APQP-PPAP(2)
五大工具手册APQP、PPAP、SPC、MSA、FMEA

五大工具手册APQP、PPAP、SPC、MSA、FMEA1.产品质量先期策划(APQP)、2.测量系统分析(MSA)、3.统计过程控制(SPC)、4.生产件批准(PPAP)5.潜在失效模式与后果分析(FMEA)一、APQP(Advanced Product Quality Planning)即产品质量先期策划,是一种结构化的方法,用来确定和制定确保某产品使顾客满意所需的步骤。
产品质量策划的目标是促进与所涉及的每一个人的联系,以确保所要求的步骤按时完成。
有效的产品质量策划依赖于公司高层管理者对努力达到使顾客满意这一宗旨的承诺。
产品质量策划有如下的益处:◆引导资源,使顾客满意;◆促进对所需更改的早期识别;◆避免晚期更改;◆以最低的成本及时提供优质产品二、PPAP:生产件批准程序(Production part approval process)ppap生产件提交保证书:主要有生产件尺寸检验报告,外观检验报告,功能检验报告,材料检验报告;外加一些零件控制方法和供应商控制方法;主要是制造形企业要求供应商在提交产品时做ppap文件及首件,只有当ppap文件全部合格后才能提交;当工程变更后还须提交报告。
ppap是对生产件的控制程序,也是对质量的一种管理方法。
三、SPC(Statistical Process Control)即统计过程控制,主要是指应用统计分析技术对生产过程进行适时监控,科学区分出生产过程中产品质量的随机波动与异常波动,从而对生产过程的异常趋势提出预警,以便生产管理人员及时采取措施,消除异常,恢复过程的稳定从而达到提高和控制质量的目的。
SPC非常适用于重复性的生产过程,它能够帮助组织对过程作出可靠的评估,确定过程的统计控制界限判断过程是否失控和过程是否有能力;为过程提供一个早期报警系统,及时监控过程的情况,以防止废品的产生,减少对常规检验的依赖性,定时以观察以及系统的测量方法替代大量检测和验证工作。
《APQP及PPAP审核》课件
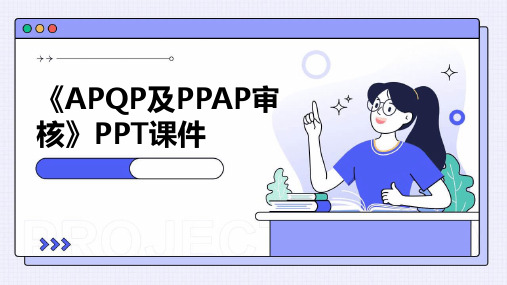
06 APQP及PPAP审核案例 分析
APQP审核案例
01
02
03
04
案例一
某汽车零部件供应商的APQP 审核
案例二
某电子产品的APQP审核
总结
APQP审核的要点和注意事项
分析
通过以上案例,分析APQP审 核中常见的问题和改进措施
PPAP审核案例
案例三
某机械制造企业的PPAP审核
案例四
某塑料制品的PPAP审核
03
02
APQP:确保产品从概念设计到量产的过程 得到有效的控制,以满足客户要求。
04 流程
APQP:需求确定、产品设计、过程设计 、产品验证、过程验证、反馈和纠正措施
。
05
06
PPAP:提交申请、形式审核、现场审核 、批准或拒绝。
审核关键要素的异同点
APQP
产品质量、生产能力、 供应商管理、过程控制
文件审核
顾客对提交的文件进行审核,确认其完整性和 准确性。
现场审核
顾客对供应商的生产现场进行审核,检查生产设 备、工艺流程、检验设备等是否符合要求。
样品测试
顾客对供应商提供的样品进行测试,确认其性能和 外观是否符合要求。
反馈与改进
根据审核和测试结果,顾客向供应商反馈意见并 要求其进行改进。
批准与供货
重要性
PPAP审核是汽车行业供应链管理中的重要环节,是供应商质量保证能力的重要组成部分。通过PPAP审核,可以 确保供应商在产品开发、工艺开发、生产制造等方面的能力符合顾客要求,提高产品质量和生产效率,降低生产 成本和风险。
PPAP审核的流程
提交PPAP申请
供应商向顾客提交PPAP申请,包括产品图纸 、工艺流程图、检验标准等文件。
APQP各个阶段

APQP各个阶段第一篇:APQP各个阶段1.APQP有哪几个阶段?共分为五个阶段:第一阶段:计划和确定项目(立项)第二阶段:产品的设计和开发(样件试制)第三阶段:过程的设计和开发(试生产策划)第四阶段:产品和过程的确认(试生产)第五阶段:反馈评定和纠正措施(量产及持续改进)没有产品设计责任时:第一阶段:计划和确定项目第二阶段:样品试制第三阶段:试生产准备第四阶段:小批量试生产第五阶段:批量生产2.APQP与几大工具的关系以及导入时间.3.APQP与工具4.QPN 阶段顺序图5.QPN相关概念序号缩写英文原文解释OTSOFF TOOL SAMPLE用批量生产的工模器具制造出的样件 2PVSProduktions – Versuchs-Serie批量试生产 3TMATrial Manufacturing Agreement试制协议QSVQualitaes-Sicherungs-Vereinbarung质量保证协议 5BMGBau-Muster-Genehmigung产品工程样件性能检验认可 6 B-Freigabe采购认可D-Freigabe试制/0批量的认可 8P-Freigabe计划认可 9TL技术资料汇编LHLastenHeft要求汇总书记 