异形件垂直交叉小深孔机加工艺探讨
机械加工过程中的深孔加工技术分析

机械 - r . 过程中的深孔加工技术分析
粱 俊
( 合肥 力威 汽车油泵有 限公 司,安徽合肥
2 3 0 0 4 1 )
摘 要 : 机械加 工行 业是保 证我 国工业化进程顺利 实施 的关键 。随着机械加 工业的发展 ,其各项工 艺技 术也得 到 了快速的 演 变。同时,在机械k _ T - 过程 中,深孔加 工技 术是 整个机械加 工的关键 所在。下面,就一起跟随本 文对机械加 工过程 中的深孔 加 工技术进行一个 简单的分析与探讨 。
关键词 : 机械加工 ; 深 孔加 工 ; 技 术 中图分类号 : T U7 文献标识码 : A
文章编号 : 1 6 7 1 . 5 5 8 6( 2 0 1 5 )1 0 . 0 0 0 8 - 0 1
在机械加 工过程 中,深孔加工是一项十分复杂的工序 ,同 交错齿 内排 削深 孔加 工技 术是 目前 应用较为 广泛 的一种深 它主要应用于钢件 的深孔加工技术 中。一般来说 , 时也是出现问题较 多的一道工序 。因此,为保证机械加 工过程 孔加工技术 , 中的各项工序顺 利实施,就必须要对深 孔加工技术进 行优 化, 在钢件上进行深孔加工远 比在 铸件 上进 行加 工要难得 多,所产 这也是 目前机械加工行业所最为重要的任务之一。 生 的铁屑也较多 。因此,必须采用像交错齿钻具这种 刀片排列 1什么是深孔 加工技术 顺序为错开式的刀具 。由于交错齿钻具的刀片的特殊 构造 ,从 所谓 的深孔 加工主 要是指在 机械 加工过程 中孔 的长度 与 而可 以使切 削通过 刀具 的两个 孔排入 到刀具 自身 的空心 刀杆 孔 的直径之 比大于 1 O 的孔。深 孔加 工技术在我 国的起步较早 , 中,切 削再 由空心刀杆 中排 出,从而实现 了排 出切削 的整个过 目前 各项技 术均 已相对较为 成熟 。 目前就 一般机械加 工企 业 程 。另外 ,刀片是在刀具 的两侧 内呈交错排列方式 的,这种排 来看 ,深孔加工时深孔与直径 的比值一般为 L / d 1 0 0 。例如 : 列方式可 以起着很好 的分屑作用 ,同时还能够使钻具两侧刀片 油箱孔、各种轴的轴向孔、空心主轴孔等 。 的受力度里平衡状态 ,即不会对刀片造成损害 ,又保证 了钻孔 2 深子 L 加工技术 的难点 的直线 性。另外 ,在 刀片 前加 工断屑槽 ,就会使钻孔 的切 削形 深孔加工 中由于对质量及其他方面 的要求均较高 ,因此在 成一种小 c形 的状态 ,从 而保证 了钻具 在高压 切削状 态下切 技术加工上有着诸多的难点 : 首先,由于机械加工过程 中深孔 削分较 容易被冲 走排 向外面 。同时,由于刀 具的钻 头沿径 向上 加工时速度不能太快 ,因此一般作业 效率均不高 ,其次在深孔 的切削在各 点的速度均不 同,例如 : 钻孔外 围部分的切削速度 加工时工作人员无法观察到设备切削时的情况 ,而 只能通过设 相 对较快,因此可采用耐磨性能较强 的 YT类硬材质 的合 金材 备切割 时所发 出的声音来判断深孔加工是否达 到一 定的标准要 料。而靠近刀具钻头中心的切 削速度 由较慢,在切削相互挤压 求 ,这种方 式在一定程度上是很容易出现误差 的。再次 ,一般 的过程 中刀片容 易受到损伤 ,因此必须采用 Y A类 型的硬质合 而 言,深孔加工 的长径距离是较大的,因此用 于切 削深孔 的刀 金 。 具等设备就相对较长较细 。但 由于刀具较长较 细的特 点,导致 另外 ,在深 孔加 工时 ,如果深 孔 的直径 大 于 6 . 5 厘 米 时, 钻 具 自身的钢性 强度较差 ,同时 由于该设备刀具刃 口偏差等 问 则可采用机械夹固式不重磨深孔加工技术,它的结构与施工方 题 ,从而在 工作 时产生较大 的振动 ,很容易在作业过程 中使钻 式与交错齿深孔加工技术基本相 同。它在作业时刀片 的内部会 孔因受到的振动较大等原 因而发生偏离设计的现象。