第11.1内燃机曲轴加工工艺
曲轴加工工艺流程
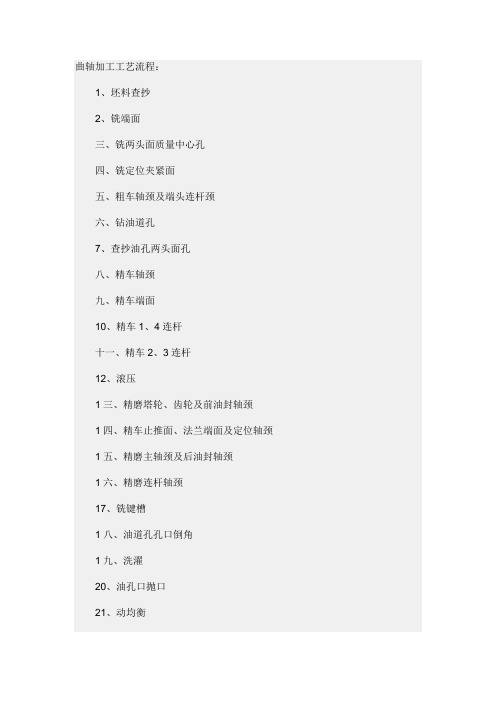
曲轴加工工艺流程:1、坯料查抄2、铣端面三、铣两头面质量中心孔四、铣定位夹紧面五、粗车轴颈及端头连杆颈六、钻油道孔7、查抄油孔两头面孔八、精车轴颈九、精车端面10、精车1、4连杆十一、精车2、3连杆12、滚压1三、精磨塔轮、齿轮及前油封轴颈1四、精车止推面、法兰端面及定位轴颈1五、精磨主轴颈及后油封轴颈1六、精磨连杆轴颈17、铣键槽1八、油道孔孔口倒角1九、洗濯20、油孔口抛口21、动均衡22、减外增补均衡去重2三、清算键槽及油道孔2四、抛光2五、清算2六、终检27、防锈此中重要工序有:钻中心孔、连杆颈加工、滚压、抛光、动均衡中心孔-粗车-调质-半精车-精车(曲轴车床/偏心车床)-轴端螺纹孔-(表面热处理)-曲轴磨床(粗磨、精磨)曲轴是发动机最重要的机件之一:结构特点: 曲轴一般由主轴颈,连杆轴颈、曲柄、平衡块、前端和后端等组成。
一个主轴颈、一个连杆轴颈和一个曲柄组成了一个曲拐,曲轴的曲拐数目等于气缸数(直列式发动机);V型发动机曲轴的曲拐数等于气缸数的一半。
主轴颈是曲轴的支承部分,通过主轴承支承在曲轴箱的主轴承座中。
主轴承的数目不仅与发动机气缸数目有关,还取决于曲轴的支承方式。
曲轴的支承方式一般有两种,一种是全支承曲轴,另一种是非全支承曲轴。
全支承曲轴:曲轴的主轴颈数比气缸数目多一个,即每一个连杆轴颈两边都有一个主轴颈。
如六缸发动机全支承曲轴有七个主轴颈。
四缸发动机全支承曲轴有五个主轴颈。
这种支承,曲轴的强度和刚度都比较好,并且减轻了主轴承载荷,减小了磨损。
柴油机和大部分汽油机多采用这种形式。
非全支承曲轴:曲轴的主轴颈数比气缸数目少或与气缸数目相等。
这种支承方式叫非全支承曲轴,虽然这种支承的主轴承载荷较大,但缩短了曲轴的总长度,使发动机的总体长度有所减小。
有些汽油机,承受载荷较小可以采用这种曲轴型式。
曲轴的连杆轴颈是曲轴与连杆的连接部分,通过曲柄与主轴颈相连,在连接处用圆弧过渡,以减少应力集中。
曲轴的机械加工工艺

曲轴的机械加工工艺
曲轴的机械加工工艺一般包括以下几个步骤:
1. 钢材修整:使用机械设备将原材料钢坯进行切割、锯割等操作,使得其与曲轴的设计尺寸接近。
同时,还需要进行热处理,使得钢材达到所需的力学性能。
2. 钢材粗加工:通过车床、铣床等机械设备,对钢材进行车削、铣削等操作,使其形成初步的几何轮廓。
3. 曲轴片的制造:将钢材分成若干段,每段分别进行车削、铣削等操作,使得每个曲轴片的几何形状和尺寸符合要求。
4. 吊挂:将曲轴片的上下端面加工成平行和垂直的状态,然后进行悬挂,使得曲轴片的主轴中心线和整体曲轴的主轴中心线重合。
