冲模零件工艺设计简介
冲裁模(冲压模具)课程设计 说明书

弓形连接固定片复合模设计零件名称:弓形连接固定片生产批量:中批量材料:零件材料为08钢,厚度为1.5mm图1-1一、零件工艺性分析弓形双孔连接固定块片是家用发电风扇中的一连接固定零件,零件的精度要求较低,具有较高的强度和刚度。
外形最大尺寸为70mm,属于小型零件。
该零件应中批量生产,外精度不高,只需平整,外轮廓是该零件需要保证的重点。
该零件用到的冲压工序有冲孔、落料,因此可设计冲孔落料复合模生产此零件。
二、工序设计及工艺计算1、排样毛坯最大尺寸70mm,不算太小,为保证冲裁件的质量,模具寿命和操作方便,采用有搭边,单排排样,如下图2-1所示,冲裁件之间的搭边值a=1.5mm,冲裁件与条料件侧边之间的搭边值a=2.3mm。
1图2-1-1计算条料的宽度:B=70+2×2.3+c=74.7(mm)其中c为调料可能的摆动量,c=0.1mm计算条料的步距:A=20+1.5=21.5(mm)图2-1-2一个步距内材料的材料利用率:η=985.182/(74.7*21.5)×100%= 61.34%2、压力中心确定和压力机的选择(1)、冲裁力的计算冲裁力 F p=Lt σb Kp (2-2-1) 其中:由图2-2知,周长L=213.057mm;=900Mpa, 此时,Kp=1,则:材料:08F钢板,查表,σbFp=213.057X1X900X1=191.75(kN) (2-2-2) 根据以上模具结构类型,采用弹性卸料和漏料出件,卸料力F q=KF,取K=0.05,则:F q =0.05×191.75=9.59(kN) (2-2-3)推料力Fq1=nK1Fp,去凹模刃壁垂直部分高度h=5mm,t=1mm,n=5/1=5;取K1=0.06,则:F q1=5X0.06X191.75=57.53(kN) (2-2-4)顶件力Fq2=K2Fp,K2=0.06,则:Fq2=0.06X191.75=11.51 (kN) (2-2-5) 本套模具用到的由压力机提供的有冲裁力和推料力,因此:总冲压力F=FP+ F q1总=191.75+57.53=249.28(kN) (2-2-6) (2)、压力中心的确定压力中心在两小圆垂直中心线上(3)、压力机的选择,取系数为1.3,则选用的压力机公称压力P≥(1.1~1.3) F总=1.3×249.28=324(kN)P≥1.3F总初选压力机公称吨位为400kN,型号为J23-40,其主要工艺参数如下:公称压力:400KN;滑块行程:100mm;行程次数:80次∕分;最大闭合高度:300mm;最大装模高度:220mm;闭合高度调节量:80mm;工作台尺寸(前后×左右):150mm×300mm;模柄孔尺寸:直径50mm,深度70mm;工作垫板:厚度80mm,孔径200mm;电动机功率:1.5kW。
冲压模具课程设计--带凸缘无底筒形件

冲压模具设计课程设计学院:姓名:寒冰色手学号:专业:11机制目录1零件冲压工艺分析---------------------------------------------03 1.1 制件介绍---------------------------------------------------03 1.2 产品结构形状分析-------------------------------------------032.零件冲压工艺方案的确定--------------------------------------033冲模结构的确定-----------------------------------------------044.