针对这 一 出现一个阶 台,并用螺丝固定在刀头部分 ,以上刀片做为断屑 点难点 , 就必须要求工作人员在深孔加工时, 首先要 间断切削 , 板 ,并将导 向板作为半 圆形状 ,从而使导 向块与孔壁形成一个 并且要 同时不断提升 刀具 ,要具备较强的判断力来对深 孔加 工 很好 的接触点 。而后再采用 4 0 C的金属制成 的钻头体将空心钻 中切削的长度及 形状进行判断 。最后 ,一般在深孔加工时会 产 杆 与 其 连 接 在 一 起 。 生较大 的热量,而这些热量受一些 因素 的影响无法在深孔加工 3 . 3喷 吸钻深子 L 加工技术 过程 中快速释放 出来, 再加之深孔加工钻具排削条件较为恶劣 。 使用该方法进行深孔加工时 ,必须要 同时配备 一套相应 的 因此在深孔加工 中必须采用冷 却法对刀具设备进行冷却, 以保 设备 ,并将管夹头 安装于车床板 的夹具 中,同时利用大拖板 的 证深孔加工质量的有效性 。深孔加工 中一定要有较好的钻具冷 自动进给使物件钻 出深度 ,另外 ,为 了防止钻 头刚钻人 工件 时 却方法 以及 良好的排削系统,因此 目前机械加工企业均采用 内 发生扭 断,要在工件前 安装一个 导向设备 ,从而使 喷吸钻 的高 排 削深钻孔机械来对大直径深孔进行加工 。 压深孔钻工作时获得一个很好的结果。 3机械加工过程 中深F U J O 工技术 例如 : 在使用 喷吸式刀 具和高压式 刀具进行深 孔加工 时, 3 . 1单刀深孔钻加工技术 切削 的液 流量需在达 到每分钟 1 5 0 L以上 ,压力 要控制在每 立 所谓 的单刀钻具的主要特 点在于它 的刀片和导 向的部位均 方厘米 3 5 公斤 以上。在这 种大流 量和压 力下 ,传 统的车床 冷 是采用材质较为坚硬的金属合 金材料构成 ,并且单刀 的刀尖部 却系统是无法满足大热量冷却需求的 ,因此必须同时配备一系 分偏离整个钻具 的中心点约 3 毫米的距离,从而使刀具在深孔 列大流量 的冷却系统支持 ,从而达到喷吸刀具 比高压刀具 内所 加 工切 削过程 中形成 了一种定心尖状态 ,因此该钻具可 以在切 排 出的切 削液压力低 的 目的 。这种方法下 的冷却系统 的功率消 削过程 中分担一部分 的径 向切割力。另 外,单刀深钻孔钻具 的 耗及钻具 的损害程度都会降低 ,因此在深孔加工时 ,要尽时 多 主 削刀在工作 中形成一种阶台型的结构 ,从而 能够很好地起到 采用喷吸式刀具进行深孔加工 。 分 削的 目的,因此在操作过程 中可以根据深孔直径 的大小要求 4 结语 来设置 单刀的使用数量 ,以此来保证排削的有效性。 综上所述 ,机械加 工过程 中深孔加工 技术 直接 关系着整个 另外,在深孔加工整个过程中 ,单刀钻 具中各刀削部分的 机械加工 的质 量,因此 ,在深孔加工 中必须针对 不同的深孔加 应 面与被加 工的深孔之 间形成一种错开的孔径距 离,从而防范 工要 求采 用不 同的加工技术措施 ,最大限度保 证深 孔加工的质 了刀具在加 工过程 中对深孔表面可能会造成的损伤。 同时,单 量 安 全 。 刀刀具 的导 向部分 的尺 寸距离 要 比单 刀尖部 的直径 尺寸距 离 参考文献 小0 . 1 毫米 ,以防止刀具钻孔时出现偏 离直线距 离的状况 发生。 [ 1 ] 王峻 . 现代深 孔加工技 术 [ M] . 哈尔滨 : 哈 尔滨工 业大学 出 最后,在使用单 刀刀 具进行深孔加工时 ,该刀具导 向垫 的倒角 版社 ,2 0 0 5 . 角度应 设计为 1 8 度 角,这种角 度更有利 于将物件 切 削排 除 出 【 2 】 邓文英 . 机械加 工过程 中深孔加工技术探讨 [ J ] . 2 0 1 3( 0 8 ) : 去。 目前该种 刀具深孔加工方法广泛应用于种类实心 的铸件油 1 4 . 1 5 . 箱上,并在 其中起着较好 的应 用效 果。 [ 3 】 李伟光 . 机械 制造 中深孔加工技术 【 J 】 . 机械 工业论坛 ,2 0 1 4 3 . 2交错齿内排 削深 孔加工技术 ( 】 7) .
