磨削
螺纹的磨削方法与磨削液的选用
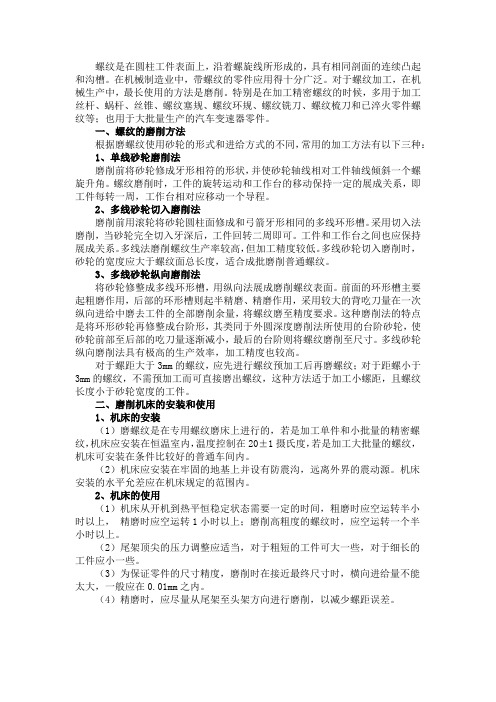
螺纹是在圆柱工件表面上,沿着螺旋线所形成的,具有相同剖面的连续凸起和沟槽。
在机械制造业中,带螺纹的零件应用得十分广泛。
对于螺纹加工,在机械生产中,最长使用的方法是磨削。
特别是在加工精密螺纹的时候,多用于加工丝杆、蜗杆、丝锥、螺纹塞规、螺纹环规、螺纹铣刀、螺纹梳刀和已淬火零件螺纹等;也用于大批量生产的汽车变速器零件。
一、螺纹的磨削方法根据磨螺纹使用砂轮的形式和进给方式的不同,常用的加工方法有以下三种:1、单线砂轮磨削法磨削前将砂轮修成牙形相符的形状,并使砂轮轴线相对工件轴线倾斜一个螺旋升角。
螺纹磨削时,工件的旋转运动和工作台的移动保持一定的展成关系,即工件每转一周,工作台相对应移动一个导程。
2、多线砂轮切入磨削法磨削前用滚轮将砂轮圆柱面修成和弓箭牙形相同的多线环形槽。
采用切入法磨削,当砂轮完全切入牙深后,工件回转二周即可。
工件和工作台之间也应保持展成关系。
多线法磨削螺纹生产率较高,但加工精度较低。
多线砂轮切入磨削时,砂轮的宽度应大于螺纹面总长度,适合成批磨削普通螺纹。
3、多线砂轮纵向磨削法将砂轮修整成多线环形槽,用纵向法展成磨削螺纹表面。
前面的环形槽主要起粗磨作用,后部的环形槽则起半精磨、精磨作用,采用较大的背吃刀量在一次纵向进给中磨去工件的全部磨削余量,将螺纹磨至精度要求。
这种磨削法的特点是将环形砂轮再修整成台阶形,其类同于外圆深度磨削法所使用的台阶砂轮,使砂轮前部至后部的吃刀量逐渐减小,最后的台阶则将螺纹磨削至尺寸。
多线砂轮纵向磨削法具有极高的生产效率,加工精度也较高。
对于螺距大于3mm的螺纹,应先进行螺纹预加工后再磨螺纹;对于距螺小于3mm的螺纹,不需预加工而可直接磨出螺纹,这种方法适于加工小螺距,且螺纹长度小于砂轮宽度的工件。
二、磨削机床的安装和使用1、机床的安装(1)磨螺纹是在专用螺纹磨床上进行的,若是加工单件和小批量的精密螺纹,机床应安装在恒温室内,温度控制在20±1摄氏度,若是加工大批量的螺纹,机床可安装在条件比较好的普通车间内。
成形磨削的加工原理

成形磨削的加工原理
成形磨削是一种通过磨削砂轮的旋转来加工工件的方法。
它的加工原理主要包括以下几个步骤:
1. 砂轮进给:砂轮被安装在磨床的主轴上,并以高速旋转。
工件被安装在工作台上,然后由工作台控制移动。
砂轮和工件之间有一个逐渐减小的间隙。
2. 磨粒切削:砂轮的旋转会使磨粒与工件接触并切削工件表面。
磨粒是在砂轮上固定的砂粒,具有尖锐的边缘。
当磨粒与工件接触时,通过切削和抛光的作用,将工件表面的材料去除。
3. 磨屑去除:在磨削过程中,被去除的工件材料以磨屑的形式产生。
这些磨屑会被冲洗液或喷气等方法及时清除,以防止堵塞磨削过程并影响加工质量。
4. 磨削力的形成:在磨削过程中,磨粒对工件表面施加力,使其发生变形和剥离。
这些力包括切削力、磨削力和垂向力。
切削力是指磨粒对工件的切割力,垂向力是指砂轮对工件施加的垂直力,磨削力是指切削力和垂向力的合力。