5. 精加工:使用磨床等设备,对曲轴片进行磨削,使其达到设计要求的尺寸和表面粗糙度。
6. 装配:将精加工好的曲轴片进行组装,根据设计要求将各段曲轴片组合在一起,形成完整的曲轴。
7. 检测:对制造好的曲轴进行质量检测,包括尺寸精度、加工粗糙度、内外表
面质量等方面的检查,以确保曲轴符合设计要求。
8. 表面处理:对曲轴进行表面处理,包括防腐蚀处理、表面涂层等,以提高曲轴的耐用性和使用寿命。
以上是曲轴的一般机械加工工艺,具体步骤和操作方式可能会因不同的曲轴类型和加工要求而有所不同。
曲轴加工工艺流程简述
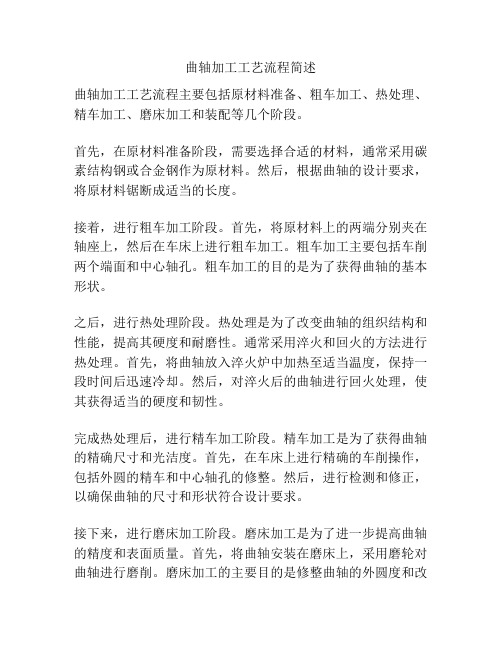
曲轴加工工艺流程简述曲轴加工工艺流程主要包括原材料准备、粗车加工、热处理、精车加工、磨床加工和装配等几个阶段。
首先,在原材料准备阶段,需要选择合适的材料,通常采用碳素结构钢或合金钢作为原材料。
然后,根据曲轴的设计要求,将原材料锯断成适当的长度。
接着,进行粗车加工阶段。
首先,将原材料上的两端分别夹在轴座上,然后在车床上进行粗车加工。
粗车加工主要包括车削两个端面和中心轴孔。
粗车加工的目的是为了获得曲轴的基本形状。
之后,进行热处理阶段。
热处理是为了改变曲轴的组织结构和性能,提高其硬度和耐磨性。
通常采用淬火和回火的方法进行热处理。
首先,将曲轴放入淬火炉中加热至适当温度,保持一段时间后迅速冷却。
然后,对淬火后的曲轴进行回火处理,使其获得适当的硬度和韧性。
完成热处理后,进行精车加工阶段。
精车加工是为了获得曲轴的精确尺寸和光洁度。
首先,在车床上进行精确的车削操作,包括外圆的精车和中心轴孔的修整。
然后,进行检测和修正,以确保曲轴的尺寸和形状符合设计要求。
接下来,进行磨床加工阶段。
磨床加工是为了进一步提高曲轴的精度和表面质量。
首先,将曲轴安装在磨床上,采用磨轮对曲轴进行磨削。
磨床加工的主要目的是修整曲轴的外圆度和改善其表面质量。
最后,进行装配阶段。
将其他零部件,如曲柄杆、连杆等组装到曲轴上,使之成为完整的曲轴装配件。
装配完成后,进行必要的检测和调整,确保曲轴的性能和工作可靠性。
以上就是曲轴加工工艺流程的简要描述。
曲轴的加工工艺复杂,需要经过多个步骤的加工和处理,才能获得高精度和高质量的曲轴产品。
曲轴工艺流程

曲轴工艺流程曲轴是内燃机的重要部件,其工艺流程直接影响着曲轴的质量和性能。
下面将从原材料选材、加工工艺、热处理工艺以及检测工艺等方面,介绍曲轴的工艺流程。
首先,原材料选材。
曲轴的主要原材料为钢铁,通常采用优质碳素结构钢或合金结构钢。
在选材时,需要考虑钢材的化学成分、机械性能、热处理性能等因素,以确保曲轴具有足够的强度和韧性。