异形轴类零件的数控加工工艺分析

异形轴类零件的数控加工工艺分析摘要:此次设计主要是介绍运用数控机床来加工异性轴类零件从毛坯到所加工零件这一过程中的工艺及其相应的工艺分析,关键词:异性轴类零件、数控机床、工艺分析。
一、典型轴类零件的加工工艺轴类零件是常见的典型零件之一。
按轴类零件结构形式不同,一般可分为光轴、阶梯轴和异形轴三类;或分为实心轴、空心轴等。
它们在机器中用来支承齿轮、带轮等传动零件,以传递转矩或运动。
1.1 零件图样分析图1-1 零件图零件车削工艺分析如图所示,零件材料为:45钢。
1.2数控加工工艺基本特点数控机床加工工艺与普通机床加工原则上基本相同,但数控机床是自动进行加工,有如下特点:①数控加工的工序内容比普通机床的加工内容复杂,加工的精度高,加工的表面质量高,加工的内容较丰富。
②数控机床加工程序的编制比普通机床工艺编制要复杂些。
这是因为数控机床加工存在对刀、换刀以及退刀等特点,这都无一例外的变成程序内容,正是由于这个特点,促使对加工程序正确性和合理性要求极高,不能有丝毫的差错,否则加工不出合格的零件。
1.3 确定主要表面的加工方法1.3.1粗基准选择原则(1)为了保证不加工表面与加工表面之间的位置要求,应选不加工表面作粗基准。
(2)合理分配各加工表面的余量,应选择毛坯外圆作粗基准。
(3)粗基准应避免重复使用。
(4)选择粗基准的表面应平整,没有浇口、冒口或飞边等缺陷,以便定位可靠。
1.3.2精基准选择原则(1)基准重合原则:选择加工表面的设计基准为定位基准。
(2)基准统一原则: 自为基准原则,互为基准原则。
1.3.3定位基准综合上述,粗、精基准选择原则,由于是轴类零件,在车床上只需用三抓卡盘装夹定位,定位基准应选在零件的轴线上,以毛坯ф30mm的棒料的轴线和右端面作为定位基准。
1.3.4装夹方式数控机床与普通机床一样也要全里选择定位基准和夹紧应力求设计、工艺与编程计算的基准统一,减少装夹次数,尽可能在一次定位装夹后,加工出全部待加工表面,避免采用占机人工调整式加工方案,以充分发挥数控机床的效能。
小直径深孔加工的探讨
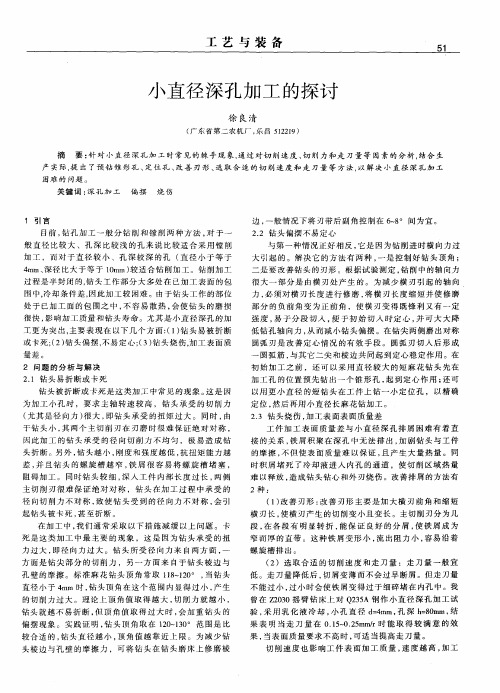
死 是这 类 加 工 中最 主 要 的现 象 ,这 是 因 为钻 头 承受 的扭 力 过大 , 即径 向力 过 大 。钻 头 所受 径 向力 来 自两 方 面 , 一 方 面是 钻 尖部 分 的切 削力 ,另 一 方 面来 自于 钻 头棱 边 与 孔壁 的 摩擦 。标 准麻 花 钻 头 顶角 常取 18 10 , 1 —2 。 当钻 头 直径 小 于 4 m 时 , 头顶 角在 这个 范 围内显 得 过小 , 生 m 钻 产 的切 削 力过 大 。理 论 上顶 角值 取 得 越大 , 削力 就 越 小 , 切 钻 头 就越 不 易折 断 , 顶 角值 取 得 过 大 时 , 但 会加 重钻 头 的 偏 摆 现 象 。实 践证 明 , 钻头 顶 角 取 在 10 10 范 围是 比 2~3 。 较合 适 的 , 头 直径 越 小 , 角 值 越靠 近 上 限 。 为减 少 钻 钻 顶