总的来说,成形磨削通过砂轮的旋转和磨粒的切削作用,将工件表面的材料去除,从而达到精加工和改善工件表面质量的目的。
加工原理的关键在于砂轮和工件之间的切削作用和力的相互作用。
简述磨削加工的工艺特点。

简述磨削加工的工艺特点。
磨削加工是一种利用磨削轮将工件表面削除材料的加工方法,其工艺特点如下:
1. 精度高:磨削加工可以实现高精度的加工,能够满足对工件精度要求较高的应用领域。
2. 表面质量好:磨削加工可以获得较好的表面光洁度和粗糙度,可以满足对工件表面平滑度和光洁度要求较高的应用。
3. 切削力小:相比其他切削加工方法,磨削加工的切削力较小,能够减少工件表面的热变形和机械变形。
4. 加工材料广泛:磨削加工适用于各种硬度的材料,包括金属、非金属和复合材料等。
5. 适用于复杂形状:磨削加工适用于各种复杂形状的工件加工,可以实现对工件的各种内外轮廓的加工。
6. 适用于批量生产:磨削加工可以实现对大批量工件的连续加工,提高生产效率。
总之,磨削加工具有高精度、好表面质量、切削力小、适用于各种材料和形状的优点,是一种广泛应用于工业生产中的高效加工方法。
磨削加工中的磨削力分析

磨削加工中的磨削力分析磨削加工是一种高精度的加工方式,可以用于加工各种材料的零部件。
其原理是使用磨料与加工物体之间的相对运动来去除材料表面的毛刺和瑕疵,制造出精密的表面和形状。
磨削加工的质量和效率与磨削力大小有着密切关系,因此对磨削力的分析和计算是磨削加工过程中极为重要的一环。
一、磨削加工的基本原理磨削加工是利用磨料与工件之间的相对运动,在压力的作用下,去除工件表面的毛刺和瑕疵,进而达到加工目的的过程。
在磨削加工中,磨料既是一个加工工具,也是一种加工介质。
其磨削力主要由切削力、磨合力和磨料轴向力三部分组成。
其中,切削力是主要作用力,因其大小和方向对于磨削加工的影响最为显著。
二、磨削力分析的原则磨削力是磨削加工过程中产生的一种重要力,其大小和方向对于成形精度、加工效率和工件表面质量等方面都有着显著的影响。
因此,了解磨削力的大小和方向,对于进行磨削加工质量的保证和高效率的实现都具有非常重要的作用。
在磨削力分析中,我们需要掌握以下几个基本原则:1.磨削力的大小和方向是磨削加工过程中的重要指标之一,需要进行精确的测量和分析。
2.在磨削加工过程中,应尽量降低磨削力的大小,实现高效率、高精度的加工目标。
3.在磨削力分析中,需要考虑到各个因素的综合影响,不能简单地直接计算或估算。
4.针对不同的磨削加工过程和实际需要,需要采用不同的磨削力分析方法和手段。
三、磨削力的计算方法磨削力的计算方法可以分为两种:经验计算法和基于力学原理的计算方法。
在实际应用中,一般采用经验计算和力学原理相结合的方法进行磨削力的估算。
一般情况下,磨削力的计算方法根据材料的硬度和材料的粘合程度分为两种:理论计算法和实验计算法。
其中,理论计算法以理论分析为基础,通过分析材料硬度和材料粘合程度之间的关系,计算出磨削力的大小和方向。
而实验计算法则以实验结果为依据,通过不同实验条件下的测量结果,计算出磨削力的大小和方向。