其次,加工工艺。
曲轴的加工工艺主要包括锻造、粗加工、精加工和平衡加工等环节。
在锻造过程中,通过热加工使原材料形成所需的曲轴形状,并提高其内部组织的致密性和均匀性。
粗加工和精加工则是通过车、铣、刨、磨等机械加工方法,将锻造好的曲轴进行尺寸精度和表面粗糙度的加工,以满足设计要求。
平衡加工则是为了保证曲轴在高速旋转时的平衡性能,通常采用钻孔、切削等方法进行。
接下来是热处理工艺。
曲轴经过加工后需要进行热处理,以改善其组织结构和性能。
热处理工艺主要包括调质、表面强化和表面渗碳等。
调质是通过加热和淬火等方法,使曲轴获得适当的硬度和强度。
表面强化则是通过表面喷丸、镀层等方法,提高曲轴的表面硬度和耐磨性。
表面渗碳则是将碳元素渗入曲轴表面,形成一层高碳含量的渗层,以提高曲轴的表面硬度和疲劳强度。
最后是检测工艺。
曲轴在完成加工和热处理后,需要进行严格的检测,以确保其质量符合要求。
检测工艺主要包括尺寸检测、力学性能检测、表面质量检测和非破坏检测等。
尺寸检测是通过测量仪器对曲轴的尺寸进行检测,以确保其尺寸精度符合设计要求。
力学性能检测则是通过拉伸、冲击等试验,检测曲轴的强度、韧性等力学性能。
表面质量检测主要是检测曲轴表面的硬度、粗糙度等指标。
非破坏检测则是采用超声波、磁粉、射线等方法,对曲轴进行内部缺陷的检测。
综上所述,曲轴的工艺流程包括原材料选材、加工工艺、热处理工艺和检测工艺等环节。
每个环节都对曲轴的质量和性能起着至关重要的作用,只有严格控制每个环节,才能保证曲轴具有优良的性能和可靠的质量。
曲轴的加工工艺
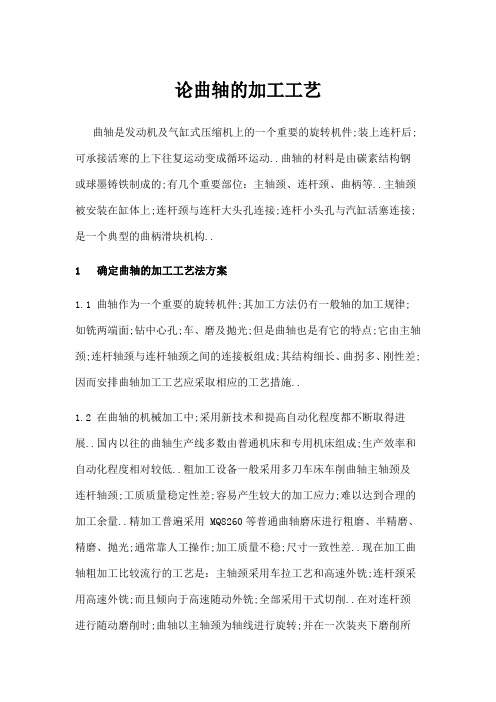
论曲轴的加工工艺曲轴是发动机及气缸式压缩机上的一个重要的旋转机件;装上连杆后;可承接活寒的上下往复运动变成循环运动..曲轴的材料是由碳素结构钢或球墨铸铁制成的;有几个重要部位:主轴颈、连杆颈、曲柄等..主轴颈被安装在缸体上;连杆颈与连杆大头孔连接;连杆小头孔与汽缸活塞连接;是一个典型的曲柄滑块机构..1 确定曲轴的加工工艺法方案1.1 曲轴作为一个重要的旋转机件;其加工方法仍冇一般轴的加工规律;如铣两端面;钻中心孔;车、磨及抛光;但是曲轴也是有它的特点;它由主轴颈;连杆轴颈与连杆轴颈之间的连接板组成;其结构细长、曲拐多、刚性差;因而安排曲轴加工工艺应采取相应的工艺措施..1.2 在曲轴的机械加工中;采用新技术和提高自动化程度都不断取得进展..国内以往的曲轴生产线多数由普通机床和专用机床组成;生产效率和自动化程度相对较低..粗加工设备一般采用多刀车床车削曲轴主轴颈及连杆轴颈;工质质量稳定性差;容易产生较大的加工应力;难以达到合理的加工余量..