零件冲压工艺计算--------------------------------------------044.1零件毛坯尺寸计算-------------------------------------------044.2 排样------------------------------------------------------064.3 拉深工序的拉深次数和拉深系数的确定------------------------064.4 冲裁力、拉深力的计算--------------------------------------074.5 拉深间隙的计算--------------------------------------------094.6 拉深凸、凹模圆角半径的计算--------------------------------09 4.7 计算模具刃口尺寸------------------------------------------094.8 计算模具--------------------------------------------------105. 选用标准模架----------------------------------------------125.1 模架的类型------------------------------------------------125.2 模架的尺寸------------------------------------------------126. 选用辅助结构零件------------------------------------------136.1 导向零件的选用--------------------------------------------136.2 模柄的选用------------------------------------------------136.3 卸料装置--------------------------------------------------146.4 推件、顶件装置--------------------------------------------146.5 定位装置--------------------------------------------------147 参考文献--------------------------------------------------141零件冲压工艺分析1.1 制件介绍零件名称:心子隔套材料:08钢料厚:1.0mm批量:大批量1.2 产品结构形状分析由图1可知该零件为圆筒件经过翻遍处理,翻边处有过渡圆弧,且半径为R=2.5mm故非常适合用模具拉深或翻边进行处理,故要对毛坯进行计算。
冲压工艺与模具设计:冲裁模的主要零部件结构设计

凹模厚(高)度
H=kb (≥15)
k见表2.22 凹模壁厚 C=(
1.5~2)H
(≥30~40)
计算值:
靠用标准,选择模架的依据。
2 工作零 件3.凸凹模
复合模中同时具有落料凸模和冲孔凹模作用的工作零件。
凸凹模的最小壁厚: 正装复合模,内孔不积存废料,胀力小,最小壁厚可以小些; 倒装复合模,若内孔为直筒形刃口形式,且采用下出料方式, 则内孔积存废料,胀力大,故最小壁厚应大些。
导料板的厚度:见表2.24
导料板结构
3 定位零件(续)
2)侧压装置
设置目的:若条料公差较大,为避免条料在导料板中偏摆,使最 小搭边得到保证。