在实际应用中,常采用理论计算法和实验计算法相结合的方法,进行磨削力的估算。
磨削过程及规律的应用

进给停止,由于工艺 系统弹性恢复,实际 磨削深度并不为零, 增加磨削次数,磨削 深度逐渐趋于零,工 件的精度和表面质量 逐渐提高。
磨削规律的应用
在开始磨削时,采用较大的径向进 给量,压缩初磨和稳定阶段,以提高 生产效率;适当增长光磨时间,可更 好地提高工件的表面质量。
4. 磨削力和磨削温度
2)耕犁阶段(刻划阶段)
磨粒切入工件,在工件上耕犁出沟槽,工件产生塑 性变形,表层产生变形强化。
3)切削阶段
磨粒切入工件 ,使被挤压金属产生剪切滑移形成切 屑。这一阶段以切削为主,也有表层变形强化。
磨削的三个阶段:
初磨阶段:由于工艺系统弹性变形,实际磨削深度小
于进给量。
稳磨阶段:实际磨削深度等于进给量。
1)磨削力的主要特征 切向力F艺系统变形 和加工精度。
4. 磨削力和磨削温度
2)磨削热
磨削产生的高温是产生磨削表面烧伤、残余应力和 表面裂纹的原因。
表面烧伤:指磨削过程中磨削表面层金属在高温下产 生相变,从而其硬度与塑性发生变化的现象。
避免烧伤的措施: ①合理选用砂轮(可选硬度较软,组织疏松的砂轮) ②合理选择磨削用量(提高圆周进给速度和轴向进给 量,减少工件与砂轮接触时间。) ③采用良好的冷却措施(加大冷却液流量)
磨削过程及规律的应用
1.砂轮工作表面的形貌特征
1)磨粒在砂轮工作表面上是 随机分布的; 2)每一颗磨粒的形状和大小 都是不规则的。
1.砂轮工作表面的形貌特征
2. 磨屑的形成过程
单个磨粒的磨削过程分为三个 阶段:
1)滑擦阶段
磨粒只是在工件表面滑擦而过, 并未切削工件,工件仅产生弹 性变形。这一阶段由于摩擦作 用产生大量的热能使工件温度 升高。
常见的3种磨削方法介绍
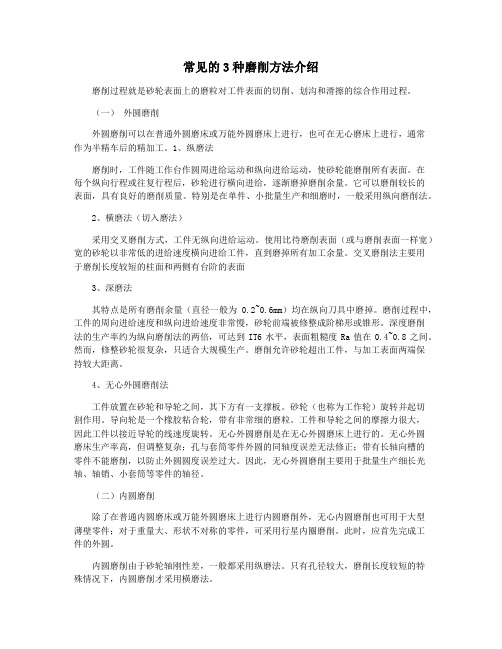
常见的3种磨削方法介绍磨削过程就是砂轮表面上的磨粒对工件表面的切削、划沟和滑擦的综合作用过程。
(一)外圆磨削外圆磨削可以在普通外圆磨床或万能外圆磨床上进行,也可在无心磨床上进行,通常作为半精车后的精加工。
1、纵磨法磨削时,工件随工作台作圆周进给运动和纵向进给运动,使砂轮能磨削所有表面。
在每个纵向行程或往复行程后,砂轮进行横向进给,逐渐磨掉磨削余量。
它可以磨削较长的表面,具有良好的磨削质量。
特别是在单件、小批量生产和细磨时,一般采用纵向磨削法。
2、横磨法(切入磨法)采用交叉磨削方式,工件无纵向进给运动。
使用比待磨削表面(或与磨削表面一样宽)宽的砂轮以非常低的进给速度横向进给工件,直到磨掉所有加工余量。
交叉磨削法主要用于磨削长度较短的柱面和两侧有台阶的表面3、深磨法其特点是所有磨削余量(直径一般为0.2~0.6mm)均在纵向刀具中磨掉。
磨削过程中,工件的周向进给速度和纵向进给速度非常慢,砂轮前端被修整成阶梯形或锥形。
深度磨削法的生产率约为纵向磨削法的两倍,可达到IT6水平,表面粗糙度Ra值在0.4~0.8之间。
然而,修整砂轮很复杂,只适合大规模生产。