精加工普遍采用 MQ8260等普通曲轴磨床进行粗磨、半精磨、精磨、抛光;通常靠人工操作;加工质量不稳;尺寸一致性差..现在加工曲轴粗加工比较流行的工艺是:主轴颈采用车拉工艺和高速外铣;连杆颈采用高速外铣;而且倾向于高速随动外铣;全部采用干式切削..在对连杆颈进行随动磨削时;曲轴以主轴颈为轴线进行旋转;并在一次装夹下磨削所有连杆颈..在磨削过程中;磨头实现往复摆动进给;跟踪着偏心回转的连杆颈进行磨削加工..2 确定曲轴的加工工艺过程2.1 曲轴的结构及其特点..曲轴一般由主轴颈;连杆轴颈、曲柄、平衡块、前端和后端等组成..一个主轴颈、一个连杆轴颈和一个曲柄组成了一个曲拐;曲轴的曲拐数目等于气缸数直列式..主轴颈是曲轴的支承部分;通过主轴承支承在曲轴箱的主轴承座中..主轴承的数目不仅与气缸数目有关;还取决于曲轴的支承方式..连杆轴颈是曲轴与连杆的连接部分;在连接处用圆弧过渡;以减少应力集中..曲柄是主轴颈和连杆轴颈的连接部分;断面为椭圆形;为了平衡惯性力;曲柄处铸有或紧固有平衡重块..平衡里块用来平衡发动机不平衡的离心力矩;有时还用来平衡一部分往复惯性力;从而使曲轴旋转平稳..2.2 曲轴的主要技术要求分析..1主轴颈、连杆轴颈本身的精度;即尺寸公关等级IT6;表面粗糙度Ra值为1.25~0.63μm..轴颈长度公差等级为IT9~IT10..轴颈的形状公差;如圆度、圆拄度控制在尺寸公差之半..2位置梢度;包括主轴颈与连杆轴颈的平行度:一般为100mm之内不大于0.02mm;曲轴各主轴颈的同轴度:小型高速曲轴为0.025mm;中大型低速曲轴为0.03~0.08mm..3各连杆轴颈的位置度不大于±20’..2.3 曲轴的材料和毛坯的确定..曲轴工作时要承受很大的转矩及交变的弯曲应力;容易产生扭振、折断及轴颈磨损;因此要求用材应有较高的强度、冲击韧度、疲劳强度和耐磨性..常用材料有:一般曲轴为35、40、45钢或球墨铸铁;对于高速、重载曲轴;可采用40Cr、42Mn2V等材料..曲轴的毛坯根据批量大小、尺寸、结构及材料品种来决定..批量较大的小型曲轴;采用模锻;单件小批的中大型曲轴;采用自由锻造;而对于球墨铸铁材料则采用铸造毛坯..2.4 曲轴的机械加工工艺过程..曲轴的尺寸精度、加工表面形状精度以及位置精度的要求都很高;但刚性比较差;容易产生变形;这就给曲轴的机械加工带来了很多困难;必须予以充分的重视..曲轴需要加工的表面有:主轴颈、连杆轴颈、键槽、外圆..由于使用了工艺轴;铣键槽安排在切除工艺轴后;磨削外圆安排在保留工艺轴前..根据曲轴的结构特点及机械加工的要求;加工顺序大致可归纳为:铣两端面;车工艺轴和钻中心孔;粗、精车三连杆轴颈;粗、精车各处外圆;精磨连杆轴颈、主轴颈和外圆;切除工艺轴、车断面、铣键槽等..3 曲轴的机械加工工艺过程分析3.1 曲轴的机械加工工艺特点..