕。
因此,DLAS 技术具有传统非分光红外分析技术无法实现的一些性能优点。
111 背景气体干扰分析非分光红外吸收技术使用的光源谱宽达10~100nm,其谱宽范围除包含被测气体吸收谱线外,还可能包含其他背景气体的吸收谱线,从而导致背景气体交叉干扰。
而半导体激光器发射的激光谱宽小于010001nm,是红外光源谱宽的1/106,远小于红外光源谱宽和被测气体单吸收谱线宽度(见图2),其频率调制扫描范围也仅包含被测气体单吸收谱线(半导体激光吸收光谱技术也因此被称为单线光谱技术),因此成功消除背景气体交叉干扰影响。
另外如果采用磁氧表的话,如果气体中含有其他成分的顺磁性气体,加上现场气体流量的变化、仪器的震动均会引起测量结果产生较大误差。
图2 /单线光谱0测量原理图112 粉尘和视窗污染分析非分光红外气体分析仪在分析粉尘含量较大的气体时,气体中的粉尘和被污染的光学元件会引起气室透光率的变化,而固定波长的光源又无法区别气体和粉尘的吸收,因此非分光红外气体分析仪无法自动修正粉尘对光学元件的污染影响。
而半导体激光的波长可以通过调制工作电流而被扫描,在一个激光波长扫描范围内使激光波长既扫描过有气体吸收的区域,也扫描过没有气体吸收的区域。
当波长位于有气体吸收区域时可测得包含气体和粉尘在内的总透光率T 总,当波长位于无气体吸收区域时可测得粉尘透光率T 粉尘,从而可准确获得被测气体的透光率T 气体=T 总/T 粉尘。
DLAS 技术通过上述激光波长扫描技术修正粉尘和视窗污染对测量的影响。
113 被测气体环境参数变化的影响被测气体环境参数)温度或压力发生变化通常导致谱线强度和展宽发生变化,对温度或压力信号不加修正就会影响测量结果。
由于DLAS 技术是对被测气体单一吸收谱线进行分析,可较容易地对温度、压力效应进行修正。
在高炉炼铁过程中,高炉炉顶煤气主要由N 2,O 2,CO ,CO 2及少量的H 2组成〔3〕。
LGA 系列激光气体分析系统通过输入4~20mA 的温度和压力信号,自动修正因被测气体环境参数变化导致谱线强度和展宽变化产生的干扰。
而非分光红外气体分析仪测量的是被测气体大量吸收谱线对光源信号衰减的平均效应,它受温度变化的影响较难被准确地修正。
如果被测混合气体中某一组分的在红外线波段内与待测成分有特征吸收峰重叠部分,那么就要对测量结果产生干扰,因此,在对钢铁生产过程气体的分析应用中,为保证非分光红外气体分析系统的测量准确性,一般在仪器前配备样气预处理器,对样气进行除尘、除水、保温、保压等处理。
由于红外气体分析仪对具有对称结构、无极性的双原子分子气体,例如O 2、H 2、N 2等,以及单原子气体例如H e 、N e 、Ar 等,在红外线波段内17现代仪器(www 1moderni n strs 1org 1cn)二〇〇七年#第三期Appli cati on of laser gas analyzer of the process gasQ i u Lij u n Zhao Yongp i n g Feng Feng(Gas -F ired Po w er Station ,Ji n an S tee lG roup I nc 1,Ji n an 250101)Abst ract The laser gas ana l y zer ,based on the technology o f se m iconductor laser absor p ti o n spectrum ,wh ich has a qu ick response speed and w ithout any preprocessi n g ,can satisfy the on li n e i n specti o n requ ire m ent of pr ocess gas i n the field of stee l i n dustry 1I n the application of t h e recovery of LDG,the response speed o f l a ser gas analyzer isfaster than that o f the gas ana l y sis sa m pling syste m for about 20s ,so thatm ore than 418%gas can be recovered 1K ey w ords Se m iconductor laser absorpti o n spectrum LDG On li n e analyzer 没有特征吸收峰,因此红外气体分析仪测量有较大的局限性〔4〕。
综上所述,单线光谱技术、激光波长扫描技术和环境参数自动修正技术使DL AS 技术可以被用于实现气体的原位分析,因此比非分光红外等传统采样气体分析系统具备更强的环境适应性。
并且由于激光气体分析系统省却采样预处理装置,结构简单、无运动部件、维护标定方便、可靠性高、响应速度快而准确,大大提升在线过程气体检测的水平。
114 钢铁冶炼中的应用激光原位气体分析系统因其技术优势,已逐步取代红外气体分析系统,并开始广泛应用于各大钢铁企业的煤气回收分析系统,炉气/烟道气分析系统、电捕焦/电除尘安全分析系统和高炉喷煤、CDQ 循环气和转炉高温端分析系统等。
就济钢来说,现用激光原位气体分析系统中就有以能源气回收为目的的转炉煤气和控制安全的电捕焦安全分析系统、现依据实际使用效果,从转炉炼钢流程出发,就激光原位气体分析系统在转炉煤气回收项目中的应用进行重点阐述。
在转炉炼钢生产过程中,1450~1600e 的转炉烟气通过转炉烟罩降温至1000e ,然后经过一级、二级文氏管除尘、降温。
经降温除尘的净煤气中通常含有微量氧和高浓度的C O 成分,通过回收这些煤气的显热和化学潜能,能够使转炉工序甚至整个炼钢厂实现/负能炼钢0)))即生产过程消耗的能量低于回收的能量。
如宝钢、武钢及济钢等通过转炉煤气回收均实现转炉工序和炼钢厂能源的负消耗。
而为保证有效、安全的回收煤气,就必须实时监测煤气管道中的CO 和O 2的含量(见图3)。
C O 的检测是保证回收到最有价值的煤气,O 2的检测是避免煤气中的氧气含量过高导致在回收或使用中发生爆炸。
济钢转炉煤气柜测氧项目现场安装的LGA 激光原位气体分析系统,实时监测过程管道内煤气中的O2图3 转炉煤气回收工艺中的气体检测点11活动烟罩;21炉口烟道;31斜后烟道;41一次除尘器(饱和塔);51二次除尘器;61弯头脱水器;71湿气分离器;81烟气流量计;91风机;101旁通阀;111三通阀;121烟囱;131水封逆止阀;141V 型阀;151煤气柜;161电除尘器浓度,替代原有的人工采样分析方式。