磨削允许砂轮超出工件,与加工表面两端保持较大距离。
4、无心外圆磨削法工件放置在砂轮和导轮之间,其下方有一支撑板。
砂轮(也称为工作轮)旋转并起切割作用。
导向轮是一个橡胶粘合轮,带有非常细的磨粒。
工件和导轮之间的摩擦力很大,因此工件以接近导轮的线速度旋转。
无心外圆磨削是在无心外圆磨床上进行的。
无心外圆磨床生产率高,但调整复杂;孔与套筒零件外圆的同轴度误差无法修正;带有长轴向槽的零件不能磨削,以防止外圆圆度误差过大。
因此,无心外圆磨削主要用于批量生产细长光轴、轴销、小套筒等零件的轴径。
(二)内圆磨削除了在普通内圆磨床或万能外圆磨床上进行内圆磨削外,无心内圆磨削也可用于大型薄壁零件;对于重量大、形状不对称的零件,可采用行星内圈磨削。
此时,应首先完成工件的外圆。
内圆磨削由于砂轮轴刚性差,一般都采用纵磨法。
磨削的加工范围
磨削的加工范围磨削是一种常见的加工方法,广泛应用于各种材料的加工工艺中。
磨削的加工范围非常广泛,可以用于金属、非金属、硬质合金等各种材料的加工,可以实现高精度、高表面质量的加工要求。
本文将从不同角度探讨磨削的加工范围,以及磨削在工业生产中的重要性。
磨削的加工范围涵盖了各种不同形状和尺寸的工件。
无论是平面、曲面、内孔、外圆、内螺纹等复杂形状的工件,都可以通过磨削加工来实现精密加工。
磨削可以用于对工件表面进行粗糙度、平整度、圆度、圆柱度等各项指标的加工和控制,从而满足不同工件的加工要求。
磨削的加工范围还包括了各种不同硬度和性质的材料。
金属材料如钢铁、铝合金等,非金属材料如陶瓷、玻璃、塑料等,硬质合金、陶瓷等超硬材料,都可以通过磨削加工来实现高精度加工。
磨削可以有效地去除材料表面的氧化层、氧化皮、毛刺等缺陷,提高工件的表面质量和精度。
磨削的加工范围还包括了不同的加工精度要求。
从数微米到数十微米的加工精度要求,都可以通过磨削来实现。
磨削可以实现对工件表面粗糙度的控制,可以实现高精度的尺寸、形状和位置公差要求,可以实现对工件表面质量的要求,如镜面光洁度、光泽度等。
磨削的加工范围还包括了不同的加工环境和条件。
无论是手动磨削、半自动磨削,还是全自动磨削;无论是常规磨削、高速磨削,还是超精密磨削,都可以根据不同的加工要求和条件来选择适合的磨削方法和设备。
磨削可以在常温、高温、低温、真空、无尘等不同环境条件下进行加工,可以适应不同的工件材料和加工要求。
总的来说,磨削的加工范围非常广泛,可以满足各种不同形状、尺寸、硬度、性质、精度和环境条件的工件加工要求。
磨削作为一种重要的加工方法,在工业生产中发挥着不可替代的作用。
通过不断改进磨削技术和设备,提高磨削效率和质量,可以进一步拓展磨削的加工范围,满足不断增长的加工需求。
希望本文对读者对磨削的加工范围有所启发,对磨削技术的发展和应用有所促进。
简述磨削加工
磨削加工1. 磨削加工的概述磨削加工是一种通过研磨工具对工件表面进行切削的加工方法。
它通过切削工具与工件之间的相对运动,在切削、研磨和磨痕的共同作用下,将工件表面不平整层次的高点消除,从而得到平整、光滑的表面。