定 位 , 后 再用 小 直径 这类 加工 中常见 的现 象 。 这是 因 为 加工 小 孔 时 ,要 求 主轴 转 速 较 高 ,钻 头 承受 的切 削 力 ( 其是 径 向力 ) 大 , 尤 很 即钻头 承 受 的扭 矩 过 大 。 同时 , 由 于钻 头小 , 其两 个 主切 削 刃 在 刃磨 时很 难 保证 绝 对 对 称 ,
起 钻头 被卡 死 , 至 折 断 。 甚 在 加 工 中 , 们 通 常 采 取 以 下 措 施 减 缓 以上 问 题 。 卡 我
时 积 屑堵 死 了冷却 液 进 入 内孔 的通 道 ,使 切 削 区域 热 量 难 以释 放 , 成 钻头 钻心 和 外刃 烧伤 。改 善排 屑 的方法 有 造
的 摩 擦 , 但 使 表 面 质 量 难 以 保 证 , 产 生 大 量 热 量 。 同 不 且
浅析机械加工过程中的深孔加工方法

浅析机械加工过程中的深孔加工方法摘要:现阶段我国科学技术发展水平的提升,对机械加工制造产生了积极影响,逐渐扩大了其产业规模。
实践中为了使机械加工效果更加显著,增加深孔加工中的技术含量,则需要考虑与之相关的加工技术使用,落实好具体的研究工作,确保深孔加工状况良好性,为机械加工行业的可持续发展提供专业支持。
基于此,本文将对机械加工作用下的深孔加工技术进行系统阐述。
关键词:机械加工;深孔加工;技术1、深孔处理技术的技术特征1.1深孔加工技术很困难首先,大多数深孔加工是在半封闭或完全封闭的环境中进行的,因此无法直接观察到诸如加工,切削和切削之类的操作人员。
因为孔的半径与深度之间的比率较大,所以它会排干金属屑并使孔难以堵塞。
毕竟,如果钻头太长,则会出现严重降低钻头刚性的问题。
由于孔偏移或抖动等问题,难以有效地保证深孔加工的精度,并且由于孔加工的散热问题,在封闭环境下,由于孔的温度升高,钻头可能会磨损。
1.2锻炼方法本身很特殊在深孔加工的整个过程中,可以通过多种方式来操作工件和刀具,其中工件旋转并且刀具同时进给。
固定工件并同时进给刀具。
选择多种运动方法,例如定向进给,是使用深孔加工技术的主要挑战之一。
1.3深孔加工中的排屑问题深孔加工中的排屑问题是要重点解决的问题之一,排屑方法主要分为两种。
首先是外部排屑。
将冷却液倒入岩心钻杆中以清除切屑。
切割区域已清洁。
第二个是去除内部切屑,将其倒入钻杆的孔和外壁中以从切削区域去除切屑。
在实际的加工过程中,内部排屑处理方法通常是优选的,因为该方法不会引起孔壁的二次摩擦,并且钻杆的高刚度不会影响孔的表面质量。
2、深孔加工中冷却润滑液的作用深孔加工中,冷却润滑液不仅要快速去除钻孔过程中产生的热量并润滑刀具和工件,减小两者间的摩擦,更主要的是要用具有一定压力和流速的冷却液来冲走切屑,以达到排屑的目的。
切屑容易堵塞排屑通道,影响刀具正常使用。
如果堵在钻头排屑孔位置,还会挤压刀片,造成崩刃影响切削加工。
异形加工的技巧

异形加工的技巧