11Pflichtenheft责任汇总书记MEMarkt-Einfuehrung市场导入MISManagement Informations-System管理信息系统 14Nullserie零批量QPNQualifizierungs-Programm Neuteile新零件质量提高计划 16SOPStart-Of-Production批量生产启动Standard Operating Procedure标准操作程序 17QSR质量体系要求APQPAdavanced part quality plan高级产品质量计划 19PPAPproduct part approval procedure生产件批准程序 20QSA质量体系评审MSAmeasurement system analysis测量系统分析 22FMEA失效模式及结果分析 23SPC统计过程控制第二篇:APQP各阶段清单APQP各阶段清单第一阶段:计划和确定项目序号表单责任部门市场调查分析表业务计划/营销策略产品/过程基准数据顾客要求可行性报告、风险评估报价单合同评审新产品开发申请表多方论证小组成员和职责表新产品开发进度计划表设计任务书产品质量保证计划设计目标确定产品可靠性和质量目标初始材料清单(产品明细表)初始过程流程图设备、工装、量具、试验装置初始清单产品和过程特殊特性初始清单产品保证计划阶段总结第二阶段:产品设计和开发序号表单责任部门DFMEA设计FMEA检查表产品可制造性和装配设计设计验证设计评审样件控制计划样件控制计划检查表工程图样工程规范材料规范图样和规范的更改新设备、工装和设施要求新设备、工装和设施采购产品和过程特殊特性清单量具和试验设备要求量具和试验设备采购生产率过程能力、成本指标新设备、工装和试验设备检查表小组可行性承诺和管理者支持第三阶段:过程设计和开发序号表单责任部门包装标准产品/过程质量体系检查表过程流程图过程流程图检查表车间平面布置图车间平面布置检查表特性矩阵图过程FMEA过程FMEA检查表试生产控制计划控制计划检查表作业指导书接收准则可追溯性预期设计质量、可靠性、可测量性数据测量系统分析计划(MSA)初始过程能力研究计划样件制造与测试包装规范阶段总结和管理者支持第四阶段:产品和过程确认序号表单责任部门试生产测量系统分析评价初始过程能力研究生产件批准生产确认试验试验报告包装评价生产控制计划生产控制计划检查表过程审核质量策划认定和管理者支持第五阶段:反馈、评定和纠正措施序号表单责任部门生产计划减少变差(X-R控制图)质量成本分析报告顾客满意度调查表顾客信息反馈更改或更新P、DFMEA和控制计划编制产品审核计划和性能检测计划项目经验教训总结第三篇:APQP的五个阶段APQP的五个阶段第一阶段:计划和确定项目第二阶段:产品设计和开发第三阶段:样件试制及过程设计开发第四阶段:产品和过程确认第五阶段:反馈评定和纠正措施(量产)没有产品设计责任时:第一阶段:计划和确定项目第二阶段:样品试制第三阶段:试生产准备第四阶段:小批量试生产第五阶段:批量生产APQP是五大手册之一,共分为五个阶段:第一阶段:计划和确定项目(立项)第二阶段:产品的设计和开发(样件试制)第三阶段:过程的设计和开发(试生产策划)第四阶段:产品和过程的确认(试生产)第五阶段:反馈评定和纠正措施(量产及持续改进)五大工具中APQP为产品质量先期策划,在策划的不同阶段,先后会用到其他几种参考手册介绍的方法.换句话说:“APQP是个筐,其他工具筐里装”.第四篇:APQP五大阶段APQP五大阶段,SQE需要做什么?问题背景:我司是发动机主机厂,在开发一款新发动机,我司实施APQP,某供方在为我司供活塞,也在实施活塞新项目APQP 问题:一、我司APQP五大阶段,各阶段主机厂SQE需要做什么?二、供方APQP五大阶段,各阶段主机厂SQE又需要做什么?该问题时国内某知名主机厂和外资某前三甲一级供方的面试题目,比较典型,请各位按照APQP五大阶段分阶段回答,感激不尽,共勉!附:APQP五阶段如下:第一阶段:计划和项目确定第二阶段:产品设计和开发第三阶段:过程设计和开发第四阶段:产品和过程确认第五阶段:反馈,评定和纠正措施回答在前面补充一下,很多朋友提到SQE除了PPAP,其他就是简单参与参与,但是我多年的经验告诉我,光是打酱油是不行滴,参与时SQE更要擦亮自己的双眼,紧盯团队是否能有质量的输出一些东西给供应商。
APQP第二阶段

DFMEA表格说明
(6)关键日期: 填入初次FMEA预定完成的日期,该日期不能超过计划开始生产的时间,比如
现在为第二阶段的样件FMEA,那么此FMEA的完成时间不能超过该样件开始生产的 时间。 (7)FMEA日期:编制此FMEA的日期
每一个于设计DFMEA列出的项目, 将在过程PFMEA的特殊过程管制中被列出.
注意符号的一致型:FMEA、控制计划、工艺文件、作业指导书、检验文件都必须
一致.
(15)频度(O) 指失效发生的可能性,可能发生的等级是一个值,评价方法1—10级,见下图 等级的判断方法: 1.过去服务取得资料和相关经验 2.零件是否为全新的产品?零件使用条件是否改变? 3.因目前的环境、设计要求、设备、工艺等是否能达到要求