2. 磨削加工的原理磨削加工的原理是力学切削。
在磨削过程中,磨粒对工件表面的切削作用类似于多个微小切削刃对工件表面的切削作用,因此磨削可以看成是由许多微小切削刃共同作用的切削过程。
3. 磨削加工的分类磨削加工根据磨粒的尺寸和磨粒与工件之间的相对运动情况可以分为不同的类型,主要包括:3.1 粗磨粗磨是指在切削速度较低、磨粒尺寸较大的条件下进行的磨削加工,主要目的是迅速去除工件表面的大量金属,使其达到一定的粗糙度,为后续磨削过程提供条件。
3.2 精磨精磨是指在切削速度适中、磨粒尺寸适当的条件下进行的磨削加工,主要目的是进一步消除工件表面的细小凹坑和凸起,提高工件表面的精度和光洁度。
3.3 超精磨超精磨是指在切削速度较高、磨粒尺寸小的条件下进行的磨削加工,主要用于加工高精度、高光洁度的工件,以提高工件表面的质量。
4. 磨削加工的过程磨削加工通常包括以下几个基本工序:4.1 磨削前准备在进行磨削加工之前,需要对磨削工具进行选择和准备,包括选用合适的磨粒、绑定磨料和磨具、选择适当的磨削液等。
4.2 磨削磨削是磨削加工的核心过程,主要包括以下几个步骤:固定工件,调整磨削参数,启动磨削机床,进行磨削操作。
4.3 表面质量检测在磨削加工完成后,需要对工件表面的质量进行检测。
常用的表面质量检测方法有视觉检测、触觉检测和测量仪器检测等。
4.4 后续处理在完成磨削加工后,还需要进行一些后续处理工序,例如清洗工件、除去残留物和保护处理等,以确保工件表面的质量和性能满足要求。
5. 磨削加工的优点和局限性磨削加工具有以下优点:•可加工具有复杂形状的工件•可加工高硬度材料•可获得高精度的加工结果•可提高工件表面的质量和光洁度然而,磨削加工也存在一些局限性:•生产效率低,加工速度较慢•工艺过程较为复杂,需要一定的技术和经验•磨具和磨料的消耗较大,成本较高6. 磨削加工的应用领域磨削加工在各个制造行业中都得到广泛应用,特别是对高精度、高光洁度的工件加工需求较高的领域,例如:•汽车制造业:发动机缸体、曲轴等零部件的加工•刀具制造业:高精度刀具的生产加工•航空航天业:航空发动机叶片、轴承等零部件的加工•电子制造业:半导体芯片、磁头等精密元件的加工7. 磨削加工的未来发展趋势随着制造技术和加工要求的不断提高,磨削加工也在不断发展和改进。
第十二章 磨削
12.3 砂轮表面形貌图
有效磨粒切削刃,无效磨粒切削刃。 测量砂轮表面形貌目前主要用接触法: 1、静态法 2、动态法 3、工件复印法
12.4 磨削过程
一、磨削运动 磨削时,一般有四个运动。 1、主运动 砂轮的旋转运动,主运动的速度 就是砂轮外圆的线速度。 vs=πdsns/1000 2、径向进给运动:砂轮切入工件的运动,其 大小用径向进给量fr表示。又称磨削深度。
• • • •
天然金刚石 人造金刚石 CBN 普通磨料
二、粒度
粒度:磨粒颗粒的尺寸大小。
粗磨粒粒度(颗粒最大尺寸大于40μm ):用机械筛分法,
每平方英寸筛网上孔的数量,如60#,80#。粒度号数越大,
颗粒尺寸越细。