曲轴除了具有轴的一般加工规律外..也有它的工艺特点;主要包括形状复杂;刚性差及技术要求高;针对这些特点应采取相应的措施..3.2形状复杂..曲轴主轴颈与连杆轴颈不在同一轴上线;偏心距有一定的尺寸要求;并且两轴有较高的位置度要求;同时主轴颈与连杆轴颈间有较大的平衡块;因此在工艺设计中应解决以下几点问题:a.设计加工连杆轴颈的偏心夹具;即连杆轴颈与机床主轴重合.并使夹具能回转180度;加工另一连杆轴颈..b.为消除加工时的不平衡力的产生;设计夹具时应精确设计平重..3.3 刚性差..由于本曲轴长颈比较大;同时具有曲拐;因此刚性较差..曲轴在切削力及自重的作用下会产生严重的扭曲及弯曲变形;特别在单边传动的机床上加工更为严重;在工艺设计中应解决以下问题:1粗加丁.时由于切削余带大;切削力也较大;可用中间托架来增强刚性;减小变形和振动;同时机床刀具及夹具都应有较高的刚度..2在加工时尽疳使切削力的作用相互抵消;可用前后刀架时横向进给..3合理安排工位次序以减少加工变形;按先粗后精的原则安排加工工序;逐步提高稍度..4在有可能产生变形的工序后面增设校直工序..3.4 技术要求高..曲轴技术要求较高;加工而多;需要保证的尺寸、形状、位置精度较多..因而总的工艺路线较长;精加工占有相当比例..加工时应要解决以下问题:1正确分配粗加工、半精加工及精加工余量..2粗基准选择用曲轴两端的中心孔..中心孔的加工以主轴颈外圆作为基准;这样能保证曲轴加丁径向及轴向加工余量的均匀性.. 3精加工时仍用中心孔作为基准;但要重新修磨中心孔;避免精加工时因中心孔磨损引起加工误差..也可一端用主轴颈定位;另一端用中心孔定位以提高刚度..4曲轴轴向定位以主轴颈轴肩定位;工艺设计时定位基准应尽量与设计基准一致..以上以普通加工方法进行介绍;目前国内有多种加工方法;并采用了先进的数控加工设备;大幅度的提商了工作效率和加工精度;使我国机械加工水平达到了国际先进行列..。
曲轴的加工工艺

论曲轴加工工艺曲轴是发动机及气缸式压缩机上一个关键旋转机件,装上连杆后,可承接活寒上下(往复)运动变成循环运动。
曲轴材料是由碳素结构钢或球墨铸铁制成,有多个关键部位:主轴颈、连杆颈、曲柄等。
主轴颈被安装在缸体上,连杆颈和连杆大头孔连接,连杆小头孔和汽缸活塞连接,是一个经典曲柄滑块机构。
1 确定曲轴加工工艺法方案1.1 曲轴作为一个关键旋转机件,其加工方法仍冇通常轴加工规律,如铣两端面,钻中心孔,车、磨及抛光,不过曲轴也是有它特点,它由主轴颈,连杆轴颈和连杆轴颈之间连接板组成,其结构细长、曲拐多、刚性差,所以安排曲轴加工工艺应采取对应工艺方法。