正措施来降低RPN值。一般实务上, 较不注意RPN质的结果, 通常严重度数(S)较高 时, 就会特别注意。
(19)建议措施 建议采取的措施,其目的是为了降低S、O、D.
PPAP-过程流程图、PFMEA、控制计划的关系
根据过程流程图制定PFMEA,根据PFMEA制定控制计划
过程流程图
ቤተ መጻሕፍቲ ባይዱ
PFMEA
控制计划
4、DFMEA——设计阶段的潜在失效模式和后果分析 FMEA 分为设计DFMEA和过程PFMEA,设计阶段主要是对
零部件的材质性能的失效分析,过程阶段主要是产品在生产 过程的失效分析。
5、采购测料清单 6、采购新增物料清单
7、样件阶段总结表---阶段评价记录表
FMEA:潜在失效模式和后果分析
FMEA的最重要因素之一,它是一个“事前的行为”,而不是“事后的 行为”,为达到最佳效益,FMEA必须在设计或过程失效模式被无意纳入 设计产品之前进行。
质量管理五大工具介绍

五大工具(SPC,MSA,FMEA,APQP,PPAP)名词解释:SPC:Statistical Process Control,统计过程控制MSA:Measure System Analyse,测量系统分析FMEA:Failure Mode &Effct Analyse,失效模式和效果分析APQP:Advanced Product Quality Planning,产品质量先期策划PPAP:Production Part Approval Process,生产件批准程序APQP=Advanced Product Quality Planning中文意思是:产品质量先期策划(或者产品质量先期策划和控制计划)是QS9000/TS16949质量管理体系的一部分。
定义及其他知识点:产品质量策划是一种结构化的方法,用来确定和制定确保某产品使顾客满意所需的步骤。
产品质量策划的目标是促进与所涉及每一个人的联系,以确保所要求的步骤按时完成。
有效的产品质量策划依赖于高层管理者对努力达到使顾客满意这一宗旨的承诺。
ppap生产件批准程序(Production part approval process)ppap生产件提交保证书:主要有生产件尺寸检验报告,外观检验报告,功能检验报告,材料检验报告;外加一些零件控制方法和供应商控制方法;主要是制造形企业要求供应商在提交产品时做ppap文件及首件,只有当ppap文件全部合格后才能提交;当工程变更后还须提交报告。
ppap是对生产件的控制程序,也是对质量的一种管理方法。
SPC开放分类:质量、管理、质量管理、质量控制SPC是Statistical Process Control的简称统计过程控制利用统计的方法来监控制程的状态,确定生产过程在管制的状态下,以降低产品品质的变异SPC能解决之问题1.经济性:有效的抽样管制,不用全数检验,不良率,得以控制成本。
使制程稳定,能掌握品质、成本与交期。
质量管理五大工具PPAP

签名)
PPAP(4) DFMEA
PPAP(5) 过程流程图
PPAP(6) PFMEA
PPAP(7)
尺寸结果
注意: A.成品全尺寸(尺寸\功能
等) B.一出几的模具全部测
PPAP(8)
材料性能试验结果
备注:1.组成产品的材料 2.质量\环境或其它的性 能要求
1.完全批准 2.临时批准 3.拒收
PPAP资料的保存
1.该零件寿命周期加1个日历年的时间 2.严格按客户规定的时间进行保管
重点:只要正式生产过程 与PPAP有不同或停产12 个月以后再生产,就应与 顾客沟通,由其决定是否
需要重新提交PPAP
(标准格式)
PPAP(14)
外观批准报告 (标准格式)
PPAP(15) 样品产品
PPAP(16) 标准样品
PPAP(17)检查Fra bibliotek具(菲林\测试 架\治具)
PPAP(18) 顾客特殊要求
PPAP应当在何时提交
试生产完成后 (APQP第四阶段)
PPAP提交等级
等级1— 只向顾客提交保证书(对指定的外观项 目,还应提供一份外观批准报告);
PPAP 的适用范围
所有汽车生产件
PPAP要求的生产件产生的条件
1.连续性的生产过程 2.生产数量最少300PCS 3.稳定的生产过程 4.检测应由有资格的实验室进行
PPAP 由18部份内容构成
PPAP(1)
设计记录(设计输出 记录)
PPAP(2)
授权时的工程更改 (ECN/ECR)
PPAP(3)
等级2— 向顾客提交保证书和产品样品及有限的 支持数据;
等级3— 向顾客提交保证书和产品样品及完整的 支持数据;
APQPPPAP2课件

Work Instruction Development
Product and Process Validation
Ensure Continuous Improvement
Phase I
Phase II
Phase II
Phase III
Phase III
Phase III
APQP