微粉磨粒粒度(颗粒尺寸小于40μm ):用显微镜分析法, 粒度号数即该颗粒最大尺寸的μm数。如W5,W3,W0.5
• 普通磨料固结磨具的标志按国标GB2484-84规定,其书写 顺序为:磨具形状、尺寸、磨料、粒度、组织、结合剂、 最高工作线速度。
国标GB2484-84
国际标准ISO
• 超硬磨料磨具的标志书写顺序为:形状、尺寸、 磨料、粒度、结合剂和浓度等。平行砂轮标志 示例如下:
超硬磨料磨具的结构
• 超硬磨料砂轮一般由磨料层、过渡层和基体组成。
四、磨削循环 一、磨削力的特征 磨削力的来源:一是各个磨粒的切削刃挤压切入工件后,工 件材料发生弹性、塑性变形时所产生的阻力;二是磨粒和结 合剂与工件表面之间的摩擦力。 以外圆纵磨为例,磨削力分解为切向力、法向力和轴向力。
由于磨粒上的切削刃为负前角,所以法向分力Fn远大于 切向分力Ft。轴向分力Fa最小。
以磨粒率表示的磨具组织及其应用范围
组织号 磨粒率 (%) 0 62 1 60 2 58 3 56 4 54 5 52 6 50 7 48 8 46
成形磨削的概念
成形磨削的概念成形磨削是一种精密磨削加工方法,通过使用特殊形状的砂轮将工件的外形加工成所需形状和尺寸的技术。
它广泛应用于精密磨削领域,如航空航天、汽车制造、模具制造、工具制造等。
成形磨削相比传统的磨削方法具有许多优势。
首先,其砂轮可以根据需要制作成各种形状,如平面、圆柱、球形、齿轮等,因此可以实现各种复杂外形的加工。
这使得成形磨削成为高精度、高效率的加工方法,尤其适用于要求外形特殊的零部件的制造。
其次,成形磨削可以实现无心磨削,即砂轮可以根据工件的轮廓形成相应的磨削轮廓,从而使得加工后的工件轮廓与模具或砂轮的轮廓一致。
这种特性使得成形磨削可以用于加工各种非圆形的工件,如凸轮、槽孔、齿轮等。
与其他加工方法相比,成形磨削具有更高的精度和更好的表面质量。
第三,成形磨削具有较大的自适应能力。
由于砂轮可以根据工件轮廓变形,因此在加工时可以自动调整切削参数,使得加工过程更加稳定和可靠。
这种自适应能力使得成形磨削能够应对工件形状复杂、切削条件发生变化等情况,提高加工效率和质量。
成形磨削的加工过程主要包括以下几个步骤:首先,选择合适的砂轮,并安装在磨床主轴上。
其次,根据工件的轮廓形状调整砂轮的位置和方向,并固定在磨床上。
然后,通过调节磨床的进给量和转速,使得砂轮与工件表面接触,并开始进行磨削。
在磨削过程中,砂轮会根据工件的轮廓变形,从而使得磨削的切削条件逐渐适应工件的形状。
最后,根据需要进行润滑和冷却处理,以保证加工质量。
成形磨削还可以与其他加工方法结合使用,如电火花加工、齿轮加工等。
这种组合加工可以进一步提高加工的精度和效率。
此外,成形磨削还可以与数控技术相结合,实现自动化和智能化加工,提高生产效率和质量。
总之,成形磨削是一种重要的精密磨削加工方法,其特点是可以根据工件的轮廓形状来磨削,并具有较高的精度、表面质量和自适应能力。
在工业生产中,成形磨削广泛应用于各种外形复杂、精度要求高的零部件的制造,对提高飞机、汽车、机床等行业产品的质量和性能具有重要意义。