1.2 在曲轴机械加工中,采取新技术和提升自动化程度全部不停取得进展。
中国以往曲轴生产线多数由一般机床和专用机床组成,生产效率和自动化程度相对较低。
粗加工设备通常采取多刀车床车削曲轴主轴颈及连杆轴颈,工质质量稳定性差,轻易产生较大加工应力,难以达成合理加工余量。
精加工普遍采取MQ8260等一般曲轴磨床进行粗磨、半精磨、精磨、抛光,通常靠人工操作,加工质量不稳,尺寸一致性差。
现在加工曲轴粗加工比较流行工艺是:主轴颈采取车拉工艺和高速外铣,连杆颈采取高速外铣,而且倾向于高速随动外铣,全部采取干式切削。
在对连杆颈进行随动磨削时,曲轴以主轴颈为轴线进行旋转,并在一次装夹下磨削全部连杆颈。
在磨削过程中,磨头实现往复摆动进给,跟踪着偏心回转连杆颈进行磨削加工。
2 确定曲轴加工工艺过程2.1 曲轴结构及其特点。
曲轴通常由主轴颈,连杆轴颈、曲柄、平衡块、前端和后端等组成。
一个主轴颈、一个连杆轴颈和一个曲柄组成了一个曲拐,曲轴曲拐数目等于气缸数(直列式)。
主轴颈是曲轴支承部分,经过主轴承支承在曲轴箱主轴承座中。
主轴承数目不仅和气缸数目相关,还取决于曲轴支承方法。
连杆轴颈是曲轴和连杆连接部分,在连接处用圆弧过渡,以降低应力集中。
曲柄是主轴颈和连杆轴颈连接部分,断面为椭圆形,为了平衡惯性力,曲柄处铸有(或紧固有)平衡重块。
曲轴工艺技术报告

曲轴工艺技术报告曲轴工艺技术报告一、引言曲轴是内燃机的关键零部件之一,其工艺技术的优劣直接影响整个内燃机的性能和寿命。
本报告旨在介绍曲轴的工艺技术,并分析其在内燃机领域的应用。
二、曲轴的制造工艺1. 材料选择:曲轴通常由高强度合金钢制成,具有较高的耐磨性和耐腐蚀性。
常用的材料有40Cr、35CrMo等。
2. 热处理:热处理是曲轴工艺技术中的关键步骤,其目的是提高曲轴的硬度和强度。
常用的热处理方法有淬火、回火等。
3. 粗车:粗车是将预制材料进行毛坯成形的过程。
粗车过程中需要注意保证曲轴的圆度和平行度,以确保其后续加工准确度。
4. 精车:精车是将粗车过程中遗留的余量进行去除的工序。
精车过程需要控制加工精度,保证曲轴的几何尺寸和表面质量。
5. 平衡:曲轴是旋转部件,因此必须进行平衡处理。
平衡通过在曲轴上加装铅块或进行动平衡测试来完成,以减少振动和噪音。
三、曲轴工艺技术在内燃机中的应用曲轴是内燃机的核心部件之一,其工艺技术的优劣直接影响内燃机的性能和寿命。
以下将介绍曲轴工艺技术在内燃机中的应用。
1. 优化设计:通过优化曲轴的设计,可以使得内燃机的重量和运动惯量减小,进而提高内燃机的动力性能和燃油经济性。
2. 确保可靠性:通过精确的加工和严格的检测,可以保证曲轴的尺寸和形状的准确度,从而确保内燃机的运转平稳可靠。