结构形式:①弹簧式侧压装置 ②簧片式侧压装置 ③簧片压块式侧压装置 ④板式侧压装置
不宜设置侧压装置的场合:①板料厚度在0.3mm以下的薄板; ②辊轴自动送料装置的模具。
谢谢!
特殊侧刃:既可定距,又可冲裁零件的部分轮廓 宽度b
侧刃断面尺寸 其他尺寸按标准规定
侧刃凹模按侧刃实际尺寸配制,留单边间隙。
侧刃数量: 一个或两个 侧刃布置: 并列布置、对角布置
侧刃定位误差比较
1-导料板 2-侧刃挡块 3-侧刃 4-条料
尖 角 形 侧 刃
特殊侧刃
3 定位零件(续)
5)导正销
使用目的: 消除送进导向和送料定距或定位板等粗定位的误差。 主要用于: 级进模
1)导料销、导料板 导料销:两个,位于条料的同侧, 从右向左送料时,导料销装在后侧; 从前向后送料时,导料销装在左侧。 结构形式: 固定式、活动式
3 定位零件(续) 1)导料销、导料板(续) 导料板:设在条料两侧 结构形式:一种是标准结构,它与卸料板(或导板)分开制造 一种是与卸料板制成整体的结构。
冲裁模设计说明

冲制图3-146所示工件,材料为08钢,料厚1mm,大批量生产,试完成:1)工艺设计2)模具设计3)绘制模具装配草图1.零件的工艺性分析(1)结构工艺性该零件结构简单,形状对称,无悬臂,孔径、孔边距均大于1.5倍料厚,可以直接冲出,因此比较适合冲裁。
(2)精度由表3-11和表3-12可知,该零件的尺寸精度均不超过ST4等级,因此可以通过普通冲裁方式保证零件精度要求。
(3)原材料 08钢是常用的冲压材料,具有良好的塑性,(伸长率δ= 33%),屈服极限>=195MPa,适合冲裁加工。
2.工艺方案确定该零件需要落料和冲孔两道工序完成,可采用的方案有三种:方案一:单工序冲裁,先落料再冲孔。
方案二:复合冲裁,落料冲孔同时完成。
方案三:级进冲裁,先冲孔再落料。
由于是大批量生产,因此方案一不满足生产率的要求,方案二和方案三都具有较高的生产效率,虽然方案三比方案二操作方便,但方案二能得到较高的精度,且由于被冲板料较薄,特别是外形与内孔的同轴度要求,因此选用方案二,即采用复合冲压。
3.模具总体设计(1)模具类型的确定考虑操作的方便与安全性,选用倒装复合模。
(2)模具零件结构形式确定。
1)送料及定位方式。
采用手工送料,导料销导料,挡料销挡料。
2)卸料与出件方式。
采用弹性卸料装置卸料,刚性推件装置推件。
3)模架的选用。
选用中间导柱导向的滑动导向模架。
4.工艺计算(1)排样设计根据工件形状,这里选用有废料的单排排样类型,查表3-3得搭边a1 = 1.5mm,侧搭边a = 2mm,则搭边宽度B= 40mm + 2x 2mm = 44mm,进距S = 23.66mm + 23.66mm + 1.77mm = 49.01mm。
查表3-4得裁板误差Δ = 0.5mm,于是得到如图所示排样图。
根据GB/T708---2006可知,这里选用的钢板规格为1420mm x 740mm,采用横裁法,则可裁得宽度为44mm的条料32条,每条条料可冲出零件15个。
冲裁工艺与冲裁模的设计
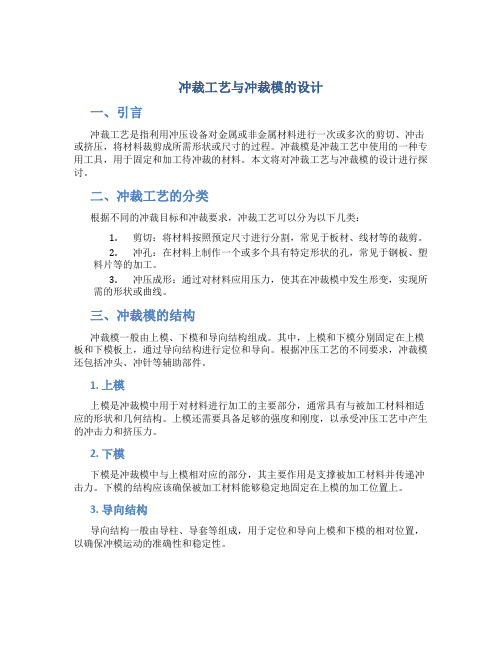
冲裁工艺与冲裁模的设计一、引言冲裁工艺是指利用冲压设备对金属或非金属材料进行一次或多次的剪切、冲击或挤压,将材料裁剪成所需形状或尺寸的过程。
冲裁模是冲裁工艺中使用的一种专用工具,用于固定和加工待冲裁的材料。
本文将对冲裁工艺与冲裁模的设计进行探讨。
二、冲裁工艺的分类根据不同的冲裁目标和冲裁要求,冲裁工艺可以分为以下几类:1.剪切:将材料按照预定尺寸进行分割,常见于板材、线材等的裁剪。