1. 选择合适的加工工艺:异形加工涉及到的工艺包括铸造、锻造、冲压、剪切、焊接等,需根据具体形状选择适合的加工工艺。
2. 制定合理的加工方案:根据加工对象的形状、尺寸、要求等制定合理的加工方案,包括材料选择、加工工艺、加工顺序等。
3. 采用先进的加工设备:使用先进的加工设备可以提高加工精度和效率,如数控机床、数控车床、激光切割机等。
4. 确保零件质量:对于异形零件,要严格控制加工精度和表面质量,保证零件符合设计要求。
5. 注意安全生产:异形加工运用的设备复杂,操作人员必须具备专业知识和操作技能,同时要注意安全生产,避免事故的发生。
机械加工中深孔加工技术的研究

机械加工中深孔加工技术的研究摘要:随着我国机械化工艺水平的日益提高,在生产活动期间深孔加工技术的应用越来越广泛。
然而,在机械加工领域,深孔加工技术存在各种问题,一定程度上阻碍了技术水平的提高。
文章主要介绍深孔加工技术的重点与难点,分析在机械加工中提升深孔加工技术的有效措施,为机械加工可持续发展打下坚实基础。
关键词:机械加工;深孔加工;钻孔引言随着机械加工技术的迅猛发展,人们对深孔加工的效率和质量提出了更高要求。
因此,需要分析目前深孔加工存在的问题,采取相应的优化措施,有效提升深孔加工的效率与质量,为机械加工可持续发展打下坚实基础。
1.深孔加工技术的重点和难点1.1深孔加工技术难度较大在机械加工生产活动中,深孔加工技术的难点主要体现在以下4个方面。
第一,绝大部分操作在较为狭窄的作业环境中实施,由于作业空间狭窄,给工作人员的操作带来了很大难度,同时不利于工作人员观察和勘验钻孔平台。
第二,深孔半径与钻孔深度中的比例无法精准确定和控制,导致作业期间极易出现金属杂物堵住深孔的问题。
第三,钻头与加工道具对深孔加工技术有一定影响。
长期的加工应用会造成钻头与加工道具出现严重磨损,导致其半径与深度等出现误差,对提高深孔加工技术水平有不良影响。
第四,导致钻头与加工刀具磨损的因素多,其中作业空间散热效果不明显和空间温度相对较高是造成磨损严重的两个主要因素。
1.2钻孔行为存在局限性钻孔期间,一系列加工零件和钻头与作业岩层有效接触,会产生各种运行模式,导致加工刀具、钻头及零部件的运行存在显著差异。
1.3碎屑排出问题整个深孔加工期间会产生大量的废料,一旦这些废料没有及时从深孔中排出,会对后续的深孔加工水平造成严重影响,进而影响整个技术的转型和发展。
目前,深孔加工技术中废料排出模式包括内部排放法和外部排放法。
两者均是将冷却液注入深孔予以实施,但是在注入部位会有明显不同。
另外,外部排放法和内部排放法在应用效果方面存在显著差异,前者在实际操作过程中会造成严重摩擦,影响整个操作精确程度,后者却不存在这一问题。
浅析深孔加工工艺改进的研究及优化
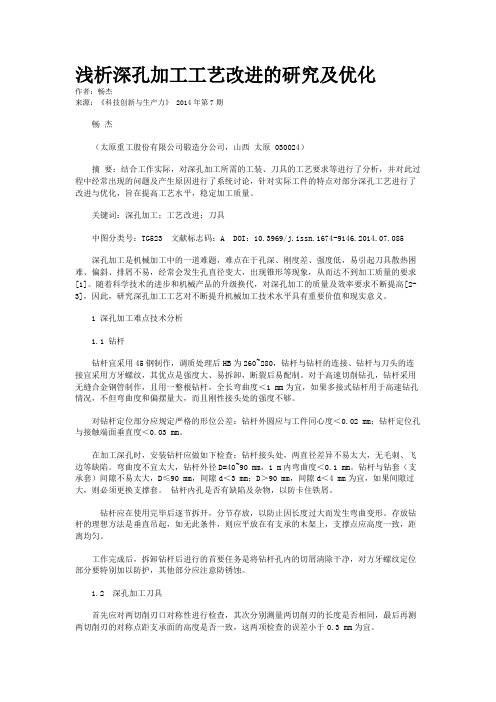
浅析深孔加工工艺改进的研究及优化作者:畅杰来源:《科技创新与生产力》 2014年第7期畅杰(太原重工股份有限公司锻造分公司,山西太原 030024)摘要:结合工作实际,对深孔加工所需的工装、刀具的工艺要求等进行了分析,并对此过程中经常出现的问题及产生原因进行了系统讨论,针对实际工件的特点对部分深孔工艺进行了改进与优化,旨在提高工艺水平,稳定加工质量。