3. 提高燃烧效率:通过改变曲轴的几何形状和重量分布,可以改变内燃机的气门正时,从而达到提高燃烧效率的目的。
4. 降低振动和噪音:通过平衡处理,可以减少曲轴的不平衡质量,降低内燃机的振动和噪音,提高其舒适性和使用寿命。
四、结论曲轴工艺技术是内燃机制造中不可或缺的一部分,它直接影响着内燃机的性能和寿命。
通过优化设计、精确加工和严格质量检测,可以提高曲轴的可靠性和工作效率。
曲轴工艺技术的不断发展,将为内燃机的进一步提高提供更多可能。
五、参考文献1. 李明. 内燃机曲轴的制造工艺[J]. 科技信息, 2020(15): 134-136.2. 张辉, 钟宝玉. 曲轴精加工技术的研究进展[J]. 计量与测试技术与装备, 2019, 7(4): 53-57.3. 赵斌. 曲轴磨削加工技术研究[J]. 特种加工技术, 2020, 46(12): 78-80.以上所述,是关于曲轴工艺技术的一份报告。
曲轴加工工艺
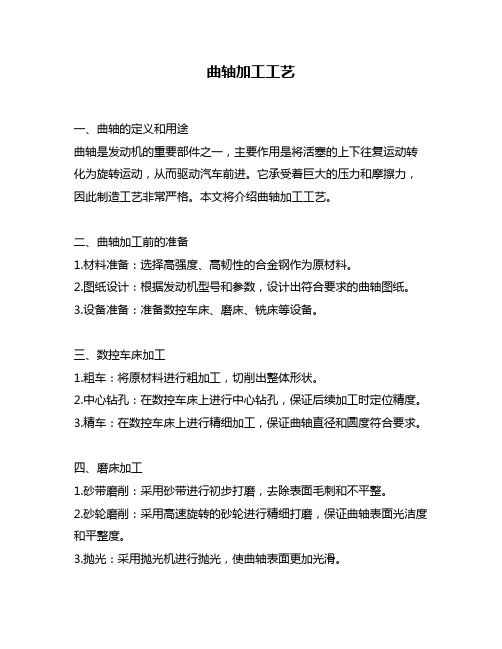
曲轴加工工艺一、曲轴的定义和用途曲轴是发动机的重要部件之一,主要作用是将活塞的上下往复运动转化为旋转运动,从而驱动汽车前进。
它承受着巨大的压力和摩擦力,因此制造工艺非常严格。
本文将介绍曲轴加工工艺。
二、曲轴加工前的准备1.材料准备:选择高强度、高韧性的合金钢作为原材料。
2.图纸设计:根据发动机型号和参数,设计出符合要求的曲轴图纸。
3.设备准备:准备数控车床、磨床、铣床等设备。
三、数控车床加工1.粗车:将原材料进行粗加工,切削出整体形状。
2.中心钻孔:在数控车床上进行中心钻孔,保证后续加工时定位精度。
3.精车:在数控车床上进行精细加工,保证曲轴直径和圆度符合要求。
四、磨床加工1.砂带磨削:采用砂带进行初步打磨,去除表面毛刺和不平整。
2.砂轮磨削:采用高速旋转的砂轮进行精细打磨,保证曲轴表面光洁度和平整度。
3.抛光:采用抛光机进行抛光,使曲轴表面更加光滑。
五、铣床加工1.铣槽:在铣床上对曲轴进行铣槽,以便安装汽缸连杆。
2.钻孔:在铣床上对曲轴进行钻孔,以便安装销子和油路。
六、渗碳处理将曲轴放入渗碳炉中,在高温高压下进行渗碳处理,增强曲轴表面硬度和耐磨性。
七、质量检测1.外观检测:检查曲轴表面是否平整、无裂纹、无气泡等缺陷。
2.尺寸检测:使用三坐标测量仪等设备对曲轴尺寸进行精确测量。
3.硬度检测:使用硬度计对曲轴硬度进行测试。
八、总结以上就是曲轴加工的详细流程。
为了保证曲轴的质量和使用寿命,每个环节都必须严格按照工艺要求进行操作。
只有这样,才能生产出符合要求的优质曲轴,为汽车行业的发展做出贡献。