2.冲孔:在材料上制作一个或多个具有特定形状的孔,常见于钢板、塑料片等的加工。
3.冲压成形:通过对材料应用压力,使其在冲裁模中发生形变,实现所需的形状或曲线。
三、冲裁模的结构冲裁模一般由上模、下模和导向结构组成。
其中,上模和下模分别固定在上模板和下模板上,通过导向结构进行定位和导向。
根据冲压工艺的不同要求,冲裁模还包括冲头、冲针等辅助部件。
1. 上模上模是冲裁模中用于对材料进行加工的主要部分,通常具有与被加工材料相适应的形状和几何结构。
上模还需要具备足够的强度和刚度,以承受冲压工艺中产生的冲击力和挤压力。
2. 下模下模是冲裁模中与上模相对应的部分,其主要作用是支撑被加工材料并传递冲击力。
下模的结构应该确保被加工材料能够稳定地固定在上模的加工位置上。
3. 导向结构导向结构一般由导柱、导套等组成,用于定位和导向上模和下模的相对位置,以确保冲模运动的准确性和稳定性。
4. 冲头和冲针冲头和冲针是一些特殊冲裁工艺中常用的辅助部件。
冲头一般是用于在材料上打孔、压印等操作,而冲针常用于冲切较薄材料或特殊形状的材料。
四、冲裁模的设计原则在进行冲裁模的设计时,需要考虑以下几个原则:1.结构合理:冲裁模的结构应该能够满足冲裁工艺的要求,并能够方便材料的定位和加工。
2.强度与刚度:冲裁模需要具备足够的强度和刚度,以承受冲击力、挤压力等工艺中产生的载荷。
3.导向准确:冲裁模的导向结构应该具备高精度的定位和导向能力,以确保冲裁过程的准确性和稳定性。
冲压模具设计与制造-冲模结构及设计
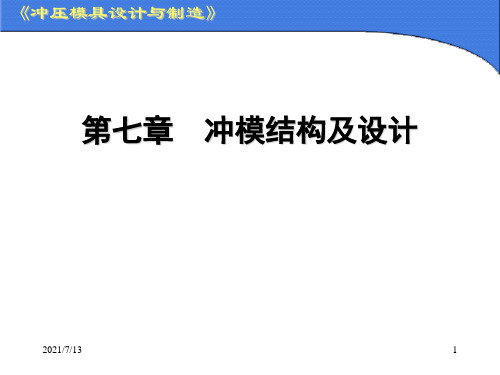
§7.2 冲模主要零件设计
七.连接与固定零件
1.固定板
将凸模或凹模按一定相对位置压 入固定后,作为一个整体安装在上 模座或下模座上。(H7/m6、H7/n6)
2.垫板
直接承受凸模的压力,以降低模 座所受的单位压力,防止模座被局 部压陷,
2021/7/13
37
§7.2 冲模主要零件设计
3.模柄
作为上模与压力机滑块连接的零件。 ① 与压力机滑块上的模柄孔正确配合,安装可靠; ② 与上模正确而可靠连接(H7/m6、H7/h6) 。
2021/7/13Fra bibliotek14§7.2 冲模主要零件设计
2021/7/13
15
§7.2 冲模主要零件设计
(2) 凹模刃口的结构类型
2021/7/13
16
§7.2 冲模主要零件设计
a. 直壁刃口 ① 刃口强度较高,修磨后刃口尺寸不变。 ② 凹模内易积存废料或冲裁件,尤其间隙较小时,刃口直壁
部分磨损较快。 ③ 用于冲裁形状复杂或精度要求较高的零件。
2021/7/13
10
§7.2 冲模主要零件设计
b. 非圆形凸模
a) 台肩固定
b) 铆接固定
2021/7/13
c) 直通式凸模
11
§7.2 冲模主要零件设计
c. 大、中型凸模 镶拼式凸模不但节约贵重的模具钢,而且减少锻造、热处理和 机械加工的困难。
2021/7/13
12
§7.2 冲模主要零件设计
工艺结构部分
定位零件
6.定位销(定位板)
7.侧压板
8.侧刃
9.卸料板
压、卸料及出件零件
10.压料板(压边圈) 11.顶件器
12.推件器
冲压模具及冲模设计

冲压模具及冲模设计引言冲压模具是冲压工艺中不可缺少的工具,通过将金属板材置于模具之间施加压力从而将其裁剪成所需形状。
冲模设计则是为了确保冲压过程能够顺利进行而进行的重要步骤。
本文将深入介绍冲压模具及冲模设计的相关内容。
一、冲压模具的分类根据冲压工艺的不同需求,冲压模具可分为以下几类:1.单工位模具:每工位完成一道工序,适用于简单形状的冲压件。