关键词:深孔加工;工艺改进;刀具中图分类号:TG523 文献标志码:A DOI:10.3969/j.issn.1674-9146.2014.07.085深孔加工是机械加工中的一道难题,难点在于孔深、刚度差、强度低,易引起刀具散热困难、偏斜、排屑不易,经常会发生孔直径变大,出现锥形等现象,从而达不到加工质量的要求[1]。
随着科学技术的进步和机械产品的升级换代,对深孔加工的质量及效率要求不断提高[2-3],因此,研究深孔加工工艺对不断提升机械加工技术水平具有重要价值和现实意义。
1 深孔加工难点技术分析1.1 钻杆钻杆宜采用45钢制作,调质处理后HB为260~280,钻杆与钻杆的连接、钻杆与刀头的连接宜采用方牙螺纹,其优点是强度大、易拆卸,断裂后易配制。
对于高速切削钻孔,钻杆采用无缝合金钢管制作,且用一整根钻杆,全长弯曲度<1 mm为宜,如果多接式钻杆用于高速钻孔情况,不但弯曲度和偏摆量大,而且刚性接头处的强度不够。
对钻杆定位部分应规定严格的形位公差:钻杆外圆应与工件同心度<0.02 mm;钻杆定位孔与接触端面垂直度<0.03 mm。
在加工深孔时,安装钻杆应做如下检查:钻杆接头处,两直径差异不易太大,无毛刺、飞边等缺陷。
弯曲度不宜太大,钻杆外径D=40~90 mm,1 m内弯曲度<0.1 mm。
钻杆与钻套(支承套)间隙不易太大,D≤90 mm,间隙d<3 mm;D>90 mm,间隙d<4 mm为宜,如果间隙过大,则必须更换支撑套。
钻杆内孔是否有缺陷及杂物,以防卡住铁屑。
深孔加工工艺探讨

深孔加工工艺探讨摘要:深孔加工一直是孔系加工中的难点。
深孔加工不仅加工量大,加工效率较低,且对加工设备、加工刀具耐用性及加工工艺提出了更严格的要求。
随着现代科学技术的发展,新型产品的不断更新换代,对产品深孔加工质量提出了更高的要求。
因此,研究深孔加工已经成为机械加工行业的必要。
关键词:深孔加工加工设备刀具耐用性加工工艺加工质量中图分类号:p624.41. 深孔定义一般机械加工方面将孔深l与孔径d之比:l/d>5的孔称为深孔。
原因为:一般实料孔采用麻花钻加工,麻花钻直径d、螺旋角β和螺旋槽导程p成以下关系:p/πd=tan(β)(1.1)在实际生产中,为了保证麻花钻在钻削过程中的排屑质量,麻花钻一次钻到底即不退刀的情况下,钻孔深度l 5的孔称为深孔。
深孔加工分为:一般深孔加工、精密深孔加工和电深孔加工,这里主要介绍一般深孔加工。
一般深孔加工按照加工方式包括以下几种:实心钻孔法即原毛坯无孔,采用钻削加工出孔;镗孔法即已有底孔,为满足孔的精度及表面粗糙度采用镗削加工孔;套料钻孔法即用空心钻头钻孔,加工完成后毛坯中心残存一根芯棒的方法。
现在产品多为焊接件、锻打件等,原毛坯大部分为无底孔结构,故实心钻孔法是现在深孔加工最常用的加工方法。
下面将重点介绍实心钻孔法。
2.加工设备的选择其中适合深孔加工的设备主要包含以下几种设备:镗床、钻床、专用钻孔机、铣床、加工中心等。