A Perspective on 8-D and PFMEA and Control Plan During APQP and Afterwards
What is APQP?
APQP is a "defined" process for a product development system for Ford, Daimler- Chrysler, GM and their suppliers. APQP is an attempt to provide a common path and synchronization of product development activities.APQP is an attempt to ensure communication both within a company and between a company and its customer
Process Design and Development
Product and Process Validation
Production
Feedback Assessment and Corrective Action
Pilot
Launch
Concept Initiation/Approval
APQP的五个阶段

APQP的五个阶段第一阶段:计划和确定项目第二阶段:产品设计和开发第三阶段:样件试制及过程设计开发第四阶段:产品和过程确认第五阶段:反馈评定和纠正措施(量产)没有产品设计责任时:第一阶段:计划和确定项目第二阶段:样品试制第三阶段:试生产准备第四阶段:小批量试生产第五阶段:批量生产APQP是五大手册之一,共分为五个阶段:第一阶段:计划和确定项目(立项)第二阶段:产品的设计和开发(样件试制)第三阶段:过程的设计和开发(试生产策划)第四阶段:产品和过程的确认(试生产)第五阶段:反馈评定和纠正措施(量产及持续改进)五大工具中APQP为产品质量先期策划,在策划的不同阶段,先后会用到其他几种参考手册介绍的方法.换句话说:"APQP是个筐,其他工具筐里装".PPAP的目的是什么,为什么要进行PPAP?PPAP 就是Production part approval process中文是“生产件批准程序” 为什么要做这是目的是用来确定供应商是否已经正确理解了顾客工程设计记录和规范的所有要求,以及其生产过程是否具有潜在能力,在实际生产过程中按规定的生产节拍满足顾客要求的产品。
就是客户要确定你们是否达到批量生产他们所需产品的能力,做ppap就是给客户证明你们的能力的,能力够,那么一切ok,你们给他们供货;达不到他们所需要求,就over了。
PPAP一般包含什么内容啊?1.设计记录.2.工程更改文件(如果有)3,顾客工程批准(如果要求)4.设计FMEA5.过程流程图6.过程FMEA7.尺寸结果8.材料,性能试验结果9.初始过程研究10.测量系统分析11.具有资格的实验室文件.12.控制计划13,0件提交保证书.(PSW)14.外观批准报告(AAR)如果适用15.生产件样品,$散件部品要求检查清单16.标准样品17.检验辅具18.符合顾客特殊要求的记录总共18部分,这是标准的要求,在实际运用中那些要强制性提供,那些可以不提供,这要看客户的要求.也要根据公司的实际情况,吃透以上18点内容与PPAP的总的内容,你就明白了.否则你知道这个名称,不知道怎么样提供才是符合标准的,那对外企来说准会让你另做的.。
- 1、下载文档前请自行甄别文档内容的完整性,平台不提供额外的编辑、内容补充、找答案等附加服务。
- 2、"仅部分预览"的文档,不可在线预览部分如存在完整性等问题,可反馈申请退款(可完整预览的文档不适用该条件!)。
- 3、如文档侵犯您的权益,请联系客服反馈,我们会尽快为您处理(人工客服工作时间:9:00-18:30)。
Develop Control Plan
Determine Methods to Improve Process and Control Variation
Work Instruction Implement Control Plan and Standardize the Process
Development
The Target and The Goal
Link Between the Documents
Байду номын сангаас
Proce ss Flow
Ope ration Numbe r
Product/Proce ss Char acte ristic
Incoming Source s of Variation
PFM EA
Planning Production
Links Between the Tools
Contract Review Program Plan
DFMEA
Determine Customer Expectations and Plan for Quality Identify Key Characteristics