2.进料式模具:通过进料装置将金属板材连续送入模具进行冲压,适用于大批量生产。
3.连续式模具:在连续进行冲压的同时,实现多道工序的一体化,提高生产效率。
4.多工位模具:在一个模具上设置多个工位,适用于复杂形状的冲压件。
二、冲压模具的设计原则在进行冲模设计时,需要遵循以下几个原则:1.合理布局:模具的各个部分要合理分布,便于材料的进料、定位和排渣。
2.简化结构:尽量减少模具的零件数量和工艺复杂度,提高制作和维修的便利性。
3.提高刚度:通过加强模具的结构,提高其刚度和稳定性,以提高冲压精度和延长使用寿命。
4.正确选择材料:根据冲压件的材质和数量,选择合适的模具材料,以确保其耐磨性和抗拉强度。
三、冲模设计的步骤进行冲模设计时,需要按照以下步骤进行:1.冲压件分析:对冲压件进行分析,包括形状、尺寸、材质等方面的特点。
2.模具结构设计:根据冲压件的特点,设计模具的整体结构,包括上模、下模、导向机构等部分。
3.模具零部件设计:对模具的各个零部件进行设计,包括定位销、排渣孔、导向柱等。
4.模具加工制造:根据设计图纸,进行模具的加工制造,包括车削、铣削、磨削等工序。
5.模具调试和试模:对制造好的模具进行调试和试模,确保其能够正常运行。
6.模具维护和维修:及时进行模具的维护和维修,以延长其使用寿命和保证冲压质量。
四、冲压模具的常见问题及解决方法在冲压模具的使用过程中,可能会遇到以下常见问题:1.模具磨损:由于长时间使用和摩擦,模具表面可能会磨损,影响冲压质量。
解决方法包括定期维护和更换磨损部件。
冲模设计概述及流程

冲模设计概述及流程冲模设计是指在塑料成型和金属加工等工艺中,按照所需零件的形状和加工要求,设计并制作适合的冲模以完成零件的成型工作。
冲模设计是制造工程中的一个重要环节,对制造工艺水平和产品质量有着直接的影响。
本文将对冲模设计的概述及流程进行探讨。
一、概述冲模设计是从产品设计到产品加工工艺的过渡,是将产品设计图转化成冲模图的过程。
冲模设计的目标是建立一个能够满足产品要求的合理工艺和工装设备,同时也需要考虑到生产的经济性和技术可行性。
冲模设计要求设计人员具备丰富的工艺和工装设备的知识,能够准确把握产品形状和尺寸要求,熟悉材料的性能和成型工艺,以及掌握冲模设计的基本原理和设计方法。
冲模设计的基本流程包括产品分析、工艺设计、冲模结构设计、零件设计和冲模制造等几个环节。
下面将详细介绍每个环节的具体内容。
二、流程1. 产品分析产品分析是冲模设计的第一步,主要目的是对所需加工的产品进行形状、尺寸、材料等要素的分析。
通过对产品的分析,设计人员可以了解产品的加工要求和特点,为后续的工艺设计和冲模结构设计提供依据。
2. 工艺设计工艺设计是冲模设计的核心环节,它直接决定了产品的成型质量和生产效率。
在工艺设计过程中,设计人员需要选择合适的冲压工艺、确定合理的冲孔顺序和工序、制定冲孔加工参数等。
同时,还需要考虑到材料的弹性变形、回弹和表面质量等因素,以确保冲制零件的精度和质量。
3. 冲模结构设计冲模结构设计是根据产品的加工要求和工艺设计的结果,设计出适合的冲模结构。
冲模结构设计包括冲头设计、下模设计、导向机构设计、顶出机构设计等。
在冲模结构设计中,需要考虑到冲孔力的传递、支撑和导向等问题,同时还需要满足冲孔顺序、定位精度和冲孔效率等要求。
4. 零件设计零件设计是指根据产品的形状和尺寸要求,进行冲模零部件的设计。
在零件设计中,需要考虑到零件的材料、强度、刚度和耐磨性等要求,同时还需要满足冲模结构的装配和使用要求。
5. 冲模制造冲模制造是根据冲模设计结果,进行冲模的制造。