根据加工工件的结构特点、现有加工设备性能、工装等进行加工设备的选择。
由于镗床、钻床、专用钻孔机等设备在加工孔前,需要借助划线或其它加工方式确定孔在整个工件中位置后,方可加工。
从而导致工件加工时工序较为分散,需要多次装夹产生大量的辅助加工时间,故在加工设备及条件允许的情况下不提倡使用镗床、钻床、专用钻孔机加工孔。
相对以上三种设备,铣床及加工中心在加工孔时,只需要在编制加工程序时确认加工孔位置坐标即可,从而实现了工序集中原则,避免多次装夹造成的装夹误差,不仅缩短了加工辅助时间且提高了加工精度。
- 1、下载文档前请自行甄别文档内容的完整性,平台不提供额外的编辑、内容补充、找答案等附加服务。
- 2、"仅部分预览"的文档,不可在线预览部分如存在完整性等问题,可反馈申请退款(可完整预览的文档不适用该条件!)。
- 3、如文档侵犯您的权益,请联系客服反馈,我们会尽快为您处理(人工客服工作时间:9:00-18:30)。
2 )基准位移 的误差会对槽 1H1 0 1的对称度产生影 响。
3 )用过盈配合刚性心轴定位 , 存在定位 心轴抽 取困难 、 取 出时易拉伤 已加 工好 的 内孔 表面 , 降低 孔表 面 的粗 糙度 , 造成工件不合格 。选用 间隙配合 刚性 心轴 , 具产生 的定 位 夹 误差分 析 J :
2 0 l m; " l H 0 m的对称度 O 1ln )1 Hlm  ̄ t 9 1 m h ・ u 。 /
图 1 击发盒体零件加工 图பைடு நூலகம்
加工 2垂 直交叉 孔 , 以加工 出 的 2垂 直交叉 孑 为精基 准 , 再 L
2 解 决方案
2 1 超 差 原 因 分 析 .
设计所有工艺流程及:序。这个方案确保了工艺基准与设 【 计基准的重合, 不存在基准不重合误差 , 却存在以下问题:
第3 2卷
第1 2期
四 川 兵 工 学 报
21 0 1年 1 2月
【 制造技术】
异 形 件 垂 直 交 叉 小 深 孑 机 加 二 艺 探 讨 L [
黄清泉
( 海装驻重 庆地 区军事代 表局 , 重庆 4 0 3 ) 00 0
摘要 : 通过对某型产 品盒体加工 中出现超 差品 的分 析 、 理 , 处 探讨 了异形件垂 直交 叉小深孔 的机加 工艺。提 出了增 加辅助基准面 、 基准统一 、 加工时先大孔后小孔 、 设计 相应 的工艺工装 等工艺 方法 , 从而保 证 了产 品质量 , 也提高 了
1 )由于深孔加 工采用 的是 工件 不动 , 刀具 旋转 。刀具
直径小 , 刚度 差 , 遇到材料 硬点 , 刀具 易发生偏 离 , 心位置 孔
原工艺方案 : 首先粗加工 A、 、 B c面 , 以此 为基 准用 镗床
收稿 日期 :0 1 0— 6 2 1 —1 0
作者简 介 : 黄清泉(93 )男 , 16一 , 硕士 , 高级工程师 , 主要从事兵工方面 的研究 。
设定位心轴为 49 ( ) t77 .∞)  ̄ i : 及 k f(。1 17 l -0 0: .