Benefits of APQP
• Ensures early planning takes place. • Directs resources to the customer. • Identifies required changes early in the process. • Provides quality product on time and at lowest cost. • Enables cross-functional inputs and outputs. • Addresses potential problems early
APQP
PPAP
APQP
A Perspective on 8-D and PFMEA and Control Plan
During APQP and Afterwards
What is APQP?
• APQP is a "defined" process for a product development system for Ford, DaimlerChrysler, GM and their suppliers.
Product and
Ensure Customer Expectations are Met
Process Validation
Ensure Continuous Exercise Management Oversight
Improvement
Phase I Phase II Phase II Phase III Phase III Phase III Phase III Phase IV Phase V
Customer and Supplier Involvement
• Customer may initiate planning process. • Supplier has the obligation to establish
cross-functional team to manage process. • Supplier should expect the same
performance from their subcontractors.
Determine Customer Requirements
• Print • Purchase Request or Request for
Quotation. • Statement of Work (SOW) • Customer visits and discussions. • Product checklists.
Prototype
Pilot
Launch
Planning Product Design and Development Process Design and Development Product and Process Validation
Feedback Assessment and Corrective Action
Team Feasibility Commitment
Produce Process Flow Diagrams
Conduct Process FMEA
Determine Risk and Feasibility
Associate Characteristics with Process Steps and Identify Key Characteristics Expose Sources of Variation and Finalize Key Characteristics
• APQP is an attempt to provide a common path and synchronization of product development activities.
• APQP is an attempt to ensure communication both within a company and between a company and its customer
Training
• Customer needs and expectations. • Working as a team. • Requirements of APQP • FMEA • APQP • PPAP
APQP Five Phase Process
Concept
Program
Initiation/Approval Approval
Control Plan Variation Class
Work Instructions
Process Flow Diagrams
• Updated after production trial run. • Need to indicate special characteristics
generated at each step. • Completed Along with Control Plan (APQP