孔 t 9 1 ” ) 位 误 差 ( 准位 移 误 差 ) D h H1 ( 。 定 l 基 A 1=
01 .3一(一 4 )= .7 ( m) 01 0 11m ;
平衡各尺寸 , 确保壁厚均匀 , 按工艺要 求划 出加工 面线 , 加工后 , 将其作为加工粗基准 , 制出两孔 的中心锥孔 、 铣平 四 个端面及 D面 ; D面及 中心锥孔为 基准 , 以 加工 A、 E面 ; B、 再以 A、 、 B E面为 精基准 加工 各孔及 其余 各处 , 样做 到 了 这
基准统一 。 两深孔的加工方法 :
孔 tlH1 h7 2(
) 位 误 差 ( 准位 移 误 差 ) D 定 基 A 2=
01 .8一(一 .3 )= . 1 ( m) 00 4 0 24 m 。
用孔  ̄ 9 1 瑚) 孔 t 7 2 b H1 ( l 、 h H1 ( 1
%) 定位 时产 生误
12 0
也会发 生偏 移。直线度差 , 垂直度就不易保证 。
四 川 兵 工 学 报
ht:/cgjusr.o / t / sb . r v cr p o e n
( 。0 ) 工艺要求 ) 用车 用夹 具保 证垂 直度 及孔 到 A面 +。 5 ..3 ( 0 .1 , ,
的距 离 。
0. 3 mm 03
1 加工孔 t 9 1 ,a. , . 0035 工 艺要求 ) ) h H 1R 161 5± .1 ( l 2 ;
因该孔深与直径之 比( / )= . 5 属于深 、 孔加 工 , L d 8 7> , 盲 根 据孔精度和表面粗糙度 的要求 , 择了钻 、 选 粗扩 、 精扩 、 粗铰 、
差 A 1 △ , 而引起定位误差 A 如 图 2所示 。 D 、 进 D, A D=2 X( 3 ac 27 X t t—A )+A 1=2 X[ 3 g D1 D 27X ( D/ A 12+A 2 2 / 2 7—8 )一A 1 D / ] (3 1 D ]+A 1=2X[ 3 D 27X ( .7/ 0 2 4 2 / 5 —0 11 0 1 1 . 1 ( 0 1 12+ . 1/ ) 16 .7 ]+ .7 —0 4 4 mm)>
可靠击发的重要件之一 , 图 1 如 。
主 篡 和 生中 难 出 的 , 要 产 很加 合 产 、 都 工格品 批
1 )两垂直交叉孔 ( l H l o  ̄ 9 f ( ” mm、 a・ b R 16和 ¥ 7 2 1H1 ( 。 m R 3 2 的垂直度 0 1m ) m、 a ・ ) ・ m。
精铰 的加工方法 , 中铰 孔为 浮动铰 削 , 其 用工装 保证 孔距 面 的距离 , 具体加工方 法为 :
显然这种定位方式的定位误差太大 , 对称度夹具 的定 其
位误差远远超过 1 H l 0 1mm槽对 t 9 1 m h H 0 m公差 值 0 1m l . m
a )镗 引孔 tl 4 m, h5深 0m 确保钻孔 时位置 正确 ; b )钻孔 + 5深 15 m 采 用分 级加 工方 法 , 钻头 加 1 6 m, 使 工一定时 间或一定深 度后退 出工 件 , 以排 出切 屑 , 借 并冷 却 刀具 。依照此方法 重复进 刀或退 刀 , 直至 加工完 毕 ; 钻削 时 应尽量避免在加工 过程 中停 车 , 如必 须停 车 , 应先 停止 进 则 给 , 刀具退 回一段距离 , 将 然后关闭油泵 , 防止 发生刀具在 孑 L 中咬住 的现象 ; c )粗 扩 , 镗引孔 41. H1 , 5 1深 6 m, 端刃扩 孔钻 扩 6 0m 用 孔 6 6 5 1镗引孔是为 了保证扩孔位 置正确 ; 1 .H1 , 因扩孔钻 外 形与麻花钻相类似 , 只是 加工余量 小 , 主切 削刃长度 短 , 因而
以 A面定位加工 1H1mm槽 产生 的定位误 差为 0 07 0 1 .2 小于工件 误 差/ ( .3 ) 能 保 证槽 对 孔 的对 称 度 不 大 于 3 00 3 , 0 1m . m的要求 , 可满足产 品要求 , 且有一定的精度储备 。
2 3 两 深 孔 加 工 工 艺 .
生产效率 。 关键词 : 机加工艺 ; 异形件 ; 垂直交叉小深孔
中图分类号 :J1 . T6 0 5 文献标识码 : A 文章编号 :0 6— 7 7 2 1 )2— 1 1 0 10 0 0 (0 1 1 0 0 — 4
l 状析 分 现
某型产品击发盒体… 为铸 造件 , 精度高 、 形状复杂 , 内置 击发保险 、 动锁 、 滑 滑轨等 2 0多 个零件 , 是确保 武器 正确 它